Abstract
Porous anodic alumina (PAA) has been produced on aluminium substrate by single-step anodising at 50 V in 0.3 M oxalic acid at 15°C for 60 min. The highly ordered pore and cell structure was achieved by subjecting the PAA to oxide dissolution treatment in a mixture of chromic and phosphoric acids. The nanostructure prior and post-oxide dissolution treatment was examined under scanning electron microscope. It was found that the oxide dissolution treatment improves the regularity of the cell and pore structure significantly. Uniform closely packed honeycomb structure of PAA is obtained. The uniformities of pore diameter and interpore distance are also enhanced. Compared to the PAA prior treatment, it was noticed that the pore diameter of the post-treatment PAA increases.
1. Introduction
Porous anodic alumina (PAA) is a self-organising porous material. After the confirmation of the classical cell model proposed by Keller et al. Citation1, PAA has attracted enormous attention as an inexpensive template for the fabrication of various nanomaterials without the need of expensive and complex lithographic techniques Citation2–6. PAA is a suitable template for the synthesis of nanomaterials because various cell parameters such as pore diameter, interpore distance and pore depth can be controlled easily by varying the anodising conditions Citation7,Citation8.
The fabrication of nanomaterials by template synthesis method employs highly ordered PAA since it provides regular pore shape and narrow distribution of specific pore diameter and interpore distance for the synthesis of nanomaterials of uniform dimensions Citation4,Citation9,Citation10. The properties of nanomaterials are significantly influenced by the dimensions. Therefore, it is important to synthesise nanomaterials of uniform dimensions. First, highly ordered PAA was realised by Masuda and Fukuda Citation11 in 1995. They employ a two-step anodising method for the synthesis of highly ordered PAA. Since then, owing to the commercial potential and scientific significance, there has been an ongoing research effort towards the fabrication of highly ordered PAA. Pre-patterning methods such as imprint lithography Citation12–14, focused ion beam lithography Citation15 and electron beam lithography Citation16 were developed for the fabrication of highly ordered PAA. These methods involved the formation of indented concave periodic patterns on the aluminium substrate prior to the anodising process. These patterns served as a guide for the nucleation and growth of highly ordered PAA. High-field anodising was also proposed as an alternative for the synthesis of well-ordered PAA Citation17. Critical high anodising potential, which is the anodising potential required to induce high current density while preventing the local current density concentration on the aluminium surface, was applied to the high-field anodising. The role of electropolishing prior to the anodising process was also emphasised in order to achieve highly ordered PAA Citation18,Citation19.
Although these methods can produce highly ordered PAA, these methods are not feasible for the manufacturing over large-scale area because of high cost and low throughput. It is impractical to utilise these methods for the production of PAA for template synthesis of nanomaterials. Two-step anodising involves a three-step processing, which are anodising, stripping of PAA and reanodising. Therefore, two-step anodising is tedious and time consuming. High-field anodising required a large volume of high-concentration electrolyte to maintain the high current density, and external cooling system and agitating condition are needed to dissipate the heat generated during the anodising to maintain low electrolyte temperature. Thus, high-field anodising incurs higher cost than the ordinary moderate-potential anodising and is not environment-friendly. Furthermore, most of these methods require a relatively long anodising duration and low electrolyte temperature in order to achieve highly ordered PAA. In addition, most of these methods employed electropolishing to improve the surface smoothness to attain highly ordered PAA. Thus, the purpose of this study is to explore a simple method of oxide dissolution treatment to attain ordered PAA in shorter anodising duration and higher temperature to enlarge the application of PAA in template synthesis of nanomaterials. The regularities of pore distribution and the distribution of pore diameter and interpore distance were studied. This method uses electrolyte of lesser volume and lower concentration and does not require agitation. This method is also more convenient than multiple-step anodising and pre-patterning method and does not require electropolishing of the surface of substrate before the anodising process.
