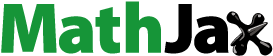
ABSTRACT
Inspired by the vast amounts of investigations carried out on three-dimensional (3D) printed structures and their recent accelerated developments, the present review paper comprehensively describes the current trends as well as promising findings of 3D printed energy absorbing structures (EAS) for crashworthiness application. Particular attention is paid to the mechanical behaviour and crushing performance of 3D printed EAS. The main 3D printing technological processes, their material feedstocks choices and unique structural designs, investigated recently, are discussed in detail. Deformation modes obtained by 3D printed EAS under different loading conditions are identified. Additionally, salient suggestions with future realisation of complex 3D printed EAS are provided. This review will serve as a springboard to propel the technological advancement of additively manufactured EAS incorporated into moving vehicles and utilised as protective devices. Hence, setting the goals to encourage novel research that guarantees the efficient protection of lives and valuables during mild and catastrophic impacts.
1. Introduction
1.1. Background
Rapid prototyping of structural parts has evolved in recent years. The technique involves fabricating models from computer-aided design files. However, a more excellent recent manufacturing process of producing prototypes of structural parts with complex geometries is the additive manufacturing commonly referred as 3D printing. This printing or manufacturing process involves the addition or accumulation of materials in successive layers or drops until the structural part is completely built. Hence, the additive manufacturing process offers the advantage of saving or ‘adding’ materials, which is in contrast with the conventional subtractive manufacturing process such as laser cutting, CNC routing, etc. The rapidly evolving additive manufacturing technology of fabricating complex and more sophisticated parts has found useful applications in virtually all sectors of industries including aerospace, automotive, marine, building, etc. Moreover, the parts built by 3D printing technology have a lightweight advantage with great potentials of improving their mechanical properties. Also, 3D printing makes room for the provision of customised design of energy absorbing structures (EAS) (Habib et al. Citation2017). These structures either absorb energy through plastic deformation (Wei et al. Citation2020) (i.e. for those fabricated with metallic material feedstocks) or through some kind of progressive crushing (Zhang et al. Citation2021) (i.e. for those fabricated with polymeric or composite material feedstocks). One of the major breakthroughs in crashworthiness application is the utilisation of 3D printing technology to fabricate complex EAS with special functionalities. The last five years have witnessed highly innovative designs of EAS and a good number of research efforts have been put into manufacturing such designs. This review aims, therefore, to critically examine the advances of energy absorbers fabricated using the 3D printed technology investigated within the past half decade.
It is fascinating to discover within the last half decade that a considerable amount of novel material feedstocks used for fabricating 3D printed EAS has emerged. Prior to the advent of this growing technology, manufacturers of conventional EAS had always encountered the challenge of customising the product. The probable reason was because the design of the desired products could either be expensive or could generate more waste of materials due to the kind of manufacturing process adopted. Consequently, less efficient EAS with restricted functional and topological designs were produced. Moreover, the conventional production of EAS is expensive and could result in mass addition, thereby increasing the overall mass of moving vehicular structures. This has resulted in higher fuel consumption of vehicles and in turn an increased release of noxious substances (i.e. carbon monoxide or dioxide) into the atmosphere (Isaac Citation2020a). However, 3D printed EAS can be tailored to achieve more lightweight advantage over their counterparts fabricated through the conventional manufacturing process (Lubombo and Huneault Citation2018). Apart from the advantages of 3D printed EAS which include low cost of production, product customisation, waste reduction and manufacturing of complex structures, their lightweight advantage make them more environmentally friendly when used as energy absorbers in cars, ships, aircrafts and other moving vehicular devices.
The advent of 3D printing has enabled the production of EAS mimicking nature. Various biomimicry designs from plants, animals, humans or other forms using 3D printing technology have shown very remarkable energy absorption capabilities (Zhang et al. Citation2020; Jiang et al. Citation2020; Nian et al. Citation2021; Li, Zhi, and Fan Citation2022). The idea of producing highly effective EAS mimicking the micro and macro structural arrangement of plants and animals has been one of the major promising subjects of current research. Additive manufacturing techniques make it seamless to fabricate various architectural designs mimicking nature. This review meticulously examines various architectural designs of 3D printed EAS mimicking nature investigated by renowned researchers over the past five years. Moreover, the architectural designs of EAS can include more special features such as the grading of 3D printed EAS (Nian et al. Citation2020; Wu et al. Citation2021), or the hierarchical cell arrangements of 3D printed energy absorbers (Liang et al. Citation2022; Zhang et al. Citation2021). Additionally, filler materials such as foams, realised via additive manufacturing and combined with energy absorbers have shown enhancement in mechanical behaviour and overall crushing performance of a hybrid energy absorber (Airoldi et al. Citation2020; Yan et al. Citation2020). In fact, in recent times, the irregular geometry of foams can be achieved through surface design and then fabricated with ease through the additive manufacturing technology (Sajadi et al. Citation2018; Gong et al. Citation2020). However, many possibilities of designing and manufacturing 3D printed EAS have not yet been fully explored. Hence, it is one of the objectives of this review paper to open up these possibilities. Moreover, it is expected that this review work will point researchers and manufacturers into the latest finding of 3D printed EAS. This will positively direct the designing and fabricating of much more sophisticated, less expensive, structurally adaptable and environmentally friendly 3D printed cross-sections with optimised energy absorption efficiency.
Quite a few numbers of 3D printing technologies have been used for fabricating EAS. Typical amongst them include but not limited to fused deposition modelling (FDM) also referred as fused filament fabrication (FFF), selective laser sintering (SLS), selective laser melting (SLM), stereolithography apparatus (SLA) and multi-jet fusion (MJF). Other promising 3D printing techniques include direct ink writing (DIW) and laminated object manufacturing (LOM). These 3D printing devices are fed with filaments or feedstock materials which are basically used in building the desired EAS prototypes in a layer-by-layer manner. There is a growing spectrum of novel feedstock materials that are currently utilised for realising 3D printed EAS. These include those made from metals and alloys, polymers and composites. Many of the 3D printed EAS made from metals and alloys are popularly manufactured via the SLM and SLS processes. For 3D printed EAS made from polymeric or composites material feedstock, the FDM or FFF technology has gained popularity. Polymer-based filaments such as polylactic acid (PLA), polyamide (PA) also called nylon, acrylonitrile butadiene styrene (ABS), thermoplastic polyurethane (TPU), etc., are some of the most common materials used during the FDM operation for producing energy absorbers. A major challenge of these polymer-based materials for the FDM technology is the weak mechanical properties encountered. However, solutions to resolving this challenge are evolving. For example, these polymeric filaments are being combined with appropriate amount of reinforcement fibres to form composite feedstocks used for the 3D printing of EAS (Chacón et al. Citation2019; Chang et al. Citation2020). This filament-combining strategy generally improves the material properties and remarkably enhances the crushing performance of the energy absorber.
Over the past five years, much research on 3D printed EAS have been carried out with quite interestingly innovative design approaches. It is the goal of this review paper to critically examine and explore the latest works of notable researchers on 3D printed energy absorbers. gives an overview of the contents of this review paper. The work presented here is outlined and summarised as follows. First, Section one introduces the material properties and characterisation. The information herein gives a platform to understanding how parent material feedstock used in additive manufacture behaves during tensile loading. After testing of material properties, the product is 3D printed and the crashworthiness characteristics are evaluated during and after the compression stages. The deformation stages and parameters used for evaluating crashworthiness performance are presented in the next sub-section. It is these crashworthiness characteristic indices that determine the potential of 3D printed EAS to effectively absorb energy. Section two illustrates some of the commonly used additive manufacturing technology for realising the energy absorbing structural parts. The types of 3D printing processes utilised can contribute to the overall crushing performance of the final printed parts. In Section three, the type of materials used for producing structural energy absorbers and their crushing response with respect to the material properties, are given. Section four gives detailed information and illustration on the crushing response of 3D printed cellular energy absorbers. Finally, Section five highlights some research gaps, drawbacks, challenges, future directions and perspectives of 3D printed energy absorbers.
1.2. Material characterisation and mechanical properties
Many of the base materials used in 3D printing of EAS were first characterised to obtain their mechanical properties. It should be noted that 3D printing processes are characterised by anisotropic behaviour. This is because the process of building the part involves a layer-by-layer deposition of the filament on the printing surface until the whole printed part is formed. The layer-by-layer process in the long run influences the mechanical properties of the final printed part. Anisotropic properties of the base or parent material can be affected by the type of orientations used in printing the part. During 3D printing process, the build direction of specimen is mostly set in the z-direction. Energy absorbing specimens are printed either in the orientation or
orientation. This helps to enhance the mechanical strength of the sample compared to when they are printed in the
orientation. Moreover, due to the anisotropic property of 3D printing technology, different mechanical properties can be obtained in different directions for the same material. Some material suppliers provide the material properties. However, it is often important to perform standard tensile tests of the material to ascertain the material characterisation according to the specific test standard of the base material. For example, the mechanical properties of ABS coupon parts manufactured through FDM technology provided by Kucewicz et al. (Citation2018), were different from those given by the supplier of the ABS coupon part. The difference in data of the tensile strength, elastic modulus and yield strength of the material supplier and investigator were 7.1%, 5.2% and 3.2%, respectively. These differences in supplier’s and investigator’s results are clear indications that the mechanical properties of base materials can be altered depending on the process being specified and how the final structural parts are being designed.
Before fabricating the EAS, the material properties of the base feedstock are first obtained through standard tensile tests. The tensile test must be done in accordance with the prescribed standards test for the specimen. This is carried out mostly, using a dog-bone coupon, fabricated by the 3D printer either in the ,
or
plane. Moreover, several orientations or directions of the dog-bone specimen on each plane can be investigated depending on how the unit cells or struts making up the final 3D printed EAS are arranged. The dog-bone coupon is aligned vertically and gripped by the tensile test machine. Various strain rates can be tested on the dog-bone sample and the mechanical properties such as the modulus of elasticity, tensile modulus, Poisson ratio, friction coefficient, density and elongation can be obtained. It is a normal practice to test three or more similar samples having the same parameters, building orientation and strain rate condition to ascertain their repeatability (Zeng et al. Citation2021). Small deviations in the mechanical properties of these similar samples are likely to occur due to the anisotropic behaviour of the 3D printer. Consequently, void or porosity is formed on the printed sample. It is also worth noting that various printing strategies can also influence the mechanical properties of printed samples. In general, the stress–strain curve enables the evaluation of yield stress, maximum tensile strength, modulus of elasticity, Poisson ratio, elongation and the onset of failure strain. During numerical approximations such as via the finite element method (Smith, Guan, and Cantwell Citation2013), the values of the stress–strain curve and mechanical properties obtained from the tensile test measurement are inserted into the finite element simulation of EAS and the approximated solutions are used to virtually validate the experimental EAS measurements.
1.3. Fabrication and crushing deformation
This section briefly describes a typical honeycomb structure fabricated via 3D printing and subjected to quasi-static loading conditions. The authors of this review fabricated a conventional honeycomb structure using the FDM technology with material feedstock made from PLA. The presentation here will help to understand the general procedures utilised by most researchers to investigate 3D printed crushed structures especially those discussed in this review.
After material characterisation, the energy absorber is fabricated using a suitable additive manufacturing technology. The fabricated EAS is then subjected to one or several loading conditions to determine its deformation modes and crashworthiness performance. To demonstrate this, an energy absorbing honeycomb-like structure made from PLA material is fabricated using the FDM technology as shown in (a) and (b). The structure is then placed between two platens of a universal crushing machine as illustrated in (c). For this demonstration, a quasi-static speed of 100 mm/min was used for the in-plane crushing of the honeycomb structure. The upper platen is the moving striker while the lower platen is fixed. At different strain values, the deformation stages (see (d)) can be captured and recorded until the honeycomb structure is fully crushed. Moreover, various crashworthiness performance indicators can be evaluated during and after the whole crushing processes.
Figure 2. From additive manufacturing through crushing of PLA honeycomb EAS: (a) layer-by-layer FDM printing process, (b) prototype of printed sample, (c) sample before in-plane crushing and (d) sample during in-plane crushing.
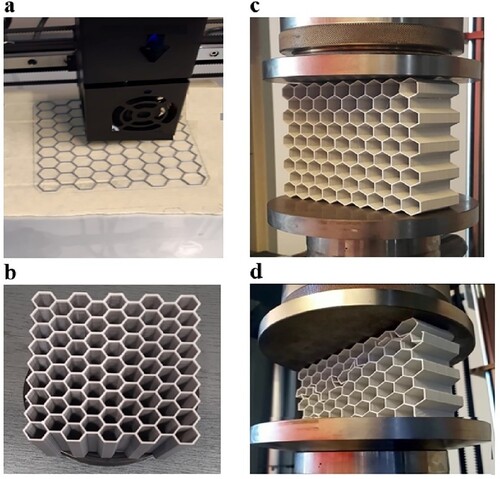
During crashing of EAS, three typical stages occur which are the elastic, plateau and densification stages as illustrated in . Embedded in the figure are two typical stress–strain dominated curves which are obtained depending on the type of fracture modes of the EAS. The first is the bending-dominated mode curve and the second is the stretching-dominated mode curve. From the illustrative diagram, the stretching-dominated curve results in downward decrease of plastic stress after yielding with the prolonged plateau stage. The bending-dominated curve, on the other hand, results in a gradual increase of plastic stress (i.e. due to strain hardening) after onset of yielding and may produce a slightly shorter plateau stage than the stretching-dominated one. Also, energy absorbers with stretching-dominated modes have higher stiffness-to-weight ratio than the bending-dominated ones (Neff, Hopkinson, and Crane Citation2018). The amount of energy absorbed either by the bending or stretching-dominated EAS is determined by the area under its curve. In the elastic stage, no yielding occurs. Only an initial bending can be found for both elastic-plastic and elastic-brittle materials (Maskery et al. Citation2016). As crushing progresses, the material reaches a point where it begins to collapse. This point is the yield point which gives the initial peak force/load in a force–displacement diagram or the peak stress
at the linear elastic stage of the stress–strain diagram. The force at this stage is very important because it shows vital information about the crushing force efficiency of the energy absorber. The lower the initial peak force at this linear elastic stage over the successive peak forces at the plateau stage, the better the efficiency of the energy absorber. The converse is also true (i.e. the higher the initial peak force over the successive peak forces, the less effective the energy absorber). In the second stage, also known as the plateau stage, the material begins to collapse or deform gradually. The type of deformation formed during this stage depends largely on the parent material, geometrical features and manufacturing process. For energy absorbing materials made via metal additive manufacturing, plastic deformation energy is relevant while for those made from composite, a form of crushing or failure-based energy absorption occurs (Isaac and Ezekwem Citation2021). The last stage is when the material deformation enters densification. At this stage, the force per unit area of the crushed EAS begins to rise rapidly. Consequently, the energy absorption of the EAS is normally stopped at this densification stage and the dissipated energy in the EAS is related to the internal strain energy of the bulk material.
For the crushing demonstration carried out with the 3D printed energy absorbing honeycomb structure represented in (c) and (d), the force–displacement curve is shown in . The diagram shows three regions – the elastic, plateau and densification regions. From the analysis of the stress–strain diagram discusses above, it is evident that the FDM 3D printed honeycomb structure is stretching-dominated with the high stiffness-to-weight ratio. Moreover, the plateau region is prolonged and characterised by brittle crushing, hence, making it a potentially promising energy absorber design. These results inform why a good number of researchers have investigated the traditional hexagonal honeycomb and its modification as promising EAS for crashworthiness applications. This bio-inspired cellular honeycomb structure is elaborately described in Section four of this review.
1.4. Crashworthiness performance indexes
Almost all research works carried out on 3D printed EAS, investigated by recent researchers, have presented one or more crushing parameters. These crushing parameters are indices employed for evaluating and comparing the crashworthiness performance of different energy absorbers. The parameters or indexes can either be dimensional or nondimensional. In this section, some definitions of the commonly used crashworthiness indexes are presented. The following gives explanation of some of the dimensional crushing indexes:
Energy absorption: Represents the crushing force along displacement
over its crushing distance
. It can be obtained by calculating the area under the curve in . It is generally expressed as.
(1a)
(1a) In terms of densification strain
as represented in the area under the compressive stress (
) – compressive strain (
) curves of , the energy absorbed before densification occurs can also be expressed as (Kader et al. Citation2020)
(1b)
(1b) Specific energy absorption: For each deformed unit mass of the energy absorption calculated in Equation (1), the specific energy absorption (SEA) is given by (Andrew et al. Citation2021)
(2)
(2) where
is the total mass of the structure and
is the mass density of the deformed structure. The higher the SEA value, the more efficient the energy absorber. It was reported that the axial SEA values of EAS manufactured via 3D printing technology with composite feedstock did not necessarily outperform those of the composite structures manufactured through the conventional manufacturing process such as pultrusion or autoclave (Morales et al. Citation2021). The reason was adduced to the low fibre content of 3D printed composite EAS. However, with 3D printed steered fibre EAS, the SEA values were significantly improved over those fabricated via conventional means.
Specific strength: This parameter is obtained by dividing the peak stress () by the apparent mass density (
) indicating the bearing capability of the unit mass of the structure (Zhang et al. Citation2021). It is calculated as
(3)
(3) During impact of 3D printed EAS, the specific impact strength can be obtained. This parameter is the measure of the ratio of the impact strength to the density of the 3D printed EAS.
Average crushing load: Also referred as mean crushing load, is the energy absorbed by the structure divided by the crushing distance of the impacting load given by (Isaac Citation2020b)
(4)
(4) Plateau stress: This corresponds to the ratio of the mean stress to the difference between the onset of densification strain and the yield strain (
) given as (Wu, Su, and Shi Citation2020; Habib et al. Citation2018)
(5)
(5) The more stable and longer the plateau stage, the better the energy absorption capability.
Several nondimensional crushing indices have also been used to characterise the crushing response of EAS. They are briefly explained thus:
Energy absorption efficiency: This parameter indicates the energy absorption per unit volume divided by the theoretical energy absorber having similar peak stress (Zhang et al. Citation2021). It is also defined as the ratio of the energy absorption to the transmitted stress during crushing expressed as (Mohsenizadeh et al. Citation2018).
(6)
(6) Equation (6) can be derived by dividing the measured energy absorption by the maximum theoretical energy absorption.
Crushing load efficiency: This represents the ratio of the mean crushing load (or the mean crushing stress, ) to the peak crushing load,
(or the peak crushing stress,
) written as
(7)
(7) Equation (7) constitutes one of the most important nondimensional parameters that indicate whether an energy absorber is efficient enough to be used for specific crushing applications. A highly efficient EAS is one that has a CLE close to hundred per cent.
Structural efficiency: Different geometrical shapes of EAS and their material properties are being compared by recent researchers to explore their effects on energy absorption capacity. This can be achieved by obtaining their structural efficiencies which correspond to the ratio of the mean crushing load to the load used to completely crush the EAS up to densification (Isaac and Oluwole Citation2018). It is written as
(8)
(8) where the term
is the undeformed cross-sectional area of the geometrical shape of the EAS.
Load uniformity: This can be calculated by dividing the mean crushing load by the maximum load (), indicated by the expression (Morales et al. Citation2021)
(9)
(9) Initial failure indicator: This is obtained by dividing the initial crushed load (
or stress (
) by the initial peak crushing load (
) or stress (
), expressed as (Isaac and Ezekwem Citation2021)
(10)
(10)
2. Main additive manufacturing technology
Novel 3D printing processes are emerging and they are being used to produce more complex, specially customised and well-tailored energy absorbing structural designs. These EAS are proved to be efficient in their crushing performance with many promising ways of improving their mechanical properties. The type of 3D printing technology used for fabricating these EAS contributes significantly to the crushing performance of the energy absorber. This section, therefore, presents the commonly adopted 3D printing technology utilised to produce EAS. It is not the goal of this review to present the whole gamut of 3D printing technological processes as quite a good number of papers have been published regarding different additive manufacturing technology. The main manufacturing technology with respect to fabricating 3D printed EAS and their energy absorbing performance recently investigated are presented in the following sections.
