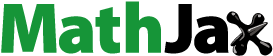
ABSTRACT
The consolidation of ceramic particles into the metallic matrix is promising to translate their exceptional properties from the micro-scale to the macro world. Herein, four different 15-5PH stainless steel (SS) matrix composites: 15-5PH/TiB2, 15-5PH/TiN, 15-5PH/TiC and 15-5PH/WC were fabricated by directed energy deposition (DED). The introduction of TiB2 particles substantially refines the martensite grain size, however, fails to achieve the performance improvement due to the elemental segregation of Cr and formation of considerable macro- and micro-cracks. The TiN composite realises a simultaneous enhancement of strength and ductility due to grain refinement, however, fails to enhance the corrosion resistance due to the Cr element segregation. The WC and TiC composites achieve the balance between the improved strength and ductility coupled with simultaneous enhancement of corrosion resistance. This work demonstrates the substantial potential in developing martensitic SS matrix composites with excellent strength-ductility synergy and corrosion resistance.
1 . Introduction
Metal matrix composites (MMCs) have stimulated tremendous interest in recent decades due to their excellent mechanical properties (Chen et al. Citation2020; Song, Dong, and Coddet Citation2014; Zou et al. Citation2021). In particular, ceramic composites, which are featured by the dispersion of secondary phase particles with the diameter scale ranging from several nanometers to micron-scale in the matrix and at the grain boundaries (GBs) (Dong et al. Citation2021), offer great potential in fabricating high-performance metallic components (Gu et al. Citation2021). However, there are significant challenges in preserving ceramic structure from powders to bulk parts after the consolidation processes. Many traditional consolidation methods, e.g. mechanical alloying, spark plasma sintering (Yang et al. Citation2017) and hot isostatic pressing (Cai et al. Citation2019a), have inherent limitations, such as the inability to obtain the homogeneous dispersion of ceramic particles in the matrix due to their high agglomeration.
Recently, additive manufacturing (AM) technologies, due to their flexibility in rapidly melting raw powders and complicated geometric formability, provide a novel route for near-net shaping of MMCs parts (Jiang et al. Citation2021a; Song et al. Citation2017). AM of 316L/SiC (Zou et al. Citation2021), Ti/TiC (Gu and Zhang Citation2013), CoCrFeNiMn/TiN (Li et al. Citation2020), Al/TiB2 (Xi et al. Citation2020) and Inconel 718/WC (Zhang et al. Citation2021) composites have been reported. Increasing the specific strength and stiffness of alloys simultaneously were achieved by assembling these rigid and light ceramic phases into the matrix. Three prevalent mechanisms can account for the performance improvement of MMCs, i.e. grain refinement, dislocation pinning/twinning, and microstructural modification in the matrix, and all of these mechanisms can appear simultaneously (Chen et al. Citation2020; Dong et al. Citation2021; Song, Dong, and Coddet Citation2014). Increased heterogeneous nucleation sites and grain growth retardation generally account for the grain refinement in MMCs (Fan et al. Citation2015). The nano- and submicron-sized particles resulting from the degradation of micron-sized ceramic particles can promote dislocation pinning/twinning (Wang et al. Citation2018). While the microstructural modification in the matrix due to the presence of transformation products can equilibrate the potential drawback of partial degradation of ceramic particles (Pelleg Citation1999).
Extensive studies have been performed to date to develop novel MMCs with high performances by selective laser melting (SLM), but a few works have been devoted to the research of directed-energy deposition (DED) processing of MMCs. Although SLM and DED share identical line-by-line and layer-by-layer manufacturing methodologies, they display noticeably different technology development directions and opportunities. The DED has more advantages than SLM in realising homogeneous dispersion of reinforcements due to the more sufficient laser energy input, larger-sized laser molten pool, and stronger molten pool flow during the DED process. On the other hand, most of the reinforced metallic matrices are Al-, Fe- and Ni-based alloys. However, there is still no comprehensive study towards the reinforcement of martensitic stainless steel (SS). Currently, the DED of high-performance martensitic SS has encountered some challenges owing to the following two reasons: (i) Martensitic SS by means of AM often suffers from the problem of low tensile ductility, and traditional methods for toughening martensitic SS inevitably result in the rapid drop of tensile strength, that is, the so-called strength-ductility trade-off (Tan et al. Citation2020; Tan et al. Citation2021b); (ii) Martensitic SS is sensitive to localised corrosion in wet and salt spray environment (especially Cl- containing condition) owing to low Cr content (Wei et al. Citation2020). Considering the importance of martensitic SS, it is thus necessary to develop novel martensitic SS matrix composites to achieve major improvements in strength-ductility and corrosion resistance.
In this paper, typical martensitic SS, 15-5PH, is specifically chosen in this work as a reinforced metallic matrix to investigate both the mechanical and electrochemical responses to different ceramic particles incorporation. Among all-ceramic particles, TiB2, TiC, TiN and WC featuring high melting, exceptional hardness and excellent wear resistance are, therefore, chosen as potential candidate reinforcements. The effects of TiB2, TiN, WC and TiC ceramic particles on the microstructure evolution, mechanical properties and corrosion resistance of DEDed MMCs were systematically investigated, and the underlying mechanisms responsible for the performance improvement/ deterioration induced by different ceramic particles were revealed.
2 . Experimental details
TiC, (d) TiB2 and (e) TiN powders. (f) A three-dimensional mixer is used for the powder mixture. (g1-g3) Experimental set-up of the DED fabrication process. (h) Graphic representation of the as-built samples showing the sample dimension, scanning strategies, and coordinate axes as well as the geometry of the samples for tensile tests.
Commercial pre-alloyed 15-5PH (Fe-0.022C-15.41Cr-4.61Ni-0.83Mn-0.31Nb-3.74Cu-0.39Si, in wt.%) SS powders (45–105 μm, supplied by VILORY Co. Ltd., China) manufactured by the gas atomization method were used as the matrix feedstock material ((a)). Considering the strong agglomeration of the nano-sized particles, micron-sized TiB2 (4–8 μm), TiN (2–8 μm), WC (2–5 μm) and TiC (2–4 μm) ceramic particles (supplied by Shanghai Macklin Biochemical Co., Ltd., China) were used as reinforcing agents ((b–e)). Four different MMC systems containing 2 wt.% TiB2, 2 wt.% TiN, 2 wt.% WC and 2 wt.% TiC ceramic particles, respectively, were blended using a three-dimensional mixer ((f)) at 30 rpm for 4 h in an inert gas atmosphere. As shown in (g), DED experiments were conducted using a coaxial powder feed laser cladding system equipped with a 10,000 W Yitterbium laser system (YLS-10000) and powder delivery system. 18-layered MMC cubic-shaped samples with each layer thickness of ∼0.87 mm were printed using a scanning rate of 5 mm/s, laser power of 1,300 W, powder feed rate of 0.25 g/s, the spot diameter of 4 mm, inter-layer idle time of 15 s, and hatch distance of 2.12 mm.
