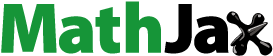
ABSTRACT
Poly(hydroxybutyrate-co-hydroxyvalerate) (PHBV) has recently caught more and more attention due to its renewability, good mechanical and barrier properties, as well as marine biodegradability. However, the severe thermal degradation during processing is a major drawback and limits its application. In this work, the thermal stability of PHBV during melt-processing was investigated by incorporating reactive agents. Various contents of Di(tert-butylperoxyisopropyl)benzene (DB), Triallyl isocyanurate (TAIC) and multi-functional epoxy chain extender (ECE) were used. The mixing torque, mechanical and thermal properties were studied. The results revealed that the mixing torque of PHBV gradually decreased during 10 min of melting time and eventually dropped to 2 N.m. Upon adding ECE, the mixing torque slightly increased but still decreased during 10 min period. For the system consisting of DB/TAIC or DB/TAIC/ECE, the mixing torque reached the equilibrium and their values were roughly twofold higher than PHBV alone. The possible crosslinking reaction and torque reversion were predominantly observed when adding high contents of DB and TAIC. 1 H NMR spectra suggested the reaction of DB/TAIC and PHBV. Young’s modulus and tensile strength of system consisting of DB at 0.3 phr, TAIC at 0.1 phr and ECE at 0.5 phr increased from 1440 and 40.4 MPa to 1803 and 55.5 MPa, respectively. TGA thermograms showed that the onset temperature and inflection point were improved when adding DB/TAIC and ECE. From the findings, it indicated that the combination of DB/TAIC and ECE was one of the simplest and effective ways to improve the melt viscosity without sacrificing the mechanical properties.
1. Introduction
Polyhydroxybutyrate-co-hydroxyvalerate (PHBV) as a family of Poly(hydroxyalkanoates) (PHAs) has become popular among researchers due to its renewability and biodegradability. This group of polymer is a polyester derived from microorganism, including bacterial fermentation of starting raw sugars or lipids. The marine biodegradability as well as good mechanical properties comparable to Polypropylene make it very attractive in terms of the sustainability of renewable resources and circular economy. However, low thermal stability of PHBV is one of the main disadvantages that has been frequently reported. The thermal processing of PHBV results in the severe thermal degradation through beta elimination random chain scission resulting in the declination of molecular weights and viscosity during melt processing [Citation1,Citation2]. In order to maintain the desired properties for certain applications, the thermal stability of PHBV must be improved. In other aspect, the thermal degradation of PHBV should be prevented.
H. Xiang et al. [Citation2] reported that Mn of PHBV rapidly decrease to 20% of initial Mn of its initial Mn after applied heat at 180°C for 30 min. Similar study was conducted by Y. Aoyagi and his coworkers [Citation3], they studied the thermal degradation of Polyhydroxybutyrate (PHB) and found that the number average degree of polymerization of PHB rapidly decreased from 1000 to about 500 after applied temperature at 170°C for 10 min. As a result of this severe problem, several researches [Citation4–10] have concentrated on the improvement of the thermal stability of PHB or PHBV. There are a few existing methods aimed to ease the thermal degradation. For instance, the molecular weights can be maintained through the addition of peroxide [Citation9,Citation11] or chain extender [Citation4,Citation5,Citation7] and other coagents [Citation6,Citation9,Citation10]. To some extents, the side reaction might result in the adverse effect such as when adding peroxide alone in the processed conditions. A. Rezaei and coworker [Citation9] reported that complex viscosity of PHB was decreased from 607 Pa.s to 435 Pa.s and 444 Pa.s after applied DCP at 0.2 and 0.3 phr. X. Zhao et al. [Citation12] also illustrated the reduction of complex viscosity of PHBV treated peroxide. This indicated that the addition of peroxide induced degradation reaction instead of the light crosslinking reaction in melt processing. B. Fei et al. [Citation11] reported an increasing of PHBV melt index from 12.48 to 34.09 g/10 min after applied with DCP 0.17%wt. However, the reduction of melt index was observed when further increased DCP content to 3 phr with melt index at 6 g/10 min and gel content more than 50% as a result of crosslinking reaction. The appropriate amounts of peroxide should be taken into account due to the undesired reactions such as chain scission or heavy crosslinking reaction. In addition, B. Immirzi et al. [Citation13] reported that the reduction of inherent viscosity of peroxide treated PHB from 2.09 to 0.69 dl/g after treated PHB with 5%DCP in PHB solution under nitrogen atmosphere and temperature at 120°C for 24 h. This result confirmed that peroxide could induced degradation reaction of PHB result in the decreased viscosity.
