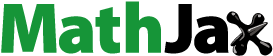
ABSTRACT
Scots pine sapwood was pretreated with two levels of propanetriol (20% and 40% w/w glycerol), and then subjected to vacuum-heat treatment (VHT) at 180°C and 200°C. The treated samples were examined with respect to their weight and volumetric changes, mechanical properties, colour changes, and dynamic water vapour sorption. The weight of the samples after VHT did not change with increasing the temperature, but it was increased in glycerol pretreated samples. Combination of glycerol pretreatment and VHT decreased the maximum swelling. Total colour change was significantly higher during VHT at a higher temperature, while no obvious trend observed in the samples pretreated with glycerol. Modulus of elasticity (MOE) and modulus of rupture (MOR) were not affected by solely VHT, but strongly decreased after glycerol pretreatment. The equilibrium moisture content (EMC) of the samples decreased by VHT. The glycerol pretreatment caused a reduction in EMC values at a relative humidity (RH) below 60%, but considerably increased the moisture sorption in the RH above 75%. VHT slightly reduced the sorption hysteresis compared to untreated wood, but an apparent reduction in hysteresis observed by glycerol pretreatment. This indicates that the flexibility of the wood cell wall polymers increases due to glycerol pretreatment, which results in decreased MOE and sorption hysteresis values.
Introduction
Wood is one of the most commonly used renewable materials in the building and furniture sectors. However, the utilisation of many wood species is limited to indoor applications due to their hygroscopicity, low durability and weathering performances. Wood modification, such as chemical modification, resin impregnation, and thermal modification, is an established technology to overcome the issues related to the susceptibility of wood against abiotic and biotic damages, and thus prolonging its lifecycle (Brischke et al. Citation2006). Thermal treatment of wood is an environmentally friendly method that has been widely studied and even applied on the industrial scale (Militz Citation2002, Weiland and Guyonnet Citation2003, Esteves et al. Citation2008, Calonego et al. Citation2010, Lekounougou and Kocaefe Citation2014, Hosseinpourpia and Mai Citation2016). The treatment can be performed at temperatures that usually range between 180 °C to 260 °C in air, in a vacuum, or under an inert atmosphere (Sivrikaya et al. Citation2019). Heat treatment alters the chemical structure of wood by the initial release of acetic acid from hemicelluloses due to deacetylation, followed by liberation of formaldehyde, furfural, and other aldehydes (Tjeerdsma et al. Citation1998). The latter compounds may react with phenolic nuclei of lignin and change its chemical structure (Hosseinpourpia et al. Citation2017). The released acetic acid degrades the amorphous regions of cellulose and increases its crystallinity index (Sivonen et al. Citation2002). Previous studies reported that the reversible and irreversible chemical and structural changes of wood due to thermal modification reduced its hygroscopicity and mechanical strength and improved the resistance to microbiological degradation (Poncsak et al. Citation2006, Rowell et al. Citation2009, Mohareb et al. Citation2012, Sandberg et al. Citation2013, Endo et al. Citation2016). Reduction in mechanical properties has always been one of the main drawbacks for thermally treated wood (Tjeerdsma and Militz Citation2005), which is mainly due to the degradation of hemicelluloses, relative increases in the amount of crystalline cellulose, and irreversible stiffening of the cell wall matrix (Tjeerdsma et al. Citation1998, Esteves and Pereira Citation2009, Suchy et al. Citation2010a, Citation2010b). On the other hand, the treatment process affects the wood properties. According to Wentzel et al. (Citation2019) chemical composition of thermally modified wood, strongly correlated with the mechanical properties, was more affected by a closed system under high pressure than the modifications in the open system. Willems and Altgen (Citation2020) introduced the hygrothermolytic(HGT) process to be a potential method with independent and continuous process variable and improved material properties and improved process characteristics.
Development of industrial kiln for thermal wood modification with an initial vacuuming step was developed by Silvaprodukt (Rep et al. Citation2012). Termovuoto® (WDE Maspell s.r.l., Terni, Italy) is however patented an alternative technology recently for thermal modification of wood under vacuum condition to avoid wood pyrolysis or combustion. The process consists of a semi-industrial prototype plant, made of stainless steel cylinder with an internal diameter of 1.7 m and operates at higher temperatures up to 250°C, with the fan speed ranges from 635 r min−1 to maximum speed of 1930 r min−1 at vacuum pressure of 200 mbar (Ferrari et al. Citation2013, Sandak et al. Citation2015). Due to the constant removal of volatile compounds from the reactor by vacuum pump, their contribution to the degradation of the cell wall polymers is limited, and thus the reduction in mechanical strength of treated wood is not as significant as the other thermal modification methods (Allegretti et al. Citation2012, Ferrari et al. Citation2013). Norway spruce and fir treated with the vacuum-heat process showed higher dimensional stability and durability against brown-rot and white-rot fungi as compared to untreated samples (Allegretti et al. Citation2012). In addition, the weight loss of the wood samples treated with the vacuum-heat systems was considerably lower than the ones treated according to Thermowood process (Pockrandt et al. Citation2018). Most recently, Sivrikaya et al. (Citation2019) quoted that Scots pine wood samples treated with the vacuum-heat process showed lower weight loss, higher lightness, and lower colour changes in comparison with that from solely a heat treatment method. The equilibrium moisture content (EMC) of wood treated with the vacuum-heat process was considerably reduced as a result of the degradation of the carbonyl groups in xylan and the loss of carbonyl group linked to the aromatic skeleton in lignin due to the treatment (Sun et al. Citation2017).
