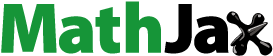
ABSTRACT
Firstly, original poly(vinyl alcohol-co-ethylene) (PVA-co-PE)/cellulose composite membranes were prepared and characterized. Then these composite membranes were applied for wastewater treatment. For this purpose, separation of Iron (III) and Copper (II) ions from the aqueous solutions with stirred ultrafiltration cell was investigated. These metal ions were complexed by using alginic acid for enhancing the retention. The effects of pH and concentration on per cent retention and flux were investigated. Ultrafiltration of Iron (III) and Copper (II) solutions were done at chosen parameters. It has been found that these composite membranes can be used in ultrafiltration processes up to 45 psi pressure. The maximum retention was found as 77% for 0.75 × 10−4 M Copper (II) solutions at a velocity of 300 rpm, pressure of 45 psi, pH of 4 in the presence of alginic acid by using 5.25% (w/v) (PVA-co-PE)/cellulose composite membranes.
1. Introduction
Nowadays, polymers can be used for the basic needs of people. In addition, they play important roles in the life of people, animals and plants. Polysaccharides such as starch and cellulose found in plants, lignin, protein, pectin, etc. substances are natural polymers. For example, nucleic acids regulate processes related to protein synthesis and birth in the organism. Proteins, which are polymers of nucleic acids, have very important biological functions for people and animals. Polymers can be classified as homopolymers and copolymers. Copolymers are formed when two or more monomers polymerize together. The physical properties of copolymers are different from homopolymers and the extent of this difference depends on the composition of the copolymer. Changing the type and amount of the monomers which entering the copolymer provides the opportunity to make almost unlimited number of different polymers. Also, composites of polymer materials have been formed for developing usage of polymers [Citation1,Citation2].
The polymer membranes are used in separation processes, especially in an aqueous solution. They have got the barrier effect between the two phases due to their selective permeability properties. The concentrates are held by membrane while filtrates are passing through the membrane [Citation3–5]. Membranes have been used widely in separation processes at last years, because membranes are becoming more preferred due to the economic efficiency. They can be worked with low energy and developed for the different purpose [Citation6–8].
The performance of membranes processes is expressed by parameters such as flux, selectivity and retention. It can be said that the membranes are ideal when high retention values obtained at acceptable flux [Citation9]. The ideal performance of a membrane relates to the correct selection of membrane material. Also, pH and temperature of an aqueous environment significantly affect the ideal performance of a membrane [Citation10].
Some properties of the membranes are important in the separation processes such as morphology, pore size and pore distribution of the membranes [Citation11]. These properties of the membranes must be able to remain constant under the pressure which exposed to during filtration processes.
There are various membrane preparation techniques. The most important of these techniques are sintering, stretching, etching, coating and phase transformation. Sintering: this method involves compressing certain size particles and sintering at high temperatures. During the sintering, the interfaces of the particles that are in contact with each other disappear and the pore is formed. Stretching; in this method, the film is stretched by applying mechanical force and small breaks occur. Abrasion: the pores of the membranes obtained by this method are about the same sized. Covering: composite membranes are composed of different materials that form a highly selective thin layer and a porous substrate. The upper layer determines the selectivity and the lower layer only serves as a support. Phase transformation: in phase transformation, the polymer is converted from liquid to solid in a controlled manner. Generally, solidification of the polymer is usually achieved by evaporation of the solvent [Citation12]. In membrane preparation techniques, thermodynamic and kinetic approaches should be applied carefully to reach the aimed products [Citation13].
Nowadays, polymer membranes are widely used for wastewater treatment [Citation14]. The most dangerous situation observed in wastewater is the presence of heavy metals. Heavy metal species can damage the environment. They are highly toxic elements. Although heavy metals such as iron, cobalt and copper are necessary for humans at low concentration, they cause serious toxic effects at high concentrations. Heavy metal concentrations in water environments are constantly increasing and emerge as pollution, since adequate measures are not taken in uncontrolled industrialization, closed lakes and water basins. Today, toxic substances given to the environment are at a level that will disrupt the balance of nature. When the concentration of heavy metals reaches the critical values, it becomes dangerous for the living beings. Heavy metals enter the human body through digestion, respiration and skin. Some of them show toxic and carcinogenic effects to living things. Pesticides, fossil fuels, domestic and industrial wastes, radioactive residues and mineral processing activities may cause pollution as a result of the spread of metals to the environment. The erosion of motor vehicle tires and the using of oil as fuel in vehicles also cause heavy metal pollution. The contamination of food, water and other substances with heavy metals brings great health risks in society. Heavy metals are commonly found largely in coal, metal mining and metal coating wastewater [Citation15].
