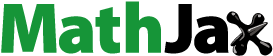
Abstract
In this paper, four groups of polyvinyl alcohol fibre-reinforced geopolymer composites containing various content of nano-alumina particles were investigated. Results showed an improvement in geopolymer fracture toughness, compressive, impact and flexural strength with the added nano-alumina particles as compared to the control specimen. Flexural strength increases as the weight ratio of nano-alumina particles increases from 0.0 to 2.0 wt% and then decreases to 6.50 MPa at 3.0 wt%. Geopolymer reinforced by 2.0 wt% of nano-alumina (PVAGNC-2) displayed the highest flexural and compressive strength of 7.51 and 23.48, respectively. PVAGNC-2 exhibited the highest mechanical (compressive, flexural, impact and hardness) properties. Scanning Electron Microscopy examination showed that the PVAGNC-2 microstructure is compacted with fewer pores indicating the probability of PVAGNC-2 to display great compressive strength and excellent mechanical resistance to the external force needed for construction.
1. Introduction
High demand for more buildings because of population growth worldwide has led to an increase in the use of Ordinary Portland Cement (OPC), which is the basic and most common material used globally in concrete. Apart from the pronounced benefits of OPC, some factors have led to the reconsideration of its use such as high CO2 emissions contributing to global warming and limited limestone reserves [Citation1,Citation2]. Due to the above facts, several measurements have been taken by researchers to develop alternative building materials equivalent to the properties of current Portland cement [Citation1,Citation2]. Geopolymer has been considered a feasible replacement by exhibiting high strength and its environmentally friendly nature [Citation3]. Geopolymers embody an extensive range of materials made up of inorganic molecule complexes [Citation4].
The geopolymer composition depends on the thermal activation of materials such as kaolin or some by-products of industry such as fly ash or slag. Kaolinite and fly ash materials are well rich in silicon (Si) and aluminium (Al) that are readily dissolved in alkaline solution and eventually polymerize into molecular chains. A well-defined mass ratio of activating solutions such as sodium silicate (water glass) and sodium hydroxide will react with either kaolin or fly ash to produce a three-dimensional polymeric chain of Si-O–Al-O bonds in the ring structure [Citation5,Citation6]. Temperature is a necessity during the curing stage of geopolymer. Curing temperature and time depend on the source of materials and activating solution [Citation5–7].
Recently, research has come to the limelight that the addition of nanoparticles to geopolymer increases mechanical strength by acting as voids-fillers thereby producing material with high density [Citation8–10]. In further investigations, it has been established that water absorption and porosity together declined dramatically when both nanoparticles and plasticizers are added to geopolymers [Citation10–12]. In a recent article, the influence of nano-alumina on the mechanical and structural behaviour of geopolymer matrices has been examined, and it has been observed that the addition of the nanoparticles develops the overall material density, thus improving the mechanical performance of the samples [Citation13,Citation14]. This research work studies the impact of nano-alumina particles on the mechanical and structural properties of geopolymer-PVA composites.
2. Experimental procedure
2.1. Materials and methods
The source material of the geopolymer is fly-ash (class-F) obtained from New South Wales, Australia. The chemical composition of the fly ash is listed in Table . The alumina nanoparticles used to support the geopolymer were provided by Sky Spring Nanomaterials Inc., United States of America. The properties of the nano-alumina as provided are listed in Table , and Figure illustrates the microstructure of nano-alumina particles.
Table 1. Chemical structure of the fly ash that was used in the preparation of geopolymer samples.
Table 2. Some physical characterization of PVA-fibres.
In this work, four sets of geopolymer composites were studied. The first set was the control sample which contained 2.0 vol% PVA fibre but not nano-alumina, this set of samples was denoted as PVAGNC-0. Then 1, 2 and 3 wt% nano-alumina were added to geopolymer samples and denoted as PVAGNC-1, PVAGNC-2 and PVAGNC-3, respectively.
