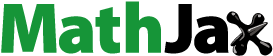
ABSTRACT
Combining poly (L-lactic acid) (PLLA) with thermoplastic polyurethane elastomer (TPU) can integrate the advantages of excellent biocompatibility and intrinsic shape memory ability of PLLA and high elasticity and excellent shape memory properties of TPU in the application of minimally invasive surgery for bone tissue engineering. However, TPU easily forms a sea-island-like structure in PLLA matrix, decreasing shape memory properties. In this study, a co-continuous structure of TPU phase in PLLA matrix was constructed by adding Fe3O4 nanoparticles due to the changed interfacial tension and flow behavior of TPU, which endowed the TPU/PLLA/Fe3O4 blend fabricated via selective laser sintering (SLS) with excellent shape memory properties. As a result, the morphology of TPU in the blend changed from sea-island-like structure to complete co-continuous structure with increasing Fe3O4 content (0 to 10wt%), and shape recovery ratios in 50 °C water increased from 66.67 to 95.92%. The introduction of Fe3O4 endowed the blend with magnetic responsive shape memory in alternating magnetic field because Fe3O4 could heat it by generating heat from relative friction and particle collisions. Besides, the tensile modulus and hardness of the specimen with 10wt% Fe3O4 nanoparticles increased. In addition, the blend demonstrated excellent biocompatibility by promoting cell adhesion, spreading, and proliferation.
1. Introduction
Shape memory polymer (SMP) possesses great potential in the application of minimally invasive surgery for bone defect repair, which can recover its original shape from the fixed compact structure to self-adapt to the irregular bone defect area after being exposed to an external stimulus after surgery [Citation1-5]. Poly (L-lactic acid) (PLLA) is a commonly employed material for bone tissue engineering, thanks to its exceptional biodegradability and biocompatibility, which has been authorised by the United States Food and Drug Administration (FDA) for use in humans [Citation6]. More importantly, PLLA is a kind of SMP because it is a semi-crystalline aliphatic polyester, which possesses intrinsic shape memory ability due to its crystalline phase as the fixing phase to maintain shape and the amorphous phase as the switching phase to provide a driving force for shape recovery. Arabiyat et al. prepared a scaffold made from poly(ϵ-caprolactone)-diacrylate (PCL-DA) combined with PLLA for shape memory, and the results indicated that the scaffold with a semi-interpenetrating network of PLLA exhibited biocompatibility and shape memory effect [Citation7]. While PLLA exhibits limited shape memory properties for the application of minimally invasive surgery due to the intrinsic brittleness originating from the slow crystallisation rates and the high glass transition temperature (Tg) [Citation8,Citation9].
For the purpose of enhancing the shape memory properties of the PLLA blend, SMP with high elasticity can be blended with PLLA to protect brittle PLLA from breakage and endow the blend with the ability to bear greater deformation forces during the shape memory process [Citation10]. Thermoplastic polyurethane (TPU) is a semi-crystalline nature biopolymer consisting of soft and hard segments, in which the non-crystalised soft segments provide high elasticity for TPU due to their elastomeric behaviour, and the polarity differences between the soft and hard segments allow TPU to possess a high degree of phase separation to accomplish shape fixity and recovery [Citation11,Citation12]. Previous researches have reported that the introduction of TPU in the PLLA matrix can reduce the brittleness by the elasticity of TPU, enabling PLLA to have greater deformation ability during the shape memory process, and TPU can act as the switching phase in the PLLA matrix to provide the additional recovery force required to recover initial shape [Citation13,Citation14]. In general, a small amount of TPU is dispersed in PLLA to form a sea-island morphology. When the TPU content reaches a critical value, its morphology changes into a co-continuous structure, which can provide stronger resilience for the shape recovery process to enhance the shape memory properties of the TPU/PLLA blend [Citation15]. However, a high TPU content will deteriorate the mechanical properties of the blend due to the poor strength and modulus properties of TPU.
Low-dimensional nanomaterials have been proven to effectively facilitate the formation of a co-continuous structure from a sea-island-like structure of a minor component phase in an immiscible polymer blend, especially when they are selectively distributed in the minor component phase. They possess great surface energy that can induce the minor component phase to elongate and interlink by changing the interfacial tension and flow behaviour [Citation16-18]. Luo et al. designed polylactic acid/high-density polyethylene/carbon black composites and found that the carbon black nanoparticles had an effect on rheological behaviours to form a co-continuous structure [Citation19]. Meanwhile, low-dimensional nanomaterials have the ability to improve the mechanical properties by hindering the crack propagation or passivate and terminate the crack in a polymer matrix, and this organic–inorganic combination could improve its bioactivity and biocompatibility. Compared with other single bioceramics, bioglass, pure polymer, and other materials, the mechanical properties, biological activity, and biocompatibility are more matched with natural human bone [Citation20-23]. Fe3O4 magnetic nanoparticles, a kind of low-dimensional nanomaterial, exhibit strong magnetism that generates heat through particle collisions and relative friction when subjected to an alternating magnetic field [Citation24]. They can be used as magnetically responsive nanofillers in the TPU/PLLA blend, which can trigger the shape memory effect to recover to the original shape by heating the blend to release the stored energy when it is exposed to an alternating magnetic field. The magnetic-triggered method can achieve a remote non-contact and harmless mode for the human body compared to the direct heat-triggered method, the electric-triggered method, and so on, which can control the shape recovery of the blend after implantation [Citation10]. In addition, Fe3O4 nanoparticles can be used as micromagnetic sources in the blend to induce cell proliferation, differentiation as well as promote bone regeneration [Citation25,Citation26].
In the present study, magnetic-responsive TPU/PLLA/Fe3O4 blends with excellent shape memory properties and mechanical properties were obtained by selective laser sintering (SLS), which was a kind of 3D printing by layer-by-layer stacking and free-forming and more suitable for processing blends with porous structures and customised shapes than other manufacturing methods [Citation27-32]. The impact of Fe3O4 on the micromorphology and mechanical properties of TPU/PLLA (70/30) were investigated. The enhancement mechanisms attributed to Fe3O4 nanoparticles and the co-continuous structure of the TPU phase were discussed via observing fracture morphologies after the tensile test. More importantly, the shape memory properties of the blends containing varying amounts of Fe3O4 under an alternating magnetic field were evaluated with a switching temperature of 50°C. The shape memory mechanism of the blends with a co-continuous structure that responded to magnetic fields was revealed. In addition, the biocompatibility of blends was assessed based on cell adhesion and proliferation behaviours.
2. Materials and methods
2.1. Materials
PLLA powders with a molecular weight of 150 kDa and a diameter of 150 μm were produced by Shenzhen Polymtek Biomaterial Co., Ltd. (Shenzhen, China). Thermoplastic TPU with a bulk density of 1.2 g/cm3 and a diameter of 60 μm was gained from LEHVOSS Chemical Trading Co., Ltd (Shanghai, China). Fe3O4 powders with 20 nm in diameter were provided by Nanjing Emperor nano Co., Ltd. (Nanjing, China).
2.2. Fabrication of composite blends
The preparation procedure of composite powders is displayed in (a). Briefly, 2.7 g of TPU powders, 6.3 g of PLLA powders and 1 g of Fe3O4 powders were added in 200 ml of ethanol. Then, the ethanol suspension was scattered for 30 min by ultrasonic dispersion. After filtering for 15 min, the precipitate was dried by a drying oven for 24 h at 40°C to obtain composite powders, named T3P7F10. Specifically, the 30: 70 wt% (TPU/PLLA) composite powders containing Fe3O4 at 0, 5, 10, and 15 wt% were denoted as T3P7F0, T3P7F5, T3P7F10, and T3P7F15 powders, respectively.
Figure 1. (a) Schematic diagram of the preparation of the T3P7F0, T3P7F5, T3P7F10, and T3P7F15 powders, (b-c) schematic diagram of the preparation of the T3P7F0, T3P7F5, T3P7F10, and T3P7F15 lotus root-like blends, (d) FTIR spectra of the TPU, PLLA, T3P7F0, and T3P7F10 powders, (e) The contact angles of the TPU, PLLA, and Fe3O4 samples, (f) interfacial tension between different pairs.
