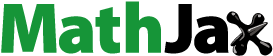
ABSTRACT
This study aims to investigate the influence of rigid polyurethane foam (RPUF) as a filling material on the energy absorption performance of thin-walled tubes through experiments. Hybrid graphene oxide-silica nanoparticles (GO-SiO2) was prepared using the electrostatic adsorption method and its potential application in RPUF enhancement were investigated. The interaction between GO and nano SiO2 inhibits the agglomeration of each other and improved the mechanical properties and energy absorption capacity of RPUF. When the GO-SiO2 hybrid content was 6 wt%, the compressive strength and total energy absorption of the GO-SiO2/RPUF composite material increased by 99.59% and 89.63% compared with those of pure RPUF, respectively. In addition, the deformation characteristics of empty tube and foam-filled tube under lateral compression were compared, and the influence of the RPUF material’s mechanical properties on the energy absorption characteristics of foam-filled tube was further analyzed. Test results show that the foam material can effectively improve the stability of the compression deformation of thin-walled circular tubes and improve the compression resistance of the structure. Improving the mechanical properties of RPUF materials can further increase the bearing capacity and energy absorption of foam-filled tubes. The results in this study validated the feasibility of using GO-SiO2 hybrid as a new nano-reinforcing filler for RPUF, and provide an experimental reference for the engineering application of foam-filled tubes as energy absorption components.
1. Introduction
Given their stable deformation mode and high energy absorption efficiency, thin-walled metal circular tubes have been widely used as energy absorption components in vehicle passive safety systems to reduce the damage to passengers and vehicle structures caused by low-speed collisions. However, the ability of thin-walled circular tubes to bear lateral load is relatively weak, so their carrying capacity and energy absorption performance do not meet the application requirements [Citation1–5]. Therefore, suitable energy absorption materials must be combined with thin-walled circular tubes exploit the performance advantages of the two materials to improve the collision resistance of the body structure and satisfy the lightweight design requirements. Rigid polyurethane foam (RPUF) is a lightweight material with excellent performance. The use of RPUF as a filling core material can improve the energy absorption characteristics of circular tube structures; consequently, RPUF has attracted increasing attention [Citation6–9]. Using nanoparticles as reinforcing filler is one of the effective ways of improving the mechanical properties of RPUF without significantly increasing the apparent density of the foam materials.
The dispersion of nanoparticles and their interaction with the resin matrix are the key factors affecting the modification effect. Silica nanoparticles (nano-SiO2) have small size and surface effects and photoelectric properties, a high mechanical strength, a good chemical stability, and a simple preparation method. Nano-SiO2 particles can enhance the performance of foam by improving the performance of the RPUF matrix and optimizing the cell structure. Nikje et al. [Citation10] found that even a low nano-SiO2 content could markedly improve the heat resistance and dimensional stability of RPUF. Zhang et al. [Citation11], Qing et al. [Citation12], and Lee et al. [Citation13] used ultrasonic dispersion to disperse nano-SiO2 particles in polyurethane foam raw materials and studied the effect of the filling content on the performance of RPUF. Their results show that the cell structure and uniformity of nano-SiO2/RPUF are better than those of pure RPUF, and the compressive mechanical properties of foam are substantially improved.
Graphene oxide (GO) has good hydrophilicity and mechanical properties and thus has become a valuable material for polymer enhancement. However, due to the Van der Waals force between the lamellae, GO easily aggregates in the polymer matrix to form soft agglomeration. High-speed shear mixing and particle functionalization modification are two commonly used methods for improving the dispersion of GO in polymers [Citation14–16]. The research results of Kim et al. [Citation17] show that the compression strength of RPUF can be improved when the GO filling content is within the range of 0.05 wt% to 0.7 wt%. When the content exceeds 0.7 wt%, GO will agglomerate and hinder the formation of a foam structure, which will decrease the stability and mechanical properties of the foam. Li et al. [Citation18] successfully prepared isocyanate-modified GO using isophorone diisocyanate (IPDI) and added it to RPUF. Their results show that the IPDI-modified GO improved the interfacial bonding strength between the filler and the matrix, which was beneficial to improving the mechanical properties and glass transition temperature of RPUF.
