ABSTRACT
Phosphorus (P)-containing monomer (P-monomer) was firstly prepared by condensation reaction between 2-hydroxyethyl methacrylate and phosphorus pentoxide (P2O5) and then used to prepare P-containing poly-styrene-acrylate (P-PSA) emulsion by semi-continuous emulsion polymerization. The components of the prepared P-monomer were characterized by potentiometric titration method. The chemical composition of the P-PSA co-polymer was studied by Fourier-transform infrared spectra. The storage stability properties of P-PSA emulsion were tested by Ca2+, centrifugal and mechanical stability tests. The thermal stability and flame retardancy of the P-PSA co-polymer were studied by thermogravimetric analysis, limiting oxygen index and UL-94 method. The results show that stable P-PSA emulsions can be successfully prepared, and the latex particles present a spherical structure. When the P-monomer content is 30 wt%, the P-PSA co-polymer can pass the UL-94 test (V0 level) and the char yield is 54 wt% at 700°C. Scanning electron microscopy results indicate that incorporation of the P-monomer shows a condensed-phase flame-retardant effect. This study provides useful suggestions for the application of the flame-retardant P-PSA emulsion in the coating industry.
KEYWORDS:
1. Introduction
Poly-acrylate (PA) or poly-styrene-acrylate (PSA) emulsion has been widely used in coatings, adhesives, paper finishes and so on for their good performances, low price and environmentally friendly properties [Citation1,Citation2]. However, flammability of PA (or PSA) polymer is a major disadvantage in applications that require high flame resistance, especially papers, textiles, plastic coatings for electronic accessories and so on. Thus, research is required to enhance the flame-retardant properties of the PA or PSA polymer for their applications in those areas [Citation3,Citation4]. Flame-retardant agents were normally added to improve their flame retardancy. However, adding flame-retardant agents to the polymers has many disadvantages such as poor compatibility and a severe reduction of the mechanical properties of the final product. Therefore, in recent years, covalently incorporating flame-retardant elements (e.g., P, N, Si) to the polymer backbones was considered a better solution because not only this method can avoid the problems caused by adding flame-retardant agent, but also the flame retardancy of modified polymer is remarkably improved even if the content of the flame-retardant element is in a low level [Citation5,Citation6]. Among many flame-retardant elements, organophosphorus has attracted many researchers’ attention due to its highly efficient flame retardancy and environmentally friendly property [Citation7,Citation8].
O’Brien [Citation9,Citation10] has already brought up the idea of using P-containing (meth)acrylate monomer (dialkylphosphonoalkyl acrylate and methacrylates) as a potential reactive flame retardant for PA co-polymer half a century ago. Years later, Ebdon [Citation11–Citation14], Pricere [Citation15–Citation20] and other coworkers reported the synthesis of a group of P-containing (meth)acrylate monomers, including diethyl(methacryloyloxymethyl) phosphonate, diethyl(acryloyloxymethyl) phosphonate, diethyl(metha cryloyloxyethyl) phosphate and diethyl(acryloyloxyethy) phosphate, diethylphosphonateand triethylphosphate, etc., and studied the flame retardancy of their co-polymer with (methy) acrylate or styrene. The results indicate that those P-containing co-polymers possess better flame retardancy than the pure PA co-polymer. However, the P-containing (meth)acrylate monomers reported by Ebdon and Price are made from expensive or toxic materials. Besides, the production procedure is tedious and under harsh reaction conditions, which are not feasible for industrial application. Therefore, there is an urgent demand for an economic method of preparing flame-retardant PA (or PSA) co-polymers to meet the needs of industrial application.
