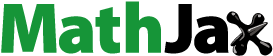
Abstract
In this article, the strength characteristics of the cement mortar with waste glass powder of different size and content at different ages were studied. The mechanism of strength development was analysed from the microstructure of mortar specimens based on scanning electron microscopy (SEM) and electronic dispersive spectroscopy (EDS). The results show that the compressive strength and flexural strength of the mortar specimens increase significantly with a higher age. There is an optimal content of glass powder corresponding to the maximum strength. The glass powder of smaller particle size clearly promotes the development of compressive strength and flexural strength in the mortar specimens. It is found from SEM-EDS that glass cement mortar has a larger amount of internal hydration products and higher density compared with ordinary cement mortar. The density of cement mortar incorporating 15 wt% glass powder increases gradually with the decrease of glass particle size. The hydration products and compactness of the cement mortar adding 200–500 mesh glass powder experience an increase and then a decrease with a rise in the glass content. The strength enhancement with the addition of glass powder are mainly attributed to the microaggregate filling effect and pozzolanic effect of the glass powder, as well as to changes in the interfacial transition zone.
1. Introduction
The production and consumption of glass are increased over the past decades and the amount of waste glass significantly increases as a consequence. For the sustainable use of resources, waste glass can be collected and processed again into new glass products [Citation1, Citation2]. The recovery and recycling rate of glass products in the world is still relatively low, mainly because the quality properties of waste glass after reprocessing do not meet the specified requirements [Citation3]. According to the statistics of the United Nations, the global waste generated every year reaches 200 million tons, of which 7% is glass waste [Citation4]. Waste glass cannot be completely incinerated, degraded in landfills, nor be decomposed or treated by general physical and chemical methods. The glass also contains heavy metals such as zinc and copper that cause soil and groundwater pollution. Reasonable recycling of the waste glass can reduce the consumption of minerals and the space occupied by a large amount of glass waste in the natural environment, thus protecting natural resources. As such the recycling of waste glass has become an imminent environmental protection measure.
The application of solid waste within the construction industry develops rapidly owing to lower cost, greater economic and environmental benefits [Citation5–10]. The recycling of waste glass is an emerging idea in the construction industry. Since the 1960s, many scholars have been conducting research into the use of waste glass in concrete. Initially, the glass was crushed to partially replace the coarse aggregates in the concrete. In this case, the glass exerts different effects on the performance of concrete. The mechanical properties of concrete exhibited a decline trend when the replacement rate was greater than 30%. For a low replacement below 30%, the filling effect of glass powder played a critical role and enabled to increase the compactness of concrete, and therefore promoting the mechanical properties and durability of concrete [Citation11]. However, due to the large amounts of silica and alkali within the glass, there is a risk of an alkali-silicate reaction (ASR) producing a gel that swells heavily when it absorbs water, leading to expansion and cracking of the concrete and hence a reduction in the stability of the building structure. This was a main reason for the stagnation of the initial use of waste glass in concrete [Citation12–14]. Later on, it was shown that pozzolanic materials such as fly ash, marble powder, brick powder, slag, silica fume and finely ground glass powder could play important roles in avoiding the alkali-silicate reaction (ASR) [Citation15–22]. Moreover, it was found that finely ground glass powder could be used as a new supplementary cementitious material to replace some of the cement in concrete because of the large amount of silica, high specific surface area and amorphous nature of the finely ground glass powder [Citation23, Citation24].
The particle size of glass powder is directly linked to the pozzolanic effect. Li et al. [Citation25] found that the compressive strength of the mortar, by adding glass powder with particle size from 74 to 150 μm, was always less than that of the control group irrespective of the amount of glass powder. Whereas, the compressive strength of mortar at 28 d and 90 d with glass addition of particle size from 20 to 74 μm was increased by 3.5% and 9.6%, respectively, compared to that of the control group. Letelier et al. [Citation26] pointed out that the fine glass particles (with sizes below 38 μm) could fill the volume of capillary pores and were more susceptible to the pozzolanic reaction due to their greater specific surface area. Shao et al. [Citation27] studied the compressive strength of concrete adding 30% glass with mean particle sizes of 150 μm, 75 μm and 38 μm. It was found that the highest compressive strength was achieved with a particle size of 38 μm and the pozzolanic effect was thus emphasized. Khmiri et al. [Citation28] studied the compressive strength of 90 d mortars incorporating 20% glass of different particle sizes. The results of glass particle size less than 20 μm were increased by 12.7%, 47.6% and 6% compared to those with particle sizes of 20–40 μm, 40–80 μm and 80–100 μm, respectively. The results from a large number of previous studies showed a consistent finding that the compressive strength of blended concrete or mortar was increased as the particle size of the glass powder was decreased. The mechanical properties, however, varied substantially depending on the composition and preparation method of the glass powder.
