ABSTRACT
Aluminium alloys are difficult to be manufactured by directed energy deposition (DED) with the widely used infrared laser because of the low absorptivity. A blue laser with a 450 nm wavelength has a significantly higher laser absorptivity in processing aluminium. Here, we developed a 2000 W blue laser directed energy deposition (BL-DED) system for additive manufacturing. In this system, a coaxial camera, a paraxial high-speed camera, and a paraxial infrared camera were simultaneously adopted to analyze the formation and evolution of molten pool characteristics. The relationships among the molten pool characteristics, depositing states, and appearance defects were built. We successfully printed the curved thin wall with good appearance quality by the manual in-situ control of appearance defects. This work demonstrated the advantages of the blue laser in DED of aluminium alloy, which could melt the powders under lower energy input conditions and result in a more stable deposition process.
SUBJECT CLASSIFICATION CODES:
1. Introduction
Among various additive manufacturing techniques, directed energy deposition (DED) is widely used in 3D deposition forming, surface cladding, and remanufacturing of metal materials. The energy sources of the DED mainly include laser beam, electron beam, and arc plasma (Tang et al. Citation2020). The laser-based directed energy deposition (L-DED) is proofed to have an extensive application potential because of the high build rate, relatively high resolution, and low possibility for contamination (CitationInternational A). Currently, the wavelength of the laser in L-DED is mainly between 980 and 1080 nm, which has a relatively low laser absorptivity for non-ferrous metal materials, such as copper alloy, aluminium alloy, etc. (Wang et al. Citation2021). Therefore, it is difficult to keep the reliability and repeatability of product qualities during the L-DED process of aluminium alloy (Wang, Wu, and Wang Citation2021). The same process parameter and scanning strategy design may have different product qualities. Though aluminium alloy has already been additively manufactured by selective laser melting, it is still a great challenge to form the aluminium alloy component with high quality by the L-DED. This is due to its strong heat accumulation and convective motion in the molten pool (Jia et al. Citation2022).
Blue laser-based directed energy deposition (BL-DED) is one of the L-DED techniques with a laser wavelength of 450 nm, which exhibits a higher absorption rate to many alloys, such as aluminium, copper, etc. (Brandau et al. Citation2022). With the development of the diode blue laser generator, some researchers have deposited the metal materials by the blue laser. In 2018, Asano et al. (Asano et al. Citation2018) deposited pure copper on 304 stainless steel by BL-DED, but the laser power and laser spot diameter are only 87 W and 0.4 mm, respectively, which resulted in a low depositing efficiency. In 2020, Hara et al. (Hara et al. Citation2020) improved the blue laser power to 200 W with a laser spot diameter of about 0.5 mm and deposited the pure copper powders on the oxygen-free copper plates. In 2022, Yang et al. (Yang et al. Citation2022) applied a diode blue laser generator of 1000 W to deposit pure copper on the AlSi7Mg through presetting the powders and obtained a continuously deposited layer. Currently, a highly efficient BL-DED technique has not been applied, and the industrial application of BL-DED is hard to realize.
To promote process efficiency, a high-power diode blue laser generator is necessary. In 2017, Wang et al (Wang et al. Citation2017) developed a 250 W diode blue laser generator by assembling 64 laser diodes of 4 W. In 2020, Das et al. (Das et al. Citation2020) applied the 500 W diode blue laser generator produced by NUBURU Inc to weld multiple stack-up joining of 316L stainless steel. In 2018-2020, Laserline GmbH developed a 1000–2000 W high-power diode blue laser generator (Britten et al. Citation2020). In 2021, Wang et al. built a BL-DED system using the 2000 W diode blue laser generator of Laserline GmbH for depositing or welding the metal materials, and the system is the main experimental setup in this work. The work in the paper is the first to apply a 2000 W high power BL-DED system for depositing the aluminium alloy single layer and thin wall structure.
A molten pool is a pivotal physical phenomenon in DED. The evolutionary behaviours of the molten pool characteristics are necessary for analyzing the deposition process, and clarifying the process mechanisms of BL-DED. To elucidate the evolutionary behaviours, non-contact monitoring devices are important. A coaxial camera, a paraxial heed-speed camera, or a paraxial infrared camera are usually used to observe the molten pool during the DED process. Tang et al. (Tang et al. Citation2021) applied a coaxial camera to clear the evolutionary behaviour of the molten pool during single-layer single-track depositing, multi-layer single-track stacking, and single-layer multi-track overlapping. They presented that the molten pool characteristics could indicate the melting, flowing, and solidifying states. Ono et al. (Ono et al. Citation2021) utilized a paraxial heed-speed camera to observe the deposition process of building a copper rod and found that a flat and thin molten pool formed at the tip of the rod. Yan et al. (Yan et al. Citation2019) used a paraxial infrared camera to study the change regulation of temperature characteristics of the molten pool with different process parameters. It is found that the temperature characteristics were more sensitive to the laser power than the other process parameters. The results from these literatures reveal the molten pool characteristics for monitoring the deposition states. These characteristics are majorly observed with the aid of the coaxial camera and the infrared camera, where the heed-speed camera is more suitable to analyze the process mechanisms.
Based on the ability of the molten pool characteristics on indicating the depositing state, some researchers tried to in-situ monitor the product qualities by those characteristics. Aiming at the molten pool characteristics from the coaxial camera, Tang et al. (Tang et al. Citation2019) researched the evolutionary behaviour of the molten pool that occurs upon the emergence of appearance defects. They presented that the molten pool characteristics had the potential for monitoring the product qualities, such as the incline edges and the width change. Aiming at the characteristics obtained from the paraxial infrared camera, Feng et al. (Feng et al. Citation2022) proposed a temperature distribution similarity detection method based on the temperature characteristics of the molten pool to monitor the surface pore defects. Similarly, Yan et al. (Yan et al. Citation2019) analyzed the relationships between the temperature characteristics and the thermal deformation. Their results indicated that it was possible to estimate the deformation based on the temperature characteristics of the molten pool. Therefore, the molten pool characteristics from the coaxial camera and the paraxial infrared camera can both be applied to monitor the product qualities.
Currently, a high-power and high-efficiency BL-DED technique for the non-ferrous metal material with high reflectance has not been found in existing literatures. To further understand the BL-DED technique, the correlations of the process parameters, the molten pool characteristics, and product qualities are vital. For the product qualities, the layer appearances are the basis to decide the success or failure of DED. Therefore, this work mainly focuses on appearance defects.
This work utilizes a BL-DED system with a 2000 W high-power diode blue laser generator to manufacture the aluminium alloy AlSi7Mg with high reflectivity. The coaxial camera, the paraxial high-speed camera, and the infrared camera are simultaneously applied to observe the BL-DED process. The coaxial camera can continuously track the molten pool and provide the top views of 2D molten pool images. The paraxial high-speed camera helps to explain the formation mechanism of the top view 2D molten pool characteristics and temperature characteristics. The infrared camera provides temperature characteristics during the BL-DED process. Based on the observations, Sections 3.1 and 3.2 study the formation and evolution of molten pool characteristics. Furthermore, utilizing these characteristics, Sections 3.3 and 3.4 show the appearance defect types and their forming reasons in the single-layer single-track deposition layer and multi-layer single-track stacking thin wall. At last, Section 4 relates the molten pool characteristics, depositing states, and appearance defects. Relying on the advantages of the blue laser in DED of aluminium alloy, the curved thin wall with good appearance quality by the manual in-situ control of appearance defects is manufactured successfully.
2. Materials and procedure
2.1. Materials
Commercial AlSi7Mg (FCA101X-2, Xiangbang Composite Material, 55∼100 um) was used as aluminium alloy powders in BL-DED. summarizes the chemical compositions of powders. The substrates were also AlSi7Mg. The single-layer single-track deposition layers were deposited on a rectangular specimen (145 × 145 × 20 mm). Prior to the deposition process of every new layer, the specimen was cooled for at least 30 s to ensure a room-temperature environment for the experimental consistency. The multi-layer single-track stacking thin walls were deposited on another rectangular specimen with 160 × 20 × 20 mm dimension. Every thin wall was built on the substrate at room temperature.
