ABSTRACT
The aim of this research was to develop composites dedicated to thermal insulation, developed on the basis of natural raw materials. The composites consisted of mixture of lime, cement, water, and two biodegradable materials: a local mountain sheep wool treated as troublesome waste and hemp shives obtained by processing decorticated hemp straw of the Białobrzeskie variety. On a laboratory scale, blocks were produced with varying percentages of shives with a fraction of 10 and 30 mm. Sheep wool used was in two ways: (1) mixed in the mass or (2) arranged in a layer between lime. The basic parameter – thermal conductivity of the composites was determined. The research showed that making a composite of lime with hemp shives decreased the thermal conductivity coefficient of the material. The addition of hemp shives reduced the thermal conductivity coefficient by an average of 36% and 45%, when using shives crushed into 10 mm fractions or 30 mm fractions, respectively. The addition of 20% and 40% sheep wool decreased the λ coefficient by approximately 40%. The λ coefficient of the composite formed using hemp shives and wool is 0.0738 W/mK. The proposed composites might be a good alternative to commonly used thermal insulation materials.
摘要
这项研究的目的是开发专门用于隔热的复合材料,该复合材料是在天然原材料的基础上开发的. 该复合材料由石灰、水泥、水和两种可生物降解材料的混合物组成: 一种是被处理成麻烦废物的当地山羊毛,另一种是通过加工Białobrzeskie品种的去壳大麻秸秆而获得的大麻草. 在实验室规模上,用不同百分比的部分为10毫米和30毫米的韭菜生产砌块. 绵羊羊毛的使用有两种方式: (1)混合在一起或(2)排列在一层甜菜酸橙中. 测定了复合材料的基本参数——导热系数. 研究表明,用大麻籽制成石灰复合材料降低了材料的导热系数. 当使用被粉碎成10毫米级或30毫米级的大麻时,添加大麻籽分别使导热系数平均降低36%和45%. 添加20%和40%的羊毛使λ系数降低了约40%. 使用大麻和羊毛形成的复合材料的λ系数为0.0738W/mK. 所提出的复合材料可能是常用隔热材料的良好替代品.
Introduction
Recently, there has been an increase in interest in ecological insulation materials produced using renewable raw materials (Cetiner and Shea Citation2018; Ulutaş, Balo, and Topal Citation2023). Raw materials of natural origin constituting waste, such as hemp shives produced in the process of extracting bast fibers and wool, are materials with high potential to be used in the manufacture of insulating products (Kicińska-Jakubowska et al. Citation2023).
Hemp is a plant that produces a large amount of biomass (Pudełko, Kołodziej, and Mańkowski Citation2021). Hemp stalk, 25% consist fiber and 75% wood together with additional accompanying substances. One of the alternative directions of utilization of hemp fiber is to use it in strengthening composite materials. The importance of thermoplastic polymer composites with lignocellulosic raw materials is increasing. Such composites are increasingly used in different branches of economy, among others, in automotive industry, construction, furniture industry, avia-tion, gardening, etc. (Spychalski et al. Citation2013).
However, about 75% of biomass constitute hemp shives. Shives are renewable, fully biodegradable raw materials that perfectly meet, for example, the requirements of green construction. The use of ecological materials in construction is considered a potential way to minimize negative effects on the natural environment (Wang et al. Citation2018). By-products generated in the fiber extraction process can be components of biocomposites used in construction. Hemp shives are less susceptible to biological corrosion than other plant raw materials (e.g. cereal straw) (Bumanis and Bajare Citation2022; Le et al. Citation2015; Sinka et al. Citation2018).
Replacing traditional mineral raw materials with reproducible plant raw materials affects not only the comfort of use but also the protection of the natural environment. Research to date shows that the production of materials for the construction of 1 m2 of a house results in the emission of over 200 kg of CO2 into the atmosphere. Using the new technology, more than half of this emission (approx. 110 kg) can be reduced by using hemp material, which absorbs CO2 from the atmosphere during vegetation. Also very important is the fact that much less energy is consumed in the disposal of materials after the end of their life (Barbhuiya and Bhusan Das Citation2022; Spychalski et al. Citation2013).
