ABSTRACT
This paper reviews the history and use of copper naphthenate as a heavy-duty wood preservative, with a focus on use patterns within the USA and opportunities for expansion in Canada and Europe. Copper naphthenate has demonstrated efficacy to preserve and protect cellulosic and wooden items essential to critical infrastructure and is an ideal choice for use in the replacement of pentachlorophenol and creosote where less toxic and environmentally friendlier alternatives are required.
Introduction and background
Creosote and pentachlorophenol have historically been the most widely-used heavy duty organic-type (oil-borne) wood preservatives used for the treatment of poles, bridge timbers and railway crossties (sleepers) in North America and Europe. However, pentachlorophenol has not been used in the European Union (EU) for decades, and creosote was given a 5-year reprieve from its original 2018 cancelation in the EU because of a perceived lack of alternative preservatives. The European Chemicals Agency is currently conducting a public consultation on the wood preservative active ingredient creosote, with the aim to collect information on the availability of alternatives, i.e. substitutes and alternative materials suitable to replace creosote treated wood under the Biocidal Products Regulation (BPR Citation2012). A “CreoSub” pan-European program was undertaken to identify alternative treatments, which ultimately resulted in a recommendation to use oil-borne copper systems (Hundhausen et al. Citation2014). Currently three oil-borne formulations, including copper naphthenate (which is diluted in oil prior to use), are seeing some use in the EU. All have copper hydroxide as the primary active ingredient and organic acid co-solvents ().
Table 1. Alternative oil-type preservatives.
This paper reviews the history and efficacy of copper naphthenate and compares its efficacy in long term field tests against other oil-borne and waterborne heavy duty wood preservatives.
Naphthenic acid and copper naphthenate
Naphthenic acid is a naturally-occurring mixture of carboxylic acids recovered from kerosene, jet fuel, and diesel fractions during petroleum refining, and consists predominantly of alicyclic acids with the formula CnH2n-zO2 where n indicates the carbon number and z specifies a homologous series (Brient et al. Citation1995). Non-cyclic and aromatic acids are also found in appreciable amounts, typically 20-30% combined. The major use of naphthenic acid is in production of oil-soluble metal soaps, including copper, cobalt, iron and zinc naphthenates (Brient et al. Citation1995).
Carboxylic acids including naphthenic acid also have confirmed fungicidal and termiticidal activity (Becker Citation1975, Avis and Bélanger Citation2001, Clausen et al. Citation2010). Antifungal fatty acids cause the release of intracellular ions and proteins when in contact with sensitive fungi, suggesting that they disrupt properties and functions of the cytoplasmic membrane (Hajlaoui et al. Citation1992). Naphthenic acid exhibits greater fungicidal efficacy than other carboxylic acids in copper-free formulations when tested against pure fungal cultures and in soil (Marsh et al. Citation1944). Loss of strength in soil burial (a) and Metarrhizium sp. fungal tests showed that low concentrations of naphthenic acid in cellulosic fabric more effectively prevented decay than any of the other carboxylic acids even when tested at much higher concentrations, as shown in (Marsh et al. Citation1944). Likewise, tests in four different soils indicated that copper naphthenate consistently provided better protection at lower copper concentrations in fabrics than the other copper carboxylates (Marsh et al. Citation1945). Yet incorporating up to 50% synthetic acids in copper naphthenate formulations has little deleterious effect on the performance as wood preservatives, and such blends have been adopted by the American Wood Protection Association (AWPA) in Standard P36 (Barnes et al. Citation2003, AWPA Citation2016).
Figure 1. Performance of naphthenic acid vs. other carboxylic acids (Marsh et al. Citation1944, Table 6). (a) 9-day soil burial results (b) 7-day Metarrhizium sp. exposure results.
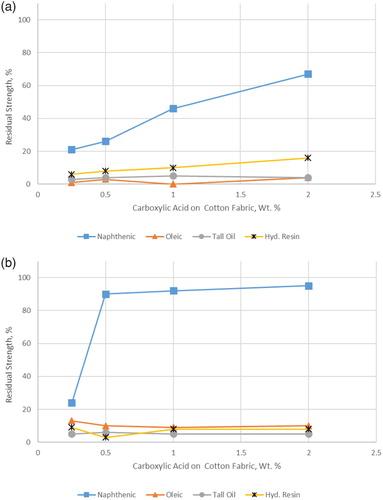
Copper naphthenate (CuN) is prepared by mixing copper (II) compounds with naphthenic acid and diluted in petroleum-based carrier oils for oil-borne systems (Brient and Freeman Citation2004). Waterborne systems are also formulated using alkanolamines as co-solvent (Shaw Citation1994). CuN was adopted into AWPA Standards specifically for sawn products (including crossarms and highway construction), poles, posts, and piles in 1988 and for crossties in 2005.
Oil-borne wood preservatives
Oil-borne wood preservatives for pressure treatment fall into two groups; one includes various creosote formulations and the second consists of solutions of active ingredients dissolved in hydrocarbon-based carrier oils (AWPA Citation2019). AWPA-standardized products in this latter group currently include pentachlorophenol, copper naphthenate, copper-8-quinolinolate (oxine copper), 4,5-dichloro-2-octyl-3(2H)-isothiazolone (DCOI), 3-iodo-2-propynyl butyl carbamate (IPBC), and oil-borne inorganic boron (SBX-O). The three oil-type systems in widest use in North America for heavy duty applications such as crossties/sleepers, utility poles and fence/highway posts are creosote, pentachlorophenol, and copper naphthenate (Groenier and Lebow Citation2006). Creosote and pentachlorophenol are currently in wider use but copper naphthenate has the highest growth rate, particularly in crossties (Gauntt Citation2019). The continuing growth of wood preservation technologies classified by the U.S. EPA as General Use (i.e. not Restricted Use) pesticides such as CuN and borate-copper naphthenate (B-CuN) suggest both a shift in crosstie marketplace dynamics as well as long-term savings (Gauntt Citation2019).
