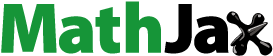
ABSTRACT
Mixtures of glass residues, deriving from the plasma processing of municipal solid waste (‘Plasmastone’), and recycled glasses have been already converted into highly porous glass-ceramics by application of an inorganic gel casting technique (foaming, by intensive mechanical stirring, of alkali activated slurries) followed by sintering at 1000°C. The full potential of recycled glass, however, has not been disclosed yet. The present investigation, in fact, demonstrates that boro-alumino-silicate glass, from discarded pharmaceutical vials, may allow for sintering of cellular glass-ceramics at particularly low temperature, i.e. at 800°C. The full stabilisation of heavy metals from Plasmastone (already assessed for treatments at 1000°C) is not compromised, whereas the low processing temperatures favour the separation of magnetite, in turn imparting new functionalities (e.g. electromagnetic shielding) to waste-derived glass-ceramic foams.
Introduction
Upcycling of vitreous residues into monolithic and cellular glass-ceramics have been extensively studied in the last decades in order to economically justify the high costs related to vitrification as well as to avoid landfilling these residues [Citation1–3].
In the present paper, we refer to a specific vitreous residue technically known as ‘Plasmastone’, deriving from enhanced landfill mining (ELFM) activities. According to ELFM, landfills are first excavated and then used as a source of fuels and other resources; more precisely, after a preliminary separation of metals, the waste is employed as solid recovered fuel (SRF), exploiting several technologies, including plasma gasification [Citation4,Citation5]. Plasma gasification converts the SRF into a synthetic gas (‘Syngas’), while the inorganic fraction melts; the melt actually consists of two phases, i.e. a liquid metal alloy, extracted from the bottom of the plasma reactor, and a slag, cooled down as Plasmastone. This glass represents the fraction of waste ‘not directly exploitable’ (as fuel, or as raw material in metallurgy): it is evident that the sustainability of the overall process will be improved reusing also Plasmastone. Preliminary studies have been already applied in the field of building materials, in the form of inorganic polymer binder and porous glass-ceramics [Citation5,Citation6].
Concerning the development of highly porous glass-ceramics, Plasmastone may be processed according to a technique (‘inorganic gel casting’) [Citation7], combining alkali activation of glass suspensions, gelation, low temperature mechanical foaming and viscous flow sintering. In fact, suspensions of Ca-rich silicate glasses may harden just by the formation of calcium silicate hydrates (C–S–H) [Citation6,Citation8], and extensive foaming may be achieved by air incorporation, in turn due to intensive mechanical stirring, with the help of a surfactant, before complete setting. Firing treatments, unlike in conventional glass-based foams [Citation2,Citation9], do not determine any substantial foaming (operated by chemical reactions involving C, SiC, or other additives), but they just stabilise the porous structure by viscous flow sintering.
The remarkable crystallisation of Plasmastone, in turn due to the particular chemical formulation (despite the reducing conditions applied in the plasma gasificator, aimed at maximising the extraction of iron as component of the liquid alloy, Plasmastone still contains a high quantity of iron oxide [Citation5], which is known to catalyse the formation of iron silicates [Citation10]), greatly complicates the sintering. The viscous flow may be improved by addition of recycled glass, in form of soda-lime glass, from glass containers, or boro-alumino-silicate glass, from discarded pharmaceutical vials [Citation6]; the latter improves also the chemical stability of the final glass-ceramic products [Citation3,Citation6,Citation11].
The present investigation concerns significant extensions of the ‘inorganic gel casting’ approach to Plasmastone combined with boro-alumino-silicate glass. Treatments at 800°C, instead of 1000°C, were intended to modify the phase assemblage of the obtained porous glass-ceramics, with special attention to iron oxide phases, known to provide interesting functionalities in waste-derived glass-ceramics (owing to their impact on magnetic, optical or electrical properties) [Citation9,Citation11]. In particular, we referred to the shielding effectiveness [Citation12,Citation13], i.e. the potential to minimise the human exposure to electromagnetic fields and to avoid electromagnetic interferences. This functionality is reputed to increase the ‘value’ of the final products and thus contribute positively to the sustainability of waste processing.
