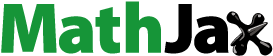
ABSTRACT
High entropy carbides (HECs) are novel materials developed in recent years that have attracted a lot of research interests. Unlike traditional carbides (containing one or two metals), HECs with multiple metals could form a very large number of different compositions that could have interesting and promising properties. The high entropy effect stabilises multi-component carbide phases and forms compositions that might otherwise not be stable. After several years of investigation of HECs, several methods of synthesising HECs have been developed. The microstructures and properties of HECs have been studied and compared with traditional carbides. Many interesting discoveries in HECs have been made. This paper reviews the theories, technologies, findings and insights gained from previous studies on HECs. The basic theory of HECs, the prediction of synthesisability of HEC phases from theoretical calculations, and some rules observed from experimental results are summarised. The preparation methods of HECs (powders, coatings, films and ceramics) and their microstructures are reviewed. Their properties, including thermal and electrical, mechanical and tribological, and oxidation, irradiation, and corrosion resistance of HECs are reviewed and discussed. Compared with traditional carbides, there is a great potential to develop new HECs due to their designable and complex compositions, and this review can guide future studies.
Introduction
Ultra-high temperature ceramics (UHTCs) are typically defined as materials with melting temperatures greater than 3000°C, including carbides, nitrides, oxides and diborides of the Group IVB, VB and VIB transition metals [Citation1,Citation2]. In addition to having ultra-high melting temperatures, UHTCs also display good mechanical properties and excellent thermal and chemical stabilities; they can therefore be used as structural or protective materials in extreme environments [Citation3–6]. For advanced technologies, such as nuclear reactors, jet engines and hypersonic vehicle leading edges, the materials used should be able to withstand a combination of many different extreme environments including high temperature, mechanical stress, corrosion and wear [Citation2,Citation3,Citation7,Citation8]. As current UHTCs may be difficult to fulfil the ever-increasing application demands, there is a need to develop new and improved materials.
In recent years, the field of high entropy ceramics has attracted much research interest, stimulated by the discoveries on high entropy alloys (HEAs). HEAs with a highly disordered and homogeneous chemical composition and a single crystalline phase have been reported to have remarkable properties, such as high strength [Citation9,Citation10], hardness [Citation10–12], wear resistance [Citation13,Citation14] and corrosion resistance [Citation15,Citation16]. Recently, Rost et al. [Citation17] have demonstrated the first crystalline bulk high entropy ceramic ((Co0.2Cu0.2Mg0.2Ni0.2Zn0.2)O), indicating that entropy stabilised single phase ceramics can be formed at sufficiently high temperatures from an endothermic transformation [Citation18]. Since then, the concept of the high entropy ceramics has been proposed [Citation19,Citation20], and a series of high entropy borides [Citation21–23], carbides [Citation24–28], oxides [Citation29–32], nitrides [Citation33–35], carbonitrides [Citation35–37] and sulphides [Citation38,Citation39] have been rapidly developed.
Carbides have great mechanical properties and good resistance to oxidation, corrosion and wear, making them promising for application as UHTCs for aerospace applications as well as drill bits and cutting tools in the mining and industry [Citation40,Citation41]. High entropy carbides (HECs) are therefore attracting considerable research interest. This paper gives an overview of the latest research progress on HECs, including theories and predictions, processing and microstructures, and properties.
Basic theories of HECs
Basic theory of high entropy materials
For multi-element solid solutions, the maximum molar configurational entropy is obtained when all of the components are equimolar. The Gibb’s free energy (G) can then be calculated as follows:
(1)
(1)
(2)
(2) where H is enthalpy, S is entropy, T is temperature, R is the gas constant, and N is the number of components. Since the Gibb’s free energy decreases with increasing number of components, the formation of single multi-element solid solution is promoted instead of forming intermediate compounds [Citation42]. It is widely acknowledged that molar configurational entropy could have a significant influence when there are ≥5 components in the solid solution, which gives S ≥ 1.61R [Citation18,Citation43]. A large lattice distortion would be introduced by the different atom sizes of components; high entropy materials are thus expected to have unexpected properties.
Based on the basic theory of high entropy materials, HECs can be defined as those single-phase solid solutions carbides with a random arrangement of different metal cations (>4) in equiatomic proportions, showing a characteristic of crystallographic order but chemical disorder.
Predicting the synthesisability of single phase HECs
A descriptor of entropy forming ability (EFA) for carbides was proposed by Sarker et al., based on the randomly calculated energy distribution (Hi) of possible configurations of carbides [Citation24]. The inverse of the standard deviation, σ, of the spectrum of Hi is used to define the descriptor EFA in (eV/atom)−1. The EFA for an N-species system is defined as follow:
(3)
(3) where
(4)
(4) where n is the number of the sampled configurations and gi is the degeneracy. Hmix is the enthalpy of mixed phases, which approximates to the average of Hi of configurations:
(5)
(5) The narrower the spectrum, the easier it is to introduce configurational disorder into the system to form a single phase, and thus the greater EFA.
The EFA of 56 carbide compositions containing five metals selected from 8 interested refractory metals (Hf, Nb, Mo, Ta, Ti, V, W, and Zr) were calculated using density functional theory (DFT) within the Automatic-Flow partial occupation (AFLOW-POCC) algorithm. Nine interesting compositions were fabricated and investigated to verify the descriptor [Citation24]. displays the calculation results of EFA and the experimental results for nine 5-metal compositions. The results indicate that the first six compositions with higher EFA (greater than or equal to 50) displayed a desired rock-salt crystal structure, while the other three compositions with lower EFA (less than or equal to 45) had secondary phases. Compositions with EFA lower than 45 (not listed here) were expected to be difficult to form as homogeneous and single-phase HECs. These results proved that the descriptor can quantitatively predict the relative possibility of forming a single-phase structure for each of the 5-metal compositions, and correctly predict the most promising candidates for experimental synthesis. The calculation methods of EFA were developed using Machine learning (ML), which is more efficient [Citation28]. The EFA of 70 new 5-metal compositions containing metals from the Group VIB metals (Cr, Mo and W) were calculated and the typical compositions were verified in experiments. Again, EFA successfully predicted the relative possibility of the formation of HEC phases.
Table 1. The selected data of ab-initio calculated EFA for nine 5-metal carbides which have been verified by experiments [Citation24].
The multi-element effects
In the studies of HEAs, there are four so-called core effects: high entropy, lattice distortion, sluggish diffusion and cocktail effects [Citation44]. It has been found that these core effects can similarly apply to other high entropy materials including HECs. Some theories relating the same core effects as HEAs have been proposed on HECs based on experimental observations.
It is well known that the carbides containing metals from only Group IVB and VB are likely to be enthalpy and entropy stabilised, and the Group VIB carbides do not form a room-temperature stable FCC structure due to their high enthalpy of formation. Thus, introducing a large amount of metals from Group IVB may drive the multi-element system to instability. As found in the results for the EFA of 5-metal carbides, the addition of W and Mo in the compositions reduced the probability of forming a single HEC phase [Citation24]. Therefore, the successful introduction of more than one Group VIB metal into the composition, such as the fabrication of (VNbTaMoW)C and (Ti, Zr, Hf, V, Nb, Ta, Mo, Cr)C, is evidence of a ‘high entropy effect’ [Citation18,Citation27,Citation28].
Similar to HEAs, the lattice of HECs is highly distorted due to the different atomic sizes of different atoms. Although there is no study on the effect of lattice distortion on the crystallinity and grain size of HECs so far, the enhanced hardness as a typical result of lattice distortion has been widely reported on HECs [Citation25,Citation26,Citation45]. For instance, the hardness of (HfTaZrNb)C ceramic (36.1 GPa) showed a 30% enhancement compared to the value of the rule of mixture (ROM) of the corresponding monocarbides, and it was also higher than the 32.9 GPa for (Hf-Ta)C [Citation25]. In addition to mechanical properties, the ‘lattice distortion effects’ would also affect the physical and chemical properties of HECs, such as thermal and electrical conductivities, which will be discussed in detail in the chapter on properties (Chapter 4).
The diffusion of atoms plays an important role in phase transformations. The formation of HEC phase, growth of HEC grains and phase transformations would be depressed by the lower diffusion kinetics of HECs. This is ‘sluggish diffusion effect’ of HEAs applied to HECs. In experiments, HEC grains in a near-equimolar (CrNbTaTiW)C film were stable at elevated temperatures (600°C), while the Ta/W-rich (CrNbTaTiW)C film transformed to polycrystalline at the same temperature [Citation46].
Each element in a composition has its own effect on the microstructure and properties of HECs. In an HEC, the interaction of different elements will also affect their own effect, showing a combined effect. This is a brief description of so-called cocktail effects of HEAs applied to HECs. Most of properties studies on HECs found a difference between the result of HECs and the ROM value, ‘cocktail effects’ could be considered to play a partial role in this difference.
A deep understanding of the core effects will help to understand and predict the formation or the properties of HECs, and to develop some novel HECs with better performance. In an experiment, a single-phase (HfTaZrNb)C and a multi-phase (HfTaZrTi)C with ZrC were fabricated by spark plasma sintering (SPS) under the same conditions [Citation25]. It is obvious that the replacement of Nb for Ti improved the formation of a single HEC phase, which is affected by the self- and inter-diffusion rates of the metal cations in the carbides. Considering the combined effect of the atomic radius of the five elements and the melting points, lattice parameters, and vacancy formation energies of their corresponding monocarbides, the expected order from the slowest to fastest inter-diffusing metals in the carbides were suggested to be: Ta < Zr∼Hf < Nb < Ti [Citation25,Citation31,Citation47,Citation48]. The slowest diffusion rate of Ta made TaC act as the host material. ZrC with lower melting point (lower atomic mobility) and similar vacancy formation energy with HfC was observed as the second phase in (HfTaZrTi)C, which indicates that the lattice parameter mismatch of the component monocarbides may be a key factor in the forming ability of solid solutions. The smallest Ti atom could have a great diffusion rate in carbides, but their carbides with the smallest lattice parameter may introduce a large lattice distortion in the HfC-TaC-ZrC-TiC system. The ‘sluggish diffusion effect’ may play a role for the incomplete mixing of ZrC in (HfTaZrTi)C. In other words, the formation of the (HfTaZrTi)C phase would result in a lower diffusion rate of each atom, which would make ZrC with its low atom mobility tend to from the second phase. In this work, it should also be noted that the physical characteristics of all component carbides work together to influence the formation of the HEC phase, demonstrating the ‘cocktail effect’.
