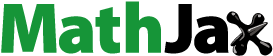
ABSTRACT
White Portland cement is an ideal choice for producing 3D printed coloured composites due to its inherent whiteness. However, the uncontrollable rheological properties limit the establishment of printed structures and thus affect the mechanical properties. In this study, the polyvinyl alcohol (PVA) and polypropylene (PP) fibres were utilised as reinforcement materials in 3D printed white Portland cement composites (WPCCs) to improve the printability and toughness by controlling creep properties, aiming to build better printed structures. Experimental results show that the addition of PVA and PP fibres effectively improve the creep properties of WPCCs, and printed structures can be well built by controlling creep properties. Specifically, the thixotropy of WPCCs with PVA and PP fibre is improved within specific content ranges of 0∼1% and 0.4∼0.8%, respectively. Compared with reference sample, the flexural strength increases by approximately 148.8% and 90.2% when the PVA and PP fibre contents reach 1.25% and 1%, respectively.
1. Introduction
3D printing of construction materials is essentially an additive manufacturing process due to the advantages of non-template, high design freedom and production efficiency, and less dependence on workers [Citation1–3]. However, there remain some issues in 3D printing technology that affect the performances of printed construction materials, which depend on the rheological properties of fresh paste, printing parameters of 3D printer, printing interlayer interval time and extrusion speed [Citation4,Citation5]. The printability of printed materials is an important index that affects the printed structure, including the extrusion performance and stacking performance [Citation6,Citation7]. Excellent printability can ensure lower structural deformation and higher mechanical properties [Citation8,Citation9].
The rheological properties of 3D printed construction materials are deemed as the most directly important factors affecting their printability and mechanical properties [Citation10–12]. When the rheology of the fresh paste is controllable, it allows for stacking without deformation. Conversely, inadequate rheology presents challenges in the extrusion process. As a result, the inadequate rheology of cement-based materials can easily lead to the blockages and solidification within the nozzle. Many researchers have conducted a lot of studies on improving the rheological properties in the application of 3D printed cementitious materials [Citation13–15]. For instance, Zhang et al. [Citation16] studied the rheological parameters by optimising the composition design of printed paste, and calculated the ultimate printing layer thickness and printing speed with dynamic/static yield stress to quantitatively characterise the stacking performance and printing efficiency of 3D printed structures. Creep is a rheological property employed to simulate the deformation of stacked structures under the influence of gravity, which applies minimal forces to ensure the stress remains below the yield stress of the paste or within the linear viscoelastic region (LVR) [Citation17,Citation18]. The structure of 3D printed paste is built by a layer-by-layer manner, which will be slowly affected by its own gravity, extremely related to the creep properties of materials. Chen et al. [Citation19] used the creep protocol to calculated the LVR and static yield stress by the slope variation. Understanding the variation of creep period helps engineers and scientists in designing and optimising the printability and durability of 3D printed paste, ensuring the long-term stability and functionality.
3D printing is a process that converts a three-dimensional digital model into a physical object layer by layer (two-dimensional) using additive manufacturing technology [Citation20,Citation21]. There is often a challenge in achieving optimal compatibility between the printing materials and models in the process of reducing dimensionality, leading to difficulties in controlling the rheological properties and stacking properties of the printed paste. In this case, the printed products present weak interlayer adhesion and anisotropy of mechanical properties [Citation22–24]. To improve the toughness of cement composites, the reinforcement materials such as fibreglass mesh and fibres are usually introduced into 3D printed structures [Citation25–27]. Rajeev et al. [Citation28] evaluated the feasibility of utilising recycled fibres from face mask waste as a reinforcement for 3D concrete printing applications to enhance printability, founding that the mechanical performance of recycled and PP fibres was comparable at a dosage of 1%. Giwa et al. [Citation29] conducted a study on the properties of printing mixtures containing various dosages of steel fibres, and founding that the mechanical properties of the reinforced mixtures presented significant improvement at high fibre dosages, specifically at 2% and 2.5% volume. Current research indicates that to ensure the orderly arrangement of fibres in 3D printed cement-based materials, two requirements are proposed for the fibres: the fibres should possess greater stiffness and the length of the fibres should be greater than the diameter of the printing nozzle [Citation30]. To achieve the goal of fibre reinforcement, using piezoelectric sensors, as suggested by Quah et al., may be a viable option for monitoring changes in toughness and the orderly arrangement of fibres [Citation31]. Despite research findings on the orientation and properties of fibre-reinforced 3D printed cement composites, the exploration of 3D printed WPCCs with good printability is still relatively recent. In addition, fibre can usually increase the overall stability and bearing capacity of cement-based materials composites effectively, thereby slowing down the creep deformation rate of paste and improving the printed structures under long-term loads.
Compared with ordinary Portland cement, white Portland cement is an excellent choice to produce lighter colours, making it well-suited for applications where aesthetics is important. Additionally, white Portland cement can improve colour consistency and can be easily tinted to achieve a wide range of colours, providing greater design flexibility in 3D printed cement composites. Furthermore, its finer particle size distribution can contribute to enhanced surface finish and detail resolution in printed objects. In this study, the PP and PVA fibres were utilised as reinforced materials in 3D printed WPCCs, aiming to improve the structure stability and toughness by controlling the creep properties. The relationship between structure deformation and creep parameters was examined. Based on the controlled printed structures, another aspect of the study involved analysing the effect of PP and PVA fibres on the flexural strength of printed samples. The use of PVA and PP fibres is an effective solution to improve the rheological properties, toughness and printed structures of 3D printed WPCCs, which shows a considerable potential in 3D printed coloured and decorated cement composites.