Membrane processes can be divided into various types such as microfiltration, ultrafiltration, nanofiltration and reverse osmosis, especially according to their pore sizes and flux values. Microfiltration membranes generally have a pore size of 0.05–5 μm; they can be used to remove colloidal substances, viruses and bacteria. They are working at pressures about between 0.2 and 3 bars. Ultrafiltration membranes have a pore size of 0.05–1 nm. The retention in these membranes depends not only on the size of the molecule, but also on its ionic charge. Pore diameters of nanofiltration membranes are about 0.005–0.001 μm. Reverse osmosis membranes can work at high pressures compared to other membranes and can hold very small size particles. These processes also can be applied to various areas such as the treatment of wastewaters and seawater [Citation16,Citation17].
In our study, new and original ultrafiltration poly(vinyl alcohol-co-ethylene) (PVA-co-PE)/cellulose composite membranes were synthesized and characterized. The produced new membrane worked smoothly in the ultrafiltration device up to 60 psi pressure. In this study, the separation of Iron (III) and Copper (II) ions from aqueous solutions by these composite membranes was investigated. Effects of pH and solution concentration on retention and flux were studied.
2. Materials and methods
2.1. General information
FeCl3·6H2O, CuCl2·2H2O, Dimethyl sulfoxide (DMSO), NaOH, Thiosemicarbazide, Alginic acid (AA) and (PVA-co-PE) are all Sigma-Aldrich products. HC1 and KSCN are Riedel products. Cellulose filter was purchased from Machery-Nagel (MN 640 de).
The concentrations of Iron (III) and Copper (II) ions were researched spectrophotometrically (Shimadzu, UV 1700 Pharma). KSCN was used for complexing of Iron (III) and the complex was measured at 456 nm [Citation9]. Thiosemicarbazide was also used for complexing of Copper (II) and the complex was measured at 357 nm [Citation18].
The morphology of the cellulose was determined by SEM (LEO 1430VP).
Retention values (% R) were calculated with the following formula:
(1)
(1) In the above equation, Cp and Cf are metal ion concentrations of the filtrate and feed solutions, respectively.
The following formula was used to calculate the permeate flux
(2)
(2)
In this formula, Q is the permeate volume, l, A the membrane area, m2 and Δt the sampling time, h.
2.2. Preparation of membranes
Firstly, DMSO solutions containing 5.25% (w/v) (PVA-co-PE) was prepared. Then 10 ml of this solution was poured on filter papers (7.6 cm, diameter) placed in Petri dish (9 cm, diameter). The casting solvent (DMSO) was completely evaporated in an oven at 70°C and then 5.25% (w/v) (PVA-co-PE)/cellulose membranes were obtained. Then the membranes were washed with distilled water to remove residual solutions.
2.3. Test equipment and filtration
In this work, a batch stirred ultrafiltration cell (Millipore, Amicon 8400) was used (Figure ). Membranes were placed in the filtration cell and the applied pressure was adjusted with nitrogen gas. In the filtration process, the volume of the 300 ml feed solution adjusted with the desired metal ions was used at different pH values. NaOH and HCl solutions were used to adjust the pH. The effects of pH and concentration of solutions on retention and permeate flux were studied.
3. Results and discussion
3.1. Studies to characterize membranes
When the (PVA-co-PE) was coated on the cellulose filter (Figure ), a small spill size of the membranes occurred. Thus, these composite membranes became available for ultrafiltration under applied pressures. The effects of applied pressures on the water flow of the membranes are shown in Figure . In this way, we can see that the water flow increases as the pressure increases. Similar results were obtained in the studies of Çifci et al. [Citation19]
Figure 2. SEM of the new membranes (a) cellulose, (b) 5.25% (w/v) (PVA-co-PE)/cellulose membrane. Magnification: 3000× for (a) and (b).
