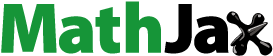
ABSTRACT
The current study presents a facile approach to synthesis carbon nanotube-anchor α-ZrP (CNT@α-ZrP) nanohybrid for multifunctional polyamide 12 (PA12) composites via ball-milling followed by selective laser sintering (SLS) process. Herein, CNTs serve dual roles; firstly, they act as a pigment, imparting black colouration to both PA12 powder and α-ZrP sheets, facilitating rapid light absorption and heating. Secondly, CNTs complement α-ZrP sheets to reinforce the PA12 matrix for strong and functional structures. The dominant filler content is α-ZrP nanosheets in PA12 powder to study the functionality of α-ZrP sheets in SLS-PA12 composites. CNT@α-ZrP hybrid enhances mechanical, tribological, corrosion resistance and flame-retarding properties of PA12 composite parts. PA12/CNT@α-ZrP composite exhibited 98.9%, 33.1%, and 34.6% increments in Young's modulus, tensile strength and impact strength, respectively. To predict the response of the composites across a range of applications, the constants for different hyperelastic models describing their mechanical behaviour were determined. The coefficient of friction and wear rate of the sintered composite parts were reduced significantly. Additionally, 1 wt% CNT@α-ZrP reduced smoke production rate and total smoke production by 36.5% and 13.8%, respectively along with a 2.2- fold increment in time-to-ignition. The work presents an industrial method to develop strong and functional intricate structures via SLS.
1. Introduction
Polymer nanocomposites exhibit enhancements in overall performance at low loadings [Citation1,Citation2]. This includes not only mechanical strength but also functional properties such as flame retarding [Citation3], thermal and electrical conductivity [Citation4]. The common processing methods for polymeric composites are melt compounding and solution mixing. However, many applications recently require parts with complex geometries, which are difficult during mould design and filling stages. Currently, additive manufacturing (AM) offers an alternative approach to manufacturing functional parts with intricate profiles and details that are either difficult or impossible to produce by traditional methods [Citation5–7]. AM uses the layer-by-layer approach to build a part directly from polymer, metal or ceramic materials; AM significantly reduces the waste material and offers fully customised products [Citation8–11]. Multiple AM techniques exist, including fused deposition modelling, stereolithography and selective laser sintering (SLS). SLS, for instance, employs a laser energy source to fuse polymer powders, enabling the creation of sizable components with robust mechanical properties at a reasonable expense. The no-support-structure and wide range of polymeric powders give SLS more design and manufacturing freedom compared to other AM techniques [Citation12]. Since polyamide 12 features high strength and toughness, high thermal stability, and excellent weather resistance, it is widely used as a mechanically functional polymer in structures. PA12 is commonly studied with SLS due to its powder-ability to various sizes and hence mixing with nanofillers [Citation13].
Recently, the aerospace industry received a significant share of SLS-produced parts (16.6%); however, this industry has stringent requirements for material properties [Citation14]. Considering these needs, considerable research is done to generate high-performance polyamide or its composites by SLS [Citation15,Citation16]. Multiphase polymer composites show growing interest due to synergistic filler additions, yielding superior mechanical and functional properties in the host matrix [Citation17–19]. Table S1 in the Supporting Information summarises the recent studies on nylon nanocomposites via 3D printing. When graphene platelets (GnPs) were mixed with PA powder at 6 wt%, the elastic modulus of 3D printed parts increased by 7% [Citation20]. Additionally, the thermal conductivity of the parts increased significantly by 51.4% [Citation20]. The aspect ratio of the nanofiller has an impact on the resulting properties of 3D printed parts. For example, when carbon nanotubes (CNTs) were added into PA12 for fused filament fabrication, the obtained parts possessed increments in Young’s modulus and ultimate tensile strength by 29% and 43%, respectively, at 5 wt% CNTs. More importantly, the printed parts gained functional properties including electrical conductivity, anti-bacterial behaviour and Electrothermal Joule-heating effect [Citation21]. In another study, AgNO3 nanoparticles with polyvinyl alcohol (PVA) were added to PA powder for material extrusion 3D printing [Citation22]. The mechanical properties of the printed parts have significantly increased; ultimate tensile strength and flexural strength increased respectively by 50% and 23.7% [Citation22]. Lupone et al. [Citation23] mixed carbon fibres (CF) and graphite with PA12 powder under a pressure of 150 bar before using the SLS process to produce PA12/CF composites. The percolation threshold of electrical conductivity of SLS-produced PA12 composites was recorded at ∼7.5 wt% of the hybrid filler in comparison with ∼12.5 wt% when only graphite is used [Citation23]. The thermal conductivity of SLS-prepared PA12 composites can be enhanced by 275% by adding 35 wt% Al2O3 nanoparticles and 15 wt% boron nitride sheets without sacrificing its tensile strength [Citation24].
Carbon nanomaterials [Citation25,Citation26], particularly CNTs, are proposed as additives to laser-sintered polymers to enhance mechanical, electrical and thermal properties [Citation14,Citation27–30]. α-ZrP nanosheets are attracting attention due to their exceptional thermal and chemical stability, ion-exchange properties, catalytic activity, and ability to intercalate with macromolecules [Citation31,Citation32]. Previous studies have identified Lewis-acid sites on the lamella of α-ZrP, which can be useful in producing flame-retardant polymers [Citation33]. α-ZrP nanosheets, with their layered structure similar to graphite, can effectively reduce friction and wear in polyamide composites with integrated components.
Although there is a potential for synergy between CNTs and α-ZrP sheets to develop mechanically durable and functional polyamide composites using the SLS process, there are no reports or studies on this topic. The current study presents a facile approach to preparing multiphase 3D-printed PA12 composites. The raw CNT@α-ZrP coated PA12 powders were prepared by a ball-milling process. The PA12/CNT@α-ZrP composite parts were sintered via the SLS process. The effect of CNT@α-ZrP on mechanical, tribological and flame-retarding properties of the laser-sintered PA12 composites was investigated systematically. Furthermore, friction and flame-retarding mechanisms of CNT@α-ZrP nanohybrid in the sintered PA12/CNT@α-ZrP composite parts were discussed. Durable and complex geometries from PA12/CNT@α-ZrP composites are SLS-manufactured. Additionally, a numerical analysis was conducted to determine the material’s constants of various hyperelastic constants; this includes Mooney-Rivlin, Ogden and Yeoh. Given the intricacies and significant costs tied to the production of these composites using selective laser sintering, theoretical models emerge as invaluable tools for engineers. These models offer a precise avenue to anticipate material behaviours across diverse applications. Moreover, they streamline the process of design optimisation, guaranteeing adherence to performance standards while minimising factors such as weight and expenses before the manufacturing phase begins.
The study demonstrates the potential of producing customised and functional parts with high mechanical strength, good friction, anti-corrosion performance and flame-retardant performance using functional α-ZrP sheets mixed with CNTs. CNT@α-ZrP offers several advantages over traditional flame retardants, including a high aspect ratio of CNTs, which allows for effective barrier formation; α-ZrP sheets have the ability to promote char formation via its surface functional groups which enhances the material's flame retarding properties. Additionally, CNT@α-ZrP is environmentally friendly and does not pose the same health and environmental risks as halogenated flame retardants. CNT@α-ZrP in PA12 composites have potential applications where high mechanical strength, wear resistance, corrosion resistance, and flame retardancy are required such as automotive and aerospace components, electronics, and military industry.
