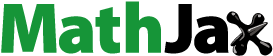
ABSTRACT
In this study, DICY (dicyandiamide)-containing novolac (NN) was first prepared, and then DOPO (9,10-Dihydro-9-oxa-10-phosphaphenanthrene-10-oxide) was introduced to react with the unsaturated bonds from DICY to obtain a novel phosphorus-nitrogen-containing novolac resin (PNN), which was used as a curing agent for epoxy resins. The curing condition was confirmed by a non-isothermal curing kinetics study. The thermal stability and flame retardancy of the cured epoxy resin system were studied by thermogravimetric analysis (TGA), limited oxygen index (LOI) measurement, UL-94 test and cone calorimeter. The morphology of the burned chard residues was observed by Scanning electron microscopy (SEM). The results show that epoxy resin cured by the prepared PNN curing system presents excellent flame retardancy. The cured resin system, which contains only 1.31wt% phosphorus and 2.48wt% nitrogen, can achieve UL 94 V-0 rating.
1. Introduction
Epoxy resins have been widely used in coatings, electronic materials, adhesives, and composites for their outstanding properties, such as good mechanical properties, high adhesion strength, low shrinkage, and excellent chemical resistance [Citation1]. However, the flammability of epoxy resins is a major disadvantage which severely limits their utilization in fields that require high flame resistance [Citation2–Citation6]. Normally, flame-retardant agents were added to improve the flame retardancy of epoxy resins. However, the added flame retardants would cause many disadvantages such as poor compatibility, migration, and even severe reduction of the mechanical properties. In recent years, covalently incorporating flame-retardant elements (e.g., P, N, Si) onto the polymer backbones by reactive flame retardants was considered to be a better solution. On the one hand, this method can avoid the problems caused by adding flame-retardant agents. On the other hand, many reports have proved that the flame retardancy of polymer modified with reactive flame retardant is remarkably improved even if the contents of the flame-retardant element are at a low level [Citation5,Citation6]. Among all of the flame retardants, phosphorus-containing flame retardants and nitrogen-containing flame retardants have attracted many researchers’ attention due to their high-efficiency flame retardancy and environmental-friendly property [Citation7,Citation8].
It is well known that epoxy resins must form a three-dimensional network with curing agents to perform their outstanding properties. Therefore, the flame-retardant element can be introduced into the cured polymer chain structure either from the epoxy resin or from the curing agent. In general, the incorporation of flame-retardant element into the epoxy resin is achieved by reacting the epoxy group with the reactive flame retardant. Among them, 9,10-Dihydro-9-oxa-10-phosphaphenanthrene-10-oxide (DOPO) is the most frequently studied reactive phosphorus-containing flame retardant and was proved to be an excellent flame retardant [Citation9–Citation12]. However, the consumption of epoxy group would not only lower the cross-linking degree of the cured epoxy resin and therefore bring negative impacts on their mechanical property, but also deteriorates other relevant material properties, in particular the glass transition temperature (Tg). Therefore, in recent years, studies on the flame retardancy of the epoxy resin system endowed by curing agent have attracted wide attention. Dicyandiamide (DICY) and novolac are both frequently used curing agents that endow epoxy resins with high Tg and thermal stability [Citation13–Citation15]. However, novolac contains no flame-retardant element and therefore cannot improve the flame retardancy of the cured epoxy resin system greatly. DICY contains a high content of N element and shows potential application as a flame retardant curing agent, but the compatibility of DICY with epoxy resin is poor.
In this study, DICY-containing novolac (NN) was first prepared; then, DOPO was introduced to react with the unsaturated bonds from DICY to obtain a novel phosphorus-nitrogen-containing novolac resin (PNN), which can act as a curing agent for epoxy resin. The chemical structure of the PNN was characterized by FTIR and 31P NMR. The non-isothermal curing kinetics of the O-cresol-novolac epoxy resin (CNE) cured by the prepared PNN were investigated by differential scanning calorimeter (DSC). Thermal stability and flame retardancy of the cured epoxy resin were studied by thermogravimetric analysis (TGA), limited oxygen index (LOI) measurement, UL-94 test and cone calorimeter. The morphology of the burned chard residue was observed by Scanning electron microscopy (SEM). The testing results show that the prepared PNN curing agent can endow epoxy resin with excellent flame retardancy.