Some experimental observations could also help to understand and predict the formation or the properties of HECs. According to some lattice parameter studies of single-phase HECs, the rearrangement of the metallic cations in the rock salt structure can cause large lattice distortion, and the lattice parameters of HECs are likely to be the average of the distortions [Citation45,Citation49]. Some studies showed that the lattice parameter of some HECs was close to their predicted value from ROM, which suggested a completely random placement of the metallic atoms in the metallic sublattice [Citation50–52]. Therefore, the lattice parameter could serve as an indicator of the ease of formation of a solid solution high entropy phase. Feng et al. proposed that the variation of lattice parameters of HECs could act as an indicator of the oxygen content when the carbides are synthesised using oxides and graphite as starting materials, because any residual oxygen dissolved in the carbide lattice will decrease the lattice constant [Citation53,Citation54]. A study on carbon vacancy reported that the vacancies can reduce the diffusion activation energy of metal atoms and increase their diffusion driving force, and thus can decrease the sintering temperature of HEC ceramics, indicating that the formation of non-stoichiometric HECs may be easier [Citation55]. Moreover, the solid solution temperature can also be seen as an importation parameter to predict the formation ability of HECs [Citation56].
Preparation of HECs
HEC powders
Equiatomic (HfZrTiTaNb)C powders were synthesised from monocarbide powders using a pressureless SPS set-up [Citation50]. As shown in the X-Ray Diffraction (XRD) patterns in (a), a single solid-solution phase was gradually formed with increasing sintering temperature. Face-centered cubic (FCC) structured (HfZrTiTaNb)C powders were finally synthesised when the sintering temperature reached 1950°C. The average size of the spherical and cuboidal particles was about 2 µm, as shown in the scanning electron microscope (SEM) images in (b). Transmission electron microscope (TEM) analysis also proved the existence of a single FCC phase ((c)). A high-angle annular dark-field signal (HAADF) image and Energy Dispersive X-ray Spectroscopy (EDS) mapping images for each metallic element are presented in . It can be concluded that the synthesised (HfZrTiTaNb)C powders were chemically and structurally homogeneous, and the metallic atoms were randomly positioned in the metallic sublattice.
Figure 1. (a) XRD patterns of powders synthesised at different temperatures; (b) SEM image and (c) TEM image with the corresponding selected area electron diffraction (SAED) pattern of (HfZrTiTaNb)C powders synthesised at 1950°C [Citation50].
![Figure 1. (a) XRD patterns of powders synthesised at different temperatures; (b) SEM image and (c) TEM image with the corresponding selected area electron diffraction (SAED) pattern of (HfZrTiTaNb)C powders synthesised at 1950°C [Citation50].](/cms/asset/f0f4cad7-d00a-4ad6-b6ba-aaa466b70ae4/yaac_a_2014277_f0001_oc.jpg)
Figure 2. (a) HAADF image and (b–f) EDS mapping images of (HfZrTiTaNb)C powders [Citation50].
![Figure 2. (a) HAADF image and (b–f) EDS mapping images of (HfZrTiTaNb)C powders [Citation50].](/cms/asset/7e95dc0e-6072-4a73-9041-e8de163ad6ae/yaac_a_2014277_f0002_oc.jpg)
Another way to synthesise the (HfZrTiTaNb)C powders with nanoscale particle size was reported [Citation54]; equiatomic (HfZrTiTaNb)C powders were synthesised by a two-step synthesis process consisting of carbothermal reduction (CTR) at 1600°C, followed by solid solution formation at 2000°C. Metals oxides and carbon black powders were used as the starting powders, and high-energy ball milling (HEBM) was used to reduce the powder size and mix them homogeneously. It was found that the HEBM could decrease the CTR temperature and thus reduce the particle size of HEC powders. This is due to the increased surface area of the powder mixtures and the decreased diffusion distances between the carbon and oxides [Citation54,Citation57]. The CTR reactions (Equation (6)–(10)) and the solid solution formation (Equation (11)) were described as follows:
(6)
(6)
(7)
(7)
(8)
(8)
(9)
(9)
(10)
(10)
(11)
(11)
Decreasing the carbon monoxide partial pressures of the furnace chamber is another way to decrease the CTR temperature [Citation54]. The Gibbs’ free energy of reactions in equations (6) to (10) at atmospheric pressure and under vacuum was calculated, and the results indicated that every CTR process becomes more favourable at lower temperatures under vacuum. The experimental results showed that the mixed powders heated under vacuum were completely carbothermally reduced after reacting at 1600°C, while the formation of solid solution started at a temperature of about 1700°C and was completed by 2000°C. After the solution formation process, a single-phase rock-salt structured (HfZrTiTaNb)C powder with an average particle size of about 550 nm was obtained.
The polymer-derived ceramic (PDC) route was also applied to synthesise HEC powders [Citation58–61]. A typical route is shown in . Liquid metal chlorides and furfuryl alcohol were selected as the raw materials to synthesise the polymer precursor, and (Ti0.2Zr0.2Hf0.2Nb0.2Ta0.2)C nanopowders were successfully synthesised through a pyrolysis procedure at 2000°C [Citation58]. The reactions during the pyrolysis are as described in equations (6) to (11). Similar, (Hf0.25Nb0.25Zr0.25Ti0.25)C powders were synthesised by a PDC route using metal chlorides and acetylmethane as the starting materials [Citation59]. In this work, the polymer precursor of HECs was first synthesised by the alcoholysis and polycondensation reactions. Novel HEC powders containing rare earth elements, including (Ti, Zr, Hf, Ta, La, Y)C, (Ti, Zr, Hf, Ta, Nb, La, Y)C and (Ti, Zr, Hf, Ta, Nb, Mo, W, La)C, were also fabricated by the pyrolysis of polymer precursors [Citation60]. The available metal candidates for HECs were extended to the Group IIIB (Y and La), which offers a new series of HECs to investigate.
Figure 3. Schematic illustration for a typical PDC route [Citation59].
![Figure 3. Schematic illustration for a typical PDC route [Citation59].](/cms/asset/f2e8496f-523e-48a0-9fd1-e8e06025e963/yaac_a_2014277_f0003_oc.jpg)
Most of reported studies of synthesising HECs require a high-temperature sintering (>1800°C), while, up to now, there are two reported methods which can synthesise HEC powders at low temperatures: the powder metallurgy method and the molten salt synthesis method [Citation62–64]. Using the powder metallurgy method to fabricate HEC powders involves a simple one-step route and can be carried out at room temperature (RT) [Citation62,Citation63]. Metal powders and graphite powder were weighted and milled at high revolutions (300 rev min−1) in a planetary ball mill. To complete the formation of HECs, the minimum milling time had to be set to 50–70 h. Several 5-metal HEC powders were successfully obtained using this method, such as (TiZrHfVNb)C5 and TiZrHfVTaC5. Molten salt synthesis method has successfully applied to synthesise (Ta0.25Nb0.25Ti0.25V0.25)C nanoparticles with an angular structure at 1300°C, which can be explained by classical molten salt-assisted growth theory [Citation64].
HEC coatings and films
In the early 2010s, The research team of Braic V. and Braic M. developed a series of 5-metal carbide coatings and films by direct current magnetron sputtering (DCMS), using an ATC ORION unit equipped with five cathodes [Citation51, Citation65–69]. The coatings were prepared by co-sputtering of five different pure metal targets in an Ar + CH4 reactive atmosphere, the phase composition, microstructure and surface morphology of the coatings could be changed by tuning of the target materials and the reactive atmosphere. (CrCuNbTiY)C, (TiZrNbHfTa)C, (CuSiTiYZr)C, (TiAlCrNbY)C, (SiZrNbHfTa)C and (TiZrNbHfSi)C coatings were successfully synthesised. Although the content of each metal in most of coatings is not strictly equimolar and some of the coatings have more than one phase, these studies still provided a great foundation for future work on HEC coatings.
The influence of carbon content and substrate temperature on the microstructure and properties of (CrCuNbTiY)C coatings was studied [Citation68]. The coatings deposited at temperatures from 80°C to 650°C consisted of crystalline carbide and amorphous carbon, and the content of the carbon in the coatings was controlled by altering the CH4/(CH4+Ar) flow ratio. Depending on the carbon content, the (CrCuNbTiY)C coatings were derived into two series: nearly stoichiometric coatings (C/metal ≈ 1.1) and over stoichiometric coatings (C/metal ≈ 2.7). The XRD results in show that the nearly stoichiometric coatings were well crystallised, while the over stoichiometric coatings were almost amorphous. Similar results were obtained for (TiAlCrNbY)C coatings [Citation65] and (TiZrNbHfTa)C coatings [Citation66]. The carbon content and deposit temperature had an interaction effect on the microstructure of the coatings, including the grain size, and the density of and the compactness of the coatings [Citation70,Citation71].
Figure 4. XRD patterns of (a) nearly stoichiometric and (b) over stoichiometric (CrCuNbTiY)C coatings deposited at different temperatures (s is the substrate) [Citation68].
![Figure 4. XRD patterns of (a) nearly stoichiometric and (b) over stoichiometric (CrCuNbTiY)C coatings deposited at different temperatures (s is the substrate) [Citation68].](/cms/asset/7c66583a-0f48-407c-9dcd-45c87535d33a/yaac_a_2014277_f0004_ob.jpg)
A near-stoichiometric (CuSiTiYZr)C coating deposited at 300°C showed an amorphous structure, while the reference (TiZr)C coating deposited under similar conditions showed good crystallinity [Citation67]. The theory of “lattice distortion effect” in HEAs was considered to play the main role in the formation of the amorphous structure of the (CuSiTiYZr)C coatings. The effect of “lattice distortion effect” on crystallisation was also reported for high entropy transition metal carbide and nitride coatings. (TiZrNbHfTa)C and (TiZrNbHfTa)N protective coatings were deposited on steel substrates for biomedical applications [Citation51]. The multi-component carbide and nitride coatings exhibited the same FCC solid-solution structure as monocarbide TiC and mononitride TiN. Compared to the crystallite size of TiC (19 nm) and TiN (17 nm) reference coatings, the multi-component carbide and nitride coatings presented finer microstructures with crystallites of about 5 and 7 nm, respectively. The possibility to improve the biocompatibility of the (TiZrNbHfTa)C was further investigated by either substituting Ti or Ta by Si [Citation69]. The replacement of Ti or Ta by Si further reduced the degree of crystallinity and the crystallite size due to the increased content of amorphous phase (C = C and Si–C–O). The surface of the Si-coatings with lower roughness became smooth and dense. Two transition metal HEC thin films, (Hf0.2Zr0.2Ta0.2Mo0.2W0.2)C1−x and (Hf0.2Zr0.2Ta0.2Ti0.2Nb0.2)C1−x, with different carbon contents were prepared recently to investigate the effect of the carbon stoichiometry on the thermal conductivity of HEC films, which will be discussed in detail in the chapter on properties (chapter 4) [Citation72].
