ABSTRACT
Citric acid can be used as a bio-based binding agent in composites made from lignocellulosic material due to its crosslinking ability with hydroxyl groups via ester formation. Even though plenty of research has investigated diverse manufacturing conditions, with a focus on citric acid content and pressing temperature, an apparent knowledge gap persists regarding their effect on the properties of particleboards made from softwood sawdust. Furthermore, the optimal temperature for particleboards crafted from mostly non-wood lignocellulosic materials was found to be 180–200°C which is lower than that observed for softwood material in a prior study. This study aimed to systematically examine the effects of citric acid content and pressing temperature on particleboards derived from softwood sawdust. Results highlighted a positive correlation of both citric acid content and pressing temperature with mechanical and hygroscopic properties of the particleboards, the best results being achieved at 20 wt% citric acid and 220°C, exhibiting a thickness swelling of 9%, internal bonding strength of 0.77 MPa and a modulus of rupture of 4.3 MPa. This study served as a foundational framework for future investigations into the addition of other chemicals, offering a comprehensive understanding of their interactions with citric acid in particleboard manufacturing.
Introduction
In 2022, the European production of particleboards amounted to 44 million m3, representing 42% of the global particleboard production. Within this context, Swedish production accounted for just over 1% of the European volume (FAOSTAT Citation2024). Particleboards are primarily composed of wood particles, such as wood chips, sawdust, and shavings, sourced from low-quality timber, small-diameter logs, and wood processing residues (EPF Citation2017). Consequently, particleboards are ecologically significant, as they enhance sustainability due to carbon sequestration and minimize waste. The particles are bonded together using resins and additives. Urea formaldehyde is the most commonly used adhesive for particleboards in dry conditions (Dunky Citation1998) due to its quick curing time and efficient production, despite its low moisture resistance and high formaldehyde emissions, which pose health risks (Kanazawa et al. Citation2010). Alternatives like melamine-enhanced urea formaldehyde and phenol formaldehyde offer better moisture resistance (Ding et al. Citation2021) but are more expensive and have their own drawbacks, prompting the search for greener, formaldehyde-free adhesives. Regulatory pressures and environmental considerations are driving the development of these eco-friendly alternatives – one of the potential ones being citric acid.
Citric acid (C6H8O7) has the capability to react with the hydroxyl groups of the wood cell wall via a two-step esterification mechanism. Its three carboxylic acid groups allow for two ester bonds to be formed which provides citric acid with a cross linking ability (McSweeny et al. Citation2006). Citric acid has been studied as a wood-modification agent and as a binding agent; on its own and in combination with other hydroxylic reagents, such as glycerol, glucose, sucrose, tannin, or sorbitol (Lee et al. Citation2020). Umemura et al. (Citation2012b) investigated the potential of citric acid as an adhesive for molding of bark powder. Since then, several studies have been executed to determine suitable raw materials, the optimal manufacturing conditions and additional chemicals for particleboards and other bio-based composites. The results of studies varying manufacture conditions for solely citric acid-bonded particleboards and moldings are presented in . It is worth noting that in addition to the manufacturing parameters presented, these studies also varied in factors such as particle size, shape, and moisture content of the raw material during pressing. From the data it is apparent that the manufacture parameters are raw material-dependent, with a citric acid content of 20–30 wt% and a pressing temperature of 180–200°C being most suitable. However, only four of the shown studies (Widyorini et al. Citation2013, Citation2018, Syamani et al. Citation2020, Nitu et al. Citation2022) varied these parameters simultaneously. Even though citric acid has been used for manufacture of softwood-based particleboard, the large share of studies investigating the influence of citric acid content and pressing parameter have been done on non-wood lignocellulosic materials. Our previous research on particleboard from softwood sawdust (Scharf et al. Citation2023) exhibited improved properties when increasing the pressing temperature from 200°C to 220°C. The objective of this study was thus to determine the effect of citric acid content and pressing temperature on the properties of particleboards made from residual softwood sawdust in a systematic approach. This allows to better evaluate future findings, which utilize citric acid, alone and in combination with other chemicals.