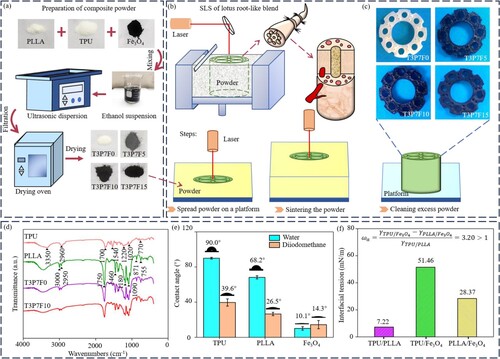
The process of fabricating composite blends is depicted in (b). Lotus root-like blends were fabricated by a self-developed SLS system with computer-control system, CO2 laser with 35-W power, and a dynamically focusing optical system, based on the 3D model of a lotus root. The fabrication process was as follows: firstly, the inner wall of the lotus root resembled the bone structure, building a porous lotus root-like model designed to be Φ15 mm × 2 mm. After each layer of powder was sintered, the platform was lowered and covered by a new layer of powder, which was then sintered. This process was repeated until the blend reached a height of 2 mm. Finally, this blend was removed from a powder bed after it had cooled down. Hereon, the optimised sintering parameters were as follows: 200 mm/s (scanning speed), 6 W (laser power), 1.2 mm (scanning spacing), 0.2 mm (powder layer thickness), 0.8 mm (spot diameter), and 80°C (preheating temperature). The blends fabricated with T3P7F0, T3P7F5, T3P7F10, and T3P7F15 powders, as shown in (c) were named as T3P7F0, T3P7F5, T3P7F10, and T3P7F15 blends, respectively.
2.3. Characterisation
The existence of particular chemical groups in the TPU, PLLA, T3P7F0, and T3P7F10 powder samples was investigated by Fourier transform infrared spectrometer (FTIR, Thermo Scientific Nicolet iS5, USA) within 400–4000 cm−1 spectral range. The contact angles of the TPU, PLLA, and Fe3O4 powder samples (10 × 10 × 2 mm3) were measured using a contact angle meter (KSV CAM 200, Finland). 2 μL distilled water or diiodomethane was dripped onto samples. Measurements of each sample were carried out ten times at different positions, and the final contact angles were the average value of the results.
The distribution state of Fe3O4 in the T3P7F0, T3P7F5, T3P7F10, and T3P7F15 blends and the co-continuity structure of the TPU phase were analysed by observing 10 mg samples of each type of blend using a polarising optical microscope (POM, batuo XP-213 V, China). To observe the co-continuity structure of the TPU phase in the T3P7F0, T3P7F5, T3P7F10 and T3P7F15 blends, the specimen (10 × 10 × 2 mm3) surfaces were etched for 6 h to remove the phase of PLLA using aqueous solution of methanol (23/17, v/v) with the addition of 1 ml of 0.05 mol/L sodium hydroxide. The unetched and etched surfaces were observed by scanning electron microscope (SEM, Phenom World BV, Netherlands) after gold sputtering. Furthermore, the distribution state of Fe3O4 in the blend was assessed utilising energy dispersive spectroscopy (EDS) coupled with SEM.
Tensile properties of dumbbell-shaped T3P7F0, T3P7F5, T3P7F10, and T3P7F15 specimens (gauge part of 5 × 5 × 10 mm3) were measured at room temperature using a universal testing machine (Zhongluchang YAW-300C, China) with a crosshead speed of 0.5 mm/min to obtain stress–strain curves, which were recorded by a test sensor during the process. The tensile strength and modulus were calculated according to the strain–stress curve to explore the ability of the blend to resist plastic deformation. To determine the final result, an average was calculated from the five measurements conducted on each sample. Similarly, compressive properties of cylindrical T3P7F0, T3P7F5, T3P7F10, and T3P7F15 specimens (Φ5 × 10 mm3) were measured at the same experimental conditions when withstanding compressive loads. The strain–stress curve was also obtained to calculate the compressive strength and modulus of the samples. Afterward, fracture surface morphologies were investigated via SEM. The hardness of the T3P7F0, T3P7F5, T3P7F10, and T3P7F15 specimens was tested via a Vickers Microindentor (Digital Micro Hardness Tester, HXD-1000TM/ LCD, China) to investigate the ability of the blend to resist external objects pressing into its surface. To obtain the average results, Vickers indentation tests were conducted on five samples (10 × 10 × 2 mm3) of each blend type, with a load of 500 g for 15 s. Thermomechanical properties of the T3P7F0, T3P7F5, T3P7F10, and T3P7F15 blends were evaluated by a dynamic mechanical analysis (DMA, Q800, China). Rectangular samples (5 × 30 × 1.5 mm3) were tested in tensile mode within −40–100°C, using a heating rate of 5°C/min and an oscillation frequency of 1 Hz.
Thermal responsive shape memory properties of the T3P7F0, T3P7F5, T3P7F10, and T3P7F15 blends were measured. The test included two stages: (1) The samples of each type of blend (5 × 30 × 1.5 mm3) were bent into a U-shape () from their initial shape (
) after being heated to 50°C in hot water for 10 min, then rapidly cooled to room temperature for 10 min, and the fixed shape (
) were recorded. (2) The samples were placed in 50°C water again to recover their initial shape, and the recovery shape (
) was recorded. Additionally, the fixing and recovering processes of each type of sample were repeated five times, and the angles of samples during cooling and heating were recorded by a camera. The shape fixity and recovery ratios (
and
) were determined via Eqs. (1) and (2), respectively.
(1)
(1)
(2)
(2)
Magnetic responsive shape memory properties of the T3P7F0, T3P7F5, T3P7F10, and T3P7F15 blends were evaluated under an alternating magnetic field produced by a Φ10 cm induction coil, rated current 5 A and a frequency of 25 kHz (inductive heating machine, Mode 1, China). The shape recovery processes of the samples (5 × 30 × 1.5 mm3) were recorded via a camera for 15 min after fixing the shape as previous described, and the synchronous temperature changes of these processes were captured by an infrared camera (FLIR One, China). The initial shape (), temporary shape (
), fixed shape (
), and recovery shape (
) were recorded. Recovering processes were performed five times for each type of sample, and the magnetic responsive shape recovery ratios (
) were calculated using the following equation (3):
(3)
(3)
2.4. Cytocompatibility
Human osteosarcoma MG-63 cells are capable of synthesising bone matrix and mineralising, making them a suitable model for studying blend cytocompatibility. We used MG-63 cells (American Type Culture Collection, USA) to assess the cytocompatibility of T3P7F10 blend (10 × 10 × 1 mm3), with T3P7F0 blend (10 × 10 × 1 mm3) serving as the control. Cells were cultured in Dulbecco’s modified Eagle’s medium (DMEM) at 37°C under a 5% CO2 atmosphere for 1, 3, and 5 d, at an initial density of 1 × 105 cells/cm2. Before seeding, specimens were cleared with ethanol, and disinfected with ultraviolet light. Three samples of each type were collected after 1, 3, and 5 d. Cell adhesion regions were observed by SEM after gold sputtering. Cell viability was assessed by exposing three samples of each type to 2 mM calcein AM and 4 mM propidium iodide for 30 min, and observing the surviving cells using fluorescence microscopy (Olympus Corporation, Japan).
2.5. Statistical analysis
Statistical significance of all data was assessed using SPSS 19.0 software (IBM Corporation, USA), presented as mean ± standard deviation. Marking *, **, and *** denote P < 0.05, P < 0.01, and P < 0.001, respectively.
3. Results and discussion
FTIR analysis was used to examine specific chemical groups of TPU, PLLA, T3P7F0, and T3P7F10 powder samples in transmittance mode within the 4000–400 cm−1 range, and the spectra were exhibited in (d). For TPU, the 3500–2800 cm−1 range corresponded to the vinyl C–H group, while the peak located at 3350 cm−1 was assigned to the stretching vibration of -NH in the urethane group. In addition, the peak located at 2960 cm−1 was due to the asymmetric vibration of the -CH2. The region of 1800-1500 cm−1 corresponded to the carbonyl band, indicating the TPU characteristics. As for PLLA, the transmittance peaks located at 3000 and 2950 cm−1 were attributed to the stretching vibration of -CH-, and the peak located at 1750 cm−1 was attributed to the stretching of -C = O- in lactide. The peak located at 1460 cm−1 belonged to the CH3, and the peaks located at 1180 and 1090 cm−1 corresponded to the C–O. The peaks located at 871 and 755 cm−1 were associated with the amorphous and crystalline phases of PLLA [Citation33]. The peaks of the T3P7F0 sample showed the characteristic functional groups of both TPU and PLLA, and the peaks of the T3P7F10 sample presented a similar profile. The results of FTIR analysis demonstrated that no chemical reaction occurred in the powder blending process because no new chemical bond was found.