(CrNbTaTiW)C films with different metal contents were deposited by non-reactive DCMS from metal, alloy and carbon targets [Citation46]. Near-equimolar (CrNbTaTiW)C films (NEC) and Ta/W-rich (CrNbTaTiW)C films (TaWC) were deposited from RT to 600°C. As shown in , the two films deposited at 300°C had a cubic (or distorted cubic) structure with many columnar grains growing from the substrate to the surface (∼600 nm). The TaWC films deposited at 600°C became polycrystalline with no clear columnar grain structure, while the NEC films deposited at 600°C showed a two-layer structure, the bottom layer had a columnar structure and the top layer (only 20 nm) was polycrystalline. The formation of the polycrystalline structure of the films was attributed to the increased atomic mobility at elevated temperatures. The NEC films with lower atomic mobility caused by the ‘sluggish diffusion effect’ showed more stable crystallisation than the TaWC films.
Figure 5. TEM images of NEC and TaWC films deposited at 300°C and 600°C [Citation46].
![Figure 5. TEM images of NEC and TaWC films deposited at 300°C and 600°C [Citation46].](/cms/asset/5f04f8a9-6ad2-4a01-b9e6-d042aa2acaaa/yaac_a_2014277_f0005_ob.jpg)
The possibility of preparing HEC coatings by scattering HEA target was proved and reported [Citation73,Citation74]. To produce high entropy TiZrHfVNbTa carbide coatings, the high entropy TiZrHfVNbTa alloys were melted in a vacuum-arc in argon and used as a target [Citation73]. Coatings were then deposited by the scattering of the HEA target with accelerated argon ions extracted from the plasma of a compressed vacuum-arc discharge. The results showed that HEC phase coatings were formed when the C2H2 concentration was 5 vol.-% or more in a gas mixture. In a 5 and 10 vol.-% of C2H2 content reaction atmosphere, the carbide coatings can be clearly defined as an FCC structure with (111) preferred orientation.
HEC ceramics
In recent years, spark plasma sintering (SPS), also referred to as field-assisted sintering technique (FAST), and hot press (HP) sintering have been successfully and widely applied to synthesising bulk HEC ceramics with different compositions.
Castle et al. fabricated a single-phase (HfTaZrNb)C ceramic using SPS [Citation25]. The four corresponding monocarbide powders were used as starting materials, and ball milling was used to mix the powders homogenously in an argon atmosphere. This is a very typical route for processing HEC ceramics, and has been widely applied in many of the following studies of HECs [Citation24,Citation26–28,Citation75–77]. The study on the influence of dwell time at 2300°C on the microstructures of (HfTaZrNb)C showed that the HEC samples became dense (99%) and homogenous with the increasing dwell time from 3 to 7 min, and a clear chemical decomposition was observed in the centre of the samples with a dwell time of 10 min. The formation of the phase separation probably occurred because of the slower cooling rate of the centre of sample than that of the edge of sample, which indicated that a miscibility gap is possibly present in the (HfTaZrNb)C system. For the HEC samples sintered at 2300°C for 7 min, the grain size varied from about 5 to 30 μm with an average grain size of 12 μm. The individual grains with different crystallographic orientations can be clearly seen in (a). The electron backscatter diffraction (EBSD) image ((b)) showed that these individual grains with different orientations were distributed randomly in the sample. Moreover, EDS maps of metallic elements in HEC lattice () confirmed that each metal was homogeneously distributed in the lattice. Annular bright field (ABF) and HAADF micrographs in showed a homogeneous solid solution phase with the arrangement of the C atoms (red dots) and metallic atoms (green dots), indicating the compositional homogeneity of HECs at the atomic level.
Figure 6. Microstructure of the (HfTaZrNb)C sintered for 7 min at 2300°C: (a) SEM; and (b) EBSD [Citation78].
![Figure 6. Microstructure of the (HfTaZrNb)C sintered for 7 min at 2300°C: (a) SEM; and (b) EBSD [Citation78].](/cms/asset/14843424-361c-4821-a8e1-9a78e9add683/yaac_a_2014277_f0006_oc.jpg)
Figure 7. STEM and EDS maps of the (HfTaZrNb)C sintered for 7 min at 2300°C [Citation78].
![Figure 7. STEM and EDS maps of the (HfTaZrNb)C sintered for 7 min at 2300°C [Citation78].](/cms/asset/8db2122b-ab02-4008-b3cd-21c8b69f8d45/yaac_a_2014277_f0007_oc.jpg)
Figure 8. ABF (left) and HAADF (right) micrographs along the [011] zone axis (Fm-3 m) of the (HfTaZrNb)C sintered for 7 min at 2300°C [Citation78].
![Figure 8. ABF (left) and HAADF (right) micrographs along the [011] zone axis (Fm-3 m) of the (HfTaZrNb)C sintered for 7 min at 2300°C [Citation78].](/cms/asset/35a5fc44-310a-4089-8a28-ae0e8af8edec/yaac_a_2014277_f0008_oc.jpg)
Many 5–8 metals carbides with a single FCC structure have also been successfully synthesised by SPS at 2000∼2300°C, and the available metal candidates for HEC ceramics contained the Group IVB, Group VB and Group VIB so far [Citation18,Citation24,Citation26,Citation27,Citation49]. The potential to develop useful new HECs shows more possibilities due to their large compositional space and designable compositions. Although the Group VIB carbides have a very limited solid substitutional solubility with Group IVB/VB carbides, HECs with metals from Group IVB/VB/VIB such as (Ti, Zr, Hf, V, Nb, Ta, Mo, Cr)C have been successfully fabricated. The successful formation of solid solution containing metals from Group IVB/VB/VIB proves the positive effect of high entropy on the formation of new solid solution phases [Citation27]. Extended X-ray absorption fine structure (EXAFS) results of single-phase (VNbTaMoW)C indicated that Mo (Group VIB metal) absorbers have a similar local surrounding with V and Nb (Group VB metal) absorbers [Citation18].
In addition to using monocarbides powers as the starting powders, there are two other typical starting materials: a mixture of metal powders and graphite powders [Citation79,Citation80]; and a mixture of metal oxide powders and graphite powders[Citation81–83]. Wei et al. studied the effect of different starting powders on the formation and microstructures of (Ti0.2Zr0.2Nb0.2Ta0.2W0.2)C ceramics [Citation84]. After ball milling, these three different mixtures were sintered using SPS at 2000°C under a uniaxial pressure of 50 MPa. The HEC samples synthesised using carbide powders, metal and graphite powders, and metal oxide and graphite powders were named as HEC-C, HEC-M and HEC-O, respectively. The XRD results showed that a single-phase HEC with a rock-salt structure was obtained in all of the samples prepared by the different processing routes. There was very little oxygen content in HEC-C (0.72 mass%) and HEC-M (0.70 mass%), while the HEC-O had 1.8 mass% oxygen content. Both HEC-M and HEC-O have a high relative density (>98%), while the relative density of HEC-C was only 95.7%. The distribution of elements Zr and Nb was not very uniform in HEC-M due to the large particle size of the metal powders, but finer metal powders may introduce more oxygen during their processing and fine zirconium powders are combustible. The HEC-O had an obvious second phase (Zr-rich phase), mainly because the temperature of CTR for zirconia and graphite was higher than for the other reactions. Their research clearly demonstrates that choosing an appropriate starting powder based on the desired quality of HEC ceramics is very necessary. Moreover, it is also possible to synthesise the HEC powders first and consolidate the powders to fabricate the HEC ceramics by SPS with high temperature and high pressure [Citation80]. Besides, metal foils and graphite disks were also used to synthesise the HEC ceramic by using a combination of arc-melting and flash-SPS [Citation85].
HP sintering is also a promising technology for sintering HEC ceramics [Citation45,Citation82,Citation83,Citation86]. Equiatomic (HfZrTaNbTi)C ceramics with a relative density of 95.3% were fabricated by ball milling and HP sintering at 1800 °C under a pressure of 30 MPa [Citation45]. After the HP sintering, single rock-salt crystal structured carbides were formed. The (HfZrTaNbTi)C ceramics were basically compositional homogeneous at the microscale except for the localisation of a small amount of Nb, which may result from the different electronic structures and atom radius between NbC and the other carbides, and the undissolved NbC may have existed at the grain boundary [Citation87]. It is also possible that the homogenisation of the material was not complete, prolonging the sintering time or sintering at higher temperatures may solve this issue.
Three different methods of sintering (Hf, Ta, Nb, Ti, V)C and (Ta, Nb, Ti, V, W)C ceramics have been compared and studied [Citation88]: SPS at 2000°C under a pressure of 60 MPa, Hot isostatic pressing (HIP) at 1900 °C with a gas pressure of 100 bar; and vacuum sintering at 2250°C. After sintering, all of the samples were single cubic phase. The relative density of all of the samples was higher than 97.9%, while the density of the SPS sintered samples can reach 100%. The grain size of HIP sintered samples is much smaller due to the lower sintering temperature, and the distribution of grain size of vacuum-sintered samples is more uniform. Another work on pressureless sintering also successfully fabricated the (TiZrHfNbTaMo)C ceramic with a density of 97% at 2500°C [Citation89].
Porous (Zr0.2Hf0.2Ti0.2Nb0.2Ta0.2)C with a high porosity of 80.99% was successfully fabricated using in-situ reaction and partial sintering method [Citation90]. The precise control of the synthesis and shrinkage process is key to the shape stability of porous carbides. The heating rate should be under 5°C/min at 1200–1600 °C to avoid the formation of cracks resulting from the rapid shrinkage and gas-release at high temperatures. The partial sintering temperature of porous (Zr0.2Hf0.2Ti0.2Nb0.2Ta0.2)C was selected as 1850°C based on the linear shrinkage rate.
Recently, some novel composites containing HEC phase were also synthesised and investigated, such as: (Fe40Co50Ni10)94(TaNbZrVC2)6 [Citation91]; MAX phase M2AlC-MC (M = Ti, Zr, Hf, Nb, Ta) composites [Citation92]; high entropy MXenes 2D flakes [Citation93]; (Ti, Zr, Nb, Ta, Hf)C within a steel matrix [Citation94]; (Mo0.2W0.2V0.2Cr0.2Nb0.2)C nanoparticles incorporated on porous carbon [Citation95]; (Zr0.25Hf0.25Ta0.25Ti0.25)C-Ni-Co composites [Citation96]; B4(HfMo2TaTi)C-SiC composites [Citation47]; (Hf0.25Zr0.25Ta0.25Nb0.25)C-SiC composites [Citation97]; (Ti0.2Zr0.2Hf0.2Nb0.2Ta0.2)C-SiC composites [Citation98]; and Cf/(Ti0.2Zr0.2Hf0.2Nb0.2Ta0.2)C-SiC [Citation99]. The development of HECs increases the diversity of the possible compositions and microstructures of composites, offering more possibility to break through the restriction of the traditional materials.