High-quality sheep wool is one of the most important animal fibers used in the textile industry. However, currently, wool of lower quality (e.g. coarse wool from mountain sheep breeds) is often treated as a troublesome by-product of breeding. Wool from Polish mountain sheep breeds is very thick and heterogeneous, its low quality prevents the use it for typical production of clothing. Wool often becomes useless waste immediately after shearing, as the economic value of the wool is lower than the cost of shearing. This problem concerns the whole Europe. Instead of being used, wool is unnecessarily stored, buried, or burned. Therefore, alternative ways of using wool are being increasingly sought. They have gained the greatest importance as insulating materials for construction (Parlato, Cuomo, and Porto Citation2022; Rubino et al. Citation2021; Zach et al. Citation2012), sound-absorbing materials (Broda and Bączek Citation2019; Broda et al. Citation2023; Kicińska-Jakubowska et al. Citation2023; Kobiela-Mendrek et al. Citation2020; Patnaik et al. Citation2015), geotextiles (Broda and Gawlowski Citation2020; Broda et al. Citation2017; Marczak, Lejcus, and Misiewicz Citation2020), or fertilizers in organic agriculture (Böhme et al. Citation2012; Bradshaw and Hagen Citation2022; Ordiales et al. Citation2016). Moreover, sheep wool, thanks to its good thermal properties, is used in construction as a heat insulator (Parlato and Porto Citation2020). Wool-based products can be used to insulate closed spaces, e.g. insulation of roofs, walls, and ceilings.
Currently, the most commonly used insulating materials in construction are products obtained in the process of processing crude oil or neopor, which change into styrene and then, after mixing with water and blowing gas, into polystyrene. The main disadvantages of commonly used thermal insulation materials result from the method of their production, which uses nonrenewable raw materials. Such materials are not biodegradable and are produced using technologies that have a negative impact on the natural environment (Garikapati and Sadeghian Citation2018).
The production of typical building materials used in construction requires a large amount of energy. Their production also produces large amounts of greenhouse gases, especially carbon dioxide (Garikapati and Sadeghian Citation2018). It is estimated that the production and transport of construction materials is responsible for 7 to 9% of global emissions in Western Europe (Berge Citation2001; Pietruszka, Gołębiewski, and Lisowski Citation2019). Unfavorable conditions also exist in interiors made of such materials, which is related to reduced water vapor permeability.
The shived-lime composite is a material with a negative carbon footprint (Pittau et al. Citation2017). This material consists of plant raw materials that absorb CO2 during growth (Kołodziej, Pudełko, and Mańkowski Citation2023) and hydrated lime, which needs carbon dioxide in the binding process (Piątkiewicz, Narloch, and Pietruszka Citation2020; Sinka et al. Citation2015).
The use of water vapor permeability material allows to avoid or at least limit the formation of moisture in building partitions. Traditional techniques using insulating materials such as glass wool, mineral wool, and polyurethane require the installation of a vapor barrier on the interior of the wall to prevent condensation and ensure comfort of residents. However, this increases the possibility of condensation forming inside the wall, as well as wall degradation and mold formation. For this reason, it is extremely important to use breathable materials for the building envelope (Busbridge and Rhydwen Citation2010).
The hemp-lime composite is a breathable material. Thanks to the hemp structure made of microscopic cavities, it has good hygrometric properties, which makes the material has an absorption capacity of up to 5 times its weight. This hygroscopic nature makes the hemp-lime mixture a humidity regulator, able to absorb excess moisture and release it when needed. Its water vapor transmission coefficient is quite high, which helps reduce the phenomenon of condensation (Agliata, Gianoglio, and Mollo Citation2019). Protection against fungi in the lime and shive composite is provided by the lime, which is a natural disinfectant (Horszczaruk et al. Citation2023).
Replacing traditionally used raw materials with reproducible natural and renewable raw materials will have a positive impact on the protection of the natural environment. The production of materials traditionally used in insulation involves significant CO2 emissions into the atmosphere. Using natural technologies, a significant part of these emissions can be reduced by using hemp material that absorbs CO2 (Kołodziej, Pudełko, and Mańkowski Citation2023).
