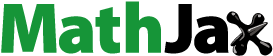
ABSTRACT
Underwater superaerophobic surface is of great significance for controllable manipulation of gas bubbles in scientific research and practical applications. However, the fabrication of arbitrary-shaped superaerophobic solid surfaces through a simple and low-cost approach is still hard. Herein, superaerophobic 3D objects were manufactured via liquid crystal display (LCD)-based 3D printing (vat photopolymerisation-based additive manufacturing) combined with one-step post-surface-treatment in sodium hydroxide (NaOH) solution. The influences of NaOH concentration, reaction temperature and time on the wettability of the polymer surface were systematically investigated. After a suitable alkali-treatment, the object surface obtained a bubble contact angle of 159° with extremely low bubble adhesion, featuring the underwater superaerophobicity. Morphology and composition characterisation demonstrated that a hydrophilic gel layer was produced on the printed sheet after the alkali-treatment, which is explained as the main mechanism of the superwetting transition from aerophobicity to superaerophobicity. Interestingly, spontaneously formed surface microgrids (size in xy direction: ∼50 μm) during 3D printing accelerated the alkali-treatment. Further, a superaerophobic 3D tweezer was designed, fabricated, and successfully applied in a toxic nitric oxide (NO) bubble reaction underwater for gas purity detection. The one-step post-surface-treatment method is also suitable for other commercial photosensitive resins and digital-light-processing (DLP) 3D printing.
1. Introduction
Manipulation of gas bubbles in aqueous media is of vital significance in mineral flotation [Citation1], matter transportation [Citation2], gas evolution reaction [Citation3,Citation4], microrobot [Citation5,Citation6], and microfluidic device [Citation7,Citation8], which has spurred considerable research interest in recent years [Citation9]. In some cases, the generation of small bubbles greatly improves the flotation recovery of tiny mineral particles, which reveals a positive implication [Citation10]. Meanwhile, in other cases, removing bubbles could efficiently reduce the fluid friction and avoid the microchannel block in a microfluidic system [Citation11]. The underwater bubble’s behaviours mainly depend on its own buoyancy and gas wettability on solid interface [Citation12]. The surface with a bubble contact angle (BCA) underwater exceeding 150° without bubble adhesion phenomenon can be defined as a superaerophobic surface [Citation13,Citation14]. Generally, the hydrophilic/superhydrophilic surface in air is intrinsically underwater aerophobic/superaerophobic [Citation15], which is affected by chemical composition and physical structure [Citation4]. Lin et al. prepared superaerophobic electrodes using hydrophilic functionalised poly(3,4-ethylenedioxythiophene) (PEDOT) and colloidal lithography for enhanced bubble release and efficient hydrogen evolution reaction [Citation16]. Yin et al. fabricated underwater superaerophobic stainless steel surfaces via femtosecond laser direct writing for efficient water boiling evaporation, which achieved a significant boost in bubble generation and departure during the boiling process [Citation17]. Further, by regulating the gas wettability on solid interface, researchers achieved the directional underwater gas bubble transportation [Citation18,Citation19] and bubble adhesion adjustment [Citation20]. Huo et al. fabricated the rough square-patterned array on intrinsic aerophobic shape-memory polymer surfaces by femtosecond laser ablation. Using this patterned solid surface, the rewritable microbubble pattern and the controllable in-situ bubble release and adhesion were realised [Citation20]. Unfortunately, to date, there exist two problems that hinder the application of the superwetting interface in bubble manipulation: (i) the device shapes for bubble manipulation are simple, which are difficult to customise according to the practical requirements [Citation9]; (ii) facile and low-cost strategies for fabricating superaerophobic surfaces are absent [Citation21]. Designing and fabricating 3D geometric configured superaerophobic solid surfaces through a simple approach may bring hope to the breakage of the bottleneck.
Additive manufacturing, also well-known as 3D printing, is a powerful technology that can rapidly translate 3D geometries into tangible objects via layer-by-layer assembly [Citation22,Citation23]. Among the numerous 3D printing technologies, vat photopolymerisation 3D printing can provide flexible, fast, and high-precision production of on-demand 3D parts, which brings an avenue to effectively manufacture functional superwetting devices with designable shapes [Citation24–26]. Dong et al. developed a digital-light-processing (DLP)-based method to 3D print superhydrophobic objects with bulk nanostructures and almost unlimited geometrical freedom via polymerisation-induced phase separation and the following supercritical drying [Citation27]. Yin et al. reported a flexible water-repelling biomimetic surface structured with mushroomlike basic units through 3D projection microstereolithography (PμSL) and spraying commercial low-surface-energy particles [Citation28]. Zhang et al. fabricated 3D polytetrafluoroethylene (PTFE) microstructures with superhydrophobic surfaces by using a self-made projection 3D micro-printer and a thermal sinter post-processing [Citation29]. Although various technique categories of vat photopolymerisation 3D printing are utilised to solve the problem of the free-form manufacturing of complex-3D-shaped objects, to date, difficulties in three aspects still hinder the facile and low-cost fabrication of 3D superaerophobic solid surfaces: (i) great effort of the published articles has been concentrated on liquid wettability, whereas the research on 3D printing-structured gas wettability is extremely rare [Citation30,Citation31]; (ii) the equipment such as PμSL and DLP 3D printer is expensive [Citation24,Citation26]; and (iii) special post-processing such as supercritical drying, high-temperature sintering, and coating is needed for specific bulk materials to obtain superwettability, making the preparation processes laborious to be promoted extensively [Citation27,Citation29,Citation32].
Liquid crystal display (LCD) 3D printing, as an emerging vat photopolymerisation-based projection 3D printing technology, obtains the advantages of high printing precision, speed, and ultra-low cost by using an LCD screen as an electrically controllable photomask [Citation24,Citation33]. Attributing to the inexpensive LCD screen and low-powered light-emitting-diode (LED) light source, the prices of commercial LCD 3D printers are even less than one-tenth of those of the popular DLP 3D printers (Table S1). On the other hand, traditional photosensitive resins of vat photopolymerisation 3D printing are also suitable for LCD 3D printing, allowing it convenient to use. Unfortunately, the typical photosensitive resins are mainly composed of acrylate-based monomers and prepolymers [Citation23,Citation34], inducing that the printed polymer objects have no underwater gas superwettability. To fabricate 3D superaerophobic objects, a simple and general post-treatment approach without any special equipment and material is expected [Citation35]. In this study, based on LCD 3D printing and its corresponding photosensitive resins, a simple one-step post-surface-treatment method in the alkaline solution was proposed and 3D superaerophobic objects were manufactured successfully ((a)). The influences of NaOH concentration, alkali-treatment temperature and time on bubble superwetting behaviours were investigated in detail. The mechanism of gas superwetting transition was explored. Excitingly, this one-step post-surface-treatment strategy can also be applied to many other commercial photosensitive resins and the DLP 3D printing technology.
Figure 1. (a) Schematic diagram of the fabrication procedure of the superaerophobic LCD 3D printed object surface. The insets show the changes in surface topography and wettability before and after the post-surface-treatment. (b) Chemical structures of the components of photosensitive resin for 3D printing. (c) The hydrolysis reaction of the 3D printed ester-containing polymer during the alkali-treatment.