2. Experimental details
2.1. Materials
The commercial PA12 powder (FS3300PA) with a density of 0.95 g/cm³ was supplied by Farsoon Technologies Co., Ltd. Multi-walled carbon nanotubes (CNTs, 8–15 nm diameter, ∼50 μm length, and 98% purity) were provided by the Chengdu Organic Chemicals Pty Ltd., Chinese Academy of Sciences, and its intrinsic electrical conductivity >100 S/cm. α-Zirconium phosphate (α-ZrP) was provided by Sunshine Factory Co., Ltd. (Mianzhu, Sichuan). All chemicals were used as received without further purification.
2.2. Preparation
shows an illustration of the preparation processes for composite powder and selective laser process. Details are as follows.
CNT-anchored α-ZrP: A high-energy planetary ball milling (F-4000, Focucy, China) was used to prepare CNT-anchored α-ZrP (CNT@α-ZrP) nanohybrid. α-ZrP nanosheets were processed by a ball mill with the assistance of 75 wt% glucose solution; details are elsewhere [Citation32,Citation34]. The 75 wt% glucose solution (150 mL), CNT (0.5 g), α-ZrP (1.5 g), and two different size ZrO2 balls with diameters of 8 mm (90 g) and 5 mm (60 g) were loaded into a 500 mL zirconia grinding bowl. The ball mill consisted of four grinding bowls vertically positioned on a rotating supporting disc. The atmosphere condition is under N₂ atmosphere. The mixing process lasted for 12 h at the speed of 300 rpm under a cooling system. After the corresponding treatment, the resulting mixture was collected by high-speed centrifugation at 6000 rpm for 30 min and further freeze-drying for the next step of preparation.
PA12/CNT@α-ZrP composite powder: A high-energy planetary ball milling (F-4000, Focucy, China) was used to prepare PA12/CNT@α-ZrP composite powder. A master batch of PA12-CNT@α-ZrP mixture (1 wt% CNT@α-ZrP) was prepared with the use of ZrO2 grinding balls of 6 and 4 mm in diameter. A rotation speed of 300 rpm was used and the grinding process was programmed to run for 10 h. After grinding, the resulting PA12/CNT@α-ZrP compound powder was collected for the SLS process.
Selective laser sintering process: The PA12/CNT@α-ZrP composite components were manufactured using an industrial-scale SLS apparatus (HT403P, Farsoon Technologies Co., Ltd). The machine model is equipped with CO₂-laser type with wavelength λ = 10.6 µm and power capacity of 55 W. A layer of PA12/CNT@α-ZrP powder is fed into the fabrication chamber over the X-Y plane, a selective laser beam heats, fuses and sinters the powder particles forming a thin and delegate layer of PA12/CNT@α-ZrP composites. The former step is repeated by feeding another layer of the powder and the laser beam builds a second layer. The process is repeated till a 3D object is constructed. The path of sintering of each layer is 90° against the previous or the consecutive layer. Thus, the product exhibits anisotropic properties on the X-Y and X-Z planes. The samples were profiled and shaped according to the measurement method. The printing parameters are shown in . Detailed information on characterisations and measurements is provided in the S2 section of the Supporting Information (SI).
Table 1. SLS processing parameters for PA12 and PA12/CNT@α-ZrP.
3. Results and discussion
3.1 Morphology of CNT@α-ZrP hybrid
The crystal structure of the CNTs, α-ZrP and CNT@α-ZrP nanohybrid is analysed using X-ray powder diffraction (XRD) in (a). The prominent diffraction peak observed at 26.0° is assigned to the (002) plane of carbon nanotubes (JCPDS Card No. 65-6212). Moreover, the X-ray diffraction (XRD) pattern of α-ZrP exhibits distinct peaks at 11.6°, 19.7°, and 24.9° (JCPDS: 33-1482), which can be attributed to the (002), (110), and (112) planes, respectively. The CNT@α-ZrP nanohybrid shows a new peak at 2θ of 26°, which corresponds to CNT diffraction peaks. The characteristic peaks at 10.7°, 19.7°, and 24.9° correspond to α-ZrP crystal planes (002), (110), and (112), indicating the coexistence of CNTs and α-ZrP. The (002) diffraction peak of CNT@α-ZrP nanohybrid shifts to a small angle, showing decreased nanosheet stacking and the involvement of CNTs in widening the interlayer space.
Thermogravimetric analysis (TGA) determines the thermal stability of CNT@α-ZrP nanohybrid. (b) displays the thermal breakdown curves of CNTs, α-ZrP, and CNT@α-ZrP nanohybrids in N2 atmosphere. The reduction in mass observed in α-ZrP sheets around 143°C primarily resulted from the evaporation of crystallisation water present between the nanoplatelets of α-ZrP. Conversely, the mass loss occurring at approximately 585°C was ascribed to the dehydration condensation process of P-OH groups. At 800°C, the α-ZrP residue was approximately 88 wt% inside the nanosheets [Citation2]. Regardless of nanotubes, the pristine form is illustrated in (b). It is stable until 620°C and decomposes at 664.4 ± 0.1°C. By introducing CNTs on the surface of α-ZrP sheets, it enhances the thermal stability of the sheets which is beneficial to delay the pyrolysis process of PA12. This would be explained in the subsequent section on flame retarding properties.
(c) illustrates the exfoliation of pristine α-ZrP into thin nanosheets through ball milling, leading to the formation of a translucent sheet-like morphology [Citation32]. (d) depicts CNTs dropped from an aqueous solution, displaying their individual presence and verifying their well-dispersed and disentangled properties. (e) shows the hybrid micro-morphology of CNT@α-ZrP. The CNTs firmly anchor onto the surface of α-ZrP nanosheets, confirming the effective fabrication of the CNT@α-ZrP nanohybrid.
3.2 Morphology of PA12 powder composites
illustrates the morphologies of PA12 and PA12/CNT@α-ZrP raw powders. PA12/CNT@α-ZrP powders are composed of two phases: (i) the polymeric phase, PA12, and (ii) the CNT@α-ZrP hybrid attached to the PA12 powder’s surface. This configuration is crucial for fully utilising CNT@α-ZrP to improve the laser absorption of powders in sintered composite parts. The addition of CNTs typically increases light energy absorption and thus facilitates the efficiency of the powder sintering process; this is in addition to the reinforcing factor of CNTs. PA12 powder composites within filler range 0–1 wt% exhibit irregular morphology with spherical-like structure as depicted in (a1 – e1). When an area on the random particle is magnified, the particle surface exhibits a cauliflower-like morphology as presented in (a2–e2) and (a3–e3). The irregular structure and cauliflower-like morphology facilitate the interlocking and fusion during the SLS process [Citation8,Citation35]. Theoretically, as the quantity of CNT@α-ZrP increases, the prevalence of these nanohybrids on the surface of PA12 particles should also increase. The excess of surface saturation from CNT@α-ZrP nanohybrid can have a negative impact on the mechanical properties of sintered objects as it hinders the adhesion and fusion between PA12 particles during the sintering process. Uniform dispersion of CNT@α-ZrP nanohybrid across the PA12 powder will result in significant networking within the PA12 matrix. CNT@α-ZrP 3D interconnected networks can improve mechanical and flame-retarding capabilities with minor additions of 0.1–1 wt%. In order to achieve high mechanical and functional properties, the powder preparation stage is imperative to avoid nanomaterial clustering and create a strong interface between nanofillers and polymer.