Water repellency provided by hydrophobic petroleum-based carriers used in oil-borne preservative formulations retards the absorption of liquid water into wood, particularly at the end grain (Williams Citation2010). The water repellency allows treatment of wood after machining, reduces splitting and checking and reduces rewetting after treatment (Lebow and Tippie Citation2001). Performance of oil-borne systems is also enhanced when heavier (higher boiling, less volatile) oils are used as diluents (Arsenault Citation1973, Nicholas Citation1988).
Copper-based wood preservatives
Copper-based fungicides have been widely and successfully used for more than a century, with the earliest known reference to the use of copper as a fungicide in 1761 (Richardson Citation1997). Copper first appeared as a component of wood preservatives in a U.S. patent issued in 1838 utilizing copper sulfate (Earle Citation1838). Copper becomes “fixed” to wood by reacting to some degree with acidic sites, mostly phenolic protons (Xue et al. Citation2014). The volume of wood products treated with copper-based preservatives grew exponentially during the 1970s and remains high, particularly in sawn products such as residential lumber (Nicholas et al. Citation1997, USEPA Citation2017). Copper compounds are relatively easy to formulate, easy to assay in solution and wood, and resistant to photodegradation and hydrolysis (Archer and Preston Citation2007). Although borates and organic (non-metallic) biocides have gained importance, copper remains the primary biocide used to protect wood in ground contact or fully exposed to weather.
In relatively low concentrations, copper compounds are quite toxic to fungi, bacteria, and algae, and this property has been exploited for over 200 years for control of fungal and bacterial diseases of plants. Copper appears in general to inhibit the germination of fungal spores (Parker Rhodes Citation1941). In particular, copper is responsible for interference with homeostatic processes and cell membrane functions (Ohsumi et al. Citation1988), protein and enzyme damage and precipitation (Kim et al. Citation2000), production of reactive oxygen species (Sharma and Dietz Citation2009), and DNA disruption (Sagripanti et al. Citation1991).
History of copper naphthenate
The interest in metal naphthenate salts for use in wood preservatives arose from the excellent oil solubility provided for the otherwise oil-insoluble metal compounds (Blew Citation1946). First used as a wood preservative in Europe in 1889, CuN was adopted by the American Wood Protection Association as a provisional standard in 1948 and formally adopted in Standard P8 (now Standard P36) in 1950 (AWPA Citation1950), with copper metal as the retention basis (AWPA Citation2016). Subsequent test data resulted in retention standards being adopted for copper naphthenate (Freeman et al. Citation2005, AWPA Citation2016) and it is now readily available and being increasingly specified for commercial products.
CuN has been registered as a pesticide for use in wood preservation in the United States since 1951, and registered by the United States Environmental Protection Agency (USEPA) since 1972. USEPA-registered copper naphthenate wood preservatives are available as oil-borne or waterborne preservative formulations used to treat utility poles, crossties, bridge ties and timbers, fence posts and pickets, highway construction lumber, wooden boxes, and as remedial treatments (USEPA Citation2011).
Treating cycles for CuN are similar to those used for pentachlorophenol in terms of pressure and temperature; treating temperatures are typically lower than those used for creosote since the CuN solution is less viscous at ambient temperature and typically has a lower flash point than creosote.
Copper naphthenate has long been recognized as an “environmentally preferred” alternative to heavy duty wood preservatives such as creosote and pentachlorophenol (Grace et al. Citation1993, Freeman and McIntyre Citation2008). Although developed in the late nineteenth century, copper naphthenate only started gaining wide use for heavy duty pressure treatments in the late 1980s, specifically for cross arms, bridge timbers, utility poles, and fence posts (Brient and Freeman Citation2004). At the same time, regulatory activities began to stimulate interest in copper naphthenate as an alternative wood treatment because of its General Use classification, making it acceptable for residential or consumer use (Becker and Hopkins Citation2008).
Wood preservatives used for utility poles in North America have been extensively reviewed by regulatory agencies as to their risks and benefits as part of the Reregistration Eligibility Decision process, with heavy emphasis on human health effects and environmental impact (USEPA Citation2007/Citation2008). The USEPA and Health Canada classify pesticides including wood preservatives as either General Use (including copper naphthenate) or Restricted Use pesticides (including creosote, pentachlorophenol, CCA, and ACZA), with specific additional requirements or restrictions and regulatory controls for the handling and use of the restricted use pesticides (CFR Citation1988). Copper naphthenate contains no dioxins or Persistent Bioaccumulative Toxins (PBTs). Unlike the other heavy duty wood preservatives that are restricted use pesticides, neither copper naphthenate nor wastes from copper naphthenate wood treating operations are designated by USEPA under the Resource Conservation and Recovery Act (RCRA) as “listed” wastes (CFR Citation2020). As a result of its General Use classification, copper naphthenate in both oil-borne and waterborne ready-to-use formulations containing 10–20% copper naphthenate (1–2% copper as metal) are sold “over the counter” for residential/consumer use (Rust-Oleum Citation2019, Nisus Citation2020). Moreover, due to its General Use classification, EPA does not require the use of automated hydraulic cylinder doors to minimize worker exposure to CuN in the recent Reregistration Eligibility Decision, unlike automated door requirements for cylinders using arsenicals, creosote and pentachlorophenol (USEPA Citation2007).
Four CuN concentrate formulations and eleven ready-to-use formulations are EPA-registered by five registrants in the US, including products formulated with other active ingredients. Copper naphthenate is also registered in Canada under Health Canada’s Pest Management Regulatory Agency (PMRA), although currently only for non-pressure application. There are currently 19 active PMRA registrations for CuN products in Canada, including 3 oil-borne (8–8.15% Cu) and one waterborne (5%) commercial concentrate products. All 15 of the ready to use products are oil-borne formulations for either domestic/residential use by brush application or commercial use by brush, dip, or spray application (Brient Citation2016). Commodities pressure-treated with copper naphthenate in the USA are currently being imported for use into Canada. An amendment to add pressure treatment to existing Canadian registrations is currently under review by PMRA.
