Abstract
(x = 0.12) nanofibres have been successfully prepared by sol-gel method, electrospinning and subsequent heat treatment. The prepared nanofibres were characterised via X-ray diffraction (XRD), transmission electron micrograph (TEM) and superconducting quantum interference device (SQUID). The XRD revealed that the crystal structure of samples was hexagonal magnetoplumbite structure at calcination temperature from 900 °C to 1100 °C. The TEM showed that the ferrite nanofibres had a smooth morphology and a bamboo joint structure, and the diameter of nanofibres increased with the increase of sintering temperature. The SQUID revealed that there were some intriguing changes in magnetic properties with the variation of sintering temperature or altering calcination time, and the optimised magnetic property of samples was Ms 70.76 emu/g, Mr 36.35 emu/g and Hc 6.26 kOe at 950 °C for 2 h, the corresponding grain size was 39.30 nm. Meanwhile, the nanofibres display more significant improvements in the magnetic properties than the nanoparticles obtained by the sol-gel process, which was probably due to the anisotropic morphology and the cylindrical magnetic domain of ferrite nanofibres.
1. Introduction
The strontium ferrite with M-type magnetoplumbite structure showed relatively high saturation magnetisation (Ms), coercivity (Hc), Curie temperature, uniaxial magnetic anisotropy, excellent chemical stability and low cost.[Citation1,2] In view of those merits, it has attracted great attention in high-density magnetic recording media, microwave devices and so on. In order to achieve better magnetic property and wide-ranging application, the samples with different morphologies including nanoparticles, thin film and nanofibres were prepared by various methods separately. For example, sol-gel auto-combustion method,[Citation3] dc magnetron sputtering [Citation4] and electrospinning.[Citation5] Nanofibres had been explored as a focus in numerous relative fields [Citation6] due to a high length–diameter ratio: anisotropy characteristics and large surface-to-volume ratio, and the method of preparation was adopted respectively by drawing,[Citation7] solvothermal [Citation8] and electrospinning.[Citation5] Among these techniques, electrospinning technology has been received extensive applications due to its simple preparation, versatility in a variety of polymeric fibres and producing fibres with the submicron range consistently,[Citation9,10] but it is difficult to achieve by other techniques. However, there were also some defects of traditional electrospinning, such as the products disorderly arranging, non-uniform in shape and size, adhesion and discontinuous. To solve these problems the electrospun set-up was improved.
Up to now, some nanofibres have been studied through single doping in M-type strontium ferrite with Al3+, Ce3+ and La3+ severally by the means of electrospinning process,[Citation11,12] and substituted strontium ferrite nanofibres reveal some improvement in magnetic properties. However, the intrinsic magnetic properties were greatly improved by the partial substitution of Sr and Fe by La and Co,[Citation13] and lanthanum- and cobalt-codoped strontium ferrite (SLFC) nanofibres have rarely been reported so far.
In the present work, SLFC nanofibres were prepared by improved electrospinning apparatus. The results exhibited some amazing alterations in structure, morphology and magnetic properties with increasing calcination temperature or altering calcination time.
2. Experimental details
The fabrication process of SLFC nanofibres was similar to the process described in our previous paper,[Citation14] which consisted of sol-gel preparation, electrospinning and calcination.
2.1. Materials
Iron nitrate nonahydrate (Fe(NO3)3·9H2O, 99.5%, A.R. Tientsin Kaixin Chemical Reagents Co.), strontium nitrate (Sr(NO3)2, 99.5% A.R.), cobalt(II) nitrate hexahydrate (Co(NO3)2·6H2O, 99% A.R.), lanthanum nitrate hexahydrate (La(NO3)3·6H2O, 99% A.R.) and PVP ((C6H9NO)n, remanent magnetism (Mr) = 10,000, N-poly-vinylpyrrolidone K-30).
2.2. Preparation of sol-gel
The mass of Sr(NO3)2, La(NO3)3·6H2O, Fe(NO3)3·9H2O and Co(NO3)2·6H2O with 1−x:x:12−x:x molar ratios of Sr:La:Fe:Co was accurately weighed by electronic scales. Appropriate Sr(NO3)2 was added into 3 mL distilled water and the others were dissolved in 3 mL ethanol. After the solutions were well mixed and PVP was added into the obtained solution, the concentration of PVP in the resultant sol-gel was 15 wt%. Last, it was magnetically stirred for about 24 h at room temperature to form a homogeneous viscous solution for electrospinning.
