Abstract
Onion-like graphite structures, also called carbon spheres (CSs), represent another new allotropic nanophase of carbon materials, which can be potentially used as single electron devices, magnetic refrigerators, nanodiodes, nanotransistors, nanoball bearings, insulator lubricants as well catalyst supports. In this study, carbon nanospheres were synthesised in a vertical swirled floating catalytic chemical vapour deposition reactor for the first time. This process allows for continuous and large scale production of these materials. The CSs were obtained by the pyrolysis of acetylene in an inert atmosphere. The effect of pyrolysis temperatures and the flow rate of argon carrier gas on the size, quality and quantity of the synthesised CSs were investigated. Transmission electron microscope analysis of the carbon material revealed graphitic spheres with a smooth surface and a uniform diameter that could be controlled by varying reaction conditions (size: 50–250 nm). The materials were spongy with very low density. The CS production rate was found to increase with the increase in pyrolysis temperature (900–1000°C) and with flow rates of the carbon source (70–370 mL min−1) and carrier gas (70–480 mL min−1). Thermogravimetric analysis, powder X-ray diffraction and carbon, hydrogen and nitrogen analysis of the samples revealed that the products mainly contained CSs (98% carbon) and Raman spectroscopy revealed that the degree of graphitisation increased with the increase in pyrolysis temperature (900–1000°C).
1. Introduction
Spherical carbon structures have been receiving interest since their discovery in the 1940s Citation1 and especially since the discovery of the fullerenes in 1985 Citation2. Indeed, in the past two decades many different types of spherical carbons have been reported, both hollow and solid, and these include carbon onions Citation3,Citation4, carbon microspheres (CMSs) Citation5–9, carbon beads Citation10–12 and carbon pearls Citation13. The type of spherical particle produced is dependent on the method of preparation, carbon source and the reaction conditions used Citation5–12. These spherical materials have many potential applications, such as use as absorbents Citation14,Citation15, as catalyst supports Citation16 or as anodes for use in lithium ion batteries Citation9,Citation17.
In the course of the work reported here, carbon spheres (CSs), both CMSs and carbon nanospheres (CNSs), have been produced in a vertical reactor using a vertical mixer i.e. using a vertical swirled floating catalyst (SFC) reactor. The method provides a means for the continuous production of high purity CSs with uniform diameter in the absence of a catalyst. Previously other methods, such as chemical vapour deposition Citation18, pyrolysis of carbon sources and catalysts Citation19, an arc plasma technique Citation20, mixed-valence oxide-catalytic carbonisation Citation6 and reduction of carbides with metal catalysts Citation21 have been reported for the synthesis of CSs.
CSs have been known for many decades and have been made by procedures similar to the procedure described herein. These materials, referred to as carbon black particles Citation22,Citation23, have been produced from a carbon source, such as oil or natural gas, typically in the presence of small amounts of oxygen. For example, when acetylene is burned under a reduced presence of oxygen the process is called the acetylene black process Citation24–26. While much information has been generated in this area, to our knowledge, no report has appeared that systematically relates CS particle size (as determined by electron microscope studies) to reaction conditions as described in this study.
2. Experimental
The synthesis of CSs was carried out in a swirled floating catalytic chemical vapour deposition (SFCCVD) reactor developed by Iyuke and Danna Citation27,Citation28 and is presented schematically in . Briefly, it consists of a vertical quartz reactor loaded in a tubular furnace. Gases (argon, nitrogen and acetylene) flow, with the aid of a system of valves and rotameters, through a swirled coiled passage that enables mixing of the gases before they enter the reactor ().
