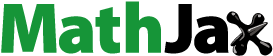
Abstract
The present study aims to enhance the mechanical, microstructural, and fracture performance of alkali-activated coal ash with different proportions of α-phase ultrafine Al2O3 nanoparticles. The inspected proportions of α-phase ultrafine Al2O3 nanoparticles are 0–3% by weight and the proportion of basalt fibres (BF) added to alkali-activated coal ash is 2% by weight of the paste. Several tests are carried out on the cubical and rectangular alkali-activated coal ash nanocomposites representative models of geopolymer to inspect their mechanical and fracture performance. Furthermore, the microstructural evaluation of tested representative pieces is carried out by making use of scanning electron microscopy. The experimental measurements portrayed the combination of 2% BF with 2% α-phase ultrafine Al2O3 nanoparticles manufactures the optimal outcomes for the mechanical and microstructural performance of alkali-activated coal ash nanocomposites. The compression strength obtained at 2% nano alumina was 26.45% larger than the regulator GC paste. The bending strength depicted the optimal outcomes at a 2% proportion of nano alumina being 118.77% larger outcomes than the regulator representative piece. The maximum elastic modulus and bending modulus at 2% nano alumina were 11.3% and 19% larger than the regulator GC paste.
GRAPHICAL ABSTRACT
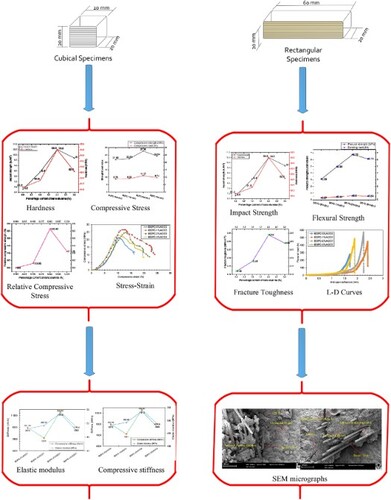
1. Introduction
Cement manufacture is likely to contribute 5% of worldwide CO2 emission and therefore it is essential to develop an alternative construction material. Geopolymer composites (GC) are considered to be the most suitable replacement for cement-based products that reduce the global CO2 emission from 9% to as high as 64% [Citation1,Citation2]. Therefore, scientists are striving to substitute cement with high-performance alkali-activated cementitious GC by ameliorating their mechanical, microstructural, and fracture efficacy. In terms of material nature, GC is mostly considered as a type of semi-crystalline or amorphous binder, which is made by alkaline activation of aluminosilicate products at elevated or ambient temperatures. The aluminoaluminate products available in GC may be activated by utilizing an alkali to enforce them to perform like a binding material [Citation3,Citation4]. Some investigations concluded that the compression and bending efficacy of GC are similar to or larger than that of cement-based materials [Citation5–9]. Many researchers have examined the applications of GC in various structural members such as masonry structures [Citation10], repair materials [Citation11], columns [Citation12,Citation13], pavements [Citation14,Citation15], and reinforced geopolymer concretes [Citation16,Citation17]. Phoo-ngernkham et al. [Citation11] examined the high calcium fly ash geopolymer mortar consisting of Portland cement for the applications in repairing material of structures and found efficient results as repair mortar. Raza et al. [Citation12,Citation13] investigated the structural behaviour of reinforced concrete columns made with geopolymer and found good results in terms of axial strength, ductility, and failure behaviour of columns. Phummiphan et al. [Citation14] and Hoy et al. [Citation15] studied the efficiency of pavements using geopolymer concrete and found that the application of geopolymer in concrete pavements is effective in limiting the cracking behaviour to make a sustainable construction. However, it is necessary to develop the mechanical efficacy of GC by utilizing new methods so that these cementitious composites may be authorized and taken for sustainable development projects. Additionally, this fly ash (FA)-based GC elaborates minimized mechanical efficacy in the initial days and portrays brittle efficiency that confines its practical uses where generally larger strengths are needed. One way to reduce the brittleness of GC and to develop mechanical performance is the inclusion of microfibres.
Many investigations have taken diverse types of fibres for amplifying the mechanical and fracture performance of GC [Citation18–34]. Wang et al. [Citation18] investigated the mechanical, fracture behaviour of geopolymer concrete with the addition of basalt fibre employing the digital image association, and determined that the addition of basalt fibre plays a vital role in enhancing the mechanical and fracture behaviour of geopolymer concrete. Some studies [Citation18–21] assessed the durability behaviour (chloride penetration and sulphate attack) of geopolymer with the addition of basalt fibres. The results depicted the improved durability behaviour of fibre-reinforced geopolymer concrete. Fibre-reinforced metakaolin-based geopolymer analysis [Citation25–28] presented that the addition of different types of fibres minimized the cracking behaviour and ameliorated the mechanical performance of geopolymer paste. The amalgamation of fibre to GC develops durability and ductility due to their property that resists the micro-cracking inside the structure. The compression and bending efficacy of GC blends are fundamentally expanded by the amalgamation of several kinds of microfibres [Citation18–27]. The existence of microfibres may be taken for the postponement of cracks generation inside the GC by transferring the internal strength between the constituents of the GC [Citation18,Citation28,Citation29]. Some experimental works concluded that the mechanical efficacy of GC consisting of micro-fibres is larger than that of the regulator GC comprising no proportions of micro-fibres [Citation18–21,Citation25]. The amalgamation of micro-fibres to GC reduced the dry shrinkage and expanded the setting time and compression strength (CS) of mixes by exchanging the fly ash with fibres [Citation27,Citation29]. Furthermore, the investigation on the impact of micro-fibres in FA-based GC concluded that the increment of micro-fibres expanded the compression efficacy of GC by 37% when the micro-fibres are incorporated by 10% of weight [Citation20]. Whereas the amalgamation of micro-fibres by 15–30%wt. expressed no significant increment in the compression efficacy of GC. Therefore, the amalgamation of microfibres may be considered as one of the best solutions to develop the performance of GC. A detailed study on the plant fibre-based bio-composites including the overall characteristics of plant fibres used in bio-composites, including source, composition, structure, type, as well as properties revealed that flexural strength, fatigue strength, moisture absorption, tensile strength, impact strength, wear behaviour have been increased by treating the fibres using different alkaline solutions [Citation35,Citation36].
