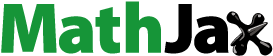
ABSTRACT
A natural fiber-reinforced composite from a locally available false banana plant is developed for a prosthesis socket application. Four batches of composite samples are fabricated by arranging the longitudinal uniformly distributed unidirectional false banana fibers in four orientations (0°, 90°, ±45°, 0°/90o). The composites’ mechanical and physical properties, such as tensile strength, compression strength, flexural strength, impact resistance, and the effect of chemical treatment on water absorption, are investigated. The results are compared with E-glass fiber-reinforced polymer matrix composite. The false banana fiber-polymer composites with a 0° fiber orientation have a tensile strength of 86.81 MPa, less than 9% lower than E-glass-fiber composites (95.44 MPa), and an impact resistance of 6.25 J, 10% higher compared to the E-glass fiber polymer composites (5.70 J). In addition, the treated false banana fiber-polymer composite absorbed 70% less water than the untreated false banana fiber-polymer composite. It is observed that the fiber treatment has increased the polymer–fiber interaction and the interface strength of the false banana fiber-polymer composites.
摘要
一种由当地可买到的假香蕉植物制成的天然纤维增强复合材料被开发用于假肢插座应用. 通过将纵向均匀分布的单向假香蕉纤维按四个方向(0o、90o、±45o、0o/90o)排列,制备了四批复合材料样品. 研究了复合材料的力学和物理性能,如拉伸强度、压缩强度、弯曲强度、抗冲击性能以及化学处理对吸水率的影响. 将结果与E-玻璃纤维增强聚合物基复合材料进行了比较. 具有0o纤维取向的假香蕉纤维-聚合物复合材料的拉伸强度为86.81MPa,比E-玻璃纤维-聚合物组合材料(95.44 MPa)低不到9%,抗冲击性为6.25J,比E-纤维-聚合物复合体(5.70 J)高10%. 此外,经处理的假香蕉纤维-聚合物复合材料比未经处理的假的香蕉纤维-聚合复合材料吸收的水少70%. 观察到纤维处理提高了假香蕉纤维-聚合物复合材料的聚合物-纤维相互作用和界面强度.
Introduction
Composite materials have recently gained significant importance in various sectors, including aerospace, automotive, and biomedical industries, due to their unique properties, such as lightweight, high strength, and stiffness (Raj et al. Citation2023; Yadav et al. Citation2020). Among the various biomedical applications, composite materials become a choice of material for the structure of the prosthetic socket, which attaches to an amputee’s residual limb (Tyagi, Sahai, and Sharma Citation2023). Usually, prosthetic sockets are fabricated from thermoset, thermoplastics, and synthetic fiber-reinforced polymer matrix composite made of carbon fiber, fiberglass, or a combination of both (Tyagi et al. Citation2024; Tyagi, Sahai, and Sharma Citation2023). These materials are light and robust and may be shaped to fit the specific shape of an individual’s residual limb. However, the synthetic fibers currently used, such as carbon and glass fibers, are not readily available locally to produce the socket required by the amputee in developing countries. On the other hand, due to extended war, conflicts, and accidents, the number of lower-limb amputees in developing countries keeps on growing, and the demand for prosthetic devices is unmet (Karin Rotter et al. Citation2006; Martin Marino et al. Citation2015).
To alleviate these problems, it is essential to study the behavior of locally available biocompatible natural fibers that can replace the existing synthetic prosthetic material, which provides low-cost prostheses for the user. Among the many natural fibers, ramie, jute, hemp, false banana, sisal, and henequen have been proposed for low-cost material applications (Andrew I Campbell et al. Citation2012; David and Johnson Citation2015; Ferede and Atalie Citation2022). False banana fiber (Ensete ventricosum) is currently the most practical and popular natural fiber among the many natural fibers (Dejene and Geletaw Citation2023). False-banana fiber can be hybrid with other synthetic fibers or used exclusively with various resins to produce a structural composite material that can be used for multiple purposes (Zelalem Biresaw, Sirahbizu Yigezu, and Gloria Citation2022).
Zelalem and Sirahbizu discovered a blend of 25 vol.% flax and 15 vol.% false banana in a unidirectional orientation, giving the most excellent tensile and flexural strengths (Temesgen Batu a and Lemu Citation2020). Boset found enhanced mechanical strength of false banana fiber-reinforced epoxy composite at 30 vol.% of the fiber (Boset Citation2019). Taye and Alemayehu showed that the fiber orientation angle could affect the mechanical strength and the water absorption rate of woven false banana fiber composite (Taye and Alemayehu Citation2023). Shimels et al. (Shimels et al. Citation2023) reported that chopped false banana fiber-reinforced polypropylene composite with 30 % vol. of fiber treated with Aloe Vera gel had improved mechanical strength. Furtos et al. (Furtos et al. Citation2022) found that wood fiber geopolymer composites with fiber wood ranging from 20 to 35 wt.% can produce novel lightweight and heat-insulating materials.
Most researchers used false bananas as fabrics or a fiber bundle by arranging the fiber in different directions. This results in the difficulty of adequately impregnating the resins during the composite fabrication. Further, the process of making yarns causes fiber breakage, compromising the strength of composite made of yarns. Due to this, false banana fiber has yet to be used to its full potential. To the author’s best knowledge, a detailed study on long and uniformly distributed unidirectional false banana fiber polymer composite and producing strong fiber using different fiber treatment techniques is missing in the open literature. In the study, mechanical and chemical fiber extraction and treatment were used to enhance the mechanical strength of the false banana fiber. Unlike the previous studies, uniformly distributed unidirectional false banana fibers were used to make the composites. The mechanical properties essential for prosthetic socket application, such as compressive, tensile, flexural, and impact strength of the false banana composites with different fiber orientations, are investigated, and the optimal fiber orientation is selected. In addition, the effect of fiber treatment on water absorption and, hence, the dimensional stability of the composite is investigated. The paper is arranged as follows: the material and fabrication process are discussed in section two. The experimental methods and the data analysis are discussed in section three. The results are discussed in section four, and the conclusion is presented in section five.