Copper naphthenate, with its complete compatibility with oil carrier systems, was used to extend the supply of creosote during its shortage during and after World War II (Baechler and Gjovik Citation1986). It is now the leading alternative to creosote for the protection of crossties (sleepers) in North America (Gauntt Citation2019). Work by the Eastern Forest Products Lab (currently FPInnovations and previously Forintek Canada) showed that copper naphthenate was a suitable alternative for creosote as a crosstie preservative based on performance at multiple test sites in Canada (Krzyzewski Citation1977). Today most “Class 1” railroads (as defined by the U.S. Surface Transportation Board; CFR Citation2018), including Norfolk Southern, CSX, Union Pacific, Canadian Pacific, Canadian National and Genesee & Wyoming, and many short line railroads in North America are increasingly using copper naphthenate as an alternative to creosote for crosstie and bridge tie treatments (Smith Citation2019; Corselli Citation2020). Nearly one-third of bridge timbers and approximately 5% of crossties are now being treated with copper naphthenate in oils conforming to AWPA Standard HSA or Standard HSG specifications, with about 4 million copper naphthenate-treated ties currently in service (Laughlin Citation2020). In the European Union, ties treated with copper naphthenate are in use in track, and commercial treatment of sleepers and poles has started in Belgium for evaluation by railways (Belgium Rail and SNCF in France) and utilities (Lloyd Citation2020). In the USA, Conrail (now Norfolk Southern) carried out a large comparative in-track evaluation where copper naphthenate, at half the AWPA standardized minimum retention, performed as well as creosote (Brient and Webb Citation2002). Subsequent studies reported on copper naphthenate-treated crossties and bridge ties (Brient Citation2014, Citation2015).
Copper naphthenate is commonly used for bridge timbers, especially over sensitive aquatic environments and where preservative drippage or bleeding is a concern (Wacker and Crawford, Citation2003). Because of its efficacy and favorable toxicology profile, copper naphthenate was identified as the optimum alternative to creosote-treated bridge crossties and timbers (Lombard and Kubiczki Citation2011). This study by the New Hampshire (USA) Department of Transportation, triggered by creosote dripping from a train trestle within an environmentally sensitive area, reviewed preservative options for future bridge timber work to identify optimum performance while mitigating damage to the environment. Of the seven products evaluated, copper naphthenate and creosote were recommended for their performance in railroad bridge timbers, with copper naphthenate being preferred for sensitive aquatic environments. As of 2019–2020, 55–60% of all bridge ties are treated with copper naphthenate (Laughlin Citation2020).
Utility poles and wooden crossarms are another commodity where copper naphthenate is increasingly specified as a less hazardous alternative to chromated copper arsenate, creosote and pentachlorophenol (SnoPUD Citation2013). Between 0.68 and 0.82 million kilograms of copper naphthenate were consumed for the treatment of utility poles in 2002, and industry sources estimate that demand for copper naphthenate could increase by up to 10% per year (Becker and Hopkins Citation2008). Of the 130–150 million wood poles in use in North America today, approximately 5 million are replaced each year, of which about 4–5% are currently being treated with copper naphthenate (Laughlin Citation2020). Copper naphthenate-treated poles are non-conductive (Ragon et al. Citation2010, Morrell et al. Citation2011) and easier to climb than poles with other treatments (Shupe et al. Citation2011). Isolated premature failure issues were seen in utility poles beginning in the late 1980s, although a survey of poles in service at the time found the failure rate (< 1%) was well below the 5% exclusion limit found in a normal distribution of samples with any preservative system (Barnes et al. Citation2000). The failures were found to be primarily the result of incipient (pretreatment) decay due to improper seasoning of “green”, unseasoned poles and emulsion formation tendencies of copper naphthenate formulations that did not conform to then-AWPA Standard P8, now numbered as Standard P36 (McIntyre Citation2000b, AWPA Citation2016). Implementation of recommended changes to treating practices identified in the root cause analysis resulted in a rapid decrease in premature failures (McIntyre and Freeman Citation2002). Similar instances of premature failure due to pretreatment infection and decay which continued to cause further strength loss in service were identified in pentachlorophenol-treated utility poles (Morris and McAfee Citation1992).
Copper naphthenate is also specified for the treatment of wood used in highway construction commodities including posts, guardrails and “salt barns” (AASHTO Citation2013). Copper naphthenate, as a result of its ready availability, low toxicity, water repellency, and ease of application, has been used to protect cellulosic textiles used in tents and other temporary shelters (Marsh et al. Citation1945). This comparative study showed copper naphthenate treatment was consistently more effective per unit weight on fabric than other copper compounds, with the cotton substrate retaining greater residual strength (i.e. less loss of tensile or “breaking” strength) after burial in non-sterile soil. The characteristic green color and odor of Army and Scouting canvas tents in the past were due in part to copper naphthenate preservative treatment. FPInnovations recently published a long-term fence post efficacy study that again showed copper naphthenate to be equally efficacious as other heavy-duty wood preservatives (Stirling et al. Citation2017). Copper naphthenate is also used extensively in the Asia Pacific region, especially for non-pressure (topical) applications (Singh et al. Citation2014).
Oil-borne copper naphthenate, being essentially insoluble in water, exhibits less leaching of copper into water and soil than aqueous inorganic copper formulations, and preservative loss rates are not significantly different between 1.28 and 2.24 kg/m3 (as Cu) retentions (Brooks Citation2003). Waterborne copper naphthenate treatment results in lower copper leaching into water than ACQ or ACZA when evaluated in dynamic immersion tests (Brooks Citation2004).
