Abstract
In this work, surface modification of nanopowders in microwave plasma process was demonstrated. In order to obtain silica nanopowder with polymeric coating, a two-step microwave process was designed. 3-Aminopropyltrimethoxysilane was used as the surface modifier. Transmission electron microscopy and electron energy loss spectroscopy have been used for the direct microstructural imaging and chemical analysis of surface modified-silica nanopowders. The silica nanopowders were uniformly coated with a thick layer of amino-silane. Surface modification in microwave plasma is a simple, direct and easy to control process without using any solvents. The surface modified-silica nanopowders can be incorporated directly into polymer matrix for the preparation of hybrid nanocomposite materials.
1. Introduction
Organic–inorganic hybrid materials have attracted considerable attention due to the unique chemical and physical properties. The mechanical, optical and electronic properties of polymer can be tuned by hybridising different kinds of inorganic nanofillers or nanopowders. However, for the successful preparation of these nanocomposites, surface modification of the nanopowders or nanofillers is needed in order to enhance the stability, dispersibility and compatibility of nanopowders in the polymer matrix. Such process can be achieved by introducing chemical coupling agents or reactive functional groups onto the surface of the nanomaterials. Various chemical and physical methods have been reported for the modification or encapsulation of nanoparticles with protective shells. For example, the fabrication of polymer-stabilised nanoparticles involves two processes, reduction of metal ions and coordination of the polymer to the metal nanoparticles Citation1. Sol–gel process coupled with polymerisation is often be used to generate organic–inorganic hybrid materials Citation2. Bokobza et al. reported the preparation of silane-modified silica sol and silica-based hybrid films by ultraviolet radiation Citation3. The modification of the surface of silica nanoparticles with methyl methacrylate by UV-induced graft polymerisation has also been studied Citation4.
Nanopowders can be prepared by a variety of methods including chemical and physical processes such as sol–gel reaction Citation5, chemical reduction Citation6, high-energy ball milling Citation7, electrodeposition Citation8, laser ablation Citation9, chemical vapour deposition and sputtering deposition Citation10,Citation11. Ball milling or mechanical attrition have been applied for nanopowders production. However, the process had some disadvantages such as low production rate and product contamination. Microwave plasma method can be employed for the synthesis of nanopowders. The rapid evaporation, decomposition and pyrolysis of precursors result in nanopowders of high purity. Other advantages include low reaction temperature (573–1173 K), good stability and can operate at normal ambient pressure during the synthesis process. Among advantages of synthesis with microwave plasma over a conventional dry process are a lower reaction temperature and uniform temperature field. For example, when silver nanopowders were prepared with a microwave plasma synthesis, the average particle size of the silver nanopowder increased with the rate of feeding the precursor material Citation12. The probability of forming agglomerates in nanopowders is decreased through the low-temperature characteristic of a microwave plasma. In this work, surface modification of nanopowders in microwave plasma process was demonstrated. The surface modified-silica nanopowders can be incorporated directly into polymer matrix for the preparation of hybrid nanocomposite materials.
2. Experimental
Our microwave plasma unit, shown in , is designed to produce ultra-dispersed and ultrafine (generally less than 100 nm) powders through condensation from a chemically reacting gas flowing at high temperature. The synthesis was performed in the reaction region with microwave radiation (2.45 GHz) and a single cavity mode. The nanopowders were obtained from a chemical reaction occurring in flowing oxygen or air heated to 2000–5000 K through the microwave irradiation. This microwave plasma exhibits satisfactory stability and can operate at pressure 1 bar. The maximum output power of the microwave generator is 5 kW.
Figure 1. (Colour online) Schematic drawing of the microwave plasma unit. 1 – microwave generator; 2 – plasmatron; 3 –the means for insertion of SiCl4; 4 – high-temperature reactor; 5 – heat exchanger; 6 – the means for insertion of the silane; 7 – low-temperature reactor; 8 – filter; 9 – dosing device for SiCl4; 10 – dosing device for silane; 11 – plasma-forming gas; 12 – carrier gas for SiCl4 and 13 – carrier gas for silane.
