Abstract
Silane coupling reagent (3-mercaptopropyl trimethoxysilane (MPTS)) was prepared on silicon substrate to form two-dimensional self-assembled monolayer (SAM) and the terminal–SH group in the film was in situ oxidised to–SO3H group to endow the film with good chemisorption ability. Thus, TiO2 thin films were deposited on the oxidised MPTS-SAM to form composite thin films, making use of the chemisorption ability of the–SO3H group. Atomic force microscope (AFM), and contact angle measurements were used to characterise TiO2 films. Adhesive force and friction force of TiO2 thin films and silicon substrate were measured under various applied normal loads and scanning speed of AFM tip. Results showed that the friction force increased with applied normal loads and scanning speed of AFM tip. In order to study the effect of capillary force, tests were performed in various relative humidity (RH). Results showed that the adhesive force of silicon substrate increases with RH and the adhesive force of TiO2 thin films only increases slightly with RH. Research showed that surfaces with more hydrophobic property revealed the lower adhesive and friction forces.
Keywords:
1. Introduction
Microelectromechanical systems (MEMS) offer great promise for integration of sensors, signal processing, and communications. Miniature smart systems that interact with the physical world and perform computations and communications with other systems are the goals of MEMS technology Citation1–3. A major hurdle toward wider application of these micro devices is the tribological issues associated with them. A variety of surface modification techniques including deposition of self-assembled monolayers (SAMs) which have advantageous characteristics of well-defined structure, strong head group–substrate binding, and dense packing of hydrocarbon chains have been employed to improve the tribological behaviour of MEMS devices, and have provided varying degrees of success Citation4–6.
Numerous studies have been conducted in order to understand the applications of TiO2 in many fields such as optics, medicine, magnetics, tribology, and so on Citation7–11. A number of studies have been done on the nano-tribological properties of different SAMs Citation12,Citation13, but the study of the TiO2 films on the nano-tribological behaviour is much lacking. The research on the deposition of TiO2 thin films on 3-mercaptopropyl trimethoxysilane (MPTS)-SAM substrates can supply valuable experimental data.
3-Mercaptopropyl trimethoxysilane can be obtained expediently and had been previously used to make functional monolayers Citation14–16. The thiol groups (–SH) can be oxidised into sulfonic acid groups (–SO3H) easily, which can provide both a high degree of surface acidity and net negative charge to deposited TiO2 thin films. In this article, MPTS was deposited by self-assembly technique, providing modestly hydrophobic monolayer films as substrates for the deposition of TiO2 thin films from aqueous solutions. Atomic force microscopy (AFM) had been applied to characterise the structure and nano-tribological properties of self-assembled TiO2 thin films on MPTS-SAM substrates.
2. Experimental
2.1. Materials
Silicon plates were used as substrates for the SAM film transfer. The silicon plates were cut into pieces of ∼1.0 × 1.0 cm before cleaning and modifying. MPTS were purchased from Sigma Aldrich (Deisenhofen, Germany) and used as received. All other chemicals used in chemical manipulations were of reagent grade. Deionised water was obtained from a Barnstead Nanopure apparatus. TiO2 were commercially purchased and the original size is 5–30 nm.
2.2. Preparation of film
First, the preparation of the MPTS-SAM was performed according to the literature Citation16. With proper prehydration, the hydroxide substrates were capable of covalent bonding to the hydrolyzed silane molecules via condensation reaction of silanol groups. Glass substrates were immersed for 30 min in Piranha solution (H2SO4 : H2O2 = 7 : 3(V/V)) at 90°C to make hydroxy radicals on the surfaces. Then the substrates were carefully rinsed with deionised water and dried. After that the hydroxide substrates were dipped into the dehydrated benzene solution containing 0.5 mM of MPTS solution for 12 h, to allow the formation of MPTS-SAM. At last the substrates were cleaned ultrasonically with chloroform, acetone, and deionised water in turn to remove the other physisorbed ions or molecules and dried for 1 h at 120°C, then cooled in a desiccator. The oxidisation of the–SH groups to the desired–SO3H groups was carried out by dipping the substrates into the solution of 30% nitric acid at 80°C for 1 h, followed by washing with distilled water and dried in nitrogen.
