Abstract
Tribochemical silica coating is a common practice to achieve suitable adhesion with intended synthetic substrates or natural tissues, and the key to this technology is the preparation of alumina abrasive coated by nano-silica (AACNS). In this paper, a novel physical method of producing silicon nanoparticles (SiNPs) that is the base to AACNS is put forward in this paper. The source of the silica coating is from SiNPs that are produced from spark erosion in deionised water, with an average size distribution between 30 and 50 nm as indicated by SEM analysis. Under optimised mixing conditions, 2 g of purified SiNPs were mixed with 20 g of alumina µ-particles (with an approximate diameter of 100 µm), in the presence of ethanol and stirred thoroughly to form a slurry. The slurry is the then co-fired in an oxidation furnace, initially heated to 120 °C for 20 minutes to evaporate the ethanol, and then re-uploaded again after compaction in a temperature of 1100 °C for 2 hours, after which AACNS are obtained. Afterwards, shear bond strength tests are applied on zirconia ceramic bars, whose surface is modified by AACNS. The result shows that average bond strength is about 12 MPa. This method also could be applied to prepare other kinds of abrasive coated by different nanoparticles for improving the bonding strength between coatings and substrates by the method of tribochemical.
1. Introduction
Developments over the last 15 years in ceramic materials science for dental applications have led to a class of high strength materials (i.e. zirconia-based ceramics), which potentially provide better fracture resistance and long-term viability compared with porcelain and other inorganic, non-metallic alternatives [Citation1,Citation2]. There is a wealth of information in the scientific literature regarding the use of zirconia (ZrO2) in dental applications [Citation2,Citation3]. Although superior in terms of mechanical performance (strength, toughness, fatigue resistance), there are some inherent problems associated with ZrO2. One problem is with adhesion to the variety of substrates (synthetics or tissues) that can be encountered in dental or other biomedical applications. Conventional cementation/attachment techniques used with ZrO2 components do not provide sufficient bond strength for many of these applications [Citation4–7]. It is important for high retention, prevention of microleakage and increased fracture/fatigue resistance, which bonding techniques be improved for zirconia-based systems. Strong resin bonding relies on micromechanical interlocking and adhesive chemical bonding to the ceramic surface, requiring surface roughening for mechanical bonding and surface activation for chemical adhesion [Citation8–10]. The use of a tribochemical silica coating is a common practice for coating zirconia-based dental ceramics with silica by the CoJet and Rocatec systems (3M ESPE; Seefeld, Germany) being the most heavily favoured commercial products utilised for applying the coating. The tribochemical technique air-abrades the ceramic surface with alumina particles that have been coated with silica, embedding/coating the surface with silica [Citation7,Citation11,Citation12]. This results in not only preparing a surface for silanisation, but also creates micromechanical retention.
Preparation of alumina abrasive coated by nano-silica (AACNS) is one of the key steps for attaining successful bonding between zirconia ceramic and resin luting cement. Currently, the methods of producing AACNS are predominantly chemical based, that includes sol–gel, silicic acid treatment, CVD and so on [Citation13]. Obviously, the overall productivity from such methods is very low [Citation14,Citation15], notwithstanding the chemical waste produced as a byproduct, which limits its applications in the field of prosthetic and implant dentistry. Hence in this paper, the focus is on the production of alumina abrasives coated by nano-silica, by using a new economically and environmentally efficient method. The silicon nanoparticles (SiNPs) used in this study are produced from spark erosion method without using any chemical reagent [Citation16,Citation17]. The microstructures of the SiNPs, AACNS and the subsequent structure of abrasives bonded to the Y-TZP are thoroughly investigated using SEM and EDS, whereas the bonding strength is measured using shear bond strength (SBS) test.
2. Materials and method
The experiment is divided into two sections; part A describes the preparation of SiNPs and Part B depicts the fabrication of AACNS.
2.1. Preparation of silicon nanoparticles
As shown in , the discharge area is submerged in a special tank, which is filled with deionised water. To improve productivity, the external circulating system is added. The electrodes (tool electrode and workpiece) are connected with polarities of pulse power, respectively. In machining, electrodes closed to each other slowly, once the suitable spark gap is achieved, the ignition of discharge is initiated by a high voltage. A channel of plasma whose temperature is up to 10,000 K was formed between the electrodes. For every pulse, discharge occurred at a single location where the electrodes materials are evaporated and melted, and then, ejected into deionised water. As a result, a small crater was generated on both surface of tool electrode and workpiece respectively. Removed materials were cooled and re-solidified to form hundreds of spherical debris particles.
