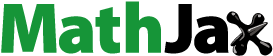
ABSTRACT
A high-volume fraction of the zeta phase in multiphase group VB transition metal tantalum carbides has been shown to dramatically increase fracture toughness. This has been attributed to its unique nanoscale lath-based microstructure. However, what governs the microstructure and how it forms is still not well understood. In this paper, we propose a precipitation model for the formation of these phases and demonstrate that the anisotropic surface energies govern the observed zeta-phase morphology. The energetics and zeta-phase microstructure for other group VB carbides were found to be similar. In contrast, multiphase hafnium nitrides can form both thin-lath-based microstructure as well as large, single zeta-phase grains. The difference between hafnium nitride and the group VB carbides is attributed to the relative bulk free energies and low-temperature stability between the phases.
Introduction
Transition metal carbides (TMCs) and transition metal nitrides (TMNs) are classes of structural ceramics that are used in a wide range of applications where high melting temperatures and/or high hardness are required [Citation1-4]. At ambient and moderately low temperatures, these ceramics are hard and brittle [Citation5]. But, at approximately one-half the homologous temperature, some of the TMC and TMN phases can show significant plasticity [Citation6-8]. Though such materials can exhibit a brittle-ductile transition, the generally low fracture toughness at lower temperatures has limited their uses as engineering materials.
Recognising that the mechanical properties of these ceramics are phase dependent, one method to increase the fracture toughness is to yield a multiphase microstructure that can provide microstructural toughening. This can be achieved by reducing either the carbon or nitrogen content from the transition metal (M) and carbon/nitrogen (X) ratio. In the transition metal group VB carbides and transition metal group IVB nitrides, as the amount of X is reduced, the structure changes from an MX compound, which is typically a rocksalt structure, to MXy. When y is low enough, metal-rich phases will precipitate out of the MX matrix. These phases are metal-rich, close-packed nanolamellar structures denoted as either the zeta (ζ) [M4X3-x] or eta (η) [M3X2-x] phase depending on the metal: non-metal stoichiometry [Citation9]. These phases generally comprise a simple structural motif of hexagonal and cubic close-packed sequences. For the transition metal group IVB carbides and transitional metal group VB nitrides, these zeta and eta phases are not observed. Rather a series of vacancy ordered phases are predicted but often are not observed experimentally because of kinetic issues in processing these phases. The reader is referred to a recent computational study done by the authors that addresses the phase stability of these particular phases [Citation10,Citation11] and predictions from order parameter functional methods [Citation12,Citation13] and a review [Citation14]. The balance of this paper will address compositions that yield the zeta phase because of its unique effect on fracture toughness, but the model’s treatment is equally applicable to the eta phase because of the similar stacking sequences. As will be shortly discussed, a high-volume fraction of the zeta phase can yield significant increases in the fracture toughness in the tantalum carbides.
When the zeta phase volume fraction is greater than ∼80% in tantalum carbides, the fracture toughness can range between [Citation15-18]. This high fracture toughness has been attributed to a combination of the material’s microstructure [Citation16,Citation18] and the associated changes in bonding [Citation19,Citation20], both of which are a direct result of the chemical content. The zeta-phase yields a series of nano-laminates in the matrix that increase in the resistance to fracture as manifested in a rising R-curve [Citation18] which is a consequence of toughening mechanisms such as a crack deflection and crack bridging in the crack wake [Citation16,Citation18]. To date, the authors are unaware of any other studies which have studied high fracture toughness responses in the same group VB TMC family, where the zeta phase has been observed in niobium carbides [Citation21] and vanadium carbides [Citation21,Citation22]. Furthermore, the zeta (and eta) phase is also known to form in the group IVB TMN hafnium nitrides [Citation23-25]. Interestingly, this zeta phase has also been observed in titanium nitride but only at elevated temperatures [Citation26,Citation27]. As predicted by first principle calculations, the zeta phase is thermodynamically stable in the hafnium nitride system at absolute zero [Citation10,Citation28] and metastable, at least in its stoichiometric form, in the other systems reported above including tantalum carbide [Citation11,Citation29,Citation30]. In fact, the stability of the zeta phase in the tantalum carbide system has been the subject of much debate [Citation12,Citation31-33].
While the zeta phase has been reported to result in an increase in fracture toughness at room temperature in the tantalum carbides, there are no reports to date on how it affects elevated temperature properties in this or the other zeta forming ceramics. Such studies are likely to be limited because the zeta phase has an upper decomposition temperature above which it transforms into the substoichiometric B1 phase. This decomposition temperature is the highest in the hafnium nitride system at around 2250°C [Citation24], 2170°C in the tantalum carbide system, 1875°C in the vanadium carbon system, 1575°C in the niobium carbide system[Citation14] and 1290°C in the titanium nitrogen system [Citation27]. Thus, it does not provide precipitate strengthening at temperatures above these decomposition temperatures.
