ABSTRACT
While machining width is an important factor of the machining time of freeform surface finishing operations, in reality the kinematic capability of the machine tool is usually the bottleneck of achieving higher feed speed and optimal machining time. The purpose of this paper is to conveniently (and approximately) determine the optimal cut direction considering the speed kinematic capability of the machine tool, without having to compute the actual tool path. We propose a mathematical instrument, called Machine Kinematic Metric (MKM), to easily evaluate infinitesimal machining time on a freeform surface based on machine kinematic consideration. It's a tensor field similar to the metric tensor in differential geometry. MKM is integrated over the part surface to approximate the cut-direction-dependent total machining time, and used to determine the optimal cut direction that minimizes the machining time. To validate the accuracy of the prediction using MKM, we apply the method and compute the machining time at every direction with one degree apart and derive the optimal cut-direction. The computation is performed on two examples: a simple freeform surface and a complex die face model. We then use a commercial CNC emulator software from Huazhong CNC to precisely simulate the machining time in distributed cut directions (five degree apart) for the two models. We find that the optimal cut direction determined from CNC simulation is consistent with the prediction from the proposed method. It validates that the proposed method is a convenient and economical tool to approximately determine the optimal cut direction based on machine speed kinematic capability.
GRAPHICAL ABSTRACT
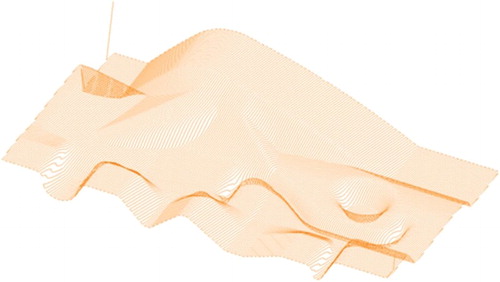
Acknowledgement
Wuhan Huazhong Numerical Control Co., Ltd provided the HNC-8 emulator that allows us to carry out the experiments. Dr. Liu, Xu (NUAA) and Mr. Guo, Xiao (HUST) helped checked the numerical computation in Section 7 with MATLAB. Mr. Guo also helped with the HNC-8 experiments. The authors gratefully acknowledge the support of the National Science and Technology Major Project of the Ministry of Science and Technology of China (2013ZX04007041) and the National Natural Science Foundation of China (51575386). We also want to thank the financial support of Wuhan Institute of Technology.
ORCID
Chen-Han Lee http://orcid.org/0000-0002-7017-0078
Changya Yan http://orcid.org/0000-0002-1614-0193