In addition to the particle size and associated effect of pozzolanic reactions, the content of glass powder also has an important influence on the strength development in cement mortar or concrete. Patel et al. [Citation29] found that the compressive strength of 90 d cement mortar by adding glass powder with mean sizes 45 μm was increased linearly with the proportion of glass powder in the range 5–20%. The mortar compressive strength with 20% glass powder even surpassed that of the control specimen. A similar result was also reported by Wang et al. [Citation30] and it was further revealed that the glass powder content played a leading role in the compressive strength of glass cement mortar, regardless of the age. Olofinnade et al. [Citation31] investigated the compressive strength of concrete with glass powder contents of 0%, 15%, 18%, 21%, 24%, 27% and 30%. A significant increase of the compressive strength of concrete was found for the replacement rate of 21%, above which the concrete strength was decreased. An optimal substitution level of glass powder of 20% has been widely accepted according to previous studies as claimed in the review of Ahmad et al. [Citation32].
A longer curing age corresponding to higher hydration degree facilitates the strength development of the mortar and concrete. Gimenez-Carbo et al. [Citation33] found that at ages from 7 d to 60 d, the strength was significantly higher in the mortar blended with glass powder than in the control specimen. The results from Kamali et al. [Citation34] showed that the compressive strength of the glass cement mortar was higher than that of the control mortar at ages from 28 d to 91 d. Ali et al. [Citation35] maintained that at early ages of the first 7 d, the strength of glass cement mortar was lower than that of the control specimen while at later ages beyond 90 d, the strength development of glass cement mortar was different from that of the control specimen.
In previous studies, the scanning electron microscopy (SEM) together with electronic dispersive spectroscopy (EDS) was used to analyse the effect of glass powder on the internal hydration products and morphological structure of cementitious materials [Citation36–38]. When ground to a certain fineness, the glass powder exhibited strong pozzolanic effect and acted as a filler in the internal structure. According to Wang et al. [Citation39], the smaller particle size glass powder was more susceptible to pozzolanic reaction. The C-S-H gels were observed in the microstructure of 1 d mortar. At 28 d a very dense microstructure of the glass cement mortar was found, and CH crystal and C-S-H gel were well distributed in this microstructure and both had been shown to be beneficial to the strength development of glass cement mortar.
In the past few years, researchers have used the glass sand with similar particle size to replace the fine aggregate sand in mortar and concrete [Citation11, Citation40–43]. Kim et al. [Citation44] found a significant improvement in the durability of concrete when waste glass was used as fine aggregate. Gorospe et al. [Citation45] emphasized that the compressive strength of the mortar with glass aggregates was significantly reduced and the potential for alkali-silicate reaction (ASR) was greatly increased. Previous studies have shown that while fine aggregates were replaced by glass, an alkali-silicate reaction (ASR) might occur, causing possibly a reduction in mechanical properties and a risk to structural stability. However, the ASR could be inhibited when the glass size was small. Related findings were noted in studies such as Saccani et al. [Citation46].
Productions of glass cement mortar and concrete with appropriate proportion and particle size of glass powder have been found to improve mechanical properties. In previous research, the glass powder was used often with particle sizes similar to the cement. Further comprehensive research is worthwhile to carry out with respect to the influences of glass particle size and content, as well as curing age, on the properties of glass cementitious systems. It is worth mentioning that substituting fine aggregate sands by glass of similar grain size may lead to the occurrence of alkali silicate reactions (ASR) and a reduction in the mechanical properties of the material. There have been relatively few studies on the properties of glass cement systems based on the selection of glass powder with a large range of particle sizes. The aim of this study is to investigate the multiple effects of glass particle size, content and curing age on the mechanical properties of cement mortar with fine aggregate sand partially replaced by glass powder. The compressive strength and flexural strength were both tested. The microstructure was subjected to scanning electron microscopy (SEM) and electronic dispersive spectroscopy (EDS) to provide a basic insight into the macroscopic strength of the glass cement mortar.
2. Materials and methods
2.1. Materials
2.1.1. Cement
The cement used in this test was P·O 42.5 grade ordinary Portland cement produced by Henan Tianrui cement group, with compressive strength of 23.4 MPa at 3 days and 42.8 MPa at 28 days. The specific surface area was 375 m2/kg, and the bulk density was 3.08 cm3/g. The chemical composition of the cement is shown in .
Table 1. Chemical composition of cement.
2.1.2. Standard sand
The standard sand was Chinese ISO standard sand produced by Xiamen Aisiou Standard Sand Co., Ltd. with an apparent density of 1,350 kg/m3.
2.1.3. Waste glass powder
Waste glass powder was made from discarded glass bottles, and flat glass was crushed and then ground by a ball mill. The particle sizes were divided into 20–100 mesh, 100–200 mesh and 200–500 mesh, as shown in . X-ray fluorescence (XRF) was used to determine the chemical composition of waste glass powder, as shown in , and the main content is SiO2. The mineral composition of waste glass powder was analysed by X-ray diffraction (XRD) and the spectrum of waste glass powder is shown in . The flow chart of the production of waste glass powder can be seen in . The wide diffraction peak presented in the XRD spectrum indicates that the glass powder was highly amorphous and the amount of crystal phases was very small.
Table 2. Chemical composition of waste glass powder.