Coagents are multifunctional monomers with high reactivity to free radicals or other reactions, which can be used in peroxide-induced crosslinking by increasing the reactive sites or the rate of reaction results in the reduction of the side reactions. These reactive agents can be classified into two types. Type I coagents increase both the rate of reaction and the reactive sites such as bismaleimide and methacrylates coagent, whereas Type II coagents increase the reactive site during free radical reaction such as allyl-containing cyanurates, isocyanurates and phthalates [Citation12,Citation14,Citation15]. A. Rezaei et al. [Citation9] modified PHB by using dicumyl peroxide with triallyl trimesate (TAM) as coagents. This resulted in crosslinking reaction as indicated by the increase of viscosity. Bor-Kuan Chen et al. [Citation6] illustrated that when incorporating PHB with benzoyl peroxide and coagent acryloyloxyethyl isocyanate, the formation of crosslink between PHB chains and poly(ester-urethane) linkage at ended group of PHB increased Mn and restrict chain mobility resulting in the formation of six membered ring transition state become harder and improved thermal stability of PHB. T. Zheng et al. [Citation10] prepared PHBV grafted GMA using DCP as an initiator through reactive extrusion process. The crosslinking reaction, grafting of GMA into PHBV chain and intermolecular chain extension reaction through DCP and GMA, caused the increase in Mn and Mw. However, to the best of our knowledge, no works on have yet been reported an emphasized on the PHBV and other coagents.
In this work, we focus on the improvement of the thermal stability during melt processing of PHBV through a combination between the free radical and condensation reaction. Di(tert-butylperoxyisopropyl)benzene (DB) was selected as a free radical initiator and triallyl isocyanurate (TAIC) was used as a coagent for inducing the crosslinking reaction, hence controlling the melt viscosity and molecular weight of PHBV through free radical reaction. Meanwhile, a multi-functional epoxy chain extender (ECE) was used for condensation reaction of PHBV during melt processing. The effect of free radical reaction, condensation reaction, and combination between free radical and condensation reaction on mechanical properties, thermal properties and chemical structure as well as thermal stability during melt processing were systematically investigated and discussed.
2. Materials and methods
Poly(hydroxybutyrate-co-hydroxyvalerate) (PHBV) Enmat Y1000P with 3 mol % hydroxyvalerate (HV) content was purchased from Tianan Biologic Material Co. (Ningbo, P. R. China) with Young’s modulus 1600–2100 MPa, Tensile strength 39 MPa and DSC melting temperature at 175–180 °C. Di(tert-butylperoxyisopropyl)benzene (DB) (assay 96.0%min), perkadox14s-fl, was purchased from AkzoNobel Co., Ltd. in slightly yellow flake form with active oxygen content peroxide 9.08%min. Triallyl isocyanurate (TAIC) was purchased from Innomax Thailand. Multi-functional epoxy chain extender (ECE) Joncryl ADR® 4468 was purchased from BASF Co., Ltd. in solid flake form with epoxy equivalent weight 310 g/mol.
The reactive melt processing of PHBV with various reactive agents was performed using a torque rheometer model MX 105-D40L50 CHAREON TUT CO., LTD. at 180°C with rotor speed 100 rpm for 10 min. For free radical reaction, PHBV with different contents of DB (0.1, 0.2, and 0.3 phr) and TAIC (0.1, 0.2 and 0.3 phr) were studied. For the sake of clarification, the sample designated as PHBV/DB0.1/TAIC0.1 was referred to 0.1 phr of DB and 0.1 phr of TAIC incorporated into PHBV. This referred designation was used throughout the text. For the condensation reaction, PHBV with various contents of ECE were studied at 0.5, 1 and 2 phr and the combination between free radical and condensation reactionห was carried out using 0.3 phr of DB, 0.1 phr of TAIC and 0.5 phr of ECE.
