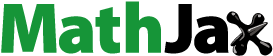
ABSTRACT
Polyamide/elastane warp-knitted fabrics were separately dyed with gall oak (Quercus infectoria Olivier) and madder (Rubia tinctorum L.). Chromatographic and spectroscopic methods were used to analyze dyed warp-knitted fabrics. A reserved phase high-performance liquid chromatography with the diode-array detection (RP-HPLC-DAD) method was utilized to determine the components of dyes present in the dyed fabrics. Scanning electron microscopy-energy X-ray spectroscopy (SEM-EDX) was utilized for morphological analysis. The undyed and dyed warp-knitted fabrics were characterized by FT-IR. The CIEL*a*b* values of the dyed polyamide-elastane warp-knitted fabrics were measured. Further, in physical testing, the pilling and abrasion resistance of raw and dyed fabrics were examined, and the water contact angle values of all fabrics were measured. Pilling test results were evaluated with a grade of 5 for all fabrics as the best score, and the resistance of fabrics to abrasion was very good. The formation of the fiber-metal-dye complex caused the fabric’s contact angle to drop, giving the fabric a hydrophilic character. The colorfastness characteristics of the dyed fabrics to light, rub, wash, and perspiration have been evaluated. The light fastness scores vary from 3 to 5, and they are satisfactory for using natural dyes to color textiles since they are in the good to moderate range. Overall, the dyed samples displayed a score of 5, which is excellent, on the Gray Scale for washing fastness.
Graphical abstract
摘要
分别用苦栎(Quercus infectioria Olivier)和茜草(Rubia tinctorum L.)对聚酰胺/弹性纤维经编织物进行染色。采用色谱法和光谱法对经编染色织物进行了分析. 采用保留相高效液相色谱-二极管阵列检测法(RP-HPLC-DAD)测定染色织物中染料的成分. 利用扫描电子显微镜能量X射线光谱(SEM-EDX)进行形态分析. 用FT-IR对未染色和染色的经编织物进行了表征,测定了染色后的聚酰胺-弹性纤维经编织物的CIEL*a*b*值. 此外,在物理测试中,检查了生织物和染色织物的抗起球性和耐磨性,并测量了所有织物的水接触角值. 所有织物的起球测试结果都以5分为最佳分数,织物的耐磨性非常好. 纤维-金属染料复合物的形成导致织物的接触角下降,使织物具有亲水性. 对染色织物的耐光、耐擦、耐洗、耐汗牢度进行了评价. 耐光性得分从3到5不等,它们对于使用天然染料给纺织品上色是令人满意的,因为它们在良好到中等的范围内. 总体而言,染色样品在洗涤牢度的灰度上显示出5分,这是极好的.
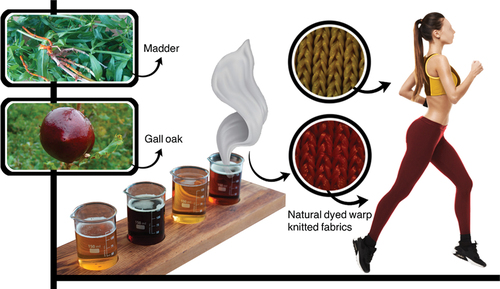
Introduction
Textile products are an indispensable part of all sports since sportswear is used in many application areas, such as swimming trunks, scuba fabrics, sports equipment, sports shoes, and clothes. As people become more interested in sports, various industries that serve these sports, including aquatic and underwater activities, are improving as time progresses (Abasi et al. Citation2013; Kim, Choi, and Shin Citation2020). A new perspective has emerged in sportswear as lifestyle wear, and accordingly, the new demands have changed the function required for sportswear to meet these requirements in general. The increasing growth in the activewear and sportswear market has important effects in terms of product development for the textile industry (Ullah et al. Citation2022). In sportswear, especially in swimwear production, the best fabric properties are provided by combining elastane and synthetic yarns. Elastic fibers and yarns that exhibit good extensibility and elastic recovery are used in the manufacture of elastic fabrics, including knitted fabrics. For this function, continuous filament yarns made from elastomeric or spandex fibers have been used with synthetic yarns like polyamide (Hoque et al. Citation2022). Polyamide fiber, one of the most frequently used engineering thermoplastics, is created by polycondensing hexamethylenediamine and adipic acid. It offers high wear resistance, abrasion resistance, and strength (Yıldız Varan, Çaydamlı, and Altay Citation2023). On the other side, it has low oil and flammability resistance and a marginally reduced ability to absorb moisture (Varan and Altay Citation2022). Elastane fiber, created in 1937 by O. Bayer and H. Rinke, is the basis of modern elastane fibers and has the outstanding property of an exceptionally high elongation at a break of 200–800% and almost completely returning to its original length after external forces have been removed (Veit Citation2023). Elastane, Spandex, or Lycra™ fibers are also, per definition, covered by at least 85% of the mass of a segmented polyurethane that may stretch up multiple times (100–600%) its normal length and immediately revert to its original shape when the applied force is removed (Boschmeier et al. Citation2023).
