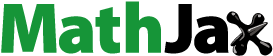
ABSTRACT
This study employed laser directed energy deposition (DED) with in-situ ultrasonic vibration to obtain AA7075 deposits. The results showed that with ultrasonic treatment, the grain morphology of DED produced AA7075 was changed from columnar grains with an average area of 1751 µm2 to equiaxed grains of 118.2 µm2, representing a reduction of about 93%. Also, the application of ultrasonic treatment led to the increase of average hardness from 93.1 HV to 110.2 HV, and the increase of average ultimate tensile strength from 226.8 MPa to 314.7 MPa, representing relative increases of 18.36% and 38%, respectively. However, it did not result in a significant reduction of ductility. It is believed that ultrasonic vibration promotes the formation of additional nucleation sites due to cavitation and acoustic streaming, as well as the formation of secondary phase particles at grain boundaries. Both mechanisms effectively augment the mechanical properties of DED produced AA7075.
1. Introduction
Additive manufacturing (AM) is an emerging manufacturing technology that is being utilised across multiple industries. The major advantages of AM include its capability to produce net-shape products with ease in one step, ultimate design freedom, and reduced waste and improved efficiency for small batch production [Citation1]. A variety of AM techniques have been invented in the last several decades, but most of them are based on the same principle, namely, layer-by-layer material deposition to form the final design geometry. In making metal components, a major AM technique is laser metal deposition or laser directed energy deposition (DED) based on metal powders, namely, the blown-powder laser DED process. In this process, metal powders are driven through a delivery system and converged at the melting pool, and at the same time a focused laser is irradiated at the convergence point to melt and fuse the powders successively [Citation2–6]. Compared with laser powder bed fusion (LPBF), which is another predominant metal AM technique, DED processes generally have higher material deposition rate and are less constrained by the build size. Also, DED is more flexible in terms of machine setup and configuration; it has lower implementation costs, a mutable energy source, less stringent requirements for environmental control, and simpler materials feeding systems for handling and recycling compared to the LPBF system [Citation7,Citation8].
Among the numerous alloys that are in use nowadays, many may not be suitable for laser AM processes. This is because melting-solidification transformations during deposition may result in intolerable microstructures of large columnar grains and periodic cracks [Citation9]. As such, extensive efforts have been made to mitigate these issues in literature. For example, addition of Nb particles to AA7075 alloy was shown to change columnar grains into ultrafine equiaxed grains [Citation10], and substrate preheating is another way of crack suppression in DED process [Citation11]. Laser AM processes are featured by small melting pools and steep temperature gradients from solid–liquid interface to the molten material. Consequently, solidification is characterised by a strong tendency for epitaxial growth from layer to layer. This leads to formation of columnar grains along the build direction and causes anisotropy, reduced mechanical properties, and increased tendency for hot tearing. As such, an important goal for metal AM is to replace coarse columnar grains with fine equiaxed grains in the material microstructure [Citation12]. Mechanical property anisotropy is an undesirable consequence of columnar microstructure as it causes difficulties in component design, build strategy and certification of products [Citation13]. For instance, previous studies have found a direct relationship between anisotropy in microstructure and anisotropy in ductility between longitudinal and transverse directions in Ti-6Al-4V produced by DED [Citation14]. Also, increases in strength and ductility are observed as the average grain size is reduced for 2219 aluminium alloy produced by wire arc additive manufacturing (WAAM) [Citation15].
High demand for lightweight yet high strength structural components makes aluminium alloys a good candidate for AM processes. However, obtaining components of aluminium alloys by laser AM could be difficult due to cracking and relatively poor mechanical properties compared to the conventional manufacturing processes. Particularly, 7000 series aluminium alloys have been considered challenging to weld and to adapt to the solidification conditions of AM methods. This is attributed to their high laser reflectivity and thermal conductivity, low viscosity, and extensive solidification range [Citation16]. Also, their microstructures consist of columnar grains and cracks that span many successive layers. When those aluminium alloys solidify, dendritic grains are generated with long channels of interdendritic regions. Cavities and hot tearing cracks form in these channels due to solidification shrinkage and thermal contraction. These cracks may span the entire length of the columnar grain. In contrast, it is easier to accommodate strain if the microstructure consists of equiaxed grains [Citation9]. Nevertheless, it is worth mentioning that limited successful AM fabrication of Al alloys was reported by the recent studies which employed an indirect arc DED for Al-Zn-Mg-Cu alloy [Citation17], or added B4C particle to AA6061 alloy matrix in laser DED process to suppress crack [Citation16]. Also, a 7000 series Al alloy was successfully deposited before using wire arc melting deposition method [Citation18].
The quaternary Al-Cu-Mg-Zn system belongs to 7000 series aluminium alloys, and it is one of the strongest commercial aluminium alloys with promising strength-to-weight ratios and whose fracture strengths above 500 MPa and low densities of about 2.8 g/cm3 [Citation19,Citation20]. AA7075 alloy is a representative alloy among the 7000 series aluminium alloys – it is an aging strengthening alloy with high content of Zn, Mg and Cu. This alloy has many advantages such as low density, high specific strength, good toughness and low cost, and therefore it is widely used in automotive, aerospace, aviation and construction industries [Citation21,Citation22]. The major disadvantage of AA7075 is the high sensitivity to hot cracking during rapid solidification and therefore poor weldability, which is a consequence of the large solidification range with low solidus temperature as well as the presence of Cu and Mg which extends the coherence range, or precipitates and increases the crack sensitivity. In addition, rapid heating and cooling cycles in AM processes often lead to inadequate precipitation of secondary phases in AM-fabricated AA7075 [Citation23].
In literature, many methods have been proposed to reduce the large dendritic structure of AA7075 such as homogenisation [Citation24] or via additives [Citation25], but most of them are for the conventionally manufactured, instead of AM produced, AA7075. In particular, the in-situ ultrasonic vibration technique in metal solidification processes has demonstrated potentials for grain refinement. In this research, it is hypothesised that laser DED process assisted by in-situ ultrasonic vibration will generate significant grain refinement effect in deposited AA7075 alloy, which in turn improves the mechanical properties of the alloy. To the best of our knowledge, such effort has not been attempted in literature, and the current study aims to bridge the research gap.
2. Related works
Post mechanical surface treatment is an effective way to refine microstructure of AM produced materials, and improve the surface condition, wear resistance, and fatigue strength. Material failures such as wear, fatigue, and corrosion usually originate at the surface or subsurface. Therefore, improving surface condition ensures better performance and extends service life of material. The typical surface treatment methods include shot peening, surface mechanical attrition treatment (SMAT) which bombards the material surface with high-hardness balls driven by ultrasonic vibration [Citation26], ultrasonic peening treatment (UPT) [Citation27], and laser shock peening (LSP) in which high-energy laser pulses create compressive shock waves that induces high plastic deformations [Citation28]. AlMangour and Yang [Citation29] and Uzan et al. [Citation30] applied shot peening to AM produced 17–4 stainless steel and AlSi10Mg alloy, respectively. For both cases, refined grain structures were observed and improvements in mechanical properties were obtained. SMAT can be regarded as a variant of shot peening process, in which the impact angles of shots are random instead of being well defined. In this regard, Retraint et al. [Citation31] adopted SMAT to achieve grain refinement effect for AISI 316L obtained by laser PBF, and also convert the surface residual stresses from tensile to compressive by more than 200 MPa. Meanwhile, Tian et al. [Citation32] applied UPT on WAAM produced aluminium alloys. It was observed that before treatment, microstructure consisted of elongated grains, but these grains became fragmented and refined after the UPT. Xing et al. [Citation33] demonstrated the effects of UPT on grain refinement and mitigation of tensile surface residual stress for LPBF produced AlSi10Mg. In addition, LSP is a cold working process during which laser pulses hit the surface through high power intensity generating shock waves, which plastically deform the surface, refine grains, and induce compressive stresses. The grain refinement effect of LSP on AM produced materials has been witnessed in literature, such as Ti-6Al-4V alloy made by electron beam melting [Citation34], 2319 aluminium alloy made by WAAM [Citation35], Inconel 718 by LPBF [Citation36].
Mechanical treatments to refine grain size could be more effective if they are applied simultaneously during the AM processes. In this regard, Wang and Shi [Citation37,Citation38] performed in-situ ultrasonic impact peening on Inconel 718 alloy manufacturing along with laser DED deposition. The hybrid process was able to significantly reduce the grain size, and highly compressive surface residual stresses were obtained as compared to the typical tensile surface residual stress for DED produced alloys. Similar in-situ ultrasonic peening efforts were made for WAAM produced Ti-6Al-4V [Citation39], LPBF produced 316L stainless steel [Citation40], laser DED produced Hastelloy X alloy [Citation18]. Meanwhile, in-situ mechanical rolling has also been attempted by multiple researchers, including [Citation41,Citation42] in which interpass mechanical rolling was applied to deposited layers of Ti6Al4 V during WAAM, and Zhao et al. [Citation43] in which rolling was applied to the melting pool of Ni60 alloy during laser DED process.
