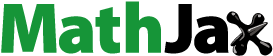
ABSTRACT
3D Concrete Printing (3DCP) is undergoing a shift from stiff printable mixtures towards set-on-demand mixtures. Nonetheless, there remains a significant gap in understanding the rheological behaviour as well as efficiency of the test methods for characterising rheological properties of set-on-demand mixtures. To address this gap, this study conducts a thorough examination of the suitability of four different characterisation test methods on a set-on-demand mixture. A stiff mixture is also tested for comparison purposes. An in-depth analysis is conducted on the strengths and weaknesses of each method in capturing the rheological evolution of both mixtures. Additionally, direct printing tests were also conducted for both mixtures. The external stresses, specifically those resulting from the self-weight during printing, were calculated. The evolving rheological properties of mixtures, measured from the instruments, were compared with the external stresses due to the printing process. Furthermore, variations in failure modes between the mixtures are revealed, with a significant discrepancy in the predicted number of printable layers based on the characterisation tests. This study offers valuable insights into the rheological characterisation and performance of test methods for the set-on-demand approaches.
1. Introduction
3D concrete printing (3DCP) is an innovative technology that has the potential to revolutionise the construction industry by enabling the creation of complex structures that were previously difficult to construct using traditional methods [Citation1,Citation2]. The main advantage of the 3DCP process is that formwork is no longer required [Citation2], material wastage can be reduced [Citation3], and its automated manufacturing method significantly reduces the need for physical labour [Citation4,Citation5]. Research indicates that 3DCP can reduce overall costs by 25.4%, carbon dioxide emissions by 85.9%, and energy consumption by 87.1% compared to traditional precast methods [Citation6]. Furthermore, this technology offers opportunities to develop sustainable mixtures for construction [Citation7,Citation8] and fabricate multifunctional concrete elements [Citation9–13]. As this technology matures and becomes more mainstream, it is expected to bring significant changes to the construction industry, offering quicker, cost-effective, sustainable, and multifunctional building solutions [Citation14,Citation15]. Among multiple available 3D printing technologies, extrusion-based 3D printing is a widely used method. This technique employs 3D printers to deposit fresh concrete layer-by-layer [Citation16].
Extrusion-based 3D concrete printing technology employs distinctive concrete mixtures and places unique demands on fresh concrete. It requires shape stability and failure resistance for the printed layers, both under their weight and that of subsequent layers, a characteristic referred to as buildability [Citation17–19]. Beyond buildability, the concrete material must sustain flowability during the pumping and extrusion process, which can be challenging given that these requirements contradict each other [Citation17,Citation20]. Consequently, understanding the characteristics of the concrete materials used in this technology is crucial for guaranteeing a successful printing process.
1.1. 3D printable concrete mixtures
Currently, different approaches exist for making concrete mixtures used in 3DCP construction. Among these, stiff mixtures (also known as mono-component mixtures, 1 K) and set-on-demand mixtures (also known as two-component mixtures, 2 K) [Citation21] are explored in this study. All ingredients of a stiff mixture are blended in a single mixing phase to achieve the desired stiffness at the end of mixing. While the sequence of adding ingredients may vary or occur stepwise, ultimately, all components are included in the primary mixing stage, resulting in a single, stiff mixture. On the other hand, for two-component mixtures (2 K), dry materials are proportioned and mixed so that a flowable concrete mixture is achieved at the end of the primary mixing stage. This mixture is then pumped to the nozzle and stiffened there by in-line injecting and mixing with another component (chemical admixture); hence, it is called a two-component mixture.
1 K mixtures have a high initial yield stress and a relatively lower structural build-up rate [Citation21]. These mixtures, known for their short open time, must be utilised within a limited time window. The ‘open time’ refers to the period when a printable concrete mixture can be extruded into the desired geometry [Citation22]. However, stiff mixtures pose a risk of causing blockages in the printing circuit if their open time is exceeded, thus contributing to interruptions in printing and potential harm to the hose, pump motors, and nozzle. Further exacerbating this is the significant pumping energy required to transport these mixtures, making pumping to great heights or long distances difficult [Citation23]. Stiff mixtures also present challenges regarding buildability, such as the maximum number of layers that can be printed and the intricacy of the design. Their printability tends to be more vertical, making them more similar to 2.5-dimensional prints rather than true 3D prints. Stiff mixtures typically can be printed to a height of around 0.5–0.7 m [Citation24–26], which motivates the use of alternative methods such as the set-on-demand approaches [Citation27,Citation28].
Set-on-demand mixtures initially use a flowable mix, such as self-consolidating concrete (SCC), which flows under self-weight. This material is stiffened by adding chemical accelerators near the nozzle, which speed up the hydration kinetics and give shape stability to the extruded concrete [Citation23,Citation29,Citation30]. Compared to stiff mixtures, set-on-demand mixtures offer a more flexible option due to their extended open time, facilitating longer transport and storage durations. The reduced pumping power required to transport flowable concrete from a hopper to the nozzle is a clear advantage, and the threat of pipe blockage is markedly diminished [Citation23]. The set-on-demand approach provides enhanced design freedom, facilitating the creation of complex structures and intended 3D prints. Importantly, with set-on-demand mixes, it becomes possible to enhance the construction rate [Citation24]. Hence, the set-on-demand approach presents an opportunity to curtail the construction time and cost associated with 3D construction printing projects, signalling an exciting prospect for the field [Citation21,Citation29,Citation31–33].
As mentioned above, this study primarily focuses on two distinct types of cementitious concrete mixtures, yet it is essential to acknowledge that other types of concrete mixtures are also being used for 3DCP application; notably, thixotropic printable mixtures present a compelling alternative to stiff mixtures [Citation22]. While these mixes intend to bring several advantages compared to stiff mixtures under study, it is important to note that they too face challenges related to buildability and set-on-demand can also be applied to thixotropic mixtures to improve their vertical construction rate and print stability. Moreover, set-on-demand strategies have been effectively employed with geopolymers [Citation34,Citation35]. Other than chemical intervention at the nozzle, rapid structural build-up has also been activated with magnetically responsive aggregates [Citation36,Citation37] and microwave heating near the nozzle [Citation38,Citation39]. Nevertheless, a comprehensive discussion of these set-on-demand methods exceeds the scope of the current paper.
1.2. Literature on buildability assessment
1.2.1. Theory
The transformation of printing concrete mixtures from a plastic state to a brittle state accompanies the development of shear and compressive strengths, as well as stiffness. This transition is predominantly governed by two interrelated processes: the physical phenomenon involving binder particle flocculation at rest and the chemical phenomenon associated with the formation of hydration products at the contact points between binder and aggregate particles [Citation40]. Upon contact with water, binder particles undergo flocculation, catalyzing a three-dimensional structural build-up; nevertheless, this structure can disintegrate under shearing forces and reassemble when allowed to rest [Citation41]. Concurrently, synthesising hydration products from the chemical reaction between binders, water, and admixtures significantly improves fresh concrete's green strength and stiffness [Citation42]. Commencing at the nano and microscales, these processes evolve progressively, developing a three-dimensional structural lattice that facilitates the hardening of fresh concrete and provides resistance to external stresses. The hardening of the fresh printable concrete can be characterised by Roussel’s linear model [Citation41], as given in Equation (1).
(1)
(1) Where
is the initial yield stress and
, represents the elapsed resting time. [Citation43,Citation44].
denotes the structuration rate or structural build-up rate which is fundamental for buildability (successful stacking of concrete layers) during the 3D concrete printing process [Citation40]. The time-dependent yield stress
, a crucial property for understanding and optimising 3D concrete printing (3DCP) processes [Citation45], can also be described using other models such as Perrot’s exponential model [Citation40], and Kruger's bilinear model [Citation26].
1.2.2. Failure modes in 3DCP
Literature regarding 3D printed concrete structures has documented two primary types of collapses: material failure, also known as plastic collapse, and stability failure, or elastic buckling. Enhancing the resistance of concrete to these failures involves optimising the strength and stiffness of deposited layers through mix design and printing process parameters. Precise measurement of the influencing rheological properties is essential for evaluating the buildability of a potential concrete mixture [Citation45]. Plastic collapse prevails when the vertical load on the bottom layers, which is time-dependent and induced by the deposition of subsequent layers, surpasses the critical failure stress
of these layers, as determined by Equation (2). This failure type manifests as flow-on-set of the bottom layers and consequently leading to the collapse of the entire structure. Flow-on-set refers to the failure state of a material where it undergoes significant deformation without a corresponding increase in external loads.
(2)
(2) Here
, g, h, R, and t represent the density, the gravitational force, the structure's height above the first layer, the building rate, and the age of the first layer, respectively. The critical vertical failure stress, in turn, is related to the yield stress of the deposited material. The material's compressive strength can be related to yield stress according to Equation (3) [Citation4,Citation45,Citation46], as employed in this study.
