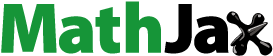
ABSTRACT
Thermal-hydro-mechanical (THM) densification treatments were performed on Populus spp. (poplar), Picea abies (spruce), and Fagus sylvatica (beech). Prior to THM treatment, a low-molecular weight resin was impregnated into the wood structure. Densification results, mechanical characteristics (modulus of elasticity, rupture, and hardness), and set-recovery were assessed. All wood species were exposed to the same THM treatment and the specific anatomy, density, and physical behaviors yielded results specific to wood species making comparisons between species difficult. However, the mechanical performance of all samples was largely dictated by the specimens' surface density as seen in the density profiles. Spruce specimens had high levels of set-recovery after the THM treatment, which is believed to be caused by pit aspiration from kiln drying, limiting impregnation of the resin. The THM treatment used in this study was successfully applied to poplar, spruce, and beech. The resin impregnation combined with THM treatment led to densified wood with improved mechanical properties. The improvements were the greatest in poplar, including the largest reduction in set-recovery, which was the objective of this study. When comparing mechanical properties to commercially available structural wood-composites the results from this study indicate that resin impregnated THM treated wood could be used in this application.
Introduction
Consumers and policy makers are requesting and promoting the use of natural, sustainable materials to lower our dependence upon fossil-based materials, reduce environmental impacts, support local and rural communities, and improve the overall environment in which humans live. Wood is one of these materials, which is a high-performance, multi-hierarchical, cellular composite. Its mechanical capabilities rival those of our most high-tech composites with the ability to transport water and nutrients from ground level to the tops of trees, withstand high winds and loading levels, and sequester carbon and produce oxygen. While a tree is still living, all these features perform when wood tissue is in a high-moisture content state to its benefit. However, when humans would like to use wood for high-performance applications, the relationship with water is still there and must be considered. Wood modification techniques have been used to help valorize under-utilized wood materials and increase their performance with respect to durability, mechanical characteristics, and new forms and functions desired by consumers and designers alike (Sandberg et al. Citation2017).
One group of modifications is thermal-hydro-mechanical (THM) treatments. THM densification uses only heat, water, and mechanical force to compress and densify the wood material. This results in increased density, hardness, abrasion resistance, and some strength properties. During the THM densification process, wood is softened and compressed, resulting in densification without fracturing the cell walls. Compression takes place in a hot press between 120°C to 180°C, in which heat is transferred to the material’s interior through contact with heated plates, dielectric heating, or similar (Navi and Sandberg Citation2012). There have been many examples of wood compression techniques through the last century. The first patents for compressed wood are found in the United States: Sears (1900); Walch and Watts (1923); Olesheimer (1929); Brossman (1931); Esselen (1934); and Olson (1934) (Kollmann et al. Citation1975). The first compressed solid wood in Europe was made in 1930 under the trade name “Lignostone” in Germany, and this type of technology still exists in Switzerland.
Only a few wood densification applications have been industrialized to some extent. The reasons for this include unsolved problems at the laboratory scale, scale-up issues, and an inadequate consideration of plasticization or stability of the products. The main challenge associated with this type of densification is the fixation of the compressive deformation when the densified wood is exposed to moisture. Studies found that wood with the highest degree of compression shows the highest potential for compression deformation recovery, i.e. set-recovery (Blomberg et al. Citation2006, Kutnar et al. Citation2009). The set-recovery effect occurs because internal stresses introduced during compression are relieved when the wood is exposed to moisture (Morsing Citation2000). Compression-recovery behavior of wood can be attributed to a combination of its cellular structure and properties of the cell wall polymers (Wolcott and Shutler Citation2003).