2.2. Methodology
The experimental glass powders were categorized into three groups of 20–100 mesh, 100–200 mesh and 200–500 mesh. The replacement levels of standard sand by the glass powder by volume were 10%, 15% and 20%. G0 was recorded as the reference group (ordinary cement mortar specimen without glass powder). G-20, G-100 and G-200 were recorded as the groups of cement mortars containing glass powders 20–100 mesh, 100–200 mesh and 200–500 mesh, respectively. Each group was further divided into 3 subgroups according to the glass powder content. For mortar specimens with 20–100 mesh glass powder, the 3 subgroups with glass replacement of 10%, 15% and 20% were recorded as G-20-10, G-20-15 and G-20-20, respectively. Similar rules were applied for mortar specimens with 100–200 mesh and 200–500 mesh glass powders. Mix proportion of waste glass powder cement mortar was shown in . When preparing cement mortar, keep the base mix ratio of cement mortar unchanged. The bulk density of standard sand and three particle sizes of glass powder was measured. The corresponding fine aggregate was replaced by the same volume of waste glass admixture. The amount of glass powder in three particle sizes was calculated and mixed into the cement mortar to make waste glass powder cement mortar. The bulk density of glass powder and standard sand are shown in .
Table 3. Bulk density of glass powder and standard sand(kg/m3).
Table 4. Mix proportion of waste glass powder cement mortar.
This experiment mainly uses the equivalent volume substitution calculation formula. The formula is as follows:
(1)
(1)
In the formula: —Quality of standard sand(g), —Bulk density of standard sand(g), —Quality of glass powder(g), —Bulk density of glass powder(g).—Content of glass powder (%).
According to the Chinese standard GB/T 17671-2020 ‘Cement mortar Strength Test Method (ISO method)’, the cement mortar specimens were at the ages of 3 d, 7 d, 14 d and 28 d. shows the flow chart of cement mortar preparation. Six representative groups of G0, G-20-15, G-100-15, G-200-10, G-200-15, and G-200-20 were selected for scanning electron microscopy (SEM) testing and electronic dispersive spectroscopy (EDS) tests to explore the microscopic mechanism about the effect of waste glass powder on the strength development of mortar specimens after 28 days.
3. Results and discussion
3.1. Effect of glass content
show the evolution of compressive strength and flexural strength of cement mortars with age. Effects of the content and particle size of the glass used as fine aggregate are studied. It can be observed that, compared with the reference group G0, the glass cement mortars exhibit great differences in the compressive strength and flexural strength. Both strengths increase first and then decrease when the glass powder content increases up to 20%. The strength changes for glass particle sizes 20–100 mesh are not significant compared with the control group, regardless of the age and glass content. A slightly lower strength than the control group is found when glass replacement is 20%. At ages of 3 d, 7 d, 14 d and 28 d, the compressive strength of G-20-20 is decreased by 4.9%, 2.6%, 1.6% and 1.7%, respectively, compared to a decrease of the flexural strength by 1.8%, 4.3%, 1.3% and 2.4%, respectively. It seems that a rather high content of glass powder is not favourable to the strength development. For the particle size of 100–200 mesh, the compressive strength and flexural strength at 3 d are increased continuously and higher than those of the control group with higher glass content. Both strengths at ages of 7 d, 14 d and 28 d, however, are increased first and then decreased with increase of glass content. The strength value is increased when the glass content rises from 10% to 15%, while decreased for a higher glass content from 15% to 20%. An optimal glass content of 15% corresponding to 100–200 mesh glass powder is demonstrated. Similar observations are found as well for the 200–500 mesh glass powder. At 3 d, the compressive strength and flexural strength are seemingly lower for the glass content of 20% than the control group. For the age beyond 7 d, the compressive strength and flexural strength are increased first and then decreased but that both are higher than those of the control group for all glass contents under study. The glass content of 15% is seemingly the optimal replacement level for the 200–500 mesh glass powder to be incorporated in the mortar for strength development.
Figure 5. Effects of replacement level of 20–100 mesh glass powder used as fine aggregate on the mortar strength development.
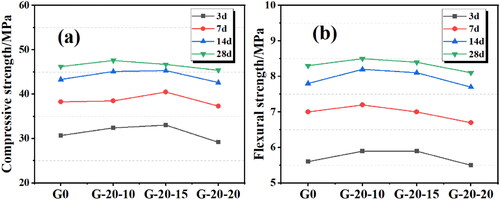
3.2. Effect of the age
show the variation trend of the mortar strength when the glass with different particle size and age was used to partially replace the fine aggregate sand. As can be seen, the compressive strength and flexural strength of cement mortar show clearly an increasing trend with age. For mortar specimens with 20–100 mesh glass powders (), the compressive strength and flexural strength at each age differ slightly from those of the control group, and the strength growth trend is basically the same. For the case of 100–200 mesh glass powders (), the early strength at a age of 3 d is higher than that of the control group. This is true for the replacement levels up to 20%. The strength shows a rapid rise from 3 d to 14 d, while a relatively slow increase after 14 d. The strength of mortar specimens with 100–200 mesh glass powders at all ages, except the 7 d, is obviously higher than that of the control group. For the case of 200–500 mesh glass powders (), the compressive strength and flexural strength at 7 d, 14 d and 28 d were higher than those of the control group, except for the strength at 3 d, at which the replacement of 15% and 20% result in the strength to be significantly lower than those of the control group. It is indicated that the hydration and associated strength development for mortar specimens with 15–20% glass powder (200–500 mesh) proceed slowly during the early 3 d and become pronounced after 7 d. There is a general observation that the strength increases rapidly in the first 14 d while relatively slowly afterwards. The most rapid increase of the strength occurs in the first 7 d for the relatively high replacement level of 20% by 200–500 mesh glass powders. It is expected that a higher replacement of fine glass powders tends to accelerate the cement hydration process owing to possibly the nucleation effect of the aggregate glass particles and the enhanced pozzolanic effect of the glass. For the case of 100–200 mesh and 200–500 mesh glass powders, the mortar specimens of all replacement up to 20% exhibit tremendously higher compressive and flexural strength than the control group at 28 d, although the control group presents a larger compressive strength at the early 3 d. The glass powder of different sizes is expected to have dissimilar influences on the microstructure formation and strength development.