When the zeta phase is present in the carbides, a complex thin-lath-based microstructure is observed, (a). [Citation21,Citation34-36] which likely results in the observed increase in fracture toughness noted above. The complex microstructure may also give rise to anisotropic mechanical properties, including elasticity and strength; however, in a polycrystalline aggregate, this anisotropy may be reduced at the macroscale and, to the authors’ knowledge, no work to date has investigate the potentially induced anisotropy. Extensive work in the tantalum carbide system has demonstrated that the precipitation is controlled by orientation relationships between zeta phases and its relationship to either the monocarbide B1 TaC or trigonal Ta2C phase. For both phase systems, the zeta phase maintains alignment of its close-packed planes between these two phases [Citation34,Citation36]. In fact, TEM characterisation of the early stages of precipitation of the zeta phase in substoichiometric TaCx have shown the zeta phase nucleates as circular loops on the {111} planes [Citation34,Citation35]. However, a more complex relationship occurs in the hafnium nitride system as large grains of the zeta (and eta) phase are able to precipitate out and consume the rocksalt grain because of their thermodynamic stability [Citation25]. However, the complex lath-based microstructure can still occur in the hafnium nitride if the zeta phase precipitates out of slightly substoichiometric HfNx rocksalt structure, shown in (b). This indicates that all of these compounds have the potential for a microstructural-based toughening mechanism but raises questions regarding the origins of the microstructures as it relates to thermodynamic stability and kinetics.
Figure 1. (a) SEM micrograph of a multiphase tantalum carbide. The matrix is TaCx with the lath-like structures in the z-Ta4C3 phase. (b) Electron backscattered diffraction phase map from a section of a Hf-HfN diffusion couple from reference [Citation24] which shows lath-like ζ-Hf4N3 (blue) in a HfNx matrix (green) next to a large, single phase ζ-Hf4N3 grain (blue). (Colour available online).
![Figure 1. (a) SEM micrograph of a multiphase tantalum carbide. The matrix is TaCx with the lath-like structures in the z-Ta4C3 phase. (b) Electron backscattered diffraction phase map from a section of a Hf-HfN diffusion couple from reference [Citation24] which shows lath-like ζ-Hf4N3 (blue) in a HfNx matrix (green) next to a large, single phase ζ-Hf4N3 grain (blue). (Colour available online).](/cms/asset/0b0f5326-1cf5-4fb6-81ee-a47d1ab2e7ef/yaac_a_1510818_f0001_oc.jpg)
In this paper, we aim to address the questions that have been raised experimentally regarding the microstructures that occur in the presence of the zeta phase in its lath-based precipitate state using primarily equilibrium thermodynamics arguments. Our previous work specifically on the tantalum carbide system [Citation37] has demonstrated that the energetics of the zeta phase can be described in terms of a set of carbon depleted stacking faults. In this work, we describe a simple kinetics model that can help explain the phase formation of this phase in terms of the thermodynamic driving forces. We then extend our previous nanolamellar model (found in reference [Citation37]) to include the hafnium nitride system and use both models to explain the differences in microstructures observed in the presence of the zeta phase between the group IVB carbides and group VB nitrides.
A simple precipitation model
To better understand microstructures that form during the precipitation of the zeta phase, we focus our attention to first describing the solid-state precipitation from a parent nitride or carbide phase, presumably the rocksalt structure. The growth of a Widmanstätten microstructure is known to give rise to platelike structures because of the coherency of the platelike precipitates relative to the parent phase. This can be attributed to two contributing factors: (1) the asymmetry in the driving force of the growth process and (2) the kinetics of the diffusion process necessary for the precipitation process.
First, we will introduce the idea of the differences in driving force for precipitation. Consider a cylindrical precipitate, the free energy difference between the matrix and precipitate can be written as:where R is the radius, h is the height, Δgv is the volumetric free energy difference between the two phases, and γs and γt and the interfacial energies between the side walls and top/bottom of the cylinder, respectively. Assuming that the driving force is the (negative) of the derivative of the free energy with respect to the radius, R, and height, h, one finds
and
. If platelike growth is to occur, then
which results in the criteria that
. Similarly, the Wulff construction can be used to predict the equilibrium shape of the cylinder as γT/γS = h/(2R). Thus, at equilibrium, a cylinder with very low sidewall energy will have a very small height to radius aspect ratio, which is the same result obtained from the thermodynamic driving forces. Here we have ignored the potential contribution of anisotropic strain energy on morphology because of the similar elastic constants and volume of the parent and precipitating phase, as reported in [Citation29,Citation38]. This means, from a thermodynamic perspective, that the equilibrium shape (and hence growth) will be controlled by the differences, or anisotropy, of the surface energies.
