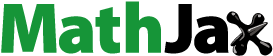
ABSTRACT
The printability of MgO-SiO2 cement pastes involving the use of microsilica (MS) and metakaolin (MK) as a SiO2 source was thoroughly investigated. Fresh properties, including rheology and early-age strength, mechanical properties and microstructures of pastes incorporating different contents of MK were presented and analyzed. Amongst samples studied, those containing 5% MK as a substitute for MS exhibited the highest static yield stress, and fastest re-flocculation and structuration rates, resulting in the best buildability. Although the inclusion of 10% MK resulted in enhanced paste strength at 7 and 28 days, increased MK content impeded paste printability due to diminished formation of hydrate phases. Use of 5% MK led to higher M-S-H generation compared to other samples at 28 days, contributing to subsequent strength development. Results demonstrated that optimisation of the MK content in MgO-SiO2 pastes can yield satisfactory mechanical strengths without compromising printability.
1. Introduction
Additive manufacturing (3D printing) is a promising technology that has experienced substantial advancements in recent years [Citation1, Citation2]. It has been utilised across several fields, including industrial design [Citation3], aeronautics and astronautics [Citation4], biomedical [Citation5] and food processing [Citation6]. The implementation of 3D printing in the construction industry is an ideal enhancement to conventional methods of fabrication. 3D printing can shorten the length of time required for construction, decrease labour costs, and improve the efficiency [Citation7, Citation8]. Furthermore, a notable benefit of 3D printing lies in its capacity to fabricate unique and intricate structures that are unattainable by traditional casting methods including formwork. This capability expands the range of options available for construction in the field of building engineering.
The prevalent 3D printing technology for architectural applications consists primarily of three types: Contour crafting, D-shape and concrete printing [Citation9–12]. The primary procedure involved in contour crafting entails the extrusion and establishment of a contour with prescribed dimensions, after which the concrete is poured into the internal space when the boundaries have sufficient strength to contain the filling concrete. Unlike concrete casting, contour printing does not necessitate the use of formworks. For concrete printing, the entire process of building structure is accomplished via 3D printing. In the context of extrusion-based 3D printing, it is imperative to utilise printed materials (e.g. cement-based formulations) that possess appropriate rheological properties. This is crucial for achieving the desired dimensional precision in the construction of buildings [Citation13]. During this process, before attaining a layered printing structure, cementitious materials are subjected to a series of complex transportation processes, including pumping, resting, and high-speed extrusion involving static and dynamic yield stresses, viscosity variations, and thixotropic structural build-up [Citation14–17]. Controlling these parameters is critical for optimising the printability of cementitious materials.
The production of Portland cement (PC), the most commonly used building material on a global level, is responsible for 5–8% of anthropogenic CO2 emissions [Citation18, Citation19]. To address this issue, alternative binder systems with potentially lower environmental impacts are being developed [Citation20, Citation21]. One system currently being investigated is MgO-SiO2 based binders, which consist of reactive magnesia cement (RMC) and a silica source [Citation22–25]. These binders present several advantages when compared to PC-based systems. Firstly, the calcination temperatures involved in the production of RMC are significantly lower than that for PC (700–1000°C vs. 1450°C). This reduction in temperature can enable lower energy consumption linked to the calcination of an equivalent amount of clinker, thereby contributing to energy conservation [Citation26–29]. Furthermore, MgO can be extracted not only from magnesium carbonate minerals [Citation30, Citation31], but also from seawater or brine sources [Citation32, Citation33]. These characteristics contribute to the potential and notable advantages of RMC as compared to other alternative binders. The utilisation of the MgO-SiO2 system has been demonstrated in several applications, such as the stabilisation/solidification of strontium [Citation34], development of composites involving natural fiber reinforcements [Citation35, Citation36] and waste encapsulation [Citation37]. These diverse applications have significantly contributed to the growing interest in exploring the properties and potential of this binder system as a building material.
While the composition of the MgO-SiO2 system is relatively straightforward, its hydration process is commonly regarded as an intricate interplay of dissolution and precipitation [Citation38–42]. Upon powder-water mixing, MgO promptly dissolves in water, releasing Mg2+ ions that disperse in the solution. The hydration of MgO is hampered by the adherence of Mg(OH)2, the main product of MgO hydration, to its surface. Additionally, owing to the initially low concentration of OH− ions in the solution, the solubility of SiO2 is considerably limited during the early stages. As hydration progresses, SiO2 coalesces into a chain structure in the form of a free silica tetrahedron (SiO(OH)3− or SiO(OH)2−), gradually transitioning from a chain structure to a layered or network structure. This transformation enhances the microstructural density.
Within the context of 3D printing, the early performance (i.e. primarily manifested in rheological properties) and the mechanical properties during the hardening stage of MgO-SiO2 mixes are intricately linked to their hydration reaction and phase evolutions. Optimising these properties through the adjustment of the binder composition can play a key role in the application of MgO-SiO2 mixes in 3D concrete printing applications.
The nature of silica sources emerges as a pivotal factor influencing the performance and environmental impact of the MgO-SiO2 system. While microsilica (MS) is the predominant SiO2 source in most MgO-SiO2 mixes, investigations into alternative sources of silica, especially concerning properties pertinent to 3D printing, are relatively limited. Apart from MS, other alternative silica sources commonly utilised include fly ash (FA) [Citation43], metakaolin (MK) [Citation44], and rice husk ash (RHA) [Citation45]. Among these, MK stands out as a promising silica source due to its notable reactivity and availability. MK, a material resulting from the calcination and dehydration of kaolinite (a globally abundant clay mineral with verified reserves amounting to 32 billion tons [Citation46]), has been studied in partially replacing PC as a supplementary cementitious material [Citation47, Citation48]. Based on the performance of MK in PC systems, several studies [Citation44, Citation49, Citation50] tried incorporating MK into MgO-SiO2 systems, yielding promising outcomes in terms of mechanical properties. Through optimizations of the water-to-binder (w/b) and the magnesia-to-silica (m/s) ratios, the hydration products of the MgO-MK system exhibit not only the formation of M-S-H gel but also a hydrotalcite-like phase. This dual-phase composition contributes to a notable strength enhancement, with samples achieving strengths of >50 MPa after 90 days of curing [Citation44].