Meanwhile, it is well known that applying vibration or mechanical stirring in metal solidification processes can disrupt dendritic growth and reduce grain size. The extension of such technique has led to ultrasonic vibration-assisted AM processes for microstructure modification of AM produced metal alloys. On this front, limited attempts have been made by researchers. Ning and Cong [Citation44] used ultrasonic-assisted laser DED process to fabricate Fe-Cr stainless steel parts. The application of ultrasonic treatment was shown to change the morphology and average size of the grains from columnar grains of 7-11 µm to equiaxed grain structures of 1.5-3 µm. Tensile strength, yield strength, ductility and toughness of parts fabricated with ultrasonic assistance were reported to be higher. Similarly, the effect of ultrasonic vibration on IN718 fabricated by laser DED was investigated by Ning et al. [Citation45]. It was found that ultrasonic assist result in higher UTS with little change in elongation while the average grain size decreased from 14.31 to 5.96 µm. Laser DED was also used to study how ultrasonic vibration affects AISI 630 stainless steel [Citation46]. In this case, remarkably higher tensile strength, yield strength, ductility, and toughness were observed for ultrasonically treated samples, and the size of columnar shape grains was reduced from 10 to 2 µm. Moreover, improvement of tensile properties as a result of ultrasonic vibration during DED process were also reported for 24CrNiMoY [Citation47] and Al-12Si alloys [Citation48]. In both cases, grain refinement was also observed. In addition, grain size refinement from 62 µm to 28 µm was observed by Zhang et al. [Citation49] in NiTi alloy, which was in-situ synthesised via ultrasonic vibration-assisted DED process.
In addition, grain refinement can also be achieved by introducing nanoparticles, and this opens new possibility for AM of Al alloys that were previously thought to be incompatible with AM [Citation9,Citation50]. Nanoparticles can act as nucleation sites which control solidification during AM process, and they lower the energy barrier for heterogeneous nucleation and thus decrease the critical undercooling required for equiaxed growth. One major requirement, however, is the uniform dispersion of nanoparticles in molten metal. This can be effectively addressed by adopting ultrasonic vibration to disperse nanoparticles during AM processes, and thus grain refinement could be achieved. Ning et al. [Citation51] investigated the influence of ultrasonic vibration on the whisker size and distribution of TiB and the grain size of TiB-reinforced Ti composites fabricated by DED. It was found that without ultrasonic treatment, TiB whiskers were accumulated in an aggregate region while relatively uniform distribution of TiB whiskers was observed in ultrasonically assisted samples. Grain refinement and more uniform distribution of reinforcement phases were observed in functionally graded Ti reinforced with TiC and Cr3C2 produced by laser DED [Citation52]. Yi et al. [Citation53] studied the effect of ultrasonic assistance of ZrO2-reinforced NiCrAlY fabricated by DED. It was found that agitation of the melting pool by ultrasound promotes uniform distribution of ceramic particles.
Nevertheless, AA7075 is considered an alloy which is unfriendly to welding and AM processes, with the deposited materials showing large grain size (over 100 μm) and being prone to cracks due to the cyclic temperature changes [Citation22]. Crack-free deposition of AA7075 materials by either PBF or DED processes has been challenging. Therefore, the adoption of either post/in-situ mechanical treatment techniques, or the in-situ ultrasonic vibration to refine microstructure and improve mechanical properties for AM produced AA7075 has not been attempted, to the best of our knowledge. Also, it should be noted that post solution heat treatment could be used in AM-fabricated AA7075 to increase the mechanical properties through the precipitation hardening mechanism. However, any post processes further decrease manufacturing efficiency of the already slow AM operations. In this regard, the in-situ ultrasonic vibration-assisted DED has great potential to overcome the challenges. In the literature, ultrasonic vibration has been used in many different alloys, such as steels, high-entropy alloys, and titanium alloys, and promising results have been reported. Encouraged by the literature, it is hypothesised that the in-situ ultrasonic vibration treatment can reduce the grain size, and further suppress crack formation for AA7075 alloy during the laser DED process.
3. Experimental procedure
3.1. Materials
Generally, for laser DED processes, it is desired to adopt spherical powders to ensure the powder flowability in the powder delivery process. Thus, spherical AA7075 powders were employed in this study. The morphology of AA7075 powders with particle size ranging from 30 to 190 μm are depicted in (a). The particle diameter distribution is shown in (b), in which the particle size varies from 65 to 165 μm. The nominal chemical composition of the AA7075 spherical powder is as follows: 5.5 wt% Zn, 2.6 wt% Mg, 1.55 wt% Cu, 0.2 wt% Cr, 0.2 wt% Si, 0.15 wt% Mn, 0.3 wt% Fe, and a balance of Al.
3.2. DED processing conditions
The laser DED experiments were carried out using a desktop laser melting and deposition machine (MX-Lab) developed by Insstek Co. (Daejeon, Korea). The machine is built on a 3-axis numerical control CNC set-up. A powder feed system is embedded with a coaxial conical nozzle for supplying metal powders, along with five powder hoppers. The DED machine uses a fibre laser unit from IPG Photonics with 200 μm laser beam diameter and maximum average power of 300W, and the laser wavelength is 1070 nm. For environment control, high-purity argon gas was continuously filling the process chamber at a rate of 8.0 L/min as the protective gas to prevent oxidation during the process. The powder feed rate was set to 0.75 g/min carried by high-purity argon transport gas. In the DED process, an S-shape pattern was used in this study with 90° rotation between adjacent deposited layers and back-and-forth motion similar to fabric weaving. After one layer was deposited, the deposition direction was changed orthogonally. The hatch spacing was set to 100 μm, equivalent to half of the laser beam diameter (which resulted in 100 μm overlapping), and the height of a single layer was approximately 150 μm. The detailed parameters of DED process are shown in .
Table 1. Laser DED process parameters used for various samples in this study.
As shown in , the laser DED experiments were carried out under two scenarios – with and without ultrasonic vibration. In the ultrasonic assisted DED process, in-situ ultrasonic vibration was introduced through an AA7075 substrate, and then AA7075 powders were melted and deposited on the substrate simultaneously. In this scenario, an ultrasonic oscillator generated the ultrasonic waves, and a transducer and booster device amplified the generated ultrasonic waves. Finally, the amplified ultrasonic waves caused ultrasonic vibrations in the AA7075 substrate. The in-situ ultrasonic vibration affects the melting pool dynamics and solidification behaviour, which results in the formation of finer grain structures and consequently an increase in mechanical properties. For comparison, specimens were also built without the ultrasonic vibrations using the identical laser DED process parameters. As a result, single track remelting samples, block samples, and tensile test samples were built. The schematic of the ultrasonic vibration assisted DED process is shown in .
3.3. Metal deposition procedure
The DED experiments to study the influence of ultrasonic vibration on AA7075 alloy consist of two steps. In the first step, single-track laser remelting was conducted along the surface of AA7075 substrate without powder deposition. The purpose of this step is to develop a preliminary understanding on the effect of in-situ ultrasonic vibration on the remelting and solidification of AA7075. By using 280W laser power and a scanning speed of 300 mm/min, a single-track remelting scan was performed with and without ultrasonic vibration. In the case of applying in-situ ultrasonic vibration, the ultrasonic frequency of 30 kHz and the system power of 250W were adopted. In the second step, rectangular shaped samples of multi-layered deposition were constructed with and without ultrasonic vibration using the identical DED process parameters. Also, the ultrasonic vibration setting was fixed for all cases where ultrasonic vibration was employed. The schematic of the steps in this section is shown in , in which Step 1 is for single-track laser remelting, and Step 2 is multi-layer deposition. The corresponding group numbers of specimens can be found in , as well as in .
Figure 3. Schematics of specimen preparations with single-track laser remelting (Step 1), and multi-layer DED material deposition (Step 2).
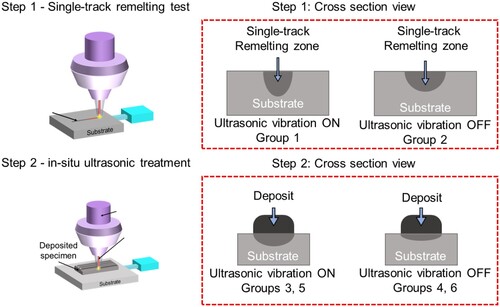
As shown in , six groups of specimens were obtained: Groups 1–2 are the single-track remelting samples; Groups 3–4 are the AA7075 block samples of 8 × 8 × 3 mm for material characterisation; Groups 5–6 are the bigger blocks of 17 × 8 × 5 mm for fabrication of miniaturised tensile samples. All those samples were sectioned off from the baseplate by wire electrical discharge machining (WEDM). The dog-bone tensile samples were EDM cut out of Groups 5–6 blocks, and the detailed dimensions of the tensile samples as well as their orientation within the deposition are shown in . Due to the size of miniaturised tensile samples, a custom tensile grip, as illustrated in (d), was designed specifically for mounting the extra small samples. This adaptation was necessary to accommodate the build size limitations of the in-house ultrasonic DED system.