2. Experimental materials and methods
2.1. Raw materials and preparation procedurals
The studied fibre-reinforced 3D printed WPCCs include 10 components based on previous research [Citation32–34]. The used cementitious material is white Portland cement (WPC) with 42.5 grade produced by Albo Co., Ltd. The calcium formate (CF, analytical reagent, Shanghai Macklin Biochemical Technology Co., Ltd) with a purity greater than 96% was used as coagulant accelerator. Redispersible emulsion powder (EVA, type 6022E, Baochen Chemical Co., Ltd) was used as the rheology modifier and the basic properties are shown in . Tributyl phosphate (TP, Shanghai Macklin Biochemical Technology Co., Ltd) was used as defoaming agent. Hydroxypropyl methyl cellulose ether (HPMC, 100,000 mPa·s, Heda Co., Ltd) was used as the thickener. Superplasticiser (polycarboxylic acid, Shandong Building Science Academy Co., Ltd) with a water reducing rate of 32% was used to improve the flowability of 3D printed paste. Nano silicon dioxide with an average particle size of 20 nm were used to improve rheological properties of 3D printed paste. The introduction of PVA and PP fibres with the length of 6 mm and the average filament diameter of 31 and 50 μm into 3D printed WPCCs improved the buildability and toughness, and the micro morphologies were shown in .
Figure 1. (a, b) SEM images of PVA and PP fibres and (c, d) SEM images of PVA and PP fibres in the 3D printed WPCCs.
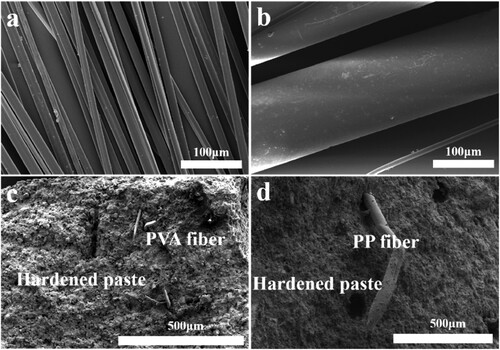
Table 1. Physical properties of redispersible emulsion powder.
The mix design of 3D printed WPCCs in this study is shown in , and the preparation procedural is as follows:
The nano SiO2, superplasticiser and part of water are ultrasonic dispersed for 10 min to prepare liquid mixture A;
The fibres, defoaming agent and remaining water are stirred and dispersed to obtain a liquid mixture B at a speed of 142 rpm for 2 min;
The CF, EVA powder, HPMC and cement particles are dry mixed in a V-shape mixer with a speed of 32 rpm for 2 min to prepare a solid powder mixture C;
The above-prepared liquid mixture A and B were stirred with the solid mixture C at a speed of 285 rpm for 2 min to prepared the fresh paste, and then it was poured into the 3D printer to print according to the pre-set procedure;
The printed sample was placed in a standard curing chamber for 3 days at a temperature of 20°C and a relative humidity of 95%.
Table 2. The mix design of 3D printed WPCCs/%.
2.2. 3D printer
The tested samples were prepared by using the 3D printer (Pottery artist) from Yueyang Dianfeng Technology Co., Ltd, as shown in (a), and the size of 3D printer is 0.88 m × 1.04 m × 1.08 m (width, height and length). The designed sample is a rectangular shape with the dimensions of 25 mm × 25 mm × 70 mm (width, height and length). The 3D printer is equipped with a nozzle diameter of 2.5 mm and the number of printed layers was determined to be 10. To ensure a continuous extrusion, the safety air pump pressure changes with the variation of paste state. In addition, the loading and feed speed were set at 15 and 10 mm/s, respectively. Additionally, a large structure was printed using the 3D printer system (HC-3DPRT/D) with printing size of 1.08 m × 1.18 m × 1.11 m (width, height and length) and the nozzle diameter of 15 mm from Jianyan Huace Technology Co., Ltd, as shown in (b,c).
2.3. Testing methods
2.3.1. Rheological measurements
In this study, the rotational rheometer HAAKE MARS 40 (produced by Thermo Fisher Scientific Inc.) is used to test the rheological properties. The temperatures for all testing procedures are controlled at 20°C. The tested rheological properties include static yield stress, compliance, zero shear viscosity, elastic modulus and thixotropy based on the creep protocol. A four-paddle rotor system with the diameter of 22 mm is used for the creep test, and the test procedure is as follows: (1) the prepared 3D printed paste is pre-sheared at 50 s−1 for 30 s; (2) rest for 2 min; (3) and apply a constant shear stress for 60s; (4) Remove the shear stress and observe the structural recovery after resting for 60 s; (5) Repeat steps (1)∼(4) until the yield stress is exceeded.
A typical creep and recovery curve are shown in . In the creep stage, the strain increases with time, and γ0 represents the initial strain. The static yield stress was obtained once the slope of curves occurs a large variation. The thixotropy (γr/γr + i) can be calculated from strain of creep and recovery period. The paste will produce small plastic deformation in the creep process, and elastic hysteresis can be avoided once the shear stress is maintained for a period of time, in this case, the elastic modulus is the ratio of the applied shear stress to the strain. In addition, the compliance is the reciprocal of the elastic modulus, that is, the deformation rate of the paste per unit of stress. Besides, the initial shear stress is small, which cannot exceed the structure strength, and the viscosity is high. Zero shear viscosity (η0) is the viscosity when the shear rate is infinitely close to zero, which represents the initial structure strength of paste.
2.3.2. Printability tests
Printability typically includes extrudability and buildability. In this study, buildability is characterised by the deformation rate of a printed structure, which is typically calculated by measuring the average deformation from length, width and height. This measurement helps assess the structural integrity and dimensional accuracy of the printed samples, which are crucial factors in determining its buildability. The formula for calculating the deformation rate is as follows:
(1)
(1) where D is the deformation rate of the printed structure,
,
and
is the original size of the digital model,
,
and
is the size of the stacked structure.
Extrudability is determined by the air pump delivery system integrated into the printer. The initially set rotation speed of the printer screw and the extrusion pressure of air pump are controlled to ensure that the diameter of the extrusion paste matches precisely with the outer diameter of the extrusion head. The extrusion pressure at this point is considered the optimal extrusion pressure, enabling efficient and consistent extrusion of the printed paste.