Warp-knitted fabrics are a crucial subcategory of textiles created using quite efficient and productive warp-knitting technology. These fabrics are especially preferred when they have properties such as drapability, moldability, knitting according to shape, openwork, extensibility, durability, strength, and a lightness of weight. Warp knitting offers higher production rates than weaving with large working widths, and costs are at a premium that can be tailored to requirements. Warp knitted fabrics are used in the production of women’s underwear (Mariem et al. Citation2020), swimsuits (Kursun and Ozcan Citation2010), sportswear (Cong et al. Citation2022), suits (Mishra Citation2022), lining (Abd El-Hady and Abd El-Baky Citation2015), and towels (Cong et al. Citation2014). Woven and non-woven fabrics account for the majority of technical textiles (Xie Citation2022), but nowadays, warp-knitted and weft-knitted structures are also increasingly used in the production of to meet different requirements as a substrate in medical (Venkatraman Citation2022), geotextiles (Tanasă et al. Citation2022), transportation (Wang et al. Citation2022) automotive (Ahirwar and Behera Citation2022), composites (Liu, Hua, and Li Citation2022) and industrial textiles (Cherradi et al. Citation2022). Regarding the large range of uses for warp-knitted materials, developing fabric structures has become increasingly complicated. Designers working in this field now need to know about the production of warp knitted fabrics (Kyosev Citation2019; Spencer Citation2001). This industry is among the most inventive producers and holds a significant position in the global textile sector. The main reason for this industry’s expansion is the change in fashion and lifestyle (Maulik, Debnath, and Pandit Citation2022).
Natural dyes are usually obtained from three primary sources: plants, animals, and minerals (Rahman et al. Citation2023). Humans have been using natural dyes since the dawn of human civilization, and with a rising interest in eco-textiles and eco-friendly processing methods, using natural dyes for simultaneous dyeing and finishing of textiles has recently become a popular trend (Fang et al. Citation2023). There are different extraction techniques for natural dyes, such as traditional aqueous extraction (Haji, Shahmoradi Ghaheh and Indrie Citation2023), alkaline or acid extraction (Agrawal and Chopra Citation2020), microwave (Adeel et al. Citation2023) or ultrasonic energy (Patil, Mudaliar, and Athalye Citation2023), plasma treatment (Eyupoglu et al. Citation2023), supercritical fluid extraction (Sk et al. Citation2021) and by just in time extraction (Karadag Citation2022a). Gall oak, which dates back to the Sumerians, is still used today for creating ink and for coloring leather and other textile materials (Abdulkadir and Karadag Citation2022). Galls of Quercus infectoria Olivier have been indicated through pharmacological investigations to possess antifungal and antibacterial properties. Studies have also documented its antioxidant, anti-diabetic, anti-parkinsonian, and anti-trembling properties (Ahmad et al. Citation2011). Madder (Schmidt-Przewozna and Rój Citation2023) and Quercus ithaburansis (Ozdemir and Karadag Citation2023a) have a high commercial, economical, and medicinal importance. The root of madder plant contains different anthraquinone-based natural colorants with alizarin as the main coloring component (Ozdemir and Karadag Citation2023b; Safapour, Mazhar, and Abedinpour Citation2023).
The use of natural dyes to color synthetic fibers, particularly polyamide, has gained attention recently, and different research teams have examined the method of natural coloring polyamide fabrics. Baaka et al. used the pre-mordanting method to color wool and polyamide fibers for developing a dyeing investigation. Janković et al. studied the potential use of the living bacterial cultures of pigment-producing bacterial strains for the dyeing of PA and polyamide-elastane (PA/EA) fabrics (Janković et al. Citation2023). Rehman et al. used microwave radiation to isolate natural colorants for the dyeing of polyamide fabric (Rehman et al. Citation2022). Haji et al. investigated the natural dyeing of polyamide fabric using the dragon’s blood resin extract (Haji, Shahmoradi Ghaheh, and Mohammadi Citation2022). The current research study aims to examine polyamide warp-knitted fabrics colored with natural dyes for sportswear production as sports textiles and how the liquor ratio affects the colorimetric and fastness characteristics of polyamide fabrics colored with natural dyes. Spectroscopic and chromatographic techniques were used to analyze warp-knitted materials.
Experimental
Materials
Commercially available Polyamide/elastane warp-knitted fabrics were provided by Pisa Textile (Istanbul, Turkey). The fabric area density (GSM) is 180 g ⁄m2 and the polyamide yarn count was calculated as 200 den. Fabric fiber composition is 80% polyamide and %20 elastane. Wale density was recorded at 27 cm−1 and course density at 40 cm−1. The thickness of the fabrics was tested at 0.65 mm. Madder and gall oak were provided by Natural Dye Raw Materials Company (Turkey). Coloring compounds, reference standards, and chemicals were provided by DATU Cultural Heritage Preservation and Natural Dyes Laboratory in Istanbul, Turkey. Non-ionic detergent (SDC Enterprıses lmt.) was provided by Labor Teknik (Turkey). Alum [KAl(SO4)2.12 H2O], hydrochloric acid (HCl), sodium carbonate (Na2CO3), methanol (CH3OH), acetonitrile (CH3CN), and trifluoroacetic acid (TFA) were provided from Merck (Germany).
Extraction
The dried and ground madder roots and gall oak dyes were transferred to separate beakers for extraction. Tap water was then added. The mixture was slowly heated to 100°C and extracted for 1 hour in a 10:1 dye bath. Finally, the temperature of the solution was decreased to 25°C, and it was filtered with 80 mesh. The dye extracts were used for dyeing.