2. Materials and methods
2.1. Materials
O-cresol-novolac epoxy resin (CNE) with EV (Epoxy Value) 0.45mol/100g was purchased from NanYa Plastics Co. Ltd. 9,10-dihydro-9-oxa-10-phosphaphenanthrene-10-oxide (DOPO) was purchased from Eutec Chemical Co., Ltd. (Shanghai). Phenol, dicyandiamide and oxalic acid were purchased from Guangzhou Chemical Reagent Factory. Paraformaldehyde was purchased from Tianjin Damao Chemical Reagent Factory. Novolac (PN, PF8013) with a hydroxyl equivalent weight of about 107 was purchased from Jinan Shengquan Group Share Holding Co., Ltd. Triphenyl phosphine (Ph3P) was purchased from Aladdin. 2-Methoxyethanol was purchased from Tianjin Fuyu Fine Chemical Co. Ltd.
2.2. Synthesis of phosphorus-nitrogen-containing novolac resin (PNN)
PNN was synthesized according to the following steps. Phenol (75.2 g, 0.8 mol), paraformaldehyde (27.0 g, 0.9 mol), dicyandiamide (16.8 g, 0.2 mol) and 1.8 g oxalic acid as catalyst were introduced into a 250-mL three-necked round-bottomed glass flask equipped with a stirrer, reflux condenser and thermometer. The reaction mixture was stirred at 90°C for 3 h to obtained Nitrogen-containing Novolac resin (NN). Then, 2-Methoxyethanol (80.0 g) and DOPO (43.2 g, 0.2 mol) were added into the system. Afterwards, the mixture was stirred at 130°C for another 2 h. After being cooled down to room temperature, the mixture was poured into deionization water. The colloid precipitate was washed two times with deionized water and dried at 105°C in a drying oven for 2 h to obtain the prepared phosphorus-nitrogen-containing novolac resin, which was defined as PNN1. PNN2 was prepared in the same manner using phenol (56.4 g, 0.6 mol), paraformaldehyde (27.0 g, 0.9 mol), dicyandiamide (33.6 g, 0.4 mol), 1.8 g oxalic acid, DOPO (86.4 g, 0.4 mol) and 2-Methoxyethanol (80.0 g). The synthesis route of the PNN is shown in .
2.3 Preparation of cured epoxy resin specimens
PN, PNN1 and PNN2 were used as curing agents for CNE to prepare cured epoxy resins. The stoichiometric formulations for CNE/PN, CNE/PNN1 and CNE/PNN2 systems with various phosphorus and nitrogen content are listed in , where the sum mole amount of amino and phenol groups is equal to the epoxy groups. Otherwise, 0.2wt% Ph3P, as a curing accelerator, was added to CNE/PN, CNE/PNN1 and CNE/PNN2 systems. Every system was mixed and stirred at 120 °C until a homogeneous solution was obtained. The mixture was then vacuum-degassed in a mold and sequentially cured for 1 h at 140 °C, 1 h at 160 °C, 1 h at 180 °C and 1 h at 200 °C, respectively, according to the curing kinetics study in Section 3.2. Then, all samples were cooled slowly to room temperature in order to avoid cracking.
Table 1. Composition of the cured epoxy resin specimens.
