ABSTRACT
The objective of this work is to examine the fire resistance of natural composite materials (NCM). The reinforcements used in this work are coir, cotton, Palmyra leaf stream, sisal fiber, and matrix selected for natural rubber resin (latex). The fibers as reinforcement and natural rubber as the matrix phase were considered, and then the composite was manufactured through the hand lay-up open mold method. The chemical compositions of specimens treated with inorganic flame retardant chemicals (Al(OH)3, Mg(OH)2, zinc borate, ZnO, and zirconium oxide). The selection of flame retardant chemicals is based on their high melting temperature, low toxicity, low smoke emission, low burning rate, easy availability, and low cost. The thermal analysis of the horizontal burn test, TGA, DSC, and cone calorimeter analysis was carried out to understand the material’s thermal stability. The important finding of this experimental work is to analyze the micro structural and thermal stability of various compositions of flame-retardant composite materials. In all aspects, the zinc-borate and zirconium oxide-added composites show more advantages in flame retardant properties compared to other composite materials.
摘要
本工作的目的是检验天然复合材料(NCM)的耐火性. 本工作中使用的增强材料是椰壳、棉花、棕榈叶、剑麻纤维和天然橡胶树脂(乳胶)基质. 以纤维为增强材料,以天然橡胶为基体相,采用手工叠层开模法制备复合材料. 用无机阻燃剂(Al(OH)3、Mg(OH)2、硼酸锌、ZnO和氧化锆)处理的试样的化学成分. 阻燃化学品的选择基于其高熔点、低毒性、低烟排放、低燃烧速率、易于获得和低成本. 进行了水平燃烧试验的热分析、TGA、DSC和锥形量热计分析,以了解材料的热稳定性. 本实验工作的重要发现是分析了不同成分阻燃复合材料的微观结构和热稳定性. 在各个方面,与其他复合材料相比,添加硼酸锌和氧化锆的复合材料在阻燃性能方面显示出更多的优势.
Introduction
In recent decades, fire-related incidents have become increasingly catastrophic, resulting in massive human and asset losses. The incomplete survey shows that asset loss due to fire is calculated at 97 million each year, with over 3000 injuries. There are $5–6 million in worldwide financial losses per year, equal to 0.3% of global GDP, and 0.1 million civilian deaths (Kandola Citation2012; N. K. Kim, Dutta, and Bhattacharyya Citation2018; Liang, Neisius, and Gaan Citation2013). As a result, the critical issue that society is concerned about is fire avoidance. Flame retardants are used to reduce the devastation caused by flames on people, assets, and the ecosystem. Flame retardant procedures involve the application of a remedy to products (such as textiles and plastics) to avoid fires from the beginning, prevent the growth of fires, and minimize fire losses (Alongi, Carosio, and Kiekens Citation2016; Bar, Alagirusamy, and Das Citation2015; Canıtez, Yüksel Yılmaz, and Çelik Bedeloğlu Citation2022). As a result, commercial and scientific research initiatives are now being utilized for the development of effective flame retardant systems for NCM (Karim-Nejad, Nazari, and Davodi-Roknabadi Citation2015).
The growth of a fire can be described as follows: When a fire starts, it develops quite quickly, and after a few minutes, it becomes dramatically important: all the vapor and heat start a general “flash-over.” Once it reaches that stage, there is no longer any way to stop it.
In the current study, we discovered that NCMs do not maintain upward flame propagation when the external radiation flux does not exist. This was followed by a section specifically to modify the flammability effort of natural composite materials using various fire retardants, such as inorganic flame retardant chemicals (Aluminum hydroxide, Magnesium hydroxide, Zinc borate, Zinc oxide, and Zirconium oxide) are experimented in the Centre for Nano Technology, Mepco Schlenk Engineering College in Sivakasi, Tamil Nadu. These chemicals can enhance flame-retardant properties as a unique filler or blend in a polymers or as a filler in flame-retardant chemicals, which can protect many types of materials (Amjad, Anjang Ab Rahman, and Shukur Zainol Abidin Citation2022; Khalili et al. Citation2019; Sain et al. Citation2004). When flame retardants are contained in a material, they can prevent burning in three ways. First, interfere with the combustion process of a fire chain (Jiao and Chen Citation2011; Kabir et al. Citation2012; Y. Kim, Lee, and Yoon Citation2021; Sen and Kumar Citation2010), which includes preventing or slowing flashover or the explosion of flames that completely cover a room and make escape extremely difficult. Second, slow down the breakdown method by physically isolating the existing fuel from the material source with a fire-resistant “char” flim. Third, emit H2O, N2, or any other inert gas to reduce the presence of flammable gas and oxygen in the flame production area (Bharath and Basavarajappa Citation2014; Zhao et al. Citation2009).