The large specific surface area and abundant highly active oxygen-containing groups of GO make it an ideal carrier for loading inorganic nanoparticles. Using tetraethyl orthosilicate (TEOS) as the silicon source, nano-SiO2 particles can be modified onto the surface of GO thin sheets through the in-situ growth method [Citation19–24]. Nano-SiO2 is used as an insertion agent to create a composite with GO, generating a hybrid filler with a three-dimensional structure. The hybrid filler used for polymer modification can endow the polymer matrix material with properties such as high strength, hardness, and toughness [Citation25,Citation26]. Bouibed et al. [Citation27] used N-(β-aminoethyl)-γ-aminopropyl methyl dimethoxyl silane (Z-6020) as a coupling agent to prepare a GO-SiO2 hybrid through a one-step sol-gel pathway. They found that the addition of the GO-SiO2 hybrid (0.1 wt%) improves the thermal stability and corrosion resistance of the epoxy resin matrix. Song et al. [Citation28] attempted to prepare nano-SiO2 through the functionalization of potassium silicate as an inorganic silicon source and introduced it into a water-based epoxy coating to study the corrosion resistance. Charoenchai et al. [Citation29] prepared a GO-SiO2 hybrid using the sol-gel method and filled them into the natural rubber (NR) matrix, enhancing the compression properties and surface hardness of GO-SiO2/NR materials.
In this work, a method was proposed for modifying RPUF with GO-SiO2 hybrid as reinforcement filler. To the best of the author’s knowledge, few literature evidence was found on the modification of RPUF using a GO-SiO2 hybrid, and the enhancement effect and the properties of foam composite require further exploration. This study aims to improve the mechanical properties of RPUF by improving the dispersion of GO and nano-SiO2 and then use foam materials as a filling core material to improve the energy absorption characteristics of thin-walled circular tubes. Herein, the preparation principle and process flow of the GO-SiO2 hybrid are described, the chemical structure composition and surface microstructure are characterized, and the effects of different contents of reinforcement fillers on the compression properties of GO-SiO2/RPUF composites are compared. The influence of the mechanical properties of foam materials on the deformation mode and energy absorption characteristics of thin-walled metal circular tubes are also discussed. The research provides a new pathway for the application of nanotechnology in polyurethane industry.
2. Materials and methods
2.1. Materials
The materials used to prepare the GO-SiO2 hybrid are as follows: GO (Suzhou carbon Feng graphene Technology Co., Suzhou, China); absolute ethyl alcohol (analytical reagent) (Harbin Chemical Reagent Co., Harbin, China); TEOS (analytical reagent) and polyethylene glycol (PEG) (analytical reagent) (Shanghai Macklin Biochemical Co., Shanghai, China); concentrated hydrochloric acid (analytical reagent) (Sinopharm Chemical Reagent Co., Shanghai, China); and ammonium hydroxide (analytical reagent) (Liaoning Quanrui Reagent Co., Jinzhou, China).
The raw materials for preparing pure RPUF include polyurethane A (polyphenyl polymethylene polyisocyanate) and polyurethane B (polyether combination material), which were obtained from Jining Huakai Resin Co., Shandong, China. The thin-walled circular tube was made of 304 stainless steel, with an outer diameter of 60 mm, a wall thickness of 1.0 mm, a tube length of 40 mm, and an empty tube (ET) mass of 50.33 g.
2.2. Preparation of GO-SiO2 hybrid
The GO-SiO2 hybrid was prepared using the electrostatic adsorption method, and the preparation process is shown in . For this purpose, a mixture of 5 ml of deionized water and 10 ml of concentrated ammonia water was added to a flask containing 8 ml of TEOS and 160 ml of anhydrous ethanol and stirred in a water bath at 60 ℃ for 3 h with reflux. Next, 8 g of PEG was added to the flask, and the reflux stirring was continued at 60 ℃ for 24 h. Then, the products were centrifuged, washed three times with anhydrous ethanol, and vacuum-dried at 100 ℃ for 10 h to obtain nano-SiO2. Subsequently, 3 g of dried nano-SiO2 was added to a flask containing 90 ml of anhydrous ethanol, and ultrasonic dispersion was performed for 30 min. Then, 0.6 ml of hydrochloric acid solution was added dropwise to the suspension and stirred at low speed for 5 min; 1 g of GO was added to 120 ml of deionized water, ultrasonic dispersion was added to the flask, and the reaction was carried out in a water bath at 60 ℃ for 5 h. Finally, the resulting products were centrifuged, precipitated by washing with deionized water and anhydrous ethanol for 3 times, and dried under vacuum at 70 ℃ for 12 h to obtain a GO-SiO2 hybrid.