2.1. Material extrusion
Fused deposition modeling (FDM) also regarded as fused filament fabrication (FFF) is one of the popular methods used for producing 3D printed EAS and this technology uses the principle of material extrusion (Huang et al. Citation2020). The filaments used for printing are essentially thermoplastic polymers or/and composites. These filaments or feedstocks are initially heated by some heating elements in the extruder and pass through a heated nozzle attached to the extruder to give a semi-liquid substance. The substance is then extruded and deposited on a platform or build surface layer-by-layer until the whole part is formed as illustrated schematically in . The figure also shows the building of a support material enabled from a different heated nozzle. Moreover, to achieve highly desirable prints, it is essential to properly calibrate the machine and use a compatible nozzle diameter. There are major drawbacks observed while using FDM/FFF technology to fabricate EAS. They include inferior surface finish of printed parts and limitation or restriction to only thermoplastic polymers or/and composites. Despite these drawbacks, the FDM/FFF technology, however, remains very attractive for the fabrication of EAS. This is because the FDM/FFF technology has a very simplified process, low cost, print versatility and satisfactory high speed. The mostly utilised feed filaments for FDM technology include the well-known PLA, nylon, ABS, etc; however, many more materials are now being used. These 3D printing material feedstocks are discussed in detail in Section 3.
The FDM technology has several process parameters which could be modified to give different outcomes for printed parts. These parameters include nozzle temperature, bed temperature, layer thickness, feed rates (nozzle speed), extrusion width and raster angle (Kafle et al. Citation2021). The mechanical properties and crashworthiness performance of the FDM parts can be influenced by the process parameters of the FDM technology. Quite a few investigations have been carried out to establish the effects of process parameters on the energy absorption capacity of structures manufactured by FDM. Tsouknidas et al. (Citation2016) investigated the effects of layer heights as well as infill patterns on the energy dissipation characteristics of PLA absorbers. The layer heights and infill patterns were shown to be less significant and negligible, respectively. However, increased infill densities were associated with higher energy absorption capacity.
Moreover, with the FDM technology, very few researchers have studied the effects of process parameters on the mechanical performance of feed filaments. Chacón et al. (Citation2019) studied the effects of layer thickness on the mechanical performance of nylon specimen. Their findings indicate that layer thickness was slightly significant. Similarly, with the FDM technology, Belarbi et al. (Citation2021) reported the effect of nozzle and bed temperatures as well as printing angle on the mechanical behaviour of PLA with and without flax. Their findings also showed that bed and nozzle temperatures do not have much effect on the mechanical performance of the two specimens. The two materials were observed to have the same effect. However, various printing angles for PLA filament showed slight difference in their tensile performance while for PLA-flux, no significant difference was observed.
Another promising extrusion-based additive manufacturing technology that could be utilised to produce composite-based or tailored multi-material energy absorber is the DIW. The technique involves the extrusion of visco-elastic ink via a fine nozzle and the extrudate is deposited layer-by-layer on a build surface until the desire part is formed (Zhang et al. Citation2021; Fernandez et al. Citation2019). One of the major features of an ideal ink utilised in the DIW technique is the capacity to maintain its shape after each extrudate. Consequently, allowing it to recover its viscosity property quickly without any additional shear stress applied to it. The main influencing process parameters for this technique include the nozzle size and printing speed (Saadi et al. Citation2022). Smaller nozzle sizes and lower printing speeds can enhance the resolution, produce good tolerance and high fidelity of the printed part. Shan et al. (Citation2015) utilised this technique to realise an energy absorber that had the potential to fully recover upon unloading; hence, giving it the advantage to be reused many times.
2.2. Powder bed fusion
The most popular techniques of powder bed fusion technology adopted for creating EAS are the SLS and selective laser melting (SLM). These techniques involve the use of laser beams in selectively fusing together very fine powder particles which are placed on a platform as shown in . The process parameters commonly considered when using PBF technology to realise energy absorbers are listed in . Moreover, the SLS and SLM techniques do not require support material in building the parts in contrast to the FDM technique. Although, the FDM technique has been successfully utilised by Kumar, Verma, and Jeng (Citation2020) to create supportless lattice structures. However, the major drawback of PBF technology is their relatively high cost of production. Apart from these drawbacks, 3D printed EAS fabricated using these two PBF techniques have very good resolution with enhanced mechanical properties. For example, Chen et al. (Citation2021), used SLS technique with a printing accuracy of 0.05 mm to fabricate a graded honeycomb structure that has negative stiffness and improved energy absorption capacity than the traditional honeycomb structures. Adopting a similar fabrication technique, Wang et al. (Citation2020) utilised the SLS technique to fabricate a polyamide cross-chiral auxetic lattice structure which could be utilised as promising energy absorber. While SLS can be used to produce EAS made from polymeric powders (i.e. nylon) as well as metallic and alloy powders, SLM, on the other hand, are restricted to producing EAS made from metals and alloys. Hence, the term ‘metal additive manufacturing’ is mostly associated with the production of SLM-based energy absorbers.
Table 1. Summary of the commonly considered process parameters for the main 3D printing techniques utilised to fabricate energy absorbers.
Very recently, considerable attention has been given to EAS fabricated via SLM technology (Calle et al. Citation2020; Tripathy and Lu Citation2018). Calle et al. (Citation2020) additively manufactured a very small marine structure using an SLM process technique. Wang et al. (Citation2021) investigated the compression characteristics of different lattice structures hierarchically arranged using SLM technology. Wang et al. (Citation2021) modified the conventional face-centred cubic (FCC) lattice structure and fabricated improved energy absorber by the SLM technique. They reported that the modified face-centred cubic lattice structure gave higher plateau stress with better energy absorption capacity. Kies et al. (Citation2018) followed this trend by comparing SLM-printed lattice structures made from high manganese steel with those made from steel 316L. They found out that the former was characterised by a much more improved SEA than the latter. Additionally, some SLM-printed EAS have been derived from triply periodic minimal surface (TPMS) which has also resulted in better mechanical properties and improved crashworthiness performance. The gyroid as one of the TPMS was utilised by Wang et al. (Citation2020) to construct cylindrical shells fabricated through the SLM technology. Superior energy absorption capacity was observed for the gyroid structures over their traditional ones. SLM-printed sandwich structures with promising energy absorption capacities have also been studied lately (Wei et al. Citation2020; Zhao et al. Citation2021; Wang et al. Citation2021).
2.3. Vat photo-polymerisation
This method involves a photo-polymerisation process in which liquid photopolymers situated in a moving vat undergo some form of curing process induced by ultraviolet light or electron beam. The laser irradiation initiates the bonding of many small monomers (i.e. either an acrylic or epoxy-based type) and, thereby, forming cross-linked polymers. After this process, the liquid layer solidifies layer-by-layer to form the 3D printed part. The commonly utilised the photo-polymerisation process for making 3D printed EAS is the SLA (Dar et al. Citation2020; Gao et al. Citation2020) as schematically depicted in . This technique has been used by Gao, Liao, and Wang (Citation2020) to fabricate a double arrowed cylindrical energy absorber made from ABS material. Laser power, laser speed, layer thickness, curing depth and post curing are some of the process parameters of the SLA technique as presented in . Energy absorbers made by this technique are very expensive, however, products made via it have very high quality as well as good resolution.
Figure 7. Schematic representation of the working and process parameters of SLA 3D printing (Mohsenizadeh et al. Citation2018).
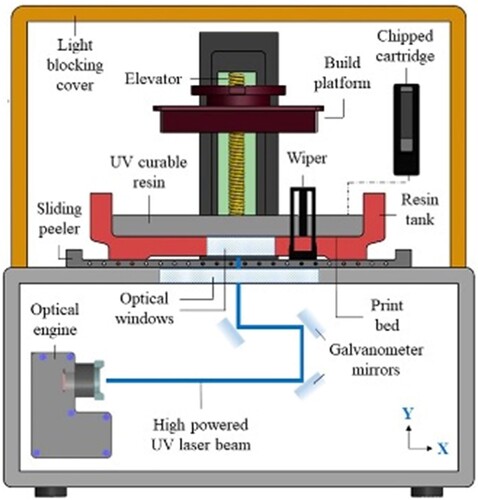
A very fine resolution 3D printed lattice EAS was produced by Wang et al. (Citation2020). The lattice structures with four different forms were fabricated using the SLA technique. Both uniform and graded body centred-cubic (BCC) structures as well as, a uniform and graded BCC structure with reinforcement along the -axis (BCCz) as shown in , were investigated by the authors. The experiment showed that the graded lattice deformed in a layer-by-layer fashion while the uniform lattice deformed in a general way. At the small deformation phase, it was reported that the uniform lattice exhibited superior energy absorption capacity over the graded lattice type. However, at a critical deformation value, the graded lattice type demonstrated a higher energy absorption capacity than the uniform ones. Additionally, when the BCC lattice structure was fabricated with graded density in the z-direction, the modulus of elasticity and the capacity of the lattice to bear load per unit area were enhanced compared to the other lattice types. In another investigation, Niknam and Akbarzadeh (Citation2020) printed graded lattice structures enabled by SLA technology and they observed that the specific energy absorption of graded lattice structures can increase up to 60% over their uniform lattice structure counterparts during strain increment. Following this trend, in recent times, Nian et al. (Citation2021) studied the energy absorption performance of a functional graded lattice structure made from SLA technology. The fabricated lattice structures were filled into circular aluminium thin-walled tubes. The graded pattern of the lattice structures was also accentuated by the authors to have influence on the energy absorption capacity of the circular tubes. Meanwhile, by subjecting the tube filled with a graded lattice core to lateral impact (i.e. transverse loading condition) it was shown that the energy absorption efficiency can be enhanced more than their corresponding thin-walled tube filled with non-graded lattice structures.
Figure 8. CAD model for 3D printing depicting uniform and graded densities for (a) BCC unit cell and lattice structure and (b) BCCz unit cell and lattice structure (Wang et al. Citation2020).
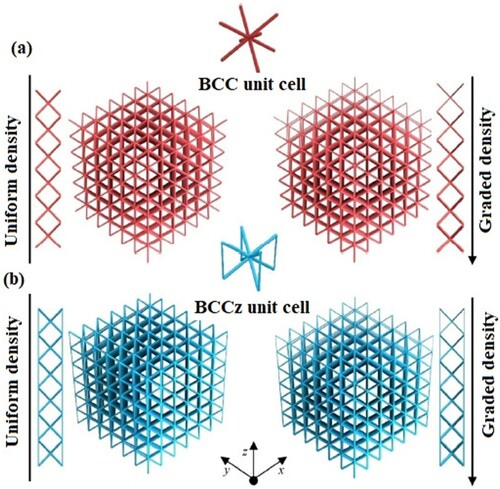
2.4. Other 3D printing technology
Apart from the above-listed 3D printing technology, other similar emerging 3D printing techniques could also be adopted to fabricate EAS prototypes. For example, material jetting technology such as the polyjet machine has been developed whose working principle is similar to that of the SLA technique. However, the resolution of the final product fabricated via polyjet is very coarse compared to those fabricated via the SLA technique. With the polyjet technique, photopolymer resin is first released from the printing head into a printing layer. The released resin then undergoes curing, enabled by an ultraviolet light and the subsequent layers are being formed until the whole process of forming the part is completed. Jiang et al. (Citation2020) utilised a polyjet multi-material printing technology to fabricate a multi-layered cellular composite structural design with the aim to study its energy absorbing performance. With a compressive strain of about 0.7, the investigated structures absorbed energy four times more than their conventional ones. Moreover, the investigated structure showed promising shape recovery characteristics when compressed up to a strain of 40%. Similarly, Wu, Su, and Shi (Citation2020) used a polyjet multi-material additive manufacturing technology (i.e. inkjet) to realise a graded auxetic metamaterial for enhanced energy absorption capacity. In their investigation, the graded auxetic configuration exhibited both structural stiffness and inertial effect-dominated regions when the loading speed was increased. Albertini et al. (Citation2021) additively manufactured prototypes of auxetic lattice with a compliant filler through the material jetting technique. By modifying the deformation mode from layer collapse mode to shear-band breakage mode of the auxetic lattice, the SEA value and absorption efficiency were substantially improved. A 3D re-entrant energy absorbing lattice structure was also fabricated by Logakannan et al. (Citation2020) using the MJF technology. Other research works which have used this jetting technology to fabricate promising EAS have been given in the literature (Kumar et al. Citation2019; Tao et al. Citation2019; Nazir, Ali, and Jeng Citation2021).
LOM is another 3D printing technology that has been used to fabricate an energy absorber (Chang et al. Citation2020). The technique involves lamination and cutting of each sheet layer using a laser or mechanical cutter which is then passed through a heated roller to enable bonding to build the platform. This technique can be used for manufacturing a wide range of structural materials as well as composite-based energy absorbers. Also, it is less expensive than the powder bed fusion and photo-polymerisation techniques. However, compared to other 3D printing techniques, the LOM technology may not be suitable for the energy absorber that requires more complex and intricate parts because of its poor surface quality and low dimensional accuracy (Ngo et al. Citation2018).
3. Materials for 3D printed energy absorbers
In this section, a discussion is provided on how the materials used for 3D printed energy absorbers affect their mechanical and crashworthiness performance. Also, the type of deformation or collapse mode formed after impact is presented. During deformation of these 3D printed materials, at a certain impact stress level, deformation begins from the impact edge of the material cell walls depending on the material properties of the EAS. The impact could result in different types of deformation such as yielding, brittle failure or buckling. The classification of materials used for crashworthiness application considered in this paper includes metal and alloys, polymeric and composite materials as well as their hybrid materials.
3.1. Metals and alloys
Metallic feedstocks for metal additive manufacturing are normally in powdered or wired feeds and can be used to produce 3D printed EAS with complex designs and tailored metallic properties. The metal additive manufacturing technique involves the use of laser or electron beam to melt the feedstock which after being exposed to the ambient surrounding, solidifies on a platform to hold the next layer until the solid part is completely formed. Direct energy deposition and PBF are the two main classes of metallic 3D printing technology (Lewandowski and Seifi Citation2016). Some commonly utilised metals and alloys, their mechanical properties and metal additive manufacturing processes recently employed by selected authors to fabricate 3D printed EAS are provided in . The table shows that the SLM technology is mostly used to create energy absorbers made from metals. Structural parts produced by metal additive manufacturing via the SLM technique can be used for load bearing purpose as well as applications involving plastic deformation. For specific design as found in strut structures such that they are used as core material for a sandwich structure, the main collapse mode includes buckling as a result of increased stresses at the plastic hinges (Wei et al. Citation2020). Buckling of struts can also be initiated from points of micro-defects which could be caused by indentation. During crushing, the metallic 3D printed EAS generally exhibits brittle cracking or fracture collapse along the plateau stage. Their base materials allow them to undergo plastic deformation at the overall plateau region which is typical to energy absorbers made from metallic materials. Before the plateau stage, deformation is first characterised by linear elastic behaviour which is caused primarily by bending. For brittle materials, as the crushing progresses, longer plateau regions are experienced. This results in increased energy absorption capacity and thereby making them attractive materials for crashworthiness application.
Table 2. Mechanical properties of metals and alloys commonly used for 3D printed energy absorber.
Aluminium-silicon alloys (AlSi10Mg) are used as a base material powder during metal additive manufacturing owing to their low density, high strength-to-weight ratio and easiness in casting (Mohamed et al. Citation2019; Kempen et al. Citation2015). When utilised for making 3D printed EAS, their energy absorption characteristics can be improved further by heat treatment processes. Stainless steel alloy especially steel 316L (Tancogne-Dejean, Spierings, and Mohr Citation2016; Wang et al. Citation2021) have been widely used for EAS owing to their good mechanical behaviour. However, in recent years, innovative approaches of fabricating 3D printed EAS made from titanium alloy (i.e. Ti6Al4V) have emerged (Drücker et al. Citation2021; Bai et al. Citation2021). Titanium alloy has higher specific stiffness and strength over aluminium and steel alloys. In , it is shown that the yield strength of titanium alloy is higher than for steel and aluminium alloys. Moreover, the investigation carried out by Baroutaji et al. (Citation2021) showed that the energy absorption capacity of graded titanium alloy specimen outperformed that of graded aluminium alloy specimen; and was 79% higher in SEA value compared to their uniform thickness counterpart. One of the drawbacks of fabricating metallic 3D printing parts via the SLM technology is their poor ductility resulting from residual stresses. As a result, fracture usually occurs at weak zones where high loading with less material resistive force is experienced. Some probable panacea for this low ductility is by optimising the process parameters of the SLM technique and performing heat treatment on the 3D printed EAS (Mohamed et al. Citation2019).
The failure modes observed during crushing of additively manufactured energy absorbers are significantly influenced by the layer-by-layer formation of the part during fabrication. Thus, deformation is generally characterised by a layer-by-layer collapse. Compressive crushing of the 3D printed EAS can generally be either static, quasi-static or dynamic in loading. In static or quasi-static loading condition, inertial or strain rate sensitivity does not affect the energy absorption or crashworthiness performance of metallic 3D printed EAS. However, for dynamic impact loading, the metallic 3D printed EAS becomes more sensitive to inertia and strain rates. Moreover, the collapse modes of these structure-based energy absorbers are influenced by their volume fractions, parent material properties, geometrical features (i.e. topologies, cell shapes, cell sizes, etc.) as well as relative densities. With these factors taking into consideration, various fracture modes can be identified.
For 3D printed structures enabled by SLM technology and made from stainless steel powder (Novak et al. Citation2021) identified two main deformation modes due to the relative densities of the most effective structures investigated. With a low relative density, the investigated gyroid structure exhibited local deformation. However, at high relative density, a uniform collapse mode was observed. Using similar material feedstock and metal additive manufactured SLM technology (Wang et al. Citation2021) identified local buckling, layer-by-layer collapse mode and global buckling of the lattice structural specimen subjected to quasi-static loading.
Direct laser sintering metal 3D printed lattice structures were investigated by Cetin and Baykasoğlu (Citation2019). The base material utilised for fabricating the lattice EAS was aluminium alloy (i.e. AlSi0Mg). Under quasi-static compression loading, progressive and global buckling modes were identified. The deformation modes and crushing performance of direct laser sintering 3D printed corrugated tubes have also been investigated by Alkhatib et al. (Citation2019). More recent are the works of Yang et al. (Citation2020) using similar metallic alloy, AlSi0Mg, to additively manufacture corrugated structures which were subjected to a quasi-static velocity of 2 mm/min. The results of their investigation indicated full-folded, transitional and global buckling modes as they vary different wave numbers (i.e. with wave numbers of 4, 5 and 6, respectively).
Energy absorbing lattice structure made from titanium alloy has also been studied and various deformation modes have been identified. For instance, in the investigation carried out by Drücker et al. (Citation2021), a sudden shift collapse and microscopic buckling were observed during the deformation process. Bai et al. (Citation2021) observed layer-by-layer collapse, shear, buckling and node failure mechanism. Also, buckling collapse mode and shear collapse mode were similarly observed by Lin et al. (Citation2021) when they investigated honeycomb structures with different twist angles as depicted in (a). These two deformation modes took place at 0.55 and 0.3 strains, respectively as shown in (b).
Figure 9. (a) CAD model of honeycomb structures with various twist angles and (b) 3D printed honeycomb deformation with various twist angles also showing the type of collapse modes at different strain values (Lin et al. Citation2021).