Materials and methods
Plasmastone (PS) and boro-alumino-silicate (BSG) glass, from discarded pharmaceutical vials, were gently provided by Scanarc (Sweden) and Nuova OMPI (Piombino Dese, Padova, Italy), respectively. The two glasses were received in the form of coarse fragments and ball milled into powders below 75 µm. The Plasmastone employed in this studied presented the following main composition (in wt. %): SiO2: 34.3; CaO: 23.2; Fe2O3: 24.8; Al2O3: 14.8; MgO: 1.2 and Na2O: 0.2. In addition, the chemical composition of boro-alumino-silicate glass was (in wt. %): SiO2: 72; B2O3: 12; Al2O3: 7; Na2O: 6; K2O: 2; CaO: 1.
Fine waste glass powders (100 wt-% Plasmastone or 70 wt-% Plasmastone 30 wt-% boro-alumino-silicate glass) were added to an alkaline activating solution of 2.5M NaOH/KOH (ratio 1:1). The overall solid loading was 68 wt-% and the suspensions were mechanically stirred at 400 rev min−1. After 3 h of partially dissolution of the fine powders, the suspensions were poured in closed polystyrene moulds with a diameter of 60 mm. Then, the suspensions were subjected to a first hardening step at 75°C (4 h for foams with only Plasmastone and 6 h for foams with boro-alumino-silicate glass). Triton X-100 surfactant (4 wt-%, polyoxyethylene octyl phenyl aether – C14H22O(C2H4O)n, n = 9–10, Sigma-Aldrich, Gillingham, UK) were added to the formed gels, which were later subjected to intensive mechanical stirring at 2000rpm. Finally, the foamed suspensions were dried at 40°C for 48 h, followed by demoulding. The green foams were fired at 800°C, with heating rate of 10°C min−1 and a holding time of 1 h [Citation6].
The mineralogical analysis of powdered samples was performed by using X-ray diffraction (XRD) (Bruker D8 Advance, Karlsruhe, Germany), operating with CuKα radiation, 0.15418 nm, 40 kV–40 mA, 2θ = 10–70°, step size 0.05°, 2 s counting time. The mineral phases were identified by using the Match!® program package (Crystal Impact GbR, Bonn, Germany), supported by data from Powder Diffraction File (PDF)-2 database (International Centre for Diffraction Data, Newtown Square, PA, USA).
The fired samples were cut into cubes of approximately 10 mm × 10 mm × 10 mm. The weight and volume of at least three samples were determined by using a digital balance and calliper, respectively. The bulk density was calculated by the weight-to-volume ratio of the measured values. The apparent and true densities of the material were measured by using a He gas pycnometer (Micromeritics AccuPyc 1330, Norcross, GA) with whole samples and with finely crushed powders, respectively.
The compressive strength of the fired foams was assessed at room temperature by using an Instron 1121 UTM (Instron Danvers, MA). The crosshead speed used was of 1 mm min−1 and 8–12 samples of each group were tested.
The morphological structure of green and fired foams of Plasmastone/boro-alumino-silicate glass was characterised by optical stereomicroscopy (AxioCam ERc 5 s Microscope Camera, Carl Zeiss Microscopy, Thornwood, New York, USA) and scanning electron microscopy (FEI Quanta 200 ESEM, Eindhoven, The Netherlands).
The chemical stability of Plasmastone/boro-alumino-silicate glass glass-ceramics was assessed by means of leaching test [Citation14]. The foam was crushed into pieces smaller than 4 mm and added to a plastic flask containing pure distilled water (L/S ratio of 10), which was then mixed for 24 h at room temperature. The eluate was obtained by filtering and centrifuging the suspension. The heavy metals content was measured by inductively coupled plasma mass spectrometry (ICP-OES, Spectro Genesis, Germany) and compared to leachate values allowed for waste acceptable at landfills for inert waste [Citation15].