The furnace was set to a desired temperature under a nitrogen flow (30 mL min−1), which was then stopped and acetylene (C2H2) together with an inert gas (argon) was fed through the reactor at specified flow rates. A smoky carbon vapour together with black soot from the direct pyrolysis of C2H2 was generated and carried to the upper end of the reactor where it was cooled in a condenser (room temperature) and collected in two cyclones. The product from the cyclones was analysed using transmission electron microscopy (TEM) (JEOL 100S Electron Microscope and a Philips CM200 High Resolution TEM), thermogravimetric analysis (TGA) (Perkin Elmer Pyris 1 TGA Anaylzer), Raman spectroscopy (J-Y T64000 micro-Raman spectrometer equipped with a liquid nitrogen cooled charge coupled device detector and excitation laser wavelength of 514.5 nm), BET surface area analysis (Micromeritics TriStar Surface Area and Porosity Analyzer) and powder X-ray diffractometry (PXRD) (Bruker axs D8 Advance PXRD). The carbon, hydrogen and nitrogen (CHN) content was performed at the Institute for Soil, Climate and Water (Pretoria). The reaction temperature (900–1000°C), acetylene (70–370 mL min−1) and argon (70–480 mL min−1) gas flow rates were varied in order to study their effect on the structure and yields of the CSs obtained.
3. Results and discussion
3.1. Characterisation of CSs
No catalyst was used for the synthesis of the CSs. The materials produced were mainly carbon (∼98%) and unlike products obtained during synthesis in the presence of a catalyst, the CSs contained no amorphous material and did not require removal of catalyst in a post-synthesis process. The yield and sizes (50–250 nm) of the spheres formed could be controlled by changing the reaction conditions. A typical example is described below.
C2H2 (118 mL min−1) was passed through the reactor at 900°C. The reaction was stopped after 4 min (gas flow changed to argon) and 1.4 g of soot was collected from both the reactor and the cyclones. The synthesis time was determined by the maximum amount of carbon soot deposited in the reactor and cyclones. TEM analysis of the soot from both the reactor and the cyclone appeared to be identical. A TEM image of the soot () reveals that only spherical nanoparticles of carbon (>99%) were formed and that these spheres have an average diameter of 100 nm and show a narrow distribution range. The time that the acetylene spends in the reactor is estimated to be 33 s and within this short time frame the spheres are already accreted Citation7.
Figure 2. (a) TEM image of CSs produced by the SFCCVD technique at 900°C with C2H2 gas flow rate of 118 mL min−1. (b) Corresponding HRTEM image of the CSs. (c) HRTEM image of CSs synthesised in a horizontal furnace with the diffraction pattern of the shell of the CS (inset).
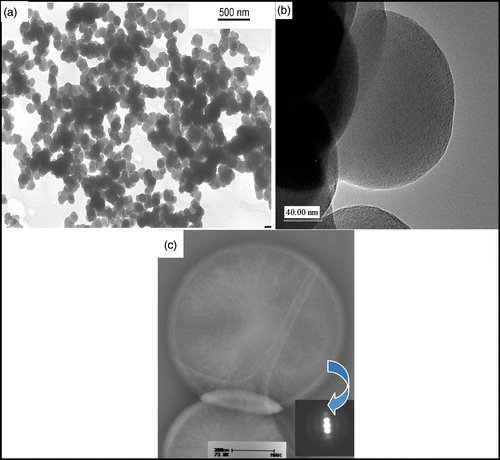
It is clear that at this high temperature, the carbon radicals formed in the gas phase under these conditions nucleate and rapidly form solid spheres Citation6–8. The current mechanism for sphere growth is consistent with the results found in earlier studies Citation7,Citation29. What is unusual is that the sizes of the spheres are uniform in diameter (refer to distribution plot). This suggests that nucleation must commence at the reactor inlet and that once nucleation has commenced deposition of further carbon onto the sphere must be more rapid than further nucleation at the upper end of the reactor. It would appear that once nuclei are formed, the rate of sphere formation will then be determined by the C2H2 concentration and the reactor length. However, it also appears that once the sphere has reached an optimum size then little further growth of the sphere takes place.