The distribution state of Fe3O4 nanoparticles was investigated from a thermodynamic perspective by calculating the interfacial energies between two different samples among the TPU, PLLA, and Fe3O4 powder samples to obtain the wetting coefficient ωa, which was widely used to predict the distribution state of nanofillers in a composite. The interfacial energies between two different samples were obtained from calculated surface energies of the dispersive and polar parts based on the following geometric-mean equation (4):
(4)
(4) where
and
were the surface energies of two different samples, and
was interfacial energy between the two different samples. The superscripts ‘d’ and ‘p’ indicated the dispersive and polar components, respectively.
In order to assess the surface energies of the samples, contact angles were measured for TPU, PLLA, and Fe3O4 powder samples, with the results presented in (e). The TPU, PLLA, and Fe3O4 surface energies were calculated at room temperature via the following Eqs. (5) and (6) of the Owens-Wendt method [Citation34]:
(5)
(5)
(6)
(6) where θ was the contact angle,
and
were the surface energies of solid and liquid. Here, two test liquids, distilled water and diiodomethane, were used as polar and nonpolar liquids, respectively. Their values of surface energies were γp = 50.7 mN/m and γd = 22.1 mN/m for distilled water, and γp = 6.7 mN/m and γd = 44.1 mN/m for diiodomethane. The calculated interfacial energies were shown in (f), and the value of the wetting coefficient ωa of Fe3O4 in the TPU/PLLA was 3.2, which was greater than 1. The results indicated that the Fe3O4 nanoparticles were tended to distribute in the TPU phase from the thermodynamic point of view [Citation10,Citation35].
It is widely recognised that the micromorphology of the phase has a significant impact on the mechanical and shape memory properties. POM was used to observe the phase micromorphologies of the T3P7F0, T3P7F5, T3P7F10, and T3P7F15 specimens, and the POM photographs were shown in (a-d). The TPU/PLLA blend without Fe3O4 revealed a sea-island-like structure, as shown in (a). Furthermore, several micrometers of the sea-island-like TPU phase were uniformly dispersed in the PLLA phase. As previously predicted from a thermodynamic perspective, Fe3O4 nanoparticles were selectively distributed in the TPU phase, so the dispersed TPU phase turned black, and the TPU phase stuck together to some extent when 5 wt% Fe3O4 nanoparticles were added, as shown in (b). As the Fe3O4 nanoparticles content reached 10 wt%, most of the TPU phase sticked together and formed co-continuous structure, as shown in (c). Observations revealed that when the Fe3O4 nanoparticle content was increased to 15 wt%, agglomerates of Fe3O4 were formed as a result of the magnetic attractive forces and high surface energy of the nanoparticles [Citation36,Citation37], which distributed in the TPU phase and even migrated to the PLLA phase, as shown in (d). SEM was used to analyse the formation of co-continuous structure, and the surface micrographs of the T3P7F0, T3P7F5, T3P7F10, and T3P7F15 specimens were displayed in (e-h). The spherical TPU droplets were embedded in the PLLA phase as displayed in (e). The dispersity of the TPU phase improved with the increase of Fe3O4 nanoparticle content. When Fe3O4 nanoparticles reached more than 10 wt%, the TPU phase was evenly dispersed in the PLLA phase and formed the co-continuous structure, as shown in (g-h).
Figure 2. (a-d) POM images, (e-h) SEM images of the unetched, (i-l) SEM images etched surfaces and corresponding element scan of the T3P7F0, T3P7F5, T3P7F10, and T3P7F15 blends.
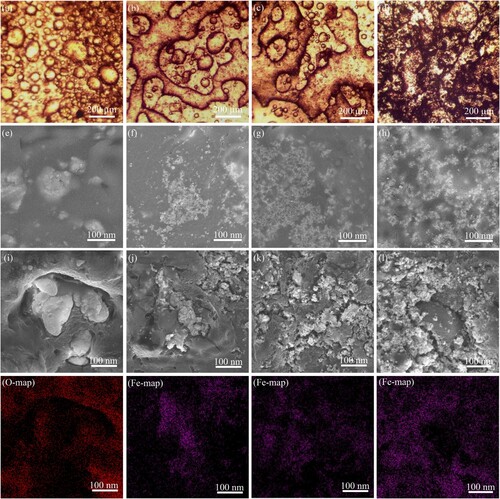
To further analyse the translation of the TPU phase micromorphology to co-continuous structure, the PLLA phase in the blend was etched while the TPU has remained, and the etched surface micrographs are shown in (i-l). The TPU phase was embedded in the PLLA phase in the form of a sea-island-like structure, and a distinct gap was observed between the TPU phase and the PLLA phase, attributed to the weak interfacial interaction, as shown in (i) [Citation38,Citation39]. The TPU phase partially interlinked into larger clusters with the addition of 5 wt% Fe3O4 nanoparticles, as shown in (j). Then, almost all the adjacent TPU phase was interlinked to form a complete co-continuous structure when Fe3O4 nanoparticle content reached 10 wt%, as displayed in (k). However, exposed Fe3O4 nanoparticle agglomerates embedded in the TPU phase were observed, and the co-continuous structure was destroyed when Fe3O4 nanoparticle content reached 15 wt%, as shown in (l). The corresponding EDS maps of O and Fe elements were obtained, and the results demonstrated that Fe element was selectively distributed in the blends, which were consistent with previous POM and SEM results. The reasons for the formation of co-continuous structure of TPU in the blend were as follows: On the one hand, the interfacial tension and flow behaviour changed upon the addition of nanoparticles, such as Fe3O4 nanoparticles, carbon nanotubes, and so on [Citation40,Citation41]. This could reduce the shape relaxation and break-up processes of the TPU phase, making itself stabilised by the kinetic trapping of the PLLA phase [Citation42]. On the other hand, Fe3O4 nanoparticles with self-networking capability that are distributed in the TPU phase could expand the composition range of co-continuity and induce the dispersed TPU phase to stretch and interlink, forming co-continuous structures [Citation43,Citation44]. However, excessive Fe3O4 nanoparticles destroyed the complete co-continuous structure.
The tensile test is an effective method to describe the deformation and fracture process [Citation45]. Tensile properties of the T3P7F0, T3P7F5, T3P7F10, and T3P7F15 blends were evaluated, and the results are shown in (a). Based on the strain–stress curve in (b), the tensile strength and modulus were measured and exhibited in (c). The tensile strength of the blend without Fe3O4 nanoparticles was 8.43 MPa, and then increased from 8.75 MPa to 9.24 MPa with adding Fe3O4 from 5 to 10 wt%, finally dropping to 8.03 MPa when Fe3O4 content reached 15 wt%. The trend of the tensile modulus was consistent with the tensile strength. Specifically, the tensile modulus increased from the initial 252.58 MPa to 260.13 MPa at 5 wt% Fe3O4 nanoparticles, then to 293.52 MPa when Fe3O4 content reached 10 wt%, and finally decreased to 241.53 MPa with the addition of 15 wt% Fe3O4 nanoparticles. The results indicated a notable enhancement in the tensile properties upon the incorporation of Fe3O4 nanoparticles. For instance, the tensile modulus of the T3P7F10 blend was 1.16 times higher than that of the T3P7F0 blend. However, the aggregation of excessive Fe3O4 nanoparticles reduced the tensile properties of the T3P7F15 blend because of the incomplete co-continuous structure. The compressive test results were similar to the tensile test results, as shown in (d-f). In (f), the compressive strength of the specimens first increased from 9.65 MPa to 11.25 MPa with the Fe3O4 content increasing from 0 to 10 wt%, and then decreased to 8.85 MPa when the Fe3O4 content reached 15 wt %. At the same time, the compressive modulus also changed with the Fe3O4 content from 0 to 10 and then to 15 wt%, from 57.48 MPa to 64.61 MPa and then to 47.61 MPa. Thus adding 10 wt% Fe3O4 also enhanced the compressive properties of the blend. Vickers indentation tests were used to measure the hardness of the T3P7F0, T3P7F5, T3P7F10, and T3P7F15 blends, and the results were exhibited in (g-i). The results show the hardness of blends enhanced from 4.41 Hv to 5.75 Hv with adding Fe3O4 from 0 to 10 wt%, and then sharply dropped to 3.65 Hv at 15 wt% of Fe3O4 nanoparticles for the same reason as before. It was important that the enhanced hardness restricted the plastic deformation of the blends, which could improve the shape fixity ratio [Citation46-48].