2. Experimental
High-purity (99.99%) aluminium substrates of thickness 4 mm were grinded by using silicon carbide paper up to 2000 grit. The substrates were then polished using diamond paste of 6, 1 and 0.05 µm successively to achieve a roughness of less than 50 nm over the entire surface. Substrates were degreased by dipping in a stirred ethanol and rinsed with deionised water. Lead plate was used as cathode. The distance between the lead cathode and aluminium anode was 40 mm. Anodising was performed at constant voltage for a sufficient time for the development of steady-state morphology within the film. Anodising was conducted in 0.3 M oxalic acid of 15°C at a constant voltage of 50 V. The concentration of electrolyte and the anodising voltage are known to produce highly ordered PAA when the starting surface is electropolished and subjected to prolonged anodising duration. The temperature variance was controlled at ±0.5°C. Current density–time curve was recorded during the anodising process. The morphology of the PAA was observed by scanning electron microscope (SEM) model JEOL JSM-6460LA. Pore diameter and interpore distance of the initially formed film were measured by using software JEOL SmileView version 2.1. The regularity of the whole distribution throughout the PAA was analysed by applying fast Fourier transform (FFT) to SEM micrograph using software ImageJ version 1.40g.
A mixture of chromic and phosphoric acids was prepared from 20 g of chromic acid and 35 mL of 85 wt% phosphoric acid in 1000 mL of distilled water. The anodised substrate was then subjected to oxide dissolution treatment in a stirred mixture of chromic and phosphoric acids at 70–80°C for 3 min. The substrate was rinsed thoroughly with distilled water and dried. The morphology of the post-treatment PAA was observed by SEM and the pore diameter and interpore distance were measured. The FFT of SEM micrograph of post-treatment PAA was calculated.
3. Results and discussion
The time variation of current density during the anodising is shown in . We found that the plot is typical for anodising of aluminium in oxalic acid Citation20. As the anodising commences, there is a current surge. This current density surge is followed by a rapid fall in current density to a minimum value. The current density then increases slowly to a steady-state value and maintains at this value for the rest of the anodising time. At the initial stage, due to the low electrical resistance of the clean surface, the current density increases rapidly. When it reaches the peak, the thickening of non-conductive barrier-type alumina occurs and the current density drops to a minimum value. However, the thickness of the barrier-type alumina film is not uniform and pores exist on the surface of the film. The thickness of the alumina is lower at these pores and the electric field will be concentrated at these pores. Field-assisted oxide dissolution mechanism occurs and the field electric resistance decreases with the emergence of the pores and the current density increases subsequently. The steady-state current density is reached when the rate of oxide dissolution at the base of the pores equals the rate of oxide formation at the metal/oxide interface, indicating the finish of pore-organising process Citation21. From , we observe that the current density attained the steady-state current density at around 10 min and this is in accordance to the previous study Citation20.
By comparing the morphology of the PAA before and after the oxide dissolution treatment, we determined the effectiveness of the treatment on improving the regularity of pore and cell distribution. shows the SEM images and FFT images of the PAA before and after the treatment. From the SEM images, we found that the pores of the PAA prior to the treatment are randomly distributed and show no ordered hexagonal cell structure. The shapes of the pores are not circular. The pore diameter and the interpore distances are non-uniform. The periodicity of pore distribution of PAA in the inverse space is reflected in the FFT images. The irregular pore distribution is reflected by the disc-shaped white form, of which the intensity is almost uniformly distributed within the disc as we can see in FFT image in . This FFT image does not indicate any order in the array structure of PAA prior to the treatment. SEM image in shows that pores in the post-treatment PAA exhibit ordered and nearly perfect hexagonal cell structure. Uniform closely packed honeycomb structure can be observed. The pore diameters and the interpore distance are nearly uniform over the analysed surface. The FFT image of the post-treatment PAA in consists of six distinct spots at the edge of a hexagon. This FFT image indicates six-fold symmetry of pore distribution over the surface of post-treatment PAA.
Figure 2. The SEM images and FFT images of PAA: (a) before the treatment and (b) after the treatment.