Figure 8. Strength development with age for cement mortars with different contents of 20–100 mesh glass powders used as fine aggregate.
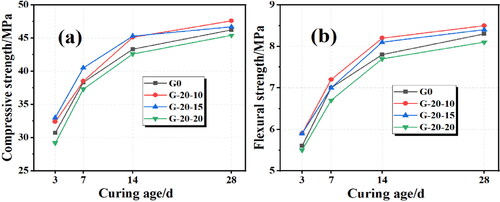
3.3. Effect of particle size
shows the effects of the glass particle size on the compressive strength and flexural strength of the cement mortar. As observed, the particle size effect highly varies with age. At the early age of 3d, incorporating glass powders of 100–200 mesh result in the mortar specimens to have the largest compressive and flexural strength. Both strengths for cases of adding 20–100 mesh and 200–500 mesh are lower. The decrease of glass particle size clearly promotes strength development at the late age of 28 d, at which both compressive and flexural strength are the highest for the finest glass particles to be included in the mortar specimens. The compressive strength and flexural strength of G-200-20 are increased by 9.1% and 14.8%, respectively, compared to those of G-20-20 at the age of 28 d. It has been shown that the density and specific surface area of glass powder increase when the glass is physically ground into particles below a critical size. Glass powder could physically fill the capillary pores to densify the microstructure of cement mortar and leading to an increase of the strength [Citation27, Citation47, Citation48]. Moreover, the pozzolanic activity of glass powder is enhanced with increasing specific surface area and a good linear relationship has been recognized between the two. Vitreous silicates within glass powder chemically react with the alkaline activator Ca(OH)2 generated by cement hydration. The reaction products, such as calcium silicate hydrate gels, could enhance the strength of cement mortar. The smaller the glass particle size, the higher the strength of the cement mortar.
Figure 11. Effect of glass particle size on compressive strength and flexural strength of cement mortar.
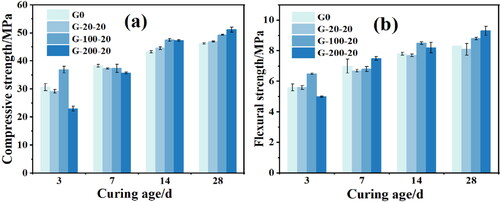
illustrates the correlation between compressive strength and flexural strength of cement mortar specimens using glass aggregate with different particle sizes and content. For all the specimens under study, a general linear relationship can be established with Equationequation (1)(1)
(1) , with a high correlation coefficient R2 of 0.9673.
(1)
(1)
3.4. SEM and EDS analysis of glass mortar
The 28-day strength of representative specimens G0, G-20-15, G-100-15, G-200-10, G-200-15, and G-200-20 were analysed by SEM-EDS. The results are shown in . The morphology of the microstructure including various hydration products such as pin-rod-like ettringite (AFt), honeycomb-like calcium silicate hydrate C-S-H gels, and lamellar CH can be examined [Citation49, Citation50]. The capillary pores and microcracks are observed. The types and content of main elements in the cementitious system are analysed in depth.
Figure 14. SEM images of interface transition zone (ITZ) in the mortar specimens G0, G-20-15 and G-200-15 after 28 d hydration.
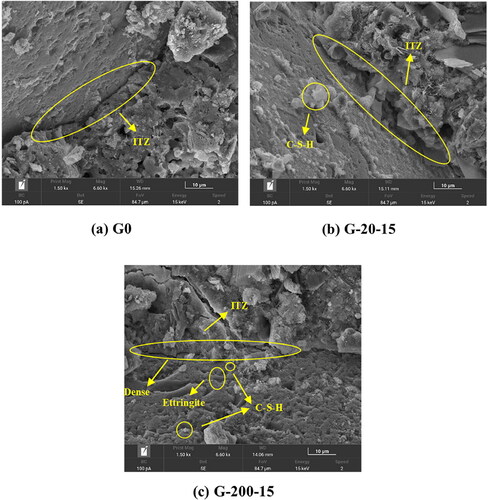
Figure 16. SEM-EDS images of 28 d cement mortar with different content of 200–500 mesh glass powder.