Figure 3. SEM images and particle size distribution of PA12/CNT@α-ZrP composite powder: (a) 0 wt%, (b) 0.1 wt%, (c) 0.2 wt%, (d) 0.5 wt% and (e) 1.0 wt%.
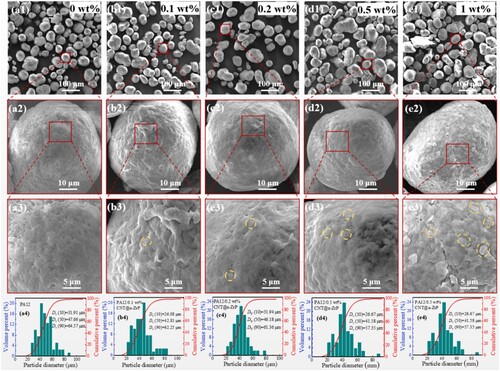
The ball milling process has an impact on the particle size distribution during the high shear mixing process between the ZrO2 balls, PA12 powder and CNT@α-ZrP nanohybrid. The obtained SEM images in (a1–e1) were further studied by ImageJ Software to analyse the particle size distribution after ball milling as presented in (a4–e4). It is evident that neat PA12 powder and PA12/CNT@α-ZrP composites after ball milling have particle size distribution ranges within 30–80 µm which is suitable for the SLS process [Citation8,Citation36]. The volume-based D-value of the processed powder gives a quantitative description of the particle size distribution. The volumetric median size, Dv (50), of neat PA 12 is 47.66 µm. After ball milling, the PA12 powder composites exhibitexhibit median size of Dv (50) within the range ∼ 41–46 µm. This highlights that ball milling has a marginal effect on changing the particle size distribution.
Since the addition of CNT@α-ZrP nanohybrid is at a very low mass content, 0.1–1 wt%, it is expected that the powder bed density of PA12 will not change upon adding the nanohybrid. Table S2 in the Supporting Information (SI) presents the angle of repose (AOR) and bulk density of neat PA12 and its CNT@α-ZrP composite powder. It is evident that both AOR and density are within the range of 41.23° and 0.484 g/cm3 with marginal alteration at various contents of CNT@α-ZrP. The bulk density of PA12 changed from 0.472 ± 0.001 g/cm3 for neat PA12 to 0.497 ± 0.003 g/cm3 at 1 wt% of CNT@α-ZrP which is a marginal change. Keeping particle size distribution and the powder bed density within the recommended commercial ranges are in favour of good flowability during the SLS process [Citation8,Citation36]. This confirms that adding CNT@α-ZrP did not negatively affect the flowability of the powder during the SLS process.
Further investigation on the morphology of PA12/CNT@α-ZrP powder was conducted by energy dispersive x-ray spectroscopy (EDS) analysis as shown in . It is evident that ZrP sheets exist on the PA12 powder. (c&e) shows gluing and bright colours in the same places for both Zr and P elements throughout the image. This is confirmed by having the same peak intensity for Zr and P elements in (f). In addition, since the C element exists in both CNTs and PA12, we cannot confirm CNTs via EDS. Overall, EDS analysis supports the coverage of CNT@α-ZrP to PA12 powder.
The level of adhesion of PA12 powder during the sintering process correlates directly with the laser power and scanning speed, both of which determine the amount of heat and duration of exposure of the powder mixture, respectively. For this investigation, the laser power and scanning speed parameters are kept constant across all 3D printing runs to identify the optimal PA12/CNT@α-ZrP weight ratio that enhances mechanical properties in the sintered objects. Surface crowding of CNT@α-ZrP on PA12 powders affects powder consolidation sintering and PA12 powder cohesiveness by SLS. It is also worth noting that the sintering process is heavily dependent on powder contact.
3.3. Melting and crystallising behaviour
illustrates the DSC curves during the second heating and cooling cycles for both PA12 and its composite powder. Additionally, presents the non-isothermal DSC data, namely: initial, peaking, and end melting temperatures (Tim, Tpm and Tem respectively); the initial, peaking, and end crystallisation temperatures (Tic, Tpc and Tec respectively); and the melting enthalpy (ΔHm).
Table 2. DSC data of PA12 and its composites.
The melting DSC curve data can be used to calculate the crystalline fraction (Xc) of any given material as [Citation37]:
1)where ƒ represents the fraction of nanoadditives. The bed temperature (Tb) of a semi-crystalline polymer during the SLS process is typically determined by Tim, as presented in . The melting enthalpy (ΔHƒ⁰) for a theoretically 100% crystalline polyamide 12 is 209.2 J/g [Citation38]. As the CNT@α-ZrP content increases, the Tb of PA12/CNT@α-ZrP powders increases by 2°C at 1.0 wt%. PA12/CNT@α-ZrP composites exhibit higher Tic, Tpc and Tec compared with neat PA12, demonstrating a nucleation effect of the nanohybrid. PA12/CNT@α-ZrP composites have lower Xc than neat PA12 powder. Shi et al. [Citation39] showed experimentally that reduced crystallinity can reduce the shrinkage ratio which in favour to 3D printing process by having higher dimensional accuracy of SLS parts. In this regard, the dimension accuracy of the 3D-printed parted was investigated and presented in PA12/CNT@α-ZrP composite powder provides higher accuracy for SLS compared to neat PA12. For complex SLS components with thin walls and microscopic holes, determining calibration factors like shrinkage can be challenging due to varying values at different locations. In such cases, materials with high-dimension stability are recommended to ensure dimension precision, as they offer improved dimensional stability and minimise the impact of shrinkage variations.
In the SLS process, the heating system pre-heats the powder bed to a temperature known as the Tb. For a semi-crystalline polymer like PA12, it is advantageous to maintain the Tb close to the melting temperature (Tim). This promotes slower crystallisation, allowing thermal tension to be released and reducing part warpage. However, Tb cannot go beyond the polymer's Tim; otherwise, polymer particles may cling together and be difficult to distribute due to poor flowability. (a) shows that the Tim of neat PA12, 0.1, 0.2, 0.5, and 1.0 wt% PA12/CNT@α-ZrP composites are 186.85°C, 187.41°C, 187.69°C, 187.92°C, and 188.32°C, respectively. Consequently, it is recommended to set the powder bed temperature (Tb) for these powders in proximity to their initial melting temperatures. This approach ensures optimal processing conditions and promotes desirable material behaviour during the manufacturing process.