Material and methods
Material
The layered false banana leaf sheaths, the raw material for the primary reinforcement of the composite, were harvested in southern Ethiopia. The general-purpose resin (GP), also known as polyester resin, Miracle Gloss (formerly Meguiar’s M-08) mold releaser wax, and Methyl Ethyl Ketone Peroxide (MEKP) catalyst/hardener were purchased from World Fiber PLC, Addis Abeba. NaOH pallets, with a 98% concentration, were purchased from Merkato and Addis to treat the fiber and remove some lignin, pectin, and other impurities from its surface. A mold made of an acrylic plate with a thickness of 4 mm and sheet metal with a thickness of 2 mm is used to fabricate the composite plates.
Fiber extraction and chemical treatment
The layered false banana leaf sheaths, which are typically long, are first cut off from the plant shaft. These sheaths are then carefully slit to the appropriate size and made to be ready for extraction. The slits are then spread over the flat wood and hand stripped with a blunt knife, and a fresh batch of fibers is extracted. After extracting the fibers, they were immersed immediately in water and thoroughly washed with tap water, and any remaining impurities from the surface of the fibers were removed. This process allows the lignin part of the fiber left on the fiber’s skin to be easily removed. Later, fresh and wet fibers were allowed to pass through a mechanically tightened blunt pair of wood strips to remove some visible lignin parts of the fiber. The fibers were then dried naturally, and they became white. Following washing, passing through these strips, and drying, the fiber is immersed in a 5% concentrated NaOH solution and soaked for two hours to remove water-insoluble materials such as the remaining lignin and hemicellulose material. The use of NaOH solution to remove water-insoluble material from fibers is well documented (Sahu et al. Citation2023). The fiber is then taken out of the solution and repeatedly washed with deionized water (DI) until the PH of the water reaches seven. This process helps remove any stuck NaOH from the fiber’s surface (Irawan, Widjajalaksmi, and Reksoprodjo Citation2011; Kumaresan et al. Citation2015; Mujahid Khan et al. Citation2019). The fiber is dried in the hot sun for four days until all moisture is removed, as shown in . After drying the washed and soaked false banana fiber, the color of the fiber becomes golden, and the external surface becomes (observed) rough.
The dimension of the single fiber after chemical treatment was measured using a Zeta 20 profilometer/3D optical microscope (Zeta 20, ZEISS., Germany), and the ultimate tensile strength was measured using a Textechno Statimat Me+ tensile testing machine (Type FPA Me+, M38911, Textechno, Germany), as shown in .
Table 1. Physical and mechanical properties of single false banana fiber.
The fibers were manually oriented in four different directions with four varying sequences of layups, as shown in . The composite plates were fabricated using the hand layup technique detailed in section 2.3.
Fabrication
To achieve the composite plate’s dimensions and regulate the resin’s volume fraction, the mold was prepared with a 275 mm x 175 mm base plate made of 2 mm sheet metal and a 30 mm wide and 4 mm thick acrylic frame bolted over it. The acrylic frame was used to keep the composite plate’s thickness uniform. Different studies indicate that the volume fraction of natural fiber in polymer matrix composite does not exceed 40 % (Arthanarieswaran, Kathirselvam, and Kathirselvam Citation2014; Furtos et al. Citation2019; Herlina Sari et al. Citation2017; Irawan and Sukania Citation2015; Irawan, Widjajalaksmi, and Reksoprodjo Citation2011; Temesgen Batu and Lemu Citation2020). Hence, 40 % volume of false banana fiber was used in this work. According to the manufacturer’s manual, the resin was mixed and stirred for two minutes with a Methyl Ethyl Ketone Peroxide (MEKP) catalyst or hardener n a ratio of 10:1. A wax mold releaser was applied uniformly before the resin was poured into the mold. The weight of the fiber and the resin was measured with a digital balance with four-digit accuracy according to the allotted fiber volume fraction for the composite. First, the mold was filled with a roughly equal volume of resin to the first layer of false banana fiber, as shown in . Then, the UDL false banana fibers were impregnated with a resin and layup layer by layer, starting from the lower mold at the calculated weight of the fiber. During layup, each layer of UDL was thoroughly mixed with resin using a brush and roller. Finally, the upper mold cover was closed and compressed at a pressure of 2 bar for 5 h. Then, it was relieved and allowed to cure for another 12 h at room temperature.
Figure 3. Composite casting process, A, 3D CAD drawing of mold; B, mold painted with wax; and C, hand layup process in the mold.
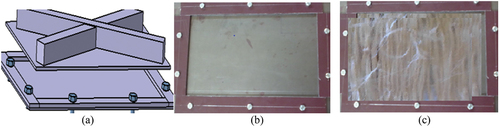
One of the materials currently used for prosthetic socks is E-glass fiber. To compare the mechanical properties of the proposed material, a composite material was fabricated with 30 vol.% of randomly distributed E-glass fiber (Chopped Strand Mat, type 450 g-CSM with sheet thickness of 1.2 mm and a fiber diameter of 17 μm) and resin following a similar procedure. Finally, composite plates with dimensions of 270 × 170 mm were made with an average thickness of 4 mm. Five specimens from each plate were prepared using a cutter of a portable grinder and then debited utilizing a milling machine to attain the shape of the specimen, required by ASTM for tensile, compression, flexural, impact strength, and moisture absorption testing as tabulated in .
Table 2. Preparation of experimental standard test specimens.
