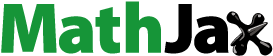
ABSTRACT
Multi Jet Fusion (MJF) has attracted extensive attention because of its ability to print support-free complex structures. However, the mechanical properties of MJF-printed polymer parts are still unsatisfactory for certain industrial requirements. Herein, by leveraging the fibre reinforcement effect and high specific strength of polyimide (PI) fibres, this work developed PI/polyamide 12 (PA12) composites with largely enhanced mechanical performance via MJF. Specifically, the tensile strength and modulus were increased by 43% and 42%, and the flexural strength and modulus were improved by 39% and 46%, respectively, compared to those of the neat PA12 parts. Furthermore, the incorporation of lightweight PI fibres endowed the composites with high specific tensile strength (67.60 kN·m/kg) and specific flexural strength (93.70 kN·m/kg), which are superior to those of MJF-printed PA12 composites reinforced with other fibres. This work provides new insights into enhancing the mechanical performance of lightweight parts printed by MJF and other powder-based techniques.
1. Introduction
The advent of additive manufacturing (AM) opens new avenues for creating objects of complex and arbitrary geometries from computer-aided designs without the need for any specific mold [Citation1–7]. Among various AM methods, powder bed fusion (PBF) techniques are especially competitive in producing polymeric parts with sophisticated details in a support-free manner [Citation8–10]. Examples of polymer-based PBF techniques include multi jet fusion (MJF) and selective laser sintering (SLS). Compared to the pointwise and time-consuming SLS technique, the HP MJF technique, which combines inkjet printing and powder-based AM process, offers a high-speed and cost-effective system for three-dimensional (3D) printing [Citation11–15]. Therefore, MJF has received considerable attention because of the ability to produce sophisticated industrial-grade functional parts and prototypes. Polyamide 12 (PA12) is the most commercially available engineering plastic for MJF processes, owing to its moderate melting temperature and the wide fusing window [Citation16–18]. However, MJF-printed neat PA12 parts exhibit an ultimate tensile strength (UTS) of around 48 MPa and a tensile modulus of lower than 2 GPa, thereby limiting their applications in various industries [Citation16]. In addition to high tensile strength and modulus, superior specific strength (i.e., high ratio of strength to weight) is an essential technical specification for applications, especially in the aerospace and automobile sectors.
Being able to achieve properties that are superior to each individual component, 3D-printed filler/polymer composite parts exhibit largely enhanced properties such as mechanical strength and thermal stability [Citation16,Citation19–23]. Various fillers have been exploited and incorporated into the polymer matrix for AM material development, such as glass beads (GBs) [Citation24,Citation25], glass fibres (GFs) [Citation26,Citation27], carbon fibres (CFs) [Citation28–30], carbon black [Citation31], graphene [Citation32], multi-wall carbon nanotubes [Citation22], and boron nitride [Citation33]. However, the unique printing mechanism of MJF, in which the powder particles are selectively fused with the aid of a dark-coloured fusing agent that absorbs infrared (IR) radiation, largely limits its feedstock options, making dark reinforcements such as CFs in feedstocks inapplicable to MJF [Citation11].
To date, the reported reinforcements for MJF are limited to the white GBs [Citation34,Citation35] and GFs [Citation36–38], and the slightly yellow aramid fibres (AFs) [Citation39,Citation40]. Compared to the MJF-printed neat PA12 parts, the tensile modulus of the MJF-printed GB/PA12 composites was increased to around 2.5 GPa, but the tensile strength was decreased to around 30.0 MPa [Citation35]. Taking advantage of the fibre alignment effect during MJF printing, our group demonstrated an anisotropic improvement in the mechanical properties of MJF-printed PA12 composites reinforced with GFs and AFs. Along the fibre alignment direction, the PA12 composite parts with the incorporation of 20 wt% GFs exhibited a largely improved tensile modulus of 4.02 GPa [Citation36]. Compared to parts reinforced with inorganic fillers, the 12 wt% organic AF-reinforced PA12 composite parts not only resulted in a substantially increased UTS of 60.41 MPa, but also maintained the lightweight characteristic [Citation39]. Furthermore, it has been demonstrated that high-temperature annealing for improving the crystallinity of composite parts and fibre surface modification for enhancing the interfacial adhesive force between the fibre and the polymeric matrix can further strengthen the mechanical properties of MJF-printed composite parts [Citation37,Citation40,Citation41]. Since GB/PA12 mixed powder is the only commercially available mixed powder used for MJF to date, the development of new high-performance composite materials suitable for industrial upscaling is still challenging and attractive.
Polyimide (PI) fibres are high-performance lightweight polymer fibres and show promising outlook in sectors including military, energy, aviation, and aerospace because of its exceptional mechanical properties, remarkable thermal stability and flame retardancy, as well as superior chemical and irradiation resistance [Citation42–44]. Recent years have witnessed the breakthrough in preparing high-strength and lightweight PI fibres. For example, PI fibres with high tensile strength of 3100.0 MPa and tensile modulus of 115.0 GPa, which are comparable to the level of CFs, have become commercially available [Citation45]. With such high mechanical performance, continuous and discontinuous long PI fibres have been demonstrated to be promising candidates as reinforcements of thermoplastic or thermoset polymer systems [Citation45,Citation46]. Nevertheless, the application of PI fibres as a reinforcement to the composite parts by powder-based printing has not been reported.
Herein, benefiting from the fibre reinforcement effect and the similar chemical structures between the PI fibres and the PA12 matrix, this work developed a new class of PI fibre–reinforced PA12 composites and demonstrated the largely enhanced mechanical performance of MJF-printed PI/PA12 composite parts. The effects of the MJF printing parameters, the PI fibre concentration, and the annealing treatment on the crystallisation behaviours, mechanical properties, and fracture morphology of the PA12 matrix were systematically investigated. The resulting process–structure–property relationship was thoroughly analyzed to determine the optimal mechanical performance of the printed parts.