Using the above machining conditions (), the mixture of debris particles and deionised water was obtained. Due to the disparity of particle size in the mixture consisting both micro and nanoparticles, the mixture was centrifuged at 1000 rpm for 10 minutes, to separate the nanoparticles, which is shown in .
Table 1. Machining conditions.
2.2. Preparation of AACNS
Silicon nanoparticles of 2 g, produced from spark erosion, was first mixed with 20 g of alumina µ-particles (average size of 100 µm bought from outsourcing) in 25 ml of ethanol solution to form a slurry. The mixture was stirred for 5 minutes after which it was co-fired in an oxidation furnace, initially to 120 °C for 5 mins to remove the ethanol and then re-uploaded again after compaction in a temperature of 1100 °C for 2 hours, after which AACNS are obtained, as depicted in . For distinguishing purposes, the product is abbreviated as AACNS. The flow chart for the complete steps of preparing AACNS is shown in .
2.3. Shear bond strength test
Twenty-four pre-sintered Yttria-stabilised zirconia (Y-TZP) blocks (KaVo Everest® ZSRonde; Kaltenbach and Voigt GmbH and Co., Biberach, Germany) (12 × 8 × 2 mm) are cut at an equal size using a low-speed saw, after which they are completely sintered. Concurrently, Nylon tubes (inner diameter: 5 mm; height: 2 mm) are filled with light polymerised resin composite (Valux PlusTM; 3M ESPE, St Paul, MN), after which together they are lightly cured for 40 seconds producing the commercial EliparTM Freelight 2 from 3M ESPE AG (Seefeld, Germany). The polymerised resin cylinders, termed as 3M ESPE for distinguishing purposes, are then removed from the nylon tubes for subsequent testing. It is to be noted that the filler of commercial composite resin from 3M consists of Barium Aluminium fluoride glass with highly dispersive silica (80–90%), whereas the base resin is made of bisphenol A-glycidyl methacrylate (Bis-GMA). As the 3M product already contains silica treated alumina abrasives, they will be used readily, whereas a separate Bis-GMA resin content will be used to bond with AACNS treated YTZP surface.
The Y-TZP blocks are categorised into three groups (8 pieces per group, with a total of 24), which were treated by different abrasive samples. Group A is sandblasted with the AACNS produced beforehand in part 2.1, whereas group B are tribochemically sandblasted with a commercial product (3M ESPE), removed from the nylon tube, from a distance of 10 mm for 15 seconds at 3 bar pressure. Finally, group C blocks are sandblasted with normal pure alumina sands from a distance of 10 mm for 15 seconds at 3 bar pressure. This is summarised in .
Table 2. List of experimental samples.
The aim of producing three set of samples is to compare and analyse the bonding strength of AACNS infused resin against 3M ESPE resin, as well as differentiate between these two types of bonding material with resin material only treated with just pure alumina particle.
Schematic diagram of testing SBS is shown in . The YTZP ceramics, separated as a Group of A, B and C are each cemented to a resin-composite cylinder using Bis-GMA resin cement (Choice: Bisco, Inc., USA). Load V is propagated along the cylinder to remove the resin from the YTZP ceramic surface and the resultant SBS is calculated. The value of the SBS was determined using, S = T/A, where S is the shear bond strength, T is the tension applied and A is the bonded area.
SBS is analysed with a universal testing machine (ElectroPulsTM 3365; Instron®, Norwood, MA) using a crosshead speed of 1.0 mm/minute after 24 hours of storage in distilled water at room temperature.
2.4. Characterisation
Field emission scanning electron microscopy (FESEM) (Hitachi S-4800 Japan) and energy-dispersive X-ray spectroscopy (EDS) are used to characterise micromorphology of alumina abrasive Y-TZP blocks surface and the material distribution. To obtain better testing quality while performing SEM, all Y-TZP blocks are sputter-coated with gold using a Baltech SCD 500 device.
