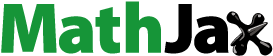
Abstract
Biocomposites (BCs) can be used as substitutes for unsustainable polymers in 3D printing, but their safety demands additional investigation as biological fillers may produce altered emissions during thermal processing. Commercial filament extruders can be used to produce custom feedstocks, but they are another source of airborne contaminants and demand further research. These knowledge gaps are targeted in this study. Volatile organic compound (VOC), carbonyl compound, ultrafine particle (UFP), and fine (PM2.5) and coarse (PM10) particle air concentrations were measured in this study as a filament extruder and a 3D printer were operated under an office environment using one PLA and four PLA-based BC feedstocks. Estimates of emission rates (ERs) for total VOCs (TVOC) and UFPs were also calculated. VOCs were analyzed with a GC-MS system, carbonyls were analyzed with an LC-MS/MS system, whereas real-time particle concentrations were monitored with continuously operating instruments. VOC concentrations were low throughout the experiment; TVOC ranged between 34–63 µg/m3 during filament extrusion and 41–56 µg/m3 during 3D printing, which represent calculated TVOC ERs of 2.6‒3.6 × 102 and 2.9‒3.6 × 102 µg/min. Corresponding cumulative carbonyls ranged between 60–91 and 190–253 µg/m3. Lactide and miscellaneous acids and alcohols were the dominant VOCs, while acetone, 2-butanone, and formaldehyde were the dominant carbonyls. Terpenes contributed for ca. 20–40% of TVOC during BC processing. The average UFP levels produced by the filament extruder were 0.85 × 102–1.05 × 103 #/cm3, while the 3D printer generated 6.05 × 102–2.09 × 103 #/cm3 particle levels. Corresponding particle ERs were 5.3 × 108–6.6 × 109 and 3.8 × 109–1.3 × 1010 #/min. PM2.5 and PM10 particles were produced in the following average quantities; PM2.5 levels ranged between 0.2–2.2 µg/m3, while PM10 levels were between 5–20 µg/m3 for all materials. The main difference between the pure PLA and BC feedstock emissions was terpenes, present during all BC extrusion processes. BCs are similar emission sources as pure plastics based on our findings, and a filament extruder produces contaminants at comparable or slightly lower levels in comparison to 3D printers.
Introduction
The additive manufacturing (AM) industry is an expanding consumer of energy and plastics which contribute to some of the most important environmental issues of recent times. Sustainable polymers derived from renewable sources and polymer composites reinforced with natural fibers referred to as biocomposites (BCs) gain popularity as environmentally friendly alternatives for petroleum-based pure polymers. The advantages of BCs include lightweight, reduced production costs, environmental friendliness, improved dimensional stability and stiffness (Ford and Despeisse Citation2016; Peng et al. Citation2018; Calí et al. Citation2020; Calvino et al. Citation2020), and even increased processability without affecting processing parameters (Mazzanti et al. Citation2019; Vaidya et al. Citation2019). The AM industry can play a role in energy conservation through a shortened supply chain as localized production and the use of sustainable feedstocks become increasingly commonplace. One way to support sustainability is the wider use of BCs which reduces the demand for unsustainable polymers (Ford and Despeisse Citation2016; Peng et al. Citation2018; Calí et al. Citation2020; Calvino et al. Citation2020).
Commercially available three-dimensional (3D) printer filament extruders have been introduced to consumer markets over the past few years. These extruders can produce custom 3D printer feedstocks from thermoplastic polymers, and additives or fillers, e.g., wood particles, if desired, but they are another source for polymer thermal degradation products. The emissions from such machines have been documented only once so far by Byrley et al. (Citation2020). Their findings indicate the emissions are similar in composition when compared to those produced by material extrusion (ME) 3D printers, but this was not confirmed by using the produced filaments in a 3D printer. Principally, a thermal extruder can produce a wide range of emissions, mainly chemical species including volatile organic compounds (VOCs), ultrafine particles (UFPs), and to a smaller extent, fine (PM2.5) and coarse (PM10) particles (Kim et al. Citation2015a, Azimi et al. Citation2016; Stabile et al. Citation2017; Steinle Citation2016; Yi et al. Citation2016; Floyd et al. Citation2017; Kwon et al. Citation2017; Mendes et al. Citation2017; Rao et al. Citation2017; Stefaniak et al. Citation2017, Citation2021; Vance et al. Citation2017; Byrley et al. Citation2019, Citation2020; Du Preez et al. Citation2018; Davis et al. Citation2019; Väisänen et al. Citation2019, Citation2021a; Jeon et al. Citation2020). These emissions can induce adverse health impacts in humans after exposure, including respiratory symptoms, depression of the central nervous system, irritation, inflammation or sensitization, and they may exacerbate preexisting health conditions, e.g., asthma (WHO Citation1995, Citation2006; Van Kampen et al. Citation2000; Pope and Dockery Citation2006; Wolkoff et al. Citation2006; Mossman et al. Citation2007; Sarigiannis et al. Citation2011; Weschler Citation2011; Shahnaz et al. Citation2012; Klaasen et al. Citation2013; Rohr Citation2013; House et al. Citation2017; Chan et al. Citation2018).
Additionally, wooden products and BCs have been documented to emit distinctive chemicals that include various terpenes (Roffael Citation2006; Kim et al. Citation2006; Höllbacher et al. Citation2015; Pohleven et al. Citation2019). BCs can therefore produce altered emissions in comparison to pure plastics when used as filament extruder or 3D printer feedstocks. To be noted, a wide range of VOCs and certain terpenes are classified as irritants or sensitizers (Kasanen et al. Citation1999; Van Kampen et al. Citation2000; Kim et al. Citation2013; Wolkoff et al. Citation2006; Mossman et al. Citation2007; Shahnaz et al. Citation2012; WHO 2021), while terpenes are identified as precursors for secondary reactive chemical species and UFPs in the air phase in the presence of ozone. (Sarwar et al. Citation2004; Rohr Citation2013; Kim et al. Citation2015b; Wolkoff Citation2020). Indoor terpenes can potentially impair indoor air quality further on this basis. However, terpenes have widely been applied in consumer products, e.g., fragrances for decades without widespread adverse impacts while being present in both indoor and outdoor environments throughout history (Sarwar et al. Citation2004; Roffael Citation2006; Wolkoff Citation2020), and thus their contribution to indoor air quality must be evaluated carefully. In contrast, volatile terpenes are also associated with various health benefits, e.g., anti-inflammatory potential, further challenging their perception as mere pollutants (Kim et al. Citation2020).
The evaluation of safe use of alternative, sustainable materials is needed to justify the encouraging shift toward BCs. Therefore, multiple relevant indoor exposure agent parameters are sampled or monitored in this study while (poly)lactic acid (PLA) based BC filaments, and a reference PLA filament are produced with a commercial filament extruder and used as an ME 3D printer feedstock. The main aims of this study are to (1) discover how the introduction of wood (and cellulose) content affects the emission composition of 3D printer feedstocks, (2) to estimate how hazardous the produced emissions are in comparison to a pure plastic, (3) to establish if terpenes or other wood-related compounds are commonly produced during thermal processing of BCs, and (4) to document how the emissions from a filament extruder compare to a 3D printer when equivalent feedstocks are used in both machines. VOCs and particles originated from BC processing, and especially their small-scale production has not previously been investigated thoroughly from a safety perspective and the impacts of the introduction of bio-content on emission compositions are not previously discussed in the AM field. Although BC filaments have occasionally been used in ME printer emission studies as a subsidiary material (Azimi et al. Citation2016; Stabile et al. Citation2017; Kwon et al. Citation2017; Vance et al. Citation2017; Väisänen et al. Citation2019; Jeon et al. Citation2020), they have not been a central material of interest and the postulated terpene emissions have not been previously targeted. This study aims to fill in the remaining data gaps.