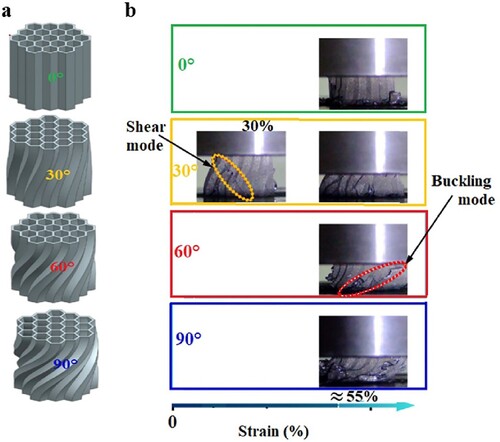
3.2. Polymers and composites
Unlike metal additive manufacturing that mostly uses the SLM technology to fabricate complex 3D printed EAS (i.e. as shown in ), the FDM or FFF technology, on the other hand, has utilised more polymeric or/and composite materials for fabricating conceptual prototypes of 3D printed EAS as seen in . For the polymeric materials, they are prepared in form of resins, monomers, or filaments. Apart from the FDM/FFF technology for producing polymer/composite-based EAS, several other polymer-based fabricating technologies have been investigated. For example, honeycomb energy absorber made from polyamide was fabricated via the SLS technique (Chen et al. Citation2021). A cylindrical arrowed honeycomb energy absorber prepared from ABS was fabricated via the SLA technique (Gao, Liao, and Wang Citation2020). Also, re-entrant honeycomb prepared from polyamide 12 were produced through the MJF technique (Logakannan et al. Citation2020). Lastly, polymer foams prepared from polyamide 12 was fabricated via MJF (Jiang et al. Citation2021). Composite-based filaments are obtained by reinforcing the pellets of the polymeric material with fibre such as carbon, glass or kevlar and subjecting them to repeated extrusion. As already mentioned, the fabricated EAS prepared by either polymer-based or composite-based 3D printed technology has weak mechanical properties. Several strategies have been adopted to resolve this drawback and improve not only their mechanical properties but also their crushing performance. A brief discussion of these strategies is provided in the following paragraphs.
Table 3. Mechanical properties of polymers and composites commonly used for 3D printed energy absorber.
The combination of polymeric materials with fibre reinforcements is one of the present strategies adopted to improve the mechanical strength of feedstocks used to produce energy absorbers. Short fibres are easily added to the polymer matrix. However, for certain 3D printing processing techniques such as FDM, continuous fibre filaments could be very difficult to achieve because the toughness ability of the feed filament during the FDM process can easily be lost. It was found by Matsuzaki et al. (Citation2016) that both the tensile modulus and strength of continuous fibre composite (i.e. carbon fibre + PLA matrix) filament were much higher than those of the single PLA filament. In the investigation carried out by Chang et al. (Citation2020), a continuous carbon fibre was combined with poly-ether-ether-ketone (PEEK) to form a composite feedstock which was used to produce a laminate enabled by a laser-assisted laminated object manufacturing (LA-LOM). Their result indicated an ultra-high improvement in the tensile strength of the laminate due to high carbon fibre content as well as strong interfacial bonding. The types of fabrication techniques used for in-nozzle impregnation to produce the laminate also influenced their mechanical strength. The FFF technology gave a lower mechanical strength than the LA-LOM. In another investigation carried out by Wang, Liu, Wang, Yao et al. (Citation2022), both glass and carbon fibres were utilised as reinforcement fibres combined with polyamide resin to form the composite filament. The 3D printed EAS made from composite filaments (i.e. glass + polyamide or carbon + polyamide) were compared with those made from the pure polyamide filaments of various geometrical shapes. It was observed that the energy absorption of all geometrical shapes made from the composite filaments was higher than those made from pure polyamide filaments. Moreover, the collapse modes of these 3D printed EAS can be affected by their geometrical configuration and material types. Different continuous fibre types such as carbon, glass and kevlar fibres were combined with nylon using the FDM technology to investigate how some process parameters influence their mechanical properties (Chacón et al. Citation2019). For kevlar fibre polymer composites were reported to give the lowest mechanical properties owing to their strong anisotropic proclivity while carbon fibre polymer composite gave the highest mechanical properties – tensile and flexural characteristics. Problems emanating from anisotropic tendencies in fibre reinforced polymer composites could be most probably addressed by adding thermoplastic elastomers (Wang et al. Citation2017; Adams et al. Citation2022).
Moreover, during the fabrication of composite-based 3D printed EAS, void formation or air gaps may constitute a major factor that reduces their mechanical strength and crashworthiness performance. Air gaps introduce weak bonding between fibre and matrix. However, by adjusting the 3D printing strategy, the porosity or void formed can be significantly minimised. For example, additional fibres could be aligned in the load-bearing direction during the printing process (Wang et al. Citation2017). This strategy could help to cushion the formation of air gaps and in turn improve the mechanical strength of the printed structures. Wang et al. (Citation2016) proposed adding thermal-expanding microspheres into composite matrix. In their investigation, different microsphere contents from 2 to 11 wt% were used and thermally subjected to heat treatment up to 140° C at different time periods (i.e. 60 and 120 s). Analysis of both tensile and compressive strengths was carried out. The result of their findings indicated an improvement in tensile strength with increased heating time at 2 wt% microsphere and a rise of compressive strength from 1.8 to 5.4 MPa. Other strategies to enhance the mechanical strength such as increasing the in-fill density and adjusting the tool-paths pattern have been introduced (Xiao, Roh, and Zhu Citation2021).
Deformation modes and failure mechanisms of polymer-based and/or composite-based 3D printed EAS have been studied by several researchers in recent times. For polymer-based 3D printed honeycomb EAS, Habib et al. (Citation2017) observed line, X-shaped band and buckling deformation modes. In a more recent investigation, the X-shaped deformation mode was reported by Wu, Su, and Shi (Citation2020) and Xu et al. (Citation2020). This X-shaped mode (Wu, Su, and Shi Citation2020) was observed when the auxetic graded energy absorbing material was compressed at a strain of 0.3 and impacted at 10 m/s. The relative density of the base materials can affect the way the structural polymer-based material deforms. Guo et al. (Citation2020) investigated the deformation pattern of energy absorbing auxetic lattice made from ABS and realised using the FDM technology. A z-mode; ring and diamond and mix-collapse modes were reported. The z-mode occurred when the relative density of the lattice structure was 1% and 2%. With increased relative densities (i.e. greater than 4%) mixed modes consisting of z-modes and ring modes were observed. However, when the absorbing configuration was subjected to low-velocity loading conditions at a relative density of 4%, a mixture of z-mode and diamond mode was reported. Between relative density of 4-10%, a pure diamond mode was observed. Moreover, at a relative density up to 10%, a pure ring mode was recorded and with larger relative density, the distance of the deformed z-mode zone was noticed to become shorter.
The direction of impact loading velocity () has also contributed to the type of deformation mode experienced by 3D printed EAS. Crushing impact direction can either be in-plane or out-of-plane (Zhang et al. Citation2019) as illustrated in . Using an MJF technique to fabricate a re-entrant structural strut made from polyamide 12; Logakannan et al. (Citation2020) observed a buckling and a pure bending mode when subjected to two different loading directions namely, z-directions and x-direction, respectively. It is noteworthy that for a proposed honeycomb compression, Xu et al. (Citation2020) explained that in-plane compression produced more favourable collapse stability over out-of-plane compression. Crushing in the z-direction is sometimes referred as out-of-plane crushing as shown in (b). In-plane crushing can be performed in x- or y-direction as seen in (c, d), respectively. It is noteworthy to investigate the deformation or collapse mechanism in these directions. Alomarah, Masood, and Ruan (Citation2020) investigated both the out-of-plane and in-plane crushing performance of hexagonal honeycomb, auxetic honeycomb and hexachiral honeycomb. During the out-of-plane compression, they observed local plastic buckling of the hexagonal honeycomb walls; a global buckling with zig-zag deformation shape for the auxetic honeycomb and a buckling of the cylinder for the hexachiral honeycomb. On the other hand, during the in-plane compression in the x-direction, an X-shaped collapse mode was noticed while a layer-by-layer collapse mode was observed for the in-plane crushing in the z-direction.
Figure 10. Illustration of 3D printed honeycomb with various directions of impact loading (a) 3D printed honeycomb structure, (b) out-of-plane crushing, (c) in-plane crushing in the x-direction and (d) in-plane crushing in the y-direction.

The crushing behaviour and collapse mode of composite-based 3D printed EAS have been studied lately. Using the FDM technology, Wang, Liu, Wang, Yao et al. (Citation2022) demonstrated various types of collapse patterns of CFRP (i.e. short carbon fibre + polyamide) and GFRP (i.e. short glass fibre + polyamide) when subjected to quasi-static and dynamic loading conditions. Various geometrical shapes of the FDM printed composite-based EAS were investigated. Under quasi-static loading, the circle-shaped, hexagon-shaped and quadrangle-shaped structures possessed progressive collapse modes, while the triangle-shaped structural EAS possessed Euler’s buckling as shown in (a). Under dynamic loading conditions, the progressive collapse mode transited to brittle fracture. This was attributed to the effect of the strain rate of the composite material utilised. Mansour, Tsongas, and Tzetzis (Citation2021) utilised the FFF technique with composite material feedstocks (i.e. ABS + carbon fibre and ABS + carbon nanotube). The authors reported that the reinforcement of the ABS with carbon fibre resulted in a more enhanced stiffness and strength compared to the polymer-based ABS and ABS/CNT-based honeycomb structures. It is worth pointing out that under impact, EAS made from composite materials mostly derive their absorption energy from brittle fracture, delamination, debonding of fibre/matrix or/and fibre breakage (Isaac and Ezekwem Citation2021). (b) gives a pictorial representation of some of the fracture modes of composite structures under failure. Using continuous carbon and glass fibre reinforcements and mixing each with polyamide resin to form composite filaments, Morales et al. (Citation2021) fabricated different sample mass of structures enabled by continuous fibre fabrication technique. The authors identified different failure mechanisms, such as fibre splaying, breakage, debonding, etc., which were also in consonance with the failure mechanisms obtained by energy absorbing composite structures.
Figure 11. (a) Progressive and Euler’s buckling of polymer-based and composite-based 3D printed cylindrical tube of various configurations and (b) schematic illustration of failure mechanisms for composite structures under compressive loading (Wang, Liu, Wang, Yao et al. Citation2022).
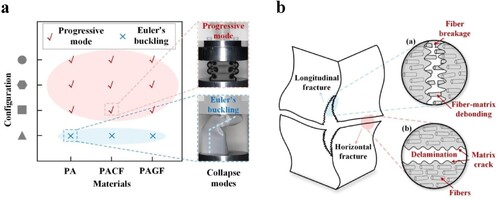
3.3. Multi-materials and hybrid structures
Current research into 3D printing feedstock has also ventured into fabricating energy absorbers made by either blending two or more material feedstocks to realise a multi-material printed structure, or by combining two or more 3D printed structural materials to form hybrid types. Apart from the potential of making complex and customised geometries, multi-material 3D printing technology (Wang et al. Citation2022) can also allow for specific functional inclusions with tailored designs of the EAS. That is, with the advent of multi-material technology, EAS can be tailored such that the Poisson ratio can alternate from zero to a negative value (Chen and Zheng Citation2018; Mishra and Senthil Citation2020).
A common problem with the application of polymeric materials in fabricating multi-material 3D printed EAS is the weak interlocking joints between the multi-polymeric materials. However, the use of appropriate additives can address this problem. In the investigation of Johnston and Kazancı (Citation2021), two polymeric materials (nylon and TPU) were blended with PLA to form the material feedstock utilised for the FDM fabrication process to produce non-auxetic and auxetic EAS. The dual material EAS were compared with EAS made from a single material (i.e. PLA material) under single and multiple loading cycles. The result of their finding pointed out that higher energy absorption capacity was obtained for the single material anti-tetrachiral EAS when subjected to single loading cycle conditions. In achieving bi-material structures a dual extrusion head is currently used. To integrate more functionalities as well as accommodate a wide array of feedstock materials for multi-material 3D printing of structural parts, Roach et al. (Citation2019) introduced a multi-material multi-method technology. This 3D printing multi-material technology was designed to allow at least four different 3D printing technologies with two additional technologies to print a structural part on a single platform. With this technology, unique structural single EAS with different mechanical properties can be realised. Moreover, 3D printing technologies enabling the alteration of material properties are promising techniques that could be used to realise EAS through 4D printing technology (Khoo et al. Citation2015). In 4D printing, the 3D printed structure has the capacity to change due to external stimulus (Bodaghi et al. Citation2020; Liu et al. Citation2020).
Hybridisation techniques are now used by few research groups to further foster mechanical properties and enhance energy absorption capacity of 3D printed EAS (Li et al. Citation2020; Sun, Guo, and Shim Citation2021; Teimouri, Mahbod, and Asgari Citation2021; Acanfora et al. Citation2021). The hybrid structure formed by combining aluminium and nylon can improve the energy absorption capacity as compared to structure made only from nylon (Fu, Zhang, and Huang Citation2021). The unfavourable effect of interlayer fracture which arose during the crushing of 3D printed EAS made from nylon was reduced when a nylon and aluminium hybrid structure was crashed axially. The interaction between the metallic tube and the 3D printed nylon configuration resulted in the increase of lobes, thereby, strengthening the mechanical properties and improving the crashworthiness characteristics. The axially crushed structure also showed a progressive buckling mode.
An FDM cylindrical structure made from PLA was combined with a honeycomb double circular configuration also made from PLA (Wang et al. Citation2021). By subjecting the hybrid structure to a hybrid quasi-static loading, it was reported that the core layer interaction with the structural walls of the tubes was improved greatly. This also determined the kind of deformation mode generated and the deformed modes were evidently different from those derived only from PLA honeycomb configuration. 3D printed hybrid structure can, therefore, be tailored to provide useful information about the microstructural parameters, which can in turn be channelled into producing very lightweight EAS with desirable mechanical performance.
A metallic layer manufactured by the cold spray deposition technique was used to coat a composite laminate with basalt reinforcement (Papa et al. Citation2020). Under impact, the treated structure showed fewer amounts of fractures, increased initial rigidity and reduced maximum force. Sang et al. (Citation2019) combined a 3D printed hybrid polymeric composite (i.e. PLA-PCL/Ba) with a 3D printed FDM circular honeycomb to form a hybrid honeycomb structure. The addition of polycaprolactone (PCL) to the polymeric composite significantly enhanced interfacial bonding. The hybrid structure was reported to give superior energy absorption capability due to the improved interfacial fibre-matrix bonding as well as the ductile behaviour of the matrix material. Moreover, hybrid composite feedstocks (i.e. PEEK/CFR-PEEK) which is a combination of polymer and composite feedstocks as investigated by Jiang et al. (Citation2022) enable to generate very promising materials that can be utilised to produce 3D printed EAS that have optimal result in their energy absorption efficiency.
4. Cellular 3D printed energy absorbers
Cellular structures are good impact absorbers, lightweight and have a high strength-to-weight ratio. They consist of inter-connected networks of thin-walled structures, shells, struts and unit cells. They can also be found in naturally occurring materials such as cork, bone and wood. Additively manufactured cellular structures for energy absorption applications have been structurally designed in the form of honeycombs, foams and lattices. While foams possess random connectivity of their unit cells, honeycombs and lattices on the other hand, possess regular connectivity. The application of additive manufacturing to fabricate cellular structures can further reduce their weight. To this end, most researchers have studied the relative density characteristics (i.e. porosity) of additively manufactured cellular structures and how this parameter influences the energy absorption performance of the structure. Other factors that influence the property and performance of cellular structures are their geometrical (i.e. shapes and forms), morphological (i.e. open or closed cell) and topological (i.e. regular or irregular) features. Some selected cellular structures including honeycomb, foams, lattices and triply periodic minimum surface are discussed in subsequent subsections.
The design and fabrication of more complex structures of energy absorbers have been made easy via 3D printing technology. Crashworthiness parameters and performance of 3D printed energy absorbers are significantly influenced by the way they are built. Moreover, the designs and cell arrangements of cellular structures also contribute to their overall mechanical and impact responses. In this section, the energy absorption, energy absorption efficiency, specific energy absorption, peak load and crush load efficiencies of recently investigated 3D printed EAS, are analysed
4.1. Honeycomb structures
The honeycomb cellular structures fabricated by 3D printing have become popular because of the promising potential to absorb energy. Geometrical and topological modifications of honeycomb structures have led to manufacturing honeycombs with the negative Poisson ratio (NPR) (Wang et al. Citation2022; Li et al. Citation2018). Honeycomb structures exhibiting such property are referred as auxetic honeycomb structures (AHSs). The realisation of NPR makes the honeycomb structure to have improved toughness as well as resistance to shearing during bending. Some common auxetic structures already investigated include re-entrant, chiral, anti-chiral, re-entrant chiral auxetic to mention a few (Zhang et al. Citation2020; Usta, Türkmen, and Scarpa Citation2021; Johnston and Kazancı Citation2021).
4.1.1. Shape/topological modifications
A regular honeycomb structure has six sides and is normally referred as a regular hexagonal honeycomb (RHH) (Habib et al. Citation2017). The compressive characteristics and energy absorption of RHH are determined by their slenderness ratio – defined as the thickness to the length ratio of the unit cell wall. During compression of RHH, as the slenderness ratio increases, the plateau stress lengthens and the densification strain decreases which in turn increases the energy absorption capacity of the RHH. The in-plane loading in the x-direction is more stable and smoother in the plateau stress region than when loaded in the y-direction. Therefore, there is a slight but significant increase in the energy absorption of RHH under in-plane loading in the x-direction compared to that in the z-direction.
3D printing technology has allowed fabricating honeycomb structures with various topological modifications as shown in . Twisted honeycomb EAS were compressed with a straight honeycomb configuration (Lin et al. Citation2021). Relative density was reported to decrease with an increased twist angle of the honeycomb structure. The study revealed that the stress distribution of honeycomb EAS can be significantly affected by various twist angles. At a twist angle of 30°, the twisted honeycomb structures possessed the highest energy absorption and specific energy absorption compared to the other structures with various angles (i.e. structure with 0o twist angle). However, the twisted honeycomb structure suffers the danger of decreased stress distribution when it undergoes fractures which adversely affect the efficiency of the energy absorption. Another study showed that an irregular tailored hexagonal honeycomb structure out-performs the non-tailored ones in energy absorption up to 60% (Andrew et al. Citation2019). Octagonal honeycombs with regular and irregular topologies have been investigated by Xu et al. (Citation2020). The authors subjected these configurations to out-of-plane loading and compared them to an RHH structure. It was shown that the RHH structure has a slightly higher energy absorption capacity than the octagonal ones. However, for the octagonal honeycomb, the in-plane crushing was suggested not to be investigated due to their strong periodicity. Moreover, octagonal honeycomb structures can be suitable for crashworthiness application where stable deformation is highly desired.
4.1.2. Graded configurations
Researchers are now taking advantage of 3D printing technology to introduce grading techniques into energy absorbing honeycomb structures (Wei et al. Citation2022). These have led to several tailored design configurations with improved EAS. Functionally graded configurations have the potential to maximise and control the amount of materials in the honeycomb design contributing to plastic deformation. Gradation of structures can be performed along thickness, length or/and width namely lateral, axial and longitudinal gradations, respectively (Isaac et al. Citation2021). Density gradation of honeycomb structures can take the form of ascending (i.e. density increase from bottom to top) or it can be descending (i.e. density increase from top to bottom) or it can have the property of the two (i.e. both ascending and descending), see (a, b) as typical illustrations. In (c), some conceptual grading techniques of honeycomb structures are illustrated and these graded honeycomb filler configurations can be realised via additive manufacturing. Graded honeycomb EAS with the high amount of density layers are well-suited in applications where load bearing, and improved energy absorption are essential (Baroutaji et al. Citation2021). Self-similar gradation of honeycomb 3D printed structures combined with or infilled into thin-walled tubes are promising hybrid techniques for increasing the crashworthiness performance of EAS (Nian et al. Citation2020). The EAS of both the ascending and descending self-similar graded 3D printed honeycomb filled configurations out-performs that of non-graded honeycomb filled tubes in SEA comparison.
Figure 12. (a) Descending graded honeycomb (Bates, Farrow, and Trask Citation2019), (b) ascending, descending and mixed gradation of fractal honeycomb (Liu, Zhang, and Ng Citation2021), (c) conceptual grading techniques of self-similar honeycomb structures (Nian et al. Citation2020) and (d) description of in-plane, out-of-plane and bi-graded honeycomb structure (Wu et al. Citation2021).