A trial-and-error experiment was employed to determine the value of Tb; initially, the pre-heating temperature was set significantly below Tim, causing warping and curling due to inadequate heat. Subsequently, the pre-heating temperature was systematically increased until reaching a threshold where minimal warpage occurred, and the powder exhibited optimal flowability. This temperature represents the Tb of the substance. For 0 wt%, 0.1, 0.2, 0.5, and 1.0 wt% PA12/CNT@α-ZrP, Tb values were 181°C, 182°C, 183°C, 183°C, and 183°C, respectively. Adding CNT@α-ZrP modifies the material's characteristics and impacts the sintering behaviour of PA12. The reduction in Tb is anticipated to decrease energy consumption during pre-heating and laser sintering processes, while also mitigating heat-induced degradation of PA12, thereby prolonging the lifespan of unsintered powders. Roughly 80-90% of the powder within the SLS construction chamber remains unsintered and could be recycled. According to Pham et al. [Citation40], Tb is one of the critical properties in the loss of SLS powder characteristics; lower Tb in PA12/CNT@α-ZrP composite powder can prevent unsintered powder from deteriorating during SLS, improving recyclability of the powder and reducing material costs along with economic and environmental benefits.
3.4. Mechanical performance and fracture analysis
The effect of CNT@α-ZrP nanohybrid content on the tensile and impact properties of the PA12/CNT@α-ZrP SLS parts is shown in . The detailed mechanical performance data of PA12 and its composites are recorded in . From and , the CNT@α-ZrP nanohybrid greatly improves the mechanical performance of sintered PA12 composite components. When adding 0.2 wt% CNT@α-ZrP nanohybrid, the Young's modulus, tensile strength, and impact strength increased by 98.9%, 33.1% and 34.6%, respectively. The CNT@α-ZrP nanohybrid effectively strengthens the PA12 matrix by homogeneous dispersion and strong contact, resulting in considerable improvements in mechanical properties. Incorporating CNT@α-ZrP into PA12 composites leverages the exceptional mechanical properties of carbon nanotubes and the reinforcing capability of α-ZrP sheets, leading to a composite material with high mechanical performance. This is attributed to three main factors: (i) adding CNT@α-ZrP nanohybrid could improve the interfacial bonding between the SLS-fused powders; (ii) given the contrast in geometry between CNTs, α-ZrP sheets and spherical powder, they can interlock the PA12 powder and fill the voids around the powder vicinity forming compact printed parts; and (iii) consequently, the mechanical load can be effectively shared and transferred between CNT@α-ZrP nanohybrid and the PA12 matrix. These factors collectively contribute to achieving PA12 composite with high strength, stiffness and impact resistance.
Table 3. Mechanical properties data of PA12 and its composites.
Mechanical properties begin to deteriorate beyond 0.2 wt% CNT@α-ZrP. The mechanical properties of sintered parts from 3D printing are affected by the quantity and overall surface area of connections among particles. It is suggested that the interference of CNT@α-ZrP nanohybrid during the sintering process would be weak since the fillers can work as a barrier for a relatively strong connection.
presents the tensile-fractured surface of the PA12 and its composites with different contents of CNT@α-ZrP nanohybrid. Polyamide 12, as a thermoplastic polymer, exhibits typical ductile fracture behaviour in (a). The PA12 undergoes plastic deformation initially, allowing for energy absorption and deformation without immediate fracture. This plastic deformation is facilitated by the sliding of the polyamide chain on account of the amorphous nature of PA12. As deformation continues, the PA12 experiences necking, characterised by localised cross-sectional area reduction due to stress redistribution. The necking region elongates until reaching a critical point, ultimately leading to material fracture.
Figure 7. SEM images of tensile fractured surface of PA12/CNT@α-ZrP composites: (a) 0 wt%, (b) 0.1 wt%, (c) 0.2 wt%, (d) 0.5 wt% and (e) 1.0 wt%.
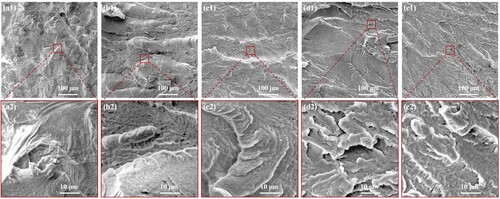
At low content (≤0.2 wt%), the nanohybrid can be dispersed relatively uniformly within the matrix, effectively transferring and sharing stress between PA12 and filler. (b) and7(c) shows a low magnification image indicating the successful production of a nearly fully dense part through laser sintering. Although some pores resulting from CNT@α-ZrP nanohybrid pull-out are visible on the fractured surface, a strong interfacial bonding has been established between CNT@α-ZrP and the PA12 matrix. However, at high filling content, the interfacial bond between the nanohybrid and the matrix weakens, leading to stress concentration within the matrix and a reduction in strength. The images in (d) and 7(e) indicate that the poor mechanical properties of PA12 composite parts are due to the addition of CNT@α-ZrP to the PA12 matrix, and the weak interfacial bonding of the nanohybrid-PA12 interface. Inadequate interfacial interaction between CNT@α-ZrP nanohybrid and PA12 matrix results in ‘fragile' debonding around filler particles. This phenomenon, along with stress concentration at CNT@α-ZrP sites, causes non-uniform stress distribution, filler-matrix debonding, and the formation of crack initiation sites, potentially leading to composite failure. Thus, the limited affinity between CNT@α-ZrP and the PA12 matrix restricts stress transfer at the interface, explaining the increased brittleness of PA12/CNT@α-ZrP composites.
3.5. Corrosion and wear resistance
The polarisation curves of neat PA12 and its composites, when soaked in 3.5 wt% NaCl and 5 wt% H2SO4 solutions, are depicted in (a) and 8(b) respectively. Electrochemical parameters such as corrosion potential (Ecorr), corrosion current density (Icorr), polarisation resistance (Rp) and corrosion rate (CR) were determined by electrochemical software based on Tafel extrapolation. PA12 composite with 1 wt% CNT@α-ZrP exhibited Ecorr values of 0.28 and 0.19 V in 3.5 wt% NaCl and 5 wt% H2SO4 solutions, respectively, which are significantly higher than neat PA12 specimens. With the most positive Ecorr and lowest Icorr, PA12 performs enhanced corrosion resistance and reduced corrosion rate with the addition of CNT@α-ZrP nanohybrid indicating that CNT@α-ZrP is an effective filler to improve the corrosion resistance of PA12 composites. This improvement is attributed to the enhancement of PA12 impermeability. CNT@α-ZrP nanohybrid can form a labyrinth within the PA12 matrix. This prolongs the fluid path through the matrix. Additionally, the nanohybrid can form a physical barrier to effectively inhibit or lessen the penetration of corrosive agents, thereby reducing the rate of corrosion and extending the material's lifespan in corrosive environments. Collectively, the aforementioned factors augment the resistance of PA12/CNT@α-ZrP composite to corrosion in both acidic and alkaline solvents.
depicts the friction performance of neat PA12 and its composites made by selective laser sintering. Adding CNT@α-ZrP to the PA12 matrix dramatically reduced the friction coefficient during testing. The coefficient of friction for neat PA12 initially climbed to 0.35 in the first 10 min, then gradually stabilised at 0.38. Adding 1 wt% of CNT@α-ZrP into PA12 reduced the coefficient of friction from 0.38–0.2, recording a 47% decrement at the steady state. The curve for the 1 wt% PA12/CNT@α-ZrP system shows less variance indicating a smoother sliding process compared to neat and low-fraction PA12 composite. (b) shows the effect of CNT@α-ZrP nanohybrid on the volume wear rate of PA12 composites; incorporating CNT@α-ZrP into PA12 composites significantly reduced volume wear rates. The volume wear rate of 3D-printed PA12 was reduced by 64.7% upon adding 1 wt% CNT@α-ZrP.