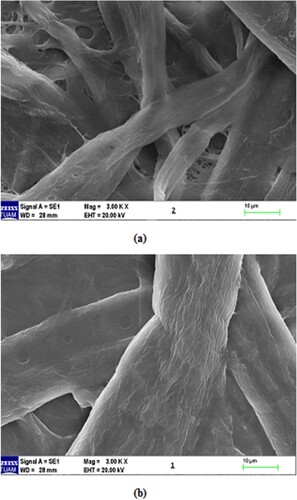
In this study, the retention of Iron (III) and Copper (II) ions by using (PVA-co-PE)/cellulose membranes was investigated. We think that hydroxyl groups of (PVA-co-PE) on the surface of membrane are effective in metal retention. The pH value is a very important factor in polymeric binding since either protons or hydroxyl groups of PVA which parts of the membrane [Citation20].
3.2. Filtration of Iron (III) solutions
Figure shows the retention and flux at different pH values for single Iron (III) ions. pH effects were examined using different pH values. The retention of metal ions is low at low pH values, because high H+ ions repel positively charged Iron (III) ions and prevent metals from binding to the membrane. In this way, the maximum retention is achieved at pH 5. Also, flux decreased with increasing pH, probably on account of cake formation on the membrane. Similar results concerning the effect of pH on the retention and flux have been reported in the study of Chang and Hwang [Citation16].
Figure 4. Effect of pH on retention and flux of Iron (III) solutions (C Fe(III) = 0.5 × 10−4 M, P = 45 psi, stirring rate = 300 rpm).
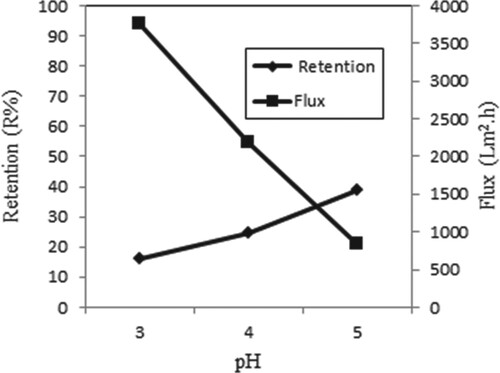
Figure shows the metal retention and flux at different initial concentrations for single Iron (III) ions. From this figure, the maximum retention of Iron (III) is achieved at a concentration of 0.5 × 10−4 M. Also, as the concentration increases, the flux decreases, possibly due to cake formation in the membrane. The high initial metal concentration accelerates collision between metal Iron (III) ion and membrane. As a result, retention increases [Citation9].
Figure 5. Effect of concentration on retention and flux of Iron (III) solutions (P = 45 psi, pH = 5, stirring rate = 300 rpm).
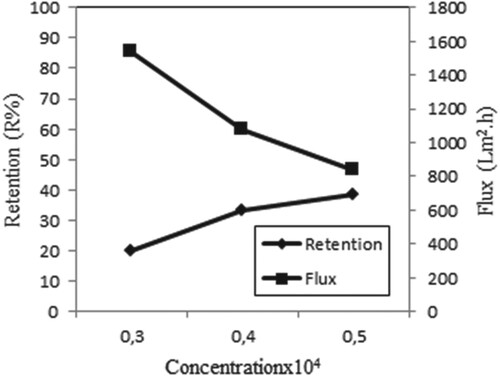
The structure of the complex formed by a combination of Fe (III) with AA is shown in Figure . AA was used to bind the metals to obtain large complexes. Due to these large complexes, retention also increases.
Figure shows the retention and flux at different pH values for Iron (III) ions in the presence of AA. pH effects were examined for these situations by adjusting different pH values. The maximum retention is achieved at pH 4. An increase in the retention by raising pH from 3 to 4 of Iron (III) ion solution at the presence of AA probably result in extra cake formation on the membrane [Citation9].
Figure 7. Effect of pH on retention and flux of Iron (III) solutions in the presence of AA (C Fe(III) = 1 × 10−4 M, C AA = 2 × 10−4 g/L, P = 45 psi, stirring rate =300 rpm).