Figure 3. (a) Representative sample under tensile test and the T3P7F0, T3P7F5, T3P7F10, and T3P7F15 specimens after tensile test, (b) tensile stress-strain curves, (c) tensile strength and tensile modulus, (d) representative sample under compressive test, (e) compressive stress-strain curves, (f) compressive strength and compressive modulus, (g) indentation on the surfaces, (h) Vickers hardness test and (i) Vickers hardness of the T3P7F0, T3P7F5, T3P7F10, and T3P7F15 specimens.
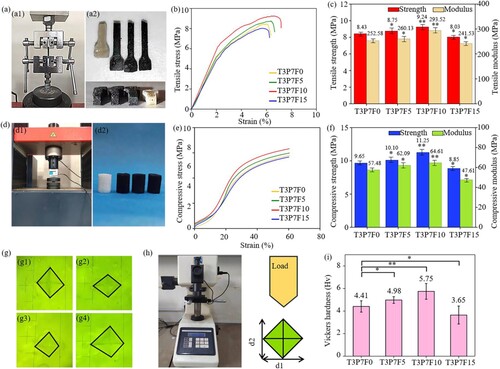
SEM was used to investigate the mechanical properties enhancement mechanisms with the addition of Fe3O4 nanoparticles, and the fracture surface morphologies corresponding to the blends broken in the previous tensile tests were shown in (c-d). The pull-out phenomenon of the TPU phase was observed on the fracture surface of the blends containing 5 and 10 wt% Fe3O4 nanoparticles. However, the phenomenon was lost when the Fe3O4 nanoparticles reached 15 wt%, and the Fe3O4 aggregates could be clearly observed embedded in the blend. According to the previous (d) and (l), as the content of Fe3O4 increased to 15 wt%, a large number of Fe3O4 aggregation appeared in the TPU phase of the blend. In (d), it could be clearly seen that the aggregation of Fe3O4 nanoparticles was distributed in the fracture surface of the TPU phase, which might be because the integrity of the co-continuous structure of the TPU phase at the fracture surface was damaged, and the cracks were easy to spread along the place of Fe3O4 aggregation, resulting in the removal of the pull-out phenomenon [Citation10]. The diagrams of mechanical properties enhancement mechanisms that revealed the reasons for the above experimental results are shown in (e-g). The formation of the co-continuous structure reflects the improved compatibility between the PLLA and TPU phases, thus facilitating stress transfer from the rigid PLLA to the ductile TPU phase. Meanwhile, the co-continuous structure of the TPU phase could be used as the propagation path of plastic deformation, and the stretch of co-continuous structure increased energy loss compared with the sea-island-like structure. Besides, Fe3O4 nanoparticles were selectively distributed in the TPU phase and prevented cracks from propagating in the phase. As a result, the crack propagation in the enhanced co-continuous structure consumed more energy. The ability to resist plastic deformation of the blends decreased because of the incomplete co-continuous structure with excessive Fe3O4 nanoparticles [Citation49-55].
Figure 4. (a-d) SEM images and corresponding partially enlarged images of fracture surfaces of the T3P7F0, T3P7F5, T3P7F10, and T3P7F15 specimens, (e-g) toughening mechanisms for the co-continuous structure and Fe3O4 nanoparticles.
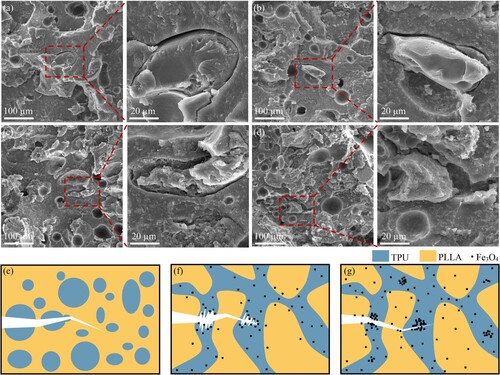
The storage modulus (E′) and loss factor (tan δ) of the T3P7F0, T3P7F5, T3P7F10, and T3P7F15 blends were measured via DMA, which played a key role in evaluating the shape memory behaviours [Citation56]. The E′ and tan δ of the blends with the temperature changes were presented in (a-b). The E′ curves demonstrated that the blends possessed variable stiffness with temperature in (a). With the temperature rising from −30 to 90°C, all E′ values declined, which meant that all the blends could be softened and hardened within this range of temperature, implying the blends had excellent shape fixity abilities due to their higher storage modulus at lower temperatures [Citation57]. The value of E’ decreased sharply at around 80°C close to the glass transition temperature (Tg) of PLLA, which originated from the movement of the amorphous PLLA chains [Citation58,Citation59]. Moreover, the E′ value of the T3P7F15 blend was relatively small at low temperatures due to the poor mechanical properties caused by excessive Fe3O4 nanoparticles. The temperature corresponding to the peak of tan δ was defined as the Tg [Citation60]. All the blends had 2 Tgs, as exhibited in (b), one for TPU at −5-5°C, and the other for PLLA at 80–90°C, implying that TPU and PLLA were immiscible in the blends [Citation61,Citation62]. Moreover, the decrease in the tan δ peak indicated that the addition of Fe3O4 nanoparticles pulled down the damping behaviour and enhanced the blends elasticity [Citation63-65].
Figure 5. (a) Storage modulus (E′) and (b) loss factor (tan δ), (c) digital photographs and (d) angles of the shape fixity and recovery processes choosing 50°C as the switch temperature, (e) shape fixity ratio (Rf) and shape recovery ratio (Rr) of the T3P7F0, T3P7F5, T3P7F10, and T3P7F15 specimens.
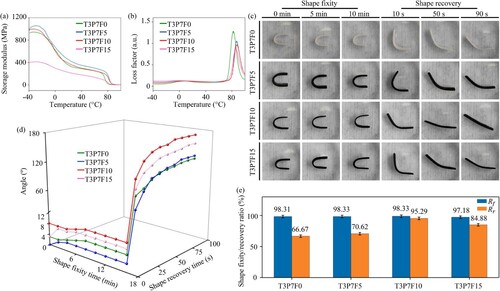
Generally, 80°C, the Tg of PLLA, is set at the transition temperature (Ttrans) of the PLLA matrix composites because of such a large decrease of E′ value [Citation10]. However, research has indicated that peri-implant tissues may experience significant and irreversible thermal damage, which can adversely impact bone integration when exposed to high temperatures (>55°C) [Citation66]. Therefore, it is necessary to consider choosing a switching temperature below 55°C. Below the Ttrans, the TPU/PLLA composite blends possess a certain shape fixity and recovering ability, which is given by the reversible plasticity shape memory effect (RP-SME), because the TPU phase in the blend has been in a highly elastic state, and the PLLA phase is in a glass state but part of its molecular chain will also be softened. The difference between the RP-SME and the conventional SME is that the switching temperature of the conventional SME is higher than Ttrans, and the blend is completely in a highly elastic state, while the RP-SME can occur when the switching temperature is lower than Ttrans, at which temperature the molecular chain is partially softened, and the blend is not entirely in a highly elastic state. Although the shape recovery ratios of the TPU/PLLA composite blends will not reach 100% due to the glassy PLLA, the RP-SME have a higher recovery force since more energy is stored during the shape fixing process, and greater deformability when the blends deform at just below the Ttrans [Citation67,Citation68]. As a result, 50°C was chosen as the switching temperature to assess the thermal responsive shape memory properties of the blends in water. This temperature, below 55°C, did not adversely affect bone integration, and the TPU/PLLA composite blends could exhibit shape fixity and recovering ability at 50°C because of the RP-SME.