3.4. Material characterisation and testing
Microstructure observations were carried out on the longitudinal sections parallel to the build direction. Samples were grinded with SiC sand papers up to 1200 grit and then polished with an alumina suspension (0.3 µm). For microstructure observation, a SCIOS Dual-Beam Scanning Electron Microscope (SEM) from Thermo Fisher Scientific equipped with an energy-dispersive X-ray spectroscopy (EDS) unit and electron backscatter diffraction (EBSD) was used for low and high-magnification microstructure examination, chemical microanalysis and grain structure analysis. EBSD samples were prepared using an automatic metallographic polisher followed by a vibration polisher. After the specimens were polished to 1 μm grit size using the metallographic polisher, the vibration polisher was employed for the final polish of the EBSD samples. A 0.02 µm non-crystallising colloidal silica suspension was utilised in the final polishing stage to achieve optimal results for the EBSD test. The EBSD analysis was vital in this study to obtain information about the grain sizes and orientations. Understanding the grain area distribution is crucial to validate the grain refinement effect of the ultrasonic treatment. In this study, an area of 1.2 mm x 0.7 mm was chosen for EBSD analysis.
For phase identification in the produced material, wide-angle (30°−90°) X-ray diffraction (XRD) profiles were recorded with CuK radiation source at a voltage of 40 kV and a current of 44 mA using an X'Pert Pro X-ray diffractometer. The microhardness of both ultrasonic treated and no ultrasonic treated samples was assessed using a Vickers micro-hardness indenter (model: HV-100) with a 0.1 kg force and 15s holding time. Last but not the least, the tensile characteristics of AA7075 alloy were determined using a Shimadzu AGS-X 50 kN tensile test machine with the rate of 0.5 mm/min. An axial extensometer (Epsilon Tech, model: 3542-025M-100-ST) which meets ASTM E83 class B-1 accuracy requirements was used to measure elongation.
4. Results and discussion
4.1. Single-track laser surface remelting
To study the influence of ultrasonic vibration on the microstructure of AA7075 alloy, the first step is to check if the melting pool and microstructure are affected under single track laser surface remelting of AA7075 substrate when ultrasonic vibration is turned off or on. As a result, two laser remelting tracks were obtained, and the SEM observations of the two tracks are shown in . (a) and 5(b) show the melting pools of the samples without and with the assistance of ultrasonic vibration, respectively. It can be seen that the melting pool geometries of the two samples are different, particularly, the melting pool depth increases significantly for the ultrasonic treated case. (c) and 5(d) show the high magnification SEM observations for the close-up areas indicated in (a) and 5(b). It can be seen that the grain size is clearly smaller for the ultrasonic treated sample. Additionally, both ultrasonically treated and untreated cases show larger grains in the bottom of melt pool and finer grains on the top. This is mainly influenced by the different cooling rates. According to Liu et al. [Citation54], in single-track laser re-melting scenarios, the top region of the melt pool exhibits much higher temperatures as well as significantly higher cooling rates compared with the bottom. The higher cooling rates result in higher nucleation rates of new grains, leading to the formation of finer grains in the upper portion of the melt pools. By using the line intercept method, it was determined that the average grain size of the untreated sample is 6.54 μm, while that of the ultrasonically treated sample is 4.73 μm. This represents a 28% reduction in grain size with the ultrasonic treatment. (e) and 5(f) show Cu distribution within single track cross sections of AA7075 without and with treatment. As will be demonstrated, Cu tends to concentrate on grain boundaries of this alloy. (e) clearly shows that Cu is distributed in a net-shape structure that aligns with the shape of the bright boundaries in (c). This proves that these bright boundaries are grain boundaries. Similar equiaxed structure is common for single laser track remelting of Al alloys [Citation55]. Based on literature, the cavitation effect from ultrasonic vibration increases the number of nucleation particles and promotes their even distribution throughout the aluminium melt. Also, the acoustic streaming also helps achieve a uniform and stable temperature field in the aluminium melt, resulting in the formation of fine and uniform equiaxed grains [Citation12,Citation56]. In this regard, the results of laser surface remelting verify that the ultrasonic treatment has a positive effect on grain refinement of the AA7075 alloy.
Figure 5. SEM observations of cross-sections for (a, c) single-track surface remelted AA7075 without ultrasonic treatment under low and high magnifications, respectively, (b, d) single-track surface remelted AA7075 with ultrasonic treatment, under low and high magnifications, respectively, (e, f) Cu distributions within yellow boxes in high magnification images for AA7075 without and with treatment.
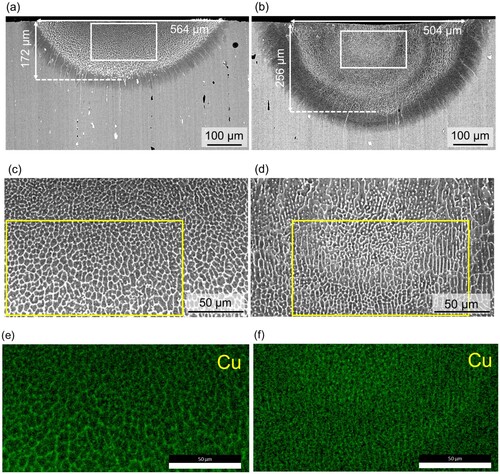
Certainly, the average grain sizes due to the laser surface remelting are smaller than those from the normal DED process, and the grain morphologies are very different too thanks to the very different thermal histories among the two operations. The conventional laser DED process tends to produce a microstructure consisting of dendrites and grains of a columnar shape along the build direction, and most grains appear to be relatively large [Citation57,Citation58]. Those can be attributed to the preferred thermal gradient in the layerwise DED deposition and high temperature of long duration, which facilitate solidification and grain growth along a particular direction. On the other hand, in the single laser track remelting, the duration of laser/material interaction is extremely short, and thus the thermal energy is insufficient for the grain growth and the rapid cooling by the surrounding substrate material results in much smaller grains. As such, the single-track remelting condition cannot fully represent the nature of laser DED process for producing multi-layer AA7075 material. Naturally, the investigation on AA7075 obtained by the DED process with and without ultrasonic vibration was conducted in the next step, and the results are shown in the following sections.
4.2. Microstructure of DED deposited multi-layer AA7075
4.2.1. SEM observation analysis
shows SEM images of the etched DED AA7075 material obtained with and without the assistance of ultrasonic vibration. As can be seen from the low-magnification figures (i.e. (a) and 6(b)), AA7075 deposition without ultrasonic treatment exhibits no obvious cracks but possesses more observable pores as compared to that with ultrasonic treatment. Moreover, both samples reveal the significant presence of small particles dispersed throughout the material, appearing as bright stripes and dots as indicated with arrows in (e) and 6(f). These bright stripes and dots are more obvious in the high-magnification SEM images (i.e. (e) and 6(f)). According to the literature on additively manufactured 7000 series aluminium alloys [Citation59–Citation61], these bright stripes and dots are commonly identified as Al2Cu, MgZn2, and Al2CuMg phases. Typically, these precipitated phases predominantly grow along the grain boundaries and some are also dispersed in the metal matrix. These precipitated phases located near the grain boundaries contribute to precipitation strengthening. This results in a strengthening effect caused by impeding dislocation motion, which in turn increases the strength of the AA7075 alloy [Citation9].
Figure 6. SEM observations for (a, c, e) DED produced AA7075 without ultrasonic treatment under low, medium, and high magnifications, respectively, (b, d, f) DED produced AA7075 with ultrasonic treatment, under low, medium, and high magnifications, respectively.
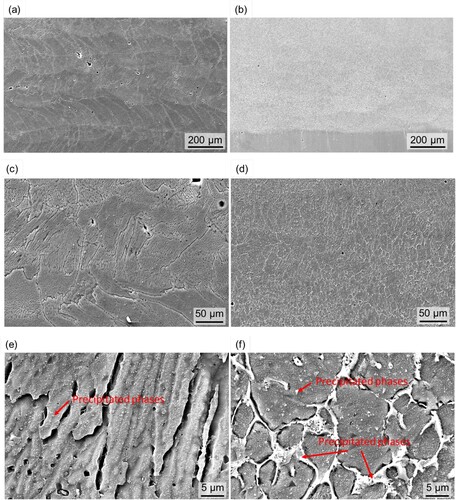
The presence of precipitated phases is more pronounced in the ultrasonic treated sample as shown in (f), indicating the likely higher fraction of precipitated phases in the ultrasonic treated sample. Moreover, based on the SEM observations, it can be seen that much finer microstructure morphology is formed in the ultrasonic treated sample. According to L. Zhou et al. [Citation62], ultrasonic assistance during the DED process initiates high-frequency vibrations that permeate the deposited material. The vibrations induce diverse effects on the material, shaping its behaviour and influencing the characteristics of the sample. One of the effects is grain refinement, which is also evident for the ultrasonically treated AA7075 alloy in this study. When ultrasonic vibration is applied in situ to the baseplate in the DED process, effects such as cavitation, acoustic streaming, and mechanical impact are generated [Citation12,Citation63–Citation65]. Cavitation bubbles rapidly grow and collapse, generating localised high temperature and pressure. This leads to the fragmentation of primary dendrites and promotion of nucleation sites. Under the influence of ultrasonic assistance, these nucleation sites distribute uniformly within the aluminium melt. Additionally, acoustic streaming contributes to a more uniform and stable temperature field in the aluminium melt during solidification, resulting in the formation of fine and uniform equiaxed grains.
