Abstract
The torsional fretting wear tests of Ti6Al4V alloy flat against alumina femoral ball in dry condition were carried out on a new high-precision torsional fretting-wear tester. The TiO2/P-methoxymethamphetamine (PMMA)/Ti6Al4V pair showed higher contact stiffness, friction torque, wear damage and material transfer than that of the presentation of TiO2/PMMA/Al2O3 pairs. The mechanisms of torsional wear under different counterbodies were discussed in detail. The mechanisms of torsional fretting wear of aluminium alloy are mainly oxidative wear, abrasive wear and delamination in the three fretting regimes. The torsional fretting running regimes transferred from partial slip regime (PSR) to SR were analysed; however, the mixed fretting regime was never appeared in this test. In PSR (lower angular displacement amplitudes), only a dint was found after the tests. The kinetics behaviours and damage mechanism of Ti6Al4V alloy under different angular displacement amplitudes with friction torque and dissipation energy, which are strongly dependent upon the imposed angular displacement amplitudes and presented in three stages, were discussed in detail.
1. Introduction
The use of artificial joints for the treatment of degenerative diseases of the hip and knee is becoming widespread. Nowadays, there are several bioimplant materials available for total joint replacements (TJR). Early studies of clinical results provide evidence that loosening of one or both components of the TJR occurs in at least 10% to as high as 70% in patients 10 years after the surgery.[Citation1] As such, three different sliding modes (tangential, radial, and circumferential) have been defined in the literature.[Citation2,3] Torsional wear is one of the main motion modes of joints, and torsional fretting can be defined as the relative motion induced by reciprocating torsion under an oscillatory vibratory environment. Several solutions have been proposed to understand torsional contact and the mechanics of its behaviour.[Citation4,5] Briscoe et al., for example, found that the damage brought about by torsional contact was more detrimental than those reduced by the rolling or rotating contacts.[Citation6,7] However, the torsional wear behaviour of TiO2/P-Methoxymethamphetamine(PMMA)/Ti6Al4V alloy and TiO2/PMMA/Al2O3 has not been clearly discussed. In this research, a new testing method is used to reveal the damage characteristics of TiO2/PMMA/Ti6Al4V alloy and TiO2/PMMA/Al2O3 caused by torsional fretting wear. There have been many tribological research focused on rolling wear, reciprocating tangential sliding and pin-on-disc sliding,[Citation8–11] and advance hip joint simulators were used to investigate the relative performance of artificial joint. These test method revealed the wear resistance of some artificial replacement materials. As a basic motion fashion, torsional motion occurs at different joints in human body such as hip joint, shoulder joint, temporomandibular joint and so on. However, relatively few studies focused on the torsion motion, and the results from previous reports cannot adequately reflect the damage originated from torsion wear.
PMMA is an amphetamine-related designer drug available in the illicit drug market and can be found by itself in ecstasy-like tablets with logos such as ‘Mitsubishi’, ‘E’, ‘Superman’ and ‘Elephant’ (EMCDDA. 2003). However, it is mostly found in combination with 3,4-methylendioxymethamphetamine (ecstasy, MDMA) or with other substances such as para-methoxyamphetamine, amphetamine, ephedrine, etc., causing serious health and social impairments.[Citation12] In the torsional contact configuration, the resulting contact zone kinematics was found to have a very pronounced influence on the accumulation, the compaction and the displacement of the debris particles from the contact. In this research, a new testing method would be applied to reveal the damage characters of TiO2/PMMA/Ti6Al4V alloy and TiO2/PMMA/Al2O3 caused by torsional wear.
2. Experimental details
Torsional fretting tests of the TiO2/PMMA in contact configuration of ball-on-flat were carried out on a new torsional fretting tester (). Flat TiO2/PMMA specimens (20 mm × 10 mm × 10 mm) were polished to an average roughness of Ra = 0.2 μm. Medical Al2O3 ceramic femoral head ball and Ti6Al4V titanium alloy ball (both with a diameter of 28 mm) were selected as the against counterbodies. The plate specimen TiO2/PMMA was fixed on the upper holder to link a six-axis torques/forces sensor through a spring suspension. The three components of the torque and force (tangential, normal and transverse- x-, y- and z-direction) were measured directly at the contact interface. A ball specimen was mounted on the lower holder which was fixed on the low-speed reciprocating rotary motor system. Angular displacement of the contact pair was measured and controlled by a sensor in the motor system and was acted as the control signal fed back to the control unit of the tester. In this study, torsional fretting tests were performed under the normal load of 100 N at a constant rotary speed of 0.2º/s. The torsional angular displacement amplitudes were set as 0.1º, 0.2°, 0.5º, 2.5º, 15º and 45º, and the number of cycles varied from 1 to 1000. After testing, the fretting scars were measured by a profilometer (AMBIOS XP-2), and the morphologies of wear scar were examined by scanning electron microscope (SEM, Quanta200) and X-ray photoelectron spectroscopy (Axis ultra).
