ABSTRACT
This work investigated laser aided additive manufacturing (LAAM) high-strength steel by leveraging the intrinsic tempering effect to facilitate the formation of high-fraction of metal carbides (e.g. M23C6 and M7C3) in the as-built samples. The intrinsic tempering effect contributes to a superior mechanical property than traditional manufacturing methods in as-built condition, promoting subsequent heat treatments (HTs) for excellent mechanical properties. The influence of HTs on the microstructures and mechanical properties were characterised in multi-scales. A large number of carbides are intrinsically formed due to the tempering effect during deposition. The high-density dislocations in the as-built sample facilitate the formation of massive nano-twins and carbides during HT. The HTed sample achieves a true tensile stress of about 1.81 GPa together with a true strain of about 21%, achieving an excellent strength-ductility combination compared to wide-range high-strength steels processed by additive manufacturing and conventional methods. The grain and twin boundaries strengthening, precipitation strengthening and dislocation strengthening contribute to the high strength, while the good ductility originates from twinning induced plasticity (TWIP) and transformation-induced plasticity (TRIP) effects, and high work-hardening rate, during deformation. The findings imply a potential way to develop AM-customised materials by fully understanding and utilising the IHT effect.
Acknowledgements
This work was supported by Agency for Science, Technology and Research (A*Star), the Republic of Singapore, under the IAF-PP program ‘Integrated large format hybrid manufacturing using wire-fed and powder-blown technology for LAAM process’ (Grant No: A1893a0031) and Career Development Fund (Grant No: C210112051). Thanks to Danli Zhang (from State Key Laboratory for Mechanical Behaviour of Materials of China) for the kind support with micropillar compression testing.
Data availability statement
The data of the findings are available from the correspondents upon reasonable request.
Disclosure statement
No potential conflict of interest was reported by the author(s).
Additional information
Funding
Notes on contributors
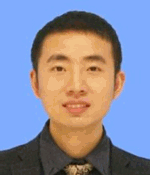
Chaolin Tan
Dr Chaolin Tan is a Research Scientist in Singapore Institute of Manufacturing Technology (SIMTech). He received his PhD degree in Materials Processing Engineering from South China University of Technology in conjunction with University of Birmingham (UK) in 2019. His research experience on laser additive manufacturing (LAM) has been over 7 years, with rich research experiences in LAM of advanced high strength steels since 2013. His research interests include LAM new materials and heterostructured materials.
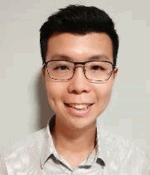
Youxiang Chew
Dr Youxiang Chew is a Research Scientist and deputy group manager in Singapore Institute of Manufacturing Technology (SIMTech). He joined SIMTech in 2015 and obtained his PhD in Mechanical Engineering from Nanyang Technological University (Singapore). He has over 8 years of experience in Laser directed energy deposition (LDED) technology, focusing on process, residual stress modelling and integration of machine learning with FEM to optimize laser deposition toolpaths. His other research interest includes the development of high entropy alloy and bulk spatially patterned heterostructured multi-materials parts using LDED.
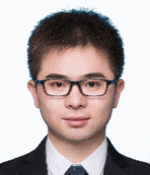
Fei Weng
Dr Fei Weng is a Research Scientist in Singapore Institute of Manufacturing Technology (SIMTech). He received his PhD degree in Materials Science and Engineering from Shandong University, China. His current research interest is in laser aided additive manufacturing of Ti-6Al-4V alloys, nickel-based alloys, high/medium entropy alloys, and other novel high-performance alloys. The emphasis is on microstructure evolution and property evaluation. Dr. Weng also has experience in repair and surface medication of metal components by laser cladding.
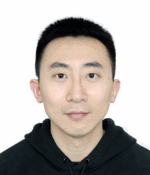
Shang Sui
Dr Shang Sui is a Research Scientist in Singapore Institute of Manufacturing Technology. He received his B.S. degree in Materials Forming and Control Engineering in 2013 as an outstanding graduate, his Ph.D. in Materials Processing Engineering in 2019, all from Northwestern Polytechnical University of China. He has been engaged in Laser Additive Manufacturing (LAM) technology for 6 years since 2013 when he was a bachelor student at Northwestern Polytechnical University. His research is focused on the microstructural optimization and mechanical performance enhancement of LAM-built nickel-based superalloy Inconel 718.
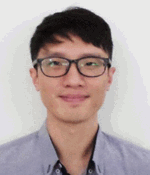
Zhenglin Du
Dr Zhenglin Du is a scientist in the Agency for Science, Technology and Research (A*STAR). He graduate from Nanyang technological University during 2018 with a Doctor of Philosophy (PhD) in Mechanical Engineering with Honors. He specializes in additive manufacturing, process optimisation and metallurgy.

Fern Lan Ng
Ms Fern Lan Ng is a Senior Research Engineer in Singapore Institute of Manufacturing Technology. She specializes in material characterization and analysis using SEM, EBSD, TEM and XRD etc.
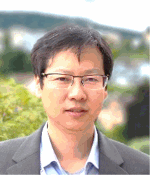
Guijun Bi
Dr Guijun Bi is a Senior Scientist and Group Manager with the Joining & Machining Group in Singapore Institute of Manufacturing Technology. He also holds the adjunct professorship with the National University of Singapore. Dr Bi received his PhD in laser material processing from Fraunhofer Institute for Laser Technology and RWTH Aachen University, Germany. His research focuses on additive manufacturing for surface modification, repair and 3D printing, development of new materials using additive manufacturing, hybrid technologies combined additive and subtractive manufacturing, process monitoring and control, modelling and simulation of additive manufacturing and joining processes.