Dyeing procedure
The dyeing was done according to different ratios of gall oak and madder. Meta-mordant dyeing methods (mordanting and dyeing together) were used for fabrics coded between F3 and F11, and direct dyeing was used for fabrics coded F2 (). Ten percent alum was used as a mordant in all meta-mordant dyeing processes. The dyeing processes were carried out for 60 minutes in a 10:1 dye bath at 100°C. Dyeing pH was between 7–8 for the madder and 5–6 for the gall oak. The dye baths were cooled to 40°C, the dyed fabrics were rinsed and washed with nonionic soap at 70°C. All dyeing procedures are given in . The SZ-PT Olympus industrial (Tokyo, Japan) optical stereo microscope that can fully integrate with digital cameras and image software (OLYMPUS Stream™ software) was used for microscope shades at a magnification of × 40. Microscope shades and real shades (according to e-paint.co.uk) are given in .
Table 1. Dyeing procedure, pilling tests, abrasion tests, real and microscope shades.
Testing and characterization
Pilling and abrasion
For physical testing and analysis, raw and dyed fabrics were conditioned at the standard testing temperature of 20 ± 2°C with a humidity of 65 ± 2% for 24 hours. The pilling and abrasion resistance tests were carried out by Martindale Testers (James H. Heal & Co. Ltd., Halifax, England). Pilling grades (1 is poor and 5 is excellent) were evaluated according to the EMPA Standard (Eidgenössische Materialprüfungs- und Forschungsanstalt). Pilling and abrasion resistance tests were applied according to ISO 12,945–2 and BS EN ISO 12,947–2, respectively. The pilling and abrasion tests are shown in .
Contact angles
The contact angles were measured using a contact angle tester (KSV Cam101, KSV Instruments, Finland). Contact geometry was obtained by measuring the deionized water contact angle using a contact angle meter. Initially, the fabric was placed on the sample stage. Then all samples were analyzed using contact angle measurements with deionized water droplets on the surface of the samples. The contact angle was measured after 10 seconds and repeated at least three times for each group of samples. The software (KSV Cam101 Software) recorded and examined the imagery. The software (KSV Cam101 Software) recorded and examined the imagery. Water contact angles and the SD of contact angles (σ) are given in .
Fastness properties
The washing, perspiration, rubbing, and light fastnesses of dyed fabrics were determined according to ISO 105: C06 (A1S), ISO 105: E04, ISO 105: X12, and ISO 105: B02 standards, respectively. The ISO 105:C06 A1S fastness test was carried out at 40°C for 30 minutes, containing 10 steel balls. The dyed fabrics were exposed to light for 24 hours from a xenon arc lamp (250 W). The results of washing, perspiration, rubbing, and light fastnesses of dyed fabrics are given in .
Table 2. The test results of washing, light, rubbing, and perspiration fastness of the dyed fabrics.
Color measurement
The reflectance values of dyed samples were measured using a Datacolor Spectraflash SF 600+ (Datacolor International, USA) instrument with specular-included mode and an LAV 30 mm viewing aperture. The CIEL*a*b* values were calculated using illuminant D65 and 10° standard observer values. Color differences (ΔE*) and color strength (K/S) were given in . The L* axis represents the lightness of the color (L* is 0 for black and L* is 100 for white), a* represents the green-red axis (a* negative: green, a* positive: red), and b* represents the blue and yellow axis (b* negative: blue, b* positive: yellow). From the reflectance values (R) in the visible spectrum (400–700 nm) at the maximum absorption wavelength (λmax) for each dye, the corresponding color strength (K/S) values of the samples were calculated by using the Kubelka – Munk equation as shown below (Deveoglu et al. Citation2021; Deveoğlu, Torgan, and Karadağ Citation2012)
Equation 1:
The color difference is expressed as ΔE* and is calculated by Equation 2:
FTIR analysis
The FT-IR spectra were recorded in the range of 650–4000 cm−1 on a Spectrometer Perkin Elmer Spectrum 100 series (USA) with universal ATR accessory sampling. FTIR analyses are given in .
HPLC analysis
Chromatographic measurements of dyed fabrics were carried out using an Agilent 1200 series system (Agilent Technologies, Hewlett-Packard, Germany), including the G1322A Degasser, G1311A Quat Pump, G1329A Autosampler, G13166 TCC, and G1315D Diode Array Detector. A Nova-Pak C18 analytical column (3.9 × 150 mm, 4 µm, part number WAT086344; Waters, Ireland) was used, which was protected by a guard column filled with the same material. Analytical and guard columns were retained at 30°C. The chromatogram and spectra of dyed samples are given in .
SEM- EDX analysis
A scanning electron microscope (SEM) with a TESCAN model VEGA3 (TESCAN, Brno, Czech Republic) equipped with a backscattered electron (BSE) detector, a secondary electron (SE) detector, and an energy dispersive X-ray (EDX) spectrometer was used for morphological and elemental analysis of the colored samples. A thermionic emission tungsten heated lamp was also used as an electron source, and a Bruker model XFlash 410-M EDX detector (ESPRIT Compact Esprit 1.9 software) was used for elemental analysis. With the EDX detector used, semi-quantitative results of elemental analyses were obtained as atomic and weight percentages. Qualitative microanalysis was carried out using the ZAF method, which allows the simultaneous determination of the concentration of each element in a multi-element material and is based on the correction of the matrix effect. This method provides X-ray intensity correction, absorption correction, and fluorescence correction due to the composition and depth of electron penetration and the atomic number effect of each element by secondary fluorescence, respectively (Oraltay and Karadag Citation2020). The results of the SEM-EDX analyses and images are shown in .