In the TPU/PLLA blend, highly elastic TPU acted as the switching phase because of the amorphous nature and PLLA acted as the fixing phase. Therefore, the photographs of the shape-fixing and recovering processes of the T3P7F0, T3P7F5, T3P7F10 and T3P7F15 blends were presented in (c). All the blends possessed excellent shape fixity and recovery rapidly in the first 10 s. When the shape of the blend was changed at 50 °C, the PLLA molecular chain was softened and had the ability to deform to a certain extent, and meanwhile, the elastic TPU ensured that the PLLA would not fail in the deformation process. During the shape-fixing process at room temperature, the molecular chain of glassy PLLA as a fixed phase was easily cooled, leading to the loss of deformation ability of PLLA, so the shape-fixed force provided by PLLA was much greater than the elastic force provided by the TPU phase, so the shape fixing ability of the blend was good. During the shape recovery process at 50 °C, the molecular chain of the fixing phase PLLA softened again. Consequently, the shape-fixing force provided by PLLA became less than the elastic force provided by the switching phase TPU. At the same time, the deformed TPU phase released its stored energy to drive the softened PLLA back to its initial shape, resulting in the shape recovery of the blend [Citation10,Citation67,Citation68].
The angles corresponding to the T3P7F0, T3P7F5, T3P7F10, and T3P7F15 blends were measured in the shape fixing and recovering processes, and the results are shown in (d). The angles in the shape-fixing processes hardly changed and recovered to their permanent shape completely within 100 s in the recovering processes. The shape fixity and recovery ratios were calculated by these angles, and the results were exhibited in (e). All the shape fixity ratios could reach above 90%, which might be attributed to the rigid PLLA phase restricting most of the elastic retraction of the elongated TPU phase during the fixing processes at room temperature. The shape recovery ratios of the blends increased from 66.67% to 70.62% with the addition of Fe3O4 from 0 to 5 wt%, then reached 95.29% at 10 wt% Fe3O4 nanoparticles, and finally declined to 84.88% at 15 wt% Fe3O4 nanoparticles. In fact, the co-continuous structure of the elastomeric TPU phase could provide a strong elastic restoring force and enhance the efficiency of stress transfer, compared with the dispersed sea-island structure. However, the incomplete co-continuous structure caused by excessive Fe3O4 nanoparticles might weaken the delivery of elastic restoring force [Citation69-71]. In general, the T3P7F10 blend had distinguished thermal responsive shape memory properties because of the integrity of the co-continuous structure and higher mechanical properties of the TPU phase.
Magnetic field, one of the most promising stimulation methods for transplanted SMP, can achieve non-contacting stimulation. Furthermore, under the influence of an external alternating magnetic field, the ferromagnetic Fe3O4 nanoparticles periodically move, and the shape-fixed blends can respond to the heat generated by relative friction and particle collisions, thus recovering the shape [Citation72,Citation73]. Therefore, to assess the effects of Fe3O4 nanoparticles on magnetic responsive shape memory properties, T3P7F0, T3P7F5, T3P7F10, and T3P7F15 blends were placed under an alternating magnetic field produced by a Φ10 cm induction coil with a rated current 5 A and a frequency of 25 kHz to trigger shape recovery behaviour after fixing their shape. The photographs of instantaneous shape and corresponding thermal images of the blends are displayed in (a). Obviously, with the increase in Fe3O4 content, both the heating speed and temperature rapidly increased after 15 min. The shape recovery effect of the T3P7F10 blend was distinct, and the shape changed dramatically at around 50°C.
Figure 6. (a) Digital photographs and corresponding thermal images, (b) temperature changes, and (c) shape recovery ratios of the T3P7F0, T3P7F5, T3P7F10, and T3P7F15 specimens in the alternating magnetic field, (d) illustration of the magnetic responsive shape memory mechanism.
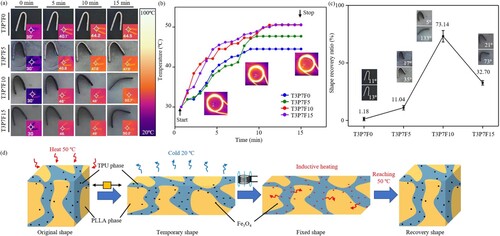
To quantitatively analyse the temperatures and heating rates during shape-recovering processes, the temperatures of the blends were recorded and shown in (b). Heating rates of the blends increased with the addition of Fe3O4 from 0 to 15 wt%. What’s more, the final temperatures of the blends rose from 44.5 to 47.9°C with the addition of 5 wt% Fe3O4 nanoparticles and then stabilised at around 50°C with 10 and 15 wt% Fe3O4 nanoparticles. The reason was that Fe3O4 nanoparticles had a high thermal conductivity in the blends, and the high content of Fe3O4 nanoparticles heightened the magnetocaloric effect [Citation74,Citation75]. Although without Fe3O4 nanoparticles, the T3P7F0 blend experienced an increase in temperature because heat was transferred slowly from the environment to the interior of the blend. The magnetic responsive shape recovery ratios were calculated and shown in (c). The shape of the T3P7F0 blend almost did not recover because it didn’t contain Fe3O4 nanoparticles to generate heat. However, the addition of too few Fe3O4 nanoparticles in the blends such as the T3P7F5 blend also could not achieve a good shape recovery due to the insufficient temperature. The blend containing 10 wt% Fe3O4 nanoparticles possessed a shape recovery ratio of 73.14%, which was higher than that of the T3P7F15 blend because the integrity of the co-continuous structure and higher mechanical properties improved the shape memory properties at the approximate temperature.
The magnetic responsive shape memory mechanism based on the selective distribution of Fe3O4 nanoparticles and the co-continuous structure of the TPU phase was revealed in (d). The TPU phase was always in a high elastic state at room temperature or above [Citation72]. With the PLLA phase heated to 50°C, the blends could be deformed to a temporary shape from the original shape easily because the amorphous soft segments in the blends were able to undergo a certain amount of elastic deformation. Then, the PLLA phase was hard and brittle after being cooled to room temperature, which resulted in the fixed force of the PLLA phase being stronger than the resilience force of the TPU phase to achieve shape fixity. Finally, when the blends with sufficient content of Fe3O4 nanoparticles such as the T3P7F10 blend could be reheated to 50°C by the alternating magnetic field, the PLLA phase could release its high internal strain stored energy by the heat from Fe3O4 nanoparticles in the TPU phase to recover the original shape as far as possible. Furthermore, the co-continuous TPU phase was promoted and enhanced by the selectively distributed Fe3O4 nanoparticles, which could provide a stronger resilient force to pull back to the original shape. As a contrast, the T3P7F15 blend exhibited an incomplete co-continuous structure and poor mechanical properties, which led to the disadvantage of shape recovery [Citation76]. To sum up, the T3P7F10 blend had relatively superior magnetic responsive shape memory properties. Notably, the shape recovery ratio of the T3P7F10 blend in alternating magnetic field was lower than the ratio of the blend in water, because the heat was generated by the internal Fe3O4 nanoparticles and not directly provided by the external. By the way, the T3P7F10 blend was unable to fully achieve shape recovery under conditions when the switch temperature was below the Ttrans of the blend, which needed to sequentially research to exploit its potential.
The T3P7F10 blend was selected for assessing the cytocompatibility in comparison with the T3P7F0 blend due to its superior mechanical and shape memory properties. (a) showed morphologies of MG-63 cells after being cultured on these two blends for 1, 3, and 5 d. Initially, the cells tightly adhered to the blends, gradually spreading and becoming polygonal as culture time increased. After 3 d, cells spread with filopodia, and by 5 d, the blend surface was mostly covered by cells, indicating the blends’ favourable effect on cell adhesion and spreading. The adhesion area measured in (c) illustrated that the T3P7F10 blend promoted cell adhesion to a greater extent than the T3P7F0 blend due to the presence of magnetic nanoparticles. The viability of MG-63 cells was investigated via observing live cells via a fluorescent microscope after incubation for 1, 3, and 5 d in (b). With the culture time increasing, the number of cells on the blends increased. (d) shows the cell density after 1, 3, and 5 d of culture in fluorescence images. The results showed that both blends had good cytocompatibility, which was consistent with the results of other related studies because a large number of vivo animal experiments results have proved the effectiveness of TPU and PLLA in bone tissue engineering applications [Citation77-79]. More importantly, cell attachment, spreading, and proliferation on the T3P7F10 blend were significantly better than on the T3P7F0 blend, demonstrating that Fe3O4 nanoparticles enhanced the capabilities of cells [Citation80-82]. On the one hand, nanoscale magnetic fields produced by Fe3O4 nanoparticles could attract cells to approach and activate certain various signalling pathways, which was beneficial for cell adhesion, spreading, and proliferation [Citation83,Citation84]. On the other hand, Fe3O4 nanoparticles were able to increase the roughness of the blend, which facilitated cell adhesion and spreading [Citation85].