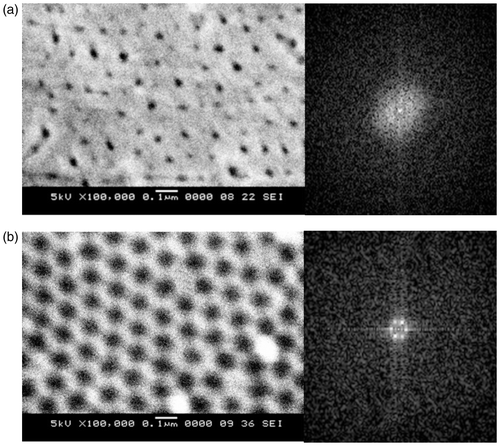
The morphology of the PAA in is generated due to the relatively rough starting surface of aluminium substrate. The starting surface has a roughness of less than 50 nm that will lead to the formation of barrier layer of non-uniform thickness on the substrate surface at the initial stage of anodising. This subsequently leads to the nucleation and growth of irregular pores at the surface of the substrate during the pore organising process. When the steady-state current density is attained, there is a constant expanding ratio of alumina for the formation of ordered pores structure Citation22. For disordered pore distribution, a higher compressive stress is formed in the higher pore density region, while a lower compressive stress is formed in the neighbouring region where the interpore distance is larger. This difference in stress changes the growth direction of the channel tip and contributes to the highly ordered pores distribution at the underneath layer Citation22. Generally, prolonged anodising duration will remove the upper layer and reveal the underneath more ordered pore distribution by chemical dissolution of the alumina by electrolyte. However, in this study, since shorter anodising duration is employed, we remove this irregular layer by treating the PAA in the mixture of chromic and phosphoric acids. The removal of the initially formed irregular layer by the oxide dissolution treatment improves the pore and cell distribution by revealing the underneath hexagonal cell structure.
In order to have a better understanding of the effect of the oxide dissolution treatment on the uniformity of pore diameter and interpore distance, we carried out 500 independent measurements on the top view of SEM image for PAA before and after the oxide dissolution treatment. All collected values of pore diameter and interpore distance of the PAA prior and post-treatment were classified into eight and nine classes covering the whole range of measured values. The pore sizes and interpore distance distributions of PAA prior and post-treatment are shown in and , respectively. As we can see from , the pore diameter of the PAA prior treatment varied from 17.5 to 52.5 nm and the maximum possible difference in the pore diameter is 35 nm. Oxide dissolution treatment significantly decreases the pore size distribution, where the maximum possible difference of pore diameter is 25 nm in post-treatment PAA. We observed similar behaviour for the interpore distance of PAA prior and post-treatment. The maximum possible difference of interpore distance reduced from 90 nm for PAA prior treatment to 40 nm for PAA post-treatment. The result obtained from the examinations of the distribution diagrams can be linked with the FFT images. Thus, we concluded that the uniformities of both pore diameter and interpore distance were significantly improved by the application of the oxide dissolution treatment. Besides, we noticed that the pore diameter increases significantly after the treatment. This is because the pore diameters of the initially formed PAA are smaller than those formed at the pore bottom Citation8,Citation21.
4. Conclusions
We have studied the effect of oxide dissolution treatment on the PAA film. The pore distribution is significantly improved by the oxide dissolution treatment. The pores in the post-treatment anodic film are highly regular in shape and size. Closely packed honeycomb structure is obtained instead of irregular pore distribution before the oxide dissolution treatment. The uniformities of the pore diameter and interpore distance are enhanced significantly. The pore diameter increases after the oxide dissolution treatment.
References
- Keller , F , Hunter , M S and Robinson , D L . 1953 . Structural features of oxide coatings on aluminum . J. Electrochem. Soc. , 100 ( 9 ) : 411 – 419 .
- Chuen-Chang , L and Ching-Long , Y . 2009 . Carbon nanotubes grown on nanoporous alumina templates/aluminum foil for electrodes of aluminum electrolytic capacitors . J. Electrochem. Soc. , 157 ( 2 ) : A237 – A241 .
- Sui , Y C , Gonzalez-Leon , J A , Bermudez , A and Saniger , J M . 2001 . Synthesis of multi branched carbon nanotubes in porous anodic aluminum oxide template . Carbon , 39 ( 11 ) : 1709 – 1715 .
- Jeong , S H , Hwang , H Y , Hwang , S K and Lee , K H . 2004 . Carbon nanotubes based on anodic aluminum oxide nano-template . Carbon , 42 ( 10 ) : 2073 – 2080 .
- Chen , Z , Lei , Y , Chew , H G , Teo , L W , Choi , W K and Chim , W K . 2004 . Synthesis of germanium nanodots on silicon using an anodic alumina membrane mask . J. Cryst. Growth , 268 ( 3–4 ) : 560 – 563 .
- Li , L , Pan , S , Dou , X , Zhu , Y , Huang , X , Yang , Y , Li , G and Zhang , L . 2007 . Direct electrodeposition of ZnO nanotube arrays in anodic alumina membranes . J. Phys. Chem. C , 111 ( 20 ) : 7288 – 7291 .
