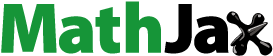
ABSTRACT
WADED Al-Mg and Al-Mg-Sc-Zr aluminium alloy thin-wall components were produced. Heat treatment (350°C aging for 4 h) was further conducted. The effects of Sc/Zr addition on porosity, microstructure, mechanical properties and corrosion behaviour were investigated. With Sc/Zr adding, pore area fraction decreased from 0.208 to 0.005% and grain size decreased from 84.34 to 19.54 μm. In WADED Al-Mg-Sc-Zr component, microstructure showed refined equiaxed grains. Mechanical properties were improved with 360 MPa ultimate tensile strength (UTS), 185 MPa yield strength, and 23.31% elongation. After heat treatment, UTS increased to 388 MPa with good ductility (22.53%) maintained. The grain refinement and Al3(Sc, Zr) particles were the key factors for mechanical property improvement. The corrosion behaviour was improved with introduced Sc/Zr and further optimised after heat treatment. The corrosion exhibited layered characteristics due to the distribution of primary Al3(Sc, Zr) while minor-size secondary Al3(Sc, Zr) along grain boundaries improved the corrosion behaviour.
1. Introduction
Wire-arc directed energy deposition (WADED) is a technology that adopts the arc heat source to melt filling metal wire and directly deposits metallic structures. Compared with alternative additive manufacturing (AM) techniques, WADED has notable advantages of high efficiency, economical cost and capacity for large-scale integrated manufacture of aluminium alloy structures [Citation1–5]. Al-Mg aluminium alloy components were extensively used in aerospace industry because of their lightweight application and excellent strength-plastic synthesis [Citation6]. Many scholars have proven the Al-Mg alloys fabricating feasibility with WADED process [Citation7,Citation8]. Meanwhile, the dimensional accuracy optimisation and defect elimination in WADED process was also conducted by numerous works [Citation9–13]. However, there are still shortcomings in WADED Al-Mg aluminium alloys, like porosity and insufficient strength (<300 MPa) [Citation14]. Moreover, with the growing requirements of aerospace aluminium, the mechanical properties and durability need to be considered simultaneously. Several attempts have been conducted to solve these problems, including process parameter optimisation [Citation15], post-treatments [Citation16,Citation17] and alloy element adding [Citation18,Citation19]. Among these methods, the microalloying of Sc/Zr elements to modify Al-Mg alloys has attracted wide attention and become a key issue in the new-generation high-performance aluminium alloy research field [Citation20,Citation21].
The introduction of Sc/Zr into Al-Mg alloy was often achieved by laser-based powder bed fusion (PBF-LB) technology in the early stage. Previous research reported the Sc/Zr addition could improve the printability of normal Al-Mg alloy [Citation22]. Zhou et al. [Citation23] reported the Zr addition into Al-Mg alloy can effectively inhibit hot cracks and reduce defect dimension. The main impact of Sc/Zr can be attributed to two types of Al3(Sc, Zr) precipitates. The primary Al3(Sc, Zr) precipitates served as nuclei for grain refinement and increased resistance to heat tears while solidifying [Citation24]. The secondary Al3(Sc, Zr) precipitating in aging treatment provided precipitation strengthening and further enhanced the strength [Citation22,Citation25]. Wang et al. [Citation10,Citation20,Citation21] discovered that fine grains formed at the molten pool boundary (MPB) due to the primary Al3(Sc, Zr) precipitating at fusion boundary. Columnar grains existed inside the molten pool because the majority of Sc/Zr were trapped in the matrix [Citation26]. Qin et al. [Citation27] thought the Sc/Zr elements in coarse columnar grains were supersaturated, and secondary Al3(Sc, Zr) preferentially formed in this area throughout aging treatment. The disparate distribution of primary and secondary precipitates resulted in dual heterogeneous structures in PBF-LB counterparts.
The attempts to add Sc/Zr into WADED aluminium alloys have been proven feasible by several studies. Dong et al. [Citation28] introduced Sc into WADED Al-Zn-Mg-Cu-Sc alloy, the average grain diameter reduced to 59.6 μm from 123 μm. Guo et al. [Citation29] fabricated Al-Zn-Mg-Cu-Sc-Zr counterparts using cold metal transfer (CMT) technology and strength could reach 600 MPa after T6 heat treatment. Ren et al. [Citation19,Citation30] reported that Sc addition could significantly improve the mechanical properties in as-deposited conditions. Xia et al. [Citation31] further studied the microstructure evolution in WADED Al-Mg-Sc component and confirmed the grain refinement and property enhancement (with 335.58 MPa ultimate tensile strength and 22.74% elongation). The Sc/Zr adding not only had effects on microstructure but also influenced mechanical properties simultaneously. However, considering the layered characteristics and dynamic thermal cycling caused by WADED process [Citation32,Citation33], the microstructure and properties of the materials prepared by WADED are different from those of the components manufactured by other processes. The comprehensive properties of WADED Al-Mg-Sc-Zr alloy have not been systematically elaborated. Studying the Sc/Zr adding effects on WADED Al-Mg component is important to provide support for Al-Mg-Sc-Zr WADED process optimisation.
Besides, the durability of large-scale WADED aerospace Al-Mg components in the practical service environment is also required to be evaluated. According to previous research, the galvanic corrosion between precipitation and matrix is the main effect factor on corrosion behaviour after Sc/Zr introduction [Citation34,Citation35]. Zhang et al. [Citation36] found the primary Al3(Sc, Zr) precipitates acting as micro-cathodic gathered along the MPBs in PBF-LB components, and corrosion pittings initiated along MPB. However, diverse viewpoints exist on the impact of secondary Al3(Sc, Zr) precipitates on corrosion behaviour. Deng et al. [Citation37] reported the corrosion behaviour of Al-Zn-Mg-Sc-Zr sheet was enhanced at 120°C as aging time prolonging because the active corrosion path was weakened and the dissolving rate was decreased by the coarsen and dispersed grain boundary precipitates (GBPs). However, Zhang et al. [Citation34] reported the secondary Al3(Sc, Zr) precipitates along grain boundaries (GBs) in PBF-LB counterparts caused more severe corrosion, and only precipitate size below 10 nm was beneficial for corrosion resistance. Zhou et al. [Citation38] thought the size and density of secondary Al3(Sc, Zr) particles in PBF-LB counterparts were mostly responsible for the corrosion behaviour, and the growth of precipitates during the aging process would weaken the corrosion resistance. As mentioned above, there is still no conclusion about the effects of secondary Al3(Sc, Zr) on corrosion behaviour, thus more factors are needed to be considered comprehensively to illustrate the corrosion mechanism.
Inspired by the above works, the process and dynamic thermal cycle of WADED are different from those in metallurgical forming and laser-based powder bed fusion, which result in distinctive microstructure, mechanical properties and corrosion behaviour. In addition, the heat treatment process for WADED Al-Mg-Sc-Zr has not been determined. WADED Al-Mg and WADED Al-Mg-Sc-Zr components were fabricated and heat treatments were conducted in this paper. Investigations were conducted on the porosity, microstructure, mechanical properties and corrosion behaviour. This paper aims to comparatively study and systematically reveal the effects of Sc/Zr addition on the properties of WADED Al-Mg alloy. This is beneficial to provide support for Al-Mg-Sc-Zr WADED process optimisation and potential utilisation in aerospace industry.
2. Materials and methods
2.1. Material preparation
WADED Al-Mg and Al-Mg-Sc-Zr components are fabricated on 5A06 aluminium alloy substrate (300 mm × 150 mm × 10 mm) with single-pass and multi-layer depositing strategy. Al-6.5Mg and Al-6.7Mg-0.3Sc-0.13Zr wires with a 1.2 mm diameter were used as filler material. lists the compositions of wires and components which were measured by inductively coupled plasma-atomic emission spectrometry (ICP-AES, Agilent 7700-CE). The WADED processing illustration is shown in , and process parameters are listed in . Heat treatment (aging at 350°C for 4 h with air cooling) was further conducted for WADED Al-Mg-Sc-Zr and the component was referred to WADED Al-Mg-Sc-Zr-HT.
Figure 1. Diagrammatic representation of WADED process and the as-deposited WADED Al-Mg-(Sc-Zr) components.