Efficacy studies
Extensive published data exists on the efficacy of copper naphthenate to support its widespread commercial use over many decades. Over 75 years ago, the USDA Forest Products Lab established field tests in a high decay and high termite hazard zone in southern Mississippi to evaluate performance of over 100 wood preservatives in southern pine fence posts (Wirka Citation1941). Follow-up reports (Davidson Citation1977, Freeman et al. Citation2005) determined estimated service life, with the most recent inspection on copper naphthenate crossties conducted in 2003 after 54 years in the test (Freeman et al. Citation2005). The data show copper naphthenate performs very well relative to competitive heavy-duty preservatives, even at retentions well below the AWPA minimum established for that hazard zone ( and , and ).
Table 2. Average service life of creosote, pentachlorophenol and CuN treated fence posts exposed during USDA FPL-RN-01 study in Mississippi, USA.
Table 3. Preservative retention and percentage of pass/fail posts evaluated after 54 years (Freeman et al. Citation2005, reporting on 2003 inspection results).
Other field stake tests conducted by the USDA Forest Products Laboratory again show copper naphthenate giving excellent service life (), even when using volatile solvents not complying with AWPA Standard HSA specifications and at copper retentions well below the AWPA minimum retention established for the test location (Crawford et al. Citation2002, Woodward et al. Citation2011). Studies on the effect of carrier oil physical properties on efficacy of oil-borne preservative systems (Arsenault Citation1973, Nicholas Citation1988, Nicholas and Freeman Citation2000) support the general conclusion that the heavier the oil, the more effective is an oil-borne copper naphthenate or pentachlorophenol system.
Table 4. Known life spans of CuN stakes in the USDA-FPL-02 Studies (Woodward et al. Citation2011, Table 7).
Ten-year field tests in Sweden with copper naphthenate showed efficacy equal to or better than CCA (Westin et al. Citation2002). A Canadian (FPInnovations) study demonstrated pressure treatment with copper naphthenate provides very long (>65 years) service life when round stock was treated to standardized retentions (Stirling et al. Citation2017). Comparative data for oil-borne pentachlorophenol (red pine treated in a full cell process) and copper naphthenate (jack pine in a Rueping empty cell process) diluted in pole oil are summarized in .
Table 5. CuN in Canadian pole stub studies (Stirling et al. Citation2017).
Recent data on field cut tests in Canada using CCA-treated western hemlock following an AWPA E32 protocol confirm its efficacy (AWPA Citation2018, Stirling and Wong Citation2019). All untreated controls had failed or exhibited very advanced decay after 10 years in ground contact exposure, whereas the copper naphthenate (2% Cu in mineral spirits) specimens showed only low levels of decay in a few instances. After 10 years in an above-ground exposure, advanced decay was again present on several of the untreated controls, while copper naphthenate (2% Cu in mineral spirits) samples remained sound. Specimens treated with waterborne copper naphthenate (1% Cu) were also largely sound, with a few specimens showing early stages of decay. Copper naphthenate has been used in combination with other preservatives such as borate salts in ties and bridge ties (Lloyd et al. Citation2017) and for remedial or supplemental treatment of poles, piles, bridge components and other commodities after years in service to extend their useful service life (Barnes et al. Citation2011).
Copper naphthenate efficacy was reviewed by McIntyre (Citation2000a), and was also shown to be highly effective against Formosan subterranean termites (Grace et al. Citation1993). Copper naphthenate is also less susceptible to copper tolerant fungal species than that observed in copper formulations containing no added co-biocide (Duncan Citation1958, Green and Clausen Citation2005, Schultz and Nicholas Citation2009).
Copper naphthenate is also widely used in non-pressure applications such as field treatment of end cuts, holes, adzed cuts, or wherever damage has occurred to the treated outer shell in accordance with AWPA Standard M4 (AWPA Citation2019). It is also widely used as a liquid or paste in remedial treatments of utility poles in service to extend their service life (RUS Citation2013). A 40 year field stake efficacy study in Australia showed comparable efficacy of copper naphthenate vs. other heavy duty preservatives in various wood species when treated by a non-pressure (cold soak) treatment (Cookson Citation2013). In an evaluation of alternatives to traditional non-pressure treatments for wood packaging materials, copper naphthenate provided protection equivalent to or greater than that of zinc naphthenate against termites and all decay fungi evaluated in ASTM D 3345–08 (ASTM Citation2008) no-choice termite tests and AWPA E10 soil block fungal decay studies (Lebow et al. Citation2017). Copper naphthenate was specifically noted to be the only preservative tested giving acceptable performance in soil blocks treated both by dipping and by vacuum impregnation, where the latter process otherwise yields a dramatic decrease in weight loss relative to dip treatment (Lebow et al. Citation2017). Of note was that the test organism used, P. placenta, is known to be tolerant to copper-based preservatives (Sutter et al. Citation1983, Green and Clausen Citation2005).
Biodiesel (mixed fatty acid methyl esters) has been increasingly used as a co-solvent with hydrocarbon diluents for oil-borne wood preservatives to enhance pentachlorophenol solvency and reduce or improve odor (Freitag and Morrell Citation2011). Biodiesel is also of interest as an odor reducing co-solvent for copper naphthenate formulations. Soil block lab studies following AWPA E10 methodology (AWPA Citation2017) found greater wood weight loss when petroleum-based diesel solutions of copper naphthenate were amended with biodiesel after exposure to a pure culture of the copper tolerant fungus P. placenta (Freitag and Morrell Citation2011). No statistical analyses were done to determine if the weight loss differences were significant. Follow-up field stake trials show B10 (10% biodiesel in #2-diesel) has a minimal (≤ 5% reduction) and inconsistent effect on mean ratings vs. B0 (straight petroleum diesel) after 58 months in two test sites in Oregon, as shown in (a and b) (Presley et al. Citation2019). The authors reported that although stakes treated with higher concentrations of biodiesel appear to be trending towards higher levels of decay than petroleum diesel-treated CuN stakes, the difference in average decay ratings at the 58-month sampling point for these two treatments were not statistically significant. Wood treated with B10 solutions of CuN have noticeably reduced odor relative to straight petroleum diesel formulations (Parrett Citation2020).