The spheres form a low density and fluffy material, quite different in texture from the spheres that we have obtained from similar studies performed in a horizontal reactor Citation30. In the horizontal reactor, the spheres are left in the reactor at high temperature for a much longer time (15–120 min) resulting in secondary reactions occurring on the sphere perimeter. High-resolution transmission electron microscopy (HRTEM) analysis of the two types of spheres also reflects this difference (). Spheres obtained from a horizontal reactor have a distinctive core/shell structure whereas the spheres synthesised in the vertical reactor do not show this phenomenon (). As seen in the HRTEM image the spheres show a poorly graphitic structure with short (wavy) carbon layers next to and on top of each other. The surface area analysis of the spheres gave a value of 7 m2 g−1 indicating that the spheres had little or no porosity. CHN analysis of the spheres revealed that the materials contained carbon (∼98%) and the remaining 2% comprising hydrogen and possibly some oxygen.
The effect of heat treatment on the CS morphology was investigated. The CSs were placed in a quartz boat in a horizontal furnace and heated under a continuous flow of nitrogen (40 mL min−1) at 800°C for 1 h. Upon heating, the surface area of the CSs increased to 15 m2 g−1. TGA analysis of both the as-prepared and post-heated samples is shown in . The TGA data indicates an approximately 20% mass loss between 100°C and 400°C for the as-prepared spheres, which is not observed after post-treatment heating. The results are consistent with the surface area data and suggest that the spheres prepared in the vertical reactor contain readily removed species (either covalently or physically attached). When the CSs were heated in the reactor under a continuous flow of argon, a black oily substance was generated inside the reactor. It is presumed that this oil may be associated with the 20% material lost in the TGA experiment. This grease was also formed when the CSs were synthesised in a horizontal furnace. However in the horizontal CVD reactor, the grease is found at the exit end of the reactor Citation30. As this material found in both the horizontal and vertical reactors must be a precursor to the solid spheres, we have not as yet undertaken analysis of this material.
The HRTEM analysis of the post-heated material is shown in . The image reveals that the CSs are made up of disordered arrays of graphene sheets of carbon. These layers are estimated to be 2–3 Å apart and they form a spherical shape that typifies the CSs. It can be observed that some of the spheres are linked together (accreted) (see arrows indicating the region where two spheres have coalesced in ). No outer core shell is again observed for the CSs produced even after the post-heating process Citation30. Thus no significant change in the sphere morphology occurs in the post-heating process.
3.2. Effect of C2H2 flow rate and temperature
A series of experiments were carried out to study the effect of acetylene flow rate and temperature on the production rate, size and structural morphology of the CSs. The acetylene gas flow rate was varied from 70 to 370 mL min−1 while the pyrolysis temperatures used were 900°C, 950°C and 1000°C, respectively. The rate of production of CSs increased with increase in the feedstock flow rate at all pyrolysis temperatures. In general, a higher temperature results in a modest increase in yield (). A maximum production rate of ∼0.35 g min−1 was obtained using an acetylene flow rate of 370 mL min−1 and a pyrolysis temperature of 1000°C. The small effect of temperature suggests that above a certain minimum temperature that the carbon species required to form the spheres are available in sufficient concentration and do not limit sphere formation.
shows the sizes of CSs obtained with different C2H2 gas flow rates and at different pyrolysis temperatures. The results show that at 900°C and as the flow rate of C2H2 increases, the size of the CSs decreases. This observation relates to the residence time of C2H2 in the reactor. The residence time of C2H2 will be higher at the lower flow rate of C2H2 and this will allow the products to further accumulate reactants before exiting into the cyclones. Results also show that the CS size increases as the pyrolysis temperature increases. At a fixed C2H2 flow rate of 118 mL min−1, the size of the CSs increases from 120 nm to 150 nm as the pyrolysis temperature increases from 900°C to 1000°C.
Table 1. Diameters of CSs produced at different temperatures and C2H2 gas flow rates.