2.3. Preparation of GO-SiO2/RPUF
Thirty grams of polyurethane A material was weighed and placed in a 45 ℃ incubator for 1 h. Then, 30 g of polyurethane B material was weighed, and the GO-SiO2 hybrid (0, 2, 4, 6, and 8 wt%) was added. After mixing for 5 min, the polyurethane A was added into the above mixed material, stirred at 1000 r/min for 10–30 s, and allowed to foam freely. After 24 hours in the room, the foam sample is cut to the standard size that needs to be measured.
2.4. Preparation of foam-filled tubes
Using the method above, polyurethane B material was weighed and injected into the circular tube cavity, and the corresponding mass fraction of the GO-SiO2 hybrid was added and fully stirred. Subsequently, polyurethane A material was added, and a mechanical stirrer was used for 10–30 s at 1000 r/min. The circular tube was fixed and placed vertically for a certain period for the mixed material to fully react in the tube. After free foaming, the foam-filled tube (FFT) specimen was cured and placed at room temperature for 24 h and then cut and polished.
2.5. Characterization
Fourier transform infrared (FT-IR) spectra were measured with a Spotlight 400 spectrometer to determine the characteristic functional groups of nano-SiO2, GO, and GO-SiO2 hybrid. Samples were scanned in the wave range between 400 and 4000 cm−1 with a resolution of 0.5 cm−1.
X-ray diffraction (XRD) was carried out on Rigaku SmartLab diffractometer equipped with a Cu Kα radiation (λ = 0.154 nm) and a nickel filter. The 2θ scanning range was 5°-70° in fixed time 0 mode with a step interval of 0.020°.
Scanning electron microscopy (SEM, Hitachi S-3400) was used to observe the dispersion quality and the surface morphology of GO-SiO2 hybrid at a 20.0 kV of accelerating voltage.
The apparent density of foams was determined according to the method described in standard ISO 845: 2006 ‘Cellular plastics and rubbers-Determination of apparent density’. The foam was cut into a standard sample with a size of 100 mm × 100 mm × 100 mm. The apparent density of five specimens was measured respectively, and the average value was taken as the measurement result.
The quasi‐static compression tests of foam samples were carried out on the CMT5105 electronic universal testing machine at 3 mm/min, according to ISO 844: 2014 ‘Rigid cellular plastics-Determination of compression properties’. Cut the foam sample into cubes with dimensions of 30 mm × 30 mm × 30 mm. The compression distance of the foam sample was set to 24 mm. Each type of foam sample was tested for five times and the average value was taken.
The mechanical properties of ET and the FFT subjecting to lateral compression load between two rigid plates was experimentally investigated. Using a displacement loading control mode, the loading plate was moved vertically downward at a constant speed of 3 mm/min. The compression distance of the ET and the FFT was set to 45 mm, and the compression deformation process of the specimen was recorded at equal time intervals using a camera.
2.6. Evaluation index of energy absorption characteristics
(1) Total energy absorption (EA)
EA represents the ability of a structure to dissipate energy through plastic deformation and is the total energy absorbed by the structure throughout the entire deformation process. EA is determined by the integral area under the corresponding load displacement curve:
where F(x) is the instantaneous load during the crushing process, and d is the compression distance.
