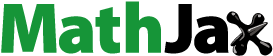
ABSTRACT
Despite the limitations imposed by their composition, natural materials overcome the trade-off between strength and ductility through their unique structural features. Inspired by the crossed-lamellar structure of conch shells, SS316L-IN625 heterostructured materials were designed and fabricated by laser directed energy deposition (LDED). Interestingly, this bionic heterostructured material (BHM) breaks the strength-ductility trade-off of the constitutive material with a tensile strength of 731.74 MPa and a uniform elongation of 34.98%. This particular with multi-scale and periodic distributions and interfaces with crossed-lamellar deliver the BHM superior performance combinations beyond the rules of mixtures. The strain gradient induced by heterogeneous deformation activates additional slip systems, and this unique slip band delays premature necking in the SS316L region and hinders crack propagation. The BHM takes full advantage of the intrinsic strength of IN625 and the toughness of SS316L to stimulate multiple enhancement and toughening mechanisms.
1. Introduction
Strength and ductility are two of the most important mechanical properties of metallic materials for structural applications in a wide variety of industries, including aerospace and nuclear plants [Citation1]. However, the strength-ductility trade-off has been a long-standing dilemma in most metallic materials. This antagonistic combination of properties seriously restricts the workability and damage tolerance of the engineered materials [Citation2]. To date, it is still extremely challenging to circumvent this exclusive relationship through traditional methods [Citation3]. Interestingly, nature-inspired heterostructured materials (HM) can achieve a combination of high strength and excellent ductility through well-crafted architectural arrangements. In this context, researchers have proposed a variety of bionic heterostructured materials (BHM) to overcome the performance trade-off challenges, such as gradient structure, lamellar structure, and bimodal structure [Citation4,Citation5]. Nevertheless, integrated manufacturing for BHM remains a great challenge for traditional fabrication methods and their mechanisms, in essence, for superior performance are also rarely revealed.
Currently, many methods have been developed to fabricate metallic materials with heterogeneous structures, but their material distribution, volume fraction controllability, and complex geometries are usually limited [Citation6,Citation7]. Recent advances in laser additive manufacturing (LAM) technology provide a constructive method for fabricating high-performance heterogeneous metallic materials, which mainly include selective laser melting (SLM) and laser directed energy deposition (LDED) [Citation8]. Compared to SLM, LDED offers tailored solutions for easily manufacturing complex functional gradients, multi-material layers, and even composite materials. Based on this concept, the combination of stainless steel 316L (SS316L) and alloy 625 (IN625) using LDED into heterogeneous metallic materials with improved properties is beneficial for the nuclear reactor, gas turbine, and automotive industries [Citation9,Citation10]. Daniel et al. investigated the mechanical properties of lamellar materials fabricated by alternately depositing SS316L and IN718 [Citation11]. Adjusting the number of interfaces in BHM is considered to be a reliable method to improve mechanical properties. The heterogeneous interface increases the yield strength of BHM and provides a strong deterrent to dislocation slides [Citation12]. The effect of printing order on the microstructural characteristics and cracks of SS316L/IN625 bimetals was investigated by Chen et al [Citation13]. They observed two types of interfaces with unique morphology and considered that the printing sequence could control the formation of interfaces with crack-free structures. Despite significant research progress, most studies on lamellar structured materials have focused on the linear direction, failing to fully exploit the performance advantages of natural materials and the unique flexibility of AM [Citation14]. At the same time, the potential deformation mechanisms of heterogeneous materials with complex layered structures have not been fully understood.
Inconel 625 (IN625) and 316L stainless steel (SS316L) are widely employed as structural materials in modern industrial applications, such as nuclear reactors, aerospace, and the energy sector [Citation15]. IN625, a nickel-based high-temperature alloy, is particularly well-suited for extreme service environments characterised by high-temperature and severe oxidation. SS316L exhibits remarkable corrosion resistance while retaining essential mechanical properties at moderately high temperatures. Both IN625 and SS316L have the similar face-centered cubic (FCC) crystal structure and display only minor differences in their coefficients of thermal expansion. This compatibility allows for a direct connection without the risk of delamination [Citation16]. Within this context, steel-nickel heterostructured materials emerge as promising alloys for structural materials in nuclear energy applications.
In this study, we explore new ways to break through the strength-ductility trade-off in SS316L-IN625 heterogeneous materials through bionic crossed-lamellar structures. By adjusting the volume distribution of different materials and changing the distribution of heterogeneous materials, crossed-lamellar structures with different aspect ratios were constructed. The microstructural evolution of BHM and its formation mechanism were investigated to figure out how the heterogeneity of the material affects the mechanical properties. The stress–strain response as well as the deformation incompatibility of BHM was characterised by uniaxial stretching, cyclic stretching and digital image correlation techniques. In addition, heterogeneous material deformation mechanisms and interfacial strengthening mechanisms are discussed. This study shows that this bionic heterostructure design strategy can provide a new route for next-generation structural materials.
2. Experimental materials and procedure
2.1. Bionic heterostructure design
Advanced structural materials inspired by nacre have attracted considerable attention in the last few decades, but artificial HM configurations are usually in linear format [Citation17]. The conch shell is an order of magnitude tougher than nacre and is considered to be one of the toughest body armours in nature [Citation18,Citation19]. The HMs with crossed-lamellar structures, inspired by the conch shell, were proposed in . The conch shell has a unique crossed-lamellar structure, exhibiting a more complex lamellar structure with distinct anisotropic features than nacre, as shown in (a). This crossed-lamellar structure cleverly limits crack propagation, showing high potential to circumvent the strength-ductility trade-off. In this study, the volume fractions of the two constitutive materials were adjusted by using different material distribution modes in the LDED process to realise the BHM in the form of periodic soft–hard-soft layering with multiple length scales.
2.2. Materials and LDED process
The SEM micrographs and particle size distribution of SS316L and IN625 powder (supplied by Minatech Co, Ltd. (Shenzhen, China)) are shown in (b). lists the chemical compositions (wt%) of SS316L and IN625 powders. SS316L powder and IN625 powder in the particle size range of 75–150 μm were deposited on SS316L base material through LDED. The BHM is fabricated on the LATEC LAM-150 V powder-feeding metal printer. The system is equipped with a 1 kW power fibre laser with a wavelength of 1060 nm, a computer numerical control (CNC) table, a four-channel brass nozzle deposition head, and a multi-material powder feeder. (c) illustrates the LDED process diagram by the design pattern, with both powders fed alternately from the feeder to the nozzle. In the deposition of BHMs, the inert argon gas was used as a powder feed carrier gas and a protective atmosphere. The O2 level in the working chamber is kept below 100 ppm to prevent oxidation of the material. Different material distribution spacings were used in the LDED process to adjust the volume fractions of the two constituent materials. The processed samples are referred to as BHM1, BHM2, and BHM3, respectively, as shown in (d). The deposition process of the bionic heterostructured material (BHM1) can be described as follows: Initially, SS316L powder was deposited onto a 316L stainless steel substrate, creating a gap between the SS316L tracks. Subsequently, IN625 powder was deposited along the central line of these intervals to form a complete layer. For the second layer deposition, the laser scanning direction was rotated by 90° and the first and second steps were repeated alternately. While the BHM3 consisted of alternate three tracks of SS316L and one track of IN625. According to the heterogeneous bionic design, the volume fractions of SS316L and IN625 in BHM1, BHM2, and BHM3 were 1:1, 2:1, and 3:1, respectively. Alternating deposition of SS316L and IN625 powders follows the process described above to form a bulk material with a configurable architecture. After replacing the deposited powder, the carrier gas will remain on for 30 s to ensure that there is no powder remaining in the powder tube. The process parameters during printing are shown in .