An alternative, but similar, point of view of kinetics suggests that the morphology should be controlled largely by the rate of the diffusion of species through the interface [Citation39]. The arguments made for the difference in morphology is that diffusion occurs more quickly through the lateral (side) interfaces of the platelike precipitate than the top/bottom surfaces, resulting in the observed lath morphologies. Of course, it is difficult to separate out these two contributions from the differences in the thermodynamic driving forces for growth from the pure kinetics of diffusion.
The energetics of the zeta phase and related stacking faults
In order to understand the precipitation of the zeta phase from the rocksalt phases of the carbides and nitrides, we must understand both the bulk and interfacial chemistries and microstructure. The authors [Citation37] have recently investigated the bulk energetics of the zeta phase in the tantalum carbides using a nanolamellar model of these formation energies. They have pointed out that the predicted bulk energies of the zeta phase, the rocksalt structure, and related carbon depleted stacking fault structures lie on a straight line between the zeta phase and the rocksalt phase in tantalum carbide. This suggests there is no bulk driving force to organise the zeta phase over a disorganised carbon depleted arrangement of stacking fault phases. We also demonstrated that the nanolamellar model predicts zero interfacial energy between the close-packed planes between the zeta phase and the rocksalt (B1) TaC phase as well as C6 α-Ta2C phase (which would be γT in the above thermodynamic model), providing further evidence for the lack of long-range organisation of zeta phase grains in the tantalum carbon system. In this section, we extend this model to the other systems with the zeta phase: the vanadium carbides, niobium carbides and, most importantly, the hafnium nitrides.
The details of the nanolamellar model can be found in references [Citation20,Citation37] but it suffices to say that the energetics of the nanolamellar phases can be related to the local stacking sequences as well as chemistry. Thus, the cohesive energy of the nanolamellar structures per-unit-atom can be written as:(1)
(1) where nc is the number of non-metal atoms, ηi is the number of layers that belong to the types summed over from the list
(the list and values can be found in ), λi is the number of metal atoms in that layer and Γi is the energy associated with that layer. The key aspect of the model is the Γi, which are the fitted energies from Density Functional Theory (DFT) calculations. We have parameterised the model for the
values for the niobium carbide systems, vanadium carbide systems, and the hafnium nitride systems as listed in .
Table 1. Cohesive energy per atom in each type of metal layer Γi (eV).
The results of the nanolamellar model are plotted in in the form of the cohesive energies of the nanolamellar phases as a function of chemistry. The lines denote the model predictions and the data points represent direct DFT data. It is interesting to note that the results of our modelling effort in these systems mimic our results from the tantalum carbon system in that the DFT data appears to lie on the predicted straight line between the zeta phase and the rocksalt structure. The only differences one might point out is that the eta phases in all of these compounds are closer to lying on the convex hull (and it does in the hafnium nitride system) than in the tantalum carbide system. This provides proof that the bulk energetics regarding the preferences of nucleating organised nanolamellar phases (like the zeta phase) are similar to disorganised stacking faults. Furthermore, the experimentally observed phase differences between the hafnium nitride system (which can make full phase zeta (and eta) grains rather than laminates of these phases) as compared to the group VB carbides (which only yields high density of zeta laminates) is more complex than simply the bulk free energy behaviour, a point we will address later in the paper.
Figure 2. The cohesive energies of the nanolamellar forms of the (a) hafnium carbides (b) niobium carbides and (c) vanadium carbides. The squares denote the results of the DFT calculations while the solid lines denote the predictions of our nanolamellar model fit to the DFT data (see ). In the tantalum carbides (shown in reference [Citation37]) the C6 structure (Ta2C) lies on the convex hull. In all of the compounds discussed here, other M2X forms are stable, all of which have hcp metal atom stacking but differ in the ordering of the carbon/nitrogen atoms, but by small (meV/atom) energies [Citation10,Citation11,Citation13,Citation46]. Thus, all phases with an * denote metastable stacking fault phases in the figure.