(2) Specific energy absorption (SEA)
SEA is the ratio of the total energy absorbed within the effective compressive displacement to the mass (m) of the deformed part of the structure and represents the ability of the structural material to absorb energy per unit mass. SEA is derived using the following equation:
(3) Mean crushing force (Pm)
Pm is defined as the ratio of EA to d, which represents the load level of structural specimens in the process of energy absorption. The calculation formula is as follows:
3. Results and discussion
3.1. Characterization of GO-SiO2 hybrid
(1) FT-IR analysis
FT-IR characterization tests were performed on nano-SiO2, GO, and GO-SiO2, and the results are shown in . In the FT-IR spectra of nano-SiO2, the stretching vibration characteristic peaks of ─OH are located at 3434 and 1632 cm−1, which belong to the absorption peaks of the water molecules contained in the test sample. The strong and wide absorption peak at 1109 cm−1 is the antisymmetric stretching vibration absorption peak of Si-O-Si, and the bending vibration absorption peak at 969 cm−1 belongs to Si-OH. The peaks at 801 and 474 cm−1 are the symmetric stretching and bending vibration absorption peaks of Si-O-Si, respectively [Citation25]. In the FT-IR spectra of GO-SiO2 hybrid, the vibration peaks of C═O and C═C of GO appear at 1730 and 1628 cm−1, respectively, and the characteristic absorption peaks of nano-SiO2 appear at 1108, 969, 801 and 474 cm−1. As expected, the same peaks as GO and nano-SiO2 appeared in the GO-SiO2 hybrid, indicating that nano-SiO2 was inserted into the structure of the GO sheets [Citation30,Citation31]. These information could be used to preliminarily determine that nano-SiO2 was attracted on the GO surface through electrostatic interaction.
(2) XRD analysis
XRD spectra of the GO-SiO2 hybrid, pure GO and nano-SiO2 were compared and shown in . According to the XRD pattern of GO, its diffraction peak is approximately 2θ = 11.43°, with a typical interlayer spacing of 0.774 nm. In the XRD pattern of nano-SiO2, a wide diffraction peak with a weak intensity exists near the approximate 2θ = 22.32°, corresponding to the diffraction peak representing the amorphous structure of nano-SiO2. In the spectra of the prepared GO-SiO2 hybrid, two kinds of peak patterns of GO and nano-SiO2 appear. The position of the characteristic peak corresponding to GO shifted to the left at 2θ = 10.69°, the peak intensity decreased significantly, and the interlayer spacing increased to 0.827 nm. This confirmed that the introduction of nano-SiO2 greatly weakened the hydrogen bond interaction and van der Waals forces between GO sheets, thereby increasing the interlayer spacing of GO [Citation32–34]. Nano-SiO2 can be well dispersed among GO sheets through electrostatic adsorption, which can effectively inhibit the stacking and agglomeration of GO sheets, and thus improve the dispersion of GO in polymers, which agrees with previous reports [Citation27–30].
(3) SEM analysis
The surface of nano-SiO2 is rich in many active hydroxyl groups, and the agglomeration effect is obvious. The addition of PEG in the preparation process partly inhibited the agglomeration of nanoparticles, which generates relatively uniform spherical nano-SiO2 (). The micro morphology of the prepared GO-SiO2 hybrid was observed by SEM, as shown in ). Nano-SiO2 was uniformly loaded on the surfaces of both sides of the GO sheet and no obvious agglomeration occurred, indicating the good interaction between the nano-SiO2 and GO sheets [Citation31]. In addition, nano-SiO2 exists only on the GO sheets, and fewer nanoparticles are found in regions far from GO. This further confirms that the nano-SiO2 particles are attracted to the GO sheets and are not present independently [Citation35]. After modification with nano-SiO2 particles, the dispersion and peeling degree of GO were effectively improved.
3.2. Compressive properties of GO-SiO2/RPUF
shows the force – displacement curve of GO-SiO2/RPUF during the compression process. The GO-SiO2/RPUF composite displayed a strong deformation resistance, and the value of the yield plateau stage force increased. Meanwhile, the foam material maintained good plasticity and toughness. As shown in , within a certain range, the addition of the GO-SiO2 hybrid increases the apparent density of GO-SiO2/RPUF composites. The maximum value was reached at the filling content of 6 wt%, which is 40.37 kg·m−3 and only 13.59% higher than that of pure RPUF (35.54 kg·m−3).
Figure 5. Force-displacement curves (a),apparent density (b) for RPUF with different contents of GO-SiO2 hybrid.