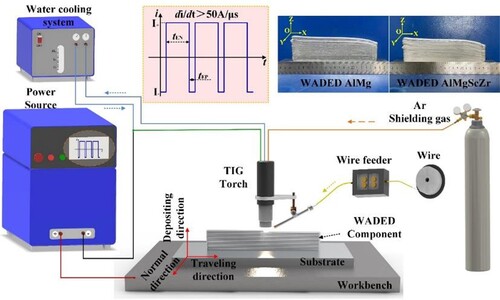
Table 1. Compositions of wire and WADED components.
Table 2. WADED processing parameters.
2.2. Microstructure and mechanical characterisation
The sampling illustration of WADED components is shown in . The samples in the centre section were used for investigating porosity, microstructure, microhardness and corrosion behaviour characteristics. To prepare samples for the horizontal and vertical tensile tests, each side was chosen. The central specimens were systematically detected using an optical microscope (OM) (ZEISS Scope A1), X-ray diffraction (XRD) (D/Max2500pc), following grinding and mechanical polishing. The micro-scale three-dimensional computed tomography system (3D-CT, NanoVoxel-2000, developed by Sanying Precision Instruments, China) was utilised to identify internal pore defects in ϕ 3.5 mm × 5 mm. The samples etched by Keller’s reagent were detected by OM, scanning electron microscopy (SEM) (JEOL JSM-7900F), and energy dispersive spectrometry (EDS). After electrolytic polishing, the central sections were investigated using 0.5 µm step length electron back-scattered diffraction (EBSD). Following ion milling and mechanical thinning, the specimens were detected using transmission electron microscopy (TEM) (JEM-2100) to achieve the composition and structural information of precipitations.
Microhardness was measured by Vickers (FALCON 500) with a 200 g load for 15 s at 0.5 mm intervals in a 7 mm × 7 mm region. The tensile properties were examined using the universal testing equipment (Instron 5565) with a strain rate of 1 mm/min. The fracture specimens were further analysed by SEM.
The thermodynamic simulation was performed using Thermo-Calc simulation based on the TCAL6 database. For Al-6.7Mg-0.3Sc-0.13Zr and Al-6.5Mg-0.73Mn alloys, elemental segregation during rapid solidification was assessed using the Scheil–Gulliver model. The phase diagram was tested with TCAL6 thermodynamic database.
2.3. Corrosion test
Electrochemical experiments were conducted in 3.5wt % NaCl solution at ambient temperature with CHI-660e electrochemical workstation. The platinum plate and a saturated calomel electrode (SCE) respectively served as a counter electrode (CE) and reference electrode (RE). All samples were mechanically ground up to 2000 grits to obtain a working electrode (WE), and the WE surface with 3 mm × 3 mm was checked to ensure no obvious pores in the vision field. Cathodic potentiostatic polarisation was carried out at −0.5 V relative to the open circuit potential (OCP) for 5 min to eliminate effects of oxidation film, then stabilised for 2400 s. With a frequency range of 100 kHz to 10 mHz, electrochemical impedance spectroscopy (EIS) was measured at corrosion potential. The commercial programme ZSimpwin was used to evaluate the experimental data. At a scanning rate of 0.1667 mV/s, the potentiodynamic polarisation was started at −0.15 VOCP, and the scanning was halted when current reached 10−2 A/cm2. The immersion experiment was conducted in 3.5 wt % NaCl solution at ambient temperature for 24 h, SEM and EDS were used to observe corrosion feature details.
3. Results
3.1. Microstructure
The 3D-reconstructed morphology, 2D micropore distribution on building direction (BD) × traveling direction (TD) plane, and micropore size statistics detected by 3D X-ray computed tomography are displayed in . Most of the micropores in all samples are near-spherical, thus it can be inferred hydrogen pore is the main form of pores [Citation39]. It can be observed a large number of micropores distribute in WADED Al-Mg with a porosity of 0.208% and the maximum diameter of 168.72 μm. The quantitative statistical result indicates the average diameter is 15.71 ± 9.65 µm. The number fraction of micropores, whose diameter is less than 30 µm, is 85.63%. In micropore projection on BD × TD plane, a large number of micropores aggregating in a specific layer leads to layered pore distribution, which is also reported in the as-deposited WADED aluminium alloys [Citation40]. After Sc/Zr adding, the number and size of micropores decreased significantly with an improved porosity of 0.005%. The largest micropore only has a diameter of 82.46 µm and the average pore size decreased to 8.20 ± 8.95 µm. Consequently, the layered pore distribution is obviously optimised. In particular, it is essential to note that the number fraction of the micropore diameter less than 10 and 30 µm is 54.16 and 95.21%, respectively, indicating the pores in WADED Al-Mg-Sc-Zr are mainly minor-size. However, WADED Al-Mg-Sc-Zr-HT exhibits a porosity of 0.045%. The average diameter is 14.41 ± 10.62 µm which is higher than the as-deposited counterpart. The maximum pore diameter also increases to 117.85 µm and the micropore number fraction less than 10 and 30 µm is 34.86 and 86.75%, respectively. This could be attributed to the heat treatment process making the micropores gather and grow [Citation41,Citation42]. Although the layered pore distribution in Sc/Zr-added component tends to be obvious after aging, it still presents an improved state compared with WADED Al-Mg. The layer-distributed micropores will influence component synergy performance.
Figure 3. The porosity and statistic results of (a1)–(a3) WADED Al-Mg, (b1)–(b3) WADED Al-Mg-Sc-Zr, (c1)–(c3) WADED Al-Mg-Sc-Zr-HT components.
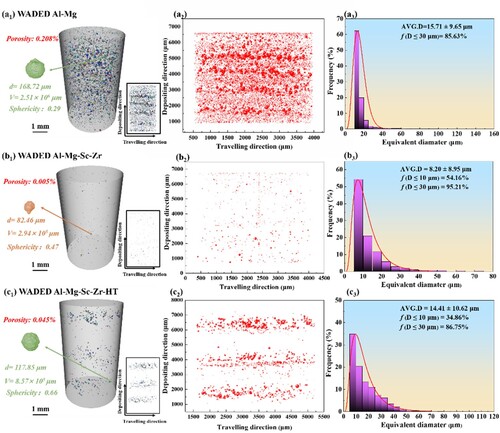
displays the XRD patterns of WADED components. The apparent peaks in WADED Al-Mg component are identified as α-Al and no other obvious precipitation phase is identified. The main peak intensity of Sc/Zr-added components increased, which could be attributed to the overlapped peak of α-Al and Al3(Sc, Zr) [Citation31,Citation43]. Moreover, the minor peak of Al3(Sc, Zr) occurred at 64.5° and 77.5° in WADED Al-Mg-Sc-Zr-HT, which relates to the secondary Al3(Sc, Zr) precipitating in aging process.
The OM () and SEM () morphologies are conducted to reveal the microstructure characteristics of WADED components, and the composition of the corresponding phases are listed in . Each layer has alternate inner-layer and inter-layer regions because of the layer-by-layer depositing mechanism [Citation41]. a shows the homogeneous microstructure of WADED Al-Mg component composed of coarse equiaxed grains (CEG). For WADED Al-Mg component in a1–a4, the slight grain size difference results in its layered characteristic not being obvious. From the corresponding EDS result and the previous studies, the large-size phases distributed along the GB can be identified as β-Al3Mg2 and Al6(Mn, Fe) [Citation14,Citation19]. For WADED Al-Mg-Sc-Zr component in b, the grain shows a smaller size and fine equiaxed grains (FEG) at MPB leading to layered characteristics obvious, which is different from the microstructure in the PBF-LB component consisting of coarse columnar grains and fine grains [Citation44,Citation45]. As b1–b4 shows, the CEG exists in inner-layer region while the FEG exists in inter-layer region. Sc/Zr-riched particles aggregated in inter-layer regions can be identified as Al3(Sc, Zr) particles [Citation46]. For WADED Al-Mg-Sc-Zr-HT sample in c and c1–c4, the GBs tend to be semi-continuous. The changed microstructure characteristics after Sc/Zr microalloying would result in performance differences.