Several approaches to fixing set-recovery of densified wood are viable, including impregnation with a synthetic resin, mechanical fixation, or THM treatments at high temperature and moisture (Navi and Heger Citation2004). Historically, impregnation of densified wood with low-molecular weight resins has found success in improving the properties of wood and was even used to make aircraft components during the Second World War (Hill Citation2006). The most success has been found with aqueous, phenol-based resins that are impregnated via vacuum treatment into the wood structure followed by densification. This method has been found to be successful in reducing the set-recovery of densified wood (Stamm and Seborg Citation1941, Citation1942, Citation1955, Stamm Citation1959, Hill Citation2006, Gabrielli and Kamke Citation2008, Citation2010).
The objective of this study was to couple a low-molecular weight phenol resin with THM treatments to reduce set-recovery in solid wood of some common wood species. The resin and process used in this paper is part of a pending patent (Kantner et al. Citation2019).
Materials and methods
Wood specimens
Wood specimens used for THM treatment were produced using three species: poplar (Populus spp.), spruce (Picea abies), and beech (Fagus sylvatica). Quartersawn specimens were selected and milled to the nominal dimensions of 300 mm in length (L) and 50 mm in width (W). Thicknesses (T) of the specimens were 6, 10, and 15 mm to observe the effect of densification ratio. Before further treatment, specimens were conditioned at 20°C and 65% relative humidity. In total, 90 specimens were prepared, 30 for each species and 10 for each thickness.
Resin impregnation
An aqueous, low-molecular weight, phenol-formaldehyde resin was supplied by Metadynea Austria GmbH (Krems an der Donau, Austria). A 30% solids content solution was prepared by mixing with water. After conditioning, wood specimens were submerged in the resin solution and vacuum impregnated at 0.001 bar for 30 min. After impregnation, excess resin was wiped from the specimens and they were dried overnight in ambient conditions. Specimens were then dried at 60°C in an oven for 24 h. Weight percent gain (WPG) was calculated using the weight of the specimen before impregnation and the weight of the specimen after impregnation and drying.
THM treatment
After drying, impregnated specimens were densified in a hydraulic, 30-ton capacity Langzauner “Perfect” LZT-UK-30-L model hot press (Lambrechten, Austria) equipped with a water-cooling system. To achieve three target thicknesses, steel hard stops with thicknesses of 2, 5, and 7 mm were used, based on the original thickness of wood specimens (). Two specimens of the same thickness were pressed simultaneously as a batch. Upper and lower platens were pre-heated to 170°C. Using the pressing parameters presented in , the press was closed and when the target thickness was reached, the compressed specimens were held at 170°C for 2 min. After this time, both upper and lower platen temperature was increased to 200°C. Immediately upon reaching 200°C, both platens were cooled to 60°C, and the pressure was released.
Figure 1. Poplar specimens prepared for flexure tests. (A) un-densified 15 mm thickness, (B) densified to 7 mm, (C) densified to 5 mm, and (D) densified to 2 mm.
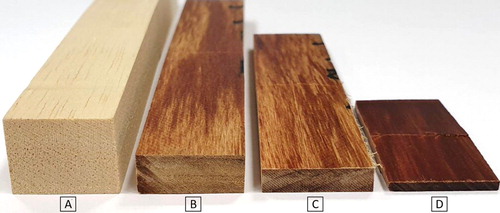
Table 1. Pressing parameters for densification.
Density of specimens
To assess the level of densification achieved, dimensions and weight of specimens were measured before and after treatment. The densification ratio was calculated using the compressed density divided by the initial oven-dry density of the specimens.
The density profile throughout the thickness of specimens was also measured. Treated and un-treated control specimens were prepared for analysis with dimensions of 50 mm × 40 mm × 6 mm, 10 mm, and 15 mm. Density profile measurements were performed using a GreCon, Type DA-X X-ray densitometer (Alfeld, Germany).
Mechanical testing
Three-point flexure tests based on ASTM D198 (Citation2008) were used to measure modulus of elasticity (MOE) and modulus of rupture (MOR). All specimens were cut to a width of 20 mm, but length varied depending upon the original thickness. Due to varying thicknesses of specimens, reaction points were adjusted to maintain span to depth ratios greater than 20. Specimens with an initial thickness of 15 mm were cut to a length of 170, 10 mm specimens were cut to 110, and 6 mm specimens were cut to 70 mm. Test speed of 2.5 mm min−1 was used.