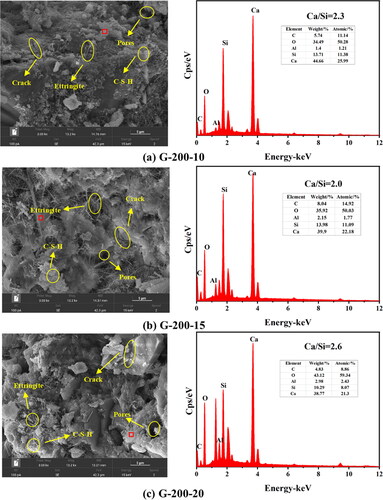
3.4.1. Comparison between glass mortar and ordinary cement mortar
Compared with the glass mortar, the ordinary cement mortar presents a rougher microstructure and the hydration products are distributed in a more disorganized manner. There are a large number of capillary pores as well as the presence of microcracks in the ordinary cement mortar (see ). In contrast, the glass mortar has a more uniform internal structure after hydration, with improved compactness and only a small amount of pores and microcracks (see d). The formation of honeycomb-like C-S-H and the reduction of CH crystallization can be clearly observed owing to the presence of glass powders. demonstrates the formation of flocculent C-S-H gel to precipitate on the surface of glass particles and to densify the interfacial transition zone (ITZ). The number and width of the cracks are reduced and thus improving the hydrates packing density of ITZ when the comparison of ITZ was made between glass mortars G-20-15/G200-15 and the reference G0.
These phenomena can be attributable to the multiple effects of glass powders on cement mortar. First, the glass powder exerts a microaggregate filling effect. The particle size of glass is smaller than that of fine aggregate sand. Replacement of the sand by finer glass powders changes the original particle gradation of fine aggregate, a well-known aggregate admixture effect. In the meantime, the finer glass powders can fill the capillary pores to a certain extent leading to a denser matrix in the cement mortar and hence an increase of the strength [Citation51]. Second, the fine glass powders (less than 150 μm) exert a pozzolanic effect and react with CH near the fine aggregate to form C-S-H gels, as formulated in EquationEquation (2)(2)
(2) , thus promoting an increase in the density of the ITZ and improving the weakness of the area between the fine aggregate and the cement paste [Citation52].
(2)
(2)
EDS analyses were performed on the specimens and the red area marked was the test area. As shown in d, the replacement of sand by the glass powder does not change the type of the main elements in the cement mortar. However, it is worthwhile to note that a clear change of the Ca/Si ratio of the C-S-H gels is found. The Ca/Si ratio is reduced as the decrease of the glass particle size. The pozzolanic effect of the glass powder led to the hydration reaction between the glass powder and the CH crystal produced by cement hydration, resulting in the formation of secondary C-S-H gel. The pozzolanic reaction consumes a large amount of Si and reduces the content of CaO, contributing to a decrease of the Ca/Si ratio within the gelation. Therefore, as sand was replaced by glass powder, with the decrease of Ca/Si ratio, the glass powder underwent volcanic ash reaction and produced a large amount of C-S-H gel, which increased the internal compactness of the slurry, resulting in the strength of glass powder cement mortar higher than that of ordinary cement mortar.
3.4.2. Comparison of the mortar microstructure with different glass particle sizes
shows the SEM-EDS images of 28 d cement mortar with different glass particle sizes. The glass powder content was constant as 15% while the glass particle size was decreased from 20–100 mesh to 200–500 mesh. A rise in the microscopic morphological integrity and compactness can be observed. The amount of hydration products and the degree of coupling are gradually increased with a decrease of the glass particle size. A larger amount of C-S-H gel is formed in the G-200-15 than in the G-20-15 and G-100-15. The amount of needle- and rod-shaped ettringite is increased and the shape is changed from fine to coarse. The ettringite crystals are swelled slightly and precipitate within the capillary pores, bonding tightly with the C-S-H gel. The amount of lamellar CH crystals that embedded in the hydration products is decreased.
The glass powder had a higher specific surface area and volume ratio when the particle size was reduced, facilitating a more favourable chemical reaction and thus allowing the glass powder with pozzolanic activity to react with the hydration product CH to form C-S-H gels. As a result, more C-S-H gels and fewer CH crystals are observed in . In addition, the enhanced filling effect of glass microaggregates with finer particle sizes can reduce the large capillary pores and microcracks within the hardened cement matrix. As such the internal structure of cement mortar becomes denser, a finding similar to the study of Sobolev et al. [Citation51]. According to ,c, it is considered that the smaller particle size of glass can largely change the microstructure of the ITZ of cement mortar. When the particle size of glass was decreased from 20–100 mesh to 200–500 mesh, more hydrated gels are generated and the pore structure of the ITZ is densified owing to the transformation of CH into the secondary C-S-H. Both the physically filling effect and the chemically pozzolanic effect contribute to the densification of the ITZ. The glass of 200–500 mesh particle size was found as the optimal addition to the mortar specimens in view of strength development, as can be deduced from the superior strength of G-200-15.
The EDS analysis was performed on mortar specimens G-20-15, G-100-15 and G-200-15. The results including the test area marked in red are shown in . For the replacement of 15% glass power, the types of main elements of the hydrated gels remain the same as decrease of glass particle size but that the Ca/Si ratio are significantly decreased. Due to the fact that finer glass powder had stronger pozzolanic activity, the glass powder was more likely to undergo secondary hydration with CH crystals, resulting in a subsequent decrease of Ca/Si ratio in the gelation. This is a further demonstration for the best strength of G-200-15. Therefore, with the decreased of Ca/Si ratio, more C-S-H gels were produced in the slurry, which made the matrix more compact. The compressive strength of glass powder cement mortar with finer particle size was higher.