2.3.3. Flexural strength
After printing, the sample was left to cure for three days at a temperature of 20°C and a relative humidity of 95%, and then processed into a test size by using a precision cutting machine (Q-100, Xinjie Electric Co., Ltd) with a flexural strength sample size of 20 × 20 × 60 (mm), and the cutting speed is 0.5 mm/s. The flexural strength was then measured using an MTS universal testing machine from the United States under a loading speed of 0.3 KN/s and measuring range of 10 ∼ 300 KN.
3. Results and discussion
3.1. Creep and recovery period of 3D printed WPCCs
3.1.1. Typical creep and recovery curves
Creep and recovery are two important phenomena observed in the 3D printed cement paste, which are commonly used in studying the flowability of paste [Citation35]. shows the effect of PVA fibre on the creep and recovery period of 3D printed WPCCs, indicating that the paste undergoes large elastic deformation initially, followed by a slow and continuous linear increase of deformation. Cement paste contains a complex microstructure consisting of interlocking particles, pores, water and hydration products. Under constant shear stress, the paste occurs the deformation in the LVR due to the temporary rearrangement of particles, hydration products or molecular structures, resulting in creep deformation. Meanwhile, the strain increases gradually as the increasing of applied shear stress. Once the stress exceeds the critical value, the strain presents a non-linear increase or largely variation, and the applied shear stress at this time is the maximum stress value in (a–f), meaning that the paste deforms beyond the LVR. The paste state changes from solid-like to liquid-like, and it occurs the flow phenomenon. (a–f) show the strain of 3D printed WPCCs under same applied shear stress decreases significantly when the PVA fibre contents increase to 1%, and then increases. The reason is that the presence of hydrophilic groups on the surface of PVA fibres enables strong bonding with hydration products, leading to improved adhesion. Consequently, high applied shear stress is necessary to enable the flow of paste [Citation36,Citation37]. Furthermore, the greater number of fibre filaments increases the probability of interlocking or entangling among the fibres, leading to improved structural integrity. These factors collectively contribute to enhanced resistance against external stress, ultimately resulting in reduced strain. However, reaching a critical fibre content might lead to fibre aggregation, which can introduce defects in the cement paste and promote paste flow, ultimately leading to decreased strain [Citation38,Citation39].
Figure 4. Typical creep curves of 3D printed WPCCs with different contents of PVA fibre: (a) Ref., (b) 0.25%, (c) 0.5%, (d) 0.75%, (e) 1.00%, (f) 1.25%.
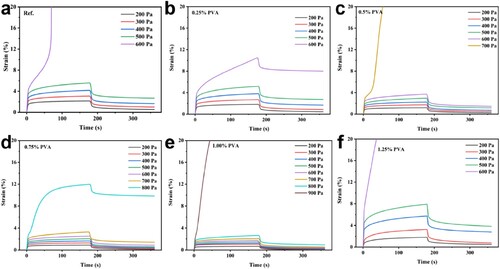
During the recovery period, the strain first drops partially, and then slowly decreases to the basic equilibrium when the applied constant stress is removed, as shown in (a–f). The reason is that the interactions between microstructural components of cement paste facilitate the reorganisation and restoration of the original structure, enabling the recovery. The presence of fibres also contributes to enhanced strength and ductility of printed cement paste, which is beneficial for withstanding the residual stresses and loadings that occur during the recovery phase. In the LVR, the relationship between stress and strain is linear, meaning that the strain of paste is elastic and reversible. However, as the applied stress exceeds the LVR, the paste undergoes large deformation. At this point, the strain of paste becomes non-linear and it starts to exhibit permanent deformation or plasticity.
shows the effect of PP fibre on the creep and recovery period of 3D printed WPCCs, presenting a similar tendency to that of PVA fibre. As shown in (a–f), the strain of paste shows a trend of first increasing when the PP fibre increases to 0.8% and then decreasing. The surface structure of the fibres plays a role in enhancing the bond between the fibres and the cement matrix. When the fibre content is higher, there is a greater probability of contact between the fibres and the surrounding cementitious material. The surface of PP fibre presents the hydrophobic nature, and the effective of resisting flow is lower than PVA fibre [Citation30]. Additionally, the mechanical interlocking or entangling of PP fibre filaments within 3D printed WPCCs can contribute to the increase in the critical shear stress. As the fibres are dispersed throughout the cement matrix, the fibres can resist deformation by transferring the applied force to adjacent fibres under the external stress, creating a mechanical interlocking effect [Citation38].
3.1.2. Yield stress
Creep period applies minimal forces to ensure the stress remains below the yield stress of the paste or within the LVR. A large change in strain means that the applied shear stress exceeds the LVR, and the critical shear stress can be considered as the yield stress. shows the yield stress of 3D printed WPCCs with different contents of PVA and PP fibre, indicating that the yield stresses increase to the maximum value of 810 and 890 Pa when the contents of PVA and PP fibre reach 1% and 0.8%, respectively. This phenomenon is similar to relevant reference [Citation40] and can be attributed to the mechanical interlocking or entangling of PVA and PP fibres, which provide resistance to the flow of the paste, thereby increasing the yield stress. The presence of fibres can improve the cohesion and internal friction of the cement paste, leading to an increase in yield stress. Nonetheless, once the contents of PVA and PP fibres exceed a certain threshold, the occurrence of agglomeration will introduce defects into the WPCCs, leading to a reduction in yield stress.
3.1.3. Zero shear viscosity
Zero shear viscosity is the viscosity when the shear rate is infinitely close to zero, which represents the initial structure strength of paste [Citation41,Citation42]. shows the zero shear viscosity of WPCCs with different contents of PVA and PP fibre under creep stress of 200 and 300 Pa, presenting that the zero shear viscosity increases to the maximum value first as the PVA fibre contents increase to 0.8% and then decreases gradually. The reason is that the likelihood of fibre mechanical interlocking increases as the increase of fibre contents [Citation43]. Consequently, a more stable network structure is formed, and the hydrophilic component of PVA fibre further increases the viscosity, implying an enhanced buildability [Citation36]. However, once PVA fibre content reaches a certain range, the aggregation phenomenon occurs between the fibres, which lead to the reduction in the ability of the fibres to resist paste flow [Citation39,Citation44]. For PP fibre, the zero shear viscosity decreases first when the PP fibre content increases to 0.2%. The reason is that the hydrophobic nature of PP fibre reduces its tendency to intertwine. Under the influence of creep stress, the fibre is prone to disrupting the internal flocculated structure of the cement paste and aligning along the direction of the creep stress, leading to a loss of shear resistance. Therefore, the zero shear viscosity will reduce when the content of PP fibre is low.
