Additive technologies in which physical objects are created directly from computer generated models emerged in the 1980s under the name of rapid prototyping. The basic concept of rapid prototyping is layer laminate manufacturing where three-dimensional (3D) structures are formed by laminating thin layers according to two-dimensional (2D) slice data, obtained from a 3D model created on a CAD/CAM system. Rapid prototyping emerged as a step forward in the product development cycle, reducing lead times for new products.
Initially, additive technologies were used as rapid prototyping mainly employed for: i) physical verification of a previously defined CAD model, ii) form, fit and function testing, iii) creating models regardless of draft angles and parting lines; iv) concept presentations and design reviews, v) creating anatomical models designed from computer-aided tomography (CAT) data for surgical planning and prosthesis design; vi) producing relief models for geographical applications; vicreating 3D portraits (three-dimensional photography) using data produced by 3D shape digitising technology, etc.
In the 1990s, additive prototyping moved from rapid prototyping to rapid tooling. In this new domain, additive technologies were used for direct tooling as well to produce masters for rapid tooling, using conversion technologies like investment casting and silicone, epoxy and spray metal moulds.
In the late 1990s, two new domains emerged of additive technologies’ applications. One is Rapid Manufacturing integrating computer automated production with intrinsic technology characteristics to make individual products in small volumes with no need of tooling. The other is Biomanufacturing combining the use of additive technologies, biodegradable and biocompatible materials, cells, growth factors, etc., to produce biological structures for tissue engineering applications.
Professor Yongnian Yan was a pioneer in the field of additive technologies and played a key role in all the abovementioned major domains. He was born in Chongqing on January, 12, 1938 at Chongqing, China. After graduating from Tsinghua University in 1962, he stayed all his academic career at the same University.
Professor Yan explored developed additive technologies in all its different aspects: materials, fabrication strategies, computer simulation, etc. He extended the use of these technologies to a wide range of new application fields and proposed novel fabrication principles such as the Rapid Ice Prototyping Forming. The first Chinese melted extrusion manufacturing system, called MEM-250-II, was also developed by his group at the Center for Laser Rapid Forming, Tsinghua University. Other systems developed by Professor Yan's group were the Auro-350 a stereolitographic machine and the Slicing Solid Manufacturing system based on the Laminated Object Manufacturing process.
Professor Yan conducted relevant research in rapid tooling too. In this domain, he studied both the use of electroforming moulds based on stereolithographic prototypes and the unbaked ceramic mould casting process based on the rapid prototyping technology. He also proposed a three dimensional non-linear thermo-mechanical model for the computer simulation of the dimensional accuracy for casting dies in rapid tooling.
In 2005, Professor Yan together with Professor Wei Sun (Drexel University), Myron Spector (Harvard Medical School) and Feng Lin (Tsinghua University) organised the first US–China National Science Foundation-sponsored workshop on biomanufacturing. This workshop, which brought together multi-disciplinary researchers from United States, China, Australia and Portugal (Figure 1), reviewed the state-of-the-art of an array of additive technologies to produce scaffolds for tissue engineering, providing precision multi-scale control of material, architecture, and cells, as well establishing the foundations of Biomanufacturing.
Figure 1. Participants at the first international workshop in biomanufacturing hosted by Tsinghua University, China, 2005.
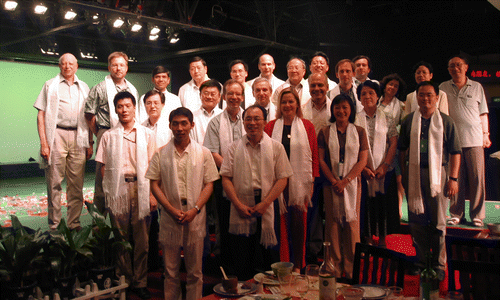
Combining principles from manufacturing and life sciences, Professor Yan developed the Low-Temperature Deposition Technique to produce scaffolds for bone and cartilage applications. In this technology, no heating process is used during the liquefying material process. Microporosity is created from the sublimation of solvent during freeze-drying. Another Biomanufacturing process developed by his group is the Multi-nozzle Deposition Manufacturing, an improvement of the Low-Temperature Deposition Technique, which incorporates more than one jetting nozzle into the systems. This technique allows the incorporation of biomolecules into the scaffold during the fabrication process, enabling the fabrication of controlled-released scaffolds. Professor Yan's group also developed the Cell Direct Controlled Assembly technology to construct precursor tissue analogs.