3.4.3. Comparison of the mortar microstructure with different glass content
d) shows the different microstructure formed by adding 200–500 mesh glass powders into the mortar specimens. With continuous increase of glass content, the microscopic morphological integrity and compactness of the mortar specimens first rise and then decrease. The cement mortar mixed with 10% glass powder () produced a large amount of honeycomb-like C-S-H gel and a small amount of fine needle-like ettringite (AFt), with traces of large capillary pores and microcracks. The most porous microstructure was found in the mortar with 20% glass powder (), containing a large number of capillary pores and microcracks. As seen from , the hydrated particles in the mortar with 15% glass powder tend to fill a large number of the pores within the ITZ. It is obvious that a considerable amount of honeycomb-like C-S-H gels and fine needle-like ettringite were produced, corresponding to the dense microstructure with only a few capillary pores and microcracks.
With the moderate increase of glass with smaller particle size, the microaggregate filling effect of the glass powder was enhanced and the internal structure was densified when the substitution was increased from 10% to 15%. Moreover, a higher amount of fine glass powders further contributed to the pozzolanic effect. The strength of the glass mortars was increased as a consequence. When the very fine glass content was increased from 15% to 20%, the free capillary water was reduced owing to the water adsorption of the finer glass particles, leading to an increase in the amount of water needed for cement hydration. The cement hydration as well as the pozzolanic reaction are relatively impeded, resulting in less amount of hydration products and a more porous microstructure. These provide explanations for the strength changes of mortar specimens with 200–500 mesh glass powders, and an optimal replacement of the very fine glass powder is 15%.
EDS analysis was performed on mortar specimens G-200-10, G-200-15 and G-200-20. The results shown in indicate that the amount of glass powder shows little effect on the types of the main elements, but has a great influence on the elemental compositions. When the glass particle size was 200–500 mesh, the Ca/Si ratio of the C-S-H gels is decreased first and then increased with the increase of glass content. An moderate increase of the replacement of glass powder was conducive to the hydration of glass powder, generating more C-S-H gels. A very high amount of fine glass powder, which adsorb a large quantity of capillary water, would reduce the capillary water available for hydration, leading to the reduction of CH crystals in the microstructure. The pozzolanic reaction the glass powder with CH was less pronounced and the microstructure becomes less dense. Consequently, there should be an optimal content of 200–500 mesh glass powders to be included in the mortar specimens for the best strength performance. Therefore, with the Ca/Si ratio decreasing first and then increasing, the pozzolanic reaction of glass powder inside the mortar increased first and then decreased, and the strength of 200 ∼ 500 mesh glass powder cement mortar increased first and then decreased.
4. Conclusions
This article presents a systematic investigation on the effects of glass powder as partial replacement of fine aggregate sand on the microstructure and strength development of cement mortars. The particle size and content of the glass were examined. The mechanisms and associated influence on strength were analysed in view of pozzolanic effect and filling effect of the glass powder, as well as densification of the interfacial transition zone, in the mortar specimens based on mechanical measurements and scanning electron microscopy and electronic dispersive spectroscopy (SEM-EDS). The main conclusions of this study are summarized as follows:
An optimal replacement of fine aggregate sand with glass powder by 15% is generally found for the three glass particle sizes 20–100 mesh, 100–200 mesh and 200–500 mesh. Such replacement facilitates the micromorphological compactness and desification of the interfacial transition zone.
An increase of the age normally results in higher compressive and flexural strength of the glass mortar. Both strength exhibits statistically a linear relationship. The strength of glass mortar with glass particle sizes of 20–100 mesh and 100–200 mesh is increased rapidly during the first 14 d while a relatively slow increase is followed afterwards. In the case of very fine glass powder of 200–500 mesh, the glass mortar has the most rapid increase of strength in the first 7 d.
Compared with the reference mortar, the mortar with very fine glass powder of 200–500 mesh has a lower strength at early age while exhibits obviously higher strength after 28 d. The strength of glass mortar is inclined to increase with smaller glass particle size owing to the enhanced effects of microaggregate filling and pozzolanic reactivity. The 200–500 mesh glass powders with a very high surface area exert water absorption effect and the free capillary water for hydration is reduced thereby.
The Ca/Si ratio of C-S-H gels changes with variations of the size and content of the glass powder. With the decreased of Ca/Si ratio, the strength of glass powder cement mortar increased.
Author contributions
Yi Zhao: Writing – review & editing, Methodology, Investigation. Jie Gao: Writing – original draft, Conceptualization, Validation, Formal analysis. Shuai Wu: Conceptualization, Validation, Formal analysis. Qinglu Li: Supervision, Data curation.
Disclosure statement
No potential conflict of interest was reported by the authors.
Data availability statement
All data generated or analysed during this study are included in this submitted article. The raw data shall be made available upon request to the corresponding author.