Figure 3. Performance of biodiesel-amended copper naphthenate treatments in field stake study (from Presley et al. 2019). (a) OSU forest test site (b) OSU field test site.
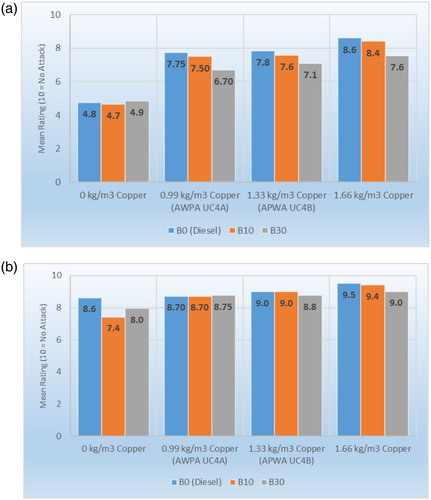
Soil block tests by other researchers also found no adverse effects on CuN performance from added biodiesel (McKillop Citation2014). Extensive mycelial growth was seen only on the biodiesel-amended wooden blocks, which prompted the author to theorize biodiesel was acting as an alternative and possibly more readily accessible carbon or energy source than the wood itself, which may have skewed results in this short 8-week test.
A survey of poles in commercial service at two utilities in Washington state was also conducted to evaluate performance differences when using CuN diluted in petroleum diesel vs. biodiesel (Presley et al. Citation2019). Although poles treated with a biodiesel carrier showed higher levels of soft rot damage than petroleum diesel-treated poles, Cu retention in the biodiesel poles was on average ∼25% lower than in petroleum diesel poles. Since more biodiesel poles were treated to below the threshold level of 1.5 kg/m3 Cu, the authors could not attribute the performance differences to biodiesel alone.
Conclusions
Copper naphthenate is a proven effective heavy-duty preservative with great potential for use in Europe as BPR regulations impact permitted wood treatments. It has a century of independent testing and over a half century of successful commercial use in both oil-borne and waterborne formulations. As such, copper naphthenate-based wood preservatives represent an effective, safe alternative preservative for the replacement of traditional technologies, especially in European countries as well as globally, where other heavy-duty wood preservatives are no longer desired or permitted. Copper naphthenate is currently under review for registration in the EU and labeling to add pressure treatment to the registration is pending in Canada.
Disclosure statement
No potential conflict of interest was reported by the author(s).
Correction Statement
This article has been republished with minor changes. These changes do not impact the academic content of the article.
References
- AASHTO (2013) Standard Specification for Preservatives and Pressure Treatment Processes for Timber. AASHTO Designation: M 133-12 (Washington, D.C.: American Association of State Highway and Transportation Officials), p. 7.
- Archer, K. and Preston, A. (2007) An overview of copper-based wood preservatives. In H. M. Barnes (ed.), Wood Protection 2006 (Madison, WI: Forest Products Society), c2007. http://www.forestprod.org/woodprotection06archer.pdf.
- Arsenault, R. D. (1973) Factors influencing effectiveness of preservative systems. In D. D. Nicholas (ed.), Wood Deterioration and its Prevention by Preservative Treatments (Syracuse, NY: Syracuse University Press), pp. 121–278.
- ASTM (2008) Method D 3345-08. Standard Test Method for Laboratory Evaluation of Wood and Other Cellulosic Materials for Resistance to Termites (West Conshohocken, PA: ASTM International). www.astm.org).
- Avis, T. J. and Bélanger, R. R. (2001) Specificity and mode of action of the antifungal fatty acid cis-9-Heptadecenoic acid Produced by Pseudozyma flocculosa. Applied and Environmental Microbiology, 67(2), 956–960.
- AWPA (1950) Report of committee P-4, non-standard preservatives. . Proceedings of the American Wood-Protection Association, 46, 33–49.
- AWPA (2016) Standard P36 – Standard for Copper Naphthenate. Book of Standards (Birmingham, AL: American Wood Protection Association).
- AWPA (2017) Standard E10: Laboratory Method for Evaluating the Decay Resistance of Wood-Based Materials Against Pure Basidiomycete Cultures: Soil/Block Test. Book of Standards (Birmingham, AL: American Wood Protection Association).
- AWPA (2018) Standard Field Test for Evaluation of Field-Cut Preservatives to be Used Above Ground (UC3B): Modified Post and Rail Test (Birmingham, AL: American Wood Protection Association).
- AWPA (2019) Standard U1 - Use Category System: User Specification for Treated Wood. Book of Standards (Birmingham, AL: American Wood Protection Association).
- Baechler, R. H. and Gjovik, L. R. (1986) Looking back at 75 years of research in wood preservation at the U.S. Forest products Laboratory. Proceedings of the American Wood-Preservation Association, 82, 133–149.
- Barnes, H. M., Amburgey, T. L., Sanders, M. G. and Lindsey, G. B. (2011) Supplemental treatments for timber bridge components. For. Prod. J., 61(6), 450–458.
- Barnes, H. M., Freeman, M. H., Brient, J. A. and Kerr, Jr. C. N. (2000) Serviceability of copper naphthenate-treated poles. Proceedings IRG Annual Meeting, International Research Group on Wood Protection Document No. IRG/WP 00-30214.
