ABSTRACT
There is a dual perspective regarding agricultural materials. The first one is regarding the removal of certain chemical elements for specific applications, and the second one is regarding the recovery of certain elements to make them more appealing. The most appropriate use of agricultural and industrial waste materials demands the development of knowledge insights as a requirement for setting up of demonstration plants on a pilot basis and large-scale industrial adoption resulting in all associated socio-economic benefits. The Stir casting method is employed to fabricate the Metal Matrix Composites (MMCs) material for the application of various industrial products. In the present paper, Aluminum (Al6061) hybrid composite is fabricated and reinforced with Silicon Carbide (SiC), Alumina (Al2O3), Zirconia (ZrSiO4) and agro-waste material, such as Rice Husk Ash (RHA) particles of various configurations. The amount of reinforcement varies SiC (0–2.5 wt%), Al2O3 (0–1.1 wt%), ZrSiO4 (0–0.5 wt%) and RHA (0–1.4 wt%). The effect of reinforcement SiC, Al2O3, ZrSiO4 and RHA on ultimate tensile strength (σut), yield strength (σyt), elongation, breaking strength (σb) and hardness has been studied. Experimental results revealed that hybrid metal matrix composites are improved for σut and σyt by 45.03% and 82.1%. The elongation and hardness of the composite are also enhanced by 19.43% and 12.72% from the base material.
GRAPHICAL ABSTRACT
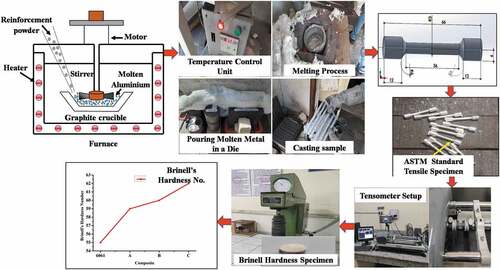
Introduction
Industrial and agricultural waste materials are increasing and creating disposal and management issues apart from contamination and intoxication to living beings. Solid waste, undesirable or unusable solid materials, can be classified based on their origin (industrial, household, civil construction, etc.); their contents (glass, metal, plastic, etc.); or their potential threat (toxic, flammable, radioactive, etc.). Prospective application of waste requires careful judgment supported by comprehensive methodological examination. When particular material segregated from trash is used directly as raw material is called recycling. Recycling can be of two types: In the first type, waste materials are directly utilized, and in the second type, waste can be repurposed as a raw material to make other goods. Recycling reduces the need for raw materials. Ore mining and subsequent processing require energy to derive virgin raw materials, and recycling reduces the carbon footprint on the environment by lowering the energy demand. For example, 1,000 kg of aluminum requires 8,000 kg of bauxite ore and 4,000 kg of chemicals, whereas recycled aluminum requires 95% less energy than virgin aluminum (Brubaker Citation1967). Another recent example is the Acheson technique, which needs extremely high temperatures to complete the reaction of silicon carbide reinforcement with aluminum matrices. The created SiC is used to produce the categorized end-product, which requires a significant amount of energy, apart from ecologically problematic carbon monoxide released during the process (Heimann Citation2010).
Fly ash (FA) and rice husk ash (RHA), formed as industrial waste during energy generation, have various applications. RHA is also used as reinforcement to fabricate matrix composites (MMCs). A MMC can be defined as a material that results in the mixture of two or more macro/micro/nano-constituents or consolidated combinations that be unlike in morphology or geometry (particles, fibers, flakes, and so on) and chemical composition following appropriate processing.
One constituent serves as the metallic matrix, while the other(s) serve as thermal (Ponnarengan et al. Citation2020), firming or/and functionality phases that can be “in-situ,” “ex-situ,” or together in origin, and can differ in size (with multi/mono-modal distribution, or ratio); the whole setup can be planned as a multilayer panel, monolith (Pech-Canul and Aldez Citation2015), or coatings/films with functionally graded or sandwich structure, with layer width that can be same or different synergistically (Pech-Canul and Aifantis Citation2014), the composite influences and maximizes the properties of each constituent (Mallik and Ekere Citation2013), causing in a functional or structural material with characteristics that the constituents could not achieve alone (Ponnarengan et al. Citation2020).
The following are five major reasons why little development has been witnessed in the previous decades in the application of agro-industrial waste materials for the production of metal MMCs:
There were no rules prohibiting the combustion of agro-waste materials (e.g., rice husk (RH), etc.) and the dumping of factory wastes (e.g., waste glass, etc.) a few decades ago.
MMCs must be manufactured at high temperatures, unlike polymer matrix composites. This fact raises a number of issues that should be sorted out to increase the exploitation of industrial agro-waste materials for MMCs:
Figuring out an appropriate calcination temperature to eliminate organic components while retaining all required chemical elements or ingredients for matrix firming.
In chemical treatment, selecting required reactants to eliminate undesirable chemical components.
Choosing an appropriate fabrication technique for MMC manufacturing with a suitable combination of parameters like process-temperature, pressure, time, matrix chemical composition, reinforcing wt%, and so on) to retain the needed qualities from waste materials. There was no motivation to address these challenges because traditional materials like alloys, plastics, and wood) met the majority of engineering requirements.
There has long been discussion that the calcination of agro-waste products is harmful to the environment. As calcination of agro-waste products does not always release more CO2 to the environment, as documented (Hall and Scrase Citation1998).
Customers lack trust due to a lack of knowledge of the properties of agro-industrial waste products. Composites made from waste materials perform equal to or better than traditional composite materials in most circumstances; clients are frequently worried about their quality and efficiency.
The aforementioned issues necessitate a period of incubation for fundamental scientific research and technological development, from laboratory to pilot plant and, eventually, at an industrial scale.
Despite the several research papers on RHA for various applications, only a few research papers with a wide range of references have been published that examine and address its usage in MMCs. As a result, the purpose of this paper is to present a study on the use of agro-waste materials in the fabrication of MMCs, deliberating the benefits and drawbacks of processing methods and the mechanical and physical properties of agro-waste materials and manufactured composites.