Results and discussion
Method of the dyeing warp knitted fabrics
Polyamide/elastane warp knitted fabrics were separately dyed with gall oak and madder. Natural dyes are better for the environment and have specific advantages. The dyeing process also adhered to the Natural Organic Dye Standard (NODS) (Karadag Citation2023). The reintroduction of natural dyes in the textile industry has become even more crucial as a consequence of growing environmental awareness and sensitivity. Along with forming a chemical bond with the natural coloring compounds, mordants can be bonded to the fiber. There is no available data on the toxicity of the potassium aluminum sulfate (alum) [KAl(SO₄)₂.12.H₂O] metal salt used in this study. In addition, this mordant substance, which is used in historical dyeing recipes, has no limits or prohibitions according to NODS and GOTS standards. Meta-mordant dyeing methods (mordanting and dyeing together) were used to dye the warp knitted fabrics. This dyeing method involves simultaneously adding the mordant material and coloring compounds to the dying bath. The method used in this research saves time, labor, and energy. The dyeing processes were carried out for 60 minutes in a 10:1 dye bath at 100°C. Therefore, a high color yield was created at a low dye bath ratio. This means that there was less water consumption, less energy consumption, and much less wastewater consumption (Karadag Citation2022b). Mordant ratios were kept constant at 10% in the dyeings, while the amounts of dye plants were used in different ratios. The dyeing procedure is given in .
Physical testing (pilling and abrasion)
The pilling formation over the surface of the warp-knitted fabrics was not observed and evaluated after a different number of rubs (125, 500, 1000, 2000, 5000, and 7000). In the examined samples of pilling tests, the increase in the number of rubs from 125 up to 7000 did not change a decrease in the grade of pilling, and the fabric pilling is evaluated with a grade of 5 for all fabrics as the best score. Pilling test results for warp-knitted fabrics are given in . To evaluate the resistance of the war-knitted samples to abrasion, the fabrics were subjected to 675,000 rubs, and yarn breakdown did not occur. Abrasion tests were performed for all of the fabrics. Sportswear resistance to abrasion and pilling is a common and fundamentally important issue. The physical and mechanical characteristics of the fabrics may be impacted by the dyeing procedure and different finishing techniques used after and before dyeing (Bekiroğlu, Özcan, and Altay Citation2022). As a result, physical testing was done to determine how the dyeing processes affected the quality-performance attributes of the warp-knitted polyamide fabrics. The effect on the physical properties of the fabrics after dyeing was examined, and it was observed that the structure of the warp knitted fabrics examined did not change significantly after the dyeing application. Polyamide filament yarns have very good abrasion resistance. It has been evaluated that the resistance of fabrics to abrasion is very good on the textile surfaces formed by the use of polyamide yarn and structurally by the warp knitting technique. In addition, it was clarified that the results of the abrasion test on the fabrics after the dyeing process were good and that there was no negative effect of dyeing. The images of fabrics taken before and after the abrasion test are given in .
Contact angle measurement
The contact angle (°) was measured for all fabrics, and distilled water was utilized as the test liquid. The geometry of solid-liquid contact is defined by the contact angle formed by water molecules and the fabric surface. Water contact angles measured indicated dye concentration dependency. The initial value of the undyed fabric’s contact angle was approximately 90°, indicating that it was hydrophobic. As the dye concentration increased, the water contact angle continued to drop, reaching 30° for coded sample F6. Al ions-tannin-fibroin complexes with the codes between F2-F6 had contact angles ranging from 46.45° to 30.80°. Al-alizarin-fibroin complexes, which were coded between F7 and F11, also had contact angles that ranged from 51° to 61°. Alum chemically forms a ternary complex with polyamide’s functional groups on one side and the dye on the other. Such a strong coordination tendency improves the connection between the fiber and the dye, resulting in lower water contact angles. In this case, it can be seen that the formation of the fiber-metal-dye complex causes the fabric’s contact angle to drop, giving the fabric a hydrophilic character. Water contact angles and the SD of contact angles (σ) are given in .
Colorfastness of dyed fabrics
Results demonstrate that wash fastness in all fabrics 5 is outstanding in grade and satisfies industrial standards. The rub fastness ratings range from 3 to 4 for fabrics between F2-F6 and 4–5 for fabrics between F7-F11. Light fastness values are in the range of 3 and 5 and they are moderate to good, which is satisfying for dyeing from natural dye in textiles. The highest light fastness was found to be 4–5 on the blue scale rating for fabrics between F7-F11. Overall, the findings of the tests for acidic and alkaline perspiration fastness were excellent. The findings of the acidic and alkaline perspiration tests were outstanding, with values of 5 between samples F7 and F11 and 4–5 between samples F2 and F6. When the madder and gall oak were mixed (between F7-F11 coded dyed fabrics), all fastness values were excellent. The rates of the fastness values increased along with the gall oak/alum ratio between coded F3-F6 dyed fabrics. The light fastness of the direct dyeing value (coded dyed fabric F2) was a little low because alum mordant was not used. Additionally, polyamide-made fabrics performed far better in fastness tests than those produced from raw materials like cotton, silk, and wool (Güzel and Karadag Citation2021). The results of washing, perspiration, rubbing, and light fastnesses of dyed fabrics are given in .
Color strength and color coordinates
Color differences (ΔE*) and color strength (K/S) values obtained for the dyed samples are given in . ΔE* is the CIEL*a*b* color difference between batch and standard. The color difference (ΔE*) values of the dyed material were found to range between 15.70 and 53.69 when the sample of the undyed fabric that had been F1-coded as a standard was used. The highest color difference value is 53.69 for sample F10 coded (% 20 madder % 10 gall oak). The effects of dye concentrations on color strength can be observed from the K/S data, as the F2-coded sample displayed a lower dye uptake than others. The highest K/S values for the dyed warp-knitted samples at the maximum absorption wavelength were 16.52 for sample F6 coded (% 40 gall oak). The color values normally vary based on the dyeing recipe. The coloristic properties of the dyed warp knitted fabrics were improved because of the high concentration of madder and gall oak in the dye bath, which used alum by creating complexes of Al-alizarin-fibroin and Al-tannin-fibroin (Torgan, Ozer, and Karadag Citation2015).