The hardness of the specimens was assessed based on the hardness modulus test found in ASTM D1037 (Citation1999). As recommended, specimens with thicknesses less than 6 mm should have an extra specimen below them as a backing material; therefore, specimens compressed to 2 mm were bonded together to achieve a 6 mm thick test specimen. The same for specimens compressed to 5 mm by bonding two specimens together. For specimens compressed to 7 mm, no additional backing material was added. Specimens were bonded together using PVA adhesive to avoid slippage during the test. A loading rate of 6 mm min−1 was used. From this test, hardness modulus was derived from the straight-line portion of the load penetration curve and an equivalent Janka hardness value was obtained by dividing the hardness modulus value by the factor 5.4. This factor is based on imperial units and all necessary conversions were made to calculate the equivalent Janka hardness in newtons.
Set-recovery
Set-recovery test specimens were prepared with dimensions of 20 mm × 20 mm. There were 10 specimens for each species/initial thickness combination, for a total of 99 specimens. Set-recovery test cycles consisted of oven drying the specimens at 103°C, followed by submersion in water (room temperature or boiling) for 24 h, and oven drying at 103°C after soaking. Specimen thickness in the direction of compression was measured before and after submersion for every cycle. In total, four cycles were completed. Set-recovery was calculated using the following expression:where tS is oven-dry thickness after soaking and tC is oven-dry compressed thickness.
Results
Density
A micrograph of an impregnated spruce specimen with a target initial thickness of 6 mm can be seen in . The compression applied during the THM process deforms the cells without visible fracture of the cell walls. Longitudinal tracheids collapse and flatten in the direction of compression. Resin present in the cell wall lumens appears lighter than the wood cell wall. The middle lamella can also be seen as lighter material between wood cells.
Figure 2. Micrograph of impregnated, densified spruce with a 2 mm target thickness. (A) Penetrated phenol resin present in lumens and (B) collapsed tracheids.
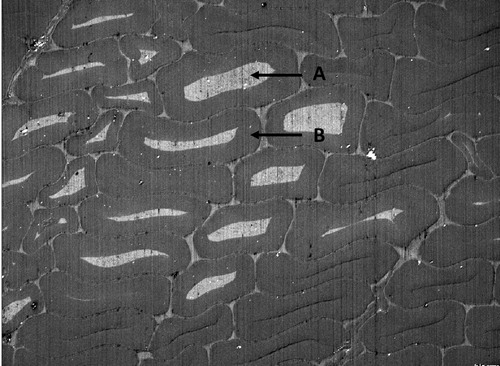
Densification results are presented in . Specimens with larger initial thicknesses had lower densification ratios for poplar and spruce. Beech specimens, regardless of initial thickness, had similar compressed densities and densification ratios. During the treatment of beech specimens, it was visibly seen that the press was unable to reach the target thickness. An excess of vapor pressure coupled with higher initial densities found in beech specimens could be one cause for this and could be overcome with a larger press capacity.
Table 2. THM and resin treatment data for beech, poplar, and spruce specimens.
shows the density profiles of THM densified specimens and a non-densified control group. Control specimens, consisting of non-densified poplar and beech wood, exhibited almost uniform density throughout their thickness. This was expected since the difference in density between earlywood and latewood is small. On the other hand, the zigzag shape seen in spruce control specimens is due to larger differences between earlywood and latewood densities.
Figure 3. Mean density profiles of beech (first row), poplar (second row), and spruce (third row) specimens.