3. Results and discussion
3.1. T–θ curves analysis
Ft–D curve is used in tangential fretting and radial fretting to analyse kinetics behaviours, T–θ curve is applied in torsional fretting mode correspondingly. shows evolution of T–θ curves under a normal load of 90 N and angular displacement of 0.95° ((a)–(c)) and 85° ((d)–(f)). In both situations, the curves generally display quasi-parallelogram shape. When the angular displacement is 0.95°, the curves are much slimmer at the first 50 cycles. After 100 cycles, no considerable changes in the shape of curves are observed. And the friction torque is slightly increased with the number of cycles. When the angular displacement is 85°, the friction torques are much higher than those of 0.95°.
Figure 2. T–θ curves of TiO2/PMMA under various torsional angular amplitudes and cycles, Fn = 100 N. (a), (c), (e) and (g) TiO2/PMMA/Al2O3; (b), (d), (f) and (h) TiO2/PMMA/Ti6Al4V.
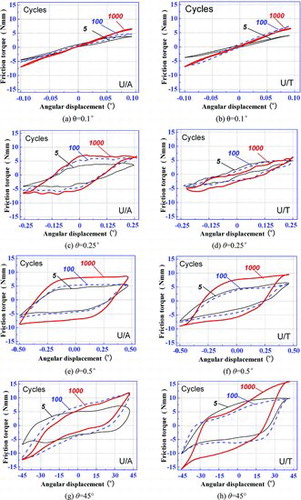
In general, the slope of friction–displacement represents stiffness which is affected by system stiffness and contact stiffness. The system stiffness can be considered as a constant during the whole testing process. Therefore, the change of slope reflected the change of contact stiffness. The area enclosed by the T–θ curves represented friction energy that has been dissipated during the cycle. The evolution of contact stiffness and dissipated energy per cycle is illustrated in (h). It can be seen that the value of contact stiffness rises rapidly at the first 200 cycles, and then it gradually reached a steady state. It is observed that the graphical representation of the energy dissipated per cycle as a function of time is similar to that of the contact stiffness. It may be explained that work hardening happened during torsional fretting wear.
In addition, it was obvious that the contact stiffness monotonically increased as a function of the number of cycles. From the slope of T–θ curves, the contact stiffness was extracted directly. Usually, the contact stiffness was found to be dependent on the loading conditions and sliding surface roughness. Increased contact stiffness may bring two effects on the torsional fretting processing. First, the increased stiffness of the tribo-pairs reduces the effect of vibrations on the slider interface. Second, plastic deformation and damage accumulation below the worn surfaces are enhanced.
3.2. Friction torque analysis
As the basic and important information in rotary motion, just like the significance of friction force in tangential wear, friction torque of torsional fretting was necessary to discuss in detail. displays the friction torque variation under various angular displacements and different normal loads. Generally, there were three typical stages occurred under all test conditions. In stage I (initial stage); the friction torques values were very low owing to the protection of the adsorbed and polluted surface films. After 10 or several decade cycles, the curves entered into the stage II (climbing stage), and the friction torques increased quickly. And then, in stage III (steady stage), the curves accessed a steady state, corresponded to the slight fluctuation within a narrow range.
(a) shows the evolution of friction torques of TiO2/PMMAcarried out at 100 N with various angular displacements. When θ = 0.1°, fretting run in PSR, and the friction torques kept at a lower level with approximate 4 N mm at about initial 100 cycles. Then the torque slowly rose as the increasing cycles and the value reached the steady stage with a final value of 6.2 N mm. There was a similar evolution for the torque under other angular displacements. Obviously, the process of stages I and II was shorten and torque reached the steady stage early. Compared with the curves of TiO2/PMMA/Ti6Al4V alloy and TiO2/PMMA/Al2O3 under 100 N ((b) and (a)), the latter usually presented a larger value.