Materials and methods
Feedstock production and 3D printing
Wood powder used for custom BC filament production was prepared by grinding dried, mixed sawdust (including ca. 40% birch, 40% spruce, and 20% aspen) with an A10 analytical grinder (IKA-Werke GmbH & Co. KG., Staufen, Germany). The powder was sifted with a 250 µm mesh sieve and the larger particles were disposed of. Transparent PLA granules (3devo B. V., Utrecht, The Netherlands) and the wood powders were mixed and heated in a portable oven at 180 °C for 10 min. Two BC batches were produced, one with 15 and the other with 30 percentage in weight (w-%) wood content. For comparison, commercial BC filaments often contain 15‒40 w-% wood or cellulose content. The composite mixes were cut into smaller pieces and shredded with a SHR3D IT plastic shredder (3devo B.V., The Netherlands). A total of five different 3D printable filaments with target thicknesses of 1.75 mm were extruded with a Filament Composer 450 extruder (3devo B.V.) using the BC shreds, the aforementioned PLA granules, and commercially available PLA-based Formi 20 and Formi 40 BC granules (UPM-Kymmene Corp., Helsinki, Finland) containing 20 and 40 w-% cellulose fibers, respectively. The filament extruder consisted of four temperature-adjustable heating zones, a feeder screw, an extruder nozzle, and filament puller and roller systems. The filament extruder heating zone temperatures and the compositions of all feedstocks used in this study are presented in .
Table 1. Material compositions and filament extruder zone temperatures.
The filament extruder was purged by extruding 250 mL of the transparent PLA granules between each feedstock material. Two-hundred-fifty (250) mL of the feedstock was also initially rejected from the spooling process to prevent filament contamination. Filament production lasted for 100‒110 min. The filaments were used in an open Ender-3 ME 3D printer (ShenZhen Creality 3D Technology Co. Ltd, Shenzhen, China) to produce sets of eight 4 × 4 × 1 cm plates over 110‒120 min. The same printer specifications were used throughout the experiment; 200°C nozzle and 50°C bed temperatures, 0.2 mm layer thickness, 0/90° raster angle, and 1 mm path width as the printer was equipped with a 1 mm diameter nozzle to prevent fiber blockages. No adhesion enhancers were used on the build plate.
Emission and exposure agent measurements
The exposure and emission measurements were performed in a mechanically ventilated office room with floor area of 38.5 m2, room height of 2.7 m, a total volume of 104 m3, and a calculated ventilation rate of 3.6 air exchanges per hour (ACH) resolved by measuring air velocity from nine points at the exhaust vent interface after the measurement campaign using a 3000 md micromanometer (Swema AB, Farsta, Sweden). The ACH was calculated using the following equation:
where CFM is the volumetric air flow per minute (m3/min) calculated using the micromanometer readings and the area of the exhaust vent, while A and h represent the room dimensions (area and height). Air mixing factors or other contributors to the exhaust rate or infiltration were not identified.
A process operator was always present in the room, while a person responsible for the measurements visited the room twice an hour. Sampling was performed at a stationary point; the altitude of the breathing zone (height of 1.5 m) and one-meter distance from the emission sources. Background samples which were used to correct the results were also collected from this point. The room was ventilated between each set of collected samples and the absence of contaminants was verified by UFP concentration reduction down to background level, followed with ventilation for an additional hour. The ANSI/CAN/UL 2904 standard for 3D printer emission sampling was not followed in this study as the collected data sets were intended to represent real-life exposure circumstances, and because the filament extruder could not confidently be operated in a closed chamber.
VOC exposures were also sampled personally. Three parallel samples were collected from both the stationary point and the breathing zone of the process operator. The process operator ensured no errors were occurring during the extrusion processes while performing other tasks in the room which did not produce airborne contaminants. Sample collection time of 45 min was used to ensure the collection of sufficient amounts of compounds with Tenax TA adsorption tubes and SKC 222 pumps (SKC Inc., Eighty-Four, PA) using a calibrated flow rate of 150 mL/min. Background VOC samples were collected like the actual VOC samples, but before the initiation of thermal processes. The samples were analyzed and the mass concentrations (Cm) of individual compounds were calculated according to the ISO 16000-6:2011 standard using a gas chromatography-mass spectrometry system consisting of a TD100 thermal desorber (Markes International Inc., Sacramento, CA), 7890 A gas chromatograph equipped with an HP-5ms UI column with 60 m length, 0.25 mm internal diameter and 0.25 μm film thickness, and 5975 C mass spectrometer (all manufactured by Agilent Technologies Inc., Santa Clara, CA) operating on scanning mode. The MSD ChemStation software (version F.01.00.1903, Agilent Technologies Inc.) paired with NIST20 database (National Institute of Standards and Technology, Gaithersburg, MD) was used for VOC identification based on compound retention times and ion fingerprints. Concentrations of individual compounds were calculated as toluene equivalents with the assistance of four-point toluene standard curves constructed with standard HC 48-component 40353-U VOC samples (Supelco Inc., Bellefonte, PA). A limitation of the toluene equivalent method is that the sensitivity of the mass spectrometer may be different for the individual chemical species which can lead to result distortion. The VOCs present in at least two of the three parallel samples were included in the results and their presented concentrations are background-corrected. For further details, please see our previous study (Väisänen et al. Citation2019).
Carbonyl compound air concentrations were sampled by collecting Sep-Pak 2,4-dinitrophenylhydrazine (DNPH) Silica cartridge samples (Waters Corp., Milford, MA) over the full duration of the thermal processes at a calibrated flow rate of 2 L/min using an N022.AN.18 pump (KNF Neuberger Inc., Trenton, NJ). The samples were selectively quantified using an LCMS-8040 triple quadrupole mass spectrometer (Shimadzu Corp., Kyoto, Japan) containing a Kinetex reversed phase C18 column with 1.7 µm pore size, 100 mm length, and 3 mm internal diameter (Phenomenex Inc., Torrance, CA). Acetonitrile and water were used as the eluents. The compounds were identified and quantified with the assistance of four-point standard curves constructed by running Carbonyl-DNPH Mix 1 certified reference material samples compromised of 13 common carbonyls (Sigma-Aldrich Corp., Saint Louis, MO) among the collected samples. The LabSolution Insight program (Shimadzu Corp.) was used to for compound identification and corresponding Cm calculations. Any carbonyls not included in the reference material evaded the analysis method. Background carbonyl samples were collected for 360 min when no operations were performed in the room. The presented results are background-corrected. For further details, please see our previous study (Väisänen et al. Citation2022).