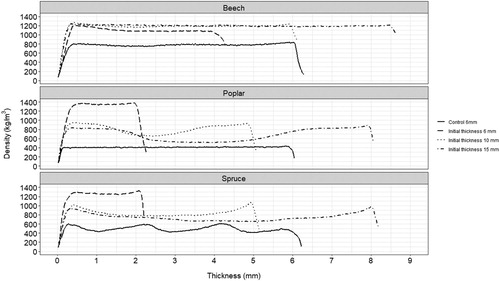
The density profile of THM treated beech specimens for all thicknesses was uniform due to an even distribution of vessels. Poplar and spruce specimens had density profiles with slightly higher face densities than the core for all thicknesses. This profile is targeted for wood-based composite panels like particleboard. Variations of temperature and MC inside the specimens during the THM process were not measured in this study, however, due to different initial thicknesses MC and temperature distribution prior to final compression thickness must have varied as well. Thinner wood specimens would lose moisture more rapidly and approach a more uniform distribution than thick ones; therefore, it was assumed that MC was nearly equal throughout the thickness in 6 mm thick specimens prior to final compression thickness. Based on the same assumption, it was concluded that for 10 and 15 mm thick specimens the MC was not consistent throughout the thickness. Impacted by these MC gradients, the local compression behavior with respect to thickness direction would also be non-uniform. Furthermore, the initial thickness of the specimen appears to have influenced the profile of the temperature and MC gradients.
Mechanical testing
Results from mechanical testing are summarized in . Reference, un-treated values are from Meier (Citation2020). As expected, higher density THM specimens resulted in higher MOE values with one exception in beech. In THM treated beech specimens, the highest MOE and MOR values were determined for specimens with a 10 mm initial thickness. The data from beech specimens do not follow the same trends as those in poplar and spruce, which can be attributed to the incomplete THM treatment.
Table 3. Mechanical test data of impregnated, THM treated specimens (mean values ± 1 standard deviation), and reference values.
MOE and MOR of THM treated poplar specimens were highest in specimens with an initial thickness of 6 mm. Specimens with initial thicknesses of 10 and 15 mm had small differences within MOE and MOR. The reason for this is associated with the density profile. As seen in , density on the surface of both groups of specimens was approximately the same (∼900 kg m−3). As with any beam in bending, the upper and lower surface undergoes the highest levels of compression and tension, largely dictating their performance.
MOE and MOR values of THM treated spruce specimens also increased with increasing density of the specimens. As with poplar, MOE and MOR values for specimens with initial thicknesses of 10 and 15 mm were not significantly different, due to similar surface densities (∼1000 kg m−3) ().
Specimens tested in this study had MOE values comparable to and exceeding values of some commercially available structural engineered wood products (EWPs) like LVL (13.8 GPa), PSL (13.8 GPa), and LSL (10.3 GPa) (Kutnar et al. Citation2008). Performance in these EWPs is modified and dictated by the species of solid wood used in their construction. With the THM treatment and impregnation applied in this study, the wood itself was being modified rather than the form it was engineered into. In this way, THM treated specimens have the potential for use in structural EWPs.
Hardness
MOH values can be seen in . The highest MOH values were found in THM poplar specimens with a 6 mm initial thickness, which also had the highest density after compression. MOH of spruce specimens with an initial thickness of 6 mm was similar to MOH of poplar specimens of the same initial thickness, although the compressed density was lower. MOH of beech specimens was the lowest for specimens with an initial 10 mm thickness. Density profiles of these specimens were not significantly different than specimens with 6 and 15 mm initial thicknesses. As the difference is not significant, results could be due to the variability of THM beech specimens. Furthermore, MOH of poplar and spruce specimens with 10 and 15 mm initial thicknesses was significantly lower and did not differ among these groups.
Equivalent Janka hardness values () range from 13,300 N (poplar, 10 mm initial thickness) to 67,400 N (poplar, 6 mm). All species and thicknesses had relatively high values compared to those of reference, non-treated wood. These high hardness levels present a possibility for use in engineered wood flooring or laminates in furniture.
