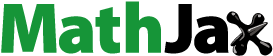
ABSTRACT
Furfurylated wood has been used widely for exterior purposes due to its superior dimensional stability and biological durability, though its fire resistance is not enhanced. Here, the introduction of the fire-retardant additive guanyl-urea phosphate (GUP) into furfurylated wood is reported. The treatment improved both the thermal and fire stabilities of the modified wood, as supported by the results of thermal gravimetric analysis (TGA) and limiting oxygen index (LOI) before and after accelerated ageing testing (according to EN 84) to determine the water resistance of the treatment. The results indicated that the hydroscopic GUP remained within the wood structure and provided superior thermal and fire properties. The work suggests the idea of combining GUP and furfuryl alcohol (FA), which has the prospective to impart substantial fire-retardancy to the furfurylated wood, thus increasing the potential for exterior applications.
Introduction
Whilst wood is a sustainable biopolymer that has been used in various applications such as construction or furniture, its intrinsic hydrophilicity, low to medium durability and low fire stability limits its application in our modern society. Bio-derived furfuryl alcohol (FA) has been shown as a means for improving the durability of wood (Baysal et al. Citation2004, Lande et al. Citation2008), since FA readily penetrates the wood cell wall and reinforces the wood cell with the polymerised hydrophobic FA (Kong et al. Citation2018). Nevertheless, the fire stability of the furfurylated wood is considered the same level as the unmodified wood (Dong et al. Citation2015). The main difficulty to improve the fire-retardancy of furfurylated wood is the low compatibility between FA with other common fire-retardant chemicals; phase separation might happen and thus reduces the treatment efficiency.
The suitability of using guanyl-urea phosphate (GUP) in conjunction with resin modifications of wood has already been demonstrated for melamine-based resins (Lin et al. Citation2021), and these initial studies outline progress in its application with furfurylation systems. The polymerised hydrophobic FA is also expected to alleviate the water leachability of GUP. Preliminary results for the leaching resistance of the modified wood were evaluated by applying the European standard EN 84 (CEN Citation2020). The thermal and fire stabilities were determined before and after excessive leaching with water.
Materials and method
Scots pine (Pinus sylvestris L.) sapwood specimens with a dimension of 10 × 10 × 150 mm (tangential (T) × radial (R) × longitudinal (L)), knot- and crack-free, were conditioned at 20°C and 65% relative humidity (RH) to reach an equilibrium moisture content (EMC) of about 12%. The density of the conditioned specimens was at about 550 ± 50 kg/m3. The weight (m1) of the conditioned specimen was recorded.
Guanyl-urea phosphate (C2H9N4O5P, 98% purity, GUP) and furfuryl alcohol (C5H6O2, 98% purity, FA) were obtained from Fisher Scientific, Sweden. Triethanolamine (C6H15NO3, 98% purity) was bought from Sigma-Aldrich, Sweden. Synthesis-grade maleic anhydride (C4H2O3) was purchased from Merck, Germany.
Three different formulations were prepared: (i) a water solution containing FA (30 wt%) with maleic anhydride (3 wt%), denoted as 0-30FA, (ii) a water solution containing FA (30 wt%), maleic anhydride (3 wt%), GUP (3 wt%) and triethanolamine (1 wt%), denoted as 3-30FA, and (iii) a water solution containing FA (30 wt%), maleic anhydride (3 wt%), GUP (5 wt%) and triethanolamine (1 wt%), denoted as 5-30FA.
The formulations were impregnated into specimens (10 replicates) following a vacuum-pressure impregnation technique. The specimens were fully immersed in the formulations prior to 30 min at 20 mbar followed by 1 hr at 15 bar. Then, the excess formulation on the surface of the specimen was removed by tissue paper before wrapping it in aluminium foil and curing at 130°C for 1 d. The cured specimens were then conditioned at 20°C and 65% RH and recorded its weight (m2). The weight percentage gain (WPG) of the modified wood was calculated:
(1)
(1) The leaching test was carried out on five replicates following European standard EN 84 over a 14-day period. Thermal gravimetric analysis (TGA) was undertaken with a PerkinElmer TGA 4000 to analyse the thermal behaviour of the specimens. The surface of the specimen was cut out with a microtome blade and 4 ± 1 mg was loaded in an alumina crucible heated from 30 to 800°C at a rate of 10°C min−1 under a N2 flow rate of 20 mL min−1. At least three replicates were performed for each treatment. The fire behaviour was characterised by limiting oxygen index (LOI) (Fire Testing Technology Ltd., UK) following standard ISO 4589-2: (ISO Citation2017).
Results and discussion
Weight percentage gain (WPG) showed the amount of loaded chemicals within the wood structure of the modified wood (), with results for the GUP-containing furfurylated wood having a slightly lower WPG than furfurylated wood.
Table 1. Weight per cent gain (WPG) obtained for various furfurylation treatments.
The TGA and first-order derivative curves are shown in . All the wood specimens had an initial small mass loss (about 3 wt%) until 110°C, due to the loss of the absorbed water. After that, the unmodified wood had a mass loss between 250°C and 370°C, due to the decomposition of the hemicellulose and cellulose components in the wood (Rowell and Dietenberger Citation2013). The decomposition of lignin happens over a wider range, between 200°C and 600°C. Decomposition above 600°C is related to the aromatic structure (Tejado et al. Citation2007). The pyrolysis of the unmodified wood has only 1.3 wt% of its original weight at 800°C.