Properties of HECs
Thermal and electrical properties
Thermal stability
The thermal stability of equiatomic (HfZrTaNbTi)C ceramics was studied by annealing the samples at 500, 800 and 1140°C in an argon atmosphere for 1 h [Citation49]. shows the XRD spectra after annealing. There was no evidence of phase decompositions or phase transformations, which indicated that the high entropy (HfZrTaNbTi)C phase was thermally stable up to 1140°C. Porous (HfZrTaNbTi)C has also been shown to possess superior thermal stability at least up to 1850°C in an argon atmosphere [Citation90].
Figure 9. XRD spectra of (HfZrTaNbTi)C before and after annealing at 500, 800 and 1140°C for 1 h in Ar [Citation49].
![Figure 9. XRD spectra of (HfZrTaNbTi)C before and after annealing at 500, 800 and 1140°C for 1 h in Ar [Citation49].](/cms/asset/052ecd9c-7a16-46b8-8136-4841eda6c04a/yaac_a_2014277_f0009_oc.jpg)
The high-temperature thermal stability of HECs was also studied by characterising the grain size of (HfZrTaNbTi)C after annealing at 1300 and 1600°C for 5 and 10 h [Citation75]. The average grain size slightly increased from 0.57 μm to 0.86 μm after annealing at 1600°C for 10 h, which did not grow as fast as TiC grains annealing at 1400–1600°C. The HEC sample with fine grains showed greater thermal stability at high temperatures. The reduced driving force (grain-boundary energy) and grain growth kinetics (grain-boundary migration rate) caused by the high entropy effects were considered as the main reasons for the improved thermal stability of HECs, which were also be observed in the study of HEAs [Citation100,Citation101].
Thermal conductivity
The thermal conductivity of the 4-metal and 5-metal HEC ceramics, corresponding monocarbides, binary carbides and ternary carbides from the literature as a function of the number of metal elements in carbides are plotted and shown in [36,79,80,86, Citation102–107]. It can be clearly seen that the thermal conductivity of carbides is decreased with an increasing number of metals. The thermal conductivity of dense HECs was in the range of only 5–15 W m-1 K−1 at RT, which is much lower than that of the traditional transition metal carbides (15–40 W m−1 K−1). It is well known that phonons and electrons play an important role in transferring heat in solids, and phonons provide the major contribution for transition metal carbides. When forming a high entropy phase from several monocarbides, the different atom sizes and bond strengths of the metals will produce lattice distortions, which may induce significant phonon scattering [Citation49]. The chemical disorder (mass and strain disorder) could also decrease the phonon free path, which in turn decreases the phonon transport and thus decrease the thermal conductivity, similar to HEAs [Citation79,Citation108]. That is why thermal conductivity is very sensitive to the number of metal elements in carbides. To accommodate the lattice distortions, the anions displace from their ideal locations, resulting in distortion of the anion sublattice of the FCC structure, which makes the scattering of phonons more serve [Citation109]. These are probably the main reasons for the low thermal conductivity of HEC ceramics. Some thermoelectric HEAs with low thermal conductivity have also been reported, such as PbSnTeSe [Citation110] and AlxCoCrFeNi (0 ≤ x ≤2) [Citation111]. The high-temperature thermal conductivity of several HECs including (VNbTaMoW)C has also been studied at temperatures up to 1000°C. The results show that the thermal conductivity of HECs gradually increases with increasing temperatures because of weakened phonon scattering at higher temperatures [Citation33,Citation49,Citation79].
Figure 10. Thermal conductivity of dense carbides with different numbers of metals at RT [Citation36,Citation79,Citation80,Citation86,Citation102–107]. The relative density of multi-metal carbides was labelled due to the large effect of porosity on thermal conductivity.
![Figure 10. Thermal conductivity of dense carbides with different numbers of metals at RT [Citation36,Citation79,Citation80,Citation86,Citation102–107]. The relative density of multi-metal carbides was labelled due to the large effect of porosity on thermal conductivity.](/cms/asset/059d25b5-653b-496c-830b-691dac64dfca/yaac_a_2014277_f0010_oc.jpg)
The effect of carbon stoichiometry on the thermal conductivity was investigated on HfZrTaMoWC1−x and HfZrTaTiNbC1−x films and carbon-rich (Ti0.2Zr0.2Hf0.2Nb0.2Ta0.2)C ceramics [Citation72,Citation112]. The carbon stoichiometry of carbides showed a huge effect on the characterisation of bonding which determined their thermal conductivity. The carbide films with low carbon content were more metallic in nature, and had many electrons which can work as thermal carriers. With increasing carbon stoichiometry, the contribution of electrons to the thermal conductivity was reduced and the contribution of phonon became more dominant. The change of microstructures, defect concentration, new phase formation and stiffness will all effect the contribution of phonons to thermal conductivity. As a result, the thermal conductivity of these two films decreased with the increase of carbon stoichiometry [Citation72]. However, the thermal conductivity of the carbon rich (Ti0.2Zr0.2Hf0.2Nb0.2Ta0.2)C ceramics increased with the increasing carbon stoichiometry, because the graphite reacted with the oxide impurities during sintering and purified the ceramics, and the residual graphite content also played a role in increasing thermal conductivity [Citation112].
A comparison of thermal diffusivity among high-entropy carbides, alloys and metallic glasses at different temperatures in the range of RT–600°C is presented in [Citation26]. The thermal diffusivity of all these materials increased with the increasing temperatures. The thermal diffusivity of HEC ceramics was comparable with that of metallic glass samples, and was much smaller than that of HEA samples and typical ceramics. Some studies showed that the thermal diffusivity of HECs is lower than that of the corresponding monocarbides, which can be mainly attributed to their chemical disorder and low diffusion rate of atoms (‘sluggish diffusion effect’) [Citation26,Citation49,Citation86].
Figure 11. Thermal diffusivity of high entropy carbides, alloys and metallic glasses at RT-600°C [Citation26].
![Figure 11. Thermal diffusivity of high entropy carbides, alloys and metallic glasses at RT-600°C [Citation26].](/cms/asset/772701d4-69a6-4edd-9e01-ddb511f21e3d/yaac_a_2014277_f0011_oc.jpg)
The thermal properties of porous (Zr0.2Hf0.2Ti0.2Nb0.2Ta0.2)C with a high porosity of 80.99% were investigated from RT to 200°C, and have been compared with the that of dense (Zr0.2Hf0.2Ti0.2Nb0.2Ta0.2)C (relative density: 93%) [Citation90]. The porous HEC sample showed a low thermal diffusivity of 0.74 mm2 s−1 and a fairly low thermal conductivity of 0.39 W m−1 K−1, which is much low than the dense one (3.6 mm2 s−1 and 6.45 W m−1 K−1).
Thermal expansion
HECs with transition metals have a great potential in cutting tools as hard coatings, the study of their thermal expansion property is thus necessary to anticipate the adhesion of their coatings. The experimental results showed that the thermal expansion coefficient of (Hf0.2Zr0.2Ta0.2Nb0.2Ti0.2)C (6.44 × 10−6 K−1 at RT) is comparable to that of the base monocarbides [Citation49]. The theoretical high-temperature thermal properties of HECs have been investigated based on density DFT [Citation33,Citation113,Citation114]. With the increasing temperature from 0 to 2400°C, the thermal expansion coefficient for both (Hf0.2Zr0.2Ta0.2Nb0.2Ti0.2)C and (HfTaZrTi)C increased. The RT thermal expansion coefficient of (Hf0.2Zr0.2Ta0.2Nb0.2Ti0.2)C predicted by Dai is closer to the experimentally measured values [Citation113].
Electrical conductivity
The electrical resistivity of (HfZrTaNbTi)C (91 ± 1.3 μΩ cm) was higher than the value predicted from ROM (57.4 μΩ cm) and comparable to that of TiC (100 μΩ cm) [Citation45]. The mechanism behind the higher electrical resistivity of HECs may lie in the enhanced scattering of electrons due to lattice distortions and carbon vacancies [Citation108]. Another factor was the relatively low porosity (The relative density was only 93%).
Previous studies indicated that increasing the number of elements in carbides is a highly effective method to decrease the mean free path of phonons and electrons, and therefore decrease thermal conductivity, which could also work for electrical conductivity. Increasing the porosity or carbon stoichiometry or altering the concentration of specific elements could play a similar role [Citation72,Citation90,Citation108]. These factors can be used to control the thermal and electrical conductivity properties of carbides, and this method could be extended and applied to other materials.
Mechanical and tribological properties
Hardness and modulus
According to the published research, HECs have excellent mechanical properties, showing improved hardness and modulus compared to the base monocarbides and the ROM value. The mechanical properties including hardness, Young’s modulus, flexural strength and fracture toughness of HECs are summarised in . Some factors, such as density and grain size, have obvious effects on the mechanical properties of carbides and are also be collected and listed in .
Table 2. Composition, experimental procedures, density, roughness, grain size, lattice parameter and mechanical properties of the reported HEC ceramics and coatings.
The measured nanoindentation hardness of (HfTaZrNb)C ceramic was 36.1 ± 1.6 GPa, showing a 30% enhancement compared to the ROM value of the corresponding monocarbides (27.7 GPa) [Citation25]. A systematic study was reported for 5-metal HECs containing metals from the Group IVB, VB and VIB fabricated by SPS. The hardness and elastic modulus of seven single-phase compositions along with their ROM values against the valence electron concentration (VEC) are shown in [Citation18]. The decreasing hardness of HECs with increasing VEC showed that there is a correlation between the hardness and electronic structure of HECs. It was also found that the measured hardness and elastic modulus for six of the HEC compositions were higher than their ROM values. Similar results can also be found for many 4–8 metals HECs [Citation26, Citation27, Citation115]. However, Yan et al. [Citation49] reported that the microhardness and elastic modulus of (HfZrTaNbTi)C were lower than those of monocarbides, but this was probably because of the low density (93%) of their samples. HECs processed with higher density and fine grain size have improved hardness and modulus [Citation75,Citation80,Citation82]. Increasing the sintering temperature of HEC ceramics can increase the density and thus increase the hardness and modulus, while rapid gain growth at high temperatures may result in a decrease of the hardness and fracture toughness [Citation26,Citation82].
Figure 12. (a) Hardness and (b) elastic modulus of 7 HECs along with the ROM value against the VEC [Citation18].