Metal Matrix Composites (MMCs) are getting attention due to their appealing mechanical and physical properties, and these are the most favorable materials for achieving improved mechanical properties (Bharath et al. Citation2006) like Elongation (E), Yield Strength (σyt), Hardness and Ultimate tensile strength (σut) due to the occurrence of micron size reinforcement particles in the MMCs (Saravanakumar, Sasikumar, and Sivasankaran Citation2014). MMCs have the metallic qualities of matrix alloys combined with the ceramic features of reinforcements, resulting in greater strength and service capabilities at increased temperatures (Hu, Zhao, and Li Citation2016). Magnesium (Mg), Aluminum (Al), Titanium (Ti), and their alloys are popular metallic matrices utilized in the manufacture of MMCs (Parikh et al. Citation2021). Aluminum Metal Matrix Composites (AMMCs) offer a wide range of usage in our everyday lives. There are several benefits to using particle reinforced AMMC materials over unreinforced Aluminum metal, including increased strength, specific modulus, enhanced stiffness, lightweight, a superior strength-to-density ratio, a small thermal expansion coefficient, custom-made electrical properties, high thermal conductivity (K), enhanced damping capabilities (ζ) and better wear resistance discs (Rahman and Rashed Citation2014). Within the matrix, reinforcing elements might take the shape of particles, continuous fibers, short fibers, or single filaments (Suthar and Patel Citation2018). AMMCs are now employed in managing heat, aerospace, industrial goods, and automotive applications such as engine pistons and brake discs (Manivannan and Sasikumar Citation2019). The matrix phase in AMMC is unalloyed aluminum (Carcea and Nedelcu Citation2012) or an alloy of it, while reinforcement is a non-metallic ceramic (Kumar et al. Citation2018) such as SiO2, SiC, Al2O3, Al – N, red mud, fly ash and B4C (Kala, Mer, and Kumar Citation2014). Al alloys are frequently utilized because of their increased damping capacity, outstanding corrosion resistance (Bhushan Citation2013), electrical and thermal conductivities and reduced density (Umanath, Palanikumar, and Selvamani Citation2013). AMMCs have been evaluated and proven to be effective in a variety of engineering fields, including structural and functional applications (Vigneshwaran, Uthayakumar, and Arumugaprabu Citation2019).
Generally, hard ceramic particles such as Zirconia (ZrSiO4), Silicon Carbide and Alumina (Al2O3) have been incorporated into an aluminum-based matrix to improve wear resistance, stiffness, strength, corrosion resistance, hardness and fatigue resistance. Silicon Carbide is chemically harmonious with aluminum (Al) and offers additional benefits such as good workability, high machinability, and superior thermal conductivity (Auradi, Rajesh, and Kori Citation2014). The need for cast AMMC incorporating hard ceramic dispersion particles has resulted from the requirement for lightweight, low-cost, and energy-efficient materials (Bains, Sidhu, and Payal Citation2016). Among the production techniques, traditional stir casting is a preferred processing method to produce AMMCs due to its wide range of materials, low cost, and processing parameters. Due to the stirring motion of the particles into the melts, stir casting provides greater matrix particle bonding (Kalaiselvan, Murugan, and Parameswaran Citation2011). As per current research investigations, selecting proper processing parameters such as stirring speed, duration, preheat temperature, the temperature of molten metal and feed rate of particles can result in homogenous mixing of matrix and reinforcement with excellent wetting (Ghandvar, Farahany, and Idris Citation2015).
The insertion of reinforcing phases with unique shapes and compositions might improve the physical and mechanical characteristics of composites. Rice husk ash (RHA), an oxygen source with a spiral-like and truss-like structure and silicon, can be employed as a one-of-a-kind reinforcing phase to meet these requirements (Deshmukh et al. Citation2012). Prior and present fabrication processes do not allow for full utilization of the RHA reinforcement’s potential since the natural structure may readily be destroyed during processing (Ghandvar, Farahany, and Idris Citation2015). Powder metallurgy (Deshmukh and Pathak Citation2012) and stir casting approaches (Prasad and Krishna Citation2010), for example, may result in the break of the as-burned ash’s spiral-like and truss-like structure (Prasad and Krishna Citation2011).
In this contribution, for the fabrication of metal matrix composites (MMCs), the authors present the utilization of agricultural and industrial waste materials, providing a detailed study of the challenges and opportunities for their full prospective usage through the careful analysis of a large and diverse reference source ranging from the oldest to the most recent. The novelty of this contribution rests, in addition to its topicality, in the showcase of crucial technical, statistical, and various properties of a wide range of waste materials classified into two major classes, namely, rice husk ash reinforced MMCs and other waste materials reinforced MMCs. Though rice husk ash has been used in a variety of applications, it appears that it has received little attention in the development of MMCs. The literature provided information in identifying the profitable and more demanding applications of rice husk ash, as well as key potential regions. Except for the recent usage of rice husk ash in the automobile sector, there is hardly any other waste material that has been repurposed for a particular industrial application. Under this perspective, one important purpose of this study is to bring the attention of academics, technologists/scientists, and industrialists to the usage of those materials for the manufacturing of MMCs by outlining five causes for the observed delay. A positive future may be predicted based on the tremendous advances made thus far in scientific and technical research.
The benefits and drawbacks of the various production procedures employed in the creation of MMCs, as well as their characteristics and usage, are examined. MMCs of high quality are produced using solid-state processes like powder metallurgy. The powder metallurgy approach entails uniform reinforcing distribution throughout the matrix material. SPS has the ability to provide homogenous sintering. HEBMS is required to provide uniform reinforcement distribution. Rapid Vacuum Sintering has the potential to be used for large-scale manufacturing with improved mechanical characteristics. Microwave sintering saves energy while improving physical and mechanical qualities. Solid state processing is restricted to simple-shaped components with minimal reinforcement content. The stir casting method is the most basic, cost-effective, and widely utilized technology in liquid state processing. The stir casting technique has various difficulties, mainly in maintaining wettability (intimate bonding between liquid and solid phase). Second, producing MMC with a homogenous particle distribution, minimal porosity, and superior mechanical characteristics is a problem. Unwanted chemical interactions between the matrix and the reinforcement, as well as poor wettability of the reinforcements with the molten matrix, result in a nonuniform particle dispersion. High porosity and micro flaws are caused by gas entrapment and slag in the melt. These difficulties can be solved by employing a suitable stir casting design for the manufacturing of, particularly, AMMCs, as explained in detail in the next section. Based on the results of this survey, it is determined that international research in the field of casting, particularly stir casting for the manufacturing of MMCs, is developing.