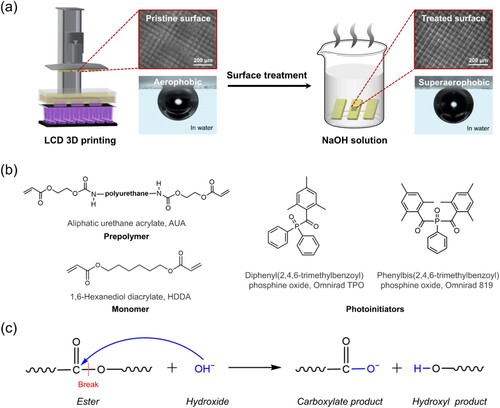
2. Materials and methods
2.1. Materials
Bifunctional aliphatic urethane acrylate (AUA, JZ-302, purity > 99%) as a prepolymer was purchased from Nanjing Jiazhong Chemical Technology Co., Ltd. (Nanjing, China). 1,6-Hexanediol diacrylate (HDDA) as a monomer was purchased from DSM (Shanghai, China). Diphenyl(2,4,6-trimethylbenzoyl)phosphine oxide (Omnirad TPO, purity > 99%) and phenylbis(2,4,6-trimethylbenzoyl)phosphine oxide (Omnirad 819, purity > 98%) as photoinitiators were purchased from IGM Resins (Waalkwijk, the Netherlands). The chemical structures of AUA, HDDA, Omnirad TPO, and Omnirad 819 are depicted in (b). Absolute alcohol (C2H6O, purity > 99.7%) was purchased from Sinopharm Chemical Reagent Co., Ltd. (Shanghai, China). Sodium hydroxide (NaOH, purity > 99.5%) was purchased from Qingdao Century Star Chemical Reagent Co., Ltd. (Qingdao, China). Oxygen (O2, purity > 99.99%), and nitric oxide (NO, purity > 95.0%) were purchased from Qingdao Ludong Gas Co., Ltd. (Qingdao, China). Before the bubble reaction experiment, NO was mixed with a small amount of air. Resin 1 was self-prepared in this work; Resin 2–4 were commercially purchased. Resin 2 (standard transparent resin) was bought from Shenzhen Creality 3D Technology Co., Ltd. (Shenzhen, China). Resin 3 (standard rigid gray resin) was purchased from Shenzhen Nova Intelligent Technology Co., Ltd. (Shenzhen, China). Resin 4 (M-Black resin) was purchased from Ningbo Makex Co., Ltd. (Ningbo, China).
2.2. 3D printing
An LCD 3D printer (Bene 3, Shenzhen Nova Intelligent Technology Co., Ltd., China) was used to manufacture 3D objects. The wavelength of the light-emitting diode (LED) light source is 405 nm. The printer has a 6-inch (13.2 cm × 7.5 cm) LCD screen with a resolution of 2560 × 1440. The 3D geometrical models for printing were designed by using SolidWorks 2018 software and exported to the stereolithography (STL) file format. The STL files were then sliced by the 3D printing software (NovaMaker) with each 35 μm layer thickness. Before 3D printing, the liquid photosensitive resin was prepared as follows. Typically, Omnirad TPO (0.70 g, 1.40 wt%) and Omnirad 819 (0.80 g, 1.6 wt%) as photoinitiators were added into HDDA (32.34 g, 64.67 wt%) and the mixture was stirred for 0.5 h at room temperature using a magnetic stirrer in a dark condition. Subsequently, AUA (16.16 g, 32.33 wt%) was added into the above solution. After being stirred for 2 h without light, a pale yellow transparent photosensitive resin was obtained. To study the wettability of the printed sample surface, rectangular sheets (25 mm × 12 mm × 2.2 mm) were printed with a layer exposure time of 8 s. After the printing was finished, the polymer sheets were immersed in absolute ethanol for 5 min to remove residual and uncured components. Finally, further photocuring was carried out by using a UV lamp (365 nm, 18 W) for 40 min to ensure a complete polymerisation of the photosensitive resin. The sheet surface toward the release film of the resin tank was noted as the pristine surface. Some samples in Section 3.6 were printed by using a DLP 3D printer (M-One Pro 30, Ningbo Makex Co., Ltd., China).
2.3. Post-surface-treatment
The LCD 3D printed sheets were alkali-treated to change the gas wettability. Typically, for the preparation of superaerophobic sheets, five printed sheets were placed into NaOH solution (1 mol·L−1, 100 mL) at 85 °C under mechanical stirring for 2 h. Then, the samples were moved out, washed with deionised water, and soaked in deionised water for 24 h. The chemical reaction that occurred during post-surface-treatment is shown in (c). After the sheets were blast dried at 50 °C for 2 h, the post-surface-treated samples were obtained. A 3D printed tweezer was post-surface-treated via a similar procedure, which was applied to manipulate gas bubbles underwater.
2.4. Characterisation
The water contact angles (WCAs), bubble contact angles (BCAs) and bubble sliding angles (BSAs) underwater were determined by using a contact angle metre (JY-PHb, Chengde Jinhe Machine Manufacturing Co., Ltd., China). The volumes of water droplets in air and bubbles underwater were 3 μL. The bubble sliding angles (BSAs) were measured using a rotating sample stage with a rotating speed of 0.1°/s. The adhesion forces between the air bubbles and sheet surfaces were evaluated by a high-sensitivity micro-electromechanical balance system (DCAT 21, Dataphysics, Germany). The volume of air bubbles for the adhesion force test was 3 μL and the bubble compression distance was 0.2 mm. Advancing process: the sample moved upward at a speed of 0.05 mm/s to contact the bubble on the copper ring with a bubble compression height of 0.2 mm. Receding process: the sample moved down to leave the bubble at the same speed of 0.05 mm/s. Because of the adhesion force, the bubble was stretched and deformed and eventually broke away from the sample surface. A field emission scanning electron microscopy (FE-SEM, SU8020, Hitachi, Japan) was utilised to observe the morphology of the pristine and treated polymer surfaces. For morphological observation, Pt was sprayed on the sample surface to increase the electroconductivity and the acceleration voltage was selected as 5 kV. An energy-dispersive spectrometer (EDS, EMAX mics2, HORIBA, Japan) was used to analyze the chemical elements of the samples and the acceleration voltage was selected as 10 kV. The surface topography of different simple surfaces was observed on an optical microscope (Theta, Biolin Scientific, Sweden). The surface roughness was tested on a laser spectroscopy confocal microscopy (LSCM, KC-H020, KathMatic, China) using these testing parameters: scanning area: 400 μm × 400 μm; scanning distance: 2 μm; scanning speed: 500 μm/s; sampling frequency: 500 Hz. The chemical groups of the sample surface were analyzed by a Fourier transform infrared (FTIR) spectroscopy system (Nicolet iS10, Thermo Fisher Scientific, USA) using the potassium bromide (KBr) pellet method and the transmission mode.