For the conventional furfurylated wood, 0-30FA, the incorporation of polymerised FA influences the thermal behaviour of the wood. The mass loss starts earlier at 200°C, relating to the cleave of the weaker chemical bonds in polymerised FA (Guigo et al. Citation2009). It is also noticed that the 0-30FA has the similar main decomposition temperature as the unmodified wood (around 370°C) without additional peak or peak shifting. This might be because the main decomposition of polymerised FA is between 320°C and 400°C, similar to the decomposition temperature of cellulose (Guigo et al. Citation2009). The furfurylated wood has a slightly increased char residue after the pyrolysis, with a carbon-residue at 800°C of 2.8 wt% of its original weight.
The incorporation of the fire-retardant additive GUP significantly increases the mass of char residue at elevated temperatures. This is because GUP causes an earlier degradation. It is evident that the main decomposition temperature of 3-30FA and 5-30FA specimens is shifted to lower temperature, 310°C. The role of GUP is to promote char formation and forming protective glassy layers, thus higher char residue at elevated temperature can be observed (Wang et al. Citation2004). The carbon-rich char residue at 800°C of the GUP containing treatments is significantly enhanced. The mass residue of 3-30FA and 5-30FA are 9.6 and 17.5 wt%, respectively.
The thermal behaviour of the water-leached 3-30FA and 5-30FA was also examined. The leached 3-30FA and 5-30FA (3-30FA-EN84 and 5-30FA-EN84) exhibited higher mass residue than the conventional furfurylated wood. The result implied the water resistance of the hygroscopic GUP by incorporating with polymerised FA. This was also supported by the main decomposition peak shifting of the leached specimens.
LOI determines the minimum oxygen concentration that supported the combustion behaviour, distinguishing the relative flammability of wood specimens. A higher LOI value indicates lower flammability of the specimens. The incorporation of the polymerised FA into the wood increases LOI value from 25% to 30% because of the slight thermal stability improvement provided by the polymerised FA () (Guigo et al. Citation2009).
The introduction of a small amount of GUP to the treatment gives higher LOI due to the fire protective effect of GUP (Wang et al. Citation2004). The higher concentration of GUP concentration realises a lower flammability of the modified wood. The water leached furfurylated wood, 3-30FA and 5-30FA, still show superior LOIs as compared with 0-30FA. The decreased LOI value indicates the partial loss of GUP during the water leaching test, confirming the observations from TGA results.
Conclusion
A leach-resistant fire-retardant furfurylated wood was successfully developed by incorporating GUP into the furfurylation system. The result of TGA and LOI indicated that GUP improved the thermal and fire stability of the modified wood. The specimens were also further subjected to water-leaching test, suggesting the water-resistance of such kind of fire-retardant treatment. This study reveals the potential way for improving the fire-retardancy of furfurylated wood through the incorporation of a fire-retardant additive.
Disclosure statement
No potential conflict of interest was reported by the author(s).
Additional information
Funding
References
- Baysal, E., Ozaki, S. K. and Yalinkilic, M. K. (2004) Dimensional stabilization of wood treated with furfuryl alcohol catalysed by borates. Wood Science and Technology, 38(6), 405–415.
- CEN 2020: SS-EN 84:2020 Wood preservatives – accelerated ageing of treated wood prior to biological testing – Leaching procedure. European Committee for Standardisation, Brussels, Belgium.
- Dong, Y., Yan, Y., Zhang, S., Li, J. and Wang, J. (2015) Flammability and physical–mechanical properties assessment of wood treated with furfuryl alcohol and nano-SiO2. European Journal of Wood and Wood Products, 73(4), 457–464.
- Guigo, N., Mija, A., Zavaglia, R., Vincent, L. and Sbirrazzuoli, N. (2009) New insights on the thermal degradation pathways of neat poly(furfuryl alcohol) and poly(furfuryl alcohol)/SiO2 hybrid materials. Polymer Degradation and Stability, 94(6), 908–913.
- ISO 2017. ISO 4589-2:2017 Plastics – determination of burning behaviour by oxygen index – Part 2: Ambient-temperature test. International Standardisation Organisation, Geneva, Switzerland.
- Kong, L., Guan, H. and Wang, X. (2018) In situ polymerization of furfuryl alcohol with ammonium dihydrogen phosphate in poplar wood for improved dimensional stability and flame retardancy. ACS Sustainable Chemistry and Engineering, 6(3), 3349–3357.
- Lande, S., Westin, M. and Schneider, M. (2008) Development of modified wood products based on furan chemistry. Molecular Crystals and Liquid Crystals, 484, 1/[367]–12/[378].
- Lin, C., Karlsson, O., Martinka, J., Rantuch, P., Garskaite, E., Mantanis, G. I., Jones, D. and Sandberg, D. (2021) Approaching highly leaching-resistant fire-retardant wood by in situ polymerization with melamine formaldehyde resin. ACS Omega, 6(19), 12733–12745.
- Rowell, R. M. and Dietenberger, M. A. (2013) Thermal properties, combustion, and fire retardancy of wood. In R. M. Rowell (ed.) Handbook of Wood Chemistry and Wood Composites (Boca Raton, FL: CRC Press), pp. 127–149.
- Tejado, A., Peña, C., Labidi, J., Echeverria, J. M. and Mondragon, I. (2007) Physico-chemical characterization of lignins from different sources for use in phenol-formaldehyde resin synthesis. Bioresource Technology, 98(8), 1655–1663.
- Wang, Q., Li, J. and Winandy, J. (2004) Chemical mechanism of fire retardance of boric acid on wood. Wood Science and Technology, 38(5), 375–389.