For the parboiling process of rice, rice mills use the husk for burning to generate the steam and the husk, after burning, turns into ash, called RHA, which is cost-effective reinforcement compared to commonly applied ceramic particles. The novelty of the current research work is the study of Rice Husk Ash (RHA) as reinforcement in the base Al6061 material. The study contains a variety of natural and industrial materials, such as SiC, Al2O3, ZrSiO4, and agricultural waste RHA, that have not been examined before. The current paper discusses in depth the synthesis methods, benefits and drawbacks, and physical and mechanical characteristics of produced composites. The objective of this research work is to investigate the mechanical characteristics of Al 6061 alloy unevenly reinforced with two distinct types of particles, reinforcement Al2O3, SiC, ZrSiO4 and sustainable material such as RHA, as well as the influence of these reinforcements on the mechanical properties of manufactured AMMCs. Stir casting is the most commonly used process for producing hybrid metal matrix composites (Krishna and Xavior Citation2014). Mechanical properties are assessed in accordance with ASTM standards utilizing an electronic tensometer and Brinell’s hardness tester.
Materials and methods
The ingot was made of Al6061 alloy with dimensions and weight of DIA 80 × 505 MM and 21 kg, supplied by Bharat Aerospace Metals Mumbai India, and the reinforcements were made of silicon carbide (SiC), aluminum oxide (Al2O3), rice husk ash (RHA), and zirconia (ZrSiO4), , supplied by SPEEDFAM (INDIA) Pvt. Ltd. The chemical composition of the aluminum ingot and initial reinforcement powders received from SPEEDFAM (INDIA) Pvt. Ltd., ASTRRA Chemicals Chennai Tamil Nadu, and Ceramique Industries Kolkata is mentioned in .
Table 1. Mechanical and physical properties of SiC, Al2O3, RHA and ZrSiO4.
The stir casting process was used to fabricate hybrid MMCs comprising Al6061, reinforcement SiC (0–2.5 wt%), Al2O3 (0–1.1 wt%), and ZrSiO4 (0–0.5 wt%) and RHA (0–1.4 wt%). show the schematic view and photographic view of the experimental setup of the stir casting process, respectively. The fabricated composites were machined in a CNC machine for performing various mechanical testing. shows the 3-D and schematic view of a tensile specimen as per ASTM standards. depicts the machine samples of a tensile specimen as per ASTM standard. The manufactured composite was subjected to a microstructure analysis in order to determine the distribution of reinforcing particles in the matrix alloy. Hardness and tensile strength were assessed.
The test results were juxtaposed to the Al6061 alloy to confirm the experiment. Al6061, having chemical composition as shown in , was chosen as a matrix material in this study. Reinforcement such as SiC particles with diameters of 3–5 µm, Al2O3 particles with diameters of 3–5 µm, ZrSiO4 particles with diameters of 10–30 µm (: Chemical and Physical Properties of SiC, Al2O3, RHA and ZrSiO4) and RHA particles with diameters of 10–30 µm (: Physical Properties) was used during the fabrication of composite material.
Table 2. Chemical composition of Al6061.
Table 3. Chemical and physical properties of Silicon Carbide (SiC), Al2O3, ZrSiO4 and RHA.
Table 4. Physical properties of RHA.
First, an identified quantity of Al alloy rods was kept in the Graphite crucible and melted at 850°C in an electric furnace. A stirring procedure was used to achieve homogeneous dispersion of reinforcing materials. A fine vortex is formed by swirling a melt for 10 min with a mechanical stirrer (Hashim, Looney, and Hashmi Citation1999). To improve wettability, the SiC, Al2O3, ZrSiO4 and RHA combination was warmed to 450°C in a separate furnace. The warmed SiC, Al2O3, ZrSiO4 and RHA combination was placed into a furnace holding molten Al6061 metal. While adding the material, a steady feed rate was maintained. The stirring motion was carried out with the assistance of an electric stirrer set to 450 rpm. From the crucible, the molten metal was poured into a hollow mold to harden at ambient temperature. The same production method was carried out repeatedly for hybrid MMCs with varied weight fractions of SiC, Al2O3, ZrSiO4 and RHA. depicts the composite reinforcement wt%.
Table 5. Composite reinforcement wt%.
The sample specimens were prepared for the examination of the microstructural and mechanical characteristics by machining the composite material. Brinell hardness testing under a load of 0.98 kN and 15 s dwell time has been performed to test the microhardness of the composites. An ER-3 Model electronic tensometer with a maximum capacity of 20 kN was employed to determine σut and σyt. The ultimate tensile strength (σut) and yield strength (σyt) of the specimen were determined using ASTM E8 standards.
The composites were metallographic alloy examined using an Olympus Optical Microscope (OM). The composite samples were sectioned and polished. Keller’s reagent was used to create the etching. This reagent contains 2.5 mL of HNO3. Cold mounting was done before polishing and etching. For Al and C, 1.0 mL HF, 1.5 mL HCl, and 95 mL water are commonly employed. The alloys are being investigated, and the grain size of the composite is fixed.
Materials for engineering purposes are often chosen based on qualities such as ultimate tensile strength, yield strength, modulus of elasticity, etc. The most regular way of choosing mechanical qualities is the tensile test. A tensile test was performed on an electronic tensometer setup in this study, as shown in and specification as per . The generated hybrid composite specimens A, B, and C were made in accordance with ASTM requirements. The yield strength and ultimate tensile strength (UTS) were determined by an electronic tensometer using ASTM E8 standards.
Table 6. Specification of tensometer.
The mechanical characteristics of Al6061 composites at various wt% were evaluated using ASTM standards. To determine the hardness of unreinforced alloy and RHA-reinforced composites, a typical Brinell hardness tester (specification shown in ) with a 500 kg and 10 mm steel ball indenter is employed. For each sample, an average of five readings were considered. The Brinell hardness machine was used to determine the hardness of Al6061 composites with different weights. This examination included five samples, with the indentation produced at different locations on each sample. The readings were taken, which resulted in the determination of the average hardness value, as well as an indentation on the right location of the reinforcing particles.
Table 7. Specification of hardness testing machine.
Results and discussion
Biomasses, particularly RH, have been employed to create electricity in recent years because a substantial amount of greenhouse gases and wastes are emitted. Eco-friendly and cleaner technologies are in focus to sustain economic development with less environmental impact (Yusoff Citation2006), the release of RHA in the environment has sparked widespread condemnation, owing to its long-term, carcinogenic, and bioaccumulative consequences, which have resulted in silicosis syndrome, weariness, asthma and loss of appetite (Foo and Hameed Citation2009). Rice husk may be used to reduce greenhouse gas emissions since plants collect CO2 for growth, and the same carbon is released during the burning of husk. The net quantity of CO2 emitted to the ambience for energy generation by biomass (Gaurav et al. Citation2020) consumption is practically zero during the whole life cycle (Hall and Scrase Citation1998).