Electromagnetic shielding effectiveness was determined on hollow cylindrical samples of Plasmastone/boro-alumino-silicate glass foam (external diameter: 36 mm; internal diameter: 7 mm; thickness: 8 mm), by using a modified coaxial waveguide (CW) connected to a vector network analyser (VNA, E5061B, Keysight Technologies, Santa Rosa, CA, USA), with frequency range of 0.1 MHz–3 GHz.
Results and discussion
The XRD patterns in show that Plasmastone in the as received condition presented an amorphous structure, with the characteristic ‘halo’ of glass materials. Interestingly, the crystallisation induced by the firing treatment was more pronounced in the foams developed by addition of boro-alumino-silicate glass. This was quite surprising, since PS was ‘diluted’ by a glass (BSG) not prone to crystallisation upon sintering at 800°C [Citation16]. In our opinion, this could be explained on the basis of the presence of interfaces between softened PS and softened BSG, with chemical gradients promoting ionic interdiffusion and modifying the crystallisation sequence. In particular, it can be observed that hedenbergite (Ca(Fe0.821Al0.179)(SiAl0.822Fe0.178)O6, PDF #78-1546), andradite (Ca3Fe2(SiO4)3, PDF#84-1935), wollastonite (CaSiO3, PDF #84-0655) and magnetite (Fe3O4, PDF #89-0691) appeared in both samples, deriving from only PS and from PS/BSG mixture; however, with BSG addition, andradite peaks decreased (see, in particular, the peak at 2θ∼33°), while those corresponding to hedenbergite and wollastonite increased. The change is even more significant considering the phase assemblages at 1000°C, analysed previously [Citation6], with samples from pure Plasmastone (featuring gehlenite, Ca2Al2SiO7, along with hedenbergite and andradite) being more crystallised than those from PS/BSG mixture (featuring hedenbergite and andradite only). The addition of a second glass is confirmed as a fundamental tool to adjust the properties of waste-derived glass-ceramics: glass-ceramic products can be ‘tuned’ not only operating operating on the formulation before vitrification, but also introducing a secondary glass after vitrification.
The density and porosity data of foams from pure PS and PS with the addition of BSG are reported in . Both materials were highly porous, with porosity exceeding 74 vol.-%, and mostly open, as illustrated by . The open-celled morphology achieved upon low temperature foaming of hardened suspensions is evident from (a,b); the firing did not determine a substantial change in the morphology, as testified by (c,e).
Figure 2. Morphology of Plasmastone-derived glass-ceramic foams (left: low magnification; right: details): (a,b) PS/BSG glass in the green state; (c,d) Pure PS, after firing at 800°C, for 1 h; (e,f) PS/BSG glass mixture, after firing at 800°C, for 1 h.
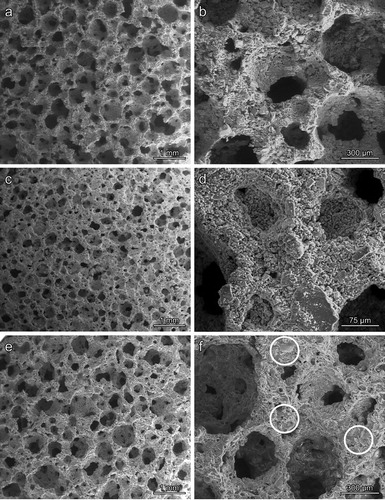
Table 1. Physical and mechanical properties and leaching behaviour of Plasmastone-derived foams.
If we consider the model for the scaling of compressive strength of cellular bodies [Citation17] – according to the bending strength of the solid phase (σbend) and the relative density (ρrel = 1−P, where P is the porosity) − we may neglect the linear term in the hypothesis of no mechanical contribution from cell walls, as follows:The equation could be used, on the basis of the measured compressive strength, to compute the bending strength of the solid phase, as a ‘quality factor’ of the developed cellular glass-ceramics. As previously observed for foams fired at 1000°C, samples from pure Plasmastone were quite weak, the bending strength of the solid phase being slightly above 10 MPa. Low temperature setting led to poor joining between adjacent particles, as shown by (d); the firing at 800°C, with crystallisation, simply ‘froze’ the structure already achieved after gelification. On the contrary, the addition of BSG had a dramatic impact on strength, the estimated value for σbend being nearly identical to that for foams fired at 1000°C [Citation6] and comparable to the bending strength of dense waste-derived glass-ceramics [Citation1]. (f) substantiate this, illustrating the change from poorly bound powders, before firing, to effectively sintered struts, after firing (see the circles in (f), underlining the presence of glassy phase from BSG glass). The remarkable porosity, accompanied by good mechanical properties, makes the optimised foam quite attractive, in buildings, as thermal and acoustic insulators.