Figure 5. OM morphology of (a) WADED Al-Mg, (b) WADED Al-Mg-Sc-Zr and (c) WADED Al-Mg-Sc-Zr-HT components.
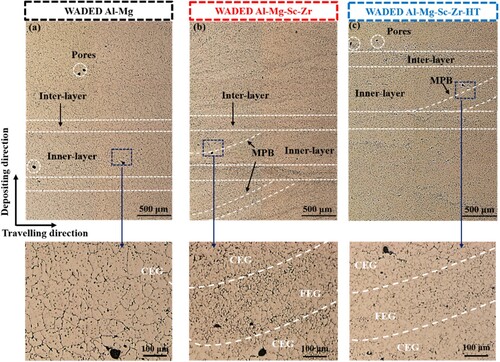
Figure 6. SEM morphology and element mapping of (a1)–(a4) WADED Al-Mg, (b1)–(b4) WADED Al-Mg-Sc-Zr and (c1)–(c4) WADED Al-Mg-Sc-Zr-HT components.

Table 3. Chemical compositions of phase in (at. %).
TEM morphologies in show characteristics of Al3(Sc, Zr) particles. As shown in a1–a3, the primary Al3(Sc, Zr) particles serve as nucleation sites and often exist at the GB of FEG [Citation21,Citation27]. Selected area electron diffraction (SAED) images along the [110] zone axis show Al3(Sc, Zr) particles with an L12 ordered structure and a {110} crystal planar space compatible with the α-Al matrix. Since the cooling rate during the forming process determines the primary Al3(Sc, Zr) size [Citation47], the primary Al3(Sc, Zr) precipitates in WADED Al-Mg-Sc-Zr component (103-105 K/s cooling rate) have a larger radius compared with that in PBF-LB counterparts (∼106 K/s cooling rate) [Citation20,Citation48].
Figure 7. TEM images and SAED patterns:(a1)–(a3) WADED Al-Mg-Sc-Zr, (b1)–(b5) WADED Al-Mg-Sc-Zr-HT, (b3) HRTEM picture of the matrix and Al3(Sc, Zr) interface, (b4) dislocations shown by inverse Fourier transformation image from the area marked in (b3) on (002) plane, (b5) HRTEM image of Al3(Sc, Zr) particle.
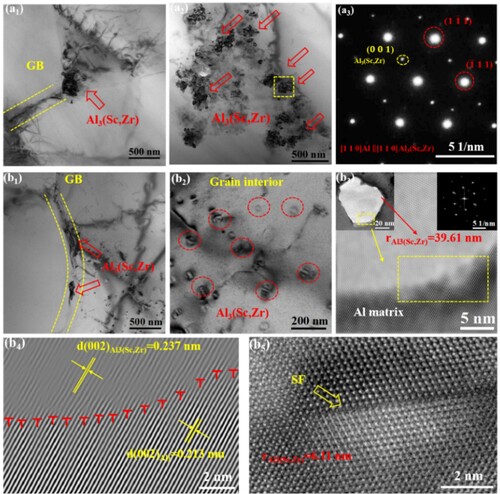
b1 and b2 show the particles with small radii are secondary Al3(Sc, Zr) precipitates [Citation38]. The precipitates along the GBs result in a narrower precipitate-free zone (PFZ) compared with that in WADED Al-Mg-Sc-Zr component. The secondary Al3(Sc, Zr) particles generated in aging process are more preferentially generated in the interior region of CEG since Sc/Zr elements in coarse grains were supersaturated in the matrix [Citation27]. Both primary and secondary Al3(Sc, Zr) precipitates exist in this condition [Citation38]. The secondary precipitates present an average radius of 24.5 nm in WADED Al-Mg-Sc-Zr-HT. The HRTEM and SAED obtained from the interface of secondary Al3(Sc, Zr) particles and the matrix show L12 structure (b3). b4 shows the inverse Fourier transformation image from the area marked by the yellow rectangle in b3 on the (002) plane. For the precipitates with a larger radius (39.61 nm), several dislocations exist at the interface of the precipitate and matrix (b4). However, for the secondary Al3(Sc, Zr) particle with a small radius (6.11 nm) (b5), the stacking faults (SFs) occurred. The various precipitate characteristics in different regions might lead to heterogeneity of service performance.
The EBSD results of WADED components are illustrated in . Grain refinement with Sc/Zr addition is apparent based on the inverse pole figure (IPF) and grain size distribution. The WADED Al-Mg component shows an average grain diameter of 84.34 ± 29.58 μm. WADED Al-Mg-Sc-Zr exhibits refined grains with an average diameter of 19.54 ± 6.26 μm and the proportion of grains smaller than 15 μm accounted for about 23.18%. After aging, WADED Al-Mg-Sc-Zr-HT shows an average grain diameter of 21.26 ± 6.47 and with about 27.91% grain less than 15 μm. The grains in WADED Al-Mg-Sc-Zr did not grow obviously after aging due to the thermal stability was improved with Sc/Zr addition [Citation49]. The grain size in WADED Al-Mg-Sc-Zr is comparable to that of powder-based DED counterparts and nearly half of that in as-cast counterparts [Citation21,Citation47,Citation50]. Moreover, there is no obvious grain growth after heat treatment. The low-angle grain boundaries (LAGBs) proportion with small misorientation angles (0°–15°) in WADED Al-Mg, Al-Mg-Sc-Zr and Al-Mg-Sc-Zr-HT components are 11.4%, 4.1%, 7.5%, respectively. The LAGB fraction decreased with Sc/Zr adding and slightly increased after aging. As the previous works reported, the percentage of LAGBs enhanced as Al3(Sc, Zr) volume fraction increased [Citation38,Citation51]. The pole figures show all WADED specimens exhibit weak texture with the maximum value in WADED Al-Mg, Al-Mg-Sc-Zr and Al-Mg-Sc-Zr-HT components are respectively 2.534, 1.669 and 1.742, indicating no preferred orientation generated.
3.2. Microhardness
WADED Al-Mg and Al-Mg-Sc-Zr both exhibit homogeneous hardness distribution (). The hardness fluctuates only in regional areas, which corresponds to the alternation of FEG to CEG. The average hardness value is enhanced from 91.7 HV0.2 to 99.5 HV0.2 after Sc/Zr adding. After 350°C -4 h aging, the hardness of WADED Al-Mg-Sc-Zr component further increases to 120.3 HV0.2. This could be attributed to the precipitation of secondary Al3(Sc, Zr) which has a strengthening effect [Citation43,Citation46].
3.3. Tensile properties
displays tensile curves and statistics results of ultimate tensile strength (UTS), yield strength (YS) and uniform elongation of samples. WADED Al-Mg components demonstrate UTS of ∼330 MPa, YS of ∼155 MPa and elongation of ∼23.56% along horizontal direction. With Sc/Zr added, the UTS and YS respectively increase to 360 and 185 MPa with good ductility (∼23.31% elongation) along horizontal direction. For WADED Al-Mg-Sc-Zr-HT, the horizontal UTS increased to 388 MPa, and the elongation could still be maintained at 22.53%.
Figure 10. (a) Engineering strain/stress curves, (b) true strain/stress curves (c) statistic results of WADED Al-Mg, Al-Mg-Sc-Zr and Al-Mg-Sc-Zr-HT components and (d) comparison between tensile properties in this work and others in Ref. [Citation8,Citation20,Citation21,Citation30,Citation31,Citation33,Citation43,Citation46,Citation52].