Additional information
Funding
Notes on contributors
Yi Zhao
Dr. Yi Zhao, Associate Professor, Master Supervisor, China, is a young backbone teacher in Henan Province, whose research interests are: new construction materials, combined structures. She has presided over one National Natural Science Foundation of China, published more than 20 papers and 10 patents, Zhengzhou, Henan, China.
Jie Gao
Jie Gao, M.Sc., School of Construction Engineering, Zhongyuan Institute of Technology, Zhengzhou, Henan, China.
Shuai Wu
Shuai Wu, M.Sc., School of Construction Engineering, Zhongyuan Institute of Technology, Zhengzhou, Henan, China.
Qinglu Li
Qinglu Li, M.Sc., School of Construction Engineering, Zhongyuan Institute of Technology, Zhengzhou, Henan, China.
References
- Kim K, Kim K. Valuable recycling of waste glass generated from the liquid crystal display panel industry. J Cleaner Prod. 2018;174:191–198. Feb
- Dixit M, Singh H, Attia MS, et al. Recent innovations in properties of nanostructured glasses and composites. J Experim Nanosci. 2021;16(1):180–211.
- Jiang Y, Ling TC, Mo KH, et al. A critical review of waste glass powder – Multiple roles of utilization in cement-based materials and construction products. J Environ Manage. 2019;242:440–449.
- Zheng K, et al. Recycled glass concrete. In: PachecoTorgal F, Jalali S, Labrincha J, editors. Eco-efficient concrete. Woodhead Publishing Series in Civil and Structural Engineering. Cambridge: Woodhead Publ Ltd; 2013. p. 241–270.
- Strenk PM, Wartman J, Grubb DG, et al. Variability and scale-dependency of tire-derived aggregate. J Mater Civ Eng. 2007;19(3):233–241. Mar
- Givi AN, Rashid SA, Aziz FNA, et al. Influence of 15 and 80 nano-SiO2 particles addition on mechanical and physical properties of ternary blended concrete incorporating rice husk ash. J Exp Nanosci. 2013;8(1):1–18. Jan
- Xiao R, Ma YT, Jiang X, et al. Strength, microstructure, efflorescence behavior and environmental impacts of waste glass geopolymers cured at ambient temperature. J Cleaner Prod. 2020;252:119610. Apr
- Samarakoon MH, Ranjith PG, De Silva VRS. Effect of soda-lime glass powder on alkali-activated binders: Rheology, strength and microstructure characterization. Constr Build Mater. 2020;241:118013.
- Kirgiz MS. Fresh and hardened properties of green binder concrete containing marble powder and brick powder. Eur J Environ Civil Eng. 2016;20:s64–s101.
- Kirgiz MS. Strength gain mechanism for green mortar substituted marble powder and brick powder for Portland cement. Eur J Environ Civil Eng. 2016;20:s38–s63.
- Limbachiya MC. Bulk engineering and durability properties of washed glass sand concrete. Constr Build Mater. 2009;23(2):1078–1083. Feb
- Liu SH, Wang S, Tang W, et al. Inhibitory effect of waste glass powder on ASR expansion induced by waste glass aggregate. Materials. 2015;8(10):6849–6862. Oct
- Visser JHM. Fundamentals of alkali-silica gel formation and swelling: condensation under influence of dissolved salts. Cem Concr Res. 2018;105:18–30. Mar
- Ismail ZZ, Al-Hashmi EA. Recycling of waste glass as a partial replacement for fine aggregate in concrete. Waste Manag. 2009;29(2):655–659. Feb
- Amaral M, Macioski G, de Medeiros MHF. Pozzolanic activity of silica fume: analysis in cement pastes with different substitution levels. Materia-Rio De Janeiro. 2021;26(3):17.
- Heikal M, El-Didamony H, Helmy IM, et al. Pozzolanic activity of fly ash. Silic Indus. 2003;68(9–10):111–117.
- Martin CM, Scarponi NB, Villagran YA, et al. Pozzolanic activity quantification of hollow glass microspheres[Article]. Cement Concrete Compos. 2021;118:10. Apr
- Song JW, Feng SL, Xiong RR, et al. Mechanical properties, pozzolanic activity and volume stability of copper slag-filled cementitious materials. Mater Sci Medziagotyra. 2020;26(2):218–224.
- Yamamoto T, Kanazu T, Nambu M, et al. Pozzolanic reactivity of fly ash – API method and K-value. Fuel. 2006;85(16):2345–2351. Nov
- Kirgiz MS. Strength gain mechanisms of blended-cements containing marble powder and brick powder. KSCE J Civ Eng. 2015;19(1):165–172.
- Kirgiz MS. Chemical properties of blended cement pastes. J Constr Eng Manage. 2011;137(12):1036–1042.
- Kirgiz MS. Effects of Blended-Cement paste chemical composition changes on some strength gains of Blended-Mortars. SciWorldJ. 2014;2014:625350.
- Chen ZY, Wang YL, Liao S, et al. Grinding kinetics of waste glass powder and its composite effect as pozzolanic admixture in cement concrete. Constr Build Mater. 2020;239:117876.
- Xiong X, Wu MM, Shen WG, et al. Performance and microstructure of ultra-high-performance concrete (UHPC) with silica fume replaced by inert mineral powders. Constr Build Mater. 2022;327:126996.