Table 1. Summary of studies varying the citric acid content and/or pressing temperature for manufacture of lignocellulosic-based particle composites with the addition of only citric acid as an adhesive. Underlined values indicate the suggested optimal manufacturing properties of each study.
Materials and methods
Sawmill residuals in the form of sawdust were acquired from a sawmill in northern Sweden (Holmen AB, Kroksjön, Västerbotten, Sweden), where Scots pine (Pinus sylvestris L.) and Norway spruce (Picea abies (L.) Karst.) were processed. Utilizing residual sawdust from sawmill processes, rather than burning it, significantly increases carbon storage and promotes more sustainable practices. The freshly obtained sawdust underwent drying in an oven at 60°C for 24 h, followed by 12 h at 103°C. To eliminate larger particles, a sieve with 3.2 mm apertures was employed, and the portion passing through the sieve was utilized for particleboard production. The particle geometry was characterized by laser line-based measurements with a 3D Particle View unit (Fagus-GreCon Greten GmbH & Co. KG, Hannover, Germany). A sample with 63,934 particles was analyzed and the size distribution in length, width and thickness is shown in . The average and median slenderness (ratio of particle length to particle thickness) was 9.7 and 8.1, respectively.
Figure 1. Measurement of particle size distribution in length, width, and thickness of the sieved sawdust fraction used for particleboard manufacture.
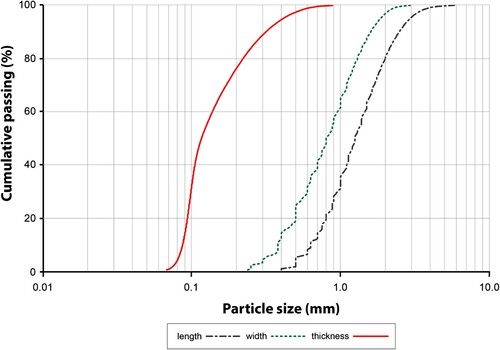
After drying, the particles were combined with an adhesive system using a blender, where aqueous solutions of analytical-grade citric acid (C6H8O7) powder (99.9%, VWR International AB, Stockholm, Sweden) were sprayed in a mass ratio of solution to particles of around 2:1. The particle blend was then dried again to approximately 0% moisture content (MC) at 60°C for 16 h, followed by 6 h at 103°C. The particle blend was pressed for 10 min to a single-layer particleboard in an open system hot press (HLOP15, Höfer Presstechnik GmbH, Taiskirchen, Germany) with target dimensions and density of 220 × 220 × 8 mm and 750 kg/m3, respectively. The chosen high density, in contrast to the common particleboards’ density of 600–650 kg/m3, was selected to compensate for the relatively low slenderness of the particles used, which would likely result in lower bending properties. Moreover, nearly all the studies summarized in aimed for a target particleboard density of 800 kg/m3.
A full factorial design was employed, varying the chemical content, and pressing temperature as shown in . The chemical content of citric acid in the dried particle blend (wt/wt) was achieved by varying the concentration of the solution. As a control, melamine urea formaldehyde (MUF) resin solution (50 wt% solid content), obtained from Dynea AS (Lillestrøm, Norway), with 1 wt% ammonium nitrate (VWR International AB, Stockholm, Sweden) added as a hardener, was directly sprayed onto the particles, and pressed without additional drying. For class P5 boards according to the EN 312 standard (CEN Citation2010), i.e. particleboards in load-bearing, moist conditions, a MUF-resin content of 8–16% is typical (Krug et al. Citation2023).
Table 2. Manufacture parameters of particleboards.
After pressing, the edges of the particleboards were trimmed. Thickness and mass were measured before and after the boards were conditioned at 20°C and 65% relative humidity (RH) for 7 days, to determine equilibrium moisture content (EMC) and thickness swelling from dry to EMC-state. Afterwards, the particleboards were separated into different specimens for further testing of modulus of elasticity (MOE) and modulus of rupture (MOR) in bending according to the EN 310 standard (CEN Citation1993a), internal bonding strength (IB) according to the EN 319 standard (CEN Citation1993b), and thickness swelling (TS) and water uptake (WA) after 24 h immersion in water according to the EN 317 standard (CEN Citation1993c). A universal testing machine (MTS System Corporation, Eden Prairie, MN, USA) equipped with either a 500 N (MOE and MOR) or a 50 kN (IB) load cell was used. The specimen dimensions were as recommended in the respective standards and two specimens per each test were prepared from each board. Density profiles of the specimens used for IB and TS testing were obtained by an X-ray densitometer (DENSE-LAB X, Electronic Wood System GmbH, Hameln, Germany).