![Figure 12. (a) Hardness and (b) elastic modulus of 7 HECs along with the ROM value against the VEC [Citation18].](/cms/asset/138d8580-93d2-4c99-902d-b7f991f9db44/yaac_a_2014277_f0012_oc.jpg)
Solid solution strengthen has been widely recognised as an important mechanism for the increased yield stress/hardness of HECs, which results from lattice distortion due to the size mismatch of the different and disordered metal atoms. The traditional solid solution strengthening mechanisms cannot adequately explain the remarkable improvements of certain HEC compositions over their ROM value. Another possibility related to the bonding nature of transition metal carbides has been proposed, the overall electronic structure of HEC phase may have an effect on their mechanical properties [Citation18,Citation25]. Comparing the hardness and elastic modulus of HECs to their VEC values may give some clues about the contribution of the electronic structure on the significantly improved hardness of HECs, as shown in the results in . The hardness of the HECs decreased with increasing VEC from 8.4 to 9.4, while the modulus of the HECs increased, which is consistent with an ab initio prediction of the influence of VEC on the mechanical properties of carbides with rock salt structure [Citation116]. According to the calculation, the authors suggested that the decreasing hardness of carbides with higher VEC was probably attributed to the increasing electron density of the d-orbitals of the metals involved in the bonding. Moreover, the predicted results also showed that a further increase of the VEC of carbides (>9) reduces their modulus, which remains to be verified in further experiments [Citation116]. Nevertheless, a study of (CrNbTaTiW)C films with varying proportions of metals has not found a clear correlation between the hardness and VEC [Citation46]. Moreover, dislocation core atomic randomness was also proposed as a hardening mechanism for HECs [Citation27]. The Peierls stress of a dislocation was calculated based on DFT. The HECs with more elements and higher atomic randomness at the dislocation core had higher Peierls stress. According to this mechanism, the HECs with more elements should have higher hardness. The experimental results have proved that the 8-metal carbides, (Ti,Zr,Hf,V,Nb,Ta,X,Y)C (X,Y = Mo,W, Cr,Mo, or Cr,W), showed a significant increase of hardness (40–41 GPa) compared to a 4-metal carbide ((HfTaZrNb)C; 36 GPa). These three 8-metal carbides with hardness higher than 40 GPa can be regarded as super-hard materials.
Figure 13. Fracture toughness-Vickers hardness of HECs compared to those of carbides and composites, and some concerned composites [Citation26].
![Figure 13. Fracture toughness-Vickers hardness of HECs compared to those of carbides and composites, and some concerned composites [Citation26].](/cms/asset/f115c223-dc07-45c8-a997-5af8fb20ba25/yaac_a_2014277_f0013_oc.jpg)
Flexural strength and fracture toughness
The flexural strength of HECs is in the range of 200–500 MPa (see ). (NbTaMoW)C showed a great flexural strength of 388 MPa, which was attributed to the energy absorption and release of dislocation movements at lattice steps [Citation107]. The flexural strength of (NbTaMoW)C was more than twice that of (VNbTaMoW)C, probably due to the low bonding energy of V–C [Citation79,Citation107]. A study on (Hf0.2Zr0.2Ta0.2Nb0.2Ti0.2)C with different grain sizes showed that the finest-grained sample (∼0.6 μm) processed a flexural strength up to 400 MPa, showing a 25% increase compared with the coarsest-grained sample (∼16.5 μm) [Citation75].
The fracture toughness of HECs is mainly in the range of 3–9 MPa m1/2 (see ). As shown in , the trade-off between hardness and toughness of some HECs was not only much higher than that of most carbides and their composites, but also higher than the composites with MAX phases, alumina matrix, or mullite.
The micromechanical properties of HECs were investigated by performing micropillar compression and microcantilver bending experiments on single HEC grain [Citation117,Citation118]. In the micropillar experiments, {110}〈1`10〉 was identified as the dominant slip system of (HfTaZrNb)C ceramics. The slip behaviour was similar to the least brittle monocarbide TaC. The yield and failure strength of HEC ceramics were significantly improved compared to the corresponding monocarbides. However, the slip system identified by nanoindentation was {111}〈1 `10〉. In the microcantilver bending experiments, 7 microcantilevers in the grains with {001} and {101} orientations were obtained. The cantilevers fractured at the fixing position had a very high fracture strength (11.8 GPa) and showed a small plastic deformation before fracture, with a yield stress of about 9 GPa. However, the cantilevers fractured at defects showed no plastic deformation and the fracture strength was decreased to 3.8–8.9 GPa. The fracture behaviour of HECs is very sensitive to the defects in HEC grains.
High-temperature mechanical properties
The high-temperature mechanical properties of HEC ceramics are important because of the potential application of HECs in structural components in high-temperature environments. The high-temperature flexural strength of (Hf0.2Zr0.2Ti0.2Nb0.2)C and (Ti, Ta, Zr, Nb)C revealed that the flexural strength of HEC ceramics maintains their RT value (300–500 MPa) up to around 1600–1800°C, showing a better strength retention than some typical mono, binary and ternary carbides [Citation76, Citation115]. The elastic behaviour of (Ti, Ta, Zr, Nb)C was observed at 1600°C, which can be used as an indicator of the subsequent plastic deformation [Citation76]. This brittle to ductile transition temperature was related to the processing conditions (mainly sintering temperature) of HECs. The creep resistance of (Ta–Hf–Zr–Nb)C was studied at 1400–1600°C under compressive stresses in the range 150–300 MPa [Citation119]. The steady-state creep rates of HEC samples ranged from 2 × 10−9/s to 8 × 10−8/s, which was only one-tenth as compared with those of base monocarbides. The similar stress exponents (n) and activation energy (Q) of HEC ceramics compared to monocarbides indicated their similar creep mechanisms, including grain boundary sliding/cracking and dislocation. The increased creep resistance of HECs was considered to be attributed to higher lattice distortion and reduced diffusion of elements (‘high entropy effect’ and ‘sluggish diffusion effect’).
Mechanical properties of HEC coatings
The mechanical properties of HEC coatings have also been studied, as shown in the results in . The microhardness of (TiZrNbHfTa)C coatings was higher than that of the corresponding monocarbide coating (TiC) [Citation51]. Solid solution strengthening mechanisms were considered to play a significant role in the observed enhancement of hardness for HEC coatings, as for HEC ceramics [Citation46,Citation51,Citation65,Citation68,Citation73]. However, the hardness of (TiAlCrNbY)C was somewhat lower than most of the reported hardness values for transition metal monocarbides, which was probably because of the existence of unreacted metals in the films and a low degree of crystallisation [Citation65]. The carbon-rich (TiZrNbHfTa)C films were significantly harder than the near-equimolar films, because the coating compactness was increased with increasing content of amorphous phase [Citation66]. Similar results were also found in crystalline (CrCuNbTiY)C coatings and amorphous (CuSiTiYZr)C coatings [Citation67,Citation68]. Increasing the depositing temperature or altering the proportion of metals in the coatings can also improve the hardness of HEC coatings [Citation46,Citation68].
Tribological behaviour
The tribological properties of (Hf–Ta–Zr–Nb–Ti)C ceramics and TaNbSiZrCr carbide coatings have also been studied. The specific wear rate of (Hf–Ta–Zr–Nb–Ti)C ceramics increased with the increasing load from 2.53 × 10−6 mm3/Nm at 5 N to 9.03 × 10−6 mm3/Nm at 50 N [Citation77]. The main mechanism is abrasion wear. A small amount of grain pull-out and a thin oxidised tribological layer was formed during the test. The TaNbSiZrCr carbide coatings showed good tribological properties with a high wear resistance (0.33 × 10−6 mm3/Nm) and a low and stable friction coeffcient (0.09) [Citation74].
Oxidation, irradiation and corrosion resistance
Oxidation resistance
High-temperature oxygen-containing environments are very common in the target applications of UHTCs. The investigation of oxidation behaviour of HECs is thus of great research significance. The metals from different Groups will result in different oxidation characteristics: Group IVB-metal oxides are the most stable with the highest melting temperatures (∼2700°C for ZrO2 and HfO2), Group VB-metal oxides have lower melting temperatures, and Group VIB-metal oxides form gaseous oxides [Citation124]. These characteristics of the oxides have a combined influence on the oxidation behaviour of multi-metal HECs. The potential of preferential oxidation for components of HECs was analysed through a computational approach. The results showed that the preferential oxidation tendency of each component was very sensitive to the relative thermodynamic stabilities of their corresponding oxides [Citation125]. Experimental studies on (HfZrTiTaNb)C and (HfTaZrNb)C showed that the metals in the oxide layer were inhomogeneously distributed in the region near the interface between the oxide layer and the carbide base, confirming the existence of preferential oxidation of elemental components in HECs [Citation126,Citation127].
The isothermal oxidation behaviour of (HfTaZrNb)C and (HfZrTaNbTi)C ceramics have been systematically studied at temperatures in the range of 800–1500°C [Citation127–131]. The oxidation behaviour of HEC ceramics obeyed a parabolic rate law, indicating a diffusion-controlled oxidation process. Two phases, a phase rich in Hf, Zr and Ti and a molten phase rich in Ta and Nb, were observed on the surface of the oxide layer of (HfZrTaNbTi)C when the oxidation temperature was increased to 1500°C [Citation128]. It is difficult to get an exact composition for the oxide products, because the oxidation products may consist of many new oxides with different proportions of metals and multiple crystal structures. But at least the formation of new 4-element oxides has been observed in the oxide layer of (HfTaZrNb)C by using a combination of XRD, TEM, EDS and SAED [Citation127]. An amorphous and compact interlayer was formed between the oxide layer and the carbide, which acts as an effective barrier for the diffusion of oxygen [Citation127]. Moreover, the oxidation behaviour of (Zr,Ti,Hf,Nb,Ta)C ceramic was investigated in a water vapour atmosphere at 1200°C [Citation130]. The parabolic rate constant (Kp) of (Zr,Ti,Hf,Nb,Ta)C is almost two order of magnitude lower than that of ZrC, demonstrating an improved oxidation resistance of HECs.
The oxidation resistance of HEC, monocarbide and binary carbide powders was compared and investigated using thermogravimetric analysis and differential scanning calorimetry (TGA-DSC). (Ti, Zr, Hf, Nb, Ta)C powders had a higher oxidation onset temperature (OOT; 403°C) than a mixture of the corresponding monocarbides (96°C) [Citation50]. shows the TGA-DSC results of (Hf–Ta–Zr–Nb)C, monocarbide and (Hf–Ta)C powders and the morphology of the powders afters oxidation [Citation132]. It was found that the HEC powders with an improved OOT (785°C) and intact particles after oxidation showed a better oxidation resistance than the monocarbides. Although the OOT of (Hf-Ta)C powders (860°C) is higher, the HEC particle showed better structural stability.
Figure 14. TGA-DSC results and SEM images after oxidation of (Hf–Ta–Zr–Nb)C, ZrC, NbC, HfC, TaC and (Hf–Ta)C powders [Citation132].