Exposure levels to particulate matter were determined with two continuously operating devices; the number concentrations (Cn) of UFPs were measured with a P-Trak 8525 device (particle size range 20–1000 nm, TSI Inc., Shoreview, MN) and Cm of coarse (PM10) and fine (PM2.5) particles were measured with an Optical Particle Sizer (OPS) 3330 instrument (16 channels, particle size range 0.3–10 µm, TSI Inc.). The OPS instrument neglects the impact of UFPs on the particle air mass concentrations because of the smallest observable particle size of 0.3 µm, which likely results in underestimated mass concentrations. Ten-second logging intervals were used in both, and the devices were zero-calibrated before each measurement set. Background concentrations were measured for 30 min before any extrusion processes were initiated, and actual sampling lasted for the full duration of an extrusion process. The presented particle concentrations are background-corrected. This study was performed in duplicate to prevent VOC sampling from being influenced by isopropyl alcohol, the working fluid emitted by the P-Trak device.
Emission rates (ERs) for TVOC and UFPs were calculated using the simplistic equation:
where S is ER per minute, Cout represents the average Cn of UFPs or Cm of TVOC in m3, Cin equals the measured background Cn of UFPs or Cm of TVOC, and Q is the volumetric flow rate (m3/h) of exhaust air. Using background-corrected values for Cout, the equation can be further simplified:
where Cavg is the average Cn of UFPs or Cm of TVOC after background-correction. These calculations are rough estimates which neglect particle losses, agglomeration, and other factors which can impact the evolution and decay of Cn of UFPs or Cm of TVOC as well as assumes complete mixing of air and constant rates for UFP and TVOC productions.
Indoor air quality (IAQ) parameters including carbon dioxide (CO2), temperature, and relative humidity (RH) were monitored with a continuously operating IAQ-Calc 7525 device (TSI Inc.) using a 30-sec logging interval. The main purpose of these measurements was quality control, but the readings were also used to discover the plausible CO2 emissions from the extrusion processes as the introduced wood content may burn in the extruder nozzles more easily than the base polymer. These parameters are not background-corrected in the results.
Results
Production of the custom BC filaments was empirically successful. All the studied materials, including the custom BC shreds were pulled into filaments with ease and 3D printing with the filaments demonstrated no malfunctions, nozzle blockages, or other critical errors and the surface qualities of the 3D printed plates were good.
The indoor air parameters were not markedly affected by the thermal processes. Room temperatures ranged between 21.2–22.8 and 19.8–20.6 °C during filament extrusion and 3D printing processes, respectively. Relative humidity is a plausible confounding factor when chemical emissions are sampled; lower RH levels are associated with diminished emissions (Manoukian et al. Citation2016), which might have had an impact on the overall VOC levels. Corresponding RH ranges were 17–27% and 27–35%. CO2 was not found to be produced in noteworthy quantities during the measurements; the highest measured single value was 860 ppm (parts per million) during 3D printing, while a peak filament extrusion concentration was only 660 ppm. Corresponding average CO2 concentrations ranged at 770–830 and 460–570 ppm during 3D printing and filament extrusion processes. These values exceed the background levels only marginally. Detailed air quality parameter results are presented in Supplementary Table 1.
VOCs and carbonyls
The main VOC results are presented in and all the detected compounds are listed in Supplementary Tables 2 and 3. The background concentrations for VOCs and carbonyls are presented in Supplementary Table 4. The same compounds were detected during filament extrusion and 3D printing processes, and the total VOC (TVOC) concentration ranges were 34–63 µg/m3 during filament extrusion and 41–56 µg/m3 during 3D printing. Lactide, commonly encountered in thermal processing of PLA, was the most abundantly detected compound (peak concentrations were 24 and 16 µg/m3 during filament extrusion and 3D printing, respectively), followed by various alcohols, acids, and aldehydes. The following terpenes were found in low concentrations: 3-carene, α-pinene, d-limonene, and p-cymene. Isoprene, the base unit of terpenes, was also detected. Cumulative terpene concentrations, including isoprene, ranged between 9 and 22 µg/m3, while the peak concentration of any single compound (3-carene and α-pinene) was only 8 µg/m3. The personal and stationary VOC results are indistinguishable as the operated machines were open and did not have any emission control mechanisms which resulted in free diffusion of the gaseous contaminants in the air. The concentrations of non-terpene VOCs were lower when wood or cellulose was present in the feedstock, but terpenes were introduced as new emission products. Hence, the TVOC levels were equal between the different feedstocks, but their VOC profiles were different. Terpenes contributed for 17–39% of TVOC during filament extrusion and 21–36% during 3D printing. The increase in wood content was associated with higher terpene portions of TVOC roughly equivalent for the wood or cellulose content, while no terpenes were encountered during processing of pure PLA. The TVOC ERs ranged between 2.6 and 3.6 × 102 µg/min during filament extrusion, and between 2.9 and 3.4 × 102 µg/min during 3D printing, and no consistent emission differences were found between the pure PLA and BC feedstocks.
Table 2. The average air concentrations of the most common VOCs, cumulative other VOCs and TVOC (µg/m3), and TVOC emission rates (STVOC, µg/min).
Table 3. The measured carbonyl compound air concentrations (µg/m3).
Table 4. The measured particle air concentrations and UFP emission rates (SUFP).
The concentrations of carbonyl compounds were notably affected by the higher extrusion temperature of the 3D printer in comparison to the lower processing temperature used during filament production. The measured carbonyl concentrations are presented in . 2-Butanone, acetaldehyde, acetone, and formaldehyde were the most abundantly encountered carbonyls which together contributed for 84–98% of the cumulative carbonyl concentrations which ranged between 60–91 µg/m3 during filament extrusion and 190–253 µg/m3 during 3D printing. Acetone was detected in the highest concentration, at 83 µg/m3 level during 3D printing of pure PLA. Peak concentrations for 2-butanone, acetaldehyde and formaldehyde were 73, 32, and 41 µg/m3, respectively, measured while printing different BC feedstocks. Several other carbonyls (acrolein, methacrolein and benzaldehyde) were detected at low (below 5 µg/m3) concentrations as well. The following carbonyls were detected at below 5 µg/m3 levels in the background: 2-butanone, acetaldehyde, acetone, acrolein, formaldehyde, hexaldehyde, and propionaldehyde. The used analysis method was selective and only the compounds in the reference material were able to be identified, and other carbonyls evaded the method. However, no distinct phantom peaks representing unidentified compounds were found in the chromatograms.