3.3. Wear damage analysis
Wear morphologies and profiles in the PSR are exhibited in . The centre region is a well-known sticking zone and no relative slip occurs at the contact interfaces. This means that the low tangential force and relative high normal load were insufficient to drive relative motion at the contact centre. The wear, shaped like a narrow annulus, occurred on the contact edge. Under torsional fretting conditions, wear debris cannot easily be discharged from the contact interfaces, especially when angular amplitude is very low. Generally, the presence of a little TiO2 does not give rise to any differences in the appearance of the worn surfaces. Therefore, the emphasis is on discussing the difference in wear behaviour for different counterfaces. It seems like the first wear step is micro-cracking of the resin between the fibres. The worn morphologies under different tribo-pairs were shown in and .
Figure 5. SEM micrographs of the worn scars under torsional fretting condition. Fn = 100 N, θ = 15°. (a), (b) and (c) TiO2/PMMA/Al2O3; (d), (e) and (f) TiO2/PMMA E/Ti6Al4V.

For the alumina femoral head, smooth worn surface without any trace could be observed at θ = 0.5° ((a)), while slight ploughing could be found at the same condition with alumina femoral head and Ti6Al4V alloy ball contact ((b)). At small displacements, the torsional fretting was running at partial slip regime (PSR) which means that the centre was sticking and micro-slip occurred at the contact edge.
With the increasing angular displacements, severe surface damage occurred at both tribo-pairs and different characteristics appeared. shows the worn photomicrography of TiO2/PMMA under a high angular displacement of 15° and the debris morphology at the contact edge of the scar. Brown particles could be found at the contact edge of the contact. It was clear that debris is formed from the steel ball being oxidised by tribo-chemical action ((a)). On the steel ball surface, some oxidative products cover at the wear zone and a large amount of fine oxidative debris with brown colour were found to scatter at the contact edge after 1000 cycles ((a) and (b)). Similar results were mentioned in Geringer's research, which emphasised that, when linking with orthopaedic fields, these oxides could be assimilated by bone cells around a femoral stem where friction occurs between the stem and bone cement. When the test duration was extended to 10,000 cycles, a transfer film of TiO2/PMMA/Ti6Al4V and TiO2/PMMA/Al2O3 film was formed at the surface of the ball specimen ((c) and (d)). Thus, TiO2/PMMA adhesion also probably contributed to the large bulge observed.
The damage of TiO2/PMMA under other test modes had been widely examined by many researchers. When a polymeric material was rubbed against metal surfaces, adhesion, abrasion and fatigue were the most recognised wear modes.
More ripples were found on the worn surface of TiO2/PMMA /Al2O3 than that of and TiO2/PMMA /Ti6Al4V alloy ball. (a) showed the mean size of ripples below 5 μm × 2 μm. Delamination and cracking appeared at large angular displacement, which corresponded to obvious deformation ((b) and (c)). The ripples perpendicular to the sliding direction on the scars have been discussed in early studies under the condition of sliding. In this study, perhaps there was the same mechanism due to the plastic flow of the polymer. Because the ripples on TiO2/PMMA/Al2O3 were more easily broke off when they are subjected to the cross-directional shearing, more wear particles were removed and higher wear mass loss of TiO2/PMMA would be induced. For TiO2/PMMA/Ti6Al4V alloy ball contact, the characters of abrasive wear were presented adequately ( and )
Figure 6. SEM micrographs of the ripple on worn scars, TiO2/PMMA/Al2O3. (a) Fn = 100 N, θ = 5°; (b) Fn = 100 N, θ = 15°; (c) Fn = 200 N, θ = 45°.
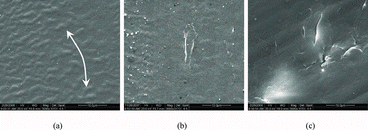
Figure 7. SEM micrographs of the scratch on worn scars of TiO2/PMMA/Ti6Al4V alloy ball. (a) Fn = 100 N, θ = 15°; (b) Fn = 200 N, θ = 15°; (c) Fn = 200 N, θ = 45°.