There are no reports in the available literature on solutions using hemp shives, sheep wool, and lime combined together for the production of insulating materials. Therefore, the aim of the current research is to develop a composite based on the above-mentioned raw materials that will demonstrate barrier properties in terms of thermal insulation and the management of natural waste resources while achieving the “zero waste” goal in accordance with the European Green Deal strategy.
Experimental
Materials
Hemp shives
The lignocellulosic raw material used in the research was hemp shives obtained by processing decorticated hemp straw of the Białobrzeskie variety. The length composition of the shives was determined: 8% (by mass) were shives with a length of more than 50 mm, 45% were shives with a length ranging from 20 to 40 mm, 20% were shives with a length of 10 to 20 mm, and 27% were shives with a length less than 5 mm. Additionally, 10% of the shives were contaminated with short fibers. Previous research has shown that short hemp fiber and dusty parts reduce the strength parameters of lime and shive composites, therefore the shives were further cleaned of short fiber using a shaking and screening device. Then, using an SM200 cutting and grinding mill, the shives were homogenized into two fractions. The device initially grinds the raw material and then rubs it through a sieve with a given mesh size. The shives were shredded into fractions of 10 and 30 mm in length.
Sheep wool
The raw material in the form of wool comes from Polish mountain sheep. It was characterized by fiber thickness in the range of 41–77 µm and fiber length in the range of 67–128 mm. The above parameters prove that this wool is thick and heterogeneous, and its low quality prevents its traditional use, but it can be used to produce technical products. Wool used in the experiment was washed to remove fatty substances.
Hemp shives-wool-lime composites
The composites were formed manually in the laboratory. For this purpose, wooden forms with dimensions of 300 × 300 × 50 mm were made. The components of the composite were properly prepared hemp shives, sheep wool, lime, portland cement, and water. After mixing using a counter-rotating mixer, the material was poured into molds and dried naturally for a period of 120 h. Nine research samples were prepared, which varied in proportions, granulation of hemp shives, and way of mixing wool (variant 1: wool mixed with lime, hemp shives, and portland cement and variant 2: wool arranged between two layers of lime mixed with hemp shives and portland cement). Percentages of individual raw materials in tested samples are presented in . presents the manufactured composites and their cross-sections.
Table 1. Percentage of individual raw materials in tested samples (by mass).
Methods
The shives were crushed using a cutting mill SM200, Retsch, Germany. Following cleaned using an analysette 3 vibrating screener, Fritsch, Germany. Photographs of the composite structure were taken with a camera Canon, D 600.
The following parameters were determined for composites:
Bulk density.
Thermal conductivity coefficient (λ) in accordance with PN-EN 12,667. The test was performed with the use of the LaserComp FOX314 Heat Flow Meter (TA Instruments, New Castle, DE, USA). The tests were carried out with the use of a fixed, constant flow of heat flux passing through the tested samples. The temperature range used was from −20°C to +55°C with a temperature difference of 25°C.
The statistical evaluation of the test results was performed on the basis of the nonparametric ANOVA Kruskal–Wallis test at a significance level of 0.05 using the Statistica software 14.
Results and discussion
Thickness, bulk density, and thermal conductivity of tested composites are presented in . The structure of the composites is presented in .
Table 2. Thickness, bulk density, and thermal conductivity of tested composites.
Figure 3. The structure of a porous limestone and hemp shives composite I0. Visible pores in the material structure.
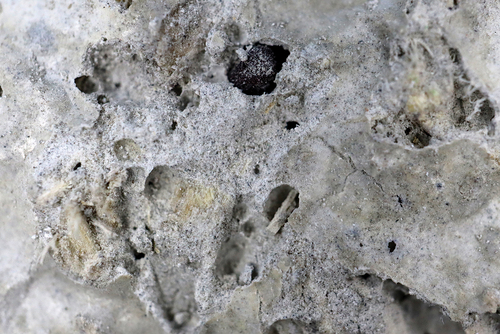
Figure 4. The structure of a porous limestone and hemp shives composite II0. Visible pores in the material structure.