The fire prevention methods nowadays are utilized to safeguard using natural composites with a flame-retardant deposit that acts as a resistive layer at the time of fire. The characteristics of the synthetic polymeric materials and natural composite materials (NCM) in this research input may be correlated with energy relationships in the molecules (Attia et al. Citation2021). The net thermal effect of combustion can be greater in synthetic materials than in natural materials. The most important energy factors are that combustion energies tend to melt and drip, increasing flame propagation (Chen and Wang Citation2010). Liu and Alongi showed that energy increases with molecular weight and may be further increased by the introduction of polar groups into the polymeric material structure. If the combustion energy exceeds the primary bond energies, the polymer molecules will decompose before they volatilize (Wang et al. Citation2017). This decomposition may lead to char formation. Therefore, the research gap identified in this area is that the natural fiber-reinforced natural latex rubber resin added to flame retardant chemicals will increase in hydrogen bonding, leading to higher melting points that will tend to favor the flame retardant effect (Knights, Nascimento, and Manners Citation2022).
In this method of fire fighting, the basic idea is to produce a various composition of composites that can protect the material and limit degradation, isolating the surface from heat and preventing the release of degradation products. This flame-retardant chemical barrier inhibits both heat transmission from the heat energy to the material and mass transfer from the material to the heat energy, resulting in material conservation.
In recent years, a new approach has been investigated as a substitute for halogenated flame retardants, which are becoming increasingly sensitive to additives due to health and environmental concerns. This new approach is to enhance the flame-retardant properties of natural composites via fillers, particularly inorganic flame-retardant chemicals (Qian et al. Citation2014). In this research work, some of the standard tests (Bourbigot and Bensabath, Sarazin, and Bourbigot Citation2021), such as ASTM E 162 for horizontal flame spread, TGA, DSC, and cone calorimetric, indicate that materials that are normally considered safe may behave acceptably under an actual fire situation, and the results show that products that are generally deemed safe may perform well in a fire.
Experimental
Materials
The mechanically extracted natural fiber reinforcements are coir, cotton, Palmyra leaf steam, and sisal fibers, which are converted into non-woven mats in the size of 500 × 500 mm was performed using an Multi-Fiber Decorticator (model: MFD-200, USA made). These fibers compositions are quite complex, because they are not a pure single molecules it is a combinations of cellulose, hemicellulose, lignin, pectin, and waxes presents, so deficult to produce chemical formulas and also it is highly depends on growth condition, species and processing method. The sizes of the fibers are in the range of 150–300 µm (coarser), density of fibers are in the range of 1.2–1.5 g/cm3, Moisture absorption of fibers are in the range of 8–25% and molar mass presents in the fiber composition Cellulose 152,000–210,000 g/mol; Hemicellulose around 60,000 g/mol; Lignin 11,000 to 190,000 g/mol, which was purchased from Textile Physics/Chemistry Division, The South India Textile Research Association, Civil Aerodrome Post, Coimbatore, Tamil Nadu, India. The matrix material is used in natural latex rubber resin, and flame-retardant chemicals are experimented for special-purpose materials like aluminum hydroxide, magnesium hydroxide, zinc borate, zinc oxide, and zirconium oxide nanoparticles with various shapes all the reagents were of special analytical 99% purity grade without any pre or post purification was purchased from Mudaliyar Enterprises (Import & Export), Hosur, and Centre for Nano Technology, Mepco Schlenk Engineering College in Sivakasi, Tamil Nadu, India. represents the selected material characteristics.
Table 1. Thermal characteristics of materials used.
Preparation of flame-retardant target samples using hand layup technique
Target samples are prepared using a hand-layup method in the cold manufacturing process. The fabrication process began with mold preparation, which ensured the mold was clean, dry, and free of any contaminants, and a mold-releasing agent (white grease) was applied inside the mold. The optimal percentages of flame retardant chemicals (FRCs) are blended with natural latex rubber resin components according to the specified ratio as given in and mixed thoroughly. Cut the reinforcement material to the desired size and shape in a 90-degree bi-direction fiber orientation. Considered overlaps on continuous fibers and specified stacked patterns are performed in the inner mold. Initial layup: Placed the first layer of reinforcement in the mold, ensuring proper alignment and avoiding wrinkles or air pockets. Resin is uniformly poured inside the mold; a thin layer of resin over the reinforcement ensures complete saturation. Hand rollers and brushes are used to remove air bubbles, trap air in between layers, and achieve uniform coverage. Added additional layers of reinforcement and resin until the desired thickness is achieved and also ensured the proper orientation and overlap of reinforcement layers to allow the laminate to cure completely at room temperature and de-molding. Once fully cured, carefully remove the target sample from the mold. These process steps are repeated for each class of composition and maintain the prepared target sample thickness uniformly. The weight fractions of flame-retardant chemicals are represented in .
Table 2. Weight fraction for flame retardant chemicals.