The surface morphologies of the corresponding balls were observed via optical microscope. Less material transferring on the worn surfaces of the ceramic ball specimens for the TiO2/PMMA/Ti6Al4V contact was detected than that of the TiO2/PMMA/Al2O3 alloy ball contact (). It might be the reason why the severe adhesion occurred on the interfaces of the TiO2/PMMA/Ti6Al4V contact. It could be seen clearly that TiO2/PMMA had transferred to the titanium ball counterpart exhibiting morphology of concentric circles. Therefore, it could be concluded that a transfer film of TiO2/PMMA was formed on the surface of the ball specimen. However, no titanium was found on the surface of TiO2/PMMA/Ti6Al4V, quite different from the damage occurred at metal materials for the different deformation behaviours of polymer.
Figure 8. (Colour online) Optical micrographs of worn ball surface, θ = 45º, Fn = 100 N. (a) worn Al2O3 ball; (b) worn Ti6Al4V ball.
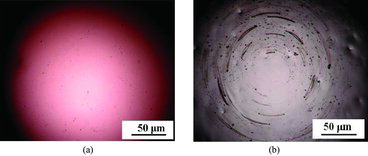
The worn profiles on TiO2/PMMA surfaces under different angular displacements were given in . The diameter (D) and maximal depth (H) of the worn scar were analysed in detail. The outer lines clearly demonstrated that the worn profile for the TiO2/PMMA/Ti6Al4V was deeper or wider ((a)) than that of TiO2/PMMA/Al2O3 (DA > DT and HA > HT). When θ increased to a large value of 45°, the difference of the worn width (ΔD) and the worn depth (ΔH)) enlarged. In addition, some shakes occurred on the profile of TiO2/PMMA/Ti6Al4V at 200 N, which proved the deep scratches.
As observed in the SEM micrographs of the untreated wear scars in , abrasive wear was manifested by grooves, pits and scratches on the worn, flat specimen surfaces. The distinct plastic grooves and deformation, detached metallic particles and debris accumulation were clear under high magnification of the worn surfaces. The external third body particles (debris) were definitively eliminated from the contact zone and distributed in a crown flake around the fretting scar. As a result, the wear mechanisms of the Ti6Al7Nb alloy were abrasive wear and oxidative wear.
The differences can be explained by the following reasons. First, the Al2O3 ceramic ball had a higher hardness (Hv = 1920) and elastic modulus (E = 380 GPa) than that of Ti6Al4V alloy (Hv = 465, E = 310 GPa). According the classical Hertzian contact theory, larger elastic modulus would induce a wider and deeper contact scar. Second, the Al2O3 ceramic ball had a smooth surface (Ra = 0.02 μm) than that of Al2O3 ceramic ball (R = 0.2 μm). It has been now accepted that when the metallic surface roughness is higher than 0.05 μm, the abrasion mechanism becomes significant. Therefore, since the roughness of the titanium alloy ball is 0.2 μm, abrasion is at the origin of the transfer film. At a lower angular displacement of TiO2/PMMA on a metal hard surface, lumps of polymer transferred to the counterbody. As for the lumpy transfer mechanism, the lumps of polymer were removed from asperity peaks and left adhering on the counterbody. The viscoelastic nature of the TiO2/PMMA/Ti6Al4V induced the tearing and raised lips formation. The appearance of arc-like track in the ball surface shown in (b) indicated the characteristics of this wear mechanism.
According to the results of the damage analyses, the damage law of flat TiO2/PMMA under torsional fretting conditions can be schematically outlined in . At lower angular displacement amplitudes (in the PSR), slight damage occurs. Since the damage mechanisms were almost same in the mixed fretting regime (MFR) and SR (no sticking zone in the SR), only physical models in the MFR were supplied.
Figure 9. The diameter and maximal height of the worn scar under various angular displacement and different normal loads Fn = 200 N, (DA - diameter of the worn scar of U/A; DT - diameter of the worn scar of U/T; HA - maximal height of the worn scar of U/A; HT - maximal height of the worn scar of U/T; ΔD = DA − DT; ΔH = HA − HT).