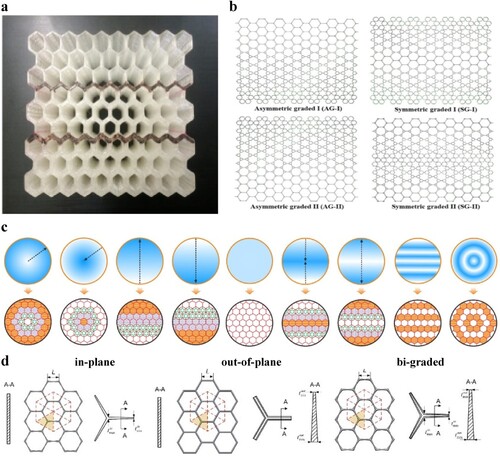
In a recent investigation carried out by Wu et al. (Citation2021), bi-graded regular honeycomb structures were designed in both out-of-plane and in-plane directions as depicted in (d) and compressed under the quasi-static axial loading condition. With the bi-graded configuration, the peak crushing load was decreased and the SEA value was increased up to 45.6% compared with the regular honeycomb structure. Another form of grading pattern, namely graded fractal honeycomb configurations were designed as shown in (b), and their crushing performance was investigated by Liu, Zhang, and Ng (Citation2021). The architectural honeycomb energy absorbing configurations consisted of two kinds of asymmetrically graded honeycombs, two kinds of symmetrically graded and one self-similar uniformly graded honeycomb. Although only the numerical investigation has been carried out, it is worthwhile fabricating these novel architectural configurations with 3D printing technology. The authors’ investigation revealed an 89% and 17% increase in the absorption energy under low and high impact velocities, respectively of the graded fractal honeycomb configurations over their convectional hexagonal honeycomb counterparts.
The idea of density gradation stems from the fact that cellular structures such as the honeycomb structures can be formed by the partial variation of the ratio between their cell wall and their cell size, to achieve a very lightweight structure useful for energy absorption application. Using an FFF technique with TPU material feedstock, Bates, Farrow, and Trask (Citation2019) manufactured a descending graded thickness honeycomb structure which was subjected to quasi-static loading conditions. The thickness of the honeycomb increases in the direction of impact (i.e. from top to bottom) as shown in (a). Under extreme loading conditions, there are low stress which can be transferred by the density graded structure. Also, at low compression energies, there were gains in the energy absorbing efficiency of the graded configurations up to densification compared to the non-graded density honeycomb configurations.
4.1.3. Hierarchical designs
3D printed hierarchical order of honeycomb cellular structures are being developed lately to improve specific strength and to mitigate the unfavourable effect of failure during crushing. Hierarchical honeycomb structures are achieved by either replacing their cell walls with smaller self-similar features as shown in (a) or by replacing the honeycomb vertices with smaller self-similar features as shown in (b). It is also promising to replace either the cell walls or the vertices of the honeycomb with a smaller non-similar feature as shown in (c). These smaller non-similar or self-similar features are called sub-structures and the concept has yielded improvement in strength and crashworthiness of 3D printed EAS. Different levels of hierarchical orders have been identified by several research work for easy structural analyses (Huang et al. Citation2021; Zhang et al. Citation2016; Tao et al. Citation2019; Chen et al. Citation2018).
Figure 13. Honeycomb hierarchical design (a) cell walls are replaced with smaller honeycombs (Li et al. Citation2020; Huang et al. Citation2021), (b) vertices are replaced with smaller honeycombs (Zhang, Lin et al. Citation2021) and (c) cell walls are replaced with smaller non-similar sub-structures (Chen et al. Citation2018).
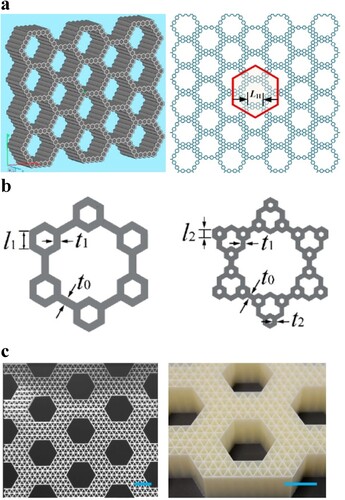
In-plane and out-of-plane crushing of 3D printed hierarchical honeycomb structures are currently being studied by researchers (Chen et al. Citation2018; Zhang et al. Citation2021; Li et al. Citation2020; Tao et al. Citation2019). Increasing the relative density and the order of hierarchy of the honeycomb can result in the change of their deformation mode from cell-wall bending to cell-wall fracture. The deformations of hierarchical honeycomb are controlled by bending, axial and shear collapse of the cell walls. Increasing wall thickness reduces the strength of the bending collapse mode but strengthens both axial compression and shear collapse of hierarchical honeycomb structures. It was reported by Zhang et al. (Citation2021) that a non-heat treatment aluminium alloy hierarchical honeycomb fabricated by SLM technology, achieved more increased in-plane compressive strength as well as elastic modulus than when the configurations undergo heat treatment. The authors attributed this result to the high tensile strength and elastic modulus of the aluminium alloy. With a tailored hierarchical design of honeycomb, the crush load efficiency (CLE) can be achieved to give nearly unity. This was demonstrated by Li et al. (Citation2020) where the designed honeycomb specimen had three layers of small similar honeycomb sub-structures. The configuration was obtained from PLA with FDM technology and subjected to in-plane dynamic compression. Though the CLE increased up to 100%, however, the SEA and specific total efficiency were slightly decreased due to shorter densification strain. Therefore, the numbers and sizes of cells as well as cell wall thickness of hierarchical honeycomb structures contribute to their overall crushing performance.
A very recent investigation on the energy absorption of the self-similar honeycomb structure with hierarchical strategy of replacing the honeycomb cell walls and vertices with smaller similar hexagonal features was performed by Liang et al. (Citation2022). They obtained a prototype of PLA and metallic samples by FDM and wire cutting technologies, respectively and subjected these samples to in-plane quasi-static compression. The study showed that the investigated structures can be used to achieve multi-stage energy absorption performance with stable characteristic collapse features. Moreover, it will be interesting to investigate and compare the crushing performance of 3D printed polymer or composite-based hierarchical honeycomb energy absorbing configurations with their metallic counterparts fabricated by non-additive manufacturing technology.
Apart from crushing the hierarchical honeycomb in the in-plane direction, few authors, on the other hand, have investigated the out-of-plane compression of hierarchical honeycomb. For example, Huang et al. (Citation2021) investigated the out-of-plane response of hierarchical honeycombs of various shapes. One of the hierarchical honeycomb designed configurations was reported to give a surprising increase in CLE and SEA values of about 241.3% and 249.1%, respectively. This report confirms the earlier results obtained by Li et al. (Citation2020) of achieving a CLE value up to unity, thereby, debunking the traditional idea that an EAS cannot have 100% crushing load capability.
4.1.4. Auxetic patterns
Shape modifications of 3D printed honeycomb structures have led to the fabrication of EAS with NPR referred as auxetic cellular honeycomb structures. This category of structures transversally decreases in size in one or many directions after subjecting them to longitudinal compression. The converse is also true, i.e. they can increase in size transversally after being stretched in the longitudinal direction. As a result, they possess excellent mechanical properties, high impact resistance, low bulk modulus, improved specific strength and enhanced shear stiffness (Zhang, Lu, and You Citation2020). The utilisation of 3D printing technology has enabled novel honeycomb structures with different auxetic patterns. For examples, three improved star honeycomb patterns with different cell-wall angles were 3D printed using SLM technique with stainless steel as the parent material feedstock (Wei, Zhao, Yu, Zhang, et al. Citation2021). While the collapse modes were not significantly influenced with cell-wall angles, the energy absorption capacity on the other hand was improved with cell-wall angle reduction. These forms of honeycomb designs can be used to enhance the stability of collapse mode during in-plane compression and can also exhibit the NPR effect. However, under compression in different directions, the NPR can be influenced. For instance, when loaded in the vertical y-direction, the NPR can be greater than when loaded in the horizontal x-direction (Wei, Zhao, Yu, and Zhu Citation2021). (a) shows how a regular honeycomb structure is transformed to re-entrant honeycomb.
Figure 14. (a) RHH structure transformed into auxetic re-entrant honeycomb structure with varying re-entrant angle and (b) SLM fabricated cylindrical steel tube with auxetic re-entrant hierarchical patterns (Lee et al. Citation2019).
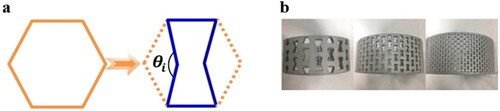
A cylindrical steel honeycomb energy absorber with three auxetic re-entrant hierarchical patterns as shown in (b) was fabricated by Lee et al. (Citation2019) using the SLM technique. The densification of the re-entrant honeycomb tube under quasi-static and low velocity impact loading resulted in improved SEA value and superior damping performance over the traditional honeycomb. Other re-entrant honeycomb EAS has been constructed by different authors (Zhang et al. Citation2020; Sang et al. Citation2019; Wang et al. Citation2022; Gao, Liao, and Wang Citation2020). The angle of re-entrant can also influence the NPR effect. As the re-entrant angle becomes large, the NPR becomes zero and eventually behaves like the traditional honeycomb structure with a positive Poisson ratio. Therefore, smaller re-entrant angles give improved energy absorption capacity with higher NPR effects for structures under complete deformation (i.e. when it enters densification stage).
4.1.5. Shape memory effects
Honeycomb designs made from polyamide and fabricated using the SLS technology have been adopted to give a kind of gradient negative stiffness where the unit cells change throughout the honeycomb thereby enabling recovery of energy absorption characteristics (Chen et al. Citation2021). This kind of structure combines the advantage of NPR effect and energy absorption recovery and reusability. The disadvantage of honeycombs with negative normal stiffness is their local unstable characteristics during loading. However, gradient negative stiffness honeycomb structures are capable of eliminating the total unstable tendency as well as regulate the collapse sequence of each layer of the structure. Furthermore, this gradient negative stiffness honeycomb design has lower initial peak load response which fortifies the claim of its superiority in energy absorption over the negative normal stiffness honeycomb structure. The lower the peak load of an energy absorber the more efficient it is for crashworthiness application. Shape recovery of honeycombs has been investigated by a few studies (Zeng et al. Citation2021). When thermally induced, the additively manufactured honeycomb EAS made from composite (i.e. Fibre + thermoplastic matrix) was reported to have a 95% shape recovery when loaded in the in-plane direction at strain value up to 0.5. Structural honeycombs have also shown the potential of being used to replicate EAS that has the capacity to withstand fracturing even after several, repeated compressions (Bates, Farrow, and Trask Citation2016).
4.2. Cellular foams
Additive manufacturing technology has become so promising that it enables the fabrication of cellular foams applied in industries where load bearing and energy absorption are desired. Polymeric and metallic foams are the two common classes of foams which are adopted for energy absorption investigation. These foams can be open cell (Zeinalabedini et al. Citation2016) or closed cell (Kader et al. Citation2020) foams. For metallic foams, the closed cell design has been analysed to outperform the open cell ones due to their higher elastic stiffness and strength (Kader et al. Citation2020). When the cell walls from closed cell foams are removed they form partially closed cells which consequently result in the lowering of their mechanical stiffness attributes. A well-structured closed cell foam is preferred to random foams because of their potential to exhibit better energy absorption. The inhomogeneous pore diameter in the randomly closed cell foams weakens their elastic stiffness during plastic loading or impact which is why they collapse at low yield strength. It is noteworthy that the open cell foams typically demonstrated randomly dominated modes i.e. bending and twisting/buckling while the closed cell foams collapse by stretching-dominated mode (Novak et al. Citation2021).
4.2.1. Graded foams
The gradient distributions of foams have a significant effect on their mechanical behaviour when subjected to dynamic loading. This was demonstrated by Duan et al. (Citation2020). It was shown by the authors that the onset collapse of graded foams takes place where their density regions are the lowest and then they move to an increased density region layer-by-layer. When the lowest density region was positioned at one end, the plateau region experienced gradual extension. However, when the highest density region was positioned at the end of the graded foam, an initial sharp variation occurred after which a gradual extension of the plateau region became noticeable. Additively manufactured polymeric graded foams have shown promising applications for enhanced energy absorption. Tailored polymeric graded foam fabricated using jet fusion printing technology with polyamide 12 as the feedstock material was investigated to evaluate their compressive mechanical performance (Jiang et al. Citation2021). The hybrid graded foam, which was one of the variant foams fabricated, was reported to increase by 141% and 32% in SEA value over graded lattice configuration and the triply period minimum surface configuration, respectively. This indicates that by using the proper material and well-selected design procedures, 3D printed graded foams can actually improve specific stiffness that can optimise the crushing response of EAS.
4.2.2. Structure-foam hybrids
Foams are used for reinforcement of energy absorbers to enhance crushing performance (Kao et al. Citation2018). 3D printed truss realised via the SLM technology and reinforced with polyurethane (PU) foam as depicted in , has been shown to produce controlled stiffness with lightweight advantage (Chapkin et al. Citation2021). Moreover, when combined with auxetic structures at low-velocity impact, foams can considerably improve the SEA value of hybrid EAS. A polymeric chiral-shaped auxetic frame was filled with visco-elastic open cell foam to form a hybrid structure which was used to investigate its energy absorption under localised impact (Airoldi et al. Citation2020). The localised impact indentation was performed using two different speeds, i.e. a quasi-static speed of 1 and a dynamic indentation speed of 500
. The EAS was reinforced with aluminium alloy to prevent the absorbing surface from local buckling. The result indicates an enhanced energy absorption capacity of the hybrid structure under localised crushing. In particular, the EAS nearer the contact zones were densified by the auxetic chiral frame while the foam supported the ligament of the frame. This effect resulted in the improvement of the SEA capability. In another investigation, a hybrid structure consisting of a PLA honeycomb structure manufactured by the FDM technology was filled with cellular foam (Yan et al. Citation2020) and subjected to in-plane compression. It was reported that the hybrid EAS exhibited improved mechanical performance compared to the empty honeycomb structure. Under out-of-plane loading, the hybrid structure increased in compression strength up to 23.5%. However, it was observed that there was no significant increase in the energy absorption capacity during out-of-plane compression loading. When foams are sandwiched between structural plates, they show lightweight property under low impact energy. However, at increased energy, the foam core structure can be characterised by reduced impact resistance (Usta, Türkmen, and Scarpa Citation2021).
Figure 15. Reinforcing SLM manufactured truss with the PU foam (Chapkin et al. Citation2021).
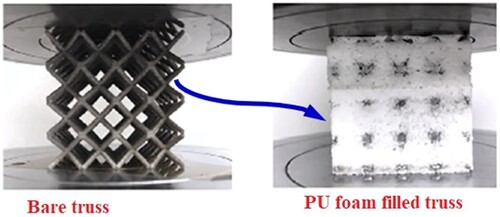
4.3. Lattice structures
4.3.1. Dominating collapse modes
Energy absorbing lattice structures are well known to give high-specific strength and stiffness. Under compressive loading, their deformations are mostly dominated either by stretching or bending modes depending on several factors (i.e. geometrical features, relative density, etc.) influencing their collapse. The stretching-dominated structure is characterised by high initial yielding with extended plateau stress region. The bending-dominated structure on the other hand has a shorter plateau stress region but a smoother stress response. It was reported by Zhang et al. (Citation2021) that stretching-dominated lattice structure has better energy absorbing characteristics and SEA than bending-dominated lattice structure. Contrary to Zhang et al. (Citation2021) report, the energy absorption efficiency and SEA value obtained when relative density was 0.2 for bending-dominated structure, was reported to be higher than the stretching-dominated ones (Nasrullah, Santosa, and Dirgantara Citation2020).
Various complex 3D printed energy absorbing lattice structures are gaining recognition for crashworthiness applications. Such architectural lattices include but not limited to kagome (Wei et al. Citation2018), gyroid (Wang et al. Citation2020), double gyroid (Maskery et al. Citation2017), diamond (Neff, Hopkinson, and Crane Citation2018) and octet truss (Tancogne-Dejean, Spierings, and Mohr Citation2016; Ling et al. Citation2019) as represented in . For the kagome lattice structure manufactured by SLM technology (Wei et al. Citation2018), the average compressive strength and bending load were raised from 2 to 17.5 MPa and 260 N up to 1750 N, respectively. Buckling of the structure occurred before strut fractured. Moreso, the structural lattices were designed based on their failure model. For example, the kagome lattice was designed as a fracture when the relative density was lower than the critical value. Also, it was designed as bending when the relative density was higher than the critical value. In the case of the gyroid lattice cylindrical structure (Wang et al. Citation2020), a globally uniform crushing mode was recorded. Under compression, the gyroid lattice showed more improved load bearing capacity and energy absorption with increase in relative density. With gradient factor consideration on the gyroid structure, there was a likelihood of the structure deforming layer-by-layer. For the double gyroid made from aluminium alloy through the SLM technology (Maskery et al. Citation2017), the cell size was a determining factor in the failure mechanism. A small cell size can prevent structural failure due to low strain. Lastly, the octet truss lattice made from stainless steel as depicted in (e) was fabricated via the SLM technology such that it possesses zero Poisson ratio (Tancogne-Dejean, Spierings, and Mohr Citation2016). Additionally, the octet truss in (e) with different strut radii was printed via the SLA technology with material feedstock from two polymer-based materials. In general, the deformations of octet truss EAS are highly influenced by the type of material used and they are particularly useful in application where multiple impacts are required.
Figure 16. Various lattice structures (a) kagome (Wei et al. Citation2018), (b) gyroid (Wang et al. Citation2020), (c) double gyroid (Maskery et al. Citation2017), (d) diamond (Neff, Hopkinson, and Crane Citation2018) and (e) octet truss with different strut radii R (Ling et al. Citation2019).
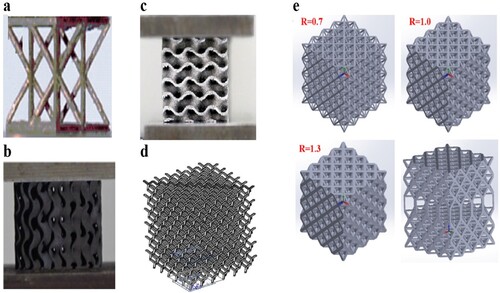
Apart from the cell sizes (for example, strut diameter as described by Tafazoli and Nouri Citation2022) and the cell topologies, relative density also plays a very important role in determining mechanical and crushing performance of lattice structures. Studies have shown that as the relative density increases, energy absorption capacity tends to increase irrespective of the EAS being characterised by either stretching or bending-dominated collapse mode (Nasrullah, Santosa, and Dirgantara Citation2020). The twisted octet lattice showed bending-dominated mode when the relative density was below 0.2 while above this value, the twisted octet lattice showed stretching-dominated collapse response. This transitional change resulted in reduction in energy absorption of the twisted octet lattice as the relative density increased from 0.2 to 0.25.
4.3.2. Shape-based lattices
Other shape configuration 3D printed lattices that have been configured as energy absorbers are the multi-circular lattice (Wang et al. Citation2021), hexagonal lattice (Dong and Fan Citation2022), octahedral lattice (Bai et al. Citation2020), cubic lattice (Wang et al. Citation2021; Wang et al. Citation2020; Shen et al. Citation2016) and hollow-walled lattice (Noronha et al. Citation2021). The hexagonal lattice is a similitude of the honeycomb structure. When subjected to in-plane loading, no outstanding energy absorption results were obtained. With out-of-plane compression, the initial peak force can be very high, and the CLE is not as competitive as for other energy absorbers. A buckling orientation systemic solution can be adopted to lower the initial peak force and consequently lead to increment in the CLE of the hexagonal lattice structure. The hexagonal lattice with this buckling orientation pattern can achieve maximum SEA when subjected to quasi-static in-plane loading condition. However, under out-of-plane loading condition, the crushing parameters such as the SEA and MCL can become decreased compared to those of the conventional hexagon lattice.