Pretreatment of wood in combination with heat treatment became attractive in recent years to make the process more economical and to reduce the negative impact of the process on some of the wood properties (Hong et al. Citation2013, Zhu et al. Citation2014, Wang et al. Citation2015, Qu et al. Citation2019). Propanetriol compound, which is the IUPAC (International Union of Pure and Applied Chemistry) name for glycerol, is a major by-product of biodiesel production. Glycerol has been widely used as a splasticiser for edible and/or biodegradable films (Vieira et al. Citation2011) to improve mechanical properties, and reduce the fragility and brittleness. The effect of glycerol pretreatment on material properties of heat-treated wood has been reported recently (Yan and Morrell Citation2014, Citation2019, Salman et al. Citation2016, Citation2017, Liu et al. Citation2018, Mubarok et al. Citation2019). Yan and Morrell (Citation2014) reported that the dimensional stability of Douglas fir heartwood improved by glycerol pretreatment followed by heat treatment, while the modulus of rupture (MOR) of the treated samples decreased with increasing the intensity of heat treatment, e.g. treatment duration and temperature. The modulus of elasticity did not show significant changes under the treatment conditions. Pretreatment of beech samples with glycerol or polyglycerol, in the presence of glycidyl methacrylate or maleic anhydride, and then heat treatment at 150, 200, or 220°C improved the dimensional stability (approximately 80%), and resistance to fungal and termite degradation, while modulus of elasticity (MOE) and MOR were reduced considerably by approximately 30% and 60%, respectively (Mubarok et al. Citation2019). The authors quoted that the degradation of cell wall polymers was accelerated by glycerol pretreatment under elevated temperature, and this resulted in a strong reduction of mechanical strength of modified wood.
The catalytic effect of glycerol during thermal modification of wood facilitates the degradation of cell wall polymers, and thus result in alteration of wood properties at relatively lower temperatures, which makes the process more economically viable. Pretreatment of wood with glycerol and followed by vacuum-heat treatment however provides a relatively milder condition than the ones under heat treatment process, and thus reducing the risk of undesirable changes on wood properties. In addition, it is expected that glycerol delivers extra hydroxyl groups to form a three-dimensional network and stabilise the wood cell wall polymers (Roussel et al. Citation2001, Soulounganga et al. Citation2004). Therefore, the present study was conducted to establish the effect of vacuum-heat treatment on mechanical properties, swelling performance and water vapour sorption behaviour of wood pretreated with glycerol. The treated samples were also evaluated via their weight changes and colour alterations, and compared with those untreated, solely vacuum-heat treated or pretreated with glycerol.
Experimental
Sample preparation
Scots pine (Pinus sylvestris L.) sapwood with the annual ring width of 1.56 mm and density of 543 kg/m3, free from knots and defects was collected from Sawmill in Bartın province, Turkey. Propanetriol, so-called glycerol (GL), anhydrous with 92.1 g/mol and 1.26 g/cm3 density was purchased from Merck KGaA, Darmstadt, Germany. The samples were vacuum impregnated (0.08 MPa) for 60 min with 20% and 40% (w/w) of glycerol dissolved in water. After impregnation, the samples were dried at 103°C for 48 h. Then, vacuum-heat treatment was performed by direct exposure of dried samples to 180°C and 200°C for 2 h using a vacuum oven (JEIO TECH OV-12; Jeio Tech Co., Ltd., Daejeon, Korea; 65 L, vacuum range: 0–0.1 MPa) under mild vacuum condition (0.08–0.09 MPa). The cross-sections of the treated samples were then observed and maximum penetration depth was confirmed visually. The weight of the samples was recorded before (w0) and after each treatment (w1) to assess the weight gain, due to glycerol treatment, and the weight loss, due to vacuum-heat treatment. The volumes of the samples were also recorded before (V0) and after treatments (V1).
Weight and dimensional changes
The leaching test was performed to remove the unreacted chemicals, by following a method described previously (Mubarak et al. Citation2019). In details, six untreated and treated samples measuring 20 × 20 × 10 mm3 (L × R × T) were initially oven-dried and then subjected to periodic leaching process by submerging in 72 ml of distilled water over 1, 2, 4, 8, 16, and 48 h under continuous shaking (175 linear shakes min−1) at 20°C. After the leaching test, samples were dried at 103°C for 48 h and reweighed (w3). The weight changes of the wood samples due to different treatment steps and leaching process were then assessed according to the following equation:
(1)
(1) where Δw is the weight change of treated or untreated wood samples before or after treatments and/or leaching test, w0 is the oven-dry weight before treatment, w1 is the dry weight of the wood samples after sole glycerol treatment at 103°C or sole vacuum-heat treatment at the higher temperatures (180°C or 200°C), w2 is the dry weight of the wood samples after glycerol pretreatment and then vacuum-heat treatment, and w3 is the oven-dry weight of the treated and untreated wood samples after leaching test.
The volumetric changes of the wood samples due to different treatment processes were calculated according to the following equation:
(2)
(2) where Δv is the volumetric changes of treated wood samples after treatments, v0 is the oven-dry volume before treatment, v1 is the dry volume of the wood samples after sole glycerol treatment at 103°C or sole vacuum-heat treatment at the higher temperatures (180°C or 200°C) and v2 is the dry volume of the wood samples after glycerol pretreatment and then vacuum-heat treatment.
Maximum swelling (Smax) was also determined as described previously (Xiao et al. Citation2010, Mubarok et al. Citation2019), according to the following equation:
(3)
(3) where Smax is the percentage of wood swelling, ad is the dry area (radial × tangential) of the wood sample, aw is the wet area of the wood sample.
