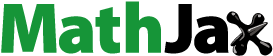
ABSTRACT
In this study, the complex aluminium nitride (AlN) components with performance comparable to those produced by conventional methods were fabricated through an improved additive manufacturing technique. The use of a novel surfactant (KMT3331) improved the dispersion of AlN powder in resin, enhancing the compatibility between the powder and the resin, resulting in a low-viscosity slurry with solid loading exceeding 60 vol.%. This approach improved the density and homogeneity of the green bodies, resulting in dense and microstructurally homogeneous AlN ceramics, as well as reduced the sintering shrinkage and grain size. Finally, by controlling oxygen impurities introduced from the debinding process, complex-shaped AlN ceramics with high thermal conductivity (184.56 ± 2.77 W·m−1·K−1), outstanding mechanical properties (bending strength of 458.09 ± 36.03 MPa, fracture toughness of 3.95 ± 0.26 MPa·m1/2) and high reliability (Weibull modulus of 14.89) were obtained, greatly broadening the prospect of AlN ceramics in advanced thermal management applications.
1. Introduction
The dynamic evolution of multi-chip components and high-power integrated circuits imposes stringent requirements on the miniaturisation, integration, and reliability of electronic devices [Citation1]. Hence, ensuring the prompt dissipation of heat is crucial for ensuring stable operation of circuits at temperatures consistently below 100°C [Citation2]. Aluminium nitride (AlN) ceramics find extensive applications as thermal dissipation substrate materials for integrated circuits [Citation3–5] and high-power light emitting diodes (LEDs) [Citation6–8]. This is attributed to their remarkable characteristics, including the thermal conductivity with the theoretical maximum of 320 W·m−1·K−1, dielectric performance, and mechanical properties.
To maximise the heat dissipation capability of aluminium nitride ceramic components, the latter are commonly crafted into intricate shapes or heat sinks featuring microchannels [Citation2,Citation9]. Nevertheless, the inherent hardness and brittleness of AlN ceramics make it challenging to achieve the necessary complex shapes through machining. Although conventional shaping methods (e.g. dry pressing [Citation8], tape casting [Citation10], slip casting [Citation11], gelcasting [Citation12], and powder injection molding [Citation13]) enable production of high-performance AlN ceramics, challenges have been faced in manufacturing complex AlN ceramic components, especially those with internal channel structures. Moreover, even though allowing for production of intricate structures, traditional shaping methods, such as gel casting and powder injection molding, require the pre-manufacture of molds, resulting in high costs, extended processing times, and the risk of losing details in the fabrication of complex components [Citation14]. Therefore, there has been an initiative to explore additive manufacturing technologies for achieving highly intricate shapes and precise AlN ceramic components.
Additive manufacturing (AM), especially digital light processing-based vat photopolymerization (DLP-based VPP), holds notable technological advantages for producing complex ceramic components by overcoming mold limitations and enabling the rapid, high-precision fabrication of ceramics with intricate geometries or interconnected channels [Citation15–18]. Currently, this AM technology is being widely applied in the manufacturing of ceramic materials, including alumina (Al2O3) [Citation9,Citation19,Citation20], zirconia (ZrO2) [Citation21–23], silicon carbide (SiC) [Citation24,Citation25], and silicon nitride (Si3N4) [Citation26–28]. Simultaneously, there are also relevant studies reporting the preparation of AlN ceramic using the DLP-based VPP process. For instance, Duan et al. [Citation29] optimised the sintering temperature for AlN ceramic fabricated through DLP-based VPP, presenting AlN components with a thermal conductivity of 155 W·m−1·K−1 and a bending strength of only 265 ± 20 MPa. Sheng et al. [Citation18] enhanced the curing performance and flowability of the AlN slurry through a powder coating strategy, ultimately producing AlN specimens with a thermal conductivity of only 144.11 W·m−1·K−1 and a bending strength of 400.07 ± 13.49 MPa. Moreover, Lin et al. [Citation30] examined the influence of the particle size of AlN powder on the rheological properties and curing behaviour of respective slurry. They attained a notable thermal conductivity of 174 W·m−1·K−1 via the production of 1.2 μm-sized AlN powder, yielding a low bending strength of 306.3 ± 6.5 MPa. For sintered AlN ceramics, there is a trade-off among bending strength and thermal conductivity, i.e. higher bending strength typically results in lower thermal conductivity, and higher thermal conductivity often leads to lower bending strength. This is mainly attributed to the fact that the bending strength of ceramics can be improved by refining the grain size; however, grain refinement enhances phonon scattering at grain boundaries, thus leading to a decrease in thermal conductivity [Citation31,Citation32]. However, for many critical commercial applications, there are demanding requirements for AlN ceramics for not only high thermal conductivity, but also high bending strength [Citation5,Citation33,Citation34]. In the above studies, it is worth noting that the solid loading in AlN ceramic slurries was below 55 vol.%, potentially reducing the performance of AlN ceramics produced through DLP-based VPP. Nevertheless, the performance of ceramics obtained via the top-down DLP printing by Gu et al. [Citation35] was comparable to traditionally formed Al2O3 ceramics due to the use of slurry with 60 vol.% solid loading. Besides that, Mu et al. [Citation36] have also suggested that the optimal slurry solid loading for DLP-formed ceramic cores is 60 vol.%. Moreover, from cost and environmental viewpoint in industry, it is crucial to minimise the use of organic substances in ceramic slurries, such as resin. Therefore, enhancing the solid loading (>60 vol.%) of AlN ceramic slurries is of great significance for DLP-based VPP.
In the DLP-based VPP process, low viscosity and high solid loading are crucial characteristics of the slurry. The former promotes the formation of a uniform and smooth coating [Citation2], while the latter helps prevent issues like layering [Citation37] and cracking [Citation38] during subsequent debinding and sintering. However, increasing solid loading while maintaining low viscosity has been challenging as the higher solid loading is associated with greater viscosity. Such high solid loading, high viscosity slurries can lead to agglomerations and bubbles during the DLP process, which can evolve into defects (such as delamination and pores), thereby compromising the mechanical properties of the material [Citation39,Citation40]. To address this issue, a polymeric surfactant is added to transform hydrophilic ceramic particles into hydrophobic ones. This modification, involving a hydrophobic anchoring head group and hydrophilic end chains, creates a steric barrier, ensuring uniform particle dispersion in the slurries [Citation41]. To date, surfactants such as oleic acid, stearic acid and silane coupling agents [Citation2,Citation42] have proven their effectiveness in increasing solid loading and reducing the viscosity of AlN slurry. However, due to limited compatibility of these surfactants with acrylate-based photosensitive resins, achieving solid loadings exceeding 50 vol.% remains challenging, potentially restricting the performance of 3D-printed AlN components. Additionally, Xu et al. [Citation43] found that acrylate-based surfactants can further enhance the wettability between the Al2O3 powder and resin. Therefore, in addition to functional groups, the compatibility of the surfactant with the chosen resin system is crucial for achieving a low-viscosity AlN slurry with a solid loading exceeding 60 vol.%, which is crucial for preparing high-density and homogeneous 3D-printed green bodies. In conventional colloidal processing methods, such as slip casting [Citation44] and gelcasting [Citation45], the homogeneity of green body significantly impacts the microstructure and final performance of the ceramics. However, this aspect has often been overlooked in previous studies on AlN ceramics obtained by DLP-based VPP.
In view of the above, this study aims to modify AlN powder with a novel acrylate-based surfactant (KMT3331) to enhance the wettability between the AlN powder and resin, thereby achieving a low-viscosity AlN slurry with a solid loading exceeding 60 vol.% for DLP-based VPP. Furthermore, the rheological property, stability, modification mechanism and curing behaviour of AlN slurries with various solid loadings were systematically analyzed. Simultaneously, the effects of the solid loading and viscosity of AlN slurry on the density and homogeneity of 3D-printed green bodies, as well as on the density, sintering shrinkage, performance, phase composition, and microstructure of the sintered bodies, were systematically discussed. Finally, a heating device was used to evaluate the heat dissipation capabilities of AlN components with various shapes.
2. Materials and experiments
2.1. Materials
The AlN raw powder (Grand JC, Toyo Aluminium, Japan) was employed in this work. SmF3 powder (99.9% purity, Shanghai Yuanye Bio-Technology Co., Ltd., China) was employed as a sintering additive. The mass ratio of the SmF3 to AlN powders was 5:95. Surface modification of AlN powder was carried out using silane coupling agent KH570 (Shanghai Yuanye Bio-Technology Co., Ltd., China) and acrylic acid-block copolymer KMT3331 (Foshan Kening New Material Ltd., China) as surfactants, respectively. The photosensitive resins consisted of ethoxylated pentaerythritol tetra acrylate (PPTTA, Royal DSM), 1, 6-hexanediol diacrylate (HDDA, Royal DSM), and dioctyl phthalate (DOP, Shanghai Macklin Biochemical Technology Co., Ltd., China). Moreover, phenyl phosphoric acid (819, Shanghai Guangyi Chemical Co., Ltd., China) was used as the photo-initiator, and its content was 2% of the mass of the photosensitive resin.
2.2. Experimental procedures
According to , AlN powder, SmF3 powder, surfactants, ZrO2 balls and anhydrous ethanol were put together in a ball milling jar, with the mass ratio of the powders, ZrO2 balls, and anhydrous ethanol being 2:2:1. Subsequently, the mixture underwent ball milling at a speed of 350 rpm for 6 h to achieve a thorough and uniform stirring. The blend was afterward dried using a rotary evaporator and subsequently sieved through a 300-mesh sieve to get the modified powder. Next, the photo-initiator, modified powder, and resins were ball-milled at 2500 rpm for 5 mins to produce the photosensitive AlN slurry.