As a matter of fact, condensation reaction can proceed between the hydroxy group of (meth) acrylate monomer P2O5. Ogliari [Citation21] successful prepared phosphate monomer (methacryloyloxypentyl phosphate and bis-methacryloyloxypentyl methacrylate) by condensation reaction between 5-hydroxypentyl methacrylate (HPMA) and P2O5. Both of the reagents are non-toxic, and the condensation reaction condition was rather mild compared to the studies of Ebdon [Citation11–Citation14] and Price [Citation15–Citation20]. But Ogliari’s [Citation21] method was never applied to flame-retardant polymer. In this paper, P-monomer was prepared by the condensation reaction between P2O5 and 2-hydroxyethyl methacrylate (HEMA). Compared to HPMA, HEMA is an inexpensive industrial raw material and can be obtained easily. Then, the P-monomer was used to prepare P-PSA emulsion by emulsion polymerization. The properties of the prepared P-PSA emulsion and the flame retardancy of the P-PSA co-polymer were studied.
2. Experimental
2.1. Materials
Reactive surfactant DNS-86 was purchased from Shuangjian Trade Co. Ltd. in Guangzhou of China. The other chemicals were purchased in their reagent grade and used without further purification including styrene (St), butyl acrylate (BA), phosphorus pentoxide (P2O5), N-methylol acrylamide (N-MA), ammonium persulfate (APS) and hydroquinone. Water was purified by a Milli-Q system (Millipore).
2.2. Preparation of P-monomer
The condensation reaction can proceed between the –OH group of HEMA and the O = P-O group from the P2O5. The reaction mechanism is as shown in . Due to the fact that the chemical structure of P2O5 has three O = P-O groups, theoretically, the obtained product might include mono-phosphate ester, di-phosphate ester, tri-phosphate ester and pyrophosphoric acid. Di-phosphate ester and tri-phosphate ester have multiple C = C groups; therefore, they might act as a cross-linking agent and might lead to the instability during the emulsion polymerization process. In our study, the mole ratio of –OH group to O = P-O group was first kept at about 1:1 to make sure that the major components of the product were mono-phosphate ester, while tri-phosphate ester is almost not formed due to the steric hindrance effect. The details are as follows: 130.2 g HEMA (1.00 mol) and 0.50 g hydroquinone were charged into a 250-mL three-necked round-bottom flask equipped with a stirrer. The temperature was cooled to about 5°C while stirring. Then, 71.0 g P2O5 (0.50 mol) was charged into the flask for five times, and the temperature was maintained under 15°C. When P2O5 was completely charged, the system was maintained under 15°C for 1 h and raised to 40°C and keep for 1 h and then raised to 70°C and keep for another 3 h. Then, another 13.0 g (0.10 mol) HEMA was added into the system to further react with the residue P2O5. The obtained product was analyzed by 1H-NMR and potentiometric titration method [Citation22], and the results show that P-monomer was successfully prepared as expected and is shown in (1H-NMR in CDCl3:δ(ppm) 1.9 (s, 2H), 4.2 (s, 3bH), 4.4 (s, 3aH), 5.6 (s, 1H), 6.1 (s, 1H), 6.7 (s, 4H)), and the prepared P-monomer (the unreacted HEMA is excluded) was composed of 79.6 wt% mono-phosphate ester, 15.0 wt% di-phosphate ester and 5.4 wt% phosphoric acid (formed by the hydrolysis of pyrophosphoric acid during titration).
2.3. Preparation of P-PSA emulsion
P-PSA emulsion was prepared by semi-continuous emulsion polymerization. All the polymerizations were carried out in a 500-mL four-neck flask equipped with reflux condenser, mechanical stirrer and dropping funnels and heated in the water bath. First, an appropriate amount of DNS-86 and NaHCO3 was introduced into the four-neck flask charged with an appropriate amount of deionized water. After complete dissolution of DNS-86 in water, the temperature was raised to 75°C, and the stirring rate was kept at about 250 rpm. Then, the pre-emulsified mixture monomers (St, BA, N-MA), APS aqueous solution and the prepared P-monomer were added drop by drop into the flask simultaneously lasting 3 h. After finishing dropping, the temperature was raised to 80°C and maintained for another 2 h. Then, the obtained latex emulsion was cooled to room temperature, and the pH of the emulsion was adjusted to about 6 by NaOH solution (5 wt%). The recipe of the prepared P-PSA emulsion is presented in .