Melt flow index (MFI) was measured according to ASTM D1238 using Plastometer: MFR1 CHAREON TUT CO., LTD. The tensile test was conducted according to ASTM D638 at speed of testing at 10 mm/min using an Instron universal testing machine model 5659 Instron CO. LTD. Test specimens were prepared by a compression molding process in dumbbell shape type V.
The chemical structure of the samples were characterized by using the nuclear magnetic resonance spectroscopy (NMR) ADVANCE III HD Bruker Optic, Germany and the Attenuated total reflection-Fourier transform infrared spectroscopy (ATR-FTIR) Spectrum 100 Perkin Elmer, USA.
Thermal properties were investigated by heating from −20 to 200°C with the heating rate 10 °C/min and held for 1 min, then cooling from 200 to −20°C with the cooling rate −10°C/min and reheating from −20 to 200°C with heating rate 10°C/min and Thermal decomposition behaviour was investigated by heating from 25 to 60°C with the heating rate 10°C/min under nitrogen atmosphere using TGA/DSC 3+ Mettler-Toledo. The crystallization temperature and melting temperature were investigated in cooling scan and 2nd heating scan, respectively. Specific melting enthalpy (∆Hm) was investigated from 2nd heating scan. The degree of crystallinity (Xc) was calculated from the melting enthalpy (∆Hm) using the following equation.
Where ∆H0m of PHBV was taken to be 146 J/g [Citation16].
3. Results and discussion
3.1. Torque versus time of PHBV and its reactive coagents
Typically, the change of the mixing torque during time interval in an internal mixer can imply the change in polymer viscosity and the molecular weight of polymer. Therefore, the observation of the evolution of the mixing torque can be used for monitoring and investigating the melt viscosity and molecular weight changes as well as the thermal stability of polymers during melt processing.
The evolution of the mixing torque of PHBV and PHBV with various contents of DB is shown in ). The mixing torque of PHBV declined from about 4 N.m at 300 s to 2 N.m at 600 s. The declination of the mixing torque indicated the reduction of the melt viscosity and possible reduced molecular weight of PHBV as a result of the thermal degradation of PHBV [Citation5,Citation17]. This result confirmed that PHBV experienced the degradation under the constant processed temperature. Similar to other researches [Citation1–4,Citation18], the thermal degradation of PHB or PHBV near the melting temperature resulted in the decrease in the viscosity as well as its molecular weight through beta-elimination random chain scission. The evolution of the mixing torque of PHBV/DB insignificantly changed as compared to neat PHBV and the declination of the mixing torque still observed even at the highest contents of DB. These results were similar to those reported by A. Rezaei and coworker [Citation9]. They found the reduction of PHB complex viscosity from 607 Pa.s to 435 Pa.s and 444 Pa.s after applied DCP at 0.2 and 0.3 phr, respectively, as a result of the degradation reaction through chain scission. B. Fei et al. [Citation11] also reported the decreasing of PHBV melt viscosity that implied by melt index. Melt index of DCP treated PHBV increased from 12.48 g/10 min to 34.09 g/10 min after applied with 0.17%wt of DCP. However, incresing melt viscosity was observed when further increased DCP content upto 1%wt with a melt index at 11.66 g/10 min. This result indicated that an addition of a free radical initiator ranging from 0.1 to 0.3 phr was insufficient to tune the thermal stability of PHBV.
The addition of ECE could promote the extents of the molecular weights as a result of the reaction of the epoxide groups with the carboxylic end groups of polyester. Thus, the viscosity and molecular weights of polyester could be altered or even increased during the melt processing. However, the evolution of the mixing torques of PHBV with various contents of ECE (0.5–2 phr) as shown in ) demonstrated the insignificant change when compared to neat PHBV. The declination of the mixing torques was still observed even at the highest content of ECE of 2 phr. This finding was consistent with other researches that also modified PHB or PHBV through condensation reaction [Citation4,Citation5,Citation7,Citation9]. The addition of ECE ranging from 0.5 to 2 phr was unable to improve the thermal stability of PHBV.