Table 1. The mass ratio of each component in the photosensitive AlN slurry.
The pre-designed STL model files were imported into a stereolithography machine, and a printing layer thickness was set at 25 μm. The photosensitive AlN slurry was then exposed layer by layer to UV light with a wavelength of 460 nm and an intensity of 50 mW/cm² for curing. This resulted in the formation of AlN green bodies. Ultimately, the AlN green bodies underwent a two-step debinding process followed by sintering in an atmosphere furnace (ZT-90-22, Shanghai Chenhua Technology Co., Ltd., China) under a nitrogen atmosphere at 1850°C for 4 h. The details about specific debinding programs are described in the previous work [Citation2]. The solid loading of photosensitive AlN slurries was set at 50, 55, 60, and 65 vol.% (as shown in ). For comparison, the pre-mixed SmF3-AlN powder was formed by dry pressing followed by cold isostatic pressing at 200 MPa for 5 mins to obtained the dry-pressed green body.
2.3. Characterisation
The rheology of the photosensitive ceramic slurry was measured by a rotational rheometer (Anton Paar, MCR 301) at room temperature of 25°C. The sintered AlN specimens were processed into smooth and flat AlN sheets. Next, these sheets were immersed in an ethanol solution containing 5.0 wt.% surfactant, followed by drying in an oven to obtain modified AlN sheets. Using a contact angle measurement instrument (OCA100, Dataphysics, Germany), the contact angles between the AlN sheets modified with different surfactants and photosensitive resin were measured to investigate the wettability between the two materials. The stability of the slurry was evaluated by conducting sedimentation experiments involving a 5.0 vol.% slurry to assess the influence of various surfactant. The morphology of the AlN powder was observed via transmission electron microscopy (TEM; FEI Talos F200X). The characteristic groups in the AlN powder surface before and after modification with acrylic acid-block copolymer were examined through the FTIR analysis (Thermofisher, Nicolet IS50, USA). An ultraviolet–visible near-infrared spectrophotometer (UV-3700i, Shimadzu, Japan) was used to measure the UV-light absorbance of the AlN powder. The excess widths of single-layer printed specimens were measured by utilising a stereo microscope. A spiral micrometer was employed to determine the cure depths of the single-layer specimens, and the dimensions of the printed specimens were assessed before and after debinding and sintering. The pore size distribution of the debound green bodies was evaluated using a mercury porosimeter (AutoPore 9500, Micrometrics Instrument Co., USA), and the full width at half maximum (FWHM) of the pore size distribution was determined by fitting the data based on the Gaussian distribution function [Citation44,Citation45].
The XRD patterns of AlN specimens were obtained by an X-ray diffractometry (XRD, D8 Advance, Bruker Corporation) using Cu Kα radiation within the 2θ range of 20° to 90° at a scan speed of 3°/min. The XRD peak indexing was conducted using the HighscorePlus software. Additionally, the phase composition and crystal structure details of AlN specimens were determined with the Rietveld method using the FULLPROF program [Citation46]. Simultaneously, employing a mixture rule and considering the phase composition obtained through the Rietveld refinement, the theoretical densities of the specimens were calculated. The densities of the debound green bodies were determined by geometry, while the densities of the sintered AlN specimens were determined using the Archimedes’ method.
The thermal diffusivity () of the AlN specimen was established at 25°C by a laser conductometer (LFA 467, NETZSCH, Germany), and the thermal conductivity (
) was subsequently calculated as follows [Citation47]:
(1)
(1) where
is the bulk density, and
refers to the specific heat capacity. Here, the
value of AlN sample was calculated using the Neumann-Kopp rule, considering the mass fraction of different phases [Citation48].
Moreover, the sintered specimens were polished and performed thermal etching at 1550°C for 30 mins under in a nitrogen atmosphere [Citation9]. The morphologies of the fractured, polished and thermally etched surfaces of AlN specimens were examined via SEM (Lyra 3 XMU, Tescan). The mean grain size for each specimen group was determined by measuring over 250 grains on the thermally etched surfaces using the intercept method with a statistical correction factor of 1.56 [Citation49,Citation50]. In addition, the Christiansen uniformity coefficient () was employed to evaluate the grain size distribution uniformity in AlN ceramics as follows [Citation51,Citation52]:
(2)
(2) where
is the total number of grains,
refers to the i-th grain size, and
is the mean grain size. A greater
value signifies a more homogeneous microstructure in the matrix.
The bending strength of the sintered ceramics was determined via a three-point bending test on a universal testing machine. The specimens with dimensions of 25 mm × 2.0 mm × 1.5 mm were loaded at room temperature at a crosshead speed of 0.2 mm/min and a loading span of 20 mm. Meanwhile, the reliabilities of AlN specimens with solid loadings of 50 and 60 vol.% were characterised via the Weibull analysis, involving a minimum of 30 specimens, as described in Refs. [Citation53,Citation54]:
(3)
(3) where
represents the failure probability of the
-th ranked specimen;
refers to the rank of the bending strength data;
is the total number of tested specimens (in this work,
= 30);
denotes the Weibull modulus;
is the measured bending strength;
is the characteristic strength [Citation53]. The fracture toughness of specimens was determined via single-edge notched beam (SENB) testing [Citation46]. The SENB specimens, measuring 35 mm × 3.0 mm ×4.0 mm with a notch width of 150 μm, were loaded at room temperature at a crosshead speed of 0.2 mm/min and a loading span of 30 mm, and the values obtained represented the mean results over at least 6 specimens.
3. Results and discussion
3.1. Characterisation of the ceramic slurries
To validate the modifying effect of surfactant KMT3331 on AlN powder, the rheological analysis was conducted on the photosensitive AlN ceramic slurries, as shown in (a). It can be observed that, at a content of 1 wt.%, both surfactants significantly reduced the viscosity of AlN ceramic slurry. Therefore, the modified AlN slurries achieved the desired level of viscosity (close to 3 Pa·s) even at a solid loading of over 50 vol.%, while the unmodified AlN slurry exhibited considerably high viscosity (7.73 Pa·s) at 30 vol.% solid loading and a shear rate of 35 s−1. It is noteworthy that the KMT3331-modified slurry displayed Newtonian fluid behaviour, i.e. it maintained consistent viscosity despite an increase in solid loading from 50 to 65 vol.%. Moreover, the KMT3331-modified slurry with 60 vol.% solid loading demonstrated a viscosity of only 6.21 Pa·s at a shear rate of 35 s−1, which was still lower than that of unmodified AlN slurry with 30 vol.% solid loading. In contrast, the KH570-modified ceramic slurries with 50 and 55 vol.% solid loadings displayed shear-thickening characteristics, which were proved to be detrimental to the uniform recoated layer during the printing process. Furthermore, the viscosity of the KH570-modified slurry with a 50 vol.% solid loading was 8.64 Pa·s at the shear rate of 35 s−1, being higher than that of the KMT3331-modified slurry with 60 vol.% solid loading.
Figure 1. (a) Rheological curves of the photosensitive AlN ceramic slurries with different surfactants; (b) relationship curves between the relative viscosity of AlN ceramic slurries and the solid loading along with the corresponding Einstein coefficient () and maximum solid loading (
) (the curve fitting is performed using the Krieger-Dougherty model); (c) rheological curves of modified slurries with KMT3331 contents ranging from 1 to 3 wt.%; (d) image of the unmodified slurry with 30 vol.% solid loading; (e-g) images of the KMT3331-modified slurries with solid loadings of 55, 60, and 65 vol.%.

To elucidate the correlation between viscosity and solid loading after modification with different surfactants, the experimental data were fitted using the Krieger-Dougherty model as follows [Citation55–57]:
(4)
(4)
where ,
, and
represent relative viscosity, ceramic slurry viscosity, and dispersant medium viscosity, respectively.
is the Einstein coefficient,
denotes the solid loading of the slurry, and
indicates the maximum solid loading.
(b) depicts the relationship curves between the relative viscosity of AlN ceramic slurries and solid loading, along with the corresponding Einstein coefficient () and maximum solid loading (
) values, fitted using the Krieger-Dougherty model. Notably, all curves exhibited satisfactory goodness-of-fit R2 parameters, exceeding 0.96. In the case of the unmodified slurry,
and
values were 6.6706 and 0.4710, respectively, while those of the KH570-modified slurry were 5.1698 and 0.6675. In contrast, the KMT3331-modified slurry boasted the lowest
value at 4.1412 in coupling with an impressive maximum solid loading (
) of 0.7575. Taking the interface compatibility into account, the hydrophobic groups in KMT3331 mainly consist of acrylic ester groups. These exhibit excellent compatibility with acrylate-based resin featuring the same type of groups. In contrast, the hydrophobic groups of KH570 consist of siloxane and alkane structure, exhibiting the lower compatibility with resin compared to KMT3331. To validate this, AlN sheets containing 5.0 wt.% SmF3 were prepared through sintering, and their contact angles (CA) with photosensitive resin were measured under the modification of various surfactants, as illustrated in . Compared to the unmodified AlN sheets, the contact angles between the modified AlN sheets and the resin noticeably decreased. Among them, the AlN sheets modified with KMT3331 exhibited the smallest contact angles (approximately 17.1° and 17.4° on the left and right, respectively), which indicates a significant improvement in wettability and compatibility between KMT331-modified AlN sheets and resin. Such improvement in wettability and compatibility, which can significantly reduce the viscosity of ceramic slurries at high solid loading and prevent their shear thickening behaviour [Citation18,Citation58], may favour to maintaining the Newtonian fluid characteristics of the KMT3331-modified slurries (as shown in (a)). Consequently, the KMT3331-modified slurry demonstrates the enhancement in flowability, maintaining excellent flow characteristics even with a solid loading as high as 65 vol.%.