The titanate solution was prepared as follows: TiO2 and ethylenediamine tetra-acetic acid (EDTA), etc. were mixed with alcohol, followed by stirring at room temperature for 1 h. Its pH was adjusted to 4–5 using nitric acid. Then the substrates deposited with the sulfonated MPTS-SAM were immersed in the resulting mixed solution at 90°C for 12 h, to allow the adherence of the TiO2 thin films on the sulfonated MPTS-SAM. At last the substrates were cleaned ultrasonically with deionised water to remove the other physisorbed ions or molecules and dried for 2 h at 120°C, then cooled in a desiccator.
2.3. Experimental apparatus and measurements
The microscopic study was conducted on a NanoScope IIIa atomic force microscopy (Digital Instruments Inc.) in the contact mode. All measurements were performed in air at 23°C and 37% relative humidity (RH). Contact angles of water were measured by the sessile drop method using the OCA-20 measurement apparatus (DataPhysics Instruments GmbH) under ambient laboratory conditions (24°C, 40% RH). Measurements were made at a minimum of five different spots on each sample. The results stated below are averages of all these measurements.
During the adhesion measurements, SPM tips were pushed to the flat surface until the normal load reached to a fixed value, and then it was pulled off from the surface until release. The maximum pull-off force was calculated from the force-displacement curve and defined as the adhesive force. In order to investigate the nano-tribological characteristics of SAM-coated surface, an AFM was used for friction measurements. Friction tests were performed using a V-shaped cantilever (radius ∼15 nm, normal stiffness ∼0.12 N m−1). Adhesion and friction tests were carried out with Si3N4 tip of under ambient condition of 20–22°C and 28–35% RH, unless otherwise specified. For each sample, adhesive and friction were measured at more than five times and five different locations.
3. Result and discussion
3.1. Characterisation of the MPTS-SAM and the deposited TiO2 thin film on sulfonated MPTS-SAM
shows the AFM images of hydroxide substrates, MPTS-SAM, oxidised MPTS-SAM, and the TiO2 thin films by contact mode. The Mean Roughness (Ra ) were 0.159, 0.527, 0.2, and 4.464 nm, respectively.
Figure 1. Atomic force microscope images of (a) the hydroxide substrate (b) MPTS-SAM (c) and oxidised MPTS-SAM, and (d) TiO2 thin films.
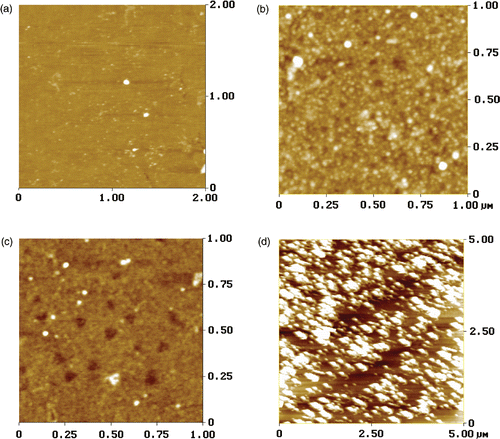
As one of the straight forward methods of identifying the presence of SAM on the surface, contact angle measurements were made. Typically, the coating angle for SAM with respect to deionised water is about 70° Citation16. From , it indicated that MPTS film had been successfully obtained in our work which led to the reduction of the surface energy. And when the terminal groups (–SH) of SAMs were oxidised into sulfonate ones (–SO3H) by dipping in a solution of 30% HNO3, the contact angle of samples decreased from 70° to 31° Citation16. The increase of contact angles from 31° to 64° indicated that the TiO2 film had been successfully obtained in our work which led to the reduction of the surface energy.
3.2. Nano-tribological properties of TiO2 thin film
3.2.1. Influence of RH on the adhesive and friction forces
The influence of RH on the adhesive force was studied in an environment at 25°C. The results were presented in . shows that the adhesive force of silicon substrate increases with RH and the adhesive force of TiO2 thin films only increases slightly with RH. The adhesive force is related to the work of adhesion of the surface which is related to the polarity of the surface terminal Citation17. The TiO2 thin films were deposited on the oxidised MPTS-SAM, making use of the chemisorption ability of the–SO3H group. The TiO2 thin films has nonpolar surface terminal and a very small work of adhesion; thus the adhesive force is not sensitive to the change of humidity. The–Si–O–H group was regarded as one terminal of silicon substrate. The electronegativity of Si and H are 1.9 and 2.1, respectively. This suggests that the silicon substrate has polar surface terminal and larger adhesive force in higher RH, which in turn increases the friction force.