![Figure 14. TGA-DSC results and SEM images after oxidation of (Hf–Ta–Zr–Nb)C, ZrC, NbC, HfC, TaC and (Hf–Ta)C powders [Citation132].](/cms/asset/b4c88aef-194b-4330-bcca-eec031b50a9a/yaac_a_2014277_f0014_oc.jpg)
Although HECs showed improved oxidation resistance compared to monocarbides, the oxidation resistance of HECs still needs to be improved to meet the requirements of the anticipated applications. It was reported that the oxide layer of the oxidised 7-metal HfMoNbTaVWZrC7 carbide is more uniform in composition and denser than that of 5-metal HfMoNbTaZrC5 carbides. A thick Hf/Zr depleted transition carbide layer was formed between the carbide substrate and the oxide layer in the oxidised 7-metal carbide due to the preferential oxidation of Hf and Zr. The formation of Hf–Zr-rich oxide layer decreases the oxidation rate and results in the improved oxidation resistance of the 7-metal carbide [Citation133]. Moreover, the effect of adding SiC on the oxidation behaviour of HEC ceramics was studied. Two composites, (HfZrTaNb)C-SiC and (HfTaZrTiNb)C-SiC, showed improved oxidation resistance compared with the corresponding HEC ceramics with no SiC [Citation97,Citation134]. Although the oxidation mechanisms of HECs were considered unchanged after adding a small amount of SiC, SiC may play a role in delaying the outward diffusion of Ta and Nb and thus improve the oxidation resistance of HECs.
Irradiation resistance
The irradiation behaviour of HECs was investigated for (Zr0.25Ta0.25Nb0.25Ti0.25)C and (Hf0.2Zr0.2Ta0.2Nb0.2Ti0.2)C ceramics, which were irradiated by Zr ions or helium ions at temperatures in a range of RT to 500 °C [Citation121,Citation135,Citation136]. After irradiation, the ceramics with no phase transformation showed good irradiation resistance. The growth and coalescence of irradiation-induced defect clusters, such as dislocation loops, were suppressed probably due to the chemical disorder and lattice distortion of HECs [Citation121,Citation135]. As a result, the irradiation-induced (ZrTaNbTi)C ceramics showed better mechanical properties than the original HEC ceramics, with a 10% improvement of hardness and a 4% increase of elastic modulus [Citation121].
Corrosion resistance
The corrosion resistance of a series of (CrNbTaTiW)C films with different metal contents was investigated in a 1.0 M HCl solution by potentiodynamic polarisation measurements [Citation46]. The corrosion potentials of all of the HEC films were two to three times higher than that of a stainless steel reference material, and the oxidation current densities of HEC films were lower than that of stainless steel. The Nb-rich HEC films showed passive current density in a small potential region, while the Ta/W-rich and the near-equimolar films showed a steady current increase. A thin surface oxide layer with no pots was observed on Nb-rich HEC films and near-equimolar HEC films, whereas the W/Ta-rich HEC films did not show any obvious morphology changes after corrosion, showing the best corrosion resistance. Moreover, the corrosion resistance of (TiZrNbHfTa)C coatings in simulated body fluid (SBF) solution at RT was evaluated by electrochemical measurements [Citation66]. Compared to the alloy substrate, the HEC coating exhibited decreased open circuit potential, corrosion current density and corrosion potential, showing an improved corrosion resistance.
Summary
As a novel class of materials, HECs have shown their unique and attractive structure and properties. In this review paper, the basic theories, design insights, preparation technologies and properties of HECs have been summarised from the recent studies: the four core effects which were used for HEAs have been discussed to understand HECs; the computer modelling results have been reviewed to predict the formation of HECs and design their composition; the different processing methods have been summarised for HEC powders, coatings and films, and bulk materials, such as SPS, HP, HIP, arc melting and DCMS; the microstructures and chemical characterisations of HECs have been reviewed to study their formation and sintering mechanisms; the thermal conductivity of HECs with different numbers of metal elements has been collected and summarised and the effect of the number of metal elements on the thermal conductivity of HECs is discussed; the electrical properties, oxidation, irradiation and corrosion resistance of HECs have been summarised and a comparison is made with transitional monocarbides; the mechanical properties of HECs with deferent compositions have been summarised and reviewed and their improved properties are discussed. Based on these findings, HECs showed many improved properties compared with the traditional monocarbides, such as increased hardness and modulus and better oxidation resistance, which make them promising new UHTCs for many potential applications, including thermal barrier coatings and cutting tools. An improved understanding of HECs and the development of novel carbides could further improve their performance and broaden their application fields such as batteries and catalysts. More modelling and experimental works need to be done in the future to better understand the fundamentals and structures of the HECs, which will give us a direction for materials for extreme conditions.
Acknowledgements
Yichen Wang would like to acknowledge her supervisor Professor Michael J. Reece for his support, encouragement and constructive suggestions and the financial support from China Scholarship Council.
Disclosure statement
No potential conflict of interest was reported by the author(s).
Correction Statement
This article has been republished with minor changes. These changes do not impact the academic content of the article.
Additional information
Funding
References
- Fahrenholtz WG, Hilmas GE. Ultra-high temperature ceramics: materials for extreme environments. Scr Mater. 2017;129:94–99.
- SCATTEIA BELLOSI. Luigi, processing and properties of ultra-high temperature ceramics for space applications. Mater Sci Eng A. 2008;485(1):415–421.
- R LEVINE, Stanley OPILA, Elizabeth J, et al. Evaluation of ultra-high temperature ceramics for aeropropulsion use. J Eur Ceram Soc. 2001;22(14):2757–2767.
- Sempere J, Nomen R, Serra E, et al. Thermal behavior of oxidation of TiN and TiC nanoparticles. J Therm Anal Calorim. 2010;105(2):719–726.
- Smith CJ, Yu X-X, Guo Q, et al. Phase, hardness, and deformation slip behavior in mixed HfxTa1-xC. Acta Mater. 2018;145:142–153.
- Opeka MM, Talmy IG, Wuchina EJ, et al. And oxidation properties of refractory hafnium and zirconium compounds. J Eur Ceram Soc. 1999;19(13):2405–2414.
- Bowen HK. Basic research needs on high temperature ceramics for energy applications. Material Science & Engineering. 1980;44(1):1–56.
- Tandon R, Dumm HP, Corral EL, et al. Ultra high temperature ceramics for hypersonic vehicle applications. Ind Heat. 2006;1:36–38.
- Zhou YJ, Zhang Y, Wang YL, et al. Solid solution alloys of AlCoCrFeNiTix with excellent room-temperature mechanical properties. Appl Phys Lett. 2007;90(18):253.
- Yang X, Zhang Y, Liaw PK. Microstructure and compressive properties of NbTiVTaAlx high entropy alloys. Procedia Eng. 2012;36:292–298.
- Senkov ON, Wilks GB, Scott JM, et al. Mechanical properties of Nb25Mo25Ta25W25 and V20Nb20Mo20Ta20W20 refractory high entropy alloys. Intermetallics. 2011;19(5):698–706.
- Senkov ON, Scott JM, Senkova SV, et al. Microstructure and room temperature properties of a high-entropy TaNbHfZrTi alloy. J Alloys Compd. 2011;509(20):6043–6048.
- Hsu C-Y, Yeh J-W, Chen S-K, et al. Wear resistance and high-temperature compression strength of Fcc CuCoNiCrAl0.5Fe alloy with boron addition. Metall Mater Trans A. 2004;35(5):1465–1469.
- Chuang M-H, Tsai M-H, Wang W-R, et al. Microstructure and wear behavior of AlxCo1.5CrFeNi1.5Tiy high-entropy alloys. Acta Mater. 2011;59(16):6308–6317.
- Chou YL, Wang YC, Yeh JW, et al. Pitting corrosion of the high-entropy alloy Co1.5CrFeNi1.5Ti0.5Mo0.1 in chloride-containing sulphate solutions. Corros Sci. 2010;52(10):3481–3491.
- Chen YY, Duval T, Hung UD, et al. Microstructure and electrochemical properties of high entropy alloys – a comparison with type-304 stainless steel. Corros Sci. 2005;47(9):2257–2279.
- Rost CM, Sachet E, Borman T, et al. Entropy-stabilized oxides. Nat Commun. 2015;6:8485.
- Harrington TJ, Gild J, Sarker P, et al. Phase stability and mechanical properties of novel high entropy transition metal carbides. Acta Mater. 2019;166:271–280.
- Xiang H, Xing Y, Dai F-z, et al. High-entropy ceramics: present status, challenges, and a look forward. J Adv Ceram. 2021;10(3):385–441.
- Oses C, Toher C, Curtarolo S. High-entropy ceramics. Nat Rev Mater. 2020;5(4):295–309.
- Mayrhofer PH, Kirnbauer A, Ertelthaler P, et al. High-entropy ceramic thin films; a case study on transition metal diborides. Scr Mater. 2018;149:93–97.
- Gild J, Zhang Y, Harrington T, et al. High-entropy metal diborides: a new class of high-entropy materials and a new type of ultrahigh temperature ceramics. Sci Rep. 2016;6:37946.
- Tallarita G, Licheri R, Garroni S, et al. Novel processing route for the fabrication of bulk high-entropy metal diborides. Scr Mater. 2019;158:100–104.
- Sarker P, Harrington T, Toher C, et al. High-entropy high-hardness metal carbides discovered by entropy descriptors. Nat Commun. 2018;9(1):4980.
- Castle E, Csanádi T, Grasso S, et al. Processing and properties of high-entropy ultra-high temperature carbides. Sci Rep. 2018;8(1):8609.
- Peng C, Gao X, Wang M, et al. Diffusion-controlled alloying of single-phase multi-principal transition metal carbides with high toughness and low thermal diffusivity. Appl Phys Lett. 2019;114(1):011905.
- Wang Y, Csanadi T, Zhang H, et al. Enhanced hardness in high-entropy carbides through atomic randomness. Adv Theory Simul. 2020;3(9).
- Kaufmann K, Maryanovsky D, Mellor WM, et al. Discovery of high-entropy ceramics via machine learning. Npj Comput Mater. 2020;6(42).
- Berardan D, Franger S, Meena AK, et al. Room temperature lithium superionic conductivity in high entropy oxides. J Mater Chem A. 2016;4:9536–9541.
- Jiang S, Hu T, Gild J, et al. A new class of high-entropy perovskite oxides. Scr Mater. 2018;142:116–120.
- Hong W, Chen F, Shen Q, et al. Microstructural evolution and mechanical properties of (Mg,Co,Ni,Cu,Zn)O high-entropy ceramics. J Am Ceram Soc. 2019;102(4):2228–2237.
- Rak Z, Rost C, Lim M, et al. Charge compensation and electrostatic transferability in three entropy-stabilized oxides: results from density functional theory calculations. J Appl Phys. 2016;120(9):095105.
- Yang Y, Ma L, Gan G-Y, et al. Investigation of thermodynamic properties of high entropy (TaNbHfTiZr)C and (TaNbHfTiZr)N. J Alloys Compd. 2019;788:1076–1083.