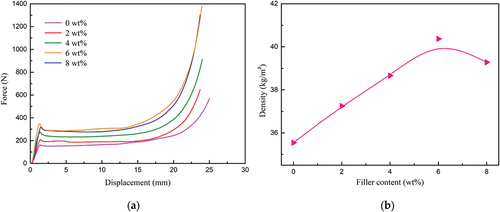
Similar to the apparent density results, the compressive strength and compressive modulus of GO-SiO2/RPUF first increased and then decreased with the increase of the filling content of the GO-SiO2 hybrid. shows that the maximum compressive strength of GO-SiO2/RPUF(6 wt%) is 385.60 kPa, and the maximum compressive modulus is 14.36 MPa, which are 99.59% and 165.97% higher than those of the pure RPUF, respectively. The GO-SiO2 hybrid content continued to increase, leading to the increase of filler agglomeration in the matrix, defects, and stress concentration in the foam material, reducing the compression strength and modulus to varying degrees. This indicates that GO-SiO2 hybrid can improve the compressive mechanical properties of RPUF and provide an effective method for obtaining high-strength foam materials. The enhancement of mechanical properties of RPUF composites may be attributed to the following reasons: (1) The GO-SiO2 hybrid with three-dimensional structure can effectively inhibit the reaggregation of GO, which improves the dispersion of the filler in the RPUF matrix [Citation22–24]. (2) Previous studies [Citation11–13,Citation17,Citation18] have confirmed that the addition of nano-SiO2 and GO alone improves the compressive mechanical properties of RPUF. The GO-SiO2 hybrid in the RPUF skeleton structure enhances the strength and hardness of the hole cell. When plastic yielding occurs in the pore wall structure, the GO-SiO2 nanofillers could suppress crack generation and serve as a framework. (3) The nucleating agent effect of GO-SiO2 hybrid increases the apparent density of RPUF, which enhances the compression properties of foam material.
Figure 6. Compressive strength and modulus (a), energy absorption (b) for RPUF with different contents of the GO-SiO2 hybrid.
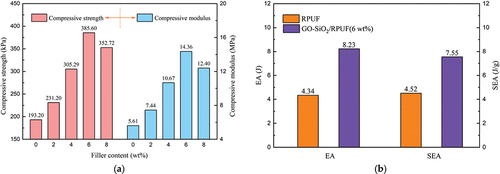
With the increase of the apparent density of GO-SiO2/RPUF, the deformation resistance of the foam material is enhanced, so increased energy is consumed when crushing the hole wall layer by layer. The calculation results of the energy absorption characteristics of the foam material are shown in . The EA value of the pure RPUF material was 4.34 J, and the SEA was 4.52 J/g. When the filling content of the GO-SiO2 hybrid was 6 wt%, the EA value was 8.23 J, which is 89.63% higher than that of pure RPUF. The apparent density of GO-SiO2/RPUF(6 wt%) increased slightly, and the value of SEA increased by 67.04% compared with that of pure RPUF, showing excellent energy absorption characteristics.
3.3. Compression experiments of ET and FFT
shows the typical progressive deformation modes of ET specimen and FFT specimen at different stages of lateral compression. No material fracture or failure of the ET structure occurred in the entire process of lateral compression, and the area of plastic deformation was mainly concentrated around the plastic hinge line formed. The deformation of ET was axisymmetric, and two pairs of plastic hinge lines were formed, whereas FFT only formed a pair of plastic hinge lines on the left and right sides of the tube wall. The foam core material was compressed only in the vertical direction, and almost no transverse expansion occurs. The reason may be that the Poisson ratio of the foam material is close to zero, and the adhesive force with the tube wall is relatively small, leading to the gradual separation of the thin-walled tube wall from the foam core material. In the latter stage of compression, the pores visible on the foam surface were gradually filled with the collapsed organizational structure, the foam material was compacted, and some parts of the foam body exhibited brittle fracture.
show diagrams of force – displacement curve and energy absorption of lateral compression for ET and FFT. The force – displacement curves of FFT are all located above ET, indicating the performance advantage of the RPUF material as an excellent filler for the metal circular tubes. The Pm of the ET was 0.59 kN, and that of the FFT filled with pure RPUF was 1.32 kN, which is 123.73% higher than that of the ET. The mechanical properties of foams are important factors in determining the energy absorption characteristics of FFT [Citation36]. As the mass fraction of the GO-SiO2 hybrid in the RPUF material increased from 2% and 4% to 6%, the Pm value of the corresponding FFT increased by 21.97%, 44.70%, and 75.76%, compared with that of the Pure RPUF-FFT. The EA value of the Pure RPUF-FFT was 59.60 J, and that of the GO-SiO2/RPUF(6 wt%)-FFT specimen was the largest, with a size of 104.29 J. The experimental results show that the energy absorption capacity of FFT is directly related to the mechanical properties of foam materials. Niknejad et al. [Citation37] also found that the energy absorption of FFT specimens increased with the increase of foam density in the lateral compression test of foam-filled circular copper tubes
Figure 8. Comparison of force–displacement curves (a) and energy absorption (b) diagrams for FFT with different filler contents.