Particulate matter
The obtained particulate matter concentrations and ERs for UFPs are presented in , and background particle concentrations are listed in Supplementary Table 5. Filament extrusion and 3D printing processes produced rather constant amounts of particles as no major concentration peaks were recorded and the concentrations fluctuated only mildly. Time series data illustrating the evolution of particle (UFP, PM2.5, and PM10) concentrations during thermal processing of pure PLA, Formi 20, and BC 30% are presented in Supplementary Figures 1–3. The top UFP concentrations were 2.30 × 102 and 1.41 × 103 #/cm3 for pure PLA during filament extrusion and 3D printing, respectively, while the corresponding peak values were 1.25 × 103 and 3.42 × 103 #/cm3 for BC feedstocks. Pure PLA was documented to produce slightly lower amounts of UFPs than BCs during filament extrusion but not during 3D printing; the respective average concentrations for PLA were 0.85 × 102 and 6.25 × 102 #/cm3 (which represent ERs of 5.3 × 108 and 3.9 × 109 #/min). The corresponding Cn ranges were 1.30 × 102‒1.05 × 103 and 6.05 × 102‒2.09 × 103 #/cm3 for BC materials, which represent ER ranges of 8.1 × 108‒6.6 × 109 during filament extrusion and 3.8 × 109‒1.3 × 1010 during 3D printing. Overall, only moderate UFP concentration or ER differences are observable between the commercial and custom feedstocks, and the 3D printer produced principally more UFPs than the filament extruder.
PM2.5 and PM10 particles were also produced during the extrusion processes. PM2.5 particles were documented at the average Cm range of 0.2–0.6 µg/m3 during filament extrusion, and between 1.2–2.2 µg/m3 during 3D printing. Cm peaks for the respective processes were 2.8 and 3.1 µg/m3 and no coherent differences were identified between the feedstocks. The highest Cm of PM10 particles (85 µg/m3) was detected during pure PLA filament extrusion, while the top Cm measured during the production of BC filaments was 75 µg/m3 (Formi 20). Mild concentration fluctuations were observed, but not in a consistent manner. The highest average filament extrusion PM10 Cm was 20 µg/m3, measured during BC 15% processing. 3D printing produced lower amounts of PM10 particles, and the highest peak value was only 20 µg/m3 recorded using Formi 40 feedstock. Otherwise, the average PM10 concentrations ranged between 5–10 µg/m3 during both filament extrusion and 3D printing processes.
Discussion
The production of functional custom 3D printable filaments using only raw materials and commercial level machines was achieved in this study. An open 3D printer and a filament extruder produced particulate matter and chemical compounds at fair concentration levels when the machines were operated at reasonable temperatures in a medium-sized and adequately ventilated office space. The measured contaminant concentrations and calculated ERs were generally at anticipated levels based on the existing literature.
The measured CO2 values were far from air quality compromising levels despite the occasional exceeding of the background concentrations by a few hundred ppm (FMSAH Citation2015, Citation2020). The elevated concentrations can be explained with the presence of the 3D printer and measurement personnel. The feedstocks were not noticed to burn in the extruder nozzles during the experiment, which is a relatively common malfunction in ME 3D printing. This is supported by the measured moderate UFP levels which are known to increase drastically in such situations and thus, the extrusion processes as the sources for CO2 are unlikely. The other air quality parameters remained constant and therefore the operated machines had a negligible influence on them. The recorded low RH levels may have diminished the total production of VOCs. Regardless, internal VOC results comparison is unperturbed by the RH levels owing to their consistency.
VOCs and carbonyls
The VOC concentrations measured during the filament extruder and 3D printer operations were very analogous. Lactide was the most abundant compound detected throughout the experiment and a common thermal degradation product of PLA. It does not have an official occupational exposure limit (OEL) value. Evidence for its toxicity was found only after 2 weeks of daily high (≥1,000 mg/kg body weight) oral dosing in an animal study (Hébert et al. Citation1999), while no human toxicity data was found by the authors. Thus, the measured exposure levels are not expected to be hazardous for humans, despite the concentration being calculated as a toluene equivalent. Majority of the other VOCs found at the highest concentrations (acetic acid and various aldehydes or alcohols) corresponded with existing literature as well (Kim et al. Citation2015a, Azimi et al. Citation2016; Steinle Citation2016; Stefaniak et al. Citation2017; Davis et al. Citation2019; Pohleven et al. Citation2019; Väisänen et al. Citation2019, Citation2021a). These compounds are not particularly harmful for human health at the measured concentration levels either, as they do not possess eminent hazardous properties which is reflected by their high OELs (FMSAH Citation2020), or maximum acceptable workplace concentrations (MAKs, DFG Citation2021). A limitation of this study is that the presented compound concentrations are calculated as toluene equivalents and the administrative guideline values are derived using the response curves of the individual compounds. Therefore, the concentrations acquired in this study do not perfectly match the true concentrations of the compounds in the air. Examples of these values are 500 mg/m3 for 8-hr exposure to 1-propanol, and 42 mg/m3 for acute exposure to hexanal (FMSAH Citation2020). Like lactide, 1-nonanol has no established OEL, but exposure to the recorded levels (2‒8 µg/m3) are unlikely to produce adverse health impacts based on the available toxicity data (PubChem Citation2022). Furfural, a compound originating from heat-treating of wood (Pohleven et al. Citation2019) was inconsistently detected during BC extrusion processes at up to 6 µg/m3 level. It has a lowest health-based concentration of interest (LCI) value of 10 µg/m3 in the air because of its hepatotoxic properties (WHO Citation1995; EC Citation2020), thus making it the only compound which approached its available official limit value in the current study. Acetic acid is another wood-originated compound, but its measured concentration is likely underestimated because the used VOC sampling method is most accurate for the collection of compounds in 6–16 carbon atom range. Its OEL of 13 mg/m3 for 8-hr exposure is, however, far higher than the recorded concentration magnitude (FMSAH Citation2020). The measured TVOC levels correspond rather well with the previously documented concentrations obtained using PLA and BC feedstocks in 3D printers (Kim et al. Citation2015a; Azimi et al. Citation2016; Floyd et al. Citation2017, Mendes et al. Citation2017, Stefaniak et al. Citation2017, Du Preez et al. Citation2018; Väisänen et al. Citation2019, Citation2021a). The TVOC levels were also low in comparison to the proposed occupational indoor air guidelines in Finland; 3000 or 250 µg/m3 for industrial workplaces, or office and analogous environments, respectively (Tuomi and Vainiotalo Citation2016). Similarly, TVOC values fell below the Finnish residential space threshold TVOC value of 400 µg/m3 and the individual non-health-based compound limit of 50 µg/m3 was not exceeded, either (FMSAH Citation2015). While TVOC is not a health-based parameter, it is an applicable indicator of indoor air quality (Tuomi and Vainiotalo Citation2016). The indoor air quality of an adequately ventilated medium sized office space is not jeopardized by operation of a single 3D printer or filament extruder using PLA or PLA-based BC feedstocks on this basis. TVOC ERs calculated for PLA and BC feedstocks in previous studies (Azimi et al. Citation2016; Steinle Citation2016; Floyd et al. Citation2017; Stefaniak et al. Citation2017, Citation2019; Davis et al. Citation2019) express remarkable differences. Stefaniak et al. (Citation2017) calculated a TVOC ER of ca. 2 µg/min for a closed printer in a chamber, but in a later study Stefaniak et al. (Citation2019) documented up to 4.4 × 104 µg/min ER using an open printer in a laboratory with a ventilation rate of 2 ACH. The documented TVOC ERs have been more modest, around 10‒50 µg/min in chamber studies (Azimi et al. Citation2016; Steinle Citation2016; Floyd et al. Citation2017). The ERs calculated in the current study represent the chamber studies more accurately than those obtained in the laboratory study, suggesting moderate TVOC emissions. The different research methods and environments contribute to the diversity of the results, as for example, a real-time TVOC sensor has been used in multiple studies as opposed to adsorption tube sampling made use of in others, like the current one.