4.2.2. EDS analysis
To gain deeper understanding of the nature of the bright features in , close-up SEM observations and EDS point analysis were conducted on the DED produced AA7075 with and without ultrasonic vibration, as shown in . The analysis focused on determining the chemical compositions of these particles and bright stripes, as shown in (a) and 7(b). It can be seen that Spots 4, 5 and 6, located within the matrix for both cases, have similar compositions of approximately 92.83-94.42% Al, 0.01%−2.0% Cu, and 1.63-1.83% Mg. On the other hand, Spots 1, 2 and 3 in (a) and 7(b) are located on grain boundaries of AA7075 samples with and without ultrasonic treatment. It is clear that the average Cu content of grain boundary spots significantly increases from 7% to 19%, and thus Al and Zn contents are reduced on grain boundaries after ultrasonic treatment is applied. The findings agree with the literature study on additively manufactured 7000 series aluminium alloys [Citation66], which identified these bright features as Al2Cu, MgZn2, and Al2CuMg phases. Typically, these precipitated phases predominantly grow along grain boundaries and occur in small proportions within matrix. Consequently, the ultrasonic assisted samples exhibited elevated concentrations of Cu in the bright stripes and dots compared to the samples without ultrasonic treatment. This suggests that the ultrasonic assisted DED process causes a higher content of precipitated phases in the alloy, which should in turn contribute to the improvement of mechanical properties.
Figure 7. EDS analysis of DED produced AA7075 samples: (a, b) spots selected for element analysis for AA7075 without and with ultrasonic treatment, respectively, (c, d) element distributions of the selected spots for AA7075 without and with ultrasonic treatment, respectively.
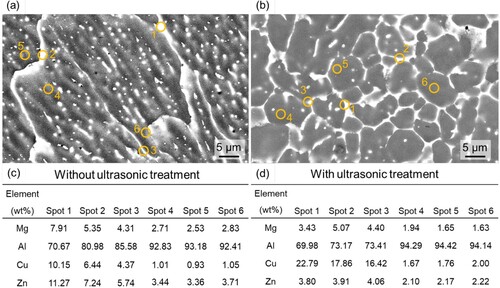
shows distributions of major elements in the cross-section of AA7075 samples with and without ultrasonic treatment. The results further confirm the findings of point analysis, as it can be seen that grain boundaries are rich in Cu, Mg and Zn without ultrasonic treatment. However, with the treatment, the content of Cu increases on grain boundaries, while segregation of Mg and especially Zn to grain boundaries becomes less apparent compared to the case without the treatment.
4.2.3. XRD analysis
shows the XRD profiles of the samples with and without ultrasonic treatment. The XRD patterns reveal the presence of the main α-Al (FCC crystal structure) phase and Al2Cu (θ-phase) intermetallic phase, while other intermetallic phases are not obvious including phases such as Al2CuMg (σ-phase) and MgZn2 (η-phase) [Citation66,Citation67]. The sample without ultrasonic treatment has the dominant intensity peak of Al (200) which corresponds to the columnar grain growth parallel to preferred growth direction in AA7075 [Citation22]. The ultrasonically treated sample exhibits a noticeably higher intensity of θ-phase peak at (111) with 2θ at about 38°. Compared to AA7075 without treatment, the ultrasonic treated sample shows that the fraction of secondary phases increases after the ultrasonic treatment. These results agree with SEM-EDS analysis that the fraction of Cu in the secondary phases significantly increases after ultrasonic treatment.
4.2.4. EBSD analysis
EBSD analysis was also performed on DED produced AA7075 materials with and without ultrasonic treatment, and the results are summarised in . As shown in (a), the inverse pole figure (IPF) of the untreated AA7075 reveals the presence of coarse columnar grains generally aligned along the build direction, which is attributed to the rapid heating and cooling process involved in laser DED. Similar morphologies are reported in literature for various materials deposited by the laser DED processes [Citation68]. However, some fine grains are also observed at the interlayer. Upon comparing the bright strips in with the grain boundaries identified in the IPF image, it becomes evident that the bright stripes correspond to the grain boundaries. The larger grains predominantly exhibit growth in the direction of the build process which agrees with the study of Bayazid et al. [Citation69]. On the other hand, the EBSD result in (b) indicates the grain size is significantly decreased in the ultrasonically treated sample. This result agrees with the observation in (b). The alignment of elongated grains in the untreated sample deviates from the build direction by about ±20° (i.e. (a)) and alternates the direction within each deposited layer. The average length of long axis in the untreated sample is 21.0 µm. In case of the ultrasonically treated sample shown in (b), grains are predominately equiaxed with an average length of the long axis of 8.8 µm. The number of elongated grains and their area are significantly reduced in the ultrasonically treated sample.
Figure 10. EBSD observations for DED produced AA7075 with and without ultrasonic treatment, (a, c, e, g) inverse pole figure, kernel average misorientation map, boundary misorientation map, grain size distribution of AA7075 without ultrasonic treatment, respectively, (b, d, f, h) inverse pole figure, kernel average misorientation map, boundary misorientation map, grain size distribution of AA7075 with ultrasonic treatment, respectively.
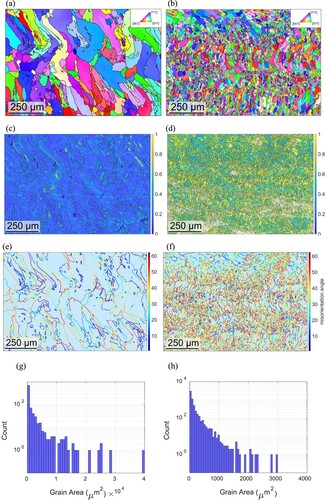
(c) and 10(d) show Kernel Average Misorientation (KAM) maps for samples without and with ultrasonic treatment, respectively. KAM provides a visual representation of the average misorientation between a given data point and its nearest neighbours that belong to the same grain. Higher KAM value (more green colour) is an indication of a high misorientation which is evidence for a high stored energy in the grain. Deformed grains generally contain higher dislocation density which appears as a higher KAM value [Citation38]. As seen from the figure, KAM is overall much higher in the ultrasonically treated AA7075, which could be an indication that ultrasonic treatment significantly increases the dislocation density. (e) and 10(f) show grain boundary misorientation maps of AA7075 without and with ultrasonic treatment, respectively. It can be seen that the misorientation distributions of grain boundaries of AA7075 sample without treatment have peaks at about 5° or 45° as indicated by the blue and yellow colours. Peaks at low misorientation angles such as 5° are associated with a large number of low-angle boundaries. Similar misorientation distributions with peak at low angle were previously observed in AA7075 [Citation70]. On the other hand, 45° peak is believed to be a manifestation of the Mackenzie distribution model for randomly distributed grain boundaries [Citation71]. In contrast, the AA7075 with the treatment contains significantly more grain boundaries with misorientation of about 45° or above, while the amount of the low misorientation boundaries is noticeably lower than in the case without the treatment. In addition, (g) and 10(h) show the histograms of grain size distribution for both cases. The average area reduces significantly after applying ultrasonic assistance: from 1751 ± 41.89 µm2 to 118.2 ± 10.87 µm2 for the untreated and ultrasonically treated samples, respectively.
4.3. Mechanical properties of DED deposited multi-layer AA7075
4.3.1. Microhardness
shows the hardness distributions along the build direction for both AA7075 materials with and without ultrasonic treatment. It is observed that the ultrasonic-treated DED AA7075 alloy has higher hardness than the untreated AA7075. The average Vickers micro-hardness of the ultrasonic-treated DED AA7075 alloy was measured to be 110.2 ± 1.1 HV under a 0.1 kg load, as opposed to the average hardness of 93.1 ± 2.0 HV for AA7075 without ultrasonic treatment. Note that the multiple indentations for each case shown in were obtained at a fixed depth along the build direction to show the overall consistency of hardness results at that depth. This represents a relative increase of 18.37% in hardness. It should be noted that the obtained hardness value for untreated AA7075 is on par with literature reporting for DED produced AA7075 [Citation22,Citation72]. Meanwhile, some fluctuations in hardness can be observed along the depth from the surface, and the fluctuation is more significant in the untreated case. This enhanced hardness can be attributed to the primary strengthening mechanism of the 7000 series aluminium alloys, facilitated by the precipitation of nano-sized second-phase particles [Citation66] and the presence of smaller grain sizes after undergoing ultrasonic treatment.