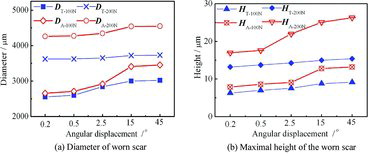
For the TiO2/PMMA/Ti6Al4V contact pair, a similar evolution in friction torques occurred during the torsional fretting process ((b)). An obvious difference, however, is that at angular displacement amplitude of 4.5° the friction torque is still present in stage I for all test cycles, and the fretting running state remains in the PSR. As such, the TiO2/PMMA/Al2O3 contact pair enters the MFR earlier compared to the TiO2/PMMA/Ti6Al4V contact pair. The distribution of the torsional fretting running regimes for the two TiO2/PMMA/Ti6Al4V contact pairs under various angular displacement amplitudes Fn = 200 N.
4. Conclusion
A comparing analysis of torsional fretting behaviour of TiO2/PMMA against different tribo-pairs was presented in this experiment. The running regime transfer from partial regime to gross SR as the increase of the angular amplitudes, and the mixed SR was not found in this research. The TiO2/PMMA/Ti6Al4V contact presented higher contact stiffness, friction torque, wear damage and material transfer than that of the TiO2/PMMA/Al2O3 contact. Damage occurred at lower angular displacement amplitudes was slighter than that of higher torsional angular displacements. The wear mechanisms of TiO2/PMMA/Ti6Al4V were combined with abrasive wear and delamination. The generation of radial ripples and micro-cracking was the main damage modes for TiO2/PMMA/Al2O3.
For both contact pairs, friction torques increased with the increase of angular displacement amplitude. Friction torques of the TiO2/PMMA/Al2O3 contact were higher than those of the TiO2/PMMA/Ti6Al4V contact under the same test conditions.
References
- Show Y, Itabashi H. Electrically conductive material made from CNT and PTFE. Diam Relat Mater. 2008;17(4–5):602–605.
- Zhaohong X, Hua LZ, Jian L, Fei FY. The effect of CF and nano-SiO2 modification on the flexural and tribological properties of POM composites. J Thermoplast Compos Mater. 2012 [first published on April 29, 2012]. doi:10.1177/0892705712443251.
- Rae PJ, Brown EN. The properties of poly(tetrafluoroethylene) (PTFE) in tension. Polymer. 2005;46(19):8128–8140.
- Wang X, Bradford PD, Liu W, Zhao H, Inoue Y, Maria J-P, Li Q, Yuan F-G, Zhu Y. Mechanical and electrical property improvement in CNT/Nylon composites through drawing and stretching. Compos Sci Technol. 2011;71(14):1677–1683.
- Xu Z. The reinforcing effect of basalt fiber and polyamide-6 on the mechanical properties of polytetrafluoroethylene composite. J Thermoplast Compos Mater. 2013 [first published on April 30, 2013]. doi:10.1177/0892705713484742.
- Ogasawara T, Moon S-Y, Inoue Y, Shimamura Y. Mechanical properties of aligned multi-walled carbon nanotube/epoxy composites processed using a hot-melt prepreg method. Compos Sci Technol. 2011;71(16):1826–1833.
- Xu Z, Li S, Qi K. Effect of environmental degradation and mechanical properties of polyamide 6-grafted carbon fiber/poly(3-hydroxybutyrate-co-3-hydroxyvalerate) composites. J Thermoplast Compos. 2013 [first published on July 26, 2013] doi:10.1177/0892705713495431.
- Steiner S, Busato S, Ermanni P. Mechanical properties and morphology of papers prepared from single-walled carbon nanotubes functionalized with aromatic amides. Carbon. 2012;50(5):1713–1719.
- Zhang J, Wang A. Study on superabsorbent composites. IX: synthesis, characterization and swelling behaviors of polyacrylamide/clay composites based on various clays. React Funct Polym. 2007;67(8):737–745.
- Cao X, Lee LJ, Widya T, Macosko C. Polyurethane/clay nanocomposites foams: processing, structure and properties. Polymer. 2005;46(3):775–783.
- Xiang Y, Peng Z, Chen D. A new polymer/clay nano-composite hydrogel with improved response rate and tensile mechanical properties. Eur Polym J. 2006;42(9):2125–2132l; Rohanova M, Balikova M. Studies on distribution and metabolism of para-methoxymethamphetamine (PMMA) in rats after subcutaneous administration. Toxicology. 2009;259(1–2):61–68.
- Kumar MA, Reddy KH, Mohana Reddy YV, Reddy GR, Naidu SV. Improvement of tensile and flexural properties in epoxy/clay nanocomposites reinforced with weave glass fiber reel. Int J Polym Mater. 2010;59(11):854–862.