Terpene compounds were found on all occasions when wood or cellulose was present in the feedstock material, even though pure cellulose should not contain terpenes. In contrast, no terpenes were present during processing of pure PLA. Drying sawdust for 3 months likely contributed to the fair obtained terpene levels as a portion of the compounds had time to spontaneously depart the wood matter (Roffael Citation2006; Höllbacher et al. Citation2015). Nonetheless, terpenes contributed to ca. 20–40% of the TVOC levels. While not particularly toxic, they may impair indoor air quality as they are precursors for air quality deteriorating secondary chemical reactions and UFP formation in the presence of ozone (Sarwar et al. Citation2004; Weschler Citation2011; Rohr Citation2013; Kim et al. Citation2015b; Wolkoff Citation2020). Secondary compounds produced in the chemical interactions in air include reactive species and carbonyls of low molecular weight, e.g., carcinogenic formaldehyde (Weschler Citation2011; Rohr Citation2013; Kim et al. Citation2015b; Wolkoff Citation2020). However, many terpenes are purposefully used in significant quantities in various consumer products, such as fragrances, and some of their benefits have also been recognized (Kim et al. Citation2020). The measured air concentrations were low in comparison to their LCI or MAK values (2.5 mg/m3 for α-pinene, 1.5 mg/m3 for 3-carene, 28 or 5 mg/m3 for d-limonene, 1 mg/m3 for cymene, and 8.5 mg/m3 for isoprene) and, thus, they are expected to have a minute impact on indoor air quality or little contribution to the induction of adverse health impacts in 3D printer operators (EC Citation2020; DFG 2021).
3D printing with PLA and PLA-based composite filaments have previously been documented to emit various carbonyls, e.g., acetaldehyde, acetone, and formaldehyde in moderate concentrations (Kim et al. Citation2015a; Mendes et al. Citation2017; Stefaniak et al. Citation2017; Du Preez et al. Citation2018; Davis et al. Citation2019; Väisänen et al. Citation2019). Unexpectedly, the filament extruder and 3D printer produced similar levels of VOCs, but the carbonyl concentrations were substantially higher, ca. two- to four-fold from the 3D printer in comparison to the filament extruder. The obtained levels were not affected by the feedstock material. It should be noted that the filament extruder operates at the lowest temperature settings that makes feedstock extrusion and spooling plausible, which is lower than the temperatures used in 3D printers. The applied temperature is one factor which contributes to the higher carbonyl levels from the 3D printer in comparison to the filament extruder. Despite existing at moderate levels at highest, all carbonyls fell below their OELs (FMSAH Citation2020), MAK values (DFG 2021), LCIs (EC Citation2020), and residential space threshold values given by WHO (Citation2018) and FMSAH (2015). The lowest official (long-term) limit value of 50 µg/m3 given for formaldehyde in residential spaces in Finland was almost exceeded during 3D printing (FMSAH Citation2015). The lowest corresponding reference values given for acetaldehyde (300 µg/m3, EC Citation2020), acetone (120 or mg/m3, EC Citation2020), and 2-butanone (20 mg/m3, EC Citation2020) are notably higher than the concentrations obtained in this study. Long-term exposure to formaldehyde and acetaldehyde still cannot be deemed completely innocuous due to their toxic properties (WHO Citation2006; Sarigiannis et al. Citation2011; Klaasen et al. Citation2013). Otherwise, the compounds are not expected to be hazardous for 3D printer personnel at the recorded levels. In addition to being more readily volatilized than VOCs, carbonyls are formed in secondary chemical interactions in the air as described above. It is plausible that these factors contributed to the unexpectedly high carbonyl levels.
Particulate matter
3D printers are identified as significant UFP emitters, but the obtained concentration levels were far below a proposed lightweight UFP exposure reference value of 4 × 104 #/cm3 given for manufactured nanomaterials (Van Broekhuizen et al. Citation2012), the only available reference as no authoritative OELs exist. PLA and BC feedstocks have been recorded to emit UFPs with an aerodynamic diameter of 20 nm and above mainly in 5 × 102–5 × 104 #/cm3 concentration levels when 200‒220 °C temperatures are used (Kim et al. Citation2015a; Yi et al. Citation2016; Azimi et al. Citation2016; Floyd et al. Citation2017; Kwon et al. Citation2017; Mendes et al. Citation2017; Vance et al. Citation2017; Du Preez et al. Citation2018; Väisänen et al. Citation2019, Citation2021a; Byrley et al. Citation2019; Jeon et al. Citation2020). These concentration ranges represent calculated ERs of ca. 108‒1011 #/min (Kwon et al. Citation2017; Vance et al. Citation2017; Byrley et al. Citation2019; Jeon et al. Citation2020). The concentrations documented in the current study are equivalent to the lower end of the documented concentration spectrum, while the calculated UFP ERs also fall within the previously reported ER ranges. The ERs calculated in the current study are, however, very likely underestimated because of the used calculation method. The studied BC feedstocks are, nevertheless, very similar UFP emitters as pure PLA feedstocks based on the results and previous literature. The filament extruder produced slightly lesser amounts of UFPs in comparison to the 3D printer, which is a consistent finding with the carbonyl levels. A filament extruder can be identified as an equivalent or a slightly lesser UFP emitter as a desktop ME 3D printer. In addition to VOCs, a higher 3D printer nozzle temperature is documented to increase UFP emissions by several studies (Yi et al. Citation2016; Byrley et al. Citation2019; Jeon et al. Citation2020; Stefaniak et al. Citation2021), and the findings of the current study reflect that (except the case of BC 30% which produced the most particles during filament extrusion). The obtained UFP levels were stable, and the absence of concentrations peaks indicates that the extrusion processes were principally undisturbed by the wood or cellulose particles.
To the best knowledge of the authors, PM2.5 levels from the operation of ME 3D printers have been only studied once in a chamber, and only using ABS as the feedstock. PM2.5 levels were documented to gradually increase from zero to as high as 900 µg/m3 level in the study by Rao et al. (Citation2017). Higher RH was associated with higher particle levels; the highest concentration was achieved at 80% RH. A concentration level of 600 µg/m3 was reached at 40% RH. These values are far higher than those found in the current study, but neither the study designs nor used feedstocks are comparable. WHO (Citation2021) has introduced a 24-hr average PM2.5 guideline value of 15 µg/m3 for ambient air, which is a suitable reference for comparison. This limit value was not reached during the current study using the CPC instrument, as the highest observed peak value was only 3.1 µg/m3, and only up to 2.2 µg/m3 average PM2.5 levels were recorded over full thermal processes. It must be emphasized that the CPC instrument could not detect particles smaller than 0.3 µm in diameter and thus the true PM2.5 (and PM10) concentrations in the air are greater than what was detected in the current study, as the UFPs were not included in the recorded mass concentrations. Larger particles are occasionally documented to be emitted by 3D printers at fair to moderate, up to 100 µg/m3 concentrations, if at all (Kim et al. Citation2015a; Yi et al. Citation2016; Väisänen et al. Citation2019; Mendes et al. Citation2017; Kwon et al. Citation2017; Byrley et al. Citation2019). The PM10 concentrations measured in this study correspond with the previously documented levels. No official OELs are established for PM10 particles, either, but they can be substituted by guideline values for ambient air and residential indoor environments. These established health-based values are almost universally set at 50 µg/m3, while WHO suggests a stricter long-term value of 20 µg/m3 for residential spaces (EU Citation2008; FMSAH Citation2015; WHO Citation2018, Citation2021). The PM10 guideline of 50 µg/m3 was temporarily exceeded during filament extrusion processes, but all average concentrations were below it. The closest comparable Finnish OEL is the one for total inhalable organic dust set at 5 mg/m3 (FMSAH 2021), which is far higher than the measured PM10 concentrations. The exposure levels to PM2.5 and PM10 particles are therefore not a significant concern for a process operator, albeit the machines temporarily produced particles at concentrations that exceeded the established PM10 guideline values.