FTIR characterization
The binding of fiber-mordant and dyes was validated by comparing the FTIR-ATR spectra of undyed and dyed fabrics. The significant characteristic bands of the polyamide were observed at 3292 cm−1 due to the stretching of hydrogen bonded to the N – H and the N – H bending. Further distinct peaks for polyamide may be found at 2927 cm−1 and 2856 cm−1 which are CH2 symmetric and asymmetric stretching associated at 720 cm−1 with the vibration of 4 or more – CH2 groups in the polymer chain. The spectra revealed that the absorption bands at 1632 and 1539 cm−1 (amide I and amide II, respectively) are related to the nature of polyamide fibers. Also, the band at 1120 cm−1 revealed the bending of the CH2 group (Metwally et al. Citation2023). It has been assumed that the metal ion and dye form bonds with the functional groups of polyamide polymer due to the higher absorption and fixation of the dyestuff by the complex between Al ions and polyamide provided the IR spectra may not reveal any evidence of the interaction between the dye and polyamide fiber. The results of the analysis performed by FTIR are given in .
HPLC and SEM-EDX results
HPLC is one of the most commonly utilized instruments for the identification of coloring compounds. Coloring compounds were analyzed by HPLC-DAD in the colored samples. Gallic acid and ellagic acid were identified in the gall oak dyed samples (F2 and F3). Alizarin, purpurin, gallic acid, and ellagic acid were identified in the gall oak and madder samples (F7-F8). The peak heights (amounts) of alizarin and purpurin increased as the amount of madder dye in the staining increased. HPLC analyses were performed according to published procedures (Buyukakinci, Guzel, and Karadag Citation2021; Deveoglu et al. Citation2012; Papliaka et al. Citation2017). The chromatogram and spectra of the dyed samples are shown in .
SEM-EDX was used to determine if the mordant was qualitatively bound to the fiber. It was found that the mordant aluminum was bound to the fiber. The effect of the mordant and dyes on the morphological structure of the fiber was also investigated. Al ions formed complexes (Al gallic acid, Al ellagic acid, Al alizarin, Al purpurin, and Al munjistin) with the coloring compounds of the dyes [madder (alizarin, purpurin, munjistin), gall oak (gallic acid and ellagic acid)]. It was observed that the mordant and coloring compounds did not cause any damage to the fiber structure during the dyeing processes. The SEM images and qualitative elemental analysis of the dyed fabrics are shown in .
Conclusion
The study revealed that using high-strength warp-knitting textiles with high added value in the production of functional sportswear that would enhance comfort will improve the quality of garments dyed with natural dyes. Warp knitted (polyamide/elastane) fabrics were colored with madder and gall oak. These natural dyes are substantive for polyamide fabrics, and the use of a mordant while applying them strengthens the color. As the concentration of dye plants increased, the color strength improved. When the dyes are mixed, it appears that the best color value is obtained in a ratio of 1:2 (gall oak: madder) in sample F10. The coloring compounds (alizarin, purpurin, munjistin, gallic acid, and ellagic acid) were identified with the HPLC-DAD in the dyed fabrics. All fabrics’ water contact angles were measured, and physical testing of both dyed and raw fabrics was examined and contrasted with how resistant they were to abrasion and pilling. Abrasion resistance was excellent, and all fabrics received a perfect rating of five in the pilling test results. Undyed polyamide/elastane warp knitted fabrics for F1 coded had an average contact angle of 90.97º, but the water droplet was absorbed into the fabric after dyeing, so especially dyed fabric for F5 coded had an average contact angle of 30.80º. Test results indicated that polyamide warp-knitted fabrics had outstanding resistance to abrasion and pilling. Yarns made of polyamide provide excellent abrasion resistance. In reality, it has been determined that the warp knitting technique and the use of polyamide yarn generate very good textile surfaces with excellent abrasion resistance. All of the natural dye combinations used in polyamide dyeing showed excellent color values and fastness (washing, light, and rubbing) testing. The dyeing procedure also adhered to the Natural Organic Dye Standard (NODS). Hazardous substances, heavy metals, pesticides, poisonous and carcinogenic colors, and artificial dyes are all excluded by the NODS. Therefore, by manufacturing materials that adhere to the NODS and simultaneously promoting sustainability and environmentally friendly dyeing, companies and the textile industry may do more. The quality of clothing dyed with natural dyes will rise when warp-knitting high-strength fabrics with high added value are produced utilizing cutting-edge technology to create functional sportswear that maximizes athletes’ comfort and performance.
Highlights
In recent years, the use of natural dyes in sportswear has been demanded by many brands.
Natural dyes have an important place in sportswear because they contain natural antifungal and anti-microbial properties.
Meta mordant dyeing [extract and dyeing together (synchronous dyeing)] and direct dyeing methods were used.
The dyed polyamide fabrics exhibited excellent fastness properties.
Coloring high-value warp knitted high-strength textiles with natural dyes will improve the quality of the clothing in the construction of functional sports gear that maximizes the comfort and performance of athletes.