Flame-retardant techniques in natural composite materials
The hand lay-up process was employed to fabricate flame-retardant natural composite materials, allowing for precise control over lamina thickness and fiber volume fraction (Vf). In this study, the hand lay-up technique was utilized to create lamina measuring 450 mm × 300 mm. NaOH treatment was applied to all natural fibers and laminas. This treatment process is unlikely to significantly impact the resulting moisture content of the fibers trapped post-resin infusion, as the majority of setup time was dedicated to blending inorganic chemicals into the rubber resin under open atmospheric conditions during the filling and resin curing phases.
Twenty SEM images were captured, showcasing compositions of four different fibers blended with five distinct chemicals to enhance the ignition delay and reduce fire spread in the materials. Powdered flame retardant chemicals were mixed with natural polymer rubber resin and coated onto natural lamina. Samples were molded using an open mold hand lay-up process. The resulting flame-retardant natural material samples had a net weight of 50 g, with 20 g attributed to reinforcement, 18 g to rubber resin, and the remaining 2 g to flame-retardant synergy. SEM images were taken with a scale reading of 5 micro and a common magnification of 5000X for all materials.
Results and discussion
The significance of this research in advancing the development of fire safety and flame-retardant composite materials is increasingly recognized due to their ability to offer a compelling blend of physical durability, heat tolerance, and innovative fire suppression methods. A pivotal aspect of the findings from this study lies in the successful formulation of diverse flame retardant chemical compositions. These compositions demonstrate efficacy in depriving the material of oxygen, thereby impeding the spread of flames and safeguarding all layers of the material. This action effectively seals the material’s surface, suffocating flames by restricting oxygen availability.
Morphological analysis of the prepared composite materials
The morphological behavior of the fabricated samples are shown in the The morphological factors influencing the fire properties of the prepared samples were changed with respect to the non-uniform coating and poor interfacial interactions between the polymeric matrix and reinforcement. The surface area influenced by the interaction strength of the composite material was analyzed using this technique. The reliability of this technique is analyzed using the micron-level surface area of the composite and the interaction between coating layers in reinforcement material. In this condition, the morphology disputes the poor surface finish of composite layers, which leads to a decrease in fire resistance properties. This microanalysis indicates the uniformly finished composite samples obtained better fire resistance properties. Otherwise the mixing of matrix and metallic oxides gives the agglomeration formed in the composite layers, which leads to a gap between matrix and reinforcement. This is the major factors influencing poor fire properties. The results predicted the exact changes in the fire properties of composite materials using morphological changes in the material. Future research focuses on developing novel synthesis methods and composite structures to achieve exceptional fire resistance through controlled morphology.
Fourier transform infrared spectroscopy analysis of extracted natural fibre reinforcements
At room temperature, an FT-IR spectrum spanning wave numbers from 500 to 4000 cm−1 was obtained for both raw seed and leaf natural fibers. The observed FT-IR spectra of seed fibers (coir and cotton) and leaf fibers (Palmyra stem and sisal) exhibit prominent absorption bands indicating the presence of mixed organic compound groups typical of lignocellulosic fibers, including cellulose, hemicellulose, and lignin. These fibers primarily consist of various oxygen-containing functional groups such as alcohols, esters, and ketones, along with other substance groups including glucose linkages, phenolic hydroxyls, alkenes, and aromatics.
The FTIR analysis of the primary constituents of the extracted coir fiber reveals the presence of lignin, indicated by the presence of carbonyl group and skeletal vibrations. The characteristics of lignin and hemicelluloses are discernible through small vibration bending.
The major constituents of cotton fiber – lignin, cellulose, and hemicelluloses – are detected. However, the hemicellulose content in cotton fiber is notably low, making its absorption challenging. β-glycosidic linkages are evident, and the moisture content is negligible. Palmyra leaf stem fiber primarily comprises hemicellulose bonds, prominently present in its raw form, while lignin content is minimal. Extracted raw sisal fiber is predominantly composed of cellulose and hemicellulose, as indicated by identified absorption peaks in its chemical composition. These observations collectively denote the characteristic polysaccharide nature of these fibers.
Fourier transforms infrared spectroscopy analysis of flame-retardant chemicals
The identification of prepared flame retardant inorganic chemicals was conducted through analysis of their FT-IR spectra. The FTIR spectrum of the nanoparticles was recorded at room temperature within the range of 4000 cm−1 to 400 cm−1.
Chemical compounds including aluminum hydroxide, magnesium hydroxide, zinc borate, zinc oxide, and zirconium oxides were subjected to FTIR analysis. The findings indicate that the conformation of the primary components within the chemical flame retardants confirms the absence of impurities. The FTIR spectra obtained align closely with other finding by A.K. Singh et al. (Citation2014) and Zhao et al. (Citation2007).