2. Materials and methods
2.1. Materials
HP 3D High Reusability PA12 powder (HP Inc., U.S.A.) was used for the polymer matrix, which had an average size of 46.80 μm and possessed a peak melting temperature of 187.7°C (Figures S1a–c). The PI fibres used as the reinforcement were purchased from Jiangsu Shino New Materials Technology Co. Ltd., China, which was chopped to an average length of 0.61 mm (Figure S2). The PI fibres possessed a smooth surface and an average diameter of 14.00 μm. The density of the PI fibres was 1.41 g/cm3. The PI/PA12 mixed powders with fibre concentrations ranging from 0 wt% to 10 wt% were prepared using a mechanical mixer (Inversina 2L, Bioengineering AG, Switzerland) at a rotation speed of 60 rpm for 6 h.
2.2. Printing process
The HP MJF testbed (HP Inc., U.S.A.) was utilised to fabricate the composite parts. (a,b) show schematic diagrams of the MJF printing process and the testbed, respectively. In a typical MJF printing process, a dark-coloured fusing agent that absorbs IR radiation is dispensed from the printhead nozzles to form the pre-designed pattern on the preheated powder bed. Then, IR lamps move left and right across the powder bed to selectively fuse the region dispensed with the fusing agent. After the fusing step, the print bed descends a specific distance of one layer thickness, and the supply bed goes up a specific distance. The ratio of the upward height of the supply bed to the layer thickness is defined as the supply ratio. The roller rotates to drag the powder forward and thereby recoating a new layer of powder particles on the print bed. Repeatedly, the desired 3D part is built layer-by-layer.
Figure 1. Printing of PI/PA12 composites by MJF: (a) Schematic drawing of the MJF process. (b) Schematic drawing of the HP MJF testbed. (c) Optical image (left) and SEM image (right) of the short-chopped PI fibres. (d) Typical optical image (left) and temperature profiles recorded by the IR camera (right) during the printing process.
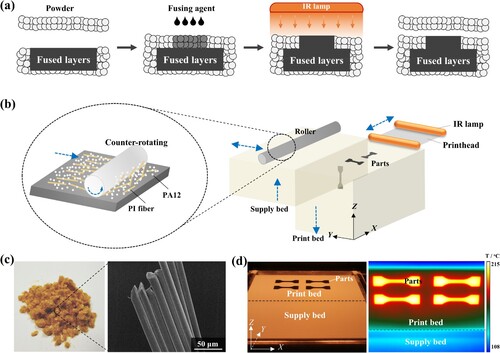
In the testbed, printing parameters such as the layer thickness, supply ratio, recoating speed, preheat temperature of the print bed, IR lamp movement speed, and irradiance were adjusted to realise the optimal fusing quality and precise dimensions of the printed parts. The optimised layer thickness, supply ratio, recoating speed, preheat temperature of the print bed, and moving speed of the IR lamp were set at 80 μm, 3.0, 250 mm/s, 150 °C, and 18 mm/s, respectively. As shown in the IR camera–captured temperature map ((d)), it is preferable to control the temperature of the selected powder particle region dispensed with the fusing agent at 210–220 °C. Consistent with prior studies, we defined the moving direction of the roller as the Y-axis and the moving direction of the IR lamp (i.e., perpendicular to the roller recoating direction) as the X-axis in this work to facilitate comparison with previously reported results ((b)). The printed parts were cooled naturally to room temperature followed by bead blasting.
2.3. Annealing of MJF-printed parts
During annealing, the MJF-printed neat PA12 parts and PI/PA12 composite parts were heated in air atmosphere at 173 °C for 5 h at a heat-up rate of 5 °C /min. All parts were buried in GB powder to ensure even heating. Based on the thermal properties of the parts and the results of previous studies, the annealing temperature was set to 173 °C and the duration was set to 5 h [Citation37]. The annealed parts were cooled naturally to room temperature followed by bead blasting.
2.4. Characterisation
The flowability of mixed powders was assessed by measuring the dynamic avalanche angles. Based on the method of rotating drum, the dynamic avalanche angle was measured by a Revolution Powder Analyzer (Mercury Scientific Inc., Switzerland). Each measurement was tested for 250 times. The drum rotation rate was set at 0.6 r/min.
The fibre direction distribution was determined by examining the optical microscope images of the polished composite parts. The evaluation process included (1) mounting the printed parts in epoxy resin, (2) polishing the surface paralleling the X-Y plane using a polishing machine (Tegramin-25, Struers, Denmark) to expose the fibres, (3) examining the morphology of the fibres with an optical microscope (SZX 16, Olympus Corp., Japan), and (4) processing the optical microscope images with ImageJ software to determine the fibre directions. Three images were analyzed for each case and over 1000 fibres were used in the calculation.
The morphology of the PI fibres and the fracture surfaces of the parts after tensile testing were observed by scanning electron microscopy (SEM) instrument (JSM-5600 LV, JEOL, Japan). The specimens were gold-plated to reduce the electric charge accumulation.
The tensile tests and three-point bending tests were conducted with a universal tester (AGX universal tester, Shimadzu Corp., Japan) to evaluate the tensile and flexural properties, respectively. The test rate was set at 10 mm/min [Citation35,Citation41,Citation47]. Moreover, the tensile tests followed the ASTM D638 Type V standard. To calculate the strain, the change in length of the sample was divided by its original length, which was marked with a white pen and tracked in real-time by a digital camera. The three-point bending tests were carried out on parts with the dimensions of 40 mm in length, 5 mm in width, and 2 mm in thickness, due to the limited build capacity of the testbed. Based on the buoyancy method, an analytical balance (XS204, Metter Toledo, U.S.A.) was used to measure the densities of the printed parts, and anhydrous ethanol (purity of 99.8%, Sigma-Aldrich) was used as an assisted testing liquid. Five parts were measured for each case.
A thermogravimetric analysis (TGA) machine (TGA-Q500, TA Instruments, UK) was utilised to evaluate the thermal stability of the powder particles and the printed parts, while a differential scanning calorimetry (DSC) instrument (DSC-Q200, TA Instruments, UK) was used to assess their crystallisation behaviours. Both TGA and DSC measurements were carried out under a nitrogen atmosphere. In detail, the TGA tests were performed from 25 °C to 800 °C and the heat-up speed was 10 °C /min. The DSC tests included a heating cycle and a cooling cycle between 25 and 250 °C at a heat-up/cool-down speed of 10 °C /min. Then, the crystallinity (Xm) was calculated by.
(1)
(1) where wPI is the actual weight fraction of PI fibres in a composite,
is the actual melting enthalpy for the tested specimen and
is the theoretical melting enthalpy for a 100% crystalline PA12 matrix (
= 209.3 J g−1) [Citation48].