Table 1. The main chemical compositions of SS316L and IN625.
Table 2. Process parameters selected for the manufacture of BHM samples.
2.3. Microstructural characterisation and mechanical properties testing
The printed samples were sliced along the laser scanning direction (X-Z plane), step-over direction (Y-Z plane), and building direction (X-Y plane), respectively. After ground, polished and etched to investigate the microstructural morphology and interfacial metallurgical properties using optical microscopy (OM) and scanning electron microscopy (SEM) equipped with energy dispersive spectroscopy (EDS). The samples were prepared for Electron Back-Scattered Diffraction (EBSD) analysis using vibratory polishing. HKL Channel 5 software to reveal the crystallographic characteristics of the BHM. To study the variation of hardness between BHM layers, the microhardness distribution in the cross section was measured using an HV-1000 hardness tester with a load of 200 g and a holding time of 10s. Tensile tests with a displacement rate of 0.5 mm/min were performed using the universal testing machine at room temperature. The local strain and failure behaviour of BHM during tensile deformation was monitored using digital image correlation (DIC) techniques.
3. Results and discussions
3.1. Microstructural characterisation
3.1.1. Micro-morphological characteristics
The spatial characteristics of BHM samples in different view planes and the microstructure at the interface are shown in . Given that both materials are austenitic matrices and have superior laser printing properties, there is essentially no porosity between SS316L and IN625 and they have great compatibility. Due to the better corrosion resistance of IN625 to aqua regia, the whiter regions are IN625 and the darker regions are SS316L. (a) reveals a bionic crossed-lamellar structure composed of two materials. The periodic distribution of the two materials is displayed in the front and side views, while the top view shows the array of deposition tracks for the two materials. BHM with different material deposition distributions shows different ordered crossed-lamellar structures in the longitudinal and transverse sections, which are related to the scanning strategy. (b) illustrates the morphology of the heterogeneous material interface on the upper surface of the BHM sample. Significant bending features can be observed at the solidification edges in the material orbit, which are related to the melt pool temperature and the surface tension coefficient. Notably, white trapped SS316L material was found on the edge of the IN625 track, which is thought to be an intermixing of the two materials caused by strong Marangoni convection. (c) shows a magnified image of the orbital boundary with the presence of interlocking microstructural features between IN625 and SS316L. Both IN625 and SS316L regions consist of cellular structures, and the material transition region forms elongated columnar dendrites. (d) shows the low magnification morphology of the BHM samples in the X-Z. When SS316L is deposited on IN625 (SS316L/IN625), SS316L penetrates IN625 more deeply and the interface exhibits wavy characteristics, while the IN625/SS316L interface is relatively flat. The dendrites in SS316L and IN625 grow in different directions, which may be related to the deposition direction, as can be seen in the higher magnification (e). When the deposited material changes to IN625, the direction of the acicular dendrites in SS316L is obstructed, which implies a change in the direction of heat flow. This dendrite growth feature may change the direction of crack propagation and delay fracture when cracks propagate along dendrites [Citation20]. Epitaxial growth of acicular dendrites can be observed on the side of the melt pool, which is closely related to the elemental transition ((f)). The acicular dendrites are perpendicular to the fusion boundary and follow the direction of heat dissipation and temperature gradients. In deposited layers of the same material, needle-like dendrites can extend several layers of growth and cross the melt pool boundary, a growth pattern that facilitates interlayer bonding, as shown in (g). LDED is characterised by rapid heating and cooling, with epitaxial growth of dendrites in adjacent deposited layers in the same direction as the maximum temperature gradient. The BHM sample consists mainly of acicular dendritic and equiaxed crystals ((h–i)), associated with heat accumulation and conduction. Differences in supercooling at different locations in the melt pool, with equiaxed grains more likely to form in the centre of the melt pool, and columnar crystals more inclined to form near the melt pool boundary and grow in the direction of the thermal gradient.
Figure 2. (a) Spatial characteristics of BHM sample with different material deposition distributions in different view planes; (b–c) Microstructure of the BHM sample in the X-Y; (d) The morphology of the BHM sample in the X-Z; (e–f) Zoomed image of the selected region from (d); (g) Dendrites can extend through the melt pool boundary in the Y-Z plane; (h–i) Common crystalline forms in BHM samples: dendritic and equiaxed crystals.
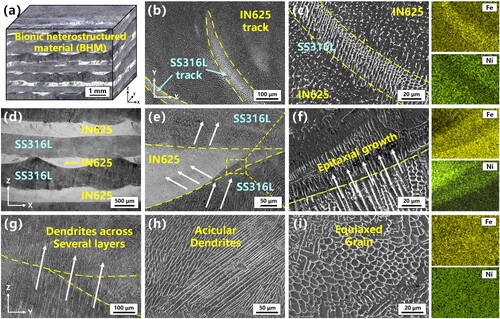
3.1.2. Compositional analysis
reveals the elemental distribution at the interface of SS316L-IN625 BHM verifying the chemical inhomogeneity of BHM. Line analysis at the interface shows that there are significant chemical fluctuations in Fe and Ni concentrations in the transition zone and occur over a relatively wide area. A typical metallurgical diffusion region exists between heterogeneous materials. Fe and Ni diffuse and dissolve at the HM interface, resulting in significant solid solution strengthening, while electronic interactions also help to achieve solid solution hardening [Citation21]. The line analysis of SS316L and IN625 shows significant variations in the major elements, reflecting full diffusion and smooth transition of the components with strong metallurgical bonding of the adjacent layers. The compositional analysis of the selected points is given in . At the SS316L/IN625 interface, selected points 3, 4, and 5 measured in the SS316L region show Ni contents of 13.67–35.01 wt%, which is higher than those found in SS316L (Ni < 10.58 wt%). Measurements of selected points 1 and 2 in the IN625 region also show small amounts of Fe elemental (1.57–2.14 wt%), although IN625 is almost free of Fe. At the IN625/SS316L interface, the buoyancy caused by the low density and low viscosity of SS316L promotes upward flow, which causes the elemental iron content at measurement points 8 to be significantly higher than at measurement points 1 and 2. The compositional analysis shows that the changes in both materials are caused by Marangoni convection and mass transfer effects through the melt pool. This indicates that localised regions may have different mechanical properties than IN625 and SS316L due to compositional variations. This diffusion of interfacial material may contribute to the bond strength. It is noteworthy that the IN625/SS316L boundary does not exactly coincide with the boundary where concentration fluctuations occur. This is probably the main reason for the creation of the planar transition layer. This indicates that a layer of stagnant SS316L liquid is retained at the HM interface, and the point scan analysis of the surface shows that this region is not fully fused to IN625. For IN625/SS316L interface, these factors hamper the IN625 mixed with SS316L. The formation of this planar transition layer may be related to the no-slip boundary conditions [Citation22]. When depositing IN625 on SS316L, the differences in physical properties, viscosity, and other factors of the liquid metal may result in zero velocity (or relative velocity) of the fluid at the interface. No significant enrichment was found as the difference in Cr content between the two alloys was not significant.