Table 1. Recipe of the prepared P-PSA emulsion.
2.4. Preparation of P-PSA co-polymer testing specimens
The prepared P-PSA emulsions were put into a PTFE (Poly tetra fluoroethylene) mold and maintained at 60°C for 96 h under vacuum (0.06 MPa) to remove water and then dried at 100°C for 1 h and cured at 130°C for 1 h. After curing, all samples were free cooled to room temperature to prevent the stress cracking.
2.5. Characterization
The monomer conversion was measured by gravimetric analysis. The Ca2+ stability property of latex is tested by adding 1 mL 5 wt% CaCl2 solution into 5 mL prepared P-PSA emulsion; the centrifugal stability property was tested by putting the P-PSA emulsion into a centrifugal machine and keeping 30 min at the speed of 5000 rpm; and the mechanical stability was tested by putting the emulsion into a shear machine and keeping 30 min at the speed of 3000 rpm. The storage stability properties mentioned above are evaluated by observing whether flocculation appeared after the test. Fourier-transform infrared (FTIR) spectra analyses of the resulting co-polymers were performed on a 380 spectrometer (Nicolet Instruments, USA). The UL 94 vertical burning classification was obtained using a burning chamber according to DIN IEC 60695-11-10. The limiting oxygen index (LOI) was obtained with an Fire Testing Technology (FTT) LOI burning chamber according to ISO 4589-2.14. The samples were 120 mm long, were 13 mm wide and had a thickness of 3 mm, and each of the data was the average of the three test results. Thermogravimetric analysis (TGA) was performed by a Q550 TGA System (TA Instruments, USA) under the air atmosphere at a heating rate of 20°C/min from 50°C to 700°C. The average particle size of P-PSA latex was measured by a Malvern particle size analyzer (ZS-Nano-3000 Malvern Instruments Ltd., Britain). The microstructure of the char residue was performed by a scanning electron microscopy (SEM, S-3700N, Japan). SEM images of surface morphology were taken by an EVO18 scanning electron microscopy (Carl Zeiss Jena, Co., Germany). Samples were coated with a thin layer of gold before testing to prevent electric discharge. The element analysis was operated with an OXFORD INCA250 energy dispersive spectroscopy (Oxford Instruments Co., Britain) united from SEM. The chemical characteristics of the prepared phosphorus monomer were tested by 600 M superconducting nuclear magnetic resonance spectrometer (Bruker Optics, Germany). The particle size of the P-PSA emulsion was observed by transmission electron microscope (TEM) JEM-1400plus (Japan Electronics, Corporation, Japan).
2.6. Results and discussion
2.6.1. FTIR spectra of P-PSA co-polymer
The PSA and P-PSA emulsions were demulsified with CaCl2 solution and then washed three times with ethanol before analysis, and the FTIR spectra are shown in .
We can see in that both curves a and b show the characteristic stretching peaks of -CH3 at 2956 and 2870 cm−1, stretching peak and distortion vibration peak of -CH2 at 2930 and 1452 cm−1, the stretching vibration of C = O at 1730 cm−1 and the adsorptions from the benzene ring of the styrene monomer units at 1500, 1600 and 3027 cm−1. Comparing curve b to curve a, there were two new strong peaks at 985 and 1025 cm−1, which could be ascribed to the group of P-OH and P-O-C. Besides, the vibration absorption peak of P = O at 1250 cm−1 [Citation21] and the stretching vibration adsorption peak of C-O-C at 1235 cm−1 overlapped with each other, which leads to the broadening of the absorption peaks at 1200–1300 cm−1. The FTIR spectra result proved that the P-monomers have successfully grafted to the P-PSA co-polymer molecular chain.