Colour measurement
The colour changes in wood samples before and after treatments were measured by a Konica Minolta CM-700d spectrophotometer (Konica Minolta, Inc., Tokyo, Japan) according to the CIE L*a*b system with five replicates, as described previously (Sivrikaya et al. Citation2019). Based on the L*, a*, b* colour coordinate system, L* represents lightness, a* presents red/green opponent colour, b* reveals the yellow/blue opponent colour. The colour change (ΔE) was calculated based on the differences in colour parameters before and after treatment according to following Equation 4:
(4)
(4)
Mechanical properties
A three-point bending test was performed according to ASTM D143-Citation14 (Citation2014) standard using a universal testing machine (MTS 810 Material Test System, 100 kN, MTS Systems Corporation, Eden Prairie, MN, USA). Prior to test, 15 wood samples with dimensions of 10 × 10 × 200 mm3 (R × T × T), from each treatment category, were conditioned at 20°C and 65% RH, until constant weight. The distance between the supports (span) was 180 mm and the testing speed was 10 mm/min. Modulus of elasticity (MOE) and modulus of rupture (MOR) were determined from Equations 5 and 6,
(5)
(5)
(6)
(6) where F is the maximum force (N), ΔF is the difference at 10% and 40% of maximum load in elastic deformation area, Δf is the increment of deflection difference at the mid-length of the test piece corresponding to ΔF, l is the span length (mm), b is the width (mm), and h is the height (mm).
Dynamic vapour sorption
The water vapour sorption behaviour of the wood samples was determined using an automated vapour sorption (AVS) apparatus (Q5000 SA, TA Instruments, New Castle, DE, USA), as reported previously (Hosseinpourpia et al. Citation2016, Citation2019). Approximately 8 mg of untreated and treated wood powder (passed through a 20-mesh sieve) were used for each measurement. The wood samples were exposed to relative humidity (RH) that increased from 0% to 90% in step sequences of 15% and of 5% from 90% to 95% RH, decreasing to 0% RH in a reverse order, at a constant temperature of 25°C. The instrument maintained a constant target RH until the mass change in the sample (dm/dt) was less than 0.01% per minute over a 10 min period. The equilibrium moisture content (EMC) of the untreated and treated wood samples was calculated based on their equilibrium weight at each given RH step throughout the sorption run measured by the sorption balance device.
Statistical analysis
Properties differences of treated samples were analysed using the statistical software package IBM SPSS Version 23 (IBM Corporation, Armonk, NY, USA). A 5% level of significance was used during ANOVA analysis. One-way analysis of variance (ANOVA) was applied to determine whether measured properties were significantly different among treated samples categories. A 5% level of significance was used to detect differences and when a significant difference was found, a Tukey HSD post-hoc test was performed.
Results and discussion
Weight and dimensional changes
Weight and dimensional changes of Scots pine samples due to different treatments are presented in . The Δw for samples treated with glycerol at 20% and 40% concentration were ranged between 23% and 53%, respectively. The weight gain of wood samples after impregnation with glycerol corresponds to its deposition in the wood cell walls and/or lumens (Berube et al. Citation2018).
Table 1. Mean values (± standard deviations) of weight and volumetric changes of wood samples due to different treatment processes.
Treatment of wood samples at high temperatures under vacuum caused a slight change in samples weight, as it is reflected by Δw before leaching (). The low Δw of wood samples due to vacuum-heat treatment was reported previously (Allegretti et al. Citation2012, Kutnar et al. Citation2013), which is mainly due to the removal of volatile compounds (Pockrandt et al. Citation2018). Combined treatment of wood samples with glycerol pretreatment and vacuum-heat treatment caused a significant change in Δw values. A direct comparison of Δw changes in sole glycerol-treated samples, and sole vacuum-heat treated samples with combined treated ones illustrates an obvious decrease of glycerol in combined treated samples. The highest Δw value was obtained by the pretreated samples with 40% glycerol and post-treated under the vacuum-heat condition. This is in accordance with reports of other authors (Yan et al. Citation2011, Luo et al. Citation2014, Liu et al. Citation2018, Mubarok et al. Citation2019), and can be attributed to: (a) degradation of glycerol molecules by exposure to high temperature, and (b) acceleration of the degradation of wood polymers in the presence of glycerol (Yan et al. Citation2011, Luo et al. Citation2014).
For leaching test, among different treatments, a dramatic reduction observed in Δw value of glycerol-treated wood cured at 103°C, which indicates that significant glycerol amounts were not fixed at this temperature. The vacuum-heat treatment of glycerol pretreated wood at higher temperatures, e.g. 180°C and 200°C, however, decreased the Δw values considerably. Comparable results were reported most recently by Mubarok et al. Citation2019. The bulking value (Δv) was increased after glycerol treatment, and it was more increased by increasing the glycerol concentrations from 20% to 40%, i.e. the Δv value was about 6% higher in GL-40 than GL-20. Although, a similar trend was observed in combined treated wood samples, smaller bulking values were obtained in these samples, which might be due to the possible degradation of glycerol induced at high temperature Evaluation of glycerol kinetics in wood at elevated temperatures were also showed a complete stress relaxation and high activation energy between 120–180°C (Yan et al. Citation2011). The Smax values (at the cycle II) decreased with increasing glycerol concentration and with the combined treatments. The sole glycerol or vacuum-heat treatments slightly decreased the Smax values. A similar trend observed in the samples after combined treatments, although there were not statistically in comparision with untreated control. The samples pretreated with 40% glycerol and followed with vacuum-heat treated exhibited the lowest Smax values, and thus the highest dimensional stability. As stated previously by Yan and Morrell (Citation2014) and Mubarok et al. (Citation2019), glycerol pretreatment combined with heat treatment increase the dimensional stability of wood due to the formation of covalent bonds between glycerol and wood polymers.