Figure 7. (a) SEM images of MG-63 cells adhered and (b) fluorescence images of live cells and dead cells on the T3P7F0 and T3P7F10 blends after culture for 1, 3, and 5 d, (c) quantification analysis of cell area and (d) cell density of MG-63 cells adhered on the T3P7F0 and T3P7F10 blends after culture for 1, 3, and 5 d.
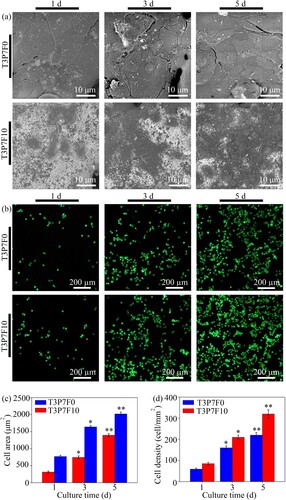
4. Conclusions
In this study, a magnetic-responsive shape memory composite blend was successfully fabricated by SLS, which possessed enhanced mechanical and shape memory properties via promoting the formation of the TPU phase co-continuous structure using the selective distribution of Fe3O4 nanoparticles in TPU. The selective distribution of 10 wt% Fe3O4 and the co-continuous structure of the elastomeric TPU phase enhanced the tensile strength and hardness of the blend with 10 wt% Fe3O4 nanoparticles from 8.43 to 9.24 MPa and 4.41–5.75 Hv compared with the blend without Fe3O4 nanoparticles, respectively. Besides, the shape memory properties of the blend with 10 wt% Fe3O4 nanoparticles in 50°C water were excellent with Rf of 98.33% and Rr increased by 43.93% compared with the blend without Fe3O4 nanoparticles. Furthermore, the introduction of Fe3O4 nanoparticles endowed the PLLA/TPU blend fabricated via 3D printing with a magnetic responsive shape memory ability in an alternating magnetic field, which breaked through the limitations of traditional 3D printing of static microstructures, and dynamically no-contact controlled the shape according to the need. Under the alternating magnetic field, the blend with 10 wt% Fe3O4 nanoparticles could recover its shape with the Rr of 73.14%. In addition, the blend possessed better biocompatibility for cells proliferation, adhesion, and spreading.
Disclosure statement
No potential conflict of interest was reported by the authors.
Additional information
Funding
References
- Chen A, Su J, Li Y, et al. 3D/4D printed bio-piezoelectric smart scaffolds for next-generation bone tissue engineering. Int J Extreme Manuf. 2023;5:032007. doi:10.1088/2631-7990/acd88f
- Oladapo BI, Zahedi SA, Ismail SO, et al. 3D printing of PEEK–cHAp scaffold for medical bone implant. Bio-des Manuf. 2021;4:44–59. doi:10.1007/s42242-020-00098-0
- Deng Y, Zhang F, Jiang M, et al. Programmable 4D printing of photoactive shape memory composite structures. Acs Appl Mater Inter. 2022;14:42568–42577. doi:10.1021/acsami.2c13982
- Gardan J. Smart materials in additive manufacturing: state of the art and trends. Virtual Phys Prototy. 2019;14:1–18. doi:10.1080/17452759.2018.1518016
- Chen A, Wang W, Mao Z. Multi-material 3D and 4D bioprinting of heterogeneous constructs for tissue engineering. Adv Mater. 2023;35:2307686.
- Nazir F, Iqbal M, Khan AN, et al. Fabrication of robust poly l-lactic acid/cyclic olefinic copolymer (PLLA/COC) blends: study of physical properties, structure, and cytocompatibility for bone tissue engineering. J Mater Res Technol. 2021;13:1732–1751. doi:10.1016/j.jmrt.2021.05.073
- Arabiyat AS, Pfau MR, Melissa GA, et al. Intrinsic osteoinductivity of PCL-DA/PLLA semi-IPN shape memory polymer scaffolds. J Biomed Mater Res A. 2021;109:2334–2345. doi:10.1002/jbm.a.37216
- Ji X, Gao F, Geng Z. Tunable shape memory of thermoplastic polyurethane/poly (lactic acid) blends via morphology control: performance and mechanism. Mater Express. 2021;11:220–227.
- Yang W, Weng Y, Puglia D, et al. Poly(lactic acid)/lignin films with enhanced toughness and anti-oxidation performance for active food packaging. Int J Biol Macromol. 2020;144:102–110. doi:10.1016/j.ijbiomac.2019.12.085
- Huang J, Cao L, Yuan D, et al. Design of multi-stimuli-responsive shape memory biobased PLA/ENR/Fe3O4 TPVs with balanced stiffness–toughness based on selective distribution of Fe3O4. Acs Sustain Chem Eng. 2019;7:2304–2315. doi:10.1021/acssuschemeng.8b05025
- Kabir S, Kim H, Lee S. Physical property of 3D-printed sinusoidal pattern using shape memory TPU filament. Text Res J. 2020;90:2399–2410. doi:10.1177/0040517520919750
- Nugroho WT, Dong Y, Pramanik A, et al. Smart polyurethane composites for 3D or 4D printing: general-purpose use, sustainability and shape memory effect. Compos Part B-Eng. 2021;223:109104. doi:10.1016/j.compositesb.2021.109104
- Guo Y, Yan L, Zeng Z, et al. TPU/PLA nanocomposites with improved mechanical and shape memory properties fabricated via phase morphology control and incorporation of multi-walled carbon nanotubes nanofillers. Polym Eng Sci. 2020;60:1118–1128. doi:10.1002/pen.25365
- Azadi F, Jafari SH, Khonakdar HA, et al. Influence of graphene oxide on thermally induced shape memory behavior of PLA/TPU blends: correlation with morphology, creep behavior, crystallinity, and dynamic mechanical properties. Macromol Mater Eng. 2021;306:2000576. doi:10.1002/mame.202000576
- Dong K, Panahi-Sarmad M, Cui Z, et al. Electro-induced shape memory effect of 4D printed auxetic composite using PLA/TPU/CNT filament embedded synergistically with continuous carbon fiber: A theoretical & experimental analysis. Compos Part B-Eng. 2021;220:108994. doi:10.1016/j.compositesb.2021.108994
- Lin W, Qu J. Enhancing impact toughness of renewable poly(lactic acid)/thermoplastic polyurethane blends via constructing cocontinuous-like phase morphology assisted by ethylene–methyl acrylate–glycidyl methacrylate copolymer. Ind Eng Chem Res. 2019;58:10894–10907. doi:10.1021/acs.iecr.9b01644
- Wang M, Liang X, Wu H, et al. Super toughed poly (lactic acid)/poly (ethylene vinyl acetate) blends compatibilized by ethylene-methyl acrylate-glycidyl methacrylate copolymer. Polym Degrad Stabil. 2021;193:109705. doi:10.1016/j.polymdegradstab.2021.109705
- Zhang H, Heng Z, Zhou J, et al. In-situ co-continuous conductive network induced by carbon nanotubes in epoxy composites with enhanced electromagnetic interference shielding performance. Chem Eng J. 2020;398:125559. doi:10.1016/j.cej.2020.125559
- Luo Y, Xiong S, Zhang F, et al. Preparation of conductive polylactic acid/high density polyethylene/carbon black composites with low percolation threshold by locating the carbon black at the interface of co-continuous blends. J Appl Polym Sci. 2021;138:50291. doi:10.1002/app.50291
- Zheng L, Zhong Y, He T, et al. A codispersed nanosystem of silver-anchored MoS2 enhances antibacterial and antitumor properties of selective laser sintered scaffolds. Int J Bioprinting. 2022;8:577. doi:10.18063/ijb.v8i3.577
- Liang H, Wang Y, Chen S, et al. Nano-hydroxyapatite bone scaffolds with different porous structures processed by digital light processing 3D printing. Int J Bioprinting. 2021;8:502. doi:10.18063/ijb.v8i1.502
- Dong Z, Gong J, Zhang H, et al. Preparation and characterization of 3D printed porous 45S5 bioglass bioceramic for bone tissue engineering application. Int J Bioprinting. 2022;8:613. doi:10.18063/ijb.v8i4.613
- Dee P, Tan S, Le Ferrand H. Fabrication of microstructured calcium phosphate ceramics scaffolds by material extrusion-based 3D printing approach. Int J Bioprinting. 2022;8:551. doi:10.18063/ijb.v8i2.551
- Pan P, Zhang T, Yu B, et al. A facile construction of bifunctional core-shell magnetic fluorescent Fe3O4@ YVO4: Eu3+ microspheres for latent fingerprint detection. J Colloid Interf Sci. 2022;605:425–431. doi:10.1016/j.jcis.2021.07.074
- Qi F, Liao R, Wu P, et al. An electrical microenvironment constructed based on electromagnetic induction stimulates neural differentiation. Mater Chem Front. 2023;7:1671–1683. doi:10.1039/D2QM01193J
- Zhang H, Zhang Y, Hou Z, et al. Magnetic skyrmions: materials, manipulation, detection, and applications in spintronic devices. Mater Futures. 2023;2:032201. doi:10.1088/2752-5724/ace1df
- Wang Q, Ma Z, Wang Y, et al. Fabrication and characterization of 3D printed biocomposite scaffolds based on PCL and zirconia nanoparticles. Bio-des Manuf. 2021;4:60–71. doi:10.1007/s42242-020-00095-3
- Gao C, Yao X, Deng Y. Laser-beam powder bed fusion followed by annealing with stress: a promising route for magneto strictive improvement of polycrystalline Fe81Ga19 alloys. Addit Manuf. 2023;68:103516.
