Abstract
The objective of this study is to systematically investigate the evolution of silver surface segregation of silver/titanium oxide nanocomposite coatings produced by reactive sputtering process. Different thickness barrier layers were deposited on the surface of Ag-TiOx two-dimensional (2D) and three-dimensional (3D) composite coatings at different deposition rates. In 2D mode, the SEM images and XPS patterns clearly show that the still strong silver segregation occurred even 50 nm thickness barrier coated with very low deposition rate (3 nm/min), while a sharp decrease of silver surface segregation can be achieved when high barrier deposition rate (20 nm/min) was applied. The high angle annular dark field (HAADF) STEM images reveal that the high silver mobility can be effectively suppressed under high barrier deposition rate. Similar phenomenon can be observed in 3D Ag-TiOx composite coatings. Moreover, the comparable study of the metallic titanium barrier layers show that a 30 nm barrier layer is enough to cover all the silver NPs, and silver atoms diffusion onto the surface was stopped under pure Ar atmosphere. The silver surface segregation evolution indicates that silver segregation could be the result of the combined effect of sputtering plasma and activated oxygen environment.
1. Introduction
Nanosilver is the most promising antibacterial material which has exhibited a broad-spectrum antibacterial activity to kill a variety of bacterial existing in everyday life. However, it is still unclear to fabricate silver-containing coatings with strong antibacterial effects and good biocompatibility and environmental safety. Aggregation of silver nanoparticles (NPs), uncontrollable release of silver ions significantly reduces antibacterial effects of silver NPs. Titanium oxide with great durability and biocompatibility has pronounced potential to retard silver aggregation and form homogeneous silver NPs distribution in coatings on various substrates. In addition, titanium oxide can be served as antibacterial material even after all the silver NPs released out. Therefore, it is profitable to combine silver NPs and titanium oxide matrix to form multifunctional composites for various applications [Citation1–3].Silver/titanium oxide nanocomposites can be synthesized with various approaches, such as chemical synthesis, ion implantation and magnetron sputtering [Citation4–6]. Magnetron sputtering has been widely used due to its flexibility, its simplicity in combining materials, and its ability to tailor the size distribution of silver nanoparticles. Considering the relatively low deposition rate and the complex production of titania targets used for RF magnetron sputtering (non-reactive sputtering), DC reactive sputtering from a metallic titanium target appears to be much more attractive nowadays. It not only provides controllable structures, sizes and morphologies but it is also straightforward to implement in industrial-scale production where relative high deposition rates and large-scale area coatings are required.
However, previous studies on silver/titanium oxide nanocomposite coatings have always showed strong segregation of silver towards the surface [Citation7–9]. This would lead abundant silver ion release in short time with the possibility of removal of silver NPs directly from the surface, preventing an exact tuning of the desired silver ion release properties. Moreover, silver surface segregation is not only observed in magnetron sputtering preparation, but also observed for silver/titanium oxide nanocomposites prepared in other ways. Yet, the factors influencing silver surface segregation in reactively sputtered nanocomposite thin films are still unclear. In this work, a series of 2D layer-by-layer and 3D structures of silver/titanium oxide nanocomposite coatings were deposited and the silver surface segregation behaviour was systematically investigated.
2. Experimental
2.1. Synthesis of 2D layer-by-layer and 3D silver/titanium oxide nanocomposites
A well-defined experimental set-up and deposition conditions were used as described in our previous work [Citation10]. The 2D and 3D silver/titanium oxide nanocomposite coatings were deposited on flat silicon substrates (0.5 cm × 0.5 cm) and carbon-coated copper TEM grids in a home-made deposition vacuum chamber by reactive co-sputtering from a Ti target (99.99%, Goodfellow GmbH) and a Ag target (99.99%, Goodfellow GmbH) from two independent magnetron sources. The distance between the Ti source and the substrate and the Ag source and the substrate were 6 cm and 12 cm, respectively. The angles of incidence were 50° for both of Ti source and Ag source. The deposition chamber was evacuated to a pressure of 10−6 mbar before deposition. In co-sputtering process metallic silver and titanium targets were deposited in the presence of oxygen and argon with the flow rate of 2 sccm and 120 sccm, respectively, corresponding to total pressure of 1.17 Pa. Oxygen in this process works as reactive specie. While argon used as process gas to produce plasma. Initially argon was introduced to clean oxide present on the surface of titanium for almost 10 min at 90 W. As cleaning was performed, oxygen was introduced which increase chamber pressure up to 0.0002 mbar. Both continuous and independent monitoring of the deposition rates of the Ag and TiOx were done in situ by using the two quartz-crystal monitors.