2.3. Preparation of SLFC nanofibres and nanoparticles
In order to improve morphologies and decrease diameter of nanofibres, the self-assembly electrospun set-up was improved elaborately, which was adopted with combination pinpoint. Four single crystal copper threads with 20 μm diameter were embedded into the needle respectively. The needle as the positive electrode was connected to a high-voltage supply, and aluminium foil that collected the composite fibre was wrapped over a rotating drum as the ground collector through metallic brush. The optimum conditions for the preparation of SLFC nanofibres as follows. The width of aluminium foil was limited to 2.5 mm, and the rolled collector with the diameter of 180 mm had a rotating speed about 1500–2000 rpm, distance between the positive electrode and the ground collector was 10 cm, the applied voltage was 9 kV and the Sol was fed at a rate of 0.5 mL/h by a syringe pump during the electrospinning process.
The as-spun fibres were dried at 50 °C for 12 h in an air atmosphere. The dried fibres were transferred to a combustion boat, and sintered subsequently in the Muffle furnace at rate 5 °C/min under the air atmosphere.
Meanwhile, the SLFC nanoparticles were prepared via sol-gel in order to compare the performance between nanofibres and nanoparticles. Part of the resultant viscous solution was evaporated at 70 °C in air atmosphere until the gel was formed; this gel was dried at 90 °C to obtain dry gel. The dry gel was calcined subsequently in the muffle furnace at rate 5 °C/min for 2 h at 950 °C under the air atmosphere.
2.4. Characterisation
The resultant nanofibres were characterised by X-ray diffraction (XRD), transmission electron micrograph (TEM) and superconducting quantum interference device (SQUID magnetometer). Structural analyses of fibres were carried out on XRD (D/Max-2400X), and XRD generator was equipped with a Cu Kα radiation (,
). The magnetic properties of the nanofibres were investigated at room temperature by SQUID magnetometer (MPMS XL-7) with a maximum magnetic field of 7 T. The diameter and morphology of as-spun and resultant nanofibres were measured by SEM (JSM-6700F) and TEM (JEM1200EX), respectively.
3. Results and discussion
3.1. Structural analyses
The XRD patterns of SLFC nanofibres annealed at different temperature are presented in . Obviously, it is concluded from the figure that the crystal structure of SLFC does not transform and keeps hexagonal magnetoplumbite structure from 900 °C to 1100 °C. However, the second phase () exists below 950 °C. The corresponding peaks for M-type ferrite become sharper and narrower with calcination temperatures increased from 900 °C to 1100 °C, which indicates that crystallisation has improved and the grain size gets larger according to the Scherer′s equation.
Figure 1. XRD pattern of the SLFC/PVP composite nanofibres calcined at different temperatures: (a) 1100 °C; (b) 1050 °C; (c) 1000 °C; (d) 950 °C and (e) 900 °C.
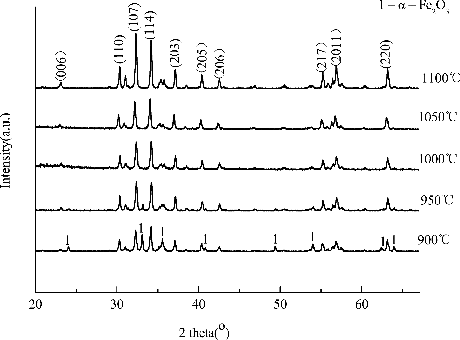
The crystallite sizes were estimated from the XRD line broadening of the peak (107), (114), (006), (110) by the classical Scherer relationship , where
(nm) is the diameter of the grain, K is a constant (shape factor) with a value of 0.89, B is the half-maximum line width and
(
) is the wavelength of the X-rays. Results show that the average grain size was calculated approximately from 54 nm to 36 nm in .
Table 1. The average grain size at different temperature.
3.2. Morphology analysis
shows the SEM image of the as-spun composite nanofibres before being calcined. While reveals the typical TEM images of the samples corresponding to the calcination temperature from 950 °C to 1100 °C for 2 h. Compared with those images, the average diameter of the fibres in is smaller than the as-prepared composite fibres before being calcined due to the complete decomposition of PVP. reveals that the resultant nanofibres generally demonstrate the obvious bamboo-like structure, high aspect ratio and smooth morphologies; however, nanofibres sintered at 950 °C for 2 h show a much more uniform diameter in (a), the diameters of resultant nanofibres increase approximately from 55 nm to 130 nm with the increasing of sintering temperature (950–1100 °C).
3.3. Magnetic analysis
The hysteresis loops of the SLFC nanofibres were revealed at various sintering temperature for 2 h in . The excellent magnetic characteristic is obtained at 950 °C, probably due to small grain size of the calcined samples. The Ms and Mr of the samples declined firstly, and then increased with enhancing calcined temperature. The sample calcined at 1050 °C shows the lowest value of the Mr and Ms, which is probably connected with the merging and growth of grains. The grain size and morphology of nanofibres were influenced by the calcination temperature;[Citation5] however, the pattern shows that the sample calcined at 1000 °C exhibits the relative Hc with 4837.51 Oe for the abnormal grain growth in and .