Previous studies have explored the feasibility of MgO-SiO2 systems for 3D printing applications. Panda et al. [Citation51] examined the effects of various parameters, such as the m/s, w/b, and superplasticizer dosage, on the performance of 3D-printable MgO-SiO2 binders. By optimising the thixotropy, the developed mixes were capable of restoring the system’s viscosity to 80% of its initial level within 60 s post-extrusion, resulting in minimal deformation when printing five layers, demonstrating excellent buildability. Building on this, Peng and Unluer [Citation52] conducted a series of rheological measurements on samples with two different MgO/MK ratios, showing that MK can be used as an alternative silica source for MS in 3D printing applications. Despite these contributions, there are still research gaps. Panda et al. only conducted an initial feasibility investigation into the printability of the MgO-SiO2 system, while Peng and Unluer focused on several rheological parameters such as median differential viscosity and dynamic and static yield stresses of MgO-MK pastes without analyzing the performance and microstructure evolution of hardened 3D-printed samples. Besides the rheology of fresh paste, the mechanical properties, phase composition, and microstructure of hardened samples are crucial for the performance in service of printed components in specific applications. This study tried to address these gaps and differentiate itself from previous research by not only using conventional sodium hexametaphosphate (SHMP) as a superplasticizer but also considering the presence of MK and employing polycarboxylate ether superplasticizer (PCE) to achieve a w/b ratio reduction to 0.38, a level not attained in previous studies.
Based on a lack of previous studies on the fresh and hardened performance of the MgO-SiO2 system incorporating MK for 3D printing applications, this study aims to evaluate the impact of partially substituting MS with MK on the printing performance of MgO-SiO2 mixes. The assessment of fresh and hardened pastes comprised of rheology, early and hardened strength, and the evaluation of the integrity of the printed structure (buildability). Furthermore, isothermal calorimetry, X-ray diffraction (XRD), thermogravimetric analysis/derivative thermogravimetry (TG/DTG) and field emission scanning electron microscopy (FESEM) were used to unveil the influence of introducing MK on the phase compositions and microstructural evolution of MgO-SiO2 systems. The results obtained in this study can pave the way for the development of effective alternative binders for 3D printing applications; and provide a theoretical foundation and experimental support for the promotion of MgO-SiO2 printed systems for future engineering applications.
2. Materials and Method
2.1. Materials and mix proportions
RMC, MS, and MK used in this study were provided by Richard Baker Harrison (UK), Elkem, and Concrete Lab (UK), respectively. Their XRF chemical composition is shown in . shows the mix proportions of this study. Three different mixes were prepared, in which the ratio of RMC to silica source (both MS and MK) was set at 1:1. The contents of MK in the system were 5, 10, and 20 wt.%, which corresponded to the replacement of 10, 20, and 40 wt.% MS, respectively. The w/b was kept constant at 0.38. Each formulation involved 4 wt.% SHMP provided by Sigma Aldrich and 0.3 wt.% PCE supplied by Master Builders Solutions to adjust the fluidity of the pastes. To prepare the mixes, SHMP and PCE were first dissolved in water and entirely mixed for 120 s, then the solution was added into the powder while mixing for 5 min using an International Automatic Programmable mortar mixer to obtain a uniform state.
Table 1. Chemical and physical properties of RMC, MS and MK.
Table 2. Mix proportions used in this study.
2.2. Method
2.2.1. Rheology
An Anton Paar MCR 302 rheometer was used to complete the rheological test. The test system was coaxial cylinder geometry, in which the cylindrical rotator surface on the inner wall was serrated to prevent lateral wall slippage. The inner and outer diameters of the cylinder system were 26.660 and 28.915 mm, respectively. The effective contact height between the inner cylinder and the paste was 40 mm. Before starting the test, the evenly mixed paste was poured into the cup, which was then installed on the PELTIER temperature control device to maintain an internal temperature of 20°C.
The rheological test in this section included two parts: Static yield stress and small amplitude oscillation shear (SAOS) measurements. The former was conducted in the rotational mode, while the latter was performed in the oscillatory mode. The measurement of the static yield stress involved the application of an external force at a low shear rate in order to determine the corresponding shear stress. The shear stress will have a distinct changing pattern characterised by an initial fast increase, followed by a slow reduction or a tendency to stabilise after reaching the maximum stress level. Prior to reaching the peak value, the microstructure of the paste remains relatively undamaged by external shear stresses, hence enabling the paste to exhibit resistance against such external forces. Nevertheless, once the stress reaches its peak, a significant portion of its network structure undergoes disintegration, hence initiating a subsequent decrease in stress levels [Citation53]. Based on the above theory, it can be considered that the peak stress is the static yield stress of the paste (τs). Due to the large yield stress of pastes used for 3D printing, 0.02 s−1 was selected as a test to maintain a constant rate, according to previous studies [Citation54]. In addition, SAOS was selected to test the non-destructive structural build-up rate, as the selected strain of SAOS would be located within the linear viscoelastic range (LVR). The microstructural development caused by hydration and flocculation could be tested without being damaged if a sufficiently small strain and appropriate frequency were applied. In the amplitude sweep, the strain was incrementally increased from 10−3% to 101%, while the frequency remained constant at 1 Hz [Citation55]. After obtaining a strain from the LVR, this strain was applied to the paste, and the time sweep test was conducted for 1800 s using this constant strain. Before all rheological tests, the pastes were subjected to a pre-shear of 40 s−1 for 60 s, followed by a resting interval of 4 min, which could eliminate the impact of shear history on test results.