Colour changes
The effect of glycerol and the combination of glycerol and vacuum-heat treatments on colour changes of the wood samples is given in . Glycerol pretreatment slightly enhanced the darkness of the samples. The blackish hue increase with increasing temperatures due to vacuum-heat treatments, i.e. there were respectively −10.17 and −17.78 at 180°C and 200°C. When the glycerol pretreatment followed by vacuum-heat treatment, the darkness decreased from −5 to −17. Bekhta and Niemz (Citation2003) quoted that the darkness accelerates when the treatment temperature exceeded approximately 200°C. Yan and Morrell (Citation2019) reported that the glycerol pretreatment did not significantly change the L* of Douglas fir heartwood, but the darkness value decreased considerably by the treatment temperature and duration. The darkness hue on the heat-treated wood is attributed to the formation of degradation products from hemicellulose (Sundqvist Citation2004). For instance, quinones from the oxidation products could be the reason for colour change (Mitsui et al. Citation2001). The Δa* values of the samples treated with 20% and 40% glycerol were 3.0 and 3.1, respectively. The wood samples treated with glycerol and the combination of glycerol and vacuum-heat treatment showed the lowest Δa* values. Sole glycerol treatment enhanced the yellowness (Δb*) of the wood samples. In contrast, the combination of glycerol and vacuum-heat treatments exhibited a blue characteristic according to colour coordinate system. In general, treatments increased the Δa* value, while Δb* value decreased for the combinations of glycerol with vacuum-heat treatments. Additionally, Δa* increased with increasing temperature, whereas Δb* decreased with increased temperature. Most recently, Yan and Morrell (Citation2019) reported that the a* value decreases by increasing treatment temperature in glycerol-treated Douglas fir, while b* values are initially increased but then decreased with increasing treatment time or temperature.
Table 2. Mean values (± standard deviations) of change of ΔL*, Δa*, and Δb* in different treated samples.
The colour changes (ΔE*) of the wood samples were increased due to the treatment and they were more pronounced in higher temperatures, e.g. 200°C (). This is in accordance with Brischke et al. (Citation2007) and Tuong and Li (Citation2010), who reported a strong correlation between colour change and heat treatment intensities. Slight colour changes were observed for the glycerol-treated samples at 20% (8.52) and 40% (10.47) weight concentrations. The lowest ΔE* value of 5.56 was obtained by the samples treated with the combination of 40% glycerol and vacuum-heat treatment at 180°C. The ΔE* was much more influenced by ΔL* than Δa* and Δb*, and thus, it can be said that the ΔL* was a major contributor to the total colour change. Similar results were reported by González-Peña and Hale (Citation2009), who suggested that the colour changes in heat-treated wood mainly originate from chemical changes in the lignin polymers than in the polysaccharides.
Figure 1. Total colour change (ΔE*) of the wood samples after treatment with glycerol, combined glycerol and vacuum-heat treatments. GL: glycerol pretreatment; VHT: vacuum-heat treatment; GL-VHT: glycerol-vacuum-heat treatment. Box-plots with whiskers from the minimum to the maximum; the box represents 25%, 50% and 75% quartile; the mean value of each data set is depicted as quadrate inside the box. Different lower case letter indicated that there was a significant difference (p ≤ 0.05) as determined by ANOVA and Tukey HSD post-hoc test.
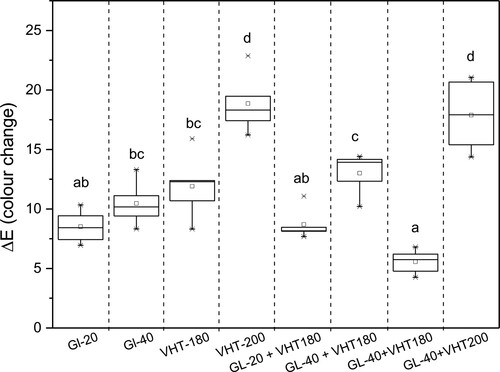
Mechanical strength of treated wood
The MOE and MOR, of untreated and treated samples, are shown in . The MOR in all cases were more affected by the treatment process than MOE.
Table 3. Mean values (± standard deviation) of MOE and MOR of different treated samples.
Treatment of wood samples with glycerol at 20% and 40% showed considerably lower bending strength than untreated control samples. Vacuum-heat treated samples illustrated comparable MOR and MOE values as untreated ones. Bending properties of thermally treated wood were extensively studied previously and different results due to the treatment process, temperature, duration, and wood species were reported (Bekhta and Niemz Citation2003, Johansson and Morén Citation2006, Poncsak et al. Citation2006, Esteves et al. Citation2007, Shi et al. Citation2007, Korkut et al. Citation2008, Behr et al. Citation2018). Allegretti et al. (Citation2012) quoted insignificant changes in bending strength and stiffness of wood samples after vacuum-heat treatment. The treatment processes carried out in this study were initiated by a drying step at 103°C and then it was followed by direct exposure to the target temperature. This approach caused therefore minor weight changes in vacuum-heat-treated samples, and subsequently, a slight alteration in bending strength of the treated samples was observed as compared with controls.