Results and discussion
shows EMC, thickness swelling, and density at EMC, influenced by pressing temperature and citric acid content. An increased temperature and a more acidic conditions accelerate hydrolysis and esterification reactions, likely impacting EMC and thickness swelling. Boards pressed at 180°C with less than 15% citric acid exhibited significant swelling due to fewer ester bonds formed and more available hydroxyl groups (Gomes et al. Citation2020). Achieving the target density of 750 kg/m3 proved challenging due to multiple factors. Density directly after pressing was influenced by the citric acid content, as this also affected the amount of sawdust in the press which had to be compacted in dry state, and thus below the glass-transition temperature of the wood. This resulted in significant springback when the pressing force was released. Higher temperature and citric acid content, and thus less amounts of sawdust mitigated springback effects. However, these two parameters correlated positively with an increased mass loss due to the release of water from citric acid in the two-step esterification mechanism. The esterification-based mass loss was considered by increasing the input mass, whilst the elastic compression and resulting springback could not. Relatively high EMC and thickness swelling further lowered the density at EMC for boards pressed at 180°C and less than 15% citric acid content.
Table 3. Specimen properties after pressing and conditioning to equilibrium moisture content (EMC).
shows the MOE, MOR, IB and TS of the conditioned specimens. The MOE of boards bond with citric acid was similar to the MUF reference boards except for the boards with a density below 700 kg/m3. MOE in (a) correlates with pressing temperature and citric acid content, mainly caused by the difference in density. Umemura et al. (Citation2015) showed a linear relationship between board density and bending properties in the range of 400–800 kg/m3. The positive influence of pressing temperatures and citric acid content was more distinct in MOR ((b)), with 220°C and 20% citric acid resulting in the highest values. A higher temperature and a higher citric acid content likely resulted in more ester formations, potentially crosslinking the particles with each other (Umemura et al. Citation2012a). The achieved MOR was however only around half of the MUF reference. Azeredo et al. (Citation2015) assigned plasticizing capabilities to citric acid for films made from wheat straw hemicelluloses which could explain the relatively high MOE and relatively low MOR in comparison to the MUF reference. IB in (c) shows a more distinct positive influence by an increase in pressing temperature from 200°C to 220°C. A citric acid content of 20 wt% pressed at 220°C resulted in a similar IB strength as the MUF reference group. Both the bending properties and the IB might be affected by the density profiles, as all citric acid-bonded boards showed flat, plateau-like density profiles while MUF-bonded boards exhibited typical “U”-shaped density profiles (Korai Citation2021). TS is shown in (d) and correlated the strongest with pressing temperature and citric acid content. The boards pressed at 180°C and with 5 wt% citric acid disintegrated during the 24 h immersion in water, whilst the 10% citric acid equivalent was sponge-like. All other boards exhibited relative rigidity. TS is highly influenced by the hygroscopicity of the wood. High pressing temperature and citric acid content led to an increased thermal and chemical modification of the hydroxyl groups lowering the hygroscopicity. Water uptake after 24 h immersion showed similar trends as TS, ranging from 167 ± 7% (10 wt% citric acid at 180°C) to 78 ± 3% (20 wt% citric acid at 220°C) and 80 ± 4% for MUF boards.
Figure 2. Mean ± standard deviation of (a) MOE, and (b) MOR during bending, (c) internal bonding strength, and (d) thickness swelling after 24 h immersion in water, where the maximum y-value in (d) indicates disintegration of the specimen. Number of replicates per group = 6.