The evolution of the mixing torque of PHBV incorporated with DB at 0.2 phr and various contents of TAIC (0.1–0.3 phr) is shown in ). The mixing torque of PHBV/DB0.2/TAIC0.1 showed the improved thermal stability. Almost constant torque at 300 s to 600 s of about 3 N.m was noteworthy observed, implying the constant melt viscosity of PHBV. The reason for this might be the expense of two or more competing reactions, such as the competition between the degradation reaction and crosslinking-branching reaction. However, the increase in the mixing torque at about 300 s followed by decreasing of the mixing torque at about 400 s were observed when the higher contents of TAIC was added. This phenomenon implied that the competing reactions could shift toward the crosslinking reaction at the beginning as a result of high concentration of reactive sites from coagent. The newly formed network may not be strong enough and the breakage of C-C network bonds between polymer chains can simultaneously occur and could lead to the decrease in the mixing torque or torque reversion. The constant torques were also observed in the case of 0.3 phr of DB with various contents of TAIC (0.1, 0.2, and 0.3 phr) as shown in ). PHBV/DB0.3/TAIC0.1 showed the constant torque from 300s to 600s at about 4.2 N.m, which indicated the improved thermal stability of PHBV. As expected, the crosslinking reaction followed by the torque reversion was also observed when the higher content of TAIC was added. The addition of free radical initiator combined with TAIC coagent could improve the thermal stability of PHBV, depending on the concentration of both. The sufficient content of initiator and coagent is required to optimally improve the thermal stability of PHBV. Otherwise, the crosslinking reaction and torque reversion or the declination of mixing torque would be observed. In addition, the melt viscosity of PHBV/DB/TAIC insignificantly changed when compared to neat PHBV and the reduction of the mixing torque was still seen when low content of DB at 0.1 phr and various contents of TAIC (0.1, 0.2 and 0.3 phr) were added (data not shown). Upon combining both systems, the evolution of the mixing torque of PHBV/DB0.3/TAIC0.1/ECE0.5 showed the constant mixing torque during process from 300 s to 600 s at 3.5 N.m, which implied the improved thermal stability of PHBV as illustrated in .
3.2. Melt flow index (MFI)
The melt viscosity of the polymer is inversely related to the melt flow index (MFI) of polymer. shows MFI values of PHBV and PHBV with different reactive agents. Neat PHBV and PHBV/ECE0.5 possessed high MFI values possibly due to the thermal degradation of PHBV during melt processing, thus the lower molecular weight and the melt viscosity of PHBV. As expected, MFI value of PHBV/DB0.3/TAIC0.1 was dropped by 44.4% when compared to that of neat PHBV. This could be due to the formation of crosslink-branching between polymer chains. This higher melt viscosity was correlated well with the mixing torque measurement. Similar to PHBV/DB0.3/TAIC0.1/ECE0.5, the lower MFI value when compared to neat PHBV indicated the higher melt viscosity after adding DB, TAIC and ECE.
Table 1. Melt flow index of PHBV and PHBV with different reactive agents
3.3. Chemical structure analysis
1H NMR was performed to elucidate the chemical structure of PHBV after applying the free radical reaction. 1H NMR spectra of PHBV and PHBV/DB0.3/TAIC0.1 are demonstrated in . PHBV showed the chemical shift at 5.27 ppm, which was related to CH (b, b’) of HB and HV sequence. The chemical shift at 2.53 ppm was assigned to -CH2- group (a, a’). The chemical shifts at 1.61 ppm, 1.27 ppm and 0.91 ppm were corresponded to -CH2- of HV side group (d), methyl group of HB (c), and methyl group of HV(c’), respectively [Citation12,Citation19,Citation20]. As expected for PHBV/DB0.3/TAIC0.1, the spectrum showed the different chemical shift at 4.1 ppm, which might correspond to H-C-N of the coagent (d) and 1.71 ppm, which was related to the formed linkage between PHBV and TAIC (e, f). In addition, the chemical shift of vinyl group of TAIC at 5.1–5.3 and 5.7–5.9 ppm [Citation21] was not observed. It indicated that all vinyl groups of TAIC reacted to form the linkage between the polymer chains, leading to the higher molecular structure of branching. Consequently, the melt viscosity of PHBV was maintained or even increased as discussed in the previous section. Surprisingly, 1H NMR spectrum of PHBV/ECE0.5 (data not shown) was similar to that of neat PHBV. The condensation reaction might not be concentrated enough. It is known that the thermal degradation of PHBV resulted in small molecular weight fractions when exposed to a longer period. In order to be reacted with epoxide groups, the available carboxylic end groups, the longer period of mixing and higher concentration of ECE should be taken into account. H. Xiang and his groups [Citation2] studied the thermal degradation processes and decomposition mechanisms of poly(3-hydroxybutyrate-co-3-hydroxyvalerate) (PHBV) using thermal gravity analysis(TGA). They reported that the depolymerization of PHBV clearly relied on the isothermal temperature and degradation time as high as 30 min. In general, the polymer processing such as for cast and blown film often operate less than 5 min. The degradation can only occur for the residual polymers in the processing equipment and might accelerate the reaction in the screw barrel.