The as-built 15-5PH and MMCs specimens were sectioned to observe the microstructure perpendicular to the building direction (BD, y-z plane). The microstructure was investigated by a Tecnai G2 F30 transmission electron microscopy (TEM) and a Zeiss Sigma 300 SEM equipped with energy dispersive spectroscopy (EDS) and Bruker e-FlashFS electron backscattered diffraction (EBSD). The TEM foils were prepared by mechanically grinding, punching and further thinning using a precision ion polishing system (PIPS II, Gatan 695). For the EBSD observation, the mechanically polished specimens were electro-polished in a solution of HClO4 (∼6 vol.%) and C2H6O (∼94 vol.%) with a direct voltage of 25 V for 30 s. The phases presented in the as-built samples were identified using a Bruker D8 Advance X-ray diffractometer (XRD) with Cu-Kα radiation. The volume fraction of RA was determined using the following equation (Fan et al. Citation2017):
(1)
(1) where Vα (Iα) and Vγ (Iγ) are the volume fraction (integrated intensities) of martensite ((110) peak) and RA ((111) peak), respectively.
The mechanical properties of the DED-processed specimens were studied by the room-temperature tensile tests, and the dog bone-shaped specimens as per ASTM E8/E8M-11 standard are shown in (h). Each tensile test was performed at least three times under the same conditions. A digital image correlation (DIC) system was used to study deformation behaviours during uniaxial tension testing. According to the ASTM G3-14 standard, electrochemical impedance spectroscopy (EIS) and potentiodynamic polarisation tests (PPTs) were performed using an electrochemical workstation (GAMRY-Interface 1000) to evaluate the corrosion resistance of 15-5PH and MMCs in the as-built condition. Approximately 10 × 10 mm2 area was exposed to the corrosion solution. Before the electrochemical measurements, the specimens were firstly mechanically ground and then polished with 2.5 μm diamond spray. The PPTs were performed at the scan speed of 0.1667 mV/s with the potential range of −0.5 V (vs. open-circuit potential) to 1 V. EIS tests were conducted at the frequency range of 100 kHz to 10 mHz with a sinusoidal voltage of 10 mV. All electrochemical tests were conducted in naturally-aerated 3.5 wt.% NaCl solution and the results of each type of sample were averaged based on three parallel samples. The macro-morphologies of the specimens after PPT tests were observed using a super depth of field microscope (ZEISS, SmartZoom5).
3. Results and discussion
During the DED process, uncontrolled metallurgical defects, coarse columnar grains, and scattered and unsatisfactory material performance are three important problems (Cai et al. Citation2019b; Chen et al. Citation2021; Gu et al. Citation2015; Song et al. Citation2013). Thus, it is important to highlight the influential role of ceramic particles in controlling metallurgical defects and minimising columnar grains in as-built parts to achieve desired mechanical properties (e.g. strength-ductility synergy) and corrosion resistance. Moreover, considering the remarkable effects of microstructure on material performance, it is thus necessary to have an in-depth understanding of complicated microstructure evolution induced by different ceramic particles to increase the confidence in tailoring the microstructure, and thereby the performance of MMCs.
3.1. Microstructural analysis
3.1.1. Sem microstructure
displays the cross-sectional (y-z plane) microstructure perpendicular to BD for the 15-5PH specimen and MMCs. Epitaxial columnar grains following the prevailing heat flow direction exist inside the as-built 15-5PH specimen ((a)), which is the typical solidified structure of the AM-processed specimens (Bermingham et al. Citation2019). As shown in (b–d), the columnar grains in WC, TiC and TiN composites become shorter and narrower, and no obvious interlayer pores or cracks exist inside these specimens. From (f), significant elemental segregation of Cr can be observed in the TiN composite. With the addition of the TiB2 particulates, macroscopic cracks with several millimeters in length and considerable micro-cracks can be observed ((e)), which can be ascribed to the reduced ductility in TiB2 composite. Moreover, the TiB2 reinforcements were tightly aggregated, and a series of highly homogeneous ring-structured reinforcement with a mean internal diameter of ∼15 μm and a thickness of ∼1.4 μm was formed. The formation of ring-structured reinforcement can be attributed to the particle accumulation structure (PAS) mechanism (Jiang et al. Citation2021a; Xi et al. Citation2020). In the PAS mechanism, particles at a dilute concentration flow in the oscillatory ring vortex, and previously uniformly distributed particles form loose agglomerations circulating under this vortex, thus resulting in the formation of the discontinuous ring structure. Previous reports (AlMangour et al. Citation2019; Asta et al. Citation2009; Xi et al. Citation2020) suggest that the Cr, Ni and Mo elements can precipitate at the ring-structure boundaries under the combined action of Marangoni convection and PAS mechanism. Further EDS mapping analysis ((g)) confirmed the elemental segregation of Cr, Ni, Mo, and Nb along the ring-structure boundaries, and a nearly identical result (elemental segregation of Cr, Ni, and Mo) was also observed by AlMangour et al. (Citation2019) in 316L/TiB2 composite.
3.1.2. Ebsd microstructure
presents the low-magnification EBSD maps (288.1 × 216.1 μm2) for 15-5PH and MMCs. In the 15-5PH specimen, a relatively strong texture with a texture index of 3.74 can be observed in the columnar grains of and . The martensite blocks with an average size of 17.4 μm dominated the microstructure and were accompanied by a small amount of retained austenite (RA; 3.9% by EBSD, and 6.9% by XRD), as shown in and . With the addition of the TiB2 and TiN particulates, the strong texture in the 15-5PH specimen diminishes and becomes more random with the texture index of 1.27 for TiB2 composite and 1.86 for TiN composite ((b, c)). Moreover, the martensite block size in TiB2 and TiN composites is decreased to 7.98 and 11 μm ((b, c)), respectively. However, there is no remarkable change of the RA in TiB2 and TiN composites (). Interestingly, the addition of WC particles leads to substantially refined martensitic grains and a dramatic increase in RA (19.8% by EBSD, and 18.5% by XRD). The relatively uniform distribution of RA and negligible diffraction peaks corresponding to WC indicate the homogeneous dispersion and complete dissolution of raw WC powders within the matrix during the DED process. The C element can act as a strong austenite stabiliser (Jiang et al. Citation2021b), hence, the dissolution of WC particles can account for the large area formation of RA. As expected, a significantly increased proportion of RA (63.5% by EBSD, and 62.7% by XRD) can be observed in the TiC composite due to the higher TiC volume content at the same weight as WC. Similar results were also observed by Jiang et al. (Citation2021b) in SLMed 15-5PH/graphene composites. Meanwhile, significant coarsening of RA (26.7 μm) can be observed with the introduction of TiC particles ((e)). According to Chen et al. (Citation2021) and Vasilyev et al. (Citation2011), the increase of C content in the matrix can reduce the self-diffusion activation energy of the Fe atom in austenite, which facilitates the formation and migration of vacancies, thus resulting in the coarsening of RA.