RH is a source of energy and creates RHA as a copious by-product among the different recognized biomasses. As per the Food and Agriculture Organization of the United Nations (FAO) rice market monitor (RMM), the world rice crop in 2013 is predicted to be 741.4 Mt (Vlaev, Markovska, and Lyubchev Citation2003). At the revised amount of 741.4 Mt, global paddy output in 2013 would be 7.8 Mt more than the record 2012 harvest, a relatively small rise compared to 2010 and 2011 (Ghandvar, Farahany, and Idris Citation2015).
Another researcher investigated the mechanical characteristics of AMMC reinforced with RHA and metallurgical grade SiO2 with different % of Mg (0.5, 1, 2.5, and 5 wt%). For making the composites, amorphous SiO2 extracted from rice husk was stir-cast into the alloy samples in a 5 wt% proportion, and the technique was repeated for the metallurgical grade SiO2. The recovered SiO2 from RH had a wavelength of 32–56 nm, whereas the metallurgical grade SiO2 had an average size of 10 mm. It was observed that raising the Mg percentage up to 2.5 wt% in the molten alloy raised the hardness values in both manufactured composites.
It is due to the improved wettability of SiO2 particles and the production of a hard phase of spinel as well as a solid solution of Mg in the Al matrix in the presence of 2.5 wt% Mg. As a result, Al experiences severe lattice distortion, causing the development of minute grains with increased hardness. Nano-scale SiO2 formed from RH possesses greater reactivity and surface area with molten alloy than metallurgical grade SiO2, resulting in the creation of porosity in the former and reduced contact area with the matrix in the latter. The wear loss of an Al 2.5 wt% Mg composite with RH SiO2 was discovered to be lower than that of other composite samples. It was determined based on the SEM micrographs of the worn-out particles that the composite with 2.5% Mg and RH silica as Reinforcement had the fewest worn-out particles, corresponding to the highest hardness and least wear loss (Das et al. Citation1986).
Few researchers examined the characterization and mechanical characteristics of an A356-RHA stir cast composite (Prasad and Krishna Citation2010). As per a study, they utilized a similar process to manufacture ash from RH. As per result, with the increase of RHA particle proportion, there is an increase in UTS and hardness for composites, whereas density got decreased (Soltani et al. Citation2015).
Mechanical properties
Microstructure analysis
The mechanical characteristics of composites are greatly affected by the structure, density, and distribution of reinforcing particles. The scanning electron micrograph of the Al6061-SiC/Al2O3/RHA/ZrSiO4 composites is shown in , which confirms the dendritic structure. This is due to the quick solidification process termed super-cooling, in which an extremely fast cooling rate occurs, resulting in the formation of the dendritic structure. The SiC/Al2O3/RHA/ZrSiO4 particles are visible in , and the particle distribution is uniform.
As demonstrated in , the composites have a reduced dendritic structure and grain refinement due to the inclusion of SiC/Al2O3/RHA/ZrSiO4 particles. The inclusion of SiC/Al2O3/RHA/ZrSiO4 particles in composites has an effect on the solidification pattern. SiC/Al2O3/RHA/ZrSiO4 particles are prohibited throughout the solidification process by the use of purified α-Al grains. In , the micrographs show that the SiC/Al2O3/RHA/ZrSiO4 particles work as an efficient grain refiner. Smaller grain size is found along with SiC/Al2O3/RHA/ZrSiO4 particles, as shown in , and is assessed using the “linear intercept approach,” which is considered to calculate the average size of grain (PraveenKumar and Birru Citation2019). The grain structure in the composites gets refinement due to the presence of SiC/Al2O3/RHA/ZrSiO4 acting as a grain nucleation point. Aluminum granules solidified on SiC/Al2O3/RHA/ZrSiO4 particles, limiting the development of α-Al grains. More SiC/Al2O3/RHA/ZrSiO4 particles cause grain nucleation that limits the formation of α-Al grains. The grain refinements are directly proportional to the grain nucleation.
Gas trapped in the molten metal causes the occurrence of porosity in the MMC. As can be seen in composite fabrication, several gas bubbles have been formed as a result of environmental penetration. The “C” composite sample had no porosity, as indicated in , of SiC/Al2O3/RHA/ZrSiO4 reinforced composites.
EDS analysis
FE-SEM (Field Emission-Scanning Electron Microscope) with an EDX (energy-dispersive X-ray spectroscopy) device, namely Thermo Scientific Apreo, was used to perform energy-dispersive X-ray analysis (EDX spectra) on AMMHCs. The composition of the micro-composite was verified by EDX analysis, and spot spectra of the same as shown in demonstrate the existence of micro-SiC/Al2O3/RHA/ZrSiO4 particles in the matrix alloy with a low presence of oxygen compared to carbon and Al in the spectrum.
displays their relative proportion in the sample, and depicts the EDX spectra of AMMHCs that comprise a considerable amount of carbon, oxygen, and silicon. Other elements, such as Mg, Fe, and Zr, were present in minuscule amounts. As per the EDX spectra, the AMMHCs are stoichiometric. The EDX graph divulges that the main ingredient of SiC/Al2O3/RHA and ZrSiO4 is SiC.
Table 8. Chemical composition of AMMHCs.
Tensile test
In this work, as per ASTM – E8/E8 M–08 standard, the test specimen was prepared with a gauge length of 36 mm, a gauge diameter of 6 mm and a gripping surface length of 12 mm, and this specimen was used for tensile test. The specimens were examined for σut and σyt using an electronic tensometer. The results of the tensile test are given, and attributes such as σut, σyt, fracture stress, and elongation percentage are determined by the graph. depict the change in Yield strength (σyt), ultimate tensile strength (σut), elongation and breaking strength (σb) due to the addition of SiC, Al2O3, ZrSiO4 and RHA particles as reinforcement. The outcomes are compared to the matrix alloy. The addition of varying wt% of reinforcement SiC, Al2O3, ZrSiO4 and RHA to Al6061 improves the alloy’s σut and σyt. The results show that the increased interfacial bonding is due to the modest variation in Si concentration caused by the Al – SiC chemical interaction. The overall characteristics of metal-matrix composites have a significant dependency on the interface (Tham, Gupta, and Cheng Citation2001). It has been discovered that reinforcement particles distributed homogeneously in matrix metal create uniform mechanical properties for composites fabricated by stir casting (Rajmohan, Palanikumar, and Ranganathan Citation2013). Stir casting is used to create aluminum-based composites reinforced with Al2O3 and Gr particles, and discovered that the reinforcements were uniformly distributed (Radhika and Subramanian Citation2013).