Figure 7. Zero shear viscosity of 3D printed WPCCs with different PVA and PP fibre contents under creep stress of 300 Pa.
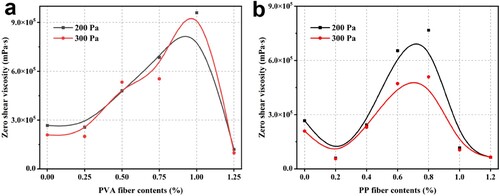
As PP fibre content further increases, the zero shear viscosity increases and finally decreases, the more network structure will be formed between the fibres to stable cement paste. However, once PP fibre content is too high, the aggregation phenomenon occurs between the fibres, resulting in the reduction of effective fibres, and the flow resistance of paste begins to decrease.
3.1.4. Compliance
The compliance of 3D printed cement paste refers to its capacity to deform or withstand stress under the external load. It should be noted that the appropriate compliance is crucial as higher compliance enhances deformability and flexibility, but excessive compliance may compromise structural integrity and stability. Thus, the optimisation of various factors is imperative to attain desired compliance for specific applications of 3D printed cement paste. shows the compliance variation of WPCCs with PVA fibres under different applied shear stress, indicating that the compliance the compliance increases linearly with time at the relatively low shear stress and starts to increase sharply until it exceeds a critical stress. The compliance of samples changes little when the creep stress is below 500 Pa and the compliance of reference sample increases sharply when the creep stress is larger than 600 Pa. The reason is that the paste structure changes little at lower creep stress in the LVR. However, the internal structure of cement paste is destroyed under high creep stress, and the state of cement paste changes from viscoelastic solid to liquid. Additionally, the compliance decreases as the PVA fibre content increases to 1% and then increases. The reason is that the fibres will impede the flow spread of fresh paste within the formed network space structure [Citation45]. As a result, the strain generated under the influence of creep stress decreases gradually. Furthermore, the surface of PVA fibre contains numerous hydrophilic groups that presents the ability to absorb free water, thereby enhancing the friction between cement particles [Citation38]. However, when the content of PVA fibre becomes excessively high, the fibres tend to aggregate together, causing a decrease in the effective number of fibres and diminishing the resistance effect [Citation36].
shows the compliance variation of WPCCs with PVA fibres under applied shear stress, indicating that the compliance increases first and then decreases as the PP fibre contents increase to 0.8%, and finally increases. Different from PVA fibre, PP fibre is characterised by stiffness and low propensity for entanglement. Once the PVA fibre content is relatively low, the hydrophobic surface of PP fibre hampers its interaction with cement paste under the influence of creep stress, potentially increase the paste deformation. Compared with PVA fibre, even a small creep stress can cause significant changes in the compliance of the paste with PP fibre. Additionally, the probability of crosslinking structures forms between fibres increases with the PP fibre content further increases, leading to a more stable network structure [Citation45]. The reason is that the fibres act as reinforcement within the cement paste matrix, effectively distributing applied loads and enhancing the ability of paste to resist deformation [Citation39]. However, when PP fibre content is excessively high, the aggregation between the fibres can occur, which reduces the resistance effect provided by PP fibre [Citation46].
3.1.5. Thixotropy
Recovery property refers to the ability of the paste to return to its original shape or dimensions after the removal of the applied load or stress, which represents the elastic response of the paste to recover its initial structure, extremely related to thixotropy. Therefore, the thixotropy refers to the property of certain materials to exhibit a time-dependent decrease in stain or resistance to flow under constant stress, followed by a recovery of stain when the stress is removed. In this study, the creep stress of 200 Pa and300 Pa belonged to the LVR were selected to investigate the thixotropy. (a,b) show the creep and recovery behaviour of WPCCs with PVA fibres under creep stress of 200 and 300 Pa, presenting that the initial elastic deformation (γ0) and recovery deformation (γr) induced by creep and recovery process both exhibit a trend of decreasing initially, followed by an increase with the PVA fibre content increases. The minimum value was obtained at a PVA fibre content of 1% when the applied creep stress is within the LVR range and the paste structure remains undamaged. (c) shows the effect of PVA fibre contents on thixotropy of 3D printed WPCCs obtained from the creep and recovery process. When the PVA fibre content ranges from 0% to 1%, the thixotropy gradually increases as the PVA fibre content increases. At 1% PVA fibre content, the thixotropy reaches its maximum values of 95% and 87%, respectively. The fibres can form a network structure within the paste that impedes the flow of the matrix, and it also can contribute to the thixotropic behaviour by increasing the viscosity of the paste and preventing excessive deformation during creep [Citation47]. However, when the PVA fibre content exceeds 1%, the thixotropy of the paste starts to rapidly decrease, which is attributed to the reduction of effective fibre filament [Citation48]. In this case, the deformation of creep period begins to increase and the recovery defamation decreases.
Figure 10. Creep and recovery behaviour of WPCCs with PVA fibres under the applied shear stress of (a) 200 Pa and (b) 300 Pa; (c) Effect of PVA fibre contents on thixotropy of WPCCs.