Figure 3. Orientation, and phase maps of the (a) 15-5PH specimen and composites reinforced with (b) TiB2, (c) TiN, (d) WC, and (e) TiC ceramic particles.
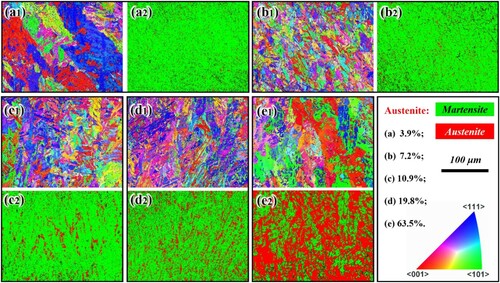
Figure 4. Inverse pole figures (IPFs) of martensite grains in the (a) 15-5PH specimen and MMCs reinforced with (b) TiB2 and (c) TiN ceramic particles.
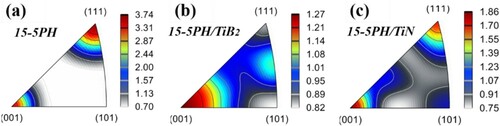
3.1.3. Tem microstructure
Further TEM observations on the as-built MMCs are provided in . Note that, no complete ceramic particles can be observed in all MMCs by the TEM observations. As can be seen in (a), a high density of plate-shaped Cr-based precipitates were continuously aligned along grain boundaries (GBs) in the TiB2 composite, which can account for the Cr element segregation observed in (g). According to the corresponding selected area electron diffraction (SAED), the Cr-based precipitates can be identified as C14 type (hexagonal close-packed, HCP) Laves precipitates (Cao et al. Citation2017; Chai et al. Citation2020). The dominant factor for the formation of C14 laves precipitates is the Cr content due to its stabilising effect on the C14 structure (Cao et al. Citation2017; Chai et al. Citation2020). High Nb and Mo element diffusion along ring-structure boundaries can further promote the growth of Laves precipitates along the GBs and lead to a continuous morphology (Chai et al. Citation2020). Note that some ferrite grains can be observed in TiB2 and TiN composites ((a, b)), which can be ascribed to the Cr element segregation because the Cr element can act as a strong ferrite stabiliser (Ooi, Garnham, and Ramjaun Citation2014). In the WC composite, dislocation networks can be observed in RA ((c)), which are believed to be formed owing to the rapid solidification of the specimen (Lin et al. Citation2020). For the TiC composite, a considerable amount of nano-scale (Nb,Ti)C particles with FCC structure and uniform size of 10–30 nm were uniformly distributed in the matrix ((d)). The massive formation of (Nb,Ti)C particles may result from the degradation of micro-sized TiC particles, and the degraded TiC particles can act as a nucleation centre for (Nb,Ti)C carbide (Li, Lei, and Fu Citation2014). Moreover, massive nano-twins with a twin thickness of approximately 10–40 nm can be observed in (d), which can affect the deformation behaviour (Tan et al. Citation2021a). The corresponding SAED reveals a bcc {112}<111 > twinning substructure, which is commonly observed in martensitic steels with a wide range of C content (Sun et al. Citation2018; Sun et al. Citation2020). According to Sun et al. (Citation2020), the twinned substructure within lath martensite becomes more significant with the increase of C content. Nano-twins were also observed by Tan et al. (Citation2021a) in heat-treated high-carbon martensite steel (AISI 420), hence, the formation of massive nan-twins in TiC composite was presumably due to the combined effect of increased C content in martensite and intrinsic heat treatment effect induced by the subsequent build layer.
Figure 7. The TEM images of MMCs in as-built condition: Bright-field (BF) TEM images and the corresponding SAED of (a1, a2) Cr-based Laves precipitates and (a3, a4) ferrite phase in TiB2 composite, as well as the (b1, b2) ferrite phase in TiN composite; (c1, c2) Retained austenite phase in WC composite; (d1) Nanoscale (Nb,Ti)C precipitates distributed in TiC composite, and the (d2) corresponding HRTEM (the inset shows the fast Fourier transform pattern of (Nb,Ti)C precipitate); (d3) BF TEM image of nano-twins formed in the TiC composite, and the (d4) corresponding SAED pattern.