Like sole glycerol treatment, a combination of glycerol pretreatment with vacuum-heat treatment significantly reduced the MOR and MOE. Although, the combined treatments, e.g. glycerol pretreatment and vacuum-heat treatment, strongly reduced the MOR and MOE, the reduction was almost half in the samples with a combined treatment containing 20% of glycerol as compared with the sole glycerol pretreated ones at a similar level. The combined modification with higher glycerol content, e.g. 40%, however, exhibited an identical reduction in MOR and MOE as those pretreated with sole glycerol. The results indicate that the effect of vacuum-heat treatment to provide a mild treatment condition is compensated with a presence of higher concentration of glycerol. Thermal degradation analysis of crude glycerol showed remarkable weight loss at temperatures between 240°C and 255°C (Castelló et al. Citation2009, Almazrouei et al. Citation2017). Treatment of wood samples at elevated temperatures such as 180°C and 200°C provides an acidic condition and the existence of a high concentration of glycerol may accelerate the degradation of wood polymers, as shown by the increase in WL value. These results are in-accordance with the Yan and Morrell (Citation2014) who found a reduction in bending properties of heat treated wood samples after pretreatment with glycerol. Nevertheless, the MOR and MOE reduction due to glycerol pretreatment and vacuum-heat treatment are still considerably lower than the values were reported previously with a combination of glycerol and heat-treatment (Mubarok et al. Citation2019).
Automated vapour sorption (AVS) analysis
The water vapour sorption of untreated and treated wood samples during adsorption and desorption processes are shown in (a,b). It should be noted that due to a strong effect of combined treatment at 180°C on the mechanical strength, the samples treated at this temperature were selected for AVS analysis. Sorption curves showed that EMC of the control and treated samples increased in the range of 0–95% RH with the increase in RH. Glycerol treatment resulted in higher EMC value than the other treatments. This can be explained by extra hydroxyl groups that have been delivered by glycerol, i.e. glycerol monomer contains three hydroxyl groups. According to Xie et al. (Citation2011), an increase in moisture content leads to swelling of viscoelastic cell walls and thus accommodation of more water. Therefore, due to the excess amount of hydroxyl groups in glycerol-treated samples, the elasticity of the wood cell wall may have been further increased, and that might have led to the accommodation of more water molecules at higher RH. It should be notified that for a direct comparison of the treatment effect on moisture sorption of wood samples, the influence of the additional weight of glycerol treatment has not been considered in this study. A significant upward bend was observed in EMC of control and treated samples, especially from 75% RH. This can be due to the relaxation of cell wall polymer, resulting in the accommodation of more water molecules (Hosseinpourpia et al. Citation2019). All treated samples (expect for GL40) showed lower EMC than the control at RH below 60%, but the EMC was sharply increased above 75% RH, where the highest EMC value at 95% RH was obtained by GL40-treated sample and followed by GL20 and GL20-VHT180. A similar trend was observed during the desorption process. The EMC value of HVT180 at 95% RH was 17.6%, while the control sample showed an EMC of 22.3% at 95% RH. The moisture increment and decrement of untreated and treated samples are presented in (a,b). Sole glycerol treatment, i.e. GL20 and GL40, showed considerably higher moisture increment and decrement pattern than the other treatments. The moisture increment constantly increased with increasing RH from 15% to 95% in glycerol-treated samples as well as the combination of glycerol and vacuum-heat-treated samples, i.e. GL20, GL40, and GL20-HVT180. The HVT180-treated wood showed the lowest changes in moisture increment and decrement, and this was comparable with the changes in the untreated control.
Figure 2. Adsorption (a) and desorption (b) isotherms of untreated and treated wood for the whole range of RH. GL: glycerol pretreatment; VHT: vacuum-heat treatment; GL-VHT: glycerol-vacuum-heat treatment.
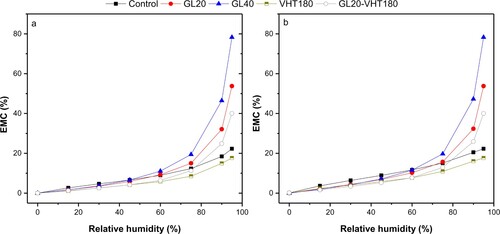
Figure 3. Moisture increment during adsorption (a) and decrement during desorption (b) of untreated and treated wood at each given RH over the full RH range. GL: glycerol pretreatment; VHT: vacuum-heat treatment; GL-VHT: glycerol-vacuum-heat treatment.
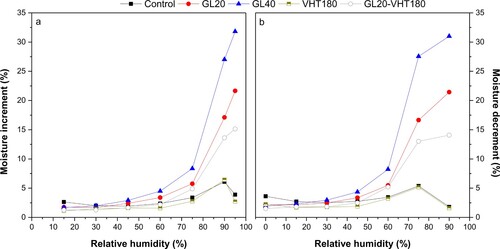
Treatment of wood samples considerably changed the sorption hysteresis over the whole hygroscopic range in comparison with untreated control (). Control samples exhibited a hysteresis maximum at 75% RH. The treated wood samples showed lower sorption hysteresis than control. The glycerol-treated samples, such as GL20 and GL40, illustrated the lowest hysteresis as compared with other treated and untreated samples. Sorption hysteresis was previously explained by the flexibility of cell wall polymer in the glassy state (Hosseinpourpia et al. Citation2016). Slight reduction in the sorption hysteresis of vacuum-heat treated sample as compared with untreated control can be due to a reduction in hydroxyl group content of the cell wall as a result of the degradation of cell wall polysaccharides. Considerably lower sorption hysteresis of combined treated samples in comparison with sole treatment and untreated control might be related to the reduction of cell wall stiffness. As indicated in , the MOE value was strongly decreased by the combined treatments. Therefore, this resulted in increasing the flexibility of wood cell wall at different RH changes during adsorption and desorption runs, and reduction of sorption hysteresis, subsequently.