- Barnes, H. M., Sanders, M. G. and Amburgey, T. L. (2003) Field testing of copper carboxylate preservatives. International research group on wood preservation, Document No. IRG/WP 03-30322, 6 pp.
- Becker, G. (1975) The effects of some organic acids on different termite species. Holz als Roh- und Werkstoff, 33(2), 57–61.
- Becker, J. and Hopkins, S. (2008) A qualitative economic impact assessment of alternatives to pentachlorophenol as a wood preservative. USEPA Office of Prevention, Pesticides and Toxic Substances, April 2, 2008.
- Blew, J. O. (1946) Preservatives for wood poles: emergency alternative methods for the standard coal-tar creosote treatment. Report No. R1693. April 1946. Madison, WI: U.S. Department of Agriculture, Forest Service, Forest Products Laboratory. 9 p.
- BPR (2012) Consultation on potential candidates for substitution. Biocidal Products Regulation (EU) 528/2012. European Chemicals Agency (ECHA). https://echa.europa.eu/public-consultation-on-potential-candidates-for-substitution/-/substance-rev/24301/term.
- Brient, J. A. (2014) Copper naphthenate treatment for wood crossties and timbers. Proceedings IRG Annual Meeting, International Research Group on Wood Protection Document No. IRG/WP 14-30647.
- Brient, J. A. (2015): A bridge not too far: copper naphthenate treated Softwoods for bridge ties. Proceedings of the American Wood-Preservation Association, 101, 112–115.
- Brient, J. A. (2016) Copper naphthenate treated wood – a review and regulatory update. In Proceedings, Canadian Wood Preservation Association, 37th Annual Meeting (Vancouver, BC), pp. 101–108.
- Brient, J. A. and Freeman, M. H. (2004) Copper naphthenate update. Proceedings of the American Wood-Preservation Association, 100, 106–118.
- Brient, J. A. and Webb, D. (2002) The performance of copper naphthenate ties in service. Proceedings of the American Wood-Preservation Association, 98, 112–115.
- Brient, J A., Wessner, P J. and Doyle, M. N. (1995): Naphthenic acids. In J. I. Kroschwitz (ed.) Kirk-Othmer Encyclopedia of Chemical Technology, 4th ed., (New York: John Wiley & Sons, Inc.) 16, pp. 1017–1029.
- Brooks, K. M. (2003) Literature review, computer model and assessment of the potential environmental risks associated with copper naphthenate treated wood products used in aquatic environments. Technical report prepared for Merichem Chemicals & Refinery Services LLC. (Houston, Texas USA). 23 p. https://preservedwood.org/portals/0/documents/archive/CN_Risk_Assessment.pdf.
- Brooks, K. M. (2004) The effects of dissolved copper on salmon and the environmental effects associated with the use of wood preservatives in aquatic environments. Technical report prepared for the Western Wood Preservers Institute, Vancouver, Washington 98665. 20 p. https://preservedwood.org/portals/0/documents/archive/Brookscopperreview12162004.pdf.
- CFR (1988) United States Code of Federal Regulations, 40 CRF 152.160-152.175. Source: 53 FR 15986, May 4, 1988. See also https://www.epa.gov/pesticide-worker-safety/restricted-use-products-rup-report.
- CFR (2018) United States Code of Federal Regulations, 40 CRF 1201 - Railroad Companies.
- CFR (2020) United States Code of Federal Regulations, 40 CRF 261.31 – Hazardous wastes from non-specific sources; and 40 CRF 261.32 – Hazardous wastes from specific sources.
- Clausen, C., Coleman, R. D. and Yang, V. W. (2010) Fatty acid–based formulations for wood protection against mold and sapstain. Forest Prod. J., 60(3), 301–304.
- Cookson, L. J. (2013) 40 year results from the largest preservative in-ground stake trial conducted in Australia. Proceedings IRG Annual Meeting, International Research Group on Wood Protection Document No. IRG/WP 13-30624.
- Corselli, A. (2020) Ties that bind. Railway Age, March 10, 2020 issue.
- Crawford, D. M., Woodward, B. M. and Hatfield, C. A. (2002) Comparison of wood preservatives in stake tests. Progress Report. Res. Note FPL-RN-02. Madison, WI: U.S. Department of Agriculture, Forest Service, Forest Products Laboratory. 120 p.
- Davidson, H. L. (1977) Comparison of wood preservatives in Mississippi Post Study (1977 Progress Report). FPL-RN-01. USDA Forest Service, Forest Products Laboratory. Madison, WI. 17 p.
- Duncan, C. G. (1958) Studies of the methodology of soil block testing. USDA Forest Service Report 2114, 108-121.
- Earle, E. (1838) Improvements in the mode of preserving timber. U.S. patent number 934, issued September 20, 1838.
- Freeman, M. H., Crawford, D., Lebow, P. and Brient, J. A. (2005): A comparison of wood preservatives in posts in southern Mississippi: results from A half-Decade of testing. Proceedings of the American Wood-Preservation Association, 101, 136–143.
- Freeman, M. H. and McIntyre, C. R. (2008) A comprehensive review of copper-based wood preservatives with a focus on new micronized or dispersed copper systems. Forest Products Journal, 58(11), 6–27.
- Freitag, C. and Morrell, J. (2011) Potential influence of biodiesel as a co-solvent on the performance of copper naphthenate. Proc. American Wood Protection Association, 107, 67–80.
- Gauntt, J. C. (2019) Economic and alternative preservative research with overview of North American Wood Tie Market Dynamics. Proceedings IRG Annual Meeting, International Research Group on Wood Protection Document No. IRG/WP 19-30751.
- Grace, J. K., Yamamoto, R. T. and Laks, P. E. (1993) Evaluation of the termite resistance of wood pressure treated with copper naphthenate. Forest Products Journal, 43(11-12), 72–76.