3. Results and discussion
3.1. Effect of post-surface-treatment
(a–c) demonstrates the changes in wettability of the printed polymer sheets before and after the one-step post-surface-treatment with a typical reaction condition (NaOH concentration: 1 mol·L−1, temperature: 85 °C, time: 2 h). On the pristine surface, the blue water droplet presented a spherical crown shape, whereas the droplet revealed a spreading state on the treated surface ((a)). The water contact angles (WCAs) of two surfaces were determined to be 77° and 13° ((b)), respectively, confirming that after the alkali-treatment the pristine polymer surface turned more hydrophilic. The underwater air-repellent property of the two samples was characterised through the bubble contact angles (BCAs, (c)). The BCAs of the pristine and treated surface were measured as 131° and 159°, respectively. An adhesion force measurement device ((d)) was used to evaluate the bubble’s adhesion on the sheet surface. For the pristine surface, the bubble adhered to the sheet and the severe dragging deformation phenomenon of the air bubble was observed during the measurement ((e)). The adhesion force between a 3-μL bubble and the pristine surface was 165.3 ± 6.9 μN. For the treated surface, the bubble was easy to depart from the surface without obvious dragging-induced deformation during the force−distance measurement ((f)). The adhesion force was only 10.2 ± 3.1 μN, which is much smaller than that of the pristine surface. Additionally, the bubble easily slid away under a slightly tilted treated surface. The bubble sliding angle (BSA) of the treated surface was measured to ∼1°, indicating an ultra-low adhesion (Movie S1). As a comparison, the bubble couldn’t slide on the pristine surface even when it was inversed by 180° (Figure S1), suggesting a high adhesion. These results feature the underwater superaerophobicity of the one-step alkali-treated polymer surface.
Figure 2. Wetting and adhesion behaviours of droplets and bubbles on the pristine and treated surfaces. The comparisons of (a) droplet wettability, (b) WCAs, and (c) BCAs between the pristine and treated surfaces. (d) Schematic of the adhesion force measurement device of air bubbles. Force−distance curves recorded before and after the air bubble contacted (e) the pristine and (f) treated surfaces. Influence of (g) NaOH concentration (temperature: 85 °C, time: 2 h), (h) alkali-treatment temperature (NaOH concentration: 1 M, time: 2 h) and (i) time (NaOH concentration: 1 M, temperature: 85 °C) on WCAs and BCAs. All the volumes of water droplets and air bubbles were 3 μL.
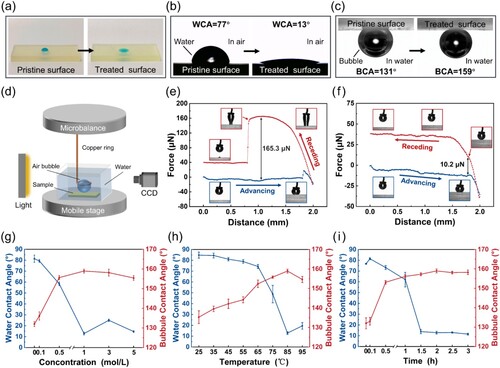
The influences of NaOH concentration, alkali-treating temperature and time on BCAs and WCAs were investigated further. (g) shows that with the increase of NaOH concentration at a low concentration range (< 1 mol·L−1), the WCAs declined and the BCAs increased. As the NaOH concentration reached 1 mol·L−1 with a reaction temperature of 85 °C and time of 2 h, the treated surface obtained a WCA of 13° ± 2° and a BCA of 159° ± 1°, with a phenomenon that bubbles easily slid along the polymer sheet, demonstrating a superaerophobic behaviour underwater. With the NaOH concentration greater than 1 mol·L−1, such as 3 and 5 mol·L−1, the WCAs of the treated surface dropped sharply below 25° and the BCAs still exceeded 150°, featuring the characteristic of underwater superaerophobicity. It is worth mentioning that although the WCAs of the surfaces treated with 1, 3, and 5 mol·L−1 NaOH solution fluctuated between 10° and 25°, their superaerophobicity wasn’t affected. Interestingly, the NaOH concentration equal to 0.5 mol·L−1 was a special case. Although the BCA reached 156° ± 1°, the WCA (58° ± 2°) remained large and air bubbles tended to adhere to the surface, which wasn’t classified as the ideal superaerophobic state here. The curves of WCAs and BCAs vs. treating temperature ((h)) exhibit a general trend that as the temperature increased, the WCAs declined and BCAs ascended. At the temperature of 85 and 95 °C, the treated surface obtained BCAs exceeding 150° and WCAs less than 20° with a characteristic that no bubble adhesion occurred, featuring the underwater superaerophobicity. The curves of WCAs and BCAs vs. reacting time ((i)) reveal that with the reacting time rising, the WCAs decreased and BCAs declined within 1.5 h. When the reacting time was equal to or longer than 1.5 h, the wettability of the treated surfaces turned to a relatively stable state with the WCA less than 15° and BCA surpassing 150°, which was regarded as a superaerophobic state. Generally, two points were summarised from the above exploration of the alkali-treatment conditions: (i) when a treated surface possessed a BCA surpassing 150° and a WCA less than 25°, a superaerophobic surface was obtained; (ii) an optimal reaction condition (NaOH concentration: 1 mol·L−1, temperature: 85 °C, time: 2 h) was obtained for the alkali-treatment of 3D printed polymer objects. Additionally, the treated sheet had good stability when stored in both water and air. After 3 weeks of storage, the BCA had an extremely slight change of only ∼1° (Figure S2).
3.2. Morphology and chemical composition
The morphology and chemical composition of the object surface before and after the post-surface-treatment were characterised through SEM, EDS, LSCM and FTIR. The SEM morphologies of the pristine and treated surfaces are shown in (a and b). Interestingly, the pristine polymer sheet appeared rough by SEM observation ((a)). Microscale square grids with an average dimension of ∼50 μm covered the entire surface. It should be noted that the square microstructures were not intentionally designed, but originated from LCD 3D printing. An obvious evidence is that the square grid size is close to that of the pixel units of the LCD screen (Figure S3) [Citation36,Citation37]. For the treated surface ((b)), the grooves between the square grids turned clear, suggesting the depth increased. Meanwhile, the nanoscale morphology of the sample changed before and after the post-surface-treatment. For the pristine surface, the spherical nanostructures (diameter: 70–110 nm, inset of (a)) and nanostructure aggregations with microscale sizes were observed. After the alkali-treatment, the spherical nanostructures turned small and the size became more uniform with an average diameter of ∼50 nm (inset of (b)). The treated sample surface revealed a slippery state, indicating the formation of a new gel layer. The thin jelly-like layer could be scraped off with a razor blade and was measured to contain 89.8 wt% of water by drying (Figure S4), which strongly confirmed the formation of the gel layer on the alkali-treated sample. On the other hand, the depth of the grooves parallel to the length direction of the polymer sheet is different from that perpendicular to the length direction, which is due to the lateral stair-stepping effect of LCD 3D printing caused by the disconnected pixels and uneven light intensity on LCD screen [Citation37,Citation38]. From the SEM analysis of the cross-section ((c and d)), the depths for pristine and treated surfaces were measured as 2.2 and 5.9 μm, respectively, confirming an obvious depth increase after the post-surface-treatment. From the high-magnification cross-section SEM image (inset of (d)), a new layer with a thickness of 5–10 μm on the treated surface was observed, which blocked the longitudinal fracture stripes of the pristine sample (inset of (c)) [Citation39]. It is explained to be the gel layer induced by the hydrolysis during the alkali-treatment. LSCM ((e and f)) was used to characterise the surface roughness of two samples and the Sa-value (in accordance to ISO 25178) was utilised to evaluate the degree of the roughness. The roughness (Sa) of the pristine surface was 0.72 μm while that of the treated surface was 2.08 μm, proving that alkali-treatment increased the microscale surface roughness. The cross-section plots (xz direction) from the LSCM images (Figure S5) also confirm that the treated surface obtained a larger roughness than that of the pristine surface.