The sodium hydroxide (NaOH) solution molarity was fixed at 10 M, besides the ratio of sodium silicate (Na2SiO3) to NaOH was set at 2.5 for all samples. Alkaline solutions were mixed one day prior to preparation. The powder contents (fly ash and nano-alumina) were initially dry-mixed in a laboratory mixer for three minutes followed by adding the alkaline solutions with mixing for three additional minutes. Then, the fibres of PVA were added gradually to the mix while blended for another three minutes. Then the resultant paste was poured into the moulds and kept in the oven at 80°C for one day. All composites were then cured at room temperature for up to four weeks. Table lists the contents of each set of samples.
Table 3. Contents of composites.
2.2. Microstructural characterization
The diffraction pattern of the pure geopolymer, geopolymer reinforced with different percentages of nano-alumina, pure fly ash and nano-alumina were collected with a diffractometer copulated with a sensitive detector (Bruker AXS, Germany). The diffractometer scan angle (2θ) was set to be between 10° and 60° with the use of a nominal step size of 0.01°.
Scanning Electron Microscope (NEON 40ESB field emission, Zeiss, Germany) was used to perform microscopic images. Geopolymer samples were attached using a conductive carbon tape to the aluminium stub and then dried with the aid of a vacuum desiccator before coating. Charging was avoided by the application of a platinum conductive layer.
2.3. Mechanical properties
The mechanical properties of geopolymer samples were measured using a three-point bending test, a common measurement test specifically used for ceramic materials. The dimensions of these geopolymer composite samples were 20 mm in width and 60 mm in length. The thickness meanwhile was nearly 20 mm. The loading span between two supporters in the three-point bending test was 40 mm. Flexural strength tests were undertaken at a crosshead speed of 1 mm/min, whereas each sample underwent five flexural tests. For each sample, the mean value of flexural strength was calculated from multiple tests that were averaged. It was calculated by the mean of the following equation (Equation1(1)
(1) ).
(1)
(1) where Pm denotes the peak load at crack extension, S refers to the sample span, B denotes the specimen width and W specifies the specimen depth or thickness.
A universal testing machine was used for compression measurements. The compression tests were performed according to the ASTM D-695-2002 standard on 20-mm cube specimens. For each sample, five compression tests were performed. Findings from all multiple tests were averaged for all samples. The sample’s compressive strength was computed by the formula as follows:
(2)
(2) where C stands for compressive strength (MPa), P signifies the total loading atop the sample at failure (N), whereas A refers to the calculated portion of the specimen’s bearing surface (mm2).
A Zwick Charpy impact tester involving a 1.0 J pendulum hammer as well as a 40-mm support span was used for evaluating the impact potency of un-notched samples. The following equation was used to calculate the impact strength (σi):
(3)
(3) where E signifies the impact, energy necessitated to break down a sample with the ligament of area A.
The hardness test on different geopolymer composites was carried out with Rockwell Hardness Tester (SAROJ ENGINEERING, 0–1200 kg, ±1G/0.0025 MM) in accordance with ASTM D785. Each obtained value presents an average of five samples.
3. Result and discussion
3.1. X-ray diffraction (XRD) analysis
Figure (a) presents the XRD patterns of fly ash and nano-alumina. Diffraction patterns vividly showed the existence of crystalline quartz and mullite associated with the fly ash used within the 2θ values of 15°–30° signifying aluminosilicate gel formation in the geopolymerization. Fly-ash and nano-alumina diffraction patterns were not similar in terms of trend and intensity indicating that the two materials are chemically different from each other in composition. Figure (b) presents the XRD patterns of all samples. Comparing both the XRD patterns and peak intensities in Figure (b), containing different percentages of nano-alumina particles display a similar trend of XRD pattern indicating that the nano-alumina did not take part in geopolymerization but rather act as a filler particle thereby reinforcing the strength of the geopolymer paste. A comparable result was observed by Assaedi et al. [Citation15].