The effect of C2H2 dilution, with carrier gas (Ar), on the production rate of the CSs was also investigated at 1000°C. The Ar flow rate was varied from 70 to 370 mL min−1 while the C2H2 flow rate was fixed at 181 mL min−1. In general, at the same flow rate, dilution of C2H2 with argon at the same total flow rate is expected to lead to lowered yields of soot. However, at the increased total flow rate the data () show that the rate of formation increases with dilution. Furthermore, the effect is not linear and a drop in sphere formation rate is to be noted between argon flow rates of 250 and 350 mL min−1. This result is reproducible. As the flow rate of the carrier gas increased beyond 310 mL min−1, the production rate of CSs, as expected, again increased. The size distributions of the CS products are shown . The spheres are quite uniform in size (>80%) and possess similar features of the CSs produced without Ar as a carrier gas.
Figure 6. Effects of carrier gas on rate of CS production at constant flow rate of acetylene and temperature.
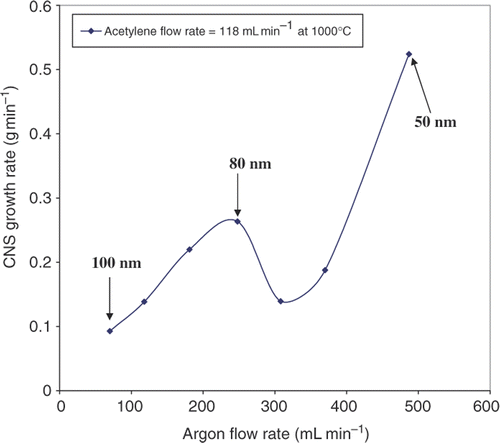
Figure 7. TEM images of CSs synthesised with Ar as carrier gas at (a) 487 mL min−1, (b) 248 mL min−1 and (c) 70 mL min−1. Histograms for the corresponding size distributions of the CSs are shown on the right side of the TEM images.
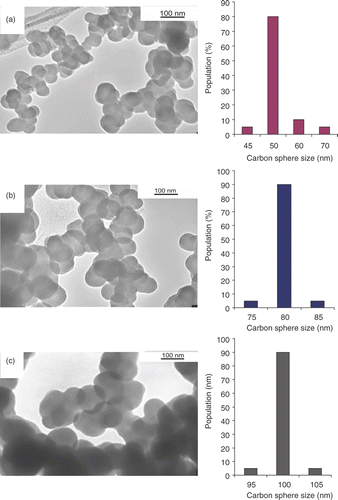
The PXRD patterns of CSs synthesised with and without carrier gas are shown in . The pattern shows two peak at 26° and 45° corresponding to carbon peaks. The PXRD of both samples show that the peaks are broad; an observation that is attributed to low graphitisation of the sample Citation31. No differences were noted between the two PXRD patterns indicating that the Ar had no impact on the CS structure.
The Raman spectra () of CSs produced at different temperatures (900°C, 950°C, 1000°C) and constant C2H2 flow rate (118 mL min−1) show the presence of two broad peaks at about 1350 cm−1 and 1580 cm−1 corresponding to the D- and G-bands of graphite, respectively. The I D /I G ratios (derived from the peak areas) were ∼4.73, 3.23 and 1.22 at 900°C, 950°C and 1000°C, respectively. Appearance of the bands is consistent with the presence of defects and disorder in the samples Citation31. Raman spectra also reveal that the intensity ratio of the two bands i.e. I D /I G decreases with increase in pyrolysis temperature. The value of I D /I G at 1000°C (∼1.22) indicates that the degree of graphitisation of the samples at this temperature has improved suggesting that at higher temperatures the graphitic layers become more ordered.