Experiment
Tensile strength test
Twenty uniformly distributed long false banana fiber-reinforced polyester matrix composite specimens for the four types of fiber orientation and five additional specimens with randomly distributed E-glass fiber reinforcement were prepared, following ASTM D-638-14 standards (ASTM International Citation2015b), as shown in and with dimensions shown in . A milling machine was used to fillet the specimen’s radius, and sandpaper was used to remove extra burrs. Specimens with a grip length of 50 mm at both ends were mounted correctly in the upper and lower grippers of the universal testing machine (UTM) and aligned axially with the axis of the cross-head of the UTM. The tensile tests were conducted using a 100kN universal testing machine (WDW-100S Computer Control Electronic Universal Testing Machine, China) at a cross-head speed of 2 mm/min and room temperature. Five specimens were tested for each type of fiber orientation, and glass fiber composite specimens were randomly distributed until the specimens failed. The average tensile strength and standard deviation were calculated using the load cell and crosshead displacement data.
Flexural strength test
Flexural tests were performed using a universal testing machine (WDW-100S Computer Control Electronic Universal Testing Machine, China.) with a 100 kN load cell in a three-point bed arrangement, as shown in . The machine’s cross-head speed (R) was estimated using EquationEquation 1(1)
(1) and set to a 5 mm/min rate. Five specimens for each fiber orientation and randomly distributed E-glass fiber reinforced polyester matrix composite (GRP) were prepared following ASTM (D-790-17 standards (ASTM International Citation2017), with a dimension shown in , as seen in .
Figure 5. False banana fiber-reinforced composite flexural strength test specimens were prepared following ASTM D-790-17 for four fiber orientations.

Where R is the crosshead speed, Ẕ is the rate of straining of the outer fiber, which is usually taken to be 0.01, L is the span of the plate between the rollers, and t is the thickness of the plate.
The bending resistance of the composites with each fiber orientation was performed by applying load axially at the midway of the specimen, and the bending stress () of the samples was calculated using EquationEquation 2
(2)
(2) .
Where P is the applied load, L is the span of the plate between the rollers, b is the container’s width, and t is the thickness of the plate.
Compressive strength test
Compression experiments were conducted for 25 specimens, including E-glass fiber polymer composites, using a WDW-100S Computer Control Electronic Universal Testing Machine at a 2 mm/min cross-head speed following the ASTM (D-695-10) standards (ASTM International Citation2015a). The dimensions of the specimens are shown in , while their geometry is presented in . The samples were held in the grips of the UTM during the test, and a compressive load was applied axially until failure. The compressive strength was calculated from the load cell data and reported, including the standard deviation.
Impact resistance test
The impact tests were performed using a pneumatic control Charpy impact test machine (JWT-406 Impact Testing Machine, China) with a 5.466 m/sec pendulum speed and a 27.13 kg hammer weight. Following ASTM A370 or EN 10,045–1 standard (Standard Citation2014), the specimens were prepared with a V-shaped notch on the surface, as shown in , and the dimensions presented in . After placing a specimen on the pair of support plates mounted at the bottom of the device, a pendulum raised to a known height was allowed to fall and strike the sample. The absorbed energy of each material was measured as the impact energy of the specimen.
Water absorption test
To evaluate the material’s dimensional stability, strength, and delamination potential, prosthetic socket material must undergo moisture content testing. The experiment followed ASTM D − 570-98 (Standard Test Method for Water Absorption of Plastics Citation2018) after preparing 10 specimens for treated and untreated fiber composite with dimensions presented in . All specimens were submerged in water for ten days, and their weights were measured at every 24-hour interval with a high-precision balance. Before weighing, the specimen was removed from the water, and any remaining water on its surface was cleaned with a dry cloth. The measurement was done immediately after the samples were taken from the water. The percentage of water absorbed was determined using EquationEquation (3)(3)
(3)
Where St is the mass of the wet specimen, and So is the weight of the dry sample
Result and discussion
Tensile strength
The tensile stress-strain curve of false banana fiber composites, with different fiber orientations, is compared with the E-glass fiber polymer composites, as presented in and . The results show that the false banana fiber reinforced polymer resin matrix composite with fiber orientation at 0° has the highest average tensile strength of 84.99 MPa compared to the rest of the fiber orientation composites. This is because the fibers are the major loading-carrying members of the composite and are distributed equally throughout the composite (Ramesh et al. Citation2022). As shown in , the false banana fiber reinforced composite with 0° fiber orientation is slightly smaller than the E-glass fiber-reinforced polyester matrix composite. In addition, the 0° fiber orientation composite has a higher tensile strain to failure (8.5%) than E-glass fiber-reinforced composites. The high failure strain and relatively high tensile strength indicate that the false banana with 0° fiber orientation is tougher and has a better energy absorption capability than the other three fiber orientations of the false banana fiber composite and the brittle GRP composite (David and Johnson Citation2015). Our results agree well with earlier studies that revealed composites reinforced with fibers aligned in the loading direction exhibit high strength and modulus of elasticity (Lasikun et al. Citation2018; Tyagi et al. Citation2024). On the other hand, as seen in , the false banana fiber composite with 90° fiber orientation has the lowest tensile strength compared to the others, indicating that the fiber aligned perpendicular to the load direction results in poor mechanical strength (Ezema et al. Citation2014). In this case, the matrix bears most of the load, leading to matrix crack, delamination, and a complete failure of the composite (Madnasri, Astika, and Marwoto Citation2022; Tyagi et al. Citation2024). The composite with mixed 0o/90° fiber orientation has medium strength and failure strain. A composite’s tensile strength and failure strain when fibers are aligned at +45° are low compared to the 0°/90° orientation. As shown in , the composite becomes less stiff and fails at low tensile stress when fibers are aligned at an angle to the loading direction. This is very consistent with the literature data on woven composites (Koohbor, Ravindran, and Kidane Citation2016). It has been well documented that fibers tend to rotate and align to the loading direction when the fibers are off-axis to the loading. This rotation creates local matrix damage, resulting in the extrusion of the matrix out of the plane. This phenomenon is called fiber trellising and is known to cause matrix failure and delamination (Koohbor, Ravindran, and Kidane Citation2016).