The filament extruder
Similar UFP ERs, but far higher particle concentration levels for PLA feedstocks were documented in a study by Byrley et al. (Citation2020) in comparison to this experiment. The extruder was in a chamber unlike in the current study, which naturally resulted in different particle concentration readings. A pulverized PLA feedstock produced as high UFP concentration peak as 3.5 × 105 #/cm3, while a granulated PLA feedstock peaked at 2.5 × 104 #/cm3. No as radical concentration differences and peaks were found in the current study. The ERs reported by Byrley et al. (Citation2020) were 1.7 × 109 and 5.6 × 1010 #/min for the granulated and shredded feedstocks, respectively. In comparison, the calculated ER for PLA was 5.3 × 108 #/min in the current study, while the commercial BC granules produced fairly higher emissions, and the custom BC shreds emitted the most particles (up to 6.6 × 109 #/min), which is a consistent finding with the previous study. Additionally, Byrley et al. (Citation2020) calculated Cm for PM2.5 using resolved UFP size distributions and feedstock densities. In this study, Cm of PM2.5 was sampled directly with the OPS instrument. The results are not comparable though, as the minimum detection limit of the OPS instrument is 0.3 µm, and thus, the majority of particles went undetected by the device in this experiment. The previously reported PM2.5 concentrations were ca. 35 µg/m3 for granulated PLA, and ca. 125 µg/m3 for shredded PLA. The highest Cm peak of PM2.5 particles during filament extrusion processes was a mere 2.8 µg/m3 in the current study, while the average concentrations were below 1 µg/m3 throughout the experiment. Also, no PM2.5 Cm differences existed between the studied feedstocks. Similarly, the obtained PM10 Cm values were indifferent between the used feedstocks in the current study, with the highest peak value reaching 85 µg/m3 and the highest average concentration being 20 µg/m3. The VOCs detected by Byrley et al. (Citation2020) included lactide, benzene derivates, and various acids and alcohols among others. These compounds correspond well with previous 3D printer emission literature and the findings of the current study, which supports the emission similarity assumption between filament extruders and 3D printers using similar feedstocks. Byrley et al. (Citation2020) ultimately identified filament extruders and desktop 3D printers as very similar emission sources, and the findings of the current study support the claim.
Conclusions
It was demonstrated in this study that functional and 3D printable BC feedstocks can be produced from commercially available plastic granules and raw wood fibers without expensive and technically advanced machines. The airborne contaminant compositions, levels, and ERs produced by a filament extruder resemble those from an open ME 3D printer when equivalent feedstocks are used in both. This was the first time this was confirmed. Emission products originated from PLA-based BC feedstocks could not be identified as severely more hazardous than those from a pure PLA feedstock, albeit some differences in chemical compositions existed. Certain compounds that originate from thermal treatment of wood, including terpenes and furfural were the most obvious differences. Terpenes can impair indoor air quality through secondary chemical reactions and UFP formation, but their impact on air quality is not expected to be significant based on the concentration levels obtained in the current study. Furfural may produce toxic effects in prolonged exposure, but it was found inconsistently and only at low concentration levels. PLA-based BC materials can be identified as environmentally friendly feedstocks which express similar hazardous properties in comparison to traditional petroleum-derived polymers based our findings as the addition of bio-content both reduced the portion of plastic-originated emission products and introduced new chemical emission products, while no major impact was observed on the produced particle levels. Nonetheless, emission control measures should be always applied when thermal extruders are operated.
Findings by Byrley et al. (Citation2020) were mostly confirmed in this study. The emissions from a filament extruder resemble those from a 3D printer accurately, for both the composition and magnitude. Filament extruders are often operated at lower temperature settings than 3D printers which contributes to slightly reduced emissions. This was observable in this study on behalf of carbonyls and UFPs. On the other hand, PM10 particles were observed at slightly greater concentrations when a filament extruder was operated, while the recorded VOC and PM2.5 particle levels were identical between the machines. The contaminant concentration levels were mostly low or moderate based on the previous literature and administrative guidelines, indicating that emissions produced by a single 3D printer or filament extruder are not excessive in a moderately sized, well-ventilated office space. Further suggested research topics include the expansion of the studied feedstocks in a filament extruder, and the examination of the mechanical properties of (customized) BCs feedstocks which could further support the transition toward sustainable 3D printer materials.
Recommendations
Similar emission and exposure control measures can and should be applied on filament extruders as on 3D printers. These measures include the use of machine enclosures, local exhaust systems and lowest functional temperature settings, and spending the least possible time in the same premises with the operated machines to prevent exposure to their emissions. The use of wood-containing BC materials does not require further protective measures than generic feedstocks.
Supplemental Material
Download PDF (649.9 KB)Acknowledgments
The authors would like to thank Mr. Pekka Oksala for supplying the sawdust used in this study and M.A. Ari-Pekka Väisänen for proof-reading the manuscript.
Conflicts of interest
The authors declare no conflict of competing interest.
Data availability statement
The authors confirm that the data supporting the findings of this study are available within the article and its supplementary materials and are shared upon request.
Additional information
Funding
References
- Azimi P, Zhao D, Pouzet C, Crain NE, Stephens B. 2016. Emissions of ultrafine particles and volatile organic compounds from commercially available desktop three-dimensional printers with multiple filaments. Environ Sci Technol. 50(3):1260–1268. doi:10.1021/acs.est.5b04983
- Byrley P, Geer Wallace MA, Boyes W, Rogers K. 2020. Particle and volatile organic compound emissions from a 3D printer filament extruder. Sci Total Environ. 736:139604. doi:10.1016/j.scitotenv.2020.139604
- Byrley P, George B, Boyes W, Rogers K. 2019. Particle emissions from fused deposition modeling 3D printers: evaluation and meta-analysis. Sci Total Environ. 655:395–407. doi:10.1016/j.scitotenv.2018.11.070
- Calí M, Pascoletti G, Gaeta M, Milazzo G, Ambu R. 2020. A new generation of bio-composite thermoplastic filaments for a more sustainable design of parts manufactured by FDM. Appl Sci. 10(17):5852. doi:10.3390/app10175852
- Calvino C, Macke N, Kato R, Rowan SJ. 2020. Development, processing and applications of bio-sourced cellulose nanocrystal composites. Prog Polym Sci. 103:101221. doi:10.1016/j.progpolymsci.2020.101221
- Chan FL, House R, Kudla I, Lipszyc JC, Rajaram N, Tarlo SM. 2018. Health survey of employees regularly using 3D printers. Occup Med. 68(3):211–214. doi:10.1093/occmed/kqy042
- Davis AY, Zhang Q, Wong JPS, Weber RJ, Black MS. 2019. Characterization of volatile organic compound emissions from consumer level material extrusion 3D printers. Build Environ. 160:106209. doi:10.1016/j.buildenv.2019.106209
- [DFG] Deutsche Forschungsgemeinschaft. 2021. Permanent Senate Commission for the investigation of health hazards of chemical compounds in the work area. Report 57. List of MAK and BAT Values 2021; [accessed Dec 8]. mbwl_2021_eng.pdf (publisso.de)
- Du Preez S, Johnson AR, LeBouf RF, Linde SJL, Stefaniak AB, Du Plessis J. 2018. Exposures during industrial 3-D printing and post-processing tasks. RPJ. 24(5):865–871. doi:10.1108/RPJ-03-2017-0050
- European Commission (EC). 2020. EU-LCI values; [accessed 2021 Nov 22]. https://ec.europa.eu/growth/sectors/construction/eu-lci-subgroup/eu-lci-values_en.