- Qi F, Wang Z, Yang L, et al. A collaborative CeO2@ metal-organic framework nano system to endow scaffolds with photodynamic antibacterial effect. Mater Today Chem. 2023;27:101336. doi:10.1016/j.mtchem.2022.101336
- Ling C, Li Q, Zhang Z, et al. Influence of heat treatment on microstructure, mechanical and corrosion behavior of WE43 alloy fabricated by laser-beam powder bed fusion. Int J Extreme Manuf. 2024;6:015001. doi:10.1088/2631-7990/acfad5
- Shuai C, Shi X, Yang F, et al. Oxygen vacancy boosting fenton reaction in bone scaffold towards fighting bacterial infection. Int J Extreme Manuf. 2024;6:015101. doi:10.1088/2631-7990/ad01fd
- Niu P, Li R, Fan Z. Inhibiting cracking and improving strength for additive manufactured AlxCoCrFeNi high entropy alloy via changing crystal structure from BCC-to-FCC. Addit Manuf. 2023;71:103584.
- Fallahiarezoudar E, Ahmadipourroudposht M, Idris A, et al. Optimization and development of Maghemite (γ-Fe2O3) filled poly-L-lactic acid (PLLA)/thermoplastic polyurethane (TPU) electrospun nanofibers using Taguchi orthogonal array for tissue engineering heart valve. Mat Sci Eng C-Mater. 2017;76:616–627. doi:10.1016/j.msec.2017.03.120
- Zhang Z, Wang W, Korpacz AN, et al. Binary liquid mixture contact-angle measurements for precise estimation of surface free energy. Langmuir. 2019;35:12317–12325. doi:10.1021/acs.langmuir.9b01252
- Xiu H, Bai H, Huang C, et al. Selective localization of titanium dioxide nanoparticles at the interface and its effect on the impact toughness of poly (L-lactide)/poly (ether) urethane blends. Express Polym Lett. 2013;7:261–271. doi:10.3144/expresspolymlett.2013.24
- Fan D, Wang Q, Zhu T, et al. Recent advances of magnetic nanomaterials in bone tissue repair. Front Chem. 2020;8:745. doi:10.3389/fchem.2020.00745
- Chen Y, Zhao X, Li Y, et al. Light-and magnetic-responsive synergy controlled reconfiguration of polymer nanocomposites with shape memory assisted self-healing performance for soft robotics. J Mater Chem C. 2021;9:5515–5527. doi:10.1039/D1TC00468A
- Huang Y, Ellingford C, Bowen C, et al. Tailoring the electrical and thermal conductivity of multicomponent and multi-phase polymer composites. Int Mater Rev. 2020;65:129–163. doi:10.1080/09506608.2019.1582180
- Yang J, Yang W, Wang X, et al. Synergistically toughening polyoxymethylene by methyl methacrylate–butadiene–styrene copolymer and thermoplastic polyurethane. Macromol Chem Phys. 2019;220:1800567. doi:10.1002/macp.201800567
- Salehiyan R, Ray SS. Tuning the conductivity of nanocomposites through nanoparticle migration and interface crossing in immiscible polymer blends: a review on fundamental understanding. Macromol Mater Eng. 2019;304:1800431. doi:10.1002/mame.201800431
- Zhu X, Kong M, Lv Y, et al. Selective distribution of nanoparticles in immiscible blends: effects on the morphology evolution and rheology in quiescent annealing, shear and extensional flow. J Rheol. 2020;64:1357–1371. doi:10.1122/8.0000069
- Yoshida S, Trifkovic M. Unraveling the effect of 3d particle localization on coarsening dynamics and rheological properties in cocontinuous polymer blend nanocomposites. Macromolecules. 2019;52:7678–7687. doi:10.1021/acs.macromol.9b01437
- Sharika T, Abraham J, George SC, et al. Excellent electromagnetic shield derived from MWCNT reinforced NR/PP blend nanocomposites with tailored microstructural properties. Compos Part B-Eng. 2019;173:106798. doi:10.1016/j.compositesb.2019.05.009
- Xu C, Cui R, Chen Y, et al. Shape memory effect of dynamically vulcanized ethylene-propylene diene rubber/polypropylene blends realized by in-situ compatibilization of sodium methacrylate. Compos Part B-Eng. 2019;179:107532. doi:10.1016/j.compositesb.2019.107532
- Zhang H, Kang B, Chen L, et al. Enhancing toughness of poly (lactic acid)/thermoplastic polyurethane blends via increasing interface compatibility by polyurethane elastomer prepolymer and its toughening mechanism. Polym Test. 2020;87:106521. doi:10.1016/j.polymertesting.2020.106521
- Amurin LG, Felisberto MD, Ferreira FLQ, et al. Multifunctionality in ultra high molecular weight polyethylene nanocomposites with reduced graphene oxide: hardness, impact and tribological properties. Polymer. 2022;240:124475. doi:10.1016/j.polymer.2021.124475
- Arora G, Pathak H. Nanoindentation characterization of polymer nanocomposites for elastic and viscoelastic properties: experimental and mathematical approach. Compos Part C. 2021;4:100103.