Figure 8. The tensile stress-strain graph for glass-reinforced and false banana fiber composite with four different fiber orientations.
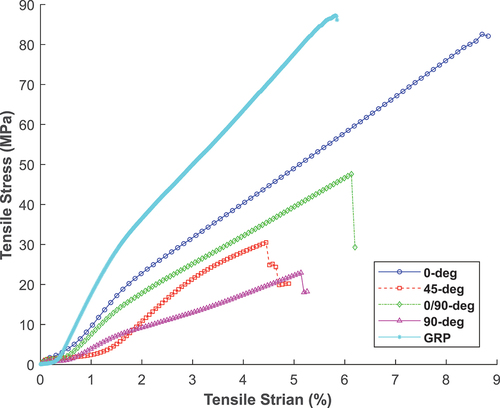
Table 3. The tensile strength results of E-glass fiber and false banana fiber composites with four different fiber orientations.
Flexural strength
The flexural strength test result of the false banana fiber-reinforced composite for the four fiber orientations is summarized in and . The results show that the composite with 0°–90° fiber orientation has the highest flexural strength of 141.73 MPa, followed by 0° fiber orientation (110.91 MPa). The composite with 90° fiber orientation has the lowest flexural strength of 33 MPa, and the composite with ± 45° fiber orientation has a flexural strength of 65.64 MPa. The 0°/90° fiber orientation has a twofold effect where fibers aligned to the 0° bear most of the load in the bending direction, and fibers aligned to the 90° provide resistance to transverse deformation. Furthermore, the 0°/90° fiber orientation reduces shear stress within the material during bending, resulting in higher bending load resistance due to better fiber–matrix interaction than unidirectional fiber orientation (Patel, Patel, and Dave Citation2020). However, as shown in , the composite with 0° fiber orientation has a better elongation (higher failure strain) than the other three fiber orientations but is slightly lower than the GRP composite.
Figure 9. The flexural stress-strain graph for glass-reinforced and false banana fiber composite with four different fiber orientations.
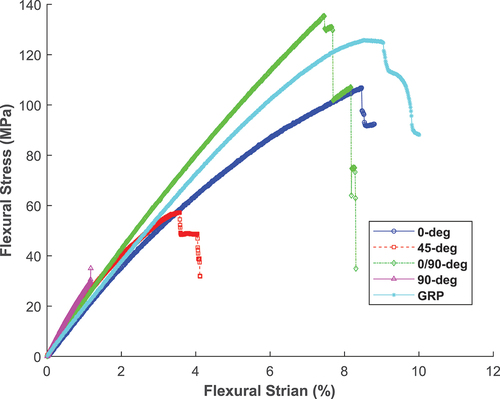
Table 4. The flexural strength results of E-glass fiber and false banana fiber composites with four different fiber orientations.
Compression strength
depicts the composite’s compressive stress-strain plot for the four types of fiber orientations, and summarizes the compressive strength test results. The graph shows that the false banana fiber reinforced composite with 0° fiber orientation has the highest compressive strength (92.79 MPa), followed by the composite with 0°/90° fiber orientation (88.65 MPa). It also observed that the compressive stiffness of the 0° fiber orientation is equal to that of the E-glass fiber composites. The higher strength in this fiber orientation is due to the uniform load distribution and the direct alignment of fibers in the direction of the load, resulting in a more efficient transfer of stress from the matrix to the fibers and a minimized occurrence of fiber buckling. The fibers in the 0° alignment can be reinforced by neighboring fibers, which reduces the likelihood of buckling and increases compressive strength; on the other hand, the false banana fiber reinforced composite with 90° fiber orientation showed the lowest compressive strength (81.61 MPa on average), followed by ± 45° fiber orientation (82.60 MPa on average), which offers a similar effect to prior studies (Seshaiah Citation2018). As shown in , as expected, the GRP composite’s compressive strength is the highest compared to the false banana fiber composites with different fiber orientations, but it is too stiff. This shows that while the GRP composite has excellent compressive strength, it lacks flexibility or ductility, implying that the GRP composite has lower resilience and shock absorption (Yan, Wang, and Kasal Citation2017), suggesting that it might not be appropriate for structures requiring some degree of flexibility or resilience.
Figure 10. The compression stress-strain graph for glass-reinforced and false banana fiber composite with four different fiber orientations.
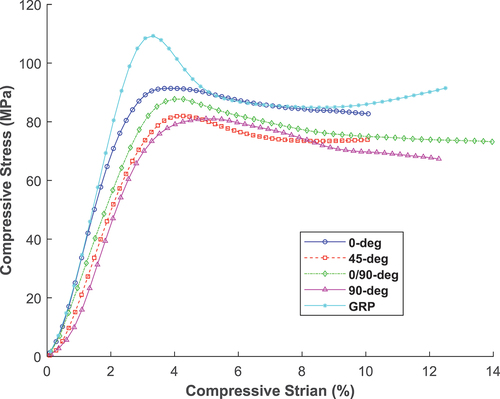
Table 5. The compression strength results from E-glass fiber and false banana fiber composites with four different fiber orientations.