Nowadays, the exercise of nanoparticles (NP) in GC for ameliorating the mechanical, microstructural, and fracture efficacy is in the spotlight of advanced research. Many investigations on the utilization of nanomaterials in the development industry have been performed to develop the mechanical and fracture efficacy of GC [Citation37–47]. The investigations on nanomaterials in composites [Citation37,Citation38] reported that the durability behaviour of nanocomposites is improved by the addition of nanoparticles due to increased density and stiff matrix. The mechanical performance of geopolymer paste including compressive, tensile, and flexural properties is significantly improved by the addition of different types of nanoparticles. This may be ascribed to the improved microstructure of paste and densified matrix due to the filling property of nanoparticles [Citation42,Citation43]. These investigations illustrated that the exercise of nanomaterials at minimized proportions instead of micromaterials develops the mechanical efficacy of GC. Though some investigations have been performed to inspect the outcome of nanoparticles on the mechanical efficacy of concrete as a binder [Citation48,Citation49], a few works have been carried out to inspect the mechanical efficacy of GC making use of NP and micro-fibres. Additionally, previous investigations have taken either nano-alumina [Citation50,Citation51] or nano-titanium oxide [Citation52,Citation53] to manufacture GC comprising small information on the outcomes of nano-alumina. A recent investigation has inspected the use of nanoparticles of calcium carbonate up to a proportion of 3% in GC [Citation40]. According to the conclusions of this investigation, 2% use of nanoparticles is the most effective for the structural performance of geopolymer. It is required to inspect the outcome of the joint exercise of basalt fibres (BF) and nano alumina on the structural efficacy of GC to implement it in construction applications. Successively, the present study has endeavoured to inspect the outcome of diverse proportions of nano alumina on the structural efficacy of BF-reinforced GC.
The literature review depicts that the collective addition of NP and microfibres to GC may be effective for amplifying its mechanical, microstructural, and fracture efficacy. Therefore, the present study targets diverse proportions of nano alumina along with a fixed proportion of micro BF to be taken in GC. Three diverse proportions of nano alumina i.e. 1–3% along with 2% micro BF are taken for investigating the compression strength (CS), elastic modulus (EM), stress–strain curves, compression stiffness, bending strength (FS), bending modulus (FM), bending stress–strain curves, bending stiffness, bending load–displacement curves, fracture toughness (FT), toughness indices (TI), hardness (HN), and impact strength (IS) of GC at 28-days of casting. The scanning electron microscopy (SEM) is taken for studying the microstructural efficacy of GC pastes with diverse proportions of nano alumina. The good outcomes of the present work will be beneficial for the practitioners in the construction industry.
2. Experimental setup
2.1. Materials
2.1.1. Nano alumina
Three diverse proportions of white powdered nano alumina particles comprising an average size of 50 are taken in the recent study. The SEM microstructure analysis of alumina is illustrated in Figure .
2.1.2. Fly ash
In the present experimental programme, class F fly ash (FA) fulfilling the requirements of ASTM C618 [Citation54] is taken in the present study as an aluminoaluminate forerunner. Table illustrates the configuration of FA achieved from X-ray fluorescence tests.
Table 1. Chemical composition of FA particles.
2.1.3. Alkali activator
The alkali activator taken for the manufacturing of GC contained sodium silicate and NaOH. The NaOH had a pureness of 98% and was obtained in flakes form. The Sodium silicate was acquired in form of a solution comprising three diverse ingredients including H2O, Al2O3 (alumina), and Na2O. The percentage proportions of H2O, Al2O3, and Na2O were 55.9%, 29.4%, and 14.7%, correspondingly.
2.1.4. Basalt fibres
The amalgamation of microfibres to GC amplifies the compression and tensile features of the mix. Thus, in the recent study, micro-BF was incorporated for amplifying the tensile efficacy of the GC. The BF was taken as a reinforcement partaking tensile strength and the modulus of elasticity of 1700 MPa and 72 GPa, correspondingly.
2.2. Manufacturing and mix design
Four diverse GCs were made by introducing several proportions of nano alumina and a constant proportion of BF. Every GC was assessed for the CS, EM, stress–strain curves, compression stiffness, FS, FM, bending stress–strain curves, bending stiffness, bending load–displacement curves, FT, TI, IS, and HN. The ratio of the combination of NaOH and sodium silicate to FA is 0.45 and the proportion of sodium silicate to NaOH ratio is 2.5 for all GC mixes. The NaOH solution comprising a concentration of 10 M was accomplished by mixing the flakes in water and mixing in with the Sodium silicate for about 24 h prior to the mixing of GC mixes. All GC was made with 2% BF and nano alumina was taken at the proportions of 1–3%, correspondingly.
In the recent study, mixing GC paste was accomplished by making use of a Hobart mixer to gain a workable and homogenous GC. Whereas mixing, the BF is added to FA and mixed for five minutes at a minimized rotation first. Later on, the Hobart mixer was driven at a high speed to appropriately mix the added soluble alkali comprising diverse proportions of nano alumina. This mixing procedure was continued until a homogenous GC was attained. The GC was poured into specific molds to manufacture the representative pieces of the required shape. Lastly, the representative pieces along with molds were moved to an oven to manufacture GC. The temperature was sustained constant at 80°C for 24 h. The methodology taken to manufacture the GC is expressed in Figure . The test structure of the present study is provided in Table .
Table 2. Test structure.
2.3. Testing methodology
2.3.1. Flexural strength
Three-point bending test was used for the measurement of samples after taking them from curing. A Material Testing Machine having a loading capacity of 50 kN was employed for the testing purpose having a displacement rate of 1.0 mm/min. The average results for each of the samples from the fabricated mix were used for the discussion of the results. The flexural strength (σF) was determined utilizing the following relationship:
(1)
(1)
In this relationship, Pm indicates the maximum loading at cracking propagation, S indicates the length of the span of the specimen, B indicates the sample width and W indicates the sample thickness.