Proposed hypothesis of this experiment is to produce three-layer system and final layer should have the ability to envelop and clutch silver particles present in middle layer. A titanium oxide buffer layer with a thickness of 10 nm was deposited on silicon substrates as the first layer to enhance adhesion of subsequent layers to be deposited. Second layer was consisting of either silver or nano-composite (Ag-TiOx) to observe behaviour of 2D (2 nm nominal thickness) and 3D (5% metal volume fraction) structure respectively as configured in . Final layer was deposited to diminish silver diffusion to the surface with high deposition rate (20 nm/min) and low deposition rate (3 nm/min), respectively. Moreover, a series of pure metallic Ti barrier layers were deposited for comparable investigation.
2.2. Structure characterization
The relative amount of silver and the silver chemical state on the surface was monitored by XPS. The measurement was done with an Omicron Full Lab XPS system with a double Al/Mg anode (VG Microtech XR3E2) and a hemispherical analyzer (VSW Instruments EA 125). The Al anode was operated at a typical power of 266 W (14.8 kV, 18 mA). Energy-dispersive X-ray spectrometry (EDX; Zeiss Supra 55VP) was used to measure the silver concentration in the composite samples. Additionally, for the study of the individual Ag NPs, carbon-coated Cu-microgrids (S160-3, Plano) were analyzed using a Tecnai F30 G2 STwin [field emission gun (FEG) cathode, spherical aberration coefficient Cs = 1.2 mm] microscope working at an accelerating voltage of 300 kV. Scanning (S) TEM images displaying atomic number dependent (Z)-contrast were recorded with a high angle annular dark field (HAADF) detector. The surface morphology of selected composite samples was investigated by scanning electron microscopy (SEM; Zeiss Supra 55VP).
3. Results and discussion
Previous studies [Citation11, Citation12] suggested that Ag NPs segregation could be suppressed by deposited a barrier layer of titanium oxide layer continuously via a RF sputtering method, and the Ag diffusion on the surface can be strongly retarded by barrier thickness with some ten nanometers. However, still quite few research focus on tailoring silver segregation in reactive sputtering condition. Here, different barrier deposition conditions were performed to investigate the barrier influence on the silver surface segregation of silver/titanium oxide nanocomposite coatings produced in reactive sputtering process.
3.1. The surface segregation evaluation of 2D layer-by-layer silver/titanium oxide nanocomposite coatings
As shown in , we surprisingly found that coated a barrier with low deposition rate (3 nm/min) showed limited effect to suppress the surface segregation, this is totally opposite with the non-reactive method. The SEM images indicate that silver still severely agglomerated on the surface even if the silver nanoparticle layer has been covered by a 50 nm TiOx barrier layer in one step. More discontinuous and larger island structures formed on the surface as the barrier layer thickness increased at this low deposition rate.
Figure 2. SEM images of the surface morphology evolution of 2 nm Ag layer coated with different barrier thicknesses produced at moderate deposition rate. (a) no barrier (b) 10 nm barrier (c) 20 nm barrier (d) 30 nm barrier (e) 40 nm barrier (f) 50 nm barrier.
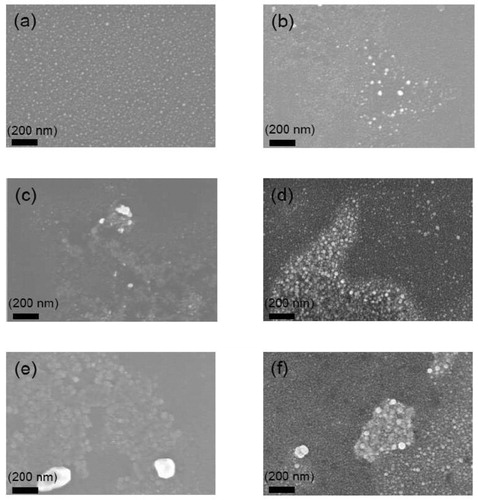
As presented in , the SEM images clearly show that the silver surface segregation can be further reduced by using a higher deposition rate up to 20 nm/min for the titanium oxide capping layers. No significant silver surface segregation was observed for the samples coated with barriers with high deposition rate. We suppose this could be ascribed to a larger nuclei formation rate at the higher deposition rate, suggesting that a continuous film is produced. The effect of a high deposition rate to suppress the silver signal for the 2D model demonstrates effect way to control silver surface segregation.