- Moskovskikh D, Vorotilo S, Buinevich V, et al. Extremely hard and tough high entropy nitride ceramics. Sci Rep. 2020;10:19874.
- Dippo OF, Mesgarzadeh N, Harrington TJ, et al. Bulk high-entropy nitrides and carbonitrides. Sci Rep. 2020;10:21288.
- Qin M, Gild J, Hu C, et al. Dual-phase high-entropy ultra-high temperature ceramics. J Eur Ceram Soc. 2020;40(15):5037–5050.
- Wen T, Ye B, Nguyen MC, et al. Thermophysical and mechanical properties of novel high-entropy metal nitride-carbides. J Am Ceram Soc. 2020:(103):6475–6489.
- Zhang R-Z, Gucci F, Zhu H, et al. Data-driven design of ecofriendly thermoelectric high-entropy sulfides. Inorg Chem. 2018;57(20):13027–13033.
- Cui M, Yang C, Li B, et al. High-entropy metal Sulfide nanoparticles promise high-performance oxygen evolution reaction. Adv Energy Mater. 2021;11(3):2002887.
- Cedillos-Barraza O, Manara D, Boboridis K, et al. Investigating the highest melting temperature materials: a laser melting study of the TaC-HfC system. Sci Rep. 2016;6:37962.
- Oyama ST. Introduction to the chemistry of transition metal carbides and nitrides. In: ST Oyama, editor. The chemistry of transition metal carbides and nitrides. Dordrecht: Springer Netherlands; 1996. p. 1–27.
- Yeh JW, Chen SK, Lin SJ, et al. Nanostructured high-entropy alloys with multiple principal elements: novel alloy design concepts and outcomes. Adv Eng Mater. 2004;6(5):299–303.
- Miracle DB, Senkov ON. A critical review of high entropy alloys and related concepts. Acta Mater. 2017;122:448–511.
- Zhang LS, Ma GL, Fu LC, et al. Recent progress in high-entropy alloys. Adv Mat Res. 2013;631–632:227–232.
- Ye B, Wen T, Huang K, et al. First-principles study, fabrication, and characterization of (Hf 0.2 Zr 0.2 Ta 0.2 Nb 0.2 Ti 0.2)C high-entropy ceramic. J Am Ceram Soc. 2019;102(7):4344–4352.
- Malinovskis P, Fritze S, Riekehr L, et al. Synthesis and characterization of multicomponent (CrNbTaTiW)C films for increased hardness and corrosion resistance. Mater Des. 2018;149:51–62.
- Zhang H, Hedman D, Feng P, et al. A high-entropy B 4 (HfMo 2 TaTi) C and SiC ceramic composite. Dalton Trans. 2019;48:5161–5157.
- Yu X-X, Thompson GB, Weinberger CR. Influence of carbon vacancy formation on the elastic constants and hardening mechanisms in transition metal carbides. J Eur Ceram Soc. 2015;35(1):95–103.
- Yan X, Constantin L, Lu Y, et al. (Hf0.2Zr0.2Ta0.2Nb0.2Ti0.2)C high-entropy ceramics with low thermal conductivity. J Am Ceram Soc. 2018;101(10):4486–4491.
- Zhou J, Zhang J, Zhang F, et al. High-entropy carbide: A novel class of multicomponent ceramics. Ceram Int. 2018;44(17):22014–22018.
- Braic V, Vladescu A, Balaceanu M, et al. Nanostructured multi-element (TiZrNbHfTa)N and (TiZrNbHfTa)C hard coatings. Surf Coat Technol. 2012;211:117–121.
- Yang Y, Wang W, Gan G-Y, et al. Structural, mechanical and electronic properties of (TaNbHfTiZr)C high entropy carbide under pressure: Ab initio investigation. Physica B-Condensed Matter. 2018;550:163–170.
- Feng L, Lee S-H, Wang H, et al. Synthesis and densification of nano-crystalline hafnium carbide powder. J Eur Ceram Soc. 2015;35(15):4073–4081.
- Feng L, Fahrenholtz WG, Hilmas GE, et al. Synthesis of single-phase high-entropy carbide powders. Scr Mater. 2019;162:90–93.
- He Y, Peng C, Xin S, et al. Vacancy effect on the preparation of high-entropy carbides. J Mater Sci. 2020;55(16):6754–6760.
- Wu K-H, Wang Y, Chou K-C, et al. Low-temperature synthesis of single-phase refractory metal compound carbides. Int J Refract Met Hard Mater. 2021;98:105567.
- Lun F, Kim JM, Lee SH, et al. Synthesis of a fine (Ta 0.8, Hf 0.2)C powder from carbide or oxide powder mixtures. J Am Ceram Soc. 2016;99(4):1129–1132.
- Li F, Lu Y, Wang X-G, et al. Liquid precursor-derived high-entropy carbide nanopowders. Ceram Int. 2019;45(17):22437–22441.
- Du B, Liu H, Chu Y. Fabrication and characterization of polymer-derived high-entropy carbide ceramic powders. J Am Ceram Soc. 2020;103(8):4063–4068.
- Sun Y, Chen F, Qiu W, et al. Synthesis of rare earth containing single-phase multicomponent metal carbides via liquid polymer precursor route. J Am Ceram Soc. 2020.
- Šolcová P, Nižňanský M, Schulz J, et al. Preparation of high-entropy (Ti, Zr, Hf, Ta, Nb) carbide powder via solution chemistry. Inorg Chem. 2021;60(11):7617–7621.
- Chicardi E, Garcia-Garrido C, Gotor FJ. Low temperature synthesis of an equiatomic (TiZrHfVNb)C-5 high entropy carbide by a mechanically-induced carbon diffusion route. Ceram Int. 2019;45(17):21858–21863.
- Chicardi E, Garcia-Garrido C, Hernandez-Saz J, et al. Synthesis of all equiatomic five-transition metals high entropy carbides of the IVB (Ti, Zr, Hf) and VB (V, Nb, Ta) groups by a low temperature route. Ceram Int. 2020;46(13):21421–21430.
- Ning S, Wen T, Ye B, et al. Low-temperature molten salt synthesis of high-entropy carbide nanopowders. J Am Ceram Soc. 2020;103(3):2244–2251.
- Braic M, Braic V, Balaceanu M, et al. Characteristics of (TiAlCrNbY)C films deposited by reactive magnetron sputtering. Surf Coat Technol. 2010;204(12-13).
- Braic V, Balaceanu M, Braic M, et al. Characterization of multi-principal-element (TiZrNbHfTa)N and (TiZrNbHfTa)C coatings for biomedical applications. J Mech Behav Biomed Mater. 2012;10:197–205.
- Braic M, Balaceanu M, Vladescu A, et al. Deposition and characterization of multi-principal-element (CuSiTiYZr)C coatings. Appl Surf Sci. 2013;284:671–678.
- Braic V, Parau A, Pana I, et al. Effects of substrate temperature and carbon content on the structure and properties of (CrCuNbTiY)C multicomponent coatings. Surf Coat Technol. 2014;258:996–1005.
- Vladescu A, Titorencu I, Dekhtyar Y, et al. In vitro biocompatibility of Si alloyed multi-principal element carbide coatings. PLoS One. 2016;11(8):e0161151.
- Liang SC, Tsai DC, Chang ZC, et al. Structural and mechanical properties of multi-element (TiVCrZrHf)N coatings by reactive magnetron sputtering. Appl Surf Sci. 2011;258(1):399–403.
- Pei YT, Chen CQ, Shaha KP, et al. Microstructural control of TiC/a-C nanocomposite coatings with pulsed magnetron sputtering. Acta Mater. 2008;56(4):696–709.
- Rost CM, Borman T, Hossain MD, et al. Electron and phonon thermal conductivity in high entropy carbides with variable carbon content. Acta Mater. 2020;196:231–239.
- Andreyev A, Kartmazov G, Chikryzhov A, et al. Production and mechanical properties of high-entropic carbide based on the TiZrHfVNbTa multicomponent alloy. J Superhard Mater. 2017;39(3):166–171.
- Kao WH, Su YL, Horng JH, et al. Mechanical, tribological, anti-corrosion and anti-glass sticking properties of high-entropy TaNbSiZrCr carbide coatings prepared using radio-frequency magnetron sputtering. Mater Chem Phys. 2021;268:124741.
- Wang F, Zhang X, Yan X, et al. The effect of submicron grain size on thermal stability and mechanical properties of high-entropy carbide ceramics. J Am Ceram Soc. 2020;103(8):4463–4472.
- Demirskyi D, Suzuki TS, Yoshimi K, et al. Synthesis and high-temperature properties of medium-entropy (Ti,Ta,Zr,Nb)C using the spark plasma consolidation of carbide powders. Open Ceramics. 2020;2:100015.
- Dusza J, Csanádi T, Medveď D, et al. Nanoindentation and tribology of a (Hf-Ta-Zr-Nb-Ti)C high-entropy carbide. J Eur Ceram Soc. 2021;41(11):5417–5426.
- Dusza J, Švec P, Girman V, et al. Microstructure of (Hf-Ta-Zr-Nb)C high-entropy carbide at micro and nano/atomic level. J Eur Ceram Soc. 2018;38(12):4303–4307.
- Liu D, Zhang A, Jia J, et al. Phase evolution and properties of (VNbTaMoW)C high entropy carbide prepared by reaction synthesis. J Eur Ceram Soc. 2020;40(8):2746–2751.
- Moskovskikh DO, Vorotilo S, Sedegov AS, et al. High-entropy (HfTaTiNbZr)C and (HfTaTiNbMo)C carbides fabricated through reactive high-energy ball milling and spark plasma sintering. Ceram Int. 2020;46(11):19008–19014.
- Wei X-F, Qin Y, Liu J-X, et al. Gradient microstructure development and grain growth inhibition in high-entropy carbide ceramics prepared by reactive spark plasma sintering. J Eur Ceram Soc. 2020;40(4):935–941.
- Feng L, Fahrenholtz WG, Hilmas GE. Low-temperature sintering of single-phase, high-entropy carbide ceramics. J Am Ceram Soc. 2019;102(12):7217–7224.
- Wang K, Chen L, Xu C, et al. Microstructure and mechanical properties of (TiZrNbTaMo)C high-entropy ceramic. J Mater Sci Technol. 2020;39:99–105.
- Wei X-F, Liu J-X, Li F, et al. High entropy carbide ceramics from different starting materials. J Eur Ceram Soc. 2019;39(10):2989–2994.
- Biesuz M, Saunders TG, Chen K, et al. Interfacial reaction between ZrNbHfTa foil and graphite: formation of high-entropy carbide and the effect of heating rate on its microstructure. J Eur Ceram Soc. 2020;40(7):2699–2708.