Figure 3. Morphologies and chemical composition of the pristine and treated surfaces. Low-magnification and high-magnification (insets) SEM images of (a) the pristine and (b) treated surfaces. Low-magnification and high-magnification (insets) cross-section SEM images of (c) the pristine and (d) treated sheets. LSCM images of (e) the pristine and (f) treated surfaces. EDS spectra of (g) the pristine and (h) treated surfaces. (i) FTIR spectra of the pristine and treated polymer surfaces.
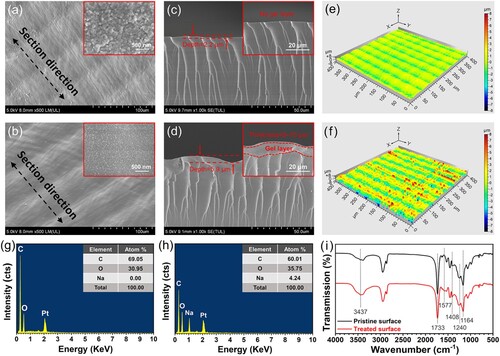
EDS analysis ((g and h)) shows the differences in chemical elements between the two samples. The result reveals that the C and O elements were detected on the pristine surface with a C/O atom ratio of 2.23, while the C, O, and Na elements were measured on the treated surface with a C/O atom ratio of 1.68. The occurrence of Na element and the decrease of the C/O atom ratio are explained by the hydrolysis of ester groups during the alkali-treatment. Due to the participation of hydroxide ions (OH−) in chemical reactions, ester groups were hydrolyzed to carboxylate (−COONa) and hydroxyl products (−OH) ((c)), which led to the occurrence of Na element and the increase of O atom. Carboxylate and hydroxyl products can raise the hydrophilicity and underwater air repellency of the polymer surface.
FTIR was performed to analyze the changes in chemical groups of the polymer surface before and after the alkali-treatment, as shown in (i). For the pristine surface, the strong characteristic peak located at 1733cm−1 is assigned to the stretching vibration of the ester carbonyl group (C = O) in the ester groups (−COOC−) [Citation40]. And the characteristic peaks located at 1240 and 1164 cm−1 are assigned to the asymmetrical stretching vibration and the symmetric stretching vibration of C−O−C in the ester groups (−COOC−) respectively [Citation41]. The ester groups originate from the two main components of the polymer sheet – AUA and HDDA. A weak peak at 1408 cm−1 is associated with the vibration of C = C in the acrylate groups [Citation42]. For the treated surface, the above three peaks at 1733cm−1, 1240, and 1164 cm−1 show slight weakening, indicating the partial hydrolysis of ester groups and the break of the acyl-oxygen bond. A new peak appeared at 1577 cm−1 and the peak at 1408 cm−1 enhanced, corresponding to the asymmetrical and symmetrical stretching vibrations originating from the carboxylate groups (−COO−), respectively [Citation43], which is the hydrolysis product of the ester groups. Another evidence for the hydrolysis of the ester groups was the increase of the intensity of hydroxyl (−OH) peak at 3437 cm−1, which is attributed to the hydroxyl products originating from the hydrolysis of the ester groups on the polymer surface. Generally, the alkali-treatment induces a morphology change and increase of hydrophilic groups (−COO− and −OH), both of which contribute to improving the hydrophilicity of the treated surface in air and its aerophobicity in water.
3.3. Mechanism
Herein, the mechanism of the one-step post-surface-treatment approach to transfer an LCD 3D printed aerophobic surface to an underwater superaerophobic surface was investigated. The conventional strategy to realise the superaerophobic effect is the construction of hydrophilic coating and surficial micro/nano roughness [Citation14,Citation44,Citation45]. To explore the role of the post-surface-treatment and LCD-3D-printing-induced roughness, the WCAs, BCAs, and surface morphologies of a pristine flat sheet, a treated flat sheet (alkali-treating time: 2 h), a treated flat sheet (alkali-treating time: 6 h), a pristine 3D printed sheet, and a treated 3D printed sheet (alkali-treating time: 2 h) were characterised in detail, as shown in . The pristine flat sheet without obvious microscale structures, which was prepared using the same 3D printing photosensitive resin in a sandwich glass mold via UV photopolymerisation, possessed a WCA of 63° and a BCA of 123° ((a)), indicating weak hydrophilicity and aerophobicity of the polymer surface. After the post-surface-treatment for 2 h, its WCA reduced to 53° and the BCA increased to 138° ((b)), confirming that the hydrophilicity and aerophobicity of the treated flat sheet increased. It is explained as the hydrophilic gel layer began to appear partly on the flat sheet surface after the polymer hydrolyzed. At this state, the BCA remained less than 150° and the air bubble tended to adhere to the surface, which suggested that it was not a superaerophobic surface. When the post-surface-treating time increased to 6 h, the WCA of the treated flat sheet decreased to 13° and the BCA increased to 157° ((c)) without bubble adhesion phenomenon, which means that it obtained underwater superaerophobicity. At this stage, a complete water-contained gel layer formed on the treated flat sheet surface. For the pristine 3D-printed sheet, LCD-3D-printing-induced square grids with a dimension of ∼50 μm occurred, which brought new micro-scale surface roughness ((d)). The WCA and BCA were measured as 77° and 131°, respectively. The WCA and BCA values revealed the differences within 15° in comparison with those of the flat sheet, indicating that micro-scale surface roughness gave a weak influence on superaerophobicity. For the treated 3D printed sheet with an alkali-treating time of 2 h, amazingly, the WCA declined to 13° and the BCA increased to 159° ((e)) with a feature that the air bubble was prone to slide away, proving that the surface obtained an obvious underwater superaerophobicity. At this state, a hydrophilic gel layer with a large microscale roughness emerged on the 3D printed sheet ((e)). The above evidence certificates two points: (i) the alkali-treatment-induced hydrophilic gel layer plays a significant role in the fabrication of the superaerophobic surface; (ii) LCD-3D-printing-induced microgrids speed up the formation of the hydrophilic gel layer ((c and e)). From the high-magnification SEM images (insets of (a and b)), various nanostructures were also observed on the pristine and treated 3D printed sheets. Some researchers reported the promoting effect of nanostructures on underwater superaerophobicity [Citation13,Citation45,Citation46].
