Abstract
In this study, we report fabrication and characterisation of a nanocomposite system composed of a commercial resin and extremely small (several nanometres in diameter) titanium dioxide particles. Nanoparticles were synthesised in situ with particle nucleation occurring inside the resin matrix. In this nanodielectric fabrication method, the nanoparticle precursor was mixed to the resin solution, and the nanoparticles were in situ precipitated. Note that no high shear mixing equipment was needed to improve particle dispersion – nanoparticles were distributed in the polymer matrix uniformly since particle nucleation occurs uniformly throughout the matrix. The properties of in situ nanodielectrics are compared to the unfilled resin and an ex situ nanocomposite. We anticipate that the presented in situ nanocomposite would be employed in high-temperature superconductivity applications. In additions, the improvement shown in the dielectric breakdown indicates that conventional high-voltage components and systems can be reduced in size with novel nanodielectrics.
Recent investigations on composites have shown that the electrical insulation reliability of composites fabricated with nanoparticles (nanodielectrics) is better than that of unfilled matrix materials or composites fabricated with micrometre-size particles Citation1–6. These new materials have potential for fusion energy and low-temperature power applications, where superconducting wires are employed, since the number of commercially available structural composites with good electrical insulation properties are few Citation7,Citation8. In conventional polymeric composites for electrical insulation, addition of micrometre size particles degrade dielectric performance of the insulation compared to unfilled polymer. However, no degradation in electrical properties, such as dielectric breakdown, with respect to time and electrical aging of electrical insulation properties has been observed in nanodielectrics for conventional applications Citation1 and for cryogenic applications Citation3,Citation8–10. Although it is clear that nanoparticles influence the dielectric performance, yet no detailed analysis has been performed on the particle size to breakdown strength statistics.
Better electrical insulation materials with improved thermal and mechanical properties, without concomitant degradation of dielectric and electrical insulation properties, are needed for energy transmission and distribution and power applications, especially in electrical insulation for cryogenic applications Citation7,Citation8. Here, we focus on a commercial cryogenic resin and fabricate a nanocomposites using in situ and ex situ synthesis methods. The Nanodielectric Research was initiated at Oak Ridge National Laboratory in 2005 by blending commercial nanoparticles with a cryogenic resin using an ex situ method Citation11. The main issue with ex situ methods has been the breaking of the agglomeration of nanoparticles Citation12. To produce well-dispersed particles or to improve the dispersion, twin-screw extruders and high-power horn sonicators are employed for polymers with no-volatile content and within diluted solutions, respectively. Later, due to problems experienced in this ex situ approach (particles were not mixed uniformly), other methods were developed based on nanoparticle synthesis and in situ particle precipitation procedures Citation3,Citation8,Citation13–15 – in situ nanoparticle synthesised polymeric nanocomposites Citation3,Citation9.
The developed in situ method is unconventional and does not require high shear force such as in twin-screw extruders. The particles are uniformly distributed (cf. ). The synthesis of extremely small particles (e.g. less than 5 nm) is a possibility, and since the particles are synthesised in situ, there are no safety issues and concerns about free nanoparticles. With conventional mixing methods, preferred by industry, particle agglomeration is an issue (see ). Another issue that merits attention is nanotoxicology Citation16,Citation17.
Figure 1. Transmission electron microscopy images of nanocomposites. (a) Commercial nanoparticles mixed in a resin using a planetary mixer – not a desired dispersion due to particle clusters, there are regions with no particles. (b) In-house prepared TiO2 nanoparticles mixed with epoxy using an ex situ method (planetary mixer). In this study this sample is labelled with ex situ nanocomposite – very small particles forming clusters. (c) In situ synthesised particles within a resin (study labelled with in situ nanocomposite) – good dispersion. (d) In situ synthesised particles within polyvinyl alcohol – good dispersion with large irregular particles.
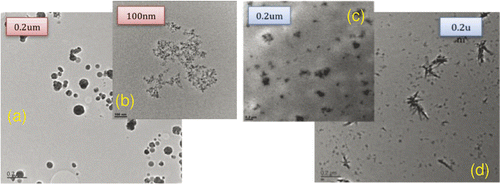
A commercial two-component bisphenol-A based resin (Araldite® CY 5808 US and Hardener HY 5808 US by Huntsman Inc., USA) was used as the matrix. The nanocomposite was fabricated as follows, which is similar to the method described by Tuncer et al. Citation3. The Araldite® resin was diluted with methanol (MeOH), and titanium trichloride (TiCl3) MeOH precursor was added in a weight ratio – this results in 2.5 wt% rutile TiO2 in the nanocomposite. The solution was stirred in a dry atmosphere under low pressure for 48 h to initiate TiO2 nanoparticle formation. A proportional recommended amount of resin hardener was added to the resin/particle mixture and stirred in a planetary mixer under vacuum. Films of nanocomposites were cast. For comparison, in-house synthesised TiO2 particles (less than 10 nm) were mixed in the resin to compare the influence of in situ and ex situ techniques on physical properties. The structures of the nanocomposites fabricated with these two methods, ex situ and in situ, are shown in , respectively. To illustrate the strength of the in situ method previously studied systems are also shown in , which clearly indicate the dispersion in the sample prepared with the in situ technique is uniform, although the particle size is not there are nanoparticles between large particles in . The commercial particle sizes in were between 20 and 100 nm Citation11, while in the particles, which were prepared in-house, have size distribution between 2 and 10 nm Citation18.