Impact resistance
The total energy absorbed by the glass fiber and false banana fiber composites with different fiber orientations is shown in and . The table shows that the false banana fiber reinforced composite with 0° fiber orientation absorbs more energy (6.11 J on average), followed by the false banana fiber composite with 0°/90° fiber orientation, which absorbs 6.05 J on average. The GRP composite absorbs the least energy (5.56 J on average), followed by the 90° fiber-oriented composites (5.76 J on average). From this, we can observe that false banana fiber reinforced composite with 0° fiber orientation has the best impact resistance, followed by 0°/90° fiber oriented false banana fiber reinforced composite. Besides the material properties, this indicates that the 0° fiber orientation provides a higher rate of energy absorption than the other forms of fiber orientation and GRP composite (Lasikun et al. Citation2018; Raj et al. Citation2024). A composite made of 0o false banana fibers exhibits significant fiber–matrix interaction and better matrix-fiber bonding due to the flexible nature of the false banana fiber, which results in higher impact energy absorption. The 90° fiber orientation reduces the impact strength of the composite while altering the fiber alignment away from the load direction.
Figure 11. The impact energy absorbed graph for glass-reinforced and false banana fiber composite with four different fiber orientations.
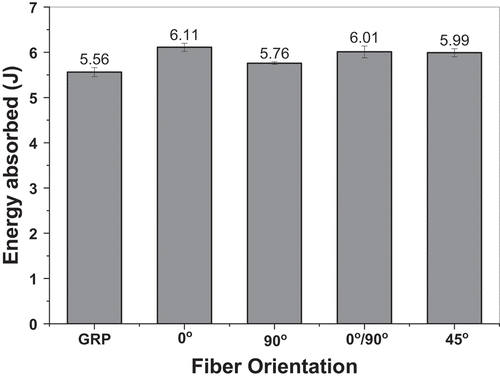
Table 6. The impact resistance results of E-glass fiber and false banana fiber composites with four different fiber orientations.
Water absorption
The water absorption performance of the treated and untreated false banana fiber polymer composite is shown in and tabulated in . Water absorption was much higher for the treated fiber composite on the first day, then dropped drastically after the first day and continued until the fifth day. After the fifth day, the water absorption rate for treated samples becomes very low and eventually drops to zero by the end of the tenth day. However, the water intake for the untreated sample was much higher and lasted for more than ten days. The rapid water absorption observed on the first day on both untreated and treated samples could be associated with porosity in the material. However, the treated fiber composites drastically decrease the absorption rate over the next four days. The total water absorption of the treated fiber-reinforced composite samples in ten days is around 2.83%, while it was 9.36% for the untreated fiber composite sample, a 70% decrease. This indicates that the proposed mechanical extraction, using a pair of wood strips, and the alkaline-based chemical treatment made the fiber more stable by removing the highly hydrophilic parts, such as lignin and hemicellulose and the ionization of OH ion of the fiber to the alkoxide of the alkaline solution. Again, the enhanced dimensional stability in the treated fiber composite was due to good interfacial adhesion between the fiber and the matrix, conceived by the fiber’s rough surface morphology related to better fiber treatment. The reaction of the false banana fiber to alkaline (NaOH) looks like the equation below.
Figure 12. The rate of average water absorption in grams per day for chemically treated and untreated false banana fiber-reinforced composite.
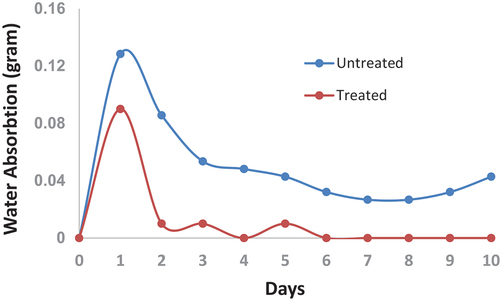
Table 7. Water absorption for treated and untreated false banana fiber reinforced composite.
Discussion
The false banana fiber-reinforced composite presented in this work has achieved strength equivalent to the glass fiber-reinforced composite. In particular, composites with 0° fiber orientation have higher tensile, compressive strength, and impact resistance, and we believe this is due to the fiber treatment proposed in this work. As presented earlier, after extraction, the fiber was immediately washed with DI water and passed through a pair of tightened blunt wood to eliminate the matrix’s barriers. This was followed by the alkaline treatment to remove any leftover contaminants from the fiber’s skin. To understand the effect of impurities such as lignin, hemicellulose, and some waxes on the surface of false banana fiber in the mechanical properties of the composites, the microstructure of both treated and untreated fiber was investigated using a zeta 20 3D optical microscope. The microstructure image in clearly shows the difference in surface morphology between the treated and untreated fibers. The figure shows that mechanical treatment removed most of the lignin left on the fiber’s surface. However, when chemical treatment using sodium hydroxyl solution was used, the remaining lignin and some hemicellulose material were removed, and a uniform surface free from pores was achieved. This chemical treatment reached a more consistent and regular rough surface than the mechanical treatment. In addition to cleaning, the rough skin of the fiber produced by the agitation of the NaOH solution enabled the composite to have more significant interaction between the fiber and matrix and reduced delamination between the fiber and matrix (Kassegn et al. Citation2024; Yeh, Wu, and Yang Citation2024).
Figure 13. Fiber Surface morphology obtained by using Zeta 20 3D optical microscope (a) untreated fiber, (b) mechanically treated fiber, and (c) chemically treated fiber.
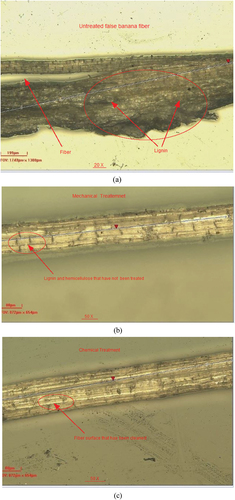
Apart from improving interfacial adhesion, the Alkali NaOH treatment reduces moisture absorption of the fiber due to skin modification and blockage of the gaps between each pair of microfibrils of the fiber, as well as the filling of some indents on the surface of the fiber by the linked agents during alkali treatment (Martel, Salgado, and Silva Citation2022; Sreekala and Thomas Citation2003). This improves dimensional stability by reducing swelling and shrinking of the fiber caused by absorbed moisture. Again, the moisture content of the fiber decreases as a result of the removal of the hydrophilic part of the fiber, mostly the substantial source of the hydroxyl group (−OH) located on the surface of the fiber, such as hemicellulose and lignin from the fiber’s skin.