Figure 4. Hysteresis of untreated and treated wood at each given RH level during the sorption run (obtained by subtraction of EMC between desorption and adsorption at the same RH level, according to Hosseinpourpia et al. Citation2019). GL: glycerol pretreatment; VHT: vacuum-heat treatment; GL-VHT: glycerol-vacuum-heat treatment
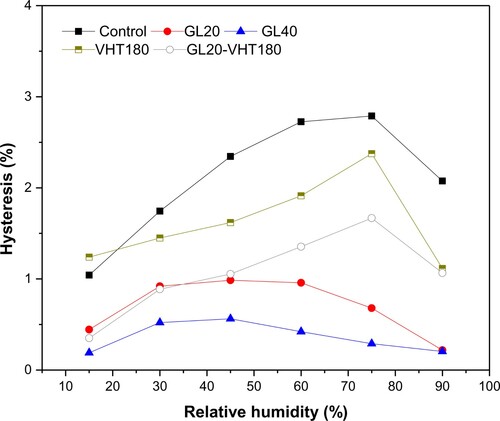
Conclusions
Pretreatment of Scots pine with propanetriol (common name is glycerol) and followed by vacuum-heat treatments increased the Δw values. Fixation of glycerol in wood matrices, as indicated by Δw after leaching, were significantly increased when the wood samples were subjected to the higher temperatures. The glycerol pretreatment induced cell wall bulking (Δv), while its effect on wood swelling is more pronounced after vacuum-heat treatments. The vacuum-heat-treated samples showed the lowest colour changes as compared to the other treatments. The sole vacuum-heat treated samples exhibited comparable bending properties to the untreated controls. While, the combined treatments significantly reduced the bending properties. The moisture content of the samples was strongly increased by glycerol pretreatment. The vacuum-heat-treated samples demonstrated the lowest EMC values in whole RH range during adsorption and desorption runs. The inferior EMC values obtained in combined treated samples as compared with the control ones, particularly at the RHs ranges below 70%. The sorption hysteresis of the samples decreased considerably by glycerol pretreatment. The results indicated that the flexibility of wood cell wall considerably increased by glycerol pretreatment, which might be due to delivering of additional hydroxyl groups into the matrix.
Acknowledgements
Dr Hüseyin Sivrikaya would like to thank the COST Action FP1407 for providing STSM grant to carry out this research.
Disclosure statement
No potential conflict of interest was reported by the author(s)
References
- Allegretti, O., Brunetti, M., Cuccui, I., Ferrari, S., Nocetti, M. and Terziev, N. (2012) Thermo-vacuum modification of spruce (Picea abies Karst.) and fir (Abies alba Mill.) wood. BioResources, 7(3), 3656–3669.
- Almazrouei, M., El Samad, T. and Janajreh, I. (2017) Thermogravimetric kinetics and high fidelity analysis of crude glycerol. Energy Procedia, 142, 1699–1705.
- ASTM D143-14 (2014) Standard Test Methods for Small Clear Specimens of Timber (West Conshohocken, PA: ASTM International).
- Behr, G., Bollmus, S., Gellerich, A. and Militz, H. (2018) Improvement of mechanical properties of thermally modified hardwood through melamine treatment. Wood Material Science & Engineering, 13(5), 262–270.
- Bekhta, P. and Niemz, P. (2003) Effect of high temperature on the change in color, dimensional stability and mechanical properties of spruce wood. Holzforschung, 57(5), 539–546.
- Berube, M. A., Schorr, D., Ball, R. J., Landry, V. and Blanchet, P. (2018) Determination of in situ esterification parameters of citric acid-glycerol based polymers for wood impregnation. Journal of Polymers and the Environment, 26(3), 970–979.
- Brischke, C., Bayerbach, R. and Otto Rapp, A. (2006) Decay-influencing factors: A basis for service life prediction of wood and wood-based products. Wood Material Science and Engineering, 1(3–4), 91–107.
- Brischke, C., Welzbacher, C. R., Brandt, K. and Rapp, A. O. (2007) Quality control of thermally modified timber: Interrelationship between heat treatment intensities and CIE L* a* b* color data on shomogenised wood samples. Holzforschung, 61(1), 19–22.
- Calonego, F. W., Severo, E. T. D. and Furtado, E. L. (2010) Decay resistance of thermally-modified Eucalyptus grandis wood at 140 ℃, 160 ℃, 180 ℃, 200 ℃ and 220 ℃. Bioresource Technology, 101(23), 9391–9394.
- Castelló, M., Dweck, J. and Aranda, D. (2009) Thermal stability and water content determination of glycerol by thermogravimetry. Journal of Thermal Analysis and Calorimetry, 97(2), 627–630.
- Endo, K., Obataya, E., Zeniya, N. and Matsuo, M. (2016) Effects of heating humidity on the physical properties of hydrothermally treated spruce wood. Wood Science and Technology, 50(6), 1161–1179.
- Esteves, B., Marques, A. V., Domingos, I. and Pereira, H. (2007) Influence of steam heating on the properties of pine (Pinus pinaster) and eucalypt (Eucalyptus globulus) wood. Wood Science and Technology, 41(3), 193–207.
- Esteves, B. M., Domingos, I. J. and Pereira, H. M. (2008) Pine wood modification by heat treatment in air. BioResources, 3(1), 142–154.
- Esteves, B. and Pereira, H. (2009) Wood modification by heat treatment: A review. BioResources, 4(1), 370–404.