3. Results and discussion
3.1. Properties of mixed powder
Owing to the MJF printing mechanism, the feedstock powder used for MJF must be light in colour because black powders particles absorb IR energy indiscriminately with or without the fusing agent, leading to undesirable caked or even fused powder outside the fusing agent deposition region. Although the PI fibres have a golden appearance ((c)), the PI/PA12 mixed powders are light yellow in colour even at high fibre fractions ((d) & Figure S3).
Apart from the appearance, the addition of fibres affects powder flowability, which is crucial in determining the smoothness of the recoated print bed in PBF techniques. Dynamic avalanche angle measurements were conducted to assess the flowability of the neat PA12 and its mixed powders. As shown in Figure S1d, and , the median avalanche angle increased with the addition of the PI fibres, compared to that of neat PA12 powder (48.2°). As the fibre concentration increased from 3 wt% to 10 wt%, the median avalanche angle of the mixed powders gradually increased from 53.5° to 61.6°, indicating a decreased powder flowability and thereby a deteriorated processability. This could be attributed to the differences in shape, size, surface morphology, and elastoviscosity between the PA12 particles and the PI fibres, which is consistent with previous studies [Citation36,Citation39]. Nevertheless, all the mixed powders used in this study were still able to form a high-quality powder bed suitable for printing. It was observed that when the fibre concentration exceeded 10 wt%, the powder recoating process failed.
Figure 2. Distribution of the avalanche angles of PI/PA12 mixed powders with various fibre fractions: (a) 3 wt%, (b) 6 wt%, (c) 8 wt%, and (d)10 wt%, respectively.
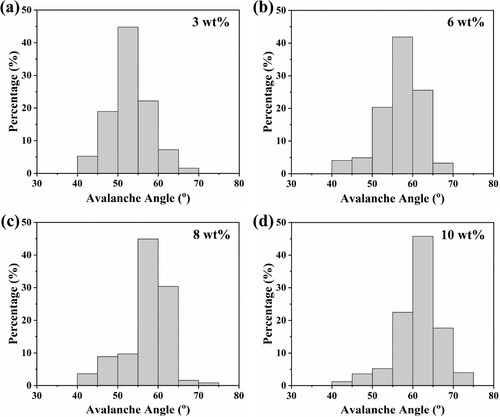
Table 1. Flowability and thermal properties of PI/PA12 mixed powders with various fibre fractions.
It is critical to investigate the crystallising and melting behaviours of the semicrystalline PA12 matrix to evaluate the fusing-ability of the PI/PA12 mixed powders and thereby optimising the printing parameters for the MJF process. DSC scans were performed to study the thermal properties of the powders. It could be seen from Figure S4 that all powders exhibited a single endothermic peak and a single exothermic crystallisation peak on their heating and cooling DSC curves, respectively. As summarised in , the addition of PI fibres showed negligible effect on the onset of melting temperature Tm, onset and the melting peak temperature Tm of the mixed powders. All of the powders possessed a moderate Tm in the range of 187.7–188.0 °C.
From the DSC cooling curves (Figure S4), the crystallisation peak temperature Tc and the onset of the crystallisation temperature Tc, onset of PA12 matrix increased with the addition of PI fibres. In detail, the Tc and Tc, onset of the mixed powders trended to increase with increasing the fibre fraction but began to decrease at the fibre content of 6 wt%. These results indicated that the addition of PI fibres could facilitate the crystallisation of PA12 matrix via a heterogeneous nucleating effect and thereby enhance the crystallinity of the matrix, which was also promising to improve the mechanical properties of the composite. However, the formation of dense fibre networks in the composites at high fibre concentrations might hinder the growth of PA12 crystals due to domain hindrance, thus resulting in a decrease in Tc. The powder bed temperature for a semicrystalline polymer should be maintained between Tc, onset and Tm, onset for as long as possible to suppress premature crystallisation of the fused layers and thus prevent warpage and curling of the printed parts. From , high ΔT (Tm, onset – Tc, onset, > 30 °C) indicated good fusing-ability of all mixed powders with the addition of PI fibres.
3.2. Properties of MJF-printed composite parts
3.2.1. Fibre alignment
Fibre alignment plays a crucial role in the mechanical properties of fibre/polymer composites. It has been reported that for PBF techniques including SLS and MJF, fibres could be aligned along the powder spreading direction, thereby leading to anisotropic mechanical behaviour and enhanced mechanical performance in the powder spreading direction [Citation28,Citation36,Citation38,Citation39,Citation49,Citation50,Citation51].
Based on our previous findings [Citation36], which demonstrated a predominant distribution of fibres in the X-Y plane (build plane) and a minimal presence of fibres oriented parallel to the X-Z plane, we specifically chose MJF-printed PI/PA12 composite parts with a polished X-Y plane for the analysis of fibre orientation. As shown by the optical microscope observation in (a–d), the fibres displayed a preferred direction along the powder recoating direction (Y orientation), agreeing with previously published works [Citation36,Citation38,Citation39]. The fibre orientation was quantitatively measured by the offset angle between the fibre and the powder spreading direction (Y orientation) in the polished X-Y planes. (e–h) show the distributions of fibre direction for PI/PA12 composite parts with different fibre concentrations. There was a slight increase in the fibre alignment in the dominant direction when the fibre concentration increased from 3 wt% to 10 wt%. Specifically, the percentages of the fibre orientation within 20° were 45.6%, 46.8%, 48.0%, and 49.8% for PI/PA12 composite parts with PI fibre concentrations of 3wt%, 6wt%, 8wt%, and 10 wt%, respectively. Such highly aligned fibres would lead to mechanical anisotropy of the composites and was expected to offer a largely enhanced mechanical strength measured along the Y orientation.
Figure 3. Optical microscope images and fibre orientation in the polished X-Y planes of composite parts with various fibre fractions: (a and e) 3 wt%, (b and f) 6 wt%, (c and g) 8 wt%, and (d and h) 10 wt%, respectively. Red dashed circles represent pores in the parts.