Figure 4. Mechanism of the surface wettability change before and after the post-surface-treatment. Diagrams, optical microscope photos, WCA images, and BCA images of (a) the pristine flat sheet, (b) the treated flat sheet (alkali-treating time: 2 h), (c) the treated flat sheet (alkali-treating time: 6 h), (d) the pristine 3D printed sheet, and (e) the treated 3D printed sheet (alkali-treating time: 2 h). Schematic diagram of the change in chemical composition and microstructure of the pristine (f) and (g) treated 3D printed sheets. (h) Influence of alkali-treating time on BCAs for flat sheets and 3D printed sheets.
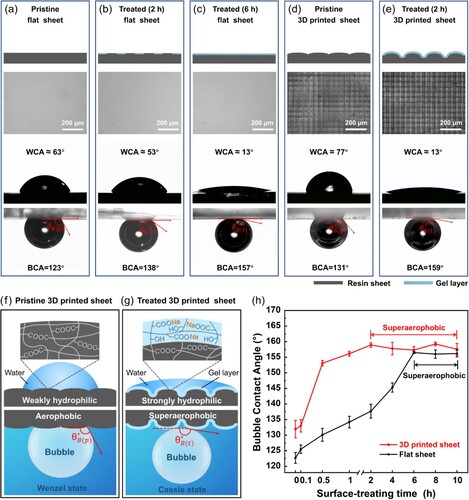
The change in chemical composition and microstructure of the pristine and treated 3D printed sheets was explicitly illustrated in (f and g). The major change in chemical composition was the conversion of weakly hydrophilic (aerophobic) ester groups to strongly hydrophilic (superaerophobic) sodium carboxylate and hydroxyl groups, while the variation in surface microstructure was the increase of microscale roughness as confirmed by (a–f). The air bubble on the pristine 3D printed sheet can be described as the Wenzel state (EquationEquation (1)(1)
(1) ) [Citation14,Citation47].
(1)
(1) where
represents the BCA on the 3D printed surface,
represents the BCA on an ideal surface (approximately flat surface here).
represents the area ratio of the solid surface relative to its projection, which is defined as the roughness factor. Due to the alkali-treatment-induced hydrophilic gel layer, the BCA on the ideal surface increased (
, (a and c)), combined with roughness changed (rp < rt, (d and e)),
can be deduced ((f and g)) according to EquationEquation (1)
(1)
(1) . The experiment results show that
was 131° and
was 159°, which fit the above deduction. At the state of (g), since
> 150° and no bubble adhesion was observed, it can be considered that the bubble state underwater turned from the Wenzel state ((f)) to the Cassie state ((g)), as expressed by EquationEquation (2)
(2)
(2) [Citation13,Citation48,Citation49].
(2)
(2)
represents the area fraction of the gas contacting with the solid surface. For the contact of the air bubble and sample,
, where
represents the area fraction of the gas contacting with the liquid water. Substituting
and
into EquationEquation (2)
(2)
(2) ,
and
can be calculated. This result suggests that part of ‘water cushions’ exist between the sample and the air bubble, which may promote the underwater superaerophobicity. It should be noted that the solid sample surface in this case was coated by a gel layer that contains part of liquid water (Figure S4), making it different from the traditional solid surface [Citation50]. Therefore, the actual
is larger than 0.16.
The acceleration effect of the LCD-3D-printing-induced roughness on the post-surface-treatment was further verified by comparing the BCA vs. alkali-treating time curves of the flat sheet and 3D printed sheet. As shown in (h), within the alkali-treating time of 0−6 h, the 3D printed sheet obtained obviously larger BCA than that of the flat sheet with the same treating time. The former needs an alkali-treating time of 2 h to obtain the superaerophobicity, whereas the latter needs 6 h. The short treating time is explained as follows: the rough surface of the 3D printed sheet possesses a large surface area, which increases the contact area with NaOH solution and promotes the hydrolysis reaction [Citation51,Citation52]. It is worth mentioning that the microscale square grids caused by the LCD pixel units during 3D printing are commonly regarded as a drawback that reduces the accuracy and quality of 3D printed objects [Citation36,Citation37], whereas they play a helpful accelerating role in constructing the superaerophobic surface. The spontaneously formed grid microstructures without special structural design need no additional cost, which sharply shorten the alkali-treating time.
3.4. Superaerophobic 3D printed tweezer
For the fabrication of the superaerophobic 3D object, the alkali-treatment effect on various faces of the object deserves attention. To clarify this problem, a cube with a side length of 8 mm was printed (Figure S6 (a and b)) and then alkali-treated. The cube contains three types of surface: the top face toward the release film (xy direction), the profile face (xz and yz direction), and the bottom face toward to platform. The top surface of the sample was investigated in detail above. After the post-surface-treatment, the BCA of the profile face turned from 148° to 160° and the BCA of the bottom face turned from 141° to 158°, both of which obtained a superwetting transition from aerophobicity to superaerophobicity. Although the surface morphologies of the profile and bottom face were different from that of the top face (Figure S6(c–f)), they still had good alkali-treatment effects. This result ensures that all surfaces of the 3D object obtained superhydrophobicity after the post-surface-treatment.
Further, A 3D customised tweezer with two hemispherical spoons was designed ((a)), 3D printed, and post-surface-treated for bubble manipulation underwater. The length of the tweezer is 87.0 mm, and the inner diameter of the spoon is 5.0 mm ((b)). To demonstrate the necessity of the post-surface-treatment, the capture, storage, and release behaviours of bubbles were compared between the pristine and treated tweezers ((c–e) and Movie S2). A little air bubble with a volume of 10 μL was injected into the cavity between the two scoops of the tweezer for bubble capture and storage. After opening the scoop, the tiny bubble adhered to the inner scoop surface of the pristine tweezer, but it floated away from the treated tweezer without any adhesion ((c)). It should be noted that the adhesion phenomenon is not conducive to the release and manipulation of bubbles. For medium (40 μL) and big (60 μL) bubbles ((d and e)), the large buoyancy normally allows an easy release of air bubbles. Unfortunately, after the tweezer was flipped horizontally by 90° and then turned back, the bubbles still adhered to the pristine spoon’s inner surface during releasing. As a comparison, the bubbles easily floated away from the treated tweezer due to the buoyancy when the tweezer arms were opened. These phenomena demonstrate that both the pristine tweezer and treated tweezer can be utilised to capture and store bubbles, but only the latter can release bubbles without any residue. Additionally, no obvious change of the superaerophobic effect was observed after 100 cycles of usage for the post-surface-treated tweezer. Therefore, the treated 3D-printed tweezer is more suitable for the bubble manipulation underwater. Owing to the free-form manufacturing ability of LCD 3D printing and one-step post-surface-treatment, the on-demand manufacturing of complex-shaped superaerophobic 3D objects becomes simple and facile.