2.6.2. Effects of P-monomer content on emulsion polymerization
Effects P-monomer content on the monomer conversion rate, coagulum content, storage stability of P-PSA emulsions and average latex particle size were studied, and the results are shown in .
Table 2. Effects of P-monomer content on the prepared P-PSA emulsion.
From we can see that the monomer conversion rate decreases as the P-monomer content increases. This is due to the fact the increasing content of H3PO4 in the emulsion system would lead to the decrease of pH (high H+ concentration) of the emulsion system, which will destabilize the electric double layer on the surface of the latex particles and, therefore, brings negative effect to the emulsion polymerization and also leads to the decrease of monomer conversion rate [Citation23]. However, due to the hydrophilic nature of the P-monomer, the increase of P-monomer content is beneficial to the emulsion polymerization stability and therefore leads to the decrease of the coagulum content and average particle size of the prepared P-PSA latex particles. Besides, the prepared P-PSA emulsion presents excellent Ca2+, centrifugal and mechanical stability, indicating that the prepared P-PSA emulsion has excellent storage stability for industrial application. shows TEM images of emulsions with different P-monomer contents.
Figure 4. TEM images of emulsions with different P-monomer contents: (a) 0, (b) 10%, (c) 20%, (d) 30% and (e) 40%.
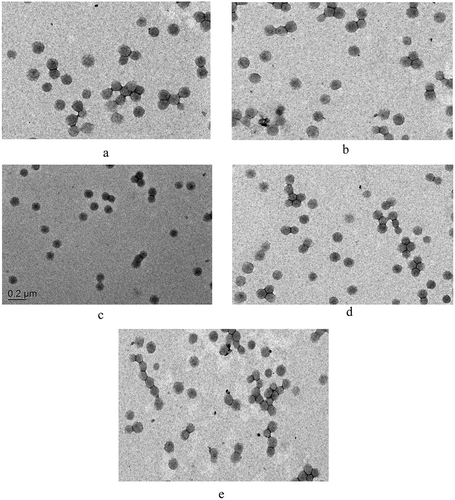
It can be seen from that the latex particles are spherical and uniform in particle size, and the size is basically consistent with the Dynamic Light Scattering (DLS) test results.
2.6.3. TGA
TGA was used to investigate the thermal stability of the P-PSA co-polymer with various P-monomer contents, and the results are shown in .
From we can see that the thermal stability of the co-polymer decreases as the P-monomer content increases when the temperature is under 250°C, which is attributed to the lower stability of the P–O–C bond as compared to the typical C–C bond. However, when the temperature is higher than 300°C, the thermal stability and the char yield of the co-polymer increase as the P-monomer content increases. When the P-monomer content is 30.0 wt%, the char residue of the P-PSA co-polymer at 600°C is 31.3 wt%. This result is attributed to the fact that the degradation of P-containing groups under air atmosphere are easy to form H3PO4 which help generates heat-resistant residues, thereby resulting in high char yields. The char can effectively prevent heat transmission and diffusion, reduce heat release rate and therefore level up the flame retardancy of the P-PSA co-polymer.
2.6.4. Effects of P-monomer content on flame retardancy of P-PSA co-polymer
The flame retardancy of P-PSA co-polymers with various P-monomer contents was evaluated by measuring their LOI values and conducting a UL-94 test.
As indicated in , the LOI values of the P-PSA co-polymer increase greatly as the P-monomer content increases. It can also be seen that the incorporation of P-monomer into the polymer chain can effectively level up the flame retardancy of the P-PSA co-polymer. In addition, the UL-94 test was also applied to examine the flame retardancy of the P-PSA co-polymer, and the vertical burning result shows that the P-PSA co-polymer can pass the V-0 rating when the co-polymer contained 30 wt% P-monomer. This flame-retardant property can meet many industrial application requirements.