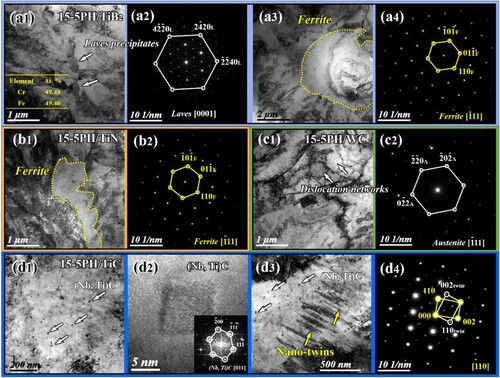
3.2. Mechanical properties analysis
Tensile tests were performed to investigate the effect of different ceramic particles on the mechanical properties of 15-5PH SS matrix composites in the as-built condition (). displays the fracture morphology of the composites. The unreinforced 15-5PH specimen exhibits an ultimate tensile strength (UTS) of 1121 ± 31 MPa and a relatively low fracture strain of 4.2 ± 2.3%. From (b), the strain hardening rate of the 15-5PH specimen decreases all the way to the final necking. The DIC strain maps of the 15-5PH specimen exhibit non-uniform strain localisation throughout the gage section ((a)). The TiB2 composite shows worse tensile properties which can be ascribed to the inherent brittleness of TiB2 reinforcements and massive macro-/micro-cracks inside the microstructure. As shown in (a), the TiB2 composite exhibits prevalent intergranular fracture along the boundary of the ring structure without dimples and quasi-cleavage fracture features. Despite significant grain refinement in TiB2 composite, the simultaneous sacrifice of strength and ductility makes TiB2 particles unsuitable for the 15-5PH SS reinforcement. The TiN composite achieves a UTS of 1213 ± 24 MPa and an elongation (EI) of 9.4 ± 1.3% and shows mainly a ductile fractured surface with the massive presence of fine dimples ((b)). According to Gu et al. (Citation2015) and Qi et al. (Citation2021), grain refinement is an effective method for achieving the simultaneous enhancement of strength and ductility, hence, the mechanical performance improvement of TiN composite can be attributed to the substantial grain refinement. The TiC composite shows stronger UTS (1372 ± 35 MPa) and simultaneously more superior plasticity (EI of 16.4 ± 1.7%), which overcomes the trade-off between strength and ductility. As shown in , the exceptional combination of strength and ductility achieved in TiC composite exceeds previously reported tensile properties of as-built and even heat-treated AM-processed 15-5PH SS (Alafaghani et al. Citation2019; Chae et al. Citation2019; Nong et al. Citation2020; Nong et al. Citation2021). From (b), the strain hardening rate of the WC composite rapidly decreases first, which is followed by an increase at about 0.01 strain, and then, drops again at about 0.0513 strain to the final necking. The progressive transformation from the metastable RA to martensite during straining (also known as the transformation-induced plasticity, TRIP) can contribute to the enhanced strain hardening as long as the newly transformed martensite remains elastic (Wu et al. Citation2016). The significantly enhanced work hardening capacity (∼920 MPa, see (a)) is advantageous in specific structural applications to ensure a large margin of safety before fracture (Easton and StJohn Citation2001). The DIC strain maps of the TiC composite show a relatively uniform strain distribution in comparison with the pure 15-5PH specimen, which leads to the long-range internal strain, thus delaying fracture and improving ductility. A similar DIC measurement result was also observed by Yang et al. (Citation2021) in medium entropy alloy. As shown in (d), the fracture morphology of the TiC composite exhibits a mixed-fracture mode including ductile-fracture portions and brittle-fracture zones characterised by quasi-cleavage and intergranular fractures. The intergranular fracture can be implied to occur along the boundaries of RA ((c)), and a similar result was also observed by Han et al. (Citation2017). Moreover, the formation of nano-twins ((c)) can trigger the twinning-induced plasticity (TWIP), which enhances the deformation homogeneity and postpones necking, thus resulting in increased EI. The dislocation pinning by nano-scale (Nb,Ti)C particles in the matrix can contribute to the higher UTS of TiC MMC. The WC composite shows high strength with UTS of 1295 ± 31 MPa and high ductility with EI of 12.1 ± 1.6%, which is much superior to the conventionally AM-processed 15-5PH SS (). The corresponding fracture surface ((d)) exhibits a typical ductile-type failure, with the presence of the dimple network. As revealed by EBSD ((b)), most of the RA grains in the WC composite were directly transformed to martensite after tensile deformation, and only 6.4% untransformed austenite can be detected. The TRIP effect provides not only enhanced work hardening capacity in a broad range of external loads during straining but also exceptional plasticity, which can explain the ductility enhancement of WC composite. The grain refinement is the primary contributor to the enhanced strength of the WC composite.
Figure 8. The representative (a) tensile stress-strain curves and the corresponding (b) strain-hardening rates of 15-5PH and composites in the as-built condition.
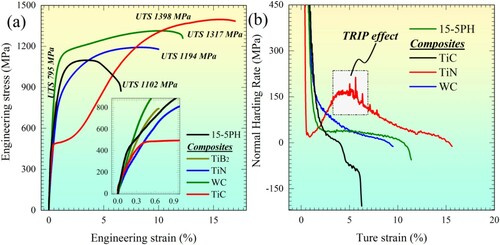
Figure 11. The achieved tensile properties of DED-processed 15-5PH and composites in our work compared with those of AM-processed 15-5PH SS in both as-built and heat-treated conditions (Alafaghani et al. Citation2019; Chae et al. Citation2019; Nong et al. Citation2020; Nong et al. Citation2021)
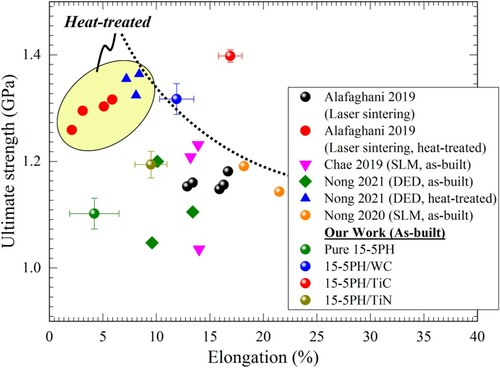
Figure 9. Typical fracture morphology of the MMCs reinforced with (a) TiB2, (b) TiN, (c) TiC, and (d) WC ceramic particles.
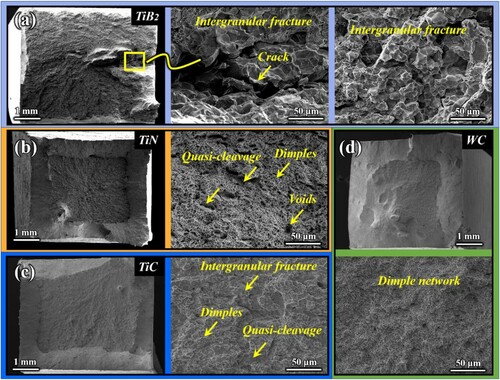
3.4 Electrochemical performance
The pitting corrosion resistance of the 15-5PH and composites in the as-built condition was measured by PPTs in naturally-aerated 3.5 wt.% NaCl solution, as shown in (a). All relevant corrosion parameters derived from the PPT plots are outlined in . The TiN and TiB2 composites exhibit lower corrosion potential (Ecorr) values (−283.5 and −314.2 mV, respectively) as compared to that of the 15-5PH specimen (−223.9 mV), and the corrosion current density (Icorr) of the TiB2 composite is the lowest (3.57 × 10−7 A/cm2), indicating a higher corrosion tendency. In comparison, the WC and TiC composites reveal increased Ecorr values (−173.6 and −95.5 mV, respectively). The pitting potential (Epit) was defined as the potential at which the specimen surface current density exceeded 1 × 10−4 A/cm2 (Lu et al. Citation2015; Pao, Muto, and Sugawara Citation2021; Wei et al. Citation2020). As shown in (a), the TiB2, TiN, WC composites and 15-5PH specimens exhibit a rapid increase in current density when the polarisation potential exceeds the Ecorr. From (a–d), the surfaces of TiB2, TiN, WC composites and 15-5PH specimen after PPTs were severely corroded with considerable corrosion pits seen by naked eyes. These results demonstrate the ‘loss of passivation’ (LOP) and deterioration of pitting corrosion resistance in these specimens, and a similar phenomenon in Cr-13 type martensite SS was also observed by Lu et al. (Citation2015) and Wei et al. (Citation2020). Interestingly, the TiC composite displays an obvious passivation region before pitting, where the current density remains nearly constant with the increase of polarisation potential ((a)), and no visible change occurs on its surface after PPT ((e)). The results indicate that the corrosion resistance will be substantially enhanced for TiC composite.