- European Union (EU). 2008. Directive 2008/50/EC of the European Parliament and of the Council on ambient air quality and cleaner air for Europe. Off J Eur Union L 152:1–44. https://eur-lex.europa.eu/eli/dir/2008/50/oj.
- Floyd EL, Wang J, Regens JL. 2017. Fume emissions from a low-cost 3-D printer with various filaments. J Occup Environ Hyg. 14(7):523–533. doi:10.1080/15459624.2017.1302587
- Finnish Ministry of Social Affairs and Health (FMSAH). 2015. Decree 545/2015 of the Ministry of Social Affairs and Health on health-related conditions of housing and other residential buildings and qualification requirements for third-party experts; [accessed 2021 Nov 25]. https://www.finlex.fi/en/.
- Finnish Ministry of Social Affairs and Health (FMSAH). 2020. Concentrations known to be harmful; [accessed 2021 Nov 22]. https://julkaisut.valtioneuvosto.fi/handle/10024/162457.
- Ford S, Despeisse M. 2016. Additive manufacturing and sustainability: an exploratory study of the advantages and challenges. J. Clean Prod. 137:1573–1587. doi:10.1016/j.jclepro.2016.04.150
- Hébert CD, Giles HD, Heath JE, Hogan DB, Modderman JP, Conn RE. 1999. Toxicity of lactide in dogs after 2 and 13 weeks of daily oral dosing. Food Chem Toxicol. 37(4):335–342. doi:10.1016/S0278-6915(99)00014-9
- Höllbacher E, Rieder-Gradinger C, Strateva D, Srebotnik E. 2015. A large-scale test set-up for measuring VOC emissions from wood products under laboratory conditions in simulated real rooms. Holzforschung. 69(4):457–462. doi:10.1515/hf-2014-0129
- House R, Rajaram N, Tarlo SM. 2017. Case report of asthma associated with 3D printing. Occup Med. 67(8):652–654. doi:10.1093/occmed/kqx129
- Jeon H, Park J, Kim S, Park K, Yoon C. 2020. Effect of nozzle temperature on the emission rate of ultrafine particles during 3D printing. Indoor Air. 30(2):306–314. doi:10.1111/ina.12624
- Kasanen J-P, Pasanen A-L, Pasanen P, Liesivuori J, Kosma V-M, Alarie Y. 1999. Evaluation of sensory irritation of 3-carene and turpentine, and acceptable levels of monoterpenes in occupational and indoor environment. J Toxicol Environ Health A. 57(2):89–114. doi: 10.1080/009841099157809.
- Klaasen CD, Casarett LJ, Doull J. 2013. Casarett & Doull’s toxicology: the basic science of poisons. 8th ed. Manhattan (NY): McGraw Hill Education.
- Kim S, Kim J-A, Kim H-J, Kim SD. 2006. Determination of formaldehyde and TVOC emission factor from wood-based composites by small chamber method. Polymer Testing. 25(5):605–614. doi:10.1016/j.polymertesting.2006.04.008
- Kim S, Hong S-H, Bong C-K, Cho M-H. 2015b. Characterization of air freshener emission: the potential health effects. J Toxicol Sci. 40(5):535–550. doi:10.2131/jts.40.535
- Kim T, Song B, Cho KS, Lee I-S. 2020. Therapeutic potential of volatile terpenes and terpenoids from forests for inflammatory diseases. Int J Mol Sci. 21(6):2187. doi:10.3390/ijms21062187
- Kim Y, Yoon C, Ham S, Park J, Kim S, Kwon O, Tsai P-J. 2015a. Emissions of nanoparticles and gaseous material from 3D printer operation. Environ Sci Technol. 49(20):12044–12053. doi:10.1021/acs.est.5b02805
- Kim YW, Kim MJ, Chung BY, Bang DY, Lim SK, Choi SM, Lim DS, Cho MC, Yoon K, Kim HS, et al. 2013. Safety evaluation and risk assessment of d-limonene. J Toxicol Environ Health B Crit Rev. 16(1):17–38. doi:10.1080/10937404.2013.769418
- Kwon O, Yoon C, Ham S, Park J, Lee J, Yoo D, Kim Y. 2017. Characterization and control of nanoparticle emissions during 3D printing. Environ Sci Technol. 51(18):10357–10368. doi:10.1021/acs.est.7b01454
- Manoukian A, Buiron D, Temime-Roussel B, Wortham H, Quivet E. 2016. Measurements of VOC/SVOC emission factors from burning incenses in an environmental test chamber: influence of temperature, relative humidity, and air exchange rate. Environ Sci Pollut Res Int. 23(7):6300–6311. doi:10.1007/s11356-015-5819-2
- Mazzanti V, Malagutti L, Mollica F. 2019. FDM 3D printing of polymers containing natural fillers: a review of their mechanical properties. Polymers. 11(7):1094. doi:10.3390/polym11071094
- Mendes L, Kangas A, Kukko K. 2017. Characterization of emissions from a desktop 3D printer. J. Ind. Ecol. 14:94–106. doi:10.1111/jiec.12569
- Mossman BT, Borm PJ, Castranova V, Costa DL, Donaldson K, Kleeberger SR. 2007. Mechanisms of action of inhaled fibers, particles and nanoparticles in lung and cardiovascular diseases. Part Fibre Toxicol. 4:4. doi:10.1186/1743-8977-4-4
- Peng T, Kellens K, Tang R, Chen C, Chen G. 2018. Sustainability of additive manufacturing: an overview on its energy demand and environmental impact. Addit Manuf. 21:694–704. doi:10.1016/j.addma.2018.04.022
- Pohleven J, Burnard MD, Kutnar A. 2019. Volatile organic compounds emitted from untreated and thermally modified wood—a review. WFS. 51(3):231–224. doi:10.22382/wfs-2019-023
- Pope CA, Dockery DW. 2006. Health effects of fine particulate air pollution: lines that connect. J Air Waste Manag Assoc. 56(6):709–742. doi:10.1080/10473289.2006.10464485
- PubChem. 2022. Compound summary. Nonan-1-ol; [accessed 2022 Feb 15]. https://pubchem.ncbi.nlm.nih.gov/compound/1-Nonanol.