4.3.2. Tensile properties
depicts the tensile behaviour of AA7075 samples produced by DED process with and without ultrasonic treatment. Notably, the ultrasonic treatment leads to a substantial enhancement in the material's tensile strength. The average ultimate tensile strength and fracture strain of DED produced AA7075 without ultrasonic treatment are 226.8 ± 11.6 MPa and 5.82 ± 0.95%, respectively. In contrast, the ultrasonically treated AA7075 exhibits significantly improved properties, with values of 314.7 ± 12.8 MPa and 5.63 ± 0.61% for ultimate tensile strength and fracture strain, respectively. Thus, the application of ultrasonic treatment proves to be an effective means of enhancing the tensile performance of the material. Note that the stress–strain curves appear to be less smooth than usual, which could be attributed to the following reason. Recall the miniaturised tensile samples cannot be accommodated by the regular grip of our material testing system, and thus a customised tensile grip was made to mount the samples. The small size of the samples contributes to noise during testing, and the potential micro-slippage in the customised tensile grip also contributes to the less smooth curves.
Figure 12. Representative tensile curves of DED produced AA7075 specimens with and without ultrasonic treatment.
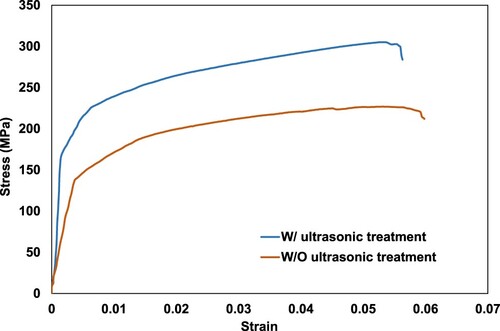
This improvement in tensile properties can be attributed to several factors, including grain refinement and precipitation strengthening. Additionally, the dissolution of second-phase particles located near the grain boundaries into the Al matrix contributes to solid solution strengthening, thereby impeding dislocation motion and further enhancing the alloy's strength. Comparing the DED-produced AA7075 with the LPBF-produced variant reported in existing literature [Citation9,Citation20,Citation73], it becomes evident that the DED-produced material exhibits significantly higher tensile properties.
4.3.3. Fracture analysis
shows fracture surfaces of AA7075 tensile samples with and without ultrasonic treatment. It can be seen that these fracture surfaces exhibit a combination of cleavage and dimple-like facets [Citation74]. Notably, both unassisted and ultrasonically assisted samples display a mix of brittle and ductile fracture features, characterised by cleavage, along with the presence of dimple-like facets. Overall, both samples exhibit similar fractographic characteristics. For example, there is no apparent difference in appearance of the ductile fracture morphology in both cases as seen under 1500× magnification and the cumulative area of ductile fracture in both cases is approximately the same, as can be seen from the lower magnification images. It is worth noting that when comparing the fractography results with the tensile data illustrated in , both samples show similar fracture strain values. Despite the difference in their tensile strength due to ultrasonic treatment, the fracture behaviour, as indicated by the fractographs, remains consistent between the two samples.
5. Strengthening mechanisms for AA7075 with ultrasonic treatment
5.1. Secondary phases at grain boundaries
The generation of acoustic cavitation and streaming in the liquid metal due to high-intensity ultrasound provides intensive agitation to the melt during solidification. The application of high-intensity ultrasonic vibration induces a phenomenon known as acoustic cavitation [Citation75,Citation76]. This involves the formation, growth, and subsequent collapse of small bubbles within the molten material. These bubbles experience rapid expansion and contraction due to the alternating high-pressure and low-pressure regions created by the ultrasonic waves [Citation75]. The collapse of these bubbles generates localised regions of intense energy-matter interactions, characterised by high temperatures and pressures. These localised conditions of high temperature and pressure during bubble collapse create favourable environments for the initiation and growth of secondary phase particles.
In general, the presence of secondary phases at grain boundaries represents a stable state for AA7075. In the conventional DED process for AA7075 alloy, the high cooling rates often exceed the precipitation kinetics of the secondary phases. This rapid cooling can suppress both the nucleation and growth of secondary phases. Therefore, post-processing techniques, such as heat treatment and aging, are commonly employed to produce these secondary phases to achieve the desired mechanical properties of AA7075. In the ultrasonic-assisted process depicted in . The cavitation effect enhances the Marangoni flow in the melt pool due to the way it alters temperature distribution. The formation and subsequent collapse of bubbles within the melt pool leads to localised changes in heat transfer and fluid flow. These changes result in a higher peak temperature when ultrasonic vibration is introduced. Consequently, the Marangoni flow, which is driven by differences in surface tension, becomes stronger. This enhancement is attributed to the larger temperature gradients created in the melt pool [Citation77,Citation78]. This cooperative effect not only increases the nucleation rate but also ensures that the nuclei are uniformly distributed throughout the melting pool [Citation78]. Therefore, when the melting pool is in the cooling stage, more nuclei are present at the grain boundaries, which provide a favourable environment for the growth of the secondary phase. In addition, the release of energy during the collapse of the bubbles supplies the necessary energy for the nucleation and subsequent growth of these secondary phase particles precisely at the grain boundaries. Ultrasonic assistance also enhances the diffusion of solute atoms, further contributing to the formation of secondary phases precipitate at the grain boundaries. The vibrational energy imparted by the ultrasonic waves induces a phenomenon known as acoustic streaming [Citation64], which promotes the thorough mixing and homogenisation of the molten material. As a result, the distribution of solute atoms becomes more uniform throughout the material. This improved mixing leads to heightened rates of solute diffusion, enabling the solute atoms to migrate towards the grain boundaries. At the grain boundaries, the concentration of solute atoms can exceed the solubility limit, resulting in the precipitation of secondary phase particles or the formation of second structures. The presence of these secondary phase particles or secondary phases at the grain boundaries leads to an increased volume fraction of the secondary phase within the microstructure. This contributes to the development of a distinct and refined microstructure. The increased presence of secondary phase precipitate at the grain boundaries plays a significant role in influencing the material properties. These secondary phase particles or secondary phase structures act as barriers to the movement of dislocations, impeding the propagation of dislocation lines. Consequently, this enhances the strength and hardness of the material for the AA7075 alloy [Citation22,Citation79].
5.2. Grain refinement
Recall that in , the grains size undergoes a noticeable reduction after ultrasonic treatment in this study. According to Todaro et al. [Citation21] and Z. Wang et al. [Citation63], the grain refinement due to ultrasonic treatment in metal AM processes can be explained as follows. The application of ultrasonic vibration during the AM process induces cavitation, acoustic streaming, and mechanical impact. Cavitation bubbles rapidly form and collapse, generating localised regions of high temperature and pressure. Similarly, as shown in , acoustic cavitation is the primary effect of ultrasonically assisted AM process, which involves the formation, growth, and collapse of bubbles within the liquid medium. B. Wang et al. [Citation80] reported that in case of molten metallic alloys, acoustic cavitation occurs almost instantaneously within approximately 0.00003 s, as observed through in-situ synchrotron X-ray imaging studies. Acoustic cavitation leads to significant energy-matter interactions, resulting in creation of hot spots inside the bubbles with temperatures of around 5000°, pressures of approximately 105 KPa, and heating and cooling rates of about 1010°C per second. These effects play a crucial role in the refinement of the grain structure through ultrasonic vibration. This in turn facilitates the fragmentation of primary dendrites and creates additional sites for nucleation within the molten material. As a result, the formation of fine and uniformly shaped equiaxed grains is favoured, leading to a smaller distribution of grain sizes. During the ultrasonic assisted laser DED process, material is obtained layer by layer on a vibrating base plate by directly depositing metal powder into a melt pool created by a moving laser beam. At the same time, high-intensity ultrasound is applied to the melt pool, which remains in its molten state for a very short duration of about 0.01-0.1 s before it solidifies [Citation81]. Z. Wang et al. [Citation63] reported a solidification time of 0.047 s in ultrasonic assisted DED process. The application of ultrasonic vibration generates mechanical and physicochemical effects. As a result, grain refinement can occur via enhancement of fragmentation and nucleation. The acoustic cavitation process induces the fragmentation of existing grains, breaking them into smaller fragments. Additionally, it enhances the nucleation of new grains, promoting the formation of a finer grain structure.
Figure 15. Schematics diagram of AA7075 microstructure evolution during the laser DED processes with and without ultrasonic assistance.