Fourier transforms infrared spectroscopy analysis for flame-retardant target samples
FT-IR spectroscopy is utilized to examine the chemical interactions within flame-retardant target samples. Recorded at room temperature, the FTIR spectra of these samples spanned the range of 4000 cm−1 to 400 cm−1.
In the preparation process, the target samples, comprising natural latex as the matrix, were subjected to FTIR analysis. Metal oxides were incorporated into the matrix material using a mechanical stirring method, with SEM analysis assessing the uniformity of metal oxide dispersion. Natural fibers served as reinforcement in the target samples. Each of the natural latex, metal oxide, and natural fabric components exhibited distinctive functional groups in the observed spectra. Interactions between chemicals were identified through both low- and high-frequency bands, as depicted in and .
Figure 2. FT-IR analyzing results for prepared target samples natural fibers with (a) Aluminum hydroxide, (b) Magnesium hydroxide, (c) Zinc borate, (d) Zinc oxide and (e) zirconium oxides natural latex matrix.
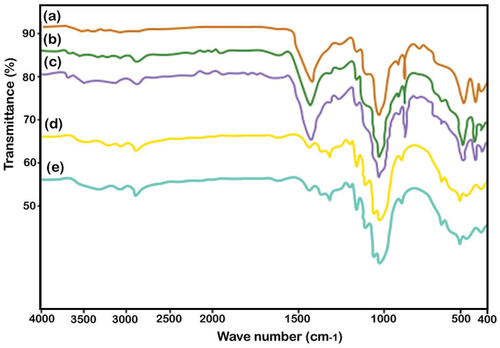
Table 3. The FTIR spectra of absorption bands assigned to vibration modes of prepared flame retardant target samples.
Although FTIR analysis was conducted for all 20 target samples, graphical representations were generated for only five. illustrates the similarity of results obtained from natural fabric-reinforced samples featuring dispersion of five different metal oxides within a natural latex rubber resin matrix. Common constituents found in natural fabrics included lignin, cellulose, and hemicellulose bonds.
Horizontal burn time test
The setup and procedure for horizontal burning adhered to the ASTM E 648 standard test method. However, it’s worth noting that the objective of this test wasn’t to measure smoke density but rather to offer a straightforward and cost-effective means of obtaining both quantitative and qualitative insights into material behavior.
Samples measuring 50 mm × 50 mm were positioned at the center of a holder atop a steel fixture. A kerosene blow flame was then applied from below at a 45° angle for a duration of four minutes before being removed. Various parameters including ignition time, flameout time, initial mass (in grams), final mass loss, limited oxygen index (LOI), and dripping were meticulously recorded. Additionally, an infrared thermometer was employed to monitor temperature changes.
For the mold preparation, a glass fiber horizontal burn time test was conducted in accordance with ASTM E 648 standards. Composite laminas of various compositions were fabricated to these standards, with test specimens following dimensions of 70 mm in length, 55 mm in width, and 20 mm in thickness.
Two distinct flame-retardant techniques are employed in the mechanism of fire prevention. The first approach involves incorporating flame-retardant chemicals or additives into the substrate, such as natural rubber or any solid material. These flame-retardant (FR) chemicals react when exposed to high temperatures, forming a protective layer that limits combustion and degradation. This method entails coating the outer surface of materials with FR chemicals.
In this study, the second method was employed to fabricate various composite materials. This involves incorporating inorganic flame retardants directly into the formulation of the natural rubber polymer. This addition serves to retard the spread of fire. To conduct this test, an infrared thermometer equipped with a computer was utilized due to the rapid rate at which it generates temperature-time graphs.
The experimental results showcase notable differences between coir and cotton-reinforced composite materials. These composites feature a matrix composed of natural rubber resin blended with flame-retardant chemicals including aluminum hydroxide, magnesium hydroxide, zinc borate, zinc oxide, and zirconium oxide. The mass loss percentages of the coir fiber-reinforced composites range between 58% and 83%, whereas those of the cotton fiber-reinforced composites range between 69% and 83%. Variations in the LOI percentage among the prepared target samples are attributed to the distinct properties of the flame-retardant chemicals used.
Comprehensive test results for the fabricated specimens are detailed in . Each composite composition demonstrates its own capability to withstand fire, indicating suitability for various fire safety applications.
Table 4. Horizontal burn test results for aluminum hydroxide blended natural composite material.
Table 5. Horizontal burn test results for magnesium hydroxide blended natural composite material.
Table 6. Horizontal burn test results for Zinc borate blended natural composite material.
Table 7. Horizontal burn test results for Zinc oxide blended natural composite material.
Table 8. Horizontal burn test results for Zirconium oxide blended natural composite material.
The effective application of flame retardant techniques in natural composite materials is briefly discussed, focusing on evaluating the flame behaviors of various formulations of composite materials to provide effective protection against fire spread or heat penetration while ensuring material stability. The analysis thoroughly examines the fire safety benefits of these techniques, including reducing or delaying flame spread rates, preventing small ignitions, enhancing material flame resistance and stability, and controlling heat release rates.