Figure 3. Morphology and chemical analysis of BHM: (a) IN625/SS316L interface; (b) SS316L/ IN625 interface.
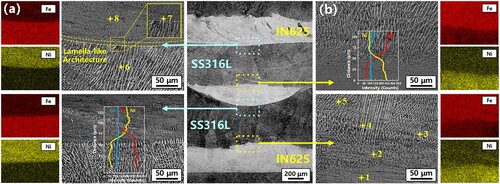
Table 3. Quantitative analysis results for the measurement points (at%).
provides a schematic illustration of the planar transition region at the BHM interface. In previous research, the IN625/SS316L interface had a gradual compositional transition and epitaxial growth [Citation13], whereas epitaxial growth is not evident in (a), which may be related to the deposition strategy. When the deposition direction is different, the temperature gradient, the direction of heat flow and the cooling rate all change, which can make a difference in laser remelting at different locations, especially when depositing different materials [Citation23]. In the no-slip boundary condition, a thin layer of SS316L liquid exists at the IN625/SS316L interface ((a)). When the deposition direction is the same, the SS316L liquid is mixed into the IN625 melt pool by the Marangoni force. The solidification range of SS316L (1673–1698 K [Citation24]) is higher than IN625 (1563–1623 K [Citation25], with a steady reduction in liquid phase temperature in the transition zone from SS316L to IN625. The rise in liquidus temperature increases the local undercooling and thus generates a potential nucleation region. Nucleation begins in the SS316L area and generates a relatively smooth planar transition layer at the interface due to the increased degree of subcooling ((b)). As the solidification proceeds, the remaining liquid enriched with IN625 begins to solidify. The grains grow epitaxially in the solidified planar transition layer, forming a solidification feature as in (a). The presence of zoned solutes enhanced the epitaxial development of cellular dendrites on the surface of the planar transition layer, resulting in the formation of an undercooled zone in front of the solidification front ((c)). The grains evolved into a dendritic structure in IN625 due to the change in composition ((d)).
3.1.3. Crystallographic features
shows the crystallographic characteristics of BHM in the XZ plane. The SS316L and IN625 regions were identified by EDS mapping to characterise the grain orientation of the heterogeneous material, with the SS316L and IN625 regions identified by EDS mapping. IN625 is melted and drawn into the melt pool through the melt pool flow ((b)), which acts as a heterogeneous nucleating agent and promotes epitaxial growth. The IPFs and their corresponding scale for the BHM sample as shown in (a). SS316L columnar cells were epitaxially grown from existing IN625 cells, which promoted the same grain orientation of IPF. The consistent grain orientation plays a significant role in the grain development process of IN625. It not only reduces the energy barrier but also enhances the bonding strength at the interface [Citation26]. (a) shows that most grains appear in green whereas a small number of grains appear in red and blue, indicating that the preferred growth direction of the grains is (101). The grain morphology in the SS316L region is columnar crystals, while the IN625 region has fine grains and is accompanied by epitaxial growth. The columnar dendrites are nearly perpendicular to the boundary lines, which is consistent with the observed microstructure in . As the grains continue to grow, those grains with growth directions closer to the temperature gradient become more competitive, leading to the evolution of coarse columnar grains with preferred growth directions. (b) shows the particle size distribution of the BHM samples, along with specific values and particle size percentages. The size of the particles varied considerably in diameter (from 0 to 62 microns), with particles of 0–5 microns accounting for 84.44% of the major components. This can indicate low deformation and high crystallinity of the sample during the LDED fabrication process. (c) shows the spherical and triangular IPFs, and no significant texture is found in the PF, with a maximum density of only 2.9. In addition, irregularly shaped coarse grains were observed on the SS316L side. This curved geometry of the grains may be caused by the print orientation and composition transition. (d) shows the Schmidt factor for the BHM sample. The Schmidt factor can be used to describe how difficult it is to deform a material. The BHM samples exhibit similar Schmidt coefficients and this similar distribution of features reduces the interfacial mismatch between the two materials.
3.1.4. Cracks formation and its mechanisms
The detected cracks in the BHM XZ plane were further examined by SEM and EBSD as shown in . The BHM samples show three different types of cracking characteristics. As shown in (a), solidification cracks were found at the SS316L/IN625 interface, where no significant elemental enrichment was evident. When SS316L was deposited, the liquid phase temperature at the interface of the HM suddenly increased and SS316L solidified first, interrupting the continuous growth of grains at the interface. Due to the rapid cooling of the molten pool, SS316L undergoes contraction during the cooling process, resulting in tensile stress at the interface. As the temperature decreases, the shrinkage strain at the interface increases. When there is insufficient liquid metal to replenish the interstitial space, small solidification cracks can form. (b) displays the observed segregation cracks in the IN625 region, where the enrichment of the Nb element can be detected within the cracks. Previous publications have demonstrated that the presence of micron-sized secondary phases rich in Nb and Mo directly contributes to the occurrence of cracks in SS304L/IN625 functionally graded materials [Citation15]. Refractory metal monocarbides in the form of (Mo, Nb)C directly contribute to the development of top-layer cracks. The segregation of Nb and Mo in the inter-dendritic regions increases the sensitivity to cracking, while more regions satisfy the conditions for Laves phase precipitation at lower cooling rates. The laves phase remelts at grain boundaries as the thermal cycling effect during deposition occurs. Despite the excellent high temperature mechanical properties of the laves phase, its fracture toughness is very low and the long chain configuration promotes crack extension. In addition to the segregation cracks, we also found straight cracks with sharp kinks extending along the grain boundaries in the IN625 region, as shown in (c). Cracks are mainly located at dendritic boundaries and propagate in the direction of solidified cell growth and are often referred to as ductile dip cracking or strain-age cracking. (d) shows the IPF and KAM maps for ductile dip cracks. When the temperature gradient induces thermal stress surpassing the yield stress, dislocation slip accumulates at high-angle grain boundaries. This process exacerbates strain and stress accumulation and eventually leads to crack formation [Citation27].
Figure 6. SEM images and EDS mapping of cracks in BHM samples: (a) solidification cracks; (b) segregation cracks; (c) ductile dip cracking; (d) IPF and KAM diagrams for ductile dip cracking.
