Abstract
A novel aluminium–zirconia composite, with improved wear resistance, has been produced. The method consists of compacting aluminium powder mixed with cellulose fibres, which are then eliminated by a heat treatment. The compacted piece was immersed several times in a colloidal (i.e. nanosized) zirconia solution until a constant weight was reached. The solution penetrated and infiltrated the preform. Then, the aluminium matrix presented zirconia tetragonal and monoclinic phases. Wear test was carried out in a pin-on-disc machine. By measuring the weight loss it was shown that the composite had significant improvement in wear resistance, as compared to pure aluminium.
1. Introduction
Metal–matrix composites (MMCs) are increasingly attracting interest because of their superior mechanical and tribological properties. These interesting materials generally consist of a metal matrix in which non-metallic fibres, particles or whiskers are dispersed. Normally, particulate-reinforced composites cost less than fibre reinforcement composites Citation1. Synthesis techniques in these cases include powder metallurgy, mechanical alloying, squeeze casting, stir casting, compocasting and low-pressure infiltration, among others. The wear behaviour of MMCs depends on the nature of particle reinforcement and on the nature of the matrix containing them. Silicon carbide and alumina are amongst the most common ceramic particles for this purpose.
Aluminium is a very attractive metal matrix for a number of technical and economical reasons. However, the wear resistance of aluminium is low in dry sliding. Moreover, prediction of wear is difficult because it is not an intrinsic property of the material but rather a function of the system. The wear resistance depends largely on the nature of the wearing surface and on the rubbing condition. A slight change in these factors sometimes causes a big difference in wear Citation2. A method to improve wear resistance is by forming a particle-dispersed alloy. Aluminium-based MMCs can provide excellent wear resistance, provided the possible limitations of the benefits of reinforcement are appreciated Citation3. Accordingly, in the last few years, aluminium matrix composites have been utilised in high-tech structural and functional applications including aerospace, defense, automotive and thermal management areas, as well as in sport and recreation Citation4.
From the industrial standpoint, it is advantageous to fabricate metal matrix-particulate composites using powder metallurgy because the fabricated composites possess a higher dislocation density, a small sub-grain size and limited segregation of particles Citation5. Aluminium–matrix-based composites have exhibited further improvement in the mechanical properties of ceramic particulates. A nanocrrystalline ZrO2/Al composite has been fabricated by the squeeze casting route using specially designed casting equipment Citation6.
There are few investigations of aluminium–matrix-based composites with reinforcement of zirconia, which has low adhesion to aluminium, Therefore, the processing of powder metals shows advantages over conventional methods of casting. Aluminium–matrix composites containing nanometre-sized particles of zirconia were prepared by the hot pressing technique, showing an increase in hardness Citation7. Studies on aluminium MMCs synthesised with nanosized dispersions of mullite and zirconia through uniaxial hot-pressing at temperatures in the range of 450–610°C showed that the values of dislocation density increased with temperature Citation8.
In preliminary research by our group, the compressed aluminium pieces were immersed in a colloidal solution of zirconium, and evidence of wear resistance was reported Citation9. An analysis of the conditions required for the infiltration was reported as well Citation10. In this present work, results on infiltration through an ammonium zirconium carbonate solution are presented. The wear resistance of aluminium-based MMCs, obtained by powder metallurgy, where the reinforcing zirconia was infiltrated according to the optimal conditions (pressure viscosity, number of immersions, etc.), is reported as well.
2. Experimental
2.1. Compacting, infiltration and sintering of composites
Two types of composites were created. The first one was compacted aluminium powder without the addition of cellulose fibres. The second one was compacted aluminium added with various amounts of cellulose fibres. The materials used were a fine aluminium powder (Almex), less than 100 µm in size and cellulose fibres (Fibrocel). The materials were mixed together, and the mixture was compacted at room temperature in an automatic hydraulic press, Graseby T-40. The mold was filled with the mix, and then 175 MPa of pressure were applied for 30 s to obtain cylindrical pieces 2 cm in diameter and 0.7 cm in height, The size distribution of the aluminium powder particles facilitated the filling process, since the empty spaces between the larger particles were filled by smaller particles. The fibres were eliminated when heat-treated at 240°C.