(3)
(3) Stability failure (buckling failure) is another common occurrence in 3DCP. It frequently happens in more considerable print heights and is characterised by local or global instability of the whole printed structure without excessive deformation in the first printed layer [Citation47]. Theoretically, it is related to Young's modulus of the material, and it should be higher than the critical stiffness value
given by Equation (4) as specified by Roussel et al. [Citation17], where ρ is the density, g is the gravitational constant, A is the area, ht is the printed structure's height at the time (t), and
is the quadratic moment of inertia. Equation (4) describes the elastic buckling resistance as a function of the rheological evolution of concrete properties, filament dimensions, print geometry, and printing speed.
(4)
(4) The above discussion indicates that a minimum of two material properties are necessary for examining printing failure: a shear or compressive strength property to ascertain the moment of plastic failure and a stiffness property to compute the moment of elastic buckling failure.
1.2.3. Buildability assessment
Buildability, the central focus of this research, refers to the capability of an extruded layer to maintain its shape and size under the self-weight and cumulative load of overhead layers [Citation18]. This critical property of the printing process depends on the mix design, structural build-up or evolution of rheological properties, and various printing process parameters, including printing geometry, printing speed, nozzle variables (geometry, size, and flow direction), inter-layer time gap, and nozzle standoff distance or layer pressing [Citation4,Citation18,Citation41,Citation48,Citation49]. To achieve buildability, preclude cold joint formation, and ensure adequate interlayer bond strength, a delicate equilibrium must be achieved between the rheological evolution of concrete and printing process parameters [Citation44,Citation46,Citation49,Citation50]. During 3D construction printing, which is a formwork-free process, extruded layers demand higher yield stress and stiffness, making it essential to measure the structural build-up and fine-tune concrete strength or printing process parameters to avert structural collapse.
Buildability tests quantify the maximum number of printable layers for a specific geometry before significant deformations occur in the extruded layers or the entire print structure fails [Citation51,Citation52]. Standard test methods for measuring the buildability of 3D printable mixtures are currently lacking [Citation53]. Buildability has also been explored through direct printing tests [Citation54] as well as indirect means, including analytical methods [Citation26,Citation40,Citation41] and simulation models [Citation47,Citation55–57]. Additional discussion about these methods can be found in the literature [Citation45,Citation54,Citation58,Citation59]. Although the direct printing tests are accurate and consider all influences, these tests are resource-intensive and time-consuming. Analytical models, such as those developed by Perrot [Citation40] and Roussel [Citation41], predict buildability through concrete rheological and mechanical properties, printing process parameters, and printing geometry characteristics. Simulations such as the finite element model (FEM), computational fluid dynamics (CFD) model, and discrete element method (DEM) have been researched to minimise potential failure modes and secure buildability of concrete [Citation54]. Set-on-demand mixtures have recently been introduced as concrete mixtures in the field of 3DCP. Compared to the stiff mixtures which are considered to evolve linearly, bi-linearly, or exponentially [Citation40], the rheological evolution of set-on-demand mixtures has not been fully explained in the literature. This necessitates detailed research investigations for shear, compressive strength, and stiffness evolution of set-on-demand mixtures to gain an understanding of their buildability and appropriate tools for quantifying these properties.
1.3. Research gap and objectives
Construction of tall and complex geometrical structures with 3D construction printing is susceptible to construction-stage instability, making the analytical prediction of printing failure crucial for engineers in this field. A thorough understanding of the constitutive behaviour of printable concrete under external stresses is essential for forecasting the stress–strain condition of individual layers and ensuring the stability of the entire printed object. The existing literature predominantly addresses stiff mixtures’ rheological evolution and buildability [Citation17,Citation26,Citation40,Citation60–62]. Perrot et al. [Citation63] used the squeeze flow test to indicate structural build-up for a stiff mixture and predicted the number of layers. Wolfs et al. [Citation47,Citation64] used direct and triaxial shear tests on a stiff mixture to estimate the number of printable layers. Kruger et al. [Citation26] used rheometry to assess the structural build-up of thixotropic mixtures. Ivonva et al. [Citation60] used compression, shear, and penetrometry tests on stiff mixtures and tried to indirectly measure the number of vertical layers. Bos et al. [Citation17] also tested stiff mixtures on compressive and shear strength tests and ultrasonic pulse velocity tests to measure structural build-up. In the case of set-on-demand mixtures, Boscaro et al. used a slow penetration test and UPV to measure the structural build-up of calcium aluminate in an accelerated mixture [Citation65]. Das et al. used the synergetic effect of calcium aluminate cement and a retarder to design a set-on-demand mixture and studied its structural build-up utilising a modified oscillatory rheometry test [Citation66]. Chen et al. used calcium nitrate in controlling the in-line rheology of a limestone-calcined based mixture and tested its structural build-up using a small amplitude oscillatory shear test [Citation67]. On the other hand, for the predication of the buildability of set-on-demand mixtures, analytical and simulation models require the temporal values of their rheo-mechanical properties (yield stress, compressive strength, stiffness, and structuration rate) during early construction stages. However, there is a notable lack of detailed discussion on the rheo-mechanical properties evolution of set-on-demand cementitious mixtures [Citation65,Citation68]. The suitability of characterisation tests designed for stiff mixtures [Citation47,Citation53,Citation69,Citation70] when applied to set-on-demand mixtures is uncertain. This uncertainty arises from their non-linear evolution of rheo-mechanical properties. Consequently, further research is needed to identify the most appropriate and efficient testing methods for these rapidly hardening mixtures. Additionally, simultaneous comparisons between the rheological evolution of stiff mixtures and set-on-demand mixtures in controlled environments is limited in the previous studies. To address these gaps, this study conducts an in-depth investigation of the rheological properties of an established shotcrete accelerated mix and compares it with a stiff mixture. Four test methods were employed to perform shear and compressive strengths, stiffness, and structuration characterisation analyses of both stiff and set-on-demand mixtures. Furthermore, printing tests were carried out with both mixtures and printing failure modes were discussed in light of the rheo-mechanical results. The findings of this study can be helpful for characterising the structural build-up of set-on-demand mixtures. By evaluating the effectiveness of various test methods in characterising set-on-demand printable mixtures, this research highlights which methods might be most reliable for measuring structural build-up during the early stages of construction.
2. Materials and experiments
2.1. Materials
This study utilised a stiff mixture without any accelerator, referred to as a one-component mixture (1 K), and a set-on-demand mixture, accelerated by inline mixing of an admixture, designated as a two-component mixture (2 K). These two mixes were specifically chosen as they represent the two popular rheology controlling mechanisms in the context of 3DCP and also provide a comprehensive perspective on the range of material behaviours, from traditional to more modern approaches. A commercial premix material (3D-ASIACEM21L) obtained from Asia Cement, Korea, was utilised for the stiff mix. The stiff mix was prepared with a water-binder ratio of 0.26 and a polycarboxylate ether-based liquid admixture. A flowable mixture was made as a base material for a set-on-demand approach using Ordinary Portland Cement (Type I), class C fly ash, silica fume, and silica sand with a maximum aggregate size of 1 mm. The water-binder ratio of 0.4 and water reducer admixture with a dosage of 1% of the binder weight was used in flowable mortar. The slump flow diameter of the flowable mix was measured after lifting the truncated-frustum flow table cone, which had a height of 60 mm, top diameter of 70 mm, and base diameter of 100 mm. It should be noted that the 25 drops typically applied in flow table test were omitted in this procedure, and the slump flow was assessed solely under the self-weight. The measured slump flow of flowable mix was 190 mm. The use of different mix compositions for the set-on-demand mixture was based on the unique requirements of the secondary in-line mixing system, as a highly flowable mixture facilitates convenient in-line mixing at the nozzle. Such a flowable composition is critical to ensure reduced residence time and minimal mixing space within a lightweight nozzle setup [Citation21]. An alkali-free liquid shotcrete accelerator with a dosage of 7.5% of the binder weight was used to obtain rapid structural build-up for set-on-demand of flowable mixture. This dosage was selected after multiple trial and error tests with different accelerator dosages. Additional details of the selection of this dosage are discussed in a previous study [Citation71]. According to ASTM C403 [Citation72], the stiff mixture showed initial and final setting times of 410 and 630 min, respectively, while the set-on-demand mixture exhibited initial and final setting times of 15 min initially and 300 min, respectively. shows the mix proportions of both investigated printable mixtures. These mixtures were initially mixed in a planetary mixer for 8 min. A portable shear vane device was used to assess the quality of the stiff mixture, while a flow table test was utilised for quality assurance of the flowable mixture at the end of mixing. For offline characterisation tests of stiff mixture, casted specimens were prepared from the fresh concrete at the end of mixing. Whereas in the scenario of set-on-demand mixture, flowable mixture underwent an additional 30 s of mixing after adding the set accelerator and then the concrete was used for making casted test specimens for offline characterisation tests. In 3D concrete printing field, offline characterisation tests can be defined as testing methods carried out independently of the main printing circuit. contrasting with inline tests conducted during printing. These tests typically involve extracting samples from freshly mixed concrete and subsequently analyzing them on a separate testing platform to assess specific properties.
Table 1. Mix proportion (kg/m3).