Table 1. Chemical compositions (wt.%) of AlSi7Mg powder.
2.2. Experimental setup
provides the schematic and photographs of the key components for a BL-DED system with the monitoring devices. The BL-DED system is consisted of a diode blue laser generator (LDMblue 2000–60 VG7H, Laserline GmbH, Mülheim-Kärlich, Germany), a three-axis displacement platform, a laser head (OTS-5 blue optics, Laserline GmbH, Mülheim-Kärlich, Germany), and a metal powder feeder (RC-PGF-D, Raycham Ltd, Nanjing, China). The energy transfer procedure from the blue laser generator to the laser head is achieved through an optical fiber with a 0.6 mm radius. The focal lengths of the focusing and collimating lens are 192 and 80 mm, respectively. The metal powders were delivered into a molten pool through an annular coaxial nozzle. The distance between the laser head and the substrate was 11 mm, while the defocusing amount of the powder flow was – 1 mm. The laser beam was focused at 11 mm with a diameter of 2.0 mm. Argon with 99.999% purity was applied as the shielding and carrier gas.
Figure 1. Schematic and photographs of the key components of the BL-DED system with the monitoring devices.
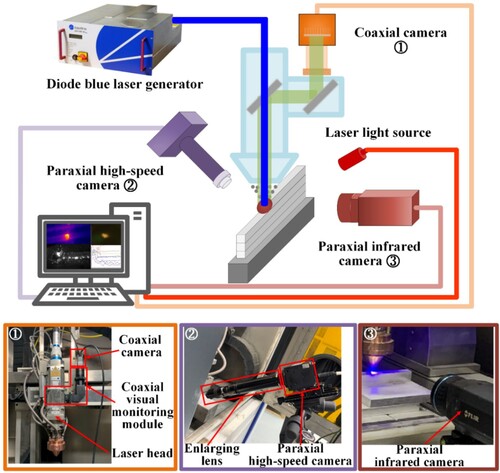
Three monitoring devices were used in the experiments: a) A coaxial camera (MQ013CG-ON/MQ013MG-E2, XIMEA GmbH, Münster, Germany) was applied with a coaxial visual monitoring module integrated into the laser head. The monitoring module could filter out the strong blue laser interference. The coaxial camera could constantly capture molten pool images at 1.3 Mpix and at least 50 fps with a resolution of around 28.6 μm/pixel. Therefore, it was utilized to observe the evolutionary behaviours of the molten pool in both the single-layer single-track deposition layer and the multi-layer single-track stacking thin wall. b) A paraxial high-speed camera (Revealer M220, Fuhuang AgileDevice, Hefei, China) with at least 2000 fps and 2.0 Mpix was utilized as an assistant device to explain and verify coaxial visual characteristics. A laser light source and optical filter with 808 nm wavelength were applied with the high-speed camera to avoid the interference of emitted light from the molten pool. An enlarging lens was also applied to obtain a clear molten pool image. Due to its small visual field and depth, the enlarging lens could only be used to watch the single-layer single-track deposition. c) A paraxial infrared camera (A615, FLIR Systems Inc, Wilsonville, America) possesses a wavelength range of 7.5 ∼ 14 μm and a temperature measurement range of −40 ∼ 2000 °C. The capturing parameters were up to 200 fps and 0.3 Mpix. The emissivity value was set to 0.3 based on the thermocouple temperature measurement of the deposition layer. This camera could capture the temperature variation tendencies to reveal the defect occurring reasons and mechanisms. However, three reasons contributed to a large monitoring deviation by the infrared camera for the single-layer single-track deposition. The first is that the intense blue laser beam interfered the signal acquisition. The second is that the molten pool occupied few pixels in the infrared image. The third is that different process parameters had obvious influences on the metallurgical behaviours. For the observation of the multi-layer single-track stacking process, the monitoring object and duration are larger and longer, respectively. In this case, the relative variation tendencies of the temperature feature are more usable and reliable.
2.3. Experimental procedure
Process parameters and scanning strategies are shown in and . All-factor test was implanted to determine the influence of laser power, scanning speed, and powder feed rate on the molten pool characteristics and appearance defects of the single-layer single-track deposition. Based on this analysis, the process parameters of 900 W, 5 mm/s, and 2.28 g/min were selected in stacking multi-layer single-track thin walls. The Z-axis increment was set with 0.2-0.4 mm with 0.1 mm interval. The residence time between layers was 5 or 15 s. The residence time at the edges was 0 or 0.2 s. The layer number was 50, 100, or 200. The stacking thin wall experiments were conducted under the open-loop condition to explore the latent defects adequately. The shielding and carrier gas rates were set as a constant value of 900 and 600 L/h, respectively.
Table 2. Process parameter design of the single-layer single-track deposition.
Table 3. Process parameter and scanning strategy designs of the multi-layer single-track stacking.
2.4. Image processing method
The molten pool of AlSi7Mg is divided into the inner region and outer region, which will be further described in Sections 3.1 and 4.1. The coaxial camera has the ability to continuously capture the molten pool. Therefore, the molten pool characteristics from the coaxial camera are the main concerning characteristics. In this work, the inner region area, the molten pool area, and the molten pool convection state were extracted through image processing to clarify the evolution process of the molten pool characteristics. The detailed image processing methods are provided in the ‘Supplementary Material’. For the infrared images, three temperature characteristics are obtained: a) the real-time temperature of the molten pool, b) the molten pool temperature change with the layer number increasing, and c) the deposition layer temperature change with an increasing layer number. The detailed calculation methods can be seen in the ‘Supplementary Material’.
3. Results
3.1. Molten pool characteristic analysis
Finding the sensitive characteristic of the molten pool is the key to monitor the BL-DED process. The forming mechanisms of the characteristics are important for understanding the deposition mechanisms. The images obtained by the coaxial camera, the paraxial high-speed camera, and the paraxial infrared camera are shown in . Among the three types of images from different monitoring devices, the ones from the coaxial camera are the main concerned object. This is related to the real-time tracking ability of the coaxial camera and the elusive forming mechanisms of the coaxial molten pool characteristics. The paraxial high-speed camera is applied to explain the forming mechanisms of the molten pool characteristics.
Figure 2. Molten pool images obtained by the (a) coaxial camera, (b) paraxial high-speed camera, and (c) paraxial infrared camera and their region divisions in BL-DED.
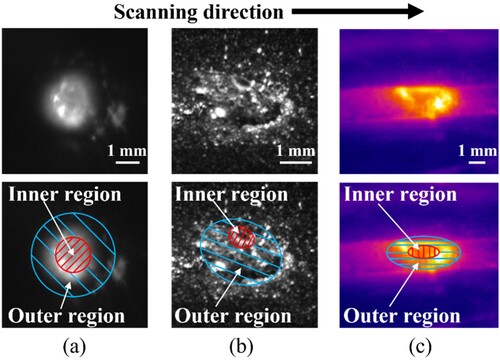
The molten pool of AlSi7Mg is not as clear as the molten pool of 316L in reference (Tang et al. Citation2021), where the head and tail of the molten pool are perdue in the coaxial image. Therefore, the molten pool in this work is divided into the inner region and outer region, as presented in . The different regions can be distinguished by the grayscale differences as shown in (a). The inner region has a significantly larger grayscale, while the outer region has a significantly lower grayscale. For the inner region, it has the potential to reflect the melting and flowing states of the molten pool. For the outer region, it can indicate the outline of the molten pool. Three factors contribute to the large grayscale of the inner region:
High temperature slags: a large number of slags cover the surface of the molten pool. The inner region is coincident with the laser spot, which has the highest laser energy. The high energy leads to the high temperature, which leads to the floating of the grayscale of the slags on the molten pool increase.
Unmelted metal powders: on the one hand, some unmelted metal powders adhere to the slags during the BL-DED process, as seen in . The metal powders, slags, and molten pools are potentially considered solid, mushy, and liquid, respectively. Due to their different emissivities at the same temperature, the following phenomena are observed: a) the liquid molten pool with the least emissivity has the least grayscale; b) the mushy slags take second place; c) the metal powders have the largest grayscale. On the other hand, the liquid metals on the surface flow from outside to inside, which can be observed by the high-speed camera, as shown in . Therefore, the unmelted metal powders all flow toward the inner region and lead to the large grayscale.