Understanding the mechanism of fire protection is crucial in the field of flame retardancy. Flame-retardant materials are tailored to suit specific applications such as railway, cable industry, buildings, and textiles. The fire mechanism operates in a continuous cycle: a heat source triggers the degradation of natural rubber polymer, leading to the formation of highly reactive degradation products that serve as fuel for the flame. The flame, in turn, heats the polymer, perpetuating its breakdown. Disrupting this cycle is vital for fire prevention, achievable at two stages: in the condensed phase and the gaseous phase. The intumescent system, which forms a fire-protective layer in the condensed phase, is particularly promising due to its ability to withstand high temperatures.
Inorganic flame retardant chemicals like aluminum hydroxide, magnesium hydroxide, zinc borate, zinc oxide, and zirconium oxide play a crucial role in the condensed phase. Incorporating these chemicals into a natural polymer enhances its flame-retardant properties by significantly reducing heat release rates and mass losses during horizontal burn tests. This reduction occurs due to the development of protective layers that inhibit the volatilization of degradation products and trap radical species, promoting cross-linking reactions to form a cohesive solid residue post-fire. Optimal dispersion of these chemicals within the natural rubber matrix is essential for achieving the best char formation and superior fire properties.
Thermal behaviour analysis for flame retardant target samples
The flame retardant target samples, which consist of natural fabrics reinforced with aluminum hydroxide, magnesium hydroxide, zinc borate, zinc oxide, and zirconium oxide individually mixed in a natural latex rubber resin matrix, undergo analysis using various analytical techniques. These techniques include thermogravimetric analysis (TGA), differential thermal analysis (DTA), and differential scanning calorimetry (DSC), as well as flame spread tests. The objective is to determine the thermal stability, degradation behavior, and decomposition temperature of the target samples.
Additionally, cone calorimeter analysis, an advanced characterization technique, is employed to assess the flammability (calorific value) of the samples. This comprehensive analysis provides essential test data, including ignition time, flameout time, total heat release, oxygen consumption, smoke release quantity, heat release rate, effective heat of combustion, mass loss rate, as well as CO and CO2 gas emissions. These tests are essential for evaluating the suitability of the prepared target samples.
Thermo-gravimetric analysis (TGA)
The thermal analysis test, conducted according to ASTM D 1311, is employed to predict or determine the thermal stability, oxidation behavior, and decomposition temperatures of both the matrix and the prepared target samples. This assessment aids in evaluating or comparing the performance of selected natural fibers in various configurations: the matrix alone, natural fibers with matrix composites, and composite materials infused with flame-retardant chemicals.
During this analysis, the thermograms of all fabricated samples and the matrix alone are scrutinized, revealing residual content ranging from 34.6% to 65.7%. These residue levels may be attributed to the presence of inorganic fillers. Notably, sample decomposition initiates at 398.38°C.
Additionally, TGA analyzes of the fabricated samples are conducted to identify physical and chemical changes in the materials. illustrates the weight loss versus temperature for samples comprising various selected natural fibers alone, while depicts the weight loss versus temperature for samples reinforced with coir, cotton, Palmyra leaf stem, and sisal fibers within a matrix composite. shows the weight loss versus temperature for samples incorporating natural fibers with a composite material of aluminum hydroxide, magnesium hydroxide, zinc borate, zinc oxide, and zirconium oxide, blended within a natural rubber latex matrix, revealing physical changes in the materials. These changes are correlated with variations in sample weight under a nitrogen atmosphere, with a heating rate of 10°C/min up to 750°C.
provides detailed experimental weight loss data during the transition period. The residue values vary among samples based on flame retardant chemical density. The weight loss percentage relative to the temperature difference between the onset and end transition temperatures signifies the residual weight containing the flame-retardant chemicals. The temperatures corresponding to the end and onset peaks (To, Tm, and Te, respectively) represent the main thermal decomposition fractions. Differential thermal analysis (DTA) serves a similar purpose to TGA.
Table 9. Samples weight loss at transition period.
Analyses of differential scanning calorimetry (DSC)
The natural fibers, rubber latex alone, composites of reinforcement with the matrix, and composite target samples infused with flame retardants undergo DSC analysis, where heat flow is measured at a specified heat rate. display the graphs illustrating the variations among reinforcement, matrix alone, reinforcement with matrix composite, and the addition of different flame retardant chemicals to the composite material. These graphs reflect the differences in composition, particularly concerning the presence of flame retardant chemicals in the samples.
Figure 4. DSC analyzing results for (a,b) Selected natural reinforcements, (c) reinforcements with matrix composite and (d) prepared target samples.