2.2. Characterisation tests
2.2.1. Uniaxial unconfined compression test
This test was conducted to determine the green strength and Young's modulus for both mixtures. Test samples had a height and diameter of 10 and 5 cm, respectively, with a height-to-diameter ratio of 2. Although sample sizes in existing literature vary, most studies use a height-to-diameter ratio of 2 [Citation53,Citation69], allowing for shear failure on a diagonal plane, as specified by ASTM D2166 [Citation73]. Specimens were tested in displacement control mode at a 20 mm/min rate. A locally developed tabletop compression testing machine, CORAL Compression machine [Citation74], with a 500 N load cell was used for the stiff mixture, while a Universal Testing Machines of MTS Systems Corporation (E43 MTS) with a 50 kN load cell was used for the set-on-demand mix, as shown in a. Load and displacement were recorded, along with the specimen's lateral and vertical deformation. Sample deformation was assessed by measuring the width changes of samples during compression in UUCT using experimental video data. This data was processed using a MATLAB programme designed to capture and analyze width changes accurately. The programme calculated the width at the midpoint of each sample, ensuring consistent measurement across all samples. Time-dependent Young's modulus was calculated by analyzing the linear portion of the strain–stress curve for each testing age. UUCT results of both mixtures were used in the calculation of the printable number of layers, as discussed in the following sections.
2.2.2. Shear vane test
The use of shear vane is a popular approach for quantifying the yield stress of fresh concrete [Citation75–77]. For both printable mixtures, the static yield stress and its growth are much more essential than the dynamic yield stress since the material's print buildability is tested after pumping and extrusion. Therefore, this study used the vane test to quantify only the static yield stress evolution through time. The vane test is conducted using an apparatus that includes a rod with mounted four-bladed vanes with a diameter (D) of 90 mm and a height (H) of 65 mm. This instrument was inserted in the concrete sample such that only its top edges were visible on the concrete surface (b). The blades were rotated at a rate of 1 rpm to determine the peak torque, which was then converted to the yield stress (τ) following Equation (5) [Citation77]. For the stiff mixture, measurements were taken until 90 min, whereas only partial results (until 11 min) could be obtained for the set-on-demand mixture.
(5)
(5)
2.2.3. Ultrasonic pulse velocity (UPV)
An IP-8 ultrasonic measuring system with a 25 kHz transducer/receiver by UltraTest GmbH, Germany, was used to measure the evolution of the ultrasonic pulse velocity, as shown in c. The material was poured slowly into the mold and compacted slightly to establish complete contact with the transducer and receiver. In this test, the transducer generates a longitudinal pulse wave, passing through the fresh concrete sample before being picked up by the receiver at the opposite end. Then, using the distance (L) between the receiver and transducer and the wave's travel time (tupv), the ultrasonic pulse velocity (UPV) was determined according to Equation (6) [Citation78]. UltraTestLab V6 (software) was used to record the UPV value of the printable mixes every minute for at least 90 min. The tests were conducted in a relatively quiet place to minimise noise interference.
(6)
(6)
2.2.4. Slow penetration test
The slow penetration testing system employed a conical penetration tip with a slant height of 13 mm and a radius of 7.5 mm. The concrete samples were placed in 90 mm diameter and 140 mm height cylindrical containers immediately after mixing. The test started after slowly submerging the cone tip into the sample until it was levelled with the top surface. The fully submerged conical tip is then further pushed into the sample with a slow penetration rate of 20 mm/h, and the penetration resistance with time is recorded for 90 min, as shown in d. The yield stress was calculated by dividing the measured force by the cone surface using Equation (7) [Citation79], where Fc, τp, R, and h represent the penetration force, slow penetration yield stress, radius and height of the conical tip, respectively.
(7)
(7)
2.2.5. Printing investigations
Currently, there is no standard test method to evaluate the buildability of printable concrete. The absence of a standardised test method has led to various approaches among researchers to test concrete using different printing process parameters [Citation47,Citation51,Citation52,Citation64]. The geometry used for buildability tests varies in the literature, but a hollow cylindrical shape is frequently employed [Citation64,Citation65,Citation80]. Consequently, this study also adopted a hollow cylindrical print geometry, as shown in e. The vertical construction rate, a crucial parameter of the printing process, determines the printing speed and the time gap between two layers [Citation40]. A high building rate can lead to premature failure, while a slower rate can mitigate failure risks and potentially result in a successful printed structure. Therefore, two distinct vertical construction rates were chosen for each mixture to achieve stable and failure states of prints for both concrete mixtures. The selection of building rates and printing speeds in this study was based on the findings of the prior research [Citation40,Citation41]. Given the stiff mixture's lower structural build-up and limitations, its vertical construction rates were set lower than those of the set-on-demand mixture. The vertical construction rates for the stiff mixture were 0.8 and 1.44 m/hr, while those for the set-on-demand mixture were 2.57 and 5.14 m/hr, respectively, as summarised in . These rates were calculated using the printing length and printing speed for extruding each layer. A hollow cylindrical geometry with a diameter of 500 mm was used for the stiff mixture, whereas a cylindrical geometry with a diameter of 250 mm was selected for the set-on-demand mixture. The use of different cylinder diameters is also based on each concrete mix's specific properties and operational requirements. The stiff mix used a larger diameter to achieve a slower printing speed and a reduced vertical construction rate, which was deemed necessary to achieve targeted structural stability given its lower initial strength and stiffness. In contrast, for the set-on-demand mixture, which has a faster structural build-up rate and shorter open time, a smaller diameter was utilised. This allowed for higher printing speeds and rapid vertical construction rates while mitigating potential issues like cold joint formation. A target height of 450 mm was set for a stiff mixture using a laboratory gantry-type printer with a maximum workspace of 500 mm in print height. The set-on-demand mixture, which has the potential to reach a higher printable height [Citation65], was assigned a target height of 1100 mm for buildability testing using a robotic arm printer. The printing processes for printable mixtures were performed for both chosen vertical construction rates until the print structure collapsed or the target print height was achieved. It is important to note that the inter-layer time gap was consciously kept short in the current work, considering the material type and printing process parameters to avoid the adverse effect of the cold joints formation [Citation81,Citation82].
Table 2. Printing strategy for 3DCP with the selected mixtures.
The plastic failure observed in direct printing tests was juxtaposed with buildability predictions derived from UUCT and shear vane tests. The number of layers the material could support before plastic failure was calculated using Equation (2), incorporating either the compressive strength result (from UUCT) or the yield strength result (from the vane shear test). These results were then compared with the number of layers that could be constructed at a specified building rate to identify the layer at which plastic failure would have occurred. It should be noted that Roussel’s model was adopted in this study, which represents the yield stress () as a linear function of time. While the selection of Roussel's model in this study was motivated by its straightforwardness and ease of interpretation. It is essential to note that this model is conservative. This conservative aspect may lead to underestimations of yield stress. Therefore, while the model provides a reliable baseline for safety, it may not fully capture the higher thresholds of material performance. For elastic buckling, the number of buildable layers was calculated using Equation (4) with the stiffness result from the UUCT and compared to the printable layer that could be printed for the selected building rates.
For 3D printing tests, the fresh stiff mixture was transported to the hopper and then transported with an eccentric screw concrete pump to the printer nozzle via a 7 metre long hose where concrete was extruded along print path (schematic illustration shown in ). The authors’ research group has locally designed this eccentric screw pump to transport concrete in a continuous filament manner. This pump functions by rotating a screw inside a barrel, moving the concrete along and directs it into the hose. A key factor in this process is the rotational speed of the screw pump, which critically influences the concrete extrusion rate, as previously discussed in another study [Citation83]. The printer system used in this study used a centralised system, where print head's three-axis (X, Y, Z) motion along print path and concrete pump's rotational speed are controlled from the single interface of the server computer. The quantity of concrete required for extrusion on the print path was determined and translated into G-code. This G-code instructed the system on both the amount of concrete to be extruded and its precise three-dimensional positioning to print the desired structures. In the case of the set-on-demand system, two pumps were used. The first is the same eccentric screw concrete pump of stiff mixture, and second is the accelerator pump to transport accelerator from the tank to the inline mixer. Flowable mortar and accelerator were mixed in the inline pan mixer with a rotational speed of 500 rotations per minute. A pan mixer with 20 blades was used at this stage. The driving torque of inline mixer was carefully monitored on a digital interface during the whole printing system to ensure it did not get clogged and that the inline mixing system stayed consistent. After each print job, this mixer was thoroughly cleaned before being used for the next printing. It is worth mentioning that both printers employed identical extrusion systems, pipes, and nozzle, ensuring consistent material handling and minimal variation. The primary difference lies in the supporting systems for nozzle holding and movement. The 1 K printer, the laboratory-scale gantry printer, uses a vertically hanging rod, which lacks the necessary stiffness to handle vibrations from inline mixing. Conversely, the robotic arm used for the 2 K mixture provides adequate stiffness to control the vibrations of the inline mixing nozzle, ensuring precise extrusion along the print path during the printing process. The detailed visualisation of the experimental setups used in the testing of both mixtures are shown in .