They have the characteristics of sustainable and industrial production in te sport wears.
wjnf_a_2378854_sm4042.docx
Download MS Word (820.3 KB)wjnf_a_2378854_sm4041.docx
Download MS Word (12.5 KB)wjnf_a_2378854_sm4043.docx
Download MS Word (13.6 KB)wjnf_a_2378854_sm4040.docx
Download MS Word (12.2 KB)Disclosure statement
No potential conflict of interest was reported by the author(s).
References
- Abasi, S., T. Nasrollahi, M. Aghajani, and M. A. Tehran. 2013. “Construction of Drag Force Measuring System to Characterize the Hydrodynamics Properties of Swimsuit Fabrics.” Journal of Industrial Textiles 43 (2): 264–18. https://doi.org/10.1177/1528083712452901.
- Abd El-Hady, R.-B., and R. Abd El-Baky. 2015. “Performance Characteristics of Warp Knitted Lining Fabrics Used for Sportswear.” Life Science Journal 12 (3): 98–104.
- Abdulkadir, P., and R. Karadag. 2022. “Applications of Laser Radiation on Cotton Fabrics Dyed Gall Oak (Quercus Infectoria Olivier).” Tekstil ve Mühendis 29 (127): 161–167. https://doi.org/10.7216/1300759920222912706.
- Adeel, S., M. Azeem, N. Habib, M. Hussaan, A. Kiran, A. Haji, and W. Haddar. 2023. “Sustainable Application of Microwave Assisted Extracted Tea Based Tannin Natural Dye for Chemical and Bio-Mordanted Wool Fabric.” Journal of Natural Fibers 20 (1): 2136322. https://doi.org/10.1080/15440478.2022.2136322.
- Agrawal, A., and S. Chopra. 2020. “Sustainable Dyeing of Selected Natural and Synthetic Fabrics Using Waste Teak Leaves (Tectona Grandis L.).” Research Journal of Textile and Apparel 24 (4): 357–374. https://doi.org/10.1108/RJTA-05-2020-0046.
- Ahirwar, M., and B. Behera. 2022. “A Mathematical Model for Objective Hand Evaluation of Automotive Seat Fabrics.” Journal of Industrial Textiles 51 (1_suppl): 458S–478S. https://doi.org/10.1177/1528083720949446.
- Ahmad, W., F. Zeenat, A. Hasan, A. Abdullah, A. Nargis, and T. Tarannum. 2011. “Mazu (Quercus Infectoria, Oliv)-An Overview.” Indian Journal of Unani Medicine 4 (1): 17–22.
- Bekiroğlu, E., G. Özcan, and P. Altay. 2022. “Improvement in Pilling Property of Viscose/PET Blended Knitted Fabric After Garment Dyeing.” The Journal of the Textile Institute 113 (6): 971–982. https://doi.org/10.1080/00405000.2021.1912953.
- Boschmeier, E., V.-M. Archodoulaki, A. Schwaighofer, B. Lendl, and A. Bartl. 2023. “A Novel Quantification Tool for Elastane in Textiles Using Thermal Treatment.” Polymer Testing 118:107920. https://doi.org/10.1016/j.polymertesting.2022.107920.
- Buyukakinci, Y. B., E. T. Guzel, and R. Karadag. 2021. “Organic Cotton Fabric Dyed with dyer’s Oak and Barberry Dye by Microwave Irradiation and Conventional Methods.” Industria Textila 72 (1): 30–38. https://doi.org/10.35530/IT.072.01.1755.
- Cherradi, Y., H. Kebir, A. Boukhriss, H. Ennamiri, and M. Benyoucef. 2022. “Mechanical Behaviour of 3D Monofilament Knitted Fabrics: Modeling, Simulation and Validation.” Journal of Industrial Textiles: 15280837221091578. https://doi.org/10.1177/15280837221091578.
- Cong, H., X. Li, A. Zhang, and Z. Gao. 2014. “Design and Simulation of Jacquard Warp-Knitted Towel Fabric.” Fibres & Textiles in Eastern 5 (107): 54–58.
- Cong, H., B. Zhao, H. Han, and X. Yu. 2022. “Investigation of the Properties of Knitted Woolen Fabrics Treated with Oxygen Low-Temperature Plasma for Sportswear Applications.” Textile Research Journal 92 (1–2): 210–218. https://doi.org/10.1177/00405175211030632.
- Deveoglu, O., R. Karadag, A. Spinella, and E. T. Guzel. 2021. “Examination of Dyeing Properties on Silk of Some Flavonoids by Spectroscopic Techniques.” Journal of Natural Fibers 18 (2): 238–249. https://doi.org/10.1080/15440478.2019.1616650.
- Deveoglu, O., B. Y. Sahinbaskan, E. Torgan, and R. Karadag. 2012. “Investigation on Colour, Fastness Properties and HPLC-DAD Analysis of Silk Fibres Dyed with Rubia Tinctorium L. and Quercus Ithaburensis Decaisne.” Coloration Technology 128 (5): 364–370. https://doi.org/10.1111/j.1478-4408.2012.00389.x.
- Deveoğlu, O., E. Torgan, and R. Karadağ. 2012. “High-Performance Liquid Chromatography of Some Natural Dyes: Analysis of Plant Extracts and Dyed Textiles.” Coloration Technology 128 (2): 133–138. https://doi.org/10.1111/j.1478-4408.2012.00358.x.
- Eyupoglu, C., S. Eyupoglu, N. Merdan, and Z. Omerogullari Basyigit. 2023. “Natural Dyeing of Air Plasma-Treated Wool Fabric with Rubia Tinctorum L. and Prediction of Dyeing Properties Using an Artificial Neural Network.” Coloration Technology 140 (1): 91–102. https://doi.org/10.1111/cote.12700.