The effect of various reactive agents on chemical structure of PHBV was also investigated using ATR-FTIR. PHBV showed the peak at around 1720 cm−1 corresponding to C = O stretching vibration, the peaks at 1278 and 1054 cm−1 corresponding to C-O stretching and the peaks at 2981, 2934 and 2880 cm−1 corresponding to C-H stretching of PHBV [Citation22]. After various reactive agents were added, the clear difference of the spectra was not pronounced. Modified PHBV showed almost similar spectra to that of neat PHBV (data not shown). It may be suggested that the reaction may not be concentrated enough to detect by this technique.
3.4. Mechanical properties
The mechanical properties of PHBV are summarized in . For PHBV/DB0.3/TAIC0.1, the tensile strength and Young’s modulus of PHBV with reactive agents were slightly increased while elongation at break was slightly decreased when compared to that of neat PHBV. Young’s modulus of 1642.66 MPa, Tensile strength of 46.91 MPa and elongation at break of 7.37 MPa were obtained when DB and TAIC were added at 0.3 and 0.1 phr, respectively. Although the addition of ECE hardly affected the melt viscosity of PHBV but this reactive agent appeared to alter the mechanical properties of PHBV. PHBV/ECE0.5 showed higher Young’s modulus and tensile strength and lower elongation at break when compared to that of neat PHBV. On the other hand, PHBV/DB0.3/TAIC0.1/ECE0.5 had higher Young’s modulus and tensile strength with slightly lower elongation at break when compared to that of PHBV/DB0.3/TAIC0.1. Based on this finding, it suggested that the addition of ECE together with DB and TAIC did not hinder the effect of DB and TAIC reaction, but improved the mechanical properties of PHBV.
Table 2. Mechanical properties of PHBV and PHBV with various reactive agents
3.5. Thermal properties
Thermal properties of PHBV and PHBV with various reactive agents are summarized in . PHBV showed the single melting temperature (Tm) at 172.13 °C and the crystallization temperature (Tc) at 121.98 °C. Thermal properties of PHBV were insignificantly altered after applying the free radical and condensation reactions. However, the degree of crystallinity (Xc) of PHBV with various reactive agents was slightly decreased from 67 to 61% in the case of PHBV/DB0.3/TAIC0.1/ECE0.5. The decrease in the crystallization temperature and the degree of crystallinity of with various reactive agent samples may be due to the effect of formed crosslinking-branching between the polymer chains, which prevented the chain arrangement into crystalline lamella, leading to the retardation of crystallization and decreasing of crystallinity of polymer [Citation11,Citation23,Citation24].