Using the SLM technology, Nasrullah, Santosa, and Dirgantara (Citation2020) designed various shape-based lattice structures including octet, kagome, tetrahedron, octahedron, open cell, truncated pyramid, pyramid, cube, rhombicuboctahedron and rhombic dodecahedron. In their investigation, bending-dominated crushing modes were observed for the cube open cell, kagome, truncated pyramid, cube, tetrahedron and pyramid lattice structures. However, for the octet, octahedron, rhombicuboctahedron and rhombic dodecahedron lattice structures, stretching-dominated crushing responses were evident. It was also observed that the octet lattice gave higher energy absorption capacity when dominated by bending collapse mode than when dominated by stretching collapse mode. The investigation of the authors showed that the deformation mode of lattice structures can be driven by their geometrical features.
To further improve the crushing performance of lattice structure, the unit cell pose can be varied (Bai et al. Citation2020). The study was performed to establish the influence of unit cell pose on the relative density as well as mechanical characteristics of different octahedral lattice structures. The rotation of these structures along their single-axis angle of pose had a great effect on their mechanical properties. For optimised mechanical properties at and at the same strain, the best energy absorption capacity was achieved.
4.3.3. Cubic lattices
The unit cell lattice can be changed to form various cubic lattice structures. These cubic lattices that have been commonly investigated for energy absorbing applications include the body centred cubic (BCC) (Li et al. Citation2021; Yuan, Chua, and Zhou Citation2019) and the FCC (Jin et al. Citation2019; Mazur et al. Citation2016; Leary et al. Citation2018; Wang et al. Citation2021). When compressed, these structures have the tendencies to form different deformation patterns such as T, X, N or I-pattern (Li et al. Citation2021). However, a typically identified deformation pattern in a lattice structure can be adjusted from one pattern to another pattern to obtain better energy absorption capacity. Controlling the mechanical properties is a promising possibility which lattice structures offer. Specific elastic strength and modulus of lattice structure can be improved using a curving strategy proposed by Bai et al. (Citation2021). In their work, BCC, FCC, BCT and F2BCC lattice structures as shown in were fabricated using the laser powder bed fusion (SLM) technology with titanium alloy as the parent material. The unit cell of each design type was strategically curved to give a curving unit cell of each original design which was also manufactured using the similar SLM technique. The result of their finding showed a 53–184%, 46–107% and 50–150% increase of the curved lattice in elastic modulus, compressive strength and yield strength, respectively. Moreover, the optimum curved lattice structure at 50% stress surprisingly showed total energy absorption of 571.4% over the traditional straight BCC lattice.
Figure 17. Various configurations of 3D printed cubic lattice structures (Bai et al. Citation2021).
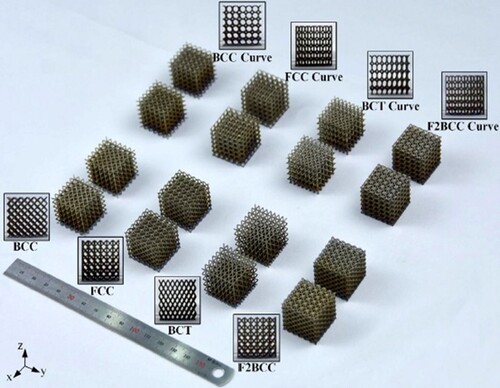
Still on the deformation pattern of FCC and BCC lattice structures, it has been reported that the former and latter are dominated by stretching and bending, respectively (Jin et al. Citation2019) with failure initiating from their face truss connection points. Under the same parametric and loading conditions, FCC lattice structures showed better mechanical properties and energy absorption capacity over the BCC lattice structures. The results outcome further confirms that lattice structures with the stretching-dominated collapse mode result in higher mechanical properties and improved crashworthiness performance over lattice structures characterised by bending-dominated deformation mode. A possible reason why the mechanical property of BCC lattice structure is lower than their FCC counterpart is due to its higher tendency of stress fluctuation especially during the plateau stage and this is as a result of its tighter struts buckling (Zhang et al. Citation2018).
In another investigation, the collapse and fracture behaviour of titanium cubic lattice EAS fabricated by SLM technology was examined by Mazur et al. (Citation2016). Some of the influencing factors such as cell size, topology, unit cell etc., contributing to the performance of the structure were studied. The BCC lattice structure was again reported to give the lowest mechanical performance amongst FCC with struts, and face body centre cubic with strut lattice structures. Following the same trend, Leary et al. (Citation2018) showed that additional vertical struts to FCC lattice structure out-performs both FCC and BCC lattice structures while the BCC configurations gave the lowest energy absorption capacity due to their lower yield and shorter plateau region (i.e. with bending-dominated deformation mode resulting). However, the energy absorption of BCC lattice can further be enhanced by using alternating vertical struts as demonstrated by Turner et al. (Citation2018). Additionally, the improved FCC and BCC strut lattice energy absorbers with improved strength and stiffness are particularly suitable for application where mechanical properties can be lost due to elevated temperatures.
4.3.4. Functionally graded lattices
To improve both the specific strength and the SEA of lattice EAS, the strut or cell walls can be density graded either step-wisely or continuously. With graded strategies on lattice structure (Mueller and Shea Citation2018), the collapse or deformation mode can be greatly controlled. Under compression, collapse of graded strut typically begins from a less densely layer, through layer-by-layer, to a more densely layer. Contrary to the non-graded structures that produce sudden and unexpected failure modes, the deformation mode of graded structures on the other hand can be distinct and predicted. That is, it moves from localised or global failure mode to progressive or gradual failure mode. Gradient lattice manufactured by SLM technology (Xiao and Song Citation2018; Maskery et al. Citation2016; Choy et al. Citation2017; Al-Saedi et al. Citation2018) or by SLA technology (Niknam and Akbarzadeh Citation2020; Nian et al. Citation2021) can be inserted into energy absorbing tubes and subjected to quasi-static, low, dynamic and transverse loading conditions. Under compressive loading, prior failure of graded lattice structure, strain can be distributed uniformly and when the strain rate increases, the deformation strength can be increased up to 25%. Moreover, the energy absorption per unit volume for functionally graded lattice structure, exponentially increase as strain function increased. Initial global failure of graded lattice structure can be a result of localised bending and fracture at regions where the density layers of the struts are very low. At high-density layers, localisation due to bending and fracture is not obvious owing to the reduced cell sizes (Xiao and Song Citation2018).
Graded lattice structures have served as fillers to EAS tubes to further enhance crushing characteristics and improve energy absorption capacity. Investigation was carried out by Nian et al. (Citation2021) to evaluate the energy absorbing characteristics of functionally graded lattice structure fabricated via SLA technology. The SLA polymer-based EAS was inserted as filler structure into a circular thin-walled tube and subjected to a three-point bending loading condition. The gradation of the filler material was patterned both, radially and axially such that each grading pattern consisted of ascending and descending graded orders as shown in . Results of investigation revealed that the graded pattern contributed significantly to the energy absorption capacity of the composite absorbing tubular structure. That is, circular tubes with radially graded patterns outperformed those with axially graded patterns. Moreover, gradation in the ascending order showed better energy absorption characteristics than both the graded tubes with descending grading patterns and the non-graded lattice-filled circular tubes. Another investigation to study the crushing performance of a direct metal laser sintered aluminium alloy graded lattice structure was carried out by Cetin and Baykasoğlu (Citation2020). The structure was used to fill a thin-walled tube which was then loaded under various impacts. The authors finding showed that reinforcing thin-walled tubes with lattice structure can as well improve the absorbed impact energy up to 146% higher than their individual counterparts loaded separately. Moreover, increased energy absorption can also be achieved with tapered graded lattice hybrid EAS especially during high impact loading.
Figure 18. Functionally graded lattice filler with reduced graded thickness (a) ascending radially, (b) descending radially, (c) ascending axially and (d) descending axially (Nian et al. Citation2021).
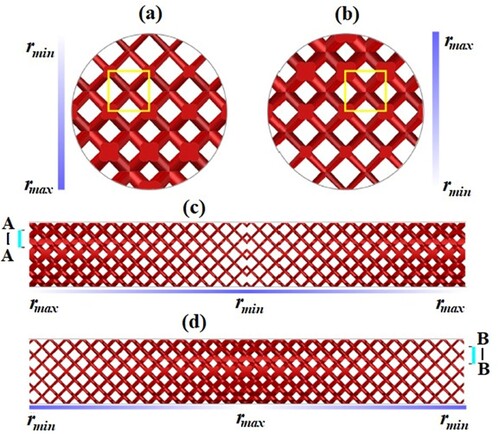
4.3.5. Hybrid lattices
As in graded lattice, a stable deformation pattern during compression can be achieved using a hybrid lattice. To improve the low plateau stress of lattice structures typically dominated by bending mode and to deal with the unstable response after yielding for stretching-dominated lattices, a well-designed hybrid lattice structure can be employed to address these challenges. (a) shows a hybrid lattice structure comprising a bending-dominated outer structure plus an octahedral structure placed inside the outer structure (Sun, Guo, and Shim Citation2021). The hybrid unit cells are assembled to form inter-connected parts of the hybrid lattice structure. Such kind of hybrid design is potentially promising to slow down instability in buckling as well as the catastrophic deformation which can occur during post yielding. Thus, producing a structure which is characterised by a stable collapse mode, high-specific stiffness and strength with improved energy absorption capacity. In (b), an octet lattice is combined with re-entrant hexagon to form a hybrid lattice structure fabricated using the digital light processing technique (Li et al. Citation2020). The realised layered hybrid structure was subjected to various loading conditions, and it was reported that the hybrid lattice structure had stable collapse mode which was evident over the entire loading velocities. Moreover, the specific strength of the hybrid structure outperformed each of the individual traditional lattice, octet truss and re-entrant hexagon by 2.6, 1.3 and 1.8, respectively when it was subjected to high-velocity loading condition. The findings show that by carefully combining two or more unidentical cells to form a hybrid lattice structure using 3D printing, the specific strength of the crushed lattice EAS can be increased especially when loaded at high speed. However, under low-velocity loadings, the specific strength values of the hybrid structure may not increase significantly over those of the traditional lattice structures, octet truss and re-entrant hexagon lattice structures.
Figure 19. Hybrid lattice strategy (a) hybrid lattice unit cell assembled to form hybrid lattice structure (Sun, Guo, and Shim Citation2021) and (b) octet truss joined with re-entrant truss to form hybrid lattice structure (Li et al. Citation2020).
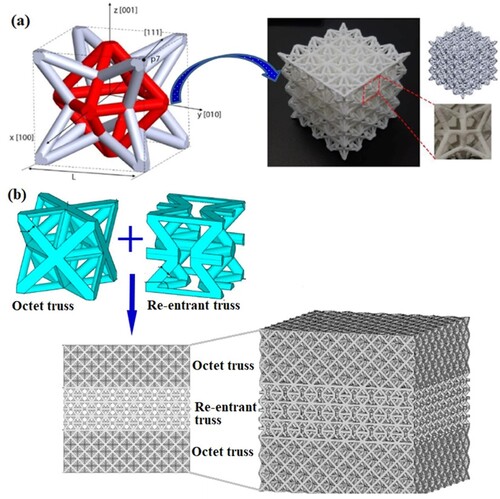
4.3.6. Hierarchical lattices
shows cubic hierarchical lattice structures proposed by Wang et al. (Citation2021) to enhance energy absorption capacity. The hierarchical EAS were manufactured using the SLM technology with steel 316L as the material feedstock. The idea was to increase the number of plastic hinge connections in the unit cell through a hierarchical strategy. This was achieved by substituting the initially straight beams of the lattice structure with circular beams of different curvatures defined as the ratio of the arc height to the length of the unit cell. The straight beams with zero curvature and arc beams with different curvatures were compared with the circular beams of the lattice structure. The conventional straight lattice design formed by making the arc beam to have zero curvature produced V-shaped shear bands during deformation. The curvature of the circular beam acted as triggers during the deformation process which was advantageous to reducing the initial peak force. However, the introduction of diagonal circular struts decreased plateau stress which resulted in stress oscillation and consequently lowering the energy absorption. One of the strategies adopted to curb this effect was to use straight struts only along the diagonal of the lattice structure. Moreover, these struts were substituted with higher level of many arc and circular beams. With these strategies, it was reported that the SEA value obtained can be three times higher from one hierarchical strategy to the other. For example, the hierarchical circular beams were three times higher in SEA value than the hierarchical arc beam FCC lattice structure. This was because of the type of deformation mode formed. The arc beam type produced a one-directional global bending while the circular beam type formed more plastic hinge connections during the deformation process. The additional plastic hinges of the hierarchical lattice structure gave it the potential to move from node-dominated collapse mode to stretching-dominated collapse mode. This was achieved because the voids in the internal lattice structure were being utilised by additional struts and the fortified plastic hinges were linearly connected.
Figure 20. Different configurations and strategic designs of hierarchical cubic lattice structures (Wang et al. Citation2021).
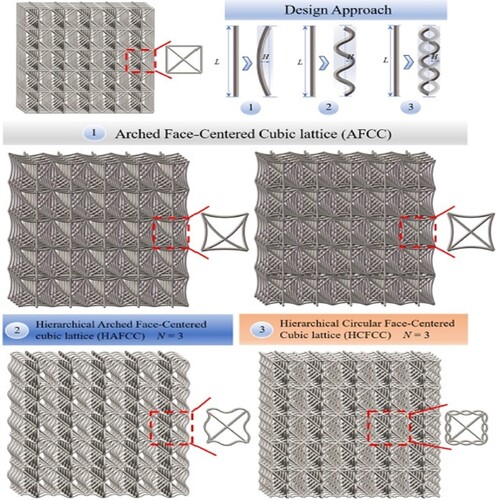
4.3.7. Triply periodic minimum surface (TPMS) lattices
This is a unique family member of lattices which is formed by 3D structures that are mathematically defined i.e. their surfaces are generated with the help of mathematical equations (Abou-Ali et al. Citation2019; Khan et al. Citation2019). They are classified as either skeletal-based TPMS or sheet-based TPMS (Yin et al. Citation2020). The sheet-based are preferably used as energy absorbers compared to their skeletal-based counterpart due to their lightweight characteristics and more excellent energy absorption capability (Li et al. Citation2019). Typical amongst the sheet-based EAS are the primitive, diamond, gyroid or double gyroid. Sheet-based TPMS structures can compete with FCC lattice structures because they both exhibit stretching-dominated modes under compression. This also implies their superiority over BCC and strut-based lattice structures since these two structures are known to exhibit bending-dominated collapse modes during their deformation process. In fact, a heat-treated double gyroid lattice at 50% compression in strain produced a SEA value that was almost three times higher than the values of the BCC lattice structure (Maskery et al. Citation2017).
In the study carried out by Yin et al. (Citation2020), four different types of TPMS lattice structures including the primitive form, gyroid form, FRD form and IWP form as shown in were investigated. Their crushing parameters (i.e. SEA, CLE, and
) were evaluated after subjecting them to different dynamic loading conditions. Results indicated that the FRD lattice structure produced the highest crashworthiness performance when tested with the same loading and parametric conditions applied to all TPMS types. The results are indications that with a strategically well-designed TPMS, the crashworthiness performance can be improved and tailored to the desired application. In a similar investigation carried out by Maskery et al. (Citation2018), the designed TPMS lattice structure was fabricated using SLS with EOS polyamide feedstock. The TPMS lattice structures include the primitive, gyroid and diamond lattice forms. It was reported that the primitive type showed strut stretching as well as buckling, while both the gyroid and diamond types showed bending-dominated modes during compression. The modes formed by the polymer-based additively manufactured TPMS were different from those of the metal additively manufactured TPMS which have stretching-dominated collapse modes. Hence, making the primitive TPMS outperform both the gyroid and diamond lattice type in stiffness and strength. This gives it the advantage of being suited in applications where a defined loading direction is required. Therefore, by properly selecting the geometrical cell of TPMS, lattice structures with unwanted collapse mode can be avoided, and a delayed plastic plateau region can be achieved with enhanced energy absorption. In a similar fashion, Zhang et al. (Citation2018) designed a BCC lattice structure and compared it with three other cellular TPMS lattice structures namely, primitive, diamond and gyroid, as shown in realised by the SLM technique with stainless steel as material feedstock. Crushing of diamond TPMS lattice structure outperformed the other two while the primitive type showed diagonal shear bands alongside with localised buckling of the cell wall. One good advantage of using SLM with metallic feedstock to fabricate TPMS lattice structures is the high-quality print void of macro defects (Li, Xiao, and Song Citation2021; Schneider et al. Citation2022). Overall, the designed TPMS lattice structures outperformed that of BCC lattice structure in compressive modulus, plateau stress and energy absorption owing to their stable collapse modes and smoothly defined geometries.
Figure 21. Various design configurations of triply periodic minimum surface lattices (a) primitive, (b) FRD, (c) IWP and (d) gyroid (Yin et al. Citation2020).
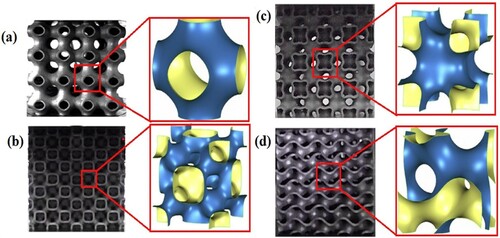
Figure 22. Various design configurations of triply periodic minimum surface lattices (a) primitive, (b) diamond, (c) gyroid and (d) BCC (Zhang et al. Citation2018).
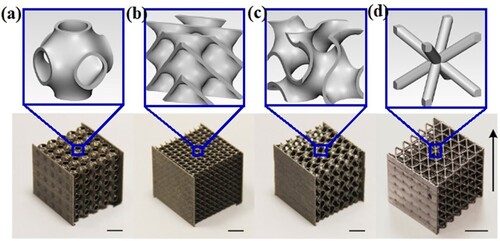
4.3.8. Other forms of lattice designs
Auxetic lattice: Recent 3D printing technological processes have realised lattices with NPR and researchers have started exploring these auxetic lattices for crushing applications (Alomarah et al. Citation2020). For example, Guo et al. (Citation2020) explored the auxetic behaviour of a cylindrical lattice energy absorber realised via the FDM technique with ABS as the printing material feedstock. Albertini et al. (Citation2021) performed both, experimental and numerical methods to give more insight into the mechanical behaviour of auxetic lattice fabricated via the material jetting technique with vero-white as the feed filament. Arjunan et al. (Citation2020) studied the effects of geometric variation on the mechanical performance of lattice structure-walled energy absorber fabricated through the SLM process with aluminium alloy as the feed filament. The effect of building such structures with NPR was that their elastic modulus was increased. Therefore, with ingenious and meticulous selection of design parameters, auxetic lattice structures can be made to outperform their traditional lattice counterparts.
Bio-inspired lattice: Apart from the architectural design of honeycomb cell structure which are originally inspired by the honeybees, other kinds of lattice structural designs used as energy absorbers have been mimicked from animals, plants and molecules (Gu et al. Citation2021; Wang, Qin, and Chen Citation2021; Ingrole et al. Citation2021; Li, Zhi, and Fan Citation2022). For instance, the wing of beetle elytra consisting of epicuticle, exocuticle, mesocuticle and endocuticle as shown in (a) have helicoidal structural design capable of absorbing energy. Inspiration can be drawn from the helicoidal structure to fabricate energy absorbers through additive manufacturing. For example, Du et al. (Citation2020) fabricated lattice structures using the SLM technique with the design structure mimicked from the front wing of beetle as shown in (b). The bio-inspired lattice design was made from aluminium alloy material feedstock and the effects of different process parameters (i.e. scanning speed and laser power) on the densification of the bio-inspired lattice structure were investigated. The bio-inspired structure showed a very high densification up to 99.93% at a scanning speed of 3500 mm/s and a laser power of 450 W. During compression, there was the fracturing of the strut accompanied by a very high stress drop which was due to the transfer of stresses concentrated at the point of intersections of the horizontal to the diagonal struts. It was reported that the bio-inspired lattice design with laser power of 375 W gave excellent energy absorption capacity of 3.45 J. Other investigated bio-inspired EAS such as bio-macromolecule cage lattice structure, etc., that have been realised through additive manufacturing are found in the works carried out by Yang et al. (Citation2021) and Yao et al. (Citation2021).