Though the fiber with 0° orientation has shown better tensile, compressive strength, and impact resistance, using different fiber orientations for other parts of the prosthesis may be necessary by arranging each lamina to counteract the load exerted on the layer of the prosthetic socket (Odusote, Adebisi, and Akande Citation2016). For instance, the inner layer of the socket faces less tensile stress but is more likely subjected to flexural load. This requires the lamina to have higher bending load resistance. On the contrary, the outer layer of the lower limb prosthetic socket or shank is exposed to tension, requiring the lamina to withstand the axially applied load. As a result, it could be essential to design the inner layer of the lower limb prosthetic socket using lamina with 0°/90° fiber orientation and the outer layer with 0° fiber orientation.
In general, since false banana fiber is abundant in various areas, particularly in the southern and western parts of Ethiopia, the finding could lead to the manufacturing of prosthetic sockets as required by the individual wearer. This study provides a basis for producing environmentally friendly biodegradable prosthetic sockets and reducing the health hazards associated with synthetic materials.
Conclusion
A natural fiber-based composite with strength in the order of glass fiber composite has been fabricated and characterized. A composite of abundant false-banana fiber and polymer materials has been produced using the hand layup method. A detailed procedure is developed to treat the fibers. The material’s tensile, compressive, flexural, and impact strengths were characterized following ASTM standards, and the results were compared with glass fiber composites.
The proposed natural fiber composite tensile and flexural strength is slightly lower than the glass fiber-polymer matrix composite. In contrast, its tensile strain and energy absorption are higher than those of glass fiber composites. This indicates that a false banana fiber reinforced polyester matrix composite with 0° fiber orientation can be substantial when absorbing more impact load. Since false banana fiber composite is less rigid than glass fiber reinforced composite, it could be an excellent candidate material for use in prosthetic sockets. Since the material is bio-friendly and less rigid, it could better comfort the prosthetic wearer.
The false banana fiber composite can be further improved with a better-treating technique and replace the synthesis fiber composites. Since the fibers are abundantly available, they are sustainable, can significantly impact the environment, and are cost-effective for prosthetic and structural material applications.
Consent
All authors have approved the manuscript and agree with its submission to the Journal of Natural Fibers.
Ethical approval
No human or animal subject is involved in this study.
Highlights
Biocompatible and unidirectional false banana fiber-reinforced composites were fabricated.
A 0o fiber orientation false banana fiber shows properties that fulfill prosthesis application.
The proposed mechanical extraction and chemical treatment technique has been found to increase the fiber’s mechanical strength.
The fiber treatment reduces the water absorption rate, thereby enhancing the dimensional stability of the composite.
Since fibers are abundantly available, the proposed material can significantly impact the environment and cost-effectiveness of prosthetic applications.
Acknowledgments
The authors greatly acknowledge the Bio and Emerging Technology Institute for providing the materials used in this research. Part of the research was conducted during the summer when Addis Kidane traveled to Ethiopia as part of the Carnegie African Diaspora fellowship program. The summer program was funded by a grant from the Carnegie Corporation of New York (CCNY) and is acknowledged.
Disclosure statement
No potential conflict of interest was reported by the author(s).
Additional information
Funding
References
- Andrew I Campbell, S. S., C. J. Schaschke, H. Kinsman, B. McLaughlin, and M. Boyle. 2012. “Prosthetic Limb Sockets from Plant-Based Composite Materials.” Prosthetics and Orthotics International 36 (2): 181–17. https://doi.org/10.1177/0309364611434568.
- Arthanarieswaran, A. K. V. P., M. Kathirselvam, and M. Kathirselvam. 2014. “Evaluation of Mechanical Properties of Banana and Sisal Fiber Reinforced Epoxy Composites: Influence of Glass Fiber Hybridization.” Materials and Design 64:194–202. https://doi.org/10.1016/j.matdes.2014.07.058.
- ASTM International. 2015a. “Standard Test Method for Compressive Properties of Rigid Plastics.” In D695-15, 8. West Conshohocken. https://doi.org/10.1520/D0695-15.
- ASTM International. 2015b. “Standard Test Method for Tensile Properties of Plastics1.” InASTM D638 − 14, Ed, 18. West Conshohocken. https://doi.org/10.1520/D0638-14.
- ASTM International. 2017. “Standard Test Methods for Flexural Properties of Unreinforced and Reinforced Plastics and Electrical Insulating Materials.” In Astm D790-17, 6. West Conshohocken. https://doi.org/10.1520/A0370-24.
- D570 − 98 Standard Test Method for Water Absorption of Plastics. ed. 2018. USA: World Trade Organization Technical Barriers. https://doi.org/10.1520/D0570-98R18.
- David, M., and A. F. Johnson. 2015. “Effect of Strain Rate on the Failure Mechanisms and Energy Absorption in Polymer Composite Elements Under Axial Loading.” Composite Structures 122:430–439. https://doi.org/10.1016/j.compstruct.2014.11.010.
- Dejene, B. K., and T. M. Geletaw. 2023. “A Review on False Banana (Enset Ventricosum) Fiber Reinforced Green Composite and Its Applications.” Journal of Natural Fibers 20 (2): 2244163. https://doi.org/10.1080/15440478.2023.2244163.
- Demissie Boset, L. 2019. “Mechanical Properties of False Banana Reinforced Epoxy Composite.” Global Scientific Journal 7 (12): 26–31.