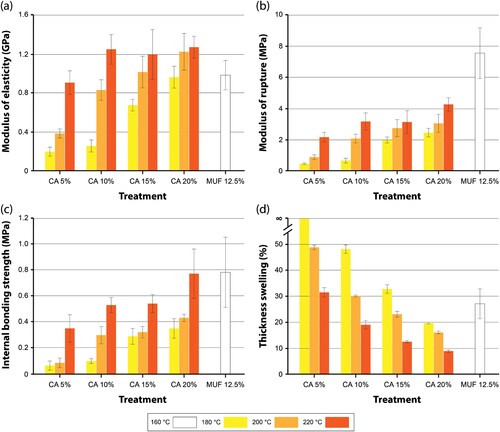
The variance between the optimal temperature determined in our study and the values listed in may arise from several factors, including the composition of the raw materials utilized and their respective thermal degradation temperature ranges. Additionally, other material properties, such as those affecting the adhesive potential of citric acid at specific temperatures, could also contribute to this. The accuracy of the press platen temperature measurements was verified.
None of the produced boards, including those bonded with citric acid and the MUF reference boards, met the EN 312 P-class requirements for MOR and MOE (CEN Citation2010). This could be attributed to particle geometry and the inherent characteristics of the wood particles used, partially unknown due to the material source being the sawmill environment, resulting in an undefined mix of species (Pinus sylvestris L. and Picea abies), sapwood and heartwood. The slenderness of particles significantly affects the properties of particleboards. Rackwitz (Citation1963) showed for single-layer particleboards of spruce that an increase in slenderness of particles leads to an increase in MOE, MOR, and TS, while IB is decreased. The best results were obtained at a slenderness of around 80 for MOE and MOR, but IB and TS were favorable at a slenderness below 25. This is also a reason why different particles are used in the surface and core layers of industrial manufactured particleboards. The particles used in this exhibited a relatively low mean slenderness (9.7). Next to the chemical loading and pressing temperature, the slenderness is likely a reason why the best boards could fulfill the P7 class requirements of the EN 312 standard in terms of IB (> 0.75 MPa) and TS (<10%), but could not fulfill the minimum requirements for P1 class in MOR (>10.5 MPa). However, especially for MOR, comparison with the MUF-control group showed significantly lower values, even though the same particles were utilized.
Conclusion
The experimental findings underscore significant differences in mechanical and hygroscopic properties for boards bonded with 5–20% citric acid and pressed at a temperature between 180°C and 220°C. Pressing temperature and citric acid content demonstrated a notable positive correlation with modulus of rupture, internal bonding strength and thickness swelling, whilst the effects on modulus of elasticity were less pronounced. The most promising results were obtained for boards pressed at 220°C and with 20% citric acid, exhibiting a thickness swelling of 9%, internal bonding strength of 0.77 MPa and a modulus of rupture of 4.3 MPa. Results indicate that both parameters can be adjusted to alter the properties of the boards. Notably, the difference in the properties between boards pressed at 200°C and 220°C was not as pronounced as between boards pressed at 180°C and 200°C.
Boards pressed at 220°C and with higher citric acid content exhibited very good thickness swelling, indicating reduced hygroscopicity. Therefore, when mechanical properties and dimensional stability are paramount, pressing at 220°C with higher citric acid content should be favored over 200°C. These findings offer valuable insights for optimizing manufacturing processes in the wood-panel industry, highlighting the importance of selecting appropriate pressing parameters to achieve desired material properties.
Acknowledgements
The authors acknowledge the Norwegian Institute of Bioeconomy Research (NIBIO) for conducting the particle geometry scanning.
Disclosure statement
No potential conflict of interest was reported by the author(s).
Additional information
Funding
References
- Azeredo, H.M.C., et al., 2015. Wheat straw hemicellulose films as affected by citric acid. Food Hydrocolloids, 50, 1–6. https://doi.org/10.1016/j.foodhyd.2015.04.005
- CEN, 1993a. EN 310; wood-based panels—determination of modulus of elasticity in bending and of bending strength. Brussels: European Committee for Standardization.
- CEN, 1993b. EN 319; particleboards and fibreboards—determination of tensile strength perpendicular to the plane of the board. Brussels: European Committee for Standardization.