2.2.2. 3D printing
The 3D printing process of MgO-SiO2 pastes was performed by a StoneFlower 4.0 Multimaterial four-axis 3D printer ((a)). Since the printer was equipped with several nozzles of different sizes, the nozzle with the largest diameter (7 mm) was selected to complete the experiment. Prior to the start of the printing procedure, Fusion 360 was employed to conceptualise and determine the specific configuration and dimensions of the model. Subsequently, the resultant file was transferred into Ultimaker Cura 5.1.0, a software program utilised for the process of slicing. Finally, the obtained Gcode was uploaded to the printer. The printing models selected for this study were circular shapes with a diameter of 100 mm and ellipses with a straight line connection in the middle (with a long axis of 200 mm and a short axis of 100 mm). Both models had a total height of 50 mm, including 10 layers each, with a height of 5 mm and a width of 10 mm.
2.2.3. Compressive strength
Both the early and ultimate strengths were measured by an Instron 3367 universal testing machine ((b)). The early strength measurements were conducted on a cylindrical sample with a diameter of 60 mm and a height of 100 mm. The evenly mixed pastes were first poured into the molds and kept in an environmental chamber (20°C and 95% RH) for 60 and 120 min respectively, which corresponds to the open time range of printable cementitious materials. Then the samples were carefully demolded. Each sample was subjected to a force at a loading rate of 0.02 mm/s, and the test stopped when the strength decreased to 60% of its peak value. Samples were prepared using 20 mm × 20 mm × 20 mm molds to complete the 3, 7, and 28 d compressive strength tests [Citation56, Citation57]. The pastes were cast into the corresponding molds and covered with a wet film to prevent the moisture from evaporating. After curing for 24 h, the specimens were removed from the mold and transferred to the same environmental chamber for subsequent curing.
2.2.4. Characterization of reaction process and products
The hydration reaction process and products of MgO-SiO2 pastes were characterised by isothermal calorimetry, XRD, TG/DTG, and SEM. The heat flow and cumulative heat release of the three mixes (MSH-MK05, MSH-MK10, and MSH-MK20) were measured using an I-Cal 4000 HPC isothermal calorimeter. The powder mass of each group of samples remained unchanged at 50 g. The experimental temperature was set to 20°C and maintained for a duration of 72 h. Data points were collected at regular intervals of 60 s.
Before performing solid phase analysis, hydration stoppage was conducted on each group of pastes. Approximately 3 g of sample was collected and soaked in a sealed bottle filled with isopropanol for a duration of 7 d, then the wet sample was taken out and placed in a 70°C drying oven for 24 h. The dried sample was fully ground with a mortar and pestle and put into a self-sealing bag in a vacuum environment in preparation for subsequent testing.
A Miniflex benchtop X-ray diffractometer was used for testing XRD. The powders were scanned at a speed of 5°/min within the 2-theta range of 5°–80° and the test points were recorded every 0.02°. TG-DTG measurements were conducted by a Perkin Elmer TGA 8000. The mass of each sample ranged from 30 to 40 mg, and the crucible was peeled prior to measurement. The heating rate was 10°C/min, and the temperature increased from 50 to 1000°C. The microscopic morphology was observed using a Field Emission Scanning Electron Microscope (FESEM, ZEISS Sigma) with a scanning acceleration voltage of 5.00 kV. To obtain the highest image resolution, the working distance was adjusted between 4.5 and 5.5 mm, and the surface of each sample was coated with gold.
3. Results and discussion
3.1. Rheology
In the absence of adverse phenomena such as bleeding, the majority of cement paste can resist external shear force to a certain extent [Citation58]. The static yield stress refers to the minimal stress required to induce the transition of the paste from its initial static condition to a macroscopic flow [Citation59]. Colloidal interactions and Brownian motions are significant factors in determining the static yield stress [Citation60]. Taking into account the hydration effect, the larger the colloidal attraction and bonding strength of the hydration product than Brownian motion, the greater the resistance to the external force of cement paste. depicts the evolution of shear stress as a function of hydration time. According to the results of static yield stress tests conducted at 10-min intervals for each paste, the change trend of shear stress over time exhibited a consistent pattern. Under the same mix proportion, the time for the shear stress to reach its peak gradually increased with the extension of hydration time, as did the corresponding peak shear stress, indicating that the paste with a longer resting time exhibited higher static yield stress prior to entering a flowing state.
Figure 2. Static yield stress measurements of MgO-SiO2 pastes incorporating MK, showing: (a) MSH-MK05, (b) MSH-MK10 and (c) MSH-MK20.

Comparing the static yield stress of different pastes reveals that the peak stress decreased with the increase in MK content. To further characterise the time-dependent evolution of the yield stress, the bi-linear model proposed by Kruger et al. [Citation61] was used to characterise the re-flocculation rate (Rthix) and structuration rate (Athix), as shown in Eqs. (1) and (2):
(1)
(1)
(2)
(2) Where, τS is the static yield stress, trf represents the duration of re-flocculation, τS,i and τD,i are the initial yield stresses before and after trf, respectively. The reversible flocculation process of particles, governed predominantly by physical interactions, can be effectively characterised by the rapid re-flocculation rate, which quantifies the recovery of shear stress in the paste after the cessation of intense mixing. Meanwhile, the hydration-induced densification of the microstructure gradually transforms the paste from a plastic fluid into an elastic solid, a process that requires a longer reaction time. Consequently, the structuration rate refers to the subsequent increase in the yield stress of the cement paste as a result of hydration. shows the fitting results of the bi-linear model based on the peak stress in , and the corresponding parameters are listed in . It can be found that samples with a MK substitution rate of 5% exhibited a strong re-flocculation at the early stage (its corresponding Rthix was 9.25), and the Rthix of the paste began to decline rapidly with the increase in MK content. When the paste entered the stage dominated by structuration, there was no significant difference between the Athix values of the three samples (2.37, 2.96, and 2.56), but the τS,i of MSH-MK05 was significantly larger than that of the other two pastes.