Figure 13. Results from electrochemical tests: (a) PPT and (b) Nyquist plots (the inset shows the equivalent circuit (Wei et al. Citation2020)).
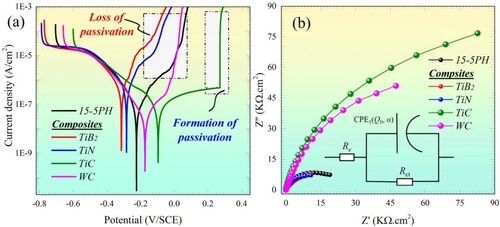
Figure 14. The macro-morphologies of the whole corrosive area after PPTs (note that: the PPTs were terminated until the current density of the specimen surface reaches 120 mA/cm2) in (a) 15-5PH specimen and composites reinforced with (b) TiB2, (c) TiN, (d) WC and (e) TiC ceramic particles.
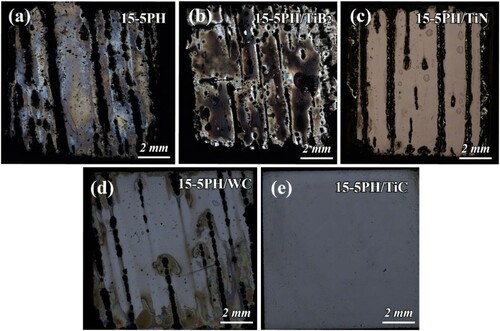
Table 1. The corrosion parameters derived from the PPT plots of all the specimens.
(b) presents the Nyquist plots 15-5PH and composites at Ecorr. The corresponding fitted parameters derived from the EIS spectra are outlined in . The EIS spectra of all specimens show a single capacitive in the high-medium frequency range. The arc diameters of TiB2, TiN composites and 15-5PH specimen are much lower than WC and TiC composites, and the TiC composite exhibits the maximum arc diameter ((b)). The equivalent circuit (R(QR)) proposed by El-Egamy and Badaway (Citation2004) is applied to simulate the EIS behaviour (the inset in (b)). In this circuit, Re and Rct represent the solution and charge transfer resistances, respectively. CPE is the constant phase element describing the dispersion behaviour, and the impedance of CPE(ZCPE) can be expressed as (Wei et al. Citation2020; Lu et al. Citation2015):
(2)
(2) where ω (rad/s) and j (j2 = −1) are the angular frequency and imaginary number, respectively. Q and α are the admittance value and fitted exponential of CPE, respectively (Luo et al. Citation2012).
Table 2. Fitted parameters of the EIS measurements.
According to Marcelin, Pébère, and Régnier (Citation2013) and Hirschorn et al. (Citation2010), the Q0 value is inversely proportional to the passive film thickness, and the Rct value can be used to evaluate the passive film stability. In comparison to the 15-5PH specimen, the WC composite shows decreased Q0 value and increased Rct value (see ), indicating improved stability of the passive film. According to the theories of Irani and Ghazani (Citation2020) and Wang et al. (Citation2019), the massive presence of RA and grain refinement can account for the enhanced electrochemical performance of WC composite. The Q0 value of TiB2 and TiN composites increases by one order of magnitude than the 15-5PH specimen, and their Rct value is relatively low, indicating the deterioration of passive films. Consequently, the TiB2 and TiN composites will be severely corroded in the Cl- containing environments. The deterioration of corrosion resistance in TiB2 and TiN composites can be attributed to the significant elemental segregation of Cr ((f, g)). In comparison, the Q0 value of the TiC composite is lower, and its Rct value is higher than other specimens, suggesting that the addition of TiC particles promotes the formation of the more protective and well-structured passive film and similar results were also observed by Xu et al. (Citation2018) and Zhang et al. (Citation2019). In addition to the great contribution from the larger area formation of RA, the formation of nano-sized (Nb,Ti)C particles and structure/composition change of passive film may be important factors that account for the improved corrosion resistance of TiC composite. These factors will be experimentally investigated in our future work by using focused ion beam (FIB), X-ray photoelectron spectroscopy (XPS), TEM, HRTEM and scanning Kelvin probe force microscopy (SKPFM).
4. Conclusions
In this paper, four different 15-5PH SS matrix composites with the reinforcements of TiB2, TiN, WC and TiC, respectively, were fabricated via DED. The influences of different ceramic particles on the microstructure evolution, mechanical properties and corrosion resistance of MMCs were analyzed. The main conclusions can be drawn as follows:
The addition of 2 wt.% TiB2 particles lead to significant grain refinement, however, show poor fracture strength and elongation due to increased brittleness of metal matrix. Moreover, significant elemental segregation of Cr along the ring-structure boundaries in TiB2 composite leads to the LOP and deterioration of corrosion resistance.
The simultaneous enhancement of strength and ductility was achieved in TiN composite due to grain refinement. However, the addition of TiN particles leads to deterioration of corrosion resistance due to the Cr element segregation.
A high UTS of 1261 ± 31 MPa and an EI of 12.1 ± 1.6% was achieved in the WC composite, which is much superior to the commercial 15-5PH SS. The improved strength and EI after WC addition can be attributed to grain refinement and progressive TRIP effect, respectively, while enhanced corrosion resistance correlates to the refined grains and large area formation of RA.
The TiC composite shows an excellent combination of high UTS of 1372 ± 35 MPa, high EI of 16.4 ± 1.7%, well surpassing the commercial 15-5PH SS. The improved strength was expected from the refined lath martensite and abundant nucleation of nanoscale (Nb,Ti)C particles, and high EI was associated with the combined action of TRIP and TWIP effects. Moreover, PPT and EIS results confirmed the excellent electrochemical performance of the TiC composite against localised corrosion attacks.