3. Results and discussion
Because of commercial AACNS have been researched by many experts in all respects, hence, this part just involves the sample produced by the new method.
shows an SEM image from a typical Si nanoparticle sample produced from the electrical discharging of the silicon ingot. Although colloidal in nature, these nanoparticles readily disperse temporarily when under the effect of ultrasonic energy. Such nanoparticles have a size distribution of 30–50nm and are generally pure albeit natural oxidation, however, the effect of oxidation is nominal as shown from the EDS in .
Figure 6. Silicon nanoparticles produced from electrical discharging pure silicon ingot (a) SEM image and (b) EDS graph.
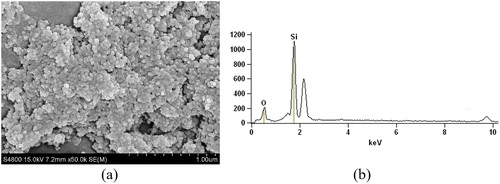
represents the typical shape of alumina microparticles. shows surface of pure alumina microparticle, it is found that there is nothing but some impurities on the surface of pure alumina. indicates the mass of nanoparticles adhere on the surface of Alumina. After obtaining AACNS, it is used to treat the surface of zirconia, the results are shown in .
Figure 7. 3D depiction of (a) pure alumina microparticle, (b) surface of pure alumina microparticle and (c) surface of AACNS.
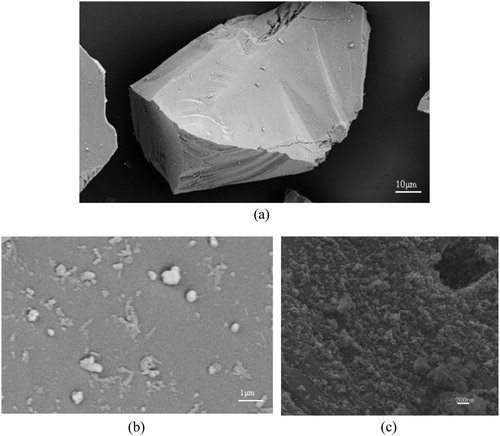
Figure 8. SEM images of YTZP blocks treated by different abrasives (a) YTZP treated with alumina abrasives only and (b) YTZP treated with AACNS.
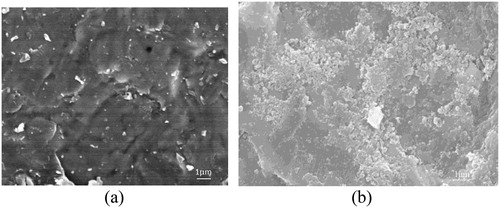
According to , Y-TZP blocks treated by different abrasives show different micromorphology. shows surface of Y-TZP block treated by pure alumina, besides notch-shaped groove, there is nothing. However, shows there are some nanoparticles adhering to the surface of Y-TZP block, and the material distribution of Y-TZP surface can be detected by EDS, and the result is shown in . According to the result of EDS, it is found that proportion of oxygen atom is high to 65.54%, that means the nanoparticles adhered to the surface of Y-TZP block are completely oxidised to become silica nanoparticles.
Initial SBS values of the three groups are shown in . According to results of the least significant difference tests, group C shows lower SBS values than both group A and group B. The other two groups show higher values, moreover, no statistical difference is detected between them.
represents the statistical representation of the graph shown in in terms of mean, maximum, minimum and median under the unit of MPa. Group A that represents YTZP samples coated with AACNS shows an average SBS value of 12.05 Mpa, which is very close to the average SBS of Group B sample, which represents YTZP coated with 3M product. Similarly, the median, max and min values have a very low disparity between Groups A and B. This signifies that the bonding strength produced from both the experimental AACNS and the commercial 3M product is very similar and hence AACNS can be used for similar applications without any improbability. This is verily due to the fact that AACNS and 3M product both includes silica–silane interlocking bonds, albeit the fact that the base silicon nanoparticles used in each product were manufactured differently, i.e. AACNS consisting of silica nanoparticles produced from a physical method (electrical discharge machining), whereas the silica attributed to 3M product from sol–gel method. To conclude, Group C that consist of pure alumina abrasives only, performed poorly in the SBS test having a mean value of 2.6225 MPa. This is significantly lower than the other two groups, simply because even though luting cement was silane treated, the YTZP surface abraded with alumina microparticles only did not consist of any silica contents, hence well-established interlocking of silica–silane bond similar with Groups A and B was not achieved. This proves that silica-coated alumina abrasives in form of AACNS on group B YTZP and commercial 3M product of Group A ceramics increased the surface area of the ceramic substrate and produced micromechanical roughness for resin bonding with luting cement, greatly improving the adhesiveness between cement and ceramic surface.