Figure 3. SEM images of the surface morphology evolution of 2 nm Ag layer coated with different barrier thickness produced at high deposition rate. (a) no barrier (b) 10 nm barrier (c) 20 nm barrier (d) 30 nm barrier (e) 40 nm barrier (f) 50 nm barrier.
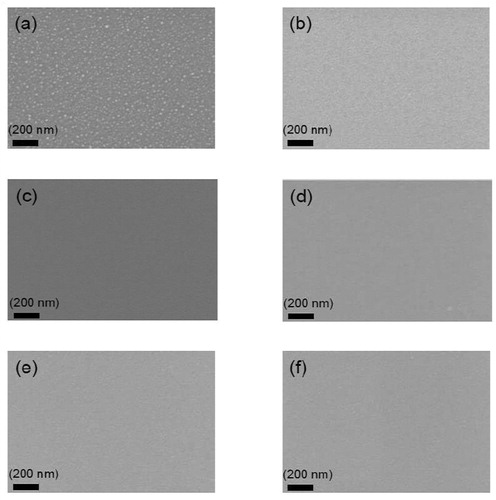
shows the X-ray photoelectron spectra of the evolution of Ag 3d core levels depending on the barrier thickness at a low/high deposition rate during deposition at the surface using 2 nm Ag layer. One can find that simply increasing the barrier thickness with 3 nm/min rate does not play a significant role in suppressing the Ag segregation on the surface in , the silver surface segregation can be hardly avoided even with the use of a 50 nm barrier layer.This clearly demonstrates that a strong surface segregation effect also occurs for already pre-formed silver NPs during barrier deposition in reactive sputtering process. However, no silver surface segregation phenomenon reported in such a 2D layer by layer structure in non-reactive sputtering environment elsewhere. This process it can be ascribed that the reactive plasma together with oxygen destroy the structure of the silver atom layer and results in the silver atom diffusion onto the surface, and the Ag layer structure has possibly been attacked by oxygen ions and thus been modified [Citation13,Citation14]. The better surface segregation suppression effect by using a higher deposition rate is also confirmed by the X-ray photoelectron spectra in . One can see that the silver signal intensity on the surface is much weaker than the same samples coated with barriers at low deposition rate, which is showed in . This indicates that the silver surface segregation can be substantially reduced by increasing the deposition rate for the barrier layers, which is consistent with the result indicated in previous SEM images.
Figure 4. X-ray photoelectron spectra of the evolution of Ag 3d core levels depending on the barrier thickness at low deposition rate (a) and high deposition rate (b).
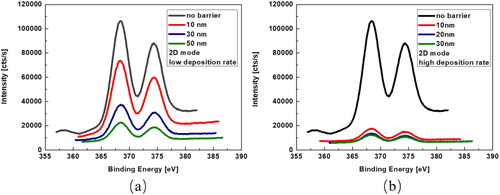
For a better understanding of the silver mobility during the different barrier deposition rates and subsequent changes of silver surface segregation, the high angle annular dark field (HAADF) STEM technique was employed. shows the HAADF-STEM images of the 2D structure coatings deposited 20 nm barrier layer with different barrier deposition rates. As shown in , it can be found that more discontinuous and larger island structures formed on the barrier surface as the 20 nm thick barrier layer deposited at low deposition rate. However, as depicted in , the silver NPs presents a more homogeneous size distribution when the 20 nm thick barrier layer deposited at a high deposition rate on 2 nm thick Ag layer, indicating that a much better silver surface segregation effect was achieved under high deposition rate for the barrier layer. It is well known that silver surface segregation has a high driving force due to the high silver atom mobility and the low silver-matrix interaction energy. Viana et al. [Citation15] suggested that silver surface segregation and the formation of irregular agglomerates on the surface can be attributed to a porous structure of the amorphous titania matrix which allows a high mobility of the silver nanoparticles. Here, the HAADF-STEM images demonstrate that the silver mobility can be effectively suppressed under high barrier deposition rate, this could be ascribed to the larger nuclei formation rate at this higher deposition rate and leads to a continuous barrier film to suppress the silver segregation, which well supports the conclusion indicated by previous XPS measurement.