Figure 9. (a) Friction coefficient, (b) volume wear rate and (c) friction mechanism of PA12 and its composites.
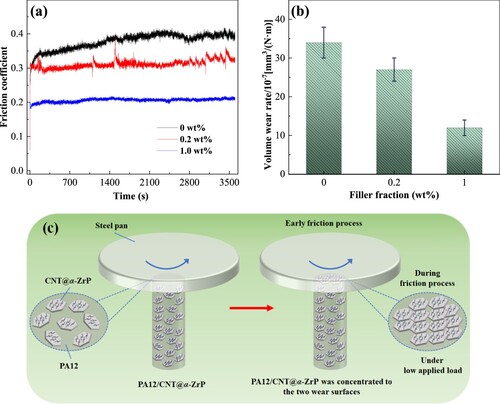
These findings can be explained as follows. (i) When neat PA12 is the under wear test, the material goes under direct surface-to-surface contact without any lubricant; this highlights the stick-slip wear mechanism recording a high coefficient of friction. This explains the high fluctuation for the neat PA12 curve in (a). With time, heat is generated; thus, PA12 loses its mass in the form of melted (soft-sticky) layers attached to the metallic surface. Therefore, the wear rate of neat PA12 is high. (ii) In the case of CNT@α-ZrP nanohybrid into PA12 matrix, at the first stage, the effect of polymer-to-metal contact is dominant until PA12 is worn out and thus CNT@α-ZrP filler has direct contact to the metallic surface. CNT@α-ZrP has high thermal stability and forms a protective layer to stop wearing more PA12 which explains the dramatic reduction in wear rate. In addition, α-ZrP filler has a a plate-like structure that can effectively work as a lubricant similar to graphene and boron nitride [Citation41]. The effect of α-ZrP as lubricant is significant when enough amount of the CNT@α-ZrP nanohybrid is added, namely 1 wt%. It is noteworthy to mention that CNTs aid the lubricant effect of α-ZrP sheets. In summary, CNT@α-ZrP nanohybrid works as a solid lubricant filler and protective layer and thus improves tribological characteristics of laser-sintered PA12.
(c) presents a friction mechanism proposed for CNT@α-ZrP in the PA12 matrix, supported by SEM images of the wear surface in Figure S1. The formation of a transfer layer comprising CNT@α-ZrP in the initial stages of friction prevents further damage to the wear surfaces. With increasing loadings of CNT@α-ZrP in PA12, the friction coefficient and wear rate decrease. The uniform dispersion of CNT@α-ZrP promotes the formation of a thin protective film between the contact composite surface and the wear track, improving the tribological properties.
3.6. Thermal properties of PA12 composites
The thermal stability of PA12 and its composites were evaluated by TGA test, with the corresponding curves depicted in . presents the relevant thermal data, including Tonset and Tmax, representing the temperatures at which 5 wt% weight loss, and the maximum mass loss rate, respectively.
Table 4. Thermal degradation data of PA12 and its composites.
illustrates that, in both nitrogen and air atmospheres, the thermal decomposing of PA12 composites typically displays a one-stage breakdown similar to neat PA12. Also, it is noted that adding CNT@α-ZrP into PA12 does not greatly affect the residual char yield; for example at 1 wt%, PA12 composite exhibits only 1.82 wt% in comparison with 0.81 wt% in the case of neat PA12. This is because of the highly cross-linked poly(HCCP-co-bPEI) on the surface of α-ZrP; this would burn out/ decompose at a temperature close to the pyrolysis temperature of neat PA12. CNTs are added at low content; therefore, their effect is not dominant. This concludes that the thermal stability of PA12 would not be affected by the addition of CNT@ α-ZrP nanohybrid.
3.7. Flame retardancy and smoke suppression
A cone calorimetry is a valuable test for determining material flammability since it can simulate polymers in real-world combustion settings. This work used a cone calorimetry test to investigate how CNT@α-ZrP affected the flammability of PA12. illustrates graphs of output parameters from the cone calorimetry test versus time; further parameters are summarised in . As neat PA12 is highly flammable and thus ignited at 43 s (time to ignition, TTI); neat PA12 exhibits a high peak heat release rate (PHRR) of 974 kW/m² and THR of 141 MJ/m². shows that adding CNT@α-ZrP to PA12 results in lower PHRR and THR values compared to neat PA12 which are in accord with TGA results.
Figure 11. (a) heat release rate, (b) total heat release, (c) smoke production rate, and (d) total smoke production of PA12 and its composites.
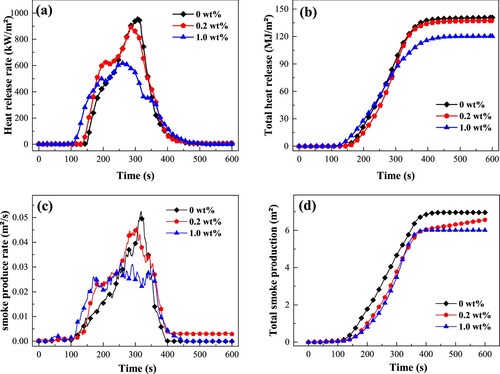
Table 5. Cone calorimeter data of PA12 and its composites.
In comparison to neat PA12, the 1 wt% CNT@α-ZrP composite exhibits a decrease in both PHRR and THR values to 622 kW/m² and 120 MJ/m², respectively. This reduction is primarily attributed to the acid catalytic effect of α-ZrP, which expedites polymer degradation in the initial stages, forming a thermally insulating char that impedes heat and mass transfer. At the same time, the TTI for PA12 composites is extended from 43 s to 94 s compared to neat PA12 indicating high thermal stability. This enhancement is attributed to the release of crystal water from α-ZrP, alongside the barrier effect exerted by both CNTs and α-ZrP, which delay ignition.
Smoke generated during a real fire poses a greater risk of suffocation, which is more hazardous than heat release alone. Adding 1 wt% CNT@α-ZrP to the PA12 matrix reduced peak smoke production rate (PSPR) and total smoke production (TSP) values by 36.5% and 13.8%, respectively, as shown in (c) and 11(d). Furthermore, 1 wt% CNT@α-ZrP reduced the Av-EHC of PA12 composites from 27.18 MJ/kg to 21.10 MJ/kg. The drop in Av-EHC demonstrates that the test produced low combustion heat due to the use of less flammable volatiles which confirms CNT@α-ZrP works in the gas phase as well. The char residue of PA12 composites from 1 wt% CNT@α-ZrP-PA12 composite increased to 7.8 wt% in comparison with 3.9 wt% for neat PA12. The addition of CNT@α-ZrP in the PA12 matrix efficiently suppresses heat and smoke release by creating adequate residual char.
TG-FTIR analysis is employed to examine the gaseous pyrolysis products generated during the degradation of PA12 composites within the N2 atmosphere. shows a semiquantitative examination of gaseous pyrolysis products while adjusting for test sample quality. Apparently, the principal pyrolysis products of plain PA12 are highly flammable and pose a fire risk. In (a), the G-S curves show that CNT@α-ZrP can reduce volatile gas emissions. (b) depicts the decomposed products at the highest mass loss rate of three samples, which have identical distinctive peaks. The examination revealed many representative peaks at 2180 and 2930 cm−1, which correspond to carbon dioxide (CO) and hydrocarbons, respectively.