Table 3. Fitting parameters of static yield stress.
Using τs and storage modulus G′ to characterise the structural build-up rate both begin with an undamaged paste microstructure. However, the state transition corresponding to τs is for the paste to transition from a non-fluid state to a fluid state, whereas the small oscillation strain used for G′ measurement hardly affects the microstructure of the paste [Citation62]. depicts the effects of strain on G′ of three pastes based on amplitude sweep. It can be found that all G′ exhibited a significant strain dependence, and the corresponding LVR critical strain was less than 10−2%. For subsequent time sweeps, it was reasonable to apply a 10−3% constant strain to ensure that the paste structure would not be damaged. reveals that all pastes exhibited significant growth only after 1000 s of hydration, whereas growth was comparatively flat before that. The MSH-MK05 sample displayed a significantly higher G′ than the other two pastes, suggesting that a moderate incorporation of MK (5%) can sustain a rapid early structural build-up. Conversely, the sample containing 20% MK exhibited a slower G′ evolution rate, attributed to the lower degree of agglomeration of MK in comparison to MS.
3.2. Early strength
In addition to the τs and G′ over time, the early strength can be used to further quantify the buildability of fresh cement pastes. Since MgO-SiO2 paste did not harden during the fresh stage and its strength was derived solely from flocculation between particles and a low degree of hydration, the strain necessary to reach the peak stress would also be significantly greater than that of the hardened specimen. (a) and (b) illustrate the variations in compressive stress with strain for the three samples during 1 and 2 h of hydration. At 1 h, the peak compressive stresses of MSH-MK05, MSH-MK10, and MSH-MK20 were 24.9, 22.1, and 18.2 kPa, respectively, indicating that the sample with the lowest MK content displayed the highest peak stress. When the hydration time was increased to 2 h, the compressive stresses of MSH-MK05 and MSH-MK10 both exceeded 34 kPa. This was analogous to the previous results of G′ evolution, in that the paste with a higher MK content demonstrated an initial period of slow development followed by a subsequent period of rapid development. Although the stress of MSH-MK20 at 2 h was 71.9% higher than that at 1 h, its strength was still only 31.2 kPa owing to the slow stress development rate in the early stage.
3.3. 3D printing and mechanical performance
depicts the modeling procedure for a 3D-printed cylinder as well as the obtained structure printed with MSH-MK05. By optimising printing parameters, including extrusion speed and time intervals, it is possible to get a printed structure with excellent dimensional accuracy. Three pastes were printed independently while keeping all other settings constant to examine their variations more closely in terms of printability. By comparing (a), (b), and (c), it is evident that only the MSH-MK05 structure performed well, whereas the lateral walls of the other two structures collapsed to varying degrees. In addition, considerable moisture could be observed on the structural surfaces of MSH-MK10 and MSH-MK20, suggesting that there was also a degree of bleeding in the paste extruded through the nozzle, a phenomenon that 3D-printed structures should avoid. Building on the previous printing results for the MgO-SiO2 system [Citation51, Citation52], the achievement of printability with lower MK content demonstrated in this study, including printing layer height and corresponding rheological parameters, closely aligns with previous findings. However, when the MK content reached 20%, there was a noticeable decline in both yield stress and structural build-up, underscoring the importance of carefully controlling MK content.
Figure 7. 3D printed cylinder of MSH-MK05 mix, showing: (a) Fusion 360 image, (b) UltiMaker Cura slicing and (c) printed sample.
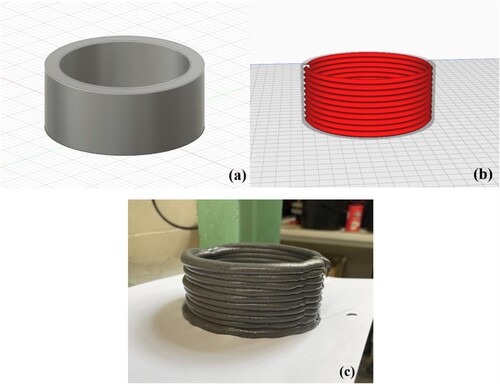
The main distinction between additive manufacturing and conventional casting is that the former does not require the use of molds, while the latter does. Nonetheless, the printing structure is susceptible to collapse, particularly when contour crafting technology is employed. Currently, two mechanisms are thought to be responsible for the failure of 3D-printed cementitious materials: loss of stability and material failure [Citation63, Citation64]. According to the previous early-age strength results, a paste with a 5% MK content had the strongest bearing capacity within 2 h, corresponding to the relatively good printing structure in (c) and (a). In (b) and (c), however, there was a substantial material failure. Due to bleeding, the subsequent extruded material could not adhere securely to its contiguous lower layer. In addition, due to the high-speed rotation of the screw during extrusion, this severe mechanical perturbation might make the initially homogeneous paste more susceptible to bleeding.
In accordance with the compressive strength of the three mixes at various ages shown in , the sample cured for 28 d exhibited a significant increase in strength compared to the samples cured for 3 and 7 d. Among the three pastes examined, MSH-MK05 demonstrated the highest 3 d strength, measuring at 16.7 MPa. However, after being cured for a duration of 7 d and 28 d, the sample containing 10% MK exhibited the highest strength (21.1 MPa at 7 d and 38.9 MPa at 28 d). This finding differed from the results obtained for early-age and 3 d strengths. As the MK content increased to 20%, the strength of the MgO-MS-MK paste began to decrease. This observation suggests the existence of an optimal MK percentage in the system. When compared to the results of previous rheological tests, the compressive strength at the same age did not exhibit such significant differences as G′ and τS between distinct mixes.