Figure 3. Variation of adhesive forces of silicon substrate and TiO2 thin film under various humidity conditions.
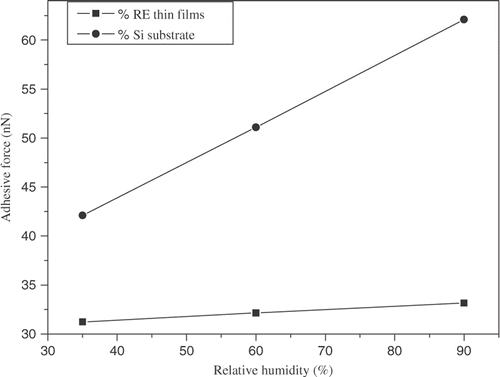
The influence of RH on the friction force was studied. The results were presented in . shows that the friction force of TiO2 thin films is lower than that of silicon substrate at the same RH. From , it can also be seen that the friction force of silicon substrate decreases with RH and the friction force of TiO2 thin films is not sensitive to the change of humidity. The thin adsorbed water layer on sample surface can produce capillary force and with thickness of water layer capillary force became larger in moist condition. The normal force becomes larger with the increasing of capillary force because the direction of capillary force is in the same with the direction of load. From the research above, the adhesive force of TiO2 thin films was smaller than that of silicon substrate. It indicated that water layer was not easy to adsorb on the TiO2 thin films. According to the above discussion, the normal force of TiO2 thin films was smaller than that of silicon substrate and friction force of TiO2 thin films did not change with an increase in humidity. The fact that silicon substrate showed lower friction force when at high RH suggested that a thin adsorbed water layer can act as a lubricant. But it may be related to the thickness of the absorbed layer. When the absorbed layer was thick enough, it can act as a kind of liquid lubricant rather than forming water capillary.
3.2.2. Influence of sliding velocity on the adhesive and friction forces
The effect of sliding velocity on the adhesive forces of silicon substrate and TiO2 thin films was investigated. shows the experimental result. From , it can be seen that the adhesive forces of silicon substrate and TiO2 thin films do not change with increasing sliding velocity. The adhesive force of sample surface is mostly affected by van der Waals force and capillary force. The change of sliding velocity did not affect van der Waals force and capillary force. So the adhesive force did not depend on the sliding velocity of tip.
Figure 5. Variation of adhesive forces of silicon substrate and TiO2 thin film with scanning speed (RH: 35%).
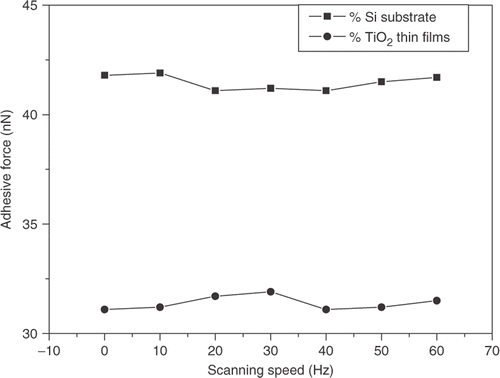
The effect of scanning speed on the frictional force of silicon substrate and TiO2 thin films was observed using a Si3N4 tip. Scan area was set to 2 × 2 µm and normal load was set to 10 nN. The influence of sliding velocity on the friction force is studied as shown in . It was shown that for a silicon substrate, cleaned by Piranha solution just before the friction test, the friction force increased with increasing velocity. also shows the effect of velocity on TiO2 thin films. For TiO2 thin film, the friction force also increased with velocity. But the friction force of silicon substrate was higher than that of TiO2 thin films at lower velocity and the increase in friction force with velocity was large for silicon substrate as compared to TiO2 thin films. It was believed that this difference was caused by the difference of the high stiffness and the viscoelastic properties of substrates. The quick increase in friction force at high velocities was the result of asperity impacts and the corresponding high-frictional energy dissipation at the sliding interface.
Figure 6. Variation of friction forces of silicon substrate and TiO2 thin film with scanning speed (Load: 10 nN, RH: 35%).