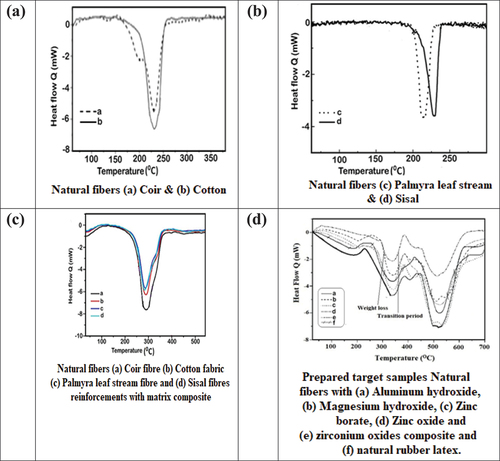
showcases the DSC curve of natural fibers, matrix alone, and prepared target samples. The addition of various flame retardant chemicals to the composite material results in loss percentages at specific points: 5.3%/min, 5.9%/min, 6%/min, 6.5%/min, and 6.8%/min, respectively. The peak degradation temperatures are recorded as 533°C, 561°C, 570°C, 605°C, and 615°C, while the peak temperatures themselves are measured at 5.1, 5.6, 5.9, 6.2, and 6.5%/min, respectively. Notably, natural rubber latex does not exhibit any peak temperature; it undergoes deformation within a very short duration.
Flammability (cone calorimetric analysis)
Flammability testing, conducted following ISO 5660–1 standards, utilizes cone calorimetry as a characterization technique to determine the flammability, or calorific value, of prepared target samples. This method provides crucial information, including the total heat release, smoke production, oxygen consumption, CO and CO2 emissions, among others, aiding in assessing the material’s thermal suitability during combustion. The comprehensive experimental data is outlined in .
For the test, specimens are cut into pieces measuring 100 mm x 100 mm x 3.2 mm. The flammability test results for the sample, with a mass of 95.5 g and a surface area of 107.98 cm2, are illustrated in the following chart.
Inference: Analysis of the test results presented in indicates that the heat of combustion for the target samples ranges from 17 to 19.63 MJ/kg. This value is notably lower when compared to common combustible materials such as coal (32.5 MJ/kg), kerosene (46 MJ/kg), methane (55.5 MJ/kg), and wood (21.5 MJ/kg), among others. The reduced heat of combustion is attributed to the presence of flame-retardant chemicals incorporated into the target structures.
Table 10. The weight loss and glass transition temperature at 10% and 15%.
Table 11. Flammability (cone calorimetric analysis) of various flame retardant chemicals blended natural composite material.
Conclusions
This paper presents a thorough characterization of natural composite materials (NCM). Various inorganic flame retardant chemicals, synthesized through methods including gas combustion, sol-gel, and hydrothermal techniques, have been explored to enhance flame resistance. The natural fibers, including coir, cotton, Palmyra leaf stem, and sisal fibers, are extracted using mechanical peeling extraction methods. These flame retardant (FR) chemicals are blended with the matrix to create a protective layer upon exposure to flame. This layer acts as a heat shield, preventing substrate melting and degradation.
Material characterization techniques employed to determine the optimal composition include SEM morphological analysis (25%), FT-IR graph analysis (20%), and thermal analyzes and horizontal burn test experiments (55%) conducted on various fiber compositions blended with five different chemical composites.
The correlation between microstructural features and flame-retardant properties of the tested composite materials is investigated. Overall, the properties of composites are intricate and influenced by factors like matrix, fiber type, fiber orientation, and dispersion of flame-retardant chemicals. However, by comprehending these key factors, composites with enhanced flame-retardant properties can be designed.
In comparison to the pure natural rubber latex, the fabricated composite specimens exhibits superior performance by igniting earlier, emitting a higher overall heat output, and sustaining combustion for a longer duration. Advanced thermal stability tests, including TGA, DSC, and cone calorimetric analyzes, are conducted to anticipate physical and chemical changes in the prepared target samples. These tests are performed on the natural rubber latex matrix alone to assess the efficacy of the formulated flame-retardant target samples. However, the matrix material alone fails all the thermal tests conducted.
The results of horizontal flame spread, oxygen index, DSC, and TG analysis for selected materials – natural reinforcements, matrix, and powdered aluminum hydroxide, magnesium hydroxide, zinc borate, zinc oxide, and zirconium oxide chemicals – are evaluated in the fire-resistant investigation. The selected reinforcements and matrix materials alone exhibit high flammability in air, easy ignition, rapid burning, and high flame spread.
Incorporating flame-retardant chemicals such as zinc borate, zinc oxide, magnesium hydroxide, aluminum hydroxide, and zirconium oxide significantly enhances the flame properties of prepared composite materials. Zinc borate reduces the flame spread level by up to 95%, followed by zirconium oxide at 90%, magnesium hydroxide at 80%, zinc oxide at 60%, and aluminum hydroxide at 40%.