![Figure 2. The cohesive energies of the nanolamellar forms of the (a) hafnium carbides (b) niobium carbides and (c) vanadium carbides. The squares denote the results of the DFT calculations while the solid lines denote the predictions of our nanolamellar model fit to the DFT data (see Table 1). In the tantalum carbides (shown in reference [Citation37]) the C6 structure (Ta2C) lies on the convex hull. In all of the compounds discussed here, other M2X forms are stable, all of which have hcp metal atom stacking but differ in the ordering of the carbon/nitrogen atoms, but by small (meV/atom) energies [Citation10,Citation11,Citation13,Citation46]. Thus, all phases with an * denote metastable stacking fault phases in the figure.](/cms/asset/0c895869-44f6-4fba-9342-0b60288ca5f9/yaac_a_1510818_f0002_oc.jpg)
It is also worth pointing out that the interfacial energies between close-packed planes in the rocksalt (B1) phase, {111}, and the zeta phase, {0001}, can be estimated from this model and it is identically zero regardless of the material system. This is a critical prediction for our simple precipitation model discussed above because it determines that the for the precipitation of the zeta phase in the rocksalt structure is zero by our theory, and in reality, should be very small. This is not surprising due to the coherent nature of the close-packed plane orientation relationships of these phases. Using this model further on the hafnium nitrogen system, it can be shown that the interfacial energies between the close-packed planes between the zeta and eta phases are also zero as well as the interfacial energies between the eta and Hf phases. The predictions of the interfacial energies based on our model for the hafnium nitride phase are listed in . These results suggest that not only would one expect that there would be thin lathes in the rocksalt HfN, but there are would be thin lathes in the other phases in the hafnium nitrogen system, which is clearly observed in recent experimental findings by the authors [Citation25].
Table 2. The interfacial energies in the hafnium nitrides predicted from the nanolamellar model
While the results of our DFT simulations combined with the nanolamellar model provide some insight to the energetics and kinetics of precipitation, we note that these results are still incomplete. First, it does not predict interfacial energies on the side (lateral walls) of the precipitation. Furthermore, these results do not clearly differentiate the hafnium nitrogen system from the group VB carbides. We will address each of these points in subsequent sections.
The interfacial energies of carbon/nitrogen depleted stacking faults
In order to provide a quantitative prediction of the side-wall interfacial energetics of the zeta phase, we must consider a mechanistic picture of the precipitation of carbon/nitrogen depleted stacking faults in the rocksalt structure. The basic idea was initially proposed by Lewis et al. [Citation36] and expanded up by others [Citation9,Citation37,Citation40] where the non-metal atoms are first depleted on a close-packed plane followed by a shear via a Shockley partial dislocation. This idea is schematically shown in (a,b). This basic model can provide the essential information required to estimate interfacial energies for the aforementioned model.
Figure 3. Schematic representation of (a) the MX matrix {111} planes as viewed from the <110> direction. Note the Roman letters represent the metal layers and the Greek letters represent the non-metal layers. The green highlighted rectangles represent every fourth non-metal layer that will be removed and the blue box the remaining layers to nucleate the correct composition of the zeta phase. (b) Upon removal of the non-metal layer, the two metal layers are now in contact and undergo a Shockley shear to create the create the correct stacking sequence of the zeta phase. (c) A macroscopic view of the zeta phase layering in the MeX matrix material with the identification of the top surface energy, γT, and the side wall surface energy, γs, for the zeta phase, ζ-M4X3. (Colour available online).
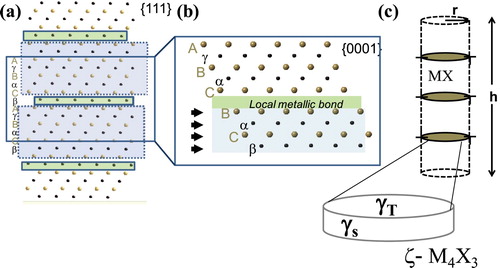
The energetics of the nucleation of a carbon depleted stacking fault can be approximated using a dislocation theory given that the boundary between the carbon depleted stacking fault and the matrix is simply a Shockley partial dislocation. Of course, the astute reader will point out that there could also be a change in z-axis bond length due to the non-metal depletion. However, Yu et al. [Citation19] has shown this to be minor and its effects can be neglected here. Thus, we can estimate the energy of a circular dislocation loop as:(2)
(2) where b is the Burgers vector, R is the radius of the loop, μ is the shear modulus, ν is the Poisson’s ratio and r0 is the inner cut-off of the dislocation. The elastic constants of the carbides and nitrides can be taken from experimental data when available or DFT data while the Burgers vector is simply
, where a is the lattice constant of rocksalt structure.