The defectiveness of the samples produced at 900°C and 950°C, associated with the high values of I D /I G , suggest that the chemical reactivity of the samples should readily lead to surface modification of the CSs. This in turn could lead to the use of CSs in various applications (e.g. catalysis) as suggested by Jin et al. Citation31 and Xu et al. Citation32. A broad peak at ∼1000 cm−1 was also observed in the Raman spectra of the CSs. This peak was found to be present even after post-heating of the CSs. At this stage the origin of this absorption is unknown and instrumental error is suspected Citation29.
4. Conclusions
CSs of diameters in the range 50–250 nm have been synthesised in a vertical SFCCVD reactor, which is a continuous process. The CSs were produced using direct pyrolysis of acetylene gas without the presence of a catalyst. A maximum production rate of about 0.35 g min−1 was obtained at an acetylene flow rate of 370 mL min−1 and a pyrolysis temperature of 1000°C which gives an indication that this process allows for the large scale production of these materials. The produced CSs were of uniform diameter and the size (nano or micro) could be controlled by changing the pyrolysis temperature as well as gas flow rates of both acetylene and Ar. However, the effect of gas flow rates displayed a larger impact on the size of the CSs compared to the temperature effect. As the Ar flow rate increased the amount of material increased and the size of the spheres became smaller.
Acknowledgements
The authors wish to acknowledge the DST/NRF Centre of Excellence in Strong Materials, the Mellon Postgraduate Mentoring Scheme, the CSIR (Pretoria) and the University of the Witwatersrand for funding this work. They also thank Mr Rudolf Erasmus for Raman analysis and Professor Mike Witcomb for TEM analysis.
References
- Smith , WR . 1949 . Encyclopaedia of Chemical Technology , Vol. 3 , 39 – 43 . New York : Interscience .
- Kroto , HW , Heath , JR , O’Brien , SC , Curl , RF and Smalley , RE . 1985 . C60: Buckminsterfullerene . Nature , 318 : 162 – 163 .
- Ugarte , D . 1992 . Curling and closure of graphitic networks under of a relatively well organised carbon structure . Nature , 359 : 707 – 709 .
- Banhart , F and Ajayan , M . 1997 . Self-compression and diamond formation in carbon onions . Adv. Mater , 9 : 261 – 263 .
- Kang , ZC and Wang , ZL . 1996 . Mixed-valent oxide-catalytic carbonization for synthesis of monodispersed nano sized carbon spheres . Philos. Mag. B , 73 : 905 – 929 .
- Wang , ZL and Kang , ZC . 1996 . Pairing of pentagonal and heptagonal carbon rings in the growth of nanosize carbon spheres synthesized by a mixed-valent oxide-catalytic process . J. Phys. Chem. , 100 : 17725 – 17731 .
- Kang , ZC and Wang , ZL . 1996 . On accretion of nanosize carbon spheres . J. Phys. Chem. , 100 : 5163
- Wang , ZL and Kang , ZC . 1997 . Graphitic structure and surface chemical activity of nanosized carbon spheres . Carbon , 35 : 419 – 426 .
- Sharon , M , Mukhopadhyay , K , Yase , K and Ijima , SX . 1998 . Spongy carbon nanobeads – A new material . Carbon , 36 : 507 – 511 .
- Inagaki , M , Washiyama , M and Sakai , M . 1988 . Production of carbon spherules and their graphitization . Carbon , 26 : 169 – 172 .
- Kamegawa , K and Yoshida , H . 1997 . Preparation and characterization of swelling porous carbon beads . Carbon , 35 : 631 – 639 .
- Wang , YG , Chang , YC , Ishida , S , Korai , Y and Mochida , I . 1999 . Stabilization and carbonization properties of mesocarbon microbeads (MCMB) prepared from a synthetic naphthalene isotropic pitch . Carbon , 37 : 969 – 976 .
- Biró , LP , Márk , GI , Horváth , ZE , Kertész , K , Gyulai , J , Nagy , JB and Lambin , Ph . 2004 . Carbon nanoarchitectures containing non-hexagonal rings: ‘Necklaces of pearls’ . Carbon , 42 : 2561 – 2566 .