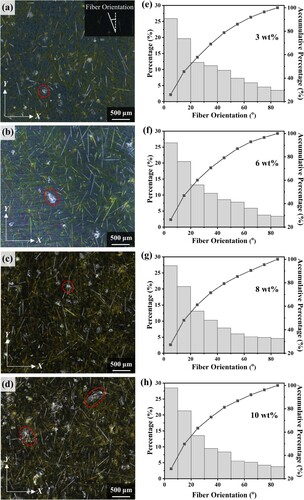
In addition, micro-sized irregular pores could be seen from the optical microscope images (red dashed circles in (a–d)). Similarly to other fibre-filled polymer systems, the pore content of the PI/PA12 composite parts increased with increasing fibre fraction, indicating an increase in porosity [Citation36,Citation39].
3.2.2. Thermal property
Thermogravimetric analysis and DSC were used to measure the actual fibre fractions and thermal stabilities, and crystallisation and melting behaviours of the printed PI/PA12 composite parts, respectively. (a,b) show the TGA and derivative thermogravimetric (DTG) curves of PI fibre and PI/PA12 composite parts with different fibre fraction, respectively. Their initial thermal decomposition temperatures Td at 1 wt% weight loss and the first exothermic peaks are summarised in Table S1. The Td and the first exothermic peaks both increased with the increase in the fibre content, demonstrating improved thermal stability of composite parts after the addition of PI fibres. Since the weight loss of PI fibres was negligible below 550 °C, the mass difference between the weight fractions of PI/PA12 composite parts and neat PA12 parts at 500 °C acquired by TGA reflects the actual fibre fraction of each composite part. These values are in good agreement with those of the PI/PA12 mixed powder.
Figure 4. The thermal properties of PI/PA12 composite parts with various fibre fractions: (a) TGA, (b) DTG, and (c) DSC curves.
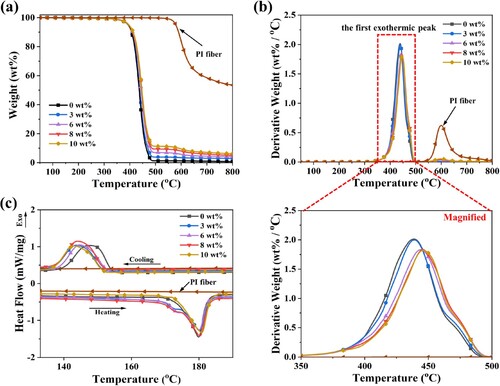
The reinforcement fillers also play a significant influence on the degree of crystallinity of the polymer matrix which subsequently affect the mechanical performance of the corresponding composite [Citation45]. (c) shows the DSC curves of the printed parts. The peak melting temperatures and the degree of crystallinity are listed in Table S1. It was revealed that the addition of PI fibres caused a slight increase in the peak melting temperatures of the composite parts. Moreover, the addition of PI fibres enhanced the degree of crystallinity Xm of the PI/PA12 composites in the appropriate range of the fibre content (lower than or equal to 8 wt%). On the contrary, excessive fibre concentration (higher than 8 wt%) limited the growth of crystals of the PA12 matrix, thus leading to a decrease in Xm, agreeing with other fibre-reinforced polymer composite systems [Citation45].
3.2.3. Mechanical property
The tensile and flexural tests were conducted on MJF-printed neat PA12 and PI/PA12 composite parts with varied fibre fractions and build directions to evaluate their mechanical performance. It is noteworthy that all samples were tested along their respective build directions. The tensile property comparison of all parts is summarised in Table S2 and . As expected, obvious anisotropy in the UTS of the PI/PA12 composite parts was observed, while the UTS of neat PA12 parts was almost isotropic ((a)). Compared with neat PA12 parts, PI/PA12 composite parts exhibited significantly enhanced UTS and tensile modulus when measured in the Y orientation and slightly decreased UTS and tensile modulus in the X orientation.
Figure 5. The tensile properties of the neat PA12 and PI/PA12 composite parts with various fibre fractions: tensile curves of (a) the neat PA12 parts and the composite parts measured in the (b) Y orientation and (c) X orientation, (d) the UTS, (e) tensile modulus, and (f) elongation at break of the parts tested along the X and Y orientations.
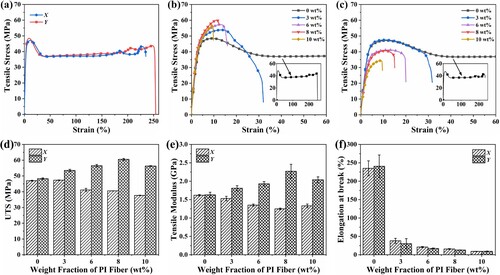
As observed in (b), the UTS of the PI/PA12 composite parts tested in the Y orientation exhibited a strong dependency on the fibre fraction and was significantly enhanced with increasing concentration of the PI fibres. The highest UTS of 60.54 MPa was obtained in the composite part with 8 wt% PI fibres, representing a 25.3% increase compared to that of neat PA12 parts. This result indicated a remarkable reinforcement effect on the PA12 matrix by incorporating short-chopped PI fibres. Such reinforcement could be attributed to the superior efficiency of stress transfer resulting from the high degree of fibre alignment as demonstrated in . Further increasing the fibre fraction led to a decreased UTS at a fibre content over 10 wt% of PI fibres. This might be owing to an increase in the pore content caused by the reduced powder flowability in the powder bed and a decreased crystallinity as confirmed by DSC ((c)). The tensile moduli of the composites presented a similar trend with the variation in the fibre concentration. With the addition of 8 wt% PI fibres, the PI/PA12 composite part exhibited the highest tensile modulus of 2.27 GPa, showing a 39.3% increase compared to that of the PA12 parts.
In contrast, a slight increase in the UTS and tensile moduli of the PI/PA12 composites tested in the X direction was observed at first and then a decrease at fibre content over 3 wt% ((c)). These results could be attributed to the competitive effects between stress transfer and diminished continuity of the matrix caused by the addition of fibre. As the fibre content increases, more fibres became perpendicular to the tensile direction, which could reduce the efficiency of stress transfer and increase the discontinuity of the matrix, resulting in lower tensile strength and modulus.