Professor Yongnian Yan is the Director of the Center for Laser Rapid Forming at Tsinghua University, Executive Trustee of the Chinese Mechanical Engineering Society Non-traditional Processing Division, chairman of Rapid Forming Technologies Committee and representative of China at Global Alliance of Rapid Prototyping Associations (GARPA). He is member of the Editorial Board of Virtual and Physical Prototyping Journal since the beginning and member of Editorial Board of other international journals like the Rapid Prototyping Journal and the Journal of Engineering Manufacturing. He also served as member of the Scientific Committee of an impressive number of International Conferences. Since 2003, he has been serving at the Scientific Committee of the International Conference on Advanced Research in Virtual and Rapid Prototyping (VRAP), which takes place biannually at Leiria, Portugal, and his contribution has been decisive for its success. In 2007, the organizing committee of VRAP distinguished Professor Yan with an Honorary Chairman award (Figure 2). He has also been awarded by several Chinese and International Organizations.
Figure 2. Professor Yan receiving a research award delivered by Professor Bidanda (Pittsburgh University) during the 2nd International Conference on Advanced Research in Virtual and Rapid Prototyping (VRAP2005), Leiria, Portugal.
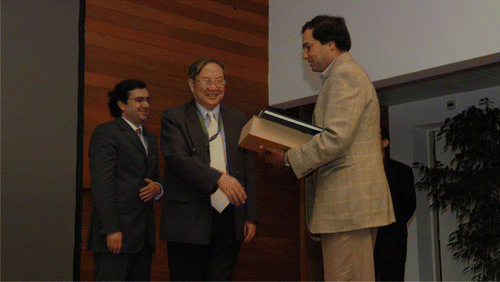
Professor Yan is a highly prestigious academic that has contributed to the advancement of engineering in society and progress in research, which we have the honour to be colleagues. In order to celebrate his 70th anniversary, we invited close friends and researchers to contribute for this issue with papers focusing on the concept of Biomanufacturing, the most recent challenge embraced by him.
A total of five papers are presented in this issue. In the first paper, Gibson and co-authors investigate the mechanical and in vitro behaviour of composite poly(l-lactide-co-d,l-lactide)/tri-calcium phosphate scaffolds. These scaffolds, produced through a customized extrusion deposition process similar to the Fused Deposition Modelling technique, exhibit good biocompatibility and potential for both functional mechanical and biological role requirements, as scaffolds for bone tissue engineering applications or bone graft substitutes.
Wei Sun and co-authors report the use of an additive fabrication technology called Precision Extrusion Deposition to manufacture three-dimensional polycaprolactane scaffolds and their surface treatment with plasma source for enhanced osteoblast cell adhesion and proliferation. The third paper from Hutmacher and co-authors present a comparison of chondrogenesis in static and dynamic environment using polycaprolactone/poly(ethylene oxide) scaffolds produced by an extrusion-based additive fabrication system. In this paper, the authors investigate the internal architecture of the scaffold, its matrix composition and dynamic environmental conditions on the resulting scaffold-cell construct.
The use of Laser Direct-Write and Laser Interference Photopolymerization to produce microstructured hydrogels is the core of the paper by Suman Das and co-authors. In this paper the authors present the results of fabrication micrometer and sub-micrometer scale structures in polyethylene glycol diacrylate hydrogel, demonstrating the ability to fabricate fine structures over large areas with no need to use templates or masks.
Finally, Malshe and co-authors in a paper entitled “Sustainable nanotechnology enabled by biomanufacturing: the cell as a production plant”, explore ability of biological cell to be a production plant for controlled green synthesis of nanoparticles. In the paper, authors investigate cell assisted programmable organization and assembly of nanoparticles using genetically engineered cells.