Figure 12. TG-FTIR data of PA12 and its composites: (a) Gram-Schmidt, (b) at maximum mass loss rate, (c) CO, and (d) hydrocarbons.
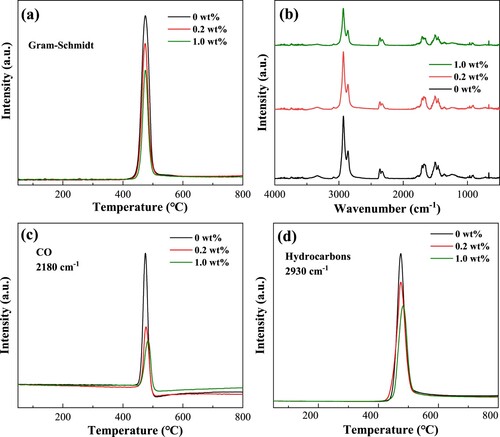
The signal intensity of gases from 1 wt% CNT@α-ZrP is substantially lower than that of neat PA12. The inclusion of CNT@α-ZrP efficiently suppresses the release of gaseous degradation products. This can be due to the continuous and compact char barrier network that can prevent the mass transfer of degraded volatiles. The combustion performance of PA12 and its composites was further examined using Limiting Oxygen Index (LOI) and vertical burning (UL-94) tests, with the results shown in . The LOI value of neat PA12 was only 21%, showing that it is highly flammable in the atmosphere and hence failed the UL-94 vertical tests. The PA12/CNT@α-ZrP composite has a LOI of 22.6%, a 7.62% increase compared to neat PA12. During LOI and UL-94 testing under a small flame, polymer extinction behaviour may be influenced primarily by relevant parameters such as melt viscosity, dripping property, and incombustible gas emissions. In contrast, the barrier effect of rough inorganic fillers and the production of char layers were less successful in improving the extinguishment effect. As a result, even after adding flame-retardant additives or fillers, changes in LOI values and UL-94 ratings may be negligible. This is because these factors are not the principal causes of flame extinguishment in small-scale flame testing.
Table 6. The LOI and UL-94 data of PA12 and its composites.
3.8. Analysis of char residues
Inorganic additives incorporated into polymers primarily serve as a ‘physical barrier’ in the condensed phase, and their efficacy in flame retardation depends greatly on the morphological structure and composition of the residual char. Therefore, examining the char residues of PA12 and its composites post-combustion provides valuable insights into the flame-retarding mechanism.
presents digital images, SEM micrographs, and Raman spectra of the char residues obtained from PA12 and its composites following cone calorimeter testing. Neat PA12, as depicted in (a1), undergoes almost complete combustion, leaving behind a small amount of fragile and flaky char residue. SEM magnification in (a2) reveals a sponge-like structure with numerous small spaces that fail to act as an effective protective shield for the underlying polymer.
Figure 13. Digital photos, SEM images and Raman spectra of char residual of PA12 and its composites: (a) 0 wt%, (b) 0.2 wt%, and (c) 1.0 wt%.
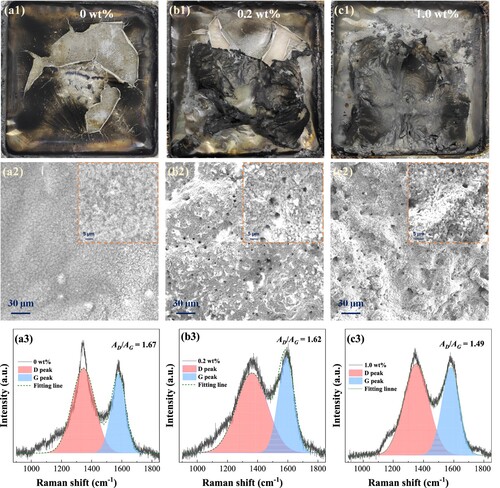
In contrast, the addition of CNT@α-ZrP nanohybrid leads to significant changes in the char residue. Composite samples containing CNT@α-ZrP nanohybrid exhibit increased char residue with fewer cracks and voids. Incorporating 1 wt% of CNT@α-ZrP yields a continuous, unbroken char residue that fully envelops the basal aluminium foil. Moreover, SEM analysis demonstrates the formation of a more compact and less cracked char residue, which serves as an efficient protective barrier for the underlying matrix, thereby aiding in the suppression of heat release.
(a3-c3) shows the Raman spectra of PA12 and its composites’ char residues and composites. The spectra show two large peaks at 1350 and 1590 cm−1, representing the D- and G- peaks. The AD/AG ratio, calculated as the area ratio of the integrated intensities of the D to G bands, serves as a metric for assessing the graphitisation degree of the char residues. A lower AD/AG value signifies a higher degree of graphitisation in the char, potentially resulting in a more effective protective effect for the underlying matrix. The AD/AG ratio reduced from 1.67 (neat PA12) to 1.49 (1 wt% PA12/CNT@α-ZrP), showing that the char residues of 1 wt% PA12/CNT@α-ZrP have the highest graphitisation degree. The increased graphitisation can be attributed to the synergistic effect of the catalytic action and the physical effect of CNT@α-ZrP nanohybrid towards producing more stable char structures that protect the underlying polymer.
illustrates a potential flame retarding mechanism for CNT@α-ZrP dispersed within the PA12 matrix, building upon earlier presented data. The incorporation of CNT@α-ZrP nanohybrid notably enhances the fire safety of PA12 through several mechanisms: (i) The α-ZrP nanosheets serve as solid acid catalysts, expediting the degradation of PA12 molecular chains and augmenting char yield during combustion; (ii) The CNT@α-ZrP nanohybrid acts as a physical barrier, hindering the infiltration of heat and oxygen, inhibiting the release of volatile degradation products, and enhancing the formation of carbon layers during combustion; (iii) The CNT@α-ZrP nanohybrid adsorbs and captures combustion products, forming a protective layer that obstructs the further diffusion of oxygen and combustion reactants, thereby retarding flame propagation.
3.9. Numerical modelling of mechanical behaviour
Neat PA12 and PA12/CNT@α-ZrP's stress–strain relationship illustrates the typical behaviour of a hyperelastic material. Different theoretical models exist in the literature to describe their behaviour. These models are described in terms of the deviatoric strain potential. The majority of them are stretch-based or invariant-based models, with definitions given in terms of principal stretch ratios (λi) and invariants (Ii), respectively. In the models using polynomials, the deviatoric strain energy potential is described as follows by the generalised Rivlin hyperelastic model [Citation42]:
(2)
(2) where the deviatoric strains’ first and second invariants are denoted by the symbols
and
. A material constant that characterises its shear behaviour is
. When N equals 1, the Mooney-Rivlin model can be found, with
equal to
. In certain variants of the polynomial model, some coefficients are set to zero. This simplified polynomial results from setting all
with j not equal to 0–0.