Consistently with most of the fibre-reinforced polymer composites, the elongation at break decreased dramatically due to the incorporation of the PI fibres ((f)), indicating a transformation of failure mode from a ductile thermoplastic polymer to brittle composites [Citation37]. Specifically, the elongation at break for all composite parts was below 30%. The reduced elongation at break is largely owing to the high stress concentration at the fibre ends, which causes matrix cracking and eventually local failure of the polymer matrix when the composite parts can no longer withstand the increasing load [Citation45,Citation52]. As a result, the higher the fibre fractions, the more stress concentration sites can be induced, and the lower the elongation at break is.
The mechanisms for the reinforcement effectiveness of the PI/PA12 composites are revealed by the fracture morphology. illustrates the SEM fractographs of the neat PA12 and PI/PA12 composites after tensile testing. For the neat PA12 parts (both Y and X orientations), rough fibrous fracture surfaces could be clearly observed ((a,b)), indicating a typical ductile tearing which led to a high elongation at break of above 200%. Similarly to the optical images of the polished parts (), the SEM images in (c–j) also indicated that the PI fibres were well dispersed in the PA12 matrix and highly aligned along the powder recoating orientation, since most of the fibres were perpendicular to the X-Z plane in parts tested along the Y orientation and parallel to the Y orientation in the parts tested along the X orientation.
Figure 6. SEM images of the tensile fracture surfaces of the MJF-printed PI/PA12 composite parts in the Y/X orientations with various fibre concentrations: (a and b) 0 wt%, (c and d) 3 wt%, (e and f) 6 wt%, (g and h) 8 wt%, and (i and j) 10 wt%. Orange dashed circles represent the hole left after the fibre pullout.
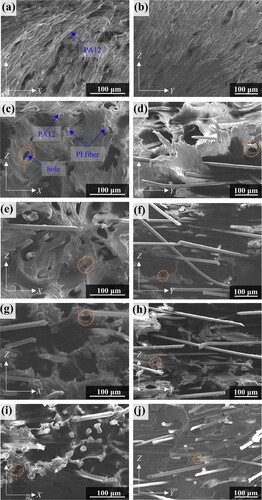
Meanwhile, the fracture surface morphology could confirm the ductile-brittle transition induced by the incorporation of fibres. With the increase in the fibre fractions, the fracture surfaces became smoother and denser. Moreover, no apparent fibrous matrix was observed in the composite parts tested in both X and Y orientations at a fibre content over 6 wt%, indicating that no large matrix deformation occurred during the tensile failure. Although some of the PA12 matrix was found to stick with the fibres, most of the PI fibre surfaces were rather smooth, suggesting fairly weak interfacial adhesion between the fibre and the polymer matrix. For composite parts tested in the Y orientation, a number of PI fibres were pulled out of the PA12 matrix, with holes left on the fracture surfaces. Therefore, these results suggested that for the short-chopped PI fibre/PA12 composites, the dominant reinforcement mechanism can be attributed to the aligned fibres absorbing energy through fibre pullout, fracture and debonding [Citation30,Citation39,Citation49,Citation50,Citation51].
From (d,f,h,j), a few holes in the fracture surfaces could also be seen in the composites tested in the X orientation. Such small amount of fibre pullouts along the tensile direction could further explain the slightly increased tensile strength and modulus of the PI/PA12 composite parts with 3 wt% fibres tested in the X orientation. However, for composite parts with higher fibre fractions, large quantities of fibres were found to be perpendicular to the tensile direction, which not only could be easily de-bonded from the matrix but also resulted in a severe discontinuity in the polymer matrix. Therefore, the tensile strength and modulus of the composite parts decreased with increasing fibre fractions, which was confirmed by the data in (b).
The flexural property comparison of all the parts is summarised in Table S3 and . These results followed the same trend as observed in the tensile strength and modulus with the variation of the fibre fraction. The flexural strength and flexural modulus could be largely improved by incorporating the PI fibres into the PA12 matrix. With the increase in the fibre fractions, the flexural strength/modulus tested along either the X or the Y orientation first increased and then decreased. Specifically, the enhanced flexural strength and modulus can be obtained in parts tested both along the X and Y orientations at fibre fractions below 8 wt%. Moreover, the anisotropy in the flexural properties increased with the increase in the fibre fractions. When loaded with 8 wt% PI fibres, the composite part tested along the Y orientation exhibited the highest flexural strength of 83.25 MPa and the highest flexural modulus of 1.60 GPa, which were improved by 20% and 12% in comparison to those of the pure PA12 parts.
Figure 7. The flexural properties of the neat PA12 and PI/PA12 composites with various fibre fractions: flexural curves of the printed parts tested in the (a) Y orientation and (b) X orientation, (c) the flexural strength and (d) flexural modulus of the printed parts tested in the X and Y orientations.
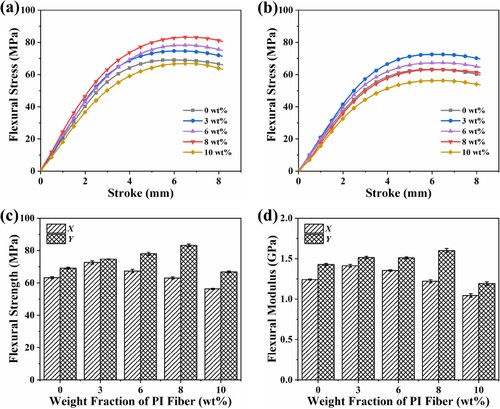
Benefiting from the fibre reinforcement effect and the highly aligned fibres, the maximum tensile and flexural performance can be simultaneously obtained in one optimised composite part with 8 wt% PI fibres, which is barely demonstrated in other fibre-reinforced PA12 composite systems for MJF. In addition, an isotropic reinforcement effect in mechanical properties can be achieved in the composite part with 3 wt% PI fibres while maintaining a relatively good ductility with the elongation at break of around 30%. Therefore, different PI fibre loading fractions can be adopted to meet specific application requirements.
Annealing has been demonstrated to not only facilitate the elimination of residual stresses inside the printed parts but also promote the crystallinity, thus leading to an improvement in the mechanical properties [Citation37,Citation39]. Our previous work also revealed that below the temperature-induced dimensional deformation, the higher the annealing temperature, the more adequate the motion of the polymer segments for crystallisation [Citation37]. In this work, annealing at 173 °C for 5 h was conducted in neat PA12 parts and composite parts with 8 wt% PI fibres to further strengthen their mechanical properties. The mechanical performances of the MJF-printed parts before and after annealing treatment are shown in (a,b) & Table S4.