We note that the energetics of a simple dislocation loop can be used to estimate the interfacial energy associated with the nucleation of the zeta phase in the rocksalt structure. We further note that for a single unit cell of the zeta phase, we need three of these dislocations to from the zeta phase, as illustrated in (c). Thus, the effective surface energy is:(3)
(3)
Of course, this provides only an estimate of the interfacial energy of the side-walls of the precipitating zeta phase as it neglects the interaction between dislocation loops, among other things. Regardless of these issues, the model does provide a relatively clear and simple means of interfacial energy estimation which has captured the precipitation physics in a realistic manner. As noted in the introduction, TEM characterisation of the early stages of zeta precipitation in the tantalum carbides [Citation34,Citation35] has shown the zeta phase as circular loops on isolated {111} TaCx planes.
To demonstrate that this is indeed a significant interfacial energy, we examine the specific case for tantalum carbide. We take representative values for this system as b = 0.18 nm, c = 3.0 nm, μ = 234 GPa and ν = 0.22 (with the elastic constants from Dodd et al. [Citation41]). For the logarithmic term, we take , which corresponds to roughly a 1 nm loop with r0 = b. Using these values results in an estimate of the effective interfacial energy as
. This value is indeed quite large and is comparable to values of stacking fault energies and surface energies in the tantalum carbon system [Citation7,Citation19,Citation42,Citation43] and thus can be accepted as reasonable. This, of course, raises the issue of the absolute accuracy of our model in the prediction of the top/bottom interfacial energies (
), shown in (c). To address this issue, we directly computed the interfacial energy between the close-packed planes in the TaC and ζ-Ta4C3 phases directly in DFT and found the interfacial in energy to be
, which is again reasonable and within the accuracy of our calculations. Note that our model, though specifically detailed for the zeta phase, can easily be translated to the eta phase, which is a similar stacking fault phase, but with the carbon depleted on every third plane rather than every fourth plane as done for the zeta phase.
Discussion
The introduction of simple thermodynamics precipitation model appears to do a reasonable job of describing the morphology of the thin-lath-based microstructure that is often observed when the zeta phase precipitates out of the parent rocksalt structure. It suggests that the large values of will drive the formation of thin plate precipitates, which are often observed in experiments [Citation15,Citation34,Citation36,Citation44,Citation45]. Our nanolamellar model and direct DFT simulations confirm that the interfacial energy between the close-packed planes of the zeta phase and the rocksalt structure are always small, which promotes the asymmetric microstructure. This idea is furthered from our dislocation model of the interfacial energy between lateral sides of the precipitate, which are found to be quite high. Combining this with the nanolamellar model prediction that the bulk energetics of the zeta phase, when compared to random faults, suggest there is no energy gain in organising the faults clearly helps explain the experimentally observed microstructures in the group VB carbides in the presences of the zeta phase.
However, the study here is primarily based on the ideas of thermodynamic equilibrium and kinetics are surely important to the resultant microstructure. Specifically, the diffusion of carbon or nitrogen, in addition to faulting, is required for the phase transition to occur. Thus, fast cooling rates have the potential to suppress the precipitation of the zeta phase and lock in the high-temperature B1 phase while slow cooling may facilitate more complete transformation. In addition, even slower cooling rates or differing processing methods may allow the zeta phase to precipitate out as large grains or potentially yield vacancy ordered forms, as computationally shown to be competing phases [Citation10-14]. Further experimental studies will greatly benefit our understanding of the precipitation kinetics of the zeta phase and add data needed to further develop the model reported here.
Nonetheless, what is perhaps perplexing is the existence of both the thin-lath microstructure, as predicted here, as well as large grains that readily form in the hafnium nitrides, (b). The theoretical work presented here clearly does not demonstrate a fundamental difference between these systems. To understand the differences, we resort to both phase diagrams [Citation12,Citation13,Citation24] and DFT predictions[Citation10,Citation11,Citation28,Citation29] of the thermodynamics stability of the zeta phase in these systems.