In summary, the addition of TiN, WC and TiC particles can effectively overcome the strength-ductility trade-off in martensitic SS. Moreover, the corrosion resistance of martensitic SS can be simultaneously enhanced by the addition of WC or TiC particles. Thus, TiC and WC ceramic particles are potential candidate reinforcements for martensitic SS. Further research will be conducted on the precipitation behaviour and post-processing heat treatments response of the WC and TiC MMCs.
Acknowledgments
The authors appreciate the financial support from the Project of the National Natural Science Foundation of China (Grant numbers: 52025052, 51975405).
Disclosure statement
No potential conflict of interest was reported by the author(s).
Additional information
Funding
Notes on contributors
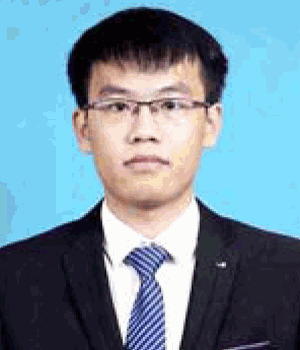
Wei Chen
Wei Chen PhD candidate, School of Materials Science and Engineering, Tianjin University. He is engaged in the research of microstructure and mechanical properties of martensitic stainless steel additive manufacturing.
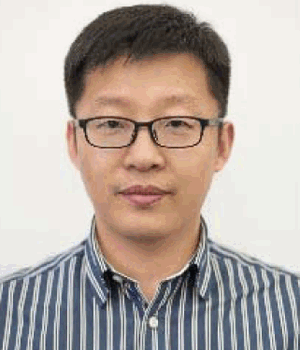
Lianyong Xu
Lianyong Xu Ph.D., Professor of School of Materials Engineering and Science, Tianjin University. He has been committed to the frontier research of welding structural mechanics and structural design, and has been engaged in the basic theory and application technology research of welding structural strength and life design, defect assessment and life assessment, additive manufacturing and other aspects.

Yankun Zhang
Yankun Zhang PhD candidate, School of Materials Science and Engineering, Tianjin University. He is engaged in the research of microstructure and mechanical properties of shape memory alloy additive manufacturing.
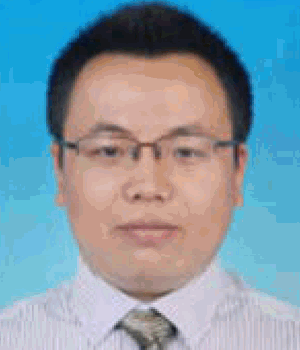
Yongdian Han
Yongdian Han Ph.D., Professor of School of Materials Engineering and Science, Tianjin University. He is engaged in the research of material, process and property evaluation (fatigue, fracture, corrosion, etc.) of new high entropy alloy, stainless steel and shape memory alloy based on additive manufacturing methods such as laser selective melting and laser cladding.

Lei Zhao
Lei Zhao Ph.D., Associate Professor of School of Materials Engineering and Science, Tianjin University. His research fields include welding stress and deformation control, high-temperature creep/fatigue behavior and mechanism of energy structures, integrity and life evaluation of high-temperature welded structures, performance and reliability evaluation of 3D printing/additive manufacturing, etc.

Hongyang Jing
Hongyang Jing Ph.D., Professor of School of Materials Engineering and Science, Tianjin University. He is engaged in high-temperature strength life design and evaluation research of welded structures under extreme environmental conditions and research on additive manufacturing principle and technology of new ultra-high temperature alloys, stainless steels and structural parts based on laser selective melting and laser cladding.
References
- Alafaghani, A., A. Qattawi, M. Jaman, and M. A. Ablat. 2019. “Microstructure and Mechanical Properties of Direct Metal Laser–Sintered 15-5PH Steel with Different Solution Annealing Heat Treatments.” The International Journal of Advanced Manufacturing Technology 105: 3499–3520.
- AlMangour, B., Y. K. Kim, D. Grzesiak, and K. A. Lee. 2019. “Novel TiB2-Reinforced 316L Stainless Steel Nanocomposites with Excellent Room- and High-Temperature Yield Strength Developed by Additive Manufacturing.” Composites Part B: Engineering 156: 51–63.
- Asta, M., C. Beckeermann, A. Karma, W. Kurz, R. Napolitano, M. Plapp, G. Purdy, M. Rappaz, and R. Trivedi. 2009. “Solidification Microstructures and Solid-State Parallels: Recent Developments, Future Directions.” Acta Materialia 57: 941–971.
- Bermingham, M. J., D. H. StJohn, J. Krynen, S. T. Jones, and M. S. Dargush. 2019. “Promoting the Columnar to Equiaxed Transition and Grain Refinement of Titanium Alloys During Additive Manufacturing.” Acta Materialia 168: 261–274.
- Cai, C., S. He, L. Li, Q. Teng, B. Song, C. Yan, Q. Wei, and Y. Shi. 2019a. “In-situ TiB/Ti-6Al-4V Composites with a Tailored Architecture Produced by hot Isostatic Pressing: Microstructure Evolution, Enhanced Tensile Properties and Strengthening Mechanisms.” Composites Part B: Engineering 164: 546–558.
- Cai, C., C. Radoslaw, J. Zhang, Q. Yan, S. Wen, B. Song, and Y. Shi. 2019b. “In-situ Preparation and Formation of TiB/Ti-6Al-4V Nanocomposite via Laser Additive Manufacturing: Microstructure Evolution and Tribological Behavior.” Powder Technology 342: 73–84.
- Cao, G., Y. Yun, L. Yang, G. Yuan, Q. Yue, G. Shao, and J. Hu. 2017. “The Formation and Stacking Faults of Fe and Cr Containing Laves Phase in Zircaloy-4 Alloy.” Materials Letters 191: 203–205.
- Chae, H., E. Huang, J. Jain, H. Wang, W. Woo, S. Chen, S. Harjo, T. Kawasaki, and S. Y. Lee. 2019. “Plastic Anisotropy and Deformation-Induced Phase Transformation of Additive Manufactured Stainless Steel.” Materials Science and Engineering: A 762: 138065.
- Chai, Y. W., K. Kato, C. Yabu, S. Ishikawa, and Y. Kimura. 2020. “Disconnections and Laves (C14) Precipitation in High-Cr Ferritic Stainless Steels.” Acta Materialia 198: 230–241.
- Chen, H., D. Gu, K. Kosiba, T. Lu, L. Deng, L. Xi, and U. Kühn. 2020. “Achieving High Strength and High Ductility in WC-Reinforced Iron-Based Composites by Laser Additive Manufacturing.” Additive Manufacturing 35: 101195.