The dynamic mechanical analysis (DMA) was employed to determine the mechanical properties of thick films, which were 15 mm long, 5.5 mm wide and 150–200 µm thick. Measurements were in the tensile mode at frequency 1 Hz. The unfilled resin has no crystallinity, and has a glass transition at 34.5°C. The thermo-mechanical properties of the resin were presented elsewhere Citation18. The in situ nanocomposite exhibited a higher storage modulus than the unfilled resin and ex situ nanocomposite over the entire temperature range, cf. . At the lowest measured temperature (128 K), the nanocomposite had a 30% higher storage modulus than the unfilled resin. Loss modulus G″ was higher compared to other samples due to the increase in the storage modulus G ′. The noise in the moduli is due to thin film thickness. The ex situ sample had degraded mechanical properties due to the capping agent used in the in-house nanoparticle synthesis with polyethylene glycol, which altered the surface dynamics of the resin–nanoparticle interface. The oscillating force applied to the samples during DMA causes polymer and particles to relax by absorbing and releasing energy, in the nanocomposites when the particles are dispersed uniformly, then the energy needed increases compared to unfilled polymer. The imaginary parts of the complex moduli in show the energy lost during the oscillating applied force, demonstrating the influence of the well-dispersed nanoparticles in the in situ sample.
Figure 2. Results of dynamic mechanical analysis, (a) storage and (b) loss moduli, of unfilled resin and two nanocomposites at 1 Hz as a function of temperature.
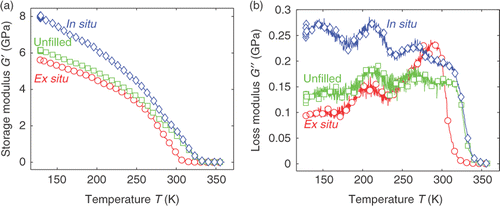
Dielectric properties of the samples were measured using aLCR meter and a cryocooler with data acquisition system that was capable of measuring capacitances between 15 and 300 K. The isochoronal dielectric data are presented in a broad temperature range in . Dielectric losses in the in situ nanodielectric were significantly lower than in the unfilled resin and the ex situ nanocomposite at temperatures below 200 K (approximately 10 times lower at 20 K). All materials had very similar relative permittivity (around 3.0) below 100 K. A broad relaxation process was present in the unfilled resin at 160 K – this relaxation was the local segmental motion. This process was also visible in the ex situ material but was narrower. We believe that the presence of nanoparticles, which were close to the size of polymer chain gyration, limited chain relaxation and therefore narrowed the distribution of relaxation times. There were clear differences in dielectric data between ex situ and others over 200 K, which were due to the capping agent used to synthesise in-house in situ nanoparticles – polyethylene glycol was used as the capping agent. The capping agent had ionic species that increased the losses above 250 K.
Figure 3. Dielectric susceptibilities (χ = χ ′−ιχ ″) of studied materials, (a) real and (b) imaginary parts.
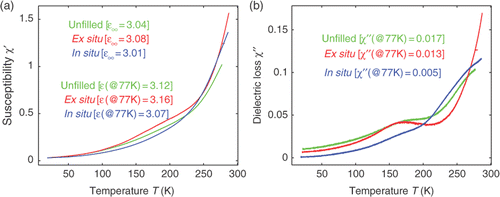
The dielectric breakdown data of the samples were analysed in terms of lognormal and Weibull distribution statistics using Dataplot Platform Citation19, cf. . The lognormal cumulative distribution is expressed as
Figure 4. Breakdown statistics analysed with (left) lognormal P L (μ, σ) and (right) two-parameter Weibull P W (α, β) of unfilled resin and its nanocomposites at 77 K. The confidence intervals for each sample are shown for the reader to determine the design parameters for their application. For example, one can consider the percentage probability at 0.1 as the design breakdown strength in engineering applications. The data were collected from dielectric breakdown tests that were performed on multiple samples with thicknesses around 50 µm using a 500 V/s voltage ramp at 77 K.