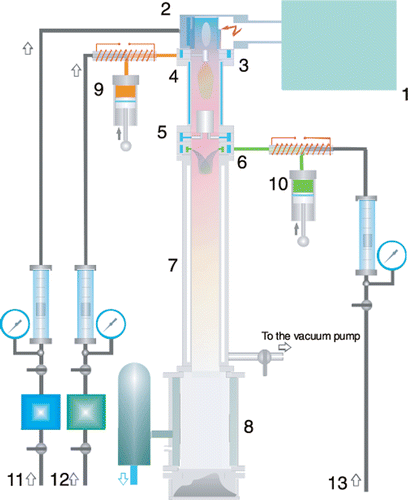
Tetrachlorosilane (SiCl4) and 3-aminopropyltrimethoxysilane served as silicon precursor and surface modifier in our preparation of silane modified-silica nanopowders, respectively. In the production of silica nanopowders, ambient air was used as plasma-forming gas. The length of the high-temperature reactor (part 4) was 200 mm. Vapours of the tetrachlorosilane mixed with carrier-gas (nitrogen mixed with air) were delivered along the flow axis through a special sprayer (part 3). The heat exchanger (part 5) that could provide the reduction of temperature to about 473 K was fixed in the bottom part of the reactor. The surface modification process was performed in a low-temperature zone of the reactor (part 7), and it was aimed at applying of the polymeric coating (amino-silane) to silica nanopowders formed in the high-temperature zone. For this purpose, the vapour of silane was directed into the flow of powder at a certain temperature. The silane vapours together with carrier-gas (nitrogen) were inserted into the cooled flow region (part 6). The length of the low-temperature reactor was 600 mm. To provide isothermal flow along the whole length of the reactor, its inside wall was made of thin stainless steel, and air inside the space between the inside and outside walls was evacuated using a vacuum pump. Such design provided minimum heat loss on the reactor wall.
The operational conditions are listed in . Atmospheric air served as the gas to form the plasma, as the carrier and for cooling. The operating current was set at 1.2 A. The silicon precursor materials were decomposed by the thermal energy of the plasma and became oxidised to silica. The synthesised nanopowders were characterised with an X-ray diffractometer (Philips 1700) equipped with a graphite-crystal monochromator for phase analysis. The diffraction pattern was obtained on scanning at a 2θ step size 0.04°. Transmission electron microscopy and electron energy loss spectroscopy (JEOL JEM-2100 F) have been used for the direct microstructural imaging and chemical analysis of surface modified-silica nanopowders.
Table 1. Process conditions for the preparation of silane-coated silica nanopowders.
3. Results and discussion
The microwave generate a plasma through the dissociation and recombination of gaseous ions and electrons that transfer the heat necessary for chemical reactions to occur. The thermal energy released during the recombination serves to decompose the chemical precursors. In typical microwave plasma, the chemical precursor of the reaction is subjected to rapid heating followed by evaporation, thermal dissociation and recondensation that occur in milliseconds to produce ultrafine powders. The desired size and size distribution of particles is controllable on manipulating the processing parameters. In order to obtain silica nanopowder with polymeric coating, a two-step microwave process was designed. 3-Aminopropyltrimethoxysilane is suitable for thermal activation of polymerisation, were used as surface modifier.
For polymerisation, it is necessary to provide an extended reaction zone with the temperature sufficient for polymerisation but not exceeding the temperature of degradation of specific polymer. For the above substances, the admissible temperature is in the range of 423–523 K. As the flow temperature at the exit of the standard reactor is about 1273 K, the heat exchanger (part 5) that could provide the reduction of temperature to about 473 K was fixed in the bottom part of the reactor.
In the preparation of silane-coated silica nanopowders, silica nanopowders were formed at the first stage of the reaction zone. In the plasma reaction region, the following reaction occur, the silicon atom becomes oxidised after the dissociation of SiCl4.
For coating the as-synthesised silica nanopowders with silane, a second precursor dosing device was inserted at part 6 of the microwave plasma unit. At this position, amino-silane was evaporated and injected into the lower portion of the plasma region. When the as-synthesised silica nanopowders travel down to the lower portion of the reaction chamber (part 7), the silane can then be encapsulated on the surface of the as-synthesised silica nanopowders before collecting by the filter (part 8). It is important that the first and second precursor dosing devices were operated simultaneously during the microwave plasma process. Once the respective nanopowders are formed at the high-temperature reactor, it can be coated with a second material at the low-temperature reactor where the second dosing device was located.