Vaporizing metal powders: while many unmelted metal powders are gathered in the inner region, some of them vaporize or burn with overexposure phenomenon due to the high laser radiation energy. The vaporizing behaviour may result from the molten metal droplet which has been proved in the reference (Prasad H, Brueckner, and Kaplan Citation2020). Because of the inhibitory action of the laser light source and optical filter with 808 nm wavelength, the overexposure phenomenon is not obvious through the high-speed camera but can be captured by the coaxial camera related to the passive lighting, as presented in .
Figure 3. Metallurgical behaviours of the molten pool observed by the paraxial high-speed camera, (a) the molten pool image without enlarging lens, (b) image with a treble enlarging lens and the typical molten pool characteristics, (c) powders adhere to slags and do not melt absolutely, (d)∼(f) powders melt gradually with grayscale decreasing and move toward the inner region.
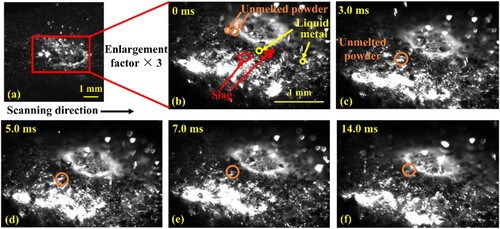
Figure 4. Metallurgical behaviours of the molten pool observed by the coaxial camera, (a) typical molten pool characteristics, (b)∼(f) the molten pool images at different times. Among (b)∼(f), (d) emerges the overexposure phenomenon due to the unmelted powder vaporizing or burning, and (f) shows the vaporizing or burning characteristic.
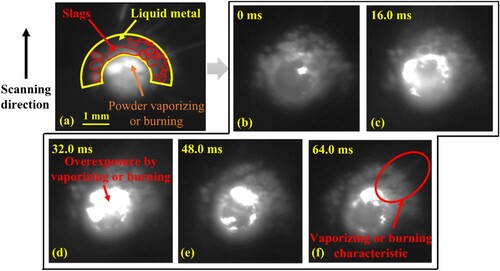
Metallurgical behaviours of the molten pool observed by the paraxial high-speed camera, (a) the molten pool image without enlarging lens, (b) image with a treble enlarging lens and the typical molten pool characteristics, (c) powders adhere to slags and do not melt absolutely, (d)∼(f) powders melt gradually with grayscale decreasing and move toward the inner region.
The outer region has a smaller grayscale than that of the inner region. The small grayscale of the outer region is affected by two major phenomena:
Low temperature slags: compared with the slags in the inner region, the temperature of the slags in the outer region is smaller. Therefore, the grayscale is also smaller.
Liquid metal: owing to the unmelted metal powders with large grayscale flowing into the inner region and the laser energy distribution, the outer region has few high grayscale unmelted metal powders. Meanwhile, the liquid molten pool has the smallest grayscale with the lowest emissivity. Due to the great grayscale gap between the inner and outer region, the outer region characteristics are not very clear in the passive lighting. Therefore, the outer region is not a perfect object during the BL-DED process.
The characteristics and forming mechanisms of the molten pool images obtained by the paraxial high-speed camera in (b) are simpler than that of the coaxial camera. This is due to the fact that the active lighting can avoid the effect of overexposure and varied emissivity. Some key characteristics have been shown in . The infrared images of (c) can refrain from the interference of flying powders and overexposure. However, the inner region grayscale is smaller than the outer region. Two reasons may cause this phenomenon:
Low emissivity of the liquid metal: the liquid with the low emissivity breaks into the slags scovering the molten pool, and the low emissivity causes a small grayscale.
High-power laser beam: the high-power laser beam with a special wavelength impacts the optical signal transmission with a wavelength range of 7.5 ∼ 14 μm during monitoring. Similar phenomena can also be found in the references (Yan et al. Citation2019) and (Doubenskaia et al. Citation2013).
3.2. Evolutionary behaviours of molten pool characteristics
3.2.1 Single-layer single-track deposition layer
Single-layer single-track depositing is the basis for evaluating the process parameters. In this section, the influence of the laser power, scanning speed, and powder feed rate on the molten pool characteristics are studied. The molten pool characteristics mainly include the inner region area, the molten pool area, and the relative standard deviation of the inner region area. The image processing methods of these characteristics are given in Section 2.4. The molten pool characteristics of the single-layer single-track deposition with different process parameters are provided in and . The inner region characteristics can be divided into two classes: small grayscale and large grayscale. The outer region characteristics can be defined as obscure slags and obvious slags, as seen in . Forming reasons for these characteristics are summarized based on different energy inputs:
Low energy input (P/v). At present, the convection state is not strong, and most of the slags and unmelted powders cannot flow to the inner region. Meanwhile, the low energy input barely vaporizes or burns the metal powders. Therefore, the grayscale of the inner region is slightly larger than the grayscale of the outer region with hardly any overexposure phenomenon. The inner region exists as the small grayscale characteristics. For an increase of the powder feed rate (f), a line mass (f/v) increases. The increasing amount of powder makes the number of slags and unmelted powders raise, and then, enhances the inner region grayscale. However, the powder feed rate has a considerable influence on molten pool height. shows a diagram of the influence of molten pool height on the two-dimensional size of the slags. When the three-dimensional height decreases (h1 > h2), the slag size lengthens (L1 < L2), which changes the grayscale representation. Meanwhile, the increasing height weakens the fluentness from the outer region to the inner region, making the texture simpler. Therefore, the slags in the outer region are obscure for an enough large value of the powder feed rate, as shown in .
Middle energy input (P/v). For higher input energy, a more violent convection state and distinct heat accumulation appear. They endue the liquid metals higher possibilities to take the slags and unmelted powders to the inner region, and thus, increase the inner region areas of large grayscale. Furthermore, the laser beam makes the slag grayscale increase and even leads to the powder vaporizing or burning with overexposure phenomenon. Therefore, the grayscale of the inner region is much larger than the grayscale of the outer region, with a common overexposure phenomenon. When the powder feed rate (f) increases, similar to that in the low energy input stage, the grayscale of the inner region and overexposure phenomenon both raise.
High energy input (P/v). When the energy input is large enough, three features appear in the inner region, including small grayscale in the centre, large grayscale at the edge, and overexposure phenomenon, as seen in . These features result from the highly violent convection state and heat accumulation. The violent fluctuation of the molten pool makes the liquid metals more possibilities to break the slags and decreases the grayscale in the centre of the inner region. Moreover, the float of the slags and unmelted powders along the edge of the inner region leads to the large grayscale and overexposure phenomenon at the edge. Because of the optical radiation at the edge of the large grayscale, the liquid metal still has the reflective grayscale. The large grayscale of the inner region is very obvious in the images from the coaxial camera, whereas cannot be observed obviously with the 808 nm active illuminating and high-speed camera. The influence of the powder feed rate (f) on the features is similar to that of the two above. However, the unmelted powder amount reduces due to sufficient energy input, and the effect of the powder feed rate is less than that of the low and middle energy input states.
Figure 5. Molten pool images and typical deposition layer outlines with different process parameters: different inner and outer region characteristics and their relationships with deposition layer outlines.
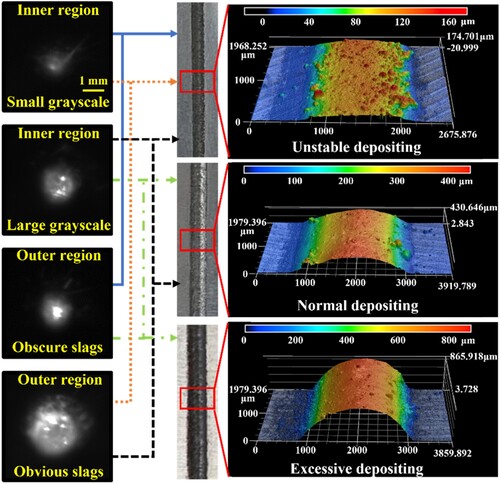
Figure 6. Molten pool images of different laser powers and scanning speeds with (a) 2.28, (b) 1.66, and (c) 1.03 g/min powder feed rate. In the images, orange, green, and blue backgrounds mean the unstable, normal, and excessive depositing states, respectively.