- Rao C, Gu F, Zhao P, Sharmin N, Gu H, Fu J. 2017. Capturing PM2.5 emissions from 3D printing via nanofiber-based air filter. Sci Rep. 7(1):10366. doi: 10.1038/s41598-017-10995-7.
- Roffael E. 2006. Volatile organic compounds and formaldehyde in nature, wood and wood based panels. Holz Roh Werkst. 64(2):144–149. doi:10.1007/s00107-005-0061-0
- Rohr AC. 2013. The health significance of gas- and particle-phase terpene oxidation products: a review. Environ Int. 60:145–162. doi:10.1016/j.envint.2013.08.002
- Sarigiannis DA, Karakitsios SP, Gotti A, Liakos IL, Katsoyiannis A. 2011. Exposure to major volatile organic compounds and carbonyls in European indoor environments and associated health risk. Environ Int. 37(4):743–765. doi:10.1016/j.envint.2011.01.005
- Sarwar G, Olson DA, Corsi RL, Weschler CJ. 2004. Indoor fine particles: the role of terpene emissions from consumer products. J Air Waste Manag Assoc. 54(3):367–377. doi:10.1080/10473289.2004.10470910
- Shahnaz B, Hayes A, Dechsakulthorn F. 2012. Nanoparticles: a review of particle toxicology following inhalation exposure. Inhal Toxicol. 24(2):125–135. doi:10.3109/08958378.2010.642021
- Stabile L, Scungio M, Buonanno G, Arpino F, Ficco G. 2017. Airborne particle emission of a commercial 3D printer: the effect of filament material and printing temperature. Indoor Air. 27(2):398–408. doi:10.1111/ina.12310
- Stefaniak AB, Du Preez S, Du Plessis JL. 2021. Additive manufacturing for occupational hygiene: a comprehensive review of processes, emissions & exposures. J. Toxicol. Environ. Health B. 24(5):173–222. doi:10.1080/10937404.2021.1936319
- Stefaniak AB, Johnson AR, du Preez S, Hammond DR, Wells JR, Ham JE, LeBouf RF, Menchaca KW, Martin SB, Duling MG, et al. 2019. Evaluation of emissions and exposures at workplaces using desktop 3-dimensional printer. J Chem Health Saf. 26(2):19–30. doi:10.1016/j.jchas.2018.11.001
- Stefaniak AB, LeBouf RF, Yi J, Ham J, Nurkewicz T, Schwegler-Berry DE, Chen BT, Wells JR, Duling MG, Lawrence RB, et al. 2017. Characterization of chemical contaminants generated by a desktop fused deposition modeling 3-dimensional printer. J Occup Environ Hyg. 14(7):540–550. doi:10.1080/15459624.2017.1302589
- Steinle P. 2016. Characterization of emissions from a desktop 3D printer and indoor air measurements in office settings. J Occup Environ Hyg. 13(2):121–132. doi:10.1080/15459624.2015.1091957
- Tuomi T, Vainiotalo S. 2016. The guideline and target values for total volatile organic compound concentrations in industrial indoor environments in Finland. Indoor Built Environ. 25(2):424–434. doi:10.1177/1420326X14554270
- Vaidya AA, Collet C, Gaugler M, Lloyd-Jones G. 2019. Integrating softwood biorefinery lignin into polyhydroxybutyrate composites and application in 3D printing. Mater Today Commun. 19:286–196. doi:10.1016/j.mtcomm.2019.02.008
- Van Broekhuizen P, Van Veelen W, Streekstra W-H, Schulte P, Reijnders L. 2012. Exposure limits for nanoparticles: report of an international workshop on nano reference values. Ann Occup Hyg. 56(5):515–524. doi:10.1093/annhyg/mes043
- Van Kampen V, Merget R, Baur X. 2000. Occupational airway sensitizers: an overview on the respective literature. Am J Ind Med. 38(2):164–218. doi:10.1002/1097-0274(200008)38:2 < 164::AID-AJIM7 > 3.0.CO;2-2
- Vance ME, Pegues V, Van Montfrans S, Leng W, Marr LC. 2017. Aerosol emissions from fuse-deposition modeling 3D printers in a chamber and in real indoor environments. Environ Sci Technol. 51(17):9516–9523. doi:10.1021/acs.est.7b01546
- Weschler CJ. 2011. Chemistry in indoor environments: 20 years of research. Indoor Air. 21(3):205–218. doi:10.1111/j.1600-0668.2011.00713.x
- World Health Organization (WHO). 1995. Dry cleaning, some chlorinated solvents and other industrial chemicals. IARC monographs on the evaluation of carcinogenic risk to humans. Vol. 63. Geneve (Switzerland): World Health Organization.
- World Health Organization (WHO). 2006. Formaldehyde, 2-butoxyethanol and 1-tert-butoxypropan-2-ol. IARC monographs on the evaluation of carcinogenic risks to humans. Vol. 88. Geneve (Switzerland): World Health Organization.
- World Health Organization (WHO). 2018. WHO housing and health guidelines. Geneva (Switzerland): World Health Organization.
- World Health Organization (WHO). 2021. WHO global air quality guidelines. Particulate matter (PM2.5 and PM10), ozone, nitrogen dioxide, sulfur dioxide and carbon monoxide. Geneva (Switzerland): World Health Organization.
- Wolkoff P. 2020. Indoor air chemistry: terpene reaction products and airway effects. Int J Hyg Environ Health. 225:113439. doi:10.1016/j.ijheh.2019.113439
- Wolkoff P, Wilkins CK, Clausen PA, Nielsen GD. 2006. Organic compounds in office environments—sensory irritation, odor, measurements and the role of reactive chemistry. Indoor Air. 16(1):7–19. doi:10.1111/j.1600-0668.2005.00393.x
- Väisänen AJK, Alonen L, Ylönen S, Hyttinen M. 2021a. The impact of thermal reprocessing of 3D printable polymers on their mechanical performance and airborne pollutant profiles. J Polym Res. 28:436. doi:10.1007/s10965-021-02723-7.
- Väisänen A, Alonen L, Ylönen S, Hyttinen M. 2022. Organic compound and particle emissions of additive manufacturing with photopolymer resins and chemical outgassing of manufactured resin products. J Toxicol Environ Health A. 85(5):198–216. doi:10.1080/15287394.2021.1998814.
- Väisänen AJK, Hyttinen M, Ylönen S, Alonen L. 2019. Occupational exposure to gaseous and particulate contaminants originating from additive manufacturing of liquid, powdered, and filament plastic materials and related post-processes. J Occup Environ Hyg. 16(3):258–271. doi:10.1080/15459624.2018.1557784
- Yi J, LeBouf RF, Duling MG, Nurkiewicz T, Chen BT, Schwegler-Berry D, Virji MA, Stefaniak AB. 2016. Emission of particulate matter from a desktop three-dimensional (3D) printer. J Toxicol Environ Health A. 79(11):453–465. doi:10.1080/15287394.2016.1166467