- Ezema, I. C., A. R. Menon, C. S. Obayi, and A. D. Omah. 2014. “Effect of Surface Treatment and Fiber Orientation on the Tensile and Morphological Properties of Banana Stem Fiber Reinforced Natural Rubber Composite.” Journal of Minerals and Materials Characterization and Engineering 2014 (3): 216–222. https://doi.org/10.4236/jmmce.2014.23026.
- Ferede, E., and D. Atalie. 2022. “Mechanical and Water Absorption Characteristics of Sisal Fiber Reinforced Polypropylene Composite.” Journal of Natural Fibers 19 (16): 14825–14838. https://doi.org/10.1080/15440478.2022.2069188.
- Furtos, G., L. Molnar, L. Silaghi-Dumitrescu, P. Pascuta, and K. Korniejenko. 2022. “Mechanical and Thermal Properties of Wood Fiber Reinforced Geopolymer Composites.” Journal of Natural Fibers 19:6676–6691. https://doi.org/10.1080/15440478.2021.1929655.
- Furtos, G., L. Silaghi-Dumitrescu, P. Pascuta, C. Sarosi, and K. Korniejenko. 2019. “Mechanical Properties of Wood Fiber Reinforced Geopolymer Composites with Sand Addition.” Journal of Natural Fibers 18 (2): 285–296. https://doi.org/10.1080/15440478.2019.1621792.
- Herlina Sari, N., I. N. G. Wardana, Y. Surya Irawan, and E. Siswanto. 2017. “The Effect of Sodium Hydroxide on Chemical and Mechanical Properties of Corn Husk Fiber.” Oriental Journal of Chemistry 33 (6): 3037–3042. https://doi.org/10.13005/ojc/330642.
- Irawan, A. P., and I. W. Sukania. 2015. “Tensile Strength of Banana Fiber Reinforced Epoxy Composites Materials.” Applied Mechanics and Materials 776:260–263. https://doi.org/10.4028/www.scientific.net/AMM.776.260.
- Irawan, T. P. S. A. P., K. Widjajalaksmi, and A. H. S. Reksoprodjo. 2011. International Journal of Mechanical and Materials Engineering, 6 (1): 46–50.
- Karin Rotter, R. S., K. Robles, M. Godoy, and M. Godoy. 2006. “A Descriptive Study of Traumatic Lower Limb Amputees from the Hospital Del Trabajador: Clinical Evolution from the Accident Until Rehabilitation Discharge.” Prosthetics and Orthotics International 30 (1): 81–86. https://doi.org/10.1080/03093640600581065.
- Kassegn, E., B. Sirhabizu, T. Berhanu, B. Buffel, and F. Desplentere. 2024. “Experimental Study on Single Fiber Tensile Properties of Sisal Fibers Using a Digital Image Correlation Method As a Strain Measurement.” Journal of Natural Fibers 21 (1): 2325557. https://doi.org/10.1080/15440478.2024.2325557.
- Koohbor, B., S. Ravindran, and A. Kidane. 2016. “Meso-Scale Study of Non-Linear Tensile Response and Fiber Trellising Mechanisms in Woven Composites.” Journal of Reinforced Plastics and Composites 35 (12): 986–995. https://doi.org/10.1177/0731684416633771.
- Kumaresan, M., S. Sathish, and N. Karthi. 2015. “Effect of Fiber Orientation on Mechanical Properties of Sisal Fiber Reinforced Epoxy Composites.” Journal of Applied Science and Engineering 18 (3): 6. https://doi.org/10.6180/jase.2015.18.3.09.
- Lasikun, L., D. Ariawan, E. Surojo, and J. Triyono. 2018. “Effect of Fiber Orientation on Tensile and Impact Properties of Zalacca Midrib Fiber-HDPE Composites by Compression Molding.” AIP Conference Proceedings, Feburary 2018, Vol. 1931. AIP Publishing. https://doi.org/10.1063/1.5024119.
- Madnasri, S., G. Astika, and P. Marwoto. 2022. “The Effects of Natural Fiber Orientations on the Mechanical Properties of Brake Composites.” Journal of Natural Fibers 19 (8): 2980–2991. https://doi.org/10.1080/15440478.2020.1838989.
- Martel, W. D. N. D. R., I. Salgado, and F. Silva. 2022. “The Influence of Fiber Treatment on the Morphology, Water Absorption Capacity and Mechanical Behavior of curauá Fibers.” Journal of Natural Fibers 19 (2): 642–657. https://doi.org/10.1080/15440478.2020.1758863.
- Martin Marino, S. P., M. Greenberg, A. Miller, E. Hocker, S. Ritter, and K. Mehta. 2015. “Access to Prosthetic Devices in Developing Countries: Pathways and Challenges.” The IEEE 2015 Global Humanitarian Technology Conference. The Pennsylvania State University. https://doi.org/10.1109/GHTC.2015.7343953.
- Mujahid Khan, S. R., M. A. Mateen, D. V. Ravi Shankar, M. Manzoor Hussain, and M. Manzoor Hussain. 2019. “Effect of NaOH Treatment on Mechanical Strength of Banana/Epoxy Laminates.” Polymers from Renewable Resources 10 (1–3): 19–26. https://doi.org/10.1177/2041247919863626.
- Odusote, A. T. O. J. K., J. A. Adebisi, and K. A. Akande. 2016. “Mechanical Properties of Banana Pseudo Stem Fibre Reinforced Epoxy Composite As a Replacement for Transtibial Prosthetic Socket.” The Journal of the Association of Professional Engineers of Trinidad and Tobago 44 (2): 4–10.
- Patel, H. V., S. M. Patel, and H. K. Dave. 2020. “Influence of Fiber Orientation and Number of Layer on Tensile and Flexural Strength of Carbon Fiber-Reinforced Composites Fabricated by VARTM Process.” In Advances in Manufacturing Processes: Select Proceedings of RAM 2020, ed: 421–430. Singapore: Springer.