Any commercial application cannot be envisaged, however, before the assessment of chemical stability. shows that foams from PS/BSG mixtures had a very limited leaching; the release of metal ions was far below the limits for inert materials [Citation15]. Pure PS-derived foams were not tested, considering the poor mechanical properties; stronger foams, developed by sintering PS mixed with soda-lime glass, from 800 to 1000°C, did not exhibit a comparable level of stabilisation of heavy metals [Citation6]. The newly developed foams, fired at 800°C, can be compared only with previous foams, with the same secondary glass, fired at 1000°C [Citation5]. We may say that BSG appears as an ideal addition for Plasmastone to be converted in useful materials, by reducing the temperature required for achieving a good densification of struts as well as good mechanical properties and good stabilisation of pollutants. The adopted temperature, in the present study (800°C), is also favourably lower than that adopted for commercial glass foams [Citation2,Citation9].
The reduced firing temperature had a significant impact also on additional functionalities. When fired at 1000°C, foams from PS/BSG mixture did not feature iron oxide as a separate phase, but just included in Ca-Fe silicates (hedenbergite and andradite) [Citation6]. On the contrary, traces of magnetite, i.e. a ferri-magnetic phase, in foams fired at 800°C, were revealed by the diffraction peaks in and by the fact that foamed samples were weakly attracted by permanent magnets.
Like analogous foams (i.e. developed by the same combination inorganic of gel casting and firing, and featuring ferri-magnetic phases) obtained from soda-lime glass and metallurgical slag [Citation17], foams from PS/BSG mixture fired at 800°C were subjected to preliminary electromagnetic shielding studies. Magnetite is not interesting, in the specific field, only for the magnetic behaviour, but for a distinctive combination of properties (electrical conductivity, atomic and electronic polarisation) [Citation18]. The measured value of shielding efficiency (SE), as shown by , was lower than 0.1 dB for frequencies below 1.7 GHz, but increased up to 2.8 dB for a frequency of 2.1 GHz. The shielding effect is not particularly strong, but it should be observed that it relies just on the nature of the adopted waste, unlike other electromagnetic shields, based on specific composite design (e.g. carbon fibres in cement-based composites) [Citation19]; it also compares favourably with the shielding effectiveness of denser waste-derived clay ceramics (although tested in a different frequency range [Citation20]). The developed foams could contribute to the definition of a new generation of building materials, coupling thermal and acoustic insulation (connected to the high porosity) with the reduction of human exposure to electromagnetic fields and of electromagnetic interferences.
Conclusions
We may conclude that:
Boro-alumino-silicate glass has a significant potential in reducing the sintering temperature required to consolidate porous structures determined by mechanical stirring of alkali activated Plasmastone-based suspensions;
The reduction of firing temperature does not compromise the stabilisation of heavy metals, that could be released from Plasmastone;
Owing to the limited sintering temperature, iron oxide remains as separate phase, in the form of magnetite; compared to pure Plasmastone, a Plasmastone-glass mixture enhances the formation of hedenbergite and wollastonite;
The presence of a separate iron oxide phase may be exploited for new functionalities; in particular, foams from Plasmastone-glass mixture exhibit some potential in electromagnetic shielding.
Disclosure statement
No potential conflict of interest was reported by the authors.