Figure 5. HAADF-STEM images of the surface morphology evolution of 2 nm Ag 2D nanocomposite coatings without barrier layer (a), with 20 nm barrier layer at low deposition rate (b) and with 20 nm barrier layer at high deposition rate (c).
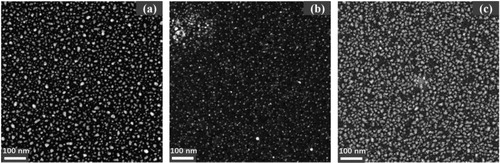
In a comparative study, 10, 30 and 50 nm pure metallic titanium non-porous barrier layers were deposited on a similar 2 nm Ag nanoparticle layer without oxygen admixture. As shown in , the X-ray photoelectron spectra indicates that a 30 nm barrier layer is the critical size to cover all the silver NPs, and silver atoms diffusion onto the surface was stopped under pure Ar atmosphere, which further supports that Ag surface segregation on the barrier layer is a plasma assisted oxygen induced process and occurs as soon as the silver atoms are exposed to activated oxygen.
3.2. The surface segregation evaluation of 3D silver/titanium oxide nanocomposite coatings (5% Ag filling factor)
presents the STEM cross-sectional pictures and EDX measurement of the Ag NPs size distribution in the bulk with 5% Ag filling factor and 30 nm barrier layer deposited at low rate. One can see that most of the Ag NPs existed in the matrix for the 5% Ag containing nanocomposite from . The silver NPs hiding inside the bulk are rather small, all around 5–10 nm, and slight surface segregation was observed in this case; most Ag NPs were buried in the titania matrix as smaller sized NPs. A strong silver signal in the nanocomposite region and on the outer surface area was detected, which indicates that strong silver segregation to the surface occurred. It is believed that the growth of the Ag NPs in the bulk would give rise to large compressive stress in the ceramic matrix, while on the surface the particles can grow unconstrained.
Figure 7. The STEM cross sectional images and EDX results of Ag NPs (black point we marked already) size distribution in the matrix and on the surface with 5% Ag filling factor and 30 nm barrier layer deposited at low rate.
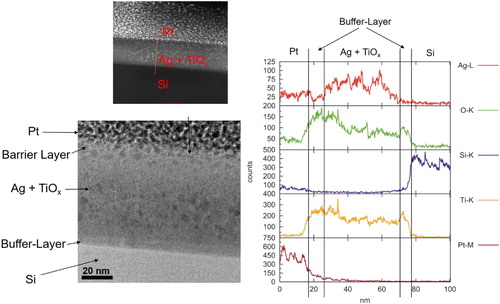
In , the XPS result shows the silver surface segregation suppression effect when different deposition rates were applied for 5% Ag containing 3D nanocomposite coatings. One can find that less silver signal was detected under the high deposition rate process when the barrier thickness was gradually increased in . However, the Ag intensity presented an irregular decrease tendency which indicates that simply increasing the barrier thickness does not play a significant role in suppressing the Ag segregation on the surface when low barrier deposition rate was applied, metallic silver still appears on the surface due to the Ag NPs diffusion and segregation that made different size Ag NPs with an associated decrease in the inter-particle distance and particle coalescence [Citation16], which is consistent with the results that were observed from the 2D structure.