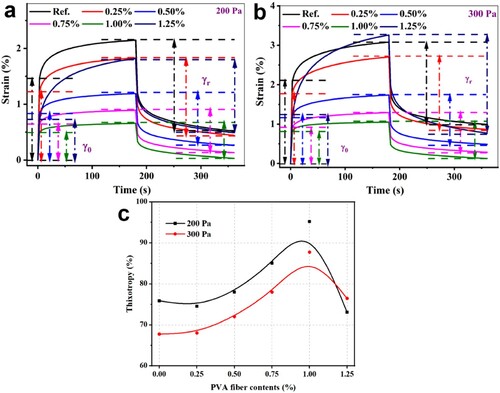
(a,b) shows the creep and recovery behaviour of WPCCs with PP fibre under creep stress of 200 Pa and300 Pa. Different with PVA fibre, the initial elastic deformation and recovery deformation increase first until the PP fibre contents reached 0.2%. This phenomenon is attributed to the poor bonding ability between the cement paste and lower PP fibre content, which results in a higher tendency for the fibres to flow together with the WPCCs in the direction of movement. Thereafter, the initial elastic deformation and recovery deformation decreases and finally increases. It should be noted that the initial elastic deformation and recovery deformation of WPCCs with PP fibres is much larger than that with PVA fibre, which indicated that 3D printed WPCCs with PP fibres is easy to occur deformation under the same creep stress. (c) illustrates the influence of PP fibre contents on the thixotropy of 3D printed WPCCs, as observed through creep and recovery process, demonstrating that the thixotropy initially decreases, followed by an increase, and ultimately decreases again as the PP fibre content increases. Notably, when the PP fibre content reaches 0.2%, the thixotropy reaches its minimum value of 52%.
3.1.6. Elastic modulus
Elastic modulus is a fundamental material property that quantifies the stiffness and deformation behaviour of paste [Citation49,Citation50]. For 3D printed concrete, the elastic modulus can be used to explain the structure build-up by describing how the paste responds to external forces. By controlling the elastic modulus of cement paste, it is possible to adjust the strength and flexibility of structure. presents the effect of PVA and PP fibre on elastic modulus of 3D printed WPCCs. In (a), as the PVA fibre content increases, the elastic modulus of 3D printed WPCCs displays an initial increase followed by a decrease. Specifically, when the PVA fibre content reaches 1%, the elastic modulus under creep stress of 200 and 300 Pa increases from 13,606 Pa to 40,160 and 9565 Pa to 24,330 Pa, respectively, indicating a significant improvement in stiffness. As PVA fibre content exceeds 1%, the elastic modulus begins to decrease sharply. The elastic modulus is mainly produced by the hydration products, such as C–S-H gel and ettringite, which is the reflection of the microstructure between the hydration products [Citation51]. In the absence of PVA fibre agglomeration, the increase of PVA fibre content will result in a more stable entwining structure between the fibres, which enhances the interaction between the PVA fibre and hydration products, leading to a greater elastic modulus [Citation52]. Different with PVA fibre, the elastic modulus decreases from 13,606 Pa to 6446 Pa when the content of PP fibre is relatively low. This result is attributed to the low probability of crosslinking structures formed between the fibres, and the surface hydrophobicity of PP fibre can contribute to a reduction in the elastic modulus [Citation53].
3.2. Printability of 3D printed WPCCs
In this study, the structure deformation and required air pressure were used to investigate the extrudability and buildability, respectively. The effect of PVA fibre on the printability of WPCCs is shown in (a), presenting that the structure deformation decreases with the increase of the PVA fibre content. As the content of PVA fibre increases from 0 to 1.25%, the final structure deformation of 3D printed WPCCs decreases from 8.93% to 3.38%. Additionally, when the content of PVA fibre exceeds 0.75%, the stacking structure cannot present any deformation in the first five minutes. (b) shows the required air pressure of 3D printed WPCCs with different PVA fibre content, indicating that the optimal extrusion pressure of 3D printed WPCCs increases first and then decreases with the increase of the PVA fibre content. When the content of PVA fibre is 1%, the optimal extrusion pressure reaches the maximum value of 0.17 MPa, but the paste still presents good extrudability. The macrographs of 3D printed WPCCs with 0%, 0.5% and 1% of PVA fibre were shown in (c–e).
Figure 13. (a) Effect of PVA fibre on the structure deformation of 3D printed WPCCs; (b) the required air pressure of 3D printed WPCCs with different PVA fibre content; (c) (d) (e) the macrographs of 3D printed WPCCs with 0%, 0.5% and 1% of PVA fibre.
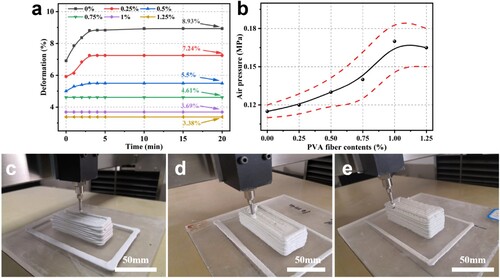
(a) shows the effect of PP fibre on the printability of 3D printed WPCCs, demonstrating that the structure deformation initially increases and then decreases. At low PP fibre content, there remains a lower probability of interlocking or entangling among fibre filaments. The hydrophobic nature of PP fibre hampers rheological improvement, resulting in a slight increase in structure deformation. Furthermore, when the fibre length is shorter and its content is lower, there is a greater occurrence of colloidal microstructure damage during the premixing process, which intensifies the tendency for flow along the direction of movement within the paste, leading to poorer resistance to deformation [Citation40]. When the PP fibre content exceeds 0.6%, the stacking structure exhibits no structural deformation within the first five minutes. As the number of fibre filaments increases, there is a higher likelihood of interlocking or entanglement between the fibres, leading to greater cross-linking and interaction between the hydration products and the fibres. Consequently, the paste exhibits enhanced resistance to deformation, showing a stronger ability to withstand structural changes [Citation30]. Additionally, the optimal extrusion pressure of the paste initially decreases and then increases with an increase in PP fibre content, as shown in (b). When the PP fibre content reaches 1%, the optimal extrusion pressure reaches its maximum value of 0.16 MPa. However, even at low extrusion pressure, the printed paste can still be extruded. It is important to note that the required extrusion pressure will exceed the safe pressure range of 0.2–0.4 MPa when the PP fibre content exceeds 1%. Considering the results of printability, 3D printed WPCCs with PVA fibre exhibit better printability compared to that with PP fibre, which is attributed to the surface nature of PVA fibre. Additionally, when PVA and PP fibre content is greater than 1% and 0.8%, respectively, the structure deformation reduced, but the creep properties become worse. The reason is that the adsorption on the surface of fibre will significantly affect the extrudable and constructable performance, and improve green strength of the printed paste, which can withstand the variation of gravity in the extrusion process. Therefore, creep properties may not be the key factor affecting the deformation of printed structure, and other rheological properties could play a more significant role.