![Figure 10. (a) Engineering strain/stress curves, (b) true strain/stress curves (c) statistic results of WADED Al-Mg, Al-Mg-Sc-Zr and Al-Mg-Sc-Zr-HT components and (d) comparison between tensile properties in this work and others in Ref. [Citation8,Citation20,Citation21,Citation30,Citation31,Citation33,Citation43,Citation46,Citation52].](/cms/asset/c2f8003f-ab94-47d7-a91a-8f2e1f703f9d/nvpp_a_2358981_f0010_oc.jpg)
It is worth noting the mechanical properties along vertical direction are inferior to horizontal direction of all samples. A similar phenomenon is often found in WADED aluminium alloy, which may related to the pore distribution and the microstructure [Citation1,Citation53]. This would be discussed in the following part combined with the fractography. Moreover, all WADED samples display typical Portevin–Le Chatelier (PLC) effects (serration in the flow curves). It was also reported in PBF-LB counterparts in previous works [Citation21]. The PLC effect is dependent on dislocation density, grain size, strain rate and temperature [Citation54–56]. Compared with WADED Al-Mg alloy, the tensile curves of WADED Al-Mg-Sc-Zr component transform from smooth flow to serrated flow due to its finer grains [Citation27]. The reduction of PLC effects in WADED Al-Mg-Sc-Zr-HT is related to the nano-size secondary precipitates forming in aging process which trapped vacancies and reduced the mobility of the Mg atoms [Citation56]. d presents the tensile properties of WADED Al-Mg-Sc-Zr components in this work compared with other Al-Mg-(Sc-Zr) components by cast, powder-based DED and WADED methods in previous works. The statistical results demonstrate that WADED Al-Mg-Sc-Zr component in this work has an excellent strength-to-ductility balance.
The side surface fractography of WADED components is shown in . For WADED Al-Mg component (a,b), the coarse β-Al3Mg2 phase distributes along GBs when Mg reaches 3.0 wt % which weakens the GB binding force, resulting in crack tendency under tensile loads [Citation30]. Intergranular fracture is the main fracture type, leaving continuous phases existing at the fracture edge. The morphology of WADED Al-Mg-Sc-Zr components varies along distinct tensile directions (c,d). In horizontal direction, several precipitated particles distribute at the fracture edge. These precipitates can be inferred as Al3(Sc, Zr) and have a relatively high strength to prevent them from plastically deforming and getting detached from the surrounding matrix in the final tensile stage [Citation9,Citation57]. In vertical direction, the fracture edge is along layer boundaries [Citation1Citation58]. The morphologies of WADED Al-Mg-Sc-Zr-HT component show features that are similar to those of the as-deposited counterpart (e,f). It can be concluded inter-layer region is a sensitive region for fracture in vertical tensile direction. In particular, the layered characteristics of microstructure tend to be more obvious in Sc/Zr added components (), which might be one of the reasons for mechanical property anisotropy.
Figure 11. Side surface fractography of horizontal and vertical direction of (a), (b) WADED Al-Mg, (c), (d) WADED Al-Mg-Sc-Zr and (e), (f) WADED Al-Mg-Sc-Zr-HT components.
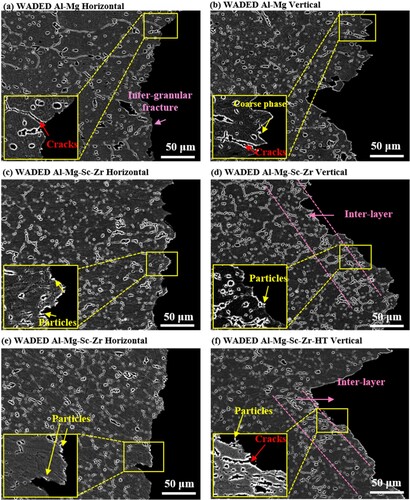
presents the front surface fracture morphologies of WADED components. The fractography of WADED Al-Mg component in horizontal and vertical directions exhibits an amount of dimples, indicating a high-degree local plastic deformation and good ductility. The dimple size in fractography of as-deposited and aged WADED Al-Mg-Sc-Zr is similar with that in WADED Al-Mg. The small particles can be observed in dimples are Al3(Sc, Zr) particles [Citation31]. The components display characteristics of ductile fracture. The coarse particles exist in the fracture surface of Sc/Zr added sample, which corresponds to the large-size particles in the interlayer region (). The large-size particles have a relatively high strength, which prevents them from plastically deforming [Citation9]. Moreover, the layered pore distribution along vertical direction also leads to mechanical properties lower than those in horizontal direction [Citation41]. Therefore, the combination effects of coarse particles distributing along the interlayer and layered pore distribution lead to the anisotropy of mechanical properties.
3.4. Corrosion behaviour
a shows the OCP evolution of each component. The OCPs range from −0.9 VSCE to −0.75 VSCE in test solution. The OCP final value enhanced after Sc/Zr addition and WADED Al-Mg-Sc-Zr-HT component has the highest OCP value, indicating the lowest corrosion tendency [Citation59]. The potentiodynamic polarisation curves (b) show a trace of active dissolution. The corrosion current decreased after Sc/Zr addition and further reduced after aging, indicating that electrochemical corrosion behaviour was improved.
Figure 13. (a) Open-circuit potential and (b) potentiodynamic polarisation curves of WADED Al-Mg, Al-Mg-Sc-Zr and Al-Mg-Sc-Zr-HT samples in 3.5 wt.% NaCl solution.
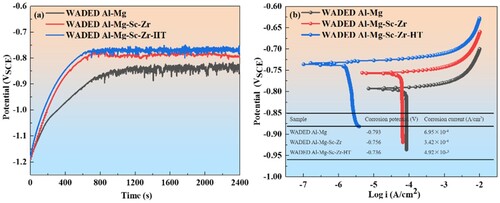
a displays the Nyquist plots of each sample which contain an impedance loop at high-frequency range and another one at low-frequency range. It indicates the electron transfer process is responsible for the electrochemistry reaction at high frequency, and the mass transfer step occurs at low frequency [Citation60]. a demonstrates the equivalent circuit model used to explain the electrochemical process on alloy surface, where Rs stands for the solution resistance, Qdl is for the double layer constant phase element, Rct represents the charge transfer resistance, L and RL denote the equivalent inductance and resistance of the corrosion induction [Citation61,Citation62]. The occurrence of induction indicates the low-resistance Al(OH)3 film on alloy surface cannot achieve a stable protective state, and local corrosion would initiate in the subsequent stage. It can be seen the impedance loop radius increases with Sc/Zr adding and WADED Al-Mg-Sc-Zr-HT sample has the largest radius. The corresponding Bode plot also shows the WADED Al-Mg-Sc-Zr-HT component has the largest modules at the low frequency, indicating a better corrosion resistance.
Figure 14. (a) Nyquist and (b) Bode plots of WADED Al-Mg, WADED Al-Mg-Sc-Zr and WADED Al-Mg-Sc-Zr-HT components in 3.5 wt.% NaCl solution.
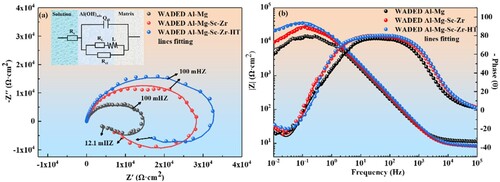
displays the corrosion morphology of each sample following a 24-h immersion in 3.5 wt % NaCl. Based on EDS findings, the corrosion tends to initiate from coarse Al3Mg2 and Al6(Mn, Fe) phases in WADED Al-Mg component. Both precipitates act as micro-anode phases and tend to be preferentially dissolved [Citation36,Citation63]. Due to the random phase distribution and the vague layered microstructure characteristic, it exhibits uniform corrosion features with large-size pittings. The corrosion morphology of WADED Al-Mg-Sc-Zr sample shows layered characteristics and pittings mainly distributed in inter-layer regions (b1, 15b2). This can be attributed to the galvanic corrosion caused by the high potential difference between Al3(Sc, Zr) and matrix, and the gathering of particles results in pitting aggregation in inter-layer region [Citation36]. The corrosion behaviour in inner-layer region is significantly improved after aging (c1, c2), which could be related to the secondary Al3(Sc, Zr) forming in aging process [Citation38]. The impacts of secondary Al3(Sc, Zr) on corrosion behaviour will be demonstrated in the discussion.
4. Discussion
4.1. Effects of Sc/Zr adding on microstructure
4.1.1. Effects of Sc/Zr adding on porosity
The previous study reported the pore-inhibition mechanism is complicated and related to the material properties, such as boiling temperature, melt viscosity and thermal conductivity [Citation23]. In this study, the pore-inhibiting process after Sc/Zr adding is discussed from the microalloying perspective.