Furthermore, the limited oxygen index demonstrates the effectiveness of these materials in various blends, with zinc borate at 34–38%, zirconium oxide at 31–34.11%, zinc oxide and magnesium hydroxide at 29–32.89%, and aluminum hydroxide at 8–31.45%.
Analyzing DSC and TGA reveals that high-temperature-resistant materials such as zirconium and zinc oxide, medium-temperature zinc borate, and low-temperature aluminum and magnesium hydroxide-blend composite materials show improved efficacy. Overall, composites with zinc borate and zirconium oxide additives exhibit superior flame retardant properties compared to other materials.
The natural rubber latex material does not pass any of the thermal tests conducted. For future research, it is recommended to explore alternative matrix materials, such as plant-based resins such as soy-based resin or lignin-based resin.
The potential for research advancements in flame-retardant natural composite materials is bright, presenting avenues for improving safety and performance across diverse industries. As researchers persist in developing novel flame retardants and refining processing techniques, these materials are anticipated to be utilized in a wide array of sectors, including automotive, aerospace, construction, and beyond.
Acknowledgments
The authors wish to express their sincere thanks to Dr. S. K. Nayak, Director General & Dr. K. Prakalathan, Director & Head, Central Institute of Petrochemicals Engineering and Technology (CIPET): CSTS - Madurai, Tamil Nadu, India, for the help rendered during characterization and polymer testing lab facilities. The authors also wish to thank Dr. K. P. Bhuvana, Scientist at CIPET: School for Advanced Research in Polymers (SARP)-Advanced Research School for Technology and Product Simulation (ARSTPS), Chennai, Tamil Nadu, India, for her support in carrying out this investigation. The authors also wish to thank Dr. R. Joseph Bensingh, Senior Scientist & head, CIPET: School for Advanced Research in Petrochemicals (SARP)-APDDRL, Bangalore, Karnataka, India, for his help in carrying out this investigation. I dedicate this work to the government of India, ministry of defence.
Disclosure statement
No potential conflict of interest was reported by the author(s).
References
- Alongi, J., F. Carosio, and P. Kiekens. 2016. “Recent Advances in the Design of Water Based-Flame Retardant Coatings for Polyester and Polyester-Cotton Blends.” Polymers 8 (10): 357. https://doi.org/10.3390/polym8100357.
- Amjad, A., A. Anjang Ab Rahman, and M. Shukur Zainol Abidin. 2022. “Effect of Nanofillers on Mechanical and Water Absorption Properties of Alkaline Treated Jute Fiber Reinforced Epoxy Bio Nanocomposites.” Taylor & Francis. Journal of Natural Fibers 19 (16): 14592–17. https://doi.org/10.1080/15440478.2022.2068171.
- Attia, N. F., S. E. Elashery, A. M. Zakria, A. S. Eltaweil, and H. Oh. 2021. “Recent Advances in Graphene Sheets As New Generation of Flame Retardant Materials.” Materials Science and Engineering: B 274:115460. https://doi.org/10.1016/j.mseb.2021.115460.
- Bar, M., R. Alagirusamy, and A. Das. 2015. “Flame retardant polymer composites.” Fibers and Polymers 16 (4): 705–717. https://doi.org/10.1007/s12221-015-0705-6.
- Bensabath, T., J. Sarazin, and S. Bourbigot. 2021. “Anisotropy of Expandable Graphite to Explain Its Behavior as a Flame-Retardant.” Journal of Fire Sciences 39 (2): 109–118. https://doi.org/10.1177/0734904120969639.
- Bharath, K. N., and S. Basavarajappa. 2014. “Flammability Characteristics of Chemical Treated Woven Natural Fabric Reinforced Phenol Formaldehyde Composites.” Procedia Materials Science 5:1880–1886. https://doi.org/10.1016/j.mspro.2014.07.507.
- Canıtez, H., A. N. Yüksel Yılmaz, and A. Çelik Bedeloğlu. 2022. “The Effect of Silicon Dioxide and Zinc Borate on the Flame Retardancy, Thermal and Mechanical Properties of Jute/Epoxy Hybrid Composite.” Journal of Natural Fibers 20 (1): 1–20. https://doi.org/10.1080/15440478.2022.2131683.
- Chen, L., and Y. Z. Wang. 2010. “A Review on Flame Retardant Technology in China. Part I: Development of Flame Retardants.” Polymers for Advanced Technologies 21 (1): 1–26. https://doi.org/10.1002/pat.1550.
- Jiao, C., and X. Chen. 2011. “Influence of Fumed Silica on the Flame‐Retardant Properties of Ethylene Vinyl Acetate/Aluminum Hydroxide Composites.” Journal of Applied Polymer Science Wiley Online Library 120 (3): 1285–1289. https://doi.org/10.1002/app.33126.