2.3.2. Compressive strength
The compressive strength of the fabricated specimens was determined utilizing the following model [Citation55]:
(2)
(2)
In this model, C shows the compressive strength in MPa, P indicates the total loading on the specimen at failure in Newton and A shows the measured area of the bearing surface of the samples in m2.
2.3.3. Impact strength
To find the impact strength of the fabricated specimens, a Charpy impact tester having a pendulum hammer with a 1.0 J impact was utilized. In all samples, 40 mm long bars were utilized. The impact strength (σi) was determined employing the following relationship:
(3)
(3) where E is the impact energy needed to fracture the fabricated specimen of area A.
2.3.4. Rockwell hardness
An Avery Rockwell hardness tester was used to determine the hardness of the fabricated specimens. Before starting the test, the surfaces of specimens were cleaned utilizing a polisher. The average results for each of the samples from the fabricated mix were used for the discussion of the results of hardness.
2.3.5. Fracture toughness
An initial crack was developed in the specimens having the ratio of 0.4 for the length to depth employing a diamond blade of 0.4 mm in width. The following formula was used for determining the fracture toughness (KIC) of the samples:
(4a)
(4a)
In this relationship, Pm is the maximum loading at crack propagation, S is the length of the specimen, B is the sample width, W is the sample thickness, a shows the crack width and f(a/W) indicates a factor for polynomial geometrical correction provided by the model below [Citation39]:
(4b)
(4b)
2.3.6. Microstructure examination
Tescan Lyra SEM machine was employed for making the scanning electron microscopy images of the fractured samples to assess the microstructural behaviour of geopolymer with nanoparticles. Before starting the making of SEM images, the fractured surfaces were covered using gold sheets to avoid the production of charge.
3. Results and discussion
3.1. Impact strength and hardness
Figure expresses the IS of the GC expanded by ameliorating the proportion of nano alumina. The IS of geopolymers is improved constantly up to the increment of 2% nano alumina after that the IS is decreased but still larger than the regulator representative piece comprising no nano alumina. The highest IS of BF-reinforced GC is accomplished by using a proportion of 2% for nano alumina. The IS of representative piece BGC-1%Al2O3 was larger than that of regulator representative piece BGC-0%Al2O3 with a 23.5% increment. The IS of representative piece BGC-2%Al2O3 was 54.4% larger than that of the regulator representative piece BGC-0%Al2O3. Additionally, the IS of representative piece BGC-3%Al2O3 was 42.6% more noteworthy than that of the regulator representative piece BGC-0%Al2O3. The failure of the GC occurred due to the agglomeration of NP inside the GC leading to the initiation of the cracking procedure. This may be correlated with the reason that the NP in the GC develops the bonding strength among structure and BF stimulating a denser and stronger structure to resist the cracking procedure of GC [Citation56]. A GC can work efficiently if the load shifting mechanisms between the NP are performing suitably. By knowing the property of alumina NP depends on the load-transferring constituent from the GC to alumina, the interfacial toughness among the structure and nano alumina have incredible importance. Further, the increment of BF amplifies the load-moving element and boundary by improving the bonding strength and showing a connecting procedure between components of the mix. Therefore, the interfacial surface will provide a greater load transferring and develop the IS. Further, the bonding efficacy of nano alumina and BF illustrated an increment in the IS of BF-reinforced GC.
The exercise of 2% nano alumina made the highest outcomes for the Rockwell HN of GC mixes. Figure displays the outcome of 0–3% proportions of nano alumina on the HN of BF-reinforced GC. As correlated with the regulator representative piece BGC-0%Al2O3, the representative piece BGC-1%Al2O3 expressed an increase of 0.7% in HN whereas the representative piece BGC-2%Al2O3 illustrated an increment of 4.1% in HN of mixes. The representative piece BGC-3%Al2O3 illustrated a reduction of 1.7% in HN correlated with the regulator representative piece. These developed values of HN up to 2% measurements of nano alumina may be linked to the high strength of nano alumina particles organized reliably to the GC framework conveying about a great interfacial area between GC structure and NP during the conduction of internal strength [Citation57]. Also, the amplification of nano alumina up to 2% brings the NP closer to every other developed stiffer mix to express greater HN.
3.2. Compression strength
The CS of all GC representative pieces is expressed in Figure . The increment of the proportion of nano alumina led to an increment in the CS up to a proportion of 2% whereas the increment of the proportion of nano alumina by 3% led to a drop in the CS of GC but not minimized than that of the regulator GC model. The GC consisting of 1% (BGC-1%Al2O3) illustrated an increase of 3.06% and the GC consisting of 2% (BGC-2%Al2O3) nano alumina illustrated an amplification of 26.45% in CS as correlated with the regulator representative piece. This may be correlated with the reason that the little proportions of nano alumina can sufficiently work as a filler to stop the nano and small voids among the GC and BF. Whereas the increment of 3% nano alumina led to an amplification of 11.19% in the CS of GC comprising 2% BF. The highest increment in the CS with the amalgamation of nano alumina may be linked with the ability of enough NP to obstruct the small openings and voids combined with the tendency of the nano alumina to increase the polymerization procedure. The polymerization procedure can speed up by the increment in nano alumina due to their ability to execute as nucleation sites for producing the valuable products in the GC structure [Citation39,Citation58,Citation59]. With alkali and FA, the amalgamation of alumina could react and form C-S-H or CASH gels leading to a larger strength GC [Citation60]. Subsequently, to attain the maximum outcomes for the CS of BF-reinforced GC, 2% of nano alumina may be taken.