Figure 2. The contact angle (CA) of the photosensitive resin on the AlN sheets modified with various surfactants.
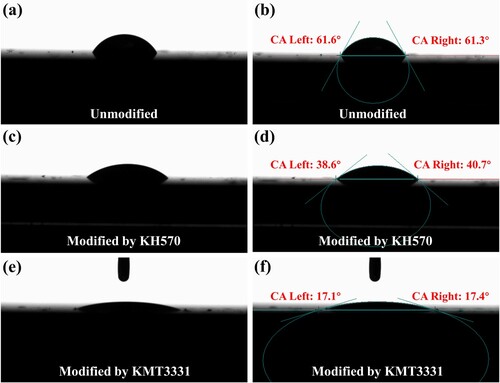
To further ascertain the optimal addition amount of KMT3331, (c) depicts the rheological curves of slurries modified by different amounts of KMT3331. The results indicated a substantial increase in slurry viscosity when the surfactant concentration exceeded 1 wt.%. This may be attributed to excessive free surfactant organic molecules in the slurry, causing the entanglement between them and resulting in both aggregation and elevated viscosity [Citation59]. (d–g) depicts the unmodified slurry with a 30 vol.% solid loading and KMT3331-modified slurries with solid loadings of 55, 60, and 65 vol.%. It was observed that the unmodified slurry exhibited poor fluidity even at only 30 vol.% solid loading, which hindered the uniform coating of the slurry during the printing process. In contrast, the KMT3331-modified slurry, even with a solid loading as high as 65 vol.%, maintained excellent flowability, facilitating efficient and homogeneous recoating of printing layers [Citation43] and thereby enhancing the quality of printed green bodies.
Given the relatively small thickness of the photocured ceramic layer (about 20 μm), a prolonged laminating process may lead to the bending of the cured layer due to the sedimentation of suspended particles [Citation60]. Therefore, it is crucial to keep the stability of the ceramic slurry and prevent sedimentation during the DLP-based VPP. To assess this, sedimentation experiments were conducted using a 5.0 vol.% slurry to evaluate the stability of the material by recording the change in sedimentation height of the ceramic slurry over 0–14 days (see ). Compared to the slurry prepared using the unmodified powder, those modified with KH570 and KMT3331 exhibited excellent stability. From (d), it was clear that the sedimentation heights of slurries modified with KH570 and KMT3331 remained stable after 6 days, while that of the unmodified powder slurry decreased noticeably within the 0–14 days. Considering the rheological properties and stability measurements, the acrylic acid-block copolymer KMT3331 demonstrated superior surface modification compared to the silane coupling agent KH570, enhancing the characteristics of AlN slurries for the DLP-based VPP.
3.2. Characterisation of modified AlN powder
To elucidate the mechanism underlying the modification of AlN powder by KMT3331, the TEM was employed to scrutinise the surface morphology of the AlN powder. (a–b) and (c–d) depict the TEM images of AlN powders before and after modification with KMT3331, respectively. The crystal lattice arrangement is clearly visible on the surfaces of both the unmodified and KMT3331-modified AlN powders, as depicted in (b,d). Furthermore, an amorphous layer with a thickness of 3.54 nm was detected at the edge of the AlN powder modified with KMT3331. From the high-angle annular dark field (HAADF)-TEM photographs and energy dispersive spectroscopy (EDS) maps (see (e–i) and (j–n)), the composition of this layer could be broadly deduced. In contrast to the unmodified AlN powder, the concentrations of C and O elements at the edges of the KMT3331-modified AlN powder were notably higher. (o–p) depict the EDS spectra, showing that the powders predominantly consisted of Al, N, O, and C elements. Moreover, the peak intensity associated with O and C elements increased in the KMT3331-modified powder, indicating a higher concentration of those elements. Therefore, the above microscopic characterisation results suggested that the amorphous layer at the edge of the KMT3331-modified powder might have consisted of C and O elements.
Figure 4. TEM images of (a-b) unmodified AlN powder and (c-d) AlN powder modified with KMT3331. HAADF-TEM photographs and EDS maps of Al, N, C, and O elements in (e-i) unmodified and (j-n) KMT3331-modified AlN powder. Energy spectrum analysis of (o) unmodified and (p) KMT3331-modified AlN powders.
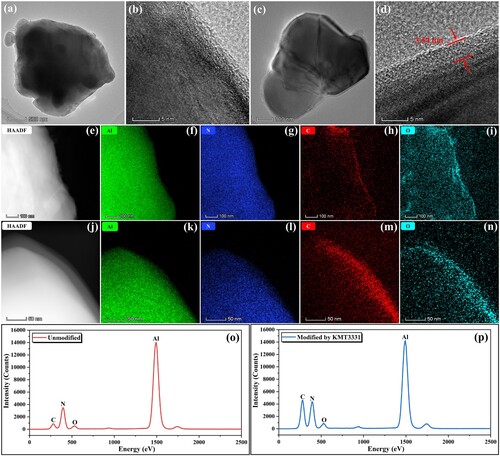
To examine the surfactant adsorption of AlN powder, the functional groups on its external surfaces were characterised via the FTIR analysis. (a) illustrates the FTIR spectra of KMT3331, unmodified AlN powder, and KMT3331-modified AlN powder. The assignment of the primary characteristic infrared absorption peaks is presented in . In all cases, the hydroxyl groups (O-H) are identified at 3480 cm−1. The presence of these groups in unmodified and modified AlN powders suggests water absorption on the AlN surface [Citation2]. In contrast to the unmodified AlN powder, the KMT3331-modified AlN one exhibited several additional bands, including CH2-CH3 (2920 cm−1), C = C (1640cm−1), COO- (1460 cm−1), and C–O (1250 and 1100 cm−1) [Citation2,Citation43,Citation61,Citation62]. The carbon double bonds (C = C) in both KMT3331 and KMT3331-modified powder originate from acrylic acid, giving them good affinity with HDDA resin, which also contains C = C bonds [Citation59]. These results confirmed that the acrylic acid-block copolymer KMT3331 was successfully absorbed onto the surface of AlN powder, and this adsorption might have been associated with the hydrogen bonding due to the O-H and O stretching vibrations. Based on this assumption, the hydrophobic groups of KMT3331 were grafted onto the surface of AlN powder, thereby reducing collisions between AlN powder particles and promoting their uniform distribution in the photosensitive resin (see (b)). Consequently, the viscosity of the AlN ceramic slurry was effectively decreased, while also avoiding shear thickening, thereby maintaining its Newtonian fluid properties. Moreover, (c) also shows the absorbance of different AlN powders. The KMT3331-modified AlN powder had a higher absorbance of UV light at 460 nm than the unmodified powder (0.26 versus 0.13), which is similarly to the KH570-modified powder (0.30). This mainly due to the above two surfactants contains an unsaturated carbon double bond (C = C) with a UV-light absorbance wavelength of approximately 400 nm [Citation2,Citation59].
Figure 5. (a) The FTIR spectra of the KMT3331, unmodified AlN powder, and KMT3331-modified AlN powder. (b) Illustration of the surface modification mechanism of AlN with KMT3331. (c) Absorbance of different AlN powders.
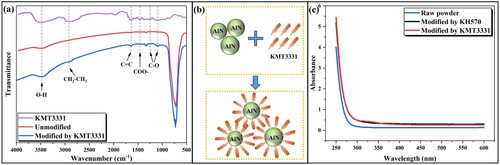
Table 2. The assignment of the primary characteristic infrared absorption peaks.
3.3. Cure behaviour of slurry
Given the combined advantages of higher solid loading, reduced sedimentation rate and lower viscosity, KMT3331 was proved to be an ideal surfactant for the photosensitive AlN ceramic slurries. Thus, the well-dispersed KMT3331-modified AlN slurries with varying solid loading were prepared for the DLP printing process. However, another key characteristic in ceramic stereolithography lies in the curing capacity of AlN ceramic slurries. Therefore, to obtain strong adhesion between individual layers, the curing behaviours of KMT3331-modified AlN slurries with various solid loadings were afterward examined. In accordance with the principles of the Beer–Lambert model, the cure depth () can be expressed is described as [Citation63]:
(5)
(5) where
is the depth sensitivity,
is the incident energy, and
is the critical energy. Besides, the excess width (
) is similarly formulated as [Citation64]:
(6)
(6) where
is the width sensitivity, and
is the critical energy in the width direction.
In (a,b), the cure depth () and excess width (
) of KMT3331-modified AlN slurries are depicted as functions of exposure time. With an increase in exposure time, both the values of
and
in all AlN slurries showed an increasing trend; whereas, the curing efficiency of AlN slurries declined as the increase in solid loading. To further understand the relationship between
and
, the various parameters of ceramic slurries with different solid loading were further analyzed (see ). It was found that
varied from 12.02 to 10.64 µm, and
decreased from 74.3 to 68.3 µm as the solid loading rose from 50 to 65 vol.%, respectively. Meanwhile, the
and
values increased from 7.51 to 8.46 mJ/cm2 and from 49.22 to 51.89 mJ/cm2, respectively. This is mainly attributed to two factors. First, the increased solid loading hinders photopolymerization due to a decrease in photosensitive resin content in the ceramic slurry [Citation2]. Second, as the solid loading rises, there is a higher concentration of ceramic powder particles per unit volume. However, a large portion of UV light gets scattered and absorbed by the AlN powder, causing a substantial attenuation of the incident UV light within the slurry [Citation2,Citation18]. Consequently, the curing process became more difficult, resulting in a decrease in both
and
, while
and
increased.
Figure 6. (a) Cure depth and (b) excess width of KMT3331-modified AlN slurries with different solid loadings.