3.2. Compressive and flexural strength of PVA fibre-reinforced geopolymer composite
Figure display the compressive and flexural strengths of the geopolymer reinforced with different percentage weight of nano-alumina particles. As displayed in Figure , flexural strength increases as the weight per cent of nano-alumina particles increases from 0.0 to 2 wt% and then decreases to 6.50 MPa at 3 wt% contrary to compressive strength. Geopolymer reinforced with 2 wt% of nano-alumina showed the highest compressive and flexural strength of 23.48 and 7.51, respectively. The growth in compressive and flexural results of samples that is enhanced with nano-alumina particles is a result of pore-filling mechanisms thereby creating dense microstructure geopolymer [Citation16,Citation17]. This enhancement can be best explained as a result of the homogeneity of geopolymer matrix structure, restructuring geopolymer chain and effective geopolymer reaction with the nano-alumina. Research investigation of compressive and flexural strength of geopolymer reinforced with nano-alumina particles also reported high strength [Citation18,Citation19].
The presence of nano-alumina is more advantageous than the addition of traditional additives such as rice husk-ash, red mud, etc. The use of nano-filler such as nano-alumina brings low porosity, high density and decrease in the interfacial transition zone of geopolymer which eventually leads to the improvement of mechanical characterization of the geopolymer [Citation15,Citation19]. The presence of nano-alumina particles also acts as catalysts thereby promoting the acceleration of geopolymerization reactions. Thus, this increases the adhesion bond between the geopolymer paste and the PVA fibres, which results in greater resistance to flexing and a clear improvement in mechanical properties.
3.3. Compressive and flexural stress–strain of PVA fibre-reinforced geopolymer nanocomposite
Stress is a force enacted on a geopolymer composite that can cause deformity while a strain is the deformation in a geopolymer attributable to the application of compressive stress [Citation20]. The flexural and compression stress–strain of PVA fibre-reinforced composite samples at a different weight percentage of nano-alumina particles were investigated and presented in Figure . For all geopolymer reinforced with different percentages of nano-alumina particles, 2 wt% nano-alumina geopolymer particle (PVAGNC-2) shows a better result when compared to other percentages of nano-alumina particles signifying a great improvement [Citation20,Citation21]. Figure presented the compression stress–strain of PVA fibre-reinforced geopolymer specimens. For all percentages of geopolymer-reinforced nano-alumina particles, an increase in strain values was observed until 0.1% before depreciation set in. 2.0 wt% nano-alumina geopolymer particle has the highest strain value (above 20 MPa) suggesting more strength, good ductility, better energy absorption and greater toughness [Citation22,Citation23].
For more understanding of the toughening mechanisms, SEM was performed to expose the pores and fracture surface of the neat sample and different percentages of the nano-alumina mixes. Figure displayed the result. Pure geopolymer SEM termed PVAGNC-0 result showed small pores that can be attributed to fracture due to the presence of partially reacted or non-reacted fly-ash particles (Figure (a)). For geopolymer samples containing PVA fibres (Figures (b–d)), some morphologies can be observed such as fibres debonding, fibres pulling out and small patches of geopolymer adhering to the PVA fibres’ surface after pulling out may also be observed. Fibres pull-out sites in fractures indicate increased fracture toughness and work of fracture [Citation24]. The presence of nano-alumina particles mixed with the geopolymer paste controls the pores by acting as filler and catalyst to activate the partially reacted and the non-reacted fly-ash particles in taking part in the geopolymerization. A slightly dense and very well-dense microstructure with few pores and cracks can be observed for GP + 1% nano-alumina (PVAGNC-1) Figure (b) and GP + 2% nano-alumina (PVAGNC-2) Figure (c), respectively, reflecting the existence and reaction of the nano-alumina given room for fracture toughness. However, GP + 3% nano-alumina (PVAGNC-3) SEM result showed a significant quantity of cracks and voids on its surface (Figure (d)) predicting excessive addition of nano-alumina particles [Citation15]. This leads to insufficient adhesion with the fibres as evident in the fibre debonding sites shown in Figure (d).