- Ye B, Wen T, Nguyen MC, et al. First-principles study, fabrication and characterization of (Zr0.25Nb0.25Ti0.25V0.25)C high-entropy ceramics. Acta Mater. 2019;170:15–23.
- WILLIAMS SW. Electrical properties of hard materials. Int J Refract Metals Hard Mater. 1999;17(1–3):21–26.
- Pötschke J, Dahal M, Herrmann M, et al. Preparation of high-entropy carbides by different sintering techniques. J Mater Sci. 2021;56(19):11237–11247.
- Zhang W, Chen L, Xu C, et al. Densification, microstructure and mechanical properties of multicomponent (TiZrHfNbTaMo)C ceramic prepared by pressureless sintering. J Mater Sci Technol. 2021;72:23–28.
- Chen H, Xiang H, Dai F-Z, et al. High porosity and low thermal conductivity high entropy (Zr0.2Hf0.2Ti0.2Nb0.2Ta0.2)C. J Mater Sci Technol. 2019;35(8):1700–1705.
- Zhou R, Li M, Wu H, et al. Effect of multi-component carbides on the mechanical behavior of a multi-element alloy. Mater Sci Eng A – Structural Materials Properties Microstructure and Processing. 2019;758:99–102.
- Bao W, Wang X-G, Ding H, et al. High-entropy M2AlC-MC (M = Ti, Zr, Hf, Nb, Ta) composite: synthesis and microstructures. Scr Mater. 2020;183:33–38.
- Nemani SK, Zhang B, Wyatt B, et al. High-Entropy 2D carbide MXenes. ChemRxiv. 2021.
- Kan WH, Zhang Y, Tang X, et al. Precipitation of (Ti, Zr, Nb, Ta, Hf)C high entropy carbides in a steel matrix. Materialia. 2020;9:100540.
- Leng Y, Zhang Z, Chen H, et al. Overcoming the phase separation within high-entropy metal carbide by poly(ionic liquid)s. Chem Commun (Camb. 2021;57(30):3676–3679.
- Liu J, Xiong J, Guo Z, et al. Preparation of high-entropy (Zr0.25Hf0.25Ta0.25Ti0.25)C-Ni-Co composite by spark plasma sintering. Metall Mater Trans A – Physical Metallurgy and Materials Science. 2020;51(12):6706–6713.
- Wang H, Wang S, Cao Y, et al. Oxidation behaviors of (Hf0.25Zr0.25Ta0.25Nb0.25)C and (Hf0.25Zr0.25Ta0.25Nb0.25)C-SiC at 1300-1500 degrees C. J Mater Sci Technol. 2021;60:147–155.
- Lu K, Liu J-X, Wei X-F, et al. Microstructures and mechanical properties of high-entropy (Ti0.2Zr0.2Hf0.2Nb0.2Ta0.2)C ceramics with the addition of SiC secondary phase. J Eur Ceram Soc. 2020;40(54):1839–1847.
- Cai F, Ni D, Chen B, et al. Fabrication and properties of Cf/(Ti0.2Zr0.2Hf0.2Nb0.2Ta0.2)C-SiC high-entropy ceramic matrix composites via precursor infiltration and pyrolysis. J Eur Ceram Soc. 2021;41(12):5863–5871.
- Zhou N, Hu T, Huang J, et al. Stabilization of nanocrystalline alloys at high temperatures via utilizing high-entropy grain boundary complexions. Scr Mater. 2016;124:160–163.
- Zhou N, Hu T, Luo J. Grain boundary complexions in multicomponent alloys: challenges and opportunities. Curr Opin Solid State Mater Sci. 2016;20(5):268–277.
- Riedel R. Handbook of ceramic hard materials. Transit Met Carbides, Nitrides, Carbonitrides. 2000: 202–252. 10.1002/9783527618217.
- Ye B, Chu Y, Huang K, et al. Synthesis and characterization of (Zr1/3Nb1/3Ti1/3)C metal carbide solid-solution ceramic. J Am Ceram Soc. 2019;102(3):919–923.
- Zhao P, Zhu J, Zhang Y, et al. A novel high-entropy monoboride (Mo0.2Ta0.2Ni0.2Cr0.2W0.2)B with superhardness and low thermal conductivity. Ceram Int. 2020;46(17):26626–26631.
- Wei X, Back C, Izhvanov O, et al. Zirconium carbide produced by spark plasma sintering and Hot pressing: densification kinetics, grain growth, and thermal properties. Materials (Basel). 2016;9(7.
- Zhang B, Yin J, Wang Y, et al. Low temperature densification mechanism and properties of Ta1-xHfxC solid solutions with decarbonization and phase transition of Cr3C2. J Materiomics. 2020.
- Liu D, Zhang A, Jia J, et al. Reaction synthesis and characterization of a new class high entropy carbide (NbTaMoW)C. Mater Sci Eng A. 2021;804:140520.
- Zhang Y, Stocks GM, Jin K, et al. Influence of chemical disorder on energy dissipation and defect evolution in concentrated solid solution alloys. Nat Commun. 2015;6(1):8736.
- Körmann F, Ikeda Y, Grabowski B, et al. Phonon broadening in high entropy alloys. Npj Comput Math. 2017;3(1):36.
- Zhao F, Hui W, Yuan W, et al. Thermoelectric performance of PbSnTeSe high-entropy alloys. Mater Res Lett. 2016: 1–8.
- Chou H-P, Chang Y-S, Chen S-K, et al. Microstructure, thermophysical and electrical properties in AlxCoCrFeNi (0≤x≤2) high-entropy alloys. Mater Sci Eng: B. 2009;163(3):184–189.
- Wei X-F, Liu J-X, Bao W, et al. High-entropy carbide ceramics with refined microstructure and enhanced thermal conductivity by the addition of graphite. J Eur Ceram Soc. 2021;41(9):4747–4754.
- Dai F-Z, Wen B, Sun Y, et al. Theoretical prediction on thermal and mechanical properties of high entropy (Zr0.2Hf0.2Ti0.2Nb0.2Ta0.2)C by deep learning potential. J Mater Sci Technol. 2020;43:168–174.
- Jiang S, Shao L, Fan T-W, et al. Elastic and thermodynamic properties of high entropy carbide (HfTaZrTi)C and (HfTaZrNb)C from ab initio investigation. Ceram Int. 2020;46(10):15104–15112.
- Feng L, Chen W-T, Fahrenholtz WG, et al. Strength of single-phase high-entropy carbide ceramics up to 2300 degrees C. J Am Ceram Soc. 2021;104(1):419–427.
- Balasubramanian K, Khare SV, Gall D. Valence electron concentration as an indicator for mechanical properties in rocksalt structure nitrides, carbides and carbonitrides. Acta Mater. 2018;152:175–185.
- Csanadi T, Castle E, Reece MJ, et al. Strength enhancement and slip behaviour of high-entropy carbide grains during micro-compression. Sci Rep. 2019;9:10200.
- Tamás Csanádi MV, Dankházi Z, Reece MJ, et al. Small scale fracture and strength of high-entropy carbide grains during microcantilever bending experiments. J Eur Ceram Soc. 2020;40(14):4774–4782.
- Han X, Girman V, Sedlak R, et al. Improved creep resistance of high entropy transition metal carbides. J Eur Ceram Soc. 2019;40(7):2709–2715.
- Zhang H, Akhtar F. Processing and characterization of refractory quaternary and quinary high-entropy carbide composite. Entropy . 2019;21(5).
- Wang F, Yan X, Wang T, et al. Irradiation damage in (Zr0.25Ta0.25Nb0.25Ti0.25)C high-entropy carbide ceramics. Acta Mater. 2020;195:739–749.
- Dusza J, Csanádi T, Medveď D, et al. Nanoindentation and tribology of a (Hf-Ta-Zr-Nb-Ti)C high-entropy carbide. J Eur Ceram Soc. 2021;41(11):5417–5426.
- Sangiovanni DG, Mellor W, Harrington T, et al. Enhancing plasticity in high-entropy refractory ceramics via tailoring valence electron concentration. Mater Des. 2021;209:109932.
- Backman L, Opila EJ. Thermodynamic assessment of the group IV, V and VI oxides for the design of oxidation resistant multi-principal component materials. J Eur Ceram Soc. 2019;39(5):1796–1802.
- Backman L, Gild J, Luo J, et al. Part I: Theoretical predictions of preferential oxidation in refractory high entropy materials. Acta Mater. 2020;197:20–27.
- Backman L, Gild J, Luo J, et al. Part II: Experimental verification of computationally predicted preferential oxidation of refractory high entropy ultra-high temperature ceramics. Acta Mater. 2020;197:81–90.
- Wang Y, Zhang R-z, Zhang B, et al. The role of multi-elements and interlayer on the oxidation behaviour of (Hf-Ta-Zr-Nb)C high entropy ceramics. Corros Sci. 2020;176:109019.
- Ye B, Wen T, Chu Y. High-temperature oxidation behavior of (Hf0. 2Zr0. 2Ta0. 2Nb0. 2Ti0. 2) C high-entropy ceramics in air. J Am Ceram Soc. 2020;103(1):500–507.
- Ye B, Wen T, Liu D, et al. Oxidation behavior of (Hf0. 2Zr0. 2Ta0. 2Nb0. 2Ti0. 2) C high-entropy ceramics at 1073-1473 K in air. Corros Sci. 2019;153:327–332.
- Tan Y, Chen C, Li S, et al. Oxidation behaviours of high-entropy transition metal carbides in 1200° C water vapor. J Alloys Compd. 2020;816:152523.
- Wang H, Han X, Liu W, et al. Oxidation behavior of high-entropy carbide (Hf0.2Ta0.2Zr0.2Ti0.2Nb0.2)C at 1400–1600 °C. Ceram Int. 2021;47(8):10848–10854.
- Wang Y, Reece MJ. Oxidation resistance of (Hf-Ta-Zr-Nb)C high entropy carbide powders compared with the component monocarbides and binary carbide powders. Scr Mater. 2021;193:86–90.
- Mellor WM, Kaufmann K, Dippo OF, et al. Development of ultrahigh-entropy ceramics with tailored oxidation behavior. J Eur Ceram Soc. 2021;41(12):5791–5800.
- Wang H, Cao Y, Liu W, et al. Oxidation behavior of (Hf0.2Ta0.2Zr0.2Ti0.2Nb0.2)C-xSiC ceramics at high temperature. Ceram Int. 2020;46(8):11160–11168.
- Wang F, Yan X, Shao L, et al. Irradiation damage behavior in novel high-entropy carbide ceramics. Transactions. 2019;120:327–327.
- Wang F, Yan X, Shao L, et al. Irradiation damage behavior in novel high-entropy carbide ceramics. Transactions Am Nucl Soc. 2019;120:327.