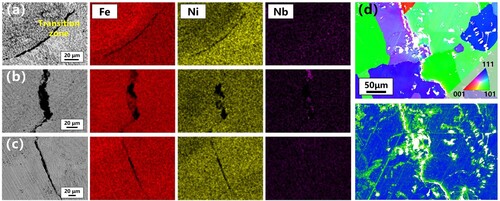
The equilibrium phase transitions of SS316L, IN625, and solidified crack zone in the molten pool at 450–1500°C were simulated by Jmatpro thermodynamic software, respectively, to further investigate the effect of compositional variations on crack formation. The mechanical properties of BHM are strongly coupled to the relative stability of the constituent phases, which particularly gives rise to the amounts of the segregants and precipitates present on the microstructure. The body-centered cubic (BCC) phase in the equilibrium phase diagram of SS316L, as shown in (a), is likely to form the δ-ferrite phase at high temperatures. In comparison to the phase diagram of pure IN625 alloy ((b)), the temperature range associated with the occurrence of Laves phase and carbides in the cracked region is considerably wider. These precipitated phases have lower apparent precipitation kinetics and are therefore thermodynamic stability over a lower and narrower temperature range. As can be seen in (c), the number of phases in the cracked region is significantly higher than that of SS316L and IN625, and mostly remains stable. Due to the small amount of oxygen in the powder, SiO2 and M2O3 phases precipitate before the formation of the austenite phase, which is thermodynamically stable over a wide range of temperatures, but at low levels, with maximum contents of only 0.0731% and 0.025%, respectively. The M(C, N) carbide begins to precipitate at 1216.13°C and exists in an equilibrium state. The Laves phase and M(C, N) carbide evolve more preferentially in the cracked region compared to the equilibrium phase diagram of IN625. Rapid cooling of the molten pool during solidification causes Nb and Mo to micro-partition along cell boundaries, hastening the creation of the Laves phase. The high melting point and high hardness of the Laves phase reduces the plasticity of the material during thermal cycling and increases the susceptibility to crack extension. The phases in the BHM were further characterised by XRD, as shown in (d). The XRD pattern did not show any α-ferrite, which indicates a fully austenitic solidification mode. No secondary peaks of Laves were found at 2θ angles in the 30–50 range, and no macroscopic amounts of secondary phases were found.
3.2. Mechanical properties
3.2.1. Hardness profile
The hardness distribution plot in shows the hardness transition of the BHM in the form of periodic soft–hard-soft layering, representing the bionic structure of the soft matrix containing the hard phase. The hardness in the SS316L and IN625 regions is approximately 200–250 HV and 240–280 HV, respectively. The transition tendency between the materials may be caused by the compositional mixing between the two materials, which mitigates the sudden hardness change at the interface. A gradual shift in hardness was observed at the interface between IN625 and SS316L tracks, which could mitigate the mismatch in mechanical properties between the heterogeneous materials. The addition of IN625 significantly increases the content of Cr, Mo, and Nb, and its high strength comes mainly from the solid solution strengthening of the high melting point solute elements. Furthermore, the absence of any mutations at the interface demonstrates that no significant formation of brittle metallic phases is found in the HM.
3.2.2. Tensile properties
The effect of different material distribution modes on the mechanical properties of the BHM samples was assessed by tensile tests and the stress–strain curves obtained are shown in (a). summarises the yield stress (YS), ultimate tensile strength (UTS), and elongation (EI) for BHMs. Despite the cracks found in the specimens, all BHM samples had higher UTS (671.14–731.74 MPa) than SS316L (647.83 MPa). The strength of the BHM sample was between SS316L and IN625. Of all the BHM samples, the BHM2 sample achieved the highest UTS of 731.74 MPA and showed an excellent strength and toughness trade-off compared to the constituent materials. It is worth noting that by varying the distribution of the HM, the BHM3 sample exhibited an excellent El value of approximately 58.5%, much higher than the other BHM samples and constituent materials. This excellent mechanical response is the result of the synergistic action of BHMs, which is often difficult to achieve with homogeneous materials. In comparison to the constituent materials, BHM surpasses the trade-off between single alloy strength and ductility, underscoring the pivotal role of tightly bonded heterogeneous interfaces in facilitating deformation during balanced tensile processes. Generally, the strength of HMs is influenced by the strength of the constituent materials and can be estimated using the Rule of Mixtures (ROM) [Citation28]:
where Vi and σi are the volume fraction and strength of component i. (b) illustrates the comparison between the tensile performance of the BHM2 sample and the calculated tensile performance using the ROM. It is worth noting that the BHM2 sample exhibited a better performance in terms of high strength and ductility compared to the prediction by ROM, although the excessive interface in the BHM sample may have led to rapid crack extension. This suggests that other strengthening mechanisms exist, leading to synergistic strengthening and toughening in heterogeneous materials. (c) compares the UTS and EL of BHM with stainless steel [Citation10,Citation29–35], nickel-based superalloys [Citation11,Citation34,Citation36,Citation37] and stainless steel/nickel-based superalloy heterogeneous metal components [Citation16,Citation32,Citation33,Citation38–48] from different AM methods. In most dissimilar material joints, it is difficult to meet the requirement for equal strength between the interface and the two base materials, and the mechanical properties at the interface often fall short of expectations. Zhang et al. fabricated SS316L and IN625 bimetallic materials by wire arc additive manufacturing with ultimate tensile strength and elongation of 406.55–444.45 MPa and 23.6–38.6%, respectively [Citation47]. The material layer interface is the weakest link in HMs. In contrast, our proposed SS316L/IN625 bionic heterogeneous material further demonstrates the possibility of achieving a combination of high strength and excellent ductility through additive manufacturing. The higher strength and toughness trade-off may be associated with a bionic crossed-lamellar structure with multiple strengthening mechanisms.
Figure 9. (a) Engineering stress-strain curves of SS316L, IN625 and BHM samples; (b) The strength level of the BHM2 sample is compared to the calculated values from ROM; (c) Comparison of UTS and EL of BHM samples with other stainless steels, nickel-based superalloys and stainless steel/nickel-based superalloy heterogeneous metal components treated by different AM processes.
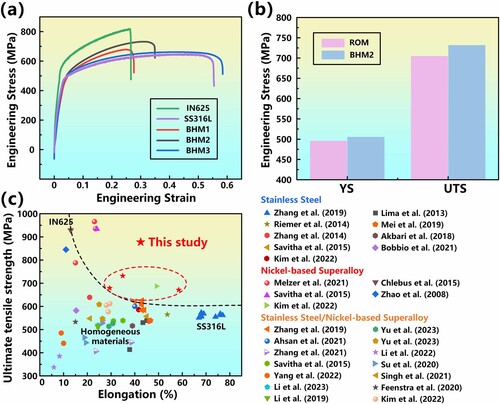
Table 4. Mechanical properties of LDED-produced SS316L-IN625 BHMs.