An evaluation of GC comprising no the amalgamation of microfibres in the literature directs that the CS accomplished for the diverse GC comprising nano alumina comprising no BF is less than that of the recent outcomes with BF [Citation40]. This expresses the proficiency of including 2% BF to GC with the diverse proportions of nano alumina. The increment in the CS of GC with the increment of BF may be linked to a more densified microstructure and an equivalent larger axial compression loads of mixes. So, it is supposed that the CS of GC may be expanded by including a higher proportion of nano alumina and BF. The CS of GC with 1–3% proportions of nano alumina and 2% BF were 103.06%, 126.45%, and 111.19% of the CS of the regulator representative piece. The relative CS of the GC with the diverse proportions of nano alumina correlated with the regulator representative piece comprising no alumina (BGC-0%Al2O3) is illustrated in Figure .
3.3. Stress–strain curves
The regulator representative piece portrayed less compression stiffness than the representative pieces comprising diverse proportions of nano alumina. This indicates that the ameliorating proportion of nano alumina amplifies the CS producing the GC mostly solid to carry larger compression loads at minimized values of compression strains. Figure elaborates the stress–strain curves of GC representative pieces with 0–3% nano alumina comprising 2% BF. The stress–strain efficacy depicts that the rise in the proportions of nano alumina amplifies the values of CS at minimized compression strain. This may be associated with denser GC and speed up the cycle of the polymerization procedure by the ameliorating proportion of nano alumina due to their tendency to give a strong bond by acting as nucleation situates revealing larger stiffness [Citation39,Citation58,Citation59]. Additionally, the representative pieces comprising the diverse proportions of nano alumina made a larger increment in CS at minimized compression strains. This can be correlated with the larger stiffness of representative pieces before the post-cracking phase that led to the breaking of GC in the post-failure phase of strength-strain curves due to the brittle efficacy of the mixes comprising NP.
The EM of the GC mixes was greater than that of the regulator representative piece BGC-0%Al2O3 except for the representative piece comprising 1% nano alumina. The EM and compression stiffness of GC were expressed in Figure . The EM of representative piece BGC-1%Al2O3 was 2.2% less than the regulator representative piece BGC-0%Al2O3 comprising no proportion of nano alumina. The EM of representative pieces BGC-2%Al2O3 was 11.3% larger than the regulator representative piece BGC-0%Al2O3. The EM of representative piece BGC-3%Al2O3 was 1.4% minimized than the regulator representative piece BGC-0%Al2O3. Subsequently, the representative piece with 2% nano alumina illustrated the largest stiffness with the highest EM of 535.65 MPa. This may be correlated with enough proportion of 2% nano alumina and 2% BF in the GC to execute effectually. Furthermore, this may be ascribed to the denser GC and speed up the cycle of the polymerization procedure by the ameliorating proportion of nano alumina due to their tendency to give a strong bond by acting as nucleation situates revealing larger stiffness [Citation39,Citation58,Citation59].
3.4. Bending strength
The highest FS of GC was acquired by making use of a 2% nano alumina proportion. Figure expresses the outcome of including 2% BF and diverse proportions of nano alumina to GC on their FS. The FS of all mixes with nano alumina was larger than that of BGC-0%Al2O3 whereas 2% illustrated the highest FS. This amplification in the FS of made GC may be linked with the refinement in the structure with the nano alumina particles and then speeding up the polymerization procedure resulting in the solidity of the GC. Additionally, the ameliorating of nano alumina particles due to the increment in the bending stiffness of the GC structure expanded the bending loads of representative pieces.
The FS measurements reported improvement by the addition of nano alumina. The increment in the FS of GC by including 2% and 3% nano alumina may be linked to the filler property of the NP. In previous investigations, the authors illustrated a wide explanation to inspect the efficacy of such mixes by including NP to understand this efficacy. Similar results are detected in previous works with unreinforced GC comprising up to 3% nano alumina particles [Citation40]. The nano alumina proportions of 1% and 2% also expressed expanded FS comprising no BF in the former investigation [Citation40]. The GC with 2% BF illustrated developed FS at all measurements of 2%, and 3% nano alumina correlated with the regulator representative piece (BGC-0%Al2O3). The use of 2% nano alumina illustrated the maximum increment in the FS of GC. Few earlier investigations illustrated that the increment of nano-alumina into GC at the proportions of 1% and 2% expanded the FS by 5.6% and 44.5%, correspondingly [Citation61]. The exercise of nano alumina at the proportions of 2% and 3% in the recent study led to an increment in FS by 118.77% and 98.38%, correspondingly. Correspondingly, the application of nano-alumina alongside the amalgamation of BF is further useable for ameliorating the FS correlated with only making use of nano-alumina. Figure expresses the relative FS of the GC with the diverse proportions of nano alumina correlated with the regulator representative piece comprising no alumina. The FS of GC with 1–3% proportions of nano alumina and 2% BF were 160.19%, 218.77%, and 198.38% of the FS of regulator representative piece, correspondingly.
3.5. Bending stress–strain curves
The regulator representative piece illustrated the minimized values of FS at improved strains exhibiting less stiffness than the representative pieces comprising diverse proportions of nano alumina evidencing that the increment of nano alumina amplifies the FS making a stiffer GC to tolerate larger bending loads at minimized bending strains. Figure demonstrates the bending stress–strain curves of GC comprising diverse proportions of nano alumina with 2% BF. The GC mix with 2% nano alumina expressed a larger bending stiffness with a larger toughness modulus whereas the GC mix with 1% nano alumina expressed the lowest bending stiffness with a minimized toughness modulus. The stress–strain efficacy similarly expresses that the amplification in the proportion of nano alumina develops the values of bending loads at minimized strains. The developed amount of FS at minimized values of bending strain may be linked to densified GC and speed up the amplification of the polymerization procedure by the linking of nano alumina due to their tendency to produce nucleation areas for developing the valuable products in the mixes showing larger bending stiffness [Citation39,Citation58,Citation59]. In addition, the representative pieces containing diverse proportions of nano alumina revealed a larger reduction of FS at minimized values of bending strains. This can similarly be credited to the larger stiffness of tests before the post-failure efficacy that led to the failure of GC in the post-failure phase of strength-strain efficacy due to their larger brittle efficacy.