Figure 23. Bio-mimetic EAS: (a) helicoidal structure mimicked from beetle elytra (Cheng, Wang, and Karlsson Citation2008) and (b) hypersurface lattice structure mimicked from adult allomyrina dichotoma of the beetle front wing (Du et al. Citation2020).
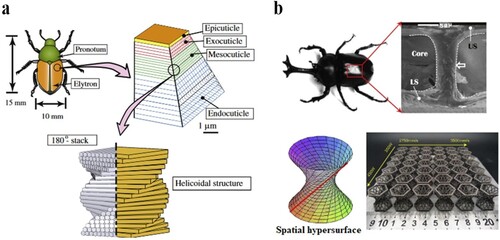
5. Summary, challenges and prospects
Additive manufacturing is opening new possibilities to realising EAS for crashworthiness application. However, some challenges which limit their production over their conventional manufacturing counterpart are still evident. This review has considered different material feedstocks, fabrication technologies and a vast number of structural designs of energy absorbers realised via 3D printing technologies. The challenges, possible solutions and future perspective are herewith given in the following subsections.
5.1. Challenges and possible solutions
(a) shows a plot of different materials (i.e. Young’s modulus against densities) commonly utilised to produce energy absorbers. It is seen that materials made from polymers and composites have low mechanical properties but good lightweight characteristics. However, from the illustrative figure, the 3D printed EAS with composite material feedstocks have promising possibilities to outperform those made from metals and alloys by using short or/and continuous fibre reinforcement. Unfortunately, some FDM 3D printers currently available cannot use composite feed-filaments. It is, therefore, expected that efforts be put towards realising more composite-based 3D printing devices and their corresponding feed filament materials. In (b), the plateau stress of various 3D printed energy absorbing cellular configurations is represented. With steel materials, gradient honeycomb configuration (Wei et al. Citation2022) gives the highest plateau stress followed by the TPMS structures. The plateau stress of bio-inspired steel lattice configurations is higher than the regular BCC lattice counterpart. This shows that a longer and more stable plateau region can be achieved for the BCC lattices by slightly modifying their design, inspired by the features of plants and/or animals. In the same vein, the plateau stress of the regular honeycomb structure (see (b)) can be increased by topologically modifying them to obtain an auxetic property i.e. NPR.
Figure 24. Comparison of (a) material elastic modulus for the four main material feedstocks described in this review and (b) plateau stress of various additively manufactured energy absorbing cellular structures.
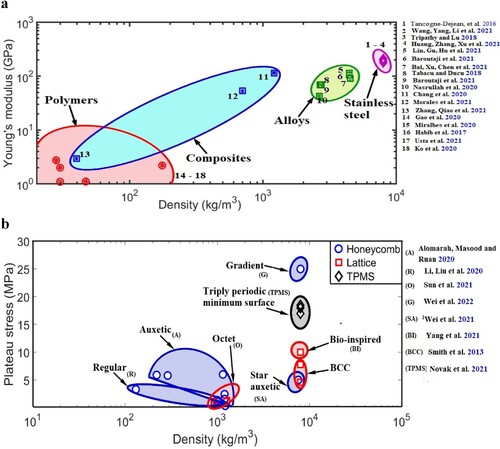
There is an appreciable number of feedstock materials for 3D printing which are currently available. Meanwhile, before these materials are sold out, their mechanical properties should have been tested by the manufacturer or supplier. Unfortunately, detailed information about these mechanical properties and other influencing parameters of the material feedstocks are not completely revealed by the supplier. This review study has shown the challenge of divergent designs with varying values of mechanical properties for the same material feedstock used during the execution stage. Suppliers’ mechanical properties of the feedstock can be divergent from the executors’. This reason has necessitated additional mechanical testing of the feed materials. The additional cost of procuring tensile test equipment and the execution time are constituting major challenges which could dissuade researchers to fully adopt 3D printing technique for creating EAS. Therefore, a simplified, cost-effective method can be developed for material re-testing of the feedstocks before being used to produce the final 3D printed EAS.
Several process parameters as listed in have been considered when using the FDM, SLA, SLM and SLS. However, very little attention has been given to compare and evaluate the effect of processing parameters on the materials used to fabricate the 3D printed EAS. For example, for the FDM technology which typically uses the polymers or/and composite feedstock, process parameters and their effects on the crashworthiness performance of EAS have not been fully studied. Future directions should, therefore, be geared towards optimising the process parameters to realise more effective energy absorbers.
To fully understand the deformation and crushing performance of 3D printed EAS, the crashworthiness performance indexes listed in Section 1.4 should be holistically explored. However, these performance indexes are not exhaustive. During the investigation of novel 3D printed energy absorbers, rapt attention should be given to finding more crushing performance indicators. Until recently, the magnitude of these indexes has not been fully covered in spite of the innovative research carried out on 3D printed energy absorbers. The authors of this review, therefore, recommends that for future innovative design, conscientious efforts should be made to evaluate not just the force–displacement results but also to evaluate novel crushing indicators as well as the crushing performance indexes which are listed in this review work.
This review has also shown that the type of materials used to fabricate 3D printed EAS affect their collapse behaviours which consequently influence their crashworthiness performances. Understanding the failure criteria for each material used for the 3D printed structure especially by using some numerical method approaches as described by Tabacu and Ducu (Citation2020) can greatly help to give the desired failure mode. However, more research should be undertaken to come up with reliable and flexible failure criteria that optimise the energy absorption capacity and crushing performance of the EAS.
During the investigation carried out by the authors of this review and those performed by various contemporary authors, it was found out that samples fabricated via 3D printing and subjected to the same parametric and loading conditions have different values of mechanical properties as well as crushing performance. Though it was mentioned that a possible cause for these discrepancies is the void formation in the printed part due to the anisotropic tendency of the 3D printer. The strategy of pre-heating the bed is being introduced, however, this strategy is still not sufficient to reduce the void formation and local stress concentration during loading. Consequently, reducing the mechanical properties and crushing performance of the printed EAS. However, further directions can be geared towards machine learning of 3D printed parts. This will help to reduce the discrepancy of results obtained by 3D printed EAS and other printed parts.
5.2. Future perspectives of 3D printing materials and energy absorbers
The rapid emergence of 3D printing materials and their application in the production of energy absorbers promises to positively impact the industrial sectors of crashworthiness application. Some future perspectives could be to particularly focus on developing new materials, improving material properties, designing well-tailored structures which are capable of achieving highly optimised crashworthiness performance of 3D printed energy absorbers. One perspective of realising this is to develop an eco-friendly additively manufactured lightweight energy absorber embedded with a sensing device which can be made from nanoparticles such as graphene and carbon nanotubes that are crushing sensitive. The sensing device will have the potential to gather useful information and monitor anisotropy of 3D printed energy absorber which is one of the key issues to be addressed in 3D printing processes. Moreover, the sensing device will be able to detect strain effects, failure modes as well as correctly measure the crushing performance (i.e. the energy absorption capacity) during pre-impact and post-impact. This prospective structural, health and damage monitoring energy absorber, when incorporated in moving vehicles, will ultimately increase the overall effectiveness to protect lives and valuables during mild and catastrophic accident events.
Thus far, polymer-based, composite-based and metal/alloy-based feedstock materials have been commonly utilised to produce 3D printed energy absorbers. However, there are still insufficient research that have been carried out by combining these feedstock materials with nanocomposite filaments to produce 3D printed energy absorber. Nanocomposites, for example, can be obtained by combining certain amounts of nanoparticles to geopolymers and when combined with composite material feedstocks can enhance their mechanical strengths and improve crushing performance of energy absorbers (Spinelli et al. Citation2018).
Majority of the polymers and reinforcement fibres used for both polymeric and composite filaments are synthetically manufactured, and they are generally non-biodegradable. However, natural fibres can be combined with their polymers to give biodegradable composite filaments. A similitude of this approach was demonstrated by Yan et al. (Citation2020). The authors fabricated honeycomb structures using FDM technology with biodegradable PLA materials and filled them with polymethacrylimide. The biodegradable PLA foam-filled structures were seen to have low densities ranging from 282 to 497 with improved SEA. Moreover, a more eco-friendly environment can be sustained by developing 3D printing filaments from green composites. Though the green composite filaments may have low mechanical properties due to their hydrophobic nature and weak interfacial bonding, the addition of appropriate amount of reinforcement additives such as nanoparticles, however, can increase their mechanical strengths. The resulting 3D printing bio-composite filaments can, therefore, be used to produce 3D printed bio/green composite-based energy absorbers and when incorporated in moving vehicles can produce a significantly lightweight advantage with improved fuel economy and less quantity of noxious substances released into the atmosphere. Consequently, producing and sustaining a cleaner and more environment-friendly atmospheric condition.
This review has demonstrated that there is an increasing pace of research efforts on 3D printed energy absorbing cellular structures. The honeycomb cellular structures, for example, have generally shown good crashworthiness performance in terms of energy per unit mass. provides a summary chart of some SEA results of 3D printed energy absorbing honeycomb structures with respect to their material densities. Under quasi-static loading condition, it is seen that the 3D printed functionally graded honeycomb EAS gives the highest SEA values. Moreover, the plateau stress obtained during the investigation of functionally graded honeycomb EAS performed by Wei et al. (Citation2022) was reported to have a very high value up to 25 MPa for stainless steel material feedstock. The hierarchical honeycomb structures from show a slightly higher SEA values than the regular honeycomb energy absorber. However, for wider range of industrial applications, especially for low-density materials, the regular honeycomb structures are good candidates with promising SEA performance. Furthermore, bio-inspired energy absorbing honeycomb structures for low-density materials produce low SEA values. However, their SEA values are seen to increase with increasing density of the parent material utilised to fabricate the energy absorber. Finally, it is also seen from the SEA chat that AHR, for example, re-entrant chiral auxetic, has promising potential of increased SEA values for low-density materials such as nylon (Alomarah, Masood, and Ruan Citation2020).
Figure 25. Specific energy absorption comparison of various 3D printed energy absorbing honeycomb cellular structures.
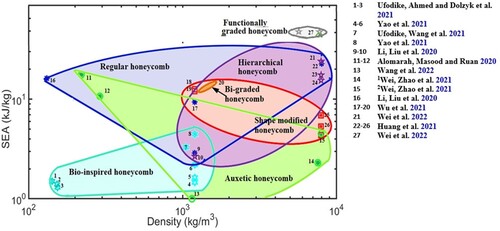
compares the energy absorption capacity of some cellular structures (i.e. honeycomb, lattice and foams) with some 3D printed tubal and sandwich structures when subjected to quasi-static or low-velocity loading condition. The tubal structures can be single or multi-cell and can further be reinforced by filling them with 3D printed lattice, foam or honeycomb cellular structures. Under impact loading, they exhibit a stable deformation mode with remarkable crushing performance (Wang, Liu, Wang, Yao et al. Citation2022; Wang, Liu, Wang, Xiang et al. Citation2022; Fu, Zhang, and Huang Citation2021). Moreover, as shown in , the hierarchical honeycomb cellular structures compete well with the hierarchical honeycomb tubal structures. Also, the bio-inspired honeycomb structures are excellent candidates for energy absorption compared to their bio-inspired cellular lattice structures. For the cellular foams, limited research has been carried out to fully understand their promising potentials as energy absorbers. However, the chiral foam hybrid structure investigated by Bates, Farrow, and Trask (Citation2016) showed remarkable energy absorption capacity. Sandwich structure with well-tailored 3D printed architectural cores can also give promising energy absorption performance. Finally, there are still more investigations that need to be carried out to improve the crashworthiness performance of 3D printed cellular, tubal and sandwich structures.
Figure 26. Energy absorption comparison of various 3D printed energy absorbing cellular, tubal and sandwich structures.
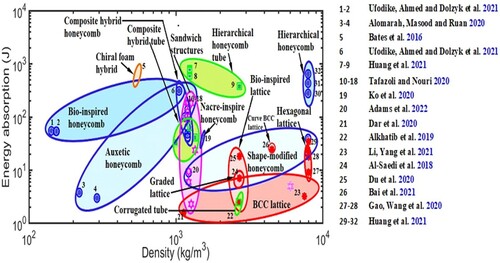
In summary, this review paper has shown that by controlling several 3D printing parameters, material feedstocks and structural designs, the mechanical response and crashworthiness performance of energy absorbers can be tuned to give the desired optimal results. Consequently, resulting in a more efficient protective package and better mitigation of crash scenarios for automobiles, aircrafts and other moving vehicular structures.
Disclosure statement
No potential conflict of interest was reported by the author(s).
Additional information
Notes on contributors
Chukwuemeke William Isaac
Dr. Chukwuemeke William Isaac studied Mechanical Engineering at the University of Ibadan, Nigeria and further obtained a research master's degree in Computational Mechanics at École Centrale de Nantes in 2013. He proceeded to obtain his Ph.D. in Applied Mechanics at the University of Ibadan in 2018. He then worked as a Postdoctoral fellow in the Department of Measurement, Faculty of Automatic Control, Silesian University of Technology (SUT) until 2021. He is currently an Assistant Professor in the Department of Machine Technology, Faculty of Mechanical Engineering, SUT, where he is actively engaged in the research of additively manufactured polymer-based, composite-based, and metal-based energy absorbing structures.
Fabian Duddeck
Prof. Dr. Fabian Duddeck studied civil engineering at the Technical University of Munich (TUM) finishing with a Ph.D. (1997) and a Habilitation in Mechanics (2001). Then, he worked at BMW/Munich until 2005 when he became Reader of Computational Mechanics at Queen Mary University of London (until 2020). In addition, he was Maître de Conférences at École des Ponts ParisTech (2006-2016). Since 2010, he is professor for Computational Mechanics at TUM leading a research group on optimization of structures for aerospace and automotive problems (e.g. crashworthiness). His group is working on structural optimization, nonlinear model order reduction, isogeometric analysis, uncertainty propagation, material modeling, crashworthiness, etc.
References
- Abou-Ali, A. M., O. Al-Ketan, R. Rowshan, and R. Abu Al-Rub. 2019. “Mechanical Response of 3D Printed Bending-Dominated Ligament-Based Triply Periodic Cellular Polymeric Solids.” Journal of Materials Engineering and Performance 28 (4): 2316–2326.
- Acanfora, V., S. Saputo, A. Russo, and A. Riccio. 2021. “A Feasibility Study on Additive Manufactured Hybrid Metal/Composite Shock Absorbers.” Composite Structures 268: 113958.
- Adams, R., S. Townsend, S. Soe, and P. Theobald. 2022. “Mechanical Behaviour of Additively Manufactured Elastomeric pre-Buckled Honeycombs Under Quasi-Static and Impact Loading.” Materials & Design 213: 110368.
- Airoldi, A., N. Novak, F. Sgobba, A. Gilardelli, and M. Borovinšek. 2020. “Foam-filled Energy Absorbers with Auxetic Behaviour for Localized Impacts.” Materials Science and Engineering: A 788: 139500.
- Al-Saedi, D. S., S. H. Masood, M. Faizan-Ur-Rab, A. Alomarah, and P. Ponnusamy. 2018. “Mechanical Properties and Energy Absorption Capability of Functionally Graded F2BCC Lattice Fabricated by SLM.” Materials & Design 144: 32–44.
- Albertini, F., J. Dirrenberger, C. Sollogoub, T. Maconachie, M. Leary, and A. Molotnikov. 2021. “Experimental and Computational Analysis of the Mechanical Properties of Composite Auxetic Lattice Structures.” Additive Manufacturing 47: 102351.
- Alkhatib, S. E., M. S. Matar, F. Tarlochan, O. Laban, A. S. Mohamed, and N. Alqwasmi. 2019. “Deformation Modes and Crashworthiness Energy Absorption of Sinusoidally Corrugated Tubes Manufactured by Direct Metal Laser Sintering.” Engineering Structures 201: 109838.
- Alomarah, A., S. H. Masood, and D. Ruan. 2020. “Out-of-Plane and In-Plane Compression of Additively Manufactured Auxetic Structures.” Aerospace Science and Technology 106: 106107.
- Alomarah, A., S. H. Masood, I. Sbarski, B. Faisal, Z. Gao, and D. Ruan. 2020. “Compressive Properties of 3D Printed Auxetic Structures: Experimental and Numerical Studies.” Virtual and Physical Prototyping 15 (1): 1–21.
- Andrew, J. J., H. Alhashmi, A. Schiffer, S. Kumar, and V. S. Deshpande. 2021. “Energy Absorption and Self-Sensing Performance of 3D Printed CF/PEEK Cellular Composites.” Materials & Design 208: 109863.
- Andrew, J. J., J. Ubaid, F. Hafeez, A. Schiffer, and S. Kumar. 2019. “Impact Performance Enhancement of Honeycombs Through Additive Manufacturing-Enabled Geometrical Tailoring.” International Journal of Impact Engineering 134: 103360.
- Arjunan, A., M. Singh, A. Baroutaji, and C. Wang. 2020. “Additively Manufactured AlSi10Mg Inherently Stable Thin and Thick-Walled Lattice with Negative Poisson’s Ratio.” Composite Structures 247: 112469.
- Bai, L., Y. Xu, X. Chen, L. Xin, J. Zhang, K. Li, and Y. Sun. 2021. “Improved Mechanical Properties and Energy Absorption of Ti6Al4V Laser Powder bed Fusion Lattice Structures Using Curving Lattice Struts.” Materials & Design 211: 110140.
- Bai, L., J. Zhang, Y. Xiong, X. Chen, Y. Sun, C. Gong, H. Pu, X. Wu, and J. Luo. 2020. “Influence of Unit Cell Pose on the Mechanical Properties of Ti6Al4V Lattice Structures Manufactured by Selective Laser Melting.” Additive Manufacturing 34: 101222.
- Baroutaji, A., A. Arjunan, M. Stanford, J. Robinson, and A. G. Olabi. 2021. “Deformation and Energy Absorption of Additively Manufactured Functionally Graded Thickness Thin-Walled Circular Tubes Under Lateral Crushing.” Engineering Structures 226: 111324.
- Bates, S. R., I. R. Farrow, and R. S. Trask. 2016. “3D Printed Polyurethane Honeycombs for Repeated Tailored Energy Absorption.” Materials & Design 112: 172–183.
- Bates, S. R., I. R. Farrow, and R. S. Trask. 2019. “Compressive Behaviour of 3D Printed Thermoplastic Polyurethane Honeycombs with Graded Densities.” Materials & Design 162: 130–142.
- Belarbi, Y. E., S. Guessasma, S. Belhabib, F. Benmahiddine, and A. E. A. Hamami. 2021. “Effect of Printing Parameters on Mechanical Behaviour of PLA-Flax Printed Structures by Fused Deposition Modelling.” Materials 14 (19): 5883.
- Bodaghi, M., A. Serjouei, A. Zolfagharian, M. Fotouhi, H. Rahman, and D. Durand. 2020. “Reversible Energy Absorbing Meta-Sandwiches by FDM 4D Printing.” International Journal of Mechanical Sciences 173: 105451.
- Calle, M. A., M. Salmi, L. M. Mazzariol, M. Alves, and P. Kujala. 2020. “Additive Manufacturing of Miniature Marine Structures for Crashworthiness Verification: Scaling Technique and Experimental Tests.” Marine Structures 72: 102764.
- Cetin, E., and C. Baykasoğlu. 2019. “Energy Absorption of Thin-Walled Tubes Enhanced by Lattice Structures.” International Journal of Mechanical Sciences 157: 471–484.
- Cetin, E., and C. Baykasoğlu. 2020. “Crashworthiness of Graded Lattice Structure Filled Thin-Walled Tubes Under Multiple Impact Loadings.” Thin-walled Structures 154: 106849.
- Chacón, J. M., M. A. Caminero, P. J. Núñez, E. García-Plaza, I. García-Moreno, and J. M. Reverte. 2019. “Additive Manufacturing of Continuous Fibre Reinforced Thermoplastic Composites Using Fused Deposition Modelling: Effect of Process Parameters on Mechanical Properties.” Composites Science and Technology 181: 107688.