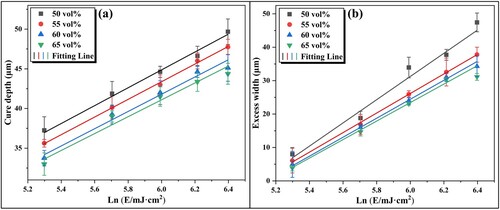
Table 3. Sensitivity of depth () and width (
) along with critical energy of depth (
) and width (
) in AlN ceramic slurries with various solid loadings.
3.4. Density and sintering shrinkage of the printed ceramics
To comprehensively understand the impact of solid loading and viscosity of slurry on the density and homogeneity of green body, the pore size distribution of the AlN green bodies obtained by DLP-based VPP and dry pressing was evaluated using a mercury porosimeter (see and ). At a solid loading of 50 vol.%, the measured mean pore size of the KH570-modified green body is comparable to that of the KMT3331-modified green body; however, the former has a larger cumulative pore volume and FWHM value, indicating that the latter is denser and more homogenous than the former. This is mainly due to the lower viscosity of the KMT3331-modified slurry (as shown in (a)), which has better self-leveling properties, facilitating efficient and homogeneous recoating of printing layers and thereby enhancing the quality of printed green bodies [Citation2,Citation43,Citation61]. As the solid loading increased, both the cumulative pore volume and the measured mean pore size decreased, indicating that the density and homogeneity of the green bodies were improved as the escalating solid loading of the slurry. Specifically, as the solid loading rose from 50 to 65 vol.%, the density of KMT3331-modified green body rose from 1.71 to 2.13 g/cm3 (the respective relative densities rose from 51.19% to 64.01%). In addition, the cumulative pore volume and measured mean pore size of green bodies prepared by dry pressing are higher than those of KMT3331-modified green bodies with solid loadings of 60 and 65 vol.%. Meanwhile, their relative density (only 57.98%) is lower than the latter two, indicating that the density and homogeneity of green bodies with solid loadings of 60 and 65 vol.% are superior to those of dry-pressed green bodies. As the high-density and homogeneous green body facilitates the achievement of high-quality ceramics [Citation45]. Therefore, with using the same sintering additives, the AlN ceramics prepared from KMT3331-modified slurries with solid loadings of 60 and 65 vol.% in this study exhibit better performance than those obtained by dry pressing in the Ref. [Citation46].
Figure 7. Pore size distribution of AlN green bodies obtained by DLP and dry pressing: (a) cumulative intrusion and (b) incremental intrusion
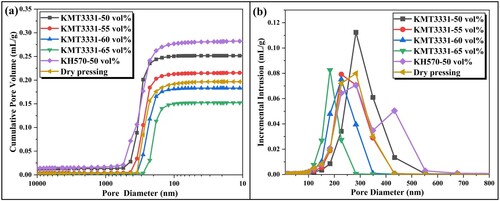
Table 4. Pore size distribution and density of AlN green bodies obtained by DLP-based VPP and dry pressing.
Moreover, Ceramic slurries with high solid loading for stereolithography purposes are expected to demonstrate enhanced mechanical performance and reduced sintering shrinkage [Citation65]. revealed density and relative density, as well as the linear shrinkage of the sintered AlN specimens with varying solid loadings. All sintered specimens achieved nearly complete densification whereby the relative density remained above 99%. Furthermore, the green bodies with higher solid loading demonstrated the increase in sintered densities, reaching a maximum of 3.32 g/cm3 (relative density of 99.70%) at 60 vol.%. The linear shrinkage decreased with the rise in solid loading, and the linear shrinkage in the Z-direction exceeded that in the X and Y directions. In the stereolithography process, the separation of the cured layer and release film introduced tension into the green body, resulting in reduced interlayer bonding and increased shrinkage rate in the vertical direction (Z) compared to the other two directions [Citation66]. Remarkably, as solid loading rose from 50 to 65 vol.%, the linear shrinkage rates in the X, Y, and Z directions decreased from 19.16%, 19.22%, and 22.33% to 13.69%, 13.74%, and 14.72%, respectively. Moreover, the linear shrinkage rate in the Z-direction gradually approached those in the other two directions. The increase in solid loading of slurry was proved to be advantageous for the reduction in the shrinkage rate of the sintered AlN component, facilitating the shrinkage uniformity in all directions and preserving the original geometric shape.
Table 5. The density and relative density, as well as the linear shrinkage of the sintered AlN specimens with varying solid loading.
To explore the influence of solid loading on the internal structure of green bodies, the SEM was utilised to observe their fracture morphology after heat treatment. displays the SEM images in which yellow circles denote pores. As shown in (a–d), cracks appeared at the joints between the layers on the fracture surface of heat-treated body with 50 vol.% solid loading. The cracks, however, gradually decreased and even disappeared with the increase in solid loadings to 60 vol.% or more. The formation of cracks seems to result from the weaker interlayer bonding in green bodies with lower solid loading, leading to the vertical propagation of cracks along the areas with a weaker interlayer bonding. Furthermore, as the solid loading rose, both size and quantity of internal pores in the heat-treated bodies decreased (see (e–h)), i.e. a higher solid loading of slurry led to the increase in green body density, which was consistent with data in . Therefore, considering the debound and sintered densities, sintering shrinkage, and the fracture morphology of green bodies, it can be concluded that slurries with high solid loading exhibit the enhancement in the initial and sintered densities and interlayer bonding strength, the reduction in internal defects, and the minimum sintering shrinkage, which coincides with previous findings [Citation2,Citation65].
3.5. Phase composition and microstructure of sintered AlN ceramic
To illustrate the phase evolution of AlN specimens with different solid loadings after sintering, the XRD analysis was conducted, and the quantitative phase composition and crystal structure information were obtained through the Rietveld refinement (see ). All sintered ceramic specimens were predominantly composed of SmAlO3 and AlN, with no other phases detected. During the sintering, the SmAlO3 phase predominantly emerged from the reaction between the sintering additive SmF3 and the Al2O3 layer in the AlN powder, resulting in the removal of impurity oxygen and densification of AlN ceramic [Citation46].
Figure 9. (a) XRD patterns of sintered AlN specimens with varying solid loading and corresponding Rietveld refinement results: (b) 50 vol.%, (c) 55 vol.%, (d) 60 vol.%, and (e) 65 vol.%.
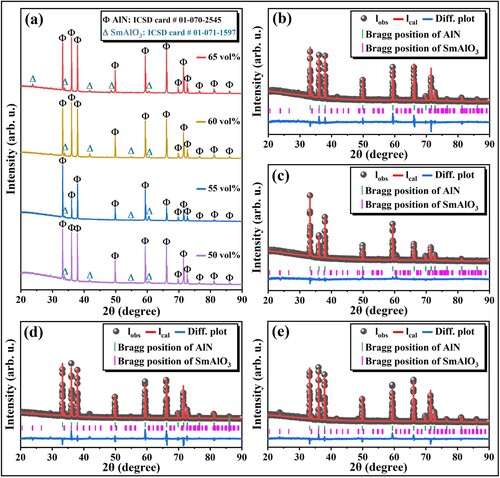
Moreover, the c-axis lattice parameters, several R-factors (Rwp, Rp, and Rexp), goodness-of-fit values (χ2) and phase compositions of AlN specimens are listed in . Based on the various R-factors and goodness-of-fit results (χ2), the calculated XRD profiles of all sintered specimens displayed the good agreement with the experimental XRD patterns of the corresponding phases, as depicted in (b–e). In addition, c-axis lattice parameter is a crucial indicator for analyzing oxygen impurity content in the AlN lattice, as it decreases due to the formation of lattice contraction resulting from the dissolution of oxygen [Citation67]. Thus, the c-axis lattice parameters of AlN specimens increased with the rise in solid loading, indicating that the higher solid loading corresponded to the lower lattice oxygen levels. This may be attributed to the high green density of AlN specimens with high solid loading, which decreases the contact area between AlN powders and air during the debinding process and reduces the degree of oxidation on the surface of AlN powder. In addition, the content of the SmAlO3 phase slightly decreases with the increase in solid loading, likely due to a reduction in oxygen content within the AlN specimens, which corroborates the above speculation.
Table 6. The c-axis lattice parameters, R-profiles (Rp), weighted R-profiles (Rwp), R-expected values (Rexp), goodness-of-fit (χ2), and phase compositions of sintered AlN specimens.
To investigate the influence of varying solid loading on the microstructure of AlN specimens, their fracture morphologies and thermally etched surfaces were observed at various magnifications, and the grain size distributions were then depicted (see ). Upon examination of the low-magnification SEM images ((a–d)), all specimens were almost fully densified with an absence of pores, which was consistent with the relative density data in . Meanwhile, as the solid loading increased, there was a gradual reduction in the number of larger grains (exceeding 10 μm) within the specimens. (i–l) also revealed a decrease in the mean grain size of the specimens from 10.11 ± 4.11 μm to 6.68 ± 2.04 μm as the solid loading rose from 50 to 65 vol.%. This trend indicates that the mean grain size of the AlN specimens decreases with increasing solid loading, which aligns with Lin's earlier findings [Citation2]. Additionally, Yin et al. [Citation68] observed the same phenomenon during the sintering process of Si3N4. This might be attributed to the occurrence of a liquid phase upon the sintering of AlN ceramics, in which grain growth is primarily governed by the solution-diffusion-reprecipitation mechanism, whereby small particles dissolve, diffuse, and then precipitate to occupy the pores, contributing to densification [Citation2]. Therefore, the AlN specimens with low solid loading, featuring a small density of green body and a high internal porosity (see ), provide the additional space for the abnormal grain growth during the sintering. Moreover, the sintered AlN specimens with high solid loading typically exhibited the higher CU values: the maximum CU value of 0.77 was achieved in the specimen with 65 vol.% solid loading, implying that its microstructure was exceptionally uniform. The above findings suggested that high solid loading could reduce the abnormal grain growth and improve the microstructure uniformity in AlN ceramic, which is a crucial aspect for improving the performance of the material [Citation9].