Table 3. Statistical representation of samples.
4. Conclusions
According to the previous paper written by the author, it was confirmed that silicon nanoparticles produced by electrical discharge machining would have the highest and optimum productivity of SINPs. With that in mind, this paper focuses on the viability of using such SiNPs for producing silica-coated alumina abrasives (AACNS) used for abrading the surface of zirconia ceramic and resin luting cement. The AACNS produced in this experiment was abraded by sandblasting on YTZP ceramic and after bonding with resin cement the consequent SBS measured.
Concurrently, the SBS of commercial produced 3M product and surface treated with normal alumina was measured to compare the results. The SBS values of the AACNS samples show strength on par with the commercial product, and far surpass the values of normal alumina. This emphasises great promise as a cheap alternative to the commercial chemical method widely used in industry.
Disclosure statement
No potential conflict of interest was reported by the authors.
Additional information
Funding
References
- Della AB, Kelly JR. J Am Dent Assoc. 2008;139:8.
- Denry I, Kelly JR. State of the art of zirconia for dental applications. Dent Mater. 2008;24:299.
- Kelly JR, Denry I. Stabilized zirconia as a structural ceramic: an overview. Dent Mater. 2008;24:289.
- Thompson JY, Stoner BR, Piascik JR, et al. Adhesion/cementation to zirconia and other non-silicate ceramics: where are we now? Dent Mater. 2011;27:71.
- Chen C, Chen G, Xie H, et al. Nanosilica coating for bonding improvements to zirconia. Int J Nanomed. 2013;8:4053.
- Xie H, Chen C, Dai W, et al. In vitro short-term bonding performance of zirconia treated with hot acid etching and primer conditioning etching and primer conditioning. Dent Mater J. 2013;32:928.
- Inokoshi M, De Munck J, Minakuchi S, et al. Meta-analysis of bonding effectiveness to zirconia ceramics. J Dent Res. 2014;93:329.
- Vanderlei A, Bottino AM, Valandro LF. Evaluation of resin bond strength to yttria-stabilized tetragonal zirconia and framework marginal fit: comparison of different surface conditionings. Oper Dent. 2014;39:50.
- Yi YA, Ahn JS, Park YJ, et al. The effect of sandblasting and different primers on shear bond strength between yttria-tetragonal zirconia polycrystal ceramic and a self-adhesive resin cement. Oper Dent. 2015;40:63.
- Amaral M, Belli R, Cesar PF, et al. The potential of novel primers and universal adhesives to bond to zirconia. J Dent. 2014;42:90.
- Usumez A, Hamdemirci N, Koroglu BY, et al. Bond strength of resin cement to zirconia ceramic with different surface treatments. Lasers Med Sci. 2013;28:259.
- Shin YJ, Shin Y, Yi YA, et al. Evaluation of the shear bond strength of resin cement to Y-TZP ceramic after different surface treatments. Scanning. 2014;36:479.
- Mattiello RDL, Coelho TMK, Insaurralde E, et al. A review of surface treatment methods to improve the adhesive cementation of zirconia-based ceramics. ISRN Biomater. 2013;2013:1.
- Zhang W, Farooq A, Wang W. Generating silicon nanoparticles using spark erosion by flushing high-pressure deionized water. Mater Manuf Process. 2016;31:113.
- Zhang W, Hong J, Wang W. Preparation of Silicon nanoparticles by pulse erosion and analysis with molecule dynamic simulation. J Nanosci Nanotechnol. 2016;16:9882.
- Efimov AA, Lizunova AA, Volkov IA, et al. A new approach to the high-yield synthesis of nanoparticles by spark discharge. J Phys. 2016;741:012035.
- Vons VA, de Smet LC, Munao D, et al. Silicon nanoparticles produced by spark discharge. J Nanopart Res. 2011;13:4867.