- Tarodiya R, Levy A. Erosion of polymers and polymer composites surfaces by particles. Adv Powder Technol. 2021;32:3149–3159. doi:10.1016/j.apt.2021.07.005
- Liu L, Wu H, Wang Y, et al. Selective distribution, reinforcement, and toughening roles of MWCNTs in immiscible polypropylene/ethylene-co-vinyl acetate blends. J Polym Sci Pol Phys. 2010;48:1882–1892. doi:10.1002/polb.22063
- Xiang F, Wu J, Liu L, et al. Largely enhanced ductility of immiscible high density polyethylene/polyamide 6 blends via nano-bridge effect of functionalized multiwalled carbon nanotubes. Polym Advan Technol. 2011;22:2533–2542. doi:10.1002/pat.1796
- Xiang F, Wang Y, Shi Y, et al. Morphology and mechanical property changes in compatibilized high density polyethylene/polyamide 6 nanocomposites induced by carbon nanotubes. Polym Int. 2012;61:1334–1343. doi:10.1002/pi.4213
- Liu Y, Cao L, Yuan D, et al. Design of super-tough co-continuous PLA/NR/SiO2 TPVs with balanced stiffness-toughness based on reinforced rubber and interfacial compatibilization. Compos Sci Technol. 2018;165:231–239. doi:10.1016/j.compscitech.2018.07.005
- Yang J, Qi X, Zhang N, et al. Carbon nanotubes toughened immiscible polymer blends. Compos Commun. 2018;7:51–64. doi:10.1016/j.coco.2017.12.010
- Hajibabazadeh S, Aghjeh MKR, Palahang M. Study on the fracture toughness and deformation micro-mechanisms of PP/EPDM/SiO2 ternary blend-nanocomposites. J Compos Mater. 2020;54:591–605. doi:10.1177/0021998319863475
- Zhang T, Zhou M, Guo Z, et al. Improving impact toughness of polylactide/ethylene-co-vinyl-acetate blends via adding fumed silica nanoparticles: effects of specific surface area-dependent interfacial selective distribution of silica. Chin J Polym Sci. 2021;39:1040–1049. doi:10.1007/s10118-021-2565-4
- Liu Y, Zhang W, Zhang F, et al. Microstructural design for enhanced shape memory behavior of 4D printed composites based on carbon nanotube/polylactic acid filament. Compos Sci Technol. 2019;181:107692. doi:10.1016/j.compscitech.2019.107692
- Wang W, Liao X, Guo F, et al. Facile fabrication of lightweight shape memory thermoplastic polyurethane/polylactide foams by supercritical carbon dioxide foaming. Ind Eng Chem Res. 2020;59:7611–7623. doi:10.1021/acs.iecr.0c00404
- Li Z, Li K, He H, et al. Tough and tunable shape memory PLA/PAE melt-blends actuated by temperature. Iran Polym J. 2019;28:371–378. doi:10.1007/s13726-019-00706-6
- Kuang T, Ju J, Liu T, et al. A facile structural manipulation strategy to prepare ultra-strong, super-tough, and thermally stable polylactide/nucleating agent composites. Adv Compos Hybrid Ma. 2022;5:948–959. doi:10.1007/s42114-021-00390-2
- Cristea M, Ionita D, Iftime MM. Dynamic mechanical analysis investigations of PLA-based renewable materials: how are they useful? Materials (Basel). 2020;13:5302. doi:10.3390/ma13225302
- Mehrpouya M, Vahabi H, Janbaz S, et al. 4D printing of shape memory polylactic acid (PLA). Polymer. 2021;230:124080. doi:10.1016/j.polymer.2021.124080
- Cao L, Liu C, Zou D, et al. Using cellulose nanocrystals as sustainable additive to enhance mechanical and shape memory properties of PLA/ENR thermoplastic vulcanizates. Carbohydr Polym. 2020;230:115618. doi:10.1016/j.carbpol.2019.115618
- Jamshaid F, Dilshad MR, Islam A, et al. Synthesis, characterization and desalination study of polyvinyl chloride-co-vinyl acetate/cellulose acetate membranes integrated with surface modified zeolites. Microporous Mesoporous Mat. 2020;309:110579. doi:10.1016/j.micromeso.2020.110579
- Chai J, Wang G, Zhao J, et al. Microcellular PLA/PMMA foam fabricated by CO2 foaming with outstanding shape-memory performance. J CO2 Util. 2021;49:101553. doi:10.1016/j.jcou.2021.101553
- Zhou C, Zhu P, Liu X, et al. The toughening mechanism of core-shell particles by the interface interaction and crystalline transition in polyamide 1012. Compos Part B-Eng. 2021;206:108539. doi:10.1016/j.compositesb.2020.108539
- Zhao Y, Peng X, Xu X, et al. Chitosan based photothermal scaffold fighting against bone tumor-related complications: recurrence, infection, and defects. Carbohydr Polym. 2023;300:120264. doi:10.1016/j.carbpol.2022.120264
- Song JJ, Chang HH, Naguib HE. Biocompatible shape memory polymer actuators with high force capabilities. Eur Polym J. 2015;67:186–198. doi:10.1016/j.eurpolymj.2015.03.067
- Lai S, Lan Y. Shape memory properties of melt-blended polylactic acid (PLA)/thermoplastic polyurethane (TPU) bio-based blends. J Polym Res. 2013;20:1–8.
- Qi X, Yang J, Zhang N, et al. Selective localization of carbon nanotubes and its effect on the structure and properties of polymer blends. Prog Polym Sci. 2021;123:101471. doi:10.1016/j.progpolymsci.2021.101471
- Ghosh SK, Das TK, Ganguly S, et al. Carbon nanotubes and carbon nanofibers based co-continuous thermoplastic elastomeric blend composites for efficient microwave shielding and thermal management. Compos Part A-Appl S. 2022;161:107118. doi:10.1016/j.compositesa.2022.107118
- Peng B, Yang Y, Ju T, et al. Fused filament fabrication 4D printing of a highly extensible, self-healing, shape memory elastomer based on thermoplastic polymer blends. ACS Appl Mater Interfaces. 2021;13:12777–12788. doi:10.1021/acsami.0c18618
- Du L, Xu Z, Fan C, et al. A fascinating metallo-supramolecular polymer network with thermal/magnetic/light-responsive shape-memory effects anchored by Fe3O4 nanoparticles. Macromolecules. 2018;51:705–715. doi:10.1021/acs.macromol.7b02641
- Li L, Zhao B, Wang H, et al. Nanocomposites of polyhydroxyurethane with Fe3O4 nanoparticles: synthesis, shape memory and reprocessing properties. Compos Sci Technol. 2021;215:109009. doi:10.1016/j.compscitech.2021.109009
- Xu S, Zhao B, Adeel M, et al. Shape memory and self-healing properties of polymer-grafted Fe3O4 nanocomposites implemented with supramolecular quadruple hydrogen bonds. Polymer. 2019;172:404–414. doi:10.1016/j.polymer.2019.04.020
- Xu C, Lin M, Wang X, et al. Fabrication of high-performance magnetic elastomers by using natural polymer as auxiliary dispersant of Fe3O4 nanoparticles. Compos Part A-Appl S. 2021;140:106158. doi:10.1016/j.compositesa.2020.106158
- Arash S, Akbari B, Ghaleb S, et al. Preparation of PLA-TPU-nanoclay composites and characterization of their morphological, mechanical, and shape memory properties. J Mech Behav Biomed Mater. 2023;139:105642. doi:10.1016/j.jmbbm.2022.105642
- Lai W, Feng S, Chan Y, et al. In vivo investigation into effectiveness of Fe3O4/PLLA nanofibers for bone tissue engineering applications. Polymers (Basel). 2018;10:804. doi:10.3390/polym10070804
- Shi Z, Huang G, Li Z, et al. A PLA-tPU based magnesium ion incorporated CSH/nHA bioactive porous composite scaffold for critical bone defect repair. Mater Adv. 2023;4:3583–3592. doi:10.1039/D3MA00109A
- Lin S, Li J, Dong L, et al. Periodic-mechanical-stimulus enhanced osteogenic differentiation of mesenchymal stem cells on Fe3O4/mineralized collagen coatings. ACS Biomater Sci Eng. 2019;5:6446–6453. doi:10.1021/acsbiomaterials.9b00833
- Russo T, Peluso V, Gloria A, et al. Combination design of time-dependent magnetic field and magnetic nanocomposites to guide cell behavior. Nanomaterials. 2020;10:577. doi:10.3390/nano10030577
- Huang D, Wang J, Wen B, et al. Emerging diagnostic and therapeutic technologies based on ultrasound-triggered biomaterials. Mater Futures. 2023;2:032001. doi:10.1088/2752-5724/acdf05
- Wu D, Kang L, Tian J, et al. Exosomes derived from bone mesenchymal stem cells with the stimulation of Fe3O4 nanoparticles and static magnetic field enhance wound healing through upregulated miR-21-5p. Int J Nanomed. 2020;15:7979–7993. doi:10.2147/IJN.S275650
- Huang Z, He Y, Chang X, et al. A magnetic iron oxide/polydopamine coating can improve osteogenesis of 3D-printed porous titanium scaffolds with a static magnetic field by upregulating the TGFβ-smads pathway. Adv Healthc Mater. 2020;9:2000318. doi:10.1002/adhm.202000318
- Lee S, Yan D, Zhou X, et al. Integrating cold atmospheric plasma with 3D printed bioactive nanocomposite scaffold for cartilage regeneration. Mat Sci Eng C-Mater. 2020;111:110844. doi:10.1016/j.msec.2020.110844
- Shaltooki M, Dini G, Mehdikhani M. Fabrication of chitosan-coated porous polycaprolactone/strontium-substituted bioactive glass nanocomposite scaffold for bone tissue engineering. Mat Sci Eng C-Mater. 2019;105:110138. doi:10.1016/j.msec.2019.110138