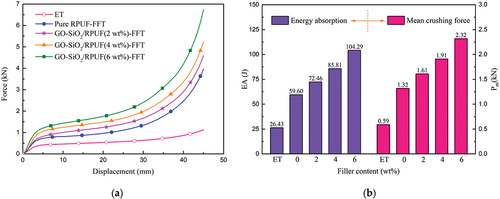
The above research indicates that GO-SiO2/RPUF has a good enhancement effect on the bearing and energy absorption capacities of thin-walled circular tube structures during plastic deformation. On the one hand, the foam material can play a great role in supporting the tube wall, so that the external load is applied to the foam surface through the inner surface of the tube wall, and more energy is absorbed by the foam material [Citation38]. In addition, the bending deformation of the top and bottom tube walls are suppressed by the foam material, thus increasing the contact area between the indenter and the tube walls, resulting in an increase in the foam volume involved in deformation. On the other hand, with the improvement of the compressive properties of the foam material, the core material has a stronger supporting effect on the deformation of the circular tube, and the Pm is doubled. In addition, an interaction exists between foam materials and thin-walled circular tubes [Citation39,Citation40], and this interaction effect is further enhanced with the improvement of the mechanical properties of foam core materials.
4. Conclusions
In this study, GO-SiO2 hybrid was prepared through the electrostatic adsorption method and used to enhance the compressive mechanical properties of RPUF. FT-IR, XRD and SEM test methods were adopted to characterize the prepared GO-SiO2 hybrid. Nano-SiO2 was successfully loaded uniformly on the GO sheets, which increased the interlayer spacing of GO from 0.774 nm to 0.827 nm and enhanced the dispersion and peeling degree of GO. The compression test results of the GO-SiO2/RPUF composites show that GO-SiO2/RPUF(6 wt%) has the best compression properties, and the compression strength and modulus are 99.59% and 165.97% higher than those of pure RPUF, respectively. The FFT structures exhibited stronger deformation resistance, smaller load fluctuations, and higher energy absorption efficiency in the compression tests than the ET structures. In addition, improving the mechanical properties of GO-SiO2/RPUF can further increase the deformation resistance of the FFT structure, enhance the interaction effect between the foam and the tube, and further improve the bearing capacity, bearing stability, and energy absorption characteristics of thin-walled circular tube structures. The EA value of the GO-SiO2/RPUF(6 wt%)-FFT structure increased by 74.98% compared with that of Pure RPUF-FFT. These experimental results demonstrate that using GO-SiO2 hybrid to enhance the mechanical properties of RPUF is a promising method, and GO-SiO2/RPUF composite is suitable as filling core material to improve the energy absorption capacity of thin-walled circular tubes.
Disclosure statement
No potential conflict of interest was reported by the authors.
Data availability statement
The data used to support the findings of this study are included in the article.