- Chang, B., X. Li, P. Parandoush, S. Ruan, C. Shen, and D. Lin. 2020. “Additive Manufacturing of Continuous Carbon Fiber Reinforced Poly-Ether-Ether-Ketone with Ultrahigh Mechanical Properties.” Polymer Testing 88: 106563.
- Chapkin, W. A., D. L. Simone, G. J. Frank, and J. W. Baur. 2021. “Mechanical Behavior and Energy Dissipation of Infilled, Composite Ti-6Al-4V Trusses.” Materials & Design 203: 109602.
- Chen, Y., T. Li, Z. Jia, F. Scarpa, C. W. Yao, and L. Wang. 2018. “3D Printed Hierarchical Honeycombs with Shape Integrity Under Large Compressive Deformations.” Materials & Design 137: 226–234.
- Chen, S., X. Tan, J. Hu, S. Zhu, B. Wang, L. Wang, Y. Jin, and L. Wu. 2021. “A Novel Gradient Negative Stiffness Honeycomb for Recoverable Energy Absorption.” Composites Part B: Engineering 215: 108745.
- Chen, D., and X. Zheng. 2018. “Multi-material Additive Manufacturing of Metamaterials with Giant, Tailorable Negative Poisson’s Ratios.” Scientific Reports 8 (1): 1–8.
- Cheng, L., L. Wang, and A. M. Karlsson. 2008. “Image Analyses of Two Crustacean Exoskeletons and Implications of the Exoskeletal Microstructure on the Mechanical Behavior.” Journal of Materials Research 23 (11): 2854–2872.
- Choy, S. Y., C. N. Sun, K. F. Leong, and J. Wei. 2017. “Compressive Properties of Functionally Graded Lattice Structures Manufactured by Selective Laser Melting.” Materials & Design 131: 112–120.
- Dar, U. A., H. H. Mian, M. Abid, A. Topa, M. Z. Sheikh, and M. Bilal. 2020. “Experimental and Numerical Investigation of Compressive Behavior of Lattice Structures Manufactured Through Projection Micro Stereolithography.” Materials Today Communications 25: 101563.
- Dong, J., and H. Fan. 2022. “Crushing Behaviors of Buckling-Oriented Hexagonal Lattice Structures.” Mechanics of Materials 165: 104160.
- Drücker, S., M. Schulze, H. Ipsen, L. Bandegani, H. Hoch, M. Kluge, and B. Fiedler. 2021. “Experimental and Numerical Mechanical Characterization of Additively Manufactured Ti6Al4V Lattice Structures Considering Progressive Damage.” International Journal of Mechanical Sciences 189: 105986.
- Du, Y., D. Gu, L. Xi, D. Dai, T. Gao, J. Zhu, and C. Ma. 2020. “Laser Additive Manufacturing of Bio-Inspired Lattice Structure: Forming Quality, Microstructure and Energy Absorption Behavior.” Materials Science and Engineering: A 773: 138857.
- Duan, Y., X. Zhao, Z. Liu, N. Hou, H. Liu, B. Du, B. Hou, and Y. Li. 2020. “Dynamic Response of Additively Manufactured Graded Foams.” Composites Part B: Engineering 183: 107630.
- Fernandez, F., W. S. Compel, J. P. Lewicki, and D. A. Tortorelli. 2019. “Optimal Design of Fiber Reinforced Composite Structures and Their Direct ink Write Fabrication.” Computer Methods in Applied Mechanics and Engineering 353: 277–307.
- Fu, X., X. Zhang, and Z. Huang. 2021. “Axial Crushing of Nylon and Al/Nylon Hybrid Tubes by FDM 3D Printing.” Composite Structures 256: 113055.
- Gao, Q., W. H. Liao, and L. Wang. 2020. “An Analytical Model of Cylindrical Double-Arrowed Honeycomb with Negative Poisson's Ratio.” International Journal of Mechanical Sciences 173: 105400.
- Gao, S., C. Wang, B. Xing, M. Shen, W. Zhao, and Z. Zhao. 2020. “Experimental Investigation on Bending Behaviour of ZrO2 Honeycomb Sandwich Structures Prepared by DLP Stereolithography.” Thin-Walled Structures 157: 107099.
- Gong, H., J. Liu, K. Xu, J. Wu, and Y. Li. 2020. “Surface-Topology-Controlled Mechanical Characteristics of Triply Carbon Schwarzite Foams.” Soft Matter 16 (17): 4324–4338.
- Gu, D., C. Ma, D. Dai, J. Yang, K. Lin, H. Zhang, and H. Zhang. 2021. “Additively Manufacturing-Enabled Hierarchical NiTi-Based Shape Memory Alloys with High Strength and Toughness.” Virtual and Physical Prototyping 16 (S1): S19–S38.
- Guo, Y., J. Zhang, L. Chen, B. Du, H. Liu, L. Chen, W. Li, and Y. Liu. 2020. “Deformation Behaviors and Energy Absorption of Auxetic Lattice Cylindrical Structures Under Axial Crushing Load.” Aerospace Science and Technology 98: 105662.
- Habib, F. N., P. Iovenitti, S. H. Masood, and M. Nikzad. 2017. “In-plane Energy Absorption Evaluation of 3D Printed Polymeric Honeycombs.” Virtual and Physical Prototyping 12 (2): 117–131.
- Habib, F. N., P. Iovenitti, S. H. Masood, and M. Nikzad. 2018. “Fabrication of Polymeric Lattice Structures for Optimum Energy Absorption Using Multi Jet Fusion Technology.” Materials & Design 155: 86–98.
- Huang, J., Q. Chen, H. Jiang, B. Zou, L. Li, J. Liu, and H. Yu. 2020. “A Survey of Design Methods for Material Extrusion Polymer 3D Printing.” Virtual and Physical Prototyping 15 (2): 148–162.
- Huang, W., Y. Zhang, Y. Xu, X. Xu, and J. Wang. 2021. “Out-of-plane Mechanical Design of Bi-Directional Hierarchical Honeycombs.” Composites Part B: Engineering 221: 109012.
- Ingrole, A., T. G. Aguirre, L. Fuller, and S. W. Donahue. 2021. “Bioinspired Energy Absorbing Material Designs Using Additive Manufacturing.” Journal of the Mechanical Behavior of Biomedical Materials 119: 104518.
- Isaac, C. W. 2020a. “Crashworthiness Performance of Green Composite Energy Absorbing Structure with Embedded Sensing Device Providing Cleaner Environment for Sustainable Maintenance.” Sustainable Materials and Technologies 25: e00196.
- Isaac, C. W. 2020b. “Crushing Response of Circular Thin-Walled Tube with Non-Propagating Crack Subjected to Dynamic Oblique Impact Loading.” International Journal of Protective Structures 11 (1): 41–68.
- Isaac, C. W., and C. Ezekwem. 2021. “A Review of the Crashworthiness Performance of Energy Absorbing Composite Structure Within the Context of Materials, Manufacturing and Maintenance for Sustainability.” Composite Structures 257: 113081.
- Isaac, C. W., and O. Oluwole. 2018. “Structural Response and Performance of Hexagonal Thin-Walled Grooved Tubes Under Dynamic Impact Loading Conditions.” Engineering Structures 167: 459–470.
- Isaac, C. W., S. Wrona, M. Pawelczyk, and N. B. Roozen. 2021. “Numerical Investigation of the Vibro-Acoustic Response of Functionally Graded Lightweight Square Panel at low and mid-Frequency Regions.” Composite Structures 259: 113460.
- Jiang, H., P. Aihemaiti, W. Aiyiti, and A. Kasimu. 2022. “Study of the Compression Behaviours of 3D-Printed PEEK/CFR-PEEK Sandwich Composite Structures.” Virtual and Physical Prototyping 17 (2): 138–155.
- Jiang, H., A. Coomes, Z. Zhang, H. Ziegler, and Y. Chen. 2021. “Tailoring 3D Printed Graded Architected Polymer Foams for Enhanced Energy Absorption.” Composites Part B: Engineering 224: 109183.
- Jiang, H., L. Le Barbenchon, B. A. Bednarcyk, F. Scarpa, and Y. Chen. 2020. “Bioinspired Multilayered Cellular Composites with Enhanced Energy Absorption and Shape Recovery.” Additive Manufacturing 36: 101430.
- Jin, N., F. Wang, Y. Wang, B. Zhang, H. Cheng, and H. Zhang. 2019. “Failure and Energy Absorption Characteristics of Four Lattice Structures Under Dynamic Loading.” Materials & Design 169: 107655.
- Johnston, R., and Z. Kazancı. 2021. “Analysis of Additively Manufactured (3D Printed) Dual-Material Auxetic Structures Under Compression.” Additive Manufacturing 38: 101783.
- Kader, M. A., P. J. Hazell, A. D. Brown, M. Tahtali, S. Ahmed, J. P. Escobedo, and M. Saadatfar. 2020. “Novel Design of Closed-Cell Foam Structures for Property Enhancement.” Additive Manufacturing 31: 100976.
- Kafle, A., E. Luis, R. Silwal, H. M. Pan, P. L. Shrestha, and A. K. Bastola. 2021. “3D/4D Printing of Polymers: Fused Deposition Modelling (FDM), Selective Laser Sintering (SLS), and Stereolithography (SLA).” Polymers 13 (18): 3101.
- Kao, Y. T., A. R. Amin, N. Payne, J. Wang, and B. L. Tai. 2018. “Low-Velocity Impact Response of 3D-Printed Lattice Structure with Foam Reinforcement.” Composite Structures 192: 93–100.
- Kempen, K., L. Thijs, J. Van Humbeeck, and J. P. Kruth. 2015. “Processing AlSi10Mg by Selective Laser Melting: Parameter Optimisation and Material Characterisation.” Materials Science and Technology 31 (8): 917–923.
- Khan, S. Z., S. H. Masood, E. Ibrahim, and Z. Ahmad. 2019. “Compressive Behaviour of Neovius Triply Periodic Minimal Surface Cellular Structure Manufactured by Fused Deposition Modelling.” Virtual and Physical Prototyping 14 (4): 360–370.
- Khoo, Z. X., J. E. M. Teoh, Y. Liu, C. K. Chua, S. Yang, J. An, K. F. Leong, and W. Y. Yeong. 2015. “3D Printing of Smart Materials: A Review on Recent Progresses in 4D Printing.” Virtual and Physical Prototyping 10 (3): 103–122.
- Kies, F., P. Köhnen, M. B. Wilms, F. Brasche, K. G. Pradeep, A. Schwedt, S. Richter, A. Weisheit, J. H. Schleifenbaum, and C. Haase. 2018. “Design of High-Manganese Steels for Additive Manufacturing Applications with Energy-Absorption Functionality.” Materials & Design 160: 1250–1264.
- Ko, K., S. Jin, S. E. Lee, and J. W. Hong. 2020. “Impact Resistance of Nacre-Like Composites Diversely Patterned by 3D Printing.” Composite Structures 238: 111951.
- Kucewicz, M., P. Baranowski, J. Małachowski, A. Popławski, and P. Płatek. 2018. “Modelling, and Characterization of 3D Printed Cellular Structures.” Materials & Design 142: 177–189.
- Kumar, S., J. Ubaid, R. Abishera, A. Schiffer, and V. S. Deshpande. 2019. “Tunable Energy Absorption Characteristics of Architected Honeycombs Enabled via Additive Manufacturing.” ACS Applied Materials & Interfaces 11 (45): 42549–42560.
- Kumar, A., S. Verma, and J. Y. Jeng. 2020. “Supportless Lattice Structures for Energy Absorption Fabricated by Fused Deposition Modeling.” 3D Printing and Additive Manufacturing 7 (2): 85–96.
- Leary, M., M. Mazur, H. Williams, E. Yang, A. Alghamdi, B. Lozanovski, X. Zhang, et al. 2018. “Inconel 625 Lattice Structures Manufactured by Selective Laser Melting (SLM): Mechanical Properties, Deformation and Failure Modes.” Materials & Design 157: 179–199.
- Lee, W., Y. Jeong, J. Yoo, H. Huh, S. J. Park, S. H. Park, and J. Yoon. 2019. “Effect of Auxetic Structures on Crash Behavior of Cylindrical Tube.” Composite Structures 208: 836–846.
- Lewandowski, J. J., and M. Seifi. 2016. “Metal Additive Manufacturing: A Review of Mechanical Properties.” Annual Review of Materials Research 46: 151–186.
- Li, T., Y. Chen, X. Hu, Y. Li, and L. Wang. 2018. “Exploiting Negative Poisson's Ratio to Design 3D-Printed Composites with Enhanced Mechanical Properties.” Materials & Design 142: 247–258.
- Li, S., M. Hu, L. Xiao, and W. Song. 2020. “Compressive Properties and Collapse Behavior of Additively-Manufactured Layered-Hybrid Lattice Structures Under Static and Dynamic Loadings.” Thin-Walled Structures 157: 107153.
- Li, D., W. Liao, N. Dai, and Y. M. Xie. 2019. “Comparison of Mechanical Properties and Energy Absorption of Sheet-Based and Strut-Based Gyroid Cellular Structures with Graded Densities.” Materials 12 (13): 2183.
- Li, S., Z. Liu, V. P. W. Shim, Y. Guo, Z. Sun, X. Li, and Z. Wang. 2020. “In-plane Compression of 3D-Printed Self-Similar Hierarchical Honeycombs–Static and Dynamic Analysis.” Thin-Walled Structures 157: 106990.
- Li, X., L. Xiao, and W. Song. 2021. “Compressive Behavior of Selective Laser Melting Printed Gyroid Structures Under Dynamic Loading.” Additive Manufacturing 46: 102054.
- Li, P., F. Yang, Y. Bian, S. Zhang, and L. Wang. 2021. “Deformation Pattern Classification and Energy Absorption Optimization of the Eccentric Body Centered Cubic Lattice Structures.” International Journal of Mechanical Sciences 212: 106813.
- Li, Q., X. Zhi, and F. Fan. 2022. “Quasi-static Compressive Behaviour of 3D-Printed Origami-Inspired Cellular Structure: Experimental, Numerical and Theoretical Studies.” Virtual and Physical Prototyping 17 (1): 69–91.
- Liang, H., W. Hao, G. Xue, B. Liu, Y. Pu, and F. Ma. 2022. “Parametric Design Strategy of a Novel Self-Similar Hierarchical Honeycomb for Multi-Stage Energy Absorption Demand.” International Journal of Mechanical Sciences 217: 107029.
- Lin, K., D. Gu, K. Hu, J. Yang, H. Wang, L. Yuan, X. Shi, and L. Meng. 2021. “Laser Powder bed Fusion of bio-Inspired Honeycomb Structures: Effect of Twist Angle on Compressive Behaviors.” Thin-Walled Structures 159: 107252.
- Ling, C., A. Cernicchi, M. D. Gilchrist, and P. Cardiff. 2019. “Mechanical Behaviour of Additively-Manufactured Polymeric Octet-Truss Lattice Structures Under Quasi-Static and Dynamic Compressive Loading.” Materials & Design 162: 106–118.
- Liu, T., L. Liu, C. Zeng, Y. Liu, and J. Leng. 2020. “4D Printed Anisotropic Structures with Tailored Mechanical Behaviors and Shape Memory Effects.” Composites Science and Technology 186: 107935.
- Liu, H., E. T. Zhang, and B. F. Ng. 2021. “In-plane Dynamic Crushing of a Novel Honeycomb with Functionally Graded Fractal Self-Similarity.” Composite Structures 270: 114106.
- Logakannan, K. P., V. Ramachandran, J. Rengaswamy, and D. Ruan. 2020. “Dynamic Performance of a 3D Re-Entrant Structure.” Mechanics of Materials 148: 103503.
- Lubombo, C., and M. A. Huneault. 2018. “Effect of Infill Patterns on the Mechanical Performance of Lightweight 3D-Printed Cellular PLA Parts.” Materials Today Communications 17: 214–228.
- Mansour, M. T., K. Tsongas, and D. Tzetzis. 2021. “3D Printed Hierarchical Honeycombs with Carbon Fiber and Carbon Nanotube Reinforced Acrylonitrile Butadiene Styrene.” Journal of Composites Science 5 (2): 62.
- Maskery, I., N. T. Aboulkhair, A. O. Aremu, C. J. Tuck, and I. A. Ashcroft. 2017. “Compressive Failure Modes and Energy Absorption in Additively Manufactured Double Gyroid Lattices.” Additive Manufacturing 16: 24–29.
- Maskery, I., N. T. Aboulkhair, A. O. Aremu, C. J. Tuck, I. A. Ashcroft, R. D. Wildman, and R. J. M. Hague. 2016. “A Mechanical Property Evaluation of Graded Density Al-Si10-Mg Lattice Structures Manufactured by Selective Laser Melting.” Materials Science and Engineering: A 670: 264–274.
- Maskery, I., L. Sturm, A. O. Aremu, A. Panesar, C. B. Williams, C. J. Tuck, R. D. Wildman, I. A. Ashcroft, and R. J. Hague. 2018. “Insights Into the Mechanical Properties of Several Triply Periodic Minimal Surface Lattice Structures Made by Polymer Additive Manufacturing.” Polymer 152: 62–71.
- Matsuzaki, R., M. Ueda, M. Namiki, T. K. Jeong, H. Asahara, K. Horiguchi, T. Nakamura, A. Todoroki, and Y. Hirano. 2016. “Three-Dimensional Printing of Continuous-Fiber Composites by In-Nozzle Impregnation.” Scientific Reports 6 (1): 1–7.
- Mazur, M., M. Leary, S. Sun, M. Vcelka, D. Shidid, and M. Brandt. 2016. “Deformation and Failure Behaviour of Ti-6Al-4V Lattice Structures Manufactured by Selective Laser Melting (SLM).” The International Journal of Advanced Manufacturing Technology 84 (5): 1391–1411.
- Miralbes R., D. Ranz, F. J. Pascual, D. Zouzias, and M. Maza. 2022. “Characterization of Additively Manufactured Triply Periodic Minimal Surface Structures Under Compressive Loading.” Mechanics of Advanced Materials and Structures 29 (13): 1841–1855.
- Mishra, P. K., and P. Senthil. 2020. “Prediction of in-Plane Stiffness of Multi-Material 3D Printed Laminate Parts Fabricated by FDM Process Using CLT and its Mechanical Behaviour Under Tensile Load.” Materials Today Communications 23: 100955.
- Mohamed, A. S., O. Laban, F. Tarlochan, S. E. Al Khatib, M. S. Matar, and E. Mahdi. 2019. “Experimental Analysis of Additively Manufactured Thin-Walled Heat-Treated Circular Tubes with Slits Using AlSi10Mg Alloy by Quasi-Static Axial Crushing Test.” Thin-Walled Structures 138: 404–414.
- Mohsenizadeh, M., F. Gasbarri, M. Munther, A. Beheshti, and K. Davami. 2018. “Additively-Manufactured Lightweight Metamaterials for Energy Absorption.” Materials & Design 139: 521–530.
- Morales, U., A. Esnaola, M. Iragi, L. Aretxabaleta, and J. Aurrekoetxea. 2021a. “The Effect of Cross-Section Geometry on Crushing Behaviour of 3D Printed Continuous Carbon Fibre Reinforced Polyamide Profiles.” Composite Structures 274: 114337.
- Morales, U., A. Esnaola, M. Iragi, L. Aretxabaleta, and J. Aurrekoetxea. 2021b. “Quasi-Static and Dynamic Crush Behaviour of 3D Printed Thin-Walled Profiles Reinforced with Continuous Carbon and Glass Fibres.” Composites Part B: Engineering 217: 108865.
- Mueller, J., and K. Shea. 2018. “Stepwise Graded Struts for Maximizing Energy Absorption in Lattices.” Extreme Mechanics Letters 25: 7–15.
- Nasrullah, A. I. H., S. P. Santosa, and T. Dirgantara. 2020. “Design and Optimization of Crashworthy Components Based on Lattice Structure Configuration.” Structures 26: 969–981.