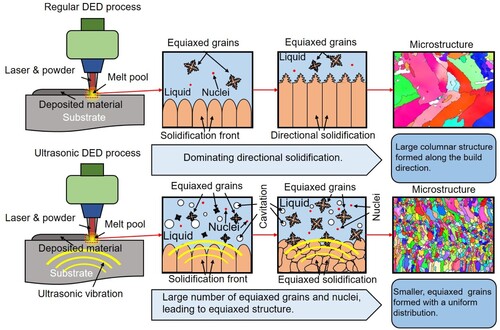
Another reason for the grain refinement effect could be that ultrasonic wave leads to more uniform temperature distribution in the melt pool. Acoustic streaming, which is the flow of molten material induced by ultrasonic vibration, contributes to a more consistent and stable temperature distribution during the solidification process [Citation63]. This uniform temperature field helps to prevent the formation of temperature gradients that could result in uneven growth of grains. Consequently, the resulting microstructure exhibits a greater degree of uniformity in terms of grain sizes. Z. Wang et al. [Citation63] study the temperature distribution in the DED melt pool. It was confirmed that the morphology and size of the deposition layer's grain structure are influenced by the combination of the temperature gradient (G) and solidification growth rate (R). When the G and R increases in the DED deposited layers, the grain structures fabricated through DED process become finer. Lower G/R ratio favours the formation of equiaxed grains and lower G/R ratio leads to uniform temperature distribution which is beneficial for higher nucleation rate and more nucleation site. As a result, ultrasonic vibration decreases the temperature gradient in the deposited layers and refines the grains. The relation between the temperature gradient and nucleation rate can be described by the following equation [Citation63].
Where
is temperature gradient, N is nucleation rate, C is local sonic velocity of the liquid, P is enthalpy difference between the liquid at pressure PL and pressure P∞, B is a constant that depends upon the type of liquid. Therefore, the nucleation rate increases with the decrease of temperature gradient which leads to a more uniform temperature distribution.
5.3. Mechanical property improvement
As shown in , the application of ultrasonic treatment to the DED-produced AA7075 samples results in a significant increase in ultimate tensile strength, 38.8% higher compared to the untreated samples (i.e. from an average of 226.8 MPa to 314.7 MPa). Both sets of samples exhibit a strain-to-failure value of around 6%, which aligns with typical values reported in the literature for as-built DED-processed AA7075 alloy [Citation22,Citation72]. The observed strengthening effect of ultrasonic treatment can be attributed to the refinement of grain size, as noted in the similar work by Todaro et al. [Citation65] on DED produced alloys. In this study, the average length of the long axis of the grains decreases by approximately 58% after undergoing the ultrasonic treatment (e.g. from an average of 21.0 µm to 8.8 µm). The significance of grain size refinement as a primary reinforcing mechanism for AA7075 alloy is supported by research from Baek et al. [Citation82]. The relationship between grain size and strength is well described by the Hall-Petch relation, , Introduced by Hall and Petch in the early 1950s [Citation83,Citation84], and this relationship has been extensively utilised in related research fields [Citation65,Citation82,Citation85]. This equation serves the purpose of explaining the strengthening effect achieved through grain size reduction in the material. Essentially, as the grain size decreases, the material becomes stronger because smaller grains provide more grain boundaries, which act as barriers to dislocation motion.
Meanwhile, the tensile results reveal that the strain-to-failure values remain similar, regardless of whether ultrasonic treatment is applied. This consistency could be attributed to the presence of precipitate (secondary phases) at grain boundaries. These precipitated secondary phases play a dual role, enhancing both the tensile strength and toughness of the AA7075 alloy while also mitigating the strength-toughness trade-off caused by grain refinement. These findings have been supported by the findings by Su et al. [Citation22] and Dharmendra et al. [Citation78]. Consequently, the ultrasonic treatment induces beneficial microstructural changes, such as reduced grain size, while significantly promoting the formation of secondary phases at the grain boundaries. These microstructural modifications collectively contribute to the observed improvements in the tensile and hardness properties of the AA7075 alloy. In addition, due to the nature of additive manufacturing, AA7075 alloys obtained in this study, similar to most AM produced alloys, are not 100 percent defect-free, as indicated by . Overall, the defects are almost negligible, but DED produced AA7075 without ultrasonic treatment appears to have slightly more defects. This may also contribute to the tensile property difference.
6. Conclusion
AA7075 is an important lightweight aluminium alloy, but its composition design is not friendly to additive manufacturing processes. In this study, we apply the in-situ ultrasonic vibration to the melting pool during the laser DED process to refine the grain structure and improve the mechanical properties of produced AA7075. To demonstrate such effects, the observations are compared with those of the regular DED produced AA7075. The results show that the application of in-situ ultrasonic assistance led to noteworthy improvements in microstructure refinement and mechanical properties in terms of hardness and ultimate tensile strengthen. By inducing cavitation and acoustic streaming, localised regions of high temperature and pressure are generated during bubble collapse, facilitating significant grain size reduction. As a result, ultrasonic treatment drastically changed grain morphology from columnar grains with an average area of 1751 µm2 to equiaxed grains of 118.2 µm2, signifying the remarkable effect of ultrasonic assistance on grain refinement. Consequently, the material hardness increased from 93.1 HV for AA7075 without ultrasonic treatment to 110.2 HV for AA7075 with ultrasonic treatment. Furthermore, the resultant ultrasonic-assisted AA7075 alloy exhibited an average ultimate tensile strength of 314.7 MPa, demonstrating an impressive 38.8% increase compared to the untreated samples. The improved microstructure, characterised by fine and uniformly shaped equiaxed grains, significantly contributes to the development of superior mechanical properties. In addition, the formation of secondary phase particles at grain boundaries further reinforces AA7075, effectively augmenting both strength and hardness. Consequently, the integration of DED technology with ultrasonic vibration offers a robust pathway to enhance the mechanical performance of AA7075 alloy.
Disclosure statement
No potential conflict of interest was reported by the author(s).
Data availability
The authors confirm that the data supporting the findings of this study are available within the article.
References
- Lu C, Jia X, Lee J, et al. Knowledge transfer using Bayesian learning for predicting the process-property relationship of inconel alloys obtained by laser powder bed fusion. Virtual Phys Prototyp. 2022;17(4):787–805. doi:10.1080/17452759.2022.2068447
- Savinov R, Wang Y, Shi J. Microstructure and properties of CeO2-doped CoCrFeMnNi high entropy alloy fabricated by laser metal deposition. J Manuf Process. 2020;56:1245–1251. doi:10.1016/j.jmapro.2020.04.018
- Lv H, Li Z, Li X, et al. Effect of vanadium content on the microstructure and mechanical properties of IN718 alloy by laser cladding. Materials (Basel). 2021;14(9):2362. doi:10.3390/ma14092362
- Kumar SP, Elangovan S, Mohanraj R, et al. A review on properties of inconel 625 and inconel 718 fabricated using direct energy deposition. Mater Today Proc. 2021;46:7892–7906. doi:10.1016/j.matpr.2021.02.566
- Wang Y, Roy S, Choi H, et al. Cracking suppression in additive manufacturing of hard-to-weld nickel-based superalloy through layer-wise ultrasonic impact peening. J Manuf Process. 2022;80:320–327. doi:10.1016/j.jmapro.2022.05.041
- Jeong W, Kwon Y, Kim D. Three-dimensional printing of tungsten structures by directed energy deposition. Mater Manuf Processes. 2019;34(9):986–992. doi:10.1080/10426914.2019.1594253
- Marques DA, Oliveira JP, Baptista AC. A short review on the corrosion behaviour of wire and arc additive manufactured materials. Metals (Basel). 2023;13(4):641. doi:10.3390/met13040641
- Felice IO, Shen J, Barragan C, et al. Wire and arc additive manufacturing of Fe-based shape memory alloys: microstructure, mechanical and functional behavior. Mater Des. 2023;231:112004. doi:10.1016/j.matdes.2023.112004
- Martin JH, Yahata BD, Hundley JM, et al. 3D printing of high-strength aluminium alloys. Nature. 2017;549(7672):365–369. doi:10.1038/nature23894
- Wang Z, Wang X, Chen X, et al. Complete columnar-toequiaxed transition and significant grain refinement in an aluminium alloy by adding Nb particles through laser powder bed fusion. Addit Manuf. 2022;51:102615. doi:10.1016/j.addma.2022.102615
- Sadhu, A, Choudhary, A, Sarkar, S, et al.. A study on the influence of substrate pre-heating on mitigation of cracks in direct metal laser deposition of NiCrSiBC-60%WC ceramic coating on inconel 718. Surf Coat Technol. (2020); 389: 125646–125646. doi:10.1016/j.surfcoat.2020.125646
- Todaro CJ, Easton MA, Qiu D, et al. Grain structure control during metal 3D printing by high-intensity ultrasound. Nat Commun. 2020;11(1):142. doi:10.1038/s41467-019-13874-z
- Bermingham MJ, StJohn DH, Krynen J, et al. Promoting the columnar to equiaxed transition and grain refinement of titanium alloys during additive manufacturing. Acta Mater. 2019;168:261–274. doi:10.1016/j.actamat.2019.02.020
- Carroll BE, Palmer TA, Beese AM. Anisotropic tensile behavior of Ti–6Al–4V components fabricated with directed energy deposition additive manufacturing. Acta Mater. 2015;87:309–320. doi:10.1016/j.actamat.2014.12.054
- Jin P, Liu Y, Sun Q. Evolution of crystallographic orientation, columnar to equiaxed transformation and mechanical properties realized by adding TiCps in wire and arc additive manufacturing 2219 aluminum alloy. Additive Manufacturing. 2021;39:101878.