Figure 10. SEM images of fracture morphologies, thermally etched surfaces and corresponding grain size distributions within specimens with (a, e, i, m) 50 vol.%, (b, f, j, n) 55 vol.%, (c, g, k, o) 60 vol.%, and (d, h, l,p) 65 vol.% solid loadings; The large grains are highlighted with yellow arrows, and the white and gray particles correspond to SmAlO3 phase and AlN grains, respectively.
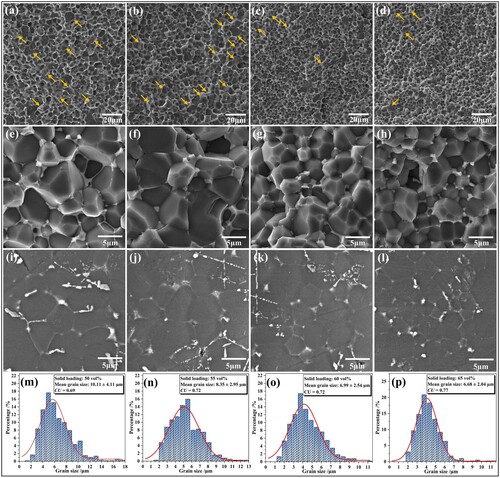
Furthermore, the morphology and distribution of SmAlO3 phases exhibited variations among sintered AlN specimens with different solid loadings (see (e–h)). In the sample with 50 vol.% solid loading, the SmAlO3 phase primarily grew along the grain boundary, presenting interconnected and elongated shape and thereby separating more AlN grains. Meanwhile, as the solid loading rose, the SmAlO3 phase became isolated and fine, occupying the triple AlN grain boundaries, i.e. the grain boundaries in specimens with high solid loading were cleaner. This was primarily attributed to the existence of larger pores within the interior of AlN specimens with low solid loading (see (e)), in which the liquid phase was subsequently aggregated during the sintering. Finally, in the later stages of AlN grain growth, the aggregated liquid phase underwent compression, resulting in the development of elongated and interconnected secondary phases. depicts the SEM images of the polished surfaces of sintered AlN specimens with varying solid loading. Here, some visible defects are mainly due to the pull-out of AlN grains or SmAlO3 particles during polishing. Since the density of the sintered bodies exceeds 99% (as shown in ), and no significant pores were observed in the above SEM images of the fracture surfaces. Nevertheless, it was evident that with an increase in solid loading from 50 to 65 vol.%, the SmAlO3 phase became noticeably finer and more isolated, thereby further confirming the earlier speculation.
3.6. Thermal and mechanical performance of ceramic components
To investigate the influence of varying solid loadings on the performance of the printed AlN specimens, (a) shows the thermal diffusivities and thermal conductivities of the sintered AlN specimens. These parameters of the specimens increased with the solid loading increase from 50 to 65 vol.%, exhibiting a trend completely opposite to that of the mean grain sizes in (m–p). Among them, the AlN specimens with solid loadings of 60 and 65 vol.% possessed thermal conductivities of 184.56 ± 2.77 W·m−1·K−1 and 186.18 ± 2.32 W·m−1·K−1, being 8.14% and 9.09% greater than those of the specimen with 50 vol.% solid loading, respectively. These findings demonstrate that the thermal properties of AlN ceramics are influenced not only by the grain size but also by a combination of grain size, relative density, lattice oxygen content, and secondary phase distribution, which agrees with the previous work [Citation46]. Typically, the thermal properties of AlN ceramics rely on the phonon propagation; therefore, the presence of pores, secondary phases, and lattice oxygen can induce phonon scattering, leading to a reduction in thermal conductivity [Citation69–71]. Therefore, sintered AlN specimens with elevated solid loadings exhibit the higher degree of densification and the larger c-axis lattice constants, i.e. the lower lattice oxygen content (see ), which enhance thermal conductivities of the former. Additionally, since the enlargement in the contact between AlN grains effectively enhanced the heat transfer capability of AlN ceramic [Citation46,Citation72], the presence of the isolated and fine SmAlO3 phase in AlN specimens with high solid loadings was more advantageous for the increase in the contact between AlN grains (see (e–h) and ), thereby improving thermal conductivities of the materials.
Figure 12. (a) Thermal and (b) mechanical properties of sintered specimens. (c)Weibull plots reflecting the bending strength (σf) of sintered AlN specimens. (d) A comparison of thermal and mechanical properties of AlN specimens prepared in this work with those reported in previous studies. Printed AlN ceramic components based on a slurry with 60 vol.% solid loading: (e, g) green bodies and (f, h) sintered bodies.
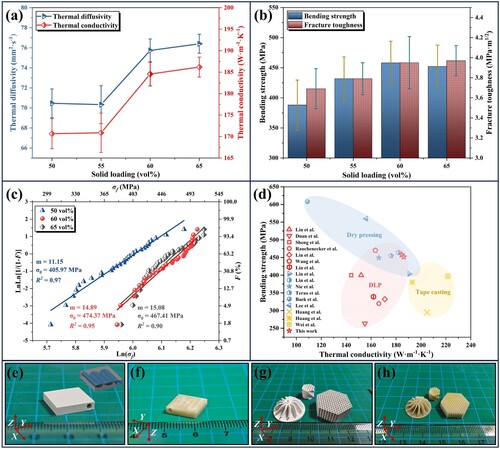
Table 7. Mean grain size, fracture toughness, transgranular fracture fraction (), and fracture toughness of grain (
) and grain boundary (
) of sintered AlN specimens.
As depicted in (b), the mechanical properties of AlN specimens, including bending strength and fracture toughness, initially showed an upward trend followed by stabilisation with the elevation in solid loading. The maximum bending strength and fracture toughness values (458.09 ± 36.03 MPa and 3.95 ± 0.26 MPa·m1/2, respectively) were attained at 60 vol.% solid loading, being 18.05% and 7.05% higher than those of the specimens with 50 vol.% solid loading. Here, the bending strength and fracture toughness of the AlN specimens with 65 vol.% solid loading are 452.18 ± 35.38 MPa and 3.97 ± 0.15 MPa·m1/2, respectively, closely resemble those of the specimens of 60 vol.% solid loading. This similarity may stem from the extremely close density and mean grain size of the sintered bodies in both groups of specimens (see and ).
According to linear fracture mechanics, the following relationship exists between the bending strength (), fracture toughness (
) and the critical defect size (
) of a brittle material [Citation5,Citation73]:
(7)
(7) where
represents a geometric constant that relies on the specimen size and loading geometry. Since the strength and toughness of the material are positively and negatively correlated with the grain size, the strengthening of AlN specimens with high solid loading is due to the enhancement of fracture toughness. Meanwhile, with the elevation in solid loading, the grain size of AlN specimens became finer and more uniform (see ), contributing to the mechanical properties of AlN ceramics. Besides, previous researches have revealed that isolated secondary phases reinforce the grain boundaries by introducing compressive stress therein, while interconnected secondary phases induce tensile stress, weakening the interfacial bonding strength between secondary phase and AlN matrix [Citation8,Citation74,Citation75]. Therefore, the isolated and fine secondary phases in the specimens with high solid loading, as confirmed by the microstructure patterns of the AlN specimens ((e–h) and ), contributed to the grain boundary reinforcement of AlN ceramic, thereby improving its fracture toughness.
To further confirm the above toughening mechanism of sintered AlN specimens, the fracture toughness values of the grain () and grain boundary (
) were calculated for AlN grains by applying the theory of stochastic analysis along the crack path of polycrystalline ceramics based on the difference between the energies released during the crack propagation, as follows [Citation5,Citation46,Citation73,Citation76]:
(8)
(8)
(9)
(9)
(10)
(10)
(11)
(11)
(12)
(12) where
refers to the critical grain size;
is the crack length (it is set to 100 μm based on the Ref. [Citation73]);
is the length of the selected intergranular fracture region;
and
are the constants;
represents the transgranular fracture fraction, obtained through the statistical analysis of the fracture modes of at least 200 grains (see ). The
value was calculated using Irwin’s equation as follows [Citation46,Citation73]:
(13)
(13) where the Poisson’s ration (
) and the elastic modulus (
) for AlN ceramic were set to 0.25 and 308 GPa, respectively [Citation5,Citation46,Citation77]. Thus, the values of
and
can be obtained from Eqs. (8)–(12), as shown in . Both the
and
parameters increased with the increase of solid loading. It is considered that a high level of oxygen can cause more lattice defects (e.g. dislocation and stacking faults) inside AlN grains, and the defects can make AlN grains weak [Citation5,Citation73,Citation78]. According to the XRD analysis, specimens with high solid loading have lower internal oxygen content, resulting in greater toughness of AlN grain (
). Meanwhile, the distribution of secondary phases (SmAlO3) in specimens with high solid loading is finer and more isolated (see ), which facilitates the introduction of residual compressive stress at grain boundaries, thereby reinforcing the grain boundaries and enhancing the mechanical properties [Citation5,Citation8,Citation73]. The increase in
indicated strengthening of grain boundaries, which confirmed the reinforcing effect of the grain boundaries caused by the isolated and fine secondary phases.