Figure 8. Effects of the annealing treatment on the mechanical and thermal properties: (a) Tensile, (b) flexural, and (c) DSC curves of the PA12 and PI/PA12 (8 wt%) composite parts before and after annealing. ‘X(Y)-(PI/)PA12’ refers to a part that was tested in the X(Y) orientation.
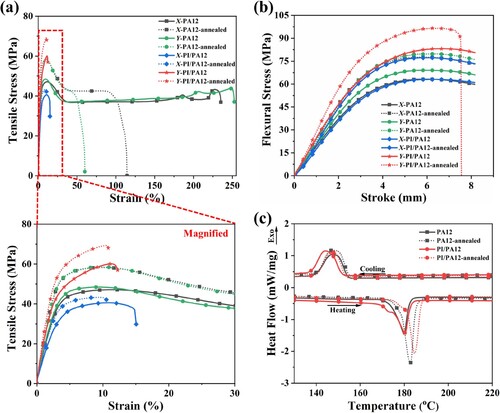
As expected, the tensile strength and flexural strength of all parts increased after annealing. Specifically, the tensile modulus, UTS, flexural modulus, and flexural strength of the 8 wt%-PI/PA12 composite parts tested in the Y orientation remarkably increased to 2.32 GPa, 69.29 MPa, 2.08 GPa, and 96.00 MPa, respectively. In comparison to the neat PA12 parts, the composite parts were found to achieve an increase of about 44%, 42%, 39%, and 46% in the UTS, tensile modulus, flexural strength, flexural modulus, respectively, at the fibre content of 8 wt%. Such results revealed a significant reinforcement effect in Y orientation on the PA12 matrix by the addition of short-chopped PI fibres and the annealing treatment. However, the annealing process also led to a sharply decreased elongation at break of both the neat PA12 and PI/PA12 composite parts, indicating a brittle failure mode. In the case of flexural testing, the PI/PA12 composite parts tested along the X orientation did not rupture at the maximum deflection, while at 7.5 mm stroke those tested in the Y orientation ruptured. This suggested the parts after annealing became much more brittle when tested in the Y orientation. In contrast, the neat PA12 parts did not break down during flexural testing.
The enhanced mechanical strength of the annealed parts could be attributed to the increased crystallinity, which was confirmed by DSC. Results in (c) and Table S5 revealed that the crystallinity of the PI/PA12 composite part increased from 26.3% to 33.6%, while that of the neat PA12 part increased from 24.4% to 31.0%. Similarly to the phenomenon observed in other fibre-reinforced polymer composite systems, it could be observed from the DSC curves that the annealing treatment could improve the Tm of the MJF-printed neat PA12 (Tm increased from 178.0 °C to 182.6 °C) and PI/PA12 composite (Tm shifted from 180.3 °C to 184.7 °C) parts. The elongation at break was determined by two competing phenomena arising from the annealing treatment: (1) elimination of residual stresses, which caused the elongation at break to increase [Citation39,Citation45]; (2) higher crystallinity, which caused the elongation at break to decrease [Citation37]. From the results of the reduced elongation at break in both the tensile and flexural tests, one may conclude that the increase in crystallinity outweighed the decreased residual stress in this case. As confirmed by the fractographs of the annealed parts after tensile and flexural testing (Figure S5), the annealing treatment in our case could cause a ductile–brittle transition of both the PA12 and PI/PA12 composites. The fracture surfaces of the tested parts were relatively flat, implying that negligible matrix deformation occurred during the tensile and flexural failure.
3.3. Comparison of the mechanical performance
Because of the high strength of the PI fibres and fibre alignment, the MJF-printed PI/PA12 composites in this work demonstrated remarkably enhanced mechanical properties in comparison to the neat PA12 parts. To verify the reinforcement effectiveness of the PI fibres, we compared the mechanical performance of the PI/PA12 composite and all reported MJF-printed composites. As shown in , the tensile strength and flexural strength of the composites with 8 wt% PI fibres in this work are among the best-performing fibre-reinforced PA12 composites printed by MJF. More importantly, the addition of the lightweight PI fibres resulted in minimal changes in the part density (Table S6), thus leading to high specific tensile strength of 67.60 kN·m/kg and specific flexural strength of 93.70 kN·m/kg, which are superior to MJF-printed PA12 composites reinforced with other fibres. Such materials hold great potential in applications that demand high strength, lightweight design, and anisotropic properties. Specifically, in aerospace and automotive industries, these materials offer significant advantages by reducing aircraft weight or enhancing vehicle safety, fuel efficiency, and performance.
Table 2. Comparison of the mechanical performance of the MJF-printed PA12 composites tested along the powder recoating direction.
4. Conclusions
In conclusion, a new PI/PA12 powder applicable to MJF was developed and the reinforcement effectiveness of the PI fibres on the mechanical performance of the PA12 matrix was demonstrated. The effects of the MJF printing conditions, the PI fibre content, and the annealing treatment on the crystallisation behaviours, mechanical properties, and fracture morphology of the PA12 matrix were systematically studied. The results revealed that the MJF-printed PI/PA12 composite parts with a fibre concentration of 8 wt% tested along the powder recoating direction simultaneously exhibited optimal tensile and flexural properties. Specifically, the UTS of 69.00 MPa, the tensile modulus of 2.32 GPa, the flexural strength of 96.00 MPa, and the flexural modulus of 2.09 GPa, could be achieved after annealing. Furthermore, the addition of the lightweight PI fibres endowed the PI/PA12 composites with high specific tensile strength of 67.60 kN·m/kg and specific flexural strength of 93.70 kN·m/kg, which are superior to MJF-printed PA12 composites reinforced with other fibres. This work provides new insights into enhancing the mechanical properties of lightweight parts printed by MJF and other powder-based techniques.
Supplemental Material
Download MS Word (21.2 MB)Acknowledgements
This study was supported by the RIE2020 Industry Alignment Fund – Industry Collaboration Projects (IAF-ICP) Funding Initiative, Singapore and the cash and in-kind contributions from the industry partner, HP Inc.
Disclosure statement
No potential conflict of interest was reported by the author(s).