4. Conclusions
A series of 2D/3D silver/titanium oxide nanocomposite coatings were successfully prepared by reactive sputtering processes. Titanium oxide barrier layers deposited with different rates were applied to tailor the silver surface segregation of 2D/3D silver/titanium oxide nanocomposite coatings. It was surprisingly found that the silver surface segregation only can be slightly reduced even 50 nm thickness barrier coated with low deposition rate (3 nm/min) in 2D/3D silver/titanium oxide nanocomposite coatings, which is totally opposite to the phenomenon reported in non-reactive sputtering process. However, silver surface segregation can be significantly reduced when 20 nm/min barrier deposition rate was used. This can be ascribed to that the high silver atom mobility was restricted by the relative dense barrier structure formed with high deposition rate, which was confirmed by the HAADF-STEM measurements. In addition, a comparative study of pure metallic titanium barrier layers was also performed to study the evolution of silver surface segregation, and silver atoms diffusion onto the surface was stopped and no silver signal was detected on the surface when 30 nm Ti barrier was used. These results indicate that the silver surface segregation evolution in 2D/3D silver/titanium oxide nanocomposite coatings was a plasma assisted oxygen induced process and only occurs as soon as the silver atoms were exposed to activated oxygen during sputtering process.
Disclosure statement
No potential conflict of interest was reported by the authors.
Additional information
Funding
References
- Ghosh M, Mondal M, Mondal S, et al. Enhanced photocatalytic and antibacterial activities of mechanosynthesized TiO2-Ag nanocomposite in wastewater treatment. J Mol Struct. 2020;1211(128076).
- Zhao C, Guo J, Yu CL, et al. Fabrication of CNTs-Ag-TiO2 ternary structure for enhancing visible light photocatalytic degradation of organic dye pollutant. Mater Chem Phys. 2020;248:122873.
- Soh MF, Noh MFM, Mohamed NA, et al. Facile incorporation of g-C3N4/Ag dopant in TiO2 as electron transport layer for organic solar cells. Mater Lett. 2019;253:117–120.
- Xu JH, Liu YQ, Zhao Y. Effect of Ag loading position on the photocatalytic performance of TiO2 nanocolumn arrays. Beilstein J Nanotechnol. 2020;11:717–728.
- Li W, Hu WP, Liu Q, et al. Antibacterial properties of Ag/TiO2/PDA nanofilm on anodized 316L stainless steel substrate under illumination by a normal flashlight. J Mater Sci. 2020;55:9538–9550.
- Zhuo T, He S, Xin B, et al. Preparation and characterization of heat-insulating Ag/TiO2 composite membranes based on magnetron sputtering technology. J Mater Res. 2020;35(5):473–480.
- Borges J, Ferreira CG, Fernandes JPC, et al. Thin films of Ag-Au nanoparticles dispersed in TiO2: influence of composition and microstructure on the LSPR and SERS responses. J Phys D Appl Phys. 2018;51(20):205102.
- Loka C, Lee K-S. Preparation of TiO2/Ag/TiO2 (TAT) multilayer films with optical and electrical properties enhanced by using Cr-added Ag film. Appl Surf Sci. 2017;415:35–42.
- Xiong J, Ghori MZ, Henkel B, et al. Controlling surface segregation of reactively sputtered Ag/TiOx nanocomposites. Acta Mater. 2014;74:1–8.
- Xiong J, Ghori MZ, Henkel B, et al. Tuning silver ion release properties in reactively sputtered Ag/TiOx nanocomposites. Appl Phys A. 2017;123(7):470.
- Hrkac T, Rohl C, Podschun R, et al. Huge increase of therapeutic window at a bioactive silver/titania nanocomposite coating surface compared to solution. Mater Sci Eng C Mater Biol Appl. 2013;33(4):2367–2375.
- Dziedzic A, Bochnowski W, Adamiak S, et al. Structure and antibacterial properties of Ag and N doped titanium dioxide coatings containing Ti2.85O4N phase, prepared by magnetron sputtering and annealing. Surf Coat Tech. 2020;393:125844.
- Chakravadhanula VSK, Kubel C, Hrkac T, et al. Surface segregation in TiO2-based nanocomposite thin films. Nanotechnology. 2012;23(49):495701.
- Liu YM, Zhang WG, Sun YH, et al. Diffusion behavior of Ag in TiO2 nanofilms. Mater Res Bull. 2018;98:240–249.
- Viana MM, Mohallem NDS, Miquita DR, et al. Preparation of amorphous and crystalline Ag/TiO2 nanocomposite thin films. Appl Surf Sci. 2013;265:130–136.
- Al-Maliki FJ, Hammadi OA, Chiad BT, et al. Photocatalytic activity of Ag-doped TiO2 nanostructures synthesized by DC reactive magnetron co-sputtering technique. Opt Quant Electron. 2020;52(188).