XRD analysis shows that the silica nanopowders are amorphous in nature. displays the TEM images of the silane-coated silica nanopowders. According to the TEM analysis, the average particle size is about 20 nm. It can be observed that the silica nanopowders were coated with a silane layer with thickness of about 20 nm so that the silica nanopowders are interconnected with each other. shows the image-EELS analysis carried out on silane-coated silica nanopowders. The bright areas represent the corresponding element being mapped. A comparison of these images clearly reveals that the silica nanopowders were covered with a thick layer of amino-silane.
4. Conclusion
Surface modification of nanopowders in microwave plasma process was demonstrated. The silica nanopowders were uniformly coated with a thick layer of amino-silane. Surface modification in microwave plasma is a simple, direct and easy to control process without using any solvents. Moreover, the method is applicable to not only silica nanopowders but also other types of materials such as metal or metal nitride nanopowders.
References
- Toshima , N and Yonezawa , T . 1998 . Bimetallic nanoparticles: Novel materials for chemical and physical applications . New J. Chem. , 22 : 1179 – 1201 . doi: 10.1039/a805753b
- Ma , JZ , Hu , J and Zhang , ZJ . 2007 . Polyacrylate/silica nanocomposite materials prepared by sol–gel process . Eur. Polym. J. , 43 : 4169 – 4177 . doi: 10.1016/j.eurpolymj.2007.06.051
- Bokobza , L , Garnaud , G and Mark , JE . 2002 . Effects of filler particle/elastomer distribution and interaction on composite mechanical properties . Chem. Mater. , 14 : 162 – 167 . doi: 10.1021/cm010462r
- Kim , S , Kim , E , Kim , S and Kim , W . 2005 . Surface modification of silica nanoparticles by UV-induced graft polymerization of methyl methacrylate . J. Colloid Interface Sci. , 292 : 93 doi: 10.1016/j.jcis.2005.09.046
- Moncada , E , Quijada , R and Retuert , J . 2007 . Nanoparticles prepared by the sol–gel method and their use in the formation of nanocomposites with polypropylene . Nanotechnology , 18 : 335606 doi: 10.1088/0957-4484/18/33/335606
- Kogiso , M , Yoshida , K , Yase , K and Shimizu , T . 2002 . One-dimensional organization of copper nanoparticles by chemical reduction of lipid-copper hybrid nanofibers . Chem. Commun. , 21 : 2492 – 2493 . doi: 10.1039/b208223c
- Munoz , JE , Cervantes , J , Esparza , R and Rosas , G . 2007 . Iron nanoparticles produced by high-energy ball milling . J. Nanoparticle Res. , 9 : 945 – 950 . doi: 10.1007/s11051-007-9226-6
- Quinn , BM , Dekker , C and Lemay , SG . 2005 . Electrodeposition of noble metal nanoparticles on carbon nanotubes . J. Am. Chem. Soc. , 127 : 6146 – 6147 . doi: 10.1021/ja0508828
- Seto , T , Hirasawa , M , Aya , N , Suzuki , N , Yoshida , T , Kawakami , Y and Ozawa , E . 2000 . Synthesis of size-selected silicon nanoparticles by laser ablation . J. Aerosol Sci. , 31 : 628 – 629 . doi: 10.1016/S0021-8502(00)90637-2
- Palgrave , RG and Parkin , IP . 2008 . Surfactant directed chemical vapour deposition of gold nanoparticles with narrow size distributions . Gold Bull. , 41 : 66 – 69 . doi: 10.1007/BF03215625
- Dreesen , L , Cecchet , F and Lucas , S . 2009 . DC magnetron sputtering deposition of titanium oxide nanoparticles: Influence of temperature, pressure and deposition time on the deposited layer morphology, the wetting and optical surface properties . Plasma Process. Polym. , 6 : S849 – S854 . doi: 10.1002/ppap.200932201
- Chau , JLH , Hsu , MK , Hsieh , CC and Kao , CC . 2005 . Microwave plasma synthesis of silver nanopowders . Mater. Lett. , 59 : 905 – 908 . doi: 10.1016/j.matlet.2004.10.068