- Green, F. and Clausen, C. A. (2005): copper tolerance of brown-rot fungi: Oxalic acid production in southern pine treated with arsenic-free preservatives. International Biodeterioration & Biodegradation, 56, 75–79.
- Groenier, J. S. and Lebow, S. (2006) Preservative-treated wood and alternative products in the forest service. United States Department of Agriculture, Technology & Development Program, Publication No. 0667-2809P-MTDC.
- Hajlaoui, M. R., Benhamou, N. and Bélanger, R. R. (1992) Cytochemical study of the antagonistic activity of Sporothrix flocculosa on rose powdery mildew, Sphaerotheca pannosa var. rosae. Phytopathology, 82, 583–589.
- Hundhausen, U., Mahnert, K.-C., Gellerich, A. and Militz, H. (2014) CreoSub – New protection technology to substitute creosote in railway sleepers, timber bridges, and utility poles. Proceedings IRG Annual Meeting, International Research Group on Wood Protection Document No. IRG/WP 14-30644.
- Kim, J. H., Cho, H., Ryu, S. E. and Choi, M. U. (2000) Effects of metal ions on the activity of protein tyrosine phosphatase VHR: highly potent and reversible oxidative inactivation by Cu 2+ ion. Archives of Biochemistry and Biophysics, 382(1), 72–80.
- Krzyzewski, J. (1977) Performance of preserved railway ties. eastern forest products lab report OPX183E. Fisheries and Environment Canada. Ottawa, ON, Canada. 43 pp.
- Laughlin, K. (2020) Personal communication. Nisus Corporation. Rockford, TN USA.
- Lebow, S. T. and Tippie, M. (2001) Guide for minimizing the effect of preservative-treated wood on sensitive environments. General Technical Report. FPL-GTR-122. USDA Forest Service, Forest Products Laboratory.
- Lebow, S. T., Zelinka, S. L., Arango, R. A., Woodward, B. M., Lebow, P. K., Ohno, K. M. and Chotlos, N. P. (2017) Evaluation of nonpressure wood preservatives for military applications. Research Paper FPL–RP–693. Madison, WI: U.S. Department of Agriculture, Forest Service, Forest Products Laboratory. 30 p.
- Lloyd, J. (2020) Personal communication. Nisus Corporation. Rockford, TN USA.
- Lloyd, J., Brischke, C., Bennett, R. and Taylor, A. (2017) Dual Borate and copper naphthenate treatment of bridge timbers – potential performance enhancements and cost savings. Proceedings IRG Annual Meeting, International Research Group on Wood Protection Document No. IRG/WP 17-40797.
- Lombard, B. and Kubiczki, J. (2011) Research-synthesis of wood treatment alternatives for timber railroad structures – Final Report. HWA-NH-RD-15680I. Prepared by the NHDOT, in cooperation with the U.S. Department of Transportation, Federal Highway Administration.
- Marsh, P., Greathouse, G., Bollenbacher, K. and Butler, M. (1944) Copper soaps as rot-proofing agents for fabrics. Industrial and Engineering Chemistry, 36(2), 176–181.
- Marsh, P. B., Greathouse, G. A., Butler, M. L. and Bollenbacher, H. (1945) Testing fabrics for resistance to mildew and rot. U.S. Department of Agriculture, Technical Bulletin No. 892. June 1945. 24 pp.
- McIntyre, C. R. (2000a) Copper naphthenate performance: A new way to look at old data. Proceedings IRG Annual Meeting, International Research Group on Wood Protection Document No. IRG/WP 00-30215.
- McIntyre, C. R. (2000b) The performance of copper naphthenate. Sixth International Conference on Utility Line Structures. EDM International, Fort Collins, CO. March 20-22, 2000.
- McIntyre, C. R. and Freeman, M. H. (2002) Copper naphthenate – an update on new trends and changes in the last decade. Proc., Northeast Pole Conference, Binghamton, New York, USA.
- McKillop, N. A. (2014) Evaluating the effect of biodiesel on the efficacy of the wood preservative copper naphthenate. MSc. Thesis, Dalhousie University, Halifax, NS, Canada.
- Morrell, J. J., Clauson, M. and Love, C. S. (2011) Effect of initial preservative treatment on electrical conductivity in Douglas-fir pole Sections. Forest Products Journal, 61(1), 28–30.
- Morris, P. I. and McAfee, B. J. (1992) Pretreatment infection and premature failure of PCP-treated southern pine Poles. Proceedings of the Canadian Wood Preservers Association, 13, 73–90.
- Nicholas, D. D. (1988) The influence of formulations on wood preservative performance. Proceedings of the American Wood-Preservation Association, 84, 178–184.
- Nicholas, D. D. and Freeman, M. H. (2000) A comparison of pentachlorophenol and copper naphthenate in long term field stake tests. Proc. International Conference on Utility Line Structures, March 2000, Ft. Collins, CO.
- Nicholas, D D, Henry, W P, Vasishth, R C (1997). The role of copper in wood preservation. Chapter 8, In H. W. Richardson (ed.) Handbook of Copper Compounds and Applications (New York: Marcel Dekker), pp. 163–176.
- Nisus Corporation (2020) QNAP2. https://nisuscorp.com/product/qnap2#single-resources.
- Ohsumi, Y., Kitamoto, K. and Anraku, Y. (1988) Changes induced in the permeability barrier of the yeast plasma membrane by cupric ion. Journal of Bacteriology, 170(6), 2676–2682.
- Parrett, J. (2020) Personal communication. Wheeler Lumber. Whitewood, SD.
- Parker Rhodes, A. F. (1941) Studies on the mechanism of fungicidal action I. Preliminary investigation of nickel, copper, zinc, silver and mercury. Annals of Applied Biology, 28(4), 389–405.
- Presley, G., Sinha, A., Cappellazzi, J. and Konkler, M. (2019) Oregon State University Utility Pole Research Cooperative (UPRC). Department of Wood Science & Engineering, Oregon Wood Innovation Center. 39th Annual Report.