The main reasons for the excellent combination of strength and ductility observed in BHM are hetero-deformation induced (HDI) strengthening and strain hardening [Citation49]. During the tensile process of HMs, the softer region will undergo plastic deformation first, while the harder region will remain elastic. The overall yield strength of the material is enhanced by redistributing stress from the soft zone (plastic deformation) to the hard zone (non-deformable) [Citation50]. The HDI enhancement of the material is achieved through the combined effects of long-range internal stresses induced by deformation, forward stresses in the hard zone, and backward stresses in the soft zone. This results in the softer region appearing stronger and capable of withstanding higher stresses. To characterise the reasons for the combined high strength and high toughness behaviour of SS316L/IN625 BHM2 and the contribution of effective and back stresses to the flow stresses, a load-unload-reload (LUR) test was carried out on the BHM to investigate the evolution of HDI stresses, as shown in (a). The HDI stress (σHDI) can be calculated based on the unloading-reloading hysteresis loop of the LUR curve, as follows [Citation51,Citation52]:
Where σr and σu are the reload yield point and unload yield point respectively, as shown in (b). lists the σr and σu values for the six LUR cycles. The BHM curve shows a clear hysteresis loop in each LUR cycle, which implies a strong Bauschinger effect [Citation53]. Compared to non-cyclic samples, the cyclic LUR samples exhibit higher true tensile strength and true strain. This can be attributed to the elevated work hardening in the BHM (Bauschinger effect), as significant deformation incompatibility may lead to higher strain hardening in HMs [Citation54]. (c) provides a close-up view of the last two cycles of the hysteresis loop, allowing estimation of the back stress and effective stress. BHM materials undergo significant heterogeneous deformation, and a larger hysteresis loop indicates a stronger Bauschinger effect. (d) illustrates the relationship between the measured HDI stress and true plastic strain. The Bauschinger effect is strong in the initial strain phase and decreases with increasing strain, confirming the dominant role of HDI hardening in the early deformation phase. At lower strain stages, SS316L yields earlier than IN625, followed by plastic deformation in the soft areas, resulting in heterogeneous deformation between the different layers. HDI stress increases significantly with deformation. HDI stress is generated through the combined effect of back stress in the soft zone and forward stress in the hard zone, tending to accumulate at the interfaces during the deformation process. Back stress always acts in the opposite direction to the externally applied stress, impeding the further release of dislocations from the sources. A higher plastic flow stress is required to overcome this stress field in order to sustain further deformation [Citation55]. The weakening of HDI at higher plastic strains may be related to the difficulty in effectively accumulating geometrically necessary dislocation (GND) changes at the boundaries. At higher strain levels, SS316 can withstand larger plastic strains compared to IN625. As a result, higher strain gradients are generated at the interfaces. As the strain gradient continues to increase, more GNDs are required to accommodate the enhanced strain gradients. The accumulated GNDs are believed to provide additional strain hardening capability, contributing to the delay of necking and improved ductility during tensile testing.
Figure 10. (a) LUR curve of BHM2 sample; (b) Different stresses are defined within the unloading-reloading hysteresis loop; (c) Close-up view of the first and last cycle of the hysteresis loop in the LUR curve of BHM2 sample; (d) The relationship between the measured HDI stress and true plastic strain.
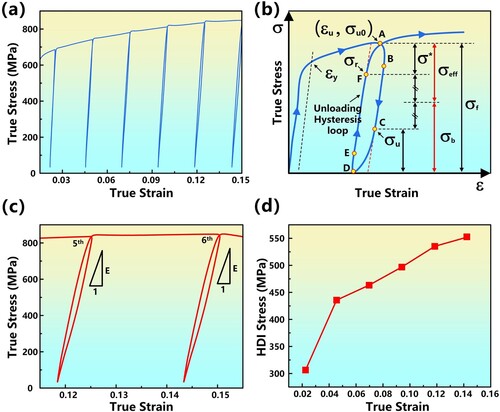
Table 5. the σr and σu values for the six LUR cycles.
3.2.3. Deformation and fracture behaviour
Microstructural analysis of the fracture surface of the BHM samples was performed to gain further insight into the deformation mechanisms. (a1–a3) depicts the SEM images of the surface slip marks at different locations of the BHM tensile specimen in the X-Y direction. From (a1), it can be observed that slip bands of different orientations intersect near the fracture region, indicating the activation of multiple slip systems [Citation56]. The continuous slip of high-density dislocation groups during the deformation process results in the formation of interconnected slip bands. Tensile stresses applied by uniaxial stresses are transformed into multi-axial stresses due to heterogeneous deformation, which activates more slip systems and significantly contributes to the accumulation of dislocations and interactions [Citation57]. Compared to the IN625 region, the SS316L region has a deformed surface with collapsed and bulging surface features, and the heterogeneous material exhibits incompatible deformations during stretching, as (a2). In the area away from the fracture, the number of short slip lines is significantly reduced and oriented at approximately 45 degrees to the axis of tension. To understand how BHM influences deformation/fracture behaviour and whether HMs can mitigate strain localisation and cracking tendencies, the dynamic strain evolution was studied during tensile testing using in-situ DIC. (b) shows the deformation process in the XY plane of the BHM specimen monitored during the tensile test. At an average strain of 1–2%, the surface of the tested BHM sample exhibits relatively uniform deformation. However, when the average strain increases to 3%, non-uniform strain points appear on the surface of the tested sample. These strain points further extend along the surface perpendicular to the loading direction, forming strain bands of 4%−6% strain. It can be observed that there is a stratification of strain concentration detected in the BHM sample. The SS316L region undergoes plastic deformation initially, while the IN625 region maintains its elastic behaviour during the tensile deformation process. Bionic materials with an excellent performance combination typically possess the following characteristics: (i) The ability to delay necking during the deformation process, and (ii) The capability to effectively postpone the formation and propagation of cracks. When plastic deformation becomes unstable, the necking region of homogeneous materials experiences higher strain concentration, leading to sample failure. BHM can effectively limit and retard premature strain concentration and local necking in the SS316L region, while the development of multiple deformation bands can effectively improve ductility.
Figure 11. (a) Surface slip traces at different locations; (b) Strain distribution maps in different stage monitored by DIC.
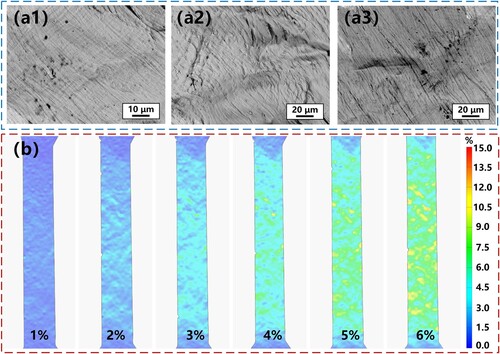
shows the fracture characteristics of the BHM sample in the XY plane. Due to the significant shear stress at the fracture surface, SS316L with good ductility, will deform in the direction of the applied load, as shown in (a). A large number of intertwined deformation bands were observed in the deformed area between SS316L and IN625, indicating that the SS316L region had undergone severe deformation. Due to the lower yield strength of SS316L compared to IN625, the SS316L region undergoes significant deformation first. The crack was initiated in the SS316L area, as shown in (b). From the surface scan analysis, it can be seen that the crack propagated in the SS316L melt pool rather than fracturing along the IN625 interface, indicating a good interfacial bond between the two materials. The stiff IN625 changes the direction of crack extension, lengthens the crack propagation path, and increases the elongation of the BHM sample. To further investigate the crystallographic characteristics of the specimens after stretching, EBSD analysis was carried out on the fractured BHM samples ((c)). Compared to the specimen before stretching (), the grain orientation of the sample after the stretching test is not strongly textured and the dendrite direction is no longer perpendicular to the melt pool boundaries. This change in grain orientation is likely due to the applied tensile strain and grain rotation [Citation58,Citation59]. Significant plastic incompatibilities exist in the SS316L and IN625 regions during plastic deformation. The inset below shows the crystallographic features away from the fracture. It is worth noting that fine grains are present at the fracture surface, indicating a phase transformation from face-centered cubic (FCC) to BCC in that region under stress-induced conditions. These BCC phases may be δ-ferritic phases formed at high temperatures in SS316L. The fracture mechanism of the BHM is analysed in (d). Due to the significant difference in properties between SS316L and IN625, cracks tend to start and propagate at the boundary between the heterogeneous materials, as shown in the inset on the right. During stretching, the high mismatch in strain causes severe deformation of SS316L. This mechanical incompatibility can lead to stress concentrations such as micro-cracks and voids at the interface during strain.