The toughness modulus (TM) and bending stiffness of diverse GC acquired from the recent study are expressed in Figure . The representative pieces with 2% and 3% proportions of nano alumina expressed a larger TM whereas the representative pieces with 1% nano alumina expressed a slightly minimized TM. The TM of representative piece BGC-1%Al2O3 was 3% minimized than the regulator representative piece BGC-0%Al2O3 comprising 2% BF and no proportion of nano alumina. The TM of representative piece BGC-2%Al2O3 was 19% larger than the regulator representative piece BGC-0%Al2O3. The TM of representative piece BGC-3%Al2O3 was 8.5% larger than the regulator representative piece BGC-0%Al2O3. Therefore, the representative piece with 2% nano alumina illustrated the improved stiffness with an improved TM of 238 MPa. The developed TM with 2% nano alumina may be correlated with enough denser GC and speed up the polymerization progression by the amalgamation of 2% nano alumina inside the structure showing larger bending stiffness of GC [Citation39,Citation59].
3.6. Bending load–displacement curves
Figure expresses the bending load–displacement efficacy of GC representative pieces. The amalgamation of several proportions of nano alumina resulted in amplification in the bending tendency of the representative pieces. The area under the bending curve expresses that the GC having diverse nano alumina proportions acquired larger displacement correlated with the regulator representative piece. This amplification may be correlated with the outcome of NP producing string structure and reducing cracking. When the cracks developed in the structure of the microfibres, they are diverted at the interface between the GC structure and fibre. In the bending test, GC with minimized proportions of nano alumina depicts the highest values of FS at strains. By ameliorating the bending loads, the GC elaborates elastic distortion and observable displacements in the failure portion. By ameliorating the bending loads, the loading produces plastic deformations until the ultimate load is reached. The applied loading is incessantly lessened with the increment in the displacement, making a long tail, leading to larger FT values. Among several nano alumina proportions, the displacement of the GC structure consisting of 2% nano alumina was most raised than others. The amplification in loads may be correlated with a decent fibre-structure bond, which increments the tendency of these mixes to retain energy by commencing twisting pathways for the crack spread that builds the FS [Citation62]. These load–displacement curves demonstrate that the amalgamation of nano alumina strengthens the mechanical behaviour of the GC; they also mention that an increment in nano alumina proportion up to 2% is noteworthy for increasing the crack resistance of a BF-reinforced GC structure.
When the amount of nano alumina advanced further i.e. greater than 2%, the GC became brittle exhibiting less displacement. It may be correlated with the reason that the amalgamation of nano alumina leads to the amplification of fibre-structure bonding efficiency, yet its increment likewise brought a fragile composite appearance minimized displacements for all representative pieces. The amalgamation of nano alumina increments the bonding among BF and GC structures, however, reduced the energy absorption measure given by the deboning and pullout procedure of fibres. Interestingly, increasing nano alumina from 2% to 3% led to a reduction in the bending displacement due to the brittle efficacy of the GC.
3.7. Toughness index
The bending TI of BF-reinforced GC is expressed in Figure . Three diverse TI (,
and
, where
is the toughness index at full damage) were calculated to exhibit bending toughness. The bending TI of BF-reinforced GC representative pieces was calculated following ASTM C1018 [Citation63].
The GC comprising no amalgamation of microfibres is weaker under tensile loading and elaborates brittle efficacy. Thus, it elaborates minimized toughness and requires combination with fibres [Citation40]. The amalgamation of 1% nano alumina expanded the TI of BF-reinforced GC representative pieces by 34.29%, 19.1%, and 0.85% for ,
, and
, correspondingly correlated with the regulator GC. The amalgamation of 2% nano alumina expanded the TI of BF-reinforced GC representative pieces by 48.57%, 41.57%, and 13.68% for
,
, and
, correspondingly related to the regulator representative pieces. Besides, the amalgamation of 3% nano alumina expanded the TI of BF-reinforced GC representative pieces by 22.86%, 35.96%, and 8.55% for
,
, and
, correspondingly correlated with the regulator GC. This displays that the 2% nano alumina elaborated expanded TI than the 3% nano alumina. The amalgamation of nano alumina developed the TI. This may be correlated with strong bonding between the fibres and GC due to the large proportion of nano alumina comprising the fibre-structure adhesion [Citation62].
3.8. Fracture toughness
Figure expresses the FT of every of the four BF-reinforced GC pastes comprising 0–3% nano alumina. The GC with nano alumina displayed larger values of FT than the regulator representative piece BGC-0%Al2O3. Also, the FT of all representative pieces comprising even smaller proportions of nano alumina was larger than 0.4 MPa·m1/2. The developed values of FT may be linked with the availability of BF leading to the amplification in the structure by providing a stiffer lattice. The ability of the BF for producing bridging in the GC expanded the FT of GC that interchanges the interior strength with the structure proceeding to the amplification in the confrontation against the production of cracking and expansions within the structure.
Figure elaborates that the FT of GC is continuously developed by ameliorating the proportion of nano alumina from 1% to 3% exhibiting the highest FT i.e. 0.64 MPa·m1/2 at 3% nano alumina. The FT of all GC containing nano alumina is protuberant than that of the mixes comprising no proportion of nano alumina representing that the amalgamation of nano alumina expanded the strength of the GC. The FT of the GC representative piece BGC-1%Al2O3 was 14.3% larger than the regulator representative piece BGC-0%Al2O3. Further, the FT of the GC representative piece BGC-2%Al2O3 was 52.4% larger than the regulator representative piece BGC-0%Al2O3. The application of 3% nano alumina expressed the highest FT correlated with the representative pieces comprising 1% and 2% proportions of NP. The representative piece BGC-3%Al2O3 expressed an increment of 40.5% in FT correlated with that of the regulator representative piece BGC-0%Al2O3. The development in the FT of GC due to the increment of nano alumina may be attributed to the ability of NP of alumina to produce the interfacial region between the GCX structure and BF resulting in the increment in the interfacial zone of BF in the GC. The NP expands the bonding strength between GC and fibres producing a harder and denser mix to avoid the breaching of interaction [Citation56].