3.4. Hydration
In order to gain a better understanding of the hydration characteristics of 3D-printed MgO-MS pastes containing MK, the heat flow and cumulative heat release of three mixes were evaluated, as shown in . Each paste exhibited a notable exothermic peak within 1 h after the powder was completely mixed with the aqueous solution, which was ascribed to the early dissolution of RMC [Citation38, Citation65]. After approximately 6 h of hydration, the heat flow rate of the paste reduced to a relatively low level, which fell within the range of the induction period. The alteration in MK content did not induce a notable variation in the initial hydration rate of the composite paste. Consequently, while the substantial augmentation in the hydration rate during the initial phase prompted a quick elevation in storage modulus and static yield stress, it is not accountable for the divergence in rheological attributes observed in the MgO-MS-MK system at varying MK contents.
Figure 10. Isothermal calorimetry results of MgO-SiO2 pastes incorporating MK, showing: (a) heat flow and (b) cumulative heat release.
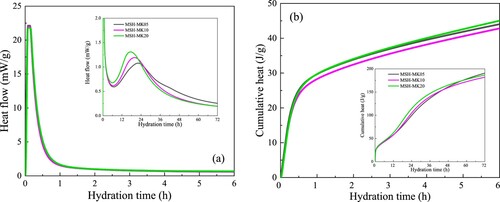
During the acceleration period (12–24 h), MK had a significant effect on the hydration rate of the MgO-MS system, primarily by increasing the peak value of heat flow, whereas it had no significant effect during the fresh stage. Analysis of the cumulative heat release curve indicates that after approximately 54 h of hydration, the cumulative heat release of MSH-MK20 was lower than that of MSH-MK05, proving that the increased MK content primarily intensified the early hydration heat release of the MgO-SiO2 paste. This observation aligns with previous strength results, which demonstrated that MSH-MK20 exhibited the lowest 28-day strength among the three sample groups.
3.5. XRD
depicts the XRD patterns of MgO-SiO2 pastes containing MK after curing for 3 d, 7 d and 28 d. Regardless of the difference in MK content or curing duration, the displayed patterns depict identical hydration product composition. The plainly observable peak was periclase (37.1°, 43.1°, 62.5°, 74.8°, and 78.8°), with the peak of 43.1° being the highest and thus considered the main peak [Citation49]. Notably, the formation of brucite was difficult to observe in the early hydration stage (3 and 7 d), indicating that the hydration degree of MgO was relatively low in the early stage. When the 2θ was in the range of 20°−25°, in addition to the inclusion of MSH, it was also due to the same amorphous MS, which required further observation of humps near 60°. It has been discovered that only after 7 d MSH had a relatively obvious generation. Due to the low MK substitution rate of the mix proportions, almost no alumina or hydrotalcite-like phases were detectable in the patterns. The reduced Al/Si atomic ratio was assumed to account for the absence of hydrotalcite formation [Citation49]. However, previous research has confirmed that aluminum could displace silicon at certain sites (tetrahedral and octahedral sites) in MSH, which was analogous to the introduction of aluminum into the CSH system [Citation44].
3.6. TG/DTG
The TG and DTG curves of the mixes at various ages are depicted in (a) and (b), respectively. Despite certain differences in the MK content, the principal thermal decomposition temperature range for all pastes was roughly the same, with two derivative mass peaks occurring between 50 and 250°C and between 250 and 500°C. The former corresponded to the mass loss of physically adsorbed water and interlayer water of M-S-H, whereas the latter was due to the decomposition of brucite, the continued dehydration of M-S-H, and hydrated magnesium carbonates (HMCs) such as hydromagnesite and dypingite [Citation45, Citation66]. Considering there is no subsequent carbonation curing for this system and that most of the M-S-H dehydration has been completed below 300°C, the second weight loss peak is primarily attributable to the dehydration of brucite. With the increase in curing duration, the intensity of the two weight loss peaks (particularly the second peak) increased substantially, which corresponded to a significant rise in Mg(OH)2 content at 28 d. In addition, as hydration increased from 3 d to 28 d, the M-S-H content in the system increased considerably, as indicated by the exothermic peak of 50–250°C. The strength of the first weight loss peak of MSH-MK05 at 28 d was substantially greater than that of the other two groups of pastes, indicating its highest M-S-H generation.
3.7. SEM
and shows the SEM microstructures of MgO-SiO2 pastes containing MK under different curing durations. In order to observe the surface morphology of the formed phases more clearly, the overall view of each sample was demonstrated with the scale of 1 μm, along with a scale of 200 nm. The predominant observed phases in MSH-MK05 () were the flocculation structures formed by MS particles adhering to the surface of MgO particles. By magnifying the MS particles, no significant dissolution of the MS surface was observed during the early stages (3 and 7 d), indicating that the MS reaction degree was notably lower than that of MgO. Some MS particles did not begin to form a relatively compact structure in the surrounding hydration products until the curing duration was extended to 28 d. As shown in , when the MK content reached 20%, a small number of angular and platy MK particles with a degree of irregularity appeared [Citation67], which were embedded in other phases such as MS. Even though the mixes containing more MK exhibited a dense microstructure, SEM results suggest that pores near MK may have resulted in a slight decrease in the mechanical strength. Additionally, there is no evidence that MK played a substantial role in the hydration reaction of the MgO-SiO2 system. The corresponding aluminosilicate hydrates were not easily identified through SEM analysis, as previously reported by the XRD results.