3. Results and discussion
3.1. Characterising test results
3.1.1. Uniaxial unconfined compression testing (UUCT)
and illustrate the evolution of compressive strength and stiffness (Young’s modulus) performance of the stiff and set-on-demand casted mixtures over time, highlighting the significant differences between the two mixtures. The stiff mix showed slow and steady progress in compressive strength and stiffness during the testing period, while the set-on-demand mix started with higher values and developed more rapidly. The measured strength and Young’s modulus values of the stiff mix discussed in this study are comparable to the strength and stiffness of stiff mixtures reported in previous literature [Citation17,Citation84]. However, data on the compressive and Young’s modulus values of the shotcrete-accelerated set-on-demand mix measured with uniaxial unconfined compression testing are rare in the current literature.
Figure 3. Green strength evolution measured with Uniaxial Unconfined Compression Test for stiff mix (1 K) versus set-on-demand mix (2 K).
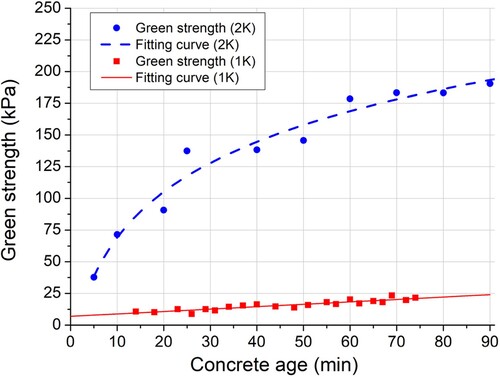
Figure 4. Young's modulus evolution measured with Uniaxial Unconfined Compression Test for stiff mix (1 K) versus set-on-demand mix (2 K).
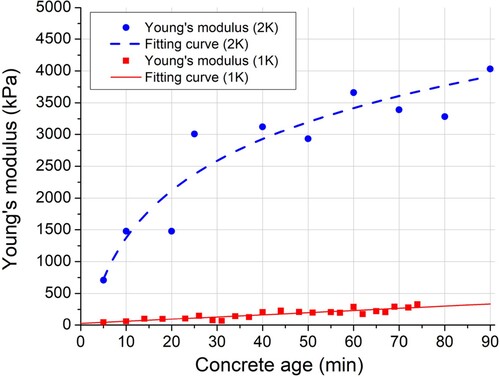
The compressive strength and Young’s modulus of the stiff mix can be described by linear equations (8 and 9). The compressive strength increased from approximately 6.95 kPa to 24.05 kPa over 90 min, with a total growth of 17.12 kPa. The structuration rate, Athix was calculated by dividing the total acquired strength by the total testing time. The measured structural build-up rate, Athix of UUCT was 0.19 kPa/min. Similarly, the Young’s modulus of the stiff mix increased from approximately 26.52 kPa to 335.67 kPa over 90 min, with a total growth of 309.15 kPa. The calculated structural build-up rate, Athix in terms of UUCT- Young’s modulus was 3.43 kPa/min. It should be noted that linear relationships have been widely used for discussing the compressive strength of stiff mixtures over time [Citation17,Citation84–86]. For instance, Wolfs et al. reported similar findings with a linear model showing a comparable rate of structural build-up of 0.15 and 0.31 kPa/min for compressive strength and 1.27 and 3.42 kPa/min for Young’s modulus in a stiff printable mixture [Citation84].
(8)
(8)
(9)
(9) In distinction to the stiff mix, the compressive strength of the set-on-demand mix exhibited a non-linear increase, as shown in . The strength and stiffness of the set-on-demand mix initially increased rapidly and then tended to saturate. A logarithmic function can better describe the development of set-on-demand strength and stiffness according to Equations (10) and (11). However, extrapolation of the compressive strength and stiffness for earlier concrete age (below three minutes) gives negative values, which is obviously not possible; hence the given logarithmic functions may be used to express the developing trend of compressive strength and stiffness beyond three minutes. Flat et al. [Citation31] reported a non-linear increase in strength gain for aluminate-accelerated concrete in the context of in-line rheology control for 3DCP. Rubine et al. [Citation87] also documented the non-linear evolution of the yield stress of shotcrete accelerated mixtures measured using a direct shear test, where the strength initially increased rapidly and then attenuated slowly. Keeping in view the reported results of previous limited research studies, it can be suggested that the developed non-linear evolution of compressive and stiffness of set-on-demand mixture can be extrapolated to other mixtures using shotcrete accelerators.
(10)
(10)
(11)
(11)
3.1.2. Shear vane test
shows the yield stress evolution with concrete age for the stiff mix and set-on-demand mix with the resting time. The yield stress evolution of the stiff mix was characterised by a linear function, as given in Equation (12). The literature shows that numerous researchers [Citation60,Citation88–90] have also used the linear approach proposed by Roussel [Citation91] to describe the evolution of yield stress of printable concrete with time. In this study, the yield stress of stiff mix was observed to increase linearly from the initial value of 2.11 kPa to 8.51 kPa with a structural build-up rate, Athix of 0.064 kPa/min during the investigated time. Bos et al., [Citation17] reported that yield stress of non-accelerated mixtures usually evolves linearly from 1 kPa to 10 kPa with a rate between 0.05 to 0.5 kPa/min, which supports the findings for this study for the stiff mixture. Ivanova et al. also reported a comparable structuration rate () after testing printable stiff mixtures with a rotational rheometer [Citation60].
Figure 5. Yield stress measured with shear vane test: stiff mix (1 K) versus set-on-demand mix (2 K).
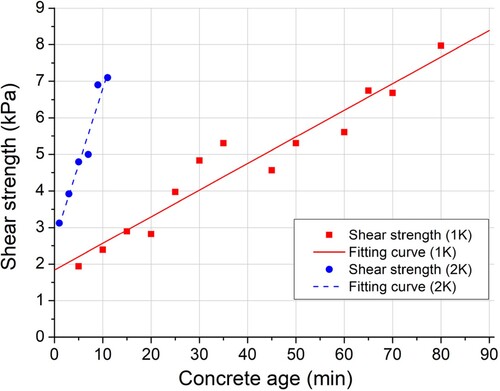
The vane shear measurement was only possible for the set-on-demand mix until 11 min after adding the set accelerator. Measurements beyond 11 min were challenging because of the difficulty of manually shearing the concrete due to its fast structuration rate. also shows the rapid evolution of yield stress of concrete until 11 min, and for this limited testing time, the evolution of yield stress was characterised by a linear function (Equation 13). The structuration rate of the set-on-demand mix was approximately 0.41 kPa/min, which is almost six times higher than that of the stiff mix, demonstrating the substantial but not sole impact of the accelerator on early-age performance, alongside other influential factors from the 1 and 2 K mix designs [Citation76].
(12)
(12)
(13)
(13)
3.1.3. Ultrasonic pulse velocity (UPV)
shows the ultrasonic pulse velocity values for the stiff mix, which increased linearly from 21.8 m/sec to 40.77 m/sec during the first 90 min of the concrete age. Based on the results of the stiff mix, the evolution of the ultrasonic pulse velocity can be expressed as a linear function of concrete age represented by Equation (14). The structuration rate, Athix of the stiff mix in terms of ultrasonic pulse velocity, is 0.22 (m/sec)/min. Wolfs et al. [Citation84] also reported a linear evolution of UPV for a stiff printable mixture during the early ages of concrete; however, the measured UPV values were reported to increase from 100 to 440 m/sec within the tested time of 0-90 min, with a structuration rate of 3.85 m/sec. This study's observed UPV values and corresponding UPV structuration rate are lower in comparison. The difference in UPV values could be attributed to the different mixture designs and particle sizes in both mixtures.
(14)
(14) For the set-on-demand mix, it can be observed that at the very beginning, the UPV increases sharply in a non-linear manner due to the accelerator effect, and then the rate of UPV slowly reaches a plateau at around 828 m/sec. This rapid evolution of the UPV value indicates the prompt changes in the microstructure of the set-on-demand mixture due to the shotcrete accelerator, which the formation of hydration products could cause, rapid connectivity of solid particles due to the precipitation of hydration products and reduction in the quantity of free water amount [Citation92]. However, after the rapid evolution, the rate of UPV growth slows down and finally reaches a plateau. A similar trend in the evolution of UPV was also reported in a recent study where calcium aluminate cement was added as an activator to control rheology of 3DCP material [Citation65]. The evolution of UPV of the set-on-demand mixture used in this study can be characterised by a logarithmic fitting model, as shown in Equation (15). The two concrete mixtures under examination exhibited distinct kinetics of strength, stiffness, and UPV developments.
(15)
(15)
3.1.4. Slow penetration test
shows the slow penetration test results for stiff and set-on-demand mixtures. The penetration resistance for the stiff mix increased from 3.04 kPa to 119.8 kPa during the initial 90 min, while the set-on-demand mix showed an evolution of 3.62 kPa to 422 kPa during the same age. The evolution of the penetration resistance or yield stress (τp) for both mixtures showed approximately a logarithmic increase, as given by Equations (16) and (17), respectively. It should be noted that the yield stress values measured from this test method are significantly higher than those obtained by the other test methods. As mentioned earlier, this method assumes that the resistance to the penetration force is mainly because of the yield strength of the material. However, the significantly higher result for the mixtures used in this study indicates that other contributing factors could lead to the overestimation of this resistance. One factor could be due to the surcharge weight of the surrounding sample. As the penetration tip penetrates deeper into the sample, the amount of the sample weight above the cone tip (surcharge weight) increases; this will apply additional resistance to the penetrating head, increasing the penetration resistance. This is a newly developed test method, and this test's measured values depend on the penetrating speed, needle shape, container size, and boundary conditions. In addition, the relationship of slow penetration results with the shear vane test results, compressive strength, and stiffness of fresh concrete mixtures has not been established yet. Likewise, the translation of the measured yield stress from the slow penetration test into the number of printable layers and print geometry stability is non-existent. Consequently, the slow penetration test requires further investigation before it can be adapted to the buildability prediction of 3D printable mixtures; hence, it is not used to predict the buildability of both mixtures in this study. However, this test is beneficial for developing new mixture designs and fine-tuning the accelerator dosage, as discussed in other studies [Citation65,Citation93].