- Raj, T., A. Jain, A. Raj, B. Tyagi, A. Sahai, and R. Swarup Sharma. 2024. “Infill Strategies for Improving the Impact Behavior of Polymer Composites Utilizing Statistical and Thermal Analysis.” International Journal of Polymer Analysis and Characterization 29 (2): 1–18. https://doi.org/10.1080/1023666X.2024.2319404.
- Raj, A., B. Tyagi, A. Goyal, A. Sahai, and R. S. Sharma. 2023. “Comparing the Predictability of Soft Computing and Statistical Techniques for the Prediction of Tensile Strength of Additively Manufactured Carbon Fiber Polylactic Acid Parts.” Journal of Materials Engineering and Performance: 1–13. https://doi.org/10.1007/s11665-023-08844-y.
- Ramesh, G., K. Subramanian, S. Sathiyamurthy, and M. Prakash. 2022. “Calotropis Gigantea Fiber-Epoxy Composites: Influence of Fiber Orientation on Mechanical Properties and Thermal Behavior.” Journal of Natural Fibers 19 (10): 3668–3680. https://doi.org/10.1080/15440478.2020.1848718.
- Sahu, S., S. Nayak, S. B. Sahu, and M. K. Roul. 2023. “Influence of Various Surface Treatments on Mechanical, Thermal, Morphological, and Water Absorption Properties of Rattan (Calamus Beccarii) Fiber.” Journal of Natural Fibers 20 (1): 2125924. https://doi.org/10.1080/15440478.2022.2125924.
- Seshaiah, T. 2018. “Effect of Fiber Orientation on the Mechanical Behavior of E-Glass Fibre Reinforced Epoxy Composite Materials.” International Journal of Mechanical and Production Engineering Research and Development 8 (4): 379–396. https://doi.org/10.24247/ijmperdaug201840.
- Shimels, H. G., S. Ketema, T. Trzepieciński, and T. Batu. 2023. “Experimental Investigation of Aloe Vera-Treated False Banana (Ensete Ventricosum) Fibre-Reinforced Polypropylene Composite.” Journal of Composites Science 7 (7): 288. https://doi.org/10.3390/jcs7070288.
- Sreekala, S. T. M. S., 1, and S. Thomas. 2003. “Effect of Fibre Surface Modification on Water-Sorption Characteristics of Oil Palm Fibres.” Composites Science and Technology 63 (6): 861–869. https://doi.org/10.1016/S0266-3538(02)00270-1.
- Standard, A. 2014. “ASTM A370: Standard Test Methods and Definitions for Mechanical Testing of Steel Products.” Annual Book of ASTM Standards. https://doi.org/10.1520/A0370-24.
- Taye, B., and Z. Alemayehu. 2023. “Synthesis and Characterization of Mechanical and Physical Properties of False Banana (ʾənäsätə) Fiber Reinforced Composite Material.” Ethiopian International Journal of Engineering and Technology 1:49–61. https://doi.org/10.59122/134CFC10.
- Temesgen Batu a, H. G. L., and H. G. Lemu. 2020. “Investigation of Mechanical Properties of False Banana/Glass Fiber Reinforced Hybrid Composite Materials.” Results in Materials 8:1–6. https://doi.org/10.1016/j.rinma.2020.100152.
- Temesgen Batu, H. G. L., and H. G. Lemu. 2020. “Investigation of Mechanical Properties of False Banana/Glass Fiber Reinforced Hybrid Composite Materials.” Results in Materials 8 (2020): 6. https://doi.org/10.1016/j.rinma.2020.100152.
- Tyagi, B., K. Dixit, A. Sahai, and R. S. Sharma. 2024. “Characterization of Flexural and Compressive Behavior in Polylactic Acid Composites for Low‐Cost Transtibial Prosthetic Applications: Influence of Reinforcements.” Journal of Applied Polymer Science 141 (18): e55319. https://doi.org/10.1002/app.55319.
- Tyagi, B., A. Raj, A. Sahai, and R. S. Sharma. 2024. “Enhancing Compressive Strength in Polymer Composites Utilized for Application of Foot Prostheses.” Journal of Polymer Research 31:30. https://doi.org/10.1007/s10965-024-03880-1.
- Tyagi, B., A. Sahai, and R. S. Sharma. 2023. “Augmenting the Flexural Strength of Polymer Composites for Stronger and More Durable Prosthetic Sockets.” Polymer Composites 44 (9): 5656–5674. https://doi.org/10.1002/pc.27517.
- Yadav, P., I. Singhal, B. Tyagi, A. Sahai, and R. S. Sharma. 2020. “Intensifying Hands-On Learning and Experimentation of Fused Deposition Modeling Three-Dimensional Printers.” Advances in Additive Manufacturing and Joining: Proceedings of AIMTDR 2018 309–317. https://doi.org/10.1007/978-981-32-9433-2_27.
- Yan, L., B. Wang, and B. Kasal. 2017. “Can Plant-Based Natural Flax Replace Basalt and E-Glass for Fiber-Reinforced Polymer Tubular Energy Absorbers? A Comparative Study on Quasi-Static Axial Crushing.” Frontiers in Materials 4 (2): 42. https://doi.org/10.3389/fmats.2017.00042.
- Yeh, C.-H., J.-H. Wu, and T.-C. Yang. 2024. “Drying Shrinkage and Mechanical Strength of Cementitious Composites with Alkali-Treated Makino Bamboo Fibers.” Journal of Natural Fibers 21 (1): 2321531. https://doi.org/10.1080/15440478.2024.2321531.
- Zelalem Biresaw, A., B. Sirahbizu Yigezu, and A. Gloria. 2022. “Investigation on the Mechanical Properties of Flax/False Banana Hybrid Fiber-Reinforced Polymer Composite.” Advances in Materials Science and Engineering 2022:1–7. https://doi.org/10.1155/2022/5696758.