- Vignal , V , Morawski , AW , Konno , H and Inagaki , M . 1999 . Quantitative assessment of pores in oxidized carbon spheres using scanning tunneling microscopy . J. Mater. Res. , 14 : 1102 – 1112 .
- Inagaki , M , Vignal , V , Konno , H and Morawski , AW . 1999 . Effect of carbonization atmosphere and subsequent oxidation on pore structure of carbon spheres observed by scanning tunneling microscopy . J. Mater. Res. , 14 : 3152 – 3157 .
- Auer , E , Freund , A , Pietsch , J and Tacke , T . 1998 . Carbon as support for industrial precious metal catalysts . Appl. Catal. , 173 : 259 – 271 .
- Flandrois , S and Simon , B . 1999 . Carbon materials for lithium-ion rechargeable batteries . Carbon , 37 : 165 – 180 .
- Serp , Ph , Feurer , R , Kalck , Ph , Kihn , Y , Faria , JL and Figueiredo , JL . 2001 . A chemical vapour deposition process for the production of carbon nanospheres . Carbon , 39 : 621 – 626 .
- Liu , XY , Huang , BC and Coville , NJ . 2002 . The Fe(CO)5 catalyzed pyrolysis of pentane: Carbon nanotube and carbon nanoball formation . Carbon , 40 : 2791 – 2799 .
- Qiu , JS , Li , YF , Wang , YP , Liang , CH , Wang , TH and Wang , DB . 2003 . A novel form of carbon micro-balls from coal . Carbon , 41 : 767 – 772 .
- Lou , ZS , Chen , QW , Gao , J and Zhang , YF . 2004 . Preparation of carbon spheres consisting of amorphous carbon cores and graphene shells . Carbon , 42 : 229 – 232 .
- Wissler , M . 2006 . Graphite and carbon powders for electrochemical applications . J. Power Sources , 156 : 142 – 150 .
- http://www.carbonblack.jp/en/cb/youto.html#top (accessed on 02/02/2009)
- Lahaye , J . 1992 . Particulate carbon from gas phase . Carbon , 30 : 309 – 314 .
- Fallcheri , F and Schwob , Y . 1995 . From methane to hydrogen carbon black and water . J. Hydrogen Energy , 20 : 197 – 202 .
- Scully , DB and Davies , RA . 1965 . Carbon from Aromatic Hydrocarbons , Vol. 9 , 185 – 191 . Manchester : Combustion and Flame .
- Iyuke , SE . ‘A process for producing carbon nanotubes’, PCT application WO 2007/026213 (Published 2007/03/08) priority data ZA 2005/03438 2005/08/29. (2007)
- Iyuke , SE and Danna , ABM . 2005 . Morphological study of carbon nanotubes synthesized by FCCVD . Microporous Mesoporous Mater. , 84 : 338 – 342 .
- Pol , VG , Motiei , M , Gedanken , A , Calderon-Moreno , J and Yoshimura , M . 2004 . Carbon spherules: Synthesis, properties and mechanistic elucidation . Carbon , 42 : 111 – 116 .
- Mhlanga , S , Mondal , K , Naidoo , N , Kunjuzwa , N , Witcomb , M and Coville , N . 2009 . Carbon microsphere supported cobalt catalysts . Afr. J. Chem. , 105 : 304 – 308 .
- Jin , XZ , Gao , C , Hsu , WK , Huczko , A , Bustrzejewski , M , Rue , M , Lee , CY , Acquah , S , Kroto , H and Walton , DRM . 2005 . Large scale production and characterization of carbon spheres prepared by direct pyrolysis of hydrocarbon . Carbon , 43 : 1944 – 1953 .
- Xu , L , Zhang , W , Yang , Q , Ding , Y , Yu , W and Qian , Y . 2005 . A novel route to hollow and solid carbon spheres . Letters to the Editor/Carbon , 43 : 1084 – 1090 .