- Ferrari, S., Cuccui, I. and Allegretti, O. (2013) Thermo-vacuum modification of some European softwood and hardwood species treated at different conditions. BioResources, 8(1), 1100–1109.
- González-Peña, M. M. and Hale, M. D. (2009) Colour in thermally modified wood of beech, Norway spruce and Scots pine. Part 1: Colour evolution and colour changes. Holzforschung, 63(4), 385–393.
- Hong, S. H., Kim, C. H., Lim, H. M. and Kang, H. Y. (2013) Measuring PEG retentions and EMCs of PEG impregnated softwood specimens after heat-treatment. Journal of the Korean Wood Science and Technology, 41(3), 173–180.
- Hosseinpourpia, R. and Mai, C. (2016) Mode of action of brown rot decay resistance of thermally modified wood: Resistance to Fenton's reagent. Holzforschung, 70(7), 691–697.
- Hosseinpourpia, R., Adamopoulos, S. and Mai, C. (2016) Dynamic vapour sorption of wood and holocellulose modified with thermosetting resins. Wood Science and Technology, 50(1), 165–178.
- Hosseinpourpia, R., Adamopoulos, S., Holstein, N. and Mai, C. (2017) Dynamic vapour sorption and water-related properties of thermally modified Scots pine (Pinus sylvestris L.) wood pretreated with proton acid. Polymer Degradation and Stability, 138, 161–168.
- Hosseinpourpia, R., Adamopoulos, S. and Parsland, C. (2019) Utilization of different tall oils for improving the water resistance of cellulosic fibers. Journal of Applied Polymer Science, 136(13), Article ID 47303.
- Johansson, D. and Morén, T. (2006) The potential of colour measurement for strength prediction of thermally treated wood. Holz als Roh-und Werkstoff, 64(2), 104–110.
- Korkut, S., Akgül, M. and Dündar, T. (2008) The effects of heat treatment on some technological properties of Scots pine (Pinus sylvestris L.) wood. Bioresource Technology, 99(6), 1861–1868.
- Kutnar, A., Kričej, B., Pavlič, M. and Petrič, M. (2013) Influence of treatment temperature on wettability of Norway spruce thermally modified in vacuum. Journal of Adhesion Science and Technology, 27(9), 963–972.
- Lekounougou, S. and Kocaefe, D. (2014) Effect of thermal modification temperature on the mechanical properties, dimensional stability, and biological durability of black spruce (Picea mariana). Wood Material Science Engineering, 9(2), 59–66.
- Liu, R., Morrell, J. J. and Yan, L. (2018) Thermogravimetric analysis studies of thermally-treated glycerol impregnated poplar wood. BioResources, 13(1), 1563–1575.
- Luo, S., Cao, J. and Peng, Y. (2014) Properties of glycerin-thermally modified wood flour/polypropylene composites. Polymer Composites, 35(2), 201–207.
- Militz, H. (2002) Thermal treatment of wood: European processes and their background (IRG/WP 02-40241), In: 33rd Annual Meeting for International Research Group on Wood Preservation, Cardiff, UK.
- Mitsui, K., Takada, H., Sugiyama, M. and Hasegawa, R. (2001) Changes in the properties of light-irradiated wood with heat treatment. Part 1. Effect of treatment conditions on the change in color. Holzforschung, 55(6), 601–605.
- Mohareb, A., Sirmah, P., Petrissans, M. and Gerardin, P. (2012) Effect of heat treatment intensity on wood chemical composition and decay durability of Pinus patula. European Journal of Wood and Wood Products, 70(4), 519–524.
- Mubarok, M., Dumarcay, S., Militz, H., Candelier, K., Thevenon, M. F. and Gérardin, P. (2019) Comparison of different treatments based on glycerol or polyglycerol additives to improve properties of thermally modified wood. European Journal of Wood and Wood Products, 77(5), 799–810.
- Pockrandt, M., Jebrane, M., Cuccui, I., Allegretti, O., UetimaneJr.E. and Terziev, N. (2018) Industrial Thermowood® and Termovuoto thermal modification of two hardwoods from Mozambique. Holzforschung, 72(8), 701–709.
- Poncsak, S., Kocaefe, D., Bouazara, M. and Pichette, A. (2006) Effect of high temperature treatment on the mechanical properties of birch (Betula papyrifera). Wood Science and Technology, 40(8), 647–663.
- Qu, L., Wang, Z., Qian, J., He, Z. and Yi, S. (2019) Effect of combined aluminum-silicon synergistic impregnation and heat treatment on the thermal stability, chemical components, and morphology of wood. Bioresources, 14(1), 349–362.
- Rep, G., Pohleven, F. and Košmerl, S. (2012) Development of the industrial kiln for thermal wood modification by a procedure with an initial vacuum and commercialisation of modified Silvapro wood. In Proceedings of the 6th European Conference on Wood Modification (pp. 11–17). Slovenia: University of Ljubljana Ljubljana.
- Roussel, C., Marchetti, V., Lemor, A., Wazniak, B., Loubinoux, B. and Gerardin, P. (2001) Chemical modification of wood by polyglycerol/maleic anhydride treatment. Holzforschung, 55, 57–62.
- Rowell, R. M., Ibach, R. E., McSweeny, J. and Nilsson, T. (2009) Understanding decay resistance, dimensional stability and strength changes in heat-treated and acetylated wood. Wood Material Science and Engineering, 4(1–2), 14–22.
- Salman, S., Pétrissans, A., Thévenon, M. F., Dumarçay, S. and Gérardin, P. (2016) Decay and termite resistance of pine blocks impregnated with different additives and subjected to heat treatment. European Journal of Wood and Wood Products, 74(1), 37–42.