- Lee T-G, Jeong W, Chung S, et al. Role of B4C in the directed energy deposition of aluminum alloy 6061/B4C composite using core-shell powder for crack annihilation, pore mitigation, and grain refinement. Additive Manufacturing. 2023;72:103622. doi:10.1016/j.addma.2023.103622
- Wang L, Wu T, Wang D, et al. A novel heterogeneous multi-wire indirect arc directed energy deposition for in-situ synthesis Al-Zn-Mg-Cu alloy: process, microstructure and mechanical properties. Additive Manufacturing. 2023;72:103639. doi:10.1016/j.addma.2023.103639
- Wang X, Xu L, Zhao L, et al. Defect-related strain-controlled high-temperature fatigue behavior in additive manufacturing hastelloy X assisted with ultrasonic micro-forging treatment. Int J Fatigue. 2023;172:107607. doi:10.1016/j.addma.2023.103639
- Montero-Sistiaga ML, Mertens R, Vrancken B, et al. Changing the alloy composition of Al7075 for better processability by selective laser melting. J Mater Process Technol. 2016;238:437–445. doi:10.1016/j.jmatprotec.2016.08.003
- Zhou SY, Su Y, Wang H, et al. Selective laser melting additive manufacturing of 7xxx series Al-Zn-Mg-Cu alloy: Cracking elimination by co-incorporation of Si and TiB2. Additive Manufacturing. 2020;36:101458. doi:10.1016/j.addma.2020.101458
- Liu P, Hu J, Li H, et al. Effect of heat treatment on microstructure, hardness and corrosion resistance of 7075 Al alloys fabricated by SLM. J Manuf Process. 2020;60:578–585. doi:10.1016/j.jmapro.2020.10.071
- Su Y, Wang Y, Shi J. Microstructure and mechanical properties of laser DED produced crack-free Al 7075 alloy: effect of process parameters and heat treatment. Mater Sci Eng A. 2022;857:144075. doi:10.1016/j.msea.2022.144075
- Kaufmann N, Imran M, Wischeropp TM, et al. Influence of process parameters on the quality of aluminium alloy EN AW 7075 using selective laser melting (SLM). Phys Procedia. 2016;83:918–926. doi:10.1016/j.phpro.2016.08.096
- Ghosh A, Ghosh M. Microstructure and texture development of 7075 alloy during homogenisation. Philos Mag. 2018;98(16):1470–1490. doi:10.1080/14786435.2018.1439596
- Liu Z, Rakita M, Wang X, et al. In situ formed Al3Ti particles in Al alloy matrix and their effects on the microstructure and mechanical properties of 7075 alloy. J Mater Res. 2014;29(12):1354–1361. doi:10.1557/jmr.2014.123
- Cui G, Bao C, Zhang M, et al. Effects of thermal aging on mechanical properties and microstructures of an interstitial high entropy alloy with ultrasonic surface mechanical attrition treatment. Mater Sci Eng A. 2022;838:142755. doi:10.1016/j.msea.2022.142755
- Gu GH, Kim RE, Kim ES, et al. Multi-layered heterostructured CoCrFeMnNi high-entropy alloy processed using direct energy deposition and ultrasonic nanocrystalline surface modification. J Mater Res Technol. 2020;21:2880–2890. doi:10.1016/j.jmrt.2022.10.099
- Ran M, Wang Q, You SL, et al. Effect of laser shock peening and surface mechanical attrition treatment on the oxidation resistance of a 20Cr-25Ni-Nb stainless steel. Mater Charact. 2023;203:113065–113065. doi:10.1016/j.matchar.2023.113065
- AlMangour B, Yang J. Improving the surface quality and mechanical properties by shot-peening of 17-4 stainless steel fabricated by additive manufacturing. Mater Des. 2016;110:914–924. doi:10.1016/j.matdes.2016.08.037
- Uzan NE, Ramati S, Shneck R, et al. On the effect of shot-peening on fatigue resistance of AlSi10Mg specimens fabricated by additive manufacturing using selective laser melting (AM-SLM). Additive Manufacturing. 2018;21:458–464. doi:10.1016/j.addma.2018.03.030
- Retraint D, Portella Q, Chemkhi M. Residual stresses analysis in AISI 316L processed by selective laser melting (SLM) treated by mechanical post-processing treatments. Materials Research Proceedings. 2018;6.271–276. doi:10.21741/9781945291890-43
- Tian Y, Shen J, Hu S, et al. Effects of ultrasonic peening treatment on surface quality of CMT-welds of Al alloys. J Mater Process Technol. 2018;254:193–200. doi:10.1016/j.jmatprotec.2017.11.029
- Xing X, Duan X, Sun X, et al. Modification of residual stresses in laser additive manufactured AlSi10Mg specimens using an ultrasonic peening technique. Materials (Basel). 2019;12(3):455. doi:10.3390/ma12030455
- Lan L, Jin X, Gao S, et al. Microstructural evolution and stress state related to mechanical properties of electron beam melted Ti-6Al-4V alloy modified by laser shock peening. J Mater Sci Technol. 2020;50:153–161. doi:10.1016/j.jmst.2019.11.039
- Sun R, Li L, Zhu Y, et al. Microstructure, residual stress and tensile properties control of wire-arc additive manufactured 2319 aluminum alloy with laser shock peening. J Alloys Compd. 2018;747:255–265. doi:10.1016/j.jallcom.2018.02.353
- Sidhu KS, Wang Y, Shi J, et al. (2019). Effect of post laser shock peening on microstructure and mechanical properties of inconel 718 by selective laser melting. In International Manufacturing Science and Engineering Conference (Vol. 58752, p. V002T03A071). American Society of Mechanical Engineers. doi:10.1115/MSEC2019-2893
- Wang Y, Shi J. Microstructure and properties of inconel 718 fabricated by directed energy deposition with in-situ ultrasonic impact peening. Metallurgical and Materials Transactions B. 2019;50:2815–2827. doi:10.1007/s11663-019-01672-3
- Wang Y, Shi J. Recrystallization behavior and tensile properties of laser metal deposited inconel 718 upon in-situ ultrasonic impact peening and heat treatment. Mater Sci Eng A. 2020;786:139434. doi:10.1016/j.msea.2020.139434
- Gou J, Wang Z, Hu S, et al. Effects of ultrasonic peening treatment in three directions on grain refinement and anisotropy of cold metal transfer additive manufactured Ti-6Al-4V thin wall structure. J Manuf Process. 2020;54:148–157. doi:10.1016/j.jmapro.2020.03.010
- Gale J, Achuhan A. Application of ultrasonic peening during DMLS production of 316L stainless steel and its effect on material behavior. Rapid Prototyp J. 2017;23(6):1185–1194. doi:10.1108/RPJ-09-2016-0140
- Martina F, Roy MJ, Szost BA, et al. Residual stress of as-deposited and rolled wire+arc additive manufacturing Ti–6Al–4V components. Mater Sci Technol. 2016;32(14):1439–1448. doi:10.1080/02670836.2016.1142704
- Hönnige JR, Colegrove PA, Ahmad B, et al. Residual stress and texture control in Ti-6Al-4V wire + arc additively manufactured intersections by stress relief and rolling. Mater Des. 2018;150:193–205. doi:10.1016/j.matdes.2018.03.065
- Zhao W, Zha GC, Xi MZ, et al. Effects of synchronous rolling on microstructure, hardness, and wear resistance of laser multilayer cladding. J Mater Eng Perform. 2018;27:1746–1752. doi:10.1007/s11665-018-3286-x
- Ning F, Cong W. Microstructures and mechanical properties of Fe-Cr stainless steel parts fabricated by ultrasonic vibration-assisted laser engineered net shaping process. Mater Lett. 2016;179:61–64. doi:10.1016/j.matlet.2016.05.055
- Ning F, Hu Y, Liu Z, et al. Ultrasonic vibration-assisted laser engineered net shaping of inconel 718 parts: a feasibility study. Procedia Manufacturing. 2017;10:771–778. doi:10.1016/j.promfg.2017.07.074
- Cong W, Ning F. A fundamental investigation on ultrasonic vibration-assisted laser engineered net shaping of stainless steel. Int J Mach Tools Manuf. 2017;121:61–69. doi:10.1016/j.ijmachtools.2017.04.008
- Zhou L, Chen S, Ma M, et al. The dynamic recrystallization mechanism of ultrasonic power on non-contact ultrasonic-assisted direct laser deposited alloy steel. Mater Sci Eng A. 2022;840:142971. doi:10.1016/j.msea.2022.142971
- Zhang Y, Guo Y, Chen Y, et al. Microstructure and mechanical properties of Al-12Si alloys fabricated by ultrasonic-assisted laser metal deposition. Materials (Basel). 2020;13(1):126. doi:10.3390/ma13010126