Set-recovery
For all specimens, the majority of set-recovery occurred immediately after the first wetting-drying cycle (). Subsequent cycles added little to the overall set-recovery measured. The highest levels of set-recovery were found in spruce specimens. The low levels of resin penetration that were achieved in spruce specimens () are assumed to be caused by the wood being kiln dried. Kiln drying is known to cause pit aspiration in the wood cells, leading to more difficult resin penetration and higher set-recovery due to lower amounts of penetrated resin ().
During the room temperature set-recovery test, beech and poplar specimens with initial thicknesses of 10 and 15 mm had less than 16% set-recovery. Only in poplar specimens with an initial thickness of 6 mm was set-recovery relatively high for both room temperature and boiling tests at 19% and 29%, respectively (). As poplar specimens with an initial thickness of 6 mm had the highest densification ratio, it is foreseeable that they would also have a greater potential for set-recovery. The lowest set-recovery was measured in beech specimens. Beech specimens with initial thicknesses of 6 and 15 mm had room temperature set-recovery of less than 5% while specimens with an initial thickness of 10 mm had a set-recovery of 11%. Moisture content and temperature gradients during the THM treatment led to a density profile with high-density surface layers and lower density core layers. When specimens were exposed to set-recovery tests using boiling water, poplar had higher mean values, with large standard deviations. Spruce specimens also had relatively high mean values with large standard deviations. Beech specimens were easily impregnated and had the lowest set-recovery values which were similar to room temperature values despite the intense test conditions.
Table 4. Set-recovery after four wetting-drying cycles (mean values ±1 standard deviation).
By using the phenol resin in this study, great improvements in set-recovery were achieved in both poplar and beech specimens. For comparison, non-impregnated, densified wood specimens undergoing thermal modification can have set-recovery values greater than 60% (Rautkari et al. Citation2010, Laine et al. Citation2016, Gao et al. Citation2019), while non-thermally modified specimens can completely revert to their original dimensions.
Conclusions
Based on results from this study, it was seen that impregnation with phenol resin can significantly reduce the set-recovery of compressed deformation. Impregnation of spruce specimens proved to be difficult due to pit aspiration and had relatively high levels of set-recovery. Beech specimens did not achieve the target thicknesses using THM treatment due to higher initial densities, resin uptake, and high internal vapor pressure. Not reaching the target thickness made the results difficult to interpret and direct comparisons were not possible with poplar and spruce specimens. Poplar and spruce specimens had similar mechanical values, which were largely dictated by specimens’ surface density rather than the species. Spruce specimens had high levels of set-recovery caused by low levels of impregnated resin. Based on the THM treatment used in this study, poplar specimens performed the best in terms of set-recovery improvement, mechanical performance, and predictability of the specimens. These improvements show great potential in THM treatments combined with resins for reducing set-recovery. To realize this potential, future work is needed to optimize THM treatment parameters, tailoring them to specific wood species and the geometric dimensions of the specimens to account for moisture and temperature gradients.
Acknowledgements
The author would also like to graciously thank the Metadynea Company for their great knowledge, donation of the resin used in this study, and general support. The author also thanks Marica Mikuljan, Michael Burnard, and Andreja Kutnar for their insight, knowledge, and support.
Disclosure statement
No potential conflict of interest was reported by the author(s).
Correction Statement
This article has been republished with minor changes. These changes do not impact the academic content of the article.
Additional information
Funding
References
- ASTM D1037 (1999) Standard test methods for evaluating properties of wood-base fiber and particle panel materials. American Society for Testing and Materials, 4, 1–31.
- ASTM D198 (2008) Standard test methods of static tests of lumber in structural sizes. American Society for Testing and Materials, 4, 1–25.
- Blomberg, J., Persson, B. and Bexell, U. (2006) Effects of semi-isostatic densification on anatomy and cell-shape recovery on soaking. Holzforschung, 60, 322–331. doi: 10.1515/HF.2006.052
- Gabrielli, C. and Kamke, F. A. (2008) Treatment of chemically modified wood with VTC process to improve dimensional stability. Forest Products Journal, 58, 82–86.