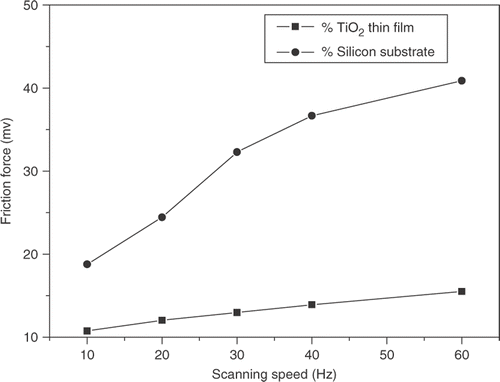
The SAM molecules reorient under the tip normal load. As the tip proceeds along the scan direction, the molecules are “relieved” from the tip load and reorient to their initial position. For our experiments, the underlayer of TiO2 thin films was the MPTS-SAM. MPTS molecules whose chain is short and rigid responds anelastically to mechanical deformation under the tip normal load with recovery after load release having a short-relaxation time. When more time was available for reorientation before the tip reached the same location on the sample surface again, most of molecules in the wake of the tip scan direction will spring back. The result above suggested that the friction force of TiO2 thin films changes lightly with increasing velocity.
3.2.3. Influence of load on the adhesive and friction forces
The average values of adhesive force measured by contact mode AFM were presented in . It showed the adhesive forces between the SPM tip and the sample at various applied normal loads in 35% RH. From the , it is seen that the adhesive force of TiO2 thin films is lower than that of silicon substrate. As the applied normal load increased from 0 to 70 nN, the adhesive force did not change. It was noted that the contact angles of the hydroxide silicon substrate and the TiO2 thin films are 1° and 64°, respectively, which indicated that surface energy of the substrate can be obviously reduced when TiO2 thin films was coated on the silicon substrate. The result implied that the wetting characteristics could be an important factor that affected the adhesion. The adhesive force of sample surface is mostly affected by van der Waals force and capillary force. The capillary force of sample surface is related with water layer on the surface. When the RH of condition did not change, capillary force of sample surface did not change. The van der Waals force of sample surface is related with distance of the AFM tip and sample surface. Therefore, the change of load did not affect van der Waals force and capillary force.
Figure 7. Variation of adhesive forces of silicon substrate and TiO2 thin film with loads (RH: 35%).
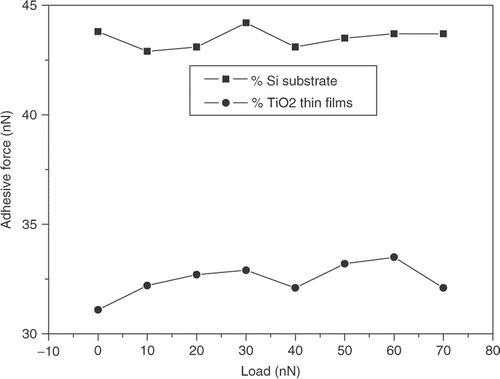
shows the influence of normal load on the friction of TiO2 thin films and silicon substrate. Friction force signals were obtained by scanning a 2 × 2 µm area at speed 5 Hz using an AFM. From the results, it was found that for TiO2 thin films and silicon substrate the friction force increased with increasing load; and the TiO2 thin films showed lower friction than silicon substrate in the testing range of the loads. The difference in the frictional behaviour of TiO2 thin films and substrate may be due to the difference of the surface energy values and surface roughness. From the results above, it was noted that the silicon substrate had a lower surface roughness but a higher surface energy value than the TiO2 thin films. The normal force is the sum of load and adhesive force. From the above research, the adhesive force of TiO2 thin films was smaller than that of silicon substrate. Therefore, the normal force of TiO2 thin films was smaller than that of silicon substrate, and friction force of TiO2 thin films was smaller than that of silicon substrate in same load. From the research, it could be noted the water wetting characteristics played an important role on the nano-friction. The strong bonding between the film and the surface can withstand the shear due to frictional force at light loads. also shows that the friction force increased linearly with the applied normal loads while friction force existed even at a zero applied normal load. It was thought that the adhesive force caused by a capillary action was mainly responsible for this friction force.