- Fang, J., C. Meng, Y. Wang, Y. Yang, L. Han, S. Wang, and J. Min. 2023. “Eco-Dyeing and Functional Finishing of Cotton Fabric by Natural Dye Derived from Lotus Seedpod Waste with Chitosan-Assistance.” Fibers and Polymers 24 (4): 1367–1377. https://doi.org/10.1007/s12221-023-00158-z.
- Güzel, E. T., and R. Karadag. 2021. “Sustainability of Organic Cotton Fabric Dyeing with a Natural Dye (Gallnut) and Analysis by Multi-Technique Approach.” Journal of Natural Fibers 18 (8): 1107–1118. https://doi.org/10.1080/15440478.2019.1687064.
- Haji, A., F. Shahmoradi Ghaheh, and L. Indrie. 2023. “Pomegranate Fallen Leaves As a Source of Natural Dye for Mordant-Free Dyeing of Wool.” Coloration Technology 139 (2): 165–170. https://doi.org/10.1111/cote.12651.
- Haji, A., F. Shahmoradi Ghaheh, and L. Mohammadi. 2022. “Dyeing of Polyamide 6 Fabric with New Bio-Colorant and Bio-Mordants.” Environmental Science and Pollution Research 30 (13): 1–16. https://doi.org/10.1007/s11356-022-24862-0.
- Hoque, M. S., M. I. Shahid, A. A. Parvez, M. J. Hossain, and S. M. Sheen. 2022. “Knitted Denim Fabrics: Fabrication Process and Fibrous Influence on Several Properties of the Fabric.” AATCC Journal of Research 9 (6): 286–300. https://doi.org/10.1177/24723444221119845.
- Janković, V., D. Marković, J. Nikodinovic-Runic, M. Radetić, and T. Ilic-Tomic. 2023. “Eco-Friendly Dyeing of Polyamide and Polyamide-Elastane Knits with Living Bacterial Cultures of Two Streptomyces sp. Strains.” World Journal of Microbiology & Biotechnology 39 (1): 32. https://doi.org/10.1007/s11274-022-03473-4.
- Karadag, R. 2022a. “Cotton Dyeing with Cochineal by Just in Time Extraction, Mordanting, Dyeing, and Fixing Method in the Textile Industry.” Journal of Natural Fibers 20 (1): 1–11. https://doi.org/10.1080/15440478.2022.2108184.
- Karadag, R. 2022b. “Sustainable and Mass Production of Cotton Dyeing with Natural Dye (Weld) in the Textile Industry.” Journal of Natural Fibers 19 (15): 10935–10945. https://doi.org/10.1080/15440478.2021.2002781.
- Karadag, R. 2023. “Establishing a New International Standard for Natural Dyed Textile Goods [Natural Organic Dye Standard (NODS)].” Journal of Natural Fibers 20 (1): 2162187. https://doi.org/10.1080/15440478.2022.2162187.
- Kim, H. S., I. Y. Choi, and H.-S. Shin. 2020. “Analysis of Trends in Diving Suits for Development of Technical Diving Suits-With Focus on Wet and Semi-Dry Types.” Journal of the Korea Fashion & Costume Design Association 22 (3): 33–47. https://doi.org/10.30751/kfcda.2020.22.3.33.
- Kursun, S., and G. Ozcan. 2010. “An Investigation of UV Protection of Swimwear Fabrics.” Textile Research Journal 80 (17): 1811–1818. https://doi.org/10.1177/0040517510369401.
- Kyosev, Y. 2019. Warp Knitted Fabrics Construction. CRC Press.
- Liu, Y., H. Hua, and B. Li. 2022. “Exploration and Design of Knitted Composites for Architectural Application: The MeiTing Project.” Frontiers of Architectural Research 11 (4): 594–608. https://doi.org/10.1016/j.foar.2022.01.004.
- Mariem, B., M. Wissal, K. Faouzi, J. Boubaker, and D. Adolphe. 2020. “A Study of the Consumption of Sewing Threads for women’s Underwear: Bras and Panties.” AUTEX Research Journal 20 (3): 299–311. https://doi.org/10.2478/aut-2019-0032.
- Maulik, S. R., C. Debnath, and P. Pandit. 2022. “Sustainable Dyeing and Printing of Knitted Fabric with Natural Dyes.” In Advanced Knitting Technology, 537–565. Woodhead Publishing. https://doi.org/10.1016/B978-0-323-85534-1.00008-8.
- Metwally, B. S., S. A. Rashed, M. El-Sheikh, and A. S. Hamouda. 2023. “Dyeing of Recycled Electrospun Polyamide 6 Nanofibers: Implications of Dye Particle Size.” Fibers and Polymers 24 (5): 1681–1693. https://doi.org/10.1007/s12221-023-00165-0.
- Mishra, R. 2022. “Assessment of Comfort and Quality of Knitted Apparels.” In Advanced Knitting Technology, 567–621. Elsevier. https://doi.org/10.1016/B978-0-323-85534-1.00013-1.
- Oraltay, R., and R. Karadag. 2020. “Surface Investigation of Metal Threads and Solid Metals of Ottoman Textiles in the Topkapi Palace Museum.” Studies in Conservation 65 (1): 59–64. https://doi.org/10.1080/00393630.2019.1647388.
- Ozdemir, M. B., and R. Karadag. 2023a. “Anatolian Acorn Oak’s Economic Potential in the Application to the Textile and Leather Industries.” Textile & Leather Review 6:320–332. https://doi.org/10.31881/TLR.2023.044.