(3)
(3)
In this abbreviated form, the Neo-Hooke and Yeoh models are produced when N is equal to 1 and 3 [Citation43]. On the other hand, the Ogden potential, which is a generalised form of stretch-based type of deviatoric strain energy, is as follows:
(4)
(4) The material constants
and
in this case, describe the shear behaviour. Further information on the model is available elsewhere [Citation31]. In the following, ABAQUS [Citation31] software is used to determine the material constants of these models. This software essentially does a reanalysis of the data collected from experimentation, generating material coefficients and employing several models to draw the stress–strain curve. For this purpose, a least-squares fit method that minimises the relative error in stress is used. The relative error measure E is minimised for the n nominal-stress–nominal-strain data pairs using the following equation [Citation42]:
(5)
(5) where
is derived from one of the nominal stress expressions, and
is a stress value from the test data. compares the stress–strain curves obtained using different hyperelastic models for 1.0 wt% CNT@α-ZrP, also comparing them with the experimental curve. It is noted that all of the curves’ overall tendencies coincide with the experimental curve. Nevertheless, compared to both Ogden models, the curves produced using the Mooney-Rivlin and Yeoh models specifically diverge further from the experimental one.
Figure 15. The stress-strain relationship of 1.0 wt% CNT@α-ZrP obtained experimentally and using different hyperelastic material models.
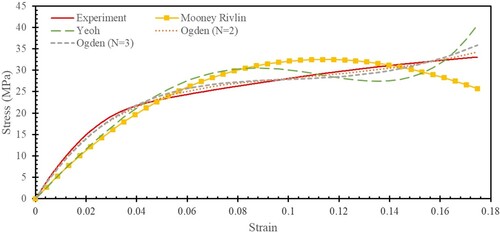
displays the constants that were determined as well as the fitting errors for every model for all of the materials that were examined. For neat PA12, the Neo-Hooke and Ogden (N = 1) models, with 100.50 and 44.04 fitting errors, respectively, were found to have the worst fit. Therefore, these models were not considered for other PA12/CNT@α-ZrP composites. However, this curve was more accurately predicted by the Mooney-Rivlin, Yeoh and both Ogden models (N = 2, 3) with a fitting error of around 10. Likewise, these models predicted the stress–strain relationship of 0.1 wt% CNT@α-ZrP with similar accuracy, with a fitting error of around 25. However, far better fits were achieved using both Ogden models when compared to those of the other two models for 0.2, 0.5 and 1.0 wt% CNT@α-ZrP. For example, for 1.0 wt% CNT@α-ZrP, the errors were just 2.64 and 3.65 for the Ogden (N = 2) and Ogden (N = 3) models, respectively, but they were 31.94 and 28.49 for the Mooney-Rivlin and Yeoh models. In addition to having a superior fit to the test data, Ogden (N = 2) has two fewer constants than Ogden (N = 3), which makes the former model overall the more appropriate one for all the materials under study.
Table 7. The constants of different hyperelastic models with the fitting errors.
The stability of the hyperelastic material models should be checked. ABAQUS makes this check using the Drucker Stability Postulates [Citation43]. For an incompressible material to meet this stability condition, the change in stress () that results from even an infinitesimal change in the logarithmic strain (
) must satisfy the following conditions:
(6)
(6) Here
is the tangent material stiffness. This inequality for material stability requires
to be positive-definite, i.e.
and
. The stability check was performed for the Ogden model for different deformation modes including uniaxial, biaxial, planar and volumetric deformations. shows the range of strains that, for the composites under study, maintain the stability of the Ogden hyperelastic material models. The Drucker Stability recommends that the stability range of Ogden (N = 3) covers more strain values than that of Ogden (N = 2). For example, Ogden (N = 3) is stable for all strain values under uniaxial tension, biaxial compression, and planar loading independent of its direction for neat PA 12 and 0.1 wt% CNT@α-ZrP; nevertheless, when Ogden (N = 2) is employed as the model, there are specific ranges for them. For other composites, their disparity was smaller, though. For any volume ratios, both models can be utilised in volumetric tension or compression.
Table 8. The range of strains and volume ratios for the Ogden hyperelastic models under various loads.
In this investigation, the material constants were established solely through uniaxial tensile testing. These constants provide insights into how polymeric composites might respond under different loads including volumetric tension and compression; planar tension and compression; biaxial tension and compression; and uniaxial compression. Given the intricacy and expense associated with producing these composites via selective laser sintering, these theoretical models offer engineers a means to accurately predict material behaviour across a range of applications. They also facilitate design optimisation, ensuring adherence to performance specifications while minimising factors like weight and cost before manufacturing. However, it's important to note that the reliability of these models can be improved through additional experimental tests under various loading conditions [Citation44].
Conclusions
The CNT@α-ZrP coated PA12 powders are utilised to prepare ideal-performance PA12 composite parts with complex geometries via the SLS approach. The micro-morphology analysis reveals that ball milling is an appropriate and facile method to uniformly disperse the nanofillers without affecting PA12 powder's morphology. Compared with neat PA12, the tensile and impact strength achieved 33.1% and 34.6% improvement with the addition of 0.2 wt% CNT@α-ZrP nanohybrid, respectively. Adding more than 0.2 wt% of CNT@α-ZrP significantly reduced mechanical strengths, owing to the surface crowding of PA12 particles by CNT@α-ZrP hindered the physical contact between PA12 particles. By adding 1.0 wt% CNT@α-ZrP, the friction coefficient and volume wear rate are reduced by 47% and 64.7%, respectively. Additionally, the addition of CNT@α-ZrP nanohybrid suppresses the smoke release and improves the fire safety of PA12 composites. The hyperelastic material constants of produced nanocomposites were best described by the Ogden models among various theoretical models used. Engineers utilise these constants to accurately model material behaviour and optimise designs for various applications, while also considering constraints such as weight, cost, and the challenges of selective laser sintering for composite production. This work provides a facile method of functional PA12 composites by employing α-ZrP sheets and CNTs nanofillers and additive manufacturing.
Supplemental Material
Download MS Word (876.9 KB)Acknowledgments
Sensen Han would like to thank Shiyanjia Lab (www.shiyanjia.com) for the XRD testing.
Disclosure statement
No potential conflict of interest was reported by the author(s).
Data availability statement
The data that support the findings of this study are available from the corresponding author, upon reasonable request.
Additional information
Funding
References
- Du H, et al. Experimental and theoretical study of the evolution of fluid-suspended graphene morphology driven by an applied electric field and the attainment of ultra-low percolation threshold in graphene-polymer nanocomposites. Compos Sci Technol. 2020;199:108315.
- Li C, et al. Mechanical properties of polymer nanocomposites with randomly dispersed and cross-linked two-dimensional diamond. Compos Sci Technol. 2022;230:109722.
- Wang W, Liu Y, Wang Q. Adjustable boron nitride segregated framework in epoxy resin for high performance thermal management and flame retardant applications. Compos Sci Technol. 2023;242:110161.
- Tang Z-H, et al. Modeling the synergistic electrical percolation effect of carbon nanotube/graphene/polymer composites. Compos Sci Technol. 2022;225:109496.
- Zhang X, et al. Revealing the apparent and local mechanical properties of heterogeneous lattice: a multi-scale study of functionally graded scaffold. Virtual Phys Prototyp. 2023;18(1):e2120406.