4. Conclusions
This study experimentally discussed the influence of MK incorporation as a substitute for MS on the fresh and hardened properties of MgO-SiO2 pastes in the context of 3D printing. The performance analysis results were supported with a detailed microstructural analysis including isothermal calorimetry, XRD, TG/DTG and SEM, which aimed to reveal the underlying mechanism of MK incorporation in this ternary system. The following conclusions were drawn:
The evolutions of static yield stress over time of MgO-MS-MK pastes were consistent with the bi-linear thixotropy model. The samples incorporating 5% MK exhibited the highest τD,i and τS,i, as well as the greatest Rthix and Athix, indicating its fastest thixotropic structural build-up. Based on the results of the SAOS measurements, lower contents of MK caused a higher storage modulus and its time-dependent structuration rate.
The printing structure obtained with MSH-MK05 exhibited superior buildability when compared to other mixes, in the sense that its shape and size were most similar to the design model when applying the same printing parameters, which could also be verified with the early age strength results. Alternatively, the contour printing walls of the other two pastes (MSH-MK10 and MSH-MK20), collapsed at varying degrees.
While increasing MK content accelerated the heat release of MgO-MS pastes in the range of 12–24 h, it had no significant impact during the fresh stage (i.e. within 2 h of hydration). Considering the preceding rheological assessments and the examination of printed structures, it was concluded that the accelerated hydration of the pastes facilitated by MK did not exert a notably favourable influence on their printability. XRD diffraction results showed lower amounts of brucite formation in the MgO-SiO2 system containing MK when the curing duration was less than 7 d. TG/DTG results revealed that when the MK content was 5%, the samples cured for 28 d had a higher content of M-S-H gel, which corresponded to their superior printability amongst the three mixes. Finally, SEM images revealed the role pores in the vicinity of MK particles may have played in the reduced mechanical properties of these samples.
Disclosure statement
No potential conflict of interest was reported by the author(s).
Data availability statement
The data that support the findings of this study are available from the corresponding author, [YP], upon reasonable request.
Additional information
Funding
References
- Wangler T, Roussel N, Bos FP, et al. Digital concrete: a review. Cem Concr Res. 2019: 123. doi:10.1016/j.cemconres.2019.105780
- Ngo TD, Kashani A, Imbalzano G, et al. Additive manufacturing (3D printing): a review of materials, methods, applications and challenges. Compos B Eng. 2018;143:172–196. doi:10.1016/j.compositesb.2018.02.012
- Sathish T, Vijayakumar M, Ayyangar AK. Design and fabrication of industrial components using 3D printing. Mater Today Proc. 2018;5(6):14489–14498. doi:10.1016/j.matpr.2018.03.036
- Kalender M, Kılıç SE, Ersoy S, et al. Additive manufacturing and 3D printer technology in aerospace industry. 2019 9th International Conference on Recent Advances in Space Technologies (RAST), IEEE. 2019: 689–694. doi:10.1109/RAST.2019.8767881
- Tetsuka H, Shin SR. Materials and technical innovations in 3D printing in biomedical applications. J Mater Chem B. 2020;8(15):2930–2950. doi:10.1039/D0TB00034E
- Guo C, Zhang M, Bhandari B. Model building and slicing in food 3D printing processes: a review. Compr Rev Food Sci Food Saf. 2019;18(4):1052–1069. doi:10.1111/1541-4337.12443
- Buswell RA, Leal de Silva WR, Jones SZ, et al. 3D printing using concrete extrusion: a roadmap for research. Cem Concr Res. 2018;112:37–49. doi:10.1016/j.cemconres.2018.05.006
- Yu K, McGee W, Ng TY, et al. 3D-printable engineered cementitious composites (3DP-ECC): fresh and hardened properties. Cem Concr Res. 2021: 143. doi:10.1016/j.cemconres.2021.106388
- Hamidi F, Aslani F. Additive manufacturing of cementitious composites: materials, methods, potentials, and challenges. Constr Build Mater. 2019;218:582–609. doi:10.1016/j.conbuildmat.2019.05.140
- Zhong H, Zhang M. 3D printing geopolymers: A review. Cem Concr Compos. 2022;128:104455. doi:10.1016/j.cemconcomp.2022.104455
- Peng Y, Unluer C. Development of alternative cementitious binders for 3D printing applications: a critical review of progress, advantages and challenges. Compos B Eng. 2023;252:110492. doi:10.1016/j.compositesb.2022.110492
- Weng Y, Lu B, Li M, et al. Empirical models to predict rheological properties of fiber reinforced cementitious composites for 3D printing. Constr Build Mater. 2018;189:676–685. doi:10.1016/j.conbuildmat.2018.09.039
- Souza MT, Ferreira IM, de Moraes EG, et al. 3D printed concrete for large-scale buildings: an overview of rheology, printing parameters, chemical admixtures, reinforcements, and economic and environmental prospects. J Build Eng. 2020;32:101833. doi:10.1016/j.jobe.2020.101833
- Liu C, Chen Y, Xiong Y, et al. Influence of HPMC and SF on buildability of 3D printing foam concrete: from water state and flocculation point of view. Compos B Eng. 2022;242:110075. doi:10.1016/j.compositesb.2022.110075
- Perrot A, Rangeard D, Pierre A. Structural built-up of cement-based materials used for 3D-printing extrusion techniques. Mater Struct. 2015;49(4):1213–1220. doi:10.1617/s11527-015-0571-0
- Jin Y, Xu J, Li Y, et al. Rheological properties, shape stability and compressive strength of 3D printed colored cement composites modified by needle-like pigment. Addit Manuf. 2022;57:102965. doi:10.1016/j.addma.2022.102965
- Li M, Weng Y, Liu Z, et al. Optimizing of chemical admixtures for 3D printable cementitious materials by central composite design. Mater Sci Addit Manuf. 2022;1:16.