- Gabrielli, C. P. and Kamke, F. A. (2010) Phenol-formaldehyde impregnation of densified wood for improved dimensional stability. Wood Science and Technology, 44, 95–104. doi: 10.1007/s00226-009-0253-6
- Gao, Z., Huang, R., Chang, J., Li, R. and Wu, Y. (2019) Effects of pressurized superheated-steam heat treatment on set recovery and mechanical properties of surface-compressed wood. BioResources, 14, 1718–1730.
- Hill, C. A. S. (2006) Wood Modification: Chemical, Thermal and Other Processes (New York: John Wiley & Sons, Inc).
- Kantner, W., Zich, T., Schwarzkopf, M. J., Burnard, M. D., Mikuljan, M. and Kutnar, A. (2019) Method for Preparation of Densified Wood Article (Munich: Metadynea Austria GmbH).
- Kollmann, F. P., Kuenzi, E. W. and Stamm, A. J. (1975) Principles of Wood Science and Technology. Vol. II: Wood Based Materials (New York: Springer-Verlag).
- Kutnar, A., Kamke, F. A. and Sernek, M. (2008) The mechanical properties of densified VTC wood relevant for structural composites. European Journal of Wood and Wood Products, 66, 439–446. doi: 10.1007/s00107-008-0259-z
- Kutnar, A., Kamke, F. A. and Sernek, M. (2009) Density profile and morphology of viscoelastic thermal compressed wood. Wood Science and Technology, 43, 57–68. doi: 10.1007/s00226-008-0198-1
- Laine, K., Segerholm, K., Wålinder, M., Rautkari, L. and Hughes, M. (2016) Wood densification and thermal modification: hardness, set-recovery and micromorphology. Wood Science and Technology, 50, 883–894. doi: 10.1007/s00226-016-0835-z
- Meier, E. (2020) The wood database. Accessed 24 January 2020, available at: https://www.wood-database.com/.
- Morsing, N. (2000) Densification of wood - the influence of hygrothermal treatment on compression of beech perpendicular to the grain. PhD Thesis. Technical University of Denmark.
- Navi, P. and Heger, F. (2004) Combined densification and thermo-hydro-mechanical processing of wood. Materials Research Society Bulletin, 29, 332–336. doi: 10.1557/mrs2004.100
- Navi, P. and Sandberg, D. (2012) Thermo-Hydro-Mechanical Wood Processing (New York: EPFL Press).
- Rautkari, L., Properzi, M., Pichelin, F. and Hughes, M. (2010) Properties and set-recovery of surface densified Norway spruce and European beech. Wood Science and Technology, 44, 679–691. doi: 10.1007/s00226-009-0291-0
- Sandberg, D., Kutnar, A. and Mantanis, G. (2017) Wood modification technologies - a review. iForest - Biogeosciences and Forestry, 10, 895–908. doi: 10.3832/ifor2380-010
- Stamm, A. J. (1959) The dimensional stability of wood. Forest Products Journal, 9, 375–381.
- Stamm, A. J. and Seborg, R. M. (1941) Resin-treated, compressed wood. Transactions of the American Institute of Chemical Engineers, 37, 385–397.
- Stamm, A. J. and Seborg, R. M. (1942) Forest Products Laboratory. Resin-treated wood (Impreg). USDA Forest Service. Report 1380 (Revised 1962), Madison, WI, USA.
- Stamm, A. J. and Seborg, R. M. (1955) Forest Products Laboratory. Impreg, Compreg. USDA Forest Service. Report 1380, 1381, Madison, WI, USA.
- Wolcott, M. P. and Shutler, E. L. (2003) Temperature and moisture influence on compression – recovery behavior of wood. Wood and Fiber Science, 35, 540–551.