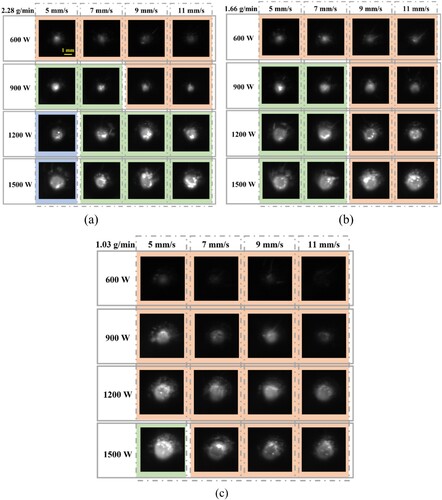
Figure 7. Influence of molten pool height on the two-dimensional shape of the slags and inner regions.
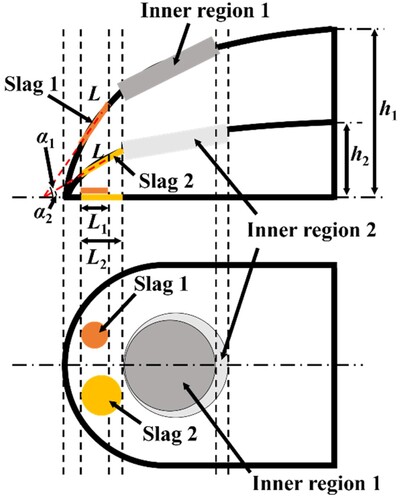
Figure 8. Different molten pool characteristics relying on the assistance of the high-speed camera with an enlarging lens and laser light source.
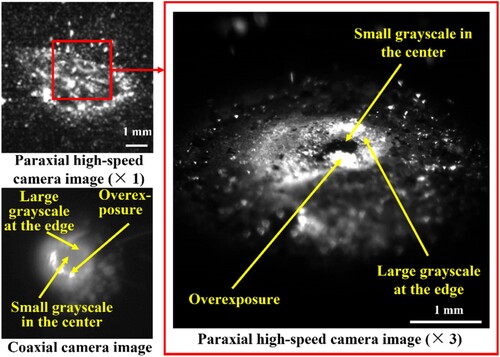
and Appendix Ⅰ exhibit the relationships between the process parameters and molten pool characteristics. The process parameters include the laser power, scanning speed, and powder feed rate, where the molten pool characteristics include the inner region area, the molten pool area, and the relative standard deviation of the inner region area. The results indicate that the molten pool area is hard to reflect the variations of the process parameters in BL-DED AlSi7Mg materials, as shown in Appendix Ⅰ. An important reason is that the liquid metal with a small grayscale in the outer region mists the molten pool boundary, where the floating slags on the surface of the outer region aggravate the monitoring degree of difficulty. When it comes to the inner region area, (a) presents the influence of the process parameters on the inner region areas. With a higher laser power and lower scanning speed, the inner region area raises when the outer region characteristic mode does not transfer between the obscure and obvious slags. When transferring behaviour occurs, the inner region areas increase rapidly. shows the distribution of molten pool images which have different inner and outer region characteristics under different process parameters. Based on the similarity principle, the change regulations of the relative standard deviation of inner region areas, meaning the convection state, is also obviously special in (b). For an invariant outer region characteristic mode, the irregular convection states strengthen, meaning the unstable melting and flowing states, with the increment in the scanning speeds and the decrement in the laser power. In general, the large inner region area indicates a relatively stable state with a low irregular convection condition and avoids accidental interference, such as the powder impact. Considering the powder feed rate at a low laser power, the inner region areas raise and the relative standard deviations descend for a higher powder feed rate. However, when the laser power is normal, the variation tendency is the opposite. It can be ascribed to the reason that massive powders cannot be melted with low laser power. The more unmelted powders lead to a larger inner region area and a more irregular convection state. When the laser power is appropriate, the powders can be melted nearly completely. The smaller powder feed rate results in a larger inner region and a smaller relative standard deviation. Two reasons contribute to this situation. One reason is that the low line mass (f/v) leads to a low layer height, and produces a two-dimension image difference, as shown in . The other one is that the fewer powders make less energy to melt the solid metal, so that more energy can be preserved to maintain the convection state of the molten pool.
Figure 9. Molten pool characteristics of different laser powers, scanning speeds, and powder feed rates. The circle sizes represent (a) inner region area and (b) relative standard deviation of the inner region area, respectively.
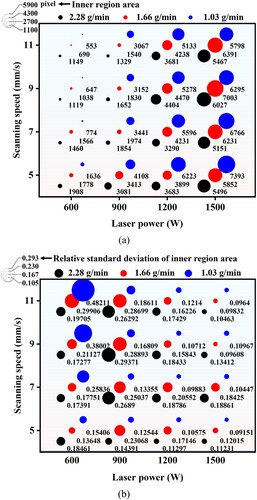
Figure 10. Distribution of Molten pool images which have different inner and outer region characteristics under different process parameters.
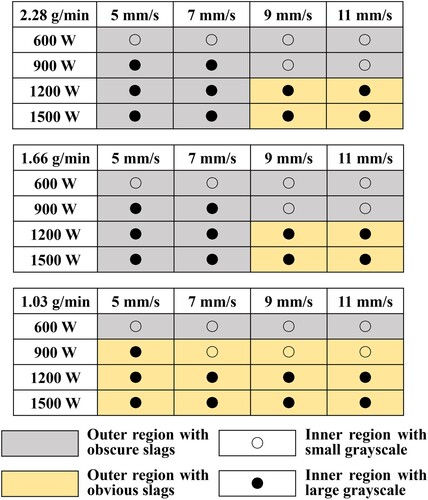
Based on the analysis above, the inner region has a better ability than the molten pool entirety to indicate the change of process parameters in the single-layer single-track deposition. The relative standard deviation of the inner region area has the potential to reflect the convection states. In addition, the characteristics of the inner region and outer region have relationships with appearance defects, as illustrated in . The monitoring ability of the molten pool in BL-DED AlSi7Mg will be discussed in Section 4.2.
3.2.2. Multi-layer single-track stacking thin wall
In the multi-layer single-track stacking thin wall, the heat accumulation remarkably influences the molten pool characteristics. With the increase in layer number, the heat accumulation leads to a more violent convection state, and results in more obvious characteristics of the inner region, as seen in . In the first layer, the slags and unmelted powders gather in the inner region with overexposure phenomenon. In the second layer, the strengthened convection state forces the slags and unmelted powders to float at the edge of the inner region. In the following layers, few slags and powders can exist in the centre of the inner region, and the inner region area tends to enhance first and then remain relatively stable. In the multi-layer single-track stacking thin wall, the molten pool characteristics are similar to that in .
Figure 11. Molten pool images and inner region areas of different layers in multi-layer single-track stacking thin wall.
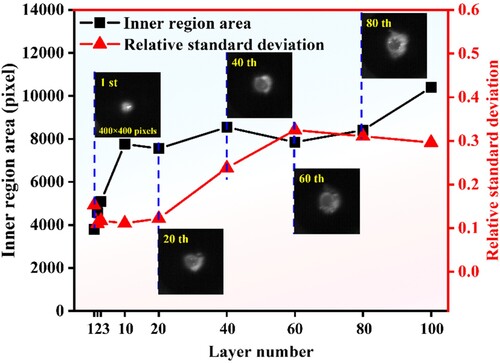
For the comparison between the inner and outer region, the large grayscale of the inner region restrains the observation of the small grayscale outer region more evidently than that in the single-layer single-track deposition. The variation tendencies of the inner region characteristics are provided in . The molten pool images are captured at the same location of every layer when the molten pools are relatively stable. The result shows that the inner region areas and their relative standard deviations both raise with the layer number increases, contributing to the heat accumulation. Compared with the outer region, the inner region characteristics have more potential to predict the product qualities.