- Kabir, M. M., K. T. L. Hao Wang, F. Cardona, and F. Cardona. 2012. “Chemical Treatments on Plant-Based Natural Fibre Reinforced Polymer Composites: An Overview.” Composites Part B Engineering 43 (7): 2883–2892. https://doi.org/10.1016/j.compositesb.2012.04.053.
- Kandola, B. K. 2012. “Flame Retardant Characteristics of Natural Fibre Composites.Natural Polymers.” 1 (1): 86–117. https://doi.org/10.1039/BK9781849734028-00086.
- Karim-Nejad, M. M., A. Nazari, and A. Davodi-Roknabadi. 2015. “Efficient Flame Retardant of Mercerized Cotton Through Cross-Linking with Citric Acid and ZnO Nanoparticles Optimized by RSM Models.” The Journal of the Textile Institute 106 (10): 1115–1126. https://doi.org/10.1080/00405000.2014.976958.
- Khalili, P., X. Liu, K. Yeow Tshai, C. Rudd, X. Yi, and I. Kong. 2019. “Development of Fire Retardancy of Natural Fiber Composite Encouraged by a Synergy Between Zinc Borate and Ammonium Polyphosphate.” Composites Part B: Engineering 159:165–172. https://doi.org/10.1016/j.compositesb.2018.09.036.
- Kim, N. K., S. Dutta, and D. Bhattacharyya. 2018. “A Review of Flammability of Natural Fibre Reinforced Polymeric Composites.” Composites Science and Technology 162:64–78. https://doi.org/10.1016/j.compscitech.2018.04.016.
- Kim, Y., S. Lee, and H. Yoon. 2021. “Fire-Safe Polymer Composites: Flame-Retardant Effect of Nanofillers.” Polymers 13 (4): 540. https://doi.org/10.3390/polym13040540.
- Knights, A. W., M. A. Nascimento, and I. Manners. 2022. “An Investigation of Polyphosphinoboranes As Flame-Retardant Materials.” Polymer 247:124795. https://doi.org/10.1016/j.polymer.2022.124795.
- Liang, S., N. M. Neisius, and S. Gaan. 2013. “Recent Developments in Flame Retardant Polymeric Coatings.” Progress in Organic Coatings 76 (11): 1642–1665. https://doi.org/10.1016/j.porgcoat.2013.07.014.
- Qian, X., L. Song, Y. Bihe, B. Yu, Y. Shi, Y. Hu, and R. K. Yuen. 2014. “Organic/Inorganic Flame Retardants Containing Phosphorus, Nitrogen and Silicon: Preparation and Their Performance on the Flame Retardancy of Epoxy Resins As a Novel Intumescent Flame Retardant System.” Materials Chemistry and Physics 143 (3): 1243–1252. https://doi.org/10.1016/j.matchemphys.2013.11.029.
- Sain, M., S. H. Park, F. Suhara, and S. Law. 2004. “Flame Retardant and Mechanical Properties of Natural Fibre–Pp Composites Containing Magnesium Hydroxide.” Polymer Degradation and Stability 83 (2): 363–367. https://doi.org/10.1016/S0141-3910(03)00280-5.
- Sen, A., and S. Kumar. 2010. “Coir-Fiber-Based Fire Retardant Nano Filler for Epoxy Composites.” Journal of Thermal Analysis and Calorimetry 101 (1): 265–271. https://doi.org/10.1007/s10973-009-0637-8.
- Singh, A. K., G. S. Thool, P. R. Bangal, S. S. Madhavendra, and S. P. Singh. 2014. “Low Temperature Mn Doped ZnO Nanorod Array: Synthesis and Its Photoluminescence Behavior.” Industrial & Engineering Chemistry Research 53 (22): 9383–9390. https://doi.org/10.1021/ie500077v.
- Wang, X., E. N. Kalali, J. T. Wan, and D. Y. Wang. 2017. “Carbon-Family Materials for Flame Retardant Polymeric Materials.” Progress in Polymer Science 69:22–46. https://doi.org/10.1016/j.progpolymsci.2017.02.001.
- Zhao, W. Y., P. Wei, H. B. Cheng, X. F. Tang, and Q. J. Zhang. 2007. “FTIR Spectra, Lattice Shrinkage, and Magnetic Properties of CoTi‐Substituted M‐Type Barium Hexaferrite Nanoparticles.” Journal of the American Ceramic Society 90 (7): 2095–2103. https://doi.org/10.1111/j.1551-2916.2007.01690.x.
- Zhao, Q., B. Zhang, H. Quan, R. C. Yam, R. K. Yuen, and R. K. Li. 2009. “Flame Retardancy of Rice Husk-Filled High-Density Polyethylene Ecocomposites.” Composites Science and Technology 69 (15–16): 2675–2681. https://doi.org/10.1016/j.compscitech.2009.08.009.