Table 3. Thermal properties of PHBV and PHBV with various reactive agents
TGA thermograms of PHBV and PHBV with various reactive agents are illustrated in and summarized in . PHBV showed one main degradation step from 285.2 to 301.78°C with inflection point at 295.1°C. After incorporating with DB 0.3 phr and TAIC at 0.1 phr, the onset degradation temperature and the inflection point of PHBV were slightly increased from 285.2 to 287.2 °C and 295.1 to 297.4, respectively. Although the addition of ECE at 0.5 phr was insufficient to improve the thermal stability during melt processing of PHBV as observed in the torque curve but the onset degradation temperature and the inflection point of PHBV/ECE0.5 were slightly increased from 285.2 to 287.3 °C and 295.1 to 297.4 °C. In the case of the combination between free radical and condensation reactions (PHBV/DB0.3/TAIC0.3/ECE0.5), the onset degradation temperature and the inflection point were improved from 285.2 to 287.9 °C and 295.1 to 298.4 °C, respectively. When considering the DTG curves of various reactive agents ), it was evident that, the combination of two reaction systems resulted in the delayed degradation compared to that of neat PHBV. Based on these findings, it could be pointed out that although an incorporation of free radical reaction combined with condensation reaction could improve the thermal stability during the melt processing of PHBV as indicated by almost stable mixing torque during mixing, these reaction systems could result in the slight improvement of the thermal stability in the case of TGA test. This finding was similar to the work reported by D.Sitthi and his coworker [Citation7]. They studied the effect of chain extender on thermal degradation behavior of PHBV and founded that although the chain extender was added up to 1%wt, the thermal degradation temperature insignificantly changed when compared with neat PHBV.
Table 4. Thermal degradation temperature of PHBV and PHBV with various reactive agents
3.6. Possible reaction mechanism
During melt process, thermal degradation of PHBV occurs result in the decreasing the melt viscosity and molecular weight. This reaction has previously been reported through beta-elimination random chain scission involving six-membered ring transition state. As a result, the vinyl end group and carboxyl end group polymer are generated as illustrated in [Citation1–3]. Typically, the addition of ECE will react with carboxylic end group and formed the chain extension or branch structures, subsequently increasing the viscosity and molecular weight [Citation25–27]. However, the addition of this reactive compound insignificantly altered the melt viscosity of PHBV as shown earlier. Similarly, the addition of DB also did not change the melt viscosity of PHBV but could lower the melt viscosity of PHBV [Citation11]. Therefore, we proposed another degradation pathway through free radical as illustrated in . This mechanism results in the formation of aldehyde and vinyl ended group polymers. As a result of low reactivity between aldehyde and epoxide groups, so that melt viscosity did not change significantly even when the high content of ECE was added.
Scheme 1. Thermal degradation mechanism of PHBV through beta-elimination random chain scission involving six-membered ring transition state
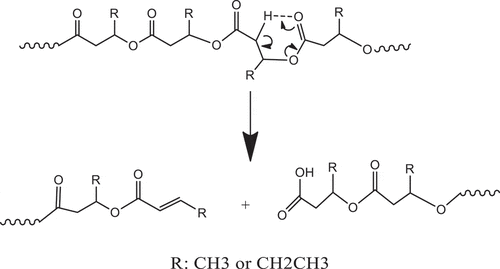
Scheme 2. Proposed thermal degradation of PHBV through beta-elimination from the formed free radicals
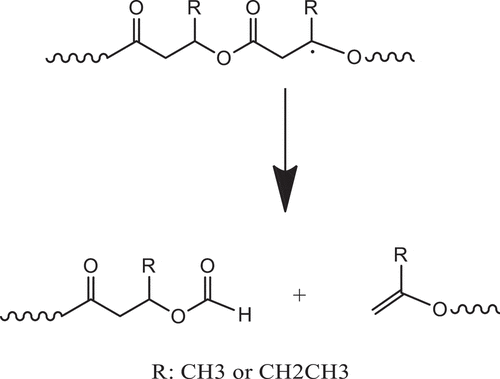
The schematic representations of the possible reactions, free radical and condensation reactions of PHBV, were illustrated in . Firstly, DB dissociated and generated alkoxyl radical when heated at the appropriate temperature. These generated free radicals can abstract H from tertiary C on PHBV chains to form macro-free radical (3a). The newly formed macro-free radicals can further react with coagent (3b), which is a multifunctional monomer that increases reactive site for free radical and results in the induced crosslink-branching reaction instead of the degradation side reaction. The reaction can however compete with another adverse reactions such as other degradation reactions. This phenomenon results in an increased or maintained melt viscosity as well as improved thermal stability of PHBV for the period of processing. In the case of the epoxide groups on the ECE chain, which has high reactivity to carboxylic group, can react with carboxylic end group of PHBV through condensation reaction [Citation7]. Although 1H NMR technique could not provide the clear evidence, the branching can also be possibly formed due to the several reactive epoxide groups. The competition between crosslinking-branching reaction, condensation reaction and degradation reaction could also take place during reactive melt process and gives rise to a variation of mixing torque behavior during melt process. The formation of branching and crosslinking between polymer chains as well as ester linkage derived from condensation reaction resulted in an increased melt viscosity and improved thermal stability of PHBV during melt processing as well as mechanical properties of PHBV.