Furthermore, the reliability analysis was performed by computing the Weibull modulus () of the bending strength distribution for a dataset of at least 30 specimens [Citation53]. A higher value of
indicates better uniformity in bending strength and higher reliability of the ceramic. The Weibull plots for the bending strength of AlN specimens are depicted in (c). The specimens with higher solid loading (60 and 65 vol.%) exhibit superior Weibull modulus (
) and characteristic strength (
) compared to the specimen with 50 vol.% solid loading. The
and
of the specimen with 60 vol.% solid loading are 14.89 and 474.37 MPa, respectively, being 33.54% and 16.85% higher than those with 50 vol.% solid loading. In addition, the
of the AlN specimen with 65 vol.% solid loading is 15.09, slightly higher than those of 60 vol.% solid loading, indicating greater reliability, which is related to its more uniform microstructure (see ). This means that the KMT3331-modified slurry with higher solid loading (This means that the KMT3331-modified slurry with higher solid loading (≥ 60 vol.%) maintains good flowability, thereby effectively improving the density and homogeneity of the printed green body, 60 vol.%) maintains good flowability, thereby effectively improving the density and homogeneity of the printed green body, which in turn enhances the mechanical properties and reliability of the sintered AlN ceramics through enhanced distribution uniformity of grains and secondary phases, as confirmed by the above microstructural analysis.
To highlight the advantages of the DLP-based VPP with high solid loading, the properties of AlN specimens prepared in this study were compared with those reported in other studies (see (d)). Additionally, (d–e) illustrate the AlN ceramic components prepared through the VPP-based additive manufacturing, including a heat spreader with the internal channel structure, an impeller, and two types of honeycomb ceramics. In this research, the AlN specimens with solid loadings of 60 and 65 vol.% possessed a remarkably high thermal conductivity (184.56 ± 2.77 W·m−1·K−1 and 186.18 ± 2.32 W·m−1·K−1, respectively) and bending strength (458.09 ± 36.03 MPa and 452.18 ± 35.38 MPa, respectively). These values significantly exceeded those reported for materials produced via the DLP-based VPP (below 171 W·m−1·K−1 and 400 MPa, respectively) [Citation2,Citation18,Citation29,Citation30,Citation79]. In a previous study by Wang et al. [Citation80], internal cracks in 3D-printed preforms were effectively reduced by increasing the resin refractive index and using dibutyl phthalate (DBP) as a plasticizer. They successfully fabricated AlN ceramics with a slightly higher flexural strength (470.39 MPa) compared to this work, but with a much lower thermal conductivity (163.45 W·m−1·K−1). However, according to the latest study by Lin et al. [Citation81], they successfully coated yttrium nitrate on the surface of AlN powder through a ball-milling method. This effectively reduced the viscosity of the AlN slurry and increased its curing depth, but the thermal conductivity of the printed AlN ceramics was still only 162 W·m−1·K−1, and the bending strength was only 339 MPa. Thus, the specimens analyzed in the present work can be positioned as highly competitive even when compared to those obtained through conventional shaping methods such as dry pressing [Citation5,Citation6,Citation8,Citation46,Citation73,Citation82] and tape casting [Citation7,Citation10,Citation83].
As depicted in (a), a thermal evaluation device was designed to assess the heat dissipation capacity of the AlN component. The heater consisted of an alumina ceramic heating plate and copper wires, and silicone grease was employed to connect the ceramic heat spreader and the heater. (b–e) depict the schematic diagrams of the thermal evaluation device without any ceramic heat spreader installed and with AlN ceramic heat spreaders with plate shape, inner channel shape, and fin shape. The installation comprising the inner channel-shaped ceramic heat spreader is illustrated in (f–g). At the beginning of the heating, the channels of the heat spreader were pre-filled with a constant-temperature (approximately 20.0°C) water that was fed at a flow rate of 3 mL/min.
Figure 13. (a) Schematic diagrams of the thermal evaluation device to assess the heat dissipation capacity of the AlN ceramic component. The thermal evaluation device (b) without any ceramic heat spreader and (c-e) with three different types of AlN ceramic heat spreaders. (f-g) Photos of the thermal evaluation device with the inner channel shape ceramic heat spreader; (h) infrared thermal images of the heat source with different heat spreaders; (i) surface temperature of the heater versus time.
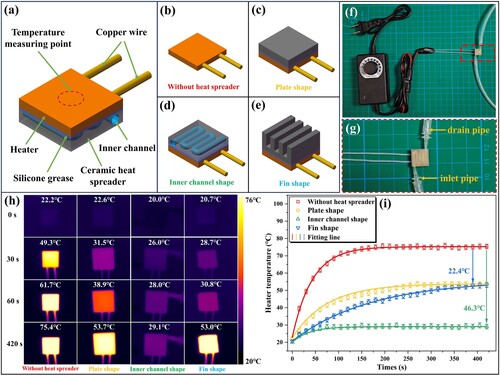
(h) illustrates the infrared thermal images of the heat source during the heating process. After heating for 420 s, the temperature of the heater without a heat spreader increased to 75.4°C. In contrast, heaters with plate- and fin-shaped AlN heat spreaders registered temperatures of 53.7°C and 53.0°C, respectively, showing a decrease of around 22.4°C. Remarkably, the heater with an inner channel-shaped AlN heat spreader exhibited an even lower temperature of only 29.1°C (i.e. there was a significant decrease of 46.3°C). The heat-dissipation ability of the inner channel-shaped AlN heat spreader increased by 23.9°C in comparison with that of a fin-shaped appliance. As shown in (i), the heating rate of the heater without a heat spreader was much higher than that of the other three heaters, achieving 75.0°C within 150 s. Meanwhile, the heating rate of the heater with the inner channel-shaped AlN heat spreader was noticeably slower than those in the other three cases. Therefore, the robust heat-dissipation capability demonstrated by the inner channel-shaped AlN component in the above experiments indicates a promising application potential in the thermal management.
4. Conclusions
In this work, a systematic examination was conducted to elucidate the influence of a novel surfactant, acrylate block copolymer, on the rheological properties, curing behaviour, and stability of AlN ceramic slurries. When incorporating 5 wt% SmF3 as a sintering additive, the effects of the solid loading and viscosity of AlN slurry on the density and homogeneity of 3D-printed green bodies, as well as on the density, sintering shrinkage, performance, phase composition, and microstructure of the sintered bodies, were systematically discussed. The key conclusions are as follows:
(1) | The KMT3331 surfactant, featuring hydrophobic acrylate groups, formed a coating layer on the surface of AlN powders, greatly improving their wettability and dispersibility with the photosensitive resin, thereby reducing the viscosity of the AlN slurry and avoiding shear thickening behaviour. Even with a solid loading as high as 65 vol.%, the modified slurry maintained excellent flowability. | ||||
(2) | The modified slurries with high solid loading and low viscosity were advantageous for the enhancement of the density and homogeneity of green bodies, improving interlayer bonding strength, reducing internal defects, and minimising sintering shrinkage. Once the solid loading rose from 50 to 65 vol.%, the linear shrinkage rates in the X, Y, and Z directions decreased from 19.16%, 19.22%, and 22.33% to 13.69%, 13.74%, and 14.72%, respectively. Meanwhile, the linear shrinkage rates in various directions tend to be consistent. | ||||
(3) | The elevated solid loading reduced the oxygen content and abnormal grain growth in sintered AlN specimens, as well as promoted the refinement and isolation of secondary phase (SmAlO3), thus enhancing the microstructure uniformity. As soon as the solid loading rose from 50 to 65 vol.%, the mean grain size of the specimens decreased from 10.11 ± 4.11 μm to 6.68 ± 2.04 μm. | ||||
(4) | The thermal characteristics, mechanical properties, and reliability were improved with the elevation in solid loading. The AlN specimen with 60 vol.% solid loading exhibited high thermal conductivity of 184.56 ± 2.77 W·m−1·K−1, flexural strength of 458.09 ± 36.03 MPa, fracture toughness of 3.95 ± 0.26 MPa·m1/2, and Weibull modulus of 14.89. These values were 8.14%, 18.05%, 7.05%, and 33.54% higher than those of the specimens with 50 vol.% solid loading, respectively. | ||||
(5) | Finally, as a heat spreader substrate, the inner channel-shaped AlN heat spreader demonstrated an increase in its heat dissipation ability by 23.9°C relative to that of a fin-shaped AlN heat spreader. This indicates that 3D-printed AlN ceramics with inner channels have superior heat dissipation compared to those utilising complex-shaped components. |
Disclosure statement
No potential conflict of interest was reported by the author(s).
Data availability statement
Data available on request from the authors.