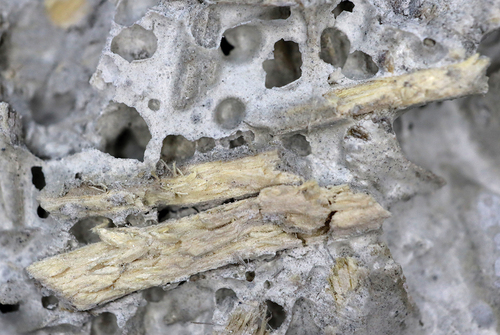
Thickness of all tested composites was about 50 mm. The value of the bulk density for all samples was in the range 422.31–854.93 kg/m3. Sample SW had the highest value of bulk density, while sample 40I the lowest. Samples containing only hemp shives (no wool) were characterized by the bulk density in the range 443.02 (II0)–561.43 (I0) kg/m3, while samples containing wool mixed in the mass were characterized the bulk density in the range 552.16–644.87 kg/m3 (III20W, III40W). Samples containing both hemp shives and wool arranged in a layer (variant 2) showed the bulk density in the range 422.31–498.89 kg/m3.
The values of the thermal conductivity coefficients, λ, of the tested samples were in the range of 0.0738–0.1752 W/mK, with the SW having the highest value of the λ coefficient, and the sample 40I the lowest. Adding 40% wool arranged in a layer resulted in a reduction of the value of thermal conductivity coefficients (40I, 40II).
The statistical analysis of the results of the thermal conductivity coefficients, λ (Kruskal–Wallis test), tested at the significance level of 0.05, showed differences (p = .0000). In order to check which samples were statistically different from each other, a post-hoc test was carried out, which showed remarkable differences between the samples: SW and II0, 20I, 40I, 40II; 0I and 40I, 40II; III20W and 40I; 20II and 40I.
It was decided to add portland cement to strengthen the formed composites. Based on the available literature, it appears that concrete, the main component of which is cement, creates durable structure which is used in the construction of insulating seals (Cheng et al. Citation2023).
Molded composite materials based on lime, hemp shives, and wool are characterized by greater porosity compared to composite made of only lime with portland cement. It is assumed that the porous structure significantly increases the thermal insulation of the material.
It was observed that the length of hemp shives affected the porosity of the material. In composites using 30 mm long hemp shives, more free spaces filled with air were observed, similarly in the case of filling the composite with wool. The material in which the wool was arranged in a layer is characterized by greater porosity compared to the specimen in which the wool was mixed in the mass. This is reflected in the thermal conductivity. The greater the porosity of the tested material, the lower the λ coefficient. The research shows that making a composite of lime with hemp shives improves the thermal insulation coefficient of the material. The addition of hemp shives reduced the thermal conductivity coefficient by an average of 36% when using hemp shives crushed into 10 mm fractions. The use of longer hemp shives (30 mm) improves the λ coefficient and reduces it by approximately 45% compared to an insulating material made of lime with portland cement. According to literature data increasing the share of hemp shives in the lime mixture leads to a decrease in the thermal conductivity coefficient (Garikapati and Sadeghian Citation2018). The density of hempcrete depends primarily on the proportions of the binder, humidity level, and degree of compaction. When any of them increases, the density increases and, consequently, the thermal conductivity value increases. Thermal conductivity depends primarily on the density of the material and changes in direct proportion to it (Dhakal et al. Citation2017; Elfordy et al. Citation2008).
As the density of the composite decreases, the heat conduction coefficient gradually decreases (Barnat-Hunek, Smarzewski, and Fic Citation2015).
The data obtained for composites are in the range reported for cementitious composites (Asadi et al. Citation2018; Khushefati, Demirboğa, and Farhan Citation2022). Relation between density and thermal conductivity was presented by (Asadi et al. Citation2018), who collected data from 185 experiments available in the literature for concrete in the range of 100 kg/m3 to 2400 kg/m3. They pointed out that filler (aggregate) type and amount are the most influential factors for thermal conductivity.
Similarly, insulating boards with the addition of sheep wool mixed in the mass are characterized by better thermal insulation parameters compared to insulating boards made of lime. The addition of 20% and 40% sheep wool improves the λ coefficient by approximately 40%.