According to , due to the high thermal conductivity and heat dissipation speed of aluminium alloys, the hydrogen not discharged from the molten pool in time would be retained to form pores in WADED process, which is the main origination of pores [Citation64,Citation65]. Pore development can be divided into four stages: formation, growth, detachment and escape of bubbles [Citation66]. When T < 250°C the Al (solid) reacts with H2O vapour to form Al(OH)3 and H2 which experience ‘adsorption-diffusion-dissolution’ in molten pool; when T > 400°C, the Al(OH)3 decomposes to H2O; T > 600°C, Al (liquid) react with H2O to form [H] that could directly dissolve into Al (l), which is considered as one of the main forms of hydrogen in Al alloys.
The classic Scheil module of thermal-calc software is used to elaborate the effects of solidification path on pore formation. As shown in a, the Al-Mg-Sc-Zr alloy system displays a more narrow solidification range in contrast to Al-Mg alloy system. According to the pore formation procedure described above, Sc/Zr adding shortens liquid phase-existence time, which restricts the [H] dissolving stage (above 600°C). The stage between 400 and 600°C where the Al(OH)3 decomposes to H2O is also restricted after Sc/Zr adding, which further limits the supplement of [H]. Moreover, due to the competitive relationship between bubble growth and grain refinement, the grain refinement promoted by Al3(Sc, Zr) particles which act as heterogeneous nucleation sites promote can effectively inhibit bubble growth ([Citation67]; [Citation21]). The combination effects of accelerated solidification range and grain refinement lead to low porosity in WADED Al-Mg-Sc-Zr.
4.1.2. Effects of Sc/Zr adding on layered characteristics
The phase diagram in b shows the primary Al3(Zr, Sc) with D023 crystal structure precipitated early in the first solidification stage and then transformed into L12 crystal structure (). The origination of the primary Al3(Sc, Zr) in WADED Al-Mg-Sc-Zr component can be divided into two types. The metallurgical process in the molten pool produces the first one, and the other is particles from the filler wire which generated during the wire preparation process and exists with relatively larger sizes [Citation68]. The primary Al3(Sc, Zr) particles from the metallurgical reaction preferentially precipitated along MPB and inter-layer region [Citation21], and those from the filler wire gravitationally collected at the bottom of the molten pool and layers. Both types of primary Al3(Sc, Zr) make the grains at MPB and inter-layer regions significantly refined [Citation69]. In contrast, CEGs exist in inner-layer region and molten pool interior due to the higher temperature in these regions making the Sc/Zr supersaturated in the matrix [Citation27]. The coexistence of FEG and CEG results in layered characteristics more obvious in WADED Al-Mg-Sc-Zr component. The phase diagram shown in b also indicates that β-Al3Mg2 is inevitably generated in Al-Mg-Sc-Zr alloy system. However, the refined grains weaken the aggregation of β-Al3Mg2 along GBs [Citation14]. After aging treatment, the grain boundaries became unclear and the layered characteristics were weakened.
4.1.3. Effects of Sc/Zr adding on grain characteristics
In previous works, the columnar grains dominate in microstructure of PBF-LB Al-Mg-Sc-Zr counterparts due to solidification conditions favouring planar growth [Citation44]. However, the microstructure exhibits equiaxed grains in this work. This could be attributed to the following factors. The columnar to equiaxed transition (CET) can be expressed by classical solidification theory [Citation24,Citation45]:
(1)
(1) where G denotes the temperature gradient, R represents the solidification velocity and N0 stands for the nuclei density. The a and m are material-dependent fitting constants, and ϕ represents the fraction of equiaxed grains. Since the slow cooling rate of deposited metal and sparse energy distribution in depositing process, WADED exhibits the characteristics of a low G/R ratio [Citation31], which is the favourable solidification condition for the equiaxed grain formation [Citation46]. In addition, the Al3(Sc, Zr) particles acting as heterogeneous nucleation sites enhanced N0, which also promoted equiaxed grain formation.
4.2. Mechanism for strength enhancement
The contribution factors that improve YS in aluminium alloy can be interpreted by applying the subsequent formula ([Citation25]; [Citation22]):
(2)
(2) Where σy is the YS evolution contains the solid-solution strengthening (σss), dislocations hardening (σd), grain boundary strengthening (σgb) and precipitation strengthening (σp). For WADED Al-Mg component, the main strengthen effect originates from the σss which is mainly contributed by the Mg content in the alloy. Based on the EDS shown in , the Mg contents in alloy matrix are similar. In addition, no work-hardening treatments are conducted for components. Therefore, the discussion of the strengthening mechanism is mainly focused on σgb and σp.
4.2.1. Grain boundary strengthening
The Hall-Petch equation can be used to quantify the grain refinement strengthening contribution:
(3)
(3) where σ0 represents the intrinsic resistance of the lattice to dislocation motion, and k (0.17 MPa·m0.5) is the constant standing for the relative strengthening contribution from GBs [Citation31]. The average grain size in WADED Al-Mg is 84.34 μm. Considering the bimodal grain structure after Sc/Zr adding, the contribution factors of FEG and CEG were calculated respectively. The FEG in WADED Al-Mg-Sc-Zr has an average size of 11.44 μm and accounts for 23.18% while those of CEG is 21.19 μm (76.82%). WADED Al-Mg-Sc-Zr-HT presents the FEG with 11.42 μm (27.91%) and CEG with 23.85 μm (72.09%). The strength increase by grain refinement is approximately 21.19 MPa in WADED Al-Mg-Sc-Zr and 18.80 MPa in WADED Al-Mg-Sc-Zr-HT.
4.2.2. Precipitation strengthening
With Sc/Zr addition, the Al3(Sc, Zr) precipitates take the main responsibility for σp. The Al3(Sc, Zr) precipitates have pinning effects on dislocation sliding and play a crucial part in strength enhancement [Citation16]. The Orowan dislocation bypassing mechanism dominates since the Al3(Sc, Zr) particles in WADED components have relatively larger radii than those in PBF-LB counterparts ([Citation44]; [Citation16]). The impact of precipitation strengthening can be calculated as [Citation22,Citation31]:
(4)
(4) where M represents the Taylor factor (3.06); G denotes the shear modulus (25.4 GPa); b stands for the Burgers vector of Al (0.28 nm);
refers to the edge spacing with of the primary Al3(Sc, Zr) particles (∼ 961 nm) and secondary Al3(Sc, Zr) particles (∼275 nm);
is the mean radius with about 110.3 nm for the primary Al3(Sc, Zr) particles and about 24.5 nm for the secondary Al3(Sc, Zr) precipitates; v is the Poisson ratio of the alloy (0.27). With Sc/Zr adding, the Orowan strengthening mechanism by primary Al3(Sc, Zr) particles contributes approximately 22.41 MPa. After aging, the secondary Al3(Sc, Zr) precipitates contribute about 60.48 MPa for WADED Al-Mg-Sc-Zr-HT.
According to the results in , the theoretical YS enhancement is about 43.60 MPa, which is slightly higher than the actual measured values (∼34.21 MPa). This may be attributed to the obvious layered characteristic with Sc/Zr adding and the fracture tends to occur at the heterogeneous structure boundary (). The calculated strength increment for WADED Al-Mg-Sc-Zr after aging is about 60.48 MPa which is higher than the experimental results (∼39.93 MPa). This may be caused by increased porosity after heat treatment ().
4.3. Corrosion mechanism
The different corrosion behaviour of each sample could be attributed to grain characteristics, crystallographic orientation and precipitates [Citation70,Citation71].
Grain size has a significant impact on corrosion behaviour, and which has been reported that the corrosion rate tends to decrease as particle size decreases, [Citation72]. In a, the OCPs of WADED Al-Mg-Sc-Zr and WADED Al-Mg-Sc-Zr-HT components rise rapidly in testing process, which represents the generation of Al(OH)3 film on alloy surface [Citation34]. Since the irregular atom arrangement and ununiform element distribution at GBs, the enhanced GB density made the alloy surface more active for reaction acceleration [Citation72]. The Sc/Zr added samples also show higher final OCP values, representing the higher quality of Al(OH)3 film. Meanwhile, the grain structure also plays an important role. The film on the heterogeneous structure transition area is believed to have poor protective quality [Citation62], and corrosion preferentially initiates from these regions, especially the inter-layer region where the transmission of FEG to CEG occurred ().