- CEN, 1993c. EN 317; particleboards and fibreboards—determination of swelling in thickness after immersion in water. Brussels: European Committee for Standardization.
- CEN, 2010. EN 312; particleboards-specifications. Brussels: European Committee for Standardization.
- Ding, Z., et al., 2021. Acidic buffering capacity and curing process of melamine-urea-formaldehyde resin. International Journal of Adhesion and Adhesives, 104, 102756. https://doi.org/10.1016/j.ijadhadh.2020.102756
- Dunky, M., 1998. Urea–formaldehyde (UF) adhesive resins for wood. International Journal of Adhesion and Adhesives, 18, 95–107.
- EPF, 2017. Annual Report 2016–2017. Brussels: EPF.
- Fehrmann, J., et al., 2024. Effects of mat composition and pressing time on citric acid-bonded ultra-low-density hemp hurd particleboard. Industrial Crops and Products, 210, 118070. https://doi.org/10.1016/j.indcrop.2024.118070
- Ferrandez-Garcia, M.T., et al., 2019. Experimental evaluation of a new giant reed (arundo donax L.) composite using citric acid as a natural binder. Agronomy, 9 (12), 882. https://doi.org/10.3390/agronomy9120882
- Food and Agriculture Organization of the United Nations, 2024. FAOSTAT Statistical Database. Available from: https://www.fao.org/faostat/en/#data/FO [Accessed 29 May 2024].
- Gomes, M.G., et al., 2020. Pretreated sugarcane bagasse with citric acid applied in enzymatic hydrolysis. Industrial Biotechnology, 16 (2), 117–124. https://doi.org/10.1089/ind.2019.0039
- Huaxu, Z., et al., 2021. Physico-Mechanical and biological durability of citric acid-bonded rubberwood particleboard. Polymers, 13 (1), 98. https://doi.org/10.3390/polym13010098
- Kanazawa, A., et al., 2010. Association between indoor exposure to semi-volatile organic compounds and building-related symptoms among the occupants of residential dwellings. Indoor Air, 20, 72–84.
- Korai, H., 2021. Difficulty of internal bond prediction of particleboard using the density profile. Journal of Wood Science, 67 (1), 64. https://doi.org/10.1186/s10086-021-01994-4
- Krug, D., et al., 2023. Particle-based materials. In: P. Niemz, A. Teischinger, and D. Sandberg, eds. Springer handbook of wood science and technology. Cham: Springer International Publishing, 1409–1490. https://doi.org/10.1007/978-3-030-81315-4_27
- Kusumah, S.S., et al., 2016. Utilization of sweet sorghum bagasse and citric acid for manufacturing of particleboard I: effects of pre-drying treatment and citric acid content on the board properties. Industrial Crops and Products, 84, 34–42. https://doi.org/10.1016/j.indcrop.2016.01.042
- Kusumah, S.S., et al., 2017. Utilization of sweet sorghum bagasse and citric acid for manufacturing of particleboard II: influences of pressing temperature and time on particleboard properties. Journal of Wood Science, 63 (2), 161–172. https://doi.org/10.1007/s10086-016-1605-0
- Lee, S.H., et al., 2020. A review on citric acid as green modifying agent and binder for wood. Polymers, 12 (8), 1692. Article 8. https://doi.org/10.3390/polym12081692
- McSweeny, J.D., Rowell, R.M., and Min, S.-H., 2006. Effect of citric acid modification of aspen wood on sorption of copper Ion. Journal of Natural Fibers, 3 (1), 43–58. https://doi.org/10.1300/J395v03n01_05
- Nitu, I.P., et al., 2022. Preparation and properties of jute stick particleboard using citric acid–glycerol mixture as a natural binder. Journal of Wood Science, 68 (1), 30. https://doi.org/10.1186/s10086-022-02039-0
- Notowiharjo, I., et al., 2022. Investigation of optimum particles size and citric acid content for coconut husk particleboard manufacturing. AIP Conference Proceedings, 2454, 020018. https://doi.org/10.1063/5.0078508
- Prasetiyo, K.W., et al., 2020. The potential of using agricultural waste: corn husk for particleboard raw material. IOP Conference Series: Earth and Environmental Science, 591 (1), 012011. https://doi.org/10.1088/1755-1315/591/1/012011.