3.4. Stiffness and flexural rigidity of PVA fibre-geopolymer nanocomposite
Figure presented the impact strength and hardness of the PVA fibre-reinforced geopolymer composite, and Figure showed the stiffness and flexural rigidity of the PVA fibre-reinforced Geopolymer Composite. After careful observation, it was noticed that the inclusion of nano-alumina particles in the geopolymer mixes significantly increases the impact strength and hardness of the geopolymer composites compared with geopolymer with 0 wt% of nano-alumina particles (PVAGNC-0). Figure clearly shows an increase in both impact strength and hardness as the weight percentage of the nano-alumina particles increases till 2 wt% (PVAGNC-2) before the rapid drop in both impact strength and hardness at 3 wt% nano-alumina particles (PVAGNC-3). 2 wt% nano-alumina particle (PVAGNC-2) presented the best values of both impact strength (9.37 kJ/m2) and hardness (85.67 HRH) indicating the probability of this geopolymer to display low creep and shrinkage, great compressive strength and excellent mechanical resistance to the external force.
To promote wider use of geopolymer materials that is reinforced with nano-alumina particles, it is critical to determine its flexural rigidity and stiffness. The flexural rigidity of geopolymer is known to be the required force needed to bend a geopolymer while stiffness is the resistance offered by a geopolymer when it is undergoing bending. Figure presented the stiffness and flexural rigidity of PVA fibre-reinforced composites. An increase in both flexural rigidity and stiffness is observed in the geopolymer mixes as the weight percentage of the nano-alumina increase from 0 to 2% and later drop at 3%. 2 wt% nano-alumina particle geopolymer (PVAGNC-2) presented the best values for both stiffness (2.05 Nm) and flexural rigidity (2.75 N/m) indicating geopolymer with a greater span, high stiffness, toughness and strength and smaller or no deformation [Citation23].
4. Conclusion
This research studies the impact of different percentages of nano-alumina particles on the fracture toughness, compressive, impact and flexural strength of PVA fibre-geopolymer composites. Four sets of composites with different contents of nano-alumina were synthesized. The result showed an improvement in geopolymer compression, impact and flexural strength with the added nano-alumina particles. Samples with 2.0 wt% nano-alumina particle termed PVAGNC-2 exhibited the highest mechanical properties. SEM examination showed that the PVAGNC-2 microstructure is compacted with few pores indicating the probability of PVAGNC-2 to display low creep and shrinkage, great compressive strength and excellent mechanical resistance to the external force needed for construction.
Disclosure statement
No potential conflict of interest was reported by the author(s).
Additional information
Funding
References
- Singh B, Ishwarya G, Gupta M, et al. Geopolymer concrete: a review of some recent developments. Constr Build Mater 2015;85:78–90. DOI:10.1016/j.conbuildmat.2015.03.036
- Robayo-Salazar RA, Mejia J, Mejia de Gutierrez R. Eco-efficient alkali-activated cement based on red clay brick wastes suitable for the manufacturing of building materials. J Clean Prod. 2017;166:242–252. DOI:10.1016/j.jclepro.2017.07.243
- Phoo-ngernkham T, Chindaprasirt P, Sata V, et al. The effect of adding nano-SiO2 and nano-Al2O3 on properties of high calcium fly ash geopolymer cured at ambient temperature. Mater Des. 2014;55:58–65. DOI:10.1016/j.matdes.2013.09.049
- Meena A, Mali HS, Patnaik A, et al. Investigation of wear behavior of nanoalumina and marble dust-reinforced dental composites. Sci Eng Compos Mater. 2019;26:84–96. DOI:10.1515/secm-2017-0152
- Kumar SR, Patnaik A, Bhat IK, et al. Optimum selection of nano- and microsized filler for the best combination of physical, mechanical, and wear properties of dental composites. Proc Inst Mech Eng L: J Mater: Des Appl. 2018;232(5):416–428. DOI:10.1177/1464420716629825
- Paul KT, Satpthy SK, Manna I, et al. Preparation and characterization of nano structured materials from fly ash: a waste from thermal power stations, by high energy ball milling. Nanoscale Res Lett. 2007;2:397–404. DOI:10.1007/s11671-007-9074-4
- Duxson P, Fernandez-Jimenez; J A, Provis L, et al. Geopolymer technology: the current state of the art. J Mater Sci 2007;42:2917–2933. DOI:10.1007/s10853-006-0637-z
- Furtos G, Molnar L, Silaghi-Dumitrescu L, et al. Mechanical and thermal properties of wood fiber reinforced geopolymer composites. J Nat Fibre. 2021:1–16. DOI:10.1080/15440478.2021.1929655
- Furtos G, Silaghi-Dumitrescu L, Pascuta P, et al. Mechanical properties of wood fiber reinforced geopolymer composites with sand addition. J Nat Fibres. 2021;18(2):285–296. DOI:10.1080/15440478.2019.1621792
- Rao JB, Narayanaswami P, Prasad KS. J Eng Sci Tech. 2010;5:284–299.