3.9. Microstructural analysis
The fracture efficacy of the tested GC may be deliberated obviously from SEM images by evaluating their broken surface. The SEM images of all GC representative pieces are expressed in Figure . The broken surface of the regulator representative piece comprising no nano alumina expresses momentous differences from that with nano alumina. A large proportion of incompletely non-reacted or reacted micro-particles of FA with voids may be envisioned in the regulator GC and the mix comprising smaller proportions of nano alumina. A densified microstructures may be imagined in the GC comprising 2% and 3% nano alumina. The calcium-aluminate-hydrate gel made in the structure spread between the FA particles and shows their contribution as sources in the space to give a denser GC structure providing a greater bonding efficacy between the NP [Citation40,Citation64,Citation65]. As the proportion of NP develops, the unreacted elements of FA diminish manufacturing a denser structure and lessening the pullout positions of unreacted FA. This can be correlated with the production of calcium silicate hydrate gel or calcium aluminosilicate hydrate gel due to the NP and FA amalgamation [Citation66].
Figure 15. SEM analysis of: (a) BGC-0%Al2O3 (b) BGC-1%Al2O3 (c) BGC-2%Al2O3 (d) BGC-3%Al2O3 representative pieces.
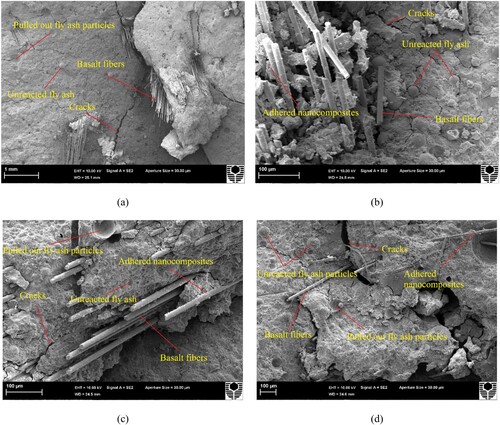
The NP of alumina was carried out as a postponement with the load transferring mechanism and prevented the spread of the micro-crack. By ameliorating the proportion of nano alumina, the cracks were reduced resulting in a denser GC. At this phase, nano alumina helped in stopping the start of micro-cracks by manufacturing a bond between the by-products developed from the GC hydration reactions. The SEM images similarly express that the BF and GC structure have a good bond that may be linked with the proficiency of nano alumina to refine and deliver a denser microstructure of GC. The pullout of unreacted fly ash particles and a few BF occurred as experimented on from SEM images. Figure elaborates that the alkaline atmosphere of the GC has no destructive outcome on BF. Only small proportions of polymerization products stick to the surface of the BF, conceivably due to the temperately hydrophilic property and the grooved surface of the BF. This permits the GC mix to develop a good bonding in the GC.
4. Conclusions
This study targets to ameliorate the mechanical and fracture efficacy of geopolymer paste by introducing BF and diverse proportions of nano alumina. Several properties of geopolymer are assessed. Microstructural analysis of broken representative pieces is carried out by making use of SEM. The following bullet points are withdrawn from the present investigation:
The combined utilization of BF and nano alumina presented development in the compression strength of GC. The optimal outcomes of compression strength were obtained by making use of 2% nano alumina that was 26.45% larger than the regulator GC paste. The improvement in compression strength may be attributed to the micro void-filling feature of nano alumina and the bridging phenomenon of micro BF. Moreover, the addition of nano alumina increased the polymerization procedure to produce a stronger and denser GC structure.
The bending strength depicted the optimal outcomes at a 2% proportion of nano alumina being 118.77% larger outcomes than the regulator representative piece. The improvement in bending strength may be ascribed to the micro void-filling feature of nano alumina, the speed-up polymerization procedure due to nano alumina, and the bridging phenomenon of micro BF.
The addition of nano alumina to BF-reinforced GC enhanced the modulus in compression as well as in tension. The optimum outcomes were observed making use of 2% nano alumina. The maximum elastic modulus and bending modulus at 2% nano alumina were 11.3% and 19% larger than the regulator GC comprising no proportion of nano alumina.
Similarly, the addition of nano alumina performed well for the fracture toughness and toughness indices portraying the maximum efficiency at 2%. The fracture toughness of GC comprising 2% nano alumina was 52.4% larger than the regulator GC. This may be ascribed to the bonding strength among structure and fibres proceeding to a denser and stronger structure to counterattack the failure mechanism of GC. Furthermore, the voids filling property of nano alumina is also prised in the availability of BF producing a bridging that transmits the interior stresses in the GC proceeding to the enrichment in the confrontation against the crack generation.
The SEM analysis of broken representative pieces indicated that the addition of micro BF along with nano alumina performed well in improving the microstructural efficacy of GC. The addition of nano alumina reduced the proportion of unreacted fly ash particles giving a denser and stronger GC. Conclusively, the joint exercise of BF and nano alumina is valuable for improving the mechanical, microstructural, and fracture efficacy of geopolymers.
4.1. Future recommendations
Future work is recommended on the mechanical and durability assessment of geopolymer mortar by adding various types of nanoparticles such as Caolin, TiO2, Na2O, CaO, SiO2, etc. along with the addition of different types of microfibres including steel fibres, natural fibres, carbon fibres, glass fibres, etc.
Disclosure statement
No potential conflict of interest was reported by the author(s).
References
- Turner LK, Collins FG. Carbon dioxide equivalent (CO2-e) emissions: a comparison between geopolymer and OPC cement concrete. Constr Build Mater. 2013;43:125–130.
- McLellan BC, Williams RP, Lay J, et al. Costs and carbon emissions for geopolymer pastes in comparison to ordinary Portland cement. J Cleaner Prod. 2011;19(9-10):1080–1090.
- Provis JL, Bernal SA. Geopolymers and related alkali-activated materials. Annu Rev Mater Res. 2014;44:299–327.
- Neupane K, Hadigheh SA. Sodium hydroxide-free geopolymer binder for prestressed concrete applications. Constr Build Mater. 2021;293:123397.
- Adesina A. Performance and sustainability overview of alkali-activated self-compacting concrete. Waste Dispos Sustain Energy. 2020;2:165–175.