In the group VB carbides, DFT simulations have suggested the stoichiometric zeta phase is metastable at low temperatures, lying just off the convex hull [Citation11,Citation29]. Similarly, experimental predictions usually list the zeta phase as a high-temperature phase in these materials [Citation12,Citation13]. Furthermore, extensive work on diffusion couples has demonstrated the stability of this phase, but the stability occurs in a substoichiometric form, about MC0.67 [Citation21,Citation33]. Collectively this suggests that the stoichiometric zeta phase is not stable, the substoichiometric form of the zeta phase is thermodynamically stabilised by entropy, all inhibiting the formation of large grains during precipitation. This results in the preservation of the easily nucleated thin-lath microstructure of the zeta phase. In comparison, experimental work and theoretical work agree in that the zeta (and eta) phases of the hafnium nitride system are stable at low temperatures [Citation10,Citation24,Citation28]. This suggests that during processing, the stoichiometric zeta phase is stable and can readily precipitate large grains within diffusion couples [Citation23-25]. The competition between bulk stability, which forms large grains, and the ability of the zeta phase to precipitate out of the rocksalt structure as a dual-phase microstructure with low thermodynamic driving force for coarsening results in a more competitive formation behaviour in hafnium nitride. The larger sidewall energies are able to be overcome by the larger volumetric energy difference to form this stable phase once the system is able to achieve a composition where it is the only stable phase and/or a different form of precipitation (a non-stacking mechanism) occurs. To determine if the nucleation of the single-phase zeta or eta hafnium nitrides is by another nucleation mechanism, more experimental work is required and beyond the scope of this paper, which is to provide a simple nucleation model for the lath shape morphologies based upon interfacial energy arguments. Regardless, the ability for the zeta phase to specifically reside as a thermodynamically equilibrium phase clearly dictates the type of morphology it will have within the ceramic – either as a single-phase grain or a complex and disorganised arrangement of thin laths. The ability to then tailor the bulk stability of the zeta phase by using metastable and stable transition metal and non-metal species creates an area for fruitful microstructure engineering of mechanical properties.
Conclusion
The zeta phase, which is a stacking fault based phase, has been shown, at least in the tantalum carbide system, to be extremely relevant in achieving high fracture toughness values. This has been associated, in part, with a microstructure composed of a highly dense, crisscross ζ-Ta4C3 lathes that provide a tortuous crack path. Through prior models, the authors have shown that the energetics of producing such a series of random stacking faults is equivalent between compositions between the stoichiometric zeta phase and the stoichiometric rocksalt structure. In this work, we have expanded that model to include the other group VB TMCs, namely vanadium and niobium carbides and have confirmed a similar trend. We have also expanded this model to include hafnium nitride, which also precipitates the zeta (and eta) phases as well and noted a similar agreement. We then expanded our stacking fault model to describe a simple precipitation-based model that would explain the shape and anisotropic growth of these laths. Recognising that the depletion of the non-metal species creates a stacking fault loop on the close-packed planes, we have estimated the side-wall energies created by this dislocation loop. We have found that the energies are nearly two orders of magnitude higher than the surface energies of the faulted phase with its close-packed orientation relationship. Consequently, this yields a significant energy difference that further drives the system to rapidly expand within the plane but not coarsening out-of-plane.
Recognising that the hafnium nitride system is able to readily precipitate single-phase grains of zeta (and eta) phase, we then considered the bulk stoichiometric thermodynamic phase stability of these phases between the carbides and nitrides. We noted that the stoichiometric zeta (and eta) phases are thermodynamically equilibrium phases whereas they are metastable in the carbides. Consequently, if the hafnium nitride system achieves the correct zeta (or eta) phase composition, the bulk thermodynamic driving force is sufficient to overcome the anisotropic interfacial energies for the growth of these lath shapes or possibly nucleates by a different mechanism that is still to be determined.
Acknowledgements
C. R. Weinberger and H. Yu recognise Air Force Office of Scientific Research grant FA9550-15-1-0217, Dr Ali Sayir programme manager. G.B. Thompson recognises Air Force Office of Scientific Research grant FA9550-15-1-0095, Dr. Ali Sayir programme manager. This work utilised the RMACC Summit supercomputer, which is supported by the National Science Foundation (awards ACI-1532235 and ACI-1532236), the University of Colorado Boulder and Colorado State University. The RMACC Summit supercomputer is a joint effort of the University of Colorado Boulder and Colorado State University. This paper was originally presented at the Ultra-High Temperature Ceramics: Materials for Extreme Environments Applications IV Conference (Windsor, UK) and has subsequently been revised and extended before consideration by Advances in Applied Ceramics.
Disclosure statement
No potential conflict of interest was reported by the authors.
ORCID
Additional information
Funding
References
- Toth L. Transition metal carbides and nitrides. New York: Academic Press; 1971.
- Storms E. The refractory carbides. New York: Academic Press; 1967.
- Upadhya K, Yang J, Hoffman W. Materials for ultrahigh temperature structural applications. Am Ceram Soc Bull. 1997;76:51–56.
- Williams WS. Physics of transition metal carbides. Mater Sci Eng A. 1988;105–106:1–10. doi: 10.1016/0025-5416(88)90474-0
- Rowcliffe DJ, Hollox GE. Plastic flow and fracture of tantalum carbide and hafnium carbide at low temperatures. J Mater Sci. 1971;6:1261–1269. doi: 10.1007/BF00552039
- Hoffman M, Williams WS. A simple model for the deformation behavior of tantalum carbide. J Am Ceram Soc. 1986;69:612–614. doi: 10.1111/j.1151-2916.1986.tb04817.x
- De Leon N, Yu X, Yu H, et al. Bonding effects on the slip differences in the B 1 monocarbides. Phys Rev Lett. 2015;114. doi:10.1103/PhysRevLett.114.165502.