Additional information
Funding
References
- Dammak K, Elhami A. Thermal reliability-based design optimization using Kriging model of PCM based pin fin heat sink. Int J Heat Mass Transfer. 2021;166:120745. doi:10.1016/j.ijheatmasstransfer.2020.120745
- Lin L, Wu H, Ni P, et al. Additive manufacturing of complex-shaped and high-performance aluminum nitride-based components for thermal management. Addit Manuf. 2022;52 :102671. doi:10.1016/j.addma.2022.102671
- Cao C, Feng Y, Qiu T, et al. Effects of isothermal annealing on the oxidation behavior, mechanical and thermal properties of AlN ceramics. Ceram Int. 2017;43(12):9334–9342. doi:10.1016/j.ceramint.2017.04.098
- Jiang H, Wang X, Fan G, et al. Effect of oxidation on flexural strength and thermal properties of AlN ceramics with residual stress and impedance spectroscopy analysis of defects and impurities. Ceram Int. 2019;45(10):13019–13023. doi:10.1016/j.ceramint.2019.03.232
- Nie G, Sheng P, Li Y, et al. Enhanced mechanical and thermal properties of AlN ceramics via a chemical precipitation process. Int J Appl Ceram Technol. 2021;18(4):1255–1268. doi:10.1111/ijac.13742
- Tummala RR. Ceramic and glass-ceramic packaging in the 1990s. J Am Ceram Soc. 1991;74(5):895–908. doi:10.1111/j.1151-2916.1991.tb04320.x
- Huang D, Liu Z, Harris J, et al. High thermal conductive AlN substrate for heat dissipation in high-power LEDs. Ceram Int. 2019;45(1):1412–1415. doi:10.1016/j.ceramint.2018.09.171
- Lin K, Nie G, Sheng P, et al. Effects of doping Al-metal powder on thermal, mechanical and dielectric properties of AlN ceramics. Ceram Int. 2022;48:36210–36217. doi:10.1016/j.ceramint.2022.08.178
- Nie G, Li Y, Sheng P, et al. Microstructure refinement-homogenization and flexural strength improvement of Al2O3 ceramics fabricated by DLP-stereolithography integrated with chemical precipitation coating process. J Adv Ceram. 2021;10(4):790–808. doi:10.1007/s40145-021-0473-2
- Huang D, Tian Z, Cui W, et al. Effects of Y2O3 and yttrium aluminates as sintering additives on the thermal conductivity of AlN ceramic substrates. Ceram Int. 2018;44(16):20556–20559. doi:10.1016/j.ceramint.2018.07.178
- Suzuki TS, Sakka Y. Preparation of oriented bulk 5 wt% Y2O3-AlN ceramics by slip casting in a high magnetic field and sintering. Scr Mater. 2005;52(7):583–586. doi:10.1016/j.scriptamat.2004.11.033
- Guo L, Yang J, Feng Y, et al. Non-aqueous gelcasting of AlN ceramics using a low-toxicity monomer (DMAA) as gelling agent. Ceram Int. 2018;44(2):1621–1626. doi:10.1016/j.ceramint.2017.10.083
- Qin M, Lu H, Wu H, et al. Powder injection molding of complex-shaped aluminium nitride ceramic with high thermal conductivity. J Eur Ceram Soc. 2019;39(4):952–956. doi:10.1016/j.jeurceramsoc.2018.11.037
- Zocca A, Colombo P, Gomes CM, et al. Additive Manufacturing of Ceramics: Issues, Potentialities, and Opportunities. J Am Ceram Soc. 2015;98(7):1983–2001. doi:10.1111/jace.13700
- Chen Z, Li Z, Li J, et al. 3D printing of ceramics: A review. J Eur Ceram Soc. 2019;39(4):661–687. doi:10.1016/j.jeurceramsoc.2018.11.013
- Halloran JW. Ceramic Stereolithography: Additive Manufacturing for Ceramics by Photopolymerization. Annu Rev Mater Res. 2016;46:19–40. doi:10.1146/annurev-matsci-070115-031841
- Li X, Chen Y. Vat-Photopolymerization-based ceramic manufacturing. J Mater Eng Perform. 2021;30(7):4819–4836. doi:10.1007/s11665-021-05920-z
- Sheng P, Nie G, Li Y, et al. Enhanced curing behavior, mechanical and thermal properties of 3D printed aluminum nitride ceramics using a powder coating strategy. Addit Manuf. 2023;74:103732. doi:10.1016/j.addma.2023.103732
- Li Q, An X, Liang J, et al. Balancing flexural strength and porosity in DLP-3D printing Al2O3 cores for hollow turbine blades. J Mater Sci Technol. 2021;84:59–64. doi:10.1016/j.jmst.2020.12.027
- Zhou M, Liu W, Wu H, et al. Preparation of a defect-free alumina cutting tool via additive manufacturing based on stereolithography - Optimization of the drying and debinding processes. Ceram Int. 2016;42(10):11598–11602. doi:10.1016/j.ceramint.2016.04.050
- He R, Liu W, Wu Z, et al. Fabrication of Complex-shaped Zirconia Ceramic Parts via a DLP- Stereolithography-based 3D printing method. Ceram Int. 2018;44(3):3412–3416. doi:10.1016/j.ceramint.2017.11.135
- Liu W, Wu H, Tian Z, et al. 3D printing of dense structural ceramic microcomponents with low cost: Tailoring the sintering kinetics and the microstructure evolution. J Am Ceram Soc. 2019;102(5):2257–2262. doi:10.1111/jace.16241
- Li Y, Wang M, Wu H, et al. Cure behavior of colorful ZrO2 suspensions during Digital light processing (DLP) based stereolithography process. J Eur Ceram Soc. 2019;39(15):4921–4927. doi:10.1016/j.jeurceramsoc.2019.07.035
- Zhu W, Fu H, Xu Z, et al. Fabrication and characterization of carbon fiber reinforced SiC ceramic matrix composites based on 3D printing technology. J Eur Ceram Soc. 2018;38:4604–4613. doi:10.1016/j.jeurceramsoc.2018.06.022
- Tang J, Chang H, Guo X, et al. Preparation of carbon fiber-reinforced SiC ceramics by stereolithography and secondary silicon infiltration. Ceram Int. 2022;48(17):25159–25167. doi:10.1016/j.ceramint.2022.05.178
- Zou W, Yang P, Lin L, et al. Improving cure performance of Si3N4 suspension with a high refractive index resin for stereolithography-based additive manufacturing. Ceram Int. 2022;48(9):12569–12577. doi:10.1016/j.ceramint.2022.01.124
- Huang S, Li Y, Yang P, et al. Cure behaviour and mechanical properties of Si3N4 ceramics with bimodal particle size distribution prepared using digital light processing. Ceram Int. 2023;49:12166–12172. doi:10.1016/j.ceramint.2022.12.068
- Huang R, Jiang Q, Wu H, et al. Fabrication of complex shaped ceramic parts with surface-oxidized Si3N4 powder via digital light processing based stereolithography method. Ceram Int. 2019;45(4):5158–5162. doi:10.1016/j.ceramint.2018.11.116
- Duan W, Li S, Wang G, et al. Thermal conductivities and mechanical properties of AlN ceramics fabricated by three dimensional printing. J Eur Ceram Soc. 2020;40(10):3535–3540. doi:10.1016/j.jeurceramsoc.2020.04.004
- Lin L, Wu H, Li Y, et al. Effect of particle size on rheology, curing kinetics, and corresponding mechanical and thermal properties of aluminum nitride (AlN) ceramic by digital light processing (DLP)-based vat photopolymerization. J Eur Ceram Soc. 2024;44:184–192. doi:10.1016/j.jeurceramsoc.2023.08.048
- Chen I-W, Wang X-H. Sintering dense nanocrystalline ceramics without final-stage grain growth. Nature. 2000;404(6774):168–171. doi:10.1038/35004548
- Kusunose T, Sekino T. Improvement in fracture strength in electrically conductive AlN ceramics with high thermal conductivity. Ceram Int. 2016;42(11):13183–13189. doi:10.1016/j.ceramint.2016.05.110
- Lee HM, Kim DK. High-strength AlN ceramics by low-temperature sintering with CaZrO3-Y2O3 co-additives. J Eur Ceram Soc. 2014;34(15):3627–3633. doi:10.1016/j.jeurceramsoc.2014.05.008
- Dong G, Chen X, Zhang X, et al. Thermal fatigue behaviour of Al2O3-DBC substrates under high temperature cyclic loading. Solder Surf Mount Technol. 2010;22(2):43–48. doi: 10.1108/09540911011036280
- Gu Q, Sun L, Ji X, et al. High-performance and high-precision Al2O3 architectures enabled by high-solid-loading, graphene-containing slurries for top-down DLP 3D printing. J Eur Ceram Soc. 2023;43(1):130–142. doi:10.1016/j.jeurceramsoc.2022.09.048
- Mu Y, Chen J, An X, et al. Effect of synergism of solid loading and sintering temperature on microstructural evolution and mechanical properties of 60 vol% high solid loading ceramic core obtained through stereolithography 3D printing. J Eur Ceram Soc. 2023;43(2):661–675. doi:10.1016/j.jeurceramsoc.2022.10.051
- Griffith ML, Halloran JW. Freeform fabrication of ceramics via stereolithography. J Am Ceram Soc. 1996;79(10):2601–2608. doi:10.1111/j.1151-2916.1996.tb09022.x
- Jang K-J, Kang J-H, Fisher JG, et al. Effect of the volume fraction of zirconia suspensions on the microstructure and physical properties of products produced by additive manufacturing. Dent Mater. 2019;35(5):e97–e106. doi:10.1016/j.dental.2019.02.001
- Zhang K, Meng Q, Zhang X, et al. Roles of solid loading in stereolithography additive manufacturing of ZrO2 ceramic. Int J Refract Met Hard Mater. 2021;99:105604. doi:10.1016/j.ijrmhm.2021.105604
- Zhang K, Meng Q, Cai N, et al. Effects of solid loading on stereolithographic additive manufactured ZrO2 ceramic: A quantitative defect study by X-ray computed tomography. Ceram Int. 2021;47:24353–24359. doi:10.1016/j.ceramint.2021.05.149
- Liu J-C, Jean J-H, Li C-C. Dispersion of nano-sized γ-alumina powder in non-polar solvents. J Am Ceram Soc. 2006;89(3):882–887. doi:10.1111/j.1551-2916.2005.00858.x
- Lin L, Wu H, Xu Y, et al. Fabrication of dense aluminum nitride ceramics via digital light processing-based stereolithography. Mater Chem Phys. 2020;249:122969. doi:10.1016/j.matchemphys.2020.122969
- Xu X, Zhou S, Wu J, et al. Inter-particle interactions of alumina powders in UV-curable suspensions for DLP stereolithography and its effect on rheology, solid loading, and self-leveling behavior. J Eur Ceram Soc. 2021;41(4):2763–2774. doi:10.1016/j.jeurceramsoc.2020.12.004
- Kim J-M, Kim H-N, Park Y-J, et al. Fabrication of transparent MgAl2O4 spinel through homogenous green compaction by microfluidization and slip casting. Ceram Int. 2015;41(10):13351–13360.