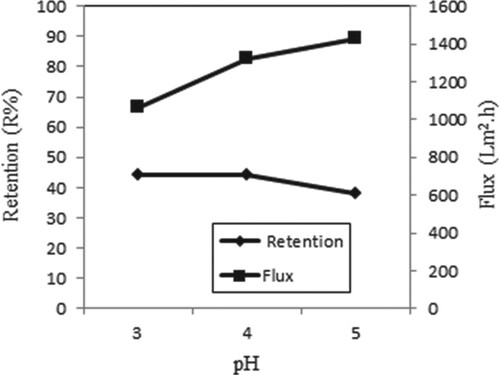
Figure shows the metal retention and flux at different initial concentrations for Iron (III) ions in the presence of AA. From this figure, the maximum retention of Iron (III) is achieved at a concentration of 0.5 × 10−4 M. Also, as the concentration increases, the flux decreases, possibly due to the cake formation in the membrane. Similar results were obtained in the studies of Çifci et al. [Citation19]
Figure 8. Effect of concentration on retention and flux of Iron (III) solutions in the presence of AA (C Fe(III) = 0.5 × 10−4 M with C AA = 1 × 10−4 g/L, C Fe(III) = 0.75 × 10−4 M with C AA = 1.5 × 10−4 g/L, C Fe(III) = 1 × 10−4 M with C AA = 2 × 10−4 g/L, P = 45 psi, pH = 5, stirring rate = 300 rpm).
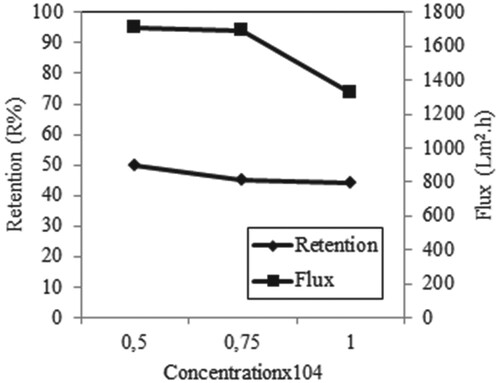
3.3. Filtration of Copper (II) solutions
According to Iron (III) filtration results, values of retentions were not enough. So, we wanted to reach effective results for another ultrafiltration studies. After we began to our ultrafiltration studies with Copper (II) species of heavy metals, we reached high retention values (77%). This result showed us that we can reach effective separation results with our original membrane.
Figure shows the retention and flux at different pH values for single Copper (II) ions. pH effects were examined using different pH values. The retention of metal ions is low at low pH values, because high H+ ions repel positively charged Copper (II) ions and prevent metals from binding to the membrane. In this study, the maximum retention is achieved at pH 4. Similar results were obtained in the study of Çifci and Şanlı [Citation21]
Figure 9. Effect of pH on retention and flux of Copper (II) solutions (C Cu(II) = 0.5 × 10−4 M, P = 45 psi, stirring rate = 300 rpm).
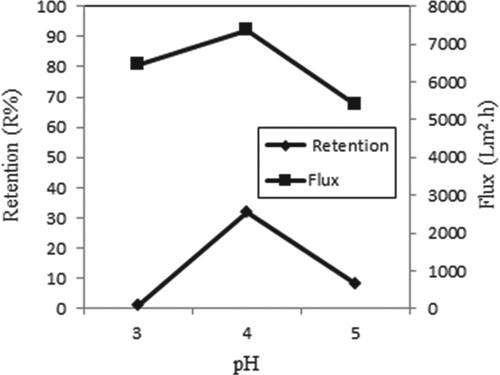
Figure shows the metal retention and flux at different initial concentrations for single Copper (II) ions. From this figure, the maximum retention of Copper (II) is achieved at a concentration of 0.5 × 10−4 M. The high initial metal concentration accelerates collision between metal Copper (II) ion and membrane. As a result, retention increases [Citation9].
Figure 10. Effect of concentration on retention and flux of Copper (II) solutions (P = 45 psi, pH = 4, stirring rate = 300 rpm).
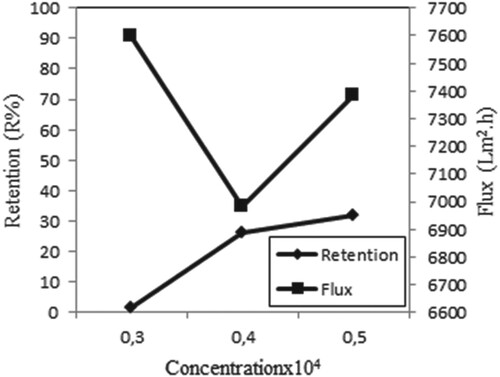
The structure of complex formed by a combination of Cu (II) with AA is shown in Figure . AA was used to bind the metals to obtain large complexes. Due to these large complexes, retention also increases.