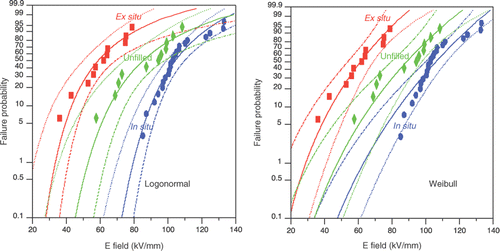
Analysis based on the Weibull expression Citation20,Citation21 showed that the data from Equation (Equation2) was not able to represent the measured dielctric breakdown values – error approximations or in other words confidence intervals were broad. However, the lognormal distribution in Equation (Equation1) yield narrower confidence intervals than the Weibull analysis for the in situ sample. To better represent the data and leave the judgement to the reader, the analysis results with both expressions are presented in . Notice that there is a large drop in the breakdown scale parameter μ between ex situ and unfilled due to the surfactant material used in the in-house nanoparticle synthesis. The surfactant has ionic species that influences the high-field behaviour of the nanocomposites Citation22 because of the large changes in the local electric field distribution in the bulk of the sample. The fluctuations in the local electric field result in high stress regions that can initiate a breakdown process, such as electrical treeing and thermal degradation.
Table 1. Statistical analysis data of breakdown data using lognormal and Weibull distributions.
The most noticeable improvement in the physical properties of the in situ nanocomposite was the scale parameter of breakdown strength α and the mean μ. Any enhancement in the breakdown characteristics leads to a reduction in electrical insulation thickness and therefore enables smaller power equipment. For example, a possible dielectric design parameter can be adopted by using the lognormal analysis at the 0.1% failure probability field ( in ), which is 61% higher in the nanodielectric (72.74 kV/mm) than in the unfilled epoxy resin (45.21 kV/mm). Similarly, the Weibull analysis yields 40% improvement in the
in .
This betterment corresponds to 0.62 times less insulation thickness for a given voltage level or 1.61 times the voltage for the same insulation thickness (assuming that both breakdown characteristics of the unfilled and nanodielectric materials scale the same with thickness). Notice that if a lower design electric field is employed other than E 001, let us say 0.01% (E 0001), then the thickness required would be much thinner and the size of an equipment would be much smaller because of the low σ in the in situ nanocomposite.
As a critique, the improvement in the breakdown strength was attributed to the size of the particles and their well-dispersion. Since the employed nanoparticles are TiO2, with significantly higher dielectric permittivity than the base resin, local electric field distribution becomes smooth and each particle acts as a field diversion point assuming that the electric field landscape in the resin is not uniform Citation22. Then these diversion points would screen the undesired effects of the defects or in other words smooth the electric field landscape – this would create a nanocomposite material that is defect tolerant. The mechanical and dielectric measurement illustrated implications for this hypothesis by exhibiting the changes in the dynamic properties of the resin and its nanocomposites. In addition, the size of the particles are small and comparable to the dimensions of polymer molecules and chains. For example the segmental motion in the resin at low temperatures was hindered in the in situ nanocomposite, and similarly nanoparticles influenced the mechanical properties.
As a conclusion we have illustrated that a thermoset polymeric nanodielectric with TiO2 nanoparticles synthesised in situ resulted in an electrical insulation material with superior cryogenic properties. The nanodielectric with 2.5 wt% TiO2 showed a uniform distribution of nanoparticles, unlike the ex situ nanodielectric. The in situ technique does not require high shear mixing, unlike the ex situ methods, for uniform nanoparticle distribution. The mechanical and dielectric properties of the in situ nanodielectric indicated improvements in its physical properties. The increase in breakdown strength at 77 K was very significant for electro- and high-voltage technology – extremely important in ‘reducing the size’ of high-voltage components and systems. The in situ fabrication method developed at Oak Ridge National Laboratory can be employed with other nanocomposites to improve physical properties and material reliability in electrical insulation and high-voltage applications.
Acknowledgements
We thank Prof. Steven A. Boggs for valuable suggestion on using lognormal distribution for our breakdown data. This research was sponsored by the US Department of Energy Office of Electricity Delivery and Energy Reliability, Advanced Cables and Conductors Program for Electric Power Systems Contract DE-AC05-00OR22725 with Oak Ridge National Laboratory, managed and operated by UT-Battelle, LLC. Research supported in part by the Oak Ridge National Laboratory's SHaRE User Facility, which is sponsored by the Scientific User Facilities Division, Office of Basic Energy Sciences, U.S. Department of Energy.
References
- Nelson, , J.K. ed., . 2010 . Dielectric Polymer Nanocomposites , New York : Springer .