ORCID
Enrico Bernardo http://orcid.org/0000-0003-4934-4405
Additional information
Funding
References
- Karamanov A. Granite like materials from hazardous wastes obtained by sintercrystallisation of glass frits. Adv App Ceram. 2009;108(1):14–21. doi: 10.1179/174367608X364302
- Fernandes HR, Tulyaganov DU, Ferreira JMF. Production and characterisation of glass ceramic foams from recycled raw materials. Adv App Ceram. 2009;108(1):9–13. doi: 10.1179/174367509X344971
- Ponsot I, Detsch R, Boccaccini AR, et al. Waste derived glass ceramic composites prepared by low temperature sintering/sinter-crystallisation. Adv App Ceram. 2015;114(Suppl. 1):S17–S25. doi: 10.1179/1743676115Y.0000000044
- Jones PT, Geysen D, Tielemans Y, et al. Enhanced landfill mining in view of multiple resource recovery: a critical review. J Clean Prod. 2013;55:45–55. doi: 10.1016/j.jclepro.2012.05.021
- Machiels L, Arnout L, Yan P, et al. Transforming enhanced landfill mining derived gasification/vitrification glass into low-carbon inorganic polymer binders and building products. J Sustain Metall. 2016;3:1–11.
- Monich PR, Rincon Romero A, Höllen D, et al. Porous glass-ceramics from alkali activation and sinter-crystallization of mixtures of waste glass and residues from plasma processing of municipal solid waste. J Clean Prod. 2018;188:871–878. doi: 10.1016/j.jclepro.2018.03.167
- Rincón A, Giacomello G, Pasetto M, et al. Novel ‘inorganic gel casting’ process for the manufacturing of glass foams. J Eur Ceram Soc. 2017;37:2227–2234. doi: 10.1016/j.jeurceramsoc.2017.01.012
- Garcia-Lodeiro I, Aparicio-Rebollo E, Fernández-Jimenez A, et al. Effect of calcium on the alkaline activation of aluminosilicate glass. Ceram Int. 2016;42:7697–7707. doi: 10.1016/j.ceramint.2016.01.184
- Chinnam RK, Francis AA, Will J, et al. Review. Functional glasses and glass-ceramics derived from iron rich waste and combination of industrial residues. J Non Cryst Solids. 2013;365:63–74. doi: 10.1016/j.jnoncrysol.2012.12.006
- Höland W, Beall GH. Glass ceramic technology. Westervile (OH): The American Ceramic Society; 2002.
- Ponsot IMMM, Pontikes Y, Baldi G, et al. Magnetic glass ceramics by sintering of borosilicate glass and inorganic waste. Materials. 2014;7:5565–5580. doi: 10.3390/ma7085565
- Maschio A, Bernardo E, Desideri D, et al. Shielding effectiveness of construction materials. Int J Appl Electromagn Mech. 2016;52:137–144. doi: 10.3233/JAE-162089
- Kumari P, Tripathi P, Parkash O, et al. Electromagnetic interference shielding effectiveness of MgO−Al2O3−SiO2 glass–ceramic system. Bull Mater Sci. 2017;40:1497–1501. doi: 10.1007/s12034-017-1505-y
- Norm EN 12457-4; 2002.
- Directive 2003/33/EC. Off. J. Eur. Communities; 2003.
- Gibson LJ, Ashby MF. Cellular solids: structure and properties. Cambridge: Cambridge University Press; 1999.
- Rincón A, Desideri D, Bernardo E. Functional glass-ceramic foams from ‘inorganic gel casting’ and sintering of glass/slag mixtures. J Clean Prod. 2018;187:250–256. doi: 10.1016/j.jclepro.2018.03.065
- Al-Ghamdi AA, Al-Hartomy OA, Al-Salamy F, et al. Novel electromagnetic interference shielding effectiveness in the microwave band of magnetic nitrile butadiene rubber/magnetite nanocomposites. J Appl Polym Sci. 2012;125:2604–2613. doi: 10.1002/app.36371
- Zornoza E, Catalá G, Jiménez F, et al. Electromagnetic interference shielding with Portland cement paste containing carbon materials and processed fly ash. Mater Constr. 2010;60:21–32.
- Bantsis G, Sikalidis C, Betsiou M, et al. Ceramic building materials for electromagnetic interference shielding using metallurgical slags. Adv Appl Ceramics. 2010;110:233–237. doi: 10.1179/1743676111Y.0000000009