Figure 5. Superaerophobic 3D printed tweezers for underwater bubble manipulation. (a) The 3D model of the customised tweezer. (b) The photo of the post-surface-treated 3D printed tweezer. The capture, store, and release operation of underwater bubbles with various volumes using pristine and treated tweezers: (c) 10 μL (little bubble), (d) 40 μL (medium bubble), and (e) 60 μL (big bubble). The white arrows indicate the next operation of the tweezers.
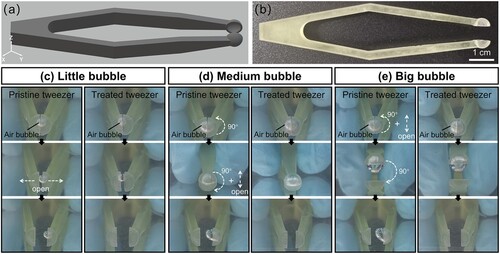
3.5. Application of underwater bubble manipulation
The post-surface-treated 3D-printed tweezer was applied in a toxic NO gas reaction underwater for purity detection (, Movie S3). NO, as a toxic, irritable, and water-insoluble gas, can easily react with O2 and generate NO2 [Citation53]. Then NO2 reacted with H2O rapidly to water-soluble HNO3 and HNO2. The gas–gas and gas–liquid reactions were described as EquationEquation (3)(3)
(3) and EquationEquation (4)
(4)
(4) [Citation54].
(3)
(3)
(4)
(4) The total reaction can be written as Equation (5):
(5)
(5) Firstly, a NO gas bubble (40 μL) and an O2 gas bubble (20 μL) were injected carefully by microinjectors onto two horizontal treated sheets underwater, respectively ((a)). The NO and O2 bubbles maintained a spherical shape due to the underwater superaerophobicity of the sheet surface. Secondly, the O2 bubble was captured by a treated tweezer and moved under the NO bubble ((b–d)). Finally, after releasing the O2 bubble, it was observed that the O2 bubble floated upward fast into the NO bubble ((e)) and then the mixed bubble turned small quickly ((f)). This phenomenon indicates that chemical reactions among NO, O2, and H2O occurred. According to Equation (5), the final bubble should disappear completely in theory if the volume ratio of NO to O2 is 2:1 since the reaction products (HNO3 and HNO2) are water-soluble liquids. However, there remained a small gas bubble on the sheet, which confirmed that the original NO gas wasn’t pure. As we know that NO and NO2 are extremely toxic and active, their relative reactions are challenging, which require complicated gas reaction equipment and strict safety protection. In this research, these gas chemical reactions were carried out underwater by using the superaerophobic tweezer and sheet. Meaningfully, attributing to the operability of the treated 3D-printed device and ultra-low volumes of gas bubbles, the toxic gas reactions turn simple and safe.
Figure 6. Demonstration of underwater bubble manipulation using a post-surface-treated 3D-printed tweezer for gas chemical reaction. (a) A NO gas bubble (40 μL) and an O2 gas bubble (20 μL) staying underneath two treated sheets; (b) and (c) The capture operation of the O2 bubble using the tweezer; (d) The release of the O2 bubble to react the NO bubble. (e) The mixed bubble after releasing the NO bubble. (f) The residual bubble after the gas chemical reaction.
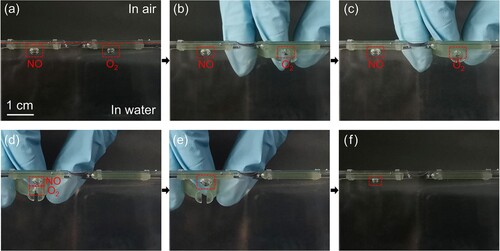
3.6. Extension of the method
demonstrates the BCAs of the pristine 3D printed and post-surface-treated polymer sheets with various photosensitive resins and 3D printing technologies. The effect of self-prepared Resin 1 has been investigated above in detail. Two commercial photosensitive resins (Resin 2: Creality resin, Resin 3: Nova resin) were utilised for LCD 3D printing. The BCA values before and after the post-surface-treatment increased from 138°± 4° to 158° ± 2° for Resin 2, and from 131° ± 3° to 158° ± 1° for Resin 3, respectively, which proves the wettability transformation from an aerophobic state to a superaerophobic state. Further, a similar wettability transformation was successfully observed for the pristine and treated polymer sheets by using the popular DLP 3D printing [Citation55] and three various resins (self-prepared Resin 1 and commercial Resin 2 and 4). The extension of resins and the 3D printing technology for the post-surface-treatment strategy is explained by the similar photosensitive resin components. Although the specific composition of the commercial photosensitive resins is unknown, urethane and epoxy acrylates as two main prepolymers and acrylate-based monomers are commonly used in most commercial resins [Citation23,Citation56], which can be hydrolyzed to the hydrophilic carboxylate and hydroxyl products in the alkaline solution. Therefore, the one-step post-surface-treatment strategy can not only be suitable for the LCD 3D printing technology and the typical photosensitive resin prepared in this research but also be applied to many other commercial photosensitive resins and the popular DLP 3D printing technology, which greatly expands the application scope of this method.
Figure 7. Demonstration of the post-surface-treatment effect with various resins and 3D printing technologies. Left: samples were LCD 3D printed; Right: samples were DLP 3D printed. Resin 1: the resin was self-prepared in this work; Resin 2–4 were commercially purchased. Resin 2: Creality standard transparent resin; Resin 3: Nova standard rigid gray resin; Resin 4: Makex M-Black resin.
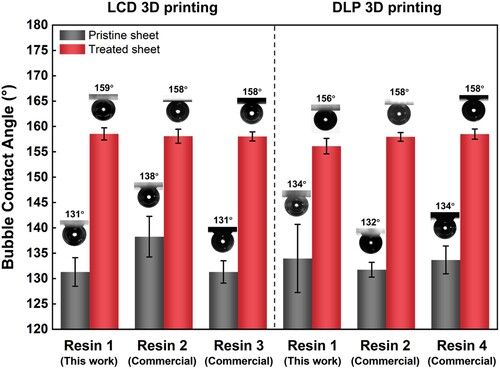
4. Conclusion
In summary, we have developed a one-step post-surface-treatment strategy to transfer the LCD 3D printed polymer surface from an aerophobic state to a superaerophobic state. It was found that during the alkali-treatment, a high NaOH concentration and reaction temperature, and a long reaction time profited the decrease of WCAs and increase of BCAs before the sample obtained the underwater superaerophobicity. The treated surface obtained superaerophobicity with a BCA of 159° and an extremely low bubble adhesive force (10.2 ± 3.1 μN) under an optimal reaction condition (NaOH concentration: 1 mol·L−1, reaction temperature: 85 °C, time: 2 h). SEM and LSCM characterisation revealed that the pristine 3D printed sample surface was covered with spontaneously formed square microgrids with a dimension of ∼50 μm. After the alkali-treatment, a new gel layer was produced on the sheet surface and the surface roughness increased. EDS characterisation revealed the C/O atom ratio of the sample surface decreased from 2.23 to 1.68 through the alkali-treatment and Na element emerged on the treated surface. FTIR characterisation proved that the ester groups (−COOC−) on the sample surface hydrolyzed to hydrophilic carboxylate (−COONa) and hydroxyl products (−OH) via the alkali-treatment. The mechanism of bubble superwetting transition was explained by the Wenzel and Cassie theories and the generation of the new hydrophilic gel layer was confirmed to be the main reason. It is worth mentioning that LCD-3D-printing-induced microstructures without any special design greatly sped up the alkali-treatment compared to the flat surface. As proof of application, a 3D tweezer was designed, LCD 3D printed, and post-surface-treated for underwater bubble manipulation. An underwater bubble chemical reaction (NO and O2) was accomplished using the superaerophobic tweezer and sheet for gas purity detection. Therefore, the inexpensive LCD 3D printing and simple post-surface-treatment allow the method to be facile and attractive for the fabrication of 3D geometric configured superaerophobic objects. Of further note, the one-step post-surface-treatment strategy is not only suitable for other commercial photosensitive resins, but also can be extended to the popular DLP 3D printing.