Table 2. The Hc, Ms and Mr of SLFC nanofibres measured under different sintering temperatures.
Figure 4. Typical hysteresis loops for the SLFC nanofibres calcined at different temperatures with same holding time.
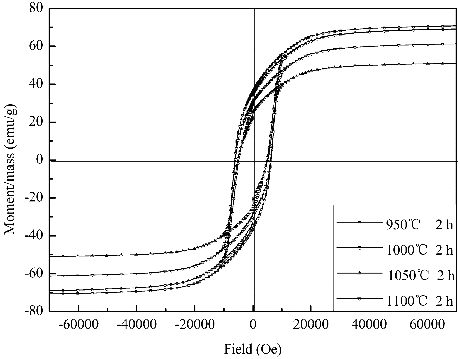
Hysteresis loops of the samples calcined at 950 °C for 2, 4 and 6 h are shown severally in . The Hc, Mr and Ms of the samples decrease gradually with increasing calcination time, respectively. The sample calcined for 2 h exhibits higher Hc with 6264.57 Oe. Obviously, it is shown that the value of Hc will reduce with a further increase of the calcination time in , which relates with the particle aggregation and grain growth for such a long calcination time, because prolonging annealing time leads to the larger particle size and the larger grain size contributes to a lower Hc and higher Ms.[Citation15]
Table 3. The Hc, Ms and Mr of SLFC nanofibres were measured under different holding time.
Table 4. The Hc, Ms and Mr of SLFC nanofibres and nanoparticles measured at 950 °C for 2 h separately.
Figure 5. Hysteresis loops of the sample SLFC nanofibres calcined at 950 °C with different holding time.
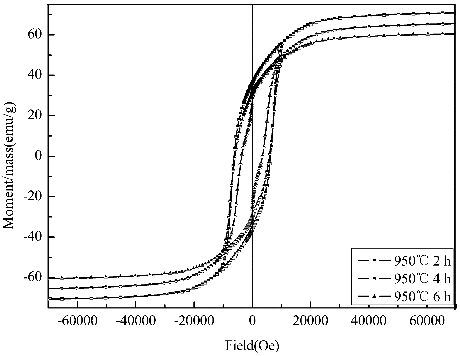
The hysteresis loops of SLFC nanofibres and nanoparticles are displayed in . shows that the nanofibres reveal much better magnetic properties than the nanoparticles obtained by the sol-gel process. It is clearly exhibited that the Hc value of nanofibres is much larger. Meanwhile, it has been reported that the maximum values of Hc with SLFC nanoparticles obtained by the ceramic process is 401.5 KA/m (5042.84 Oe),[Citation16] and it is around 24.2% smaller than the nanofibres obtained in the present work, implying the hard magnetic characteristic of the SLFC nanofibres improved significantly, which means that the nanofibres have an advantage in anisotropy characteristics, because the smaller diameter may prompt crystal growth along the axial direction of nanofibres; this result may lead to enhancing value of the Hc. The value of Mr and Ms is slightly higher than particle, which means that the codoped nanofibres are more suitable for high-density recording materials.
Figure 6. Typical hysteresis loops for the SLFC nanofibres and nanoparticles sintered at 950 °C for 2 h separately.
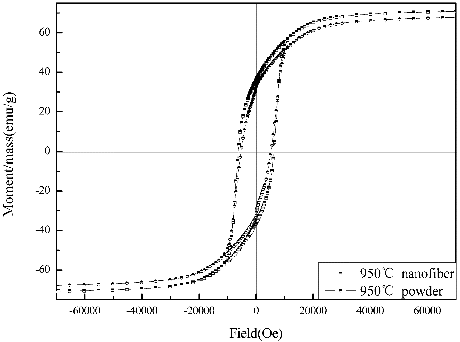
In the present work, the magnetic properties of SLFC nanofibres are better than La3+, Ce3+ ions-doped strontium ferrite nanofibres,[Citation12] The one reason probably is that Co2+ anisotropic constant is larger about two orders of magnitude than Fe3+ in the similar crystal bits.[Citation17] The other, La3+, may improve the intrinsic magnetic properties. Hc value of SLFC nanofibres is slight lower than strontium ferrite nanofibres with the non-magnetic Al3+ substitution at room temperature, but the Ms and Mr values of the nanofibres are superior to strontium ferrite nanofibres with Al3+ substitution. These results can be explained through the non-magnetic Al3+ ions that replace the magnetic Fe3+ ions, which suppress the superexchange interactions resulting in the magnetic collinearity breaking down.[Citation11]
4. Conclusions
SLFC magnetic nanofibres have been combined via sol-gel method, electrospinning and subsequent heat treatment technique. The prepared nanofibres with the bamboo joint structure, high aspect ratio and smooth morphologies are fabricated, and the diameter of nanofibres increases with the increase of sintering temperature. The high Hc (6.26 kOe) and Ms (70.76 emu/g) of the sample sintered at 950 °C for 2 h were observed at room temperature. The results of SQUID show that the coercivity decrease gradually with increasing calcination time, presumably due to the particles’ aggregation and grain growth for such a long calcination time. However, with enhancing calcination temperature, the Ms and Mr first decrease, then increase slightly. The nanofibres show better magnetic properties than the nanoparticles obtained by the sol-gel processing, which is probably superior in anisotropy characteristics because of its morphology characteristics. It is concluded that the codoped nanofibres are more suitable for high-density recording materials and various microwave devices.