Table 3. Effects of P-monomer content on flame retardancy of P-PSA co-polymers.
2.6.5. Microstructure and element composition of char residue of P-PSA co-polymer
SEM was used to observe the surface and interior microstructure of char residue of P-PSA co-polymer (with 30 wt% P-monomer) after the UL-94 test, and the results are shown in . The element composition of P-PSA co-polymer before and after the burning test was characterized by EDS test, and the results are shown in .
Figure 6. Morphology and components of char residue of P-PSA co-polymer: (a) exterior and (b) interior.
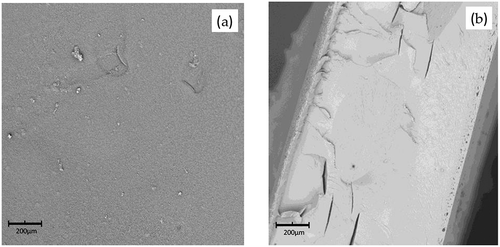
Table 4. Element composition of P-PSA (30 wt% P-monomer) resin content before and after burning.
From we can see that the char residue of P-PSA co-polymer displays a compact charred layer both on the outer surface and the inner structure. Besides, from EDS results ( and ), we can see that the char residue of P-PSA both mainly composed of C, O and P elements, but the weight percent of C element increases from 66.68 wt% to 83.30 wt%, while the O element decreases from 29.92% to 13.30%, which further indicating that the increasing of P element has the retardancy to form a carbon char structure. This carbon char residue structure can resist both mass and heat transfer and acted as barriers to segregate the transportation of heat and combustible gas, resulting in the reduction of the heat release and increase of char yield. Therefore, the P-PSA resin exhibits good flame retardancy. These results are consistent with the aforementioned TGA and flame-retardant tests.
3. Conclusion
P-monomer was prepared by condensation reaction between HEMA and P2O5 and used to prepare P-PSA emulsion in this study. FTIR spectra show that P-monomer was covalently incorporated into the co-polymer molecular chain. Stability tests show that the prepared P-PSA emulsion has excellent storage stability. TGA and flame retardancy test result shows that the incorporation of P-monomer into the co-polymer can greatly increase the char yield and its flame retardancy. When the P-monomer content is 30 wt%, the P-PSA co-polymer can pass the UL-94 V-0 level and the char yield can reach 31.3 wt%. This flame-retardant property can meet many industrial application requirements. The micro-morphology and chemical components (SEM and EDS) of the char residue indicate that the covalently incorporating P-monomer onto the polymer backbones presents a condensed-phase flame-retardant effect. It is expected that the prepared P-PSA emulsion will enable the industrial application.
Acknowledgments
The authors are grateful for the financial support by the National Key R&D Program of China (2017YF0308100), Ministry of Education Project (6141A02011704) and the Open Fund of the State Key Lab of Pulp and Paper Engineering (201834).
Disclosure statement
No potential conflict of interest was reported by the authors.
Additional information
Funding
References
- Li KQ, Lei HM, Zeng XR, et al. Preparation of a flame retardant phosphorus-containing polyacrylate/α-zirconium phosphate nanocomposite through in situ emulsion polymerization. RSC Adv. 2017;78(7):49290–49298.
- Lin J, Chen XY, Chen CY, et al. Durably antibacterial and bacterially antiadhesive cotton fabrics coated by cationic fluorinated polymers. ACS Appl Mater Interfaces. 2018;10(7):6124–6136.
- Lindsay CI, Hill SB, Hearn M, et al. Mechanisms of action of phosphorus based flame retardants in acrylic polymers. Poly Int. 2015;49(10):1183–1192.
- Qian X, Tai Q, Song L, et al. Thermal degradation and flame-retardant properties of epoxy acrylate resins modified with a novel flame retardant containing phosphorous and nitrogen. Fire Safety Sci. 2014;11:883–894.