Figure 12. (a) Microstructure and elemental distribution of BHM samples after tensile stretching; (b) EBSD analysis of BHM samples after tensile stretching; (c) Fracture mechanism of BHM samples.
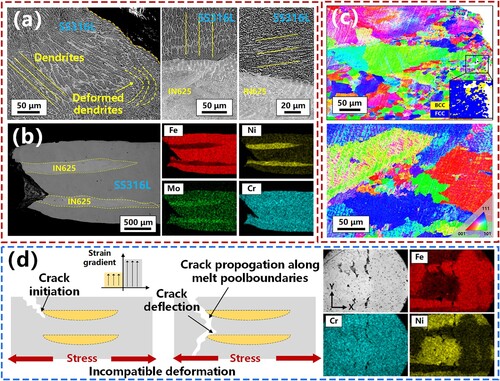
outlines the deformation strengthening mechanism of the BHM. The tensile deformation process at BHM can be divided into three stages. In the first stage, both SS316L and IN625 undergo elastic deformation. In the second stage, SS316L begins to deform plastically while IN625 remains elastic. Although both IN625 and SS316L have FCC phases, there may be secondary phases and precipitates present in IN625 that have higher yield strengths than SS316L. SS316L cannot deform freely due to IN625 constraints and strain gradients occur in SS316L near the interface. A large number of GNDs are created at the interface to accommodate the strain height mismatch and plastic incompatibility between the HMs, which typically increases the strength level and strain-hardening capacity of the HMs and maintains the deformation compatibility of the heterogeneous materials [Citation1]. During this stage, the IN625 region remains elastic, preventing the release of dislocations and slip in SS316L until the back stress in SS316L reaches a critical value, ultimately increasing the overall yield strength [Citation60]. In the third stage, SS316L and IN625 are plastically deformed together. The experiments described above show that the grains in the SS316L of the deformed BHM samples become elongated, while IN625 remains mostly unchanged after deformation, indicating that the SS316L is subjected to higher plastic strains than the IN625. GND in the SS316L is blocked by the IN625 and generates a strain gradient. Strain gradients occur at the interfaces of BHMs to accommodate the stress and strain distributions during the loading process. The resulting reaction forces enhance the strain hardening capability, thereby contributing to improved mechanical properties. Unlike traditional strengthening mechanisms, BHM exhibits multiple enhancement and toughening mechanisms, along with a high work hardening ability, which can significantly enhance the strength and plasticity of the material.
Figure 13. Deformation process of BHM in different stages [Citation62].
![Figure 13. Deformation process of BHM in different stages [Citation62].](/cms/asset/c38b967a-eed9-46b7-b091-3dfd5953cc87/nvpp_a_2266640_f0013_oc.jpg)
shows the fracture morphology of the tensile specimen of the BHM. The presence of several large and deep voids in the BHM implies strong interactions between the heterogeneous materials even after necking, as shown in (a–c). In (b), it can be seen that significant fracture voids exist at the SS316L/IN625 interface, while the IN625/SS316L interface is relatively intact. This is related to the large differences between the physical properties of HMs [Citation13]. The SS316L region shows small dimples with significant plastic deformation, which is a typical ductile fracture mode ((d)). The good toughness characteristics of SS316L help to improve the ductility of BHM samples. In the process of tensile deformation, the crack propagates to the IN625 region. It is observed from (e) that the fracture is significantly hindered when entering the IN625 region, which may delay fracture and enhance the work hardening of the material. Since secondary phases such as Mo, Nb form micro-scale voids in the IN625 region, cracking features along grain boundaries are formed during deformation ((f)). The EDS mapping at the fracture is shown in (g), and these HMs composed of highly mechanically incompatible regions are an effective approach to balance the trade-off between strength and ductility in metallic materials [Citation61].
4. Conclusions
In summary, we propose a bionic heterostructure strategy inspired by conch shells, investigate the microstructure, mechanical properties, and deformation characteristics of BHM in detail, and discuss the strengthening mechanism of BHM. The following conclusions are mainly drawn:
(1) The SS316L-IN625 heterogeneous metallic material with a bionic crossed-lamellar structure has a tensile strength of 731.74 MPa and a uniform elongation of 34.98%. Despite the presence of cracks, the BHM samples exhibited greater yield strength and tensile strength than predicted by the ROM.
(2) Microstructural characterisation revealed a multi-scale periodic distribution of BHM in the form of a soft–hard-soft layered structure. The similar grain preferential growth directions and Schmidt factor reduced the interfacial mismatch between the two materials. Three different types of cracking features were identified in the BHM samples including solidification cracking, segregation cracking, and ductile dip cracking.
(3) BHM has three stages of deformation: 1. SS316L and IN625 undergo elastic deformation; 2. SS316L begins to deform plastically while IN625 remains elastic. To adapt to the high strain mismatch and plastic incompatibility between the heterogeneous materials, a large number of GNDs are generated at the interface to maintain deformation compatibility of the BHM. 3. SS316L and IN625 are plastically deformed together. The severe strain gradient at the interface increases the HDI stress evolution and strain hardening rate.
(4) The BHM tensile specimens showed delayed fracture under necking deformation with the presence of multiple deformation bands, which contributed to good ductility. Fracture morphology showed incompatible deformation. The synergistic effect between hard IN625 and soft SS316L enhances the overall strength of BHM.
This research demonstrates the flexibility of preparing BHM with excellent performance trade-offs through LDED, providing a new approach for producing controllable high-strength and ductility combinations of heterogeneous metal components.
Disclosure statement
No potential conflict of interest was reported by the author(s).
Data availability statement
Data will be available upon request.