- Ragon, K. W., Shupe, T., Wu, Q., Donohoe, P. and Freeman, M. (2010): The electrical properties of treated wood with a focus on utility pole conductivity: part II. Proc. American Wood-Protection Assoc., 106, 153–167.
- Richardson, H. W. (1997): Copper fungicides/bactericides. Chapter 5, in H. W. Richardson (ed.) Handbook of Copper Compounds and Applications (New York: Marcel Dekker), pp. 95–122.
- RUS (2013) Wood pole inspection and maintenance. Bulletin 1730B-121. United Sates Department of Agriculture – Rural Utilities Service. 20 p.
- Rust-Oleum Corporation (2019) Safety data sheets for WolmanTM Woodlife® CopperCoatTM Green Wood Preservative (Product Identifier 1904A) and CreoCoatTM Black Wood Preservative (Product Identifier 14436A). https://www.rustoleum.com/en/product-catalog/consumer-brands/wolman/woodlife-coppercoat.
- Sagripanti, J. L., Goering, P. L. and Lamanna, A. (1991) Interaction of copper with DNA and antagonism by other metals. Toxicology and Applied Pharmacology, 110(3), 477–485.
- Schultz, T. P. and Nicholas, D. D. (2009) Short- and long-term ground-contact decay efficacies of three copper-organic systems and possible implications for standardization criteria for copper-based systems. Forest Products Journal, 59(5), 13–18.
- Sharma, S. S. and Dietz, K. J. (2009) The relationship between metal toxicity and cellular redox imbalance. Trends in Plant Science, 14(1), 43–50.
- Shaw, J. L. (1994) Results of test activity on a water-borne copper naphthenate wood preservation system. Proceedings American Wood Preservers Association, 90, 385–392.
- Shupe, T. F., Wu, Q. and Freeman, M. (2011) Effect of preservative type and Gaff Style on Gaff Penetration into wood Poles. Proceedings American Wood-Protection Association, 107, 150–152.
- Singh, T., Page, D. and Bennett, A. (2014) Effectiveness of on-site remediation treatments for framing timber. International Biodeterioration Biodegradation, 86, 136–141.
- Smith, S. T. (2019) 2018 railroad Tie survey. Journal of Transportation Technologies, 9, 276–286.
- SnoPUD (2013) The copper naphthenate pole experience. Snohomish County (WA) Public Utility District (SnoPUD). Presented to the Northwest Public Power Association Environmental Task Force meeting, September 2013.
- Stirling, R., Ingram, J., Wong, D. and Morris, P. (2017) Field Testing in Canada XXVI: Posts and Poles. Submitted to the Canadian Wood Preservation Association, Proceedings of the 38th Annual Meeting, Toronto, Ontario. October 25-26, 2017.
- Stirling, R. and Wong, D. (2019) Performance of field cut preservatives above-ground and in ground contact exposures. Proceedings IRG Annual Meeting, International Research Group on Wood Protection Document No. IRG/WP 19-30742.
- Sutter, H. P., Jones, E. B. G. and Walchli, O. (1983) The mechanism of copper tolerance in Poria placenta (Fr.) Cke. and Poria vaillantii (Pers.) Fr. Material und Organismen, 18, 241–262.
- USEPA (2007/2008) United States Environmental Protection Agency, Reregistration Eligibility Decision for: Copper and Zinc Naphthenate Salts (2007; Case 3099); Creosote (2008; Case 0139); Chromated Arsenicals (2008; Case 0132); Pentachlorophenol (2008; Case 2505).
- USEPA (2011) United States Environmental Protection Agency, Pesticide Registration Numbers 64405-15 (QNAP5W waterborne copper naphthenate concentrate) and 64405-16 (QNAP8 oil-borne copper naphthenate concentrate), both registered to Nisus Corporation, Rockford, TN USA. http://npirspublic.ceris.purdue.edu/ppis/http://npirspublic.ceris.purdue.edu/ppis/.
- USEPA (2017) Overview of Wood Preservative Chemicals. United States Environmental Protection Agency. https://www.epa.gov/ingredients-used-pesticide-products/overview-wood-preservative-chemicals#:~:text=Copper%20azole%20is%20a%20water,paintable%20surface%20after%20they%20dry.
- Wacker, J. P. and Crawford, D. M. (2003) Extending service life of timber with preservatives. Proc. 19th U.S. – Japan Bridge Engineering Workshop. U.S. – Japan Natural Resource panel on Wind and Seismic Effects (M. Ishida and M, Shirato, editors), Tsukuba, Japan, October 27-30, 2003.
- Westin, M., Rapp, A. O., Hadi, Y. S. and Nilsson, T. (2002) Field trials with mini-stakes. Proceedings IRG Annual Meeting, International Research Group on Wood Protection Document No. IRG/WP 02-02044.
- Williams, R. S. (2010) Chapter 16 – Finished Wood. In: Ross R J (Ed.): Forest Products Laboratory Wood Handbook – Wood As An Engineering Material. General T Report FPL-GTR-190. Madison, WI: U.S. Department of Agriculture, Forest Products Laboratory.
- Wirka, R. M. (1941) Comparison of preservatives in Mississippi fence post study. Proceedings of the American Wood-Preservation Association, 37, 365–379.
- Woodward, B. M., Hatfield, C. A. and Lebow, S. T. (2011) Comparison of wood preservatives in Stake Tests: 2011 Progress Report. Research Note FPL-RN-02. Madison, WI: U.S. Department of Agriculture, Forest Service, Forest Products Laboratory. 120 p.
- Xue, W., Kennepohl, P. and Ruddick, J. (2014) Chemistry of copper preservative treated wood. Proceedings IRG Annual Meeting. International Research Group on Wood Protection Document No. IRG/WP 14–30651.