4. Conclusions
Thermal stability of PHBV was enhanced through both free radical and condensation reactions. The addition of DB and TAIC coagent could result in the formation of branching-crosslinking between PHBV chains, hence improving the thermal stability of PHBV during the period of the melt processing as well as the increase in the melt viscosity. However, the sufficient contents of DB and TAIC must be added, in this case 0.3 phr of DB and 0.1 phr of TAIC. The incorporation of ECE alone insignificantly altered the melt viscosity during processing. The 1H NMR results suggested the reaction of TAIC in the presence of DB with PHBV. The reactions of ECE, TAIC and DB could not however be observed using ATR-FTIR technique. The increase in the tensile strength and Young’s with the expense of elongation at break was observed when the free radical and condensation was applied. The mixing torque of PHBV incorporated with 0.3 phr of DB, 0.1 phr of TAIC and 0.5 phr of ECE reached an equilibrium about 3.8 N.m, where the tensile strength and Young’s modulus were increased to 55.54 MPa, 1802.74 MPa and the elongation at break was dropped slightly to 6.47%. The free radical and condensation reactions slightly affected the thermal properties of PHBV with various reactive agents. The melting temperature, crystallization temperature and degree of crystallinity were slightly lower when compared to neat PHBV. TGA thermograms confirmed the slight improvement of the thermal degradation when combining two reaction systems. These results indicated that combination of DB/TAIC/ECE is one of the simplest and effective ways to improve thermal stability of PHBV without sacrificing thermal and mechanical properties of PHBV.
Acknowledgments
The authors greatly acknowledge the financial support provided by Department of Materials Science and Engineering, Faculty of Engineering and Industrial Technology, Silpakorn University.
Disclosure statement
No potential conflict of interest was reported by the author(s).
Correction Statement
This article has been republished with minor changes. These changes do not impact the academic content of the article.
Additional information
Funding
References
- Chen Y, Chou IN, Tsai Y-H, et al. Thermal degradation of poly(3-hydroxybutyrate) and poly(3-hydroxybutyrate-co-3-hydroxyvalerate) in drying treatment. J Appl Polym Sci. 2013;130:3659–3667.
- Xiang H, Wen X, Miu X, et al. Thermal depolymerization mechanisms of poly(3-hydroxybutyrate-co-3-hydroxyvalerate). Prog Nat Sci Mater Int. 2016;26(1):58–64.
- Aoyagi Y, Yamashita K, Doi Y. Thermal degradation of poly[(R)-3-hydroxybutyrate], poly[ε-caprolactone], and poly[(S)-lactide]. Polym Degrad Stab. 2002;76(1):53–59.:
- Arza CR, Jannasch P, Johansson P, et al. Effect of additives on the melt rheology and thermal degradation of poly[(R)-3-hydroxybutyric acid]. J Appl Polym Sci. 2015;132:15.
- Bousfield G Effect of chain extension on rheology and tensile properties of PHB and PHB-PLA blends. 2014.
- Chen B-K, Lo SH, Shih CC, et al. Improvement of thermal properties of biodegradable polymer poly(3-hydroxybutyrate) by modification with acryloyloxyethyl isocyanate. Polym Eng Sci. 2012;52: DOI:https://doi.org/10.1002/pen.23099
- Duangphet S, Szegda D, Song J, et al. The effect of chain extender on poly(3-hydroxybutyrate-co-3-hydroxyvalerate): thermal degradation, crystallization, and rheological behaviours. J Polym Environ. 2014;22(1):1–8.
- Liu Q-S, Zhu M-F, Wu W-H, et al. Reducing the formation of six-membered ring ester during thermal degradation of biodegradable PHBV to enhance its thermal stability. Polym Degrad Stab. 2009;94:18–24.