Additional information
Funding
References
- Rouzegar J, Niknejad A, Elahi SM, et al. Experimental investigation into the energy absorption of composite-metal tubes subjected to lateral load. Iran J Sci Technol Trans Mech Eng. 2020;44(3):585–598. doi: 10.1007/s40997-019-00295-y
- Shen J, Lu G, Ruan D, et al. Lateral plastic collapse of sandwich tubes with metal foam core. Int J Mech Sci. 2015;91:99–109. doi: 10.1016/j.ijmecsci.2013.11.016
- Firouzsalari SE, Dizhur D, Jayaraman K, et al. Flax fabric-reinforced epoxy pipes subjected to lateral compression[J]. Compos Struct. 2020;244:112307. doi: 10.1016/j.compstruct.2020.112307
- Baroutaji A, Gilchrist MD, Olabi AG. Quasi-static, impact and energy absorption of internally nested tubes subjected to lateral loading. Thin Walled Struct. 2016;98:337–350. doi: 10.1016/j.tws.2015.10.001
- Niknejad A, Javan YT. Circular metal tubes during lateral compression between aV-shape indenter and aplaten–theory and experiment. Proc Inst Mech Eng Part L: J Mater Des Appl. 2015;229(4):318–331. doi: 10.1177/1464420713518744
- Elahi SA, Rouzegar J, Niknejad A, et al. Theoretical study of absorbed energy by empty and foam-filled composite tubes under lateral compression. Thin Walled Struct. 2017;114:1–10. doi: 10.1016/j.tws.2017.01.029
- Rezvani MJ, Souzangarzadeh H. Effects of triggering and polyurethane foam on energy absorption of thin-walled circular tubes under the inversion process. J Energy Storage. 2020;27:101071. doi: 10.1016/j.est.2019.101071
- Ren X, Zhang Y, Han CZ, et al. Mechanical properties of foam-filled auxetic circular tubes: Experimental and numerical study[J]. Thin Walled Struct. 2022;170:108584. doi: 10.1016/j.tws.2021.108584
- Zhang J, Du J, Miao F, et al. Plastic behavior of slender circular metal foam-filled tubes under transverse loading[J]. Thin Walled Struct. 2022;171:108768. doi: 10.1016/j.tws.2021.108768
- Nikje MMA, Tehrani ZM. Thermal and mechanical properties of polyurethane rigid foam/modified nanosilica composite. Polymer Engineering & Science. 2010;50(3):468–473. doi: 10.1002/pen.21559
- Zhang Q, Lin X, Chen W. Modification of rigid polyurethane foams with the addition of nano-SiO2 or lignocellulosic biomass. Polymers. 2020;12(1):107. doi: 10.3390/polym12010107
- Qing JQ, Liang SE, Cao F, et al. Morphology and properties of silica nanosphere/rigid polyurethane composites foams. China Plastics. 2016;30(7):23–29.
- Lee DI, Ha YH, Jeon H, et al. Preparation and properties of polyurethane composite foams with silica-based fillers. Appl Sci. 2022;12(15):7418
- Zhang JH, Wang X. Study on flame retardancy of polyurethane foam affected by graphene oxide. China Adhesives. 2020;29(4):53–56.
- Xie Y. Preparation and performance study of functional graphene oxide/polyurethane foams[D]. Beijing, China: Beijing University of Chemical Technology; 2017.
- Yan R. Amino-graphene oxide with polyurethane foam’s composite materials: synthesis and research[D]. Beijing, China: Beijing University of Chemical Technology; 2017.
- Kim JM, Kim JH, Choe YR, et al. Effect of graphene oxide on mechanical characteristics of polyurethane foam. J Korean Soc Mar Engg. 2016;40(6):493–498. doi: 10.5916/jkosme.2016.40.6.493
- Li Y, Tian H, Zhang J, et al. Fabrication and properties of rigid polyurethane nanocomposite foams with functional isocyanate modified graphene oxide. Polym Composites. 2020;41(12):5126–5134
- Wang M, Ma L, Li B, et al. One-step generation of silica particles onto graphene oxide sheets for superior mechanical properties of epoxy composite and scale application. Compos Commun. 2020;22:100514. doi: 10.1016/j.coco.2020.100514
- Dolatzadeh F, Moradian S, Jalili MM. Influence of various surface treated silica nanoparticles on the electrochemical properties of SiO2/polyurethane nanocoatings. Corros Sci. 2011;53(12):4248–4257. doi: 10.1016/j.corsci.2011.08.036
- Amirabadi‐Zadeh M, Khosravi H, Tohidlou E. Preparation of silica‐decorated graphene oxide nanohybrid system as a highly efficient reinforcement for woven jute fabric reinforced epoxy composites. J Appl Polym Sci. 2021;138(2):49653. doi: 10.1002/app.49653
- Shitre PV, Harale RR, Sathe BR, et al. Silica nanosphere-graphene oxide (SiO2-GO) hybrid catalyzed facile synthesis of functionalized quinoxaline derivatives. Res Chem Intermed. 2017;43(2):829–841. doi: 10.1007/s11164-016-2667-8
- Haeri SZ, Ramezanzadeh B, Asghari M. A novel fabrication of a high performance SiO2-graphene oxide (GO) nanohybrids: characterization of thermal properties of epoxy nanocomposites filled with SiO2-GO nanohybrids. J Colloid Interface Sci. 2017;493:111–122. doi: 10.1016/j.jcis.2017.01.016
- Zhang ML. Study on anticorrosion property of silica coated graphene oxide/epoxy composite coating[D]. Xian, China: Northwest University; 2018.