Additional information
Funding
References
- Fang XT, He GZ, Zheng C, et al. Effect of heterostructure and hetero-deformation induced hardening on the strength and ductility of brass. Acta Mater. 2020;186:644–655. doi: 10.1016/j.actamat.2020.01.037
- Li Y, Yuan G, Li L, et al. Ductile 2-GPa steels with hierarchical substructure. Science. 2023;379(6628):168–173. doi: 10.1126/science.add7857
- Zhao Y, Wang T, Gao B, et al. Towards enhanced strength-ductility in pure copper by fabricating hetero grain composite laminates. J Alloys Compd. 2022;928:167192. doi: 10.1016/j.jallcom.2022.167192
- Xu C, Chen X, Wu W, et al. Bioinspired multi-metal structures produced via direct Ink writing. J Bionic Eng. 2022;19(6):1578–1588. doi: 10.1007/s42235-022-00257-2
- Wei J, Pan F, Ping H, et al. Bioinspired additive manufacturing of hierarchical materials: from biostructures to functions. Research. 2023;6:0164. doi: 10.34133/research.0164
- Lin L, Kollipara PS, Zheng Y. Digital manufacturing of advanced materials: challenges and perspective. Mater Today. 2019;28:49–62. doi: 10.1016/j.mattod.2019.05.022
- Saleh B, Jiang J, Fathi R, et al. 30 years of functionally graded materials: an overview of manufacturing methods, applications and future challenges. Compos B Eng. 2020;201:108376. doi: 10.1016/j.compositesb.2020.108376
- Bandyopadhyay A, Zhang Y, Onuike B. Additive manufacturing of bimetallic structures. Virtual Phys Prototyp. 2022;17(2):256–294. doi: 10.1080/17452759.2022.2040738
- Chen B, Su Y, Xie Z, et al. Development and characterization of 316L/Inconel625 functionally graded material fabricated by laser direct metal deposition. Opt Laser Technol. 2020;123:105916. doi: 10.1016/j.optlastec.2019.105916
- Mei X, Wang X, Peng Y, et al. Interfacial characterization and mechanical properties of 316L stainless steel/inconel 718 manufactured by selective laser melting. Mater Sci Eng A. 2019;758:185–191. doi: 10.1016/j.msea.2019.05.011
- Melzer D, Džugan J, Koukolíková M, et al. Structural integrity and mechanical properties of the functionally graded material based on 316L/IN718 processed by DED technology. Mater Sci Eng A. 2021;811:141038. doi: 10.1016/j.msea.2021.141038
- Wang J, Misra A. An overview of interface-dominated deformation mechanisms in metallic multilayers. Curr Opin Solid State Mater Sci. 2011;15(1):20–28. doi: 10.1016/j.cossms.2010.09.002
- Chen N, Khan HA, Wan Z, et al. Microstructural characteristics and crack formation in additively manufactured bimetal material of 316L stainless steel and inconel 625. Addit Manuf. 2020;32:101037. doi: 10.1016/j.addma.2020.101037
- Wang R, Gu D, Lin K, et al. Multi-Material additive manufacturing of a bio-inspired layered ceramic/metal structure: formation mechanisms and mechanical properties. Int J Mach Tools Manuf. 9.670. 2022;175:103872. doi: 10.1016/j.ijmachtools.2022.103872
- Carroll BE, Otis RA, Borgonia JP, et al. Functionally graded material of 304L stainless steel and inconel 625 fabricated by directed energy deposition: characterization and thermodynamic modeling. Acta Mater. 2016;108:46–54. doi: 10.1016/j.actamat.2016.02.019
- Kim YS, Yun D, Han JH, et al. Bimetallic additively manufactured structure (BAMS) of inconel 625 and austenitic stainless steel: effect of heat-treatment on microstructure and mechanical properties. Int J Adv Manuf Technol. 2022;121(11–12):7539–7549. doi: 10.1007/s00170-022-09723-x
- Peng X, Zhang B, Wang Z, et al. Bioinspired strategies for excellent mechanical properties of composites. J Bionic Eng. 2022;19(5):1203–1228. doi: 10.1007/s42235-022-00199-9
- Li H, Li X. The art of curved reinforcing in biological armors – seashells. J Bionic Eng. 2019;16(4):711–718. doi: 10.1007/s42235-019-0057-9
- Gu GX, Takaffoli M, Buehler MJ. Hierarchically enhanced impact resistance of bioinspired composites. Adv Mater. 2017;29(28):1700060. doi: 10.1002/adma.201700060
- Tan C, Chew Y, Weng F, et al. Laser aided additive manufacturing of spatially heterostructured steels. Int J Mach Tools Manuf. 2022;172:103817. doi: 10.1016/j.ijmachtools.2021.103817
- Shinoda T, Masuda-Jindo K-i, Mishima Y, et al. Extra contribution of transition-metal solutes to the solid-solution hardening of nickel. Phys Rev B. 1987;35(5):2155–2161. doi: 10.1103/PhysRevB.35.2155
- Soysal T, Kou S, Tat D, et al. Macrosegregation in dissimilar-metal fusion welding. Acta Mater. 2016;110:149–160. doi: 10.1016/j.actamat.2016.03.004
- Chen H-y, Gu D-d, Ge Q, et al. Role of laser scan strategies in defect control, microstructural evolution and mechanical properties of steel matrix composites prepared by laser additive manufacturing. Int J Miner Metall Mat. 2021;28(3):462–474. doi: 10.1007/s12613-020-2133-x
- Kim CS. Thermophysical properties of stainless steels. ANL-75-55. IL, USA: Argonne National Lab; 1975. doi: 10.2172/4152287
- INCONEL Alloy 625 – Special Metals Corporation. https://www.specialmetals.com/documents/technical-bulletins/inconel/inconel-alloy-625.pdf.
- Tan C, Wang D, Ma W, et al. Ultra-strong bond interface in additively manufactured iron-based multi-materials. Mater Sci Eng A. 2021;802:140642. doi: 10.1016/j.msea.2020.140642
- Qian D, Xue J, Zhang A, et al. Statistical study of ductility-Dip cracking induced plastic deformation in polycrystalline laser 3D printed Ni-based superalloy. Sci Rep. 2017;7(1):2859. doi: 10.1038/s41598-017-03051-x
- Zhao Y, Wang T, Gao B, et al. Towards enhanced strength-ductility in pure copper by fabricating hetero grain composite laminates. J Alloys Compd. 2022;928:167192. doi: 10.1016/j.jallcom.2022.167192
- Bobbio LD, Bocklund B, Liu Z-K, et al. Tensile behavior of stainless steel 304L to Ni-20Cr functionally graded material: experimental characterization and computational simulations. Materialia. 2021;18:101151. doi: 10.1016/j.mtla.2021.101151
- Riemer A, Leuders S, Thöne M, et al. On the fatigue crack growth behavior in 316L stainless steel manufactured by selective laser melting. Eng Fract Mech. 2014;120:15–25. doi: 10.1016/j.engfracmech.2014.03.008
- De Lima MSF, Sankaré S. Microstructure and mechanical behavior of laser additive manufactured AISI 316 stainless steel stringers. Mater Des. 2014;55:526–532. doi: 10.1016/j.matdes.2013.10.016
- Zhang X, Chen Y, Liou F. Fabrication of SS316L-IN625 functionally graded materials by powder-Fed directed energy deposition. Sci Technol Weld Joining. 2019;24(5):504–516. doi: 10.1080/13621718.2019.1589086
- Savitha U, Jagan Reddy G, Venkataramana A, et al. Chemical analysis: structure and mechanical properties of discrete and compositionally graded SS316–IN625 dual materials. Mater Sci Eng A. 2015;647:344–352. doi: 10.1016/j.msea.2015.09.001