- Duxson P, Fernández-Jiménez A, Provis JL, et al. Geopolymer technology: the current state of the art. J Mater Sci. 2007;42(9):2917–2933.
- Zhuang XY, Chen L, Komarneni S, et al. Fly ash-based geopolymer: clean production, properties and applications. J Cleaner Prod. 2016;125:253–267.
- Zhang P, Zheng Y, Wang K, et al. A review on properties of fresh and hardened geopolymer mortar. Compos B Eng. 2018;152:79–95.
- Davoodabadi M, Liebscher M, Hampel S, et al. Multi-walled carbon nanotube dispersion methodologies in alkaline media and their influence on mechanical reinforcement of alkali-activated nanocomposites. Compos B Eng. 2021;209:108559.
- Arulrajah A, Kua T-A, Horpibulsuk S, et al. Strength and microstructure evaluation of recycled glass-fly ash geopolymer as low-carbon masonry units. Constr Build Mater. 2016;114:400–406.
- Phoo-ngernkham T, Sata V, Hanjitsuwan S, et al. High calcium fly ash geopolymer mortar containing Portland cement for use as repair material. Constr Build Mater. 2015;98:482–488.
- Raza A, Manalo AC, Rafique U, et al. Concentrically loaded recycled aggregate geopolymer concrete columns reinforced with GFRP bars and spirals. Compos Struct. 2021;268:113968.
- Raza A, Rashedi A, Rafique U, et al. On the structural performance of recycled aggregate concrete columns with glass fiber-reinforced composite bars and hoops. Polymers (Basel). 2021;13(9):1508.
- Phummiphan I, Horpibulsuk S, Rachan R, et al. High calcium fly ash geopolymer stabilized lateritic soil and granulated blast furnace slag blends as a pavement base material. J Hazard Mater. 2018;341:257–267.
- Hoy M, Rachan R, Horpibulsuk S, et al. Effect of wetting–drying cycles on compressive strength and microstructure of recycled asphalt pavement – fly ash geopolymer. Constr Build Mater. 2017;144:624–634.
- Mo KH, Alengaram UJ, Jumaat MZ. Structural performance of reinforced geopolymer concrete members: a review. Constr Build Mater. 2016;120:251–264.
- Visintin P, Mohamed Ali MS, Albitar M, et al. Shear behaviour of geopolymer concrete beams without stirrups. Constr Build Mater. 2017;148:10–21.
- Wang Y, Hu S, He Z. Mechanical and fracture properties of geopolymer concrete with basalt fiber using digital image correlation. Theor Appl Fract Mech. 2021;112:102909.
- Pham TM. Enhanced properties of high-silica rice husk ash-based geopolymer paste by incorporating basalt fibers. Constr Build Mater. 2020;245:118422.
- Timakul P, Rattanaprasit W, Aungkavattana P. Improving compressive strength of fly ash-based geopolymer composites by basalt fibers addition. Ceram Int. 2016;42(5):6288–6295.
- Ren D, Yan C, Duan P, et al. Durability performances of wollastonite, tremolite and basalt fiber-reinforced metakaolin geopolymer composites under sulfate and chloride attack. Constr Build Mater. 2017;134:56–66.
- Ding Y, Bai Y-L. Fracture properties and softening curves of steel fiber-reinforced slag-based geopolymer mortar and concrete. Materials (Basel). 2018;11(8):1445.
- Guo X, Pan X. Mechanical properties and mechanisms of fiber reinforced fly ash–steel slag based geopolymer mortar. Constr Build Mater. 2018;179:633–641.
- Yang M, Paudel SR, Gao ZJ. Snow-proof roadways using steel fiber–reinforced fly ash geopolymer mortar–concrete. J Mater Civ Eng. 2021;33(2):04020444.
- Riahi S, Nemati A, Khodabandeh AR, et al. Investigation of interfacial and mechanical properties of alumina-coated steel fiber reinforced geopolymer composites. Constr Build Mater. 2021;288:123118.
- Zhang P, Wang K, Wang J, et al. Mechanical properties and prediction of fracture parameters of geopolymer/alkali-activated mortar modified with PVA fiber and nano-SiO2. Ceram Int. 2020;46(12):20027–20037.
- Liu Y, Shi C, Zhang Z, et al. Mechanical and fracture properties of ultra-high performance geopolymer concrete: effects of steel fiber and silica fume. Cem Concr Compos. 2020;112:103665.
- Ali N, Canpolat O, Aygörmez Y, et al. Evaluation of the 12–24 mm basalt fibers and boron waste on reinforced metakaolin-based geopolymer. Constr Build Mater. 2020;251:118976.
- Punurai W, Kroehong W, Saptamongkol A, et al. Mechanical properties, microstructure and drying shrinkage of hybrid fly ash-basalt fiber geopolymer paste. Constr Build Mater. 2018;186:62–70.
- Guo L, Wu Y, Xu F, et al. Sulfate resistance of hybrid fiber reinforced metakaolin geopolymer composites. Compos B Eng. 2020;183:107689.
- Kheradmand M, Mastali M, Abdollahnejad Z, et al. Experimental and numerical investigations on the flexural performance of geopolymers reinforced with short hybrid polymeric fibres. Compos B Eng. 2017;126:108–118.
- Khandelwal S, Rhee KY. Recent advances in basalt-fiber-reinforced composites: tailoring the fiber-matrix interface. Compos B Eng. 2020;192:108011.
- Chen X, Zhang J, Lu M, et al. Study on the effect of calcium and sulfur content on the properties of fly ash based geopolymer. Constr Build Mater. 2022;314:125650.
- Kaze CR, Lecomte-Nana GL, Adesina A, et al. Influence of mineralogy and activator type on the rheology behaviour and setting time of laterite based geopolymer paste. Cem Concr Compos. 2022;126:104345.
- Ramesh M, Palanikumar K, Reddy KH. Plant fibre based bio-composites: sustainable and renewable green materials. Renew Sustain Energy Rev. 2017;79:558–584.