LAGB has been proven to exhibit better corrosion resistance [Citation73]. However, the GB density of WADED Al-Mg-Sc-Zr (162.93 mm−1) and WADED Al-Mg-Sc-Zr-HT (172.59 mm−1) samples are much higher than that of the WADED Al-Mg sample (43.32 mm−1). Thus the total LAGB length is more suitable for evaluating the corrosion behaviour [Citation71]. The total LAGB length in WADED Al-Mg, Al-Mg-Sc-Zr and Al-Mg-Sc-Zr-HT components are respectively 1.04, 1.79 and 3.50 mm, with the densities of 4.06, 6.63 and 12.96 mm−1. The LAGB density is enhanced with Sc/Zr addition and further improved after aging treatment, which is consistent with the electrochemical results.
The precipitates also have a significant effect on corrosion behaviour. The precipitates mostly contain β-Al3Mg2 and Al6(Mn, Fe) in WADED Al-Mg alloy. The β-Al3Mg2 continuously distributing along the GBs is the main factor for corrosion since it serves as the anodic to the matrix and dissolves preferentially [Citation63], leading to corrosion propagation along GBs (a1, a2). Since the low Fe content in WADED Al-Mg and Al-Mg-Sc-Zr, the fewer Al6(Mn, Fe) only acts as corrosion feature site due to the anodic potential relative to the Al matrix and is not the main factor for corrosion behaviour. The main factor for corrosion improvement in WADED Al-Mg-Sc-Zr is the high GB density rather than the lower Fe content, which weakens the aggregation of β-Al3Mg2 to improve corrosion along GBs. In addition, the gathering of the Al3(Sc, Zr) particles results in the regional distribution of pittings in inter-layer region. For WADED Al-Mg-Sc-Zr-HT, the minor-size secondary Al3(Sc, Zr) along GBs results in a narrow PFZ, which cuts the corrosion channel and decreases the electrochemical difference between GB and grain interior [Citation37,Citation38,Citation74]. Therefore, the corrosion behaviour in inner-layer region where secondary Al3(Sc, Zr) preferentially precipitated was improved.
5. Conclusions
In this study, WADED Al-Mg and WADED Al-Mg-Sc-Zr components were fabricated, and aging heat treatment (350°C-4 h aging) was further conducted. The effects of Sc/Zr addition on porosity, microstructure, mechanical characteristics, and corrosion behaviour were studied. The following conclusions can be drawn:
The total pores area fraction of WADED Al-Mg, Al-Mg-Sc-Zr and Al-Mg-Sc-Zr-HT components were 0.208%, 0.005% and 0.045%, respectively. The addition of Sc/Zr elements could effectively inhibit pore formation.
The equiaxed grain can be refined with Sc/Zr addition (from 84.34 μm in WADED Al-Mg to 19.54 μm in WADED Al-Mg-Sc-Zr) and slightly grew with heat treatment (21.26 μm). The layered microstructure characteristics tended to be more obvious with Sc/Zr adding.
The mechanical properties of WADED Al-Mg-Sc-Zr alloy are improved with 360 MPa ultimate tensile strength (UTS), 185 MPa yield strength (YS) and 23.31% elongation than that of WADED Al-Mg (UTS: 330 MPa, YS: 155 MPa, elongation: 23.56%). After heat treatment, the UTS further increased to 388 MPa while maintaining good ductility (22.53%). The strengthening enhancing mechanisms were mainly grain boundary and precipitation strengthening.
The corrosion behaviour was improved with Sc/Zr addition, as the grain refinement weakened phase aggregation along grain boundary. The Al3(Sc, Zr) caused the matrix nearby dissolution. The corrosion behaviour was further optimised after heat treatment due to the narrow PFZ along grain boundary cut the corrosion channel.
CRediT authorship contribution statement
Yubin Zhou: Data curation, Formal analysis, Investigation, Methodology, Visualisation, Writing – original draft. Zewu Qi: Investigation, Methodology, Resources, Supervision, Writing – review & editing, Funding acquisition. Baoqiang Cong: Investigation, Resources, Supervision, Writing – review & editing. Zihao Jiang: Visualisation, Writing – review & editing. Xinyi Cai: Investigation, Writing – review & editing. Hongwei Li: Investigation, Writing – review & editing. Jiaqi Zhang: Investigation, Writing – review & editing. Chaofang Dong: Software, Writing – review & editing. Xing He: Software, Writing – review & editing. Sanbao Lin: Writing – review & editing. Xiaoyu Cai: Writing – review & editing. Bojin Qi: Investigation, Project administration, Resources, Writing – review & editing.
Disclosure statement
No potential conflict of interest was reported by the author(s).
Data availability statement
Data will be available upon reasonable request.
Additional information
Funding
References
- Cong BQ, Cai XY, Qi ZW, et al. The effects of ultrasonic frequency pulsed arc on wire + arc additively manufactured high strength aluminum alloys. Addit Manuf. 2022;51:102617. doi:10.1016/j.addma.2022.102617
- Cao QH, Zeng CY, Qi BJ, et al. Excellent isotropic mechanical properties of directed energy deposited Mg-Gd-Y-Zr alloys via establishing homogeneous equiaxed grains embedded with dispersed nano-precipitation. Addit Manuf. 2023;67:103498. doi:10.1016/j.addma.2023.103498
- Yi H, Jia L, Ding JL, et al. Achieving material diversity in wire arc additive manufacturing: leaping from alloys to composites via wire innovation. Int J Mach Tools Manuf. 2024;194:104103. doi:10.1016/j.ijmachtools.2023.104103
- Wu BT, Shao ZX, Shao DD, et al. Enhanced corrosion performance in Ti-6Al-4 V alloy produced via wire-arc directed energy deposition with magnetic arc oscillation. Addit Manuf. 2023;66:103465. doi:10.1016/j.addma.2023.103465
- Wang LW, Wu T, Wang DL, et al. A novel heterogeneous multi-wire indirect arc directed energy deposition for in-situ synthesis Al-Zn-Mg-Cu alloy: process, microstructure and mechanical properties. Addit Manuf. 2023;72:103639. doi:10.1016/j.addma.2023.103639
- Lee S, Utsunomiya A, Akamatsu H, et al. Influence of scandium and zirconium on grain stability and superplastic ductilities in ultrafine-grained Al-Mg alloys. Acta Mater. 2002;50(3):553–564. doi:10.1016/S1359-6454(01)00368-8
- Horgar A, Fostervoll H, Nyhus B, et al. Additive manufacturing using WAAM with AA5183 wire. J Mater Process Technol. 2018;259:68–74. doi:10.1016/j.jmatprotec.2018.04.014
- Tonelli L, Laghi V, Palermo M, et al. Aa5083 (Al-Mg) plates produced by wire-and-arc additive manufacturing: effect of specimen orientation on microstructure and tensile properties. Prog Addit Manuf. 2021;6(3):479–494. doi:10.1007/s40964-021-00189-z
- Cordova L, Bor T, Smit MD, et al. Effects of powder reuse on the microstructure and mechanical behaviour of Al-Mg-Sc-Zr alloy processed by laser powder bed fusion (LPBF). Addit Manuf. 2020;36:101625. doi:10.1016/j.addma.2020.101625
- Wang ZH, Lin X, Kang N, et al. Directed energy deposition additive manufacturing of a Sc/Zr-modified Al-Mg alloy: effect of thermal history on microstructural evolution and mechanical properties. Mater Sci Eng A. 2021;802:140606. doi:10.1016/j.msea.2020.140606