Supplemental Material
Download MS Word (6 MB)Data availability statement
Data will be made available on request from authors.
Disclosure statement
No potential conflict of interest was reported by the author(s).
Additional information
Funding
References
- Zhou ZA, Xu Z, Finch JA, et al. On the role of cavitation in particle collection in flotation – a critical review. II. Miner Eng. 2009;22(5):419–433. doi:10.1016/j.mineng.2008.12.010
- Weinstein T, Gilon H, Filc O, et al. Automated manipulation of miniature objects underwater using air capillary bridges: pick-and-place, surface cleaning, and underwater origami. ACS Appl Mater Interfaces. 2022;14(7):9855–9863. doi:10.1021/acsami.1c23845
- Ma L, Wei Z, Zhao C, et al. Hierarchical superhydrophilic/superaerophobic 3D porous trimetallic (Fe, Co, Ni) spinel/carbon/nickel foam for boosting oxygen evolution reaction. Appl Catal B Environ. 2023;332:122717, doi:10.1016/j.apcatb.2023.122717
- Zhang S, Xu L, Wu J, et al. Femtosecond laser micro-nano processing for boosting bubble releasing of gas evolution reactions. Nano Res. 2022;15(2):1672–1679. doi:10.1007/s12274-021-3811-3
- Zhou Y, Dai L, Jiao N. Review of bubble applications in microrobotics: propulsion, manipulation, and assembly. Micromachines (Basel). 2022;13(7):1068, doi:10.3390/mi13071068
- Kobo D, Pinchasik B-E. Backswimmer-inspired miniature 3D-printed robot with buoyancy autoregulation through controlled nucleation and release of microbubbles. Adv Intell Syst. 2022;4(6):2200010, doi:10.1002/aisy.202200010
- Tenjimbayashi M, Doi K, Naito M. Microbubble flows in superwettable fluidic channels. RSC Adv. 2019;9(37):21220–21224. doi:10.1039/c9ra04212a
- Ben S, Ning Y, Zhao Z, et al. Underwater directional and continuous manipulation of gas bubbles on superaerophobic magnetically responsive microcilia array. Adv Funct Mater. 2022;32(28):2113374, doi:10.1002/adfm.202113374
- Lin F, Wo K, Fan X, et al. Directional transport of underwater bubbles on solid substrates: principles and applications. ACS Appl Mater Interfaces. 2023;15(8):10325–10340. doi:10.1021/acsami.2c21466
- Tao DP. Recent advances in fundamentals and applications of nanobubble enhanced froth flotation: a review. Miner Eng. 2022;183:107554, doi:10.1016/j.mineng.2022.107554
- Gunatilake UB, Alvarez-Braña Y, Ojeda E, et al. Underwater magneto-driven air de-bubbler. J Mater Chem A. 2022;10(24):12832–12841. doi:10.1039/d2ta01009g
- Zhang X, Dong Y, He Z, et al. Efficient gas transportation using bioinspired superhydrophobic yarn as the gas-siphon underwater. ACS Appl Mater Interfaces. 2020;12(15):18174–18181. doi:10.1021/acsami.0c03366
- Huang C, Guo Z. The wettability of gas bubbles: from macro behavior to nano structures to applications. Nanoscale. 2018;10(42):19659–19672. doi:10.1039/c8nr07315e
- George JE, Chidangil S, George SD. Recent progress in fabricating superaerophobic and superaerophilic surfaces. Adv Mater Interfaces. 2017;4(9):1601088, doi:10.1002/admi.201601088
- Liu M, Wang S, Jiang L. Nature-inspired superwettability systems. Nat Rev Mater. 2017;2(7):17036, doi:10.1038/natrevmats.2017.36
- Lin H-H, Lin C-H, Luo S-C. Engineering superaerophobic electrodes using hydrophilic PEDOT and colloidal lithography for enhanced bubble release and efficient hydrogen evolution reaction. ACS Appl Mater Interfaces. 2023;15(24):29214–29223. doi:10.1021/acsami.3c05049
- Yin K, Wang L, Deng Q, et al. Efficient water boiling evaporation via a laser-architected superhydrophilic, underwater superaerophobic, and high infrared emissivity interface. Chem Eng J. 2023;466:143336, doi:10.1016/j.cej.2023.143336
- Wang X, Bai H, Yang J, et al. Designing flexible but tough slippery track for underwater gas manipulation. Small. 2021;17(8):2007803, doi:10.1002/smll.202007803
- Ning Y, Zhang D, Ben S, et al. An innovative design by single-layer superaerophobic mesh: continuous underwater bubble antibuoyancy collection and transportation. Adv Funct Mater. 2020;30(7):1907027, doi:10.1002/adfm.201907027
- Huo J, Bai X, Yong J, et al. How to adjust bubble’s adhesion on solid in aqueous media: femtosecond laser-ablated patterned shape-memory polymer surfaces to achieve bubble multi-manipulation. Chem Eng J. 2021;414:128694, doi:10.1016/j.cej.2021.128694
- Yong JL, Zhuang J, Bai X, et al. Water/gas separation based on the selective bubble-passage effect of underwater superaerophobic and superaerophilic meshes processed by a femtosecond laser. Nanoscale. 2021;13(23):10414–10424. doi:10.1039/d1nr01225h
- Ngo TD, Kashani A, Imbalzano G, et al. Additive manufacturing (3D printing): a review of materials, methods, applications and challenges. Compos B Eng. 2018;143:172–196. doi:10.1016/j.compositesb.2018.02.012
- Ligon SC, Liska R, Stampfl J, et al. Polymers for 3D printing and customized additive manufacturing. Chem Rev. 2017;117(15):10212–10290. doi:10.1021/acs.chemrev.7b00074
- Quan H, Zhang T, Xu H, et al. Photo-curing 3D printing technique and its challenges. Bioact Mater. 2020;5(1):110–115. doi:10.1016/j.bioactmat.2019.12.003
- Jiang P, Ji Z, Wang X, et al. Surface functionalization – a new functional dimension added to 3D printing. J Mater Chem C. 2020;8(36):12380–12411. doi:10.1039/d0tc02850a
- Dong Z, Levkin PA. 3D microprinting of super-repellent microstructures: recent developments, challenges, and opportunities. Adv Funct Mater. 2023;33(39):2213916, doi:10.1002/adfm.202213916
- Dong Z, Vuckovac M, Cui W, et al. 3D printing of superhydrophobic objects with bulk nanostructure. Adv Mater. 2021;33(45):2106068, doi:10.1002/adma.202106068