- Chen, W., L. Xu, Y. Han, L. Zhao, and H. Jing. 2021. “Control of Residual Stress in Metal Additive Manufacturing by low-Temperature Solid-State Phase Transformation: An Experimental and Numerical Study.” Additive Manufacturing 42: 102016.
- Dong, B., Q. Li, Z. Wang, T. Liu, H. Yang, S. Shu, L. Chen, F. Qiu, Q. Jiang, and L. Zhang. 2021. “Enhancing Strength-Ductility Synergy and Mechanisms of Al-Based Composites by Size-Tunable in-Situ TiB2 Particles with Specific Spatial Distribution.” Composites Part B: Engineering 217: 108912.
- Easton, M. A., and D. H. StJohn. 2001. “A Model of Grain Refinement Incorporating Alloy Constitution and Potency of Heterogeneous Nucleant Particles.” Acta Materialia 49: 1867–1878.
- El-Egamy, S. S., and W. A. Badaway. 2004. “Passivity and Passivity Breakdown of 304 Stainless Steel in Alkaline Sodium Sulphate Solutions.” Journal of Applied Electrochemistry 34: 1153–1158.
- Fan, Z., Y. Wang, Y. Zhang, T. Qin, X. Zhou, G. Thompson, T. Pennycook, and T. Hashimoto. 2015. “Grain Refining Mechanism in the Al/Al–Ti–B System.” Acta Materialia 84: 292–304.
- Fan, Y. H., B. Zhang, H. L. Yi, G. S. Hao, Y. Y. Sun, J. Q. Wang, E. Han, and W. Ke. 2017. “The Role of Reversed Austenite in Hydrogen Embrittlement Fracture of S41500 Martensitic Stainless Steel.” Acta Materialia 139: 188–195.
- Gu, D., X. Shi, R. Poprawe, D. L. Bourell, R. Setchi, and J. Zhou. 2021. “Material-structure-performance Integrated Laser-Metal Additive Manufacturing.” Science 372, eabg1487.
- Gu, D., H. Wang, D. Dai, P. Yuan, W. Meiners, and R. Poprawe. 2015. “Rapid Fabrication of Al-Based Bulk-Form Nanocomposites with Novel Reinforcement and Enhanced Performance by Selective Laser Melting.” Scripta Materialia 96: 25–28.
- Gu, D., and G. Zhang. 2013. “Selective Laser Melting of Novel Nanocomposites Parts with Enhanced Tribological Performance.” Virtual and Physical Prototyping 8: 11–18.
- Han, J., A. K. D. Silva, D. Ponge, D. Raabe, S. M. Lee, Y. K. Lee, S. I. Lee, and B. Hwang. 2017. “The Effects of Prior Austenite Grain Boundaries and Microstructural Morphology on the Impact Toughness of Intercritically Annealed Medium Mn Steel.” Acta Materialia 122: 199–206.
- Hirschorn, B., M. E. Orazem, B. Tribollet, V. Vivier, I. Frateur, and M. Musiani. 2010. “Determination of Effective Capacitance and Film Thickness from Constant-Phase-Element Parameters.” Electrochimica Acta 55: 6218–6227.
- Irani, H., and M. S. Ghazani. 2020. “Effect of Grain Refinement on Tensile Properties and Electrochemical Behavior of Fe-18.5%Cr Ferritic Stainless Steel.” Materials Chemistry and Physics 251: 123089.
- Jiang, J., S. T. Newman, and R. Y. Zhong. 2021a. “A Review of Multiple Degrees of Freedom for Additive Manufacturing Machines.” International Journal of Computer Integrated Manufacturing 34: 195–211.
- Jiang, J., X. Zhang, F. Ma, S. Dong, W. Yang, M. Wu, G. Chang, L. Xu, C. Zhang, and F. Luo. 2021b. “Novel Phenomena of Graphene Secondary Dispersion and Phase Transformation in Selective Laser Melting of 15-5PH/Graphene Composites.” Additive Manufacturing 47: 102207.
- Li, Q., Y. Lei, and H. Fu. 2014. “Growth Mechanism, Distribution Characteristics and Reinforcing Behavior of (Ti, Nb)C Particle in Laser Cladded Fe-Based Composite Coating.” Applied Surface Science 316: 610–616.
- Li, B., L. Zhang, Y. Xu, Z. Liu, B. Qian, and F. Xuan. 2020. “Selective Laser Melting of CoCrFeNiMn High Entropy Alloy Powder Modified with Nano-TiN Particles for Additive Manufacturing and Strength Enhancement: Process, Particle Behavior and Effects.” Powder Technology 360: 509–521.
- Lin, D., L. Xu, H. Jing, Y. Han, L. Zhao, Y. Zhang, and H. Li. 2020. “A Strong, Ductile, High-Entropy FeCoCrNi Alloy with Fine Grains Fabricated via Additive Manufacturing and a Single Cold Deformation and Annealing Cycle.” Additive Manufacturing 36: 101591.
- Lu, S. Y., K. F. Yao, Y. B. Chen, M. H. Wang, X. Liu, and X. Ge. 2015. “The Effect of Tempering Temperature on the Microstructure and Electrochemical Properties of a 13wt.% Cr-Type Martensitic Stainless Steel.” Electrochimica Acta 165: 45–55.
- Luo, H., C. F. Dong, X. G. Li, and K. Xiao. 2012. “The Electrochemical Behaviour of 2205 Duplex Stainless Steel in Alkaline Solutions with Different pH in the Presence of Chloride.” Electrochimica Acta 64: 211–220.
- Marcelin, S., N. Pébère, and S. Régnier. 2013. “Electrochemical Characterisation of a Martensitic Stainless Steel in a Neutral Chloride Solution.” Electrochimica Acta 87: 32–40.
- Nong, X., X. Zhou, J. Li, Y. Wang, Y. Zhao, and M. Brochu. 2020. “Selective Laser Melting and Heat Treatment of Precipitation Hardening Stainless Steel with a Refined Microstructure and Excellent Mechanical Properties.” Scripta Materialia 178: 7–12.
- Nong, X., X. Zhou, Y. Wang, L. Yu, and J. Li. 2021. “Effects of Geometry, Location, and Direction on Microstructure and Mechanical Properties of 15–5PH Stainless Steel Fabricated by Directed Energy Deposition.” Materials Science and Engineering: A 821: 141587.
- Ooi, S. W., J. E. Garnham, and T. I. Ramjaun. 2014. “Review: Low Transformation Temperature Weld Filler for Tensile Residual Stress Reduction.” Materials & Design (1980-2015) 56: 773–781.