2.4 Characterization
Fourier Transform Infrared (FT-IR) spectra were recorded with KBr pellet by VERTEX33 FT-IR spectrophotometer (Bruker, Germany). 31P nuclear magnetic resonance (NMR) spectra were obtained from Bruker DRX 600 spectrometer by using DMSO as solvent. Differential scanning calorimetry (DSC) scans were obtained from samples of approximately 5–10 mg using a DSC Q200 (TA, USA) in the range of 0–300 °C under a nitrogen atmosphere. Thermogravimetric analysis (TGA) was performed using a TGA Q5000 (TA, USA) at a heating rate of 20 °C/min under both nitrogen and air atmosphere from room temperature to 800°C. LOI measurement was conducted on an oxygen index instrument (Fire Testing Technology Co., Ltd, UK) with the sheet dimension of 130 × 6.5 × 3.2 mm3 according to ASTM D-2863-77. The vertical burning test was carried out on a UL 94 flammability meter (Fire Testing Technology Co. Ltd., UK) with the sheet dimension of 130 mm×13 mm×3.2 mm. Cone calorimeter test was carried out on an FTT cone calorimeter with the sheet dimension of 100 mm×100 mm×3 mm according to ISO5660 under an external heat flux of 45 kW/m2. The morphology of residues collected after the cone calorimeter test was observed by a Phenom G2 Pro scanning electron microscope (SEM) with an accelerating potential of 5 kV.
3. Results
3.1. Characterization of PNN
The FTIR spectra of PNN2, NN and DOPO are shown in and the 31P NMR spectra of DOPO and PNN2 are shown in .
As is shown in , curve (a) displays the FT-IR spectra of DOPO and the absorption peak at 2430 cm-1 is attributed to the P-H group. Curve (b) displays the FT-IR spectra of NN and the absorption peak at 2180 cm-1 is attributed to the -C ≡ N group. While form curve (c) we can see that the peak at 2430 cm-1 cannot be detected and the peak at 2180 cm-1 decreases greatly, which indicates the reaction between the P-H group of DOPO and the -C ≡ N group of the NN occurred as expected. Moreover, from we can also see that the 31P NMR spectrum of DOPO shows peaks at 14.55 and 15.82 ppm, while the 31P NMR spectrum of the PNN2 shows a single peak at 12.33 ppm. The 31P NMR characterization results further confirm that the chemical structure of the prepared PNN2 is prepared as is depicted in .
3.2 Curing behavior and kinetics of CNE/PNN2 system
The non-isothermal curing kinetics of CNE/PNN2 system was studied by DSC and the results are shown in . Ozawa’s method was used to obtain the apparent activation energy during the curing process. Ozawa’s method is expressed by Equation (1).
presents the DSC thermogram for CNE/PNN2 system heated at 5, 10, 15 and 20 °C/min. The obtained linear plot of lgθ versus 1000/Tp is illustrated in . The apparent activation energy of CNE/PNN2 system, which is obtained from the slope of the corresponding straight line according to Ozawa’s methods, is calculated to be 84.3 kJ/mol.
The initial temperature (Ti), peak temperature (Tp) and final temperature (Tf) of the exothermic process at different heating rate during DSC test are shown in . The linear plots of Ti, Tp and Tf versus the heating rate (θ) are shown in . The Ti, Tp and Tf of the exothermic process are about 140 °C, 160 °C and 200 °C, respectively, when the heating rate is zero. The exothermic process of CNE/PNN2 system when cured in drying oven is considered to be similar to the exothermic process in DSC test when the heating rate is close to zero. Therefore, the curing conditions of CNE/PNN system were set to be 140 °C for 1 h, 160 °C for 1 h, 180 °C for 1 h and 200 °C for 1 h.
Table 2. Ti, Tp and Tf of the heat release process at different heating rate.
3.3 Thermal properties of the cured epoxy resin
The thermal decomposition behaviors of CNE/PN, CNE/PNN1 and CNE/PNN2 systems were evaluated by TGA in nitrogen () and air atmosphere (), respectively. The initial degradation temperatures for 5% weight loss (T5%) and 10% weight loss (T10%), and the residual char yield are listed in .
Table 3. Thermal properties of cured epoxy resin systems.