- Zong X, Wang H, Gu H, et al. Highly transparent Mg0.27Al2.58O3.73N0.27 ceramic fabricated by aqueous gelcasting, pressureless sintering, and post-HIP. J Am Ceram Soc. 2019;102(11):6507–6516. doi:10.1111/jace.16544
- Lin K, Zong X, Sheng P, et al. Effects of SmF3 addition on aluminum nitride ceramics via pressureless sintering. J Eur Ceram Soc. 2023;43(15):6804–6814. doi:10.1016/j.jeurceramsoc.2023.07.051
- Lu H, Qin M, Wu H, et al. Effect of AlN powders on the debinding and sintering behavior, and thermal conductivity of injection molded AlN ceramics. Ceram Int. 2019;45(18):23890–23894. doi:10.1016/j.ceramint.2019.08.183
- Leitner J, Voňka P, Sedmidubský D, et al. Application of Neumann–Kopp rule for the estimation of heat capacity of mixed oxides. Thermochim Acta. 2010;497(1):7–13. doi:10.1016/j.tca.2009.08.002
- Wurst JC, Nelson JA. Lineal intercept technique for measuring grain size in two-phase polycrystalline ceramics. J Am Ceram Soc. 1972;55:109. doi:10.1111/j.1151-2916.1972.tb11224.x
- Zuo F, Badev A, Saunier S, et al. Microwave versus conventional sintering: estimate of the apparent activation energy for densification of α-alumina and zinc oxide. J Eur Ceram Soc. 2014;34(12):3103–3110. doi:10.1016/j.jeurceramsoc.2014.04.006
- Gang C, Jia W, Ning H, et al. Strengthening mechanisms based on reinforcement distribution uniformity for particle reinforced aluminum matrix composites. Trans Nonferrous Metals Soc China. 2018;28(12):2395–2400. doi:10.1016/S1003-6326(18)64885-X
- Zhang L, Hui X, Chen J. Effects of terrain slope on water distribution and application uniformity for sprinkler irrigation. Int J Agric Biol Eng. 2018;11(3):120–125. doi:10.25165/j.ijabe.20181103.2901
- Lu Y, Mei Z, Zhang J, et al. Flexural strength and Weibull analysis of Y-TZP fabricated by stereolithographic additive manufacturing and subtractive manufacturing. J Eur Ceram Soc. 2020;40(3):826–834. doi:10.1016/j.jeurceramsoc.2019.10.058
- Nie G, Li Y, Sheng P, et al. Fabrication of Al2O3/AlN composite ceramics with enhanced performance via a heterogeneous precipitation coating process. Ceram Int. 2020;46(13):21156–21165. doi:10.1016/j.ceramint.2020.05.193
- Krieger IM, Dougherty TJ. A Mechanism for Non-Newtonian Flow in Suspensions of Rigid Spheres. Trans Soc Rheol. 2000;3(1):137–152. doi:10.1122/1.548848
- Liu D-M. Particle packing and rheological property of highly-concentrated ceramic suspensions: φm determination and viscosity prediction. J Mater Sci. 2000;35:5503–5507. doi:10.1023/A:1004885432221
- Mueller S, Llewellin EW, Mader HM. The rheology of suspensions of solid particles. Proc R Soc A Math Phys Eng Sci. 2010;466(2116):1201–1228. doi:10.1098/rspa.2009.0445
- Camargo ILDC, Morais MM, Fortulan CA, et al. A review on the rheological behavior and formulations of ceramic suspensions for vat photopolymerization. Ceram Int. 2021;47(9):11906–11921. doi:10.1016/j.ceramint.2021.01.031
- Li K, Zhao Z. The effect of the surfactants on the formulation of UV-curable SLA alumina suspension. Ceram Int. 2017;43(6):4761–4767. doi:10.1016/j.ceramint.2016.11.143
- Liu Y, Cheng L, Li H, et al. Formation mechanism of stereolithography of Si3N4 slurry using silane coupling agent as modifier and dispersant. Ceram Int. 2020;46(10):14583–14590. doi:10.1016/j.ceramint.2020.02.258
- Sun J, Binner J, Bai J. Effect of surface treatment on the dispersion of nano zirconia particles in non-aqueous suspensions for stereolithography. J Eur Ceram Soc. 2019;39(4):1660–1667. doi:10.1016/j.jeurceramsoc.2018.10.024
- Adake CV, Bhargava P, Gandhi P. Effect of surfactant on dispersion of alumina in photopolymerizable monomers and their UV curing behavior for microstereolithography. Ceram. Int. 2015;41(4):5301–5308. doi:10.1016/j.ceramint.2014.12.066
- Tomeckova V, Halloran JW. Critical energy for photopolymerization of ceramic suspensions in acrylate monomers. J Eur Ceram Soc. 2010;30(16):3273–3282. doi:10.1016/j.jeurceramsoc.2010.08.003
- Gentry SP, Halloran JW. Absorption effects in photopolymerized ceramic suspensions. J Eur Ceram Soc. 2013;33(10):1989–1994. doi:10.1016/j.jeurceramsoc.2013.03.004
- Song X, Chen Z, Lei L, et al. Piezoelectric component fabrication using projection-based stereolithography of barium titanate ceramic suspensions. Rapid Prototyp J. 2017;23(1):44–53. doi:10.1108/RPJ-11-2015-0162
- Zhang K, He R, Ding G, et al. Effects of fine grains and sintering additives on stereolithography additive manufactured Al2O3 ceramic. Ceram Int. 2021;47(2):2303–2310. doi:10.1016/j.ceramint.2020.09.071
- Harris J, Youngman R, Teller R. On the nature of the oxygen-related defect in aluminum nitride. J Mater Res. 1990;5(8):1763–1773. doi:10.1557/JMR.1990.1763
- Yin S, Jiang S, Pan L, et al. Effects of solid loading and calcination temperature on microstructure and properties of porous Si3N4 ceramics by aqueous gelcasting using DMAA system. Ceram. Int. 2019;45(16):19925–19933. doi:10.1016/j.ceramint.2019.06.250
- Khor K, Cheng K, Yu L, et al. Thermal conductivity and dielectric constant of spark plasma sintered aluminum nitride. Mater Sci Eng A. 2003;347(1-2):300–305. doi:10.1016/S0921-5093(02)00601-9
- Medraj M, Baik Y, Thompson W, et al. Understanding AlN sintering through computational thermodynamics combined with experimental investigation. J Mater Process Technol. 2005;161(3):415–422. doi:10.1016/j.jmatprotec.2004.05.031
- He X, Ye F, Zhang H, et al. Effect of Sm2O3 content on microstructure and thermal conductivity of spark plasma sintered AlN ceramics. J Alloys Compd. 2009;482(1-2):345–348. doi:10.1016/j.jallcom.2009.04.013
- Tajika M, Matsubara H, Rafaniello W. Effect of grain contiguity on the thermal diffusivity of aluminum nitride. J Am Ceram Soc. 1999;82(6):1573–1575. doi:10.1111/j.1151-2916.1999.tb01958.x
- Terao R, Tatami J, Meguro T, et al. Fracture behavior of AlN ceramics with rare earth oxides. J Eur Ceram Soc. 2002;22(7):1051–1059. doi:10.1016/S0955-2219(01)00422-8
- Xu F, Zhang Z, Shi X, et al. Effects of adding yttrium nitrate on the mechanical properties of hot-pressed AlN ceramics. J Alloys Compd. 2011;509(35):8688–8691. doi:10.1016/j.jallcom.2011.05.110
- Zhan J, Cao Y, Zhang H, et al. Low-temperature sintering of AlN ceramics by Sm2O3-Y2O3-CaO sintering additives formed via decomposition of nitrate solutions. J Mater Eng Perform. 2017;26:453–459. doi:10.1007/s11665-016-2453-1
- Tatami J, Yasuda K, Matsuo Y, et al. Stochastic analysis on crack path of polycrystalline ceramics based on the difference between the released energies in crack propagation. J Mater Sci. 1997;32:2341–2346. doi:10.1023/A:1018588620081
- Du X, Qin M, Rauf A, et al. Structure and properties of AlN ceramics prepared with spark plasma sintering of ultra-fine powders. Mater Sci Eng A. 2008;496(1-2):269–272. doi:10.1016/j.msea.2008.05.027
- Lee R-R. Development of high thermal conductivity aluminum nitride ceramic. J Am Ceram Soc. 1991;74(9):2242–2249. doi:10.1111/j.1151-2916.1991.tb08291.x
- Rauchenecker J, Rabitsch J, Schwentenwein M, et al. Additive manufacturing of aluminum nitride ceramics with high thermal conductivity via digital light processing. Open Ceramics. 2022;9:100215. doi:10.1016/j.oceram.2021.100215
- Wang J, Wu H, Qi Y, et al. High-performance aluminum nitride made by Vat photopolymerization through optimization of resin refractive index and plasticizer content. Ceram Int. 2024;50(9):14896–14906. doi: 10.1016/j.ceramint.2024.01.405
- Lin L, Wu H, Lin K, et al. Effect of yttrium nitrate coating on the vat photopolymerization forming process and sintering properties of aluminum nitride ceramics. Addit Manuf. 2024;84:104115. doi:10.1016/j.addma.2024.104115
- Baek S-H, Jeong H, Ryu S-S. Aln with high strength and high thermal conductivity based on an MCAS-Y2O3-YSZ multi-additive system. J Eur Ceram Soc. 2022;42(3):898–904. doi:10.1016/j.jeurceramsoc.2021.11.012
- Wei X, Zhang H, Dang J, et al. Phase and microstructure optimization of grain boundary oxides and its effect on the thermal conductivity of Y2O3-doped AlN ceramics. J Eur Ceram Soc. 2022;42(12):4855–4865. doi:10.1016/j.jeurceramsoc.2022.05.042