- Rezaei A, Kontopoulou M. Chain extended poly(3-hydroxybutyrate) with improved rheological properties and thermal stability, through reactive modification in the melt state. Polym Degrad Stab. 2015;121: DOI:https://doi.org/10.1016/j.polymdegradstab.2015.09.008.
- Zheng T, Zhang Z, Shukla S, et al. PHBV-graft-GMA via reactive extrusion and its use in PHBV/nanocellulose crystal composites. Carbohydr Polym. 2019;205:27–34.
- Fei B, Chen C, Chen S, et al. Crosslinking of poly[(3‐hydroxybutyrate)‐co‐(3‐hydroxyvalerate)] using dicumyl peroxide as initiator. Poly Int. 2004;53:937–943.
- Zhao X, Cornish K, Vodovotz Y. Synergistic mechanisms underlie the peroxide and coagent improvement of natural-rubber-toughened poly(3-hydroxybutyrate-co-3-hydroxyvalerate) mechanical performance. Polymers. 2019;11:565.
- Immirzi B, Malinconico M, Orsello G, et al. Blends of biodegradable polyesters by reactive blending: preparation, characterisation and properties. J Mater Sci. 1999;34(7):1625–1639.
- George KE, Varghese S, Rajan R. Role of coagents in peroxide vulcanization of natural rubber. Rubber Chem Technol. 2013;86(3):488–502.
- Henning SK, In CR. Fundamentals of curing elastomers with peroxides and coagents I: coagent structure-property relationships, 167th technical meeting of the rubber division. Am Chem Soc. 2005;2005:16–18.
- Oner M, Kizil G, Keskin G, et al. The effect of boron nitride on the thermal and mechanical properties of poly(3-hydroxybutyrate-co-3-hydroxyvalerate). Nanomaterials (Basel). 2018;8:11.
- Souza Junior OF, Staffa LH, Costa LC, et al. Thermal and rheological behavior of binary blends of poly(hydroxybutyrate-co-hydroxyvalerate) and poly(ethylene-co-vinyl acetate) with different vinyl acetate content. Macromol Symp. 2019;383:1.
- Wang S, Chen W, Xiang H, et al. Modification and potential application of short-chain-length polyhydroxyalkanoate (SCL-PHA). Polymers (Basel). 2016;8:8.
- Bhattacharyya A, Pramanik A, Maji S, et al. Utilization of vinasse for production of poly-3-(hydroxybutyrate-co-hydroxyvalerate) by Haloferax mediterranei. AMB Express. 2012;2:34.
- Elsawy M, Saad G, Elsabee M. Grafting of N-isopropyl acrylamide onto bacterial polyhydroxybutrate/hydroxyvalerate copolymers. Polym-Plast Technol Eng. 2011;50:1055–1063.
- Li H, Li W, Wu H, et al. Synthesis and application of a thermoplastic plate of poly(lactide-epsilon-caprolactone) for radiation therapy. Biomolecules. 2019;10:1.
- Bai J, Dai J, Li G. Electrospun composites of PHBV/pearl powder for bone repairing. Prog Nat Sci Mater Int. 2015;25(4):327–333.
- Niu Y-H, Liang W-B, Zhang Y-L, et al. Crosslinking kinetics of polyethylene with small amount of peroxide and its influence on the subsequent crystallization behaviors. Chin J Polym Sci. 2016;34(9):1117–1128.
- Zhang X-H, Yang H-M, Song Y-H, et al. Influence of crosslinking on physical properties of low density polyethylene. Chin J Polym Sci. 2012;30(6):837–844.
- Khankrua R, Pivsa-Art S, Hiroyuki H, et al. Effect of chain extenders on thermal and mechanical properties of poly(lactic acid) at high processing temperatures: potential application in PLA/polyamide 6 blend. Polym Degrad Stab. 2014;108:232–240.
- Arruda LC, Magaton M, Bretas RES, et al. Influence of chain extender on mechanical, thermal and morphological properties of blown films of PLA/PBAT blends. Polym Test. 2015;43:27–37.
- Al-Itry R, Lamnawar K, Maazouz A. Reactive extrusion of PLA, PBAT with a multi-functional epoxide: physico-chemical and rheological properties. Eur Polym J. 2014;58:90–102.