- Kim C, Gottstein G, Grummon DS. Plastic flow and dislocation structures in tantalum carbide: deformation at low and intermediate homologous temperatures. Acta Metall Mater. 1994;42:2291–2301. doi: 10.1016/0956-7151(94)90308-5
- Demyashev GM. Review: transition metal-based nanolamellar phases. Prog Mater Sci. 2010;55:629–674. doi: 10.1016/j.pmatsci.2010.02.002
- Weinberger CR, Yu X-X, Yu H, et al. Ab initio investigations of the phase stability in group IVB and VB transition metal nitrides. Comput Mater Sci. 2017;138:333–345. doi: 10.1016/j.commatsci.2017.07.005
- Yu X-X, Weinberger CR, Thompson GB. Ab initio investigations of the phase stability in group IVB and VB transition metal carbides. Comput Mater Sci. 2016;112:318–326. doi: 10.1016/j.commatsci.2015.10.038
- Gusev AI, Rempel, AA, Magerl AJ. Disorder and order in strongly nonstoichiometric compounds: transition metal carbides, nitrides, and oxides. Berlin; New York: Springer; 2001.
- Gusev AI. Order–disorder transformations and phase equilibria in strongly nonstoichiometric compounds. Phys Uspekhi. 2000;43:1–37. doi: 10.1070/PU2000v043n01ABEH000647
- Weinberger CR, Thompson GB. Review of phase stability in the group IVB and VB transition metal carbides. J Am Ceram Soc. 2018;101:4401, doi:wiley.com/10.1111/jace.15768
- Hackett K, Verhoef S, Cutler RA, et al. Phase constitution and mechanical properties of carbides in the Ta-C system. J Am CeramSoc. 2009;92:2404–2407. doi: 10.1111/j.1551-2916.2009.03201.x
- Schulz BC, Lee H, Mogilevsky P, et al. Experimental investigation into the crack propagation in multiphase tantalum carbide ceramics. Mater Sci Eng A. 2017;695:315–321. doi: 10.1016/j.msea.2017.04.043
- Limeng L, Feng Y, Yu Z, et al. Microstructure and mechanical properties of spark plasma sintered TaC0.7 ceramics: rapid communications of the American ceramic society. J Am Ceram Soc. 2010;93:2945–2947. doi: 10.1111/j.1551-2916.2010.03908.x
- Sygnatowicz M, Cutler RA, Shetty DK. ζ-Ta4C3-x : a high fracture toughness carbide with rising-crack-growth-resistance (R-curve) behavior. Hsueh C-H, editor. J Am Ceram Soc. 2015;98:2601–2608.
- Yu H, Thompson GB, Weinberger CR. The role of chemistry and bonding in regulating fracture in multiphase transition metal carbides and nitrides. Extreme Mech Lett. 2017;17:1–6. doi: 10.1016/j.eml.2017.09.004
- Yu H. Stacking faults in the transition metal carbides and nitrides: stability and mechanical properties. Philadelphia (PA): Drexel University; 2017.
- Wiesenberger H, Lengauer W, Ettmayer P. Reactive diffusion and phase equilibria in the V–C, Nb–C, Ta–C and Ta–N systems. Acta Mater. 1998;46:651–666. doi: 10.1016/S1359-6454(97)00204-8
- Ghaneya A, Carlson O. Investigation of vanadium solid solution and zeta phase regions of the vanadium-carbon system. J Common Met. 1985;109:57–69. doi: 10.1016/0022-5088(85)90107-9
- Lengauer W, Rafaja D, Täubler R, et al. Preparation of binary single-phase line compounds via diffusion couples: the subnitride phases η-Hf3N2-x and ζ-Hf4N3-x. Acta Metall Mater. 1993;41:3505–3514. doi: 10.1016/0956-7151(93)90230-P
- Lengauer W, Rafaja D, Zehetner G, et al. The hafnium-nitrogen system: phase equilibria and nitrogen diffusivities obtained from diffusion couples. Acta Mater. 1996;44:3331–3338. doi: 10.1016/1359-6454(95)00438-6
- Schulz BC, DiPietro S, Weinberger CR, et al. Phase transformations and microstructural features in hafnium nitrides. J Eur Ceram Soc. 2017;37:4532. doi: 10.1016/j.jeurceramsoc.2017.06.016
- Lengauer W, Ettmayer P. The crystal structure of a new phase in the titanium-nitrogen system. J. Common Met. 1986;120:153–159. doi: 10.1016/0022-5088(86)90637-5
- Lengauer W. The titanium-nitrogen system: a study of phase reactions in the subnitride region by means of diffusion couples. Acta Metall Mater. 1991;39:2985–2996. doi: 10.1016/0956-7151(91)90031-U
- Zhang J, Oganov AR, Li X, et al. Pressure-stabilized hafnium nitrides and their properties. Phys Rev B. 2017;95. doi:10.1103/PhysRevB.95.020103.