- Ramesh M, Deepa C, Rajesh Kumar L, et al. Life-cycle and environmental impact assessments on procedureing of plant fibres and its bio-composites: a critical review. J Ind Text. 2020. DOI:10.1177/1528083720924730
- Adesina A. Durability enhancement of concrete using nanomaterials: an overview. Materials Science Forum. Trans Tech Publ; 2019.
- Adesina A. Nanomaterials in cementitious composites: review of durability performance. J Build Pathol Rehabil. 2020;5(1):1–9.
- Gülşan ME, Alzeebaree R, Rasheed AA, et al. Development of fly ash/slag based self-compacting geopolymer concrete using nano-silica and steel fiber. Constr Build Mater. 2019;211:271–283.
- Assaedi H, Alomayri T, Kaze CR, et al. Characterization and properties of geopolymer nanocomposites with different contents of nano-CaCO3. Constr Build Mater. 2020;252:119137.
- Nuaklong P, Sata V, Wongsa A, et al. Recycled aggregate high calcium fly ash geopolymer concrete with inclusion of OPC and nano-SiO2. Constr Build Mater. 2018;174:244–252.
- Chen X, Niu Z, Wang J, et al. Effect of sodium polyacrylate on mechanical properties and microstructure of metakaolin-based geopolymer with different SiO2/Al2O3 ratio. Ceram Int. 2018;44(15):18173–18180.
- Xu S, Malik MA, Qi Z, et al. Influence of the PVA fibers and SiO2 NPs on the structural properties of fly ash based sustainable geopolymer. Constr Build Mater. 2018;164:238–245.
- Assaedi H, Shaikh F, Low IM. Characterizations of flax fabric reinforced nanoclay-geopolymer composites. Compos B Eng. 2016;95:412–422.
- Luo Z, Li W, Gan Y, et al. Maximum likelihood estimation for nanoindentation on sodium aluminosilicate hydrate gel of geopolymer under different silica modulus and curing conditions. Compos B Eng. 2020;198:108185.
- Chen F, Wang K, Shao L, et al. Synthesis of Fe2O3-modified porous geopolymer microspheres for highly selective adsorption and solidification of F− from waste-water. Compos B Eng. 2019;178:107497.
- Cao Y, Wang Y, Zhang Z, et al. Recent progress of utilization of activated kaolinitic clay in cementitious construction materials. Compos B Eng. 2021;211:108636.
- Tanzadeh J. Laboratory evaluation of self-compacting fiber-reinforced concrete modified with hybrid of nanomaterials. Constr Build Mater. 2020;232:117211.
- Guler S, Türkmenoğlu ZF, Ashour A. Performance of single and hybrid nanoparticles added concrete at ambient and elevated temperatures. Constr Build Mater. 2020;250:118847.
- Mustakim SM, Das SK, Mishra J, et al. Improvement in fresh, mechanical and microstructural properties of fly ash-blast furnace slag based geopolymer concrete by addition of nano and micro silica. Silicon. 2020;13:1–14.
- Al Bakri AM, Kamarudin H, Bnhussain M, et al. Nano geopolymer for sustainable concrete using fly ash synthesized by high energy ball milling. Appl Mech Materi. 2013;313:169–173.
- Tuntachon S, Kamwilaisak K, Somdee T, et al. Resistance to algae and fungi formation of high calcium fly ash geopolymer paste containing TiO2. J Build Eng. 2019;25:100817.
- Sastry KGK, Sahitya P, Ravitheja A. Influence of nano TiO2 on strength and durability properties of geopolymer concrete. Mater Today Proc. 2020;45:1017–1025.
- ASTMC618-19. Standard specification for coal fly ash and raw or calcined natural pozzolan for use in concrete. West Conshohocken (PA): ASTM International; 2019.
- D695-15, A. Standard test method for compressive properties of rigid plastics. West Conshohocken (PA): ASTM International; 2015.
- Shaikh F, Shafaei Y, Sarker P. Effect of nano and micro-silica on bond behaviour of steel and polypropylene fibres in high volume fly ash mortar. Constr Build Mater. 2016;115:690–698.
- Assaedi H. The role of nano-CaCO3 in the mechanical performance of polyvinyl alcohol fibre-reinforced geopolymer composites. Compos Interfaces. 2020;28:1–16.
- Saini G, Vattipalli U. Assessing properties of alkali activated GGBS based self-compacting geopolymer concrete using nano-silica. Case Stud Constr Mater. 2020;12:e00352.
- Nuaklong P, Jongvivatsakul P, Pothisiri T, et al. Influence of rice husk ash on mechanical properties and fire resistance of recycled aggregate high-calcium fly ash geopolymer concrete. J Cleaner Prod. 2020;252:119797.
- Chindaprasirt P, De Silva P, Sagoe-Crentsil K, et al. Effect of SiO2 and Al2O3 on the setting and hardening of high calcium fly ash-based geopolymer systems. J Mater Sci. 2012;47(12):4876–4883.
- Alomayri T. Experimental study of the microstructural and mechanical properties of geopolymer paste with nano material (Al2O3). J Build Eng. 2019;25:100788.
- Assaedi H, Shaikh F, Low IM. Influence of mixing methods of nano silica on the microstructural and mechanical properties of flax fabric reinforced geopolymer composites. Constr Build Mater. 2016;123:541–552.
- ASTM C. Standard test method for flexural toughness and first-crack strength of fiber-reinforced concrete (using beam with third-point loading), in C-1018; 1997.
- Yip CK, Lukey G, Van Deventer JS. The coexistence of geopolymeric gel and calcium silicate hydrate at the early stage of alkaline activation. Cem Concr Res. 2005;35(9):1688–1697.
- Yip CK, Lukey GC, Provis JL, et al. Effect of calcium silicate sources on geopolymerisation. Cem Concr Res. 2008;38(4):554–564.
- Phoo-ngernkham T, Chindaprasirt P, Sata V, et al. The effect of adding nano-SiO2 and nano-Al2O3 on properties of high calcium fly ash geopolymer cured at ambient temperature. Mater Des. 2014;55:58–65.