It was also discovered that the inclusion of reinforcing particles enhanced the tensile strength and hardness of the composite. Interfacial connection heavily contributes to the strength of hard particle reinforcement. A perfectly bonded interface allows for more effective load distribution and transmission from the matrix metal to the reinforcement material, resulting in higher composite strengths.
The σut and σyt of the composites increase by up to 45.03% and 82.1%, with the addition of 1.5 wt% SiC, 1.1 wt% Al2O3, 0.7 wt% ZrSiO4 and 1.2 wt% RHA, owing to hard SiCp sharing strength with the soft Al matrix and resulting in increased resistance for an applied tensile load. As the wt% of SiC, Al2O3, ZrSiO4, and RHA increases, the strength trend becomes negative, and this tends to reduce the strength after 1.5 wt% SiC, 1.1 wt% Al2O3, 0.7 wt% ZrSiO4, and 1.2 wt% RHA. This might be related to the brittleness of reinforcing particles, which has a significant influence on reducing composite strength. Increasing the weight percentage of 1.5 wt% SiC, 1.1 wt% Al2O3, 0.7 wt% ZrSiO4 and 1.2 wt%, RHA has a reverse impact and reduces the strength. Properties, shape, and size of the reinforcements control the mechanical properties, which are attributed to the well-bonded interface that distributes and transfers the load from matrix metal to the reinforcement, thus resulting in enhanced E and σut (Wang, Wang, and Weatherly Citation1992).
Ductility
Ductility property (elongation percentage) of cast Al6061– SiC, Al2O3, ZrSiO4, and RHA particle composites influenced by SiC, Al2O3, ZrSiO4, and RHA concentration plotted in . The ductility of the composites reduces considerably and monotonically as the Al2O3, SiC, ZrSiO4 and RHA percentage increases. With the increase of reinforcement concentration from 1.5 wt% SiC, 1.1 wt% Al2O3, 0.7 wt% ZrSiO4 and 1.2 wt% RHA, the ductility decreases by roughly 25.15%. This reduction in ductility, as compared to the matrix metal alloy, is the most typical drawback in unevenly reinforced MMCs. The hard ceramic phase, which is susceptible to localized fracture initiation and enhanced embrittlement impact owing to the concentration of localized stress at the interface, might be linked to the loss of ductility.
Slip areas are formed as a result of the entrance of this second phase of hard ceramic. The reinforcing particles resist dislocation passage by either substantial inducing variations in the elastic behavior of the dispersoid and the matrix or producing stress fields in the matrix (Ramesh et al. Citation2009). depicts the relationship between %elongation and SiC, Al2O3, ZrSiO4 and RHA concentration. The line chart demonstrates that %elongation firstly increases from 19.43% at 1.5 wt% SiC, 1.1 wt% Al2O3, 0.7 wt% ZrSiO4 and 1.2 wt% RHA, then lowers to 25.15% at 2 wt% SiC, 1.1 wt% Al2O3, 0.6 wt% ZrSiO4 and 1.0 wt% RHA.
Breaking strength (σb)
depicts an experimental line chart that shows the fracture stress on the Y-axis and the function of SiC, Al2O3, ZrSiO4 and RHA concentration on the X-axis. As per graph, the fracture stress steadily rises from 156.6 N/mm2 at 1 wt% SiC, 1.1 wt% Al2O3, 0.8 wt% ZrSiO4 and 1.6 wt% RHA to 188.01 N/mm2 at 1.5 wt% SiC, 1.1 wt% Al2O3, 0.7 wt% ZrSiO4 and 1.2 wt% RHA.
As per the results, the reinforcement particles are dispersed evenly throughout the matrix alloy. Porosity has also been found to be lower. It was found that there is decent bonding between the reinforcement particulates and the matrix, which results in effective load distribution and transfer from the metal to the reinforcement.
Generally, particulate-reinforced AMMCs show higher fatigue strength, E and σut, than base matrix metal alloys (Yu et al. Citation1997). In the case of ceramic particle reinforced AMMCs, it is noticed that the strength rises when the volume percentage of ceramic increases and the size of the reinforcement in the composite decreases, at the expense of lower ductility (Wilson and Alpas Citation1996).
Hardness
According to the ASTM E10-07a standard, a test specimen diameter of 20 mm and length of 15 mm was prepared, and Brinell’s hardness test was conducted at room temperature. A steel ball indenter is used under the load of 500 kg during Brinell’s hardness testing to measure the hardness of Al6061 and its composites comprising reinforcement SiC (0–2 wt%), Al2O3 (0–1.1 wt%), ZrSiO4 (0–0.8 wt%) and RHA (0–1.6 wt%). Each value displayed is a six-measurement average. The outcome can be reproduced because all outcomes fall within a 5% deviation from the mean value. The outcome of the hardness test is shown in . It can be seen that the composite has a higher hardness than its cast matrix metal. Composites with a higher filler content have a higher toughness. The hardness of the Al6061–SiC, Al2O3, ZrSiO4 and RHA composite material rises by 12.72% as the SiC, Al2O3, ZrSiO4 and RHA concentration increases from different wt%. The reason for increased hardness is that the addition of SiC and ZrSiO4, which have high hardness, increases the composite’s hardness.
As the bulk hardness of AMMCs increased significantly with the addition of hard ceramic particles (Hamid, Citation2008). This is attributed to the higher particle volume percentage in the matrix metal material for the improved hardness of AMMC (Howell and Ball Citation1995). A researcher integrated silicon with Aluminum alloys and determined that a greater wt% of Si enhances composite hardness. Especially at higher loads, composites having second-phase volume content and the highest hardness are the most resistant to wear (Subramanian Citation1992).