- Nazir, A., M. Ali, and J. Y. Jeng. 2021. “Investigation of Compression and Buckling Properties of a Novel Surface-Based Lattice Structure Manufactured Using Multi Jet Fusion Technology.” Materials 14 (10): 2599.
- Neff, C., N. Hopkinson, and N. B. Crane. 2018. “Experimental and Analytical Investigation of Mechanical Behavior of Laser-Sintered Diamond-Lattice Structures.” Additive Manufacturing 22: 807–816.
- Ngo, T. D., A. Kashani, G. Imbalzano, K. T. Nguyen, and D. Hui. 2018. “Additive Manufacturing (3D Printing): A Review of Materials, Methods, Applications and Challenges.” Composites Part B: Engineering 143: 172–196.
- Nian, Y., S. Wan, M. Li, and Q. Su. 2020. “Crashworthiness Design of Self-Similar Graded Honeycomb-Filled Composite Circular Structures.” Construction and Building Materials 233: 117344.
- Nian, Y., S. Wan, P. Zhou, X. Wang, R. Santiago, and M. Li. 2021. “Energy Absorption Characteristics of Functionally Graded Polymer-Based Lattice Structures Filled Aluminum Tubes Under Transverse Impact Loading.” Materials & Design 209: 110011.
- Niknam, H., and A. H. Akbarzadeh. 2020. “Graded Lattice Structures: Simultaneous Enhancement in Stiffness and Energy Absorption.” Materials & Design 196: 109129.
- Noronha, J., M. Qian, M. Leary, E. Kyriakou, and M. Brandt. 2021. “Hollow-walled Lattice Materials by Additive Manufacturing: Design, Manufacture, Properties, Applications and Challenges.” Current Opinion in Solid State and Materials Science 25 (5): 100940.
- Novak, N., O. Al-Ketan, L. Krstulović-Opara, R. Rowshan, R. K. A. Al-Rub, M. Vesenjak, and Z. Ren. 2021. “Quasi-static and Dynamic Compressive Behaviour of Sheet TPMS Cellular Structures.” Composite Structures 266: 113801.
- Papa, I., P. Russo, A. Astarita, A. Viscusi, A. S. Perna, L. Carrino, and V. Lopresto. 2020. “Impact Behaviour of a Novel Composite Structure Made of a Polymer Reinforced Composite with a 3D Printed Metallic Coating.” Composite Structures 245: 112346.
- Roach, D. J., C. M. Hamel, C. K. Dunn, M. V. Johnson, X. Kuang, and H. J. Qi. 2019. “The m4 3D Printer: A Multi-Material Multi-Method Additive Manufacturing Platform for Future 3D Printed Structures.” Additive Manufacturing 29: 100819.
- Saadi, M. A. S. R., A. Maguire, N. Pottackal, M. S. H. Thakur, M. M. Ikram, A. J. Hart, P. M. Ajayan, and M. M. Rahman. 2022. “Direct Ink Writing: A 3D Printing Technology for Diverse Materials.” Advanced Materials 34 (19): 2108855.
- Sajadi, S. M., P. S. Owuor, S. Schara, C. F. Woellner, V. Rodrigues, R. Vajtai, J. Lou, D. S. Galvão, C. S. Tiwary, and P. M. Ajayan. 2018. “Multiscale Geometric Design Principles Applied to 3D Printed Schwarzites.” Advanced Materials 30 (1): 1704820.
- Sang, L., S. Han, X. Peng, X. Jian, and J. Wang. 2019. “Development of 3D-Printed Basalt Fiber Reinforced Thermoplastic Honeycombs with Enhanced Compressive Mechanical Properties.” Composites Part A: Applied Science and Manufacturing 125: 105518. doi:10.1016/j.compositesa.2019.105518
- Sarvestani, H. Y., A. H. Akbarzadeh, H. Niknam, and K. Hermenean. 2018. “3D Printed Architected Polymeric Sandwich Panels: Energy Absorption and Structural Performance.” Composite Structures 200: 886–909.
- Schneider, J., A. Schiffer, F. Hafeez, and S. Kumar. 2022. “Dynamic Crushing of Tailored Honeycombs Realized via Additive Manufacturing.” International Journal of Mechanical Sciences 219: 107126.
- Shan, S., S. H. Kang, J. R. Raney, P. Wang, L. Fang, F. Candido, J. A. Lewis, and K. Bertoldi. 2015. “Multistable Architected Materials for Trapping Elastic Strain Energy.” Advanced Materials 27 (29): 4296–4301.
- Shen, F., S. Yuan, Y. Guo, B. Zhao, J. Bai, M. Qwamizadeh, C. K. Chua, J. Wei, and K. Zhou. 2016. “Energy Absorption of Thermoplastic Polyurethane Lattice Structures via 3D Printing: Modeling and Prediction.” International Journal of Applied Mechanics 8 (07): 1640006.
- Smith, M., Z. Guan, and W. J. Cantwell. 2013. “Finite Element Modelling of the Compressive Response of Lattice Structures Manufactured Using the Selective Laser Melting Technique.” International Journal of Mechanical Sciences 67: 28–41.
- Spinelli, G., P. Lamberti, V. Tucci, L. Vertuccio, and L. Guadagno. 2018. “Experimental and Theoretical Study on Piezoresistive Properties of a Structural Resin Reinforced with Carbon Nanotubes for Strain Sensing and Damage Monitoring.” Composites Part B: Engineering 145: 90–99.
- Sun, Z. P., Y. B. Guo, and V. P. W. Shim. 2021. “Characterisation and Modeling of Additively-Manufactured Polymeric Hybrid Lattice Structures for Energy Absorption.” International Journal of Mechanical Sciences 191: 106101.
- Tabacu, S., and C. Ducu. 2018. “Experimental Testing and Numerical Analysis of FDM Multi-Cell Inserts and Hybrid Structures.” Thin-Walled Structures 129: 197–212.
- Tabacu, S., and C. Ducu. 2020. “Numerical Investigations of 3D Printed Structures Under Compressive Loads Using Damage and Fracture Criterion: Experiments, Parameter Identification, and Validation.” Extreme Mechanics Letters 39: 100775.
- Tafazoli, M., and M. D. Nouri. 2022. “Investigation of the Experimental, Statistical and Optimisation of 3D Printed Lattice Core Sandwich Panel Energy Absorber with Novel Configuration Using Response Surface Method.” International Journal of Crashworthiness 27 (1): 261–272.
- Tancogne-Dejean, T., A. B. Spierings, and D. Mohr. 2016. “Additively-Manufactured Metallic Micro-Lattice Materials for High Specific Energy Absorption Under Static and Dynamic Loading.” Acta Materialia 116: 14–28.
- Tao, Y., W. Li, K. Wei, S. Duan, W. Wen, L. Chen, Y. Pei, and D. Fang. 2019. “Mechanical Properties and Energy Absorption of 3D Printed Square Hierarchical Honeycombs Under in-Plane Axial Compression.” Composites Part B: Engineering 176: 107219.
- Teimouri, M., M. Mahbod, and M. Asgari. 2021, February. “Topology-Optimized Hybrid Solid-Lattice Structures for Efficient Mechanical Performance.” Structures 29: 549–560.
- Tripathy, L., and W. F. Lu. 2018. “Evaluation of Axially-Crushed Cellular Truss Structures for Crashworthiness.” International Journal of Crashworthiness 23 (6): 680–696.
- Tsouknidas, A., M. Pantazopoulos, I. Katsoulis, D. Fasnakis, S. Maropoulos, and N. Michailidis. 2016. “Impact Absorption Capacity of 3D-Printed Components Fabricated by Fused Deposition Modelling.” Materials & Design 102: 41–44.
- Turner, A. J., M. Al Rifaie, A. Mian, and R. Srinivasan. 2018. “Low-Velocity Impact Behavior of Sandwich Structures with Additively Manufactured Polymer Lattice Cores.” Journal of Materials Engineering and Performance 27 (5): 2505–2512.
- Ufodike, C. O., M. F. Ahmed, and G. Dolzyk. 2021. “Additively Manufactured Biomorphic Cellular Structures Inspired by Wood Microstructure.” Journal of the Mechanical Behavior of Biomedical Materials 123: 104729.
- Ufodike, C. O., H. Wang, M. F. Ahmed, G. Dolzyk, and S. Jung. 2021. “Design and Modeling of Bamboo Biomorphic Structure for in-Plane Energy Absorption Improvement.” Materials & Design 205: 109736.
- Usta, F., H. S. Türkmen, and F. Scarpa. 2021. “Low-Velocity Impact Resistance of Composite Sandwich Panels with Various Types of Auxetic and non-Auxetic Core Structures.” Thin-Walled Structures 163: 107738.
- Wang, T., J. An, H. He, X. Wen, and X. Xi. 2021. “A Novel 3D Impact Energy Absorption Structure with Negative Poisson’s Ratio and Its Application in Aircraft Crashworthiness.” Composite Structures 262: 113663.
- Wang, S., C. Deng, O. Ojo, B. Akinrinlola, J. Kozub, and N. Wu. 2022. “Design and Modeling of a Novel Three Dimensional Auxetic Reentrant Honeycomb Structure for Energy Absorption.” Composite Structures 280: 114882.
- Wang, X., M. Jiang, Z. Zhou, J. Gou, and D. Hui. 2017. “3D Printing of Polymer Matrix Composites: A Review and Prospective.” Composites Part B: Engineering 110: 442–458.
- Wang, D., L. Liu, G. Deng, C. Deng, Y. Bai, Y. Yang, W. Wu, et al. 2022. “Recent Progress on Additive Manufacturing of Multi-Material Structures with Laser Powder bed Fusion.” Virtual and Physical Prototyping 17 (2): 329–365.
- Wang, K., Y. Liu, J. Wang, J. Xiang, S. Yao, and Y. Peng. 2022. “On Crashworthiness Behaviors of 3D Printed Multi-Cell Filled Thin-Walled Structures.” Engineering Structures 254: 113907.
- Wang, J., Y. Liu, K. Wang, S. Yao, Y. Peng, Y. Rao, and S. Ahzi. 2022. “Progressive Collapse Behaviors and Mechanisms of 3D Printed Thin-Walled Composite Structures Under Multi-Conditional Loading.” Thin-Walled Structures 171: 108810.
- Wang, Y., F. Liu, X. Zhang, K. Zhang, X. Wang, D. Gan, and B. Yang. 2021. “Cell-size Graded Sandwich Enhances Additive Manufacturing Fidelity and Energy Absorption.” International Journal of Mechanical Sciences 211: 106798.
- Wang, X., R. Qin, and B. Chen. 2021. “Laser-based Additively Manufactured Bio-Inspired Crashworthy Structure: Energy Absorption and Collapse Behaviour Under Static and Dynamic Loadings.” Materials & Design 211: 110128.
- Wang, Y., X. Ren, Z. Chen, Y. Jiang, X. Cao, S. Fang, T. Zhao, Y. Li, and D. Fang. 2020. “Numerical and Experimental Studies on Compressive Behavior of Gyroid Lattice Cylindrical Shells.” Materials & Design 186: 108340.
- Wang, S., J. Wang, Y. Xu, W. Zhang, and J. Zhu. 2020. “Compressive Behavior and Energy Absorption of Polymeric Lattice Structures Made by Additive Manufacturing.” Frontiers of Mechanical Engineering 15 (2): 319–327.
- Wang, J., H. Xie, Z. Weng, T. Senthil, and L. Wu. 2016. “A Novel Approach to Improve Mechanical Properties of Parts Fabricated by Fused Deposition Modeling.” Materials & Design 105: 152–159.
- Wang, P., F. Yang, P. Li, B. Zheng, and H. Fan. 2021. “Design and Additive Manufacturing of a Modified Face-Centered Cubic Lattice with Enhanced Energy Absorption Capability.” Extreme Mechanics Letters 47: 101358.
- Wang, Q., Z. Yang, Z. Lu, and X. Li. 2020. “Mechanical Responses of 3D Cross-Chiral Auxetic Materials Under Uniaxial Compression.” Materials & Design 186: 108226.
- Wang, P., F. Yang, D. Ru, B. Zheng, and H. Fan. 2021. “Additive-manufactured Hierarchical Multi-Circular Lattice Structures for Energy Absorption Application.” Materials & Design 210: 110116.
- Wang, S., M. Zhang, Y. Wang, Z. Huang, and Y. Fang. 2021. “Experimental Studies on Quasi-Static Axial Crushing of Additively-Manufactured PLA Random Honeycomb-Filled Double Circular Tubes.” Composite Structures 261: 113553.
- Wang, Z., Y. Zhou, X. Wang, and K. Wei. 2021. “Compression Behavior of Strut-Reinforced Hierarchical Lattice—Experiment and Simulation.” International Journal of Mechanical Sciences 210: 106749.
- Wei, K., Q. Yang, B. Ling, H. Xie, Z. Qu, and D. Fang. 2018. “Mechanical Responses of Titanium 3D Kagome Lattice Structure Manufactured by Selective Laser Melting.” Extreme Mechanics Letters 23: 41–48.
- Wei, K., Q. Yang, X. Yang, Y. Tao, H. Xie, Z. Qu, and D. Fang. 2020. “Mechanical Analysis and Modeling of Metallic Lattice Sandwich Additively Fabricated by Selective Laser Melting.” Thin-Walled Structures 146: 106189.
- Wei, Y., Y. Zhang, Q. Song, X. Zhou, Y. Zhou, and Y. Shen. 2022. “Effects of Different Configurations and Gradients on Compression Responses of Gradient Honeycombs via Selective Laser Melting.” Thin-Walled Structures 170: 108462.
- Wei, L., X. Zhao, Q. Yu, W. Zhang, and G. Zhu. 2021. “In-plane Compression Behaviors of the Auxetic Star Honeycomb: Experimental and Numerical Simulation.” Aerospace Science and Technology 115: 06797.
- Wei, L., X. Zhao, Q. Yu, and G. Zhu. 2021. “Quasi-static Axial Compressive Properties and Energy Absorption of Star-Triangular Auxetic Honeycomb.” Composite Structures 267: 113850.
- Wu, X., Y. Su, and J. Shi. 2020. “In-Plane Impact Resistance Enhancement with a Graded Cell-Wall Angle Design for Auxetic Metamaterials.” Composite Structures 247: 112451.
- Wu, Y., L. Sun, P. Yang, J. Fang, and W. Li. 2021. “Energy Absorption of Additively Manufactured Functionally Bi-Graded Thickness Honeycombs Subjected to Axial Loads.” Thin-Walled Structures 164: 107810.
- Xiao, X., B. M. Roh, and F. Zhu. 2021. “Strength Enhancement in Fused Filament Fabrication via the Isotropy Toolpath.” Applied Sciences 11 (13): 6100.
- Xiao, L., and W. Song. 2018. “Additively-Manufactured Functionally Graded Ti-6Al-4V Lattice Structures with High Strength Under Static and Dynamic Loading: Experiments.” International Journal of Impact Engineering 111: 255–272.
- Xu, G., Z. Wang, Z. Li, and X. Liang. 2020. “Theoretical and Numerical Analyses on Mechanical Performance of Octagonal Honeycomb Structures Subjected to Out-of-Plane Compression.” Mechanics of Advanced Materials and Structures 27 (17): 1461–1472.
- Yan, L., K. Zhu, Y. Zhang, C. Zhang, and X. Zheng. 2020. “Effect of Absorbent Foam Filling on Mechanical Behaviors of 3D-Printed Honeycombs.” Polymers 12 (9): 2059.
- Yang, H., X. Cao, B. Liao, G. Wang, Z. Huang, and Y. Li. 2021. “Mechanical Properties of Bio-Molecular Inspired MnL2n Cage-Lattices: Simulations & Experiments.” Materials Science and Engineering: A 826: 141991.
- Yang, J., D. Gu, K. Lin, C. Ma, R. Wang, H. Zhang, and M. Guo. 2020. “Laser 3D Printed Bio-Inspired Impact Resistant Structure: Failure Mechanism Under Compressive Loading.” Virtual and Physical Prototyping 15 (1): 75–86.
- Yao, G., R. Liu, Z. Xu, R. Xin, L. Chen, Z. Yu, and Z. Zhang. 2021. “Study on Quasi-Static Mechanical Properties of Four 3D-Printed bio-Inspired Structures Based on Functional Relationship.” Composite Structures 274: 114304.
- Yin, H., Z. Liu, J. Dai, G. Wen, and C. Zhang. 2020. “Crushing Behavior and Optimization of Sheet-Based 3D Periodic Cellular Structures.” Composites Part B: Engineering 182: 107565.
- Yuan, S., C. K. Chua, and K. Zhou. 2019. “3D-Printed Mechanical Metamaterials with High Energy Absorption.” Advanced Materials Technologies 4 (3): 1800419.
- Zeinalabedini, H., Y. O. Yildiz, P. Zhang, K. Laux, M. Kirca, and A. C. To. 2016. “Homogenization of Additive Manufactured Polymeric Foams with Spherical Cells.” Additive Manufacturing 12: 274–281.
- Zeng, C., L. Liu, W. Bian, J. Leng, and Y. Liu. 2021. “Compression Behavior and Energy Absorption of 3D Printed Continuous Fiber Reinforced Composite Honeycomb Structures with Shape Memory Effects.” Additive Manufacturing 38: 101842.
- Zhang, X. C., C. C. An, Z. F. Shen, H. X. Wu, W. G. Yang, and J. P. Bai. 2020. “Dynamic Crushing Responses of Bio-Inspired Re-Entrant Auxetic Honeycombs Under In-Plane Impact Loading.” Materials Today Communications 23: 100918.
- Zhang, B., S. H. Chung, S. Barker, D. Craig, R. J. Narayan, and J. Huang. 2021. “Direct ink Writing of Polycaprolactone/Polyethylene Oxide Based 3D Constructs.” Progress in Natural Science: Materials International 31 (2): 180–191.
- Zhang, L., S. Feih, S. Daynes, S. Chang, M. Y. Wang, J. Wei, and W. F. Lu. 2018. “Energy Absorption Characteristics of Metallic Triply Periodic Minimal Surface Sheet Structures Under Compressive Loading.” Additive Manufacturing 23: 505–515.
- Zhang, Z., H. Lei, M. Xu, J. Hua, C. Li, and D. Fang. 2019. “Out-of-Plane Compressive Performance and Energy Absorption of Multi-Layer Graded Sinusoidal Corrugated Sandwich Panels.” Materials & Design 178: 107858.
- Zhang, Y., Y. Lin, Y. Li, and X. Li. 2021. “3D Printed Self-Similar AlSi10Mg Alloy Hierarchical Honeycomb Architectures Under in-Plane Large Deformation.” Thin-Walled Structures 164: 107795.
- Zhang, Y., M. Lu, C. H. Wang, G. Sun, and G. Li. 2016. “Out-of-plane Crashworthiness of Bio-Inspired Self-Similar Regular Hierarchical Honeycombs.” Composite Structures 144: 1–13.
- Zhang, J., G. Lu, and Z. You. 2020. “Large Deformation and Energy Absorption of Additively Manufactured Auxetic Materials and Structures: A Review.” Composites Part B: Engineering 201: 108340.
- Zhang, Y., J. Qiao, G. Zhang, Y. Li, and L. Li. 2021. “Prediction of Deformation and Failure Behavior of Continuous Fiber Reinforced Composite Fabricated by Additive Manufacturing.” Composite Structures 265: 113738.
- Zhang, H., H. Zhou, Z. Zhou, H. Zeng, X. Zhang, J. Yang, H. Lei, and F. Han. 2021. “Energy Absorption Diagram Characteristic of Metallic Self-Supporting 3D Lattices Fabricated by Additive Manufacturing and Design Method of Energy Absorption Structure.” International Journal of Solids and Structures 226: 111082.
- Zhao, X., L. Wei, D. Wen, G. Zhu, Q. Yu, and Z. D. Ma. 2021. “Bending Response and Energy Absorption of Sandwich Beams with Novel Auxetic Honeycomb Core.” Engineering Structures 247: 113204.