Additional information
Funding
References
- Ligon SC, Liska R, Stampfl J, et al. Polymers for 3D printing and customized additive manufacturing. Chem Rev. 2017;117(15):10212–10290. DOI:10.1021/acs.chemrev.7b00074
- Falahati M, Ahmadvand P, Safaee S, et al. Smart polymers and nanocomposites for 3D and 4D printing. Mater Today. 2020;40:215–245. DOI:10.1016/j.mattod.2020.06.001
- Han C, Fang Q, Shi Y, et al. Recent advances on high-entropy alloys for 3D printing. Adv Mater. 2020;32(26):1903855. DOI:10.1002/adma.201903855
- Chen M, Gao M, Bai L, et al. Recent advances in 4D printing of liquid crystal elastomers. Adv Mater. 2023: 2209566. DOI:10.1002/adma.202209566
- Saadi MASR, Maguire A, Pottackal NT, et al. Direct ink writing: a 3D printing technology for diverse materials. Adv Mater. 2022;34(28):2108855. DOI:10.1002/adma.202108855
- Peng X, Kuang X, Roach DJ, et al. Integrating digital light processing with direct ink writing for hybrid 3D printing of functional structures and devices. Addit Manuf. 2021;40:101911. DOI:10.1016/j.addma.2021.101911
- Gu D, Shi X, Poprawe R, et al. Material-structure-performance integrated laser-metal additive manufacturing. Science. 2021;372(6545):eabg1487. DOI:10.1126/science.abg1487
- Chatham CA, Long TE, Williams CB. A review of the process physics and material screening methods for polymer powder bed fusion additive manufacturing. Prog Polym Sci. 2019;93:68–95. DOI:10.1016/j.progpolymsci.2019.03.003
- Tan LJ, Zhu W, Zhou K. Recent progress on polymer materials for additive manufacturing. Adv Funct Mater. 2020;30(43):2003062. DOI:10.1002/adfm.202003062
- Yang W, Bai X, Zhu W, et al. 3D printing of polymeric multi-layer micro-perforated panels for tunable wideband sound absorption. Polymers. 2020;12(2):360. DOI:10.3390/polym12020360
- Tey WS, Cai C, Zhou K. A comprehensive investigation on 3D printing of polyamide 11 and thermoplastic polyurethane via multi jet fusion. Polymers. 2021;13(13):2139. DOI:10.3390/polym13132139
- Xu Z, Wang Y, Wu D, et al. The process and performance comparison of polyamide 12 manufactured by multi jet fusion and selective laser sintering. J Manuf Process. 2019;47:419–426. DOI:10.1016/j.jmapro.2019.07.014
- Cai C, Tey WS, Chen J, et al. Comparative study on 3D printing of polyamide 12 by selective laser sintering and multi jet fusion. J Mater Process Technol. 2021;288:116882. DOI:10.1016/j.jmatprotec.2020.116882
- Majewski CE, Oduye D, Thomas HR, et al. Effect of infra-red power level on the sintering behaviour in the high speed sintering process. Rapid Prototyp J. 2008;14(3):155. DOI:10.1108/13552540810878012
- Sillani F, Kleijnen RG, Vetterli M, et al. Selective laser sintering and multi jet fusion: Process-induced modification of the raw materials and analyses of parts performance. Addit Manuf. 2019;27:32–41. DOI:10.1016/j.addma.2019.02.004
- Goh GD, Yap YL, Agarwala S, et al. Recent progress in additive manufacturing of fiber reinforced polymer composite. Adv Mater Technol. 2019;4(1):1800271. DOI:10.1002/admt.201800271
- Osswald PV, Obst P, Capote GAM, et al. Failure criterion for PA 12 multi-jet fusion additive manufactured parts. Addit Manuf. 2021;37:101668. DOI:10.1016/j.addma.2020.101668
- Rosso S, Meneghello R, Biasetto L, et al. In-depth comparison of polyamide 12 parts manufactured by multi jet fusion and selective laser sintering. Addit Manuf. 2020;36:101713. DOI:10.1016/j.addma.2020.101713
- Farahani RD, Dubé M, Therriault D. Three-dimensional printing of multifunctional nanocomposites: manufacturing techniques and applications. Adv Mater. 2016;28(28):5794–5821. DOI:10.1002/adma.201506215
- Armstrong CD, Todd N, Alsharhan AT, et al. A 3D printed morphing nozzle to control fiber orientation during composite additive manufacturing. Adv Mater Technol. 2021;6(1):2000829. DOI:10.1002/admt.202000829
- Leigh SJ, Purssell CP, Bowen J, et al. A miniature flow sensor fabricated by micro-stereolithography employing a magnetite/acrylic nanocomposite resin. Sens Actuat A. 2011;168(1):66–71. DOI:10.1016/j.sna.2011.03.058
- Yuan S, Bai J, Chua CK, et al. Highly enhanced thermal conductivity of thermoplastic nanocomposites with a low mass fraction of MWCNTs by a facilitated latex approach. Compos Part A Appl Sci Manuf. 2016;90:699–710. DOI:10.1016/j.compositesa.2016.09.002
- Parandoush P, Lin D. A review on additive manufacturing of polymer-fiber composites. Compos Struct. 2017;182:36–53. DOI:10.1016/j.compstruct.2017.08.088
- Guo B, Xu Z, Luo X, et al. A detailed evaluation of surface, thermal, and flammable properties of polyamide 12/glass beads composites fabricated by multi jet fusion. Virtual Phys Prototyp. 2021;16(Suppl. 1):S39–S52. DOI:10.1080/17452759.2021.1899463
- O’Connor HJ, Dowling DP. Comparison between the properties of polyamide 12 and glass bead filled polyamide 12 using the multi jet fusion printing process. Addit Manuf. 2020;31:100961. DOI:10.1016/j.addma.2019.100961
- Kleijnen RG, Sesseg JPW, Schmid M, et al. (2017). Insights into the development of a short-fiber reinforced polypropylene for laser sintering. Paper presented at the AIP Conference Proceedings.