(16)
(16)
(17)
(17)
3.2. Buildability results
3.2.1. Direct printing test results
Stiff mixture: Print test I was performed with a building rate of 0.8 m/h, and it was stopped after the structure reached its desired height (450 mm). The structure was stable, with no excessive deformation or bulging observed, and consisted of 45 layers, as shown in a. Print test II with a building rate of 1.44 m/hr was initially stable, and no excessive deformation or bulging was detected. However, as the printing progressed to higher print heights, the bottom layer started showing excessive deformation, and print failure occurred at 16 layers, as shown in b. This collapse mode was initiated by the material failure due to excessive cumulative gravitational load from the subsequent layers imparted on the first layer, initiating plastic failure, and followed by the collapse of the printed layers. The observed buildability is the cumulative result of several factors, including the structural build-up rate, structure dimensions, printing speed, extrusion rate, etc. It should be noted that initiation of the plastic failure in the second layer has been also reported instead of the first layer. This failure in the second layer has been associated with the more rigid base friction and confinement effects upon the first layer compared to the second layer [Citation94]. Print tests I and II also show that increasing the construction rate decreased the buildability of the printable cementitious material since the yield stress of the first layer had less time to develop due to structuration and compete with the gravitational force-induced shear stresses. It should be noted that the print path in the G-code was designed so that the nozzle ascends to the next layer height along a sloped path, rather than abruptly rising from one layer to the next layer. This is clearly demonstrated in b.
Set-on-demand mixture: Print test III was conducted at the rate of 2.57 m/hr, and it was stable throughout the printing test until the target printable height was reached, as shown in a, whereas Print test IV showed an initially stable structure, but as the printing progressed, the structure became unstable and failed by global instability at the 88th layer of the structure. The structure showed no excessive deformation at the bottom layers, as depicted in b. The occurrence of structural instability is due to lateral sway, which occurs when the required stiffness exceeds the actual stiffness of the set-on-demand mixture. This discrepancy stems from the material's intrinsic stiffness and geometrical properties of the printed hollow cylinder structure. Direct printing results are also summarised in .
Figure 8. Buildability test using stiff mixture: (a) successful print with the building rate of 0.8 m/hr and (b) plastic failure at the building rate of 1.44 m/hr.
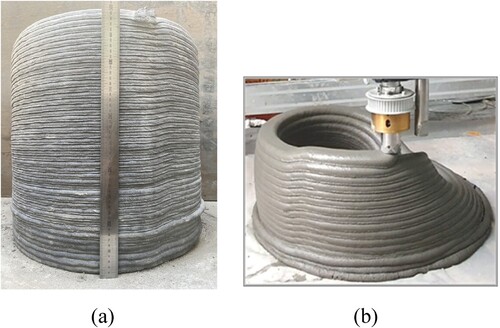
Figure 9. Buildability tests using set-on-demand mixture: (a) successful printing with the building rate of 2.57 m/hr, (b) elastic buckling failure at the building rate of 5.14 m/hr.
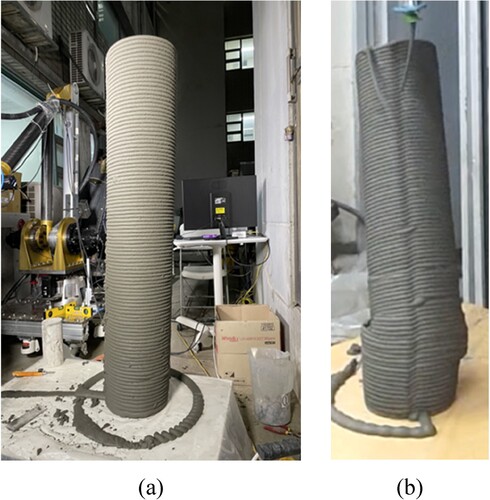
Table 3. Direct printing test results.
3.2.2. Material buildability behaviour versus buildability predictions
The direct printing test results revealed a plastic failure mode for the stiff mixture and an elastic failure for the set-on-demand mixture for the tested print geometries and adopted vertical construction rates. Consequently, the forthcoming discussion in this study will be confined to the plastic failure mode of the stiff mixture and the elastic buckling failure mode of the set-on-demand mixture. Predictions of elastic buckling failure for the stiff mixture and plastic failure for the set-on-demand mixture were excluded from further discussion in this article. Nonetheless, relevant discussions can be found in previously published literature [Citation71].
The two distinct building rates (0.8 and 1.4 m/hr) employed for the stiff mix resulted in varying rates of subsequent layer deposition over time, as depicted by the staircase lines in . These building rates generate different external stress rates [Citation95]. As evident in , a building rate of 1.44 m/hr accelerates the layering process compared to the rate of 0.8 m/hr, thereby reducing the printing time gap and intensifying the external stresses on the first layer. To resist plastic failure, the intrinsic yield strength of the first printed layer must consistently surpass the induced stresses. Therefore, the amount of layers that can be deposited on the top of the first layer is contingent on its evolving intrinsic yield stress. The yield stress of the concrete was gauged through indirect tests (UUCT and vane shear test), and these values were translated into the number of depositable layers using Equation (4). As discussed in earlier sections, the slow penetrometer results were excluded from buildability predictions, as this test tended to overestimate the yield stress. presents the calculated number of depositable layers from UUCT and vane shear tests, indicating that these tests do not predict identical buildability for the stiff mixture. UUCT forecasts a higher buildability, followed by vane shear.
Figure 10. Predicted number of layers for plastic failures using the UUCT and shear vane test for the stiff mixture.
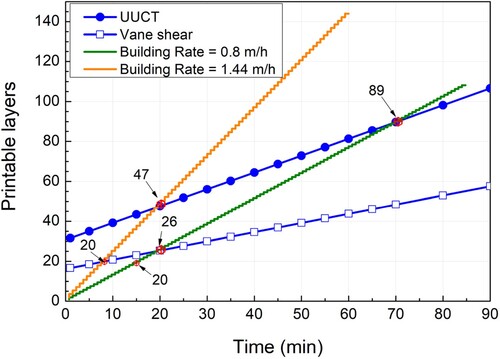
The points of intersection between the vertical building rates (0.8 and 1.4 m/hr) and the calculated permissible number of layers over time, as determined from the indirect tests, predict the print failure moments. These intersection points are marked with red circles in . At a building rate of 1.44 m/hr, the print experienced plastic collapse at the 16th layer. However, illustrates that the UUCT significantly overestimated the plastic failure up to the 47th layer. The shear vane test predicted plastic failure at the 20th layer. At a building rate of 0.8 m/hr, shows that the UUCT predicted plastic failure at the 89th layer, and the shear vane results anticipated failure at the 26th layer. Despite these predictions, the printed structure remained intact until the 45th layer. This discrepancy underscores the limitations of the vane shear results in accurately predicting buildability at the specified printing rate and time.
represents the vertical building rate for the set-on-demand mixture with rates of 2.57 and 5.14 m/hr. This figure shows that the 2.57 m/hr rate leads to a lower increase in the layer's number compared to 5.14 m/hr. Hence, the stiffness stresses induced by 2.57 m/hr are lower than those induced by 5.14 m/hr [Citation71]. also shows the permissible number of layers based on the intrinsic stiffness evolution of the material measured with the UUCT and print geometry characteristics. The trend of the permissible number of layers to avoid elastic buckling is non-linear and can be represented with a logarithmic pattern. Here, the number of permissible layers to avoid plastic buckling predominantly depends on the stiffness evolution of the set-on-demand mixture. In contrast, UUCT test results showed that stiffness evolves non-linearly, and its evolution was earlier described with a logarithmic Equation (11), applicable to concrete age beyond three minutes. The prediction of printable layers in is based on UUCT-stiffness results and does not predict the printable layers below three minutes. However, the print structure was stable at the age of three minutes and did not collapse. Thus, the utilised approach is limited in predicting buckling failure at a very early age. It is worth mentioning here that a bi-linear approach can also be used for expressing the stiffness evolution of set-on-demand mixtures based on UUCT, and in such a case, the number of printable layers to avoid elastic buckling would also be bilinear and with an intercept of a physical number of layers below three minutes. For a succinct discussion, the use of the bilinear approach is not considered here, and the discussion is only limited to the logarithmic function. Nonetheless, it is clear from this discussion that although the predicted number of printable layers for a set-on-demand mixture depends on the characteristic equation used to describe the stiffness evolution, non-linear buildability is expected for shotcrete accelerated mixtures. The current literature has not widely discussed the buildability of shotcrete-accelerated set-on-demand mixtures; however, the findings of this study open a new research opportunity to analyze the buildability of shotcrete accelerators using non-linear approaches.