- Y. Uozumi, Y. Kikuchi, N. Fukumoto, M. Nagata, Y. Wakimoto, and T. Yoshimitsu, CEIDP'07 2007 Annual Report, IEEE Dielectrics and Electrical Insulation Society (IEEE, 2007), IEEE Publications, Conference on Electrical Insulation and Dielectric Phenomena, pp. 228–231
- Tuncer , E , Sauers , I , James , DR , Ellis , AR , Paranthaman , MP , Goyal , A and More , KL . 2007 . Enhancement of dielectric strength in nanocomposites . Nanotechnology , 18 5pp
- Tanaka , T . 2005 . Dielectric nanocomposites with insulating properties . IEEE Trans. Dielectr. Electr. Insul. , 12 : 914 – 928 .
- Nelson , JK and Hu , Y . 2005 . Nanocomposite dielectrics – properties and implications . J. Phys. D: Appl. Phys. , 38 : 213 – 222 .
- Nelson , JK and Fothergill , JC . 2004 . Internal charge behaviour of nanocomposites . Nanotechnology , 15 : 586 – 595 .
- Tuncer , E and Sauers , I . 2010 . Dielectric Polymer Nanocomposites, Chap. 11 , New York : Springer .
- Tuncer , E , Sauers , I , James , DR , Ellis , AR , Pace , M , More , KL , Sathyamurthy , S , Woodward , J and Rondinone , AJ . 2009 . Nanodielectrics for cryogenic applications . IEEE Trans. Appl. Supercond. , 19 : 2354 – 2358 .
- Polizos , G , Tuncer , E , Sauers , I and More , KL . 2010 . Properties of a nanodielectric cryogenic resin . Appl. Phys. Lett. , 96 3pp
- Tuncer , E , Sauers , I , James , DR , Ellis , AR and Duckworth , RC . 2008 . Nanodielectric system for cryogenic applications: Barium titanate filled polyvinyl alcohol . IEEE Trans. Dielectr. Electr. Insul. , 15 : 236 – 242 .
- Tuncer , E , Sauers , I , James , DR , Ellis , AR , Paranthaman , MP , Aytuğ , T , Sathyamurthy , S , More , KL , Li , J and Goyal , A . 2007 . Electrical properties of epoxy resin based nano-composites . Nanotechnology , 18 6pp
- E. Allen, P. Smith, and J. Henshaw, A review of particle agglomeration, AEA Technology Engineering Services, Inc (2001), Tech. Rep., Sterling, VA. Available at: URL www.tanks.org/ttgdoc/AEAT-R-PSEG-0398.doc
- E. Tuncer, G. Polizos, I. Sauers, D. James, A. Ellis, and K. More, IEEE Conference on (IEEE, 2009), Electrical Insulation and Dielectric Phenomena, 2009. CEIDP '09, Piscataway, NJ, USA, pp. 527–530, ISSN 0084-9162
- Liu , S and Mark , J . 1987 . Precipitation of iron oxide filler particles into an elastomer . Polym. Bull. , 18 : 33 – 37 .
- Wang , S-B and Mark , J . 1987 . In-situ precipitation of reinforcing titania fillers . Polym. Bull. , 17 : 271 – 277 .
- Oberdörster , G , Oberdörster , E and Oberdörster , J . 2005 . Nanotoxicology: An emerging discipline evolving from studies of ultrafine particles . Environ. Health Perspect. , 113 : 823 – 839 .
- Warheit , DB , Borm , PJ , Hennes , C and Lademann , J . 2007 . Testing strategies to establish the safety of nanomaterials: Conclusions of an ECETOC workshop . Inhal. Toxicol. , 19 : 631 – 643 .
- G. Polizos, E. Tuncer, I. Sauers, and K.L. More, Physical properties of epoxy resin/titanium dioxide nanocomposites, J. Polym. Eng. Sci. (2010) DOI:10.1002/pen.21783 (in press)
- A. Heckert and J. Filliben, Dataplot Reference Manual; NIST Handbook 148, United States Department of Commence Technology Administration, National Institute of Standards and Technology, Gaithersburg, MD USA, 1995
- Tuncer , E , Sauers , I , James , DR , Ellis , AR and Pace , MO . 2006 . On dielectric breakdown statistics . J. Phys. D: Appl. Phys. , 39 : 4257 – 4268 .
- Xu , C , Ho , J and Boggs , SA . 2008 . Automatic breakdown voltage measurement of polymer films . IEEE Electr. Insul. Mag. , 24 : 30 – 34 .
- Tuncer , E , Rondinone , AJ , Woodward , J , Sauers , I , James , DR and Ellis , AR . 2009 . Cobalt iron-oxide nanoparticle modified poly(methyl methacrylate) nanodielectrics . Appl. Phys. A: Mater. Sci. and Process. , 94 : 843 – 852 .