As per research, microstructure analysis of RHA (rice husk ash) + SiC (8 wt% with RHA to SiC ratios 1:4, 2:3 and 0:1) demonstrated that particles were distributed uniformly. Since SiO2 has a lower hardness and elastic modulus than SiC, the hardness and tensile strength dropped as the wt% of RHA increased. The hardness and tensile strength of the RHA-reinforced products, on the other hand, are significantly higher than those of the non-reinforced AA 6061 alloy, supporting the notion that it may be employed as a viable material. The porosity level in Al 6061/RHA/SiC composites was much lower than 2.86%. As a result, these composites can be used in engineering applications as lightweight materials (Sarkar et al. Citation2018).
Remarks
Variety of industries, including cement, electronics, catalytic supports, and others (Ghandvar, Farahany, and Idris Citation2015), and it is now widely employed in the manufacture of hybrid MMC (Bahrami, Citation2016a) Though rice husk SiO2 is non-wettable by nature, embedding crystalline and amorphous SiO2-derived RHA onto SiC reinforcement up to 20% will not convert the system to non-wettable by Al-Si-Mg alloys (Bahrami, Citation2015a). For Al/SiC/RHA system, RHA acts as an oxygen donor, forming MgO and MgAl2O4 and resulting in the production of a hybrid composite. With amorphous RHA, the development of the detrimental phase of Al4C3 was abolished. In comparison to conventional Al/SiC composites, the hardness of the fabricated hybrid Al/SiC/RHA composite increased significantly. Few studies have successfully generated AMCs reinforced with RHA particles utilizing various techniques such as stir casting (Bahrami, Citation2015b).
Aluminum matrix composites (AMCs) are a popular type of sophisticated engineering material in today’s world. AMCs have a unique mix of qualities that are sought after in a variety of sectors, and they may be used to replace traditional aluminum alloys. AMCs are presently used in the component design for aircraft, automobiles, marine, defense assemblies, structures and facilities. The expensive cost of creating AMCs may restrict their widespread use. Using industrial waste and natural minerals as reinforcing particles is one way to reduce manufacturing costs. In comparison to commonly applied ceramic particles, RHA provides a cost-effective reinforcement. RHA is a kind of agricultural waste that is abundant around the world and pollutes the land and the environment, whereas appropriate exploitation of this farm waste would benefit the environment.
Conclusions
In this paper, the stir casting approach was used to successfully fabricate Al6061/SiC/Al2O3/ZrSiO4/RHA AMCs with even intra-granular dispersion of RHA particles. Key findings of the research work on Al6061 Hybrid Metal Matrix Composites are mentioned below:
Rice Husk Ash (RHA) is one of the most cost-effective and low-density natural reinforcements that can be recommended for the fabrication of sustainable hybrid composite.
Liquid metallurgy technology with a stir casting approach was effectively used to fabricate Al6061–SiC, Al2O3, ZrSiO4, and RHA composites with filler amounts up to 6 wt%.
The microstructural investigations demonstrated that the particles in the matrix metal system were distributed uniformly.
As observed, with the increase in filler level, the hardness of the composites increased. The composites’ ultimate tensile strength characteristics are observed to be greater than those of the basic matrix and Al6061– reinforcement SiC (0-2.5 wt%), Al2O3 (0-1.1 wt%), ZrSiO4 (0-0.5 wt%) and RHA (0-1.4 wt%).
The tensile strength of SiC, Al2O3, ZrSiO4 and RHA composites is higher than that of other composites examined.
Overall, Al6061– reinforcement SiC (0-2.5 wt%), Al2O3 (0-1.1 wt%), ZrSiO4 (0-0.5 wt%) and RHA (0-1.4 wt%) composites have superior mechanical characteristics when compared to Al6061 alloy.
A biomass (Rice Husk) based power plant, an energy source, produces the agro-waste RHA that is used/recycled as reinforcement to fabricate Al MMC, helping in reducing the carbon footprint.
Finally, industrial and agro-waste should be in focus for systematic research for getting their application to new areas by harnessing their potential as valuable resources.
Key Highlights
Making use of Rice Husk Ash (RHA), an agricultural waste, to form sustainable hybrid composites using the stir casting process.
Appropriate exploitation of agriculture farm waste would benefit the environment.
An aluminum-based matrix is responsible in improvement of wear resistance, stiffness, strength, corrosion resistance, hardness, and fatigue resistance.
Traditional stir casting is a preferred processing method to create Aluminum Metal Matrix Hybrid Composites (AMMHCs).
Overall, Al6061– reinforcement composites have superior mechanical characteristics when compared to conventional Al6061 alloy.
Credit authorship contribution statement
Alok Ranjan: Conceptualization, Methodology, Writing – original draft. Harish Kumar: Supervision, Conceptualization, Methodology, Writing – original draft, Writing – review & editing. Leeladhar Nagdeve: Supervision, Writing – original draft, Writing – review & editing. Abhishek Mishra: Supervision, Conceptualization, Methodology, Writing – original draft, Writing – review & editing. Gajendra Kumar Gaurav: Writing – original draft, Writing – review & editing, Jiří Jaromír Klemeš: Writing – review & editing, Proofreading, Supervising, Funding acquisition.
Acknowledgment
The research has been in collaboration with the National Institute of Technology, Delhi. This research was also supported by a project, “Sustainable Process Integration Laboratory - SPIL”, project No. CZ.02.1.01/0.0/0.0/15_003/0000456 funded by EU as “CZ Operational Programme Research, Development and Education”, Priority 1: Strengthening capacity for quality research and by the Grant Agency of the Czech Republic under Project No. 21-45726L collaboration with the Slovenian Research Agency (projects No. N2-0138 and J7-3149 and research core funding No. P2-0412, P2-0421 and P2-0414).
Disclosure statement
No potential conflict of interest was reported by the author(s).
Additional information
Funding
References
- Auradi, V., G. L. Rajesh, and S. A. Kori. 2014. Preparation and evaluation of mechanical properties of 6061al–b4cp composites produced via two-stage melt stirring. Materials and Manufacturing Process 29 (2):194–200. doi:10.1080/10426914.2013.872265.
- Bahrami, A., M. I. Pech-Canul, C. A. Gutierrez, and N. Soltani. 2015a. Effect of rice-husk ash on properties of laminated and functionally graded Al/SiC composites by one-step pressureless infiltration. Journal of Alloys and Compounds 644:256–66. doi:10.1016/j.jallcom.2015.04.194.