- Belwalkar , A , Grasing , E , Van Geertruyden , W , Huang , Z and Misiolek , W Z . 2008 . Effect of processing parameters on pore structure and thickness of anodic aluminum oxide (AAO) tubular membranes . J. Membr. Sci. , 319 ( 1–2 ) : 192 – 198 .
- Ono , S and Masuko , N . 2003 . Evaluation of pore diameter of anodic porous films formed on aluminum . Surf. Coat. Technol. , 169–170 : 139 – 142 .
- Zhao , Y , Chen , M , Liu , X , Xu , T and Liu , W . 2005 . Electrochemical synthesis of polydiphenylamine nanofibrils through AAO template . Mater. Chem. Phys. , 91 ( 2–3 ) : 518 – 523 .
- Qu , X , Dai , J , Tian , J , Huang , X , Liu , Z , Shen , Z and Wang , P . 2009 . Synthesis of Nd2O3 nanowires through sol–gel process assisted with porous anodic aluminum oxide (AAO) template . J. Alloys Compd. , 469 ( 1–2 ) : 332 – 335 .
- Masuda , H and Fukuda , K . 1995 . Ordered metal nanohole arrays made by a two-step replication of honeycomb structures of anodic alumina . Science , 268 ( 5216 ) : 1466 – 1468 .
- Choi , J , Nielsch , K , Reiche , M , Wehrspohn , R B and Gosele , U . 2003 . Fabrication of monodomain alumina pore arrays with an interpore distance smaller than the lattice constant of the imprint stamp . J. Vac. Sci. Technol., B , 21 ( 2 ) : 763 – 766 .
- Kwon , N , Kim , K , Heo , J and Chung , I . 2009 . Fabrication of ordered anodic aluminum oxide with matrix arrays of pores using nanoimprint . J. Vac. Sci. Technol., A , 27 ( 4 ) : 803 – 807 .
- Masuda , H , Asoh , H , Watanabe , M , Nishio , K , Nakao , M and Tamamura , T . 2001 . Square and triangular nanohole array architectures in anodic alumina . Adv. Mater. , 13 ( 3 ) : 189 – 192 .
- Liu , C Y , Datta , A and Wang , Y L . 2001 . Ordered anodic alumina nanochannels on focused-ion-beam-prepatterned aluminum surfaces . Appl. Phys. Lett. , 78 ( 1 ) : 120 – 122 .
- Jeong , G H , Lim , S K , Park , J K , Lee , D , Lee , B K and Suh , S J . Nano-pore arrays of anodic aluminum oxide fabricated using a Cr mask, Proceedings of the Microprocesses and Nanotechnology, 2007 Digest Papers, Kyoto, Japan, 5–8 November 2007, pp. 192–193
- Chu , S Z , Wada , K , Inoue , S , Isogai , M and Yasumori , A . 2005 . Fabrication of ideally ordered nanoporous alumina films and integrated alumina nanotubule arrays by high-field anodization . Adv. Mater. , 17 ( 17 ) : 2115 – 2119 .
- Rauf , A , Mehmood , M , Asim Rasheed , M and Aslam , M . 2009 . The effects of electropolishing on the nanochannel ordering of the porous anodic alumina prepared in oxalic acid . J. Solid State Electrochem. , 13 ( 2 ) : 321 – 332 .
- Rahimi , M H , Tabaian , S H , Hoveyda Marashi , S P , Amiri , M , Dalaly , M M , Saramad , S , Ramazani , A and Zolfaghari , A . 2008 . The effect of aluminum electropolishing on nano-pores arrangement in anodic alumina membranes . Int. J. Mod. Phys. B , 22 ( 18–19 ) : 3267 – 3277 .
- Wang , N , Zhang , W , Xu , J , Ma , B , Zhang , Z , Jin , Q , Bunte , E , Hüpkes , J and Bochem , H . 2009 . Initial stage of pore formation process in anodic aluminum oxide template . J. Solid State Electrochem. , 14 ( 8 ) : 1377 – 1382 .
- O'sullivan , J P and Wood , G C . 1970 . The morphology and mechanism of formation of porous anodic films on aluminium . Proc. R. Soc. London, Ser. A , 317 ( 1531 ) : 511 – 543 .
- Long , B and Wei Sang , L . 2000 . Influence of anodizing conditions on the ordered pore formation in anodic alumina . J. Phys. D: Appl. Phys. , 33 ( 20 ) : 2527 – 2531 .