- Yin Q, Guo Q, Wang Z, et al. 3D-printed bioinspired cassie–baxter wettability for controllable microdroplet manipulation. ACS Appl Mater Interfaces. 2020;13(1):1979–1987. doi:10.1021/acsami.0c18952
- Zhang Y, Yin M-J, Ouyang X, et al. 3D μ-printing of polytetrafluoroethylene microstructures: a route to superhydrophobic surfaces and devices. Appl Mater Today. 2020;19:100580, doi:10.1016/j.apmt.2020.100580
- Liu H, Zhang Z, Wu C, et al. Biomimetic superhydrophobic materials through 3D printing: progress and challenges. Micromachines (Basel). 2023;14(6):1216, doi:10.3390/mi14061216
- Yan C, Jiang P, Jia X, et al. 3D printing of bioinspired textured surfaces with superamphiphobicity. Nanoscale. 2020;12(5):2924–2938. doi:10.1039/c9nr09620e
- Gaxiola-López JC, Lara-Ceniceros TE, Silva-Vidaurri LG, et al. 3D printed parahydrophobic surfaces as multireaction platforms. Langmuir. 2022;38(25):7740–7749. doi:10.1021/acs.langmuir.2c00788
- Song Y, Yang F, Zheng Z, et al. Synthesis of hyperbranched polymer for 3D printing. Chin J Chem. 2021;39(11):3064–3070. doi:10.1002/cjoc.202100521
- Mendes-Felipe C, Oliveira J, Etxebarria I, et al. State-of-the-art and future challenges of UV curable polymer-based smart materials for printing technologies. Adv Mater Technol. 2019;4(3):1800618, doi:10.1002/admt.201800618
- Tamburrino F, Barone S, Paoli A, et al. Post-processing treatments to enhance additively manufactured polymeric parts: a review. Virtual Phys Prototyp. 2021;16(2):221–254. doi:10.1080/17452759.2021.1917039
- Caplins BW, Higgins CI, Kolibaba TJ, et al. Characterizing light engine uniformity and its influence on liquid crystal display based vat photopolymerization printing. Addit Manuf. 2023;62:103381, doi:10.1016/j.addma.2022.103381
- Shan Y, Krishnakumar A, Qin Z, et al. Reducing lateral stair-stepping defects in liquid crystal display-based vat photopolymerization by defocusing the image pattern. Addit Manuf. 2022;52:102653, doi:10.1016/j.addma.2022.102653
- Lin D-Z, Yu P-H, Zhang Z-J, et al. Design and fabrication of large area vat photopolymerization 3D printing system using a 32-inch quasi-collimated visible backlight module with local dimming control. Addit Manuf. 2023;73:103665, doi:10.1016/j.addma.2023.103665
- Zhang X, Xu Y, Li L, et al. Acrylate-based photosensitive resin for stereolithographic three-dimensional printing. J Appl Polym Sci. 2019;136(21):47487, doi:10.1002/app.47487
- Barkane A, Platnieks O, Jurinovs M, et al. Thermal stability of UV-cured vegetable oil epoxidized acrylate-based polymer system for 3D printing application. Polym Degrad Stab. 2020;181:109347, doi:10.1016/j.polymdegradstab.2020.109347
- Khatri Z, Jatoi AW, Ahmed F, et al. Cell adhesion behavior of poly(ϵ-caprolactone)/poly(L-lactic acid) nanofibers scaffold. Mater Lett. 2016;171:178–181. doi:10.1016/j.matlet.2016.02.061
- Simon J, Langenscheidt A. Curing behavior of a UV-curable inkjet ink: distinction between surface-cure and deep-cure performance. J Appl Polym Sci. 2020;137(40):e49218, doi:10.1002/app.49218
- Wang XL, An WL, Tian F, et al. High-efficiency hydrolysis of thermosetting polyester resins into porous functional materials using Low-boiling aqueous solvents. ACS Sustain Chem Eng. 2020;8(42):16010–16019. doi:10.1021/acssuschemeng.0c06240
- Moraila CL, Montes Ruiz-Cabello FJ, Cabrerizo-Vilchez M, et al. Wetting transitions on rough surfaces revealed with captive bubble experiments. The role of surface energy. J Colloid Interface Sci. 2019;539:448–456. doi:10.1016/j.jcis.2018.12.084
- Zhang P, Wang S, Wang S, et al. Superwetting surfaces under different media: effects of surface topography on wettability. Small. 2015;11(16):1939–1946. doi:10.1002/smll.201401869
- Shen J, Li B, Zheng Y, et al. Engineering the composition and structure of superaerophobic nanosheet array for efficient hydrogen evolution. Chem Eng J. 2022;433:133517, doi:10.1016/j.cej.2021.133517
- Wenzel RN. Resistance of solid surfaces to wetting by water. Ind Eng Chem. 1936;28(8):988–994. https://doi.org/10.1021/ie50320a024.
- He H, Ji L, Wei Y, et al. Superaerophobic copper-based nanowires array for efficient nitrogen reduction. J Colloid Interface Sci. 2022;608:1489–1496. doi:10.1016/j.jcis.2021.10.062
- Yong J, Chen F, Fang Y, et al. Bioinspired design of underwater superaerophobic and superaerophilic surfaces by femtosecond laser ablation for anti- or capturing bubbles. ACS Appl Mater Interfaces. 2017;9(45):39863–39871. doi:10.1021/acsami.7b14819
- Zhang P, Zhao C, Zhao T, et al. Recent advances in bioinspired gel surfaces with superwettability and special adhesion. Adv Sci. 2019;6(18):1900996, doi:10.1002/advs.201900996
- Grenman H, Salmi T, Murzin DY. Solid-liquid reaction kinetics - experimental aspects and model development. Rev Chem Eng. 2011;27(1-2):53–77. doi:10.1515/Revce.2011.500
- Sun YP, Liu MC, Li XL, et al. Adjustable underwater gas transportation using bioinspired superhydrophobic elastic string. Coatings. 2022;12(5):638, doi:10.3390/coatings12050638
- Bruckdorfer R. The basics about nitric oxide. Mol Asp Med. 2005;26(1-2):3–31. doi:10.1016/j.mam.2004.09.002
- Squire S, Kightley R, Petros AJ. An effective method of scavenging nitric oxide. Br J Anaesth. 1996;77(3):432–434. doi:10.1093/bja/77.3.432
- Wang X, Liu J, Zhang Y, et al. Advances in precision microfabrication through digital light processing: system development, material and applications. Virtual Phys Prototyp. 2023;18(1):e2248101, doi:10.1080/17452759.2023.2248101
- Zhang J, Xiao P. 3D printing of photopolymers. Polym Chem. 2018;9(13):1530–1540. doi:10.1039/c8py00157j