- Bahrami, A., M. I. Pech-Canul, C. A. Gutiérrez, and N. Soltani. 2015b. Wetting and reaction characteristics of crystalline and amorphous SiO2 derived rice-husk ash and SiO2/SiC substrates with Al–Si–Mg alloys. Applied Surface Science 357 Part A.:1104–13. doi:10.1016/j.apsusc.2015.09.137.
- Bahrami, A., U. Simon, N. Soltani, S. Zavareh, J. Schmidt, M. I. Pech-Canul, and A. Gurlo. 2016b. Ecofabrication of hierarchical porous silica monoliths by ice- templating of Rice Husk Ash. Green Chemistry 19 (1):188–95. doi:10.1039/C6GC02153K.
- Bahrami, A., N. Soltani, M. I. Pech-Canul, and C. A. Gutiérrez. 2016a. Development of metal-matrix composites from industrial/agricultural waste materials and their derivatives. Critical Reviews in Environmental Science and Technology 46 (2):143–208. doi:10.1080/10643389.2015.1077067.
- Bains, P. S., S. S. Sidhu, and H. S. Payal. 2016. Fabrication and machining of metal matrix composites: A review. Materials and Manufacturing Process 31 (5):553–73. doi:10.1080/10426914.2015.1025976.
- Bharath, V., M. Nagaral, V. Auradi, and S. A. Kori. 2006. Preparation of 6061al–al2o3 MMC’s by stir casting and evaluation of mechanical and wear properties. Tribology International 39 (6):213–20. doi:10.1016/j.mspro.2014.07.151.
- Bhushan, R. K. 2013. Optimisation of cutting parameters for minimising power consumption and maximiing tool life during machining of Al alloy SiC particle composites. Journal of Cleaner Production 39:242–54. doi:10.1016/j.jclepro.2012.08.008.
- Brubaker, S. 1967. Trends in the world aluminium industry, p. 260. Baltimore, MD, USA: The John Hopkins Press for Resources for the Future.
- Carcea, I., and D. Nedelcu. 2012. Technology for obtaining composite material with metallic matrix and Si-C particles. Materials and Manufacturing Process 27 (6):694–701. doi:10.1080/10426914.2011.602786.
- Das, S., T. K. Dan, S. V. Prasad, and P. K. Rohatagi. 1986. Aluminium alloy-rice husk ash particle composites. Journal of Materials Science Letters 1986 (5):562–64.
- Deshmukh, P., J. Bhatt, D. Peshwe, and S. Pathak. 2012. Development and characterisation of Al based MMC by using RHA and metallurgical grade SiO2 with varying percentage of Mg. Nano Trends: A Journal of Nanotechnology and Its Applications 12 (2):1–10.
- Deshmukh, P., and S. Pathak. 2012. Influence of varying SiO2 % on the mechanical properties of Al based MMC. Transactions of the Indian Institute of Metals 65 (6):741–45. doi:10.1007/s12666-012-0196-8.
- Foo, K., and B. Hameed. 2009. Utilisation of rice husk ash as novel adsorbent: A judiciousrecycling of the colloidal agricultural waste. Current Opinion in Colloid & Interface Science 152:39–47. doi:10.1016/j.cis.2009.09.005.
- Gaurav, G. K., T. Mehmood, L. Cheng, J. J. Klemeš, and D. K. Shrivastava. 2020. Water hyacinth as a biomass: A review. Journal of Cleaner Production 277:122214. doi:10.1016/j.jclepro.2020.122214.
- Ghandvar, H., S. Farahany, and J. Idris. 2015. Wettability enhancement of SiCp in cast A356/SiCp composite using semisolid process. Materials and Manufacturing Process 30 (12):1442–49. doi:10.1080/10426914.2015.1004687.
- Hall, D., and J. Scrase. 1998. Will biomass be the environmentally friendly fuel of thefuture? Biomass & Bioenergy 15 (4–5):357367. doi:10.1016/S0961-9534(98)00030-0.
- Hamid, A.A., Ghosh, P.K., Jain, S.C., Ray, S.,The influence of porosity and particles content on dry sliding wear of cast in situ Al(Ti)-Al2O3(TiO2) composite, Wearthis link is disabled, 2008, 265(1–2), pp. 14–26
- Hashim, J., L. Looney, and M. S. J. Hashmi. 1999. Metal matrix composites: Production by the stir casting method. Journal of Materials Processing Technology 92-93:1–7. doi:10.1016/S0924-0136(99)00118-1.
- Heimann, R. B. 2010. Classic and advanced ceramics: From fundamentals to applications, p. 539. Germany: John Wiley & Sons.
- Howell, G. J., and A. Ball. 1995. Dry sliding wear of particulate-reinforced aluminium alloys against automobile friction materials. Wear 181–183:379–90. doi:10.1016/0043-1648(95)90045-4.
- Hu, Q., H. Zhao, and F. Li. 2016. Effects of manufacturing processes on microstructure and properties of Al/A356–B4C composites. Materials and Manufacturing Process 31 (10):1292–300. doi:10.1080/10426914.2016.1151049.
- Kalaiselvan, K., N. Murugan, and S. Parameswaran. 2011. Production and characterisation of AA6061–B4C stir cast composite. Materials & Design 32 (7):4004–09. doi:10.1016/j.matdes.2011.03.018.
- Kala, H., K. K. S. Mer, and S. Kumar. 2014. A review on mechanical and tribological behaviours of stir cast aluminium matrix composites. Procedia Materials Science (6), 1951–60. doi: 10.1016/j.mspro.2014.07.229.
- Krishna, M. V., and A. M. Xavior. 2014. An investigation on the mechanical properties of hybrid metal matrix composites. Procedia Engineering 97:918–24. doi:10.1016/j.proeng.2014.12.367.
- Kumar, A. H., R. Prasad, A. Srivastava, M. Vashista, and M. Z. Khan. 2018. Utilisation of industrial waste (Fly ash) in synthesis of copper-based surface composite through friction stir processing route for wear applications. Journal of Cleaner Production 196:460–68. doi:10.1016/j.jclepro.2018.06.029.
- Mallik, S., and N. Ekere. 2013. Metal matrix composites as thermal management materialsfor automotive applications. In Engineered metal matrix composites: Forming methods, material properties and industrial applications, ed. L. Magagnin, p. 113126. New York, USA: Nova Science Publishers, Inc.
- Manivannan, A., and R. Sasikumar. 2019. Exemplary encapsulate feeding in stir casting for quality composites. Materials and Manufacturing Process 34 (6):689–94. doi:10.1080/10426914.2019.1566962.