- Liu RQ, Pan H, Wang SX, et al. Preparation and application of nano-SiO2/graphene oxide nanocomposites. Chem Res. 2018;29(1):90–98.
- Wei BJ, Xiao T, Li XJ, et al. Preparation and properties of graphene and MWCNTs reinforced epoxy resin composites. Acta Materiae Compositae Sinica. 2012;29(5):53–60.
- Bouibed A, Doufnoune R. Synthesis and characterization of hybrid materials based on graphene oxide and silica nanoparticles and their effect on the corrosion protection properties of epoxy resin coatings. J Adhes Sci Technol. 2019;33(8):834–860. doi: 10.1080/01694243.2019.1571660
- Song B, Shi Y, Liu Q. An inorganic route to decorate graphene oxide with nanosilica and investigate its effect on anticorrosion property of waterborne epoxy. Polym Adv Technol. 2020;31(2):309–318. doi: 10.1002/pat.4770
- Charoenchai M, Tangbunsuk S, Keawwattana W. Silica-graphene oxide nanohybrids as reinforcing filler for natural rubber[J]. J Polym Res. 2020;27(8):1–16. doi: 10.1007/s10965-020-02209-y
- Gu Y, Xia K, Wei Z, et al. Synthesis of nanoSiO2@graphene-oxide core-shell nanoparticles and its influence on mechanical properties of cementitious materials. Constr Build Mater. 2020;236:117619. doi: 10.1016/j.conbuildmat.2019.117619
- Yu ZR, Li SN, Zang J, et al. Enhanced mechanical property and flame resistance of graphene oxide nanocomposite paper modified with functionalized silica nanoparticles. Composites. 2019;177:107347. doi: 10.1016/j.compositesb.2019.107347
- Long Z, Chen Y, Yin W, et al. The effects of graphene oxide-silica nano-hybrid materials on the rheological properties, mechanical properties, and microstructure of cement-based materials. Materials. 2022;15(12):4207
- Qiu J, Zhang K, Yan L. Mercaptopropyl-doped ultra-small silica modified GO nanosheets to enhance mechanical properties of nitrile butadiene rubber[J]. Polymer. 2022;243:124627. doi: 10.1016/j.polymer.2022.124627
- Mowlaei R, Lin J, de Souza FB, et al. The effects of graphene oxide-silica nanohybrids on the workability, hydration, and mechanical properties of Portland cement paste. Constr Build Mater. 2021;266:121016. doi: 10.1016/j.conbuildmat.2020.121016
- Xu XL, Wang XF, Li JL, et al. Preparation of hybrid graphene oxide/nano‐silica nanofillers and their application in poly (vinyl alcohol) composites. Polym Composites. 2017;38(S1):E89–E97. doi: 10.1002/pc.23808
- Niknejad A, Assaee H, Elahi SA, et al. Flattening process of empty and polyurethane foam-filled E-glass/vinylester composite tubes-an experimental study. Compos Struct. 2013;100:479–492. doi: 10.1016/j.compstruct.2013.01.009
- Niknejad A, Elahi SA, Liaghat GH. Experimental investigation on the lateral compression in the foam-filled circular tubes. Materials & Design (1980-2015). 2012;36:24–34. doi: 10.1016/j.matdes.2011.10.047
- Yan L, Chouw N, Jayaraman K. Lateral crushing of empty and polyurethane-foam filled natural flax fabric reinforced epoxy composite tubes. Composites. 2014;63:15–26. doi: 10.1016/j.compositesb.2014.03.013
- Niknejad A, Rahmani DM. Experimental and theoretical study of the lateral compression process on the empty and foam-filled hexagonal columns. Materials&design. 2014;53:250–261. doi: 10.1016/j.matdes.2013.06.077
- Zhang B, Wang L, Zhang J, et al. Deformation and energy absorption properties of cenosphere/aluminum syntactic foam-filled circular tubes under lateral quasi-static compression. Int J Mech Sci. 2021;192:106126. doi: 10.1016/j.ijmecsci.2020.106126