- Yu X-X, Weinberger CR, Thompson GB. Ab initio investigations of the phase stability in tantalum carbides. Acta Mater. 2014;80:341–349. doi: 10.1016/j.actamat.2014.07.070
- Yu S, Zeng Q, Oganov AR, et al. Phase stability, chemical bonding and mechanical properties of titanium nitrides: a first-principles study. Phys Chem Chem Phys. 2015;17:11763–11769. doi: 10.1039/C5CP00156K
- Brizes WF, Tobin JM. Isolation of the zeta phase in the system tantalum-carbon. J Am Ceram Soc. 1967;50:115–116. doi: 10.1111/j.1151-2916.1967.tb15055.x
- Zaplatynsky I. Observations on zeta phase in the system Ta-C. J Am Ceram Soc. 1966;49:109–109. doi: 10.1111/j.1151-2916.1966.tb13223.x
- Gusev AI, Kurlov AS, Lipatnikov VN. Atomic and vacancy ordering in carbide ζ-Ta4C3-x (0.28⩽x⩽0.40) and phase equilibria in the Ta–C system. J. Solid State Chem. 2007;180:3234–3246. doi: 10.1016/j.jssc.2007.09.015
- Morris RA, Wang B, Matson LE, et al. Microstructural formations and phase transformation pathways in hot isostatically pressed tantalum carbides. Acta Mater. 2012;60:139–148. doi: 10.1016/j.actamat.2011.09.036
- Morris RA, Wang B, Butts D, et al. Variations in tantalum carbide microstructures with changing carbon content. Int J Appl Ceram Technol. 2013;10:540–551. doi: 10.1111/j.1744-7402.2012.02761.x
- Lewis MH, Billingham J, Bell PS. Non-stoichiometry in ceramic compounds. Electron Microsc Struct Mater. University of California Press; p. 1084–1115.
- Yu H, Guziewski M, Thompson GB, et al. A model for understanding the formation energies of nanolamellar phases in transition metal carbides and nitrides. Model Simul Mater Sci Eng. 2016;24:055004. doi: 10.1088/0965-0393/24/5/055004
- Yu X-X, Thompson GB, Weinberger CR. Influence of carbon vacancy formation on the elastic constants and hardening mechanisms in transition metal carbides. J Eur Ceram Soc. 2015;35:95–103. doi: 10.1016/j.jeurceramsoc.2014.08.021
- Cahn RW, Haasen P, editors. Physical metallurgy. 4th, rev. and enhanced ed. Amsterdam; New York: North-Holland; 1996.
- Yvon K, Parthé E. On the crystal chemistry of the close-packed transition-metal carbides. I. The crystal structure of the ζ-V, Nb and Ta carbides. Acta Crystallogr B. 1970;26:149–153. doi: 10.1107/S0567740870002091
- Dodd SP, Cankurtaran M, James B. Ultrasonic determination of the elastic and nonlinear acoustic properties of transition-metal carbide ceramics: TiC and TaC. J Mater Sci. 2003;38:1107–1115. doi: 10.1023/A:1022845109930
- Yu H, Bahadori M, Thompson GB, et al. Understanding dislocation slip in stoichiometric rocksalt transition metal carbides and nitrides. J Mater Sci. 2017;52:6235–6248. doi: 10.1007/s10853-017-0857-4
- Wang B, De Leon N, Weinberger CR, et al. A theoretical investigation of the slip systems of Ta2C. Acta Mater. 2013;61:3914–3922. doi: 10.1016/j.actamat.2013.01.047
- Santoro G. Variation of some properties of tantalum carbide with carbon content. Trans Metall Soc AIME. 1963;227:1361–1368.
- Rowcliffe DJ, Thomas G. Structure of non-stoichiometric TaC. Mater Sci Eng. 1975;18:231–238. doi: 10.1016/0025-5416(75)90174-3
- Epicier T, Dubois J, Esnouf C, et al. High temperature powder neutron diffraction studies of structural transformations in transition metal hemicarbides M2C1−x. Phys B Condens Matter. 1989;156–157:44–46. doi: 10.1016/0921-4526(89)90581-4