Acknowledgements
The authors gratefully acknowledge the financial support from the National Natural Science Foundation of China (Grant No. 50873047) and Foundation of Gansu Education Department of China (Grant No. 0903-02).
References
- Zlatkov BS, Nikolic MV, Aleksic O. A study of magneto-crystalline alignment in sintered barium hexaferrite fabricated by powder injection molding. J Magn Magn Mater. 2009;321:330–335.
- Pullar RC, Taylor MD, Bhattacharya AK. A halide free route to the manufacture of microstructurally improved M ferrite (BaFe12O19 and SrFe12O19) fibres. J Eur Ceram Soc. 2002;22:2039–2045.
- Wang Z, Zhong L, Lv J, Qian H, Zheng Y, Fang Y, Jin M, Xu J. Microwave-assisted synthesis of SrFe12O19 hexaferrites. J Magn Magn Mater. 2010;322:2782–2785.
- Kaewrawang A, Ghasemi A, Liu X, Morisako A. Underlayer dependence of microtexture, microstructure and magnetic properties of caxis oriented strontium ferrite thin films. Thin Solid Films. 2010;518:7059–7063.
- Shen X, Liu M, Song F, Meng X. Structural evolution and magnetic properties of SrFe12O19 nanofibers by electrospinning. J Sol-Gel Sci Technol. 2010;53:448–453.
- Maensiri S, Sangmanee M, Wiengmoon A. Magnesium ferrite (MgFe2O4) nanostructures fabricated by electrospinning. Nanoscale Res Lett. 2009;4:221–228.
- Ondarcuhu T, Joachim C. Drawing a single nanofibre over hundreds of microns. Europhys Lett. 1998;42:215–220.
- Chen D, Qiao X, Qiu X, Chen J, Jiang R. Convenient synthesis of silver nanowires with adjustable diameters via a solvothermal method. J Colloid Interface Sci. 2010;344:286–291.
- Bhardwaj N, Kundu SC. Electrospinning: a fascinating fiber fabrication technique. Biotechnol Adv. 2010;28:325–347.
- Lima HS, Kimb B, Suha KD. Multiwalled carbon nanotube/SiO2 composite nanofibres prepared by electrospinningy. J Exp Nanosci. 2011;5:329–336.
- Liu M, Shen X, Song F, Xiang J, Meng X. Microstructure and magnetic properties of electrospun one-dimensional Al3+-substituted SrFe12O19 nanofibers. J Solid State Chem. 2011;184:871–876.
- Li C, Wang J. Electrospun SrRe0.6Fe11.4O19 magnetic nanofibers: fabrication and characterization. Mater Lett. 2010;64:586–588.
- Kools F, Morel A, Grössinger R, Breton JML, Tenaud P. LaCo-substituted ferrite magnets, a new class of high-grade ceramic magnets; intrinsic and microstructural aspects. J Magn Magn Mater. 2002;242–245:1270–1276.
- Dai J, Chen X. Ultralong and single-crystalline YMnO3 nanofibers synthesized by improved electrospinning. IEEE, MPES 2010; 2010; Hong Kong. p. 29–32.
- Pullar RC, Bhattacharya AK. The magnetic properties of aligned M hexa-ferrite fibres. J Magn Magn Mater. 2006;300:490–499.
- Liu X, Pablo HG, Huang K, Zhou S, Wang Y, Cai X, Sun H, Ma B. Research on La3+–Co2+-substituted strontium ferrite magnets for high intrinsic coercive force. J Magn Magn Mater. 2006;305:524–528.
- Zhong W. Ferromagnetism. Beijing: Science Publishing Company; 1998.