Figure 11. Predicted number of layers for buckling failure using the UUCT result for the set-on-demand mixture.
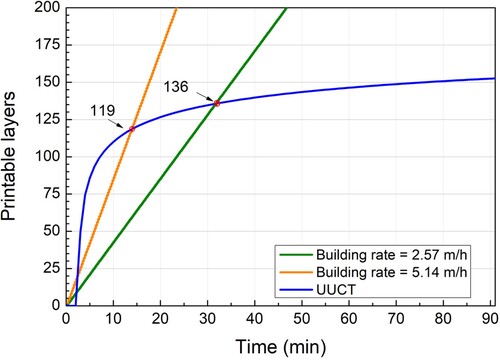
displays the buildability prediction of a set-on-demand mixture at two different building rates (2.57 and 5.14 m/hr), along with the permissible number of layers, as determined by the UUCT and print geometry properties. The points of intersection between the vertical building rates and the calculated permissible number of layers over time, as indicated by the red circles, represent the predicted failure moments of the print geometry. At a building rate of 5.14 m/hr, the structure was predicted to encounter an elastic buckling failure at 119 layers. However, the structure collapsed at the 88th layer. The predicted number of stable layers with a building rate of 2.57 m/hr is approximately 136 layers. A cylindrical structure up to 110 layers was printed, and it was stable. Hence, the buildability test partially corroborated the prediction for slower printing speed, which suggested that the structure would not collapse within the achievable print height (110 layers) of the robotic arm printer. presents a comparison of predicted print failure layer counts from test methods versus actual failure triggering layer counts in direct 3D printing tests. From these experimental results, it is apparent that the UUCT may be used to estimate the buildable heights for a set-on-demand mixes with approximate assessment, whereas the shear vane test cannot be used for such mixtures with a rapid structuration but is more suitable for stiff mixtures.
Table 4. Comparison of predicted print failure layer counts from test methods versus actual failure triggering layer counts in direct 3D printing tests.
It should be noted that the correlation between construction rates and print failure modes in 3D concrete printing is an area of active investigation, and a conclusive understanding of how specific construction rates influence print failure modes remains elusive. Current methodologies, including analytical models [Citation40,Citation41], finite element modelling (FEM), computational fluid dynamics (CFD), and discrete element methods (DEM) [Citation54], offer preliminary insights but are still in developmental stages. These approaches have yet to fully capture the complexities associated with the relationship between stresses in printed layers at the non-linear vertical and horizontal construction rates as well as the possible failure modes. Consequently, this aspect of 3D concrete printing necessitates more comprehensive research to accurately predict print stability.
3.2.3. Limitation of indirect characterisation tests
The buildability test results highlight a discrepancy between the predictions made using various indirect testing methods and those obtained from direct printing test methods. This discrepancy underscores the need for further research and the development of standardised test methods for accurately gauging the structural build-up of concrete mixtures and predicting their buildability. The non-conformity of prediction results with the direct printing results has also been previously reported [Citation51,Citation60,Citation77,Citation86]. Moreover, the predicted number of layers is derived from indirect test results, are highly dependent on factors such as shearing rate, test sample geometry, and boundary conditions. Offline test methods also fall short in accurately replicating the geometry, boundary conditions, and shearing rate of the first printed layer, which can contribute to discrepancies in buildability predictions. Another factor potentially contributing to prediction errors is that indirect characterisation test methods do not account for changes that may occur in the concrete mixture during transportation. The process of pumping and extrusion can alter the rheological properties of printable concrete. In this study, samples used for characterisation techniques were sourced from a planetary mixer, which may not fully represent the concrete's quality after pumping and extrusion. It is suspected that the pumping through a stator-rotor and extrusion could modify the rheological properties and temperature of the concrete due to the high shearing and excessive pressure applied, leading to increased dispersion of cement particles and admixtures [Citation51]. Particularly in industrial-scale extrusion-based 3D-printing processes, printable concrete is subjected to high shear rates and pressure in the rotor-stator and the extruder. Consequently, the exact rheological state of the extruded concrete may significantly vary depending on the specific extruder and printing circuit used. Therefore, a more comprehensive understanding of pumping and extrusion's impact on printable concrete's rheological properties and its influence on buildability is necessary.
4. Conclusions
This research aims to critically investigate the structural build-up in a set-on-demand concrete printing approach and compares it with that of a stiff concrete printing approach. Additionally, it evaluates the effectiveness of four characterisation methods for assessing the structural build-up of both mixtures. Investigated offline characterisation techniques were Uniaxial Unconfined Compression test, shear vane test, UPV test, and slow penetration test. Direct printing tests were also conducted to assess the print failure of both mixtures. The following conclusions are drawn from this study
Compressive strength and stiffness of stiff mixture exhibited a linear increase, adhering to established models. However, the set-on-demand mix demonstrated a more complex, non-linear growth pattern that initially accelerated before reaching a saturation point.
The yield stress of the stiff mixture steadily increased over time on the hand vane, corroborating its compressive strength results. On the other hand, set-on-demand mixture showed a rapid structural build-up which was measurable up to 11 min due to the practical limitations of this instrument.
UPV results mirrored the compressive strength results. The stiff mixture demonstrated a linear evolution, whereas the shotcrete-accelerated mixture exhibited a rapid surge followed by a gradual plateau.
The slow penetrometer test produced significantly higher yield stress and structural build-up rates for both mixtures in a non-linear manner. While this test can be a promising test for mixture design optimisation, it has limitations in predicting the maximum number of printable layers, which necessitates further research.
Direct printing tests revealed varying failure modes depending on the testing conditions. Plastic failure was identified in the stiff mixture, whereas elastic buckling initiated print failure in the set-on-demand mixture for the tested geometries and printing parameters. Moreover, a significant discrepancy was found in the number of predicted printable layers based on offline characterisation tests, indicating the need for further research to improve the precision of layer predictions in 3D concrete printing.
The results highlight that indirect experimental methods did not produce quantitatively similar results, particularly regarding the structural build-up, indicating an inherent challenge in comparing structural build-up and buildability prediction across different mixtures and testing methods, which necessitates additional research.
Credit authorship contribution statement
Bizu Melesse Birru and Atta Ur Rehman: Conceptualisation, Methodology and Data curation, Writing original-draft, Writing–review & editing. Jung-Hoon Kim: Conceptualisation, Methodology and Data curation, Writing–review & editing, Resources and Supervision.
Disclosure statement
No potential conflict of interest was reported by the author(s).
Data availability statement
The authors confirm that the data supporting the findings of this study are available within the article.
Additional information
Funding
References
- Khoshnevis B. Automated construction by contour crafting-related robotics and information technologies. Autom Constr. 2004;13:5–19. doi:10.1016/j.autcon.2003.08.012
- Tay YWD, Panda B, Paul SC, et al. 3D printing trends in building and construction industry: a review. Virtual Phys Prototyp. 2017;12:261–276. doi:10.1080/17452759.2017.1326724
- Yang W, Wang L, Ma G, et al. An integrated method of topological optimization and path design for 3D concrete printing. Eng Struct. 2023;291:116435, doi:10.1016/j.engstruct.2023.116435
- Wangler T, Roussel N, Bos FP, et al. Digital concrete: a review. Cem Concr Res. 2019;123; doi:10.1016/j.cemconres.2019.105780
- Bos F, Wolfs R, Ahmed Z, et al. Additive manufacturing of concrete in construction: potentials and challenges of 3D concrete printing. Virtual Phys Prototyp. 2016;11:209–225. doi:10.1080/17452759.2016.1209867
- Weng Y, Li M, Ruan S, et al. Comparative economic, environmental and productivity assessment of a concrete bathroom unit fabricated through 3D printing and a precast approach. J Cleaner Prod. 2020;261:121245, doi:10.1016/j.jclepro.2020.121245
- Singh A, Wang Y, Zhou Y, et al. Utilization of antimony tailings in fiber-reinforced 3D printed concrete: a sustainable approach for construction materials. Constr Build Mater. 2023;408:133689, doi:10.1016/j.conbuildmat.2023.133689
- Zhu B, Wang Y, Sun J, et al. An experimental study on the influence of waste rubber particles on the compressive, flexural and impact properties of 3D printable sustainable cementitious composites. Case Stud Constr Mater 2023;19:e02607.
