Introduction
In volume 33, issue 7 of Energy Sources, Part A: Recovery, Utilization, and Environmental Effects, an incorrect sentence appeared in the abstract and certain figures were printed without the Y-axis in Predicting Frictional Pressure Loss During Horizontal Drilling for Non-Newtonian Fluids by M. Sorgun and M. E. Ozbayoglu, pages 631–640. The correct abstract and figures are shown below.
Abstract
Accurate estimation of the frictional pressure losses for non-Newtonian drilling fluids inside annulus is quite important to determine pump rates and select mud pump systems during drilling operations. The purpose of this study is to estimate frictional pressure loss and velocity profile of non-Newtonian drilling fluids in both concentric and eccentric annuli using an Eulerian-Eulerian computational fluid dynamics (CFD) model. An extensive experimental program was performed in METU-PETE Flow Loop using two non-Newtonian drilling fluids including different concentrations of xanthan biopolimer, starch, KCl and soda ash, weighted with barite for different flow rates and frictional pressure losses were recorded during each test. Computational fluid dynamic simulations were performed to compare with experimental data gathered at the METU-PETE flow loop and previous studies as well as slot flow approximation for the annulus. Results show that the computational fluid dynamic model simulations are capable of estimating frictional pressure drop with an error of less than 10% in most cases, more accurately than the slot equation.
Figure 3. Comparison of CFD simulation, slot equation, and mud 1 experimental data for fully eccentric annuli.
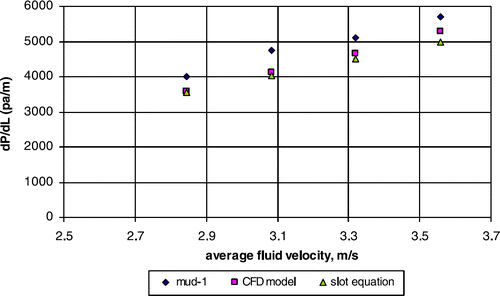
Figure 4. Comparison of CFD simulation, slot equation, and mud 2 experimental data for fully eccentric annuli.
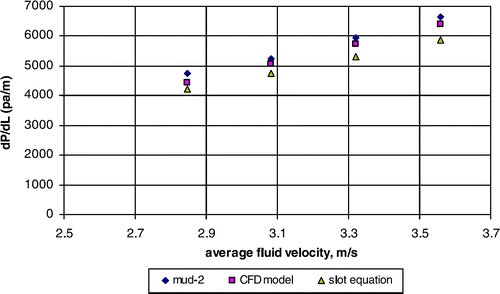
Figure 5. Comparison of CFD simulation, slot equation, and mud 3 experimental data for concentric annuli.
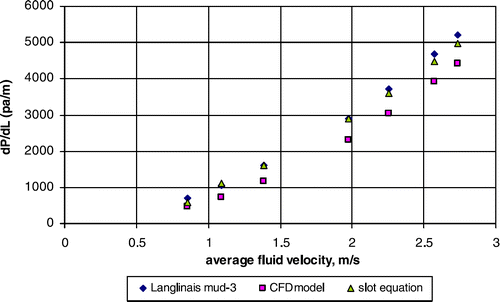