3.3. Relationship of creep properties and structure deformation
Based on the above results, the structure deformation or printability is affected by the creep properties obviously. Therefore, controlling the creep properties can reduce structural deformation, which is closely related to yield stress, thixotropy, zero shear viscosity and elastic modulus. shows the relationship of creep properties and structure deformation of WPCCs. It should be noted that the relationship was discussed when the PVA and PP fibre contents are smaller than 1% and 0.8%, respectively. Here, the yield stress in (a) derives from typical creep curves, the zero shear viscosity in (b) is calculated from the compliance curves under shear stress of 200 Pa, thixotropy in (c) is calculated from the creep and recovery curves under shear stress of 200 Pa, and the elastic modulus in (d) is obtained from creep period under shear stress of 200 Pa. Based on the results of (a–d), the structure deformation of 3D printed PP fibre-reinforced WPCCs correlates well with the creep properties compared with that of 3D printed PVA fibre-reinforced WPCCs.
3.4. Mechanical strength of 3D printed WPCCs
The 3D printing process of paste typically involves two stages: pumping and extrusion. During these stages, the fibres in the paste were aligned along the flow direction. This alignment significantly enhances the utilisation efficiency of fibre and results in a better toughening effect compared with traditional casting moulding methods. shows the effect of PVA and PP fibre on the flexural strength of WPCCs, exhibiting that flexural strength increases with the increase of PVA and PP fibre contents. The flexural strength of WPCCs with PVA fibre increases about 25.6%, 45.1%, 81.7%, 114.6% and 148.8% when the PVA contents increase from 0.25 to 1.25%, and the highest flexural strength can reach to 7.7 MPa. This is similar to the results of Liu et al., and the highest flexural strength can reach 6.8 MPa under the optimal PVA fibre content of 0.5% for 3D printed PVA fibre reinforced concrete [Citation54]. For PP fibre, the flexural strength increases about 14.6%, 40.1%, 57.1%, 82.1% and 90.2% when the PVA contents increase from 0.2 to 1%. The reason is that the bridging effect provided by the fibre combined with the excellent elongation allows for the absorption of energy released during cracking, effectively preventing crack propagation, and the directional arrangement achieved through the 3D printing process contributes to the toughening effect of fibre [Citation43,Citation55,Citation56]. Additionally, the surface structure of the PVA fibre and the strong interfacial adhesion between the fibre and matrix further enhance the bridging effect, making the toughening effect of PVA fibre in the 3D printed WPCCs superior to that of PP fibre [Citation44,Citation57].
4. Conclusions
In this study, the PP and PVA fibres were utilised as reinforced materials in 3D printed WPCCs to improve the structure stability and toughness by controlling the creep properties. The main conclusions are obtained regarding the effect of PVA and PP fibres on the creep properties, printability and toughness of 3D printed WPCCs.
Based on the creep and recovery protocol, the incorporation of PVA and PP fibres can effectively increase the yield stress, zero shear viscosity and elastic modulus. In addition, the thixotropy of WPCCs with PVA and PP fibre was improved in the content of 0∼1% and 0.4∼0.8%, respectively.
As PVA and PP fibre contents increase to 1.25 and 1%, the structure deformation decreases to 3.38 and 4.69%, respectively, and the required extrusion pressure are smaller than the safe pressure.
The structure deformation of 3D printed PP fibre-reinforced WPCCs exhibits a stronger correlation with creep properties compared to that of 3D printed PVA fibre-reinforced WPCCs when the PVA and PP fibre contents are smaller than 1% and 0.8%
Compared to reference sample, the flexural strength of 3D printed WPCCs with PVA fibre increases about 25.6%, 45.1%, 81.7%, 114.6% and 148.8% when the PVA contents increase from 0.25 to 1.25%. For PP fibre, the flexural strength increases about 14.6%, 40.1%, 57.1%, 82.1% and 90.2% when the PVA contents increase from 0.2 to 1%.
This study mainly focusses on the printability and mechanical properties of fibre-reinforced WPCCs, but its durability and interface properties of fibre-reinforced cement composites still need to be further studied and improved. In particular, the relationship between rheological parameters, durability and bonding properties between layers will be studied in the future.
Disclosure statement
No potential conflict of interest was reported by the author(s).
Data availability statement
The authors confirm that the data supporting the findings of this study are available within the article.
Additional information
Funding
References
- Ding T, Xiao J, Mechtcherine V. Microstructure and mechanical properties of interlayer regions in extrusion-based 3D printed concrete: a critical review. Cem Concr Compos. 2023;141:105154. doi:10.1016/j.cemconcomp.2023.105154
- Tay Y, Lim S, Phua S, et al. Exploring carbon sequestration potential through 3D concrete printing. Virtual Phys Prototy. 2023;18:e2277347. doi:10.1080/17452759.2023.2277347
- Chen M, Li L, Zheng Y, et al. Rheological and mechanical properties of admixtures modified 3D printing sulphoaluminate cementitious materials. Constr Build Mater. 2018;189:601–611. doi:10.1016/j.conbuildmat.2018.09.037
- Salet TA, Ahmed ZY, Bos FP, et al. Design of a 3D printed concrete bridge by testing. Virtual Phys Prototy. 2018;13(3):222–236. doi:10.1080/17452759.2018.1476064
- Xiao J, Ji G, Zhang Y, et al. Large-scale 3D printing concrete technology: current status and future opportunities. Cem Concr Compos. 2021;122:104115. doi:10.1016/j.cemconcomp.2021.104115
- Chen Y, Zhang Y, Pang B, et al. Extrusion-based 3D printing concrete with coarse aggregate: printability and direction-dependent mechanical performance. Constr Build Mater. 2021;296:123624. doi:10.1016/j.conbuildmat.2021.123624
- Jiang Q, Liu Q, Wu S, et al. Modification effect of nanosilica and polypropylene fiber for extrusion-based 3D printing concrete: printability and mechanical anisotropy. Addit Manuf. 2022;56:102944.