As shown in , the initial degradation temperatures (T5% and T10%) decreased with the increase of phosphorus content due to the lower stability of the O-P-C bond as compared to the typical C-C bond. The char yield of the cured resin increases as the increase of P content which is due to the reason that incorporated P element can promote the formation of char residue during burning. However, we can observe that the char yield of the cured resin system in N2 atmosphere is much higher than in air atmosphere. This is because the main-chain structure of the cured epoxy resin system is mainly a benzene ring linked by methylene group, which is easy to form a carbon structure when pyrolysis in N2 atmosphere. In addition, we can also detect that the effects of P content on the char residue of the cured resin system are much greater when in air atmosphere. According to our previous study [Citation16], this is because the DOPO group in the polymer chain decomposed and generated phosphoric acid or polyphosphoric acid which promoted the char yield in air atmosphere, but mainly decomposed and generated PO· free radical and benzofuran in N2 atmosphere.
3.4 Flame retardancy of the cured resin systems
The vertical burning test and the LOI values are used to value the flame retardancy of the cured epoxy resin systems, Cone calorimetry test was used to investigate the peak of heat release rate (pk-HRR), average of heat release rate (av-HRR) and average of effective heat of combustion (av-EHC) of the cured epoxy resins, the results are listed in . The HRR and THR curves of the cured epoxy resin are shown in and , respectively.
Table 4. Flame retardancy and combustion parameters of cured epoxy resins.
It can be observed from that the LOI values of the cured epoxy resins increased significantly with the increase of P and N content. Cured epoxy resin system with only 1.31wt% P content and 2.48wt% N content could reach an LOI of 29.2% and pass the V-0 rating of UL-94 classification. We can also see that the HRR and THR decreased significantly with the increase of P and N content which indicates the excellent flame retardancy of epoxy resin cured by PNN. The av-EHC also decreased greatly when using PNN as curing agent which proves that an effective gaseous-phase flame-retardant mechanism exists when the PNN cured resin system was under a fire.
3.5 Micro-morphology of the burned char
Micro-morphology of the char residues of PNN cured epoxy system is shown in .
Figure 11. SEM images of char residue (A1) CNE/PNN1 exterior; (A2) CNE/PNN1 interior; (A3) enlargement of A2; (B1) CNE/PNN2 exterior (B2) CNE/PNN2 interior; (B3) enlargement of B2.
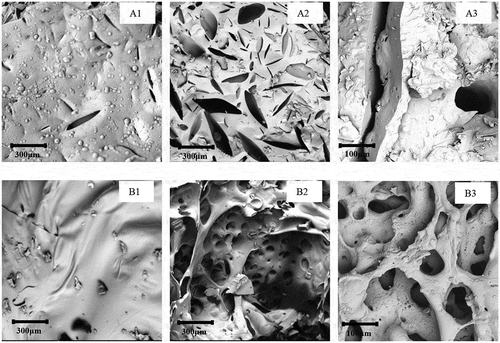
We can see from A1) and B1) that the surface of the char residues from a more compact and dense structure With the increase of the P content in the cured resin system, which further indicates that the incorporation of P can greatly promote the formation of the char yield at the surface and therefore can effectively resist heat transfer and retard the degradation of underlying polymer materials. Moreover, we can also see from A2 and A3) in and B2 and B3) that the interior char residue presents a more hollow and loose structure with the increases of N content, indicating that more nonflammable gaseous were released during the decomposition, which can dilute the concentration of oxygen and take away heat [Citation17,Citation18]. The micro-structure of the char residues proves that both the condensed-phase and gaseous-phase flame-retardant mechanisms exist in the cured resin system during its combustion process.
4. Conclusion
PNN, a novel flame-retardant curing agent for epoxy resins, was successfully designed and synthesized. The chemical structure of the prepared PNN was confirmed by FTIR and 31P NMR. The apparent curing activation energy and the curing condition of CNE/PNN2 system were obtained according to the DSC test result. Epoxy resin systems with various phosphorus and nitrogen contents were prepared. Flame-retardant test results showed that the cured resin system containing only 1.31wt% phosphorus and 2.48wt% nitrogen can achieve UL 94 V-0 rating and LOI value reaches 29.2%. The TGA, cone calorimeter test and SEM observation of the char residue results revealed that both the condensed-phase and gaseous-phase flame-retardant mechanism existed in the cured resin system during the combustion process.