- Ozdemir, M. B., and R. Karadag. 2023b. “Madder (Rubia Tinctorum L.) As an Economic Factor Under Sustainability Goals in the Textile Dyeing.” Journal of Natural Fibers 20 (1): 2128968. https://doi.org/10.1080/15440478.2022.2128968.
- Papliaka, Z. E., A. Konstanta, I. Karapanagiotis, R. Karadag, A. A. Akyol, D. Mantzouris, and P. Tsiamyrtzis. 2017. “FTIR Imaging and HPLC Reveal Ancient Painting and Dyeing Techniques of Molluskan Purple.” Archaeological and Anthropological Sciences 9 (2): 197–208. https://doi.org/10.1007/s12520-015-0270-3.
- Patil, H., S. Mudaliar, and A. Athalye. 2023. “Ultrasound-Assisted Enzymatic Scouring of Jute Optimised by Response Surface Methodology and Its Natural Dyeing.” Coloration Technology 139 (1): 97–108. https://doi.org/10.1111/cote.12638.
- Rahman, M. M., M. Kim, K. Youm, S. Kumar, J. Koh, and K. H. Hong. 2023. “Sustainable One-Bath Natural Dyeing of Cotton Fabric Using Turmeric Root Extract and Chitosan Biomordant.” Journal of Cleaner Production 382:135303. https://doi.org/10.1016/j.jclepro.2022.135303.
- Rehman, F. U., S. Adeel, W. Haddar, R. Bibi, M. Azeem, R. Mia, and B. Ahmed. 2022. “Microwave-Assisted Exploration of Yellow Natural Dyes for Nylon Fabric.” Sustainability 14 (9): 5599. https://doi.org/10.3390/su14095599.
- Safapour, S., M. Mazhar, and S. Abedinpour. 2023. “Broadening Color Shade Range of Rubia Tinctorum L. Natural Colorants on Wool Fibers via Combination of Metal Mordants: Color Characteristics and Fastness Studies.” Journal of Natural Fibers 20 (1): 2157923. https://doi.org/10.1080/15440478.2022.2157923.
- Schmidt-Przewozna, K., and E. Rój. 2023. “Green Sustainable Textile Supercritical Dyeing Process Using CO2 Madder (Rubia T Inctorum L.) Extract.” Journal of Natural Fibers 20 (2): 2277836. https://doi.org/10.1080/15440478.2023.2277836.
- Sk, S., R. Mia, M. Haque, and A. M. Shamim. 2021. “Review on Extraction and Application of Natural Dyes.” Textile & Leather Review 4 (4): 218–233.
- Spencer, D. J. 2001. “A Comprehensive Handbook and Practical Guide.” In Knitting Technology, 3rd ed. Woodhead Publishing Ltd., and Technomic Publishing Company Inc.
- Tanasă, F., M. Nechifor, M.-E. Ignat, and C.-A. Teacă. 2022. “Geotextiles—A Versatile Tool for Environmental Sensitive Applications in Geotechnical Engineering.” Textiles 2 (2): 189–208. https://doi.org/10.3390/textiles2020011.
- Torgan, E., L. M. Ozer, and R. Karadag. 2015. “Colorimetric and Fastness Studies and Analysis by Reversed-Phase High-Performance Liquid Chromatography with Diode-Array Detection of the Dyeing of Silk Fabric with Natural Dye Helichrysum Arenarium.” Coloration Technology 131 (3): 200–205. https://doi.org/10.1111/cote.12141.
- Ullah, H. M. K., J. Lejeune, A. Cayla, M. Monceaux, C. Campagne, and É. Devaux. 2022. “A Review of Noteworthy/Major Innovations in Wearable Clothing for Thermal and Moisture Management from Material to Fabric Structure.” Textile Research Journal 92 (17–18): 3351–3386. https://doi.org/10.1177/00405175211027799.
- Varan, N. Y., and P. Altay. 2022. “Antibacterial Activity and Thermophysiological Comfort Enhancement by Calcium Chloride Solutions of Highly Elastane Polyamide 66 Fabrics.” Fibers and Polymers 23 (4): 967–976. https://doi.org/10.1007/s12221-022-4274-1.
- Veit, D. 2023. “Elastane.” In Fibers: History, Production, Properties, Market, 749–759. Switzerland AG: Springer Nature.
- Venkatraman, P. D. 2022. “Application of Knitted Fabrics in Medical Textiles.” In Advanced Knitting Technology, 471–502. Elsevier. https://doi.org/10.1016/B978-0-323-85534-1.00004-0.
- Wang, M., Z. Pan, J. Yu, R. Xu, X. Du, and Z. Wu. 2022. “Triaxial Braided Sandwich Composite Guide Bar Potentially Used in High-Speed Warp Knitting Machine.” Journal of Industrial Textiles 51 (5_suppl): 7455S–7479S. https://doi.org/10.1177/15280837221091932.
- Xie, Z. 2022. Study of the Viability for Production of Conductive Nonwoven Reinforcement from Technical Textile Waste. Master in Textile Design and Technology. Universitat Politècnica de Catalunya.
- Yıldız Varan, N., Y. Çaydamlı, and P. Altay. 2023. “Effect of Hydrophilic Procedures on Carboxyl Content and Antimicrobial Activity of Silver-Treated Nylon 6, 6 Fabrics.” Tenside Surfactants Detergents 60 (1): 54–63. https://doi.org/10.1515/tsd-2022-2469.