Figure shows the retention and flux at different pH values for Copper (II) ions in the presence of AA. pH effects were examined for these situations by adjusting different pH values. The maximum retention is achieved at pH 4. An increase in the retention by raising pH from 3 to 4 of Copper (II) ion solution at the presence of AA probably results in the extra cake formation on the membrane [Citation9].
Figure 12. Effect of pH on retention and flux of Copper (II) solutions in the presence of AA (C Cu(II) = 1 × 10−4 M, C AA = 2 × 10−4 g/L, P = 45 psi, stirring rate = 300 rpm).
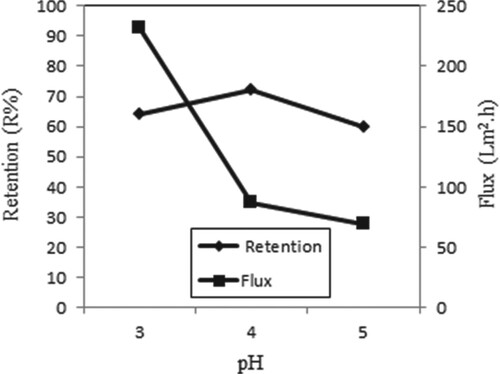
Figure shows the metal retention and flux at different initial concentrations for Copper (II) ions in the presence of AA. From this figure, the maximum retention of Copper (II) is achieved at a concentration of 0.75 × 10−4 M as a value of 77%. Also, as the concentration increases from 0.75 × 10−4 to 1 × 10−4 M, the flux decreases, possibly due to the cake formation in the membrane. Similar results were obtained in the studies of Çifci et al. [Citation19].
Figure 13. Effect of concentration on retention and flux of Copper (II) solutions in the presence of AA (C Cu(II) = 0.5 × 10−4 M with C AA = 1 × 10−4 g/L, C Cu(II) = 0.75 × 10−4 M with C AA = 1.5 × 10−4 g/L, C Cu(II) = 1 × 10−4 M with C AA = 2 × 10−4 g/L, P = 45 psi, pH = 4, stirring rate = 300 rpm).
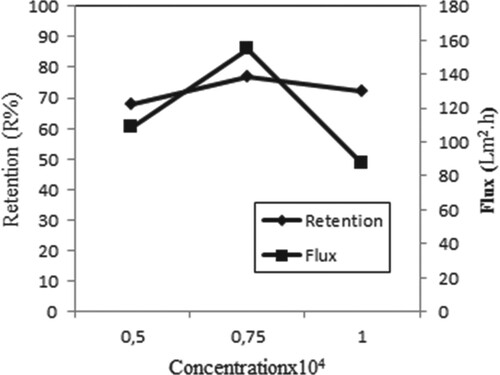
4. Conclusion
In this study, 5.25% (w/v) (PVA-co-PE)/cellulose membranes were obtained and characterized. Then the removal of Iron (III) and Copper (II) ions from aqueous solutions was investigated using a stirred ultrafiltration cell. The effects of solution pH and concentration on permeate flux and retention were investigated. Ultrafiltration of Iron (III) and Copper (II) solutions were done at chosen parameters. It has been found that these membranes can be used in ultrafiltration processes up to 45 psi pressure. The maximum retention was found as 77% for 0.75 × 10−4 M Copper (II) solutions at a velocity of 300 rpm, pressure of 45 psi, pH of 4 in the presence of AA by using 5.25% (w/v) (PVA-co-PE)/cellulose composite membranes. According to Iron (III) filtration results, values of retentions were not enough. So, we wanted to reach effective results for another ultrafiltration studies. After we began to our ultrafiltration studies with Copper (II) species of heavy metals, we reached high retention values than Iron (III) ions. This result showed us that we can reach effective separation results with our original membrane. This study is applicable if it is worked at specified parameter values. These new and original composite membranes can be used to remove other large molecules from their aqueous solutions.
Disclosure statement
No potential conflict of interest was reported by the author(s).
References
- Falahati H, Wong L, Davarpanah L, et al. The zeta potential of PMMA in contact with electrolytes of various conditions: theoretical and experimental investigation. Electrophoresis. 2014;35(6):870–882. doi: 10.1002/elps.201300436
- Baysal B. Polimer Kimyası. Ankara: Orta Doğu Teknik Üniversitesi; 1994.