The compacted pieces were immersed several times in the stabilised ammonium zirconium carbonate solution (Mel Chemicals), until the weight reached a constant value. This solution, with a viscosity of 5 cp, penetrated the piece, infiltrating the narrow channels of the preform. Afterwards, when the solution was dry, it changed to a gel.
Specimens were sintered at a temperature of 600°C in standard atmosphere in a Lindberg oven; model 51848 CTD for 3 h. During the sintering, the lowering of the free energy of the particles produces agglomeration. The conditions of immersion, compacting, sintering and wear were the same for both composites, and both were compared with pure aluminium.
2.2. Tests for wear resistance
The tests for wear resistance were done in a pin-in-disk machine. The pin is an aluminium cylinder that is pushed from above to a level surface of a rotating steel disk. To carry out the tests of wear resistance, a Jean Wirtz polishing machine, TG-250 with an odometer to measure the rpm's, was used. A steel disc, treated thermally to achieve a hardness of 48 HRC in the Rockwell scale, was employed. We attached the steel disc to the machine to produce wear, and also an additional part was connected to the pin so we could add and change weight during the sliding wear tests.
The composite pins were submitted to wear tests on the disc, at a speed of 360 rpm and with a load of 9 N, without lubrication for 2 h. The weight loss of the piece due to wear was every 30 min.
3. Results and discussion
The amorphous gel obtained from the colloidal solution of zirconium underwent changes in its appearance when thermally treated. After the treatment, the zirconia presented crystalline phases, both monoclinic and tetragonal at low temperatures. shows the corresponding XRD patterns: at 450°C there exists a transformation from amorphous to tetragonal structure, and at 600°C, monoclinic and tetragonal phases coexist. This is important because the sintering of aluminium must be lower than its fusion point (660°C).
In , the wear behaviour of the composite is shown, the composite being the compacted aluminium powder without the addition of cellulose fibres, but later infiltrated with zirconia. It is then compared with pure aluminium. A decrease in the wear of the composite with respect to pure aluminium is observed. However, for this composite, the quantity of zirconia which infiltrated the preform was less than 1%, and the analysis of the preforms by Scanning Electron Microscopy indicated that the infiltration was only partial in the piece. It was observed that all of the zirconia penetrated only 2 mm, decreasing towards the interior of the preform. shows a photograph where a ring, which contains zirconia, can clearly be appreciated.
The behaviour of wear of composites was in dry sliding against steel counterfaces. The results of the wear resistance tests are shown in , which correspond to preforms compacted of aluminium powder with cellulose fibres. For these tests, it is important to say that various preforms with different quantities of cellulose fibres were used, and that the infiltration was done with and without elimination of the fibres. However, when the fibres were not eliminated, the infiltration was poor. On the other hand, the composite in which the fibres were eliminated prior to reinfiltration showed improvements in wear resistance. The reinfiltration with the colloidal solution was carried out until it reached a constant weight. Afterwards, the preform was sintered. The tribological behaviour can be seen in , where there is less loss of weight of the composite, as compared to pure aluminium. This composite showed wear resistance in preforms with 0.2 and 0.1% in weight, but the best result was when a weight of 0.05% of fibre was used.
Figure 4. Wear vs. time for the aluminium–zirconia composites (cellulose fibres have been eliminated). The pure alloy is also displayed.
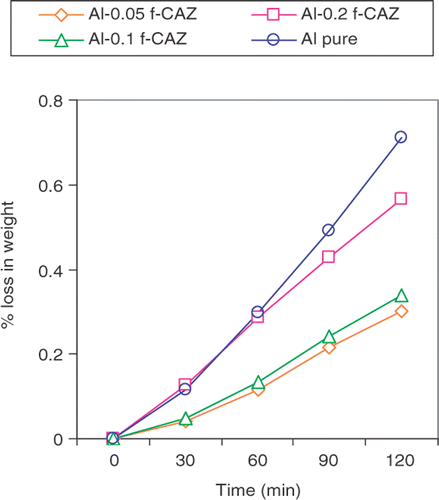
In , a SEM micrograph of the interior of a preform of the composite aluminium–zirconia in which fibre was used is shown. In this figure, the porosity can be observed, allowing an infiltration with a larger quantity of zirconia, up to 3% in weight, and also more homogeneity of the zirconia throughout the interior of the preform. The material showed a 4% increase in hardness and 2.715 gr cm−3 of density.