3.3. Appearance analysis of single-layer single-track deposition layer
The appearance analysis of a single-layer single-track deposition layer can supply some effective information to optimize the process parameters. If the relationship among the molten pool characteristics, depositing states, and appearance defects can be built, it is an efficient way to realize a rapid optimization of the process parameters. The rapid optimization is necessary for rapid manufacturing and remanufacturing. Based on the appearances of the single-layer single-track deposition layers, there are three types of depositing states and defects, as seen in .
The first type is the unstable depositing state. At this state, as shown in , the layer is either not continuous or has a too low height and inhomogeneous width, where many situations can cause the depositing state. The molten pool images at the state have an orange background in . The low energy input (P/v) or powder feed rate (f) may lead to the problem with the small grayscale in the inner region or obvious slags in the outer region. When the energy input is not enough, instead of decreasing the scanning speed, increasing laser power is easier to turn the depositing state from the first type to the second type. It is contributed that the line mass (f/v) increases with the reduction in scanning speed, thus changing the ratio of laser power to melting powder quality.
The second type is the normal depositing state. At the depositing state, the grayscale of the inner region is relatively large (), in which the molten pool images have a green background. In general, few appearance defects are observed in the deposition layer. The energy input can maintain a better deposition height and more stable width than the other two depositing states.
The third type is the excessive depositing state. At the depositing state, the grayscale of the inner region is similar to that of the normal depositing state, but with few slags in the outer region. Few slags can pass through the outer region, which leads to an unclear edge. It can be ascribed to the increment in the layer height, which has been clarified in . Here, the deposition layer has a large height and wetting angle. When it comes to overlap, pores are easy to emerge in the overlapping position (Onwubolu et al. Citation2007).
3.4. Appearance defects in multi-layer single-track stacking thin wall
There are four types of appearance defects in the multi-layer single-track stacking thin wall, as shown in . The first type is named edge tilt. The molten pool images of ① can reflect the process of the initiation of defects. First, the original error results from the curved edge of deposited layers, which influences the degree of stability of the molten pool. It makes the molten pool area decline and reduces the powder capturing efficiency. The low capturing efficiency leads to a shorter edge than the last layer. For a short edge, the inner region area enlarges and almost covers the molten pool in the future, contributing to the increment in the defocusing amount. The increasing defocusing amount makes the laser beam radiate the powder flow focal point before the powders touch the molten pool. A great number of unmelted powders with large grayscale enhance the molten pool grayscale under the laser radiation. As a result of the continuous circular processing, the short edge accumulates to occur the edge tilt. Therefore, to avoid the defect, increasing the residence time at the edge is an effective method.
Figure 12. Four types of defects and their molten pool images in the multi-layer single-track stacking thin wall.
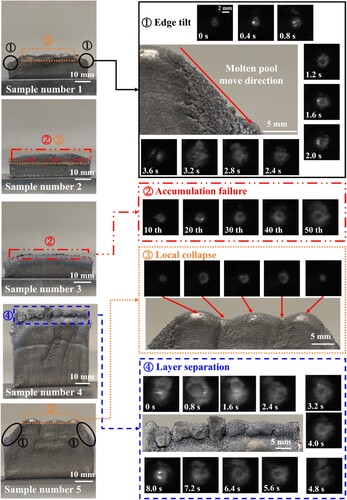
The second type is accumulation failure, as shown in ②. It results from a large distance between the laser head and the deposited layer. The main reason is that the Z-axis increment is too large compared to the layer height. It is unable to accumulate successfully with a small layer height and a large layer width. The distance leads to a positive focused state, which cannot keep the BL-DED in a self-optimization state (Donadello et al. Citation2022).
The third type is a local collapse, as illustrated in ③. It results from an unstable contour profile of the molten pool. The unsteadiness is mainly from the low melting point, high reflectance, and low viscosity of aluminium alloy, which leads to a violent flow in the molten pool. The phenomenon results in an error, and then, with the cycles by layer, the error will gradually convert to the local collapse defect. Based on the coaxial visual characteristics, the variation tendency of the molten pool is clear. When the error occurs, the inner region starts to fluctuate, and then, its area gradually increases. The reason for the area change is the same as that in the first and second types. Under the error occurrence, the operation staff can adjust the process parameters to avoid worse, and then, fill the local collapse.
The fourth type is layer separation, as shown in ④. This type of defect is the one follow-up appearance when the thin wall is enough high. During the deposition of the thin walls, a massive amount of sintered powders heap up on the side surface of the thin wall. This phenomenon is also found in the other aluminium alloy stacking thin wall research (Kiani et al. Citation2020; Singh, Ramakrishnan, and Dinda Citation2017) and titanium alloy deposition research (Sinclair et al. Citation2022). When the sintered powders of both side surfaces overtop the layers, the powders concentrate on the deposited layers. Once the sintered powder layer on one side is melted into the thin wall, the layer separation defects occur. Through the layer-by-layer processing, the defect aggravates.
4. Discussions
4.1. Metallurgical behaviours of the molten pool
The relationship between the molten pool characteristic and the metallurgical behaviour is essential for understanding the process mechanisms, and provides the basal theories to improve the product qualities. Metallurgical behaviours inside the molten pool during BL-DED consist of a) the melting, flowing, and solidifying states and b) interactions among liquid metal, air, and slags. The interactions among liquid metal, air, and slags have been elucidated in Sections 3.1 and 3.2 in detail.
The melting state is the solid-to-liquid phase transition process of the metallic material. The melting states relate to the layer appearance directly (Tang et al. Citation2019). The unstable depositing, the normal depositing, and the excessive depositing states, which indicate the layer appearances, have been defined in Section 3.3. Therefore, the different characteristics of the molten pool can indicate the melting states, as seen in . Given the flowing state, it includes the flowing velocities, flowing directions, oscillation level, etc. The forming mechanisms of the inner region are mainly ascribed to the liquid metal flowing and slags floating, which have been interpreted in Sections 3.1 and 3.2. Therefore, the inner region has the potential to indicate the flowing state. Section 2.4 has shown the characterization methods for the inner region. The flowing velocities and directions can be tracked by the slags on the molten pool. In addition, the flowing state is commonly considered to relate to the dilution depth. Tang et al. (Tang et al. Citation2020) used the coaxial two-dimension images of the molten pool in laser surface melting to indicate the flowing state, and predict the dilution depths based on the flowing characteristics. Caprio et al. (Caprio, Demir, and Previtali Citation2020) also applied a similar method in the laser powder bed fusion. Therefore, the inner region can represent the flowing state. When it comes to the solidifying state, it is challenging to indicate the solidifying states directly based on the molten pool characteristics owing to a large number of slags, the paraxial visual field, and the limitation of the coaxial passive lighting. The coaxial active lighting may be a way to give the correlation between the molten pool characteristics and the solidifying state in processing AlSi7Mg by BL-DED. However, the light path design and alteration are complex.
4.2. Appearance defect monitoring based on the molten pool characteristics
Based on the research in Section 3, the coaxial camera, the paraxial high-speed camera, and the paraxial infrared camera have several features for monitoring appearance defects.
Coaxial camera. Coaxial monitoring can track the molten pool during all DED processes. Compared to the molten pool images of 316L, EN25, and 18Ni300 powders in the references (Tang et al. Citation2021), (Sampson et al. Citation2020), and (Chen et al. Citation2019), respectively, it is difficult to observe the molten pool outlines based on passive lighting due to existing slag and a great grayscale gap between the inner and outer regions. Especially, the traditional characteristics, such as the width, length, and area of the molten pool, are not easy to be obtained when processing AlSi7Mg powders. The active lighting can supply a better visual effect, but it is hard to integrate into the blue laser head. The inner region characteristics presented in the work have the ability to indicate the melting and flowing states of the molten pool, and thus, it is a way to realize the quality monitoring.
Paraxial high-speed camera. The high-speed camera has a high frame rate to clear the process mechanisms, and it is also easy to apply the paraxial high-speed camera with a lighting source and an enlarging lens. The images are well clear to show the characteristics. But the visual field and focus depth restrict the application of the paraxial high-speed camera in monitoring DED. It is suited to study the deposition mechanisms.
Paraxial infrared camera. The infrared camera can avoid the interference of flying powders, but massive slags and sintered powders in BL-DED aluminium alloy reduce the monitoring accuracy of the infrared camera, due to the various emissivity. Meanwhile, the monitoring accuracies for the single-layer single-track depositing and single-layer multi-track overlapping processes are considerable problems.