- Xiao Z, et al. Recent progress on microstructure manipulation of aluminium alloys manufactured via laser powder bed fusion. Virtual Phys Prototyp. 2023;18(1):e2125880.
- Al Noman A, Kumar BK, Dickens T. Field assisted additive manufacturing for polymers and metals: materials and methods. Virtual Phys Prototyp. 2023;18(1):e2256707.
- Wang H, et al. Laser powder bed fusion of poly-ether-ether-ketone/bioactive glass composites: processability, mechanical properties, and bioactivity. Compos Sci Technol. 2023;231:109805.
- Wang H, et al. Comparative evaluation of printability and compression properties of poly-ether-ether-ketone triply periodic minimal surface scaffolds fabricated by laser powder bed fusion. Addit Manuf. 2022;57:102961.
- Wang H, et al. Isothermal crystallization behavior of poly-ether-ether-ketone/bioactive glass composites and its correlation with scaffold warpage in laser powder bed fusion process. Addit Manuf. 2023;78:103852.
- Chen P, et al. Mechanical properties and microstructure characteristics of lattice-surfaced PEEK cage fabricated by high-temperature laser powder bed fusion. J Mater Sci Technol. 2022;125:105–117.
- Ou J, et al. Additive manufacturing of flexible polymer-derived ceramic matrix composites. Virtual Phys Prototyp. 2023;18(1):e2150230.
- Rosso S, et al. In-depth comparison of polyamide 12 parts manufactured by multi Jet fusion and selective laser sintering. Addit Manuf. 2020;36:101713.
- Yuan S, et al. Electrical and thermal conductivities of MWCNT/polymer composites fabricated by selective laser sintering. Compos Part A Appl Sci Manuf. 2018;105:203–213.
- Chatham CA, Long TE, Williams CB. A review of the process physics and material screening methods for polymer powder bed fusion additive manufacturing. Prog Polym Sci. 2019;93:68–95.
- Cai C, et al. Comparative study on 3D printing of polyamide 12 by selective laser sintering and multi jet fusion. J Mater Process Technol. 2021;116882.
- Araby S, et al. Graphene platelets versus phosphorus compounds for elastomeric composites: flame retardancy, mechanical performance and mechanisms. Nanotechnology. 2019;30(38):385703.
- Araby S, et al. Recent advances in carbon-based nanomaterials for flame retardant polymers and composites. Compos Part B: Eng. 2021;212:108675.
- Han S, et al. Synergistic effect of graphene and carbon nanotube on lap shear strength and electrical conductivity of epoxy adhesives. J Appl Polym Sci. 2019;136(42):48056.
- Zhu D, et al. Thermal and mechanical properties of polyamide 12/graphene nanoplatelets nanocomposites and parts fabricated by fused deposition modeling. J Appl Polym Sci. 2017;134(39):45332.
- Vidakis N, et al. Multi-functional polyamide 12 (PA12)/ multiwall carbon nanotube 3D printed nanocomposites with enhanced mechanical and electrical properties. Adv Compos Mater. 2022;31(6):630–654.
- Vidakis N, et al. Medical grade polyamide 12 silver nanoparticle filaments fabricated with in-situ reactive reduction melt-extrusion: rheological, thermomechanical, and bactericidal performance in MEX 3D printing. Appl Nanosci. 2024;14(1):69–88.
- Lupone F, et al. Innovative approach to the development of conductive hybrid composites for selective laser sintering. Compos Part A Appl Sci Manuf. 2021;147:106429.
- Yuan Y, et al. The combination of Al2O3 and BN for enhancing the thermal conductivity of PA12 composites prepared by selective laser sintering. RSC Adv. 2021;11(4):1984–1991.
- Han S, et al. Using renewable phosphate to decorate graphene nanoplatelets for flame-retarding, mechanically resilient epoxy nanocomposites. Prog Org Coat. 2023;182:107658.
- Meng Q, et al. Preparation of high-performance bismuthene thermoelectric composites doped with graphene using UV-curing 3D printing technology. Polym Compos. 2024;45(9):8176–8186.
- Lopes AC, Sampaio AM, Pontes AJ. Composite materials with MWCNT processed by selective laser sintering for electrostatic discharge applications. Polym Test. 2022;114:107711.
- Azam MU, Schiffer A, Kumar S. Mechanical and piezoresistive behavior of selectively laser sintered MWCNT/UHMWPE nanocomposites. Compos Part A Appl Sci Manuf. 2023;173:107701.
- Lopes ACF, Sampaio ÁM, Pontes AJ. Composite materials with MWCNT processed by selective laser sintering for electrostatic discharge applications. Polym Test. 2022;114:107711.
- Aghajani S, et al. Additively manufactured composite lattices: A state-of-the-art review on fabrications, architectures, constituent materials, mechanical properties, and future directions. Thin-Walled Struct. 2024;197:111539.
- Systemes D. Abaqus 6.12 Online documentation. Accessed on 26 April 2024.
- Han S, et al. Tackling smoke toxicity and fire hazards of thermoplastic polyurethane by mechanochemical combination of Cu₂O nanoparticles and zirconium phosphate nanosheets. Polym Degrad Stab. 2023;212:110350.
- Han, S., et al., Supramolecular-Wrapped α-zirconium phosphate nanohybrid for fire safety and reduced toxic emissions of thermoplastic polyurethane. ACS Appl Polym Mater, 2024;6:1376–1388.
- Han S, et al. Synergetic effect of alpha-ZrP nanosheets and nitrogen-based flame retardants on thermoplastic polyurethane. ACS Appl Mater Interfaces. 2023;15(13):17054–17069.
- Dadbakhsh S, et al. Effect of powder size and shape on the SLS processability and mechanical properties of a TPU elastomer. Phys Procedia. 2016;83:971–980.
- Schmid M, Amado A, Wegener K. Polymer powders for selective laser sintering (SLS). AIP conference proceedings. 2015. AIP Publishing
- Chávez-Medellín R, Prado LASdA, Schulte K. Polyamide-12/Functionalized carbon nanofiber composites: evaluation of thermal and mechanical properties. Macromol Mater Eng. 2010;295(4):397–405.
- McNally T, et al. Polyamide-12 layered silicate nanocomposites by melt blending. Polymer. 2003;44(9):2761–2772.
- Shi Y, et al. Effect of the properties of the polymer materials on the quality of selective laser sintering parts. Proc Inst Mech Eng. 2004;218(3):247–252.
- Pham DT, Dotchev KD, Yusoff WAY. Deterioration of polyamide powder properties in the laser sintering process. Proc Inst Mech Eng Part C. 2008;222(11):2163–2176.
- Meng Q, et al. Highly ductile and mechanically strong Al-alloy/boron nitride nanosheet composites manufactured by laser additive manufacturing. J Manuf Process. 2023;89:384–396.
- Abdelsalam A, et al. Effect of filler surface treatment on the physico-mechanical properties of filler/styrene-butadiene rubber nanocomposites. J Thermoplast Compos Mater: 08927057241244708. doi:10.1177/0892705724124470.
- Li W, Xin Z. Flexural fatigue life prediction of a tooth V-belt made of fiber reinforced rubber. Int J Fatigue. 2018;111:269–277.
- Abubakar I, Myler P, Zhou E. Constitutive modelling of elastomeric seal material under compressive loading. 2016.