Tests on lime-shock boards show that a thermal conductivity coefficient of 0.08 W/(m∙K) is achieved at a board density of 540 kg/m3 (Sinka, Sahmenko, and Korjakins Citation2014). In our research, the addition of 40% wool allowed to achieve a similar value of the thermal conductivity coefficient with a board density of 457 kg/m3. Bulk density is influenced by the size of hemp shives. Finer shives require a larger amount of binder to obtain the desired consistency, which results in increased bulk density (Brzyski et al. Citation2021).
Positive results of forming insulating boards consisting of mixed hemp shives or sheep wool prompted attempts to produce insulating boards containing both lignocellulosic parts from hemp and sheep wool. For this purpose, insulating materials consisting of wool arranged between two layers of lime mixed with hemp shives and portland cement were made. The outer layers are a composite of lime, portland cement, and hemp shives. The middle layer is made of sheep wool. The addition of 35% of shives and 20% of wool arranged in a layer of lime does not significantly reduce the λ coefficient compared to insulating boards based on lime and hemp shives or lime and wool.
Increasing the share of wool to 40% leads to a reduction in the thermal insulation coefficient of the material by approximately 27% compared to a board made of lime and shives or wool, and by as much as approximately 60% compared to an insulating board made only of lime. During the tests, it was observed that partial replacement of mineral raw materials such as lime and cement with natural raw materials increases the flexibility of the formed block, preventing it from cracking. The lime contained in the composite protects the structure against biological corrosion. Lime is a natural disinfectant with antiseptic properties. It destroys mold spores and also helps maintain a favorable humidity level. The influence of contamination with dusty parts on strength and mechanical stability was presented in studies by M. Sinka (Sinka, Sahmenko, and Korjakins Citation2014). The properties of the composite material are also determined by the proportion of hemp shives in relation to lime and cement. Doubling the content of cement-lime binder in hempcrete allows to obtain compressive strength comparable to the class of concrete with lightweight aggregate (Horszczaruk et al. Citation2023).
Conclusions
Domestic natural raw materials in the form of hemp shives and sheep wool from mountain sheep breeds were used in this study. Both types of raw materials are often treated as a by-product of bast fibers processing and animal husbandry. It has been shown that thermal properties depend on the composition of the composite. Conducted research has shown that the addition of hemp shives to lime improves the thermal insulation coefficient compared to a composite made only of lime. Similarly, insulating composites with addition of sheep wool mixed in the mass are characterized by better thermal insulation parameters compared to insulating materials made of lime.
Supplementing the composition of the formed composites with hemp shives, which are a lignocellulosic raw material, and a layer of wool increases the porosity of the material. The good thermal insulation properties of the formed composites, confirmed by tests, eliminate the need to use insulating foil, which increases the vapor permeability of the structure and prevents excessive dampness.
Taking into account bulk density and thermal conductivity of composites II0, 40I, 40II are preferred. In composite II0 use of longer hemp shives makes the composite more porous. The addition of 40% wool arranged between two layers of lime mixed with hemp shives and portland cement (40I, 40II) improves the thermal conductivity parameters without increasing the bulk density of the composite.
The proposed composite may be a good alternative to commonly used thermal insulation materials. In addition, the production of the composites described allows for reducing the amount of by products and implements the “zero waste” goal in accordance with the European Green Deal strategy.
Highlights
Hemp shives produced in the process of extracting bast fibers are an excellent ecological raw material for the production of barrier products in the field of thermal insulation.
Wool treated nowadays as troublesome and useless waste is a precious raw material, which can be used as an additive in a mixture with other materials for the production of innovative products.
Replacing traditionally used non-ecological raw materials with reproducible and renewable natural raw materials like wool or hemp shives has a positive impact on the protection of the natural environment.
The manufactured composites based on lime, hemp shives, and wool are characterized by good thermal insulation properties and may be a good alternative to commonly used thermal insulation materials.
Composites consisting of hemp shives 30 mm long and 40% addition of wool are preferred.
Disclosure statement
No potential conflict of interest was reported by the author(s).
References
- Agliata, R., S. Gianoglio, and L. Mollo. 2019. “Hemp-Lime Composite for Buildings Insulation: Material Properties and Regulatory Framework.” VITRUVIO - International Journal of Architectural Technology and Sustainability 4 (1): 48. https://doi.org/10.4995/vitruvio-ijats.2019.11771.