Therefore, the coaxial camera monitoring is performed in both the single-layer single-track deposition layer and the multi-layer single-track stacking thin wall. The infrared is applied to monitor the thin wall stacking.
4.2.1. Single-layer single-track deposition layer
The unstable depositing, normal depositing, and excessive depositing states have been presented in Section 3.3, where the functionality of these states is to map the appearance defects. The recognition processes of these states are seen in . The molten pool characteristics and the appearance defects both have a nonlinear relationship with the powder feed rates because of the coupling effect of line mass (f/v) and mass energy (P/f), as shown in and . Therefore, the powder feed rate is not an adjustable process parameter during in-situ monitoring and control of BL-DED. For the low power feed rate at 1.03 g/min, two depositing states are observed: unstable and normal depositing states. When it meets two conditions, it is a normal depositing state or else an unstable depositing state. One condition is that the grayscale of the inner region is large with the overexposure phenomenon. The other condition is that the inner region area is greater than x1 which is decided by the experimental conditions. Considering the middle powder feed rate at 1.66 g/min, when the inner region grayscale is large with the overexposure phenomenon and obvious slags are observed in the outer region, the depositing state is normal, or the state is unstable. For the high powder feed rate at 2.28 g/min, the small grayscale of the inner region means an unstable depositing state. If the grayscale of the inner region is large, there are obscure slags in the outer region, and the inner region area is greater than x2, the relative standard deviation (RSD) of the inner region area is less than y, the process state is excessive depositing. The other situations belong to normal depositing. The requested wet angle, x1, x2, and y values all need to be decided based on the actual working conditions. When applying the experimental conditions in the work, the wet angle, x1, x2, and y can be assigned as 70°, 7000, 3500 pixels, and 0.12, respectively.
4.2.2. Multi-layer single-track stacking thin wall
has shown the evolutionary process of the coaxial visual characteristics when the defects occur and aggravate. The real-time temperatures of the molten pool during the generation of defects are provided in . The molten pool and deposition layer temperature changes with the layer number increasing from the paraxial infrared camera are in .
Edge tilt. Considering the coaxial characteristics where the defect emerges, the inner region outline at the layer edge is not regular for insufficient residence time at the edges. With the defect aggravating, the inner region area enlarges, owing to the increment in the defocusing amount. Meanwhile, incremental unmelted powders going through the laser beam raise the grayscale of the inner region, as described in ①. For the temperature features, the real-time temperature increases evidently as shown in (a) and (d). The main reason is that the raising defocusing amount results in preheating the metal powders. Meanwhile, the massive powders cannot enter the molten pool and distribute near the molten pool. Compared with the liquid molten pool, the solid metal powders have a similar temperature but with high emissivity. Therefore, the temperature is larger.
Accumulation failure. The coaxial visual and paraxial temperature characteristics have an obvious representation when the defect occurs. For the coaxial characteristics when the distance increases, the images in ② will turn blurry due to the limit of the focus depth. Simultaneously, the incremental distance makes the amounts of powders suffer laser radiating, and enlarges the outer region grayscale. Similar to the edge tilt, the accumulation failure defect will lead to the increment in the real-time temperature of the molten pool when it comes to the temperature feature, as shown in (b). The defocusing amount also makes part of the laser energy not melt the metal powders, and heats the deposited layers. Thus, the deposition layer temperature increases more obviously when an accumulation failure defect appears, as seen in .
Local collapse. Similar to the first and second types, the inner region starts to fluctuate with a gradual increase in its area when the error occurs. When the error develops into the local collapse defect, the inner region areas change circularly, as exhibited in ③. It attributes to the variation trend of the defocusing amount. Compared with coaxial characteristics, the temperature characteristics are not very explicit.
Layer separation. The type of defect is simple to be monitored by both coaxial characteristics and temperature characteristics, because the defect impacts the energy and powder distribution seriously. Focusing on the coaxial characteristics, ④ shows the molten pool characteristics when the deposited layer separation defect occurs, and the one molten pool is split into two or three molten pools. Meanwhile, the defect also raises the molten pool temperature dramatically due to the sintered powders on the layer surface impacting the temperature measuring, as shown in (c) and .
Figure 14. Real-time temperature of the molten pool when generating defects: (a) edge tilt and local collapse, (b) local collapse, (c) local collapse and deposition layer separation, (d) edge tilt and local collapse.
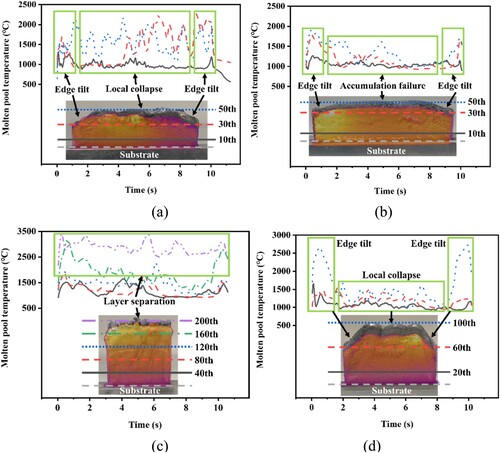
Figure 15. Variation trends of the molten pool temperature (MPT) and deposition layer temperature (DLT) in the fixed region with different defects. Sample number 1: edge tilt and local collapse; Sample number 2: local collapse; Sample number 4: local collapse and deposition layer separation; Sample number 5: edge tilt and local collapse.
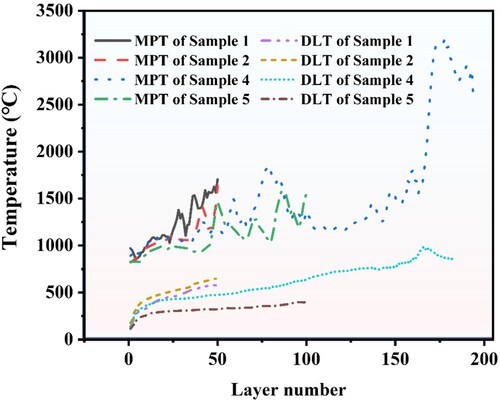
In conclusion, the coaxial characteristics, such as the inner region mentioned in the work, have the potential to indicate the appearance defects in both the single-layer single-track deposition layer and multi-layer single-track stacking thin wall of AlSi7Mg powders. The paraxial temperature characteristics can monitor the appearance defects of thin walls. Due to the complex forming mechanisms of the molten pool characteristics, deep learning algorithms are more suited to monitor the product qualities in the future (Akbari et al. Citation2022).
4.3. Advantages of BL-DED on aluminium alloy
Some researchers have utilized the infrared laser to melt the AlSi10Mg powders, which are similar to AlSi7Mg powders in previous works (Kiani et al. Citation2020; Gao et al. Citation2019; Wang et al. Citation2019; Chen et al. Citation2018). (Wang, Wu, and Wang Citation2021) have reviewed that the blue laser processing aluminium alloy has the advantages of a high absorption rate to a) enable the material to be melted under low power conditions; b) result in a more stable deposition process. Considering the laser energy input, some researchers have done a few works (Kiani et al. Citation2020; Gao et al. Citation2019; Wang et al. Citation2019; Chen et al. Citation2018) in which most infrared energy inputs are between 71∼222 W/mm2. Based on the results from these works, the blue laser can fabricate a deposition layer with a relatively well appearance as low as 54 W/mm2. In addition, the appearance of the single-layer single-track deposition layer in this work is better in terms of the deposition process with more uniform widths than the results in the reference (Kiani et al. Citation2020). Compared with the single layer, though the differences of the stacking thin walls are not very obvious, the thin walls with fine product quality can still be produced through in-situ adjusting the defocusing amount layer to layer as shown in . The difference between the single layer and thin wall is potentially caused by the increased sensitivity of the high absorption rate to the glossy surface of the substrate in the single-layer single-track deposition layer compared to the coarse surface of the deposited layer in the multi-layer single-track stacking thin wall. The better appearances during the application of the blue laser instead of the infrared laser, are attributed to the improved stability of the molten pool with the low power conditions. Another potential cause for this phenomenon is that the absorption rates of the solid, mushy, and liquid aluminium alloy respond in a different manner to the infrared laser. Then, due to massive slags and unmelted powders floating on the molten pool surface, the various absorption rates disturb the depositing states. In contrast to the low absorption rates of the infrared laser, the high absorption rates of the blue laser have possible to restrain the situation. Therefore, to a certain extent, the aluminium alloy forming by the blue laser has better appearance quality than that by the infrared laser.