4. Conclusions
The process described is rather simple. The pieces were obtained in the best conditions of compactation and immersion. There is zirconia present in interconnected porosity. The best wear resistance was observed in the composite of aluminium–zirconia, using 0.05% cellulose fibres to create the porosity, which allowed a homogeneous distribution of zirconia. The zirconia present was approximately 3% in weight in the interior of the aluminium preforms. The diminish of wear is due to the fact that the ceramic material introduced into the pores acts as a reinforcement. The best tribological behaviour of this composite was achieved when there was a bigger presence and distribution of zirconia in the specimens, which resulted in increased porosity when mixed with the cellulose fibres during the compacting process. Elimination of the fibres afterwards created more interconnected porosity and, as a result, the quantity of zirconia was increased. Following this new methodology a composite with improved wear resistance (twice as much) was obtained.
Acknowledgements
The authors are indebted to Margarita Reyes (Instituto de Geologia, UNAM) for her technical help. This work was supported through a Promep program (folio UGTO-EXB-51).
References
- Rohatgi , PK , Lie , Y and Ray , S . 1992 . “ Friction and wear of metal-matrix composites ” . In Friction, Lubrication and Wear Technology, ASM Handbook , Edited by: Blau , PJ . Vol. 18 , 801 – 811 . Metals Park, OH : ASM International .
- Shiota , I and Suzuki , M . 1993 . “ Wear resistance of metal matrix composites ” . In Mechanical Properties of Metallic Composites , Edited by: Ochia , S . 681 – 704 . New York : Marcel Dekker Inc. .
- Hutchings , IM , Wilson , S and Alpas , AT . 2000 . Wear of aluminum-based composites . Compre. Compos. Mater. , 3 : 501 – 519 .
- Surappa , MK . 2003 . Aluminium matrix composites: Challenges and opportunities . Sadhana , 28 ( 1&2 ) : 319 – 334 .
- Liu , YB , Lim , SC , Lu , L and Lai , MO . 1994 . Recent development in the fabrication of metal matrix-particulate composites using powder metallurgy techniques . J. Mater. Sci. , 29 ( 8 ) : 1999 – 2007 .
- Geng , L , Ochiai , S , Peng , HX , Gao , L , Sun , J and Sun , ZQ . 1998 . Fabrication of nanocrystalline ZrO2 particle reinforced aluminum alloy composite by squeeze casting route . Scr. Mater. , 38 ( 4 ) : 551 – 557 .
- Pradhan , SK , Datta , A , Chatterjee , A , De , M and Chakravorty , D . 1994 . Synthesis of aluminium matrix composites containing nanocrystalline oxide phase . Bull. Mater. Sci. (India) , 17 ( 6 ) : 849 – 853 .
- Shee , SK , Pradhan , SK and De , M . 1998 . Effect of thermal stress on the microstructures of aluminium metal matrix composites . Mater. Chem. Phys. (Switzerland) , 52 ( 3 ) : 228 – 234 .
- Jimenez , S , Rodriguez , R , Lima , R , Fuentes , R , Rubio , E , Herrera , A and Castaño , V . 2000 . Tribological improvement of aluminum infiltrated with zirconia nanoparticles . Mater. Res. Innovations , 4 ( 1 ) : 42 – 44 .
- Fuentes , R , Rubio , E , Herrera , A , Ramos , E , Jiménez , S and Castaño , VM . 2001 . Modificación de Probetas de Aluminio Mediante Inmersión en Soles de Zirconio , Vol. 11 , 22 – 27 . Mexico : Acta Universitaria . No. 3