- Asadi, I., P. Shafigh, Z. F. Abu Hassan, and N. B. Mahyuddin. 2018. “Thermal Conductivity of Concrete –A Review.” Journal of Building Engineering 20:81–11. https://doi.org/10.1016/j.jobe.2018.07.002.
- Barbhuiya, S., and B. Bhusan Das. 2022. “A Comprehensive Review on the Use of Hemp in Concrete.” Construction and Building Materials 341:127857. https://doi.org/10.1016/j.conbuildmat.2022.127857.
- Barnat-Hunek, D., P. Smarzewski, and S. Fic. 2015. “Mechanical and Thermal Properties of Hemp-Lime Composites.” Composites Theory and Practice 15 (1): 21–27. https://kompozyty.ptmk.net/pliczki/pliki/4_2015_t1_Barnat%20Hunek.pdf.
- Berge, B. 2001. The Ecology of Building Materials. 1st ed. London, UK: Oxford: Elsevier. https://doi.org/10.4324/9780080504988.
- Böhme, M. H., I. Pinker, H. Grueneberg, and S. Herfort. 2012. “Sheep Wool as Fertiliser for Vegetables and Flowers in Organic Farming.” Acta Horticulturae 933 (933): 195–202. https://doi.org/10.17660/ActaHortic.2012.933.23.
- Bradshaw, T., and K. Hagen. 2022. “Wool Pellets are a Viable Alternative to Commercial Fertilizer for Organic Vegetable Production.” Agronomy 12 (5): 1210. https://doi.org/10.3390/agronomy12051210.
- Broda, J., and M. Bączek. 2019. “Acoustic Properties of Multi-Layer Wool Nonwoven Structures.” Journal of Natural Fibers 17 (11): 1567–1581. https://doi.org/10.1080/15440478.2019.1584078.
- Broda, J., and A. Gawlowski. 2020. “Influence of Sheep Wool on Slope Greening.” Journal of Natural Fibers 17 (6): 820–832. https://doi.org/10.1080/15440478.2018.1534190.
- Broda, J., A. Gawlowski, S. Przybylo, D. Binias, M. Rom, J. Grzybowska-Pietras, and R. Laszczak. 2017. “Innovative Wool Geotextiles Designed for Erosion Protection.” Journal of Industrial Textiles 48 (3): 599–611. https://doi.org/10.1177/1528083717695837.
- Broda, J., K. Kobiela-Mendrek, M. Bączek, M. Rom, and I. Espelien. 2023. “Sound Absorption of Tufted Carpets Produced from Coarse Wool of Mountain Sheep.” Journal of Natural Fibers 20 (2): 2246103. https://doi.org/10.1080/15440478.2023.2246103.
- Brzyski, P., P. Gleń, M. Gładecki, M. Ruminska, Z. Suchorab, and G. Łagód. 2021. “Influence of the Direction of Mixture Compaction on the Selected Properties of a Hemp-Lime Composite.” Materials 14 (16): 4629. https://doi.org/10.3390/ma14164629.
- Bumanis, G., and D. Bajare. 2022. “PCM Modified Gypsum Hempcrete with Increased Heat Capacity for Nearly Zero Energy Buildings.” Environmental and Climate Technologies 26 (1): 524–534. https://doi.org/10.2478/rtuect-2022-0040.
- Busbridge, R., and R. Rhydwen. 2010. “An Investigation of the Thermal Properties of Hemp and Clay Monolithic Walls.” Proceedings of Advances in Computing and Technology, The School of Computing and Technology 5th Annual Conference, London, UK. University of East London Institutional Repository.
- Cetiner, I., and A. D. Shea. 2018. “Wood Waste as an Alternative Thermal Insulation for Buildings.” Energy and Buildings 168:374–384. https://doi.org/10.1016/j.enbuild.2018.03.019.
- Cheng, J., Q. Fu, Z. Wang, Y. Qin, H. Jiang, K. Gao, and L. Zhang. 2023. “Dynamic Response Characteristics and Structural Optimization of Isolation Seal Under the Impact of Gas Explosion.” Journal of Loss Prevention in the Process Industries 84:105095. https://doi.org/10.1016/j.jlp.2023.105095.