- Liu DH, Wu DJ, Wang RZ, et al. Formation mechanism of Al-Zn-Mg-Cu alloy fabricated by laser-arc hybrid additive manufacturing: microstructure evaluation and mechanical properties. Addit Manuf. 2022;50:102554. doi:10.1016/j.addma.2021.102554
- Wang Y, Guo W, Xie YK, et al. In-situ monitoring plume, spattering behavior and revealing their relationship with melt flow in laser powder bed fusion of nickel-based superalloy. J Mater Sci Technol. 2023;177:44–58. doi:10.1016/j.jmst.2023.07.068
- Yi H, Wang Q, Zhang WJ, et al. Wire-arc directed energy deposited Mg-Al alloy assisted by ultrasonic vibration: improving properties via controlling grain structures. J Mater Process Technol. 2023;321:118134. doi:10.1016/j.jmatprotec.2023.118134
- Baek M-S, Shah AW, Kim YK, et al. Microstructures, tensile properties, and strengthening mechanisms of novel Al-Mg alloys with high Mg content. J Alloys Compd. 2023;950:169866. doi:10.1016/j.jallcom.2023.169866
- Dong BL, Cai XY, Lin SB, et al. Microstructures and mechanical properties of wire arc additive manufactured 5183-Al: influences of deposition dimensions. CIRP J Manuf Sci Technol. 2021;35:744–752. doi:10.1016/j.cirpj.2021.08.014
- Li D, Wu YY, Geng ZW, et al. High strength Al−Mg−Sc−Zr alloy with heterogeneous grain structure and intragranular precipitation produced by laser powder bed fusion. J Alloys Compd. 2023;939:168722. doi:10.1016/j.jallcom.2023.168722
- Dai W, Guo W, Xiao J, et al. Tailoring properties of directed energy deposited Al-Mg alloy by balancing laser shock peening and heat treatment. J Mater Sci Technol. 2024;203:78–96. doi:10.1016/j.jmst.2024.03.051
- Ren LL, Gu HM, Wang W, et al. Effect of Sc content on the microstructure and properties of Al-Mg-Sc alloys deposited by wire arc additive manufacturing. Met Mater Int. 2021;27(1):68–77. doi:10.1007/s12540-020-00763-0
- Ren LL, Gu HM, Wang W, et al. The microstructure and properties of an Al-Mg-0.3Sc alloy deposited by wire arc additive manufacturing. Metals (Basel). 2020;10(3):320. doi:10.3390/met10030320
- Wang ZH, Lin X, Kang N, et al. Strength-ductility synergy of selective laser melted Al-Mg-Sc-Zr alloy with a heterogeneous grain structure. Addit Manuf. 2020;34:101260. doi:10.1016/j.addma.2020.101260
- Wang ZH, Lin X, Wang JF, et al. Remarkable strength-impact toughness conflict in high-strength Al-Mg-Sc-Zr alloy fabricated via laser powder bed fusion additive manufacturing. Addit Manuf. 2022;59:103093. doi:10.1016/j.addma.2022.103093
- Ma KK, Wen HM, Hu T, et al. Mechanical behavior and strengthening mechanisms in ultrafine grain precipitation-strengthened aluminum alloy. Acta Mater. 2014;62:141–155. doi:10.1016/j.actamat.2013.09.042
- Zhou L, Hyer H, Park S, et al. Microstructure and mechanical properties of Zr-modified aluminum alloy 5083 manufactured by laser powder bed fusion. Addit Manuf. 2019;28:485–496. doi:10.1016/j.addma.2019.05.027
- Gaumann M, Bezencon C, Canalis P, et al. Single-crystal laser deposition of superalloys: processing-microstructure maps. Acta Mater. 2001;49(6):1051–1062. doi:10.1016/S1359-6454(00)00367-0
- Kendig KL, Miracle DB. Strengthening mechanisms of an Al-Mg-Sc-Zr alloy. Acta Mater. 2002;50(16):4165–4175. doi:10.1016/S1359-6454(02)00258-6
- Yang KV, Shi YJ, Palm F, et al. Columnar to equiaxed transition in Al-Mg(-Sc)-Zr alloys produced by selective laser melting. Scr Mater. 2018;145:113–117. doi:10.1016/j.scriptamat.2017.10.021
- Qin ZH, Kang N, Mansori ME, et al. Anisotropic high cycle fatigue property of Sc and Zr-modified Al-Mg alloy fabricated by laser powder bed fusion. Addit Manuf. 2022;49:102514. doi:10.1016/j.addma.2021.102514
- Dong BL, Xia YH, Cai XY, et al. Addition of Sc in wire-based directed energy deposition of Al-Mg-Zn-Cu alloy: microalloying to refine grains and improve mechanical properties. Addit Manuf. 2023;67:103494. doi:10.1016/j.addma.2023.103494
- Guo YL, Han QF, Lu WJ, et al. Microstructure tuning enables synergistic improvements in strength and ductility of wire-arc additive manufactured commercial Al-Zn-Mg-Cu alloys. Virtual Phys Prototyp. 2022;17(3):649–661. doi:10.1080/17452759.2022.2048236
- Ren LL, Gu HM, Wang W, et al. Microstructure and properties of Al-6.0Mg-0.3Sc alloy deposited by double-wire Arc additive manufacturing. 3D Print Addit Manuf. 2022;9(4):301–310. doi:10.1089/3dp.2020.0039
- Xia YH, Cai XY, Dong BL, et al. Wire arc additive manufacturing of Al-Mg-Sc alloy: An analysis of the effect of Sc on microstructure and mechanical properties. Mater Charact. 2023;203:113116. doi:10.1016/j.matchar.2023.113116
- Dong BL, Cai XY, Lin SB, et al. Wire arc additive manufacturing of Al-Zn-Mg-Cu alloy: microstructures and mechanical properties. Addit Manuf. 2020;36:101447. doi:10.1016/j.addma.2020.101447
- Dong BL, Cai XY, Xia YH, et al. Effects of interlayer temperature on the microstructures of wire arc additive manufactured Al-Zn-Mg-Cu alloy: insights into texture responses and dynamic precipitation behaviors. Addit Manuf. 2021;48:102453. doi:10.1016/j.addma.2021.102453
- Zhang H, Gu DD, Dai DH, et al. Influence of heat treatment on corrosion behavior of rare earth element Sc modified Al-Mg alloy processed by selective laser melting. Appl Surf Sci. 2020;509:145330. doi:10.1016/j.apsusc.2020.145330
- Qiu YC, Yang XF, Li JX, et al. The influence of Sc and Zr additions on microstructure and corrosion behavior of AA5182 alloy sheet. Corros Sci. 2022;199:110181. doi:10.1016/j.corsci.2022.110181
- Zhang ZQ, Sun JE, Xia JY, et al. Anisotropic response in corrosion behavior of laser powder bed fusion Al-Mn-Mg-Sc-Zr alloy. Corros Sci. 2022;208:110634. doi:10.1016/j.corsci.2022.110634
- Deng Y, Yin ZM, Zhao K, et al. Effects of Sc and Zr microalloying additions and aging time at 120 °C on the corrosion behaviour of an Al–Zn–Mg alloy. Corros Sci. 2012;65:288–298. doi:10.1016/j.corsci.2012.08.024
- Zhou ZX, Chen JQ, Wen F, et al. Optimization of heat treatment for an Al-Mg-Sc-Mn-Zr alloy with ultrafine grains manufactured by laser powder bed fusion. Mater Charact. 2022;189:111977. doi:10.1016/j.matchar.2022.111977
- Zeng CY, Cai XY, Qi ZW, et al. Effect of in-situ synthesized TiC particles on microstructure and mechanical properties of directed energy deposited AA2219 Al-Cu alloy. J Alloys Compd. 2023;964:171331. doi:10.1016/j.jallcom.2023.171331
- Yi H, Yang L, Jia L, et al. Porosity in wire-arc directed energy deposition of aluminum alloys: formation mechanisms, influencing factors and inhibition strategies. Addit Manuf. 2024;84:104108. doi:10.1016/j.addma.2024.104108
- Qi ZW, Qi BJ, Cong BQ, et al. Microstructure and mechanical properties of wire plus arc additively manufactured 2024 aluminum alloy components: As-deposited and post heat-treated. J Manuf Process. 2019;40:27–36.