- Peng Y, Unluer C. Analyzing the mechanical performance of fly ash-based geopolymer concrete with different machine learning techniques. Constr Build Mater. 2022;316:125785. doi:10.1016/j.conbuildmat.2021.125785
- Peng Y, Unluer C. Modeling the mechanical properties of recycled aggregate concrete using hybrid machine learning algorithms. Resour Conserv Recycl. 2023;190:106812. doi:10.1016/j.resconrec.2022.106812
- Weng Y, Li M, Ruan S, et al. Comparative economic, environmental and productivity assessment of a concrete bathroom unit fabricated through 3D printing and a precast approach. J Clean Prod. 2020;261:121245. doi:10.1016/j.jclepro.2020.121245
- Juenger MCG, Winnefeld F, Provis JL, et al. Advances in alternative cementitious binders. Cem Concr Res. 2011;41(12):1232–1243. doi:10.1016/j.cemconres.2010.11.012
- Zhang T, Cheeseman C, Vandeperre L. Development of low pH cement systems forming magnesium silicate hydrate (MSH). Cem Concr Res. 2011;41(4):439–442. doi:10.1016/j.cemconres.2011.01.016
- Zhang T, Vandeperre LJ, Cheeseman CR. Formation of magnesium silicate hydrate (M-S-H) cement pastes using sodium hexametaphosphate. Cem Concr Res. 2014;65:8–14. doi:10.1016/j.cemconres.2014.07.001
- Kumar S, Lei J, Yang E-H, et al. Influence of different additives on the rheology and microstructural development of MgO–SiO2 mixes. Compos B Eng. 2022;235:109784. doi:10.1016/j.compositesb.2022.109784
- Weng Y, Ruan S, Li M, et al. Feasibility study on sustainable magnesium potassium phosphate cement paste for 3D printing. Constr Build Mater. 2019;221:595–603. doi:10.1016/j.conbuildmat.2019.05.053
- Hay R, Celik K. Hydration, carbonation, strength development and corrosion resistance of reactive MgO cement-based composites. Cem Concr Res. 2020: 128. doi:10.1016/j.cemconres.2019.105941
- Dung NT, Lesimple A, Hay R, et al. Formation of carbonate phases and their effect on the performance of reactive MgO cement formulations. Cem Concr Res. 2019: 125. doi:10.1016/j.cemconres.2019.105894
- Khalil A, Wang X, Celik K. 3D printable magnesium oxide concrete: towards sustainable modern architecture. Addit Manuf. 2020: 33. doi:10.1016/j.addma.2020.101145
- Peng Y, Unluer C. Interpretable machine learning-based analysis of hydration and carbonation of carbonated reactive magnesia cement mixes. J Clean Prod. 2024;434:140054. doi:10.1016/j.jclepro.2023.140054
- Ruan S, Unluer C. Comparative life cycle assessment of reactive MgO and Portland cement production. J Clean Prod. 2016;137:258–273. doi:10.1016/j.jclepro.2016.07.071
- Unluer C. Carbon dioxide sequestration in magnesium-based binders. Carbon Dioxide Sequestration in Cementitious Construction Materials; 2018; p. 129–173.
- Ruan SQ, Yang EH, Unluer C. Production of reactive magnesia from desalination reject brine and its use as a binder. J CO2 Util. 2021: 44. doi:10.1016/j.jcou.2020.101383
- Dong H, Unluer C, Yang E-H, et al. Synthesis of reactive MgO from reject brine via the addition of NH4OH. Hydrometallurgy. 2017;169:165–172. doi:10.1016/j.hydromet.2017.01.010
- Zhang T, Zou J, Li Y, et al. Stabilization/solidification of strontium using magnesium silicate hydrate cement. Processes. 2020;8(2):163. doi:10.3390/pr8020163
- Zhang T, Dieckmann E, Song S, et al. Properties of magnesium silicate hydrate (MSH) cement mortars containing chicken feather fibres. Constr Build Mater. 2018;180:692–697. doi:10.1016/j.conbuildmat.2018.05.292
- Mármol G, Savastano Jr H. Study of the degradation of non-conventional MgO-SiO2 cement reinforced with lignocellulosic fibers. Cem Concr Compos. 2017;80:258–267. doi:10.1016/j.cemconcomp.2017.03.015
- Zhang T, Vandeperre LJ, Cheeseman CR. Magnesium-silicate-hydrate cements for encapsulating problematic aluminium containing wastes. J Sustain Cem-Based Mater. 2012;1(1–2):34–45. doi:10.1080/21650373.2012.727322
- Sonat C, Dung N, Unluer C. Performance and microstructural development of MgO–SiO2 binders under different curing conditions. Constr Build Mater. 2017;154:945–955. doi:10.1016/j.conbuildmat.2017.08.020
- Jia Y, Wang B, Wu Z, et al. Role of sodium hexametaphosphate in MgO/SiO2 cement pastes. Cem Concr Res. 2016;89:63–71. doi:10.1016/j.cemconres.2016.08.003
- Jin F, Al-Tabbaa A. Thermogravimetric study on the hydration of reactive magnesia and silica mixture at room temperature. Thermochim Acta. 2013;566:162–168. doi:10.1016/j.tca.2013.05.036
- Jia Y, Zou Y, Jiang Y, et al. Effect of a Ca-rich environment on the reaction process of the MgO-activated SiO2 system. Cem Concr Compos. 2023;136:104855. doi:10.1016/j.cemconcomp.2022.104855
- Peng Y, Unluer C. Investigation of the viscoelastic evolution of reactive magnesia cement pastes with accelerated hydration mechanisms. Cem Concr Compos. 2023;142:105191. doi:10.1016/j.cemconcomp.2023.105191