- Dhakal, U., U. Berardi, M. Gorgolewski, and R. Richman. 2017. “Hygrothermal Performance of Hempcrete for Ontario (Canada) Buildings.” Journal of Cleaner Production 142 (142): 3655–3664. https://doi.org/10.1016/j.jclepro.2016.10.102.
- Elfordy, S., F. Lucas, F. Tancret, Y. Scudeller, and L. Goudet. 2008. “Mechanical and Thermal Properties of Lime and Hemp Concrete (“Hempcrete”) Manufactured by a Projection Process.” Construction and Building Materials 22 (10): 2116–2123. https://doi.org/10.1016/j.conbuildmat.2007.07.016.
- Garikapati, K. P., and P. Sadeghian. 2018. “Physical and Mechanical Properties of Flax Lime Concrete.” Paper presented at the CSCE Annual Conference, Fredericton NB, New Brunswick, Canada. Canadian Society of Civil Engineers. June 13–16.
- Horszczaruk, E., J. Strzałkowski, A. Głowacka, O. Paszkiewicz, and A. Markowska-Szczupak. 2023. “Investigation of Durability Properties for Lightweight Structural Concrete with Hemp Shives Instead of Aggregate.” Applied Sciences 13 (14): 8447. https://doi.org/10.3390/app13148447.
- Khushefati, W. H., R. Demirboğa, and K. Z. Farhan. 2022. “Assessment of Factors Impacting Thermal Conductivity of Cementitious Composites—A Review.” Cleaner Materials 5:100127. https://doi.org/10.1016/j.clema.2022.100127.
- Kicińska-Jakubowska, A., J. Broda, M. Zimniewska, M. Bączek, and J. Mańkowski. 2023. “Effect of Blend Composition on Barrier Properties of Insulating Mats Produced From Local Wool and Waste Bast Fibres.” Materials 16 (1): 459. https://doi.org/10.3390/ma16010459.
- Kobiela-Mendrek, K., M. Bączek, J. Broda, M. Rom, I. Espelien, and I. Klepp. 2020. “Acoustic Performance of Sound Absorbing Materials Produced from Wool of Local Mountain Sheep.” Materials 15 (9): 3139. https://doi.org/10.3390/ma15093139.
- Kołodziej, J., K. Pudełko, and J. Mańkowski. 2023. “Energy and Biomass Yield of Industrial Hemp (Cannabis sativa L.) as Influenced by Seeding Rate and Harvest Time in Polish Agro-Climatic Conditions.” Journal of Natural Fibers 20 (1): 2159609. https://doi.org/10.1080/15440478.2022.2159609.
- Le, A. T., A. Gacoin, A. Li, T. H. Mai, and N. E. Wakil. 2015. “Influence of Various Starch/Hemp Mixtures on Mechanical and Acoustical Behavior of Starch-Hemp Composite Materials.” Composites Part B Engineering 75:201–211. https://doi.org/10.1016/j.compositesb.2015.01.038.
- Marczak, D., K. Lejcus, and J. Misiewicz. 2020. “Characteristics of Biodegradable Textiles Used in Environmental Engineering: A Comprehensive Review.” Journal of Cleaner Production 268:122129. https://doi.org/10.1016/j.jclepro.2020.122129.
- Ordiales, E., J. I. Gutiérrez, L. Zajara, J. Gil, and M. Lanzke. 2016. “Assessment of Utilization of Sheep Wool Pellets As Organic Fertilizer and Soil Amendment in Processing Tomato and Broccoli.” Modern Agricultural Science and Technology 2:20–35. https://doi.org/10.15341/mast(2375-9402)/02.02.2016/003.
- Parlato, M., M. Cuomo, and S. M. C. Porto. 2022. “Natural Fibers Reinforcement for Earthen Building Components: Mechanical Performances of a Low Quality Sheep Wool (“Valle Del Belice” Sheep).” Construction and Building Materials 326 (9): 126855. https://doi.org/10.1016/j.conbuildmat.2022.126855.