- Arai S, Tsunoda S, Yamaguchi A, et al. Effects of short-glass-fiber content on material and part properties of poly (butylene terephthalate) processed by selective laser sintering. Addit Manuf. 2018;21:683–693. DOI:10.1016/j.addma.2018.04.019
- Jansson A, Pejryd L. Characterisation of carbon fibre-reinforced polyamide manufactured by selective laser sintering. Addit Manuf. 2016;9:7–13. DOI:10.1016/j.addma.2015.12.003
- Zhu W, Yan C, Shi Y, et al. A novel method based on selective laser sintering for preparing high-performance carbon fibres/polyamide12/epoxy ternary composites. Sci Rep. 2016;6(1):1–10. DOI:10.1038/s41598-016-0001-8
- Yang Z, Yang Z, Chen H, et al. 3D printing of short fiber reinforced composites via material extrusion: Fiber breakage. Addit Manuf. 2022;58:103067. DOI:10.1016/j.addma.2022.103067
- Hong R, Zhao Z, Leng J, et al. Two-step approach based on selective laser sintering for high performance carbon black/polyamide 12 composite with 3D segregated conductive network. Compos Part B Eng. 2019;176:107214. DOI:10.1016/j.compositesb.2019.107214
- Mu Q, Wang L, Dunn CK, et al. Digital light processing 3D printing of conductive complex structures. Addit Manuf. 2017;18:74–83. DOI:10.1016/j.addma.2017.08.011
- Yang L, Wang L, Chen Y. Solid-state shear milling method to prepare PA12/boron nitride thermal conductive composite powders and their selective laser sintering 3D-printing. J Appl Polym Sci. 2020;137(23):48766. DOI:10.1002/app.48766
- O’Connor HJ, Dickson AN, Dowling DP. Evaluation of the mechanical performance of polymer parts fabricated using a production scale multi jet fusion printing process. Addit Manuf. 2018;22:381–387. DOI:10.1016/j.addma.2018.05.035
- HP Development Company, L.P. (2017). HP 3D high reusability PA12 glass beads. https://cimquest-inc.com/resource-center/HP/Materials/HP-PA12GB-Datasheet.pdf.
- Liu X, Tey WS, Tan P, et al. Effect of the fibre length on the mechanical anisotropy of glass fibre–reinforced polymer composites printed by Multi Jet Fusion. Virtual Phys Prototyp. 2022;17(3):734–748. DOI:10.1080/17452759.2022.2059638
- Liu X, Tey WS, Choo JYC, et al. Enhancing the mechanical strength of Multi Jet Fusion–printed polyamide 12 and its glass fiber-reinforced composite via high-temperature annealing. Addit Manuf. 2021;46:102205. DOI:10.1016/j.addma.2021.102205
- Tan P, Shen F, Tey WS, et al. A numerical study on the packing quality of fibre/polymer composite powder for powder bed fusion additive manufacturing. Virtual Phys Prototyp. 2021;16(Suppl. 1):S1–S18. DOI:10.1080/17452759.2021.1922965
- Chen J, Tan P, Liu X, et al. High-strength light-weight aramid fibre/polyamide 12 composites printed by Multi Jet Fusion. Virtual Phys Prototyp. 2022;17(2):295–307. DOI:10.1080/17452759.2022.2036931
- Chen J, Zhao L, Zhou K. Improvement in the mechanical performance of Multi Jet Fusion–printed aramid fiber/polyamide 12 composites by fiber surface modification. Addit Manuf. 2022;51:102576. DOI:10.1016/j.addma.2021.102576
- Hou Y, Gao M, Chen J, et al. Preparation of iron oxide–coated aramid fibres for improving the mechanical performance and flame retardancy of multi jet fusion–printed polyamide 12 composites. Virtual Phys Prototyp. 2023;18(1):e2171892. DOI:10.1080/17452759.2023.2171892
- Niu H, Qi S, Han E, et al. Fabrication of high-performance copolyimide fibers from 3, 3’, 4, 4'-biphenyltetracarboxylic dianhydride, p-phenylenediamine and 2-(4-aminophenyl)−6-amino-4 (3H)-quinazolinone. Mater Lett. 2012;89:63–65. DOI:10.1016/j.matlet.2012.08.088
- Zhang M, Niu H, Chang J, et al. High-performance fibers based on copolyimides containing benzimidazole and ether moieties: Molecular packing, morphology, hydrogen-bonding interactions and properties. Polym Eng Sci. 2015;55(11):2615–2625. DOI:10.1002/pen.24154
- Yi X, Kuang X, Zhang M, et al. Surface modification of polyimide fibers by novel alkaline–solvent hydrolysis to form high-performance fiber-reinforced composites. J Appl Polym Sci. 2018;135(33):46595. DOI:10.1002/app.46595
- Jiang C, Han E, Wang X, et al. Effect of discontinuous long polyimide fiber on mechanical properties, fracture morphology, and crystallization behaviors of polyamide-6 matrix composites. J Thermoplast Compos Mater. 2018;31(2):223–245. DOI:10.1177/0892705717697776
- Ding Y, Hou H, Zhao Y, et al. Electrospun polyimide nanofibers and their applications. Prog Polym Sci. 2016;61:67–103. DOI:10.1016/j.progpolymsci.2016.06.006
- HP Development Company, L.P. (2019). HP 3D high reusability PA12. https://cimquest-inc.com/resource-center/HP/Materials/HP-PA12-Datasheet.pdf.
- Gogolewski S, Czerntawska K, Gastorek M. Effect of annealing on thermal properties and crystalline structure of polyamides. Nylon 12 (polylaurolactam). Colloid Polym Sci. 1980;258:1130–1136. DOI:10.1007/BF01382456
- Tang H, Chen H, Sun Q, et al. Experimental and computational analysis of structure-property relationship in carbon fiber reinforced polymer composites fabricated by selective laser sintering. Compos Part B Eng. 2021;204:108499. DOI:10.1016/j.compositesb.2020.108499
- Chen H, Zhu W, Tang H, et al. Oriented structure of short fiber reinforced polymer composites processed by selective laser sintering: the role of powder-spreading process. Int J Mach Tools Manuf. 2021;163:103703. DOI:10.1016/j.ijmachtools.2021.103703
- Chen H, Cheng T, Wei Q, et al. Dynamics of short fiber/polymer composite particles in paving process of additive manufacturing. Addit Manuf. 2021;47:102246. DOI:10.1016/j.addma.2021.102246
- Curtis PT, Bader MG, Bailey JE. The stiffness and strength of a polyamide thermoplastic reinforced with glass and carbon fibres. J Mater Sci. 1978;13:377–390. DOI:10.1007/BF00647783