Acknowledgments
The authors are grateful for the financial support by the National Key R&D Program of China (2017YF0308100), Ministry of Education Project (6141A02011704) and The Open Fund of the State Key Lab of Pulp and Paper Engineering (201834).
Disclosure statement
No potential conflict of interest was reported by the authors.
Additional information
Funding
References
- Fan LJ, Xiang L, Soo JP. Synthesis and application of epoxy resins: a review. J Ind Eng Chem. 2015;29:1–11.
- Muriel R, Sebastian W, Manfred D. Recent developments in halogen free flame retardants for epoxy resins for electrical and electronic applications. Materials. 2010;3(8):4300–4327.
- Weihua X, Alvianto W, Shumei L, et al. Highly effective flame retarded epoxy resin cured by DOPO-based co-curing agent. Polym Degrad Stab. 2015;122:44–51.
- Miaojun X, Guangrui X, Yang L, et al. Synthesis of a novel flame retardant based on cyclotriphosphazene and DOPO groups and its application in epoxy resins. Polym Degrad Stab. 2016;123:105–114.
- Toldy A, Anna P, Csontos I, et al. Intrinsically flame retardant epoxy resin-fire performance and background – part I. Polym Degrad Stab. 2007;92:2223–2230.
- Sergei VL, Andrew MP, Edward DW, et al. New developments in flame retardancy of epoxy resins. Polym Degrad Stab. 2005;88:57–62.
- Mengmei Z, Alfons B, Xiaodong L. Brominated flame retardants and the formation of dioxins and furans in fires and combustion. J Hazard Mater. 2016;304:26–39.
- Maria PL, Aliaksandr IB, Marco Z, et al. Thermal decomposition of fire retardant brominated epoxy resins cured with different nitrogen containing hardeners. Polym Degrad Stab. 2007;92:1088–1100.
- Khalifah AS, Sabyasachi G. An overview of some recen advances in DOPO-derivatives: chemistry and flame retardant applications. Polym Degrad Stab. 2015;113:119–134.
- Ionela DC, Diana S, Tachita VB, et al. A straightforward, eco-friendly and cost-effective approach towards flame retardant epoxy resins. J Mater Chem. 2014;2:16230–16241.
- Toldy A, Anna P, Csontos I, et al. Intrinsically flame retardant epoxy resin–fire performance and background – part II. Polym Degrad Stab. 2008;93: 2007–2013.
- Jianhua H, Jiye S, Jiangqing Z, et al. Isothermal curing kinetics of a flame retardant epoxy resin containing DOPO investigated by DSC and rheology. Thermochim Acta. 2016;632:56–63.
- Yuanqin X, Zhuojuan J, Yanyan X, et al. Development of a DOPO-containing melamine epoxy hardeners and its thermal and flame-retardant properties of cured products. J Appl Polym Sci. 2013;10:4352–4358.
- Shengxiong C, Chinghsuan L. Flame-retardant epoxy resins with high glass transition temperatures from a novel trifunctional curing agent: dopotriol. J Polym Sci Part A. 2005;43:2862–2873.
- Shieh. JY, Chunshan W. Synthesis of novel flame retardant epoxy hardeners and properties of cured products. Polymer. 2001;42:7617–7625.
- Yanchong Z, Guilong X, Yun L, et al. Preparation of flame retarded epoxy resins containing DOPO group. Thermochim Acta. 2016;643:33–40.
- Rong Y, Binbin M, Hui Z, et al. Preparation, thermal degradation, and fire behaviors of intumescent flame retardant polypropylene with a charring agent containing pentaerythritol and triazine. Ind Eng Chem Res. 2016;55(18):5298–5305.
- Limin G, Chunpeng C, Yunjun L. Preparation and performance evaluation of phosphorus-nitrogen synergism flame-retardant water-borne coatings for cotton and polyester fabrics. J Polym Res. 2016;23(4):64.