- Liu Y, Wang L, Yuan Q, et al. Effect of coarse aggregate on printability and mechanical properties of 3D printed concrete. Constr Build Mater. 2023;405:133338. doi:10.1016/j.conbuildmat.2023.133338
- Ibrahim KA, van Zijl GP, Babafemi AJ. Influence of limestone calcined clay cement on properties of 3D printed concrete for sustainable construction. J Build Eng. 2023;69:106186. doi:10.1016/j.jobe.2023.106186
- Tay YWD, Ting GHA, Qian Y, et al. Time gap effect on bond strength of 3D-printed concrete. Virtual Phys Prototy. 2019;14(1):104–113. doi:10.1080/17452759.2018.1500420
- Wang C, Chen B, Vo TL, et al. Mechanical anisotropy, rheology and carbon footprint of 3D printable concrete: a review. J Build Eng. 2023: 107309. doi:10.1016/j.jobe.2023.107309
- Arunothayan AR, Nematollahi B, Khayat KH, et al. Rheological characterization of ultra-high performance concrete for 3D printing. Cem Concr Compos. 2023;136:104854. doi:10.1016/j.cemconcomp.2022.104854
- Xu Z, Zhang D, Li H, et al. Effect of FA and GGBFS on compressive strength, rheology, and printing properties of cement-based 3D printing material. Constr Build Mater. 2022;339:127685. doi:10.1016/j.conbuildmat.2022.127685
- Zhao Z, Chen M, Jin Y, et al. Rheology control towards 3D printed magnesium potassium phosphate cement composites. Compos Part B-Eng. 2022;239:109963. doi:10.1016/j.compositesb.2022.109963
- Souza MT, Ferreira IM, de Moraes EG, et al. Role of chemical admixtures on 3D printed Portland cement: assessing rheology and buildability. Constr Build Mater. 2022;314:125666. doi:10.1016/j.conbuildmat.2021.125666
- Zhang Y, Jiang Z, Zhu Y, et al. Effects of redispersible polymer powders on the structural build-up of 3D printing cement paste with and without hydroxypropyl methylcellulose. Constr Build Mater. 2021;267:120551. doi:10.1016/j.conbuildmat.2020.120551
- Kolawole JT, Combrinck R, Boshoff WP. Rheo-viscoelastic behaviour of fresh cement-based materials: cement paste, mortar and concrete. Constr Build Mater. 2020;248:118667. doi:10.1016/j.conbuildmat.2020.118667
- Zhao Z, Chen M, Zhong X, et al. Effects of bentonite, diatomite and metakaolin on the rheological behavior of 3D printed magnesium potassium phosphate cement composites. Addit Manuf. 2021;46:102184.
- Chen M, Liu B, Li L, et al. Rheological parameters,: thixotropy and creep of 3D-printed calcium sulfoaluminate cement composites modified by bentonite. Compos Part B-Eng. 2020;186:107821. doi:10.1016/j.compositesb.2020.107821
- Ju Y, Wang L, Xie H, et al. Visualization of the three-dimensional structure and stress field of aggregated concrete materials through 3D printing and frozen-stress techniques. Constr Build Mater. 2017;143:121–137. doi:10.1016/j.conbuildmat.2017.03.102
- Sacks R, Barak R. Impact of three-dimensional parametric modeling of buildings on productivity in structural engineering practice. Automat Constr. 2008;17(4):439–449. doi:10.1016/j.autcon.2007.08.003
- Panda B, Paul SC, Tan MJ. Anisotropic mechanical performance of 3D printed fiber reinforced sustainable construction material. Mater Lett. 2017;209:146–149. doi:10.1016/j.matlet.2017.07.123
- Yang Y, Wu C, Liu Z, et al. Mechanical anisotropy of ultra-high performance fibre-reinforced concrete for 3D printing. Cem Concr Compos. 2022;125:104310. doi:10.1016/j.cemconcomp.2021.104310
- Liu C, Xiong Y, Chen Y, et al. Effect of sulphoaluminate cement on fresh and hardened properties of 3D printing foamed concrete. Compos Part B-Eng. 2022;232:109619. doi:10.1016/j.compositesb.2022.109619
- Zhang Y, Zhu Y, Ren Q, et al. Comparison of printability and mechanical properties of rigid and flexible fiber-reinforced 3D printed cement-based materials. Constr Build Mater. 2023;400:132750. doi:10.1016/j.conbuildmat.2023.132750
- Ma G, Li Z, Wang L, et al. Mechanical anisotropy of aligned fiber reinforced composite for extrusion-based 3D printing. Constr Build Mater. 2019;202:770–783. doi:10.1016/j.conbuildmat.2019.01.008
- Shakor P, Nejadi S, Paul G, et al. Effects of different orientation angle, size, surface roughness, and heat curing on mechanical behavior of 3D printed cement mortar with/without glass fiber in powder-based 3DP. 3D Print Addit Manuf. 2023;10(2):330–355. doi:10.1089/3dp.2021.0067
- Rajeev P, Ramesh A, Navaratnam S, et al. Using fibre recovered from face mask waste to improve printability in 3D concrete printing. Cem Concr Compos. 2023;139:105047. doi:10.1016/j.cemconcomp.2023.105047
- Giwa I, Game D, Ahmed H, et al. Performance and macrostructural characterization of 3D printed steel fiber reinforced cementitious materials. Constr Build Mater. 2023;369:130593. doi:10.1016/j.conbuildmat.2023.130593
- Teixeira RS, Santos SF, Christoforo AL, et al. Extrudability of cement-based composites reinforced with curauá (Ananas erectifolius) or polypropylene fibers. Constr Build Mater. 2019;205:97–110. doi:10.1016/j.conbuildmat.2019.02.010
- Quah T, Vo T, Tay Y, et al. Real time assessment of smart concrete inspection with piezoelectric sensors. Electronics. 2023;12:3762. doi:10.3390/electronics12183762
- Xu J, Chen M, Zhao Z, et al. Printability and efflorescence control of admixtures modified 3D printed white Portland cement-based materials based on the response surface methodology. J Build Eng. 2021;38:102208. doi:10.1016/j.jobe.2021.102208
- Jin Y, Zhou X, Chen M, et al. High toughness 3D printed white Portland cement-based materials with glass fiber textile. Mater Lett. 2022;309:131381. doi:10.1016/j.matlet.2021.131381
- Jin Y, Xu J, Li Y, et al. Rheological properties, shape stability and compressive strength of 3D printed colored cement composites modified by needle-like pigment. Addit Manuf. 2022;57:102965.