- Rackwitz, G., 1963. Der Einfluß der Spanabmessungen auf einige Eigenschaften von Holzspanplatten. Holz als Roh- und Werkstoff, 21 (6), 200–209. https://doi.org/10.1007/BF02609724
- Santoso, M., et al., 2017. Bonding performance of maltodextrin and citric acid for particleboard made from nipa fronds. Journal of the Korean Wood Science and Technology, 45 (4), 432–443. https://doi.org/10.5658/WOOD.2017.45.4.432
- Santoso, M., et al., 2020. Effect of pressing temperatures on bonding properties of sucrose-citric acid for nipa palm fronds particleboard. Wood Research, 65 (5), 747–756. https://doi.org/10.3776/3wr.1336-4561/65.5.747756
- Scharf, A., et al., 2023. Particleboards bonded by an imidazole-based adhesive system. Materials, 16 (22), 7201. https://doi.org/10.3390/ma16227201
- Syamani, F.A., et al., 2018. Effect of pre-drying time and citric acid content on Imperata cylindrica particleboards properties. IOP Conference Series: Earth and Environmental Science, 209, 012034. https://doi.org/10.1088/1755-1315/209/1/012034
- Syamani, F.A., et al., 2020. High quality sugarcane bagasse-citric acid particleboards. IOP Conference Series: Earth and Environmental Science, 415 (1), 012006. https://doi.org/10.1088/1755-1315/415/1/012006
- Syamani, F.A., et al., 2022. Utilization of citric acid as bonding agent in sembilang bamboo (dendrocalamus giganteus munro) particleboard production. Indonesian Journal of Forestry Research, 9 (1), 99–120. https://doi.org/10.2088/6ijfr.2022.9.1.99-120
- Umemura, K., et al., 2012a. Application of citric acid as natural adhesive for wood. Journal of Applied Polymer Science, 123 (4), 1991–1996. https://doi.org/10.1002/app.34708
- Umemura, K., Ueda, T., and Kawai, S., 2012b. Characterization of wood-based molding bonded with citric acid. Journal of Wood Science, 58 (1), 38–45. Article 1. https://doi.org/10.1007/s10086-011-1214-x
- Umemura, K., Ueda, T., and Kawai, S., 2012c. Effects of moulding temperature on the physical properties of wood-based moulding bonded with citric acid. Forest Products Journal, 62 (1), 63–68.
- Umemura, K., Sugihara, O., and Kawai, S., 2015. Investigation of a new natural adhesive composed of citric acid and sucrose for particleboard II: effects of board density and pressing temperature. Journal of Wood Science, 61 (1), 40–44.
- Widodo, E., et al., 2020. Development of moulding using sweet sorghum bagasse and citric acid: effects of application method and citric acid content. Forest Products Journal, 70 (2), 151–157. https://doi.org/10.1307/3FPJ-D-19-00060
- Widyorini, R., et al., 2013. Characteristic of bamboo particleboard bonded with citric acid. Wood Research Journal, 4 (1), 31–35. https://doi.org/10.5185/0wrj.2013.4.1.31-35
- Widyorini, R., et al., 2014. Improving the physico-mechanical properties of eco-friendly composite made from bamboo. Advanced Materials Research, 896, 562–565. https://doi.org/10.4028/www.scientific.net/AMR.896.562.
- Widyorini, R., et al., 2016a. Bonding ability of a new adhesive composed of citric acid-sucrose for particleboard. BioResources, 11 (2), 4526–4535. https://doi.org/10.1537/6biores.11.2.4526-4535
- Widyorini, R., et al., 2016b. Manufacture and properties of citric acid-bonded particleboard made from bamboo materials. European Journal of Wood and Wood Products, 74 (1), 57–65. https://doi.org/10.1007/s00107-015-0967-0
- Widyorini, R., et al., 2018. Properties of citric acid-bonded composite board from elephant dung fibers. Journal of the Korean Wood Science and Technology, 46 (2), 132–142. https://doi.org/10.5658/WOOD.2018.46.2.132