5. Conclusions
We simultaneously captured the molten pool characteristics in 2000 W BL-DED of AlSi7Mg with a coaxial camera, a paraxial high-speed camera, and a paraxial infrared camera. We built the relationships among the process parameters, the inner region characteristics, deposition states, and appearance defects based on the experimental results. In addition, we successfully deposited the AlSi7Mg curved thin wall with good appearance quality. The following conclusions have been achieved:
A molten pool can be separated into two regions: the inner one and the outer one. The inner region areas, the slags in the outer region, and the relative standard deviations of the inner region areas can be applied to indicate the melting and flowing states of the molten pool. The large grayscale of the inner region characteristics results from the high temperature slags and unmelted powders vaporizing or burning. The liquid metal and low temperature slags lead to the small grayscale of the inner region characteristics.
Defect monitoring is necessary for AlSi7Mg material in BL-DED. However, monitoring the molten pool during the depositing of the AlSi7Mg powders is more difficult than the other metal materials due to the factors including the massive slags above the molten pool, the sintered powders on the side surface, and unsharp outer regions. This work provides a preliminarily possible characteristic, the inner region, to monitor the appearance defects.
There are three depositing states which can be monitored based on the relationships among the inner region area, RSD of the inner region area, the inner region grayscale, and the slag distribution in the outer region. The unstable depositing state leads to a layer that is either incontinuous or has a too low height and inhomogeneous width. For the normal depositing state, few appearance defects generate. At the excessive depositing state, the deposition layer has a large height and wetting angle.
There are four types of appearance defects in the multi-layer single-track stacking thin wall, which include the edge tilt, accumulation failure, local collapse, and layer separation. Low powder capturing efficiency resulted from the curved edge of deposited layers; the increasing defocusing amount from the large Z-axis increment; the unstable molten pool of AlSi7Mg; the sintered powders heaping up on the side surface of the deposited layers, contribute to the four appearance defects, respectively. The irregular shape of the inner region at the layer edge; the obvious increase of the inner region area and outer region grayscale; the circularly changed inner region areas; more molten pools are the main indicators for the four defects, respectively.
The blue laser has the advantage of forming AlSi7Mg parts. Compared with the conventional infrared laser, the blue laser can enable the material to be melted under low power conditions and result in a more stable deposition process. Future research should focus on the effect of blue laser on the microstructure and properties of AlSi7Mg.
This work analyzes the molten pool characteristics in BL-DED of both AlSi7Mg single layer and thin wall. The captured molten pool behaves great potential for rapid process parameter designing, process monitoring, and feedback control. In the further, this work can be extended to processes with other feedstocks, substrate materials, or energy sources.
Declaration of competing interest
The authors declare that they have no known conflicting financial interests or personal relationships that could have appeared to influence the work reported in this paper.
Supplemental Material
Download MS Word (483.7 KB)Acknowledgments
This work is sponsored by the National Natural Science Foundation of China (52105469, 52075327, and 52004160), China Postdoctoral Science Foundation (2021M692038), Shanghai Sailing Program (20YF1419200), Natural Science Foundation of Shanghai (20ZR1427500), and Major Science and Technology Project of Huaibei (Z2020001).
Disclosure statement
No potential conflict of interest was reported by the author(s).
Correction Statement
This article has been corrected with minor changes. These changes do not impact the academic content of the article.
Additional information
Notes on contributors
Zijue Tang
Zijue Tang is a post-doctoral research fellow at the School of Materials Science and Engineering, Shanghai Jiao Tong University. His main research interests are laser manufacturing, additive manufacturing process monitoring, green manufacturing, etc.
Qianglong Wei
Qianglong Wei is a M.S. student at the School of Materials Science and Engineering, Shanghai Jiao Tong University. His research interest is the simulation of laser directed energy deposition.
Zhenyang Gao
Zhenyang Gao is a PhD student at the School of Materials Science and Engineering, Shanghai Jiao Tong University. His research activities mainly focus on additive manufacturing lattice structure materials.
Huihui Yang
Huihui Yang is a post-doctoral research fellow at the School of Materials Science and Engineering, Shanghai Jiao Tong University. Her main research interest is process control of selective laser melting.
An Wang
An Wang is a PhD student at the School of Materials Science and Engineering, Shanghai Jiao Tong University. His main research interests are process control and performance analysis of blue laser directed energy deposition.
Le Wan
Le Wan is a post-doctoral researcher fellow at the School of Materials Science and Engineering, Shanghai Jiao Tong University. His main research interest is process control and analysis of blue laser directed energy deposition.
Cheng Luo
Cheng Luo is a post-doctor at the School of Mechanical Engineering, Shanghai Jiao Tong University. Her main research interest is joining of additive manufacturing components.
Yi Wu
Yi Wu is a Senior Engineer at the School of Materials Science and Engineering, Shanghai Jiao Tong University. His main research interest is high-performance additive manufacturing of aluminium alloys
Haowei Wang
Haowei Wang is a professor at the School of Materials Science and Engineering, Shanghai Jiao Tong University. His main research interest is high-performance aluminium matrix composite materials.
Hongze Wang
Hongze Wang is an associate professor at the School of Materials Science and Engineering, Shanghai Jiao Tong University. His main research interests are laser additive manufacturing and in-situ imaging of manufacturing process.
References
- Akbari, P., F. Ogoke, N. Y. Kao, K. Meidani, C. Y. Yeh, W. Lee, and A. B. Farimani. 2022. “MeltpoolNet: Melt Pool Characteristic Prediction in Metal Additive Manufacturing Using Machine Learning.” Additive Manufacturing 55): 102817. doi:10.1016/j.addma.2022.102817.
- Asano, K., M. Tsukamoto, Y. Funada, Y. Sakon, N. Abe, Y. Sato, R. Higashino, M. Sengoku, and M. Yoshida. 2018. “Copper Film Formation on Metal Surfaces with 100 W Blue Direct Diode Laser System.” Journal of Laser Applications 30 (3): 032602. doi:10.2351/1.5040635.
- Brandau, B., A. Da Silva, C. Wilsnack, F. Brueckner, and A. F. H. Kaplan. 2022. “Absorbance Study of Powder Conditions for Laser Additive Manufacturing.” Materials & Design 216): 110591. doi:10.1016/j.matdes.2022.110591.
- Britten, S. W., L. Schmid, T. Molitor, and M. Rütering. 2020. “Blue High-Power Laser Sources for Processing Solutions in e-Mobility and Beyond.” Procedia CIRP 94: 592–595. doi:10.1016/j.procir.2020.09.082.
- Caprio, L., A. G. Demir, and B. Previtali. 2020. “Observing Molten Pool Surface Oscillations During Keyhole Processing in Laser Powder bed Fusion as a Novel Method to Estimate the Penetration Depth.” Additive Manufacturing 36): 101470. doi:10.1016/j.addma.2020.101470.
- Chen, B., Y. Z. Yao, Y. H. Huang, W. K. Wang, C. W. Tan, and J. C. Feng. 2019. “Quality Detection of Laser Additive Manufacturing Process Based on Coaxial Vision Monitoring.” Sensor Review 39 (4): 512–521. doi:10.1108/SR-03-2018-0068.
- Chen, B., Y. Z. Yao, X. G. Song, C. W. Tan, L. Cao, and J. C. Feng. 2018. “Microstructure and Mechanical Properties of Additive Manufacturing AlSi10Mg Alloy Using Direct Metal Deposition.” Ferroelectrics 523 (1): 153–166. doi:10.1080/00150193.2018.1392147.
- Das, A., R. Fritz, M. Finuf, and I. Masters. 2020. “Blue Laser Welding of Multi-Layered AISI 316L Stainless Steel Micro-Foils.” Optics & Laser Technology 132): 106498. doi:10.1016/j.optlastec.2020.106498.