- Kumar S, Sonat C, Yang E-H, et al. Performance of reactive magnesia cement formulations containing fly ash and ground granulated blast-furnace slag. Constr Build Mater. 2020: 232. doi:10.1016/j.conbuildmat.2019.117275
- Dhakal M, Scott AN, Shah V, et al. Development of a MgO-metakaolin binder system. Constr Build Mater. 2021;284:122736. doi:10.1016/j.conbuildmat.2021.122736
- Sonat C, Unluer C. Development of magnesium-silicate-hydrate (M-S-H) cement with rice husk ash. J Clean Prod. 2019;211:787–803. doi:10.1016/j.jclepro.2018.11.246
- Zheng S, Zhou X, Xing W, et al. Analysis on the evolution characteristics of kaolin international trade pattern based on complex networks. Resources Policy. 2022;77:102783. doi:10.1016/j.resourpol.2022.102783
- Sabir B, Wild S, Bai J. Metakaolin and calcined clays as pozzolans for concrete: a review. Cem Concr Compos. 2001;23(6):441–454. doi:10.1016/S0958-9465(00)00092-5
- Siddique R, Klaus J. Influence of metakaolin on the properties of mortar and concrete: a review. Appl Clay Sci. 2009;43(3-4):392–400. doi:10.1016/j.clay.2008.11.007
- Shah V, Scott A. Hydration and microstructural characteristics of MgO in the presence of metakaolin and silica fume. Cem Concr Compos. 2021;121:104068. doi:10.1016/j.cemconcomp.2021.104068
- Shah V, Dhandapani Y, Scott A. Pore structure characteristics of MgO–SiO2 binder. J Am Ceram Soc. 2021;104(11):6002–6014. doi:10.1111/jace.17971
- Panda B, Sonat C, Yang E-H, et al. Use of magnesium-silicate-hydrate (M-S-H) cement mixes in 3D printing applications. Cem Concr Compos. 2021: 117. doi:10.1016/j.cemconcomp.2020.103901
- Peng Y, Unluer C. Understanding the rheological behavior of reactive magnesia-metakaolin system in the context of digital construction. Cem Concr Compos. 2024;149:105534. doi:10.1016/j.cemconcomp.2024.105534
- Yuan Q, Zhou D, Li B, et al. Effect of mineral admixtures on the structural build-up of cement paste. Constr Build Mater. 2018;160:117–126. doi:10.1016/j.conbuildmat.2017.11.050
- Yuan Q, Zhou D, Khayat KH, et al. On the measurement of evolution of structural build-up of cement paste with time by static yield stress test vs. small amplitude oscillatory shear test. Cem Concr Res. 2017;99:183–189. doi:10.1016/j.cemconres.2017.05.014
- Yuan Q, Lu X, Khayat KH, et al. Small amplitude oscillatory shear technique to evaluate structural build-up of cement paste. Mater Struct. 2017;50(2):1–12. doi:10.1617/s11527-016-0978-2
- Alejandre F, Flores-Ales V, Villegas R, et al. Estimation of Portland cement mortar compressive strength using microcores. Influence of shape and size. Constr Build Mater. 2014;55:359–364. doi:10.1016/j.conbuildmat.2014.01.049
- Joseph S, Unluer C. Effect of nanoparticles on the hydration of NaOH-activated GGBFS. J Am Ceram Soc. 2024;107(4):2196–2206. doi:10.1111/jace.19572
- Peng Y, Ma K, Unluer C, et al. Method for calculating dynamic yield stress of fresh cement pastes using a coaxial cylinder system. J Am Ceram Soc. 2021;104(11):5557–5570. doi:10.1111/jace.17979
- Qian Y, Kawashima S. Distinguishing dynamic and static yield stress of fresh cement mortars through thixotropy. Cem Concr Compos. 2018;86:288–296. doi:10.1016/j.cemconcomp.2017.11.019
- Perrot A, Lecompte T, Khelifi H, et al. Yield stress and bleeding of fresh cement pastes. Cem Concr Res. 2012;42(7):937–944. doi:10.1016/j.cemconres.2012.03.015
- Kruger J, Zeranka S, van Zijl G. An ab initio approach for thixotropy characterisation of (nanoparticle-infused) 3D printable concrete. Constr Build Mater. 2019;224:372–386. doi:10.1016/j.conbuildmat.2019.07.078
- Peng Y, Unluer C. Advances in rheological measurement and characterization of fresh cement pastes. Powder Technol. 2023;429:118903. doi:10.1016/j.powtec.2023.118903
- Mechtcherine V, Bos FP, Perrot A, et al. Extrusion-based additive manufacturing with cement-based materials–production steps, processes, and their underlying physics: a review. Cem Concr Res. 2020;132:106037. doi:10.1016/j.cemconres.2020.106037
- Chen M, Li H, Yang L, et al. Rheology and shape stability control of 3D printed calcium sulphoaluminate cement composites containing paper milling sludge. Addit Manuf. 2022;54:102781. doi:10.1016/j.addma.2022.102781
- Sonat C, Teo WW, Unluer C. Performance and microstructure of MgO-SiO2 concrete under different environments. Constr Build Mater. 2018;184:549–564. doi:10.1016/j.conbuildmat.2018.07.032
- Dung NT, Unluer C. Development of MgO concrete with enhanced hydration and carbonation mechanisms. Cem Concr Res. 2018;103:160–169. doi:10.1016/j.cemconres.2017.10.011
- Pillay DL, Olalusi OB, Kiliswa MW, et al. Engineering performance of metakaolin based concrete. Clean Eng Technol. 2022;6:100383. doi:10.1016/j.clet.2021.100383