- Sun J, Tang W, Wang Y, et al. Electromagnetic and mechanical performance of 3D printed wave-shaped copper solid superstructures. J Mater Res Technol. 2023;27:6936–6946. doi:10.1016/j.jmrt.2023.11.116
- Yao X, Lyu X, Sun J, et al. AI-based performance prediction for 3D-printed concrete considering anisotropy and steam curing condition. Constr Build Mater. 2023;375:130898, doi:10.1016/j.conbuildmat.2023.130898
- Sun J, Aslani F, Wei J, et al. Electromagnetic absorption of copper fiber oriented composite using 3D printing. Constr Build Mater. 2021;300:124026, doi:10.1016/j.conbuildmat.2021.124026
- Sun J, Huang Y, Aslani F, et al. Electromagnetic wave absorbing performance of 3D printed wave-shape copper solid cementitious element. Cem Concr Compos. 2020;114:103789, doi:10.1016/j.cemconcomp.2020.103789
- Ma G, Sun J, Aslani F, et al. Review on electromagnetic wave absorbing capacity improvement of cementitious material. Constr Build Mater. 2020;262:120907, doi:10.1016/j.conbuildmat.2020.120907
- Tay YWD, Lim SG, Phua SLB, et al. Exploring carbon sequestration potential through 3D concrete printing. Virtual Phys Prototyp. 2023;18:e2277347, doi:10.1080/17452759.2023.2277347
- Tay YWD, Lim JH, Li M, et al. Creating functionally graded concrete materials with varying 3D printing parameters. Virtual Phys Prototyp. 2022;17:662–681. doi:10.1080/17452759.2022.2048521
- Buswell RA, da Silva WRL, Bos FP, et al. A process classification framework for defining and describing digital fabrication with concrete. Cem Concr Res. 2020;134; doi:10.1016/j.cemconres.2020.106068
- Bos FP, Kruger P, Lucas SS, et al. Juxtaposing fresh material characterisation methods for buildability assessment of 3D printable cementitious mortars. Cem Concr Compos. 2021;120:104024, doi:10.1016/j.cemconcomp.2021.104024
- Mechtcherine V, Bos FP, Perrot A, et al. Extrusion-based additive manufacturing with cement-based materials–production steps, processes, and their underlying physics: a review. Cem Concr Res. 2020;132:106037, doi:10.1016/j.cemconres.2020.106037
- Lao W, Li M, Wong TN, et al. Improving surface finish quality in extrusion-based 3D concrete printing using machine learning-based extrudate geometry control. Virtual Phys Prototyp. 2020;15:178–193. doi:10.1080/17452759.2020.1713580
- Ashrafi N, Duarte JP, Nazarian S, et al. Evaluating the relationship between deposition and layer quality in large-scale additive manufacturing of concrete. Virtual Phys Prototyp. 2019;14:135–140. doi:10.1080/17452759.2018.1532800
- Wangler T, Pileggi R, Gürel S, et al. A chemical process engineering look at digital concrete processes: critical step design,: inline mixing, and scaleup. Cem Concr Res. 2022;155:106782, doi:10.1016/j.cemconres.2022.106782
- Rehman AU, Kim J-H. 3D concrete printing: a systematic review of rheology, mix designs, mechanical, microstructural, and durability characteristics. Materials (Basel). 2021;14:3800, doi:10.3390/ma14143800
- Rehman AU, Birru BM, Kim J-H. Set-on-demand 3D concrete printing (3DCP) construction and potential outcome of shotcrete accelerators on its hardened properties. Case Stud Constr Mater. 2023;18:e01955, doi:10.1016/j.cscm.2023.e01955
- Kruger J, Cho S, Zeranka S, et al. 3D concrete printer parameter optimisation for high rate digital construction avoiding plastic collapse. Composites Part B: Eng. 2020;183:107660, doi:10.1016/j.compositesb.2019.107660
- Bester F, Kruger J, van Zijl G. Rivet reinforcement for concrete printing. Addit Manuf. 2023;67:103490, doi:10.1016/j.addma.2023.103490
- Kruger J, Zeranka S, van Zijl G. 3D concrete printing: a lower bound analytical model for buildability performance quantification. Autom Constr. 2019;106; doi:10.1016/j.autcon.2019.102904
- Inayath Basha S, Ur Rehman A, Khalid HR, et al. 3D printable geopolymer composites reinforced with carbon-based nanomaterials–a review. Chem Rec. 2023;23:e202300054, doi:10.1002/tcr.202300054
- Inayath Basha S, Ur Rehman A, Aziz MA, et al. Cement composites with carbon-based nanomaterials for 3D concrete printing applications–a review. Chem Rec. 2023;23:e202200293, doi:10.1002/tcr.202200293
- Tao Y, Rahul AV, Lesage K, et al. Stiffening control of cement-based materials using accelerators in inline mixing processes: possibilities and challenges. Cem Concr Compos. 2021;119:103972, doi:10.1016/j.cemconcomp.2021.103972
- Reiter L, Wangler T, Anton A, et al. Setting on demand for digital concrete – principles, measurements, chemistry, validation. Cem Concr Res. 2020;132:106047, doi:10.1016/j.cemconres.2020.106047
- Flatt RJ, Wangler T. On sustainability and digital fabrication with concrete. Cem Concr Res. 2022;158:106837, doi:10.1016/j.cemconres.2022.106837
- Mohan MK, Rahul AV, De Schutter G, et al. Early age hydration, rheology and pumping characteristics of CSA cement-based 3D printable concrete. Constr Build Mater. 2021;275:122136, doi:10.1016/j.conbuildmat.2020.122136
- Bizu Melesse Birru AUR, Seungwoo K, Kim J-H. Realization of high speed 3D concrete printing with vertical construction speed of 5 m/hr, Korean concrete institute. Spring Convention. 2023;35:643–644.
- Muthukrishnan S, Ramakrishnan S, Sanjayan J. Set on demand geopolymer using print head mixing for 3D concrete printing. Cem Concr Compos. 2022;128:104451, doi:10.1016/j.cemconcomp.2022.104451
- Muthukrishnan S, Ramakrishnan S, Sanjayan J. Rapid early age strength development of in-line activated geopolymer for concrete 3D printing. Constr Build Mater. 2023;406:133312, doi:10.1016/j.conbuildmat.2023.133312
- Jiao D, Shi C, De Schutter G. Magneto-rheology control in 3D concrete printing: a rheological attempt. Mater Lett. 2022;309:131374, doi:10.1016/j.matlet.2021.131374
- Yue H, Zhang Z, Hua S, et al. Solid waste-based set-on-demand 3D printed concrete: active rheological control of cement-based magneto-rheological fluids. Constr Build Mater. 2023;404:133269, doi:10.1016/j.conbuildmat.2023.133269
- Muthukrishnan S, Ramakrishnan S, Sanjayan J. Effect of microwave heating on interlayer bonding and buildability of geopolymer 3D concrete printing. Constr Build Mater. 2020;265:120786, doi:10.1016/j.conbuildmat.2020.120786
- Kanagasuntharam S, Ramakrishnan S, Sanjayan J. Investigating PCM encapsulated NaOH additive for set-on-demand in 3D concrete printing. Cem Concr Compos. 2024;145:105313, doi:10.1016/j.cemconcomp.2023.105313
- Perrot A, Rangeard D, Pierre AJM. Structures, Structural built-up of cement-based materials used for 3D-printing extrusion techniques. Mater Struct. 2016;49:1213–1220. doi:10.1617/s11527-015-0571-0
- Roussel N. Rheological requirements for printable concretes. Cem Concr Res. 2018;112:76–85. doi:10.1016/j.cemconres.2018.04.005
- De Schutter G, Lesage K, Mechtcherine V, et al. Vision of 3D printing with concrete - technical, economic and environmental potentials. Cem Concr Res. 2018;112:25–36. doi:10.1016/j.cemconres.2018.06.001
- Mehta PK, Monteiro PJ. Concrete: microstructure, properties, and materials. New York: McGraw-Hill Education; 2014.
- Reiter L, Wangler T, Roussel N, et al. The role of early age structural build-up in digital fabrication with concrete. Cem Concr Res. 2018;112:86–95. doi:10.1016/j.cemconres.2018.05.011
- Liu Z, Li M, Quah TKN, et al. Comprehensive investigations on the relationship between the 3D concrete printing failure criterion and properties of fresh-state cementitious materials. Addit Manuf. 2023;76:103787, doi:10.1016/j.addma.2023.103787
- Timothy W, Ena L, Lex R, et al. Digital concrete: opportunities and challenges. RILEM tech lett. 2016;1.
- Wolfs R, Bos F, Salet T. Triaxial compression testing on early age concrete for numerical analysis of 3D concrete printing. Cem Concr Compos. 2019;104:103344, doi:10.1016/j.cemconcomp.2019.103344
- Perrot A, Pierre A, Nerella VN, et al. From analytical methods to numerical simulations: a process engineering toolbox for 3D concrete printing. Cem Concr Compos. 2021;122:104164, doi:10.1016/j.cemconcomp.2021.104164
- Li M, Zhang D, Wong TN, et al. Modeling and experimental investigation of fiber orientation in cast and 3D-printed cementitious composites. Mater Sci Addit Manuf. 2023;2:1603, doi:10.36922/msam.1603
- Tay YWD, Ting GHA, Qian Y, et al. Time gap effect on bond strength of 3D-printed concrete. Virtual Phys Prototyp. 2019;14:104–113. doi:10.1080/17452759.2018.1500420
- Nerella VN, Krause M, Mechtcherine V. Direct printing test for buildability of 3D-printable concrete considering economic viability. Autom Constr. 2020;109; doi:10.1016/j.autcon.2019.102986
- Le TT, Austin SA, Lim S, et al. Structures, Mix design and fresh properties for high-performance printing concrete. Mater Struct. 2012;45:1221–1232. doi:10.1617/s11527-012-9828-z
- Nicolas R, Richard B, Nicolas D, et al. Assessing the fresh properties of printable cement-based materials: high potential tests for quality control. Cem Concr Res. 2022;158:106836, doi:10.1016/j.cemconres.2022.106836
- Nguyen-Van V, Li S, Liu J, et al. Modelling of 3D concrete printing process: a perspective on material and structural simulations. Addit Manuf. 2022;61:103333.