4. Conclusions
1. | The results presented above demonstrate that TiO2 thin film was obtained using the self-assembly technique on MPTS-SAM. | ||||
2. | Compared with bare silicon substrate, the adhesive force of TiO2 thin films coated silicon was much less sensitive to RH conditions, applied load, and scanning speed of tip. | ||||
3. | For TiO2 thin film, the friction force increased with increasing slightly RH, applied load, and scanning speed of tip. The TiO2 thin films showed lower friction than silicon substrate in the same test condition. | ||||
4. | The adhesive force of sample surface is mostly affected by van der Waals force and capillary force. The influence of van der Waals force on the adhesive force is not affected by environment. The lower adhesive force of TiO2 thin films was attributed to nonpolar surface terminal. The lower friction of TiO2 thin films is dominated by the lower adhesive force of TiO2 thin films. |
Acknowledgements
The authors would like to thank the help from School Fund (Project No. JD208001), Shanghai Second Polytechnic University.
References
- Eappen , KC , Patton , ST and Zabinski , JS . 2002 . Lubrication of micro-electromechanical systems (MEMS) using bound and mobile phases of fomblin zdol . Tribol. Lett. , 12 : 35 – 42 .
- Yoon , ES , Yang , SH , Han , HG and Kong , H . 2003 . An experimental study on the adhesion at a nano-contact . Wear , 254 : 974 – 980 .
- Patton , ST and Zabinski , JS . 2005 . Fundamental studies of Au contacts in MEMS RF switches . Tribol. Lett. , 18 : 215 – 230 .
- Cha , KH and Kim , DE . 2001 . Investigation of the tribological behavior of octadecyltrichlorosilane deposited on silicon . Wear , 251 : 1169 – 1176 .
- Ashurst , WR and Yau , C . 2001 . Alkene based monolayer films as antistiction coatings for polysilicon MEMS . Sens. Actuators A Phys. , 91 : 239 – 248 .
- Maboudian , R , Ashurst , WR and Carraro , C . 2000 . Self-assembled monolayers as anti-stiction coatings for MEMS: characteristics and recent developments . Sens. Actuators A Phys. , 82 : 219 – 223 .
- Konishi , Y , Shimaoka , JC and Asai , S . 1998 . Sorption of rare-earth ions on biopolymer gel beads of alginic acid . React. Funct. Polym. , 36 : 197 – 204 .
- Sidebottom , DL , Hruschka , MA , Gpotter , AB and Brow , RK . 1997 . Structure and optical properties of rare earth-doped zinc oxyhalide tellurite glasses . J. Non-Cryst. Solids , 222 : 282 – 287 .
- Cheng , XH and Bai , T . 2006 . Characterization and tribological investigation of self-assembled lathanum-based thin films on glass substrates . Wear , 260 : 745 – 751 .
- Yu , LG , Lian , YF and Xue , QJ . 1998 . Investigation of tribological behavior of lanthanum-based thin films on sulfonated self-assembled monolayer . Wear , 214 : 114 – 119 .
- Chen , BS , Dong , JX and Ye , Y . 1998 . Lubrication performances of rare earth compounds . J. Rare Earth. , 16 : 358 – 362 . (in Chinese)
- Cha , KH and Kim , DE . 2001 . Nanotribological properties of organic boundary lubricants: Langmuir films versus self-assembled monolayers . Wear , 251 : 489 – 495 .
- Bhushan , B . 2005 . Nanotribology and nanomechanics . Wear , 259 : 1507 – 1513 .
- Wang , JQ , Yang , SR , Liu , XH , Ren , SL , Guan , F and Chen , M . 2004 . Preparation and characterization of ZrO2 thin film on sulfonated self-assembled monolayer of 3-mercaptopropyl trimethoxysilane . Appl. Surf. Sci. , 221 : 272 – 276 .
- Alessandro , A , Nunzio , T , Silvio , Q , Giovanni , M and Fausto , P . 2004 . ToF-SIMS investigation of functional mixed aromatic thiol monolayers on gold . Appl. Surf. Sci. , 231–232 : 314 – 321 .
- Xiao , ZL , Su , L , Gu , N , Lu , Z and Wei , Y . 1998 . The growth of TiO2 thin films on mixed self-assembly monolayers from solution . Thin Solid Films , 333 : 25 – 37 .
- Liu , HW and Bhushan , B . 2002 . Investigation of nanotribological properties of self-assembled monolayers with alkyl and biphenyl spacer chains . Ultramicroscopy , 91 : 185 – 194 .