- Wen PY, Wang XF, Feng XM, et al. A novel UV-curing flame retardant film with significantly intumescent effect. Polym Degrad Stab. 2015;119:288–294.
- Lu SY, Hamerton I. Recent developments in the chemistry of halogen-free flame retardant polymers. Prog Poly. 2002;27(8):1661–1712.
- Wang XF, Xing WY, Song L, et al. Flame retardancy and thermal properties of novel UV-curing epoxy acrylate coatings modified by phosphorus-containing hyperbranched macromonomer. J Polym Res. 2013;20(7):1–11.
- Qian XD, Song L, Hu Y, et al. Combustion and thermal degradation mechanism of a novel intumescent flame retardant for epoxy acrylate containing phosphorus and nitrogen. Ind Eng Chem Res. 2011;50(4):1881–1892.
- O’Brien JL, Park E, Lane CA US Patent 2,934,555. 1960.
- O’Brien JL, Park E, Lane CA US Patent 3,030,347. 1962.
- Banks M, Ebdon JR, Johnson M. Influence of covalently bound phosphorus-containing groups on the flammability of poly (vinyl alcohol), poly (ethylene-co-vinyl alcohol) and low-density polyethylene. Polymer. 1993;34(21):4547–4556.
- Banks M, Ebdon JR, Johnson M. The flame-retardant effect of diethyl vinyl phosphonate in copolymers with styrene, methyl methacrylate, acrylonitrile and acrylamide. Polymer. 1994;35(16):3470–3473.
- Ebdon JR, Price D, Hunt BJ, et al. Flame retardance in some polystyrenes and poly (methyl methacrylate)s with covalently bound phosphorus-containing groups: initial screening experiments and some laser pyrolysis mechanistic studies. Polym Degrad Stab. 2000;69:267–277.
- Ebdon JR, Hunt BJ, Joseph P, et al. Thermal degradation and flame retardance in copolymers of methyl methacrylate with diethyl (methacryloyloxymethyl) phosphonate. Polym Degrad Stab. 2000;70:425–436.
- Price D, Pyrah K, Hull TR, et al. Ignition temperatures and pyrolysis of a flame retardant methyl methacrylate copolymer containing diethyl (methacryloyloxymethyl) phosphonate units. Polym Int. 2000;49:1164–1168.
- Price D, Pyrah K, Hull TR, et al. Flame retarding poly(methyl methacrylate) with phosphorus-containing compounds: comparison of an additive with a reactive approach. Polym Degrad Stab. 2001;74:441–447.
- Price D, Pyrah K, Hull TR, et al. Flame retardance of poly(methyl methacrylate) modified with phosphorus-containing compounds. Polym Degrad Stab. 2002;77:227–233.
- Price D, Bullett KJ, Cunliffe LK, et al. Cone calorimetry studies of polymer systems flame retarded by chemically bonded phosphorus. Polym Degrad Stab. 2005;88:74–79.
- Price D, Bullett KJ, Cunliffe LK, et al. Thermal behavior of covalently bonded phosphate and phosphonate flame retardant polystyrene systems. Polym Degrad Stab. 2007;92:1101–1114.
- Price D, Bullett KJ, Cunliffe LK, et al. Thermal behavior of covalently bonded phosphonate flame retarded poly(methyl methacrylate) systems. Polym Adv Technol. 2008;19:710–723.
- Ogliari FA, da Silva EO, da Silveira LG, et al. Synthesis of phosphate monomers and bonding to dentin: esterification methods and use of phosphorus pentoxide. J Dent. 2008;36(3):171–177.
- Tian X, Dong WZ. Determination of nonoester and diester contents in alkyl phosphate. Print Dyeing Auxiliary. 2000;17(3):29–30.
- Cao TY, Liu QP, Hu JS. The synthesis principle, performance and application of polymer emulsion [M].Beijing: Chemical Industry Press; 2007. p. 120–121.