- Li Q, Qiao HX, Li AY, et al. Performance of waste glass powder as a pozzolanic material in blended cement mortar. Constr Build Mater. 2022;324:126531.
- Letelier V, Henriquez-Jara BI, Manosalva M, et al. Use of waste glass as a replacement for raw materials in mortars with a lower environmental impact. Energies. 2019;12(10):1974.
- Shao YX, Lefort T, Moras S, et al. Studies on concrete containing ground waste glass. Cem Concr Res. 2000;30(1):91–100.
- Khmiri A, Chaabouni M, Samet B. Chemical behaviour of ground waste glass when used as partial cement replacement in mortars. Constr Build Mater. 2013;44:74–80.
- Patel D, Shrivastava R, Tiwari RP, et al. Properties of cement mortar in substitution with waste fine glass powder and environmental impact study. J Build Eng. 2020;27:100940.
- Wang YR, Cao YB, Zhang P, et al. Effective utilization of waste glass as cementitious powder and construction sand in mortar. Materials. 2020;13(3):707.
- Olofinnade OM, Ndambuki JM, Ede AN, et al. Application of waste glass powder as a partial cement substitute towards more sustainable concrete production. JERA. 2017;31:77–93.
- Ahmad J, Zhou ZG, Usanova KI, et al. A step towards concrete with partial substitution of waste glass (WG) in concrete: a review. Materials. 2022;15(7):2525. Apr
- Gimenez-Carbo E, Soriano L, Roig-Flores M, et al. Characterization of glass powder from glass recycling process waste and preliminary testing. Materials. 2021;14(11):2971. Jun
- Kamali M, Ghahremaninezhad A. Effect of glass powders on the mechanical and durability properties of cementitious materials. Constr Build Mater. 2015;98:407–416. Nov
- Ali HA, Xuan DX, Poon CS. Assessment of long-term reactivity of initially lowly-reactive solid wastes as supplementary cementitious materials (SCMs). Constr Build Mater. 2020;232:117192. Jan
- Nasry O, Samaouali A, Belarouf S, et al. Thermophysical properties of cement mortar containing waste glass powder. Crystals. 2021;11(5):488.
- Pan Z, Tao Z, Murphy T, et al. High temperature performance of mortars containing fine glass powders. J Cleaner Prod. 2017;162:16–26. Sep
- Jing GQ, Huang G, Zhu WJ. An experimental study on water permeability of architectural mortar using waste glass as fine aggregate. Materials. 2020;13(5):1110. Mar
- Wang HY, Zeng HH, Wu JY. A study on the macro and micro properties of concrete with LCD glass. Constr Build Mater. 2014;50:664–670. Jan
- Tamanna N, Tuladhar R, Sivakugan N. Performance of recycled waste glass sand as partial replacement of sand in concrete. Constr Build Mater. 2020;239:117804. Apr
- Devaraj R, Jordan J, Gerber C, et al. Exploring the effects of the substitution of freshly mined sands with recycled crushed glass on the properties of concrete. Appl Sci Basel. 2021;11(8):3318. Apr
- Bawab J, Khatib J, El-Hassan H, et al. Properties of cement-based materials containing cathode-ray tube (CRT) glass waste as fine Aggregates-A review. Sustainability. 2021;13(20):11529. Oct
- Sasui S, Kim G, Nam J, et al. Effects of waste glass sand on the thermal behavior and strength of fly ash and GGBS based alkali activated mortar exposed to elevated temperature. Constr Build Mater. 2022;316:125864. Jan
- Kim IS, Choi SY, Yang EI. Evaluation of durability of concrete substituted heavyweight waste glass as fine aggregate. Constr Build Mater. 2018;184:269–277. Sep
- Gorospe K, Booya E, Ghaednia H, et al. Effect of various glass aggregates on the shrinkage and expansion of cement mortar. Constr Build Mater. 2019;210:301–311. Jun
- Saccani A, Bignozzi MC, Barbieri L, et al. Effect of the chemical composition of different types of recycled glass used as aggregates on the ASR performance of cement mortars. Constr Build Mater. 2017;154:804–809. Nov
- Aliabdo AA, Abd Elmoaty AM, Aboshama AY. Utilization of waste glass powder in the production of cement and concrete. Constr Build Mater. 2016;124:866–877. Oct
- Lee H, Hanif A, Usman M, et al. Performance evaluation of concrete incorporating glass powder and glass sludge wastes as supplementary cementing material. J Cleaner Prod. 2018;170:683–693. Jan
- Tchamba AB, Mbessa M, Metekong JVS, et al. Mechanical and microstructural properties of cameroonian bauxite ceramics for ballistic applications. Int J Appl Ceram Technol. 2020;17(3):949–962.
- Matos AM, Sousa-Coutinho J. Durability of mortar using waste glass powder as cement replacement. Constr Build Mater. 2012;36:205–215.
- Sobolev K, Turker P, Soboleva S, et al. Utilization of waste glass in ECO-cement: strength properties and microstructural observations. Waste Manag. 2007;27(7):971–976.
- Wu K, Shi HS, Xu LL, et al. Microstructural characterization of ITZ in blended cement concretes and its relation to transport properties. Cem Concr Res. 2016;79:243–256.