- Donadello, S., V. Furlan, A. G. Demir, and B. Previtali. 2022. “Interplay Between Powder Catchment Efficiency and Layer Height in Self-Stabilized Laser Metal Deposition.” Optics and Lasers in Engineering 149): 106817. doi:10.1016/j.optlaseng.2021.106817.
- Doubenskaia, M., M. Pavlov, S. Grigoriev, and I. Smurov. 2013. “Definition of Brightness Temperature and Restoration of True Temperature in Laser Cladding Using Infrared Camera.” Surface and Coatings Technology 220: 244–247. doi:10.1016/j.surfcoat.2012.10.044.
- Feng, W., Z. Z. Mao, Y. Yang, H. Ma, K. Zhao, C. Q. Qi, C. Hao, Z. W. Liu, H. M. Xie, and S. Liu. 2022. “Online Defect Detection Method and System Based on Similarity of the Temperature Field in the Melt Pool.” Additive Manufacturing 54): 102760. doi:10.1016/j.addma.2022.102760.
- Gao, Y., J. B. Zhao, Y. H. Zhao, Z. G. Wang, H. W. Song, and M. Q. Gao. 2019. “Effect of Processing Parameters on Solidification Defects Behavior of Laser Deposited AlSi10Mg Alloy.” Vacuum 167: 471–478. doi:10.1016/j.vacuum.2019.06.042.
- Hara, T., Y. Sato, R. Higashino, Y. Funada, T. Ohkubo, K. Morimoto, N. Abe, and M. Tsukamoto. 2020. “Pure Copper Layer Formation on Pure Copper Substrate Using Multi-Beam Laser Cladding System with Blue Diode Lasers.” Applied Physics A 126 (6): 418. doi:10.1007/s00339-020-03559-6.
- International A. Standard Guide for Directed Energy Deposition of Metals. West Conshohocken, PA.: ASTM International. https://www.astm.org/f3187-16.html.
- Jia, H. L., H. Sun, H. Z. Wang, Y. Wu, and H. W. Wang. 2022. “Size Effect in Selective Laser Melting Additive Manufacturing of 700 mm Large Component.” Journal of Manufacturing Processes 75: 125–137. doi:10.1016/j.jmapro.2022.01.011.
- Kiani, P., A. D. Dupuy, K. K. Ma, and J. M. Schoenung. 2020. “Directed Energy Deposition of AlSi10Mg: Single Track Nonscalability and Bulk Properties.” Materials & Design 194): 108847. doi:10.1016/j.matdes.2020.108847.
- Ono, K., Y. Sato, Y. Takazawa, Y. Morimoto, K. Takenaka, Y. Yamashita, Y. Funada, N. Abe, and M. Tsukamoto. 2021. “Development of High Intensity Multibeam Laser Metal Deposition System with Blue Diode Lasers for Additively Manufacturing of Copper rod.” Journal of Laser Applications 33 (4): 042014. doi:10.2351/7.0000510.
- Onwubolu, G. C., J. P. Davim, C. Oliveira, and A. Cardoso. 2007. “Prediction of Clad Angle in Laser Cladding by Powder Using Response Surface Methodology and Scatter Search.” Optics & Laser Technology 39 (6): 1130–1134. doi:10.1016/j.optlastec.2006.09.008.
- Prasad H, Siva, F. Brueckner, and A. F. H. Kaplan. 2020. “Powder Incorporation and Spatter Formation in High Deposition Rate Blown Powder Directed Energy Deposition.” Additive Manufacturing 35: 101413. doi:10.1016/j.addma.2020.101413.
- Sampson, R., R. Lancaster, M. Sutcliffe, D. Carswell, C. Hauser, and J. Barras. 2020. “An Improved Methodology of Melt Pool Monitoring of Direct Energy Deposition Processes.” Optics & Laser Technology 127: 106194. doi:10.1016/j.optlastec.2020.106194.
- Sinclair, L., S. J. Clark, Y. H. Chen, S. Marussi, S. R. Shah, O. V. Magdysyuk, R. C. Atwood, G. J. Baxter, M. Jones, D. G. McCartney, et al. 2022. “Sinter Formation During Directed Energy Deposition of Titanium Alloy Powders.” International Journal of Machine Tools and Manufacture 176): 103887. doi:10.1016/j.ijmachtools.2022.103887.
- Singh, A., A. Ramakrishnan, and G. P. Dinda. 2017. “Direct Laser Metal Deposition of Eutectic Al-Si Alloy for Automotive Applications.” TMS, 146t. h Annual Meeting & Exhibition Supplemental Proceedings2017. p. 71-80. Springer International Publishing.
- Tang, Z. J., W. W. Liu, Z. R. Yan, H. Wang, and H. C. Zhang. 2019. “Study on Evolution Behavior of Geometrical Accuracy Based on Dynamic Characteristics of Molten Pool in Laser-Based Direct Energy Deposition.” Journal of Mechanical Engineering 55 (15): 39–47. doi:10.3901/JME.2019.15.039.
- Tang, Z. J., W. W. Liu, Y. W. Wang, K. M. Saleheen, Z. C. Liu, S. T. Peng, Z. Zhang, and H. C. Zhang. 2020a. “A Review on in Situ Monitoring Technology for Directed Energy Deposition of Metals.” The International Journal of Advanced Manufacturing Technology 108 (11-12): 3437–3463. doi:10.1007/s00170-020-05569-3.
- Tang, Z. J., W. W. Liu, N. Zhang, Y. W. Wang, and H. C. Zhang. 2020. “Real-time Prediction of Penetration Depths of Laser Surface Melting Based on Coaxial Visual Monitoring.” Optics and Lasers in Engineering 128: 106034. doi:10.1016/j.optlaseng.2020.106034.
- Tang Z-j,: Liu W-w, Zhu L-n, Liu Z-c, Yan Z-r, Lin D, Zhang Z, Zhang H-C. 2021. “Investigation on Coaxial Visual Characteristics of Molten Pool in Laser-Based Directed Energy Deposition of AISI 316L Steel.” Journal of Materials Processing Technology 290 (290): 116996. doi:10.1016/j.jmatprotec.2020.116996.
- Wang, H., Y. Kawahito, R. Yoshida, Y. Nakashima, and K. Shiokawa. 2017. “Development of a High-Power Blue Laser (445 nm) for Material Processing.” Optics Letters 42 (12): 2251–2254. doi:10.1364/OL.42.002251.
- Wang , X., L. Q. Li, J. Y. Qu, and W. Tao. 2019. “Microstructure and Mechanical Properties of Laser Metal Deposited AlSi10Mg Alloys.” Materials Science and Technology 35 (18): 2284–2293. doi:10.1080/02670836.2019.1674022.
- Wang, A., H. Z. Wang, Y. Wu, and H. W. Wang. 2021. “3D Printing of Aluminum Alloys Using Laser Powder Deposition: A Review.” The International Journal of Advanced Manufacturing Technology 116 (1-2): 1–37. doi:10.1007/s00170-021-07440-5.
- Wang, H., Y. Wu, and H. Wang. 2021. “Current Status of Applying the Blue Laser in Nonferrous Metals Processing.” Chin J Nonferrous Met 31 (11): 3059–3070. doi:10.11817/j.ysxb.1004.0609.2021-42030.
- Yan, Z. R., W. W. Liu, Z. J. Tang, X. Y. Liu, N. Zhang, Z. Q. Wang, and H. C. Zhang. 2019. “Effect of Thermal Characteristics on Distortion in Laser Cladding of AISI 316L.” Journal of Manufacturing Processes 44: 309–318. doi:10.1016/j.jmapro.2019.06.011.
- Yang, H., J. Wu, Q. Wei, Z. Tang, A. Wang, X. Jin, X. Li, Y. Wu, G. Lu, H. Wang, et al. 2022. “Stable Cladding of High Reflectivity Pure Copper on the Aluminum Alloy Substrate by an Infrared-Blue Hybrid Laser.” Additive Manufacturing Letters 3: 100040. doi:10.1016/j.addlet.2022.100040.
Appendix Ⅰ
Molten pool areas of different laser powers, scanning speeds, and powder feed rates..