- Zhang D, Li Y, Wang H, et al. Ultrasonic vibration-assisted laser directed energy deposition in-situ synthesis of NiTi alloys: effects on microstructure and mechanical properties. J Manuf Process. 2020;60:328–339. doi:10.1016/j.jmapro.2020.10.058
- Shi J, Wang Y. Development of metal matrix composites by laser-assisted additive manufacturing technologies: a review. J Mater Sci. 2020;55(23):9883–9917. doi:10.1007/s10853-020-04730-3
- Ning F, Hu Y, Cong W. Microstructure and mechanical property of TiB reinforced Ti matrix composites fabricated by ultrasonic vibration-assisted laser engineered net shaping. Rapid Prototyp J. 2019;25(3):581–591. doi:10.1108/RPJ-05-2018-0118
- Qin LY, Wang W, Yang G. Experimental study on laser metal deposition of FGMs with ultrasonic vibration. Appl Mech Mater. 2013;271:131–135. doi:10.4028/www.scientific.net/AMM.271-272.131
- Yi Z, Song C, Zhang G, et al. Microstructure and wear property of ZrO2-added NiCrAlY prepared by ultrasonic-assisted direct laser deposition. Materials (Basel). 2021;14(19):5785. doi:10.3390/ma14195785
- Liu Y, Wang Y, Savinov R, et al. Epitaxial growth of a single-crystal nickel-based superalloy during laser melting with high-power flat-top laser. Opt Laser Technol. 2021;144:107444. doi:10.1016/j.optlastec.2021.107444
- Ghasri-Khouzani M, Karimialavijeh H, Tangestani R, et al. Single-track study of A20X aluminum alloy fabricated by laser powder bed fusion: modeling and experiments. Opt Laser Technol. 2023;162:109276–109276. doi:10.1016/j.optlastec.2023.109276
- Khalifa W, Tsunekawa Y, Okumiya M. Effect of ultrasonic treatment on the Fe-intermetallic phases in ADC12 die cast alloy. J Mater Process Technol. 2010;210(15):2178–2187. doi:10.1016/j.jmatprotec.2010.08.008
- Gonzalez LC, Tuominen J, Ahmed S, et al. Directed energy deposition of AA7075 - effect of TiC nanoparticles on microstructure. Results in Materials. 2022;16:100341. doi:10.1016/j.rinma.2022.100341
- Guo Y, Wei W, Shi W, et al. Effect of Er and Zr additions and aging treatment on grain refinement of aluminum alloy fabricated by laser powder bed fusion. J Alloys Compd. 2022;912:165237. doi:10.1016/j.jallcom.2022.165237
- Griffiths S, Croteau JR, Rossell MD, et al. Coarsening- and creep resistance of precipitation-strengthened Al–Mg–Zr alloys processed by selective laser melting. Acta Mater. 2020;188:192–202. doi:10.1016/j.actamat.2020.02.008
- Kim J, Jhang K, Kim C. Dependence of nonlinear ultrasonic characteristic on second-phase precipitation in heat-treated Al 6061-T6 alloy. Ultrasonics. 2018;82:84–90. doi:10.1016/j.ultras.2017.07.015
- Wang P, Li HC, Prashanth KG, et al. Selective laser melting of Al-Zn-Mg-Cu: heat treatment, microstructure and mechanical properties. J Alloys Compd. 2017;707:287–290. doi:10.1016/j.jallcom.2016.11.210
- Zhou L, Chen S, Jia W, et al. Effects of preheating-ultrasonic synergistic on the microstructure and strength-ductility of 24 CrNiMoY alloy steel by laser directed energy deposition. Mater Sci & Eng A: Struct Mater: Prop Microstruct. Process. 2023;863:144463. doi:10.1016/j.msea.2022.144463
- Wang Z, Jiang F, Guo C, et al. Effects of ultrasonic vibration on microstructure and mechanical propertiesof 1Cr12Ni3MoVN alloy fabricated by directed energy deposition. Ultrasonics. 2023;132:106989. doi:10.1016/j.ultras.2023.106989
- Wang T, Mazánová V, Liu X. Ultrasonic effects on gas tungsten arc based wire additive manufacturing of aluminum matrix nanocomposite. Mater Des. 2022;214:110393.
- Todaro CJ, Easton MA, Qiu D, et al. Grain refinement of stainless steel in ultrasound-assisted additive manufacturing. Additive Manufacturing. 2021;37:101632. doi:10.1016/j.addma.2020.101632
- Yazdian N, Karimzadeh F, Tavoosi M. Microstructural evolution of nanostructure 7075 aluminum alloy during isothermal annealing. J Alloys Compd. 2010;493(1):137–141. doi:10.1016/j.jallcom.2009.12.144
- Nama HAA, Esen İ, Ahlatcı H, et al. Effect of aging heat treatment on wear behavior and microstructure characterization of newly developed Al7075+Ti alloys. Materials (Basel). 2023;16(12):4413. doi:10.3390/ma16124413
- Savinov R, Wang Y, Shi J. Evaluation of microstructure, mechanical properties, and corrosion resistance for Ti-doped inconel 625 alloy produced by laser directed energy deposition. Mater Sci Eng A. 2023;884:145542. doi:10.1016/j.msea.2023.145542
- Bayazid SM, Farhangi H, Asgharzadeh H, et al. Effect of cyclic solution treatment on microstructure and mechanical properties of friction stir welded 7075 Al alloy. Materials Science & Engineering. A, Structural Materials: Properties, Microstructure and Processing. 2016;649:293–300.
- Romero-Reséndiz L, Amigó V, Escuder ÁV, et al. Effect of the microstructure generated by repetitive corrugation and straightening (RCS) process on the mechanical properties and stress corrosion cracking of Al-7075 alloy. Journal of Materials Research and Technology. 2021;15:4564–4572. doi:10.1016/j.jmrt.2021.10.043
- Kusakin P, Terentev VF. Structure and mechanical properties of high-strength austenitic-martensitic trip-steel VNS9-Sh. Met Sci Heat Treat. 2019;61:10–14. doi:10.1007/s11041-019-00369-3
- Bhagavatam A, Ramakrishnan A, Adapa V, et al. Laser metal deposition of aluminum 7075 alloy. International Journal of Material Science and Research. 2019;2(2):50–55. doi:10.18689/ijmsr-1000108
- Reschetnik W, Brüggemann J, Aydinöz ME, et al. Fatigue crack growth behavior and mechanical properties of additively processed EN AW-7075 aluminium alloy. Procedia Structural Integrity. 2016;2:3040–3048. doi:10.1016/j.prostr.2016.06.380
- Li R, Wang M, Li Z, et al. Developing a high-strength Al-Mg-Si-Sc-Zr alloy for selective laser melting: crack-inhibiting and multiple strengthening mechanisms. Acta Mater. 2020;193:83–98. doi:10.1016/j.actamat.2020.03.060
- Ashokkumar M, Lee J, Iida Y, et al. Spatial distribution of acoustic cavitation bubbles at different ultrasound frequencies. Chemphyschem. 2010;11(8):1680–1684. doi:10.1002/cphc.200901037
- Apfel RE. Acoustic cavitation prediction. J Acoust Soc Am 1978;64.:S1–S63. doi:10.1121/1.2004304
- Ning F, Jiang D, Liu Z, et al. Ultrasonic frequency effects on the melt pool formation, porosity, and thermal-dependent property of inconel 718 fabricated by ultrasonic vibration-assisted directed energy deposition. J Manuf Sci Eng. 2021;143(5):051009. doi:10.1115/1.4048515
- Yang Z, Zhu L, Wang S, et al. Effects of ultrasound on multilayer forming mechanism of inconel 718 in directed energy deposition. Additive Manufacturing. 2021;48:102462. doi:10.1016/j.addma.2021.102462
- Dharmendra C, Hadadzadeh A, Amirkhiz BS, et al. Microstructural evolution and mechanical behavior of nickel aluminum bronze Cu-9Al-4Fe-4Ni-1Mn fabricated through wire-arc additive manufacturing. Additive Manufacturing. 2019;30:100872. doi:10.1016/j.addma.2019.100872
- Wang B, Tan D, Lee TL, et al. Ultrafast synchrotron X-ray imaging studies of microstructure fragmentation in solidification under ultrasound. Acta Mater. 2018;144:505–515. doi:10.1016/j.actamat.2017.10.067
- Ramirez A, Qian M, Davis B, et al. Potency of high-intensity ultrasonic treatment for grain refinement of magnesium alloys. Scr Mater. 2008;59(1):19–22. doi:10.1016/j.scriptamat.2008.02.017
- Baek M, Euh K, Lee K. Microstructure, tensile and fatigue properties of high strength Al 7075 alloy manufactured via twin-roll strip casting. Journal of Materials Research and Technology. 2020;9(5):9941–9950. doi:10.1016/j.jmrt.2020.06.097
- Hall EO. The deformation and ageing of mild steel: II characteristics of the L ders deformation. Proc Phys Soc London Sect B. 1951;64(9):742. doi:10.1088/0370-1301/64/9/302
- Petch NJ. The orientation relationships between cementite and α-iron. Acta Crystallogr. 1953;6(1):96. doi:10.1107/S0365110X53000260
- Hansen N. Hall–petch relation and boundary strengthening. Scr Mater. 2004;51(8):801–806. doi:10.1016/j.scriptamat.2004.06.002