- Wolfs R, Suiker A. Structural failure during extrusion-based 3D printing processes. Int J Adv Manuf Technol. 2019;104:565–584. doi:10.1007/s00170-019-03844-6
- Ooms T, Vantyghem G, Van Coile R, et al. A parametric modelling strategy for the numerical simulation of 3D concrete printing with complex geometries. Addit Manuf. 2021;38:101743, doi:10.1016/j.addma.2020.101743
- Lim S, Buswell RA, Valentine PJ, et al. Modelling curved-layered printing paths for fabricating large-scale construction components. Addit Manuf. 2016;12:216–230. doi:10.1016/j.addma.2016.06.004
- Chang Z, Liang M, Xu Y, et al. 3D concrete printing: lattice modeling of structural failure considering damage and deformed geometry. Cem Concr Compos. 2022;133:104719, doi:10.1016/j.cemconcomp.2022.104719
- Wu Y, Liu C, Liu H, et al. Study on the rheology and buildability of 3D printed concrete with recycled coarse aggregates. J Build Eng. 2021;42:103030, doi:10.1016/j.jobe.2021.103030
- Ivanova I, Ivaniuk E, Bisetti S, et al. Comparison between methods for indirect assessment of buildability in fresh 3D printed mortar and concrete. Cem Concr Res. 2022;156:106764, doi:10.1016/j.cemconres.2022.106764
- Chen Y, Rodriguez CR, Li Z, et al. Effect of different grade levels of calcined clays on fresh and hardened properties of ternary-blended cementitious materials for 3D printing. Cem Concr Compos. 2020;103708.
- Tay YWD, Qian Y, Tan MJ. Printability region for 3D concrete printing using slump and slump flow test. Compos Part B: Eng. 2019;174.
- Perrot A. 3D printing of concrete: state of the Art and challenges of the digital construction revolution. London: John Wiley & Sons; 2019.
- Wolfs RJM, Bos FP, Salet TAM. Early age mechanical behaviour of 3D printed concrete: numerical modelling and experimental testing. Cem Concr Res. 2018;106:103–116. doi:10.1016/j.cemconres.2018.02.001
- Boscaro F, Quadranti E, Wangler T, et al. Eco-friendly, set-on-demand digital concrete. 3D Print Addit Manuf. 2022;9:3–11.
- Das A, Reiter L, Mantellato S, et al. Early-age rheology and hydration control of ternary binders for 3D printing applications. Cem Concr Res. 2022;162:107004, doi:10.1016/j.cemconres.2022.107004
- Chen Y, Rahmani H, Schlangen E, et al. An approach to develop set-on-demand 3D printable limestone-calcined clay-based cementitious materials using calcium nitrate. Cem Concr Compos. 2023;105373.
- Esnault V, Labyad A, Chantin M, et al. Experience in Online Modification of Rheology and Strength Acquisition of 3D Printable Mortars. Cham: Springer International Publishing; 2019, pp. 24-38.
- Rehman AU, Perrot A, Kim JH. A critical evaluation of Ten quality control test methods for 3D concrete printing with Mono-component concrete. Dev Built Environ. 2023;16.
- Rehman AU, Jhun JH, Nam J, et al. Use of slug test as an In-line technique for the quality control of 3D concrete printing, Korean society of civil engineers journal. Proc Annu Fall Symp. 2021;33:649–650.
- Melesse BB. Characterization of Fresh Properties of 3D Printable Concrete Mixtures and Buildability Assessment. Seoul, Korea: YONSEI University; 2022.
- A. C403/C403M-16. Standard test method for time of setting of concrete mixtures by penetration resistance, ASTM International: West Conshohocken, PA, USA, (2016).
- [73] D. ASTM. 2166; Standard Test Method for Unconfined Compressive Strength of Cohesive Soil, West Conshoshocken, PA, United States, (2016).
- Kim I, Lee J, Kim J. Design of a compression test machine for measuring fresh properties of 3D printable concrete, Korean Soc, Civ. Eng. Fall Conf. Proc, 2020.
- Koehler EP, Fowler DW, Ferraris CF, et al. A new: portable rheometer for fresh self-consolidating concrete. ACI Spec Publ. 2005;233:97.
- Omran AF, Naji S, Khayat KH. Portable vane test to assess structural buildup at rest of self-consolidating concrete. ACI Mater J. 2011;108.
- Nishijo K, Ohno M, Ishida T. Quantitative evaluation of buildability in 3D concrete printing based on shear vane test, EASE(C16): Proceedings of The 16th East Asian-Pacific Conference on Structural Engineering and Construction, 2019, Springer, 2021, pp. 1891-1901.
- ASTM C597. Standard Test Method for Pulse Velocity Through Concrete. PA, USA: ASTM West Conshohocken; 2016.
- Lootens D, Jousset P, Martinie L, et al. Yield stress during setting of cement pastes from penetration tests. Cem Concr Res. 2009;39:401–408. doi:10.1016/j.cemconres.2009.01.012
- Zhu B, Pan J, Nematollahi B, et al. Development of 3D printable engineered cementitious composites with ultra-high tensile ductility for digital construction. Mater Des. 2019;181:108088, doi:10.1016/j.matdes.2019.108088
- Munemo R, Kruger J, van Zijl GP. Improving interlayer bond in 3D printed concrete through induced thermo-hydrokinetics. Constr Build Mater. 2023;393:132121, doi:10.1016/j.conbuildmat.2023.132121
- Malan JDM, van Rooyen AS, van Zijl GP. Chloride induced corrosion and carbonation in 3D printed concrete. Infrastructures. 2021;7:1, doi:10.3390/infrastructures7010001
- Kim J. Development of Concrete 3D Printing Extruder and Extrusion Performance Evaluation for Various Printing Speed, MS Thesis, Graduate School, Yonsei University (2017).
- Wolfs RJM, Bos FP, Salet TAM. Correlation between destructive compression tests and non-destructive ultrasonic measurements on early age 3D printed concrete. Constr Build Mater. 2018;181:447–454. doi:10.1016/j.conbuildmat.2018.06.060
- Chen Y, He S, Gan Y, et al. A review of printing strategies,: sustainable cementitious materials and characterization methods in the context of extrusion-based 3D concrete printing. J Build Eng. 2022;45:103599, doi:10.1016/j.jobe.2021.103599
- Casagrande L, Esposito L, Menna C, et al. Effect of testing procedures on buildability properties of 3D-printable concrete. Constr Build Mater. 2020;245:118286, doi:10.1016/j.conbuildmat.2020.118286
- Prevedello Rubin A, Hasse JA, Longuini Repette W. The evaluation of rheological parameters of 3D printable concretes and the effect of accelerating admixture. Constr Build Mater. 2021;276:122221, doi:10.1016/j.conbuildmat.2020.122221
- Ivanova I, Mechtcherine V. Possibilities and challenges of constant shear rate test for evaluation of structural build-up rate of cementitious materials. Cem Concr Res. 2020;130; doi:10.1016/j.cemconres.2020.105974
- Rubin AP, Hasse JA, Repette WL. The evaluation of rheological parameters of 3D printable concretes and the effect of accelerating admixture. Constr Build Mater. 2021;276:122221, doi:10.1016/j.conbuildmat.2020.122221
- Rehman AU, Lee S-M, Kim J-H. Use of municipal solid waste incineration ash in 3D printable concrete. Process Saf Environ Prot. 2020;142:219–228. doi:10.1016/j.psep.2020.06.018
- Roussel N. A thixotropy model for fresh fluid concretes: theory: validation and applications. Cem Concr Res. 2006;36:1797–1806. doi:10.1016/j.cemconres.2006.05.025
- Lu Z, Peng X, Dorn T, et al. Early performances of cement paste in the presence of triethanolamine: rheology, setting and microstructural development. J Appl Polym Sci. 2021;138:50753, doi:10.1002/app.50753
- Rehman AU, Kim I-G, Kim J-H. Towards full automation in 3D concrete printing construction: development of an automated and inline sensor-printer integrated instrument for in-situ assessment of structural build-up and quality of concrete. Dev Built Environ. 2024;17:100344, doi:10.1016/j.dibe.2024.100344
- Suiker AS, Wolfs RJ, Lucas SM, et al. Elastic buckling and plastic collapse during 3D concrete printing. Cem Concr Res. 2020;135:106016, doi:10.1016/j.cemconres.2020.106016
- Tripathi A, Nair SAO, Neithalath N. A comprehensive analysis of buildability of 3D-printed concrete and the use of bi-linear stress-strain criterion-based failure curves towards their prediction. Cem Concr Compos. 2022;128:104424, doi:10.1016/j.cemconcomp.2022.104424