- Nazari A, Sanjayan JG. Hybrid effects of alumina and silica nanoparticles on water absorption of geopolymers: application of Taguchi approach. Measurement. 2015;60:240–246.
- Olawale MD, Ogundiran MB. Am J Appl Chem. 2014;3(3):134.
- Korniejenko K, Łach M, Dogan-Saglamtimur N, et al. The overview of mechanical properties of short natural fiber reinforced geopolymer composites. Environ Res Technol. 2020;3(1):28–39. DOI:10.35208/ert.671713
- Alomayri T. Experimental study of the microstructural and mechanical properties of geopolymer paste with nano material (Al2O3). J Build Eng. 2019;25:100–788. DOI:10.1016/j.jobe.2019.100788
- Assaedi H, Shaikh FUA, Low IM. Effect of nanoclay on durability and mechanical properties of flax fabric reinforced geopolymer composites. J Asian Ceram Soc. 2017;5(1):62–70. DOI:10.1016/j.jascer.2017.01.003
- Kenny K, Mohan TP. Resin infusion analysis of nanoclay filled glass fiber laminates. Compos B Eng. 2014;58:328–334. DOI:10.1016/j.compositesb.2013.10.025
- Hakamy A, Shaikh FUA. Characteristics of nanoclay and calcined nanoclay-cement nanocomposites. Compos B Eng. 2015;78:174–184. DOI:10.1016/j.compositesb.2015.03.074
- Zidi Z, Ltifi M, Ben Ayadi Z, et al. Synthesis of nano-alumina and their effect on structure, mechanical and thermal properties of geopolymer. J Asian Ceram Soc. 2019;7(4):524–535. DOI:10.1080/21870764.2019.1676498
- Rees CA, Provis JL, Lukey GC, et al. The mechanism of geopolymer gel formation investigated through seeded nucleation. Colloids Surf A: Physicochem Eng Asp. 2008;318(1-3):97–105.
- Liu Y, Wang W, Chen Y, et al. Residual stress-strain relationship for thermal insulation concrete with recycled aggregate after high temperature exposure. Const Build Mater. 2016;129:37–47. DOI:10.1016/j.conbuildmat.2016.11.006
- Mohammed MS, Ali A. The ratio between static and dynamic modulus of elasticity in normal and high strength concrete. J Eng Sustain Dev. 2006;10(2):163–174.
- Chitrala S, Jadaprolu GJ, Chundupalli S. Study and predicting the stress-strain characteristics of geopolymer concrete under compression. Constur Mater. 2018;8:172–192.
- Yadollahia MM, Benli A. The effects of silica modulus and aging on compressive strength of pumice-based geopolymer composites. Const Build Mater. 2015;94:767–774.
- Furtos G, Tomoaia-Cotisel M, Baldea B, et al. Development and characterization of new AR glass fiber-reinforced cements with potential medical applications. J Appl Polym Sci. 2013;128:1266–1273. DOI:10.1002/app.38508