- Salman, S., Thévenon, M. F., Pétrissans, A., Dumarçay, S., Candelier, K. and Gérardin, P. (2017) Improvement of the durability of heat-treated wood against termites. Maderas Ciencia y Tecnología, 19(3), 317–328.
- Sandak, A., Sandak, J. and Allegretti, O. (2015) Quality control of vacuum thermally modified wood with near infrared spectroscopy. Vacuum, 114, 44–48.
- Sandberg, D., Haller, P. and Navi, P. (2013) Thermo-hydro and thermo-hydro-mechanical wood processing: An opportunity for future environmentally friendly wood products. Wood Material Science and Engineering, 8(1), 64–88.
- Shi, J. L., Kocaefe, D. and Zhang, J. (2007) Mechanical behaviour of Quebec wood species heat-treated using Thermowood process. Holz als Roh-und Werkstoff, 65(4), 255–259.
- Sivonen, H., Maunu, S. L., Sundholm, F., Jämsä, S. and Viitaniemi, P. (2002) Magnetic resonance studies of thermally modified wood. Holzforschung, 56(6), 648–654.
- Sivrikaya, H., Tesařová, D., Jeřábková, E. and Can, A. (2019) Color change and emission of volatile organic compounds from Scots pine exposed to heat and vacuum-heat treatment. Journal of Building Engineering, 26, Article ID 100918.
- Soulounganga, P., Loubinoux, B., Wozniak, E., Lemor, A. and Gérardin, P. (2004) Improvement of wood properties by impregnation with polyglycerol methacrylate. Holz als Roh-und Werkstoff, 62(4), 281–285.
- Suchy, M., Virtanen, J., Kontturi, E. and Vuorinen, T. (2010a) Impact of drying on wood ultrastructure observed by deuterium exchange and photoacoustic FT-IR spectroscopy. Biomacromolecules, 11(2), 515–520.
- Suchy, M., Kontturi, E. and Vuorinen, T. (2010b) Impact of drying on wood ultrastructure: Similarities in cell wall alteration between native wood and isolated wood-based fibers. Biomacromolecules, 11(8), 2161–2168.
- Sun, B., Wang, Z. and Liu, J. (2017) Changes of chemical properties and the water vapour sorption of Eucalyptus pellita wood thermally modified in vacuum. Journal of Wood Science, 63(2), 133–139.
- Sundqvist, B. (2004) Colour Changes and Acid Formation in Wood During Heating, Doctoral Thesis, Lulea University of Technology, Lulea, Sweden.
- Tjeerdsma, B. F., Boonstra, M., Pizzi, A., Tekely, P. and Militz, H. (1998) Characterization of thermally modified wood: Molecular reasons for wood performance improvement. Holz als Roh-und Werkstoff, 56(3), 149–153.
- Tjeerdsma, B. F. and Militz, H. (2005) Chemical changes in hydrothermal treated wood: FTIR analysis of combined hydrothermal and dry heat-treated wood. Holz als roh-und Werkstoff, 63(2), 102–111.
- Tuong, V. M. and Li, J. (2010) Effect of heat treatment on the change in color. BioResources, 5(2), 1257–1267.
- Vieira, M. G. A., da Silva, M. A., dos Santos, L. O. and Beppu, M. M. (2011) Natural-based plasticizers and biopolymer films: A review. European Polymer Journal, 47(3), 254–263.
- Wang, W., Zhu, Y., Cao, J. and Guo, X. (2015) Thermal modification of southern pine combined with wax emulsion preimpregnation: Effect on hydrophobicity and dimensional stability. Holzforschung, 69(4), 405–413.
- Weiland, J. J. and Guyonnet, R. (2003) Study of chemical modifications and fungi degradation of thermally modified wood using DRIFT spectroscopy. Holz als Roh-und Werkstoff, 61(3), 216–220.
- Wentzel, M., Fleckenstein, M., Hofmann, T. and Militz, H. (2019) Relation of chemical and mechanical properties of Eucalyptus nitens wood thermally modified in open and closed systems. Wood Material Science & Engineering, 14(3), 165–173.
- Willems, W. and Altgen, M. (2020) Hygrothermolytic wood modification. Process description and treatment level characterisation. Wood Material Science & Engineering, 15(4), 213–222.
- Xiao, Z., Xie, Y., Militz, H. and Mai, C. (2010) Effect of glutaraldehyde on water related properties of solid wood. Holzforschung, 64(4), 483–488.
- Xie, Y., Hill, C. A., Xiao, Z., Mai, C. and Militz, H. (2011) Dynamic water vapour sorption properties of wood treated with glutaraldehyde. Wood Science and Technology, 45(1), 49–61.
- Yan, L., Cao, J., Gao, W., Zhou, X. and Zhao, G. (2011) Interaction between glycerin and wood at various temperatures from stress relaxation approach. Wood Science and Technology, 45(2), 215–222.
- Yan, L. and Morrell, J. J. (2014) Effects of thermal modification on physical and mechanical properties of Douglas fir heartwood. BioResources, 9(4), 7152–7161.
- Yan, L. and Morrell, J. J. (2019) Kinetic color analysis for assessing the effects of borate and glycerol on thermal modification of wood. Wood Science and Technology, 53(23), 263–274.
- Zhu, Y., Wang, W. and Cao, J. (2014) Improvement of hydrophobicity and dimensional stability of thermally modified southern pine wood pretreated with oleic acid. BioResources, 9(2), 2431–2445.