- Pao, L., I. Muto, and Y. Sugawara. 2021. “Pitting at Inclusions of the Equiatomic CoCrFeMnNi Alloy and Improving Corrosion Resistance by Potentiodynamic Polarization in H2SO4.” Corrosion Science 191: 109748.
- Pelleg, J. 1999. “Reactions in the Matrix and Interface of the Fe–SiC Metal Matrix Composite System.” Materials Science and Engineering: A 269: 225–241.
- Qi, Y., Z. Hu, H. Zhang, X. Nie, C. Zhang, and H. Zhu. 2021. “High Strength Al-Li Alloy Development for Laser Powder bed Fusion.” Additive Manufacturing 47: 102249.
- Song, B., S. Dong, and C. Coddet. 2014. “Rapid in Situ Fabrication of Fe/SiC Bulk Nanocomposites by Selective Laser Melting Directly from a Mixed Powder of Microsized Fe and SiC.” Scripta Materialia 75: 90–93.
- Song, B., S. Dong, P. Coddet, G. Zhou, S. Ouyang, H. Liao, and C. Coddet. 2013. “Microstructure and Tensile Behavior of Hybrid Nano-Micro SiC Reinforced Iron Matrix Composites Produced by Selective Laser Melting.” Journal of Alloys and Compounds 579: 415–421.
- Song, B., Z. Wang, Q. Yan, Y. Zhang, J. Zhang, C. Cai, Q. Wei, and Y. Shi. 2017. “Integral Method of Preparation and Fabrication of Metal Matrix Composite: Selective Laser Melting of in-situ Nano/submicro-sized Carbides Reinforced Iron Matrix Composites.” 707: 478–487.
- Sun, J., T. Jiang, Y. Wang, S. Guo, and Y. Liu. 2018. “Effect of Grain Refinement on High-Carbon Martensite Transformation and its Mechanical Properties.” Materials Science and Engineering: A 726: 342–349. doi:https://doi.org/10.1016/j.msea.2018.04.098
- Sun, H., Y. Wang, Z. Wang, N. Liu, Y. Peng, X. Zhao, R. Ren, and H. Zhang. 2020. “Twinned Substructure in Lath Martensite of Water Quenched Fe-0.2 %C and Fe-0.8 %C Steels.” Journal of Materials Science & Technology 49: 126–132.
- Tan, C., Y. Chew, F. Weng, S. Sui, Z. Du, F. L. Ng, and G. Bi. 2021a. “Superior Strength-Ductility in Laser Aided Additive Manufactured High-Strength Steel by Combination of Intrinsic Tempering and Heat Treatment.” Virtual and Physical Prototyping 16: 318–332.
- Tan, C., F. Weng, S. Sui, Y. Chew, and G. Bi. 2021b. “Progress and Perspectives in Laser Additive Manufacturing of key Aeroengine Materials.” International Journal of Machine Tools and Manufacture 170: 103804.
- Tan, C., K. Zhou, W. Ma, and D. Zeng. 2020. “Research Progress of Laser Additive Manufacturing of Maraging Steels.” Acta Metallurgica Sinica 56: 36–52.
- Vasilyev, A., S. Sokolov, N. Kolbasnikov, and D. Sokolov. 2011. “Effect of Alloying on the Self-Diffusion Activation Energy in γ-Iron.” Physics of the Solid State 53: 2194–2200.
- Wang, L., C. Dong, J. Yao, Z. Dai, C. Man, Y. Yin, K. Xiao, and X. Li. 2019. “The Effect of ɳ-Ni3Ti Precipitates and Reversed Austenite on the Passive Film Stability of Nickel-Rich Custom 465 Steel.” Corrosion Science 154: 178–190.
- Wang, Y. M., T. Voisin, J. T. McKeown, J. Ye, N. P. Calta, et al. 2018. “Additively Manufactured Hierarchical Stainless Steels with High Strength and Ductility.” Nature Materials 17: 63–71.
- Wei, G., S. Lu, S. Li, K. Yao, H. Luan, and X. Fang. 2020. “Unmasking of the Temperature Window and Mechanism for “Loss of Passivation” Effect of a Cr-13 Type Martensite Stainless Steel.” Corrosion Science 177: 108951.
- Wu, X. L., M. X. Yang, F. P. Yuan, L. Chen, and Y. T. Zhu. 2016. “Combining Gradient Structure and TRIP Effect to Produce Austenite Stainless Steel with High Strength and Ductility.” Acta Materialia 112: 337–346.
- Xi, L., S. Guo, D. Gu, M. Guo, and K. Lin. 2020. “Microstructure Development, Tribological Property and Underlying Mechanism of Laser Additive Manufactured Submicro-TiB2 Reinforced Al-Based Composites.” Journal of Alloys and Compounds 819: 152980.
- Xu, X., G. Mi, L. Xiong, P. Jiang, X. Shao, and C. Wang. 2018. “Morphologies, Microstructures and Properties of TiC Particle Reinforced Inconel 625 Coatings Obtained by Laser Cladding with Wire.” Journal of Alloys and Compounds 740: 16–27.
- Yang, Y., T. Chen, L. Tan, and D. Poplawsky. 2021. “Bifunctional Nanoprecipitates Strengthen and Ductilize a Medium-Entropy Alloy.” Nature 595: 245–249.
- Yang, M., L. Weng, H. Zhu, T. Fan, and D. Zhang. 2017. “Simultaneously Enhancing the Strength, Ductility and Conductivity of Copper Matrix Composites with Graphene Nanoribbons.” Carbon 118: 250–260.
- Zhang, H., D. Gu, C. Ma, M. Guo, J. Yang, H. Zhang, H. Chen, C. Li, K. Svynarenko, and K. Kosiba. 2021. “Understanding Tensile and Creep Properties of WC Reinforced Nickel-Based Composites Fabricated by Selective Laser Melting.” Materials Science and Engineering: A 802: 140431.
- Zhang, H., D. Gu, L. Xi, H. Zhang, M. Xia, and C. Ma. 2019. “Anisotropic Corrosion Resistance of TiC Reinforced Ni-Based Composites Fabricated by Selective Laser Melting.” Journal of Materials Science & Technology 35: 1128–1136.
- Zou, Y., C. Tan, Z. Qiu, W. Ma, M. Kuang, and D. Zeng. 2021. “Additively Manufactured SiC-Reinforced Stainless Steel with Excellent Strength and Wear Resistance.” Additive Manufacturing 41: 101971.