- Zhao ZJ, Dong CF, Kong DC, et al. Influence of pore defects on the mechanical property and corrosion behavior of SLM 18Ni300 maraging steel. Mater Charact. 2021;182:111514. doi:10.1016/j.matchar.2021.111514
- Ren Y, Dong P, Zeng Y, et al. Effect of heat treatment on properties of Al-Mg-Sc-Zr alloy printed by selective laser melting. Appl Surf Sci. 2022;574:151471. doi:10.1016/j.apsusc.2021.151471
- Li RD, Wang MB, Li ZM, et al. Developing a high-strength Al-Mg-Si-Sc-Zr alloy for selective laser melting: crack-inhibiting and multiple strengthening mechanisms. Acta Mater. 2020;193:83–98. doi:10.1016/j.actamat.2020.03.060
- Wang ZN, Lin X, Wang LL, et al. Microstructure evolution and mechanical properties of the wire + arc additive manufacturing Al-Cu alloy. Addit Manuf. 2021;47:102298. doi:10.1016/j.addma.2021.102298
- Wang ZH, Lin X, Kang N, et al. Laser powder bed fusion of high-strength Sc/Zr-modified Al–Mg alloy: phase selection, microstructural/mechanical heterogeneity, and tensile deformation behavior. J Mater Sci Technol. 2021;95:40–56. doi:10.1016/j.jmst.2021.03.069
- Hyde KB, Norman AF, Prangnell PB. The effect of cooling rate on the morphology of primary Al3Se intermetallic particles in Al-Sc alloys. Acta Mater. 2001;49(8):1327–1337. doi:10.1016/S1359-6454(01)00050-7
- Kong DC, Dong CF, Wei SL, et al. About metastable cellular structure in additively manufactured austenitic stainless steels. Addit Manuf. 2021;38:101804. doi:10.1016/j.addma.2020.101804
- Zha M, Tian T, Jia HL, et al. Sc/Zr ratio-dependent mechanisms of strength evolution and microstructural thermal stability of multi-scale hetero-structured Al–Mg–Sc–Zr alloys. J Mater Sci Technol. 2023;140:67–78. doi:10.1016/j.jmst.2022.09.009
- Jiang JY, Jiang F, Zhang MH, et al. Al3(Sc, Zr) precipitation in deformed Al-Mg-Mn-Sc-Zr alloy: effect of annealing temperature and dislocation density. J Alloys Compd. 2020;831:154856. doi:10.1016/j.jallcom.2020.154856
- Zhang ZQ, Sun JE, Wu JS, et al. Influence of heat treatment on corrosion behavior of Al-Mn-Mg-Sc-Zr alloy produced by laser powder bed fusion. J Mater Res Technol. 2023;23:4734–4746. doi:10.1016/j.jmrt.2023.02.029
- Geng HB, Li JL, Xiong JT, et al. Geometric limitation and tensile properties of wire and arc additive manufacturing 5A06 aluminum alloy parts. J Mater Eng Perform. 2017;26(2):621–629. doi:10.1007/s11665-016-2480-y
- Yuan T, Ren XL, Chen SJ, et al. Al-Zn-Mg-Cu alloy with both high strength and high plasticity fabricated with wire arc additive manufacturing. Sci Technol Weld Joining. 2022;28(1):81–88. doi:10.1080/13621718.2022.2117532
- Saad G, Fayek SA, Fawzy A, et al. Serrated flow and work hardening characteristics of Al-5356 alloy. J Alloys Compd. 2010;502(1):139–146. doi:10.1016/j.jallcom.2010.04.119
- Hu ZH, Qi Y, Nie XJ, et al. The Portevin-Le Chatelier (PLC) effect in an Al-Cu aluminum alloy fabricated by selective laser melting. Mater Charact. 2021;178:111198. doi:10.1016/j.matchar.2021.111198
- Bakare F, Schieren L, Rouxel B, et al. The impact of L1(2) dispersoids and strain rate on the Portevin-Le-Chatelier effect and mechanical properties of Al-Mg alloys. Mater Sci Eng Struct Mater Prop Microstruct Process. 2021;811:141040. doi:10.1016/j.msea.2021.141040
- Van Hooreweder B, Moens D, Boonen R, et al. Analysis of fracture toughness and crack propagation of Ti6Al4 V produced by selective laser melting. Adv Eng Mater. 2012;14(1-2):92–97. doi:10.1002/adem.201100233
- Fu R, Lu WJ, Guo YL, et al. Achieving high strength-ductility of Al-Zn-Mg-Cu alloys via hot-wire arc additive manufacturing enabled by strengthening precipitates. Addit Manuf. 2022;58:103042. doi:10.1016/j.addma.2022.103042
- Kong DC, Wang L, Zhu GL, et al. Heat treatment effects on the metastable microstructure, mechanical property and corrosion behavior of Al-added CoCrFeMnNi alloys fabricated by laser powder bed fusion. J Mater Sci Technol. 2023;138:171–182. doi:10.1016/j.jmst.2022.08.018
- Li N, Dong CF, Man C, et al. Insight into the localized strain effect on micro-galvanic corrosion behavior in AA7075-T6 aluminum alloy. Corros Sci. 2021;180:109174. doi:10.1016/j.corsci.2020.109174
- Ao M, Liu HM, Dong CF, et al. Degradation mechanism of 6063 aluminium matrix composite reinforced with TiC and Al2O3 particles. J Alloys Compd. 2021;859:157838. doi:10.1016/j.jallcom.2020.157838
- Ji YC, Dong CF, Kong DC, et al. Design materials based on simulation results of silicon induced segregation at AlSi10Mg interface fabricated by selective laser melting. J Mater Sci Technol. 2020;46:145–155. doi:10.1016/j.jmst.2020.01.037
- Davenport AJ, Yuan Y, Ambat R, et al. Intergranular corrosion and stress corrosion cracking of sensitised AA5182. Aluminium Alloys Pts 1 and 2. 2006;519-521:641–646.
- Da Silva CLM, Scotti A. The influence of double pulse on porosity formation in aluminum GMAW. J Mater Process Technol. 2006;171(3):366–372. doi:10.1016/j.jmatprotec.2005.07.008
- Boeira AP, Ferreira IL, Garcia A, et al. Alloy composition and metal/mold heat transfer efficiency affecting inverse segregation and porosity of as-cast Al-Cu alloys. Mater Des. 2009;30(6):2090–2098. doi:10.1016/j.matdes.2008.08.032
- Hou XR, Zhao L, Ren SB, et al. A comparative study on Al-Mg-Sc-Zr alloy fabricated by wire arc additive manufacturing with controlling interlayer temperature and continuous printing: porosity, microstructure, and mechanical properties. J Mater Sci Technol. 2024;193:199–216. doi:10.1016/j.jmst.2023.12.062
- Cong BQ, Ouyang RJ, Qi BJ, et al. Influence of cold metal transfer process and Its heat input on weld bead geometry and porosity of aluminum-copper alloy welds. Rare Met Mater Eng. 2016;45(3):606–611. doi:10.1016/S1875-5372(16)30080-7
- Guo XP, Li HJ, Xue P, et al. Microstructure and mechanical properties of 600 MPa grade ultra-high strength aluminum alloy fabricated by wire-arc additive manufacturing. J Mater Sci Technol. 2023;149:56–66. doi:10.1016/j.jmst.2022.12.007
- Shen JJ, Chen B, Wan J, et al. Effect of annealing on microstructure and mechanical properties of an Al-Mg-Sc-Zr alloy. Mater Sci Eng Struct Mater Prop Microstruct Process. 2022;838:142821. doi:10.1016/j.msea.2022.142821
- Ralston KD, Fabijanic D, Birbilis N. Effect of grain size on corrosion of high purity aluminium. Electrochim Acta. 2011;56(4):1729–1736. doi:10.1016/j.electacta.2010.09.023
- Gu DD, Zhang H, Dai DH, et al. Anisotropic corrosion behavior of Sc and Zr modified Al-Mg alloy produced by selective laser melting. Corros Sci. 2020;170:108657. doi:10.1016/j.corsci.2020.108657
- Ralston KD, Birbilis N, Davies CHJ. Revealing the relationship between grain size and corrosion rate of metals. Scr Mater. 2010;63(12):1201–1204. doi:10.1016/j.scriptamat.2010.08.035
- Zhang RF, Qiu Y, Qi YS, et al. A closer inspection of a grain boundary immune to intergranular corrosion in a sensitised Al-Mg alloy. Corros Sci. 2018;133:1–5. doi:10.1016/j.corsci.2018.01.009
- Ahmad Z, Ul-Hamid A, Bj AA, et al. The corrosion behavior of scandium alloyed Al 5052 in neutral sodium chloride solution. Corros Sci. 2001;43(7):1227–1243. doi:10.1016/S0010-938X(00)00147-5