- Parlato, M., and S. M. C. Porto. 2020. “Organized Framework of Main Possible Applications of Sheep Wool Fibers in Building Components.” Sustainability 12 (3): 761. https://doi.org/10.3390/su12030761.
- Patnaik, A., M. Mvubu, S. Muniyasamy, A. Botha, and R. D. Anandjiwala. 2015. “Thermal and Sound Insulation Materials from Waste Wool and Recycled Polyester Fibers and Their Biodegradation Studies.” Energy and Buildings 92:161–169. https://doi.org/10.1016/j.enbuild.2015.01.056.
- Piątkiewicz, W., P. Narloch, and B. Pietruszka. 2020. “Influence of Hemp-Lime Composite Composition on Its Mechanical and Physical Properties.” Archives of Civil Engineering LXVI (3): 485–503. https://doi.org/10.24425/ace.2020.134409.
- Pietruszka, B., M. Gołębiewski, and P. Lisowski. 2019. “Characterization of Hemp-Lime Bio-Composite.” IOP Conference Series: Earth and Environmental Science 290 (1): 012027. https://doi.org/10.1088/1755-1315/290/1/012027.
- Pittau, F., F. Krause, G. Lumia, and G. Habert. 2017. “Fast-Growing Bio-Based Materials As an Opportunity for Storing Carbon in Exterior Walls.” Building and Environment 129:117–129. https://doi.org/10.1016/j.buildenv.2017.12.006.
- Pudełko, K., J. Kołodziej, and J. Mańkowski. 2021. “Restoration of Minesoil Organic Matter by Cultivation of Fiber Hemp (Cannabis Sativa L.) on Lignite Post-Mining Areas.” Industrial Crops & Products 17:113921. https://doi.org/10.1016/j.indcrop.2021.113921.
- Rubino, C., M. Bonet Aracil, S. Liuzzi, P. Stefanizzi, and F. Martellotta. 2021. “Wool Waste Used as Sustainable Nonwoven for Building Applications.” Journal of Cleaner Production 278:123905. https://doi.org/10.1016/j.jclepro.2020.123905.
- Sinka, M., A. Korjakins, D. Bajare, Z. Zimele, and G. Sahmenko. 2018. “Bio-Based Construction Panels for Low Carbon Development.” Energy Procedia 147:220–226. https://doi.org/10.1016/j.egypro.2018.07.063.
- Sinka, M., L. Radina, G. Sahmenko, A. Korjakins, and D. Bajare. 2015. “Enhancement of Lime-Hemp Concrete Properties Using Different Manufacturing Technologies.” Academic Journal of Civil Engeenering 33 (2): 301–308. https://doi.org/10.26168/icbbm2015.46.
- Sinka, M., G. Sahmenko, and A. Korjakins. 2014. “Mechanical Properties of Pre-Compressed Hemp-Lime Concrete.” Journal of Sustainable Architecture and Civil Engineering 8 (3): 92–99. https://doi.org/10.5755/j01.sace.8.3.7451.
- Spychalski, G., J. Mańkowski, A. Kubacki, J. Kołodziej, W. Cierpucha, I. Pniewska, P. Baraniecki, and L. Grabowska. 2013. Industrial Hemp Cultivation and Processing Technology. Poznan, Poland: INF&MP.
- Ulutaş, A., F. Balo, and A. Topal. 2023. “Identifying the Most Efficient Natural Fibre for Common Commercial Building Insulation Materials with an Integrated PSI, MEREC, LOPCOW and MCRAT Model.” Polymers 15 (6): 1500. https://doi.org/10.3390/polym15061500.
- Wang, H., P. C. Chiang, Y. Cai, L. Chunhui, X. Wang, T. L. Chen, S. Wei, and Q. Huang. 2018. “Application of Wall and Insulation Materials on Green Building: A Review.” Sustainability 10 (9): 3331. https://doi.org/10.3390/su10093331.
- Zach, J., A. Korjenic, V. Petránek, J. Hroudová, and T. Bednar. 2012. “Performance Evaluation and Research of Alternative Thermal Insulations Based on Sheep Wool.” Energy and Buildings 49:246–253. https://doi.org/10.1016/j.enbuild.2012.02.014.