- Parikh, V. K., V. J. Badheka, A. D. Badgujar, and N. D. Ghetiya. 2021. Fabrication and processing of aluminium alloy metal matrix composites. Materials and Manufacturing Process 36 (14):1604–17. doi:10.1080/10426914.2021.1914848.
- Pech-Canul, M. I., and E. Aifantis. 2014. A revamped paradigm of composite materials:From ancient-to-modern concepts and applications. In F. Kongoli, (ed.), Sustainable Industrial Processing Summit/SHECHTMAN International Symposium, Montreal. QC, Canada, 449458.
- Pech-Canul, M. I., and S. Aldez. 2015. Contemporary concepts and applications in the fieldof composites materials, SAMPE. Baltimore, MD: Society for the Advancement of Material and Process Engineering.
- Ponnarengan, H., L. Kamaraj, S. R. Balachandran, and S. KatharBasha. 2020. Reusing exhausted alkaline battery powder as reinforcement in AA6061 composites and mechanical characterisation. Energy Sources, Part A: Recovery, Utilisation, and Environmental Effects 1–14. doi:10.1080/15567036.2020.1795308.
- Prasad, D. S., and A. R. Krishna. 2010. Fabrication and characterisation of A356. 2-Rice husk ash composite using stir casting technique. International Journal of Engineering Science and Technology 2:7603–08.
- Prasad, D. S., and A. R. Krishna. 2011. Production and mechanical properties of A356. 2/RHA composites. International Journal of Advanced Science and Technology 33:51–58.
- PraveenKumar, B., and A. K. Birru. 2019. Strengthening of Al-4.5% Cu alloy with the addition of silicon carbide and bamboo leaf ash. International Journal of Structural Integrity 10 (2):149–61. doi:10.1108/IJSI-03-2018-0018.
- Radhika, N., and R. Subramanian. 2013. Effect of Reinforcement on wear behaviour of aluminum hybrid composites. Tribology - Materials, Surfaces & Interfaces 7 (1):36–41. doi:10.1179/1751584X13Y.0000000025.
- Rahman, M. H., and H. M. M. Rashed. 2014. Characterisation of silicon carbide reinforced aluminium matrix composites. Procedia Engineering 90:103–09. doi:10.1016/j.proeng.2014.11.821.
- Rajmohan, T., K. Palanikumar, and S. Ranganathan. 2013. Evaluation of mechanical and wear properties of hybrid aluminium matrix composites. Transactions of Nonferrous Metals Society of China 23 (9):2509–17. doi:10.1016/S1003-6326(13)62762-4.
- Ramesh, A., J. N. Prakash, S. S. Gowda, and A. S. Appaiah Sonnappa. 2009. Comparison of the mechanical properties of AL6061/Albite and AL6061/graphite metal matrix composites. Journal of Minerals and Materials Characterization and Engineering (JMMCE), USA (JMMCE), USA 8 (2):93–106.
- Saravanakumar, A., P. Sasikumar, and S. Sivasankaran. 2014. Synthesis and mechanical behaviour of AA 6063-X wt% Al2O3- 1% Gr (X = 3, 6, 9 and 12 wt%) hybrid composites. Procedia Engineering 97:951–60. doi:10.1016/j.proeng.2014.12.371.
- Sarkar, S., A. Bhirangi, J. Mathew, R. Oyyaravelu, P. Kuppan, and A. S. S. Balan. 2018. Fabrication characteristics and mechanical behaviour of Rice Husk Ash-silicon carbide reinforced Al-6061 alloy matrix hybrid composite. Materials Today: Proceedings 5 (5):12706–18. doi:10.1016/j.matpr.2018.02.254.
- Soltani, N., A. Bahrami, M. I. Pech-Canul, and L. A. González. 2015. Review on the physicochemical treatments of rice husk for production of advanced materials. Chemical Engineering Journal 264:899–935. doi:10.1016/j.cej.2014.11.056.
- Subramanian, C. 1992. Some considerations towards the design of a wear resistant aluminium alloy. Wear 155 (1):193–205. doi:10.1016/0043-1648(92)90118-R.
- Suthar, J., and K. M. Patel. 2018. Processing issues, machining, and applications of aluminium metal matrix composites. Materials and Manufacturing Process 33 (5):499–527. doi:10.1080/10426914.2017.1401713.
- Tham, L. M., M. Gupta, and L. Cheng. 2001. Effect of limited matrix reinforcement interfacial reaction on enhancing the mechanical properties of aluminium–silicon carbide composites. Acta Materialia 49 (16):3243–53. doi:10.1016/S1359-6454(01)00221-X.
- Umanath, K., K. Palanikumar, and S. T. Selvamani. 2013. Analysis of dry sliding wear behaviour of al6061/sic/al2o3 hybrid metal matrix composites. Composites Part B: Engineering 53:159–68. doi:10.1016/j.compositesb.2013.04.051.
- Vigneshwaran, S., M. Uthayakumar, and V. Arumugaprabu. 2019. Development and sustainability of industrial waste-based red mud hybrid composites. Journal of Cleaner Production 230:862–68. doi:10.1016/j.jclepro.2019.05.131.
- Vlaev, L., I. Markovska, and L. Lyubchev. 2003. Non-Isothermal kinetics of pyrolysis of ricehusk. Thermochimica Acta 406 (1–2):17. doi:10.1016/S0040-6031(03)00222-3.
- Wang, N., Z. Wang, and G. C. Weatherly. 1992. Formation of magnesium aluminate (spinel)in cast SiC particulate-reinforced Al(A356) metal matrix composites. Metallurgical Transactions A 23 (5):1423–30. doi:10.1007/BF02647325.
- Wilson, S., and A. T. Alpas. 1996. Effect of temperature on the sliding wear performance of Al alloys and Al matrix composites. Wear 196 (1–2):270–78. doi:10.1016/0043-1648(96)06923-2.
- Yu, S. Y., H. Ishii, K. Tohgo, Y. T. Cho, and D. Diao. 1997. Temperature dependence of sliding wear behaviour in SiC whisker or SiC particulate reinforced 6061 aluminum alloy composite. Wear 213 (1–2):21–28. doi:10.1016/S0043-1648(97)00207-X.
- Yusoff, S. 2006. Renewable energy from palm oil – innovation on effective utilization of waste. Journal of Cleaner Production 14 (1):87–93. doi:10.1016/j.jclepro.2004.07.005.