- Zhang K, Wang S, Liu W, et al. Characterization of stainless steel parts by laser metal deposition shaping. Mater Des. 2014;55:104–119. doi: 10.1016/j.matdes.2013.09.006
- Akbari M, Kovacevic R. An investigation on mechanical and microstructural properties of 316LSi parts fabricated by a robotized laser/wire direct metal deposition system. Addit Manuf. 2018;23:487–497. doi: 10.1016/j.addma.2018.08.031
- Zhao X, Chen J, Lin X, et al. Study on microstructure and mechanical properties of laser rapid forming inconel 718. Mater Sci Eng A. 2008;478(1-2):119–124. doi: 10.1016/j.msea.2007.05.079
- Chlebus E, Gruber K, Kuźnicka B, et al. Effect of heat treatment on the microstructure and mechanical properties of inconel 718 processed by selective laser melting. Mater Sci Eng A. 2015;639:647–655. doi: 10.1016/j.msea.2015.05.035
- Yang SW, Yoon J, Lee H, et al. Defect of functionally graded material of inconel 718 and STS 316L fabricated by directed energy deposition and its effect on mechanical properties. J Mat Res Technol. 2022;17:478–497. doi: 10.1016/j.jmrt.2022.01.029
- Feenstra DR, Molotnikov A, Birbilis N. Effect of energy density on the interface evolution of stainless steel 316L deposited upon INC 625 via directed energy deposition. J Mater Sci. 2020;55(27):13314–13328. doi: 10.1007/s10853-020-04913-y
- Singh SP, Aggarwal A, Upadhyay RK, et al. Processing of IN718-SS316L bimetallic-structure using laser powder bed fusion technique. Mater Manuf Process. 2021;36(9):1028–1039. doi: 10.1080/10426914.2021.1885701
- Li P, Gong Y, Xu Y, et al. Inconel-steel functionally bimetal materials by hybrid directed energy deposition and thermal milling: microstructure and mechanical properties. Arch Civ Mech Eng. 2019;19(3):820–831. doi: 10.1016/j.acme.2019.03.002
- Xing L, Quanjie W, Qirui Z, et al. Interface analyses and mechanical properties of stainless steel/nickel alloy induced by multi-metal laser additive manufacturing. J Manuf Process. 2023;91:53–60. doi: 10.1016/j.jmapro.2023.02.038
- Su Y, Chen B, Tan C, et al. Influence of composition gradient variation on the microstructure and mechanical properties of 316 L/Inconel718 functionally graded material fabricated by laser additive manufacturing. J Mater Process Technol. 2020;283:116702. doi: 10.1016/j.jmatprotec.2020.116702
- Li T, Wang Z, Hu S, et al. Hot cracking during the fabrication of inconel 625/stainless steel 308 L functionally graded material by dual-wire arc additive manufacturing. J Manuf Process. 2022;82:461–473. doi: 10.1016/j.jmapro.2022.08.018
- Yu X, Xue J, Shen Q, et al. Dual-Wire plasma arc additively manufactured SS 316L-inconel 625 functionally graded material: microstructure evolution and mechanical properties. J Mater Eng Perform. 2023;32(3):1412–1422. doi: 10.1007/s11665-022-07158-9
- Yu X, Xue J, Shen Q, et al. Effect of composition gradient design on microstructure and mechanical properties of dual-wire plasma arc additively manufactured 316L/IN625 functionally graded materials. Mater Chem Phys. 2023;307:128121. doi: 10.1016/j.matchemphys.2023.128121
- Zhang W, Lei Y, Meng W, et al. Effect of deposition sequence on microstructure and properties of 316L and inconel 625 bimetallic structure by wire Arc additive manufacturing. J Mater Eng Perform. 2021;30(12):8972–8983. doi: 10.1007/s11665-021-06137-w
- Ahsan MRU, Fan X, Seo G-J, et al. Microstructures and mechanical behavior of the bimetallic additively-manufactured structure (BAMS) of austenitic stainless steel and inconel 625. J Mater Sci Technol. 2021;74:176–188. doi: 10.1016/j.jmst.2020.10.001
- Zhu Y, Wu X. Perspective on hetero-deformation induced (HDI) hardening and back stress. Mater Res Lett. 2019;7(10):393–398. doi: 10.1080/21663831.2019.1616331
- Zhu Y, Ameyama K, Anderson PM, et al. Heterostructured materials: superior properties from hetero-zone interaction. Mater Res Lett. 2021;9(1):1–31. doi: 10.1080/21663831.2020.1796836
- Yang M, Pan Y, Yuan F, et al. Back stress strengthening and strain hardening in gradient structure. Mater Res Lett. 2016;4(3):145–151. doi: 10.1080/21663831.2016.1153004
- Zhu Y, Wu X. Heterostructured materials. Prog Mater Sci. 2023;131:101019. doi: 10.1016/j.pmatsci.2022.101019
- Gao S, Yoshino K, Terada D, et al. Significant bauschinger effect and back stress strengthening in an ultrafine grained pure aluminum fabricated by severe plastic deformation process. Scr Mater. 2022;211:114503. doi: 10.1016/j.scriptamat.2022.114503
- Park HK, Ameyama K, Yoo J, et al. Additional hardening in harmonic structured materials by strain partitioning and back stress. Mater Res Lett. 2018;6(5):261–267. doi: 10.1080/21663831.2018.1439115
- Merklein M, Jäckisch M, Kuball C-M, et al. Mechanical joining of high-strength multi-material systems − trends and innovations. Mech Ind. 2023;24:16. doi: 10.1051/meca/2023013
- Kreins M, Schilli S, Seifert T, et al. Bauschinger effect and latent hardening under cyclic micro-bending of Ni-base alloy 718 single crystals: part I. experimental analysis of single and multi slip plasticity. Mater Sci Eng A. 2021;827:142027. doi: 10.1016/j.msea.2021.142027
- Ding H, Cui X, Wang Z, et al. A New strategy for fabrication of unique heterostructured titanium laminates and visually tracking their synchronous evolution of strain partitions versus microstructure. J Mater Sci Technol. 2022;107:70–81. doi: 10.1016/j.jmst.2021.08.016
- Du C, Gao Y, Zha M, et al. Deformation-Induced grain rotation and grain boundary formation achieved through dislocation-disclination reactions in polycrystalline hexagonal close-packed metals. Acta Mater. 2023;250:118855. doi: 10.1016/j.actamat.2023.118855
- Barbier D, Favier V, Bolle B. Modeling the deformation textures and microstructural evolutions of a Fe–Mn–C TWIP steel during tensile and shear testing. Mater Sci Eng A. 2012;540:212–225. doi: 10.1016/j.msea.2012.01.128
- Chen X, Zhang B, Zou Q, et al. Design of pure aluminum laminates with heterostructures for extraordinary strength-ductility synergy. J Mater Sci Technol. 2022;100:193–205. doi: 10.1016/j.jmst.2021.05.030
- Lei YB, Wang ZB, Zhang B, et al. Enhanced mechanical properties and corrosion resistance of 316L stainless steel by pre-forming a gradient nanostructured surface layer and annealing. Acta Mater. 2021;208:116773. doi: 10.1016/j.actamat.2021.116773
- Romero-Resendiz L, El-Tahawy M, Zhang T, et al. Heterostructured stainless steel: properties, current trends, and future perspectives. Mater Sci Eng R: Rep. 2022;150:100691. doi: 10.1016/j.mser.2022.100691