- Qian Y, Kawashima S. Use of creep recovery protocol to measure static yield stress and structural rebuilding of fresh cement pastes. Cem Concr Res. 2016;90:73–79. doi:10.1016/j.cemconres.2016.09.005
- Hu D, Guo Z, Jun T, et al. A novel hydrophilic PVA fiber reinforced thermoplastic polyurethane materials for water-lubricated stern bearing. Fiber Polym. 2021;22:171–183. doi:10.1007/s12221-021-0013-2
- Wang J, Dai Q, Si R, et al. Investigation of properties and performances of polyvinyl alcohol (PVA) fiber-reinforced rubber concrete. Constr Build Mater. 2018;193:631–642. doi:10.1016/j.conbuildmat.2018.11.002
- Kuder KG, Ozyurt N, Mu EB, et al. Rheology of fiber-reinforced cementitious materials. Cem Concr Res. 2007;37:191–199. doi:10.1016/j.cemconres.2006.10.015
- Cao M, Wang C, Chen P, et al. Preparation and performance of the modified high-strength/high-modulus polyvinyl alcohol fiber/polyurethane grouting materials. Constr Build Mater. 2018;168:482–489. doi:10.1016/j.conbuildmat.2018.02.173
- Chen M, Yang L, Zheng Y, et al. Rheological behaviors and structure build-up of 3D printed polypropylene and polyvinyl alcohol fiber-reinforced calcium sulphoaluminate cement composites. J Mater Res Technol. 2021;10:1402–1414. doi:10.1016/j.jmrt.2020.12.115
- Han F, Pu S, Zhou Y, et al. Effect of ultrafine mineral admixtures on the rheological properties of fresh cement paste: a review. J Build Eng. 2022;51:104313. doi:10.1016/j.jobe.2022.104313
- Bessaies-Bey H, Khayat KH, Palacios M, et al. Viscosity modifying agents: key components of advanced cement-based materials with adapted rheology. Cem Concr Res. 2022;152:106646. doi:10.1016/j.cemconres.2021.106646
- Das S, Sobuz MHR, Tam VW, et al. Effects of incorporating hybrid fibres on rheological and mechanical properties of fibre reinforced concrete. Constr Build Mater. 2020;262:120561. doi:10.1016/j.conbuildmat.2020.120561
- Zhu C, Zhang J, Peng J, et al. Physical and mechanical properties of gypsum-based composites reinforced with PVA and PP fibers. Constr Build Mater. 2018;163:695–705. doi:10.1016/j.conbuildmat.2017.12.168
- Cao M, Li L, Shen S. Influence of reinforcing index on rheology of fiber-reinforced mortar. ACI Mater J. 2019;116:95–105.
- Yaghoobi A, Chorzepa MG. Meshless modeling framework for fiber reinforced concrete structures. Comput Struct. 2015;161:43–54. doi:10.1016/j.compstruc.2015.08.015
- Hao H, Song J, Chen M, et al. Rheological and mechanical properties of oil-well cement reinforced by hybrid inorganic fibers. Constr Build Mater. 2023;377:131002. doi:10.1016/j.conbuildmat.2023.131002
- Kaya Y, Biricik Ö, Bayqra SH, et al. Rheological properties and thixotropic behavior of cementitious systems containing different fiber types. Arab J Sci Eng. 2023: 1–21.
- Harbouz I, Roziere E, Yahia A, et al. Printability assessment of cement-based materials based on rheology, hydration kinetics, and viscoelastic properties. Constr Build Mater. 2022;325:126810. doi:10.1016/j.conbuildmat.2022.126810
- Chen M, Li H, Yang L, et al. Rheology and shape stability control of 3D printed calcium sulphoaluminate cement composites containing paper milling sludge. Addit Manuf. 2022;54:102781.
- Dunant CF, Granja J, Muller A, et al. Microstructural simulation and measurement of elastic modulus evolution of hydrating cement pastes. Cem Concr Res. 2020;130:106007. doi:10.1016/j.cemconres.2020.106007
- Keshtkar M, Heuzey MC, Carreau PJ. Rheological behavior of fiber-filled model suspensions: effect of fiber flexibility. J Rheol. 2009;53:631–650. doi:10.1122/1.3103546
- Song J, Xu M, Tan C, et al. Study on an epoxy resin system used to improve the elasticity of oil-well cement-based composites. Materials. 2022;15:5258. doi:10.3390/ma15155258
- Liu B, Liu X, Li G, et al. Study on anisotropy of 3D printing PVA fiber reinforced concrete using destructive and non-destructive testing methods. Case Stud Constr Mat. 2022;17:e01519.
- Kang ST, Kim JK. Numerical simulation of the variation of fiber orientation distribution during flow molding of ultra high performance cementitious composites (UHPCC). Cem Concr Compos. 2012;34:208–217. doi:10.1016/j.cemconcomp.2011.09.015
- Özkan Ş, Demir F. The hybrid effects of PVA fiber and basalt fiber on mechanical performance of cost effective hybrid cementitious composites. Constr Build Mater. 2020;263:120564. doi:10.1016/j.conbuildmat.2020.120564
- Ding C, Guo L, Chen B, et al. Micromechanics theory guidelines and method exploration for surface treatment of PVA fibers used in high-ductility cementitious composites. Constr Build Mater. 2019;196:154–165. doi:10.1016/j.conbuildmat.2018.11.118