- Lastra A, Gomeza D, Romerob J, et al. Removal of metal complexes by nanofiltration in a TCF pulp mill: technical and economic feasibility. J Membr Sci. 2004;242:97–105. doi: 10.1016/j.memsci.2004.05.012
- Gzara L, Dhahbi M. Removal of chromate anions by micellar-enhanced ultrafiltration using cationic surfactants. Desalination. 2001;137:241–250. doi: 10.1016/S0011-9164(01)00225-9
- Molinari R, Arguiro P, Romeo L. Studies on interactions between membranes (RO and NF) and pollutants (SiO2, NO3−, Mn++ and humic acid) in water. Desalination. 2001;138:271–281. doi: 10.1016/S0011-9164(01)00273-9
- Hosseini SM, Madaeni SS, Khodabakhshi AR. Heterogeneous cation exchange membrane: preparation, characterization and comparison of transport properties of mono and bivalent cations. Sep Sci Technol. 2010;45:2308–2321. doi: 10.1080/01496395.2010.497792
- Wang D, Hu J, Liu D, et al. Selective transport and simultaneous separation of Cu(II), Zn(II) and Mg(II) using a dual polymer inclusion membrane system. J Membr Sci. 2017;524:205–213. doi: 10.1016/j.memsci.2016.11.027
- Judd SJ. Membrane technology costs and me. Water Res. 2017;122:1–9. doi: 10.1016/j.watres.2017.05.027
- Çifci C, Kopan İ. Preparation of poly(acrylonitrile-co-methyl acrylate)/cellulose composite membranes and their application in wastewater treatment. J Macromol Sci Part A: Pure Appl Chem. 2019;56(6):529–534. doi: 10.1080/10601325.2019.1586441
- Dhodapkar RS, Pophali GR, Nandy TN, et al. Exploitation results of seven RO plants for recovery and reuse of treated effluents in textile industries. Desalination. 2007;217(3):291–300. doi: 10.1016/j.desal.2007.02.015
- Neelakandan C, Pugazhenthi G, Kumar A. Preparation of NOx modified PMMA-EGDM composite membrane for the recovery of chromium (VI). Eur Polym J. 2003;39:2383–2391. doi: 10.1016/S0014-3057(03)00183-6
- Mulder M. Basic principles of membrane technology. London: Kluwer Academic Publishers; 1992. p. 1–285.
- Çifci C. Multilayered universe model with thermodynamics and kinetics studies. Chem Phys Let. 2020;747:137356. doi: 10.1016/j.cplett.2020.137356
- Chen SH, Wu BH, Fu JC, et al. Vertically oriented microporous membranes prepared by bidirectional freezing. Chin J Polym Sci. 2018;36:880–887. doi: 10.1007/s10118-018-2113-z
- Al-Asheh S, Banat F, Mohai F. Sorption of copper and nickel by spent animal bones. Chemosphere. 1999;39(12):2087–2096. doi: 10.1016/S0045-6535(99)00098-3
- Chang DJ, Hwang SJ. Removal of metal ions from liquid solutions by crossflow microfiltration. Separ Sci Technol. 1996;31:1831–1842. doi: 10.1080/01496399608001013
- Juang RS, Shiau RC. Metal removal from aqueous solutions using chitosan-enhanced membrane filtration. J Membr Sci. 2000;165(2):159–167. doi: 10.1016/S0376-7388(99)00235-5
- Donat R, Durmaz Ö, Cetişli H. The kinetic analysis of optimization and selective transportation of Cu(II) ions with TNOA as carrier by MDLM system. Chin J Chem Eng. 2017;25:415–425. doi: 10.1016/j.cjche.2016.08.023
- Çifci C, Savrık M, Erol İ. Purification of wastewater by using poly(methyl methacrylate-co-ethyl acrylate)/poly(vinyl alcohol)-cellulose membranes. Fresen Environ Bull. 2018;27(3):1855–1861.
- Aroua MK, Zuki FM, Sulaiman NM. Removal of chromium ions from aqueous solutions by polymer-enhanced ultrafiltration. J Hazard Mater. 2007;147:752–758. doi: 10.1016/j.jhazmat.2007.01.120
- Çifci C, Şanlı O. Crossflow filtration of Iron(III), Copper(II), and Cadmium(II) aqueous solutions with alginic acid/cellulose composite membranes. J Appl Polym Sci. 2010;115:616–623. doi: 10.1002/app.31066